各种橡胶的混炼特性(ppt 25页)
橡胶塑炼与混炼—塑炼(橡胶加工课件)

保持变形后的形状
降低弹性、增大塑性 塑炼
塑炼
1、塑炼概念与原理
讨论:塑炼、塑炼目的及不利面
分组汇报: 教师点评 1、塑炼: 炼:炼胶、炼胶作业,在炼胶机完成的作业过程。
简要:提高橡胶塑性的炼胶
详细:将橡胶经过机械加工、热处理或加入某些化学助剂,使其由强韧的弹性状态转变为柔 软而便于加工的塑性状态的工艺过程称之为塑炼。
塑炼
1、塑炼概念与原理 2、生胶塑炼前的准备 3、塑炼的工艺方法 4、影响塑炼的工艺因素 5、开炼机塑炼实训 6、常见塑炼胶质量分析
1、塑炼概念与原理
引入新课 F 塑性
F 弹性
F 刚性
1、塑炼概念与原理
引入新课 橡胶具有高弹性 优点:
缓冲、减震、柔软
缺点:
产品加工过程是受力变形并定型,如发生弹性回复,尺寸形状不能保持
2、生胶塑炼前的准备-烘胶
目的
对象
“两保证两可以” (1)保证切胶机的安全操作和
工作效率; (2)保证炼胶机的安全操作和
工作效率; (3)可以烘去水份; (4)可以解除结晶(对结晶橡
胶) 。
(1)硬橡胶 如:硬NBR等 (NBR3606)
(2)结晶橡胶 如:NR、CR 等
实物展示 ( NBR 、NR、CR、 EPDM、SBR、BR)
2、生胶塑炼前的准备-破胶
使块状的橡胶变为碎胶 (1)便于称量; (2)便于塑炼; (3)保护设备; (4)提高效率(塑
炼)。
用于开炼机塑混炼的大块橡胶, 如:NR和CR。 说明: ❖ 1、用密炼机塑混炼的NR和CR, 一般无需破胶而直接进行塑混炼。 ❖ 2、其它合成橡胶,一般无需破 胶而直接进行塑混炼。
6、常见塑炼胶质量分析
常用典型橡胶的混炼工艺特点
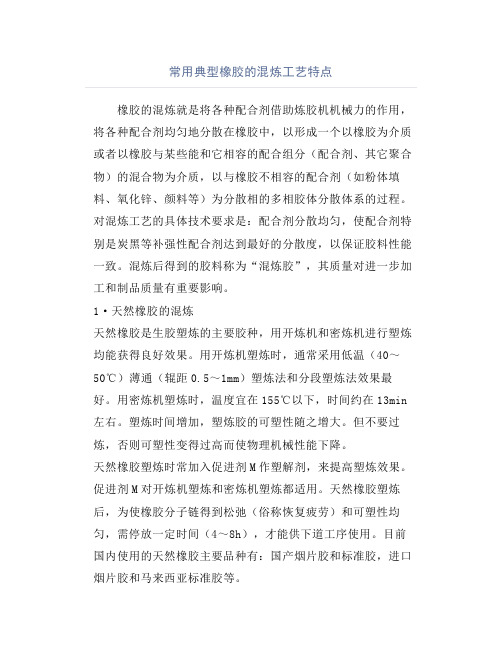
常用典型橡胶的混炼工艺特点橡胶的混炼就是将各种配合剂借助炼胶机机械力的作用,将各种配合剂均匀地分散在橡胶中,以形成一个以橡胶为介质或者以橡胶与某些能和它相容的配合组分(配合剂、其它聚合物)的混合物为介质,以与橡胶不相容的配合剂(如粉体填料、氧化锌、颜料等)为分散相的多相胶体分散体系的过程。
对混炼工艺的具体技术要求是:配合剂分散均匀,使配合剂特别是炭黑等补强性配合剂达到最好的分散度,以保证胶料性能一致。
混炼后得到的胶料称为“混炼胶”,其质量对进一步加工和制品质量有重要影响。
1·天然橡胶的混炼天然橡胶是生胶塑炼的主要胶种,用开炼机和密炼机进行塑炼均能获得良好效果。
用开炼机塑炼时,通常采用低温(40~50℃)薄通(辊距0.5~1mm)塑炼法和分段塑炼法效果最好。
用密炼机塑炼时,温度宜在155℃以下,时间约在13min 左右。
塑炼时间增加,塑炼胶的可塑性随之增大。
但不要过炼,否则可塑性变得过高而使物理机械性能下降。
天然橡胶塑炼时常加入促进剂M作塑解剂,来提高塑炼效果。
促进剂M对开炼机塑炼和密炼机塑炼都适用。
天然橡胶塑炼后,为使橡胶分子链得到松弛(俗称恢复疲劳)和可塑性均匀,需停放一定时间(4~8h),才能供下道工序使用。
