FANUC 系统常见术语
FANUC系统常用指令

FANUC系统常⽤指令⼀、FANUC 系统常⽤指令1、快速定位指令G002、直线插补指令G013、圆弧插补指令G02、G03该指令使⼑具从圆弧起点沿圆弧移动到圆弧终点。
4、主轴速度设置指令和转速控制指令G96、G97、G50。
(1)主轴线速度恒定指令G96 格式:G96 S ;S 单位为m/min。
此时应限制主轴最⾼转速,即⽤G50 指令。
如:G50 S1500;主轴最⾼转速限制为1500r/min。
(2)直接设定主轴转速指令G97。
格式:G97 S ;S 的单位为r/min(注:⼀般系统G97)G96、G97 均为模态指令,可相互取消。
5、每转进给指令G99 和每分钟进给指令G98。
格式:G99 F ;F 单位为mm/rG98 F ;F 单位为mm/min G98、G99 均为模态指令,机床初始状态默认G99。
6、螺纹车削加⼯(可加⼯直螺纹和锥螺纹)⽅式有直进式和斜进式(1)螺纹切削指令G32,可车削直螺纹、锥螺纹和端⾯螺纹。
G32 指令进⼑⽅式为直进式。
注:螺纹切削时不可⽤主轴线速度恒定指令G96。
格式:G32 X Z F ;其中:X Z 为螺纹终点坐标,F 为螺距。
螺纹深度计算:h=0.6495p 螺纹⼩径:d1=d-h×27、⼑具功能指令T 格式:T 02 02 T:为⼑具02:⼑具号00-99 02:⼑具补偿号00-99 注;(1)⼑具号可与转位⼑架上的⼑具号相对应。
(2)⼑具补偿包括形状补偿和磨损补偿。
(3)为了⽅便,⼑具号和⼑具补偿号通常是⼀致的。
(4)⼑具号为0 或00 时,取消⼑具;⼑具补偿号为0或00 时,相当于取消补偿。
例:T0或T00、T0200。
8、辅助功能指令M M00—程序停⽌M01—选择停⽌M02—程序停⽌M03、M04、M05—主轴正、反、停转M08—切削液开M09—切削液关M30—程序结束并返回M98—⼦程序调⽤M99—⼦程序调⽤返回(⼦程序结束)⼆、固定循环指令为了简化程序,数控装置可以⽤⼀个程序段指定⼑具作反复切削,这就是固定循环指令。
fanuc功能指令

FANUC 系统功能的介绍点击数:79 发布时间:来源:中华工具网1、控制轨迹数(Controlled Path)CNC控制的进给伺服轴(进给)的组数。
加工时每组形成一条刀具轨迹,各组可单独运动,也可同时协调运动。
2、控制轴数(Controlled Axes)CNC控制的进给伺服轴总数/每一轨迹。
3、联动控制轴数(Simultaneously Controlled Axes)每一轨迹同时插补的进给伺服轴数。
4、PMC控制轴(Axis control by PMC)由PMC(可编程机床控制器)控制的进给伺服轴。
控制指令编在PMC的程序(梯形图)中,因此修改不便,故这种方法通常只用于移动量固定的进给轴控制。
5、Cf轴控制(Cf Axis Control)(T系列)车床系统中,主轴的回转位置(转角)控制和其它进给轴一样由进给伺服电动机实现。
该轴与其它进给轴联动进行插补,加工任意曲线。
6、Cs轮廓控制(Cs contouring control)(T系列)车床系统中,主轴的回转位置(转角)控制不是用进给伺服电动机而由FANUC主轴电动机实现。
主轴的位置(角度)由装于主轴(不是主轴电动机)上的高分辨率编码器检测,此时主轴是作为进给伺服轴工作,运动速度为:度/分,并可与其它进给轴一起插补,加工出轮廓曲线。
7、回转轴控制(Rotary axis control)将进给轴设定为回转轴作角度位置控制。
回转一周的角度,可用参数设为任意值。
FANUC 系统通常只是基本轴以外的进给轴才能设为回转轴。
8、控制轴脱开(Controlled Axis Detach)指定某一进给伺服轴脱离CNC的控制而无系统报警。
通常用于转台控制,机床不用转台时执行该功能将转台电动机的插头拔下,卸掉转台。
9、伺服关断(Servo Off)用PMC信号将进给伺服轴的电源关断,使其脱离CNC的控制用手可以自由移动,但是CNC仍然实时地监视该轴的实际位置。
机床程序英语学习(FANUC)
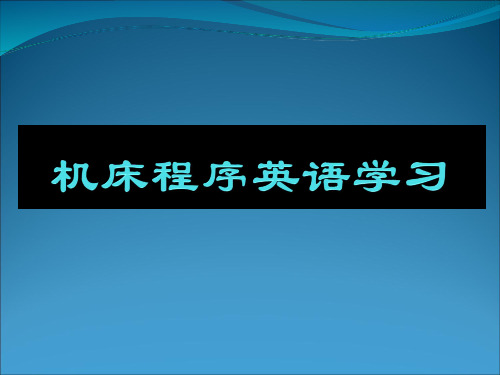
overload超负荷,超载
字母W
W[w] Workpiece工件 Ow[偶] [au] Low低 blow吹 tower转塔 ew[u:] screw 螺杆,卷屑器
down向下
up向上
字母X
X[ks] axis ex-jig外部治具 ex=external外部的 index cycle start SW 循环启动开关
字母P
p[p]、[b] Operation操作 speed速度 workpiece工件 Position位置 Program程序 Optional stop
字母Q
Q[阔] Quality质量 Q[K] torque 扭力,扭矩
字母R
r[r] Reset重设,复位
ready准备
字母R
or/er[儿] Sensor近接开关,传感器,感应器 Tr[tr] trip=skip跳脱 Dr[dr] Dry run模拟运转 Hydraulic 液压
后鼻音[n] Tank水槽 coolant tank切削水槽
复习要点-2
detect=check autodoor SP=spindle delay Overload Index hydraulic reset REF=reference Power broken finish emergency stop feedrate delete Release=unclamp REF=reference tool life LSW=limit SW fault=error forward reverse single block program Origin high高 low低 though穿过 though coolant LED holder Chip conveyor Thread cut timer=TR counter override jig jog feed
FANUC数控知识简介

FAM BC 数控知识一、操作和相关注意事项1、空运转、加工中出现故障或者其他一些异常情况的处理,在操作之前,先查看机床内主轴、工件和刀具的位置,保证安全。
2、开机、空运转及其他开关加工门的操作,必要时都先走一次回零程序。
3、了解机床常用的变量,主要是#500之后的一些变量,便于查看设备的状态。
4、在设备故障时,不要急于Reset,留意当前的程序段,坐标位置以及程序的模态代码。
此处应注意,故障时NC标示的程序段,不一定是运行出错的程序段,因为NC有预读的功能,出错的程序段可能是预读结束但尚未运行的程序。
