宝钢股份电炉工艺(201409)
宝钢1550mm冷轧电工钢机组退火炉安装工艺
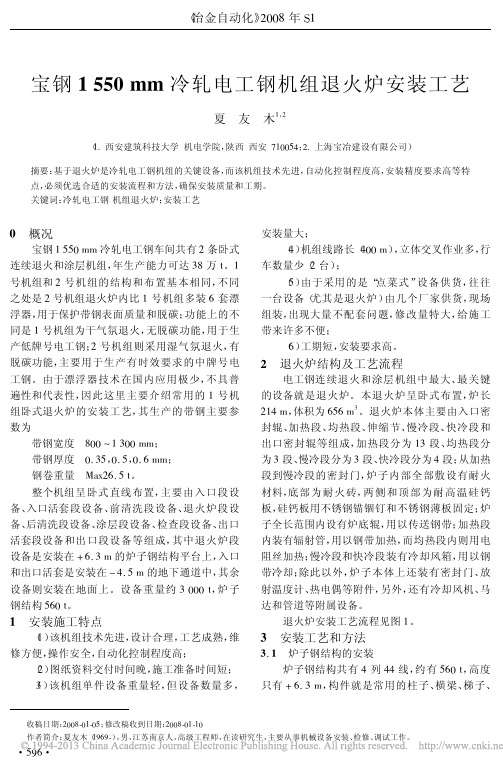
#% 概况
宝钢 " ’’& )) 冷轧电工钢车间共有 # 条卧式 连续退火和涂层机组, 年生产能力可达 *+ 万 ,。" 号机组和 # 号机组的结构和布置基本相同, 不同 之处是 # 号机组退火炉内比 " 号机组多装 - 套漂 浮器, 用于保护带钢表面质量和脱碳; 功能上的不 同是 " 号机组为干气氛退火, 无脱碳功能, 用于生 产低牌号电工钢; # 号机组则采用湿气氛退火, 有 脱碳功能, 主要用于生产有时效要求的中牌号电 工钢。由于漂浮器技术在国内应用极少, 不具普 遍性和代表性, 因此这里主要介绍常用的 " 号机 组卧式退火炉的安装工艺, 其生产的带钢主要参 数为 带钢宽度! +&& . " *&& )); 带钢厚度! &/ *’ , &/ ’ , &/ - )); 钢卷重量! 012#-/ ’ ,。 整个机组呈卧式直线布置, 主要由入口段设 备、 入口活套段设备、 前清洗段设备、 退火炉段设 备、 后清洗段设备、 涂层段设备、 检查段设备、 出口 活套段设备和出口段设备等组成, 其中退火炉段 设备是安装在 3 -/ * ) 的炉子钢结构平台上, 入口 和出口活套是安装在 4 (/ ’ ) 的地下通道中, 其余 设备则安装在地面上。设备重量约 * &&& ,, 炉子 钢结构 ’-& ,。
《 冶金自动化》 "))’ 年 8! !" 退火炉气密性试验
由于退火炉在正常工作状态下, 炉内冲有氢 氮保护气体, 为了防止气体外泻引起爆炸, 因此在 退火炉安装完毕后要进行气密性试验。 ( !) 气密性试验的前提条件 入出口 密 封 辊、 炉 壳、 伸 缩 节、 炉 底 辊、 辐射 管、 冷却风箱风管和风机、 人孔、 检修孔、 观测孔、 测电偶等炉子本体及其附属设备和装置全部安装 完毕。 ( ") 气密性试验的准备工作 气源:直接利用厂房内的压缩空气, 就近接入 炉内; 或用空压机提供气源。 盲板: 在入出口密封辊处、 压力调整装置处、 氢气和氮气输入处等地方加上封堵盲板。 仪表: 观测炉内气体泄露量用的 # 形管 $ 套, 用于控制炉内最大压力用的刻度玻璃管 ! 套。 查漏工 具: $% 肥 皂 水 和 喷 壶, 粉 笔, 对讲机 等。 人员: 气源控制 ! 人, 仪表观测 & 人, 查漏 &’ 人。 ( $) 气密性试验步骤 !) 彻底检查整个退火炉与气密性试验有关的 设备和部件均已全部安装完毕。 ") 将所有盲板全部安装到位。 $) 将气源管路接上炉子, 将 # 形管和刻度玻 璃管接入炉子。 &) 查漏工具准备好、 人员组织安排到位。 () 开启开大气源处阀门, 将气体充入炉内, 当 $ 个 # 形管的水柱均达到 () **+" , ( ! **+" , ./ ’)0 12, 下同) 时, 调整气源处阀门使炉内压力保 持在 () **+" ,; 由于炉子较长, 开始充气时炉内 气压 不 是 很 均 匀, $ 个 # 形 管 不 会 同 时 达 到 () **+" ,, 因此 要 控 制 炉 内 最 大 压 力 不 能 超 过 3) **+" ,。 开始查漏, 查漏重点位置在现场焊接的焊缝 ( 炉壳间焊接、 风管焊接、 辐射管法兰焊接等) , 尤 其是较难焊接的位置; 法兰连接处( 人孔、 检修孔、 观测孔、 测电偶、 炉底辊、 盲板等处的法兰连接) ; 当第 ! 次检查出的泄露点全部处理完毕后, 检查泄露处理点是否还漏; 重复上述充气步骤 ( , 检查是否还有新的泄露点; 一般来说, “ 查漏( 步骤 () — — —处理( 步骤 0 ) ” 这一过程要重复 $ 4 ( 次, 时间要 !) 4 !( 5。 ( &) 退火炉气密性试验合格判断标准 根据日方和宝钢的要求, 退火炉气密性试验 的合格 标 准 为: 炉 内 气 压 从 () **+" , 降 至 !) **+" , 时, 时间为 $) *67。该退火炉气密性试验 的实况为: 炉内气压从 () **+" , 降至 !) **+" , 时, 时间为 &0 *67, 大大超出合格标准, 整个气密 性试验工作花了 !" 5 时间。 工厂焊接焊缝和法兰连接处。查到漏气处就用粉 笔做上记号, 当整个炉子第 ! 遍全部查完后, 关闭 气源处阀门。 0) 当炉内气体全部泄露完 毕 后 开 始 进 行 处 理, 焊缝泄露处先要对泄露点焊缝打磨修整干燥 后进行补焊; 法兰连接处泄露, 先打开法兰, 检查 是否加有密封垫, 密封垫是否完好、 垫好, 两片法 兰是否平整, 有无变形, 法兰连接螺栓孔是否偏大 等, 处理方法如表 ( 所示。
宝钢4号高炉(二代)开炉炉温平衡实践