目前国内使用的天然橡胶主要品种有:国产烟片胶和标准胶,进口烟片胶和马来西亚标准胶等。
由于上述胶种的初始门尼粘度不同,欲获得相同的可塑性,所需的塑炼时间当然不同。
其塑炼时间按长短排列的顺序为:进口烟片胶>国产烟片胶>国产标准胶>马来西亚标准胶。
恒粘和低粘标准马来西亚橡胶、充油天然橡胶、轮胎橡胶、易操作橡胶的初始门尼粘度较低(一般小于65),可不经塑炼直接混炼。
天然混炼胶(NR)具有综合性好的物理机械性能,在常温下具有很高的弹性,弹回率可达50%~85%以上。
天然胶还具有较高的机械强度,很好的耐屈挠疲劳性能,滞后损失小,多次变形下生热量低,撕裂强度高,耐磨性和耐寒性良好,以及良好的气密性、防水性、电绝缘性和绝热性。
各种原材料的混炼特性

软化剂一般为加工油或操作油,用以改善乙丙橡胶的加工及操作性能。此外,还可起增量填充作用,以降低胶料成本。与乙丙橡胶相容性好,可大量采用酯类增塑剂。
促进剂
促进剂大部分都是粉状物质,且用量较小。因此在胶料中必须混炼均匀,分散良好,否则会影响硫化胶性能或出现喷霜现象。为了防止促进剂粉料飞扬造成损失,最好采用预先制成的造粒产品,而且能提高分散性。加入促进剂的混炼胶料,下片后应立即冷却,并在规定时段内使用,否则可能因焦烧失效。
补强剂和填充剂
这是乙丙橡胶中用量最大的配合剂,与分散的关系也最密切。一般来说,补强填充剂粒径越小,表面积越大,对乙丙橡胶的润湿性越差,也越难分散。由于炭黑在橡胶中的用量大,为获得良好分散性,可采取分批投料的方法。与炭黑一样,无机填充剂的分散难易亦取决于粒子大小。粒子愈小,分散愈难,生热量也愈大,但补强效果愈好。改进填充剂分散性的方法是进行表面化学预处理后再使用,或加入分散助剂、流动助剂等加工助剂。
各种原材料的混炼特性
原材料名称
混炼特性
乙丙橡胶生胶
乙丙橡胶为非极性橡胶且不饱和度低,因此通常对填料和配合剂的浸润性较差,混入速度较慢,但通过配合相应的软化剂或操作剂而使混炼性能改善。乙丙橡胶在开炼机辊筒பைடு நூலகம்包辊时对温度较为敏感。在允许温度范围内,为使填充剂能很快分散均匀,混炼温度应高于一般合成橡胶。
硫黄
硫黄熔点较低,100℃以上即发生液化结团,难以分散。因此,加硫黄时胶料温度必须冷却到100℃以下,以利分散。硫黄可与EPDM生胶经过预先混合制成母胶颗粒使用,以促进其分散并防止飞扬。为防止焦烧,硫黄一般在混炼最后阶段加入,并要求操作迅速完成。
氧化锌
氧化锌是乙丙橡胶胶料中应用最广泛的配合剂之一。通常有轻质氧化锌和活性氧化锌之分,一般用作活性剂,对提高硫化速度效果显著。使用活性氧化锌对提高乙丙橡胶的硫化速度更有帮助。有时也用作填充剂。由于其本身化学特性,氧化锌在橡胶中极易混入,但分散极难。氧化锌不易分散的原因是混炼时与生胶一样带负电荷,两者相斥。为改善氧化锌混炼分散的效果,最好使用预先造粒的氧化锌颗粒制剂,或粒子较细的氧化锌产品。
第十二章橡胶混炼工艺.pptx
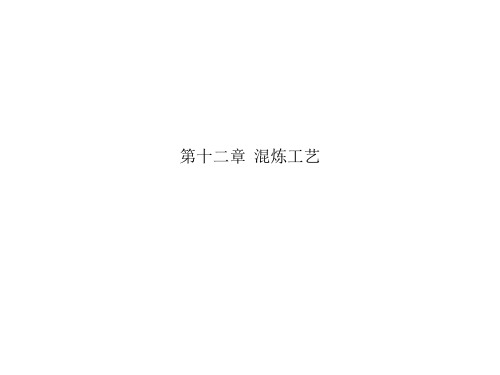
(二)开炼机混炼的影响因素 (1)装胶容量 装胶容量需依据开炼机的规格及胶料配方特性合理确定。容量过大,使