必要时,根据模态代码、坐标位置和工件的实际情况,判断加工状态。
5、一般情况下,不允许修改主程序中的坐标位置,主程序是依据工艺编制,修改后与工艺要求不符。
在程序修改时,要谨慎小心,要先记下当前的程序或参数,然后再修改、核对,避免手误或出错。
6、由于三坐标测量的坐标系,与机床加工的坐标系,在方向上可能是不一致的,所以依据三坐标报告调整NC程序的时候,主要是关注实际尺寸与理论尺寸的偏差,不能完全根据测量报告的正负,确定坐标调整的方向。
7、熟悉设备的夹紧定位,加工基准和加工内容的代号。
8、在更换光栅或调整夹具后,如果尺寸超差,通常要先调整机床精度或者机床参数设置,然后再考虑程序调整;如果是更换主轴,要根据实际情况来定。
通常,超差大于20-30丝,优先考虑调整设备。
9、对于新员工,正常加工生产的时候,强调注意主轴转速和进给倍率的位置,同时加工过程中,避免操作“Reset”按钮。
二、NC培训1、CNC功能框图CNC数控机床由以下几部分组成:加工程序、输入/输出设备、CNC装置、可编程控制器(PLC)、主轴驱动装置、进给驱动装置和机床。
其中,CNC主要控制主轴和进给轴的运动,包括基本移动、程序暂停、平面选择、坐标设定、刀具补偿、基准点返回和固定循环等;PLC主要用于辅助功能的控制,包括主轴起停、主轴转向、切削液的开关或刀库的起停等。
FANUC数控车床基本知识

FANUC数控车床基本知识学习目标:当完成本单元学习之后,就能够熟悉FANUC 0I MATE-TB数控车床数控系统基本知识,与机床操作面板各按键的名称与功能。
有关学习单元——《数控系统基本性能》——《机床操作面板按键》——《G指令代码》——《M指令代码》一、数控系统基本性能:二、机床操作面板按键1.功能键:POS—位置画面 PROG—程序画面OFFSET—刀具偏置 SYSTEM—系统画面MESSAGE—信息画面 GRAPH—图形画面 CUSTOM—用户宏画面2.编辑键:SHIFT—上档键 INSERT—输入键(程序输入)INPUT—输入键(参数输入) CAN—取消键ALTER—修改键(替换) DELETE—删除HELP—帮助键 RESET—复位键PAGE—上翻页键 PAUP—下翻页—地址/ 数字键←↑→↓—光标移动XC3.操作键盘功能按键:编辑方式(在此方式下可进行程序的输入、删除、修改等)手动数据输入方式(执行MDI程序运行)存储程序自动方式(自动运行程序加工操作按键)手动进给方式(手动运行操作按键)手摇脉冲方式(脉冲手轮进给运行按键返回参考点方式(每天上、下班机床务必返参考点) X轴手摇脉冲进给(X向脉冲进给配合手轮使用)Z轴手摇脉冲进给(Z向脉冲进给配合手轮使用)手摇脉冲最小单位0,001MM/G00速度F0手摇脉冲单位0,01MM/G00速度倍率25%手摇脉冲单位0,1MM/G00速度倍率50%G00速度倍率100%X轴参考点指示(灯亮X轴返回参考点)Z轴参考点指示(灯亮Z轴返回参考点)单程序段(按程序段执行加工程序通常用于首件加工)任选程序段跳过(程序中有程序跳跃符使用该键才有效)空运转(使用该键可快速校验程序)机床锁住(程序校验时机床锁住而程序在运行)X轴负向点动(刀具运行速度由进给倍率操纵)X轴正向点动(刀具运行速度由进给倍率操纵)Z轴负向点动(刀具运行速度由进给倍率操纵)Z轴正向点动(刀具运行速度由进给倍率操纵)手动快速(刀具运行速度由G00进给倍率操纵)程序选择停(程序中有M01指令使用该键才有效)手动选刀(手动状态下按次键可任选刀号致加工位置)手动冷却液开闭(按下此键可随时打开、关闭冷却液)手动润滑开闭(按下此键可随时润滑机床)卡盘卡紧松开(适用于液压机床设备)台尾前进后退(适用于液压机床设备)液压启动停止(适用于液压机床设备)手动主轴正转(正转换反转一定先主轴停)手动主轴反转(正转换反转一定先主轴停)手动主轴点动手动主轴停手动主轴升速(主轴速度提升可在屏幕中观察到)手动主轴降速(主轴速度下降屏幕中观察到)(左)主轴速度档位显示;(右)当前刀号4.操作面板按钮:数控系统上电(上电后不要马上进行操作)数控系统断电(断电后不要马上上电)循环启动(程序运行加工的启动按键)进给保持(运行中有问题按下此键)进给倍率开关(修调程序中F值及点动进给)急停按钮(关闭所有的运行及操作)三、G指令代码:代码组别功能★G00 01 速定位G01 01 直线插补G02 01 圆弧插补(顺圆)G03 01 圆弧插补(逆圆)G04 00 暂停★G18 16 ZX平面选择G20 06 英制输入★G21 06 公制输入G27 00 参考点返回检查G28 00 参考点返回G30 00 第二参考点返回G32 01 螺纹切削★G40 07 刀尖半径补偿取消G41 07 刀尖半径左补偿G42 07 刀尖半径右补偿G50 00 坐标系设定/主轴限速设定G70 00 精加工循环G71 00 外圆粗车循环G72 00 端面粗车循环G73 00 封闭切削循环G74 00 端面深孔加工循环G75 00 外圆、内圆切槽循环G76 00 螺纹切削复合循环G90 01 横向固定循环切削G92 01 螺纹固定循环切削G94 01 端面固定循环切削G96 02 恒线速操纵★G97 02 恒线速撤消G98 05 每分钟进给四、M指令代码:代码功能代码功能M00 程序无条件停止M10 卡盘松开M01 程序条件停止M11 卡盘卡紧M02 程序结束M30 程序结束反头M03 主轴正转M40 主轴空挡M04 主轴反转M41主轴Ⅰ档(22~246)M05 主轴停止M42主轴Ⅱ档(66~725)M08 冷却液开M43主轴Ⅲ档(203~2200)M09 冷却液关M44 主轴Ⅳ档M98 调用子程序M99 子程序返回注意及技巧:1.程序中遇M00指令主轴不停程序停止运行,不须与操作键盘按纽配合使用。
FANUC指令
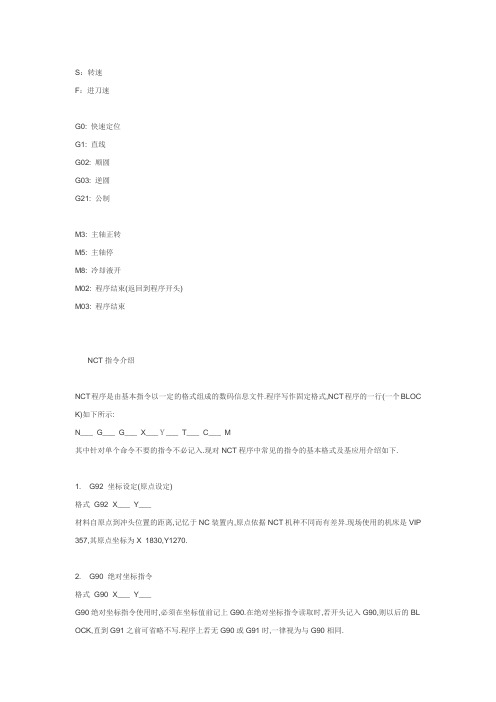
