75_硅铁电炉极心圆直径与电气参数的关系
高纯硅铁技术操作规程

高纯硅铁技术操作规程(12500kV A敞口电炉)1 成品规格1.1技术要求1.1.1高纯硅铁按杂质含量,分为如下几个牌号,其化学成份应符合表1规定。
1.1.2需方如对化学成份有特殊要求,可与供方另行协商供货。
1.2物理状态1.2.1高纯硅铁浇注厚度:各种规格高纯硅铁浇注的铁锭厚度不得超过100mm,每炉的偏析不大于4%。
1.2.2高纯硅铁供货粒度按表2规定。
1.2.3需方对供货粒度有特殊要求,可与供方协商解决。
2 原料技术条件冶炼高纯硅铁所用的原料有硅石、碳质还原剂(兰炭、石油焦、煤、木块等)、铁料(铁鳞、钢屑、硅钢屑等)。
2.1硅石2.1.1化学成份SiO2≥99%,Al2O3≤1.0%,P2O5≤0.02%,Ti≤0.02%,其它杂质总和小于1.0%。
2.1.2物理性质2.1.2.1硅石表面应清洁,不粘有泥土等杂质,入炉前一定要水洗干净。
2.1.2.2硅石要有足够高的机械强度和良好的高温抗爆性,通常抗爆率不应低于80%。
2.1.2.3硅石的粒度为60-120mm。
2.1.3不同产地的硅石应分开存放。
2.2碳质还原剂2.2.1化学成份石油焦:固定碳≥86%,灰份≤1%,挥发份≤13%。
兰碳:固定碳≥85%,灰份≤6%,挥发份≤9%。
2.2.2物理性质石油焦:粒度0-15mm,不得有外来夹杂。
兰炭:粒度5-18mm,不得混有外来夹杂。
木块:粒度≤100mm的硬杂木。
不同产地的碳质还原剂应分别存放。
2.3铁料2.3.1冶炼高纯硅铁的铁料为铁鳞、钢屑、硅钢屑等,不准含有有色金属屑、鳞、铸铁屑、鳞和合金钢屑、鳞等,不准用生锈严重的钢屑和铁鳞,钢屑长度不应超过100mm,铁料应清洁,不得有明显的外来夹杂。
3 精炼剂3.1生产高纯硅铁使用的精炼剂有石英砂、硅石粉、石灰粉、萤石粉、工业碱、铁鳞、铁精矿等。
3.2精炼剂的粒度:石灰小于10mm,其它均小于5mm。
3.3精炼剂按要按技术人员规定的比例配制,并混合均匀。
25000KVA硅铁电炉开炉方案
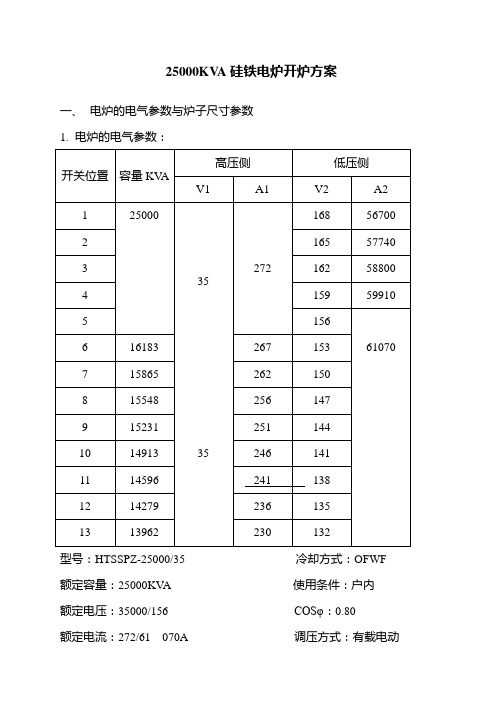
25000KV A硅铁电炉开炉方案一、电炉的电气参数与炉子尺寸参数1.电炉的电气参数:型号:HTSSPZ-25000/35 冷却方式:OFWF 额定容量:25000KV A 使用条件:户内额定电压:35000/156 COSφ:0.80额定电流:272/61 070A 调压方式:有载电动相数:3 有功功率:0.84 连接标号:2、电炉的尺寸参数及功率密度3、电炉其它参数3、1电极采用组合把持器。
3、2电极工作行程:1000mm3、3电极最大行程:2100mm3、4烟道直径:φ 2200mm3、5烟道高度:26 m3、6料管直径:φ400 mm3、7冷却水用量:270 t/h二、烘炉1、烘炉前的准备工作1、1电炉的供电、导电系统、电极升降、压放系统等机电设备,冷却系统均要进行检查和试车,所有设备经空载和有载(小负荷)运转正常方可烘炉。
由于是冬季开炉,一定要作到在投料后少出现事故。
1、2炉底中心、极心圆圆心和炉盖中心必须处于同一垂直线上(偏差小于15mm)方可烘炉。
1、3准备好炉上、炉下使用的各种工具以及两个干燥好的铁水包。
1、4准备烘炉木材4吨,及40吨大块冶金焦(φ100 mmφ200mm)1、5电极糊采用密闭糊,要求糊块度小于100 mm,粉末筛除。
1、6每根电极下平铺黏土砖三层,电极座在其上。
1、7导电元件下沿距炉口平面250—300 mm。
1、8电极压放的系统处于上限200 mm左右。
1、9每根电极用22 mm的圆钢做一个焦烘铁笼高1900mm,纵向间距35 mm 每400mm高焊接固定带,两个半笼组合,便于拉出,1、10外露电极壳用电钻或电焊机打φ5-6mm的孔,每个孔距大约100mm,便于挥发物挥发。
1、11装电极糊糊柱高度应至保护屏上沿500mm,经常监测,专人负责。
1、12炉底用细缝糊涂一层厚10 mm的保护层,炉墙碳砖外露部分砌一层黏土砖,避免氧化。
1、13将把持器冷却水量控制在正常水量的1/4,电极冷却风机停开。
矿热炉的基本原理

发布时间:2011-4-27 10:04:46 浏览量:40【字体:大中小]矿热炉的基本原理、构造及部分参数矿热炉的基本原理、构造及部分参数(1 )电耗值随原料成分,制成品成分,电炉容量等的不同而有很大差异。
这里是约值。
(二): 结构特点矿热炉是一种耗电量巨大的工业电炉。
主要由炉壳,炉盖、炉衬、短网,水冷系统,排烟系统,除尘系统,电极壳,电极压放及升降系统,上下料系统,把持器,烧穿器,液压系统,矿热炉变压器及各种电器设备等组成。
根据矿热炉的结构特点以及工作特点,矿热炉的系统电抗的70%是由短网系统产生的,而短网是一个大电流工作的系统,最大电流可以达到上万安培,因此短网的性能决定了矿热炉的性能,正是由于这个原因,因此矿热炉的自然功率因数很难达到以上,绝大多数的炉子的自然功率因数都在〜之间,较低的功率因数不仅使变压器的效率下降,消耗大量的无用功,且被电力部分加收额外的电力罚款,同时由于电极的人工控制以及堆料的工艺,导致三相间的电力不平衡加大,最高不平衡度可以达到20% 以上,这导致冶炼效率的低下,电费增高,因此提高短网的功率因数,降低电网不平衡就成了降低能耗,提高冶炼效率的有效手段。
如果采取适当的手段,提高短网功率因数,可以达到以下的效果:(1)降低电耗5〜20%(2)提高产量5%〜1%以上。
从而给企业带来良好的经济效益,而投入的改造费用将可以在节约的电费中短期内收回。
三:方法及原理一般情况下为了解决矿热炉功率因数低下的问题,我国目前一般采用电容补偿的方式来解决,通常是在高压端进行无功补偿,但是由于高压端补偿不能解决三相平衡的问题,而且由于短网的感抗占整个系统感抗的70%以上,因此高压端补偿并没有达到降低短网系统感抗,提高短网功率因数。
增加变压器出力的目的,仅仅是对供电部门有意义。
因此目前也有部分单位在新建炉子上采取了高低压同时进行无功补偿的措施,来解决以上的问题,在短网端进行补偿能够大幅提高短网端的功率因数,降低电耗,针对炉变低压侧短网的大量无功消耗和不平衡性,兼顾有效提高功率因数而实施无功就地补偿技术改造,从技术上来讲是可靠、成熟的,从经济上来讲,投入和产出是成正比的。
12.5 MVA硅铁炉极心圆参数的探讨

第16卷Vol16增刊重庆工业高等专科学校学报JournalofChongqingPolytechnicCollege2001年10月Oct.200112.5MVA硅铁炉极心圆参数的探讨熊明森谢泽强(重钢集团铁舍垒有限责任公司,重庆401220)摘要:简要分析电炉极。
圆直径与炉料电阻的关系,极。
圆直径大小对炉内功率分布及热分布的影响,结合我公司12.5MVA硅铁炉极心圆直径长期探索,指出12.5MVA硅铁炉极·e.2囤直径在2.60一2.65m较合适,且能取得良好经济技术指标。
关键词:极。
圆;炉料电阻;功率分布中图分类号:TF3412文献标识码:文章编号:1009—3494(2001)SO一0108—02电炉参数合理确定,是电炉设备高效率生产的基本前提。
大量生产实践表明:电炉参数选择主要是正确确定极心圆直径D搬,电炉生产技术指标的好坏与极心圆选择合理与否关系极大。
