粉末冶金与陶瓷材料的成型工艺技术.pptx
粉末冶金与陶瓷材料的成型工艺ppt

第二节 粉体制备技术
<2> 溶 剂 蒸 发 法 (Solvent Vaporization Process) a.冰冻干燥法 a.冰冻干燥法 b.喷雾干燥法 b.喷雾干燥法 c.喷雾热分解法 c.喷雾热分解法 ② 熔液法 <1>等离子体喷射法 典型的等离子喷管如图 11所示 典型的等离子喷管如图7-11所示 <2>激光法 图7-12为激光法制超微粉工艺原理图。 12为激光法制超微粉工艺原理图。 为激光法制超微粉工艺原理图 3)气相法制备粉末 蒸发- ① 蒸发-凝聚法 ② 气相化学反应法
第七章 粉末冶金与陶瓷材料的成型工艺
第七章 粉末冶金与陶瓷材 料的成型工艺
粉末冶金( Metallurgy)与陶瓷(Ceramic) (Ceramic)的 粉末冶金(Powder Metallurgy)与陶瓷(Ceramic)的 主要制备工艺过程包括粉末制备、成型和烧结。 主要制备工艺过程包括粉末制备、成型和烧结。其生产工 艺过程可简单地表示为: 艺过程可简单地表示为:粉末制备坯料制备成型干燥烧结 后处理热压或热等静压烧结成品
粉碎(Porphyrization) (Porphyrization)与机械合金化 一 、 粉碎 (Porphyrization) 与机械合金化 Alloying)方法 (Mechanical Alloying)方法
粉碎的过程是由机械能转变为粉料表面能的能量转 化过程。 机械粉碎法因其设备定型化, 产量大, 化过程 。 机械粉碎法因其设备定型化 , 产量大 , 容易 操作等特点,被广泛地应用于粉末生产中。 操作等特点,被广泛地应用于粉末生产中。 在相同的工艺条件下, 在相同的工艺条件下 , 添加少量的助磨剂往往可 10) 使粉碎效率成倍地提高( 使粉碎效率成倍地提高(图7-10)。
粉末冶金与陶瓷材料的成型工艺技术

粉末冶金与陶瓷材料的成型工艺技术粉末冶金是一种重要的材料成型技术,它通过将金属或非金属粉末在高温下压制成形,进而得到各种金属零件和陶瓷材料。
粉末冶金不仅可以制造出形状复杂的零件,还能够获得优良的材料性能,因此被广泛应用于汽车、航空、航天等工业领域。
粉末冶金的成型工艺技术主要分为两个步骤:粉末的制备和成型。
首先是粉末的制备。
粉末冶金所需的粉末通常通过机械研磨、化学反应、气相沉积等方法制备而成。
机械研磨是最常用的方法,它通过将金属块或合金块放入球磨机中与磨料球一起进行高速旋转,使金属块逐渐研磨成粉末。
化学反应法利用化学反应生成粉末,例如气相法将金属气体于高温下反应生成粉末。
制备好的粉末应具备一定的粒度、形状和分布以满足成型的需求。
其次是成型工艺技术。
成型是将粉末压制成所需形状的过程。
常用的成型工艺有冷压成型、等静压成型和注浆成型等。
冷压成型是最简单的成型方法,它通过将粉末放置在模具中,然后在模具上施加压力,使粉末紧密结合成形。
但冷压成型得到的零件强度较低,通常需要进行后续的烧结工艺。
等静压成型是常用的粉末冶金成型方法。
它通过在模具中施加等压力,使粉末均匀密实地填充模具,然后通过高温烧结使粉末颗粒结合成致密的金属材料。
等静压成型可以获得高密度、高强度的零件,适用于制造各种金属零件。
注浆成型是粉末冶金的一种新型成型工艺。
它通过在模具中注入粉末与流体混合物,然后通过高压使混合物注入模具的空隙中,最后再进行烧结。
注浆成型可以制造出形状复杂的零件,并且具有较高的密度和强度。
总之,粉末冶金是一种重要的材料成型技术,它通过粉末的制备和成型工艺来制造各种金属零件和陶瓷材料。
