FASTMELT流程-环境友好的煤基直接还原技术
第四章 直接还原流程(下)
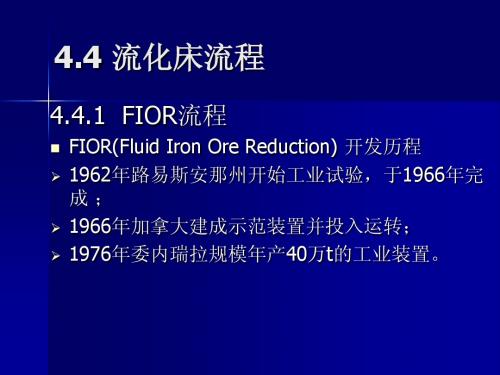
还原气为H2(约96%)。有利循环使用。氢 气用天然气或焦炉煤气为原料制取。制取过程: 原料气→加压至3.54MPa→不完全燃烧法→粗 还原气→饱和塔→水汽饱和,洗去炭黑→预热 →水煤气反应→([H]↑,CO→CO2)→ 脱CO2和水→纯度约96%的还原气 。 还原尾气中含有大量水蒸气和物理热。还原尾 气→换热器(回收余热,预热还原气)→洗涤 降温(脱除水蒸气和粉尘)→干燥脱水→加新鲜 氢气→还原气。还原气通过一个加热炉将温度 提高至590℃。
应用于工业生产时适当降低产品还原率在经济上 更为有利。产品被确定为f=75%左右的热压块, 并改名为HIB。 1968年,委内瑞拉开始建设该流程工业装置, 1979年完工投产,年产100万t海绵铁。
HIB还原气制备采用水蒸气催化裂化技术,还原气含 氢85%~97%。 矿石使用回转窑在300℃下烘干,燃料为天然气。然 后破碎至小于1.65mm。破碎后的矿粉送入两段流化 床,进行预热处理。 预热后的矿粉进入一个双层流化床反应器进行还原。 在上层流化床中,矿粉被还原至FeO;在下层流化 床中,矿粉被进一步还原至f=75%。产品排出流化 床后,送人一个中间料仓,并热压成团块。 HIB流程还原气一次利用率为32%~36%。尾气经 清洗脱尘后,作为燃料供还原气转化炉和加热炉使 用。 HIB流程压块金属化率偏低,不适合直接用于电炉炼 钢。一般可用于高炉或电炉炼铁。
SPM回转窑与其他还原窑结构基本相同,窑头设有 煤气烧嘴,窑身设有二次风机。此外,还设有专门 的清料镗杆,以清理粘附在窑壁上的炉料。 原料主要是高炉尘泥、转炉尘泥和轧钢铁鳞。混合 炉料品位约为57%。还原剂为无烟煤粉。燃料是焦 炉煤气,辅以炉气的一次燃烧。此外还需要少量烟 煤或脱水褐煤作为保护煤。 炉料在升温和还原的过程中产生部分液相,在滚动 中形成大小不一的团粒。 还原产物排出回转窑后进入冷却筒,进行直接水冷、 冷却后再对产物进行破碎和筛分。取7~50mm的部 分供高炉冶炼,小于7mm的部分送烧结厂或返回重 新处理。 粉尘原料中含锌较高。
转底炉直接还原-电炉炼铁流程与高炉炼铁流程的对比

转底炉直接还原-电炉炼铁流程与高炉炼铁流程的对比
秦廷许
【期刊名称】《现代冶金》
【年(卷),期】2004(032)002
【摘要】通过计算和对比,分析了转底炉(RHF)-电炉(EAF)炼铁流程与高炉传统炼铁流程的区别,表明两者在铁精矿消耗量,在还原剂和燃料的能源消耗量上相差不大.依中国的市场条件,RHF-EAF流程与高炉流程相比,吨铁成本低约10%;基建投资省20%左右;在环境污染和原燃料适应方面,RHF-EAF流程明显优于高炉流程.但是,采用电炉式的熔化炉炼制铁水,其业绩和经验远不如高炉,在规模大型化上也相差甚远.本技术适合无焦资源地区和第三世界中小国家推广.
【总页数】3页(P9-11)
【作者】秦廷许
【作者单位】马鞍山钢铁设计研究总院,马鞍山,243005
【正文语种】中文
【中图分类】TF111.13
【相关文献】
1.Fastmelt和ITmk3——转底炉RHF煤基直接还原新炼铁工艺 [J], 张化义
2.转底炉直接还原——电炉炼铁流程与高炉炼铁流程的技术经济对比 [J], 秦廷许
3.当今非高炉炼铁技术及发展趋势:谈直接还原和熔融还原 [J], 秦廷许
4.当今非高炉炼铁技术及发展趋势:谈直接还原和熔融还原 [J], 秦廷许
5.气基竖炉直接还原炼铁流程重构优化 [J], 于恒;周继程;郦秀萍;上官方钦
因版权原因,仅展示原文概要,查看原文内容请购买。
气基竖炉直接还原低碳炼铁方案(一)
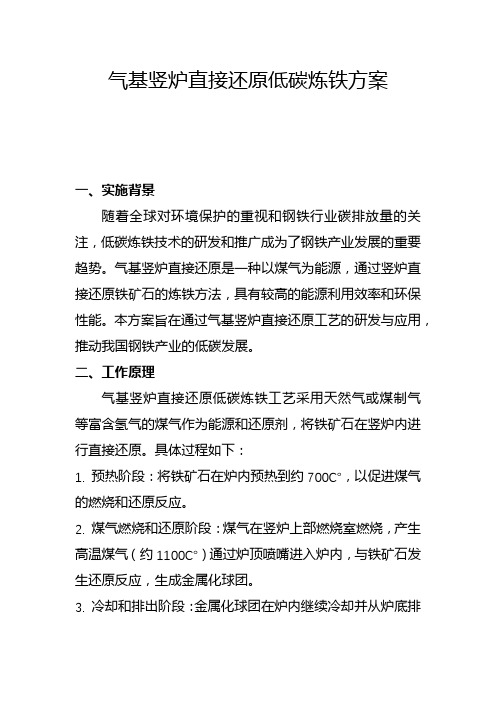
气基竖炉直接还原低碳炼铁方案一、实施背景随着全球对环境保护的重视和钢铁行业碳排放量的关注,低碳炼铁技术的研发和推广成为了钢铁产业发展的重要趋势。
气基竖炉直接还原是一种以煤气为能源,通过竖炉直接还原铁矿石的炼铁方法,具有较高的能源利用效率和环保性能。
本方案旨在通过气基竖炉直接还原工艺的研发与应用,推动我国钢铁产业的低碳发展。
二、工作原理气基竖炉直接还原低碳炼铁工艺采用天然气或煤制气等富含氢气的煤气作为能源和还原剂,将铁矿石在竖炉内进行直接还原。
具体过程如下:1. 预热阶段:将铁矿石在炉内预热到约700℃,以促进煤气的燃烧和还原反应。
2. 煤气燃烧和还原阶段:煤气在竖炉上部燃烧室燃烧,产生高温煤气(约1100℃)通过炉顶喷嘴进入炉内,与铁矿石发生还原反应,生成金属化球团。
3. 冷却和排出阶段:金属化球团在炉内继续冷却并从炉底排出。
4. 成品处理阶段:对金属化球团进行破碎、筛分、磁选等处理,得到最终产品。
三、实施计划步骤1. 研发与设计:开展气基竖炉直接还原工艺的基础研究和应用研究,设计适合我国钢铁产业的气基竖炉直接还原工艺流程和设备。
2. 设备制造与安装:根据设计要求,制造设备并在现场安装调试。
3. 工业试验:在制造和安装完成后,进行工业试验,验证工艺流程和设备的可行性和稳定性。
4. 生产调试:根据工业试验结果,对工艺流程和设备进行优化调整,逐步达到设计产能。
5. 技术服务与培训:提供相关技术服务和培训,确保企业能够自主运行和维护气基竖炉直接还原生产线。
四、适用范围本方案适用于大型钢铁企业和中小型民营钢铁企业。
特别是对于具有丰富铁矿资源和煤气资源的钢铁企业,气基竖炉直接还原低碳炼铁工艺具有较高的适用性和优势。
此外,对于地处环保要求较高地区或面临转型升级压力的钢铁企业,该工艺也具有较大的应用潜力。
五、创新要点1. 竖炉结构优化设计:通过对竖炉内部结构的优化设计,提高煤气与铁矿石的接触面积和热交换效率,降低能源消耗。
煤基直接还原炼铁技术分析

鞍 钢 技 术
