混合比例对双组份结构胶的影响
双组份环氧树脂胶成分含量

双组份环氧树脂胶成分含量1. 简介双组份环氧树脂胶是一种常用的结构胶,由环氧树脂和固化剂两部分组成。
它具有优异的粘接性能、耐化学腐蚀性和机械强度,广泛应用于建筑、航空航天、汽车制造等领域。
本文将详细介绍双组份环氧树脂胶的成分含量及其对产品性能的影响。
2. 成分含量双组份环氧树脂胶主要由以下成分组成:2.1 环氧树脂环氧树脂是双组份环氧树脂胶的主要基础材料,占总配方的一部分。
它是一种聚合物,具有良好的附着性和耐化学性。
常用的环氧树脂有DGEBA(双酚A型环氧树脂)、EP(环氧丙烷)等。
不同类型的环氧树脂具有不同的特性,在选择时需要考虑使用环境和要求。
2.2 固化剂固化剂是双组份环氧树脂胶的另一个重要成分,与环氧树脂发生反应形成胶体结构。
常用的固化剂有胺类、酸酐类等。
不同的固化剂可以调节胶体的硬度、粘度和耐热性等性能。
2.3 填料填料是为了改善双组份环氧树脂胶的流变性能和增加其体积,常用的填料有二氧化硅、纳米材料等。
填料的添加量会影响胶体的黏度和流动性,同时也会对产品的强度和硬度产生影响。
2.4 助剂助剂是为了改善双组份环氧树脂胶的加工性能和终产品性能而添加的辅助材料。
常见的助剂有防老剂、促进剂、稳定剂等。
它们可以提高胶体的耐候性、抗老化性、粘接力等。
3. 成分含量对产品性能的影响双组份环氧树脂胶中各成分含量对产品性能具有重要影响,下面将详细介绍:3.1 环氧树脂含量环氧树脂含量的增加可以提高双组份环氧树脂胶的粘接强度和硬度,但也会降低其韧性和耐冲击性。
因此,在实际应用中需要根据具体要求进行调节。
3.2 固化剂含量固化剂含量的增加会加快胶体固化速度,并提高产品的硬度和耐热性。
但过高的固化剂含量可能会导致胶体过于脆硬,降低其韧性。
3.3 填料含量填料的添加可以改善双组份环氧树脂胶的流变性能,使其更易于施工。
同时,适当的填料含量还可以提高产品的强度和硬度。
然而,过多的填料会增加黏度,降低流动性。
3.4 助剂含量助剂对产品性能的影响较为细微,但仍然不可忽视。
双组份结构胶密度

双组份结构胶密度一、背景介绍双组份结构胶是一种常用于建筑、工程和家居装饰等领域的胶粘剂。
它由两种不同的组分(一般为胶浆和固化剂)混合而成,具有优异的粘结强度和耐久性。
而胶粘剂的密度是一个重要参数,它直接影响到胶水在使用过程中的流动性、涂布性以及固化效果等方面。
二、双组份结构胶的密度对胶水性能的影响2.1 流动性双组份结构胶的流动性主要受胶水密度的影响。
密度较低的胶水更容易流动,适用于需要较大涂布面积或较细小粘接间隙的场合。
而密度较高的胶水则更适用于需要填充较大空隙或形成较高胶层厚度的场合。
2.2 固化时间胶水的密度也会影响其固化时间。
一般来说,密度较低的胶水固化速度较快,而密度较高的胶水固化速度较慢。
因此,选择合适的胶水密度可以根据具体的施工需求来控制固化时间,以确保施工过程的顺利进行。
2.3 胶接强度胶水的密度对胶接强度也有一定影响。
密度较高的胶水在固化后往往具有更高的胶接强度,能够有效提升胶接件的抗剪强度和抗拉强度。
因此,在需要承受较大力学负荷的工程结构中,可以选择密度较高的胶水以提升胶接强度。
三、如何确定双组份结构胶的密度确定双组份结构胶的密度需要进行密度测试。
下面介绍一种常用的测试方法:3.1 实验工具与材料•密度计•量筒•秤量瓶•双组份结构胶样品3.2 实验步骤1.使用秤量瓶将胶水样品的质量测量并记录下来。
2.使用量筒将一定体积的胶水样品倒入秤量瓶中,注意避免空气泡存在。
3.用密度计测量秤量瓶中的胶水样品的体积并记录下来。
4.将步骤3中测得的胶水样品体积值除以质量值,即可得到胶水的密度。
四、常见双组份结构胶的密度范围根据不同的组分配比和固化剂比例,双组份结构胶的密度会有所差异。
以下是一些常见双组份结构胶的密度范围参考:1.低密度胶水:0.8-1.2 g/cm³–适用于需要较好的流动性和较大涂布面积的场合。
2.中密度胶水:1.2-1.6 g/cm³–适用于填充较小空隙和形成中等胶层厚度的场合。
双组份环氧胶_固化机理_解释说明以及概述

双组份环氧胶固化机理解释说明以及概述1. 引言1.1 概述双组份环氧胶作为一种常见的结构胶,广泛应用于各个领域,具有良好的粘接性能和耐化学品腐蚀性。
它由两个成分组成:环氧树脂和固化剂。
在固化过程中,这两个组分发生化学反应,形成胶体并硬化。
本文将重点讨论双组份环氧胶的固化机理,并探讨影响固化过程的因素以及解决方法。
1.2 文章结构本文共分为五个部分进行阐述。
在引言部分,我们将对双组份环氧胶进行概述,并介绍文章的结构和目的。
其次,在第二部分中,我们将详细介绍双组份环氧胶的基本概念、特点、成分和性质以及应用领域。
第三部分将解析双组份环氧胶的固化机理,包括固化剂与环氧树脂反应机制、温度和压力对固化过程的影响以及添加剂对固化速度和性能的影响。
接着,在第四部分中,我们将讨论影响环氧固化反应的主要阻碍因素,并提供相应的解决方法。
最后,在第五部分中,我们将对双组份环氧胶的固化机理进行总结,展望其未来应用,并提出未来研究方向和建议。
1.3 目的本文的目的是通过深入研究和详细解释双组份环氧胶的固化机理,使读者了解其基本概念、特点和成分,并了解其在各个领域中的应用。
同时,本文还旨在探讨固化过程中遇到的问题,并提供相关的解决方法。
通过本文的阐述,读者将能够更好地理解双组份环氧胶固化机理,并为未来研究和应用提供参考和指导。
2. 双组份环氧胶的基本概念和特点2.1 双组份环氧胶的定义双组分环氧胶是由两种不同成分组成的一种胶粘剂,其中一种成分为环氧树脂,另一种成分为固化剂。
这两种成分在使用之前需要分别储存在两个不同的容器中,混合使用时发生化学反应,形成坚固耐用的胶体。
2.2 双组份环氧胶的成分和性质(1)环氧树脂:环氧树脂是双组份环氧胶中的一部分,在固化过程中起到主要结构形成的作用。
它具有良好的粘接性、机械性能和耐腐蚀性,并且在低温下也能够硬化。
(2)固化剂:固化剂是双组份环氧胶中的另外一个关键部分,它与环氧树脂发生反应并使其硬化。
固化比例和养护温度对双组分硅酮结构密封胶性能的影响