硅铁是铁合金中产量和耗能最大的品种,如何选择合适的极心圆,从而达到增大炉料电阻、炉内功率和热分布均匀,提高硅铁电炉的效率,达到优质、高产和低耗的目的,已成为硅铁技术生产者探索的重要课题。
l极心圆直径与炉料电阻的关系据文献“介绍硅铁炉炉内等效电路及简化电路如图1,熔池电阻R。
,即电极下端反应区电阻,它主要取决于极下端至炉底距离及反应区直径与该区的温度。
炉料电阻R“,指未熔化的炉料区电阻,它主要决定于炉料的组成,电极插入炉料的深度及电极间距,当然也与该区温度有关。
通常情况下炉料电阻远比熔池电阻大,为了寻找炉料电阻与极心圆直径的关系,现假设L为电极间中心距,d为电极直径,^为电极插入炉料深度,S为炉料圆柱形侧面积,to为电阻半,』Y为炉料圆柱侧面至电极轴心距、^离。
D*与L的关系L=等D&,根据欧姆定律R#:掣则3枷”=舞….(1),对(1)积分R¨:『笔等(令x:{一罢则R#=ii烹=景zn詈删R。
=焘InU-等,即“:历而。
硅铁合金冶炼岗位试题600题
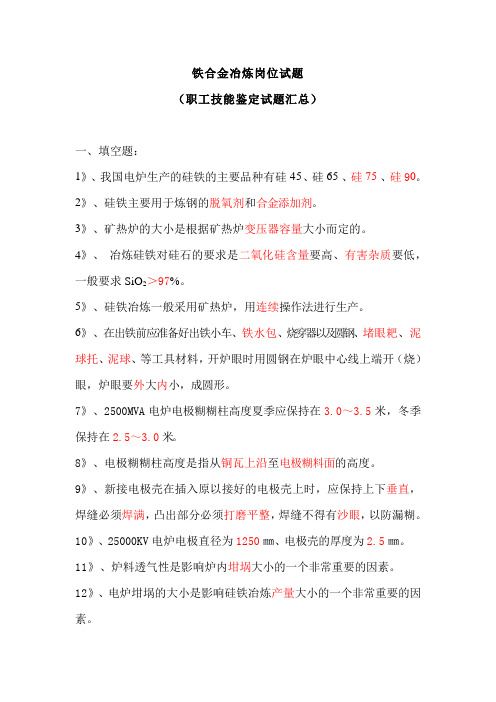
铁合金冶炼岗位试题(职工技能鉴定试题汇总)一、填空题:1》、我国电炉生产的硅铁的主要品种有硅45、硅65 、硅75 、硅90。
2》、硅铁主要用于炼钢的脱氧剂和合金添加剂。
3》、矿热炉的大小是根据矿热炉变压器容量大小而定的。
4》、冶炼硅铁对硅石的要求是二氧化硅含量要高、有害杂质要低,一般要求SiO2>97%。
5》、硅铁冶炼一般采用矿热炉,用连续操作法进行生产。
6》、在出铁前应准备好出铁小车、铁水包、烧穿器以及圆钢、堵眼耙、泥球托、泥球、等工具材料,开炉眼时用圆钢在炉眼中心线上端开(烧)眼,炉眼要外大内小,成圆形。
7》、2500MVA电炉电极糊糊柱高度夏季应保持在3.0~3.5米,冬季保持在2.5~3.0米。
8》、电极糊糊柱高度是指从铜瓦上沿至电极糊料面的高度。
9》、新接电极壳在插入原以接好的电极壳上时,应保持上下垂直,焊缝必须焊满,凸出部分必须打磨平整,焊缝不得有沙眼,以防漏糊。
10》、25000KV电炉电极直径为1250㎜、电极壳的厚度为2.5㎜。
11》、炉料透气性是影响炉内坩埚大小的一个非常重要的因素。
12》、电炉坩埚的大小是影响硅铁冶炼产量大小的一个非常重要的因素。
13》、自焙电极在焙烧过程中强度逐渐增加,但温度从200℃加热到400℃时,电极变软,机械强度在下降。
14》、自焙电极在焙烧过程中强度逐渐增加,当电极温度从400℃上升到700℃时,电极的机械强度急剧上升到最大值。
15》、冶炼硅铁对焦炭的要求是固定碳含量要高灰分要低电阻率要高、气孔率要大、水分波动要小、反应性能要好,高温下有一定的机械强度。
16》、焦炭灰分高低会严重影响硅铁的质量和技术经济指标。
因此,要求焦炭灰分越低越好,一般要求焦炭灰分<1417》、在电极周围所堆成的一种锥形料面,习惯上成为:锥体18》、炭质电极按其加工制作工艺不同可分为、石墨电极、炭素电极和自焙电极。
19》、自焙电极的特点是:边使用、边成型、边烧结、边接长。
20》、矿热炉生产硅铁、硅铬、硅锰等铁合金都采用自焙电极。
12. 5MVA 硅铁炉极心圆参数的探讨
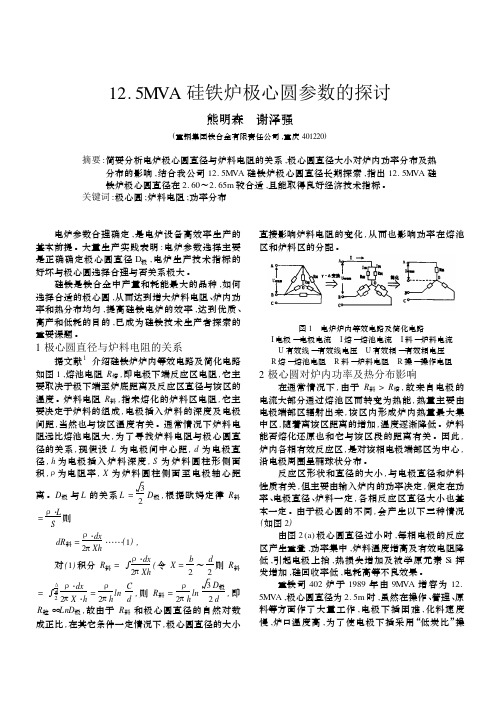
在通常情况下 , 由于 R料 > R熔 , 故来自电极的 电流大部分通过熔池区而转变为热能 , 热量主要由 电极端部区辐射出来 , 该区内形成炉内热量最大集 中区 ,随着离该区距离的增加 ,温度逐渐降低 。炉料 能否熔化还原也和它与该区段的距离有关 。因此 , 炉内各相有效反应区 ,是对该相电极端部区为中心 , 沿电极周围呈椭球状分布 。
反应区形状和直径的大小 , 与电极直径和炉料 性质有关 ,但主要由输入炉内的功率决定 ,假定在功 率 、电极直径 、炉料一定 , 各相反应区直径大小也基 本一定 。由于极心圆的不同 , 会产生以下三种情况 (如图 2)
由图 2 (a) 极心圆直径过小时 ,每相电极的反应 区产生重叠 ,功率集中 ,炉料温度增高及有效电阻降 低 ,引起电极上抬 ,热损失增加及被学原元素 Si 挥 发增加 ,硅回收率低 ,电耗高等不良效果 。
极心圆直径过大 ,炉内三相电极下部反应区自成独 立坩埚 ,不能相互连通 ,这势必导致炉内整个反应容
积功率降低 ;炉心化料慢 ,甚至在炉心炉料堆积 ;炉
子发凉 ,炉内化学反应气氛呆滞 ;电极下插困难 ,刺
火频率高 ,硅铁挥发损失大 ,电耗高 ,产量不理想 ,我 们可从表 1 的正交数据比较及表 3 炉况正交数据比
成正比 ,在其它条件一定情况下 ,极心圆直径的大小
直接影响炉料电阻的变化 , 从而也影响功率在熔池 区和炉料区的分配 。
图 1 电炉炉内等效电路及简化电路 I 电极 —电极电流 I 熔 —熔池电流 I 料 —炉料电流
U 有效线 —有效线电压 U 有效相 —有效相电压 R 熔 —熔池电阻 R 料 —炉料电阻 R 操 —操作电阻
熊明森 谢泽强
(重钢集团铁合金有限责任公司 ,重庆 401220)
硅铁电弧炉的电路分析
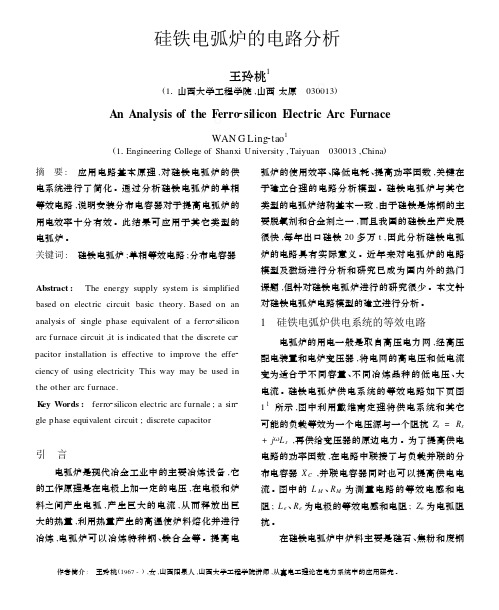
电弧炉是现代冶金工业中的主要冶炼设备 ,它 的工作原理是在电极上加一定的电压 ,在电极和炉 料之间产生电弧 ,产生巨大的电流 ,从而释放出巨 大的热量 ,利用热量产生的高温使炉料熔化并进行 冶炼 ,电弧炉可以冶炼特种钢 、铁合金等 。提高电
弧炉的使用效率 、降低电耗 、提高功率因数 ,关键在 于建立合理的电路分析模型 。硅铁电弧炉与其它 类型的电弧炉结构基本一致 ,由于硅铁是炼钢的主 要脱氧剂和合金剂之一 ,而且我国的硅铁生产发展 很快 ,每年出口硅铁 20 多万 t ,因此分析硅铁电弧 炉的电路具有实际意义 。近年来对电弧炉的电路 模型及磁场进行分析和研究已成为国内外的热门 课题 ,但针对硅铁电弧炉进行的研究很少 。本文针 对硅铁电弧炉电路模型的建立进行分析 。
硅铁电弧炉的电路分析
王玲桃1
(11 山西大学工程学院 ,山西 太原 030013)
An Analysis of the Ferro2sil icon Electric Arc Furnace
WAN G Ling2tao1
(11Engineering College of Shanxi U niversity , Taiyuan 030013 ,China)
11. 56°kA
电弧电流 :
Ia
=
Zc Zc + ( Zf +
Za)
I
= 78. 17 ∠-
18. 12°kA
电 弧 电 压 : V a = ZaI a = 282. 43 ∠- 13. 23°V
三相电源功率 : Ps = 3 EIcos11. 56°= 83. 82 MW 三相电弧功率 : Pa = 3 V aIacosφa = 65. 99 MW
3 计算实例
硅铁冶炼考试题答案
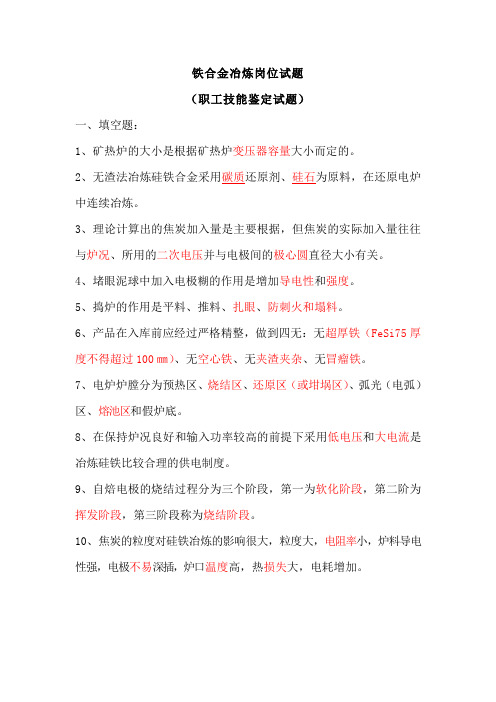
铁合金冶炼岗位试题(职工技能鉴定试题)一、填空题:1、矿热炉的大小是根据矿热炉变压器容量大小而定的。
2、无渣法冶炼硅铁合金采用碳质还原剂、硅石为原料,在还原电炉中连续冶炼。
3、理论计算出的焦炭加入量是主要根据,但焦炭的实际加入量往往与炉况、所用的二次电压并与电极间的极心圆直径大小有关。
