注塑及吹膜常见问题及解答共55页文档
注塑产品在生产中存在的问题及解决方法

管件在生产中存在的问题及解决方法(1)注塑产品收缩变形,达不到标准,如:注塑90°弯头不够90°或大于90°。
可能出现问题的原因:A、模具设计没有考虑管件收缩的因素,模具设计为90°,但半成品收缩后不够90°或大于90°。
B、冷却时间短,开模造成管件变形。
C、模具温度高。
D、保压时间短或保压压力小,管件收缩大。
补救方法:设计模具和调整工艺时应充分考虑管件收缩问题,注塑半成品冷却收缩后为90°;调整注塑工艺,延长冷却时间,使模具温度保持在30--50°范围内,增加保压时间或保压压力。
(2)注塑产品气孔。
(目前无法解决)。
半产品在车削过程中经常出现空穴和气孔,使产品合格率降低。
这与制品厚度有关,而且常因塑料冷却收缩离开注塑件中心而引起。
可能出现问题的原因:A、模具未充分填充或填充不实。
B、止流阀的不正常运行,有回流现象。
C、原料未彻底干燥,水分含量高。
D、预塑或注射速度过快。
E、模具浇口位置和形式设计不合理,模具形状设计不合理。
目前的补救方法:A、增加射料量;B、增加注塑压力;C、增加螺杆向前时间;D、降低熔融温度;E、降低或增加注塑速度;F、检查止逆阀是否裂开或无法运作;G、让原料彻底干燥(≤300ppm);H、适当降低螺杆转速和增大背压,或降低注射速度;I、改变浇口位置和形式,必要时改变模具的设计。
(3)注塑产品褶皱流纹,车削断削。
可能出现问题的原因:通常与表面痕有关,而且是塑料从模具表面收缩脱离形成的,也有注射时造成。
A、原料熔融温度不是太高就是太低;B、模腔内塑料不足;C、冷却阶段时接触塑料的面过热;D、流道不合理、浇口截面过小;E、模温是否与原料特性相适应;F、产品结构不合理(过厚或明显厚薄不一);G、模具冷却效果不好。
补救方法:A、调整料筒温度;B、调整螺杆速度以获得正确的螺杆表面速度和剪切温度;C、增加注塑量;D、保证使用正确的垫料;增加螺杆向前时间;增加注塑压力;增加注塑速度;E、检查止流阀是否安装正确,因为非正常运行会引致压力流失,造成注不实。
吹塑薄膜成型故障的产生原因及排除方法

吹塑薄膜成型故障的产生原因及排除方法一、吹塑薄膜成型常见故障的排查1、引膜困难故障分析及排除方法:(1)机头温度控制不当。
当机头温度太高或太低时,都会引起牵引困难,应适当调整机头温度。
(2)口模出料不均匀。
应调整口模间隙,使周边间隙均匀。
同时,适当调节机头连接器温度,使之与机身温度相协调。
(3)熔料中含有焦料杂质。
应净化原料及清理机头和螺杆。
(4)挤出工艺条件控制不当。
应适当调整工艺条件。
几种常用塑料吹塑薄膜的挤出工艺条件如表3-1所示。
2、泡管歪斜故障分析及排除方法:(1)机身及口模温度太高。
应适当降低。
(2)机头连接器温度太高。
应适当降低。
(3)口模出料不均匀,薄膜厚薄不均。
应适当调整口模间隙及机头连接器温度。
表3-1 几种常用塑料吹塑薄膜的挤出工艺条件故障分析及排除方法:(1)泡管呈规律性的葫芦形是由于牵引辊的夹紧力太小,或牵引辊的转速受到机械传动阻力规律性变化的影响所致。
对此,应适当增加牵引辊的夹紧力,检修牵引装置的机械传动部分,使牵引辊的转速平稳。
(2)泡管呈无规律的葫芦形是由于牵引速度不稳定,以及冷却风环的风压太大。
对此,应调整牵引速度,使其运行稳定;风环的风压应适当降低。
4、泡管摆动故障分析及排除方法:(1)熔料温度太高。
应适当降低机身及机头温度。
(2)冷却风环的冷却效率太低。
应提高冷却系统的冷却效率,可适当加大风环的风压和风量。
(3)泡管与人字夹板的摩擦力太大。
应适当加大人字板夹角,减小泡管与夹板的接触面积。
(4)机头温度太低,出料困难,膜泡跳动。
应适当提高机头温度及增加螺杆转速。
5、薄膜表面发花故障分析及排除方法:(1)机身或机头温度偏低,熔料塑化不良。
应适当提高机身或机头温度。
(2)螺杆转速太快。
应适当减慢。
(3)螺杆温度太高或太低。
应通过调整螺杆内冷却介质的流量,将螺杆温度控制在适宜的温度范围内。
6、挂料线明显故障分析及排除方法:(1)口模出料口处有分解物料或杂质粘附。
应用铜铲将杂质或焦料刮除,严重时应顶出芯棒进行清理。
注塑过程中常见的问题及解决方案