宝钢4号高炉(二代)开炉炉温平衡实践朱勇军;林成城;刘开华【摘要】宝钢4号高炉(二代)于2014年11月12日点火投产,在总结历次大型高炉开炉经验后,从选择开炉料及其填充方式、提高烘炉效果、开炉初始制度和加风节奏以及送风过程中的炉热炉况调整等方面优化开炉过程中的炉温平衡,取得了良好的效果.开炉首次铁水温度达到1 510℃,创造了宝钢高炉开炉首次铁的最高温度.后续的降硅过程平稳进行,第13次出铁时铁水硅降至1.0%以下.从开炉准备和点火送风两个阶段介绍了宝钢4号高炉(二代)开炉过程中的炉温平衡操作和实际效果,供以后大型高炉开炉参考和借鉴.【期刊名称】《宝钢技术》【年(卷),期】2016(000)001【总页数】5页(P36-40)【关键词】高炉;开炉;炉温平衡【作者】朱勇军;林成城;刘开华【作者单位】宝山钢铁股份有限公司炼铁厂,上海200941;宝山钢铁股份有限公司炼铁厂,上海200941;宝山钢铁股份有限公司炼铁厂,上海200941【正文语种】中文【中图分类】TF542+.5开发与应用朱勇军工程师1982年生2007年毕业于中南大学现从事高炉炼铁工作电话26647174E-mail ***********************宝钢股份公司4号高炉于2014年9月1日停炉进行炉缸大修,二代设计炉容为4 747 m3,于2014年11月12日点火开炉,全开风口并插煤枪送风。
总结宝钢历次大型高炉开炉经验,从开炉料的选择、填充方式、提高烘炉效果、开炉初始制度和加风节奏以及送风过程中炉热炉况调整等方面不断优化开炉过程中的炉温平衡,取得了良好的效果。
送风后21 h 23 min首次出铁593 t,铁水温度最高达到1510 ℃,创造了宝钢高炉开炉首次铁的最高温度,并成功冲制水渣。
后续降硅过程平稳进行,第13次出铁时铁水硅降至1.0%以下。
出铁后第5天,风量为6 800m3/min,氧量为5 000 m3/h,全天产量为9 536 t,利用系数为2.01 t/(m3·d),实现了安全稳定高效开炉。
电炉炼钢工艺

电炉炼钢工艺电炉炼钢,主要是指电弧炉炼钢,是目前国内外生产特殊钢的主要方法。
目前,世界上90%以上的电炉钢是电弧炉生产的,还有少量电炉钢是由感应炉、电渣炉等生产的。
通常所说的电弧炉,是指碱性电弧炉。
电弧炉主要是利用电极与炉料之间放电产生电弧发出的热量来炼钢。
其优点是:(1)热效率高,废气带走的热量相对较少,其热效率可达65%以上。
(2)温度高,电弧区温度高达3000℃以上,可以快速熔化各种炉料。
(3)温度容易调整和控制,可以满足冶炼不同钢种的要求。
(4)炉内气氛可以控制,可去磷、硫,还可脱氧。
(5)设备简单,占地少,投资省。
第一节冶炼方法的分类根据炉料的入炉状态分,有热装和冷装两种。
热装没有熔化期,冶炼时间短,生产率高,但需转炉或其他形式的混铁炉配合;冷装主要使用固体钢铁料或海绵铁等。
根据冶炼过程中的造渣次数分,有单渣法和双渣法。
根据冶炼过程中用氧与不用氧来分,有氧化法和不氧化法。
氧化法多采用双渣冶炼,但也有采用单渣冶炼的,如电炉钢的快速冶炼,而不氧化法均采用单渣冶炼。
此外,还有返回吹氧法。
根据氧化期供氧方式的不同,有矿石氧化法、氧气氧化法和矿、氧综合氧化法及氩氧混吹法。
冶炼方法的确定主要取决于炉料的组成以及对成品钢的质量要求,下面我们扼要介绍几种冶炼方法:(1)氧化法。
氧化法冶炼的特点是有氧化期,在冶炼过程中采用氧化剂用来氧化钢液中的Si、Mn、P等超规格的元素及其他杂质。
因此,该法虽是采用粗料却能冶炼出高级优质钢,所以应用极为广泛。
缺点是冶炼时间长,易氧化元素烧损大。
(2)不氧化法。
不氧化法冶炼的特点是没有氧化期,一般全用精料,如本钢种或类似本钢种返回废钢以及软钢等,要求磷及其他杂质含量越低越好,配入的合金元素含量应进入或接近于成品钢规格的中限或下限。
不氧化法冶炼可回收大量贵重合金元素和缩短冶炼时间。
在缺少本钢种或类似本钢种返回废钢时,炉料中可配入铁合金,这种冶炼方法又叫做装入法,用“入”字表示,多用于冶炼高合金钢等钢种上。
宝钢生产工艺流程

宝钢生产工艺流程
炼铁的主要原料铁矿石、焦炭和煤通过高炉中一系列反应变为铁水,铁水和废钢通过转炉加工为钢水。
钢水可通过连铸加工成板坯,也可通过模铸加工成钢锭后在初轧厂最终加工成板坯、初轧方坯和管坯。
由于连铸避免了模铸的过程,使得钢的构成更为均匀,成品率和质量也大幅提高。
1999年,宝钢的连铸比约为73%。
今后计划将连铸比例再提高到100%。
钢锭、板坯、初轧方坯和管坯为半成品,除一小部分直接销往市场外,大部分将通过下道轧钢工序制成成品。
板坯、初轧方坯和管坯分别是制成热轧产品、钢丝和钢筋及管材的原料,最终将制成不同品级和用途的热轧板卷、线材和无缝钢管。
热轧板卷部分作为成品销售;部分作为冷轧的原料,经过酸洗、轧钢、退火、涂层和油漆,制成具有高附加值的冷轧板卷,包括电镀锌板卷、热镀锌板卷和彩涂板卷。
宝钢股份高炉生产工艺与设备-yj上课讲义

小钟
溜槽 探尺
导料板
大钟
探尺
串罐式炉顶装料流程
Z-401BC
上部闸阀
上料罐
一次排压阀
二次排压阀
GAS N2
消音器
上部密封阀
一均
二均
Z-401BC驱动马达
旋转溜槽
FCG阀 下部密封阀
探尺
并罐式炉顶装料系统
并罐式炉顶装料系统 优点: 系统上料能力较强,具有 互为备份功能;
缺点: 炉料粒度偏析和轨迹偏析 较大,不易消除。
W .G
CB
AB
BB
H
CB
AB
BB
H
CB
AB
BB
H
CB
AB
BB
H
B
M
B
M
B
M
B
M
4HS
3HS
2HS
1HS
H
H
H
H
SII WS W E SI C SII WS W E SI C SII WS W E SI C SII WS W E SI C
高炉炉顶装料流程
项 目 单位 1BF 2BF 3BF
上部漏斗 m3 40 80 80
下料罐 m3 80 80 80
溜槽长度 mm
4500 4500
大钟直径 mm 7300
炉顶压力 MPa 0.25 0.25 0.25
探尺数量 把 4 3 3