4、堵眼泥球中加入电极糊的作用是增加导电性和强度。
5、捣炉的作用是平料、推料、扎眼、防刺火和塌料。
6、产品在入库前应经过严格精整,做到四无:无超厚铁(FeSi75厚度不得超过100㎜)、无空心铁、无夹渣夹杂、无冒瘤铁。
7、电炉炉膛分为预热区、烧结区、还原区(或坩埚区)、弧光(电弧)区、熔池区和假炉底。
8、在保持炉况良好和输入功率较高的前提下采用低电压和大电流是冶炼硅铁比较合理的供电制度。
9、自焙电极的烧结过程分为三个阶段,第一为软化阶段,第二阶为挥发阶段,第三阶段称为烧结阶段。
10、焦炭的粒度对硅铁冶炼的影响很大,粒度大,电阻率小,炉料导电性强,电极不易深插,炉口温度高,热损失大,电耗增加。
二、判断题:1、炉况发粘时,应适当减少焦炭的配入量。
答案:(×)2、电极插入炉料较浅时,可适当附加一些焦炭。
答案:(×)3、同容量的矿热炉,其极心圆直径较大时,焦炭加入量应多一些。
答案:(√)4、硅铁冶炼的基本反应,是利用铁质还原剂中的铁将硅石中二氧化硅中的硅还原出来的反应。
答案:(×)5、电极深插到炉料中,可提高炉温和扩大坩埚。
答案:(√)6、料面控制过低,电极插入炉料较深,但由于料层薄,容易塌料,甚至产生露弧现象,热损失大。
答案:(√)7、焦炭的粒度大、表面积增大,增加炉料的接触面积,炉料的电阻大,则电极可以插入炉料较深。
答案:(×)8、捣炉是挑翻炉内粘结大块的炉料和料面的烧结区,以增加料面的透气性,扩大坩埚。
答案:(√)9、长时间停炉送电后,电极不能上下活动,根据炉况恢复情况压放电极。
硅铁炉

4000kVA硅铁矿热炉技术规格书一、硅铁的用途硅铁是炼钢工业中必不可少的脱氧剂,也作为合金剂添加。
在炼钢工业中,每生产1t钢大约消耗3-5kg 75%硅铁。
二、 4000kVA电炉主要参数1.电极直径:φ680mm2.炉壳直径:φ5300mm3.炉膛直径:φ3800mm4.炉膛深度:1800mm5.炉壳高度:3400mm6.极心圆直径:φ1800±50mm7.电极工作行程:1000mm8.电极检修行程:1600mm9.出铁口:2个10.变压器额定容量:4000kVA11.一次侧电压:35KV12.二次侧额定电流:20620A13.二次电压:100\104\108\112\116\120\125V二次常用电压 112V100-112V恒电流 112-125V恒功率三、主要技术经济指标:1.冶炼电耗(75%硅铁):8500-8800kWh/t2.动力用电:250-300 kWh/t3.年工作天数:340-3454.产品合格率:>99.5%5.元素回收率: 90%-92%6.入炉料品位:SiO2>97%四、主要原材料消耗(75%硅铁):1.硅石:1780-1850kg/t2.焦碳:890-930kg/t3.钢屑:220-230 kg/t4.电极糊:45-55 kg/t5.电极壳:3-6 kg/t6.锭模及渣罐:15-20 kg/t7.耐火材料:15-25 kg/t8.功率因数cosф:0.85-0.88五、日产量:7.5t六、主体设备简介:本设计选用矮烟罩半封闭固定式炉型,使4000KVA硅铁炉设备先进、工艺合理,主要设备简介如下:1.炉体:炉壳采用δ16钢板焊接成圆柱体,炉底采用δ20钢板并用工字钢(25#)支撑在基础上,自然通风冷却炉底。
炉衬采用耐火砖(轻质粘土砖,重质粘土砖,高铝砖),炉底炉圈采用碳砖砌筑,砖缝用电极粉、矿粉的混合物填充。
2.矮烟罩:采用20#槽钢制作水冷骨架;立柱采用φ159钢管;烟罩上盖由耐热混凝土浇注,矮烟罩侧壁采用耐火砖砌筑。
铁合金电炉设备合理参数的选择与计算

铁合金电炉设备合理参数的选择与计算 电炉通常分为三类:电弧炉’电弧电阻炉’电阻炉.除对碳含量要求较低碳微碳产品外绝大部分粗炼产品的生产都是用电弧电阻炉---矿石电热还原炉,通常称矿热炉进行生产.炉子连续作业使用低电压大电流的操作方法,功率一般在冶炼中保持变.矿热炉一般以碳质材料<有时也用镁质的>做内用自培电极,采用埋弧连续作业.一般用碳质还原剂,通过电弧电阻加热产生高温将矿物中有用的氧化物还愿成金属组成合金.炉用变压器小于5000KVA为小容量电炉,小于10000KVA为中容量电炉.大于己于10000KVA的为大容量电炉.按电极分成单相一根电极电炉,单相三根电极电炉,三相长方形电炉,三相园形电炉,三相六根电极电炉.一.矿热炉参数计算新方法计算公式及计算步骤<适用于硅75电炉>1.已知设计产量G<吨/日>2.计算熔池冶炼功率P熔池P熔池=G/0.0031<KW>3.功率密度变量r=a+bP熔池当P熔池≤5000KW时r=0.0502+7.3×10.-6P熔池<KW/CM2>当P熔池>5000KW时r=0.092+1×10-6P熔池<KW/CM2>4.电极直经D电D电=( P熔池x102/3πr)1/2毫米5.电极常用工作电压V2=a1+b. P熔池当P熔池≤3420KW时V2=69.5+0.011P熔池<V>当P熔池>3420KW时V2=97.6+0.0053P熔池<V>6.电极极心圆直经D极心当P熔池≤3420KW时D极心=2.4 D电+1.283<V2-36>毫米当P熔池>3420KW时D极心=2.4 D电+0.642<V2-36>毫米7.电极中心间距L=0.866 D极心 <mm>电炉熔池工作电阻<操作电阻>R操=K’.10/πD电<Ω>式中D电-----电极直径<mm>K’----电阻变量K’=<﹙ρ1-ρ2﹚/﹛﹙ρ2+﹙ρ2-X’﹚/Lnl’/D电﹜>1/2<Ω/cm>式中ρ1,ρ2值根据冶炼品种分别实测求得的.ρ1熔容炉料及金属液平均比电阻<Ω/cm>ρ2热炉料平均比电阻<Ω/cm>l’两电极中心距离<cm>X’电极插入炉料深. 对硅 75配料正常情况下ρ1=10<Ω/cm>. ρ2=0.5<Ω/cm> 所以硅75 K’=﹙ρ1-ρ2﹚÷﹛﹙ρ2+﹙ρ2-X’﹚÷Lnl’/D电﹜当P熔池≤5000KW时X’=0.42+5.5×10-5P熔池当P熔池>5000KW时X’=0.542+2.5×10-5P熔池11.电炉总电阻R总=R操+R损<Ω>12.电炉总电抗X总=a2±b2 P熔池当P熔池≤6900KW时X’总=0.0019-1.6×10-7P熔池<Ω>当P熔池>6900KW时X’总=0.0083+5.4×10-9P熔池<Ω>13.功率因数cosΦ=R总/(R2总+X2总)½14.电效率η= R操/R总15.变压器容量S=3I2 R操/<ηcosΦ.1000><KVA>16.有功攻率P有=S. cosΦ<KW>.17.校核电炉有功功率P有= P熔池+P损=<3I2 R操+3I2 R损>/1000<KW>18.电炉无功功率Q=3I2 X总/1000<千乏>19.电极电流密度δ=4I电极102/πD2〈A/CM2〉校核δ值δ=6.545-4.7×10-5 P熔池〈A/CM2〉允许误差P熔池〈32000KWδ=0.5〈A/CM2〉P熔池〉32000KWδ=0.9〈A/CM2〉20.电流电压比δ=I电极/V21.炉膛直径D膛=1.866D极心+1.1D电〈mm〉22.炉膛深度H=β.D电<mm>β为系数冶炼硅铁取2.1-1.9.23.电极极心圆单位面积功率P1=4P有.106/πD2极心<KW/M2>24.炉膛单位面积功率P2=4P有.106/πD2膛<KW/M2>25.炉膛单位面积功率P3=4P有.109/πD2极心H<KW/M3>26.