注塑过程中常见的问题及解决方案一、飞边(披锋)1. 问题描述- 这飞边就像塑料偷偷长出来的小翅膀,在注塑件的边缘或者分型面那里冒出来,看着可闹心了。
就像好好的一块蛋糕,边缘突然多出了一些不规则的奶油坨坨。
2. 解决方案- 首先得检查模具的合模力。
要是合模力不够,那塑料就会像调皮的小孩从门缝里挤出来。
适当增加合模力,把模具紧紧抱住,让塑料乖乖待在该待的地方。
- 模具的磨损也会导致飞边。
就像穿破了的鞋子会漏脚指头一样,磨损的模具缝隙变大了。
这时候就得修模啦,把那些磨损的地方补一补或者磨平。
- 注塑压力也不能太大。
如果压力太大,塑料就像被大力士猛推的水,到处乱流。
降低注塑压力,找到一个合适的值,既能把模具填满,又不会让塑料溢出来。
二、短射(缺料)1. 问题描述- 短射就像给一个杯子倒水,结果没倒满一样。
注塑件看着不完整,有些地方该有塑料的却空着,就像一个没发育好的小怪物。
2. 解决方案- 先看看注塑压力是不是太小。
压力小的话,塑料就像没力气的小蚂蚁,爬不到模具的每个角落。
增加注塑压力,让塑料充满整个模具型腔。
- 塑料的流动性也很关键。
如果塑料太黏,就像浓稠的糨糊,很难流到模具的远端。
这时候可以提高料筒温度,让塑料变得稀一点,流动性更好,就像把糨糊加热变成稀粥一样,能顺利流到各个地方。
- 浇口尺寸也可能有问题。
要是浇口太小,就像一个小得可怜的水龙头,水流不出来多少。
适当扩大浇口尺寸,让塑料能畅快地流进模具。
三、气泡(气穴)1. 问题描述2. 解决方案- 注塑速度可能太快了。
塑料像一阵风呼呼地冲进模具,把空气都裹在里面了。
降低注塑速度,让塑料慢慢流进去,就像散步一样,这样空气就有机会跑出来了。
- 模具的排气也很重要。
如果模具没有排气孔或者排气不良,空气就被困在里面出不来。
在模具上开排气槽或者使用透气钢材料,给空气一条逃跑的路。
- 塑料干燥不彻底也会产生气泡。
如果塑料里有水份,加热的时候就会变成水蒸气,形成气泡。
吹膜常见问题及原因分析(1)

吹膜常见问题及原因分析(1)1. 薄膜太粘,开口性差原因1:树脂原料型号不对,不是吹膜级的低密度聚乙烯树脂,其中不含开口剂或者开口剂含量偏低;原因2:熔融树脂的温度太高,流动性太大;原因3:吹胀比太大,造成薄膜的开口性变差;原因4:冷却速度太慢,薄膜冷却不足,在牵引辊压力的作用下发生相互粘结;原因5:牵引速度过快。
2. 薄膜透明度差原因1:挤出温度低,树脂塑化不良,造成吹塑后薄膜的透明性较差;原因2:吹胀比过小;原因3:冷却效果不佳,从而影响了薄膜的透明度;原因4:树脂原料中的水分含量过大;原因5:牵引速度太快,薄膜冷却不足。
3. 薄膜出现皱折原因1:薄膜厚度不均匀;原因2:冷却效果不够;原因3:吹胀比太大,造成膜泡不稳定,左右来回摆动,容易出现皱折;原因4:人字夹板的角度过大,膜泡在短距离内被压扁,因此薄膜也容易出现皱折;原因5:牵引辊两边的压力不一致,一边高一边低;6、各导向辊之间的轴线不平行,影响薄膜的稳定性和平展性,从而出现皱折。
4. 薄膜有雾状水纹原因1:挤出温度偏低,树脂塑化不良;原因2:树脂受潮,水分含量过高。
5. 薄膜厚度不均匀原因1:模口间隙的均匀性直接影响薄膜厚度的均匀性,如果模口间隙不均匀,有的部位间隙大一些,有的部位间隙小一些,从而造成挤出量有多有少,因此,所形成的薄膜厚度也就不一致,有的部位薄,有的部位厚;原因2:模口温度分布不均匀,有高有低,从而使吹塑后的薄膜厚薄不均;原因3:冷却风环四周的送风量不一致,造成冷却效果的不均匀,从而使薄膜的厚度出现不均匀现象;原因4:吹胀比和牵引比不合适,使膜泡厚度不易控制;原因5:牵引速度不恒定,不断地发生变化,这当然就会影响到薄膜的厚度。
6. 薄膜的厚度偏厚原因1:模口间隙和挤出量偏大,因此薄膜厚度偏厚;原因2:冷却风环的风量太大,薄膜冷却太快;原因3:牵引速度太慢。
7.薄膜厚度偏薄原因1:模口间隙偏小,阻力太大,因此薄膜厚度偏薄;原因2:冷却风环的风量太小,薄膜冷却太慢;原因3:牵引速度太快,薄膜拉伸过度,从而是厚度变薄。
吹膜中常见问题分析解决
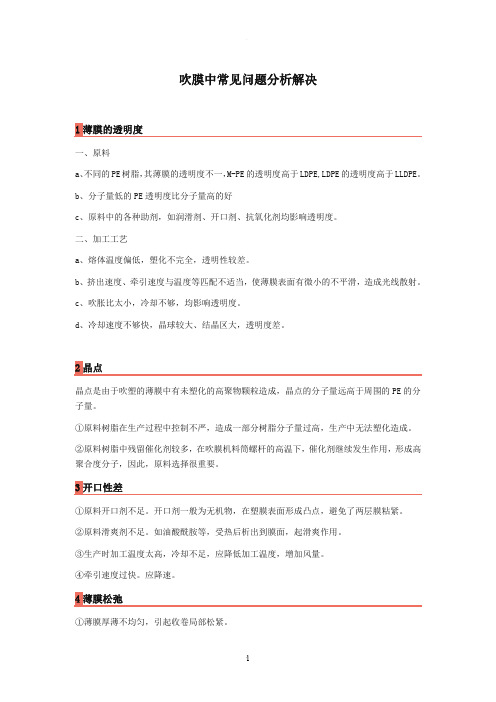
吹膜中常见问题分析解决一、原料a、不同的PE树脂,其薄膜的透明度不一,M-PE的透明度高于LDPE,LDPE的透明度高于LLDPE。
b、分子量低的PE透明度比分子量高的好c、原料中的各种助剂,如润滑剂、开口剂、抗氧化剂均影响透明度。
二、加工工艺a、熔体温度偏低,塑化不完全,透明性较差。
b、挤出速度、牵引速度与温度等匹配不适当,使薄膜表面有微小的不平滑,造成光线散射。
c、吹胀比太小,冷却不够,均影响透明度。
d、冷却速度不够快,晶球较大、结晶区大,透明度差。
2晶点晶点是由于吹塑的薄膜中有未塑化的高聚物颗粒造成,晶点的分子量远高于周围的PE的分子量。
①原料树脂在生产过程中控制不严,造成一部分树脂分子量过高,生产中无法塑化造成。
②原料树脂中残留催化剂较多,在吹膜机料筒螺杆的高温下,催化剂继续发生作用,形成高聚合度分子,因此,原料选择很重要。
①原料开口剂不足。
开口剂一般为无机物,在塑膜表面形成凸点,避免了两层膜粘紧。
②原料滑爽剂不足。
如油酸酰胺等,受热后析出到膜面,起滑爽作用。
③生产时加工温度太高,冷却不足,应降低加工温度,增加风量。
④牵引速度过快。
应降速。
①薄膜厚薄不均匀,引起收卷局部松紧。
②膜泡冷却风环冷却不当,冷却不均匀。
③膜泡进入夹棍前局部被冷却。
④模口与牵引辊中心不一致。
⑤切刀切边时,切刀锋刃不一致,角度不一致。
⑥收卷时压辊压力不一致。
⑦稳定板夹缝不均匀。
5横向厚度不均匀①模口间隙不均匀,应按要求仔细调节。
②机头四周加热不均匀,检查风环是否堵塞,开度是否合理。
③机头四周加热不均匀,应检查加热器。
④吹胀比过大,调换模头或换规格。
⑤过滤网破损,按时更换。
⑥风环进风软管破损或扭曲,有温度差或长短过于悬殊,应加以调整更换。
⑦稳泡器位置偏向心或开角不均,应加以调节。
⑧夹棍的压力不均匀,水平不平齐,应加以检查。
⑨模腔中有杂物,从而引起物流紊乱,出料不均,应当定期清洗口模。
⑩熔体压力或温度过高或波动太大,这样造成挤出熔流不稳,影响厚度不均,可调解温度,挤出速度改善。
吹膜工艺及常见问题的分析解决