Z-101BC
闸阀
No 1 No 2 No 3 No 4
No 1 No 2 No 3 No 4
原料工序是我国钢铁企业第一个现代化的大型原料处理厂,对全公司的 原燃料进行集中管理,以精料为宗旨向全公司各用户供料。具有以下特点: 大型化:料场占地面积1.02平方公里;年作业总量1亿吨。 现代化:计算机、PLC高效率集中分级控制,并实现三电一体化。 先进性:装备良好的环境保护设备;混匀矿堆积采用先进的数模智能控制。
电炉炼钢原理及工艺

电炉炼钢原理及工艺
电炉炼钢是利用电力作为热源,通过电弧加热的方式,将生铁
或废钢进行熔炼,加入适量的合金元素,最终得到符合特定要求的
钢铁产品的一种炼钢工艺。
电炉炼钢具有能耗低、环保、生产灵活
等优点,因此在现代钢铁工业中得到了广泛应用。
电炉炼钢的原理主要是通过电弧将炉料加热至熔化温度,同时
控制合金元素的加入,最终实现对炉料成分和温度的精确控制,从
而得到符合要求的钢铁产品。
电炉炼钢主要包括三种类型,直接电
弧炉、感应电炉和电渣重熔炉。
不同类型的电炉在原理和工艺上略
有不同,但基本的炼钢原理是相似的。
电炉炼钢的工艺流程一般包括,炉料装入、预热、电弧加热、
合金元素加入、脱氧、脱硫、炉渣处理等环节。
在整个工艺过程中,需要严格控制炉料的成分和温度,合理控制电弧加热的能量,确保
炼钢过程中的各项参数处于合适的范围,从而保证炼钢的质量。
电炉炼钢的原理和工艺虽然相对复杂,但是在实际生产中已经
得到了充分的验证和应用。
随着现代工艺技术的不断进步,电炉炼
钢的工艺也在不断完善和提高。
在炼钢过程中,需要考虑原料的选
择、电弧加热的控制、合金元素的加入、炉渣的处理等诸多因素,以确保最终生产出符合要求的钢铁产品。
总的来说,电炉炼钢是一种先进的炼钢工艺,其原理和工艺流程相对复杂,但是通过合理的控制和优化,可以实现对钢铁产品质量的精确控制。
随着工艺技术的不断进步,电炉炼钢必将在钢铁工业中发挥越来越重要的作用,为钢铁生产的发展做出更大的贡献。
电炉炼钢工艺流程

电炉炼钢工艺流程
《电炉炼钢工艺流程》
电炉炼钢是一种利用电弧加热来熔化金属的工艺方法,它是现代钢铁生产中的重要环节之一。
下面将介绍电炉炼钢的工艺流程。
首先,在电炉炼钢的工艺流程中,需要准备原料。
通常情况下,原料包括废钢、废铁、废钢包和铁合金等。
这些原料需要经过严格的分类和筛选,以确保炼钢的质量和成本。
接下来,原料将被装入电炉中。
电炉的设计通常包括一个底部出口,以方便放入和取出原料。
一旦原料放入电炉,就需要关闭电炉的盖子,并开始预热电炉。
然后,电炉将被通电,电极将产生强烈的电弧,使原料受热。
在炉内,温度逐渐上升,金属开始熔化。
在这个过程中,通过向炉内注入氧气、碳和其他合金元素,可以调整熔池的成分和温度,使得最终产出的钢材符合指定的要求。
最后,当钢水达到设计要求的成分和温度后,电炉的出口将被打开,将炉内熔融的金属倒出,成为成品钢。
在一些特殊情况下,还需要进行连铸和连轧等后续工序,以将熔融的金属成形为各种规格和形状的钢材。
综上所述,电炉炼钢工艺流程包括原料准备、电炉装料、预热、
加热炼炉、调质、出钢等环节。
这一工艺流程不仅改善了钢铁生产的生产效率,还提高了钢材的质量。
电炉炼钢原理及工艺
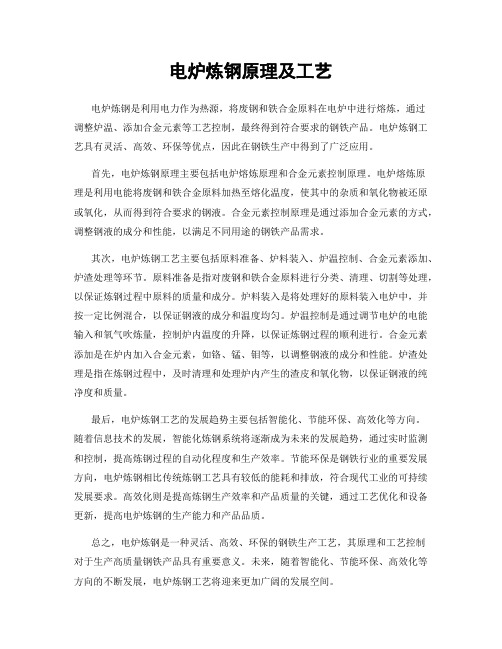
电炉炼钢原理及工艺电炉炼钢是利用电力作为热源,将废钢和铁合金原料在电炉中进行熔炼,通过调整炉温、添加合金元素等工艺控制,最终得到符合要求的钢铁产品。
电炉炼钢工艺具有灵活、高效、环保等优点,因此在钢铁生产中得到了广泛应用。
首先,电炉炼钢原理主要包括电炉熔炼原理和合金元素控制原理。
电炉熔炼原理是利用电能将废钢和铁合金原料加热至熔化温度,使其中的杂质和氧化物被还原或氧化,从而得到符合要求的钢液。
合金元素控制原理是通过添加合金元素的方式,调整钢液的成分和性能,以满足不同用途的钢铁产品需求。
其次,电炉炼钢工艺主要包括原料准备、炉料装入、炉温控制、合金元素添加、炉渣处理等环节。
原料准备是指对废钢和铁合金原料进行分类、清理、切割等处理,以保证炼钢过程中原料的质量和成分。
炉料装入是将处理好的原料装入电炉中,并按一定比例混合,以保证钢液的成分和温度均匀。
炉温控制是通过调节电炉的电能输入和氧气吹炼量,控制炉内温度的升降,以保证炼钢过程的顺利进行。
合金元素添加是在炉内加入合金元素,如铬、锰、钼等,以调整钢液的成分和性能。
炉渣处理是指在炼钢过程中,及时清理和处理炉内产生的渣皮和氧化物,以保证钢液的纯净度和质量。
最后,电炉炼钢工艺的发展趋势主要包括智能化、节能环保、高效化等方向。
随着信息技术的发展,智能化炼钢系统将逐渐成为未来的发展趋势,通过实时监测和控制,提高炼钢过程的自动化程度和生产效率。
节能环保是钢铁行业的重要发展方向,电炉炼钢相比传统炼钢工艺具有较低的能耗和排放,符合现代工业的可持续发展要求。
高效化则是提高炼钢生产效率和产品质量的关键,通过工艺优化和设备更新,提高电炉炼钢的生产能力和产品品质。
总之,电炉炼钢是一种灵活、高效、环保的钢铁生产工艺,其原理和工艺控制对于生产高质量钢铁产品具有重要意义。
未来,随着智能化、节能环保、高效化等方向的不断发展,电炉炼钢工艺将迎来更加广阔的发展空间。
电炉炼钢工艺流程

电炉炼钢工艺流程
电炉炼钢工艺流程一般包括以下步骤:
1.收集废钢:搜集合适的废钢材料进行预处理。