S:转速F:进刀速G0: 快速定位G1: 直线G02: 顺圆G03: 逆圆G21: 公制M3: 主轴正转M5: 主轴停M8: 冷却液开M02: 程序结束(返回到程序开头)M03: 程序结束NCT指令介绍NCT程序是由基本指令以一定的格式组成的数码信息文件.程序写作固定格式,NCT程序的一行(一个BLOC K)如下所示:N___ G___ G___ X___Y___ T___ C___ M其中针对单个命令不要的指令不必记入.现对NCT程序中常见的指令的基本格式及基应用介绍如下.1. G92 坐标设定(原点设定)格式 G92 X___ Y___材料自原点到冲头位置的距离,记忆于NC装置内,原点依据NCT机种不同而有差异.现场使用的机床是VIP 357,其原点坐标为X 1830,Y1270.2. G90 绝对坐标指令格式 G90 X___ Y___G90绝对坐标指令使用时,必须在坐标值前记上G90.在绝对坐标指令读取时,若开头记入G90,则以后的BL OCK,直到G91之前可省略不写.程序上若无G90或G91时,一律视为与G90相同.3. G91 相对坐标指令G91指令指定的坐标不是从原点算起,而是自前一个孔位算起的增加值,使用此指令时必须在坐标值前记入G91.相对坐标指令读取时,最初以G91记入,以后的BLOCK一直到G90出现之前,G91均可省略不写.4. G50 回归原点指令使用G50指令,材料依G92指定的位置回归的同时,回复到NC初期状态,程序最后必须作G50单一行之输入.5. G70 不冲孔指令格式 G70 X___ Y___材料仅位移,不冲孔.G70与G90或G91可以同时使用,且位置先后不影响其指定.G70的指令只在所属BL OCK内有效.例:G90 X100.00 Y100.00 (有冲孔)G70 G91 X200.00 (无冲孔)G90 Y300.00 (有冲孔)6. G27?G25 自动移爪格式 G27(或G25) X___(移动量)G27?G25指令是用来换板及加工范围不够宽时所使用的换板功能.通常使用G27,当材料在夹爪夹住的边上有突出不平等的情形时,则使用G25.7. G04 暂停(滞留状态)格式 G04 X___ (时间)在轴移动时,作预定时间内暂停的机能8. G72 模式基准点指令格式 G72 X___ Y___欲使用模式基准点时,坐标值之前要加上G72.l G72与G90或G91同时使用,且那一个先写都相同l G72仅有指示坐标的作用,而无决定位置或实行冲孔的动作.l G72的下一行必需是实行冲孔的指令.l 与G72在同一行内不可存在M?T等功能的指令.9. T指令定义刀具T为三位数字所组成,用来指令所使用模具的STATION,位于X?Y的位置之后.若为相同之模具继续使用时,一直到另一模具使用前,不须再另行指定模具.10. C指令设置刀具角度C指令位于X?Y(位置)与T(使用模具)之指令之后.自动转角可于±360°的范围内指定,同角度的加工时,C指令为必重复指定.11. G26 BLOT HOLE CIRCLE (BHC)以现在的位置或G72指定的位置为中心,在半径为r的圆周上,与X轴夹θ角的点开始,将圆周分成n等分,作n个点的冲孔指令.格式 G26 I r J±θ K n T___ (C___ )I=圆的半径r.输入正值J=冲孔起始点与X轴之夹±θ.反时针方向为正(+),顺时针方向为负(-)K=冲孔个数,反时针方向加工为正(+),顺时针方向为负(-)12. G28 LINE AT ANGLE (LAA)以现在的位置或G72指令的位置算起,与X轴夹θ角的方向,间隔d的距离,冲n个孔的指令.格式 G28 I d J±θ K n T___ (C___ )I=间隔±d.d为负时,以模式基准点作为中心,于对称方向冲孔J=角度±θ,反时针方向为正(+),顺时针方向为负(-)K=冲孔个数n.不包括模式基准点13. G29 圆弧 (ARC)以现在的位置或G72所指定的基准点为中心,半径为r的圆周上,与X轴夹角为θ的开始点,角度间隔Δθ,排列n个点的冲孔指令.格式 G28 I r J±θP±Δθ K n T___ (C___ )I=圆的半径r,为正数J=最初冲孔起始点,角度±θ,反时针方向为正(+),顺时针方向为负(-)P=角度间隔为±Δθ,为正时,以反时针方向冲孔,为负时,以顺时针方向冲孔K=冲孔的个数14. G36?G37 格状孔此模式从G72指定的位置开始,X轴方向以d1为间隔.做n个,Y轴方向以d2为间隔,做n2个格子状冲孔的指令.G36是以X轴方向为优先加工指令,G37是以Y轴方向为优先加工指令,考虑到板料在运动中的稳定性,一般选用G36.格式 G36 I±d1 P n1 J±d2 K n2 T___ (C___ )G37 I±d1 P n1 J±d2 K n2 T___ (C___ )I=间隔±d1,正(+)时为X轴方向,负(-)时为-X方向取间隔P=X轴方向的冲孔数n1(不含基准点)J=间隔±d2,正(+)时为Y轴方向,负(-)时为-Y方向取间隔K=Y轴方向的冲孔数n2(不含基准点)15. G66 切边 (SHP)此模式是由G72所指定之基准点开始,在与X轴夹角为θ°的方向上,以W1×W2之模具,作长度为±d的连续冲孔指令.格式 G66 I e J±θ P±W1 Q±W2 D±d T___I=连续冲孔加工之长度eJ=角度±θ.反时针为(+)时针为(-)P=模具边长±W1(J方向的模具尺寸)Q=模具边±W2(与J成90°方向的模具尺寸)W1与W2必需同号,若W1=W2时Q可省略不写.D=对加工长度作补正之值±d(d=0时,D项可省略)l D若为负时连续冲也的长度比I短少2倍D的长,为正时则比I长2 倍D.l 连续冲孔的长度I,至少需为P(W1)之1.5倍以上方可.16. G67 矩形 (SQR)此模式是由G72所指定的基准点开始,平行X轴方向长度e1,Y轴方向长e2的矩形,以长W1W2的模具连续冲孔的指令.格式 G67 I±e1 J±e2 P W1 Q W2 T___I=X轴方向冲孔长度±e1.正为X方向.负为X轴负方向J=Y轴方向冲孔长度±e1.正为Y方向.负为Y轴负方向P=X方向模具长度W1,为正值Q=Y方向模具长度W2,为正值.若W1=W2时,Q可省略因通常使用正方形模,帮Q不使用.17. G68 蚕食圆弧 (NBL-A)此模式是以G72所指定的基准点为中心,半径为r的圆周上,与X轴夹角为θ1的点开始,增加θ2的角度,以直径为ψ的模具,间隔为d来作蚕食加工之指令.格式 G68 I r J±θ1K±θ2P±ψ Q d T___I=圆的半径r,输入正值(但I<5700mm)J=加工起始点自X轴算起之角度±θ1,反时针方向为正,顺时针方向为负K=蚕食加工的角度±θ2,(+)时为逆时针加工,(-)时为顺时针加工P=模具直径±ψ,正时在圆的外侧加工,负时在圆的内侧加工Q=蚕食的间隔为d,输入正数(最大d值为8mm)l 板厚3.2mm以上场合,或是间隔超过8mm时,以G78代替G68使用之.l 蚕食所使用之模具,必须小于所蚕食之圆的半径.18. G69 I e J±θP±ψ Q d T___此模式是从G72指定的基准点开始,与X轴成θ角方向,长度e,以直径ψ模具,间隔d来蚕食的加工模式. 格式 G69 I e J±θP±ψ Q d T___I=蚕食执行的长度,为模式起点至模式终点的长度J=角度±θ,反时针为正,顺时针为负P=模具直径±ψ,正时加工方向在直线之左侧,负时加工于直线右侧Q=蚕食间隔d,正值输入,最大值为8mm19. G78 冲孔圆弧 (PNC-A)此模式是以G72所指定之基准点为中心,半径为r的圆周上,与X轴夹角为θ1的点开始,增加θ2之角度,以直径ψ的模具,间隔为d来作蚕食加工之指令.