圆螺母规格
圆螺母尺寸规格一览
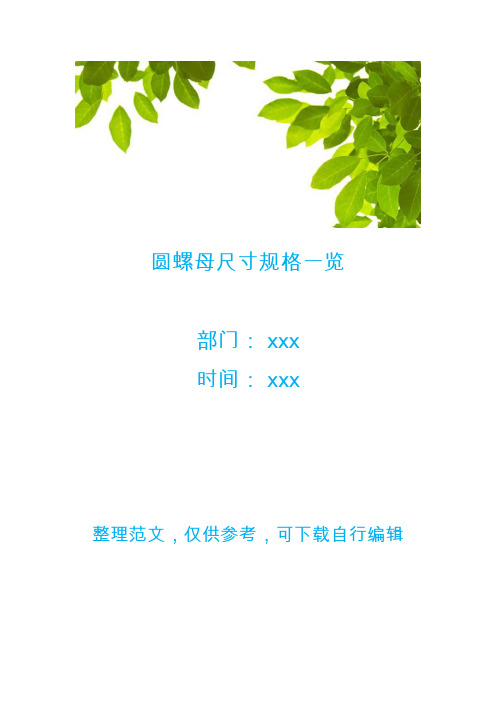
圆螺母尺寸规格一览
部门: xxx
时间: xxx
整理范文,仅供参考,可下载自行编辑
圆螺母尺寸规格一览
圆螺母尺寸是其使用最标准的参考,包括圆螺母的螺纹规格、公称直径等信息,因此不少朋友都十分关注圆螺母尺寸。
下面,世界工厂泵阀网为大家汇总圆螺母尺寸规格一览,以供查询参考。
圆螺母尺寸解读:
1.槽数n: 当D≤100×2时,n = 4。
D≥M102×2时,n = 6。
2.标有“*”的规格仅用于滚动轴承锁紧装置。
3.材料:45
4.标记示例:螺纹规格D=M16×1.5,材料为45钢,槽或全部热处理硬度HRC35~45, 表面氧化的圆螺母:螺母 GB812-88
M16×1.5b5E2RGbCAP
圆螺母尺寸规格表如下:
申明:
所有资料为本人收集整理,仅限个人学习使用,勿做商业用途。
GB812 圆螺母开槽圆螺母 圆形精密锁紧螺母
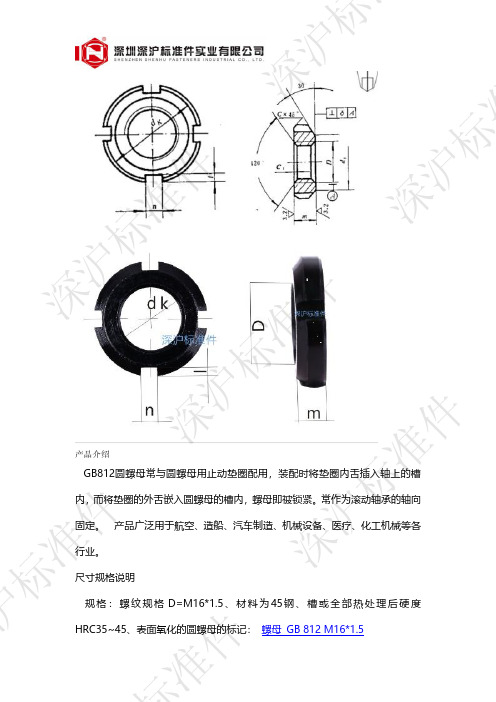
产品介绍
GB812圆螺母常与圆螺母用止动垫圈配用,装配时将垫圈内舌插入轴上的槽内,而将垫圈的外舌嵌入圆螺母的槽内,螺母即被锁紧。
常作为滚动轴承的轴向
固定。
产品广泛用于航空、造船、汽车制造、机械设备、医疗、化工机械等各行业。
尺寸规格说明
规格:螺纹规格D=M16*1.5、材料为45钢、槽或全部热处理后硬度HRC35~45、表面氧化的圆螺母的标记:深沪标准件
沪
标
准
件
件
深沪标准件深
沪标准件深
沪
标
深
材料参数
沪
标
准
件
标准件
深
沪标准件深
沪
标
深
螺丝攻牙钻孔对照表
深沪
标
准
沪
标
准
件
件
深
标
深
沪
标
准件
沪标
准
件
件
深沪标准件
深沪标准件
深沪标深。
圆螺母国标代号

圆螺母国标代号圆螺母是一种常用的紧固件,广泛应用于机械设备、汽车、航空航天等领域。
圆螺母的国标代号是GB/T 6187-2000。
该国标规定了圆螺母的尺寸、材质、力学性能等技术要求,确保螺母的质量和使用性能。
在GB/T 6187-2000中,圆螺母按照螺纹尺寸、螺距和螺纹制作方法进行了分类。
其中,螺纹尺寸和螺距的分类决定了螺母的名称和尺寸标记,而螺纹制作方法决定了螺母的制作工艺和表面处理要求。
1. 螺纹尺寸和螺距的分类根据GB/T 6187-2000,圆螺母的螺纹尺寸和螺距分为以下几类:- M1.6-M39: 这类螺母适用于常规机械设备和一般紧固件,广泛使用。
- M39-M64: 这类螺母适用于大型机械设备和重型紧固件,强度和耐久性要求较高。
- M64-M100: 这类螺母适用于特殊机械设备和大型工程结构紧固件,承载能力要求很高。
对于每个螺纹尺寸和螺距,国标还规定了螺母的尺寸和标记。
例如,M6的螺母的外径为10mm,高度为5mm,标记为M6×1。
2. 螺纹制作方法的分类根据GB/T 6187-2000,圆螺母的螺纹制作方法分为以下几类:- 等大螺纹:这种螺纹的加工方法适用于生产大批量螺母,成本低廉。
- 车削螺纹:这种螺纹的加工方法适用于生产小批量螺母,加工精度高。
- 冷镦螺纹:这种螺纹制作方法适用于生产大量、直径较小的螺母,成本低廉。