Li Wa n y o n g, Xi e Zh e n, Yu Yi f a n
( C h i n a B u i l d i n g Ma t e i r a l T e s t &C e r t i i f c a t i o n G r o u p S u z h o u C o . , L t d . , S u z h o u , J i a n g s u 2 1 5 0 0 8 , C h i n a )
混合比例对双组分硅酮结构胶性能影响的探讨

c o n t r ol l e d d ur ing c o n s t u ct r i o n.
Ke y wo r d s : t wo — c o mp o n e n t s i l i c o n e s t uc r t u r a l s e a l a n t ; mi x i n g r a t i o ; s n a p t i me ; h a r d n e s s ; t e n s i l e b o n d i n g p e r f o ma r n c e
mi x i n g r a t i o o n p e r f o r ma n c e s o f t w o— c o mp o n e n t s i l i c o n e s e a l a n t s s u c h a s s n a p t i me ,h a r d n e s s a n d t e n s i l e b o n d i n g p e f r o r ma n c e s a t r o o m t e mp e r a t u r e a n d a f t e r i mme r s i o n . T h e r e s u l t s s h o w t h a t t h e o p t i ma l p e f r o r ma n c e s c a n b e o b t a i n e d wh e n s e a l a n t s mi x e d b y r e c o mme n d r a t i o ;i f t h e mi x i n g r a t i o b e y o n d t h e a l l o w e d r a n g e , t h e r e wi l l b e s e c u r i t y r i s k s b e c a u s e t h e p e f r o r ma n c e s o f s e a l a n t s a r e i mp a c t e d .I t s u g g e s t s t h a t mi x i n g r a t i o o f t wo - c o mp o n e n t s i l i c o n e s e a l a n t s s h o u l d b e s t i r c t l y
双组分环氧树脂胶粘剂

双组分环氧树脂胶粘剂
双组分环氧树脂胶粘剂是由两种不同组分混合而成的胶粘剂,其中一部分是环氧树脂,另一部分是硬化剂。
这两个组分在混合后会发生化学反应,形成一种强硬、耐化学腐蚀的胶黏剂。
以下是关于双组分环氧树脂胶粘剂的一些基本信息:
一、组成
1环氧树脂(Epoxy Resin):是一类高分子化合物,具有优异的附着性、机械强度和耐化学性能。
环氧树脂通常是液体或半固体,可以在室温下保存。
2硬化剂(Hardener):用于触发环氧树脂的固化反应。
硬化剂的种类和配比会影响胶黏剂的固化速度、硬度和性能。
二、固化过程:
1当环氧树脂与硬化剂混合时,它们发生化学反应,形成三维网络结构。
2这个化学反应通常是放热的,即产生热量。
这种放热反应是胶黏剂硬化的迹象。
三、特性和应用:
1强度:双组分环氧树脂胶粘剂通常具有很高的抗拉强度、抗剪切强度和抗撕裂强度。
2耐化学性:环氧树脂的化学稳定性使得它在许多化学环境下都能保持稳定。
环氧胶混合比例的转换

环氧胶混合比例的转换
双组份环氧胶转换重量混合比例到体积混合比例
1. 什么是混合比例?
环氧胶的混合比例对固化来说是非常重要。
环氧胶是树脂和固化剂的按一定化学计量比(两种物质反应的相对比例)进行化学反应。
不同产品的比例见TDS。
通泰化学
2. 为什么重要?
尽管不同化学混合都有不同的偏差,低于+/- 5%是可接受的。
在混合时偏差越大,使得未反应的成分残留在产品中,导致溢气率的增加,TG的减小,抗化学腐蚀和抗水能力减弱。
3. 混合比例可参考的是?
所有双组份环氧胶的混合比例。
对于一些应用,客户认为体积比混合相对重量比混合更加容易。
不经转换,直接使用TDS 的重量混合比用作体积混合会导致不能正确固化。
4. 如何转换?
通过使用TDS 上每个各组分的比重能够很容易的得到体积比,比重是无单位的量纲,定义为物质的密度与水的密度的比值。
因为水的密度大约为1g/cc,比重在计算中可以被认
作为密度。
ab双组份胶的粘结力
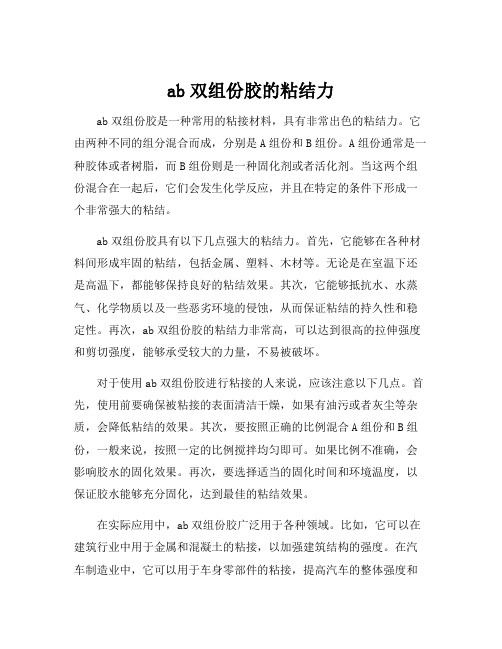
ab双组份胶的粘结力ab双组份胶是一种常用的粘接材料,具有非常出色的粘结力。
它由两种不同的组分混合而成,分别是A组份和B组份。
A组份通常是一种胶体或者树脂,而B组份则是一种固化剂或者活化剂。
当这两个组份混合在一起后,它们会发生化学反应,并且在特定的条件下形成一个非常强大的粘结。
ab双组份胶具有以下几点强大的粘结力。
首先,它能够在各种材料间形成牢固的粘结,包括金属、塑料、木材等。
无论是在室温下还是高温下,都能够保持良好的粘结效果。
其次,它能够抵抗水、水蒸气、化学物质以及一些恶劣环境的侵蚀,从而保证粘结的持久性和稳定性。
再次,ab双组份胶的粘结力非常高,可以达到很高的拉伸强度和剪切强度,能够承受较大的力量,不易被破坏。
对于使用ab双组份胶进行粘接的人来说,应该注意以下几点。
首先,使用前要确保被粘接的表面清洁干燥,如果有油污或者灰尘等杂质,会降低粘结的效果。
其次,要按照正确的比例混合A组份和B组份,一般来说,按照一定的比例搅拌均匀即可。
如果比例不准确,会影响胶水的固化效果。
再次,要选择适当的固化时间和环境温度,以保证胶水能够充分固化,达到最佳的粘结效果。
在实际应用中,ab双组份胶广泛用于各种领域。
比如,它可以在建筑行业中用于金属和混凝土的粘接,以加强建筑结构的强度。
在汽车制造业中,它可以用于车身零部件的粘接,提高汽车的整体强度和稳定性。
在家具制造业中,它可以用于木材的粘接,增加家具的稳固性。
此外,在航空航天、电子、电气等领域,ab双组份胶也有着广泛的应用。
总的来说,ab双组份胶具有粘结力强、适用范围广的特点。
在使用时,要注意表面清洁、正确比例的混合以及适当的固化时间和环境温度。
相信通过正确的使用和操作,ab双组份胶将为我们的粘接工作提供高效、可靠的解决方案。
双组份胶比例管控 -回复