格式 G78 I r J±θ1K±θ2P±ψ Q d D t T___I=圆的半径r.输入正值J=加工起始点自X轴算起之角度±θ1.反时针方向为正,顺时针方向为负K=蚕食加工的角度±θ2.(+)时逆时针加工,(-)时顺时针加工P=模具直径±ψ.(+)时在圆的外侧加工,(-)时在圆的内侧加工Q=蚕食的间隔为dD=使用板厚t,(d≧t)20. G79 冲孔长圆 (PNC-L)此模式是从G72指令的基准点开始,与X轴成θ1角方向,长度e,直径ψ的模具,间隔d来蚕食的加工模式. 格式 G79 I e J±θ1P±ψ Q d D t T____I=蚕食执行的长度,为模式起点至模式终点的长度J=角度±θ1,反时针为正,顺时针为负P=模具直径±ψ.正时加工方向在直线之左侧,负时加工于直线右侧Q=蚕食间隔dD=使用板厚t.(d≧t)21. G98 多数取的基准点与排列间隔之设定多数取加工时,制品对于材料作何种排列的指令格式 G98 Xx0 Yy0 Ixp Jyp Pnx Knyx0……排列在左下方制品的左下角点的X坐标y0……排列在左下方制品的左下角点的Y坐标xp……X方向上制品排列的间隔yp……Y方向上制品排列的间隔nx……X方向上排列的间隔数ny……Y方向上排列的间隔数22. G75 76 多数取执行指令除多数取程序外,UOO~VOO为止,为一个制品的子程序,此编号的MACRO对应WOO,根据G98所设定之排列,令材料全部执行的指令.格式 G75 W___ Q___ ……以X方向为优先级执行G76 W___ Q ___……以Y方向为优先级执行W=为MACRO编号,与程序中的UOO~VOO对应Q=为加工开始的角落.Q1—左下角;Q2—右下角;Q3—左上角;Q4—右上角23. MACRO机能(U)MACRO记忆机能,UOO与VOO为程序中数个BLOCK之记忆OO则为不限次数之记忆呼出时使用,这时U 所对应读取之数值,需为相同格式 UOO...VOOWOO注:一个U…V对应一个W.U~V之间不可有M02M03及50之指令存在.24. M13 加工结束指令加工结束之后单一行输入25. M510~M559 冲凸台形强筋前之指令.在冲凸台形强筋前单一行输入.指令可在M510~M559中任选一个,但在同一程序中,不同模具前不能用同一M指令.26. M560~M563 打标记沙拉孔前之指令在打标记沙拉孔前单一行输入,可在M560~M505中任选一个,但在同一程序中,不同的模具前不能使用同一M指令.27. M502~M505 冲敲落孔前之指令在冲敲落孔前单一行输入,可在M502~M505中任选一个,但在同一程序中不同模具前不能使用同一M指令.。
FANUC数控系统常用英语专用术语
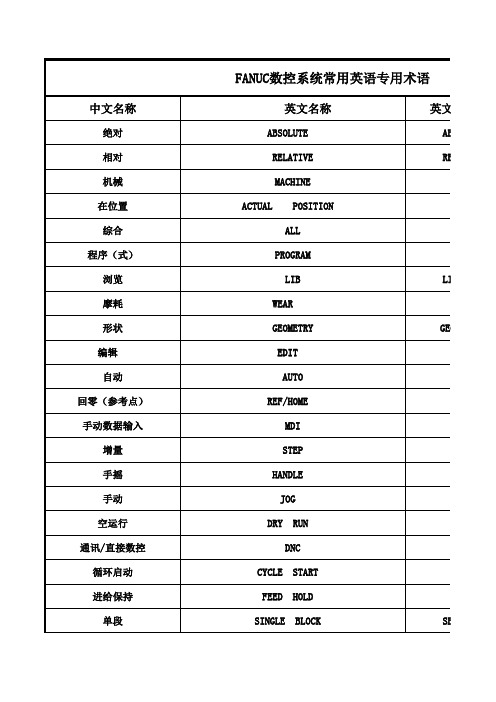
中文名称
绝对 相对 机械 在位置 综合 程序(式) 浏览 摩耗 形状 编辑 自动 回零(参考点) 手动数据输入 增量 手摇 手动 空运行 通讯/直接数控 循环启动 进给保持 单段
英文名称
ABSOLUTE RELATIVE MACHINE ACTUAL POSITION ALL PROGRAM LIB WEAR GEOMETRY EDIT AUTO REF/HOME MDI STEP HANDLE JOG DRY RUN DNC CYCLE START FEED HOLD SINGLE BLOCK
术语
英文简写
ABS REL
图形符号
LIB
GEOM
SBK
CW
CCW
பைடு நூலகம்
PRGRM
英文简写
ABS REL
LIB
GEOM
SBK
程序跳段 任选暂停 主轴正转 主轴停 主轴反转 位置 程序 刀具偏置 参数诊断 报警显示 图形显示 启动输入 启动输出 复位 替换 插入 删除 急停 手动进给修调 移动距离
BLOCK SKIP OPTION STOP SPIHDL CW SPIHDL STOP SPIHDL CCW POS PROGRRM MEHU OFSET DGHOS PARAM OPR ALARM AUX GRAPH INPUT OUTPUT START RESET ALTER INSERT DELET EMERGENCY STOP JOG FEEDRATE OVERRIDE DISTANCE TO GO PRGRM CCW CW
FANUC系统参数资料

FANUC系统参数资料FANUC系统参数是指FANUC数控机床控制系统中的一种关键设置参数。
在FANUC系统中,有大量的系统参数可以进行配置和调整。
这些参数一般可以通过特定的输入方式进行修改,如MDI(手动数据输入)方式或专用的参数设置界面。
FANUC系统参数主要分为基本参数和扩展参数两个部分。
基本参数是FANUC系统中最基础、最重要的一类参数,它们对机床的基本运动、位置、速度等进行定义和配置。
扩展参数是在基本参数的基础上,提供了一些更加细微和专业的功能,如分段加工控制、插补算法、轴线性补偿等。
在FANUC系统参数中,常见的基本参数包括:1.通用参数:包括机床型号、进给轴个数、主轴个数等基本信息。
2.机床坐标系参数:用于定义机床坐标系的原点、旋转中心点等。
3.进给轴参数:用于配置进给轴的运动速度、加减速度、保持速度等。
4.主轴参数:用于配置主轴的转速范围、最大功率、刹车开关等。
5.轴线性补偿参数:用于配置轴线性补偿的相关信息,如基准坐标、最大补偿量等。
扩展参数中的常见配置包括:1.插补控制参数:用于配置插补控制算法的精度、速度、加减速度等相关信息。
2.分段加工控制参数:用于配置分段加工控制的相关信息,如每段时间、每段距离等。
3.坐标转换参数:用于配置坐标系转换、切换的相关信息,如工件坐标系、手动坐标系等。
4.工具偏置参数:用于配置工具偏置的相关信息,如刀长补偿、半径补偿等。
5.外部输入/输出参数:用于配置输入和输出信号的规范、通道、配置信息等。
FANUC系统参数的修改和配置一般需要特定的权限和操作方法。
在修改参数时,需要仔细阅读相关的文档和操作手册,确保了解参数的含义和影响范围。
同时,在修改之前,最好备份原有的参数设置,以防止错误操作导致机床无法正常运行。
总之,FANUC系统参数是数控机床控制系统中非常重要的配置信息。
通过对参数的调整和配置,可以实现机床的不同运动、加工方式和功能需求。
因此,熟悉并了解FANUC系统参数资料是每个数控操作和编程人员都应该掌握的基本知识。
(完整版)FANUC系统编程
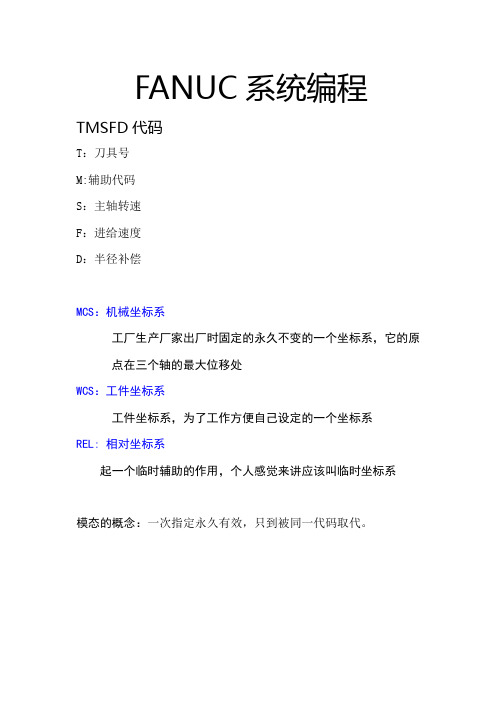