润禾丰包装材料有限公司吹膜相关工艺及常见问题的分析解决摘要:在吹膜过程中,常见问题如薄膜出现褶皱、薄膜透明度差,鱼眼多、薄膜厚度不均、卷绕时跑卷等,本文将针对这些问题进行一些简单的分析和探讨,并提出相应的解决办法。
关键词:吹膜塑料薄膜薄膜透明度膜泡1引言塑料吹膜机是将塑料粒子加热融化再吹成薄膜。
塑料吹膜机分很多种,有PE,POF 等等。
用全新的粒子吹出的是新料,色泽均称,干净,袋子拉伸好。
也有人用回收的塑料袋来制成粒子,这种粒子一般叫旧料,制成粒子时通常是灰色的,在制成袋子时通常要添加色素,制成袋子着色不匀,脆且易断,价格也较低。
虽然是回收的塑料袋但一般都是制袋过程中的废品袋和通常意义上的垃圾塑料还是有很大的区别的[1]。
塑料吹膜机生产的是塑料膜适用于各种高档薄膜包装。
该种膜由于其阻隔性好,保鲜,防湿,防霜冻,隔氧,耐油,可广泛用于轻重包装。
如各种鲜果、肉食品、酱菜、鲜牛奶、液体饮料、医药用品等[2]。
2 聚乙烯吹塑薄膜材料的选择2.1 选用的原料应当用吹膜级的聚乙烯树脂粒子,含有适量爽滑剂,保证薄膜的开口性。
[3] 2.2 树脂粒子的熔融指数(MI)太大,则熔融树脂的粘度太小,加工范围窄,加工条件难以控制,树脂成膜性差,不容易加工成膜;此外,熔融指数(MI)太大,聚合物相对分子量分布太窄,薄膜强度差。
因此,应当选用熔融指数(MI)较小,且相对分子量分布较宽的数值原料,这样既能满足薄膜的性能要求,又能保证树脂的加工特性。
吹塑聚乙烯薄膜一般选用熔融指数(MI)在2-6g/10min范围质检的聚乙烯原料。
[4]3 吹塑工艺控制要点3.1 吹塑薄膜工艺大致如下:料斗上料→物料塑化挤出→吹胀牵引→风环冷却→人字夹板→牵引辊牵引→薄膜收卷但是,值得指出的是,吹塑薄膜的性能跟生产工艺参数有着很大的关系,因此,在吹膜过程中,必须要加强对工艺参数的控制,规范工艺操作,保证生产的顺利进行,并获得高质量的薄膜产品[5]。
吹膜工艺的常见问题