单位产品冶炼电耗A=24P有/G<KW.h/T>通过这公式可以看到:<1>从炉内操作电阻公式: R操=K’/πD电和K’=ρ1ρ2/<ρ2+3ρ1X’/(lnl’/D电)>中得知炉内操作电阻与电极直经成反比例.当电炉容量增大时炉内电阻值减少,所以大容量电炉更要注意增大炉内电阻否则造成操作困难.<2>对现有电炉而言选择比电阻大的还原剂,对增大K’值,提高R 操是有利的,这样电极还能深插料层,使高温区下移,热损失减少,能收到较好的效果,因此是降低电耗的重要途径.<3>随着电炉容量的增加cosφ则明显减小,设计时要设法降低炉子电抗以提高cosφ.二.常规计算方法1.变压器容量的选择S=GA/24cosφK1K2K3S---变压器容量<KVA>G---要求的电炉日产水平<吨/日>A---冶炼产品的单位电耗<度/吨>cosφ:功率因数. 主要取决于炉子大小及短网配置情况,一般中小炉子取0.8—0.95炉子越小cosφ越高.K1:实际工作时变压器利用系数,决定冶炼方法.连续作业取0.98,间歇作业取0.8.K2:实际工作时间与日历时间之比,主要取决于炉子工作情况,硅铁取0.96,碳素铬铁取0.93.K3:供电线路上实际供给的平均电压与额定电压之比一般取0.95.。
电炉(矿热炉)炉膛温度、功率密度、三相电极功率分布特性与电极插入深度分析及控制措施
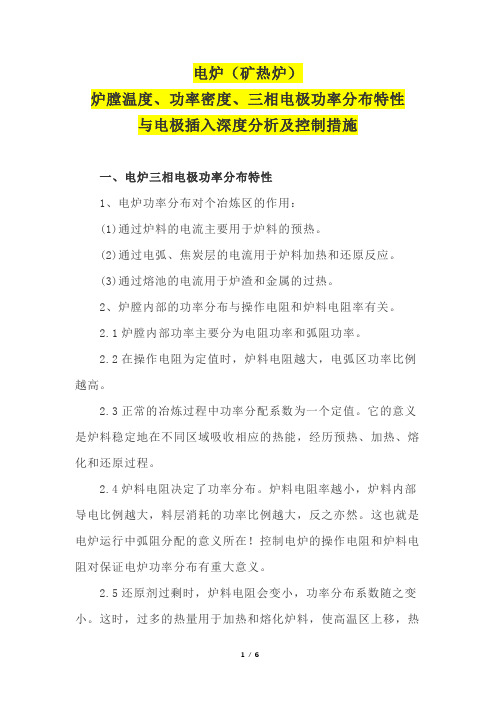
电炉(矿热炉)炉膛温度、功率密度、三相电极功率分布特性与电极插入深度分析及控制措施一、电炉三相电极功率分布特性1、电炉功率分布对个冶炼区的作用:(1)通过炉料的电流主要用于炉料的预热。
(2)通过电弧、焦炭层的电流用于炉料加热和还原反应。
(3)通过熔池的电流用于炉渣和金属的过热。
2、炉膛内部的功率分布与操作电阻和炉料电阻率有关。
2.1炉膛内部功率主要分为电阻功率和弧阻功率。
2.2在操作电阻为定值时,炉料电阻越大,电弧区功率比例越高。
2.3正常的冶炼过程中功率分配系数为一个定值。
它的意义是炉料稳定地在不同区域吸收相应的热能,经历预热、加热、熔化和还原过程。
2.4炉料电阻决定了功率分布。
炉料电阻率越小,炉料内部导电比例越大,料层消耗的功率比例越大,反之亦然。
这也就是电炉运行中弧阻分配的意义所在!控制电炉的操作电阻和炉料电阻对保证电炉功率分布有重大意义。
2.5还原剂过剩时,炉料电阻会变小,功率分布系数随之变小。
这时,过多的热量用于加热和熔化炉料,使高温区上移,热效率降低。
2.6炉料电阻过大会使功率分布系数变大,电极埋入深度增加。
2.7由此产生的后果是:上层炉料得不到充分预热就进入反应区,正常冶炼物料的融化、还原平衡破坏。
同时电弧对炉底侵蚀严重,影响电炉寿命。
二、电极插入深度1、电极工作端长度是指底环下沿到电极顶端的电极长度。
2、电极下插深度是指埋人炉料内部的电极长度。
3、电极插深度反映了炉膛反应区在竖直方向上的位置,是判断炉况的重要特征之一。
4、随着铁水在炉膛中的积聚和排出,熔炼区的位置和电极下插深度会发生一定改变。
5、影响电极插入深度主要因素:5.1正常熔炼过程中,电极端部距炉底的距离为一定值,它与冶炼品种,电极直径和电炉的电气参数有关。
距离为电极直径的0.6~1倍。
5.2正常冶炼过程中电极位置的波动比较小。
5.3当炉况变化时电极插入深度变化较大。
5.4电极插入过深通常表明炉膛电阻增大,这多是由于还原剂不足或炉渣碱度过低引起的。
【收藏】电石炉的电极直径、极心圆直径、炉膛内径和深度这样计算!
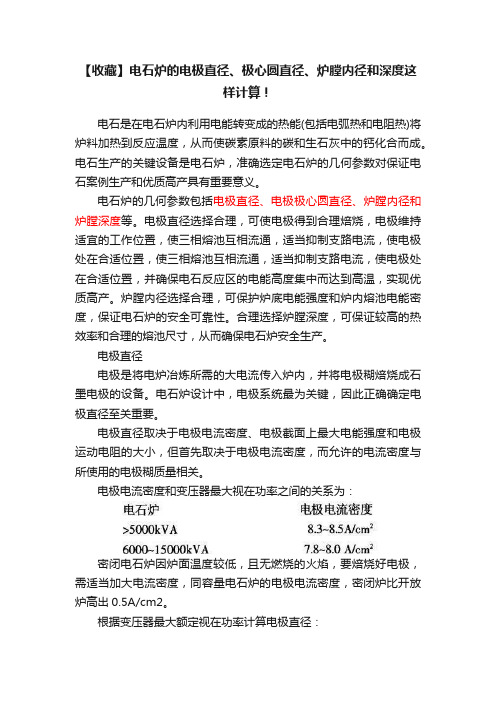
【收藏】电石炉的电极直径、极心圆直径、炉膛内径和深度这样计算!电石是在电石炉内利用电能转变成的热能(包括电弧热和电阻热)将炉料加热到反应温度,从而使碳素原料的碳和生石灰中的钙化合而成。
电石生产的关键设备是电石炉,准确选定电石炉的几何参数对保证电石案例生产和优质高产具有重要意义。
电石炉的几何参数包括电极直径、电极极心圆直径、炉膛内径和炉膛深度等。
电极直径选择合理,可使电极得到合理焙烧,电极维持适宜的工作位置,使三相熔池互相流通,适当抑制支路电流,使电极处在合适位置,使三相熔池互相流通,适当抑制支路电流,使电极处在合适位置,并确保电石反应区的电能高度集中而达到高温,实现优质高产。
炉膛内径选择合理,可保护炉底电能强度和炉内熔池电能密度,保证电石炉的安全可靠性。
合理选择炉膛深度,可保证较高的热效率和合理的熔池尺寸,从而确保电石炉安全生产。
电极直径电极是将电炉冶炼所需的大电流传入炉内,并将电极糊焙烧成石墨电极的设备。
电石炉设计中,电极系统最为关键,因此正确确定电极直径至关重要。
电极直径取决于电极电流密度、电极截面上最大电能强度和电极运动电阻的大小,但首先取决于电极电流密度,而允许的电流密度与所使用的电极糊质量相关。
电极电流密度和变压器最大视在功率之间的关系为:密闭电石炉因炉面温度较低,且无燃烧的火焰,要焙烧好电极,需适当加大电流密度,同容量电石炉的电极电流密度,密闭炉比开放炉高出0.5A/cm2。
根据变压器最大额定视在功率计算电极直径:式中:De—电极直径,cm;Smax—变压器最大额定视在功率,kVA.若根据电极电流密度和二次电流计算:式中:De—电极直径,cm;δ—电极电流密度,A/cm2;I—变压器最大二次额定电流,A根据以上两公式可计算出各种容量电石炉的电极直径,其与电极电流密度和变压器最大额定视在功率的关系值见表1。
表1 电炉变压器容量与电极直径的关系电极的电流密度过大,则电极直径过小,会增加电极的电阻电耗,电极容易因过焙烧而硬断,同时缩小电石炉熔池;电极电流密度过小,则电极直径过大,虽然能扩大熔池,并减少电极电阻电耗,但电极不易深入炉料,且会增加热损耗而降低热效率,电极焙烧不足易软断,电弧温度也会降低,对生产不利。
75硅铁工艺控制

75%硅铁的工艺控制选择了合适的炉膛直径、料面高度和比电阻变化采用相应的平均粒度,使工艺控制合理,电耗降低,共节电656万度。
一、前言75%硅铁是炼钢和铸造等工业不可缺少的原料,约占铁合金总产量305。
生产一吨75%硅铁耗电8300-10500度,我国一年用于生产75%硅铁的总耗电量在32亿度以上,占全国总用电量的1%以上,是最大的用电户之一。
电费在75%在硅铁总成本中占65-70%。
降低电耗是生产75%硅铁节能增益的重要坏节。
原料、设备和操作等的改进,都能使75%硅铁电耗降低。
1979年8月至1684年1月,我们进行了四个阶段的研究,掌握了炭平衡、焦炭最大使用粒度选择、粒度搭配、提高极心园功率密度,共节电2000万度。
在此基础上,我们对本厂75%硅铁电炉的参数和所用原料的性质作了分析,放大了炉膛直径,控制合适的低料面,随焦炭比电阻变化采用相应的平均粒度,使工艺控制合理,75%硅铁电耗降低,节电共656万度。
二、电炉参数改进75%硅铁电炉,多数是三相三电极,接等边三角形布置的。
炉内电路可以认为如图1所示。
图一炉内电路示意图电炉运行时,炉内电路一条是电极下端通过电弧电阻、合金熔体电阻相互间的串联电阻值,即熔池电阻Rr,构成星形主回路。
另一条是电极通过炉料,由各种炉料形成的串联电阻值,即炉料电阻RΔ,构成三角形支路。
星形主回路和三角形支路是等效并联的。
按照热分布原理,在电炉正常运行的硅铁生产中,支路电流仅占电极电流很小的比例,约10%以下。