FANUC系统编程TMSFD代码T:刀具号M:辅助代码S:主轴转速F:进给速度D:半径补偿MCS:机械坐标系工厂生产厂家出厂时固定的永久不变的一个坐标系,它的原点在三个轴的最大位移处WCS:工件坐标系工件坐标系,为了工作方便自己设定的一个坐标系REL: 相对坐标系起一个临时辅助的作用,个人感觉来讲应该叫临时坐标系模态的概念:一次指定永久有效,只到被同一代码取代。
常用的M代码:M0:程序停止M1:程序选择性停止M2:程序结束M3:主轴正转M4:主轴反转M5:主轴停止M6:刀具交换M8:切削液开启M9:切削液关闭M30:程序结束返回开头M98:调用子程序M99:子程序结束G代码注:不同组的G代码写在同一行同时生效,同一组的G代码写一在同一行最后的一个生效G17 G18 G19:平面选择指令平面指令平面第一轴/平面第二轴平面第三轴G17 X/Y ZG18 Z/X YG19 Y/Z X注:平面第三轴的正方向往该平面看,顺时针为正转,逆时针为反转G0:快速定位格式:G17 G0 X_ Y_以快速定位的方式到达G17平面的X Y 位置。
G0不需要指定速度,是系统预设好的。
G1:直线切削运动G43:刀具长度补偿(对刀长)G0 Z0 G43 H1(指定刀具补偿号为1号刀补,并快速定位到Z0位置)G94 G95:进给方式格式1:G17 G94 G1 X_ Y_ F100在G17平面以mm/分钟的速度直线切削到XY坐标位置。
G94是以 mm/分钟的速度进给(分钟进给)格式2:G17 G94 G1 X_ Y_ F0.5G95是以 mm/转为单位,也就是说刀具转一圈往前走多少毫米。
通常情况下用G94比较多,很少用G95G90:绝对坐标G91:增量坐标绝对坐标是相对于原点来确定位置的A(40,40) B(40,60) C(30,60)…………增量坐标是第二个点是相对于第一个点来确定的,也就是说第二个点是第一个点的坐标增量G90 A(40,40) G91 B(0,20) C(-10,0) D(10,30)…………G0 G1小练习M6 T1; 换1号刀G17 G54 G90; 指定平面、工件坐标,以绝对编程的方式G0 X40 Y40; 到工件起始坐标点准备下刀Z100 G43 H1; 刀具抬到Z100的位置M3 S600; 主轴正转,转速600M8; 开冷却液G0 Z2; 靠近工件Z2位置G1 Z-2 F20; 刀具下刀深2mm 速度20 开始刀削Y60;X30;X40 Y90;X80;X90 Y60;X80;Y40;X40;G0 Z100; 抬刀到100的位置M9; 关冷却液M5; 主轴停转M30; 程序结束并返回程序开头G2 G3 :圆弧指令G2:顺时针圆弧 G3:逆时针圆弧格式1:(终点+半径)G17 G2/G3 X_ Y_ R_ F_G18 G2/G3 X_ Y_ R_ F_G19 G2/G3 X_ Y_ R_ F_G17 G18 G19 为平面选择,X Y 是圆弧终点坐标,R是圆弧半径,F是进给速度。
发那科(FANUC)数控系统使用小贴士16:报警分类
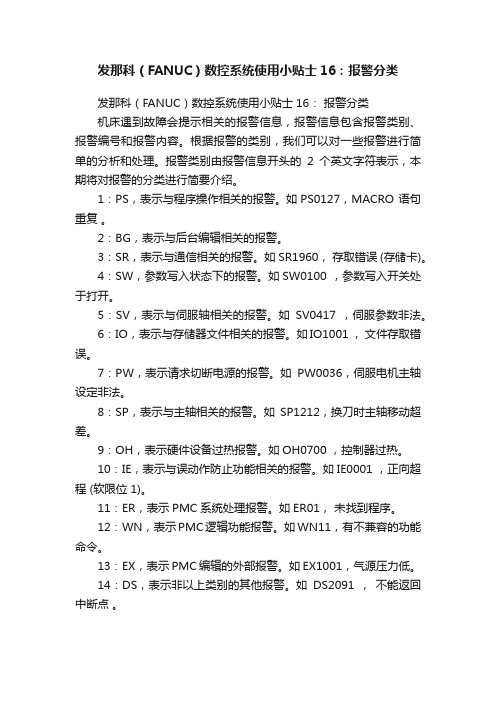
发那科(FANUC)数控系统使用小贴士16:报警分类发那科(FANUC)数控系统使用小贴士16:报警分类机床遇到故障会提示相关的报警信息,报警信息包含报警类别、报警编号和报警内容。
根据报警的类别,我们可以对一些报警进行简单的分析和处理。
报警类别由报警信息开头的2个英文字符表示,本期将对报警的分类进行简要介绍。
1:PS,表示与程序操作相关的报警。
如PS0127,MACRO 语句重复。
2:BG,表示与后台编辑相关的报警。
3:SR,表示与通信相关的报警。
如SR1960,存取错误 (存储卡)。
4:SW,参数写入状态下的报警。
如SW0100 ,参数写入开关处于打开。
5:SV,表示与伺服轴相关的报警。
如SV0417 ,伺服参数非法。
6:IO,表示与存储器文件相关的报警。
如IO1001 ,文件存取错误。
7:PW,表示请求切断电源的报警。
如PW0036,伺服电机主轴设定非法。
8:SP,表示与主轴相关的报警。
如SP1212,换刀时主轴移动超差。
9:OH,表示硬件设备过热报警。
如OH0700 ,控制器过热。
10:IE,表示与误动作防止功能相关的报警。
如IE0001 ,正向超程 (软限位 1)。
11:ER,表示PMC系统处理报警。
如ER01,未找到程序。
12:WN,表示PMC逻辑功能报警。
如WN11,有不兼容的功能命令。
13:EX,表示PMC编辑的外部报警。
如EX1001,气源压力低。
14:DS,表示非以上类别的其他报警。
如DS2091 ,不能返回中断点。
fanuc常用参数

fanuc常用参数Fanuc是一种集成电路,常用于数控机床的控制系统中,其参数的设置对于机床的运转和加工结果具有至关重要的作用。
下面将介绍Fanuc开发的一些常用参数及其相关的参考内容。
1. R参数R参数是Fanuc控制系统用来调整切削进给速度的一个参数。
由于每种材料的切削性质不同,因此需要根据不同的加工材料进行调整。
参考内容:根据不同的材料,可以设置不同的R数值。
一般来说,对于黄铜、铝合金等比较软的材料,需要设置较大的R 值,以保证刀具不会因为进给速度过快而被磨损。
而对于硬质合金等材料,则需要设置较小的R值,以保证刀具进给速度的稳定性。
2. F参数F参数用于控制主轴的进给速度。
在加工过程中,需要根据不同的加工要求和切削条件进行设置。
参考内容:根据不同的加工要求,可以在G代码中设置不同的F值。
一般来说,加工大型工件时需要较低的进给速度,而加工小型工件时则可以适当提高进给速度。
在切削条件较差的情况下,也需要适当降低进给速度以保障切削质量。
3. G参数G参数是Fanuc控制系统所使用的语言。
在进行加工操作时,需要编写G代码,用来控制机床的各项操作,包括切削进给、主轴转速等。
参考内容:在编写G代码时,需要根据具体的加工步骤和要求来设置相应的G参数。
比如,在进给过程中,需要设置G01,表示线性进给。
在顺时针或逆时针旋转时,需要分别使用G02和G03命令。
4. P参数P参数通常用来进行辅助功能的设置,比如刀具长度补偿、孔加工、线割等。
参考内容:在使用P参数时,需要根据不同的功能进行设置。
比如刀具长度补偿,可以使用P值来控制刀具头到工件表面的距离,以保证切削的准确性。
5. T参数T参数通常用来设置刀具的切削参数。
在进行不同的切削操作时,需要使用不同的刀具,并设置相应的刀具参数。
参考内容:在进行刀具的切削参数设置时,需要考虑到切削条件、材料、刀具类型等因素。
不同的切削操作需要使用不同的刀具,并设定相应的刀具编号。
FANUC所有系统参数