2.加入废钢:把打好成小块的废钢投入电炉中,加入铁合金和石墨棒等辅料。
3.预热:将电炉加热并预热至一定温度。
4.熔化:将电炉内的废钢、铁合金和辅料熔化。
5.制取钢渣:制取钢渣以清理炉中杂质。
6.精炼冶炼:利用电炉通入氧气对炉内物质进行冶炼,降低碳含量,提高钢的质量。
7.取钢水:完成精炼后,通过倾炉将钢水倾进连铸机进行冷却,形成钢坯。
8.连铸:将钢坯放入连铸机中,通过连铸冷却形成钢板。
9.加工:将冷却的钢板进行下一步加工,如轧制、拉拔、热处理等。
宝钢股份电炉工艺(201409)
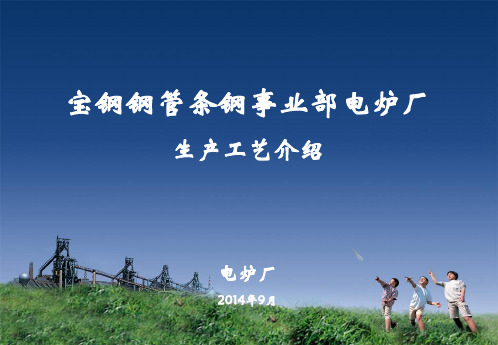
钢种。
将石墨电极降低到钢渣面以下,可以使钢水
以每分种3°C 的速度升温。
LF炉的另外起到在转炉和连铸中的一个缓 冲作用。
1
圆方坯产线
LF设备组成
1——电极加热系统; 2——铁合金投料系统;
3——底吹搅拌系统;
4——水冷炉盖; 5——除尘系统;
6——事故顶枪系统;
7——喂丝系统; 8——装有透气塞的钢包;
通过吹氩及CO、H2气泡使夹杂物集聚并上浮
1
圆方坯产线
设备组成
VD真空系统设备主要包括:真空罐 和盖车系统、废气冷却除尘系统、真空 抽气系统、蒸汽蓄热器和除氧系统、底 吹搅拌系统、投料系统、喂丝系统、氮
气系统、压缩空气系统、真空测量系统、
TV摄像监视和电气控制等。
1
圆方坯产线
装备特点
真空特性
帘线处理
为电炉与连铸的匹配提供时间弹性、保证
Ar
多炉连浇
1 供电特点
圆方坯产线
本座LF炉由一台容量为22MVA的变压器提供三相交流电,三根电极可单 独调节;
―
电极液压系统由驻留于 PLC 中的标准软件包进行控制,即电极控制单元
(ECU ),可实现电极升降的快速响应,减少钢水“舔”电极而导致增
宝钢钢管条钢事业部电炉厂
生产工艺介绍
电炉厂
2014年9月
炼钢厂区域图
电炉
电炉厂所处位置
•
电炉与转炉炼钢的区别: – 投资方面:转炉投资大,流程长,电炉投资小,流程短; – 原料方面:转炉以铁水为主要原料,电炉以废钢为主要原料; – 能源方面:转炉以铁水的物理热和化学热为能源,电炉主要以电能为能源; – 冶炼钢种方面:传统意义上,转炉以铁水的物理热和化学热为能源,因能 量有限,以冶炼普碳钢为主,电炉则因以电能为主要能源,可冶炼合金钢 和高合金钢,电炉可冶炼更多的钢种,另外因电炉冶炼有还原期,电炉钢 的质量要优于转炉钢。但随着炉外精炼及铁水预处理的发展,电炉冶炼钢 种及质量方面已无明显优势。
电炉炼钢基本工艺

电弧炉炼钢基本工艺电弧炉炼钢从整体可分为原材料的收集、冶炼前的准备工作、熔化期、氧化期和还原期五大阶段。
原材料的收集废钢是电弧炉炼钢的主要材料,废钢质量的好坏直接影响钢的质量、成本和电炉生产率,因此,对废钢有如下几点要求:(1)废钢表面应清洁少锈,因废钢中沾有的泥沙等杂物会降低炉料的导电性能,延长熔化时间,还会影响氧化期去磷效果以及侵蚀炉衬。
废钢锈蚀严重或沾有油污时会降低钢和合金元素的收得率,增加钢中的含氢量。
(2)废钢中不得混有铅、锡、砷、锌、铜等有色金属。
铅的密度大,熔点低,不溶于钢液,易沉积在炉底缝隙中造成漏钢事故。
锡、砷和铜,易引起钢的热脆。
(3)废钢中不得混有密封容器,易燃、易爆物和有毒物,以保证安全生产。
(4)废钢化学成分应明确,硫、磷含量不宜过高。
(5)废钢外形尺寸不能过大(截面积不宜超过150mm×150mm,最大长度不宜超过350mm)。
生铁在电弧炉炼钢中,一般被用来提高炉料的配碳量,通常配入量不超过炉料的30%。
冶炼前的准备工作配料是电炉炼钢工艺中不可缺少的组成部分,配料是否合理关系到炼钢工能否按照工艺要求正常地进行冶炼操作。
合理的配料能缩短冶炼时间。
配料时应注意:一是必须正确地进行配料计算和准确地称量炉料装入量。
二是炉料的大小要按比例搭配,以达到好装、快化的目的。
三是各类炉料应根据钢的质量要求和冶炼方法搭配使用。
四是配料成分必须符合工艺要求。
一般冶炼方法对炉料中的主要元素含量要求如下:(1)碳含量。
炉料中含碳量应保证氧化期有足够量的碳进行碳氧反应,达到去气、去夹杂物的目的。
配碳量根据熔化期碳的烧损、氧化期的脱碳量和还原期增碳量这3个因素来确定,要求炉料熔清时,钢中碳量高出成品规格下限0.3%~0.4%;但配碳量也不能过高,否则会延长氧化时间并使钢液过热。
(2)硅含量。
含硅量一般不大于炉料的0.8%,过高会延缓钢液的沸腾。
(3)锰含量。
一般钢种配料时对锰可不考虑,通常熔清后锰含量小于0.3%,否则也会延缓熔池沸腾。
宝钢电炉、圆(方)坯连铸三电系统概要

宝钢电炉、圆(方)坯连铸三电系统概要0 引言宝钢直流电炉、圆(方)坯连铸工程为宝钢三期工程项目之一,主体工艺设备及三电系统分别由法国CLECIM和意大利DANIELI公司引进,其装备水平属当今世界上较先进水平,合同于1994年签定,1997年6月15日开始设备热试运转,建成投产后年产100万t钢水,铸成96万t圆(方)坯。
三电系统包括基础自动化、过程控制、生产控制和管理三级计算机系统。
工厂自动化系统与公司管理计算机系统有机整合,形成管、线材等生产的综合一贯管理,以达到提高产品的产量和质量、节能、省力、降低成本,在满足市场要求的同时,获得最大的盈利。
1 工艺及主要设备简介工艺设备及物流概要见图1。