不同的成型工艺可以得到不同性能的材料,所以在应用中需要根据具体要求来选择合适的成型工艺。
粉末冶金是一种重要的材料成型技术,其广泛应用于汽车、航空、航天等众多领域。
通过将金属或非金属粉末在高温下压制成形,可获得形状复杂且性能优良的材料。
下面将进一步探讨粉末冶金与陶瓷材料的成型工艺技术。
粉末冶金工艺(共17张PPT)

粉末冶金工艺过程
• 粉末冶金材料是指不经熔炼和铸造,直接 用几种金属粉末或金属粉末与非金属粉末, 通过配制、压制成型,烧结和后处理等制 成的材料。粉末冶金是金属冶金工艺与陶 瓷烧结工艺的结合,它通常要经过以下几 个工艺过程:
一、粉料制备与压制成型
• 常用机械粉碎、雾化、物理化学法制取粉 末。制取的粉末经过筛分与混合,混料均 匀并加入适当的增塑剂,再进行压制成型, 粉粒间的原子通过固相扩散和机械咬合作 用,使制件结合为具有一定强度的整体。 压力越大则制件密度越大,强度相应增加。 有时为减小压力合增加制件密度,也可采 用热等静压成型的方法。
三、后处理
• 一般情况下,烧结好的制件能够达到所需 性能,可直接使用。但有时还需进行必要 的后处理。如精压处理,可提高制件的密 度和尺寸形状精度;对铁基粉末冶金制件 进行淬火、表面淬火等处理可改善其机械 性能;为达到润滑或耐蚀目的而进行浸油 或浸渍其它液态润滑剂;将低熔点金属渗 入制件孔隙中去的熔渗处理,可提高制件 的强度、硬度、可塑性或冲击韧性等。
粉末冶金工艺的基本工序
• 1、原料粉末的制备。现有的制粉方法大体 可分为两类:机械法和物理化学法。而机 物理化学法又分为:电化腐蚀法、还原法、化合法、还原-化合法、气相沉积法、液相沉积法以及电解法。
粉末冶金方法起源于公元前三千多年。 从民用工业到军事工业;
械法可分为:机械粉碎及雾化法;物理化 现有的制粉方法大体可分为两类:机械法和物理化学法。
将低熔点金属渗入制件孔隙中去的熔渗处理,可提高制件的强度、硬度、可塑性冲击韧性等。 3、由于粉末冶金工艺在材料生产过程中并不熔化材料,也就不怕混入由坩埚和脱氧剂等带来的杂质,而烧结一般在真空和还原气氛中进行,不 怕氧化,也不会给材料任何污染,故有可能制取高纯度的材料。
粉末冶金与陶瓷材料的成形工艺
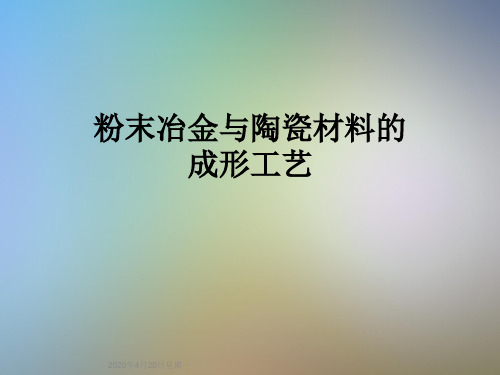
液相的数量和性质:水分是泥团出现可塑性的必 要条件,当水分适量时才能呈现最大可塑性。
第一节 粉体成形原理
可塑性评价指标:σy*εp 。 屈服值随含水量增加而减少; 最大变形量随含水量增加而增加。
•Forming theory •of powder
•可塑泥团的可塑性与含水量的关系
第一节 粉体成形原理
•Forming theory •of powder
粉料的堆积(填充)特性 与形状有关:拱桥效应,形状越不规则,空隙率 越高。 与粒径分布有关:粒径分布越宽,空隙率越小, 堆积密度越大。
粉料的流动性 自然安息角越小,反映出流动性越好 球形粉末的流动性好
第一节 粉体成形原理
•Forming theory •of powder
粉末冶金与陶瓷材料的 成形工艺
2020年4月20日星期一
第七章 粉末冶金与陶瓷材料的成形工艺
本章基本要求 粉体的基本物理性能 粉体成形原理 了解几种常用的成形工艺
第七章 目录
❖ 第一节 粉体成形原理 ❖ 第二节 粉体制备技术 ❖ 第三节 粉末冶金的成形工艺 ❖ 第四节 陶瓷材料的成形工艺 ❖ 第五节 烧结 ❖ 第六节 陶瓷与粉末快速成形工艺 ❖