FANUC所有系统参数1.轴参数:FANUC系统可以控制多个轴,每个轴都有自己的参数。
这些参数包括轴的最大速度、加速度和减速度,轴的分辨率和精度等。
通过调整这些参数,可以改变轴的运动性能,以适应不同的加工需求。
2.切削参数:切削参数用于控制刀具的运动。
这些参数包括切削速度、进给速度和进给量等。
通过调整这些参数,可以控制切削过程中刀具的运动轨迹和速度,从而实现不同的加工效果。
3.进给参数:进给参数用于控制工件在加工过程中的运动。
这些参数包括进给速度、进给量和加速度等。
通过调整这些参数,可以控制工件在加工过程中的运动轨迹和速度,以实现不同的加工需求。
4.插补参数:插补参数用于控制多个轴之间的相互作用。
这些参数包括插补速度、加速度和减速度等。
通过调整这些参数,可以控制轴之间的协调运动,以实现复杂的加工过程。
5.程序参数:程序参数用于控制加工程序的执行。
这些参数包括程序起始位置、程序停止位置和程序执行速度等。
通过调整这些参数,可以控制加工程序的执行过程,以实现不同的加工目标。
6.通信参数:通信参数用于控制FANUC系统与外部设备之间的通信。
这些参数包括通信速度、通信协议和通信地址等。
通过调整这些参数,可以实现FANUC系统与其他设备的数据交换。
7.报警参数:报警参数用于控制系统报警功能的设置。
这些参数包括报警等级、报警条件和报警响应方式等。
通过调整这些参数,可以根据实际需要设置系统的报警功能。
8.系统参数:系统参数用于控制FANUC系统的整体性能和功能。
这些参数包括系统的最大速度、加速度和减速度,系统的分辨率和精度等。
通过调整这些参数,可以提高系统的运行速度和精度,以满足不同的生产需求。
总之,FANUC系统具有多个不同的参数,通过调整这些参数,可以实现不同的机械加工和自动化生产需求。
不同的参数组合可以产生不同的加工效果,提高生产效率和产品质量。
FANUC编程手册

第一节 编程常用术语简介数控机床是一种综合应用了计算机技术、自动控制技术、精密测量技术和机械设计等先进技术的典型机电一体化产品,1.插补:加工时刀具沿构成工件形状的直线和圆弧移动刀具沿直线和圆弧移动的功能称为插补功能。
2.进给功能为切削工件,刀具以指定速度移动称为进给。
指定进给速度的功能称为进给功能G94是模态代码,一旦G94被指定,在G95(每转进给)指定前它将一直保持有效。
在电源接通时,设置为每分进给方式。
3.参考点一台数控机床设定一个特定位置。
通常,在这个位置进行换刀和设定编程的绝对零点。
这个位置称为参考位置(点)。
4.工件坐标系,零件图纸上的工件坐标系和CNC 系统指定的工件坐标系。
为了正确地把工件加工成图纸指定的形状,两个坐标系必须设在同一位置。
5. 机床坐标系固定于机床上,以机床零点为基准的笛卡尔坐标系。
6. 绝对值指令指令刀具移动到“距坐标系零点某一距离”的点,即刀具移动到坐标值的位置。
7. 增量值指令指令刀具从前一个位置移动到下一个位置的位移量。
8.切削速度切削工件时刀具相对于工件的速度称为切削速度。
9.刀具功能给每把刀具赋给一个编号,在程序中指令不同的编号时,就选择相应的刀具。
当把某一把刀具放在ATC的某号位时,通过指令Txx可以选择这把刀具。
该功能称为刀具功能10.辅助功能指令机床部件的启停操作的功能称为辅助功能。
11. 程序暂停程序段的所有命令执行完后,删除主轴功能和其他功能,并终止其后的数据处理的辅助功能.12. 准备功能使机床或控制系统建立加工功能方式的命令.13.程序结构为运行机床而送到CNC的一组指令称为程序。
按照指定的指令,刀具沿着直线或圆弧移动,主轴电机按照指令旋转或停止。
一组单步的顺序指令称为程序段。
程序是由一系列加工的单组程序段组成的。
用于区分每个程序段的号码称为顺序号,用于区分每个程序的号码称为程序号。
程序段和程序的结构如下所示。
14.主程序和子程序当在程序中多次出现相同的加工模式时,可把这个模式编成一个程序。
fanucpmc中文注释
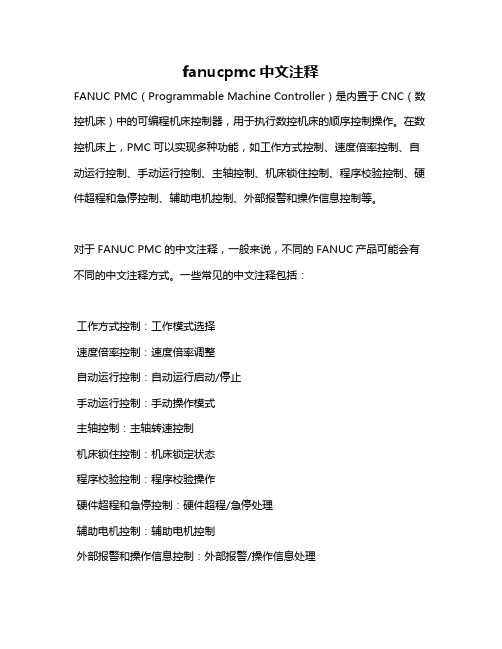
fanucpmc中文注释
FANUC PMC(Programmable Machine Controller)是内置于CNC(数控机床)中的可编程机床控制器,用于执行数控机床的顺序控制操作。
在数控机床上,PMC可以实现多种功能,如工作方式控制、速度倍率控制、自动运行控制、手动运行控制、主轴控制、机床锁住控制、程序校验控制、硬件超程和急停控制、辅助电机控制、外部报警和操作信息控制等。
对于FANUC PMC的中文注释,一般来说,不同的FANUC产品可能会有不同的中文注释方式。
一些常见的中文注释包括:
工作方式控制:工作模式选择
速度倍率控制:速度倍率调整
自动运行控制:自动运行启动/停止
手动运行控制:手动操作模式
主轴控制:主轴转速控制
机床锁住控制:机床锁定状态
程序校验控制:程序校验操作
硬件超程和急停控制:硬件超程/急停处理
辅助电机控制:辅助电机控制
外部报警和操作信息控制:外部报警/操作信息处理
这些注释仅为常见用法,具体的中文注释还需要根据具体的FANUC产品手册或技术文档来确定。
如果您需要更准确的中文注释,建议您查阅FANUC 官方文档或与FANUC技术支持联系以获取更准确的信息。
FANUC系统PMC基础知识介绍

FANUC系统PMC基础知识介绍【PMC的基本配置】【PMC的相关地址】【地址符号和信号的种类】【PMC信号】· X:来自机床侧的输入信号。
如接近开关、极限开关、压力开关、操作按钮等输入信号元件。
PMC 接收从机床侧各装置的输入信号,在梯形图中进行逻辑运算,作为机床动作的条件及对外围设备进行诊断的依据。
· Y:由PMC 输出到机床侧的信号。
在PMC 控制程序中,根据机床设计的要求,输出信号控制机床侧的电磁阀、接触器、信号灯等动作,满足机床运行的需要。
· F:由控制伺服电机与主轴电机的系统部分侧输入到PMC 信号。
系统部分就是将伺服电机和主轴电机的状态,以及请求相关机床动作的信号(如移动中信号、位置检测信号、系统准备完成信号等),反馈到PMC 中去进行逻辑运算,作为机床动作的条件及进行自诊断的依据。
· G:由PMC 侧输出到系统部分的信号。
对系统部分进行控制和信息反馈(如轴互锁信号、M代码执行完毕信号等)。
· R\E:内部继电器R、扩展继电器E。
在顺序程序执行处理中使用于运算结果的暂时存储的地址。
内部继电器的地址包含有PMC 的系统软件所使用的预留区,预留区的信号不能在顺序程序中写入。
· A:信息显示的信号地址。
顺序程序所使用的指令中,备有在CNC画面上进行信息显示的指令( DISPB )· 非易失性存储器地址:定时器( T )、计数器( C )、保持型继电器( K )、数据表( D ) 在断电时要保持其中的值。