电炉(EAF)采用一电(源)双炉座的150t超高功率直流电弧炉,以废钢和铁水为原料,冶炼石油用管钢、高压锅炉管钢、帘线钢、冷镦钢等诸多优质钢种的钢水。
钢包精炼炉(LF)将电炉熔炼的钢水采用交流供电加热进行成分、温度微调,成为合格的钢水。
真空脱气装置(VD)用高架坑式的真空装置将钢包内钢水净化,满足高级钢种的质量要求。
连铸机(CC)采用一机六流圆、方可更替的高速连铸机,将钢水铸成钢管所需的圆坯和线材所需的方坯,一个铸机最多连浇10炉。
铸坯空冷场(BY)连铸机生产的圆、方坯在场内冷却、进行质检和必要的处理,然后将合格的铸坯送到钢管厂和线材厂,少量外供。
废钢料场(SY)符合要求规格的各种废钢在废钢料场按类堆放,根据计算机下达的品种数量装卡车运往电炉厂装篮。
铁水(HM)高炉铁水通过混铁车运到电炉厂,然后按需倒入铁水包兑入电炉。
2 三电系统概要2.1 系统配置信息流及相关接口见图2。
三电系统配置如图3所示。
L3采用1台DEC Alpha 2100;L2采用2台DEC Alpha 2100和1台DEC Alpha 1000;L1采用18台S5 155U。
2.2 特点(1)采用网络及分布式技术电炉、圆(方)坯连铸工艺设备的特点是工艺设备分布较分散,作业连续化,高速化程度要求不高(连铸部分要求高些),所以采用分散控制集中管理显得尤为重要,分布式控制的基础是必须实现数据传送的网络化,本系统在工厂自动化内采用3级网络控制。
宝钢高炉炉前铁水预脱硅技术

宝钢高炉炉前铁水预脱硅技术王天球王士彬(上海宝山钢铁股份有限公司炼铁厂)摘要:本文介绍了宝钢高炉炉前铁水预脱硅技术,并根据现场实际生产数据及操作经验,分析总结出了影响脱硅效果和泡沫渣的诸多因素,通过采取一系列改进措施,使高炉炉前脱硅取得了很大的进步,为炼钢冶炼低磷低硫精品钢提供了优质低硅铁水。
关键词:炉前脱硅脱硅效果泡沫渣影响因素1.概述高炉炉前脱硅主要是为炼钢提供低硅铁水,冶炼高附加值精品钢。
以往铁水预处理都是由炼钢“三脱”来进行的。
由于其工艺复杂,处理时间长,铁水热损失大,渣量大,成本高,八十年代初以来,日本、韩国、台湾等国家和地区相继采用高炉炉前铁水脱硅技术。
其目的在于缩短钢铁冶炼全流程生产时间,降低炼钢熔剂消耗量,为生产低磷低硫高级钢,提高产品竞争力以及改善企业的经济效益提供必要条件。
高炉炉前脱硅所用的方法主要有投撒法和喷吹法两种。
脱硅剂靠自重撒落到铁水表面的称为投撒法,用载气将脱硅剂以一定速度喷入铁水中的称为喷吹法。
这两种方法都有使用实例。
比较而言,投撒法所用的脱硅剂在粒度和种类上可选范围较宽(如烧结矿粉和氧化铁皮等均可应用),其系统工艺流程及设备都比较简单,造价低,但脱硅剂消耗量大,脱硅剂与铁水搅拌不充分,脱硅产生泡沫渣多,脱硅效果欠佳。
日本福山4BF、千叶6BF、韩国光阳4BF等高炉所用的脱硅系统均属于投撒法。
喷吹法脱硅工艺及设备相对要复杂些,所用的脱硅剂粒度、水分等要求也较高,但脱硅剂与铁水的混合较好,反应界面大,有利于脱硅反应进行,脱硅效果较好。
所用的脱硅剂一般为烧结厂除尘灰和出铁厂除尘灰。
喷吹法是目前采用较多的一种炉前脱硅工艺。
日本的千叶5BF、水岛2BF、3BF、4BF、鹿岛2BF、3BF、福山2BF、神户3BF、加古川2BF 以及台湾中钢1BF等均采用了喷吹法脱硅。
宝钢采用铁水预处理技术,有利于调整公司产品结构,冶炼国内、外市场需求量不断增加的低磷、低硫、高纯度、高附加值的钢种,提高公司市场竞争力和经济效益。
热处理篇-宝钢热处理炉

目 录 表大分类 中分类 小分类 活页号 工艺描述 YARX0500101-0 总论概述热处理总则 YARX0500102-0 功能描述 YARX0510101-0 钢板上料装置主要技术参数 YARX0510102-0 功能描述 YARX0510201-0 辊底式固溶热处理炉主要技术参数 YARX0510202-0 功能描述 YARX0510301-0 淬火机主要技术参数 YARX0510302-0 功能描述 YARX0510401-0 室式高温固溶炉主要技术参数 YARX0510402-0 功能描述 YARX0510501-0 冷却室主要技术参数 YARX0510502-0 功能描述 YARX0510601-0 温矫直机主要技术参数 YARX0510602-0 功能描述YARX0510701-0 主要技术参数 YARX0510702-0 冷床区域工艺路线基准YARX0510703-0 功能描述 YARX0510801-0 钢板堆垛装置主要技术参数 YARX0510802-0 功能描述 YARX0510901-0 移罩式电加热热处理炉主要技术参数 YARX0510902-0 钢板连续固溶入炉基准 YARX0511001-0 辊底式固溶热处理炉区管理钢板连续固溶在炉时间基准YARX0511002-0 钢板固溶(淬火)冷却基准YARX0511101-0 淬火机运行基准 YARX0511102-0 淬火机管理淬火速度基准 YARX0511103-0 高温固溶炉钢板入炉基准YARX0511201-0 高温固溶炉钢板在炉时间基准YARX0511202-0 高温固溶炉区管理高温固溶炉钢板出炉基准 YARX0511203-0 电加热炉钢板入炉基准YARX0511301-0 电加热炉钢板在炉时间基准YARX0511302-0 电加热炉区管理电加热炉钢板出炉基准YARX0511303-0 热处理炉精度管理热处理炉精度管理基准 YARX0511401-0 矫直钢板尺寸管理基准 YARX0511501-0 矫直辊调零基准YARX0511502-0 矫直速度基准 YARX0511503-0 矫直辊使用,修磨基准 YARX0511504-0 热处理 矫直机管理矫直辊换辊基准YARX0511505-0活页号Y A R X0500101-0大分类 总论 中分类 概述 小分类 工艺描述1.热处理工艺、装备及流程概要炉卷热轧项目设计年产量共28.22万吨,其中热轧板17.3吨;热轧卷10.92万吨。