混炼分散效果降低,混炼温度升高,容易产生焦烧现象而影响胶料质 量;容量过小会降低生产效率。
Q K•D•L
式中 V—装胶容量,L;D—辊筒直径,cm;L—辊筒长度;
(2)辊距 辊距一般取4~8mm为宜。辊距减小,剪切效果增大,但生热大。 (3)混炼温度
四.称量配合
要求称量配合操作做到:精密、准确、不漏、不错。
称量配合的操作方式有两种:(1)手工操作;(2)机械化自动称量配 合。
§12.2 混炼工艺
一.混炼胶的结构 混炼胶是由粒状配合剂(如炭黑、促进剂、填充剂等)分散于生胶中组
成的分散体系。在分散体系中,生胶的分散呈连续状态,称为分散质, 粒状配合剂为分散相。 混炼胶不同于一般的胶体分散体系: (1)橡胶的粘度很高,胶料的热力学不稳定性在一般情况下不太显著; (2)某些组分(如再生胶、增塑剂等)与橡胶能互容,从而构成了混炼 胶的复合分散介质; (3)粒状配合剂(如炭黑合促进剂等)与橡胶在接触界面上产生了一定 的物理和化学结合,这对胶料和硫化胶的性能起着重要的影响。 因此,可以认为混炼胶是一种具有复杂结构特性的胶态分散体。
(4)混炼时间
应适当掌握配合剂的混入和分散时间,避免混炼时间过长,否则容易产 生过炼现象。
(5)辊速和速比
辊速控制在16~18r/min内。辊速快,操作不安全且温度控制困难;辊速 慢,混炼效率低。
速比一般为1:1.1~1:1.2。生热高的胶料应选择速比在1:1.15以下的开 炼机。
(6)加料顺序
一般的加料原则是:用量少、难分散的配合剂先加;用量大、易分散的 后加;为了防止焦烧,硫黄和超速促进剂一般最后加入。通常采用的 加料顺序如下:
橡胶的配合与开炼机混炼工艺-PPT文档资料

橡胶工艺实验 Experiment of Rubber Technology
不同胶料开炼机混炼时辊筒温度
胶 种 天然胶 辊 温℃
前辊
55~60
后辊
50~55
丁苯胶
氯丁胶
45~50
35~45Βιβλιοθήκη 50~5540~50
丁基胶
丁腈胶 顺丁胶 三元乙丙胶 氯磺化聚乙烯 氟橡胶23—27 丙烯酸酯橡胶
40~45
≦40 40~60 60~75 40~70 77~87 40~55
橡胶工艺实验 Experiment of Rubber Technology
四、影响因素
1、胶料的包辊性
胶料的包辊性好坏会影响混炼时吃粉快慢、配合剂分散, 如果包辊性太差,甚至无法混炼。
2、装胶容量
装胶容量过大,增加了堆积胶量,使堆积胶在辊缝上方 自行打转,失去了起折纹夹粉作用,影响配合剂的吃入 和分散效果,延长混炼时间,胶料的物性下降,同时会 增大能耗,增加炼胶机的负荷,易使设备损坏。如果装 胶量过少,堆积胶没有或太少,吃粉困难,生产效率太 低。
6、按下列加料顺序依次沿辊筒轴线方向均匀加入各种配合 剂,每次加料后,待其全部吃进去后,左右3/4割刀各两 次,两次割刀间隔20秒钟;