如果支路电流过大,输入电能过多用于加热炉料,使料层温度过高,电极会上抬,使熔池反应区上移和温度不足。
为了使炉内功率分配适当,必须选择合适的电炉参数,控制合适的炉料电阻。
这样才能取得硅铁电炉良好的经济指标。
我们调查了75%硅铁炉电耗与操作电阻的关系,在1982年调整了20000千伏安电极极心园尺寸,由原来φ2950毫米缩小到φ2700毫米。
在1983年调整了10000千伏安电极极心园尺寸,由原来φ2250毫米缩小到φ1950毫米。
矿热炉变压器、补偿设计及应用概述
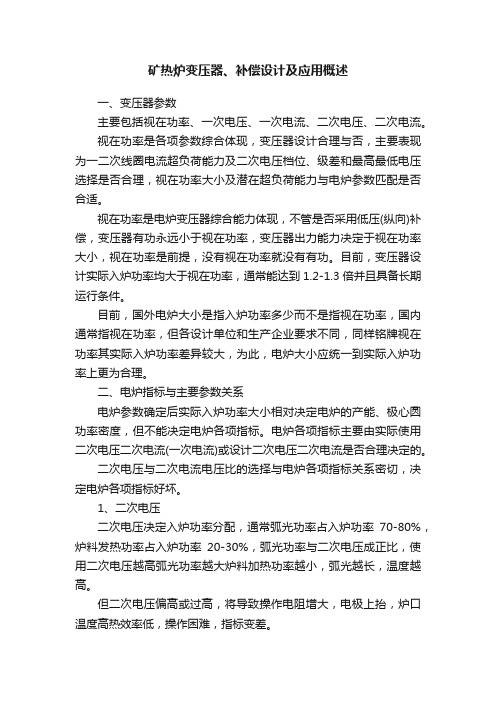
矿热炉变压器、补偿设计及应用概述一、变压器参数主要包括视在功率、一次电压、一次电流、二次电压、二次电流。
视在功率是各项参数综合体现,变压器设计合理与否,主要表现为一二次线圈电流超负荷能力及二次电压档位、级差和最高最低电压选择是否合理,视在功率大小及潜在超负荷能力与电炉参数匹配是否合适。
视在功率是电炉变压器综合能力体现,不管是否采用低压(纵向)补偿,变压器有功永远小于视在功率,变压器出力能力决定于视在功率大小,视在功率是前提,没有视在功率就没有有功。
目前,变压器设计实际入炉功率均大于视在功率,通常能达到1.2-1.3倍并且具备长期运行条件。
目前,国外电炉大小是指入炉功率多少而不是指视在功率,国内通常指视在功率,但各设计单位和生产企业要求不同,同样铭牌视在功率其实际入炉功率差异较大,为此,电炉大小应统一到实际入炉功率上更为合理。
二、电炉指标与主要参数关系电炉参数确定后实际入炉功率大小相对决定电炉的产能、极心圆功率密度,但不能决定电炉各项指标。
电炉各项指标主要由实际使用二次电压二次电流(一次电流)或设计二次电压二次电流是否合理决定的。
二次电压与二次电流电压比的选择与电炉各项指标关系密切,决定电炉各项指标好坏。
1、二次电压二次电压决定入炉功率分配,通常弧光功率占入炉功率70-80%,炉料发热功率占入炉功率20-30%,弧光功率与二次电压成正比,使用二次电压越高弧光功率越大炉料加热功率越小,弧光越长,温度越高。
但二次电压偏高或过高,将导致操作电阻增大,电极上抬,炉口温度高热效率低,操作困难,指标变差。
选择合适二次电压是决定电炉指标的关键。
既要考虑功率分配又要考虑操作电阻及极心圆电压密度(有补偿后极心圆功率密度提高不代表电压密度提高,光有功率但分配不一定合理)。
目前国内新建电炉,各品种极心圆直径电压降大致如下:碳锰55-60V/m,硅锰 60-65V/m,高碳铬铁 65-75V/m,硅铁(工业硅) 70-75V/m,镍铁 120-130V/m,根据变压器设计能力及电炉参数,二次电压使用根据各品种可在此范围内操作,基本达到了使用电压较高和电压超负荷的目的。
硅铁电炉炉衬及其维护

膛不同区域温度的不同,可对硅铁电炉内的热分布 估测为如下区带。 预热带:处于整个炉膛的最上层,分新料和预热 料。通常厚度在100—250 mm,其厚度随电炉容量的 大小、加料时间长短及速度的快慢不同而变化,此带 温度大约为500~1
000℃。
适宜的电极工作端长度 保持合适的电极工作端长度,对炉底将起到一
INTRODUCES THE LINING oF FERROSILION FURNACE
AND ITS
MAINTENANCES
Ba Duohua
(Dragon Northwest Ferroalloys Co.,Ltd,Lanzhou 730334,China)
Abstract Briefly introduced the material of ferrosilicon furnace lining and its¥oul.ce of damage.It puts of lining in technology.It has
料市场面临的形势不容乐观。
下,市场上的炼钢生铁价格在3
2
050.3
100元/吨,有的报 800元/吨。一
价2 950—3 000元/吨;云南地区的炼钢生铁价格在2 650—
700元/吨;内蒙古市场炼钢生铁2
700—2
些经营者认为,后期生铁市场价格有可能继续下滑。 业内人士认为,这周一些钢铁炉料市场震荡,价格回落, 主要是受钢材市场价格的大幅下跌影响。8月份的第二个交 易周,国内钢市与上一周仿佛“冰火两重天”。在上周一、二,螺 纹钢、线材市场价格几乎是“日涨两三次,日涨两三百”,十分 火爆,在其带动下,废钢、生钢、钢坯、铁合金、焦炭等原料价格 紧跟上涨,步步走高。而这一周,国内钢市急剧变化,行情急转 直下,一路下滑。如在上海地区,普通Ⅱ级螺纹钢(‘p18ram— tp25mm)从上周最高的4 600元/吨,下跌到这周末的3 900 元/吨,下跌了700元/吨;上海周边的南京等地的螺纹钢价 格也下跌了400多元/吨,济南、南昌、郑州、长沙、哈尔滨、西 安市场的建筑钢材市场价格的跌幅在300—400元/吨。这 周,北京市场上的首钢产螺纹钢、线材的价格也下跌了350— 500元/吨;国内其它地区的建筑钢材市场价格均有200元/ 吨以上的跌幅。其它钢材,如中厚板、冷热板、型钢等价格也纷 纷下跌,中厚板价格跌幅100—200元/吨;冷热轧下跌300 元/吨左右。 钢市价格的全面下挫,受其影响,钢厂也下调螺纹钢、线 材等钢材的出厂价格,下跌幅度200—300元/吨,因而,带动 了部分钢铁炉料价格的下滑。如钢坯市场首当其冲,一些购坯 轧材的中小型钢厂,对高位运行的钢坯已不再看好,认为螺纹 钢价格猛跌500—600元/吨,钢坯价格如果再在高价位上, 无法生产,一时间钢坯市场需求明显减少,迫使价格的下跌。 而一些钢坯的生产厂家心态不稳,看空后市,也都降价抛售, 使钢坯现货价持续大幅走低。 同样,废钢市场价格也从高位上震荡而下。在跌势之中。 一些钢厂基本以消化库存资源为主,观望气氛浓重,市场需求 不旺,经销量对后市预期看淡,急于出货,便降价销售,一度的 恐慌心态,加速废钢市场价格的快速下跌。此外,市场需求减 少。据悉,在东北地区,随着建筑钢材市场价格的大幅下跌,当 地一些小电炉厂陆续停止废钢采购,废钢贸易商心态波动,以 降价吸引终端用户采购。 业内人士认为,近期一些钢铁炉料价格的震荡回落,主要 是由钢材市场的震荡而起引的,如果后期钢市继续走软,价格 震荡下行,那么还将对钢铁炉料市场带来影响,废钢、钢坯、生 铁、铁合金等市场价格仍将跟随波动,向下而行。尤其是废钢、 钢坯等,其价格仍有下跌空间。 摘自《铁合金经济技术信息>
电石炉中重要参数的确定

电石炉中重要参数的确定发布时间:2023-03-08T03:37:57.008Z 来源:《福光技术》2023年3期作者:马英博[导读] 电石炉内电石生产时,既要把电能转变成热能,又要使原料之间发生物理化学变化。
新疆圣雄电石有限公司新疆吐鲁番 838100摘要:电石炉内电石生产时,既要把电能转变成热能,又要使原料之间发生物理化学变化。
所以,工艺过程比较复杂。
电石生产的关键设备是电石炉,准确选定电石炉的几何参数对保证电石安全生产和优质高产具有十分重要的意义。
本文就电石炉的设计,对其电极直径、电极同心圆直径、炉膛直径及深度的准确选定进行讨论。
关键词:电石炉;设计参数;确定电石是在电石炉内用电能转变成的热能把炉料加热到反应温度,而使碳素原料的碳与生石灰中的钙化合而成,即电石炉内电石生产时,既要把电能转变成热能,又要使原料之间发生物理化学变化。