自动喷煤技术在宝钢4号高炉的应用

检测主管输送煤粉管道内的煤粉量,通过流量变送
阀打开;流量范围:0.85 MPa时为85 t/h、1.35 MPa
器检测并输出反馈回中控控制系统(PLC),同时由
时为125 t/h。底座泄漏等级为ANSI的IV级。
新增加的煤粉调节阀来担当和执行调节与控制煤粉 喷吹量的任务。
3.2 改善和优化喷煤控制过程 (1)完善喷煤逻辑控制回路。当高炉喷吹量的
大喷煤下高炉喷煤量的稳定控制,是高炉炉况 稳定的重要基础。随着宝钢4号高炉(4747 m3)喷 煤量的不断增加,在缺少相应煤量检测和调节控制 装置的情况下,采用人工手动和半自动的控制方式 对煤量控制已显得较为困难,瞬时煤量波动呈加大 的趋势,难以满足高炉稳定和顺行的需求。因此,分 析原有工艺设计(控制软件、设备硬件),对不合理 的地方进行完善和优化,使用一种全新的控制模式 来解决喷煤量波动的问题,为高炉稳定顺行创造条 件。 1喷煤工艺流程
第2 8卷第5期 2 0 0 9年1 0月
炼钦
IRONMAKING
V01.28,No.5 0ctober 2009
自动喷煤技术在宝钢4号高炉的应用
朱锦明 沈雪峰徐天凤
(宝山钢铁股份有限公司宝钢分公司)
施月明
(上海德司克测控公司)
摘要对自动喷煤技术在宝钢4号高炉的应用进行了总结。结合宝钢4号高炉喷煤工艺特点,采用喷煤量在线检 测和连续调整等技术,成功开发了一种新型的喷吹控制模式,使自动喷煤技术得到了应用,提高了喷煤系统设备的 安全性与稳定性,提高了每小时人炉喷煤量的控制精度,为高炉稳定顺行创造了条件。 关键词大型高炉 自动控制喷煤煤量
为提高喷煤量控制精度,实现自动喷煤工艺,改 变原有控制模式,将输送气流量控制转为自动控制。 喷吹罐罐压根据喷煤量对应的关系,通过喷吹罐罐 压曲线设定画面自动实现,对应关系可以随时根据 需要进行修改。实现自动喷煤后,喷煤量波动大大 减小。
宝钢高炉炼铁工艺介绍ppt课件
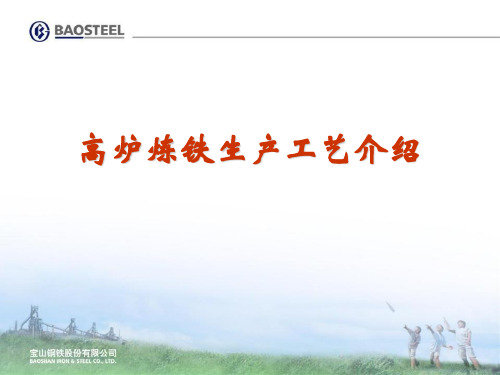
1 2 0 m /m i n
CC OO O
炉顶装料
BF
喷煤系统
重力 除尘器
热风
1VS 2VS
TRT
调压阀组
消音器
水封装置
冷风
HS HS
HS
HS
最高风温
1310℃
最高拱顶温度 1450℃
最高废气温度
350℃
混铁车
高炉脱硅装 置
2、高炉工艺流程介绍
高炉冶炼物流流程
原燃料 鼓风机
矿石 焦炭 辅料 煤粉
高温鼓风
1、行车、悬臂吊车等起重设备; 2、泥炮; 3、开口机; 4、移盖机; 5、摆动流嘴; 6、残铁开口机; 7、主沟、渣铁沟; 8、液压系统。
2.6高炉炉前工艺流程
2、高炉工艺流程介绍
2.7高炉炉渣处理流程
2、高炉工艺流程介绍
渣处理方式
水渣:熔渣经过冷却水急冷,产生细碎颗粒状水渣,用于制作水泥。 干渣:熔渣放入坑中,洒水冷却,冷却后挖掘清运出厂,用于铺路。
水渣处理工艺
LASA法:粗粒分离槽与脱水槽脱水;电消耗大,管道易磨损,占地大 。 INBA法:转鼓与成品槽脱水,水电消耗少,管道阀门寿命长,占地少。 新INBA法:较INBA法增加了蒸汽冷却装置,环保,耗电增多。
2.7高炉炉渣处理流程
压缩空气
烟囱
2、高炉工艺流程介绍
风扇
冷却 塔
炉渣
渣水槽
渣水沟
冲渣水
P 事故水
渣皮带
输送皮带
渣槽
转鼓
P
集水槽 温水槽
P
水渣
P
P
2.7高炉炉渣处理流程
2、高炉工艺流程介绍
2.8高炉除尘系统
电炉炼钢的工艺流程

电炉炼钢的工艺流程
《电炉炼钢的工艺流程》
电炉炼钢是一种先进的钢铁生产技术,其工艺流程主要包括充电、融化、除渣、合金调整和出钢等步骤。
首先,将废钢、铁水和合金料等原料按一定的比例装入电炉中,称为充电。
然后,通过高温电弧、电感加热等方式将原料融化,得到液态钢水。
在融化过程中产生的渣浮于钢水表面,需要进行除渣处理,以保证钢水质量。
接着,根据钢水的成分和性能要求,进行合金调整。
通过添加合金元素,可以改变钢水的化学成分,从而调整成钢的性能。
最后,将处理好的钢水浇铸成坯料或直接进行连铸,得到成品钢材。
整个电炉炼钢的工艺流程较为简单,操作灵活,能够生产各种品种的钢材。
同时,相较于传统的炼钢工艺,电炉炼钢能够减少环境污染,具有较高的能源利用率,深受钢铁企业的青睐。
宝钢4号高炉设计采用的新材料新技术新工艺
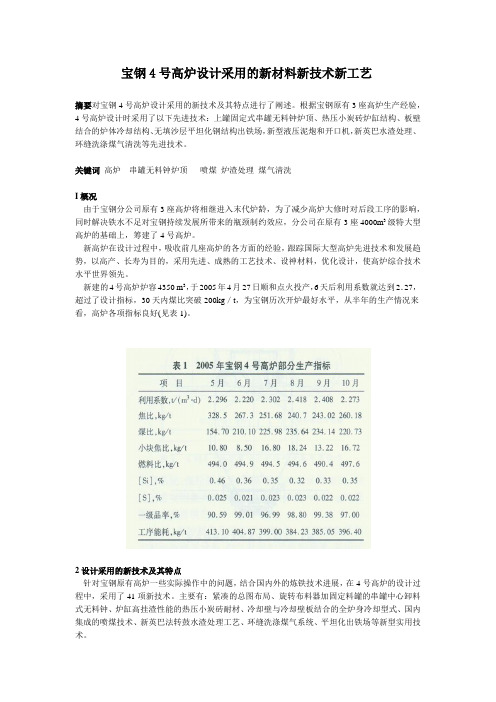
宝钢4号高炉设计采用的新材料新技术新工艺摘要对宝钢4号高炉设计采用的新技术及其特点进行了阐述。
根据宝钢原有3座高炉生产经验,4号高炉设计时采用了以下先进技术:上罐固定式串罐无料钟炉顶、热压小炭砖炉缸结构、板壁结合的炉体冷却结构、无填沙层平坦化钢结构出铁场,新型液压泥炮和开口机,新英巴水渣处理、环缝洗涤煤气清洗等先进技术。