ANGANG TECHNOLOGY 总 第 3 9期 6
一. 专 ~ 冢
~ 一 论 坛一
、 ~,
,
I●
,
煤 基直 接 还原 炼铁 技 术 分 析
庞 建 明 , 培 民 , 沛 郭 赵
( 国钢 研科 技 集 团有 限公 司低 温 冶金 及 资 源高效 利 用 中心 , 中 北京 1 0 8 ) 0 0 1
a to e e a u e nd a e u tma i g 1 t n o le r n r q r sa o t1 0 g C as r m c in t mp r t r .a s a r s l k n o fmo tn io e uie b u 0 k O l .F o 0
下 。可见 , 目前 的 煤 基 直 接 还 原 炼 铁 工 艺 , 离低 能 耗 、 污 染 的 炼 铁 目标 相 差 甚 远 , 大 的 问题 低 最
是 固态条件 下的还 原反应 效 率过低 , 高铁 矿 的低 温反 应性 能是 煤基 直接 还 原 炼铁 走 向成 功 、 提
高 效 、 保 的 关键 所 在 。 环
pr c s ,t e h a r nse r m he t n s c nti ng b e z s c n b a re u n y by me ns o o e s h e tta f r fo t a k o ani r e e a e c rid o to l a f
Ab ta t o l b s d d r c e u t n i n k n r c s e r n l z d h o a y k l s s r c :C a — a e i t d c i r ma i g p o e s s a e a ay e .T e r tr i i e r o o n o e ai g w t o r r a t n k n t s l n e ci n t n i h rl s f h a u o i o e p r t i p o e c i i e i , o g r a t i a d h g e o s o e td e t t l w r — n h o c o me s
转底炉
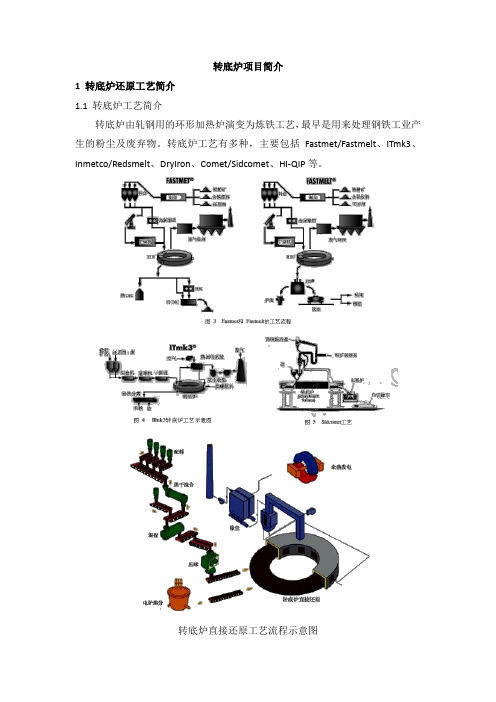
转底炉项目简介1 转底炉还原工艺简介1.1 转底炉工艺简介转底炉由轧钢用的环形加热炉演变为炼铁工艺,最早是用来处理钢铁工业产生的粉尘及废弃物。
转底炉工艺有多种,主要包括Fastmet/Fastmelt、ITmk3、Inmetco/Redsmelt、DryIron、Comet/Sidcomet、HI-QIP等。
转底炉直接还原工艺流程示意图1.2 转底炉工艺与其它相似工艺比较转底炉是煤基直接还原工艺中的核心设备之一,煤基直接还原工艺主要包括回转窑法(如SL-RN法)和转底炉法(如COMET法)。
而煤基直接还原工艺和气基直接还原工艺都是直接还原工艺,以铁产品为例直接还原工艺的产品为海绵铁(又称直接还原铁—DRI即Direct Reduced Iron)。
直接还原和熔融还原是两种主要的非高炉炼铁思路。
当转底炉的原料加入含碳球团时,其产品为金属化球团,可供电炉使用,也作为高炉的原料。
而链篦机—回转窑—环冷机(链回环)生产出来的产品是氧化球团,是为高炉炼铁提供的原料之一,称之为球团矿,而高炉炼铁的含铁原料还包括天然块矿、烧结矿。
转底炉直接还原技术采用含碳球团作原料,反应速度快,同时符合中国以煤为主要能源的特点。
以直接还原技术用于钒钛磁铁矿为例,转底炉技术相比隧道窑、回转窑工艺,以ITmk3为代表的转底炉工艺的优点主要是:○1还原原料在预热和还原过程中始终处于静止状态下随炉底一起进行,所以对生球强度要求不高;○2较高的还原温度(1350℃或更高)、反应快、效率高。
反应时间可在10-50min范围,可与矿热电炉熔炼容易实现同步热装;○3可调整喷入炉内燃料(可以是煤粉、煤气或油)和风量,能准确控制炉膛温度和炉内气氛;○4过程能耗低,回转窑法折算成每吨海绵铁的煤耗通常大于800kg,而转底炉法为600kg;○5从工艺角度来看,ITmk3技术流程简单,投资成本低,产品价格低,铁矿石原料及还原剂选择灵活。
另外,据马鞍山钢铁设计研究总院秦廷许的研究:转底炉-电炉炼铁流程与高炉传统炼铁流程比较,虽在铁精矿消耗量、还原剂和燃料的能源消耗量上相差不大,但吨铁成本低约10%;基建投资省22%左右;全流程电耗低48.6%。
直接还原技术

预还原器:(炉身):要求较高的 还原效率,允许使用低质量的还原 剂 终还原反应器(炉缸):顺利完成 终还原、渣铁熔化分离,在终还原 器中 完成造气
连接注意事项
满足合理的还原度分配 终还原器为预还原器提供合适的还 原剂 工艺合理,结构简单,可靠热损失 小
4 各主要熔融还原工艺比较
第八章 非高炉炼铁
一 非高炉炼铁简介
1 非高炉炼铁概念
非高炉炼铁法 除高炉炼铁以外的其它还原铁矿石的方法
直接还原定义 Direct Reduction 指铁矿石在低于熔化温度之下还原成海绵铁的生 产过程 熔融还原 Smelting Reduction 指非高炉炼铁方法中那些冶炼液态生铁的工艺过 程
Corex主要生产技术指标
生产能力 熔炼系数 作业率 煤耗量 输出煤气 煤气热值 球团矿 熔剂 氧 氮气 工业用水 电
单位 t/h t/m3· d kg/t Nm3/t kJ/Nm3 t/t t/t Nm3/t Nm3/t t/t kwh/t
指标 4.5 3.0 92% 1020 1650 7000 1.5 0.2 500~550 70~100 1.5~2.0 60
2 气基直接还原法分类
气基直接还原
移动床 Midrex HYLIII
固定床 HYL法
流化床
目前世界海绵铁产量达2300万吨, 大部分用M氏法(Midrex)生产 主要问题 这种工艺必须用天然煤气制备还 原剂,在天然气缺乏的地方无法 采用;此外此种工艺设备复杂,投 资巨大。