粉碎法:机械粉碎、气流粉碎 不易制备1微米以下的微细颗粒 设备定型化,产量大,容易操作,被广泛地应用 于粉末生产中,属于物理法 机械合金化(高速高能球磨)
第一节 粉体成形原理
第一节 粉体成形原理
•Forming theory •of powder
与材料液态铸造成形与固态塑性成形方法不同,粉 末冶金与陶瓷的成形方法是利用粉末特有的性能,通 过坯体成形、烧结等系列工艺组成的。
生产工艺过程:
粉末冶金与陶瓷所用原材料都是“粉体”
粉末冶金与陶瓷材料的成型工艺PPT文档共68页

31、只有永远躺在泥坑里的人,才不会再掉进坑里。——黑格尔 32、希望的灯一旦熄灭,生活刹形成天才的决定因素应该是勤奋。——郭沫若 35、学到很多东西的诀窍,就是一下子不要学很多。——洛克
粉末冶金与陶瓷材料的成型工艺
1、合法而稳定的权力在使用得当时很 少遇到 抵抗。 ——塞 ·约翰 逊 2、权力会使人渐渐失去温厚善良的美 德。— —伯克
3、最大限度地行使权力总是令人反感 ;权力 不易确 定之处 始终存 在着危 险。— —塞·约翰逊 4、权力会奴化一切。——塔西佗
5、虽然权力是一头固执的熊,可是金 子可以 拉着它 的鼻子 走。— —莎士 比
第六章粉末冶金及陶瓷成型技术

6.1 粉末冶金及陶瓷成型的基本原理
➢ 熔铸法 熔、炼、铸 铸件 机加工零件 铸坯塑性成形热处理 机加工零件
➢ 粉末冶金法 制粉(powder making)压型 (pressing)烧结(sintering)
6.1 粉末冶金及陶瓷成型的基本原理
6.1 粉末冶金及陶瓷成型的基本原理
1.概述
➢金属材料 冶炼→铸造
仍然连通,形如隧道。
6.2 粉体的成形方法及设备
6. 2.5烧结 烧结过程
烧结后期: 传质继续进行,粒子长大,气孔变成孤立闭气孔,密
度达到95%以上,制品强度提高。
6.2 粉体的成形方法及设备
6. 2.5烧结 烧结过程
❖按照烧结过程有无明显的液相出现进行分类,可 分为固相烧结和液相烧结两类。
固相烧结:指烧结温度下基本上无液相出现的烧结, 如高纯氧化物之间的烧结过程。
❖采用热等静压法获 得的制品,性能优 良、均匀、强度高, 但成本较高。
谢谢大家!
6.2 粉体的成形方法及设备
浇注成形
❖浇注成形是陶瓷坯体成形中的一个基本成 形工艺,在粉末冶金中有时也用来成形一 些形状比较复杂的零件。
6.2 粉体的成形方法及设备
6. 2.5烧结
烧结的基本原理
烧结过程
❖ 烧结是将成形的坯体在低于其主要成分熔点的温 度下加热,粉体相互结合并发生收缩与致密化, 形成具有一定强度和性能的固体材料的过程。
许多雾化法部是采用双液流:一为液态金属流,—为液 体或气体流。后者冲击液态金属流,将之破碎成金属液 滴,随后凝固成粉末颗粒。对于制取铁、钢粉末,一般 用水或油作为冲击流体;对于某些特殊金属和/或应用, 则采用空气、水蒸气或惰件气体作为冲击流体;对 于其他金属,用惰性气体氮、氩或氮作为雾化介质;在 某些场合.采用水蒸气。
CIM陶瓷粉末注射成型技术ppt课件

脱脂工艺
• 脱脂是通过加热及其它物理方法将成型体内的有机 物排除并产生少量烧结的过程。与配料、成型、烧 结及陶瓷部件的后加工过程相比,脱脂是注射成型 中最困难和最重要的因素。脱脂过程不正确的工艺 方式和参数使产品收缩不一致,导致变形、开裂、 应力和夹杂。脱脂对其后烧结也很重要,在脱脂过 程中产生的裂纹和变形不能通过烧结来弥补。粘结 剂和脱脂是联系在一起的,粘结剂决定脱脂方式。 目前的脱脂工艺除了传统的热脱脂、溶剂脱脂外, 还有最近几年发展起来的催化脱脂以及水基萃取脱 脂.