关键词高炉串罐无料钟炉顶喷煤炉渣处理煤气清洗I概况由于宝钢分公司原有3座高炉将相继进入末代炉龄,为了减少高炉大修时对后段工序的影响,同时解决铁水不足对宝钢持续发展所带来的瓶颈制约效应,分公司在原有3座4000m3级特大型高炉的基础上,筹建了4号高炉。
新高炉在设计过程中,吸收前几座高炉的各方面的经验,跟踪国际大型高炉先进技术和发展趋势,以高产、长寿为目的,采用先进、成熟的工艺技术、设神材料,优化设计,使高炉综合技术水平世界领先。
新建的4号高炉炉容4350 m3,于2005年4月27日顺和点火投产,6天后利用系数就达到2.27,超过了设计指标,30天内煤比突破200kg/t,为宝钢历次开炉最好水平,从半年的生产情况来看,高炉各项指标良好(见表1)。
2设计采用的新技术及其特点针对宝钢原有高炉一些实际操作中的问题,结合国内外的炼铁技术进展,在4号高炉的设计过程中,采用了41项新技术。
主要有:紧凑的总图布局、旋转布料器加固定料罐的串罐中心卸料式无料钟、炉缸高挂渣性能的热压小炭砖耐材、冷却壁与冷却壁板结合的全炉身冷却型式、国内集成的喷煤技术、新英巴法转鼓水渣处理工艺、环缝洗涤煤气系统、平坦化出铁场等新型实用技术。
2.1 总图布置由于受建设场地的限制,4号高炉厂区用地面积仅为13.96万m2。
为了不影响现有生产设施,保证物流顺畅,为一代炉龄后的大修留出施工通道,设计时采用了如下方法:(1)结合场地条件,采用半岛式布置,同类成组紧凑安排;(2)管线尽量平行于建筑物和道路布置;(3)场地狭窄和管网密集地段采用管廊。
- 1、下载文档前请自行甄别文档内容的完整性,平台不提供额外的编辑、内容补充、找答案等附加服务。
- 2、"仅部分预览"的文档,不可在线预览部分如存在完整性等问题,可反馈申请退款(可完整预览的文档不适用该条件!)。
- 3、如文档侵犯您的权益,请联系客服反馈,我们会尽快为您处理(人工客服工作时间:9:00-18:30)。
圆方坯产线
两套吹氩系统,即钢包底吹氩系统和事故枪顶吹氩系统; 钢包底吹氩系统氩气管路由LF钢包台车上的自动吹氩接头与钢包连接; 氩气经安装于钢包底部的两只透气砖(狭缝式)吹入钢水中,每只透气 砖的最大气体流量为600Nl/min; 在LF处理的不同阶段设定不同的吹氩流量(吹氩模式),会在钢水温度 及成分均匀、脱硫与脱氧、去除夹杂等方面取得很好的效果; 事故顶枪系统在底吹氩系统不能正常工作时使用,如底吹氩系统失效时 进行紧急处理,底吹流量无或低(透气砖堵塞)时利用事故枪顶吹以使 底吹恢复正常。
帘线处理
为电炉与连铸的匹配提供时间弹性、保证
Ar
多炉连浇
1 供电特点
圆方坯产线
本座LF炉由一台容量为22MVA的变压器提供三相交流电,三根电极可单 独调节;
―
电极液压系统由驻留于 PLC 中的标准软件包进行控制,即电极控制单元
(ECU ),可实现电极升降的快速响应,减少钢水“舔”电极而导致增
电炉厂圆方坯产线于1996年12月建成投产,具有100万吨钢水、96万吨的 年生产能力。产品的规格为178mm, 153mm圆坯及 160mm方坯。圆坯 的主要钢种为各类油井管、锅炉管及普通结构管用钢(主要供无缝钢管厂); 方坯钢种主要为弹簧钢、各类高强度低合金钢、预应力建筑钢筋、高碳
钢、钢绞线钢及汽车轮胎钢帘线用钢等(主要供高速线材厂及外供)。
在100m3储存仓下部安装4台Rotofeeders,每座炉壳配备两个Rotofeeders,通 过调节电机速度可在设计的流量范围内(10—50kg/min)实现无级调速,能按 照智能炼钢的要求,与氧枪同步实现自动化。
1
圆方坯产线
LF处理
LF用来加热钢水,吹氩用来均匀钢水成份 和温度。LF钢包炉既可以与电炉配合以取 代电炉的还原期,还可以配合生产各种优质
1
圆方坯产线
1
圆方坯产线
一电二炉
工艺流程
连铸机
炉外精炼
真空脱气
圆、方坯
1 电炉设备参数
圆方坯产线
µ» ç ¡Â ¯µ ÄÖ ÷Ò ª¼Ê õ² ÎÊ ù í ±1 ç µ ¯¸ «³ ÆÈ ÝÁ ¿ 150 Ö ¶ ô· Á ÖÁ ¿ 40 Ö ¶ 99MVA äÑ ± ¸Æ ÷È ÝÁ ¿ 3 ³µ µ ç¼ «· ùÊ ù 711 mm ¯Ä Ê «µ ç¼ «Ö ±¾ ¶ ö· ³ Ö² ½Ê ½ «Ð Æ Ä ¯µ ³³ ö· Ö¨ £ EBT© £
钢种。
将石墨电极降低到钢渣面以下,可以使钢水
以每分种3°C 的一个缓 冲作用。
1
圆方坯产线
LF设备组成
1——电极加热系统; 2——铁合金投料系统;
3——底吹搅拌系统;
4——水冷炉盖; 5——除尘系统;
6——事故顶枪系统;
7——喂丝系统; 8——装有透气塞的钢包;
2015-6-4
1
圆方坯产线
1
圆方坯产线
电炉主要设备
重要控制系统及功能
• 多功能集束射流枪
每座炉体安装四套多功能氧枪,一套EBT氧枪。每一套氧枪水冷底板上装有主 氧枪、环焦炉煤气、环氧气、碳粉枪和后燃烧枪。 • 氧气和煤气的控制阀架 控制阀架根据电炉冶炼要求准确地显示和控制Cojet氧枪的主氧、辅助氧气、 二次燃烧氧气和焦炉煤气的流量、压力和温度,实现各种不同的功能或功能组 合。 • 碳粉输送及喷吹系统
碳;
―
变压器二次侧共有 13级抽头,每级抽头又有6 个电流设定值,因此功率
范围很宽,操作过程中可根据精炼不同阶段的特点及炉渣状况选择不同
的电压级数和电流值,实现优化的电能输入,获得更好的埋弧效果(配 合自主开发的LF埋弧渣),从而减轻钢包耐材损耗、提高热效率、降低
电极消耗和噪音。