3 煤基直接还原法
7 非高炉炼铁法使用的原料及能源
含铁原料 1.1要求较高的含铁品位。 原因:(并非工艺本事),电炉炼钢要求,(电耗增 加,生产率降低及炉衬寿命缩短)。要求铁矿石 脉石含量<3%,最高不超过5% CaO:希望的成分 MgO:有利于提高矿石软化温度,改善还原性,提 高强度 Cu:有害元素,污染电炉钢质量,Cu全部进入进 入海绵铁 Zn:碱金属:对竖炉有害 矿石中水分和烧损:越少越好,耗热
熔融还原炼铁技术综述

目录1.概述 (1)2.国际熔融还原技术发展 (3)2.1.工业化的COREX工艺 (5)2.2.进入示范性工厂试验的Hismelt技术 (7)2.3.FINEX技术 (8)2.4.第三代炼铁法--ITmk3 (9)3.国内熔融还原(非高炉炼铁)技术发展现状 (11)3.1.概述 (11)3.2.2T/h的半工业联动热态试验装置-COSRI (11)3.3.宝钢Corex 3000 (14)3.4.20万吨纯氧非高炉炼铁工业试验装置 (14)3.5.8m3一步法熔融还原试验装置 (18)3.6.基于氢冶金的熔融还原炼铁新工艺 (20)3.6.1.万吨级两级循环流化床示范装置-营口中板厂 (21)3.6.2.宝钢万吨级两级冷态循环流化床装置建设 (24)3.7.直接还原在国内的发展 (24)3.8.几种非高炉炼铁的综合分析 (26)4.炼铁技术的发展方向 (28)4.1.欧盟——ULCOS超低CO2排放钢铁技术研究 (28)4.2.日本——COURSE50技术研究 (30)4.3.中国——新一代可循环钢铁流程工艺技术技 (30)5.具有自主知识产权的熔融还原炼铁技术发展建议 (31)5.1.建立长期开发组织机构与募集资金 (31)5.2.加强合作、充分利用现有成果深入研究 (31)5.3.新一代具有自主知识产权的熔融还原流程建议 (32)熔融还原炼铁技术综述全强1.概述改革开放30年来,中国钢铁冶炼技术取得了巨大的进步。
在炼铁领域,技术进步的主要表现是装备的大型化、操作的自动化信息化、生产的高效与清洁化,高风温技术、富氧技术、喷煤技术、煤气干式除尘技术、煤气余压发电、煤气燃气技术、高炉长寿技术、与高炉废弃物的综合利用等方面的应用取得明显的进步。
据2010年的统计,国内炼铁产量已超过5.9亿吨,约占世界产量的40%。
其中大于1000m3以上高炉的产量约为60%,也就是说,按照国家产业政策的要求,有40%的产能需要进行技术改造。
FASTMET

F a s t m e t 工艺是由美国Mid r e x 直接还 原公司于60 年代开发的 近年来, 世界上直接还原铁(D R I) 的生产呈 现持续大幅度增长的势头, 1 9 9 4 年产量达 27· M t,比1 9 9 3 年增15.8 % 38 2005年, M id re x 公司正同日本神户制钢合 作, 在神户制钢的加古川钢铁厂进行Fas t m et 示范装置的工业性试验, 以期进一步验证 该工艺并使其尽快实现工业化。
裂解产物H2 和C 还原
煤
C+ 挥发分 低分子碳氢化
高分子碳氢化合物 合物+ C + H2 Fex Oy + CO /H2 /H2O
FexOy- 1 + CO2
FexOy + C
FexOyOy- 1 + CO
F a s t m et 工艺使用与轧钢环形加热炉类似 的转底炉作为工艺主体设备。这种装置与竖 炉和回转窑相比具有以下特点: 1. 料层薄, 易于加热和还原; 2. 炉料相对不运动, 适合于使用低强度的冷 固 结含碳球团; 3. 炉料与拱顶及周边炉衬无接触, 避免了炉 衬 的机械磨损和粘接; 4. 系统基本处于常压状态, 易于密封控制; 5. 装置高度低、体积小, 便于操作和维护;
铁精粉或钢厂废料 粘结剂 粉状还原剂(煤) 气体燃料:天然气、油
冷固结含碳球团是实现Fas t m e t 工艺的关 键因素。 1.冷固结含碳球团具有与一般氧化球团和块矿 不同的还原方式: 是靠内部碳进行自身直接 还原, 无需外部提供还原剂。 2.在还原过程中, 气相产物C O 将不断排出, 形 成一个气圈环绕球团, 因而使球团可在氧化 性气氛下进行还原反应。此外, 含碳球团允 许大大提高反应温度, 而不致于软化和熔化。 3.采用冷固结含碳球团实现了人们使用粉矿直 接还原一步法工艺的追求。
煤基直接还原铁生产技术的发展

一、工艺流程
Fastmelt 工艺是 Fastmet 工艺和炼铁电炉的综合。来自回 转窑的直接还原铁在炼铁电炉中熔化生产铁水。
ITmk3 工艺是在回转窑中生产粒状铁。团块在回转炉中 加热到 1450℃, 在还原和熔化之后, 炉渣在回转窑中分离。铁 水和炉渣被冷却并从回转窑中排出。
0.00 GJ
2.47 GJ
4.10 GJ
燃气
( 0 kg- CO2 ) ( 141 kg- CO2 ) ( 234 kg- CO2 )
1.54 GJ
2.95 GJ
0.00 GJ
电能
( 103 kg- CO2 ) ( 198 kg- CO2 ) ( 0 kg- CO2 )
0.00 GJ
0.07 GJ
表 8 研究 A 研究结果概括
高炉( 50 万吨 / Fastmelt 工艺( 50 ITmk3 工艺( 50
年铁水) 万吨 / 年铁水) 万吨 / 年粒状铁)
消耗
31.47GJ
14.26 GJ
14.09 GJ
煤
( 2936kg- CO2 ) ( 1330kg- CO2) ( 1314kg- CO2)
技术与装备纵横
煤基直接还原铁生产
技术的发展
□袁 文
目前, 世界炼铁生产的主流是高炉工艺, 但该工艺需要 一些原料准备设备, 如焦炉、烧结设备等, 而其会给环境带来 很大影响。气基直接还原铁如 MIDREX 工艺是高炉炼铁工艺 的替代方法之一, 然而, 该工艺受到以经济方式获得天然气 的限制。在这一背景下, 对可以使用更广泛的原料和燃料, 且 对环境更加友好的新炼铁工艺的需求日益增加。为了满足这 种 需 求 , 人 们 开 发 出 3 种 煤 基 直 接 还 原 铁 生 产 工 艺— —— Fastmet 工艺、Fastmelt 工艺和 ITmk3 工艺。采用这些工艺可以 通过粉矿和煤生产出高质量的铁, 如直接还 原 铁 、铁 水 和 粒 状铁。而且, 这 3 种工艺在能耗和环保方面可以与高炉竞争。