陶瓷粉末注射成型技术应用
随着CIM技术的快速发展,其已在一些方面得到了应用 • 瑞士三分之一的手表表壳采用CIM技术生产,材料是称永不磨损的
陶瓷材料氧化锆 • 日本已将内孔直径为0.015mm的氧化锆光纤接头实现产业化,每年
垄断了全球数亿美元的市场 • 美国已实现氧化锆理发推剪的生产和发动机中氮化硅零部件的应用
CIM中几种常见的粘结剂组成
近年来国际上各种陶瓷粉末注射成型中经常用到的较典型的粘结剂,从表中可以
看出,CIM中用粘结剂体系还主要属于热塑性多组分体系。
CIM混料制备
• 混料是粉末和粘结剂的混合物。在整个注射成型的工艺中,粉末和 聚合物粘结剂混合物的制备是最重要的步骤之一。工艺要求混料具 有良好的均匀性、良好的流变特性,以及好的脱脂特征。只有这三 个方面都照顾到的粉末注射系统才是一个成功的体系。
• 粉末注射成型源于20世纪20年代的一种热压铸成型技术,当时已用于生产汽车 火花塞等产品。
• 20世纪50年代,用环氧树脂作粘结剂试制了大量的硬质合金、难熔金属、陶瓷 等,预示着此技术在应用中的地位。但因理论欠缺,加之制粉、成型和烧结等 技术存在一系列不足,离应用的距离还比较远。
粉末冶金成型工艺 PPT
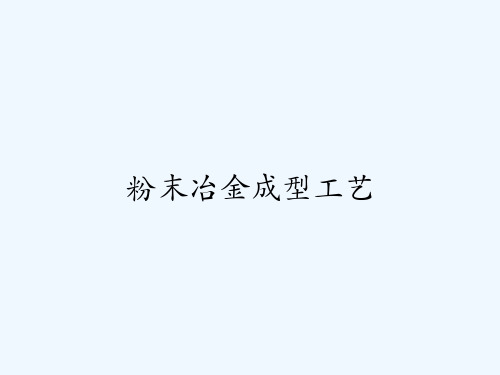
(2) 机械粉碎法
就是靠压碎、击碎与磨削等作用,将 块状金属或合金机械地粉碎成粉末。
粉末冶金成型
(2) 机械粉碎法 • 特点:
– 既就是一种独立制粉方法, – 又常作为某些制粉方法不可缺少得
(4)电解法
从金属盐水溶液中电
粉末冶金成型
解沉积金属粉末。
• 特点: – 电解末高纯度,高密度,高压缩性; – 生产率低,成本高(高于还原法与雾化 法)。
• 应用 – 纯铜粉大多用该法制造。 – 电解铁粉仅在特殊性能要求时才用。
*说明 金属粉末得各种性能均与制粉方法密切相关。
§2 粉末冶金成型工艺简介
补充工序。
• 应用 – 比较适用于脆性材料(虽然所有得金 属与合金都可以被机械地粉碎)
粉末冶金成型
(3)蒸汽冷凝法
即将金属蒸汽冷 凝而制取金属粉末
(4)还原法(常用化学方法)
• 特点:
– 该法简单,费用低
• 应用
– 目前铁粉大部分 由还原法生产。
从固态金属氧 化物或金属化合物 中还原制取金属粉 末,就是最常用得生 产方法之一。
二、粉末成型
粉末冶金成型
2、特殊成型方法(非钢模成型法)
• 分类
(按工作原理 与特点分为)
等静压成型 连续成型 无压成型 注射成型 高能成型等
§2 粉末冶金成型工艺简介
粉末冶金成型
2、特殊成型方法(非• 钢等模静成压型成法型) 借助于高
(1)等静压成型 (2)金属粉末轧制 (3)粉浆浇注
压泵得作用把流体介质(气体或 液体)压入耐高压得钢质密封容 器内,高压流体得静压力直接作 用在弹性模套内得粉末上;粉末 体在同一时间内在各个方向上 均衡地受压而获得密度分布均 衡与强度较高得压坯。
材料加工工艺第五章 粉末冶金及陶瓷成形

材料工艺基础(粉末冶金及陶瓷成形)
4
粉末冶金制品在各工业部门的应用
应用部门 金属粉末和粉末冶金材料与制品应用举例
采矿
硬质合金,金刚石-金属组合材料
机械加工
硬质合金,陶瓷刀具,粉末高速钢
汽车制造
机械零件,摩擦材料,含油轴承,过滤器
造船
摩擦材料,油漆用铝粉
电机制造
含油轴承,铜-石墨电刷
精密仪器
加压方式的影响
➢ 振动压制 ➢ 磁场压制
材料工艺基础(粉末冶金及陶瓷成形)
11
6.3.2 粉末等静压成形
将待压试样置于高压容器中,利 用液体介质不可压缩的性质和均 匀传递压力的性质从各个方向对 试样进行均匀加压的一种成形方 法。
材料工艺基础(粉末冶金及陶瓷成形)
12
粉末等静压成形工艺
材料工艺基础(粉末冶金及陶瓷成形)
24
粉末烧结过程
2. 烧结密度与尺寸的变化
在烧结过程中,多数情况下压制的烧结件尺寸是收 缩的,但由于某些原因有时也会膨胀。比如压制压坯时 压力过大、升温速度过快等。所以为了有效地控制烧结 体的尺寸,要从压制压力、粉末的选择、压模设计和烧 结参数的选择等多方面考虑。