双组份胶比例管控-回复[双组份胶比例管控],是指在使用双组份胶粘剂时,确保两个组分的比例正确,以达到最佳的粘接效果和性能。
正确的比例管控是使用双组份胶粘剂的关键,否则可能导致不完全固化、降低粘接强度或者产品性能不稳定等问题。
本文将逐步回答如何进行双组份胶比例管控,以确保胶粘剂的质量可靠。
第一步:了解胶粘剂的组分和比例要求在进行双组份胶比例管控前,首先需要了解胶粘剂的组分和所需的比例要求。
一般来说,双组份胶粘剂由胶胶和固化剂两部分组成。
不同的胶粘剂有不同的配比要求,可以通过查阅产品说明书、技术资料或者咨询生产厂家等方式获取这些信息。
明确了双组份胶粘剂的组分和比例要求后,才能进行后续的比例管控操作。
第二步:选择合适的比例控制装置为了精确控制双组份胶的比例,通常需要使用比例控制装置。
在选择比例控制装置时,需要考虑胶粘剂的特性、使用环境、生产需求等因素。
常见的比例控制装置包括手动比例泵、气动比例泵、电动比例泵等。
每种比例控制装置都有其特点和适用范围,需要根据具体情况进行选择。
第三步:校准和测试比例控制装置在使用比例控制装置之前,需要对其进行校准和测试,确保其输出的比例准确可靠。
校准和测试的方法可以根据具体的比例控制装置进行操作。
一般来说,可以通过准备一定量的胶粘剂混合物,将其按比例加入比例控制装置,并通过称重或者流量计等方式检测装置的输出比例,来判断其准确性。
第四步:进行比例管控的实际操作根据胶粘剂的比例要求和已校准的比例控制装置,可以开始进行比例管控的实际操作。
具体操作步骤如下:1. 将两个组分的胶粘剂分别放置在专用容器中,然后通过比例控制装置将其按照要求的比例混合在一起。
2. 注意在混合过程中保持混合均匀,可以通过搅拌或者机械混合等方式来实现。
3. 在混合完成后,根据实际需要进行胶粘剂的使用或者存储。
第五步:检验和监控胶粘剂的比例在比例管控操作完成后,需要对混合后的胶粘剂进行检验和监控,以确保比例控制的准确性和一致性。
双组份硅酮胶固化原理