加料顺序:胶料→小料(固体软化剂、活化剂、促进剂、 防老剂、防焦剂等)→大料(炭黑、填充剂等)→液体 软化剂→硫黄和超速级促进剂 7、割断并取下胶料,将辊距调整到0.5mm,加入胶料薄通, 并打三角包,薄通5遍; 8、按试样要求,将胶料压成所需厚度,下片称量质量并放 置于平整、干燥的存胶板上(记好压延方向、配方编号)待 用。 9、关机,清洗机台。
二、实验设备及工作原理
1、实验设备
ф160×320mm双辊筒开炼机,上海机械技术研究所 产品。
橡胶混炼工艺介绍 ppt课件

2
精品资料
2020/11/29
• 你怎么称呼老师? • 如果老师最后没有总结一节课的重点的难点,你
是否会认为老师的教学方法需要改进? • 你所经历的课堂,是讲座式还是讨论式? • 教师的教鞭 • “不怕太阳晒,也不怕那风雨狂,只怕先生骂我
二、机械塑炼工艺
3、密炼机塑炼工艺
(1).密炼机塑炼方法 密炼机塑炼的工艺方法有一段塑炼法、分段塑炼法和化
学增塑塑炼法。 若塑炼胶的可塑度要求较低时,采用一段塑炼法即可,
如胶料的可塑度要求较高,采用一段塑炼时间太长,可采用 分段塑炼法或化学增塑法塑炼。
24
2020/11/29
影响开炼机塑炼的因素:
17
一、生胶的增塑方法和机理
2020/11/29
(二)、生胶塑炼的增塑机理
4.化学塑解剂 的作用
在生胶机械塑炼过程中,加入某些低分子化学物 质可通过化学作用增加机械塑炼效果,这些物质称为 化学塑解剂。
18
一、生胶的增塑方法和机理
2020/11/29
(二)、生胶塑炼的增塑机理
5.电与臭氧的作用
用开炼机塑炼时因辊筒表面与胶料之间的剧烈摩 擦会产生静电,并在胶料表面积累,到一定程度便产 生静放电,生成臭氧和原子氧,对橡胶的氧化裂解作 用更大。
28
二、机械塑炼工艺
2020/11/29
5、合成橡胶的机械塑炼特性
(1).天然生胶 无论哪种方法都比较容易获得可塑性.用开炼机塑炼时采用低辊温(40-50 ℃)、小 辊距(0.5-1.0mm)薄通塑炼法和分段塑炼法效果最好。用密炼机塑炼时,温度宜在155 ℃ 以下,塑炼 时间约在13min左右。
橡胶的塑炼与混炼原理工艺24页PPT

41、实际上,我们想要的不是针对犯 罪的法 律,而 是针对 疯狂的 法律。 ——马 克·吐温 42、法律的力量应当跟随着公民,就 像影子 跟随着 身体一 样。— —贝卡 利亚 43、法律和制度必须跟上人类思想进 步。— —杰弗 逊 44、人类受制于法律,法律受制于情 理。—敢地 走到底 ,决不 回头。 ——左
45、法律的制定是为了保证每一个人 自由发 挥自己 的才能 ,而不 是为了 束缚他 的才能 。—— 罗伯斯 庇尔
56、书不仅是生活,而且是现在、过 去和未 来文化 生活的 源泉。 ——库 法耶夫 57、生命不可能有两次,但许多人连一 次也不 善于度 过。— —吕凯 特 58、问渠哪得清如许,为有源头活水来 。—— 朱熹 59、我的努力求学没有得到别的好处, 只不过 是愈来 愈发觉 自己的 无知。 ——笛 卡儿
- 1、下载文档前请自行甄别文档内容的完整性,平台不提供额外的编辑、内容补充、找答案等附加服务。