国标还规定了螺母的材质和力学性能要求,确保了螺母的机械性能和耐久性。
例如,螺母的材质可以是碳钢、合金钢等,在使用过程中应具有一定的抗拉强度和抗腐蚀性能。
除了尺寸、材质和力学性能要求,国标还规定了螺母的表面处理要求,如镀层、磷化等。
这些表面处理措施可以提高螺母的防腐性能和美观度。
总之,GB/T 6187-2000通过对圆螺母的尺寸、材质、力学性能和表面处理要求的规定,确保了圆螺母的质量和使用性能。
使用该标准的螺母能够满足不同领域的紧固需求,并确保机械设备、汽车、航空航天等领域的安全和可靠性。
[宝典]常用圆螺母规格
![[宝典]常用圆螺母规格](https://img.taocdn.com/s3/m/215c76c6541810a6f524ccbff121dd36a32dc42f.png)
[宝典]常用圆螺母规格规格型号(螺操作纹规格dk d1 m h(最小) t(最小) C C1 每1000个的质量/kg? 参考价位D×P)M10×1 22 16 8 4 2 0.5 0.5 16.82 暂无M100×2 135 122 18 12 5 1.5 1 873.3 暂无M105×2 140 127 18 12 5 1.5 1 895 暂无M110×2 150 135 18 14 6 1.5 1 1076 暂无M115×2 155 140 22 14 6 1.5 1 1369 暂无M12×1.25 25 19 8 4 2 0.5 0.5 21.58 暂无M120×2 160 145 22 14 6 1.5 1 1423 暂无M125×2 165 150 22 14 6 1.5 1 1477 暂无M130×2 170 155 22 14 6 1.5 1 1531 暂无M14×1.5 28 20 8 4 2 0.5 0.5 26.82 暂无M140×2 180 165 26 14 6 1.5 1 1937 暂无M150×2 200 180 26 16 7 1.5 1 2651 暂无M16×1.5 30 22 8 5 2.5 0.5 0.5 28.44 暂无M160×3 210 190 26 16 7 2 1.5 2810 暂无M170×3 220 200 26 16 7 2 1.5 2970 暂无M18×1.5 32 24 8 5 2.5 0.5 0.5 31.19 暂无M180×3 230 210 30 16 7 2 1.5 3610 暂无M190×3 240 220 30 16 7 2 1.5 3794 暂无M20×1.5 35 27 8 5 2.5 0.5 0.5 37.31 暂无M200×3 250 230 30 16 7 2 1.5 3978 暂无M22×1.5 38 30 10 5 2.5 0.5 0.5 54.91 暂无M24×1.5 42 34 10 5 2.5 1 0.5 68.88 暂无M25×1.5? 42 34 10 5 2.5 1 0.5 65.88 暂无M27×1.5 45 37 10 5 2.5 1 0.5 75.49 暂无M30×1.5 48 40 10 5 2.5 1 0.5 82.11 暂无M33×1.5 52 43 10 6 3 1 0.5 92.32 暂无M35×1.5? 