双组份硅酮胶固化原理双组份硅酮胶固化原理什么是双组份硅酮胶双组份硅酮胶是一种两种单体组成的胶粘剂,其中一个组份为硅酮单体,另一个组份为交联剂。
这种胶粘剂在使用前需要将两组份混合,然后经过一定时间后会固化成坚固且耐用的材料。
硅酮胶固化的原理双组份硅酮胶固化的过程主要通过反应中的交联反应实现。
在混合二组份硅酮胶后,其中的交联剂会与硅酮单体中的活性基团发生反应,形成化学键,从而使整个体系固化。
交联反应的机理交联反应是指两个或多个分子之间通过化学键连接在一起的过程。
在双组份硅酮胶中,交联剂通常是含有两个或多个反应活性基团的化合物。
这些基团能够和硅酮单体中的活性基团发生反应,形成硅氧键或其他强化学键。
双组份硅酮胶固化过程1.混合两组份:将硅酮单体和交联剂按照一定的比例混合在一起。
2.反应发生:随着两组份的混合,交联剂中的活性基团开始与硅酮单体中的活性基团发生反应。
这些反应会引发多个交联反应链的形成。
3.交联扩散:在反应过程中,交联反应链会扩散至整个混合体系中,进一步形成更多的交联连接。
4.固化完成:随着交联反应的进行,双组份硅酮胶逐渐从流动的液体固化为坚固的固体材料。
固化的时间通常取决于胶粘剂的配方和环境条件。
双组份硅酮胶固化的特点•快速固化:双组份硅酮胶的固化速度较快,可以在短时间内达到一定的强度。
•耐高温:固化后的双组份硅酮胶具有较高的耐高温性能,可以在高温环境下维持稳定性。
•耐候性好:双组份硅酮胶固化后的材料具有良好的耐候性,能够长时间抵御紫外线、氧气和潮湿等因素的侵蚀。
•优异的弹性和粘接性:双组份硅酮胶固化后形成柔软有弹性的材料,具有良好的粘接性和密封性能。
应用领域双组份硅酮胶固化原理的独特性能使其广泛应用于各个领域,包括建筑、航天航空、汽车制造、电子设备等。
它可以用于密封、粘接、填缝和绝缘等多种用途。
结论双组份硅酮胶的固化原理主要通过交联反应实现。
交联剂与硅酮单体之间的反应形成了耐高温、耐候性好、具有优异弹性和粘接性的固体材料。
双组分丙烯酸结构胶
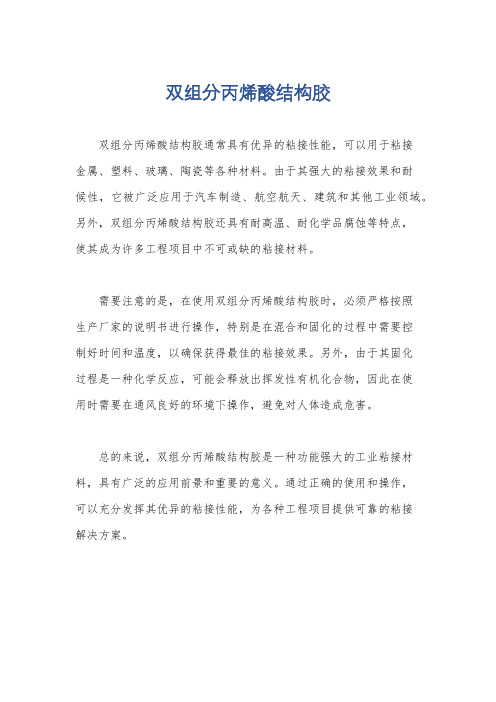
双组分丙烯酸结构胶
双组分丙烯酸结构胶通常具有优异的粘接性能,可以用于粘接
金属、塑料、玻璃、陶瓷等各种材料。
由于其强大的粘接效果和耐
候性,它被广泛应用于汽车制造、航空航天、建筑和其他工业领域。
另外,双组分丙烯酸结构胶还具有耐高温、耐化学品腐蚀等特点,
使其成为许多工程项目中不可或缺的粘接材料。
需要注意的是,在使用双组分丙烯酸结构胶时,必须严格按照
生产厂家的说明书进行操作,特别是在混合和固化的过程中需要控
制好时间和温度,以确保获得最佳的粘接效果。
另外,由于其固化
过程是一种化学反应,可能会释放出挥发性有机化合物,因此在使
用时需要在通风良好的环境下操作,避免对人体造成危害。
总的来说,双组分丙烯酸结构胶是一种功能强大的工业粘接材料,具有广泛的应用前景和重要的意义。
通过正确的使用和操作,
可以充分发挥其优异的粘接性能,为各种工程项目提供可靠的粘接
解决方案。
双组份胶比例管控
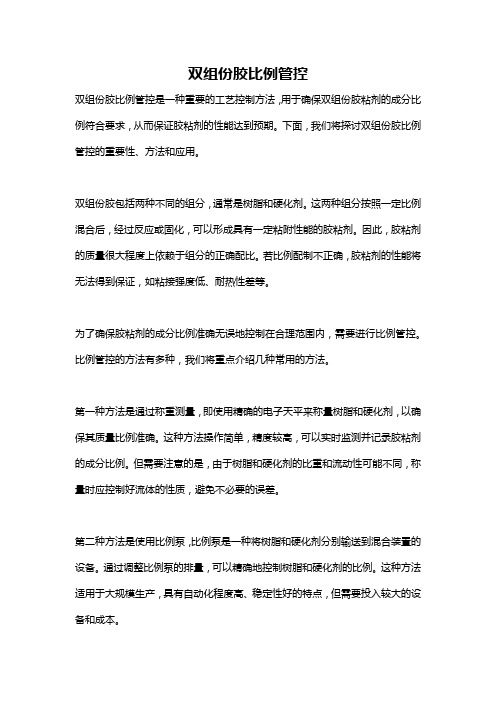
双组份胶比例管控双组份胶比例管控是一种重要的工艺控制方法,用于确保双组份胶粘剂的成分比例符合要求,从而保证胶粘剂的性能达到预期。
下面,我们将探讨双组份胶比例管控的重要性、方法和应用。
双组份胶包括两种不同的组分,通常是树脂和硬化剂。
这两种组分按照一定比例混合后,经过反应或固化,可以形成具有一定粘附性能的胶粘剂。
因此,胶粘剂的质量很大程度上依赖于组分的正确配比。
若比例配制不正确,胶粘剂的性能将无法得到保证,如粘接强度低、耐热性差等。
为了确保胶粘剂的成分比例准确无误地控制在合理范围内,需要进行比例管控。
比例管控的方法有多种,我们将重点介绍几种常用的方法。
第一种方法是通过称重测量,即使用精确的电子天平来称量树脂和硬化剂,以确保其质量比例准确。
这种方法操作简单,精度较高,可以实时监测并记录胶粘剂的成分比例。
但需要注意的是,由于树脂和硬化剂的比重和流动性可能不同,称量时应控制好流体的性质,避免不必要的误差。
第二种方法是使用比例泵,比例泵是一种将树脂和硬化剂分别输送到混合装置的设备。
通过调整比例泵的排量,可以精确地控制树脂和硬化剂的比例。
这种方法适用于大规模生产,具有自动化程度高、稳定性好的特点,但需要投入较大的设备和成本。
第三种方法是采用专用的比例控制系统,该系统通常由控制器、流量传感器和执行器等组成。
通过实时监测树脂和硬化剂的流量,并通过控制器根据设定的比例控制信号来调节流量,从而保证树脂和硬化剂的比例准确。
这种方法相对复杂,但适用于对比例精度要求较高的情况。
双组份胶比例管控广泛应用于各种工业领域,特别是在粘接、密封和涂覆等工艺中。
在汽车制造、电子器件封装、建筑施工等领域,这种胶粘剂被广泛应用。
比例管控的良好效果可以确保产品质量符合规定标准,提高生产效率,减少浪费和成本。
在实际应用过程中,双组份胶比例管控也需要注意一些问题。
首先,需要选用合适的校验方法来验证比例控制的准确性。
可以通过对成品产品进行物理性能测试和使用寿命试验来检验胶粘剂的性能是否符合要求。
双组份结构胶协议

双组份结构胶协议一、胶粘剂的定义和分类胶粘剂是指用于粘接及连接材料的一种材料。
根据其化学成分和特性,胶粘剂可以分为多种不同类型,如单组份胶粘剂、双组份胶粘剂等。
本文将重点介绍双组份结构胶协议。
二、双组份结构胶的特点和应用范围1.高强度:作为一种结构胶,双组份胶粘剂具有较高的强度,能够提供可靠的结构连接。
2.快速固化:双组份结构胶具有较快的固化速度,能够在短时间内形成高强度的粘接。
3.耐久性好:双组份结构胶的粘接具有优异的耐久性,能够在恶劣环境中保持良好的粘接性能。
4.适用性广:双组份胶粘剂适用于多种不同材料的粘接,如金属、塑料、玻璃等。
双组份结构胶的应用范围非常广泛,包括建筑、汽车制造、航空航天等领域。
在建筑领域,双组份结构胶主要用于玻璃幕墙、铝合金门窗等结构的粘接。
在汽车制造领域,双组份结构胶主要用于车身和车门的粘接。
在航空航天领域,双组份结构胶主要用于航空器的粘接。
三、双组份结构胶的使用和注意事项1.混合比例:使用双组份胶粘剂前,需要正确的混合两种组分的比例。
不同的胶粘剂有不同的混合比例,必须根据产品说明书来操作。
2.混合搅拌:将两种组分倒入专用容器中,用搅拌器均匀搅拌1-2分钟,直到得到均匀混合的粘合剂。
3.施工温度:双组份结构胶的施工温度一般在5-35℃之间,过低或过高的温度都会影响胶粘剂的固化速度和性能。
4.施工条件:施工表面需要干燥、清洁、平整,没有油污、灰尘等杂质。
施工前需要做好表面处理工作。
5.固化时间:胶粘剂的固化时间受到温度、湿度、厚度等因素的影响。
在固化时间内,需要保持胶粘剂的温度和湿度稳定。
6.安全注意事项:在使用双组份结构胶时,需要注意防止胶粘剂溅入眼睛或皮肤,必要时使用个人防护措施。
四、双组份结构胶在实际工程中的应用案例1.玻璃幕墙粘接:在建筑行业中,双组份结构胶广泛应用于玻璃幕墙的粘接。
它可以提供稳定的结构连接,使幕墙具有抗风压和抗震能力。
2.车身粘接:在汽车制造行业中,双组份结构胶用于车身零部件的粘接。
双组份结构胶质量控制SXF-07