- 2、"仅部分预览"的文档,不可在线预览部分如存在完整性等问题,可反馈申请退款(可完整预览的文档不适用该条件!)。
- 3、如文档侵犯您的权益,请联系客服反馈,我们会尽快为您处理(人工客服工作时间:9:00-18:30)。
(二)开炼机混炼的影响因素 (1)装胶容量 装胶容量需依据开炼机的规格及胶料配方特性合理确定。容量过大,使
混炼分散效果降低,混炼温度升高,容易产生焦烧现象而影响胶料质 量;容量过小会降低生产效率。
QK•D•L
式中 V—装胶容量,L;D—辊筒直径,cm;L—辊筒长度;
(2)辊距
辊距一般取4~8mm为宜。辊距减小,剪切效果增大,但生热大。
塑炼胶、再生胶、母炼胶 → 促进剂、活性剂、防老剂 →补强、填充剂 →液体软化剂 → 硫黄、超速促进剂
三.密炼机的混炼工艺
优点:混炼容量大,混炼时间短,效率高;投料、捏炼、加压和排料操 作易于机械化、自动化,劳动强度低,操作安全性大,配合剂损失、 粉尘飞扬状况得到改善,胶料质量和环境卫生条件好。
缺点:混炼时温度较高,对温度敏感的胶料易发生焦烧,需要对排胶进 行补充加工。
(一)密炼机混炼工艺操作方法
1.一段混炼法
(1)传统一段混炼法
把塑炼胶和各种配合剂逐步分次加入,每次加料后,放下上顶栓,加压 程度视具体情况而定。
传统一段混炼法的混炼程序一般为:橡胶(生胶、塑炼胶、再生胶等) → 硬脂酸 → 促进剂、活性剂、防老剂 → 补强速促进剂 → 下片 → 冷却、停 放
(4)混炼时间
应适当掌握配合剂的混入和分散时间,避免混炼时间过长,否则容易产 生过炼现象。
(5)辊速和速比
辊速控制在16~18r/min内。辊速快,操作不安全且温度控制困难;辊速 慢,混炼效率低。
速比一般为1:1.1~1:1.2。生热高的胶料应选择速比在1:1.15以下的 开炼机。
(6)加料顺序
一般的加料原则是:用量少、难分散的配合剂先加;用量大、易分散的 后加;为了防止焦烧,硫黄和超速促进剂一般最后加入。通常采用的 加料顺序如下:
二.配合剂的补充加工
(一)粉碎 块状和粗粒状配合剂必须经过粉碎或磨细处理才能使用,如沥青、松香和古
马隆等固体用粉碎机粉碎。 (二)干燥 干燥的目的是减少配合剂中的水分和其他挥发分含量,防止粉末状配合剂结
团,便于筛选和混炼分散,避免某些配合剂遇水变质和胶料内部产生气 泡和海绵。 干燥方式可采用真空干燥箱、干燥室或螺旋式连续干燥机等。 (三)熔化与过滤及加温 低熔点固体软化剂如石蜡和松香等须进行加热熔化,达到干燥脱水和降低粘 度作用后,再经过滤去掉其中的机械杂质。 (四)筛选 粉末状固体软化剂粒度及粒度分布达不到规定标准的,或已经发生配合剂结 团及含有机械杂质的必须经过筛选加工,去掉其中的机械杂质、较大颗 粒与结团。
三.油膏和母炼胶的制造
油膏:为了使配合剂易于在胶料中混合分散,减少飞扬损失造成环境污 染,保证胶料的混炼质量,将某些配合剂、促进剂等事先以较大比例 与液体软化剂混合制成膏状混合物。
母炼胶:将在通常混炼条件下短时间内难以混合均匀且混炼生热量多, 能耗较大的某些配合剂以较大的比例事先与生胶单独混合制成组分比 较简单的混合物料。最常见的有促进剂母胶、炭黑母胶、化学塑解剂 母胶等。