3. 烧结过程中的再结晶与晶粒长大
仪表零件,软磁材料,硬磁材料
电器电子工业 电触头材料,电真空电极材料,磁性材料
计算机工业 记忆元件
石油化工
过滤器,防腐零件,催化剂
国防工业
穿甲弹头,炮弹箍,军械零件
航空工业
刹车片,过滤器,防冻多孔材料,粉末超合金
航天与火箭 发汗材料,难熔金属与合金,纤维强化材料
原子能工业
核燃料元件材料,工反艺基应础堆(粉结末构冶金材及料陶瓷,成控形)制材料
第七章粉末冶金与陶瓷材料的成形工艺

Preparation technologies of powder
金属粉末的合成方法 还原法 雾化法 电解法
化合物粉末的合成方 法
固相法
– 化合反应法 – 热分解反应法 – 氧化物还原法
液相法
– 生成沉淀法 – 水热法 – 溶胶凝胶法 – 溶剂蒸发法 – 熔液法
气相法
– 蒸发-凝聚法 – 气相化学反应法
利用液体介质的不可压缩性和均匀传递压力性 先将配好坯料装入用塑料或橡胶做成的弹性模具内,置
于高压容器内,密封后,打入高压液体介质,压力传递 至弹性模具对坯料加压。释放压力取出模具,得到坯件。 形状复杂、大件、细而长制品 成型质量高、密度高而均匀 模具寿命长、成本低
Forming techniques
粉碎法:机械粉碎、气流粉碎 不易制备1微米以下的微细颗粒 设备定型化,产量大,容易操作,被广泛地应用 于粉末生产中,属于物理法 机械合金化(高速高能球磨)
合成法:通过离子、原子、分子反应,成核、生长、 收集、后处理获得微细颗粒 ✓纯度高 ✓粒度可控 ✓均匀性好 ✓颗粒微细
第二节 粉体制备技术
强化注浆方法:(提高吸浆速度和坯体强度) 真空注浆 离心注浆 压力注浆
❖ (2)热压铸成形
利用石蜡的热流行特点,与坯料配合,是用金属模具在 压力下成形,冷凝后坯体能够保持其形状。 蜡浆料的制备:浆坯料加入到以石蜡为主的粘结剂 中 热压铸 高温排蜡
Forming techniques
第三节 粉末冶金成形工艺
Powder metallurgy
❖ 粉浆浇注成形
将粉末预先制成悬浮状或浆糊状物质,然后注入石膏 模中的成形方法,叫粉浆浇注.
粉浆的制备 模具材料:石膏(200度失去结晶水) 浇注方法: 手工浇注(倾倒浇注)、压缩空气浇注
第六章__粉末冶金及陶瓷成型技术

粉体的成形方法及设备
2.2粉体的制备
用机械粉碎法生产粉末,通常只能用于脆性金属,也可用 于将脆性的金属的金属间化合物或经脆件处理的金属制成 粉末。一般不易获得粒径在1 mm以下的微细颗粒。
物理化学法 液体金属雾化法
许多雾化法部是采用双液流:一为液态金属流,—为液 体或气体流。后者冲击液态金属流,将之破碎成金属液 滴,随后凝固成粉末颗粒。对于制取铁、钢粉末,一般 用水或油作为冲击流体;对于某些特殊金属和/或应用, 则采用空气、水蒸气或惰件气体作为冲击流体;对 于其他金属,用惰性气体氮、氩或氮作为雾化介质;在 某些场合.采用水蒸气。
粉体的成形方法及设备
2.4 粉体的成形
通过一定的方法,将粉体原料制成具有一 定形状、尺寸、密度和强度坯体的过程称 为成形 (1)压制成形 ——粉末冶金、陶瓷 (2)塑性成形 ——陶瓷 (3)浇注成形 ——陶瓷、粉末冶金
粉体的成形方法及设备
2.4 粉体的成形
压制成形——是粉 末冶金和陶瓷成形 的常用方法之一。 将松散的粉状原料 放入模具中,并施 加一定的压力后便 获得块状坯体。
粉体的成形方法及设备
2.1.粉体的基本性能
粒度: 颗粒大小:通常用直径表示。不规则颗粒用等效半径。 粒度分布:不同大小颗粒占的百分比。 颗粒形状: 颗粒形状表示粉体颗粒的几何形状, 常用的颗粒形状有球形、片形、针形、柱形等。
粉末冶金和陶瓷成形技术培训课件:粉末冶金制品的结构工艺性
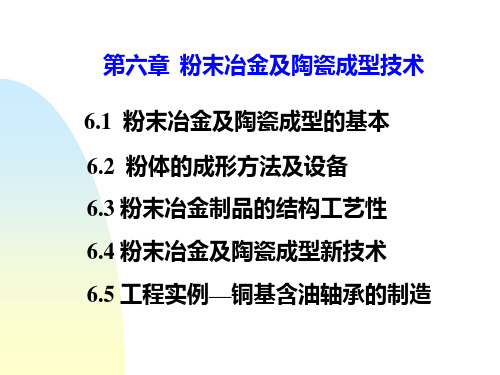
阅读材料—电灯钨丝与粉末冶金