双组份结构胶质量控制(一)Q u a l i t y C o n t r o l f o r D o u b l e-C o m p o n e n t S t r u c t u r a l S e a l a n t(1)项目名称Project Name:检验项目Inspection Item:蝴蝶测试Butterfly Test测试方法Testing Method 测试结果Test Result 蝴蝶测试控制程序C o n t r o l P r o g r a m f o r B u t t e r f l y Te s t这个程序是为了确定双组份密封剂是否已彻底混合均匀。
This program is to determine if the double-component sealant is mixed completely.混合不均会引起产品性能的极大变化。
Under-mixing will greatly affect the performance of production.1.将纸折叠(白色纸A4的1/2大小)Fold the paper(1/2 of the size of A4 paper)2.将混合后的密封剂涂在纸上,将纸折叠使密封平整。
Apply the blended sealant on the paper, and fold it to make the sealant even.3.打开纸,检查密封剂,如是密封剂上出现白色条纹,表示混合不充分,如果没有条纹出现则表明已充分混合,并在纸上记录年月日及结构胶基质与固化剂的批号。
Open the paper, check the sealant, If there is a white strip on the sealant, indi cating that it is under-mixing, otherwise it is mixed completely. 结构胶牌号Sealant Trademark:基质(白色)批号Base (White) Batch A:固化剂(黑色)批号Hardener(Black) Batch B:测试时间Testing Time:操作者Operator:专职质检员Sole Duty Inspector:Form No.表格编号:SXF–07(1)双组份结构胶质量控制(二)Q u a l i t y C o n t r o l f o r D o u b l e-C o m p o n e n t S t r u c t u r a l S e a l a n t(2)工程名称Project Name:检查项目Inspection Item:拉断时间测试Snap Time Test测试方法Testing Method 测试结果Testing Result拉断时间测试程Test Program of Snap Time此程序用来测定双组份结构密封剂的固化速率,不正常的拉断时间(或长或短)表明混合过程中基体/固化剂的比例存在问题。
双组份胶比例管控

双组份胶比例管控
【原创版】
目录
1.双组份胶的概述
2.双组份胶比例管控的重要性
3.双组份胶比例管控的方法
4.双组份胶比例管控的应用实例
5.双组份胶比例管控的未来发展
正文
一、双组份胶的概述
双组份胶,顾名思义,是由两种不同成分的胶粘剂组成的。
这两种成分在储存时是分开的,但在使用时需要按一定比例混合,才能发挥最佳的粘接效果。
双组份胶广泛应用于建筑、家居、汽车、电子等领域。
二、双组份胶比例管控的重要性
双组份胶的粘接效果与其成分比例密切相关,如果比例控制不准,可能会导致粘接强度不足,影响产品的使用寿命和性能。
因此,双组份胶比例管控是保证产品质量的关键环节。
三、双组份胶比例管控的方法
目前,双组份胶比例管控主要采用称重法和容积法。
称重法是利用电子称精确地称量出两种成分的重量,然后按比例混合。
容积法则是利用容器的体积来精确计量两种成分的比例。
四、双组份胶比例管控的应用实例
以聚氨酯泡沫胶为例,它是一种常见的双组份胶,用于保温材料、家具制造等领域。
在使用聚氨酯泡沫胶时,需要将 A、B 两种成分按 1:1 的
比例混合,才能达到最佳的粘接效果。
五、双组份胶比例管控的未来发展
随着科技的进步,双组份胶比例管控将更加精确和智能化。
例如,通过引入机器学习和人工智能技术,可以实现更准确的比例控制,提高生产效率和产品质量。
双组分聚氨酯胶粘剂介绍及特点(精)