所以,工艺过程比较复杂。
电石生产的关键设备是电石炉,准确选定电石炉的几何参数对保证电石安全生产和优质高产具有十分重要的意义。
1 电极直径在电石炉设计中,电极最为重要,因此正确选定电极直径至关重要。
电极直径取决于电极电流密度、电极横截面上最大电能强度和电极运动电阻的大小,但首先取决于电极电流密度。
而允许的电流密度与所使用的电极质量有关。
电极电流密度弹性很大,依各厂生产实践,可归纳出电极电流密度和变压器最大视在功率之间的关系。
2熔池当电石炉通电后,电流经碳素电极通过炉料,使电极端头间的气体电离,电离后的气体形成一个导体,在电极一端至炉料间产生电弧。
电弧作用区域(即电弧发出的高温作用到的区域)通常称为熔池。
根据长期电石炉操作经验,得出计算电石炉熔池半径Rm的经验公式:Rm=(Pt/3πPu)1/2=(0.1061Pt/Pu)1/2(2)式中Rm为熔池半径,cm;Pt为电炉最佳运行有功功率,kW;Pu为熔池单位面积上的功率强度,kW/cm2。
通常熔池内单位面积上的功率强度Pu是随电炉变压器容量的大小而变化的,同时也与变压器功率因数有关。
硅铁冶炼技术操作规程
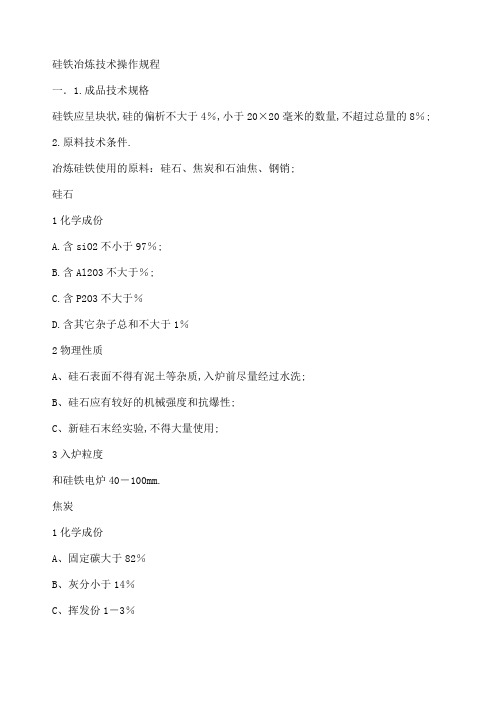
硅铁冶炼技术操作规程一.1.成品技术规格硅铁应呈块状,硅的偏析不大于4%,小于20×20毫米的数量,不超过总量的8%;2.原料技术条件.冶炼硅铁使用的原料:硅石、焦炭和石油焦、钢销;硅石1化学成份A.含siO2不小于97%;B.含Al2O3不大于%;C.含P2O3不大于%D.含其它杂子总和不大于1%2物理性质A、硅石表面不得有泥土等杂质,入炉前尽量经过水洗;B、硅石应有较好的机械强度和抗爆性;C、新硅石末经实验,不得大量使用;3入炉粒度和硅铁电炉40-100mm.焦炭1化学成份A、固定碳大于82%B、灰分小于14%C、挥发份1-3%2物理性质A、入炉粒度硅铁电炉5-16%钢销1化学成份含铁量不低于97%2应是普通碳素钢销,不得混有合金钢销,有色金属销和生铁销等;3生锈严重的钢销不得使用4钢销的卷曲长度不大于100mm5要纯净,不得混有泥土等杂质二、配料操作1、每班配料前要一次小车重量和磅秤的准确度;2、在按照冶炼班长通知的料比组成进行配料;每批料以200公斤硅石为基准,以上电炉每批料以300公斤硅石为基准;3、称量要准确,误差正负1%,钢销要单称后再混入配料小车内;4、每次只准称量一批料;5、发现原料质量有变化和设备有问题时几时报告班长;6、下班前要将配料场地清扫干净,所有的工具设备要精心保护交换;7、下班前要把当班配料批数报告班长做好记录;三、冶炼供电和电极操作1、正常冶炼操作使用电压:电炉104V-125V为宜电炉140V-188V为宜2、一次电压波动较大时,为保证炉用变压器正常运行和冶炼的适宜的功率,经炉长批准可在规定级别内调整二次电压;3、严禁超负荷运行、4、三相电流应尽量保持平衡,最大波动不准超过25%;5、冶炼保证应认真贯彻执行电器工作制度;6、操作工应严格按电流供电制度,进行操作工作,并听从电工和冶炼班班长指挥;7、送电前先将电极适当提起,方准送电;8、发生电极事故后和长期停炉重新送电时,首先要降低档位,采用低负荷,并听班长指挥;四、冶炼操作1、每批料运至炉上平台,首先要摊平混合均匀,才准加入炉内;2、混合均匀的炉料,应以分批分期的方式加到电极周围的炉料下沉的部位,严禁偏加料;3、炉料向垂直与电极的方向加入炉内,加入炉内的炉料不准碰电极,力求准确无误;4、炉料在电极周围堆成平顶和均衡的锥体,在操作中稳定控制料面高度一般与炉口相平,也可控制在炉口以下200mm左右;硅铁炉保持炉心料饱满,严格控制料面高度,三班认真交接;5、控制电极插入炉料中的深度硅铁电炉插入深入900-1400mm.6、铜瓦下端距料面高度硅铁电炉不少于400mm.7、要适时扎眼,以经常保持料面良好的透气性,利于扩大坩埚,加速冶炼速度;8、电极周围出现白光时,采用撤火等措施尽快消灭;9、经常保持电极工作表面光滑,粘有粘料时及时清理,以减少冒白光现象;10、电极周围塌料时,先把坩埚附近的大块硬料推入炉心,然后将附近的熟料推入坩埚,之后再加入新料;11、每一次出炉后,捣完炉应迅速平整炉面,将周围的熟料推至电极周围,再覆盖新料,根据电极工作端长度,出炉后争取进行下放电极操作;12、根据炉况,每班要捣炉2-3次,捣炉操作应在出炉后立即进行,捣炉时捣炉机找好角度,动作迅速,逐相电极进行,严禁碰撞电极炉内烧结的大快粘料尽量不要拔出,如拔出将其砸碎,做到当班加入炉内,不得任意扔掉;13、配料比的调整,班长在保证炉况正常情况下可调整正负2公斤碳质还原剂,炉长有权调整正负6公斤钢销;14、出炉前15-20分钟,采取维护好炉面,消灭白光等措施,处理好炉况,尤其是出铁口相电极更要注意,以防出铁过程中塌料现象而影响出铁;15、出炉过程中要正常加料;16、冶炼班长与操作工经常取得联系,操作工在业务上,在不违反供电制度的前提下,应听从冶炼班长的指挥;17、冶炼班长要认真填写电炉冶炼操作记录卡片;五、正常炉况特征及不正常炉况的处理一正常炉况特征1、电极深而稳地插入炉内,负荷稳定,易于控制;2、料面冒火均匀,透气性良好,没有暗色,刺火现象少;3、电极周围沉料均匀,没有大塌料现象;4、出铁口用木杆通时畅通无阻;5、出铁口好开好堵;6、产量和产品质量稳定;二不正常炉况1、还原剂不足即炉况粘电极往往插入炉中过深,电炉表指针波动频繁,不易给上负荷,炉况过粘,料面有烧结现象,刺白光现象严重,炉况过粘时,电极有时也难以下插;处理方法:1增加料比中的碳质还原剂配入量;2彻底捣炉同时可附加炭质还原剂处理;2、还原剂过剩电极插入炉内深度过浅,坩埚不易塌料,出铁时感到铁水温度低,好给负荷,特别是捣炉下料,电极容易上抬,大面蓝色火焰多,火焰无力;处理方法:1减少料比中的炭质还原剂的配入量;2严重时单加一定量的硅石要有炉长指导附加六、炉前出铁操作1、出铁要按规定时间进行,不得提起和拖后,炉况正常情况下,每班2-3炉电炉2、出铁前要清扫炉台和流铁槽;3、锭模必须保持干燥,出铁前应清扫干净,并薄涂石英沙玻璃水也行;用合格硅块将锭模垫好,其厚度少于70mm,严禁用废品和碎渣垫模;4、根据出铁口情况,出铁前用圆钢清理出铁口,出炉时尽量用圆钢开出铁口,必要时可使用烧窜器,先烧中心靠上面,不准烧下面,以防出坑;烧窜器用完后立即分闸,出铁口要保持喇叭型,内径70mm,外径90mm;5、用氧气烧出铁口时,必须注意以下几点:1由班长指挥烧出铁口的操作,设专人看管氧气瓶;氧气瓶应放在安全地区,距电炉五米处的地方;2烧氧气所有的工具和保护用品不准带油类物质;3输送氧气胶管,铁管等连接部位必须牢固的紧密结触,不准漏气;4开始先用电烧,然后开始送是少量氧气,待烧着后,再逐渐增大气量,同时氧气管应不断的向前推进,但用力不能过猛;5当发生回火时,应立即关闭氧气瓶,同时折叠胶管;6出铁口烧开后,立即将氧气瓶撤走;6、烧出铁口要严格控制铁口高度,不准任意提高;7、出铁前准备好以下物品:1堵眼耙三个以上;2托泥铲两个以上;3干泥球五个以上;4长圆钢四根以上;8、浇注过程中严格控制产品厚度,72硅铁一般为70-90mm,以上的电炉用铁水包浇注,采取两次浇注法;9、炉内积杂渣过多,不能自动流出时,首先将