用钨丝(tungsten filament)作为灯丝制作白炽灯, 是照明发展史上的一座里程碑,同时也奠定 了粉末冶金技术的基础。
2. 避免局部薄壁,以利于装 粉压实和防止出现裂纹。
3. 设计时应避免与压制方向垂 直或斜交的沟槽、孔腔,以 利于压实和减少余块。
4. 沿压制方向的横截面要均 匀变化。
6.4 粉末冶金及陶瓷成形新技术
1. 快速成型技术 2. 等静压成型
一、快速成型技术
1. 选择性激光烧结
选择性激光烧结(selective laser sintering, SLS)
四、后处理
粉末冶金和陶瓷制品在烧结中通常产生收缩、 变形以及一些表面缺陷,烧结后的表面粗糙 度差,一般情况下,不能作为最终产品直接 使用。为了获得所需要的尺寸精度和表面质 量,需要对制品进行机械加工。
浸渍。 精整 精压 复压。
6.3 粉末冶金制品的结构工艺性
模压法是常用的成形方法,因此,采用压制成 形的零件应考虑其结构工艺性。 1. 尽量采用简单、对称的形状,避免尖角。
(2)当密度达到一定程度 后,密度不随压力的增 大而明显增加。
(3)继续增大成形压力, 使颗粒之间的结合进一 步增强,坯体的密度增 大。
2. 塑性成形
塑性成形利用各种外力,对具有可塑性的坯料 进行成形加工,迫使坯料在外力作用下产生塑 性变形,并保持其形状,从而制成坯体。
3. 浇注成形
浇注成形是陶瓷坯体成形中的一个基本成形工 艺,在粉末冶金中有时也用来成形一些形状比 较复杂的零件。
粉碎法通过将粗粒的原材料粉碎而获得细粉,粉碎过程中基本 不发生化学反应。但是在粉碎过程中会混入杂质,而且采用粉 碎法一般不易获得粒径在1 mm以下的微细颗粒。物理化学法通 过物理或化学作用,改变材料的化学成分或聚集状态而获取粉 体。这种方法的特点是粉体的纯度和粒度可控,均匀性好,颗 粒微细。并且可以实现粉体颗粒在分子级水平上的复合和均化。
粉末冶金和陶瓷的制备汇总课件

高温陶瓷制备工艺
01
02
03
04
高温合成
在高温条件下,通过固相反应 或熔融反应合成陶瓷材料。
烧结工艺
采用高温烧结炉,在高温下对 陶瓷原料进行烧结,促进颗粒
之间的结合。
热压工艺
在高温和压力的作用下,将陶 瓷原料压制成制品,可缩短烧 成时间并提高制品致密度。
熔融工艺
将陶瓷原料加热至熔融状态, 再冷却固化得到陶瓷制品。
新型陶瓷制备工艺
化学气相沉积(CVD)
利用化学反应将气体中的元素沉积在基体上 形成陶瓷膜。
溶胶-凝胶法
通过溶胶凝胶化反应将前驱物转化为陶瓷材 料。
物理气相沉积(PVD)
利用物理方法将气体中的元素蒸发并沉积在 基体上形成陶瓷膜。
3D打印技术
利用3D打印设备将陶瓷粉末逐层堆积成型 ,制备出具有复杂形状的陶瓷制品。
06 未来发展趋势与挑战
新材料研发
高性能复合材料
环境友好材料
通过优化材料成分和微观结构,提高 材料的综合性能,满足各种复杂应用 场景的需求。
开发低成本、低能耗、低碳排放的绿 色环保材料,减少对环境的负面影响 。
智能材料
研究具有自适应、自修复、记忆等功 能的材料,拓展其在传感器、执行器 、结构健康监测等领域的应用。
航空航天
高性能粉末冶金和陶瓷材 料在航空航天领域的应用 将进一步拓展。
新能源
粉末冶金和陶瓷材料在新 能源领域,如太阳能、风 能等,具有广阔的应用前 景。
THANKS FOR WATCHING
感谢您的观看
粉末冶金具有材料利用率高、产 品性能优异、可加工复杂形状等
特点。
粉末冶金可以制备传统熔炼方法 难以制备的高熔点材料、难熔金
粉末冶金和陶瓷的制备PPT课件
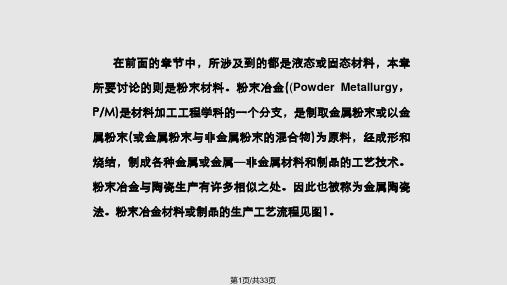
水溶液电解
与
淀
粉
末
近球形 气体雾化,置换(溶 不规则形 水雾化,机械粉碎,化学
生
液)
沉淀
产
方
多角形 机械粉碎
法
多 孔 海 绵 金属氧化物还原 状
的
关
系
片状
塑性金属机械研 碟 状 磨
金属旋涡研磨
第12页/共33页
粉末的制取及特征——粉末的形状和
结构