(3)混炼温度
辊温过低,胶料硬度太大,容易损坏设备。辊温提高有利于降低胶料的 粘度,加快混炼吃粉速度,但温度太高,容易使胶料产生脱辊现象和 焦烧现象,难以操作。
辊温一般通过冷却的方法保持在50~60℃之间。但在混炼含有高熔点配合 剂(高熔点古马隆树脂等)的胶料时,需要适当提高辊温;而混炼顺 丁胶时,辊温不得超过50℃。
四.称量配合 要求称量配合操作做到:精密、准确、不漏、不错。 称量配合的操作方式有两种:(1)手工操作;(2)机械化自动称量配
合。
§12.2 混炼工艺
一.混炼胶的结构 混炼胶是由粒状配合剂(如炭黑、促进剂、填充剂等)分散于生胶中组
成的分散体系。在分散体系中,生胶的分散呈连续状态,称为分散质, 粒状配合剂为分散相。 混炼胶不同于一般的胶体分散体系: (1)橡胶的粘度很高,胶料的热力学不稳定性在一般情况下不太显著; (2)某些组分(如再生胶、增塑剂等)与橡胶能互容,从而构成了混炼 胶的复合分散介质; (3)粒状配合剂(如炭黑合促进剂等)与橡胶在接触界面上产生了一定 的物理和化学结合,这对胶料和硫化胶的性能起着重要的影响。 因此,可以认为混炼胶是一种具有复杂结构特性的胶态分散体。
二.开炼机的混炼工艺 (一)开炼机混炼原理 开炼机混炼过程一般包括包辊、吃粉和翻炼三个阶段。
1.包辊
1-橡胶不易进入辊缝;2—紧包前辊;3—脱辊成袋囊状;4—呈粘流包辊
2.吃粉 在胶料包辊,加入配合剂之前,要使辊距上端保留适当的堆积胶,适量
的堆积胶是吃粉的必要条件。 3.翻炼 周向:混炼最均匀;轴向:不均匀;径向:均匀性最差
第十二章 混炼工艺
§12.1 §12.2 §12.3 §12.4
混炼前的准备 混炼工艺 混炼胶的质量检查 各种橡胶的混炼特性
§12.1 混炼前的准备
一.原材料与配合剂的质量检验 通常对配合剂检验的内容主要有:纯度、粒度及分布、机械杂质、灰分
及挥发分含量、酸碱度等。具体依配合剂类型不同而异。 生胶一般检验化学成分、门尼粘度及物理机械性能。
炭黑与橡胶混炼后形成的补强结构,对胶料和硫化胶的力学性能和流变性能等都有较 大的影响。
1.炭黑网络结构
炭黑与橡胶混炼时,形成炭黑—橡胶聚集体,聚集体在剪切力的作用下逐步分散。当 混炼胶中炭黑的用量较高时,炭黑通过链状结构相互连结,构成炭黑网络。
炭黑网络结构的体现:(a)Payne效应;(b)混炼胶比纯胶具有较高的导电性。
2.吸留橡胶结构
混炼时,形成吸留橡胶。在混炼过程中,受剪切力的作用,吸留橡胶的一部分或大部 分被重新释放出来。但是,吸留橡胶多少都会部分地保留在炭黑聚集体中,成为 混炼胶填料的一部分。
3.炭黑结合橡胶
炭黑结合橡胶对胶料的性能影响很大,可提高硫化胶的模量、耐磨性以及减少滞后生 热等。
4.可溶胶
结合橡胶在混炼胶中只占一小部分。而大部分橡胶未与炭黑结合,称为可溶胶。这两 部分橡胶对混炼胶的物理性能都有贡献。
(2)分段投胶一段混炼法
分批加入生胶,以强化炭黑的分散,达到改善合提高胶料的工艺性能及 硫化较的物理机械性能。