烧窜器开关分闸,可用圆钢向外拉渣,也可以用木杆带渣要关好出铁门小心烫伤;10、尽量缩短出炉时间,出铁后将出铁口附近的炉渣清理干净,出铁口还冒火时立即再堵,防止炉眼氧化可用碎硅铁渣捂住出铁口有碳砖的地方;堵出铁口的泥球用焦炭粉和粘土制成,或者用石墨粉:焦炭:石灰粉=4:3:3制成,或用粘土、焦炭粉、电极糊粉;11、出炉完毕,开动炉前小车前,检查轨道上有无障碍物;12、硅铁锭完全凝固后,才准起吊铁锭;13、起出铁锭后,四十分钟内垫好锭模,并将炉前小车开到出铁口下,防止跑眼;14、每炉产品要规整的放在精整盘上;七、硅铁产品的精整和入库1、精整工必须严格按标准或按用户的要求对产品进行认真的精整;2、精整下来的不合格产品,可作回炉用,不准重熔或垫模;3、经检查人员检查合格后,方准入库;八、电极维护一下放电极和维护1铜瓦下端距料面小于150mm时要下放电极,每相电极下放时间不少于4小时,不多于24小时,要做到勤放少放就是每班每次少放点多放几次2正常情况下电极下放长度不超过100mm;3正常情况下,出完铁之后开始进行电极下放操作,操作工要听从班长指挥;4严禁带负荷下放电极;5电极下来后,立即观察电极烧结情况,以防出现电极事故;6下放电极后根据电极烧结情况,缓慢地给负荷;7设备检修或事故长时间停炉时,为了保护炉温,利于电极维护,防止电极事故,应在电极周围加入适量炭质还原剂,停电期间,每小时活动一次电极,以防止电极粘结;8装入电极壳内的电极糊柱高度保持在铜瓦上端2-.9根据电极消耗情况,一般每班要一次电极糊,勤加入量根据电极糊柱高度而定,加入电极糊要注意安全操作,电极糊加入前砸成小块,要均衡地加入电极壳内,以防悬料,如悬料不得加入,待悬料消除后再加;二接长电极壳1用电气焊接长电极壳,焊缝要牢固平整,表面不得凸凹不平,周围要满焊;2、电极壳接长之前,应认真接长电极壳质量如圆度,筋片和触舌等,不合格的电极壳不准使用,接长时新旧的电极壳的中心,在一条直线上,筋片更为重要,不得有歪曲现象;3操作人员或圆钢等金属块不能同时接触两相电极,以防出现人身和设备事故;要遵守操作制度;4接触电极壳工作结束后,必须将电极平台清扫干净;三电极事故的处理1凡属电极下滑,硬断,软断和流糊均应立即停电处理;2电极流糊时如孔洞不大,可用石棉布堵牢,以低负荷送电烧结,如孔洞很大,必须用薄钢板焊补,堵住流糊;3干净硬断时,取出硬头,下放电极以低负荷降低二次电压,也就是降低档位进行烧结,折断长度大于可用把持器夹紧,继续烧结;4电极软断,立即停电,松开铜瓦再夹紧软断部分,开始以20%负荷送电进行慢慢烧结,恢复负荷时间视情况而定,软断严重时需要木柴烘烤,然后再送电,电极糊如流空时,要重新陪烧电极;5电极发生软硬断时,均要补充电极糊;九、烘炉和开炉规程1、烘炉目的有二,其一是为了陪烧电极工作端,使其硬化后从而能承受一定的电流能力;其二烘干炉衬,提高炉温,使电炉加料后炉况和生产早期正常,因此,烘炉分为二个阶段,第一阶段采用焦炭烘或木柴烘,以陪烧电极,第二阶段采用电烘,进一步陪烧电极,烘干炉衬并使炉衬达到一定温度,以适应加料进行冶炼;2、烘炉前的准备工作1所有设备系统如导电、水冷、电极悬挂、绝缘、电极升降、电极压放、吊运上料和配料等系统,必须进行全面检查和试车;2先在每相电极底下垫一层厚65mm的粘土砖,而后将有底电极平稳地落在粘土砖上,以防电极与炉底粘结;3将电极把持器移到上限位置,使电极有足够长的工作端,一般-2m;4向有底的电极壳内装入块度为40-80mm的电极糊,糊柱高度3m.5在电极工作端部位的电极壳,可均匀地扎一些小孔,使电极陪烧过程中挥发分顺利逸出,加速电极陪烧速度;6在出铁口内放一直径100-120mm的钢管,中间填满焦粉,两端用泥球堵严实;7烘炉初其设备受热量较小,所以冷却水开到小量,随着温度升高,冷却水量逐渐加大,以放烧坏设备和绝缘系统;但铜瓦冷却水,始终不要过大,以利于加快电极的烧结;8用焦炭烧烤时应围绕三相电极的周围用圆钢焊成的花栏,以便盛装焦炭,将花栏吊在把持器上随着电极烧结程度逐步提升,到上限为准,花栏高-为宜;3、烘炉的原则为使焦炭烘或木柴烘和电烘过程中符合电极烧结规律,烘炉期间应遵守下列几项原则;1电极烘烤部位应由小而大;2燃烧的火焰应小而大;3电极升温速度有慢逐步加快;4电极糊柱高度由低而高;4、焦炭或木柴烘烤电极1准备5-8吨大块焦粒度150-250mm运到电炉平台上一做烘炉燃料用;2先将一些木柴投入到圆钢制的花栏内,而后以油类物质点燃,之后加入焦炭,要精整电极周围,使其慢慢燃烧;逐步地加入新焦炭,每次加入量不要过多,要均匀加入;3焦炭烘后期应用大火烘烤,必须注意电极小面的烘烤情况,力争达到烘的均匀; 4焦炭烘烤时要活动电极由炉长安排提升;5焦炭烘时间,根据电极陪烧质量而定,一般20-36小时;6电极烧结良好的特征是:电极壳表面呈灰白色,暗而不红或微红,电极冒烟量少,用尖头钢针刺探稍有软的感觉,而戳穿后没有电极糊外流的现象,当确认电极烘烧良好后,由炉长决定焦炭烘烤结束,进行准备电烘炉工作;7如果电极壳表面墨色,电极冒黑浓烟,用钢尖刺探时软的感觉,而且戳穿后电极糊注出并冒黑烟;则说明电极糊烧烤不足,应继续烘烤,直到烘烤质量良好为止;8因烘烤电极是一项极为重要的工作,炉长要经常在现场指挥;9遵守技术安全规程,特别要注意不要烧坏设备,防止人身事故;5、电烘炉操作送电烘炉前准备工作:1将炉内残存的焦炭和炉灰尽量清理干净;2再认真检查一次所有设备,尤其是供电,导电的绝缘系统,使其具备正常送电条件,紧固有关的螺丝;3炉底铺一层厚度为150-200mm粒度15-30mm的焦炭;要准备这种焦炭1-2吨,备电烘过程中加入;4将把持器向下移动,使电极工作端长度保持在-,而后对各相电极铜瓦进行紧固,使之与电极紧密接触;5正式送电前,可用线将三相电极围联一起,先用电冲击一次,以检查继电保护装置的灵敏度;送电1送电时由班长指挥,并警告各岗位的人员,遵守安全规程,观察设备情况;2送电时首先用低电压,有时为了便于引弧,开始时可用略高电压引弧,两小时后电弧稳定后仍要使用低电压,电烧过程中逐步升变电压;3当不易引弧时各相电极间加些钢销联通也可用25圆钢焊成等边三角形放在三相电极底下,利于引弧;4为使电弧稳定和保持一定的功率应向炉内和电极周围加些焦炭;5要缓慢地下降电极,电流小时不要硬插电极,可将炉内旧焦炭推至炉边,补加新焦炭;6应尽量少活动电极,当发现电极冒严重时应立即停电处理,防止事故的发生;7烘炉时电极消耗较快,下放电极时应停电,必须停电放电极,电极下来后,要观察电极烧结情况;8电炉电烘炉进度表1. 1A一5A 小时散热半小时2. 5A一10A 小时散热半小时3. 10A一15A 小时散热半小时4. 15A一20A 小时散热半小时5. 20A一25A 小时散热半小时6. 25A一30A 小时散热半小时7. 30A一40A 小时散热半小时8. 40A一50A 小时散热半小时9. 50A一60A 小时散热半小时10. 60A一70A 小时散热半小时11. 