我国煤基直接还原炼铁工艺发展
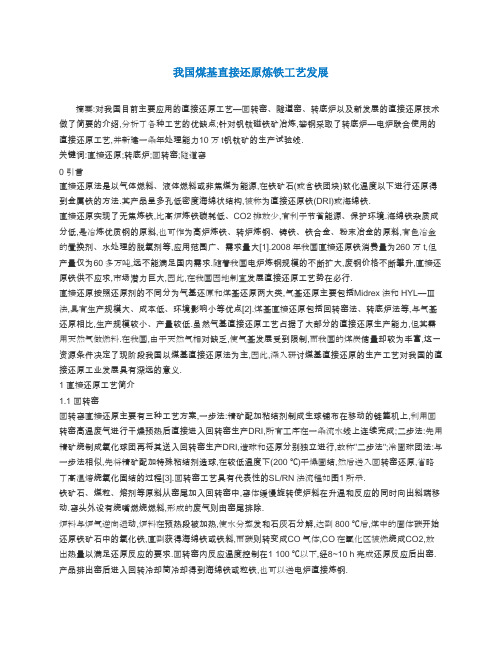
我国煤基直接还原炼铁工艺发展摘要:对我国目前主要应用的直接还原工艺—回转窑、隧道窑、转底炉以及新发展的直接还原技术做了简要的介绍,分析了各种工艺的优缺点;针对钒钛磁铁矿冶炼,攀钢采取了转底炉—电炉联合使用的直接还原工艺,并新建一条年处理能力10万t钒钛矿的生产试验线.关键词:直接还原;转底炉;回转窑;隧道窑0 引言直接还原法是以气体燃料、液体燃料或非焦煤为能源,在铁矿石(或含铁团块)软化温度以下进行还原得到金属铁的方法.其产品呈多孔低密度海绵状结构,被称为直接还原铁(DRI)或海绵铁.直接还原实现了无焦炼铁,比高炉炼铁碳耗低、CO2排放少,有利于节省能源、保护环境.海绵铁杂质成分低,是冶炼优质钢的原料,也可作为高炉炼铁、转炉炼钢、铸铁、铁合金、粉末冶金的原料,有色冶金的置换剂、水处理的脱氧剂等,应用范围广、需求量大[1].2008年我国直接还原铁消费量为260 万t,但产量仅为60多万吨,远不能满足国内需求.随着我国电炉炼钢规模的不断扩大,废钢价格不断攀升,直接还原铁供不应求,市场潜力巨大,因此,在我国因地制宜发展直接还原工艺势在必行.直接还原按照还原剂的不同分为气基还原和煤基还原两大类,气基还原主要包括Midrex法和HYL—Ⅲ法,具有生产规模大、成本低、环境影响小等优点[2].煤基直接还原包括回转窑法、转底炉法等,与气基还原相比,生产规模较小、产量较低.虽然气基直接还原工艺占据了大部分的直接还原生产能力,但其需用天然气做燃料.在我国,由于天然气相对缺乏,使气基发展受到限制,而我国的煤炭储量却较为丰富,这一资源条件决定了现阶段我国以煤基直接还原法为主,因此,深入研讨煤基直接还原的生产工艺对我国的直接还原工业发展具有深远的意义.1 直接还原工艺简介1.1 回转窑回转窑直接还原主要有三种工艺方案,一步法:精矿配加粘结剂制成生球铺布在移动的链篦机上,利用回转窑高温废气进行干燥预热后直接进入回转窑生产DRI,所有工序在一条流水线上连续完成;二步法:先用精矿烧制成氧化球团再将其送入回转窑生产DRI,造球和还原分别独立进行,故称"二步法";冷固球团法:与一步法相似,先将精矿配加特殊粘结剂造球,在较低温度下(200 ℃)干燥固结,然后送入回转窑还原,省略了高温焙烧氧化固结的过程[3].回转窑工艺具有代表性的SL/RN法流程如图1所示.铁矿石、煤粒、熔剂等原料从窑尾加入回转窑中,窑体缓慢旋转使炉料在升温和反应的同时向出料端移动.窑头外设有烧嘴燃烧燃料,形成的废气则由窑尾排除.炉料与炉气逆向运动,炉料在预热段被加热,使水分蒸发和石灰石分解,达到800 ℃后,煤中的固体碳开始还原铁矿石中的氧化铁,直到获得海绵铁或铁料,而碳则转变成CO气体,CO在氧化区被燃烧成CO2,放出热量以满足还原反应的要求.回转窑内反应温度控制在1 100 ℃以下,经8~10 h完成还原反应后出窑.产品排出窑后进入回转冷却筒冷却得到海绵铁或粒铁,也可以送电炉直接炼钢.与高炉工艺相比较,回转窑工艺设备简单,投资少,适用于地方钢铁工业,弥补了高炉—转炉工艺的不足,此外,回转窑还适用于复合矿冶炼,冶金灰尘及各种工业废渣的回收利用,减少环境污染,降低了钢铁生产能耗.同时,回转窑工艺也存在一些缺点,包括窑内结圈、还原温度低(1 100 ℃以下)、流程长、对块矿或球团矿冷强度要求高、要求使用低硫煤等[4].我国山东鲁中矿山公司通过采取提高冷固烧结球团的冷热态强度、加强还原煤的选择和管理、优化回转窑的送风、抛煤、控温温度等措施,预防并降低回转窑结圈,取得了较好的收效.图1 SL/RN法工艺流程1.2 隧道窑隧道窑工艺即将精矿粉、煤粉、石灰石粉,按照一定的比例和装料方法,分别装入还原罐中,然后把罐放在罐车上,推入条形隧道窑中或把罐直接放到环形轮窑中,料罐经预热到1 150 ℃加热焙烧和冷却之后,得到直接还原铁.目前江苏永钢集团拥有两条260 m长煤气隧道窑,为亚洲最长隧道窑.隧道窑生产海绵铁工艺流程如图2所示.图2 隧道窑生产海绵铁工艺流程煤基隧道窑直接还原工艺具有技术成熟、作简单的特点,可因地制宜采用此工艺,利用当地小型分散的铁矿及煤矿资源优势,发展直接还原铁生产,为电炉提供优质原料.但是,总体上讲,我国隧道窑直接还原中存在生产规模较小、能耗高、污染严重、缺乏稳定的原料供应渠道等问题[5],所以,提高机械化程度、改变原料入炉方式、改进燃料及其燃烧、增设余热回收等成为各厂家不断努力改进工艺的方向.我国已建成或正在建设的隧道窑有100多座,约70多个单位规划建设产能5~30 万t/a的隧道窑直接还原铁厂,在不断总结实践经验的基础上,改进现行工艺,开发出诸如大型隧道窑直接还原、AMR—CBI隧道窑直接还原工艺、宽体球状海绵铁隧道窑、L-S快速还原工艺等多种新技术,掀开了隧道窑工艺规模扩大、产能提高、机械及自动化提升的序幕.1.3 转底炉转底炉煤基直接还原是最近几十年间发展起来的炼铁新技术,代表工艺为Fastmet,它由美国Midrex公司与日本神户制钢于20世纪60年发,是采用环形转底炉生产直接还原铁的一种方法.经过多年的半工业性试验和深入的可行性研究,现已完成工艺作参数和装置设计的优化.Fastmelt和ITmk3工艺是在此基础上增加对直接还原铁的处理.图3显示了这三种以转底炉为主体的直接还原工艺流程.图3 转底炉直接还原工艺流程煤粉与铁精粉按比例混匀制成球团,干燥后以1~3层球铺放在转底炉床面,随着炉底的旋转,炉料依次经过预热区、还原区和冷却区.