吹膜工艺的常见问题1.问题1:薄膜出现褶皱原因:薄膜横向厚度不均匀,哪怕是很微小,经过积累后也可造成比较明显的褶皱,影响落膘实验、薄膜撕裂实验、薄膜摩擦系数等的测定数据。
解决方法:(1)降低熔体温度,可以有效降低熔体流动性,在模头挤出时比较结实,不因冷却风波动使膜泡歪斜而造成薄膜冷却不均。
(2)减少冷却风量或调解冷却风不匀的情况。
(3)人字板的夹角过大,使得薄膜在短时间内被压扁,因而出现褶皱的问题,应适当减小人字板的夹角。
(4)膜口挤料不均匀,应调解口模,使之处于竖直状态。
(5)收卷辊张力过大把膜拉褶。
应适当减小收卷辊张力。
2.问题2:薄膜透明度差原因:主要影响因素是树脂原料,降低结晶度及使球晶细小,特别是添加剂的影响。
解决方法:(1)挤出温度偏低,熔体塑化不良,透明度较大,应适当提高熔体温度。
(2)冷却效果不佳,影响了透明度,应适当增大冷却风量。
(3)树脂粒子中含有大量水分,应充分干燥粒子。
3.问题3:薄膜鱼眼多原因:树脂中的析出物造成的,不能从根本上消除。
主要方法:(1)一定时间后,加大螺杆速度,提高熔体挤出压力,带走析出物。
(2)定期清洁模具头。
(3)适当提高熔体温度,充分塑化。
4.问题4:薄膜横向厚度不均匀.原因:在模口的出料量不均匀。
解决方法:(1)模具唇间隙调节不当,需局部调整或全部重新调整。
(2)模腔中有杂物,从而引起物流紊乱,出料不均,应当定期清洗口模。
(3)熔体压力或温度过高或波动太大,这样造成挤出熔流不稳,影响厚度不均,可调解温度,挤出速度改善。
5.问题5:膜泡扭动不稳原因:外部原因:如吹膜机没有在封闭区域内,室内对流严重,造成膜泡扭动解决方法:关闭门窗即可。
内部原因:(1)模具唇间隙调节不当,出料不均匀。
解决方法:需局部调整或全部重新调整。
(2)冷却风不匀。
解决方法:调节冷却风使其均匀。
(3)人字板的夹角过大。
解决方法:应适当减小人字板角度。
结论要想使试验数据准确,就必须吹制出优质的膜片试样,而吹制出优质的膜片,就难免会遇到上述问题,那么就可以参照上面论述的方法加以解决。
吹膜异常问题及处理方法

吹膜异常问题及处理方法高密度聚乙烯吹塑薄膜常见的异常现象、产生原因及其解决办法。
1、开始吹模时薄膜损失量太多。
产生原因:1、稳泡器尺寸不合适。
2、稳泡器过冷。
解决办法:1、更换尺寸适宜的稳泡器。
2、需要预热或绕上毯类物。
2、薄膜厚度不均。
产生原因:1、口膜间隙不均。
2、稳泡器未处垂直状态。
3、吹塑空气量不均匀。
4、机头温度不均。
稳泡器尺寸不适当。
解决办法:1、调整口模间隙。
2、很好地系紧,如支持棒弯曲需进行更换。
3、检查空冷环的水平管有无偏处。
4、检查加热器是否短路。
5、更换尺寸适宜的稳泡器。
3、膜泡不稳定。
产生原因:1、冷固线过高。
2、冷却空气乱流。
解决办法:1、调整至适当高度(勿下降太多)。
2、检查鼓风机、管及外部冷却装置。
4、膜泡断裂。
产生原因:1、混入异物。
2、薄膜厚度不均。
3、内稳泡器粗大或带有斜度。
4、成型温度底。
5、牵引速度快。
解决办法:1、更换滤网,清理机头。
2、参照序号2。
3、换适宜尺寸的稳泡器,高速时使用直筒型。
4、适当提高成型的温度。
5、降低牵引速度。
5、薄膜有纵向裂纹。
产生原因:1、横向取向度低。
2、厚度不均。
3、膜面存在的伤痕。
解决办法:1、缩小口模直径(即提高吹胀比)提高冷固线如稳泡器直径过大予以更换。
2、参照序号2。
3、检查口模、稳泡器有无损伤。
6、薄膜强度不够。
产生原因:1、吹胀比不当。
2、冷固线偏低。
3、牵引速度慢。
解决办法:1、将吹胀比调至3~5。
2、降低冷却风。
3、增加牵引速度。
7、薄膜中央起皱。
产生原因:1、冷固线至夹辊距离太长。
2、稳定板张开角小。
解决办法:1、升高冷固线或降低夹棍。
2、调大稳定板开角。
8、薄膜边缘松弛。
产生原因:1、冷固线至夹辊距离短。
解决办法:降低冷固线或升高夹辊。
分切、制袋工序中常见质量问题及解决方法在软包装材料(包括单质薄膜与复合膜)的生产工序中,分切作为承上启下的“特殊”工序,对内部影响下道制袋工序的质量及正品率,对外部顾客提供事先约定的、不同规格的卷材产品交付顾客使用,分切的质量就显得特别重要。
注塑时出现的问题及解决方法

注塑时出现的问题及解决方法
注塑的时候要是出问题了那可真让人头疼!比如说出现飞边,这就像一个调皮的孩子在不该出现的地方捣乱。
那咋解决呢?得调整模具的合模力呀,就像给一个调皮的孩子戴上紧箍咒,让它老老实实地待在该待的地方。
注塑产品出现缩水,哎呀,这就好像一个气球瘪了一块。
这时候可以增加注射压力和保压时间,就如同给气球多吹点气,让它鼓起来。
注意哦,压力也不能太大,不然模具可受不了,那可就糟糕啦!
注塑过程安全不?那肯定得重视啊!就像开车一样,得时刻小心。
操作设备要规范,不然很容易出事故。
稳定性也很重要,要是一会儿好一会儿坏,那可就像坐过山车,让人心里七上八下的。
注塑的应用场景可多啦!玩具、电子产品外壳,到处都能看到注塑的身影。
为啥这么受欢迎呢?因为它生产效率高啊!就像一个高效的小蜜蜂,不停地为我们制造各种好用的东西。
而且可以做出各种复杂的形状,这多厉害呀!
我就知道一个实际案例,有个工厂生产玩具,一开始注塑总是出问
题,产品质量参差不齐。
后来经过技术人员的调整,问题解决了,生产出的玩具又漂亮又结实。
这效果,杠杠的!
注塑虽然有时候会出问题,但只要我们认真对待,找到解决方法,就能发挥它的巨大优势。
让我们一起用好注塑技术,创造更多美好的产品吧!。
注塑过程中存在的问题及解决办法