52 43 10 6 3 1 0.5 84.99 暂无M36×1.5 55 46 10 6 3 1.5 0.5 100.3 暂无M39×1.5 58 49 10 6 3 1.5 0.5 107.3 暂无M40×1.5? 58 49 10 6 3 1.5 0.5 102.5 暂无M42×1.5 62 53 10 6 3 1.5 0.5 121.8 暂无M45×1.5 68 59 10 6 3 1.5 .0.5 153.6 暂无M48×1.5 72 61 12 8 3.5 1.5 0.5 201.2 暂无M50×1.5 72 61 12 8 3.5 1.5 0.5 186.8 暂无M52×1.5 78 67 12 8 3.5 1.5 0.5 238 暂无M55×2 78 67 12 8 3.5 1.5 0.5 214.4 暂无M56×2 85 74 12 8 3.5 1.5 1 290.1 暂无M60×2 90 79 12 8 3.5 1.5 1 320.3 暂无M64×2 95 84 12 8 3.5 1.5 1 351.9 暂无M65×2 95 84 12 8 3.5 1.5 1 342.4 暂无M68×2 100 88 12 10 4 1.5 1 380.2 暂无M72×2 105 93 15 10 4 1.5 1 518 暂无M75×2 105 93 15 10 4 1.5 1 477.5 暂无M76×2 110 98 15 10 4 1.5 1 562.4 暂无M80×2 115 103 15 10 4 1.5 1 608.4 暂无M85×2 120 108 15 10 4 1.5 1 640.6 暂无M90×2 125 112 18 12 5 1.5 1 796.1 暂无M95×2 130 117 18 12 5 1.5 1 834.7 暂无槽或全部热槽或全部热槽或全部热处理后处理后处理后槽或全部热处理后螺纹公螺纹公35~45HRC;35~45HRC;35~45HRC; 技术条件材料:45钢 35~45HRC;调质暂无暂无差:6H 差:6H 调质调质调质24~30HRC;氧化 24~30HRC;24~30HRC;24~30HRC;氧化氧化氧化。
m80圆螺母标准尺寸
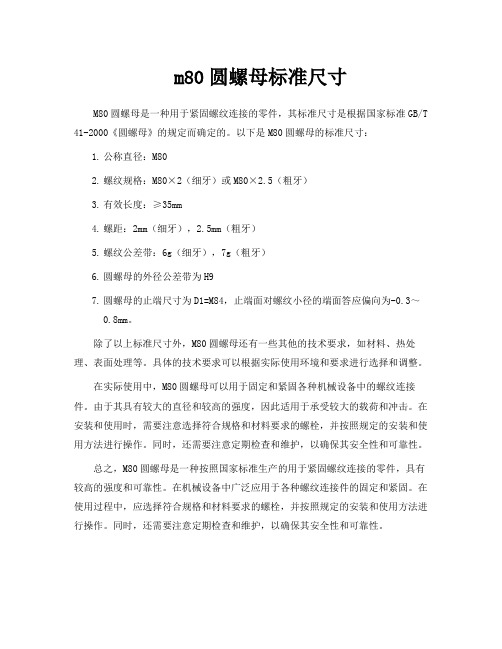
m80圆螺母标准尺寸
M80圆螺母是一种用于紧固螺纹连接的零件,其标准尺寸是根据国家标准GB/T 41-2000《圆螺母》的规定而确定的。
以下是M80圆螺母的标准尺寸:
1.公称直径:M80
2.螺纹规格:M80×2(细牙)或M80×2.5(粗牙)
3.有效长度:≥35mm
4.螺距:2mm(细牙),2.5mm(粗牙)
5.螺纹公差带:6g(细牙),7g(粗牙)
6.圆螺母的外径公差带为H9
7.圆螺母的止端尺寸为D1=M84,止端面对螺纹小径的端面答应偏向为-0.3~
0.8mm。
除了以上标准尺寸外,M80圆螺母还有一些其他的技术要求,如材料、热处理、表面处理等。
具体的技术要求可以根据实际使用环境和要求进行选择和调整。
在实际使用中,M80圆螺母可以用于固定和紧固各种机械设备中的螺纹连接件。
由于其具有较大的直径和较高的强度,因此适用于承受较大的载荷和冲击。