还原区内球团被加热到1 250~1 350 ℃,由于煤粉与铁氧化物紧密接触,铁氧化铁被碳迅速还原成DRI,成品在800~1 000 ℃左右连续从转底炉卸出.球团矿在炉底停留8~30 min,这取决于原料特性、料层厚度及其他因素,成品可作电炉热装炉料或者转炉炉料,也可冷却或生产热压块(HBI).Fastmet工艺技术特点:①在高温敞焰下加热实现快速还原,反应时间只需10~20 min,生产效率高;②原料来源广泛,铁原料方面,除使用高品位粉矿、精矿外,还可用氧化铁皮、代油铁泥、炼钢粉尘、含En、Pb、As等有害杂质的铁矿等;还原剂方面,除煤以外焦末、沥青均可利用,不必担心出现结圈问题;③炉料相对炉底静止,对炉料强度要求不高;④废气中含有大量显热,可用作预热空气、干燥原料等[6]. Fastmelt工艺流程基本与Fastmet一致,只是在后续添加一个熔炉来生产高质量的液态铁水.Itmk3工艺是使金属化球团在转底炉中还原时熔化,生成铁块(Nuggets),同时脉石也熔化,形成渣铁分离.当然转底炉也存在着设备复杂、炉内气氛难控制、传热效率低以及对还原剂硫含量要求严格的缺点.就目前转底炉工艺开发的水平和规模而论,与高炉还有较大差距,但仍存在发展的广阔空间,天津荣程联合钢铁集团已兴建一条100万t级Fastmet生产线,建成目前世界最大的转底炉.另外,用转底炉可处理一些特殊铁矿,如含锌、铅、砷等有害杂质,或含镍、钒、钛等有用元素,均可利用转底炉的工艺优势,或高温挥发,或选择性还原,配合后续工艺,实现资源综合利用.马钢尘泥脱锌转底炉工程项目于2008年5月开工建设,2009年7月6日正式竣工投产,建成了整套转底炉(RHF)脱锌工艺技术装置,不仅解决了含锌尘泥循环利用的后顾之忧,而且将综合利用技术上升到高品质资源化水平.1.4 其他新工艺1.4.1 PF法煤基竖炉直接还原工艺中冶集团北京冶金设备研究设计总院,结合国内情况创新发明了PF法竖炉直接还原工艺.PF法是在吸收K-M法外热式竖炉煤基直接还原工艺的经验基础上,设计的以一种中国特色的罐式还原炉为主反应器的直接还原法.这种工艺技术可靠,技术经济指标在各种煤基直接还原工艺中属先进水平.PF法直接还原工艺流程如图4所示.图4 PF法直接还原工艺流程PF法直接还原工艺主要特点[1]:1)主体设备选用外热式竖炉,预热、还原、冷却三段根据不同的作用和温度选用不同材质和结构,便于传热和化学反应进行,提高热效率和设备寿命.2)原燃料适用性强,对精矿、还原剂和燃料没有特殊要求.3)采用外配碳工艺,还原剂适当过量,扩大了煤的选用范围,造球工艺也因不定量配入煤粉而简化,球团强度较高,DRI质量较好.4)多个反应罐可并列组成任意规模的还原设备,设计和组织生产灵活.1.4.2 低温快速还原新工艺2004年钢铁研究总院提出了低温快速冶金新工艺.新工艺利用纳米晶冶金技术的特点将铁矿的还原温度降低到700 ℃以下.新流程分为气基和煤基两种方法,工艺流程如图5、图6所示.图5 煤基低温快速还原新工艺图6 气基低温快速还原新工艺煤基法使用煤粉为还原剂,在700℃左右快速还原铁精矿粉;气基法使用还原性气体还原铁精矿粉,还原温度可低于600℃.新工艺具有能耗低、环境友好等特点,省去了烧结或造球工艺,缓解了钢铁行业对焦煤的依赖,符合我国国情[7].2 攀钢现状钒钛磁铁矿是攀西地区的特色资源,与普通矿相比,钒钛矿直接还原温度较高、还原时间较长,还原过程产生特有的膨胀粉化现象,因此,存在竖炉结瘤、流化床失流和黏结、回转窑结圈等技术难题.高炉流程冶炼钒钛矿,只回收了铁和钒,钛进入高炉渣没有回收,造成钛资源的大量流失.2005年以来,攀钢科研人员在充分吸收、借鉴新流程及相关研究成果的基础上,通过大量的试验研究,针对钒钛磁铁矿特点,提出并验证了钒钛磁铁矿"转底炉直接还原—电炉深还原—含钒铁水提钒—含钛炉渣提钛"工艺路线,彻底打通了钒钛矿资源综合利用新工艺流程,稳定获得了质量满足要求的低碳生铁、达到GB3283-87要求的片状V2O5和PTA121质量要求的钛白产品.依托该研究成果,攀钢集团攀枝花钢铁研究院于2008年5月4日正式启动了攀钢10 万t/a钒钛矿资源综合利用新工艺中试线工程项目,新建一条转底炉—熔分电炉联合使用,年处理能力10万t钒钛矿的试验生产线,为更深入地研究实践,实现转底炉处理钒钛矿的规模化生产提供了广阔的平台.中试线工艺流程如图7所示.本流程采用硫含量较低的白马铁精矿,还原剂采用无烟煤煤粉,粘结剂为有机粘结剂,原料混合后经高压压球机压球,生球烘干后进入转底炉系统.球团在转底炉内停留10~30 min后出料,金属化球团直接热装进入熔分电炉,在一定温度下还原后,产出含钒铁水及含钛炉渣.继续对铁水进行脱硫、提钒后,得到半钢、脱硫渣及钒渣,半钢进入铸铁机铸铁,生产出铸铁块.钛渣制取钛白,实验室条件下钛回收率达到80%以上;钒渣制取钒氧化物(V2O5),实验室条件下,钒回收率达到65%以上.与高炉流程相比,转底炉流程采用100%钒钛矿冶炼,克服了高炉流程必须配加普通矿的不足,在当前铁资源紧张的形势下,有助于充分发挥攀西地区资源优势,拉动区域经济发展.此外,转底炉流程的铁精矿不需烧结处理,不使用焦炭,从根本上避免了烧结烟气脱硫、焦煤资源采购困难以及环保压力大等问题.3 结语图7 资源综合利用中试线工艺流程煤炭资源总量丰富、焦煤短缺,铁矿资源储量大、富矿少、贫矿和共生矿多是中国钢铁工业面临的现实状况.这种能源、资源结构给煤基直接还原法生产海绵铁的发展提供了机遇.转底炉直接还原技术由于在生产率、规模化、投资费用、单位成本等方面都占有明显的优势,可作为发展直接还原技术的首选工艺.鉴于转底炉处理钒钛磁铁矿技术尚属世界首创,并无较多的经验借鉴,因此要大力开展针对钒钛磁铁矿直接还原的基础研究工作,在实践中借鉴各种直接还原方法已取得的成果,开拓创新,开创钒钛矿直接还原新纪元.参考文献[1] 陈守明,黄超,张金良.煤基竖炉直接还原工艺//2008年非高炉炼铁年会文集.中国金属学会,2008:132-135.[2] 杨婷,孙继青.世界直接还原铁发展现状及分析.世界金属导报,2006.[3] 刘国根,邱冠周,王淀佐.直接还原炼铁中的粘结剂.矿产综合利用,2001(4):27-30.[4] 韩跃新,高鹏,李艳军.白云鄂博氧化矿直接还原综合利用前景.金属矿山,2009 (5):1-6.[5] 魏国,赵庆杰,沈峰满,等.非高炉生产技术进步//2004年全国炼铁生产技术暨炼铁年会文集.2004:878-882.[6] 陶晋. 环形转底炉直接还原工艺现状及发展趋势. 冶金信息工作, 1997.6.[7] 郭培民,赵沛,张殿伟.低温快速还原炼铁新技术特点及理论研究.炼铁,2007,26(1): 57-60.来源:攀枝花钢铁研究院网站。