注塑过程中存在的问题及解决办法在注塑过程中,可能会出现一些问题,影响产品的质量和生产效率。
下面列举一些常见的问题及解决办法:1. 热熔物质不充分:热熔物质的充填不充分可能会导致制品的短射或缩水等问题。
解决办法是检查喂料系统,确保熔料能够充分填充模具的所有空间,同时调整熔融温度和压力以适应具体材料和模具的要求。
2. 热熔物质的脱模性差:脱模性差可能导致产品拉伸、变形、形状不完整等问题。
解决办法是优化注塑工艺参数、或改进模具设计,增加脱模剂的使用量,确保热熔物质能顺利脱模。
3. 模具磨损严重:在长时间使用后,模具可能会出现磨损,导致制品尺寸偏差增大、质量下降。
解决办法是定期检查模具状态,必要时进行维护和修复,并妥善保养模具,延长使用寿命。
4. 模内气泡和气体线:模具填充时,可能会产生气泡或气体线,这会对产品的外观和性能造成影响。
解决办法是优化注塑压力和速度,以减少气体产生;在设计模具时,合理设置通气口和冷却系统,以排除气泡。
5. 温度控制不准确:温度是影响注塑过程和产品性能的重要因素,如果温度控制不准确,可能导致产品变形、气泡、表面瑕疵等问题。
解决办法是使用高质量的注塑机和热控系统,严格控制加热和冷却时间,确保温度分布均匀。
注塑过程中存在的问题多种多样,解决办法也需因情况而异。
因此,对于每个具体问题,需要仔细分析原因并采取相应的措施,以确保最终生产出符合要求的产品。
注塑过程中存在的问题及解决办法可以从多个方面展开,下面将深入探讨一些常见的问题,并提供相应的解决办法。
1. 模具设计问题:模具是注塑过程中至关重要的部分,如果设计不合理,就会导致一系列问题。
常见的问题包括产品尺寸偏差大、表面粗糙、开裂等。
解决办法是优化模具的进料系统和冷却系统,确保充填均匀,并增加冷却时间和加热时间。
2. 注塑机参数调节不当:注塑机的温度、压力和速度等参数设置不当,会导致产品质量问题。
例如,温度过高或过低会导致材料熔化不完全或固化不充分;压力过高或过低会影响产品的密度和强度。
注塑成型常见问题和解决方案综合

射出保持壓不足
原料溫度低,流動性不足
料管溫度太低
射出速度太快
流痕
模具溫度太低
冷卻井太小
模具冷卻不適當
射嘴孔太小
Flow mark
模具設計
射出機
塑膠原料
更換材料
調整冷卻井
升高模具溫度
增加水路
成型不良對策
成型條件
增加墊料量
增加射出保持壓
延長保壓時間
增加料管溫度
升高原料溫度
減慢射出速度
流痕
加大射嘴孔
Flow mark
成型不良分析
塑膠原料
成型條件
原料中有揮發性成分
潤滑劑太多
用回收次料比例太多
用熱安定不好材料
料管內原料摩擦生熱或空氣 料管溫度太高 之絕熱壓縮引起之燃燒
冷卻環冷卻不良
原料在料管停留太久
射出速度太快
射出壓力太高
燒焦
模具內有油附著
排氣不良
澆口太小摩擦過熱分解
射嘴設計不良 (油壓封嘴)
料管太小
Burn Mark
(Torsion)。
塑膠原料
退火不適當
使用流動性 不好塑料
用流動方向成型縮收率差距大的塑料源自成型不良分析成型條件
射出速度太慢
保壓壓力未逐漸降低
射膠太飽(保壓時間太久)
料管溫度太低 模具溫度不適宜(太高; 保壓壓力太大
太低或未採用溫差)
冷卻時間不足
翹曲變形
模具冷卻不均 一或不充分
澆口位置不當
脫模方式不良
增加射嘴溫度
減少離型劑
增加料管溫度
加快射膠速度
熔接痕
增大澆口,橫澆口
更換料管
升高模具溫度
注塑中产生的问题及解决办法
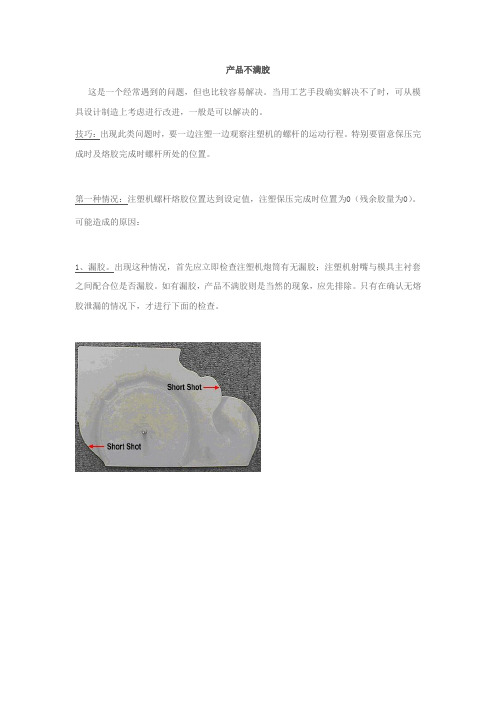
产品不满胶这是一个经常遇到的问题,但也比较容易解决。
当用工艺手段确实解决不了时,可从模具设计制造上考虑进行改进,一般是可以解决的。
技巧:出现此类问题时,要一边注塑一边观察注塑机的螺杆的运动行程。
特别要留意保压完成时及熔胶完成时螺杆所处的位置。
第一种情况:注塑机螺杆熔胶位置达到设定值,注塑保压完成时位置为0(残余胶量为0)。
可能造成的原因:1、漏胶。
出现这种情况,首先应立即检查注塑机炮筒有无漏胶;注塑机射嘴与模具主衬套之间配合位是否漏胶。
如有漏胶,产品不满胶则是当然的现象,应先排除。
只有在确认无熔胶泄漏的情况下,才进行下面的检查。
当产品不满胶,而又无胶体泄漏时,可能是胶量不够。
这时需要增加熔胶行程,增加胶量。
增加熔胶行程后要继续一边注塑一边观察螺杆残余胶量、熔胶行程及产品的进胶情况。
2、胶量不够。
增加熔胶行程后,产品进胶增加,说明胶量不够,需要继续增加熔胶行程。
当熔胶行程达到最大后,产品仍不满胶,则需要更换大型号的注塑机。
3、过胶介子漏胶。
如随着熔胶行程的增加,注塑时产品的进胶量并没有相应的增加,则可能为注塑机的过胶介子漏胶。
检查过胶介子漏胶的方法:保留某一注塑循环的产品于模腔内,改用手动射胶。
注塑压力由小变大,观察螺杆的前进量就可以判断过胶介子的漏胶情况。
手动射胶时,螺杆不前进的,说明过胶介子密封良好,不漏胶。
在较大的注塑压力下,螺杆有少许前进量,是允许的,此时不是熔胶泄漏,而是熔胶受压何种收缩所致。
凡是出现产品不满胶的情况,首先必须检查注塑机炮筒、注塑机射嘴模具间有无漏胶的情况发生;其次是检查注塑机螺杆前端的过胶介子有无漏胶。
只有排除了这两种情况后,才能进行其它方面的判定,下面的判定方法,都是建立在排除了这两种情况后的情况下,不再作累述。
第二种情况:注塑机螺杆能达到设定的熔胶行程,但达不到设定的注塑行程(有残余胶量)。
这种情况即是说:炮筒中有熔胶,但射不进模腔。
可能造成的原因:1、熔胶的流动性不够。
模具注塑常见问题及解决方法