1 吹氩特点
― ― ―
参数
150 90 1200 457 750 4 300 28 22(可过载20%) 220-350 13 40-50
1
圆方坯产线
工艺效果
加热升温并准确控制钢水温度 微调、均匀钢水成分和温度
深脱硫功能:成品〔S〕≤10ppm
深脱氧功能:成品〔O〕≤15ppm 去除夹杂物、控制夹杂物形态:钢
1
圆方坯产线
工艺流程
钢包吊运并接氩 吊运至连铸
测温取样
喂丝,停止吹氩
盖上真空盖
测温取样/氧/定氢
抽真空
成分微调
加合金
提盖盖车开出
破真空
1
圆方坯产线
功能特点
有效的脱气(降低钢液中[H]、[N]含量)温度 脱氧(通过C-O反应去除钢液中的[O])
深脱硫通过碱性渣与钢水的反应脱[S]
通过合金微调及吹氩控制钢液成份和温度
宝钢钢管条钢事业部电炉厂
生产工艺介绍
电炉厂
2014年9月
炼钢厂区域图
电炉
电炉厂所处位置
•
电炉与转炉炼钢的区别: – 投资方面:转炉投资大,流程长,电炉投资小,流程短; – 原料方面:转炉以铁水为主要原料,电炉以废钢为主要原料; – 能源方面:转炉以铁水的物理热和化学热为能源,电炉主要以电能为能源; – 冶炼钢种方面:传统意义上,转炉以铁水的物理热和化学热为能源,因能 量有限,以冶炼普碳钢为主,电炉则因以电能为主要能源,可冶炼合金钢 和高合金钢,电炉可冶炼更多的钢种,另外因电炉冶炼有还原期,电炉钢 的质量要优于转炉钢。但随着炉外精炼及铁水预处理的发展,电炉冶炼钢 种及质量方面已无明显优势。
6(从大气压到66.7pa) 66.7 40 15 Ø6400*6700 30
10 11
※
真空抽气系统共有 9 只蒸汽喷射泵,布置成五级串联式,可按低抽 气模式和高抽气模式进行抽真空作业。
※
各级泵投入基准: 真空开始:蒸汽压力>8bar。 – 步1:真空度≥190mbar,<1013mbar,5级泵投入 – 步2:真空度≥75mbar,<190mbar,4级泵投入 – 步3:真空度≥15mbar,<75mbar,3级泵投入 – 步4:真空度≥4mbar,<15mbar,2级泵投入 – 步5:真空度<4mbar到0.3~0.6mbar,1级泵投入
1 喂丝工艺
将比较轻、易氧化、
圆方坯产线
易挥发的合金元素制成包
芯线或实心线快速输入钢
液。在钢液深处熔化溶解
,从而达到脱氧、脱硫、 改变夹杂物形态。实现成 份微调等冶金目的。
主要参数 项
流数 实芯丝直径
目
单位
流 mm
参
4
数
Φ5~13
包芯丝直径
实际工作压力 喂丝速度
mm
Mpa m/min
Φ5~16
2015-6-4
工艺流程
1
圆方坯产线
2
大方坯产线
1
圆方坯产线
电炉厂圆方坯产线是宝钢三期工程之一,主要装备有:一电两炉的150t
超高功率直流电弧炉、150tLF炉、VD炉及圆方坯兼容的六流弧形连铸机, 主要装备中,直流电弧炉由法国CLECM公司设计,而LF、VD及连铸系 统则由意大利DANIELI公司设计。
1
圆方坯产线
项目
设备工艺参数
项目
设备工艺参数
炉座形式
一电两炉
留钢量
35吨
电炉公称容量
150吨
炉膛内容积
180m3
炉壳直径
7300mm
额定二次侧电压
670V
变压器公称容量
99MVA
碳粉喷吹罐
4个
石墨电极直径
711mm
Cojet主氧气流量
3180Nm3/h×4
1
泡沫渣操作:
圆方坯产线
超高功率电弧炉采用大电压长弧供电,如无泡沫渣埋弧操作,电弧热
1
圆方坯产线
Õ æ¿ ÕÍ ÑÆ ÷³ °Ö õ ÄÖ ÷Ò ª¼Ê õ² ÎÊ ù í ±3 Õ æ¿ ÕÍ ÑÆ ÷³ °Ö ÃÐ ÍÊ ½ ÞÊ ¸ ½ æ¿ Õ Õ³ éÆ ÷Ä ÜÁ ¦ 320 kg/Hr¨ £ 0.5 × ±Ê ±£ © 40 Pa «Ï ¼ ÞÕ æ¿ Õ¶ È æ¿ Õ Õ± ÃÐ ÍÊ ½ 5¼ ¶Õ ôÆ øÅ çÉ ä± Ã 66.7 Pa ¤³ ¸ ÷Õ æ¿ Õ¶ È éÆ ³ ÷Ë Ø¶ È 6² ÖÖ Ó£ ¨´ Ó´ óÆ ÷Ñ ¸µ ½ 66.7 Pa© £
1 脱气特点
※
圆方坯产线
本台VD配备有Hydris在线定氢仪,快速方便,数据的稳定性及重现性
好。
※
早期认为 VD 脱氮效果不好,但后来的实践与研究表明, VD 处理同样 可具有良好的脱氮能力。
※
实践表明VD脱氮率还与钢中成份有关,一般情况下Ti、Cr等元素会降
低VD脱氮率,降低钢中的硫含量则会明显提高脱氮率。
通过吹氩及CO、H2气泡使夹杂物集聚并上浮
1
圆方坯产线
设备组成
VD真空系统设备主要包括:真空罐 和盖车系统、废气冷却除尘系统、真空 抽气系统、蒸汽蓄热器和除氧系统、底 吹搅拌系统、投料系统、喂丝系统、氮
气系统、压缩空气系统、真空测量系统、
TV摄像监视和电气控制等。
1
圆方坯产线
装备特点
真空特性
※
脱气过程还与真空保持时间有关。一般情况下高真空时间超过 13分钟即 能满足[H]<2ppm的要求,对于低氮钢要适当延长高真空时间,目前主要 根据钢种的氮含量要求确定VD的高真空保持时间。
※
VD终点气体含量与初始气体含量亦有关系;合理的吹氩制度对脱气效果 的好坏有直接的影响,吹氩强度提高,可加快脱气过程。
量会辐射到炉盖、炉壁,不仅热效率低,对耐材、水冷炉壁也会造成严重
的侵蚀,可以说有了泡沫渣埋弧操作,才使得超高功率电弧炉的大电压长 弧供电成为可能。泡沫渣埋弧操作还能屏蔽电炉噪音,从而大大改善操作