一种外热式煤基直接还原铁竖炉排料工艺及系统的制作方法
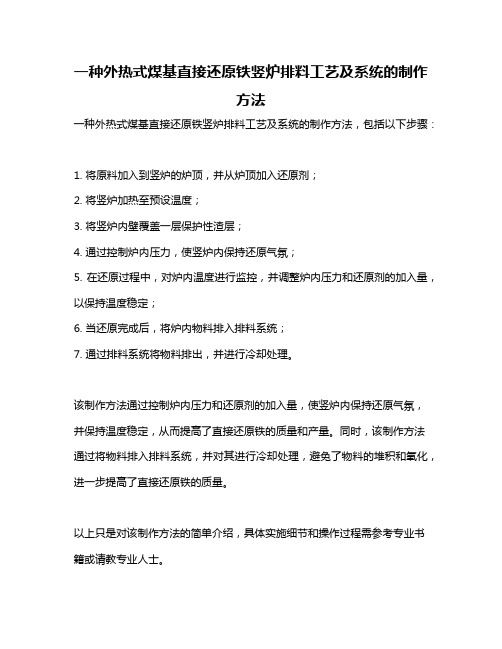
一种外热式煤基直接还原铁竖炉排料工艺及系统的制作
方法
一种外热式煤基直接还原铁竖炉排料工艺及系统的制作方法,包括以下步骤:
1. 将原料加入到竖炉的炉顶,并从炉顶加入还原剂;
2. 将竖炉加热至预设温度;
3. 将竖炉内壁覆盖一层保护性渣层;
4. 通过控制炉内压力,使竖炉内保持还原气氛;
5. 在还原过程中,对炉内温度进行监控,并调整炉内压力和还原剂的加入量,以保持温度稳定;
6. 当还原完成后,将炉内物料排入排料系统;
7. 通过排料系统将物料排出,并进行冷却处理。
该制作方法通过控制炉内压力和还原剂的加入量,使竖炉内保持还原气氛,并保持温度稳定,从而提高了直接还原铁的质量和产量。
同时,该制作方法通过将物料排入排料系统,并对其进行冷却处理,避免了物料的堆积和氧化,进一步提高了直接还原铁的质量。
以上只是对该制作方法的简单介绍,具体实施细节和操作过程需参考专业书籍或请教专业人士。
国内外转底炉的发展趋势及我国发展转底炉技术的建议

• 含碳球团内,矿粉与还原剂具有良好的接触条件。在高温下 ,还原反应以高速进行。经过15~20min的还原,球团矿金 属化率即可达到88%~92%。还原好的球团经一个螺旋排料 机卸出转底炉,供电炉作炼钢原料。
属化球团经过冷却区后被排出炉外冷却,部分再氧化金属化率降低一些。煤气燃烧
及反应生成的烟气沿着与炉料转动相反的方向流动,最后流入废气净化处理及余热 回收系统。
装料 区
900~1100 ℃
预热区
烟气流动方向 1200~1400℃
还原区
1100~900℃
烧嘴
冷却区
排料区
转底炉炉底转动方向
一、国内外转底炉技术的发展过程简介
一、国内外转底炉技术的发展过程简介
DRYIRON工艺流程图
料仓
空气
换热器
烟气
混 压球机
布料器
螺旋排料
DRI料罐
布袋除尘器
一、国内外转底炉技术的发展过程简介
⑵. 干铁法
GLOBA公司(原MR&E公司)在1960年是米德兰-罗斯的快速加热工艺的技 术开发部门,1985年成为独立公司。曾经为美国Ameristeel公司的电炉粉 尘处理系统以及美国Rouge Steel公司综合钢铁厂的粉尘和污泥处理系统提 供DRYIRON法的相关设备,具备丰富的应用实绩。GLOBA公司开发的干铁法 有两项专利技术:用废糖浆作为粘结剂,利用氧化铁粉与碳粉混合物成型 的干压块方式对辊压球机压成球团后直接装入转底炉,取消了球团的烘干 程序;采用特殊的震动传送装置的炉料装入方法。可以得到金属化率大于 90%的DRI。 是一种较理想的煤基直接还原工艺。 该工艺过程中在转底炉 内的高温作用与短暂的停留时间(约10min),其操作具有巨大的灵活性, 而且设备的操作控制非常容易。考虑到上述炼铁厂粉尘和污泥处理以及还 原铁生产的需要,新日铁钢铁事业部于1999年从美国MR&E公司引进转底炉 DRYIRON法,并且争取到代理推销资格。 这是日本FASTMET法发展的基础。
神户制钢煤基直接还原铁生产工艺(下)
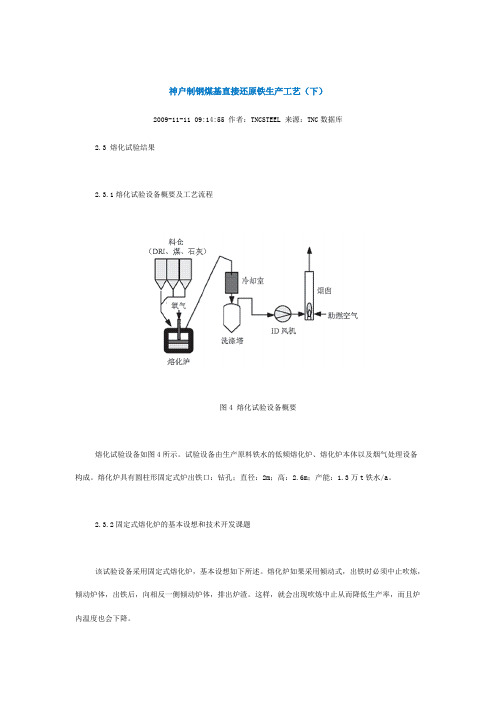
神户制钢煤基直接还原铁生产工艺(下)2009-11-11 09:14:55 作者:TNCSTEEL 来源:TNC数据库2.3 熔化试验结果2.3.1熔化试验设备概要及工艺流程图4 熔化试验设备概要熔化试验设备如图4所示。
试验设备由生产原料铁水的低频熔化炉、熔化炉本体以及烟气处理设备构成。
熔化炉具有圆柱形固定式炉出铁口:钻孔;直径:2m;高:2.6m;产能:1.3万t铁水/a。
2.3.2固定式熔化炉的基本设想和技术开发课题该试验设备采用固定式熔化炉,基本设想如下所述。
熔化炉如果采用倾动式,出铁时必须中止吹炼,倾动炉体,出铁后,向相反一侧倾动炉体,排出炉渣。
这样,就会出现吹炼中止从而降低生产率,而且炉内温度也会下降。
而采用固定式炉,出铁时不需倾动炉体,继续吹氧和熔化直接还原铁,可定时排出铁水和熔渣,出铁渣时只是带出铁渣显热,炉内温度没有下降,而且生产率也基本没有降低,可以连续作业。
如将RHF生产的还原铁高温状态装入炉内,则可进一步提高生产率。
2.3.3熔化试验条件及操作参数熔化试验为一周几次的间歇运转,将低频炉约1450℃的原料铁水(6t)装入熔化炉后,开始第一次吹炼。
吹氧使铁水中碳燃烧,充分运用炉内二次燃烧升温,铁水温度达到规定值后,从中间出铁口排出约2t 的铁水和熔渣。
然后,在残留铁水(约4t)和少量渣的状态,反复多次进行还原铁(DRI)熔化和出铁渣操作,试验结束时从残铁排出口排出铁渣。
本试验所用的原料铁水成分和DRI成分分别示于表4和表5。
装入熔化炉的碳材使用钢铁厂产生的小粒焦粉(固定[C]=85%)。
表4 原料铁水主要成分 %表5 直接还原铁(DRI)主要化学成分 %2.3.4熔化试验结果(1)吹炼中铁水温度、[C]的变化将原料铁水装入炉内时,铁水温度大约降到1350℃,但第一次吹炼升温到1500℃左右出铁。
第二次吹炼后,铁水温度基本保持不变,反复进行直接还原铁的熔化和出铁渣作业。