粉末颗粒的形状直接影响粉末的流动性、松装密度、 透气性、压制性及烧结强度等制粉工艺对粉末颗粒的 晶体结构起主要作用。一般情况下,粉末颗粒为多晶 体结构。晶粒内存在亚结构,同时晶体还存在严重的 不完整性,如空隙、畸变、夹杂等,晶粒内部往往含 有较高的空位浓度和位错密度。
第1页/共33页
图1 粉末冶金材料或制品的工艺流程
第2页/共33页
粉末冶金的生产过程
粉末冶金的生产过程主要包括粉末的制取、成形和烧结。
粉末制备
坯料制备
成型
干燥
烧结
后处理
成品
热压或热等静压烧结
粉末冶金的生产过程示意图
3
第3页/共33页
粉末冶金的生产过程
1、 金属粉末的制取和准备 粉末冶金所用的原料粉可能是一种,也可能是数种
热压铸成形
29
第29页/共33页
塑性成形
包括:挤压、喷射成形, 旋坯成形等
(a) Extruding and (b) jiggering operations. Source: R. F. Stoops. 第30页/共33页
坯体干燥与陶瓷烧成
1、坯体干燥
采用注浆法成形的泥浆,含水率一般在30%-35%,呈流动状 态;用塑性成形的泥料,含水率为15%-26.7%,呈可塑状态; 即使干压或半干压的制品,其含水量也为0.1%-8%。
- 1、下载文档前请自行甄别文档内容的完整性,平台不提供额外的编辑、内容补充、找答案等附加服务。
- 2、"仅部分预览"的文档,不可在线预览部分如存在完整性等问题,可反馈申请退款(可完整预览的文档不适用该条件!)。
- 3、如文档侵犯您的权益,请联系客服反馈,我们会尽快为您处理(人工客服工作时间:9:00-18:30)。
第七章 粉末冶金与陶瓷材 料的成型工艺
粉末冶金(Powder Metallurgy)与陶瓷(Ceramic) 的主要制备工艺过程包括粉末制备、成型和烧结。其生产 工艺过程可简单地表示为:粉末制备坯料制备成型干燥烧 结后处理热压或热等静压烧结成品
粉末制备
坯料制备
成型
粉碎的过程是由机械能转变为粉料表面能的能量转化 过程。机械粉碎法因其设备定型化,产量大,容易操作 等特点,被广泛地应用于粉末生产中。
在相同的工艺条件下,添加少量的助磨剂往往可使 粉碎效率成倍地提高(图7-10)。
第二节 粉体制备技术
二、 合成法(Synthetic)
1. 原料合成的目的和作用 2. 合成方法
均距离越小,吸引力增大,位移时所需克服的阻 力增大,流动性减少。
第一节 粉体成型原理
3)电解质的作用 向泥浆中加入电解质是改善其流动性和稳
定性的有效方法。 4)泥浆的pH值
pH值影响其解离程度,又会引起胶粒ζ电位发生变化,导致改变胶粒表面的吸力与 斥力的平衡,最终使这类氧化物胶溶或絮凝 。
第一节 粉体成型原理
粒度是指粉料的颗粒大小,通常以颗粒半径r 或直径d表示。粒度分布是指多分散体系中各种 不同大小颗粒所占的百分比。
第一节 粉体成型原理
2. 颗粒的形态与拱桥效应
人们一般用针状、多面体状、柱状、球状等来 描述颗粒的形态。
粉料自由堆积的空隙率往往比理论计算值大得 多,就是因为实际粉料不是球形,加上表面粗糙 图表,以及附着和凝聚的作用,结果颗粒互相交 错咬合,形成拱桥型空间,增大了空隙率。这种 现象称为拱桥效应(见图7-1)。
耗压力。 压制过程中的总压力P=P1+P2,即成型压力。
(2)加压方式 图7-4为加压方式和压力分布关系图。 (3)加压速度 (4)添加剂的选用
第一节 粉体成型原理
3. 对压制用粉料的工艺性能要求
由于压制成型时粉料颗粒必须能充满模 型的各个角落,因此要求粉料具有良好的 流动性。为了得到较高的素坯密度,粉料 中包含的气体越少越好,粉料的堆积密度 越高越好。
干燥
烧结
后处理
成品
热压或热等静压烧结
本章将讨论粉末冶金与陶瓷的成型原理、粉体制备技术 、粉末冶金的成型工艺和陶瓷材料的成型工艺,最后介绍 快速成型工艺。
第一节 粉体成型原理
第一节 粉体成型原理
一、 粉料的基本物理性能
1.粒度(Particle Size)和粒度分布(Particle Size Distribution)