模具注塑常见问题及解决方法模具注塑是一种常见的塑料加工方法,在生产过程中常常会遇到一些问题。
本文将针对模具注塑常见问题进行分析,并提出相应的解决方法,以帮助读者更好地应对这些问题。
一、模具注塑常见问题及解决方法1. 产品缺陷问题在模具注塑过程中,常常会出现产品缺陷问题,如翘曲、热缩、短射等。
这些问题的出现可能是由于模具设计不合理导致的,解决方法是对模具进行优化设计,确保模具的结构合理,避免产品缺陷的出现。
2. 模具磨损问题随着模具的使用,模具表面会出现磨损现象,这可能会导致产品的尺寸不准确或表面粗糙。
为了解决这个问题,可以采用定期维护模具的方法,及时清理模具表面的污垢,使用润滑剂减少磨损,并定期对模具进行研磨或更换磨损部位。
3. 模具温度控制问题在模具注塑过程中,温度的控制对产品质量至关重要。
如果温度控制不当,可能会导致产品尺寸不稳定、表面质量差等问题。
解决这个问题的方法是通过调节注塑机的温度控制系统,确保模具的温度在合适的范围内,并根据具体产品的要求进行调整。
4. 模具开裂问题模具在使用过程中可能会出现开裂的情况,这可能是由于模具材料强度不够或者受到过大的应力导致的。
解决这个问题的方法是选择合适的模具材料,并进行合理的模具结构设计,以增强模具的强度和稳定性。
5. 模具尺寸偏差问题在模具注塑过程中,由于材料的收缩和其他因素的影响,可能会导致产品尺寸与设计要求有偏差。
解决这个问题的方法是通过调整注塑工艺参数,如注塑温度、注塑压力等,来控制产品的尺寸,并根据实际情况进行模具结构的调整。
6. 模具堵塞问题在模具注塑过程中,有时会出现模具堵塞的情况,导致无法正常注塑。
解决这个问题的方法是通过清理模具内部的积聚物,如残留物、杂质等,并确保模具的通道畅通,以保证正常的注塑。
7. 模具寿命问题模具在长时间的使用过程中,可能会出现疲劳、损耗等问题,导致模具寿命减少。
为了延长模具的寿命,可以采取以下措施:定期对模具进行维护和保养,及时更换损坏的模具零件,提高模具的使用寿命。
注塑过程中常见问题及对策
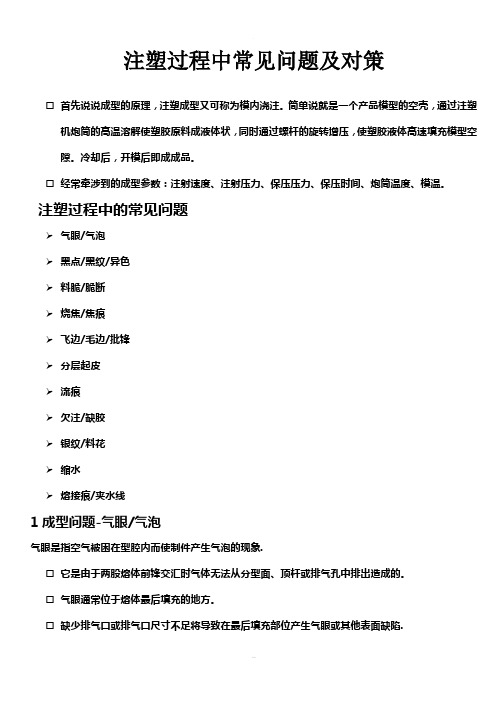
注塑过程中常见问题及对策☐首先说说成型的原理,注塑成型又可称为模内浇注。
简单说就是一个产品模型的空壳,通过注塑机炮筒的高温溶解使塑胶原料成液体状,同时通过螺杆的旋转增压,使塑胶液体高速填充模型空隙。
冷却后,开模后即成成品。
☐经常牵涉到的成型参数:注射速度、注射压力、保压压力、保压时间、炮筒温度、模温。
注塑过程中的常见问题➢气眼/气泡➢黑点/黑纹/异色➢料脆/脆断➢烧焦/焦痕➢飞边/毛边/批锋➢分层起皮➢流痕➢欠注/缺胶➢银纹/料花➢缩水➢熔接痕/夹水线1成型问题-气眼/气泡气眼是指空气被困在型腔内而使制件产生气泡的现象.☐它是由于两股熔体前锋交汇时气体无法从分型面、顶杆或排气孔中排出造成的。
☐气眼通常位于熔体最后填充的地方。
☐缺少排气口或排气口尺寸不足将导致在最后填充部位产生气眼或其他表面缺陷.☐如果制件设计薄厚不均,也非常容易造成气眼现象。
气眼可能引起的问题:☐困在型腔内气体不能被及时排出,易导致出现表面起泡,制件内部夹气,注塑不满等现象。
改进方法2成型问题-黑点/黑纹/异色黑点/黑纹/异色是指在制件表面存在黑色斑点,或是其它色泽条纹。
黑点/黑纹/异色的起因材料降解: 塑胶过热分解将导致黑点或条纹。
塑胶如果在封闭的料筒内、螺杆表面停留时间过长,将导致炭化降解,故而在注塑过程中产生黑点或条纹。
色粉分布不均或困气烧焦也会产生黑纹或异色。
材料污染: 塑胶中存在脏的回收料、异物、其他颜色的材料或易于降解的低分子材料,都可能引起上述现象。
空气中的粉尘也容易引起制件表面的黑点。
改进方法☐增加材料的热稳定性模具设计☐清洁顶杆和滑块.☐改进排气系统.☐清洁和抛光流道内的任何死角,保证不产生积料☐注塑前清洁模具表面.注塑机☐选择合适的注塑机吨位☐检查料筒内表面、螺杆表面是否刮伤积料.工艺条件☐降低料筒和喷嘴的温度.☐清洁注塑过程的各个环节.☐避免已经产生黑点/黑纹的料被重新回收利用.3成型问题-料脆/脆断制件料脆是指制件在某些部位出现容易开裂或折断。
注塑过程中的常见问题及对策