吹炼中控制炉渣的形成,[C]含量基本保持在饱和状态。
煤基直接还原炼铁法的能耗与环境负荷

煤基直接还原炼铁法的能耗与环境负荷(表)据中国钢铁新闻网2007年2月13日报道:近年,世界粗钢产量随着亚洲的经济成长而持续增加。
现代炼铁法的主流是高炉法,但高炉法为了提高其效率而必须大型化,并且需要环境负荷大的烧结设备和炼焦炉。
作为替代高炉法的炼铁法,有MIDREX法所代表的气基还原铁冶炼法,但气基还原铁冶炼法需要大量的天然气,所以地区选定受到限制。
在上述背景下,对于今后的炼铁法而言,如下的期待正在日益高涨:1)降低能耗与环境负荷;2)减少投资费用与运行成本;3)适应宽泛的原料与能源。
为了回应这样的期待,神户制钢与Midrex技术公司共同开发了3种煤基直接还原炼铁法——FASTMET、FASTMELT和ITmk3。
这些方法可以用世界各地富存的铁矿粉和煤炭生产高质量的铁源,例如DRI(直接还原铁)、铁水和粒铁。
它们的能耗与环境负荷与当今普遍使用的大容量高炉法不相上下。
煤基还原冶炼法1 煤基还原铁冶炼法的定位作为煤基还原铁冶炼法的FASTMET、FASTMELT、ITmk3是使用世界上较为大量存在的粉矿石和煤炭的方法。
2 工艺流程铁矿石和作为还原剂的煤炭预先混合,并被成型为球团或压块状的团块化混合物。
这种团块化混合物供给RHF(转底炉),在RHF内被还原。
团块化混合物在RHF的炉床上铺一层或两层予以加热。
在FASTMET、FASTMELT法中,炉内加热到1250~1350℃,以直接还原铁的形式排至炉外,而在ITmk3法中则加热到1450℃,在炉内还原、熔融而以粒珠的形式排至炉外。
对FASTMET法来讲,可以做成高温还原铁和经冷却做成低温还原铁,或者以HBI(热压团块铁)的形式来利用制品还原铁。
FASTMELT法是将还原铁熔炼炉组合到FASTMET法中的方法,把RHF排出的高温的铁装入还原铁熔炼炉,边利用其显热边冶炼生产生铁。
ITmk3法则在RHF内生产与炉渣分离的粒铁,与炉渣一起排出的粒铁,用磁选机等分选机选出粒铁。
fastmet工艺的进展

FASTMET工艺的进展1 前言日本神户制钢在美国的子公司MIDREX的前身MIDLAND ROSS公司采取将掺入炭材的球团预热后加入转底炉(RHF)加热还原为直接还原铁的FASTMET工艺试验,并于196 5年建成中试装置,开展了一年试验。
但是该公司同时开发的用天然气做还原剂生产直接还原铁的MIDREX工艺,因天然气价格便宜而率先实现商业化生产,致使FASTMET工艺未能早日实现商业化。
2 FASTMET工艺及特点FASTMET工艺是将粉矿和含铁粉尘掺入一定的炭材制成球团,经干燥后加入RHF内处理。
但在加入时应保持炉内和外气隔断,且需精确控制加入量,FASTMET工艺按炉容的大小采取可调节送料管实现加入量的精确控制。
在1~2层炉的顶装时,采取螺旋式水平布料方式。
采取神户制钢快速加热法以1350℃高温对炉床上球团快速加热。
这时球团内煤炭引起还原反应,滞留8min~16min即可生成还原铁(DRI),并在1200℃~1000℃排出炉外。
高温DRI向炉外排出采用移动床型还原炉的操作方法,以实现稳定的连续作业。
FASTMET和高炉法不同,在产量调整以及作业启动、停止方面具有较大的灵活性,可及时适应需求变化而调整。
对排出炉外的DRI,可采取热运输容器送往电炉和转炉以利用余热实现节能,也可在冷却后供高炉代烧结矿,由于简化了烧结工艺又可节焦,具有节能作用。
通常被还原的DRI具有由还原反应生成的气孔,若长期在大气中暴露,将因被氧化而降低质量,故在不能及时利用时,应通过压块以形成无孔的热压块铁(HBI),防止再氧化,除有利于长期保存外,还可供出口和外运。
各厂可根据实际情况选定DRI或HBI。
FASTMET工艺的主要特点:① FASTMET工艺是将块矿、球团等在炉床上填装1~2层,利用辐射热加热时,即使在燃烧炉内仍可防止燃烧气对被加热物的氧化。
②作为转底炉可实现在完全空气比下的燃烧,并对被加热物实现了高效的加热、高效的还原反应。
煤基竖炉直接还原技术

武汉科思瑞迪科技有限公司(以下简称“科思瑞迪”)坐落于武汉市东湖新技术开发区,是以武汉桂坤科技有限公司为主体,整合相关社会资源,汇集了冶金、工业炉、机电技术等各专业技术人才,集数十年研发、工程及生产经验,组建的一家专业从事煤基竖炉直接还原技术的开发、推广及应用的科技公司。
该公司的技术及成套核心设施已经在中国、越南、缅甸等国的工程项目中得到了应用,取得了良好的社会及经济效益。
煤基竖炉直接还原技术李森蓉李建涛(武汉科思瑞迪科技有限公司)摘要:本文对煤基竖炉直接还原技术从工艺流程、技术指标、技术特点等方面进行了较为详实的介绍和分析;该技术生产海绵铁的质量有保证,市场发展前景可期,市场竞争力强。
关键词:煤基竖炉直接还原铁技术特点产品质量直接还原是指铁矿石或含铁氧化物在低于熔化温度下还原成金属产品的炼铁过程;其所得的产品称为直接还原铁,简称DRI(Direct Reduction Iron),也称海绵铁。
优质DRI由于其成分稳定,有害元素含量低,粒度均匀,不仅可以补充废钢资源的不足,而且还可以作为电炉炼钢的原料以及转炉炼钢的冷却剂,对保证钢材的质量特别是合金钢的质量,起着不可替代的作用,是冶炼特钢的优质原料;同时,高品位DRI还可以供粉末冶金行业使用【1】。
直接还原铁生产方法中,主要分为气基法和煤基法。
由于我国天然气资源缺乏,但是煤炭资源丰富,煤基直接还原技术成为我国直接还原铁生产的重要工艺方法【2】。
煤基直接还原是指直接以廉价的非焦煤作还原剂生产直接还原铁的方法。
在我国煤基直接还原技术主要是回转窑法和隧道窑法【3】,近几年也相继建设了多座转底炉装置,同时也建设了一些煤基连续式竖炉装置。
在直接还原技术日益发展、大力提倡环保节能减排的今天,一些新的更先进的直接还原工艺及设备被迫切需要【4,5】。