塑性时所需的水分愈少,最大可塑性愈低;颗 粒愈细则比表面愈大,每个颗粒表面形成水膜 所需的水分愈多,由细颗粒堆积而成的毛细管 半径越小,产生的毛细管力越大,可塑性也高 。不同形状颗粒的比表面是不同的,因而对可 塑性的影响也有差异。 (2)液相的数量和性质
水分是泥团出现可塑性的必要条件。泥团中 水分适当时才能呈现最大的可塑性,如图7-7所 示。
第一节 粉体成型原理
4. 粉 料 的 堆 积 ( 填 充 ) 特 性 (Packing Property)
单一颗粒(即纯粗颗粒或细颗粒)堆积时的 空隙率约40%。若用二种粒度(如平均粒径比为 10:1)配合则其堆积密度增大;而采用三级粒度 的颗粒配合则可得到更大的堆积密度。
5. 粉料的流动性(Flowing Property)
(1)金属粉末的合成方法 1)还原法(Reduction Method) 还原法的基本原理就是所使用的还原剂对氧的亲和
力比相应金属对氧的亲和力大,因而能够夺取金属氧 化物中的氧而使金属被还原出来。
2)雾化法(Atomization Method) 雾化法生产金属和合金粉末就是利用高压气体(空 气、惰性气体)或高压液体(通常是水)通过喷嘴作 用于金属液流使其迅速地碎化成粉末。 3)电解法(Electrolysis Method) 电解法既可以在水溶液中进行,也可以在熔盐状态 下进行。
(1)密度的变化 (2)强度的变化 (3)坯体中压力的分布 图7-3为单面加压是坯体内部压力分布情况 。
第一节 粉体成型原理
2. 影响坯体密度(Density)的因素
(1)成型压力 压制过程中,施加于粉料上的压力主要消耗在以下二
方面: 1)克服粉料的阻力P1,称为净压力。 2)克服粉料颗粒对模壁摩擦所消耗的力P2,称为消
第一节 粉体成型原理
三、 可塑泥团的成型原理
1. 可 塑 泥 团 的 流 变 特 性 (Rheological Behavior)
图7-5为粘土泥团的应力-应变曲线。 图7-6表示了粘土的含水量与其应力-应变 -曲线的关系。
第一节 粉体成型原理
2. 影响泥团可塑性的因素
(1)固相颗粒大小和形状 一般地说,泥团中固相颗粒愈粗,呈现最大
第一节 粉体成型原理
3. 对可塑坯料的工艺性能要求
可塑性好,含水量适当,干燥强度高,收 缩率小,颗粒细度适当,空气含量低。
第一节 粉体成型原理
四、 泥浆/粉浆的成型原理
1. 泥浆的流变特性
(1)泥浆的流动曲线 图7-8为一些陶瓷原料泥浆的流动曲线。
(2)影响泥浆流变性能的因素 1)泥浆的浓度 图7-9为不同浓度的可塑泥浆的流动曲线。 2)固相的颗粒大小 一定浓度的泥浆中,固相颗粒越细、颗粒间平
第一节 粉体成型原理
3. 粉体的表面特性
(1)粉体颗粒的表面能(surface energy)和表面 状态
粉体颗粒表面的“过剩能量”称为粉体颗粒的表 面能。
表7-1是当粒径发生变化时,一般物质颗粒其原 子数与表面原子数之间的比例变化。
(2)粉体颗粒的吸附与凝聚(Coagulation) 一个颗粒依附于其它物体表面上的现象称之为附 着。而凝聚则是指颗粒间在各种引力作用下的团聚 。
2.注浆成型对泥浆的工艺性能的要求
制备出的泥浆应能够满足下列基本要求 :流动性好,稳定性好,适当的触变性, 含水量少,滤过性好,坯体强度高,脱模 容易,不含气泡。
第二Байду номын сангаас 粉体制备技术
第二节 粉体制备技术
一 、 粉 碎 (Porphyrization) 与 机 械 合 金 化 (Mechanical Alloying)方法
粉料虽然由固体小颗粒组成,但由于其分散 度较高,具有一定的流动性。当堆积到一定高度 后,粉料会向四周流动,始终保持为圆锥体(图 7-2),其自然安息角(偏角)α保持不变。
第一节 粉体成型原理
二、 压制成型原理
压制成型是基于较大的压力,将粉状坯料在 模型中压成块状坯体的。
1. 压制成型过程中坯体的变化