注塑过程中的常见问题及对策1.刚开机时产品跑披锋(飞边),生产一段时间后产品缺胶的原因及解决方案。
刚开机时注塑机料管内的熔胶由于加热时间长,熔胶粘度低,流动性好,产品易跑披锋,生产一段时间后由于熔胶不断把热量带走,造成熔胶不足,粘度大,流动性差,使产品缺胶。
在生产一段时间后,逐渐提高料管温度来解决。
2.在生产过程中,产品缺胶,有时增大射胶压力和速度都无效,为什么?生产一段时间后由于熔胶不断把热量带走,造成熔胶不足,粘度大,流动性差,使产品缺胶。
提高料管温度来解决。
3.产品椭圆的原因及解决方法。
产品椭圆是由于入胶不均匀,造成产品四周压力不匀,使产品椭圆,采用三点入胶,使产品入胶均匀。
4.精密产品对模具的要求。
要求模具村料钢性好,弹变形小,热涨系数小。
5.产品耐酸试验的目的。
产品耐酸试验是为了检测产品的内应力,和内应力着力点位置,以便消除产品内应力。
6.产品中金属镶件受力易开裂的原因及解决方法。
产品中放镶件,在注塑时由于热泪盈眶熔胶遇到冷镶件,会形成内应力,使产品强度下降,易开裂。
在生产时,对镶件进行预热处理。
7.模具排气点的合理性与选择方法。
模具排气点不合理,非但起不到排气效果,反而会造成产品变形或尺寸变化,所以模具排气点要合理。
选择模具排气点,应在产品最后走满胶的地方和产品困气烧的地方开排气。
8.产品易脆裂的原因及解决方法。
产品易脆裂是产品使用水口料和次料太多造成产品易脆裂,或是料在料管内停留时间过长,造成胶料老化,使产品易脆裂。
增加新料的比例,减少水口料回收使用次数,一般不能超过三次,避免胶料在料管内长时间停留。
9.加玻纤产品易出现泛纤的原因及解决方法。
是由于熔胶温度低或模具温度低,射胶压力不足,造成玻纤在胶内不能与塑料很好的结合,使泛纤出现。
加高熔料温度,模具温度,增大射胶压力。
10.进料口温度对产品的影响。
进料口温度的过高或过低,都会造成机器回料不稳定,使加料量不稳定,而影响产品的尺寸和外观。
注塑过程中常见的问题与对策

模具设计
工艺条件
Injection Molding Troubleshooting
成型问题---脱模困难 成型问题 脱模困难
脱模困难是制件生产中经常会遇到的问题,其原因和表现形式很多, 脱模困难是制件生产中经常会遇到的问题,其原因和表现形式很多, 常见的有顶白或顶出痕、顶出变形、不易顶出、断浇口等, 常见的有顶白或顶出痕、顶出变形、不易顶出、断浇口等,其产生 的原因一般有 模具粗糙或倒陷 脱模斜度不足 过充模 不合适的顶杆 顶杆位置顶出 冷却时间不足 材料问题
产生原因 •物料黏度高 •注塑和模具温度过低 •注塑压力太小 •排气困难 •流道或者浇口过小
Injection Molding Troubleshooting
改进方法
材料 •提高材料流动性 提高材料流动性 •合理设置排气槽 合理设置排气槽 •增加浇口、流道尺寸 增加浇口、 增加浇口 •设置足够大的冷料井 设置足够大的冷料井 •抛光流道 抛光流道 •提高料筒和模具温度 提高料筒和模具温度 •增加注射速度 增加注射速度 •增加注塑压力 增加注塑压力
Injection Molding Troubleshooting
黑点/黑纹案例 黑点 黑纹案例
Injection Molding Troubleshooting
改进方法
材料 •采用无污染的原材料 采用无污染的原材料 •提高材料的热稳定性 提高材料的热稳定性 •改善排气系统 改善排气系统 •清洁和抛光模具表面及流道,防止死角积料 清洁和抛光模具表面及流道, 清洁和抛光模具表面及流道 •选择合适大小的注塑机 选择合适大小的注塑机 •清洁注塑机筒和螺杆,确保无损伤及积料 清洁注塑机筒和螺杆, 清洁注塑机筒和螺杆 •降低料筒温度 降低料筒温度 •避免污染和已降解物料的回用 避免污染和已降解物料的回用
注塑常见问题汇总及解决对策方法汇总