双组分聚氨酯胶粘剂介绍及特点双组分聚氨酯胶粘剂是聚氨酯胶粘剂中最重要的一个大类,用途广,用量大。
通常由甲、乙两个组分组成,两个组分是分开包装的,使用前按一定比例配制即可。
甲组分(主剂)为羟基组分,乙组分(固化剂)为含游离异氰酸酯基团的组分。
也有的主剂为端基NCO的聚氨酯预聚体,固化剂为低分子量多元醇或多元胺,甲组分和乙组分按一定比例混合生成聚氨酯树脂。
双组分聚氨酯胶粘剂具有以下特点。
(1)属反应性的胶粘剂在两个组分混合后,发生交联反应,产生固化产物。
(2)制备时,可以调节两组分的原料组成和分子量,使之在室温下有合适的粘度,可制成高固含量或无溶剂双组分胶粘剂。
(3)通常可室温固化,通过选择制备胶粘剂的原料或加入催化剂可凋节固化速度。
一般,双组分聚氨酯胶粘剂有较大的初粘合力,叫加热固化,其最终粘合强度比单组分胶粘剂大,可以满足结构胶粘剂的要求。
(4)两个组分的用量可在一定范围内调节,一般存在着一定容忍度。
两组分的NCO /OH摩尔比在一般情况下大于或等于l,当固化时,一部分NCO基团参与胶的固化反应,产生化学粘合力,多余的NC0基团在加热固化时,还可产生脲基甲酸酯、缩二脲等,增加交联度,提高了胶层的内聚强度和耐热性。
对于无溶剂双组分聚氨酯胶粘剂来说,因各组分起始分子量不大,一般来说NCO/OH摩尔比等于或稍大于l,有利于固化完全,特别在粘合密封件时,注意NCO组分不能过量太多。
而对于溶剂型双组分胶粘剂来说,其主剂分子量较大,初粘性能较好,两组分的用量可在较大范围内调节,NCO/OH摩尔比可小于1或大于1的数倍。
当NCO组分(固化剂)过量较多的场合,多异氰酸酯自聚形成坚韧的胶粘层,适合于硬材料的粘接;在NCO组分用量少的场合,则胶层柔软,可用于皮革、织物等软材料的粘接。
双组分聚氨酯胶粘剂自问世以来,由于具有性能可调节性、粘合强度大、粘接范围广等优点,已成为聚氨酯胶粘剂中品种最多、产量最大的产品。
通用型双组分聚氨酯胶粘剂通用型聚氨酯胶粘剂是以聚己二酸乙二醇酯为原料、以溶剂聚氨酯树脂为主成分(甲组分),以三羟甲基丙烷—T1)I加成物为固化剂(乙组分)的双组分聚氨酯胶粘剂。
双组份胶比例管控
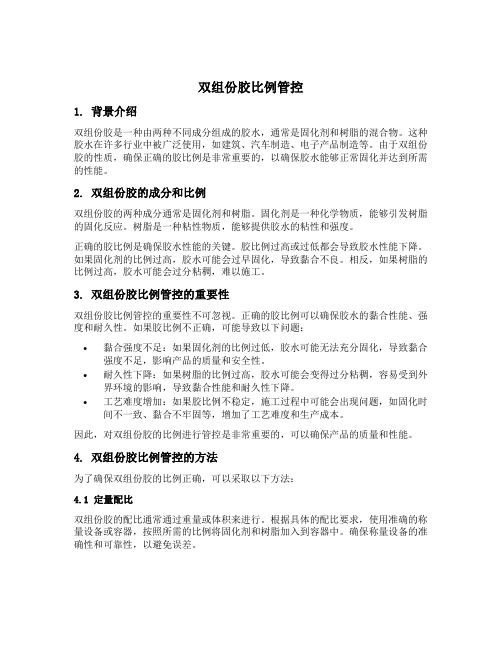
双组份胶比例管控1. 背景介绍双组份胶是一种由两种不同成分组成的胶水,通常是固化剂和树脂的混合物。
这种胶水在许多行业中被广泛使用,如建筑、汽车制造、电子产品制造等。
由于双组份胶的性质,确保正确的胶比例是非常重要的,以确保胶水能够正常固化并达到所需的性能。
2. 双组份胶的成分和比例双组份胶的两种成分通常是固化剂和树脂。
固化剂是一种化学物质,能够引发树脂的固化反应。
树脂是一种粘性物质,能够提供胶水的粘性和强度。
正确的胶比例是确保胶水性能的关键。
胶比例过高或过低都会导致胶水性能下降。
如果固化剂的比例过高,胶水可能会过早固化,导致黏合不良。
相反,如果树脂的比例过高,胶水可能会过分粘稠,难以施工。
3. 双组份胶比例管控的重要性双组份胶比例管控的重要性不可忽视。
正确的胶比例可以确保胶水的黏合性能、强度和耐久性。
如果胶比例不正确,可能导致以下问题:•黏合强度不足:如果固化剂的比例过低,胶水可能无法充分固化,导致黏合强度不足,影响产品的质量和安全性。
•耐久性下降:如果树脂的比例过高,胶水可能会变得过分粘稠,容易受到外界环境的影响,导致黏合性能和耐久性下降。
•工艺难度增加:如果胶比例不稳定,施工过程中可能会出现问题,如固化时间不一致、黏合不牢固等,增加了工艺难度和生产成本。
因此,对双组份胶的比例进行管控是非常重要的,可以确保产品的质量和性能。
4. 双组份胶比例管控的方法为了确保双组份胶的比例正确,可以采取以下方法:4.1 定量配比双组份胶的配比通常通过重量或体积来进行。
根据具体的配比要求,使用准确的称量设备或容器,按照所需的比例将固化剂和树脂加入到容器中。
确保称量设备的准确性和可靠性,以避免误差。
4.2 自动控制系统在大规模生产中,可以使用自动控制系统来实现双组份胶的比例管控。
通过传感器和控制器,监测和调节固化剂和树脂的流量,确保其比例稳定和准确。
4.3 质量控制检测在生产过程中,需要进行质量控制检测,以确保双组份胶的比例符合要求。
胶粘剂 双组分

胶粘剂双组分
胶粘剂是一种广泛应用于工业生产和日常生活中的化学制品。
它的主要作用是将两个或多个物体粘合在一起,以达到固定和加强的效果。
而双组分胶粘剂则是一种由两种不同的化学物质混合而成的胶粘剂,它们在混合后会发生化学反应,从而形成一种强力的粘合剂。
双组分胶粘剂的主要成分是树脂和固化剂。
树脂是一种具有粘性的高分子化合物,它可以在固化剂的作用下形成一种坚固的结构。
而固化剂则是一种化学物质,它可以促进树脂的固化反应,从而形成一种强力的粘合剂。
双组分胶粘剂的使用非常广泛,它可以用于粘合各种材料,如金属、塑料、木材、陶瓷等。
它的粘合效果非常好,可以承受很大的拉力和剪切力,而且具有很好的耐久性和耐腐蚀性。
因此,它被广泛应用于汽车、航空、建筑、电子、家具等领域。
双组分胶粘剂的使用方法也非常简单。
首先,将树脂和固化剂按照一定的比例混合在一起,然后将混合好的胶粘剂涂在需要粘合的物体表面上,最后将两个物体紧密地压在一起,等待一定的时间后,胶粘剂就会固化成为一种坚固的结构。
双组分胶粘剂是一种非常实用的化学制品,它具有很好的粘合效果和耐久性,被广泛应用于各个领域。
在使用时,我们需要注意混合比例和固化时间,以确保粘合效果的最佳。
双组分涂料,配方设计中的配料比