这4 个叫做PMC 参数。
PMC信号与地址· 地址G 和F 信号,由CNC 控制软件决定其地址。
· 机械和PMC 之间的接口信号X 和Y 地址是由机床厂家设计人员分配的。
· 急停(*ESP)和跳转信号等,由于受PMC 扫描时间的影响使处理缓慢,因此由CNC 直接进行读取。
这些输入信号的X 地址是确定的。
FANUC 常用文字码及其含义
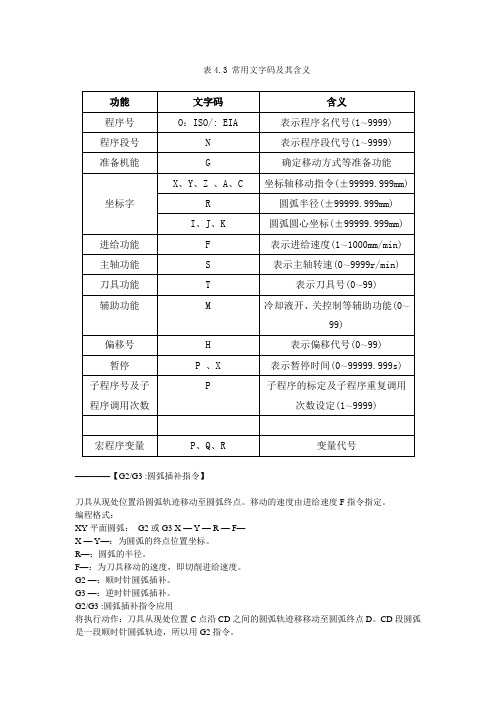
表4.3 常用文字码及其含义————【G2/G3 :圆弧插补指令】刀具从现处位置沿圆弧轨迹移动至圆弧终点。
移动的速度由进给速度F指令指定。
编程格式:XY平面圆弧:G2或G3 X — Y — R — F—X — Y—:为圆弧的终点位置坐标。
R—:圆弧的半径。
F—:为刀具移动的速度,即切削进给速度。
G2 —:顺时针圆弧插补。
G3 —:逆时针圆弧插补。
G2/G3 :圆弧插补指令应用将执行动作:刀具从现处位置C点沿CD之间的圆弧轨迹移移动至圆弧终点D。
CD段圆弧是一段顺时针圆弧轨迹,所以用G2指令。
加工程序:绝对坐标编程:N80 G90 G2 X63.0 Y20.0 R23.0相对坐标编程:N80 G91 G2 X23.0 Y-23.0 R23.0 F100平面的选择:数控系统一般可以加工XY、XZ、YZ平面的圆弧。
G17:该指令表示选择XY平面,在此平面中进行圆弧插补和刀具补偿。
此代码为系统初始代码。
电源一接通G17 就作为平面选择的起始代码而自动生效。
G18:该指令表示选择XZ平面,在此平面中进行圆弧插补和刀具补偿。
G19:该指令表示选择YZ平面,在此平面中进行圆弧插补和刀具补偿。
选择性单节删除:”/”在单节的最前端加一斜线"/"(选择性单节删除指令)时,该单节是否被执行,是由执行操作面板上的选择性单节删除开关来决定。
当此开关处于"ON"(灯亮),则该单节会被忽略而不被执行;当此开关处于 "OFF" (灯熄),则该单节会被执行。
所以程序中有"/"指令之单节可由操作者视情况选择该单节是否被执行。
例子:N1;=>粗铣外形:/M00;N2;=>粗铣凹槽:/M00;N3;=>精铣外形:/M00;N4;=>精铣凹槽以上例子,当单节删除开关处于"ON"时,则所有的M00(程序停止指令)皆不被执行。
反之设于 "OFF" ,则全部执行。
- 1、下载文档前请自行甄别文档内容的完整性,平台不提供额外的编辑、内容补充、找答案等附加服务。
- 2、"仅部分预览"的文档,不可在线预览部分如存在完整性等问题,可反馈申请退款(可完整预览的文档不适用该条件!)。
- 3、如文档侵犯您的权益,请联系客服反馈,我们会尽快为您处理(人工客服工作时间:9:00-18:30)。
FANUC 系统常见术语1、控制轨迹数(Controlled Path):CNC控制的进给伺服轴(进给)的组数。
加工时每组形成一条刀具轨迹,各组可单独运动,也可同时协调运动。
2、控制轴数(Controlled Axes):CNC控制的进给伺服轴总数/每一轨迹。
3、联动控制轴数(Simultaneously Controlled Axes):每一轨迹同时插补的进给伺服轴数。
4、PMC控制轴(Axis control by PMC):由PMC(可编程机床控制器)控制的进给伺服轴。
控制指令编在PMC的程序(梯形图)中,因此修改不便,故这种方法通常只用于移动量固定的进给轴控制。
5、Cf轴控制(Cf Axis Control)(T系列):车床系统中,主轴的回转位置(转角)控制和其它进给轴一样由进给伺服电动机实现。
该轴与其它进给轴联动进行插补,加工任意曲线。
6、Cs轮廓控制(Cs contouring control)(T系列):车床系统中,主轴的回转位置(转角)控制不是用进给伺服电动机而由FANUC主轴电动机实现。
主轴的位置(角度)由装于主轴(不是主轴电动机)上的高分辨率编码器检测,此时主轴是作为进给伺服轴工作,运动速度为:度/分,并可与其它进给轴一起插补,加工出轮廓曲线。
7、回转轴控制(Rotary axis control):将进给轴设定为回转轴作角度位置控制。
回转一周的角度,可用参数设为任意值。
FANUC系统通常只是基本轴以外的进给轴才能设为回转轴。
8、控制轴脱开(Controlled Axis Detach):指定某一进给伺服轴脱离CNC的控制而无系统报警。
通常用于转台控制,机床不用转台时执行该功能将转台电动机的插头拔下,卸掉转台。
9、伺服关断(Servo Off):用PMC信号将进给伺服轴的电源关断,使其脱离CNC的控制用手可以自由移动,但是CNC仍然实时地监视该轴的实际位置。
该功能可用于在CNC机床上用机械手轮控制工作台的移动,或工作台、转台被机械夹紧时以避免进给电动机发生过流。
10、位置跟踪(Follow-up):当伺服关断、急停或伺服报警时若工作台发生机械位置移动,在CNC的位置误差寄存器中就会有位置误差。
位置跟踪功能就是修改CNC控制器监测的机床位置,使位置误差寄存器中的误差变为零。
当然,是否执行位置跟踪应该根据实际控制的需要而定。
11、增量编码器(Increment pulse coder):回转式(角度)位置测量元件,装于电动机轴或滚珠丝杠上,回转时发出等间隔脉冲表示位移量。
由于码盘上没有零点,故不能表示机床的位置。
只有在机床回零,建立了机床坐标系的零点后,才能表示出工作台或刀具的位置。
使用时应该注意的是,增量编码器的信号输出有两种方式:串行和并行。
CNC单元与此对应有串行接口和并行接口。
12、绝对值编码器(Absolute pulse coder):回转式(角度)位置测量元件,用途与增量编码器相同,不同点是这种编码器的码盘上有绝对零点,该点作为脉冲的计数基准。
因此计数值既可以映位移量,也可以实时地反映机床的实际位置。
另外,关机后机床的位置也不会丢失,开机后不用回零点,即可立即投入加工运行。
与增量编码器一样,使用时应注意脉冲信号的串行输出与并行输出,以便与CNC单元的接口相配。
(早期的CNC系统无串行口。
)13、FSSB(FANUC 串行伺服总线):FANUC 串行伺服总线(FANUC Serial ServoBus)是CNC单元与伺服放大器间的信号高速传输总线,使用一条光缆可以传递4—8个轴的控制信号,因此,为了区分各个轴,必须设定有关参数。
14、简易同步控制(Simple synchronous control):两个进给轴一个是主动轴,另一个是从动轴,主动轴接收CNC的运动指令,从动轴跟随主动轴运动,从而实现两个轴的同步移动。