在安装和使用时,需要注意选择符合规格和材料要求的螺栓,并按照规定的安装和使用方法进行操作。
同时,还需要注意定期检查和维护,以确保其安全性和可靠性。
总之,M80圆螺母是一种按照国家标准生产的用于紧固螺纹连接的零件,具有较高的强度和可靠性。
在机械设备中广泛应用于各种螺纹连接件的固定和紧固。
在使用过程中,应选择符合规格和材料要求的螺栓,并按照规定的安装和使用方法进行操作。
同时,还需要注意定期检查和维护,以确保其安全性和可靠性。
- 1、下载文档前请自行甄别文档内容的完整性,平台不提供额外的编辑、内容补充、找答案等附加服务。
- 2、"仅部分预览"的文档,不可在线预览部分如存在完整性等问题,可反馈申请退款(可完整预览的文档不适用该条件!)。
- 3、如文档侵犯您的权益,请联系客服反馈,我们会尽快为您处理(人工客服工作时间:9:00-18:30)。
记录号:JS-AL-其它-007
18×64 I型联接环开裂原因分析
摘要:某18×64 I型联接环,材料为23MnVB钢,联接环是由Φ55的圆钢经锻造加工而成,该批联接环成品检查中发现大量开裂件,通过裂纹剖面分析、断口分析及材料的组织分析,结果表明:联接环中段的纵向裂纹产生于余热淬火过程,余热淬火造成的应力过大是导致裂纹的主要原因。
严格控制余热淬火温度,降低冷却速度可以降低余热淬火在组织中产生的应力,降低试件淬裂倾向。
关键词:18×64 I型联接环;裂纹;余热淬火;淬火应力
材料种类/牌号:合金钢/23MnVB
概述
某18×64 I型联接环,材料为23MnVB钢,联接环是由Φ55的圆钢经锻造加工而成,具体加工工艺过程如下:
剪床下料(Φ55×10mm圆钢)—加热(炉温1300℃,坯料温度1150℃~1250℃,保温时间10~15分钟)—锻造(制坯始锻温度1250℃;终锻成形,终锻温度1100℃)—切边(始切温度1100℃~终切1000℃,切边时温度高于700℃)—冲孔(始冲温度1000℃~终冲700℃,冲孔时温度高于700℃)—余热淬火。
联接环成形后进行热处理,热处理工艺为:正火900℃×120min;淬火900℃×120min;低温回火230℃×240min。
该批联接环成品检查中发现大量开裂件,肉眼可以看见张开的裂纹,裂纹位置不同,但主要为纵向裂纹。
如图1是联接环的形状和裂纹的形态之一,裂纹呈两侧对称分布。
图2
是另一类裂纹的形态,裂纹位于中段,该图是从裂纹的中段沿横截面将联接环截断所看到的裂纹形态,测量出该裂纹的最大深度超过12mm。
图1 连接环的形状和裂纹的形态之一
本工作所分析的裂纹为图2所示联接环中的裂纹,分析了造成该联接环发生开裂的工艺
因素和材料因素。
图2 连接环中裂纹的形态之二及剖面形态
测试过程与结果
裂纹剖面分析
裂纹的位置和宏观形态如图2,裂纹位于联接环中段较粗的截面区域,基本呈直线状,且关于联接环结构中段对称分布。
裂纹中部开口很宽,两端渐细,从剖面观察,裂纹呈薄楔形垂直表面向内扩展。
裂纹中段横剖面的低倍组织形态:呈薄楔形的裂纹垂直表面穿过模锻形成的带状组织,扩展深度约12mm。
裂纹的开口很宽,是从表面向内扩展的。
这些特征表明,裂纹产生于模锻成型后的冷却过程,冷却过程中表面的拉应力较大,形成较宽的裂口。
观察裂纹附近的显微组织看到,裂纹两侧直至尖端处的组织都有严重脱碳,裂纹没有分叉,如图3和图4,脱碳区组织主要为铁素体,基体组织为回火马氏体。