双组分涂料,配方设计中的配料比配方设计是双组分涂料制备过程中十分重要的环节,配料比的确定直接影响到涂料的性能和应用效果。
本文将从配料比的选择、配料的选择和具体配方设计三个方面进行阐述。
一、配料比的选择配料比是指涂料中各组分的质量或体积比例。
在配方设计过程中,需要根据涂料的使用要求和性能指标来选择合适的配料比。
一般来说,影响涂料性能的因素有很多,如涂料的固化速度、附着力、硬度、耐候性等。
因此,在确定配料比时,需要综合考虑这些因素,并结合实际情况进行调整。
二、配料的选择配料的选择是指根据涂料的性能要求和使用环境选择合适的配料。
在双组分涂料中,通常包括树脂和固化剂两部分。
树脂是涂料的主要成分,决定了涂料的基本性能,如耐化学性、耐热性等。
固化剂则是决定涂料固化速度和硬度的关键因素。
在选择配料时,需要考虑树脂和固化剂之间的相容性、反应性以及与基材的粘附性等。
三、具体配方设计在具体的配方设计中,需要根据涂料的使用要求和性能指标来确定每个配料的用量。
一般来说,树脂和固化剂的用量是根据化学计量比来确定的,即树脂和固化剂的摩尔比。
此外,还需要考虑到其他助剂的添加,如稀释剂、增稠剂、消泡剂等,以及颜料的选择和添加。
这些助剂和颜料的添加不仅可以改善涂料的性能,还可以调整涂料的颜色和外观效果。
在配方设计过程中,还需要考虑到涂料的加工性能和施工性能。
加工性能是指涂料在制备过程中的流变性能,如粘度、流动性等。
施工性能是指涂料在实际使用中的涂布性能,如涂料的干燥时间、涂膜的光泽度等。
为了提高涂料的加工性能和施工性能,可以通过调整配料的选择和用量来进行优化。
配方设计是双组分涂料制备过程中不可或缺的环节。
通过合理选择配料比和配料的选择,并进行具体的配方设计,可以得到性能优良的双组分涂料。
在实际应用中,还需要根据不同的使用环境和要求进行调整和优化,以达到最佳的涂料效果。
- 1、下载文档前请自行甄别文档内容的完整性,平台不提供额外的编辑、内容补充、找答案等附加服务。
- 2、"仅部分预览"的文档,不可在线预览部分如存在完整性等问题,可反馈申请退款(可完整预览的文档不适用该条件!)。
- 3、如文档侵犯您的权益,请联系客服反馈,我们会尽快为您处理(人工客服工作时间:9:00-18:30)。
混合比例对双组份结构胶的影响————————————————————————————————作者: ————————————————————————————————日期:混合比例对双组份结构胶的影响硅酮结构胶由于优异的耐候性成为幕墙的首选材料。
双组份硅酮结构胶因为具有固化时间短、深层固化快的特点,可大幅提高施工效率、加快施工速度,所以目前已在幕墙和中空玻璃上大量应用。
但是,双组分硅酮结构胶一般需要专门的打胶设备将A、B组分混合好才能使用,混合不好或混合比例不当容易出质量问题;因此,双组份硅酮结构胶的混合问题值得我们关注。
一般的,双组份硅酮结构密封胶厂家提供的混合比例是一个范围。
主要是基于以下两个方面的考虑:一方面,考虑使用的环境不同和气候条件的变化,从而导致双组份胶固化反应的快慢不同,为达到理想、适度的固化速度,所以混合比例不可能是一成不变的,要有一个适度的范围,以便使产品具有一定的环境适应性;另一方面,在保持胶的性能变化不大的情况下,可适度调整固化速度的快慢,给予用户适度的生产效率调控空间,以便使产品具有一定的用户适应性。
本文通过对目前工程上使用的双组分产品白云牌SS622、国内某品牌产品和进口某品牌产品作为代表性试样进行试验,探讨其不同混合比例对其性能的影响,为双组分结构胶同类产品的使用提供参考。
1 试验部分1.1 试样制备及测试方法1)试样双组份硅酮结构胶:试样A:白云牌SS622双组份结构胶(混合体积比范围9:1~11:1,推荐体积比A:B=10:1)、试样B:国内某品牌双组份结构胶(混合体积比范围7.6:1~10.6:1,推荐体积比A:B=9:1)、试样C:进口某品牌双组份结构胶(混合体积比范围7.2:1~8.7:1,推荐体积比A:B=8:1)。
基材:阳极氧化表面处理铝型材,普通浮法玻璃;用异丙醇溶液处理,不抹底涂;2)测试项目及标准拉伸粘接性测试、硬度和拉断时间按:GB 16776-2005 《建筑用硅酮结构密封胶》1.2 实验设备万能拉力实验机:CMT 4304,深圳三思纵横科技股份有限公司邵氏硬度计:LX-A型橡胶硬度计,上海市六菱仪器厂1.3 实验方案每个试样按照其生产厂家分别推荐的A 、B 组分混合比例以及允许的混合比例的上下限和超出上下限比例进行混胶,试样混胶方案,见表1。
已混合好的试样按标准GB 16776-2005相关要求进行制样、养护和测试。
2 结果与讨论2.1 拉断时间按GB 16776-2005测试了三个试样分别在不同混合比例下的拉断时间变化,见图1。
用户在使用前调试过程中,拉断时间是判断混合比例是否正常的重要标志。
拉断时间过短,固化过快不利于使用和修整,拉断时间过长,固化过慢,影响幕墙和中空玻璃的养护时间,延长工期。
在已确定混合比例下,拉断时间是确定混胶设备是否正常及产品稳定性的指标。
双组分胶混合后的时间一旦超过拉断时间,就会急剧增稠,呈半固化状,无法继续施工修整。
如图1所示:试样A,在比例范围内,混合比为10:1时拉断时间为55min ,11:1时拉断时间延长到63min,拉断时间较为合适,而超出比例范围为12:1时拉断时间大大延长为 85m in ,8:1时急剧缩短为 30min 。
试样B,在比例范围内,混合比例为9:1时为40m in,10.6:1时延长到57min,而在超出范围为12:1时拉断时间急剧延长为93mi n,8:1时迅速缩短为27min。
试样C,在比例范围内,混合比为8:1时拉断时间为42min,在比例上限8.7:1时拉断时间缓慢延长到50min,超出比例范围后,混合比为10:1时,拉断时间大大延长为79min。
经以上分析可认为:在允许比例范围内,双组份的拉断时间变化不是非常明显;低于允许比例下限时,即B组分添加过多,拉断时间明显变短;高于允许比例上限,即B组分过少,拉断时间明显延长。
拉断时间过短不利于使用和修整,施工过程中打胶枪容易出现“堵枪”现象,拉断时间过长可能会导致固化时间大大延长。
2.2硬度硬度是GB 16776-2005中的一个指标,GB16776-2005要求硬度范围为20~60Hs A。
按GB 16776-2005测试了三个试样不同混合比例对胶的硬度的影响,见图2。