CNC随时监视两个轴的移动位置,但是并不对两者的误差进行补偿,如果两轴的移动位置超过参数的设定值,CNC即发出报警,同时停止各轴的运动。
该功能用于大工作台的双轴驱动。
15、双驱动控制(Tandem control):对于大工作台,一个电动机的力矩不足以驱动时,可以用两个电动机,这就是本功能的含义。
两个轴中一个是主动轴,另一个为从动轴。
主动轴接收CNC的控制指令,从动轴增加驱动力矩。
16、同步控制(Synchrohouus control)(T系列的双迹系统):双轨迹的车床系统,可以实现一个轨迹的两个轴的同步,也可以实现两个轨迹的两个轴的同步。
同步控制方法与上述“简易同步控制”相同。
17、混合控制(Composite control)(T系列的双迹系统):双轨迹的车床系统,可以实现两个轨迹的轴移动指令的互换,即第一轨迹的程序可以控制第二轨迹的轴运动;第二轨迹的程序可以控制第一轨迹的轴运动。
18、重叠控制(Superimposed control)(T系列的双迹系统):双轨迹的车床系统,可以实现两个轨迹的轴移动指令同时执行。
与同步控制的不同点是:同步控制中只能给主动轴送运动指令,而重叠控制既可给主动轴送指令,也可给从动轴送指令。
从动轴的移动量为本身的移动量与主动轴的移动量之和。
19、B轴控制(B-Axis control)(T系列):B轴是车床系统的基本轴(X,Z)以外增加的一个独立轴,用于车削中心。
其上装有动力主轴,因此可以实现钻孔、镗孔或与基本轴同时工作实现复杂零件的加工。
20、卡盘/尾架的屏障(Chuck/Tailstock Barrier)(T系列):该功能是在CNC 的显示屏上有一设定画面,操作员根据卡盘和尾架的形状设定一个刀具禁入区,以防止刀尖与卡盘和尾架碰撞。
21、刀架碰撞检查(Tool post interference check)(T系列):双迹车床系统中,当用两个刀架加工一个工件时,为避免两个刀架的碰撞可以使用该功能。
其原理是用参数设定两刀架的最小距离,加工中时时进行检查。
在发生碰撞之前停止刀架的进给。
22、异常负载检测(Abnormal load detection):机械碰撞、刀具磨损或断裂会对伺服电动机及主轴电动机造成大的负载力矩,可能会损害电动机及驱动器。
该功能就是监测电动机的负载力矩,当超过参数的设定值时提前使电动机停止并反转退回。
23、手轮中断(Manual handle interruption):在自动运行期间摇动手轮,可以增加运动轴的移动距离。
用于行程或尺寸的修正。
24、手动干预及返回(Manual intervention and return):在自动运行期间,用进给暂停使进给轴停止,然后用手动将该轴移动到某一位置做一些必要的操作(如换刀),操作结束后按下自动加工启动按钮即可返回原来的坐标位置。
25、手动绝对值开/关(Manual absolute ON/OFF):该功能用来决定在自动运行时,进给暂停后用手动移动的坐标值是否加到自动运行的当前位置值上。
26、手摇轮同步进给(Handle synchronous feed):在自动运行时,刀具的进给速度不是由加工程序指定的速度,而是与手摇脉冲发生器的转动速度同步。
27、手动方式数字指令(Manual numeric command):CNC系统设计了专用的MDI画面,通过该画面用MDI键盘输入运动指令(G00,G01等)和坐标轴的移动量,由JOG(手动连续)进给方式执行这些指令。
28、主轴串行输出/主轴模拟输出(Spindle serial output/Spindle analog output):主轴控制有两种接口:一种是按串行方式传送数据(CNC给主轴电动机的指令)的接口称为串行输出;另一种是输出模拟电压量做为主轴电动机指令的接口。
前一种必须使用FANUC的主轴驱动单元和电动机,后一种用模拟量控制的主轴驱动单元(如变频器)和电动机。
29、主轴定位(Spindle positioning)(T系统):这是车床主轴的一种工作方式(位置控制方式),用FANUC主轴电动机和装在主轴上的位置编码器实现固定角度间隔的圆周上的定位或主轴任意角度的定位。
30、主轴定向(Orientation):为了执行主轴定位或者换刀,必须将机床主轴在回转的圆周方向定位与于某一转角上,作为动作的基准点。
CNC的这一功能就称为主轴定向。
FANUC系统提供了以下3种方法:用位置编码器定向、用磁性传感器定向、用外部一转信号(如接近开关)定向。
31、Cs轴轮廓控制(Cs Contour control):Cs轮廓控制是将车床的主轴控制变为位置控制实现主轴按回转角度的定位,并可与其它进给轴插补以加工出形状复杂的工件。
Cs轴控制必须使用FANUC的串行主轴电动机,在主轴上要安装高分辨率的脉冲编码器,因此,用Cs轴进行主轴的定位要比上述的主轴定位精度要高。
32、多主轴控制(Multi-spindle control):CNC除了控制第一个主轴外,还可以控制其它的主轴,最多可控制4个(取决于系统),通常是两个串行主轴和一个模拟主轴。
主轴的控制命令S由PMC(梯形图)确定。
33、刚性攻丝(Rigid tapping):攻丝操作不使用浮动卡头而是由主轴的回转与攻丝进给轴的同步运行实现。
主轴回转一转,攻丝轴的进给量等于丝锥的螺距,这样可提高精度和效率。
欲实现刚性攻丝,主轴上必须装有位置编码器(通常是1024脉冲/每转),并要求编制相应的梯形图,设定有关的系统参数。
铣床,车床(车削中心)都可实现刚性攻丝。
但车床不能像铣床一样实现反攻丝。
34、主轴同步控制(Spindle synchronous control):该功能可实现两个主轴(串行)的同步运行,除速度同步回转外,还可实现回转相位的同步。
利用相位同步,在车床上可用两个主轴夹持一个形状不规则的工件。
根据CNC系统的不同,可实现一个轨迹内的两个主轴的同步,也可实现两个轨迹中的两个主轴的同步。
接受CNC指令的主轴称为主主轴,跟随主主轴同步回转的称为从主轴。
35、主轴简易同步控制(Simple spindle synchronous control):两个串行主轴同步运行,接受CNC指令的主轴为主主轴,跟随主主轴运转的为从主轴。
两个主轴可同时以相同转速回转,可同时进行刚性攻丝、定位或Cs轴轮廓插补等操作。
与上述的主轴同步不同,简易主轴同步不能保证两个主轴的同步化。
进入简易同步状态由PMC信号控制,因此必须在PMC程序中编制相应的控制语句。
36、主轴输出的切换(Spindle output switch)(T):这是主轴驱动器的控制功能,使用特殊的主轴电动机,这种电动机的定子有两个绕组:高速绕组和低速绕组,用该功能切换两个绕组,以实现宽的恒功率调速范围。