煤基竖炉直接还原技术是一项符合中国能源结构特点的可大型化生产高品质海绵铁的直接还原铁生产技术【6】,可广泛用于处理高品位铁精粉制取高纯度还原铁粉用于粉末冶金领域,也可用于处理普通品位的铁精粉制取炼钢用海绵铁,处理复合铁矿生产普通铁水及提取钒、钛、硼等高附加值资源。
煤基直接还原铁综述

低品位铁矿石煤基直接还原铁摘要:文章介绍介绍了直接还原铁的两种生产方法,并联系国内实际着重介绍煤基直接还原法,联系我国铁矿石的供需现状,通过分析近年来直接还原铁发展状况,提出低品位铁矿石用褐煤半焦做还原剂生产直接还原铁的思路。
直接还原是指用气体或固体还原剂在低于铁矿石软化温度下,在反应装置内将铁矿石还原成金属铁的方法。
其产品称直接还原铁,这种铁保留了失氧前的外形,因失氧形成了大量微孔隙,显微镜下形似海绵结构,故又称海绵铁。
[4]直接还原铁(DRI)因质地纯净、成分稳定,是一种替代废钢、冶炼优质钢和特殊钢的理想原料。
很多用废钢不能生产的特种钢都能用海绵铁生产出来[3].一、直接还原铁的生产方法直接还原工艺根据还原剂不同可分为气基直接还原和煤基直接还原。
气基直接还原工艺以天然气为主要还原剂,包括竖炉、反应罐和流化床流程。
煤基直接还原以煤为主要能源,主要是使用回转窑为主体设备的流程[1]。
目前运行中的气基直接还原设备有三种。
第一种是竖炉,是成熟的主导工艺,以MIDREX 流程为代表,具有容易控制、产品质量好、能耗低、环境污染轻、生产率高等特点,竖炉流程占据了大部分直接还原生产能力[6]。
第二种是反应罐,使用反应罐的流程只有HYL法。
反应罐采用落后的固定床非连续生产模式,证处于被逐渐淘汰的过程中。
第三种是流化床,目前唯一的代表是FIOR法[1]。
煤基直接还原法工艺主要包括回转窑法、转底炉法、隧道窑法。
只有回转窑流程拥有可观的生产能力,具有代表性的回转窑流程是SL-RN法。
推动直接还原工艺技术发展的客观原因主要有以下几点;1)世界多数国家严重缺少焦煤,但其中不少国家拥有优质丰富的铁矿以及天然气和非焦煤资源,可以因地制宜地发展直接还原来解决生铁资源问题。
委内瑞拉、墨西哥、伊朗等国具有丰富的天然气及优质铁矿,主要发展竖炉气基直接还原工艺,而南非、印度、新西兰等国家具有丰富的烟煤及优质铁矿,则主要发展回转窑煤基直接还原工艺。
气基直接还原炼铁工艺的汇报材料之一
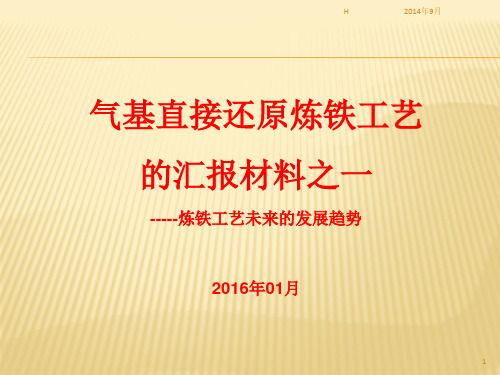
By Product Plant COG
Bin
Bin
Coke
CDQ &
Quenching
Tower
3
H
2.COREX熔融还原炼铁工艺流程示意图
煤
块矿/球团/熔
剂 洗涤塔 输出煤气
炉顶煤
还原竖炉
气
热还原气
洗涤塔
熔融 气化炉
粉尘
热旋风 除尘器
冷煤气
铁水与炉渣
氧气
4
H 2014年9月
宝钢COREX C3000顺利出铁!
直接还原铁技术与高炉炼铁技术相比,具有节能减排降碳的 特性,符合建设“两型”社会的基本国策。直接还原铁的优势 主要体现在以下三个方面:
26
H
(1) 杂质含量低 S、P和残余元素的含量很低,可以保证钢液的成分均匀,使用的过
程中不会产生环境污染。 (2)实现炉料热装
减少电炉电力需求量I20~14OkWh/t; 降低电炉电极消耗0 5—0.6kg; 降低耐火材料损耗; (3)生产灵活。 电炉停产时,直接还原设备能继续生产:直接还原殳备停产时.电 炉能用库存的直接还原铁或热压块铁生产;剩余直接还原铁或热压块 铁可供出售。
BF+烧结+炼焦 16.25 320~400 90000
COREX
煤\焦
(4000m3)
COREX
17 150
500
SL/RN回转窑
煤
回转窑
18 15 1440
隧道窑
煤
隧道窑 25~30 1~4 20
—————————————————————————————
﹡MIDREX HYL Ⅲ 气基直接还原的能耗最低。
29
经验证的钢厂废料回收利用工艺

FASTMET经验证的钢厂废料回收利用工艺James M.Mc clelland,Jr.P.EManager-Techincal SalesMidrex Technologes,Incorproated2725 Water Ridge ParkwayCharlotte,North Carolina,28217USATel:704-378-3359Fax:704-373-1611:jmcclellandmidrex.关键词:FASTMET;FASTMELT®;转底炉;直接还原;铁氧化物;电炉粉尘;钢厂废料;锌的回收利用。
摘要:两个用于回收利用钢铁厂废料的FASTMET流程工厂现在已处于商业运作。
这些FASTMET流程设备正在将钢铁厂废料转变为有用的铁产品和有价值的副产品。
本文将通过这两个工厂来讨论包括废弃燃料油操作,产品质量,锌的回收利用和排放物的测试等操作经验。
绪论Midrex技术公司和它的母公司神户钢铁公司合作,已经开发出了一种以固体炭为基础的还原技术FASTMET流程:这种流程可应用于加工铁矿石,也可应用于加工含有铁氧化物的材料,比如钢厂的废料。
将一台电化铁炉添加到FASTMET 流程就得到了FASTMELT®----------一种生产高质量铁水的经济的方法。
大多数钢铁厂都正在寻求一种合适的方式来回收利用包括高炉和碱性氧化顶吹转炉粉尘、淤泥、轧钢皮、电弧炉粉尘在内的各种钢铁生产废弃物。
电弧炉炼钢粉尘的积聚以及对它们的处理已成为了一个世界性课题。
电弧炉粉尘的回收利用包含两个方面:一方面是回收利用有价值的资源,回收含铁料来炼钢,粗氧化锌用于回收有色金属;另一方面是降低对环境的污染。
从经济与环保两方面来考虑,FASTMET流程都是一种十分吸引人的电弧炉粉尘回收利用技术。
在将粉尘回收起来做电弧炉和碱性氧气顶吹转炉的原料方面,这个流程有两个主要目标。
一个是为了提高铁氧化物的金属化率,这样可以减轻熔化过程的负担。