注塑常见问题及解决对策方法汇总1. 刚开机时产品跑披锋,生产一段时间后产品缺胶的原因及解决方案。
刚开机时注塑机料管内的熔胶由于加热时间长,熔胶粘度低,流动性好,产品易跑披锋,生产一段时间后由于熔胶不断把热量带走,造成熔胶不足,粘度大,流动性差,使产品缺胶。
在生产一段时间后,逐渐提高料管温度来解决。
2. 在生产过程中,产品缺胶,有时增大射胶压力和速度都无效,为什么?解决方法?是因为生产中熔胶不断把热量带走,造成熔胶不足,胶粘度大,流动性差,使产品缺胶。
提高料管温度来解决。
3. 产品椭圆的原因及解决方法。
产品椭圆是由于入胶不均匀,造成产品四周压力不匀,使产品椭圆,采用三点入胶,使产品入胶均匀。
4. 精密产品对模具的要求。
要求模具材料刚性好,弹变形小,热涨性系数小。
5. 产品耐酸试验的目的产品耐酸试验是为了检测产品内应力,和内应力着力点位置,以便消除产品内应力。
6. 产品中金属镶件受力易开裂的原因及解决方法。
产品中放镶件,在啤塑时由于热熔胶遇到冷镶件,会形成内应力,使产品强度下降,易开裂。
在生产时,对镶件进行预热处理。
7. 模具排气点的合理性与选择方法。
模具排气点不合理,非但起不到排气效果,反而会造成产品变形或尺寸变化,所以模具排气点要合理。
选择模具排气点,应在产品最后走满胶的地方和产品困气烧的地方开排气。
8. 产品易脆裂的原因及解决方法。
产品易脆裂是产品使用水口料和次料太多造成产品易脆裂,或是料在料管内停留时间过长,造成胶料老化,使产品易脆裂。
增加新料的比例,减少水口料回收使用次数,一般不能超过三次,避免胶料在料管内长时间停留。
9. 加玻纤产品易出现泛纤的原因及解决方法是由于熔胶温度低或模具温度低,射胶压力不足,造成玻纤在胶内不能与塑胶很好的结合,使纤泛出。
加高熔胶温度,模具温度,增大射胶压力。
10. 进料口温度对产品的影响。
进料口温度的过高或过低,都会造成机器回料不稳定,使加料量不稳定,而影响产品的尺寸和外观。
吹膜常出现问题及原因及解决方法

4、对准中心线
5、减小夹板夹角
6、调整牵引辊
7、调节摩擦力大小
六
拉不上牵引
1、机头温度过高或过低
2、单边厚薄相差太大
1、调整机温度
2、调整单边厚薄
吹膜机常见故障解决排除方法
序号
不正常现象
产生原因
解决办法
一
泡管歪斜
1、机身、口膜温度过高
2、边接器温度过高
3、薄膜厚度不均匀
1、降低机身温度、口膜温度
2、适当降低边接器温度
3、调节薄膜厚度
二
有点白或胶粒
1、原料中有杂质
2、过滤网破裂
3、颗粒混料不均匀
1、原料过筛
2、调换过滤网
3、严格控制捏和、膜温度过低
2、螺杆转速太快
3、螺杆温度过高或过低
4、聚乙烯配方不合理(铅盐稳定剂过多或耐寒塑剂过多)
1、适当升高机身和口膜温度
2、适当降低转速
3、调整螺杆冷却介质流量
4、改进配方
四
薄膜厚度不均匀
1、机头设计不合理
2、芯棒偏中变形
3、机头四周温度不均匀
4、吹胀比太大
5、冷却不均匀
6、压缩空气不稳定
1、修正改进机头工艺参数
2、调换芯棒
3、检查机头加热器
4、改小吹胀比
5、调节冷却介质流量
6、检修压缩泵
五
皱折
1、机头安装不平
2、薄膜厚度不均匀
3、冷却不够或者不均匀
4、夹板或牵引辊与机头中心未对准
5、夹板夹角太大
6、牵引辊的松紧不一致
7、卷取张力不恒定
1、校正机头水平度
2、调整薄膜厚度
吹膜常出现问题及原因及解决方法

吹膜常出现问题及原因及解决方法
吹膜机常见故障解决排除方法
不正常现象产生原因解决办法序号泡管歪斜一二有点白或胶粒1、机身、口膜温度1、降低机身温度、过高口膜温度2、边接器温度过高2、适当降低边接器温度3、薄膜厚度不均匀3、调节薄膜厚度1、原料中有杂质1、原料过筛2、过滤网破裂2、调换过滤网3、颗粒混料不均匀3、严格控制捏和、造料工艺薄膜表面发花1、机身或口膜温度1、适当升高机身和过低口膜温度2、螺杆转速太快2、适当降低转速三3、螺杆温度过高或3、调整螺杆冷却介过低质流量4、聚乙烯配方不合4、改进配方理(铅盐稳定剂过多或耐寒塑剂过多)1、机头设计不合理1、修正改进机头工艺参数2、芯棒偏中变形2、调换芯棒3、机头四周温度不均匀3、检查机头加热器4、吹胀比太大5、冷却不均匀5、调节冷却介质流量6、压缩空气不稳定6、检修压缩泵4、改小吹胀比四薄膜厚度不均匀五皱折1、机头安装不平1、校正机头水平度2、薄膜厚度不均匀2、调整薄膜厚度3、冷却不够或者不3、调整冷却装置或均匀降低线速度4、夹板或牵引辊与4、对准中心线机头中心未对准5、减小夹板夹角5、夹板夹角太大6、调整牵引辊6、牵引辊的松紧不7、调节摩擦力大小一致7、卷取张力不恒定1、机头温度过高或1、调整机温度过低2、调整单边厚薄2、单边厚薄相差太大六拉不上牵引。