如图2所示,双组份结构胶的硬度受混合比例的影响较明显。
试样A 在推荐比例10:1时,硬度为40HsA ,在允许比例上限时硬度为39HsA,在允许比例下限时硬度41HsA ,硬度变化较缓慢;而超出范围混合比为12:1时硬度急剧变小为37HsA,混合比为8:1时硬度增大为43Hs A。
试样B,在推荐比例9:1时,硬度为39H sA,在允许比例上限时硬度为37HsA,在允许比例下限时硬度为41HsA,硬度变化小。
试样C,在推荐比例8:1时,硬度为38HsA ,在允许比例上限时硬度为38Hs A,在允许比例下限时硬度为39HsA,硬度变化不明显,而超出范围混合比为6:1时硬度值大大提高到42H sA 。
由以上分析可以认为:上述硬度变化范围虽然仍在标准GB16776-2005要求范围内,但是混合比例超出厂家允许的比例范围时,硬度的变化的趋势更为明显:高于上限时,B组分过少,硬度明显变低,低于下限时,B组分过多,硬度明显偏高。
2.3常温拉伸粘接性2.3.1常温拉伸粘接性的最大强度值按照GB16776-2005分别测试了三个试样不同混合比例的常温拉伸结性,其中拉伸粘结性最大强度值见图3。
图3所示三个试样的拉伸粘结性中最大强度值与混合比例的对应关系。
试样A,在推荐混合比10:1时,强度达到最大值为1.49MPa;在推荐范围内,混合比为9:1时强度为1.44MPa,1 1:1时强度为1.45MPa,强度有小幅度下降,下降幅度在3%左右;超出比例范围时,混合比为12: 1强度为1.35MPa,强度值下降幅度较大,超过9%。
B试样和C试样均在推荐混合比时最大强度值达到最大,试样B为1.23MPa,试样C为1.36MPa;在比例范围内强度值均有降低趋势,试样B降低幅度为7%试样,C降低幅度为3%; 而超出比例范围后,强度均急剧下降,下降幅度均超过10%。
由以上分析可以认为:双组份结构胶在厂家推荐混合比例时最大强度值最大,在允许比例范围内时,所测得最大强度值下降幅度较小;超出比例范围后,最大强度值下降幅度急剧增大。
2.3.2 常温拉伸粘结性的最大强度时伸长率2.3.1所测试的三个试样的拉伸粘结性,拉伸粘结性中最大强度时伸长率,见图5。
图4所示三个试样的最大强度时伸长率与混合比例的对应关系。
如图4所示,随着B组分含量的增加,最大强度伸长率逐渐下降。
如果超过推荐的混合比例,B组分过多,胶固化后的最大强度伸长率会降低,影响胶的弹性。
2.3.3 常温拉伸粘结性的粘结破坏面积2.3.1所测试的三个试样的拉伸粘结性,拉伸粘结性的粘结破坏面积,见表2。
如表2所示,三种试样在推荐比例范围内,均粘接良好。
而超出允许比例范围,均出现小面积粘接破坏,分别为A试样2%,B试样8%和C试样2%及5% 。
由以上分析可认为:双组分结构胶的常温拉伸粘结性破坏面积,在允许混合比例范围内,粘结良好;超出允许比例范围,有可能会出现部分不粘的现象。
2.4浸水后的拉伸粘接性2.4.1浸水后的拉伸粘接性的最大强度值按GB16776-2005测试了三个试样浸水后的拉伸粘结性,最大强度值见图5。
图5所示,三个试样浸水后的最大强度受混合比例的影响明显。
三个试样均在推荐混合比例时最大强度值最大,其中试样A为1.35MPa、试样B为1.23MPa、试样C为1.33MPa。
在允许比例范围内强度的下降幅度较小,其中试样A为3%、试样B为4.9%和试样C为3%。
超出比例范围后,最大强度值下降趋势明显,分别为A试样7.4%、B试样12.2%和C试样13. 5%。
由上述分析可以认为:双组份结构胶浸水后最大强度值在推荐混合比例时最大强度值相对最优。
大于或小于推荐比例,最大强度均有下降,在允许比例范围内最大强度相对不明显;超出允许比例范围,最大强度下降较为明显。
2.4.2 浸水后拉伸粘接性的粘接破坏面积2.4.1 ,所测试的三种试样的浸水后拉伸粘接性的粘结破坏面积,见表3如表3所列,三种试样的浸水后拉伸粘结性破坏面积在推荐比例时均为0,粘接良好,;在允许比例范围内B试样和C试样出现小面积粘接破坏,其中B试样为3%和5%,C试样5%,但粘接破坏面积在国家标准要求范围内。
当混合比例超出允许比例范围时,粘接破坏面积显著增大,分别为A试样10%及15%,B试样30%及35%,C试样10%和20%。
由以上分析可以认为:双组分结构胶浸水后的粘接性受混合比例影响较为明显。
在允许比例范围内时,浸水后粘接性符合都能符合国家标准要求;但超出允许比例范围时,浸水后粘接性明显变差,不能符合国家标准要求。
2.5 双组份硅酮结构胶混合比例对性能影响机理浅析双组份硅酮结构胶通常由有机硅聚合物、交联剂、固化催化剂、填料和其他添加剂组成。
双组份硅酮结构胶的硫化反应是靠催化剂来引发的。
常用的催化剂有有机锡化合物、铂化合物及其配合物,交联剂正硅酸乙酯、甲基三乙氧基硅烷或他们的部分水解缩合物。
其硫化反应是α,ω—二羟基聚硅氧烷和交联剂在在催化剂的作用下,交联成三维结构的硅橡胶弹性体。
双组分硅酮结构胶A组分主要由有机硅聚合物和填料组成,B组分主要由交联剂和固化催化剂组成。
随着B组份用量的增加,交联剂的用量也相应增加,胶料的硫化速度加快,交联密度增加,使得胶片变得硬而脆,伸长率下降,强度相应降低。
不同的混合比例,主要是影响混合后胶体中的交联剂和固化催化剂及其他添加剂的量。
交联剂和固化催化剂量的差异就会导致胶体固化后的胶体的交联密度不一样,进而导致其三维立体交联网状结构也会有明显差异,所以其各项性能均会有相应的差异。
双组份结构密封胶生产厂家提供的混合比例和最佳混合比,均是严格按照双组份胶的固化机理和大量的实验数据及实践经验得出来的科学参考标准。
在最佳混合比例时,胶体的硫化速度适中,其交联密度去在最优性能范围,胶体的各项性能才能得到最可靠的保证。
交联密度过大,胶的适用期过短且胶体变脆,强度下降,伸长率变短。
交联密度过小,胶的适用期过长且胶体过软,强度偏低,伸长率偏长,固化不好,出现不粘带来安全隐患。
生产厂家开发双组分产品通常是在推荐混合比例基础上,确认产品的最佳性能数据,同时在允许混合比例内确认其相应性能数据以适应用户。
允许混合比例范围是基于用户在使用环境条件变化的情况下,有一定调整的范围以便环境条件一定变化范围内,双组分胶仍有较为理想的固化速度。
但偏离推荐混合比例范围,性能会有一定的变化,因此,双组分生产厂家给出的允许混合比例范围不宜过宽;同时,考虑到用户在使用过程中双组分混胶设备计量波动等因素,生产厂家给出的允许混合比例范围不能给到明显影响到产品使用性能的极端值。