显然,联接环中裂纹形成后又经过了加热到奥氏体化温度以上的热处理过程,因此裂纹附近组织出现脱碳。
有由于裂纹的尖端处组织亦已脱碳,表明在最后的淬火冷却过程中裂纹没有进一步扩展。
图3 裂纹尖端形态和脱碳区组织 图4 裂纹口部脱碳区组织
在高倍下用SEM分析裂纹附近的组织和氧化物形态,如图5和图6,裂纹附近的铁素体
组织晶界上出现细粒状含Si、Mn的氧化物,这些氧化物是在高温加热过程中经扩散氧化形
成的,其中易氧化的合金元素Si、Mn也发生了一定距离的扩散,这是在奥氏体相区以上温
度较长时间加热的结果。
图 5 裂纹尖端形态和脱碳区组织 图6裂纹口部脱碳区组织
裂纹剖面分析结果表明,所分析联接环中的裂纹产生于模锻成型后的冷却过程,裂纹形
成后试样被加热到奥氏体化温度以上进行热处理,因此裂纹附近组织出现严重的氧化脱碳。
但是,在最后的淬火冷却过程中裂纹没有进一步扩展,由此看来加热到900°后淬火不会产
生严重不良的组织应力和热应力,导致淬火裂纹。
断口分析
将裂纹起开,观察断口,如图7和图8,裂纹断口面很平坦,已严重氧化,已经不能看
出断口的原始形态。
微观上的较平坦断口意味着原始断口可能是以穿晶解理断口为主,裂纹
没有微观分叉,说明出现裂纹时组织没有明显的过热或火烧问题。
符合冷却过程温差应力造
成的裂纹的特征。
用EDS在断面上分析未见有明显的夹杂物集中分布的现象,看来裂纹的产
生与圆钢的原始夹杂类缺陷没有直接关系。
图7 裂纹面断口的形态图 图8 人工断口的形态,解理断口
材料的组织分析
圆钢横截面中心疏松1级,锭型偏析2级。
成品件裂纹位置横截面较明显的偏析带流线分布于中部,裂纹穿过流线。
垂直裂纹的纵剖面低倍组织未见明显的偏析和带状组织。
成品件的显微组织形态如图9和图10,为正常的回火马氏体组织。
图9 成品件的显微组织形态 图10 成品件的高倍显微组织形态
讨论
上述分析表明,所分析联接环中的裂纹与模锻组织流线相交,是产生于模锻成型后的冷却过程。
裂纹形成后试样又被加热到奥氏体化温度以上进行热处理,因此裂纹附近组织出现严重的氧化脱碳。
但是,在最后的淬火冷却过程中裂纹没有进一步扩展,可见,该试件加热到900°后淬火不会导致淬火裂纹,相应的,冷却速度较慢的正火处理导致裂纹的可能性应该更小。
而显微分析见到,裂纹两侧金属组织发生了严重的扩散型氧化,是在奥氏体化温度以上长时间氧化的结果。
因此可以断定,裂纹产生于联接环成型之后,正火和淬火热处理之前。
又从裂纹的形态来看,是一种冷却过程的应力裂纹,由此判断裂纹是产生于余热淬火过程或之后,余热淬火应力过大是导致该试件产生裂纹的主要因素。
严格控制余热淬火温度,降低冷却速度可以降低余热淬火在组织中产生的应力,降低淬裂倾向。
锭型偏析对淬火应力分布状态又一定的不利影响。
结论和建议
联接环中段的纵向裂纹产生于余热淬火过程,余热淬火造成的应力过大是导致裂纹的主要原因。
严格控制余热淬火温度,降低冷却速度可以降低余热淬火在组织中产生的应力,降低试件淬裂倾向。
主要分析人员及单位
朱衍勇 教授级高工 钢铁研究总院
董毅 工程师 钢铁研究总院
资料整理人:王冬梅 国家钢铁材料测试中心 审核人: 吴伯群 国家钢铁材料测试中心。