60A一70A 2小时烘炉完毕6、加料开炉操作一加料的条件和时间1当电流表针的电流值达到额定电流50-60%.2由炉壳中部的外部,试探温度达600C以上;3炉壁预留的排气孔,已不再逸出气体;二已确认具备加料条件时,要尽快将炉内的剩余焦炭,尽量清除;三开炉配料比;因开炉时炉温较低,为尽快出合格产品,配料比200公斤硅石为准,加5公斤钢销为宜;焦炭量按正常加入量;四从加料开始间记,约经过16-22小时,可出第一产品,第二炉冶炼时间为10小时,第三炉为8小时,第四炉6小时,第五炉4小时;五加料速度一定要慢,严格控制料面高度,一周才准升到炉口;六出炉时间和配料比,可根据炉温和产品含硅量进行调整;七开炉工作是一项很重要的工作,炉长必须经常在现场指挥,尤其要严格控制料面高度和安全操作;B.新开炉操作准备工作1、检查机械系统,电器系统确保正常,水冷设备,液压及压放系统,各焊接点,油路不得漏水,漏油现象,各油缸及阀件动作灵活可靠,各部件之间绝缘可靠;在检查完各系统设备后,进行二到三次冲击送电实验;2、检查电极极心园直径,当电极升降时,其极心园应保持不变;单相电极升降,两相电极升降、三相电极同时升降各进行一次,三相之间不得有干扰,电极压放系统能灵活的夹紧放松,并能可靠地紧固电极,电极壳不变形;3、电极壳接好后应装入破碎的电极糊,其高度略低于平时正常生产时的糊柱高度;4、在检查和验收完设备后,做好送电前的装入工作;首先在炉底铺上一层200mm碳层,其次将三相电极的导电柱略大于电极直径50mm,高度为400-500mm,里面装入1mm粒度的焦炭麽放入炉内,并把电极堕在筒上;然后向炉内铺一层小木块,形状为椎体状;5、铺完木材之后,向炉内加入混好的炉料,其加入量以盖完木材为准,其料比为硅石200公斤,焦炭40公斤,氧化铁32公斤钢削20公斤;6、下放电极到合适的位置,并紧好电极,进一步的检查各系统,并确认各系统可靠无误,并确保机电设备附近无人后进行实验性送电三次,在完成第三次试送电后,下插三相电极,使其坐死在炉内导电柱上;送电时选择较低的电压等级;7、送电时生产部,机电维修人员、冶炼负责人及相关的人员必须在现场方能送电;8、送电后严禁活动电极,当炉内起弧后,严禁大升大降电极,其负荷应尽量保持稳定和均匀上升,不准单独增大某相电流,以防止出现电极事故;9起弧后开始向炉内加料,加料开始后要严格控制其加料速度防止料面过快上涨,从开始投料起到其后的一星期内料面的高度必须控制在炉口以下400mm,一星期后料面达到正常高度;在投料的初期一个班以内8小时以半烘炉半冶炼为主,从第二个班开始正常冶炼;其料面高度为炉口以下600mm,料比中的焦炭量根据冶炼的进程和负荷的使用情况作及时的调整;10、在冶炼初期,应根据炉内情况,向炉体边缘附加一定数量的焦炭;其附加量应控制在2000公斤左右;11、在正常冶炼30小时,根据用料用电情况准备出铁,在此之前应做好出铁前各项准备工作,一般情况下在耗电达到10万左右开始出铁;12、每班压放电极的长度应准确记入冶炼记录,要注意观察电极烧结情况,发现冒烟冒较大时应降低负荷,当班班长应在交班时正确填写各种记录,将设备的运行的情况,附加料的数量等向下班班长介绍情况及需要注意事项;13、在新开炉期间,料比要准,电极要稳,料面要控制好,炉料要混合均匀加入炉内,一批用完再加第二批,绝不允许偏加料;出铁前要铁水包准备好并保持干燥,做好各项安全工作;炉前交接班制度1、班前5-10分钟内,班长进行现场交接,并于整点交接;2、交班班长必须向接班班长交接生产情况内容包括:炉况运行、设备运行、产品质量、三相电极插入料面深度、出铁流量大小及炉眼否好开好堵;3、交接班人员在交接时,必须给接班人员备交班料,工作现场清扫干净,在各类设备、设施完好的情况下方可交班;4、上班不许占用下班冶炼时间;不许保证炉况稳定,如交班占用下班时间或炉况出现异常,根据有关规定对班组作出严肃出炉;5、交接班工作完毕后,交班人员方可离开工作岗位;操作工工作制度1、必须确保记录数据清楚、准确、整洁;2、在当班期间严禁长时间打电话,或接私人电话闲谈;3、操作室除班长、炉长其余闲杂人员一律不大擅自入内,操作工有权禁止闲杂人员入内;4、要配合炉前操作,有问题要及时反映给班长、炉长;不准无故障掉负荷;5、要做到合理用电,电极要插平衡,每班用电不得少于电炉,不高于.6、在当班期间必须保持室内清洁干净;7、在停电期间要坚守岗位,按照要求及时活动电极;出铁工工作制度1、出铁工要严格按照出铁操作观察操作,认真负责产品外观质量;认真做好出铁前的各项准备工作,如因出铁工具不齐全延误出铁时间或堵不住眼,造成损失者追究其责任;2、出铁工要严格按照要求做好泥球并烘干,如因泥球质量影响出铁时间或堵不住炉眼,造成损失者追究其责任;3、出铁工有权指挥行车工浇注,浇注厚度不得超过80mm,以免铁水大量外溅;4、冬天浇注20分钟,夏天40分钟,将铁撬出锭模,以便化验员取样化验,当铁水没有凝固好时不能脱模以免冒瘤,影响外观质量;5、出铁工要在交班前半小时或1小时内把工作场地、锭模周围、地坑、出铁平台和炉子周围清扫干净,并经常清理和维护好流槽,保持炉眼外大内小外面100毫米,内80毫米,堵眼深度100毫米;6、出铁工将最后一炉铁拉入库场后,将拉铁小车拉回本工作现场,车内不能有存铁带回,方可交接;加糊工工作制度1、加糊工必须准确测量糊柱高度;及时补加糊柱高度,如测量失误造成损失责任自负;糊柱高度夏季是铜瓦上端的,冬天是3m.2、严格监督计量和电极糊的质量,不允许带有泥沙的电极糊,电极糊必须按要求砸成小块加入,以防澎糊悬糊;3、加糊完毕必须盖好电极筒上的压盖,以防尘土刮入造成电极事故;4、加糊国要精心维护好自己所有使用的上班器具,严禁违章操作,严禁加糊工超装,否则出现上班事故自己负责;5、加糊工所有工作场地及卫生区域和原料场地,修包场地卫生清扫干净,要把当天所出的渣拉干净,方可离开岗位;6、拉渣时要把料面的好铁筛选出来,进入车间存放场地;7、三层平台加完糊要详细检查,有没有电极糊块掉到三层平台并按紧电极筒,如因电极糊没有检查到造成联电将电极筒击成洞,责任自负;行车工工作制度1、行车工负责行车的正常和使用及自检工作,保证行车无油垢、无积灰;2、行车工必须掌握一些简单事故处理方法,接班时应先检查设备运转情况,交班时检查所有设备运转正常,行车工才能离开工作岗位,否则不予下班;3、行车工严格遵守行车操作规程,听从指挥,注意安全,如不听从指挥出现事故自行负责;4、行车工实行一岗多职,看好产品库,防止盗铁事故出现,如盘库数量对不上要对行车工进行经济处罚,进行维护炉眼工作配合工作,清扫车间环境卫生及行车卫生;计量工与绞车工职责1、计量工要认真计量,计量时检查衡器的准确性,给炉前创造一个好的条件;2、计量工要认真执行计量标准,计量时准确无误,不能有误差;3、计量时不得随意更改计量标准,及配比数量,对变料时间、数据要填写清楚;4、计量工不得听从其它人员说变料及单加洗炉材料;5、计量工只有接到炉长签字的变料单,方可变料或单加料;6.计量工随时检查衡器准确,要随时把衡器卫生及工作场地打扫干净;7、绞车工要认真对待自己的本职工作,要求安全第一;8、绞车工有权禁止任何人员乘提升机上下;如有不听者及时向车间反映如发现一次提升机站人,调离本工作岗位;9.绞车工要听从炉前上料的铃声,不要随意上下开绞车,以免出现设备事故10、绞车工上夜班时要集中精力,以免开错绞车出现人身或设备事故;11、绞车工认真执行绞车绞车操作规程,发现绞车有异常及时向车间反映;12、所有属绞车工的工作场地卫生要清扫干净;13、绞车工要绞车钢丝在卷筒上是否排列整齐,绝不允许钢丝在卷筒上乱卷;班长工作职责1、班长负责本班的全面管理工作,着重抓好本班工艺操作,劳动纪律、安全生产、产品质量及精神文明建设等工作;。