Alignment 光刻对准
光刻机中的自动对位与校准技术

光刻机中的自动对位与校准技术自动对位与校准技术是光刻机中的重要技术之一。
在光刻制程中,准确的对位和校准是确保产品质量和工艺稳定性的关键步骤。
本文将介绍光刻机中常见的自动对位与校准技术,并探讨其在半导体制造过程中的应用和影响。
自动对位与校准技术是光刻机中的关键控制技术,可以实现光刻模板与半导体晶圆的精确对位。
光刻模板(也称为掩膜)上有图案,通过光刻机将这个图案投影到半导体晶圆上,从而实现芯片的制作。
而对位技术的目的则是将光刻模板上的图案准确地对准到晶圆上的指定位置,确保每一块晶圆上的芯片都具有一致的制作效果。
传统的对位与校准技术主要依靠人工操作来完成,但这种方式存在着操作效率低、人为因素干扰大等问题。
为了提高操作效率和准确性,光刻机中的自动对位与校准技术得以广泛应用。
光刻机中的自动对位与校准技术主要分为两种:基于对比法的全局对位和基于特征法的局部对位。
基于对比法的全局对位是一种通过比对光刻模板上的参考点和晶圆上的对位标记来实现对位准确性的方法。
在光刻过程中,光刻机会使用精密的图像传感器来捕捉光刻模板和晶圆上的图案。
然后,通过算法分析图像中的特征点,确定模板和晶圆之间的偏差,最终将晶圆上的芯片与模板上的图案进行对正。
这种方法操作简单,适用于对位准确度要求不太高的场景,如批量生产等。
而基于特征法的局部对位则是通过检测光刻模板和晶圆上特定区域的特征来实现对位的。
这种方法通常需要在光刻模板和晶圆上设计特定的对位标记或辅助结构,通过对齐这些特定的标记来实现对位的准确性。
这种方法对于对位精度要求较高的场景更为适用,如微纳制造领域。
自动对位与校准技术在半导体制造过程中起着至关重要的作用。
首先,它可以提高生产效率。
在传统的人工操作中,对位校准需要耗费大量时间和人力,而自动对位技术可以减少操作时间,提高生产效率。
其次,它可以提高产品质量和制造稳定性。
自动对位技术通过减少人为干扰,避免了人为操作中可能出现的误差,从而提高了对位的精确性和一致性,确保了产品质量和制程的稳定性。
光刻工艺介绍

光刻工艺介绍一、定义与简介光刻是所有四个基本工艺中最关键的,也就是被称为大家熟知的photo,lithography,photomasking, masking, 或microlithography。
在晶圆的制造过程中,晶体三极管、二极管、电容、电阻和金属层的各种物理部件在晶圆表面或表层内构成,这些部件是预先做在一块或者数块光罩上,并且结合生成薄膜,通过光刻工艺过程,去除特定部分,最终在晶圆上保留特征图形的部分。
光刻其实就是高科技版本的照相术,只不过是在难以置信的微小尺寸下完成,现在先进的硅12英寸生产线已经做到22nm,我们这条线的目标6英寸砷化镓片上做到0.11um。
光刻生产的目标是根据电路设计的要求,生成尺寸精确的特征图形,并且在晶圆表面的位置正确且与其它部件的关联正确。
二、光刻工艺流程介绍光刻与照相类似,其工艺流程也类似:实际上,普通光刻工艺流程包括下面的流程:1)Substrate Pretreatment 即预处理,目的是改变晶圆表面的性质,使其能和光刻胶(PR)粘连牢固。
主要方法就是涂HMDS,在密闭腔体内晶圆下面加热到120℃,上面用喷入氮气加压的雾状HMDS,使得HMDS和晶圆表面的-OH健发生反应已除去水汽和亲水健结构,反应充分后在23℃冷板上降温。
该方法效果远比传统的热板加热除湿好。
2)Spin coat即旋转涂光刻胶,用旋转涂布法能提高光刻胶薄膜的均匀性与稳定性。
光刻胶中主要物质有树脂、溶剂、感光剂和其它添加剂,感光剂在光照下会迅速反应。
一般设备的稳定工作最高转速不超过4000rpm,而最好的工作转速在2000~3000rpm。
3)Soft Bake(Pre-bake)即软烘,目的是除去光刻胶中溶剂。
一般是在90℃的热板中完成。
4)Exposure即曝光,这也是光刻工艺中最为重要的一步,就是用紫外线把光罩上的图形成像到晶圆表面,从而把光罩上面的图形转移到晶圆表面上的光刻胶中。
半导体工艺与制造技术习题答案(第五章)
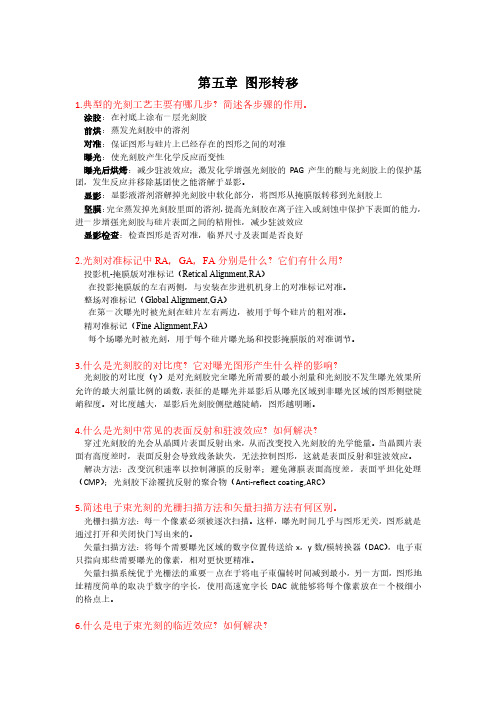
第五章图形转移1.典型的光刻工艺主要有哪几步?简述各步骤的作用。
涂胶:在衬底上涂布一层光刻胶前烘:蒸发光刻胶中的溶剂对准:保证图形与硅片上已经存在的图形之间的对准曝光:使光刻胶产生化学反应而变性曝光后烘烤:减少驻波效应;激发化学增强光刻胶的PAG产生的酸与光刻胶上的保护基团,发生反应并移除基团使之能溶解于显影。
显影:显影液溶剂溶解掉光刻胶中软化部分,将图形从掩膜版转移到光刻胶上坚膜:完全蒸发掉光刻胶里面的溶剂,提高光刻胶在离子注入或刻蚀中保护下表面的能力,进一步增强光刻胶与硅片表面之间的粘附性,减少驻波效应显影检查:检查图形是否对准,临界尺寸及表面是否良好2.光刻对准标记中RA,GA,FA分别是什么?它们有什么用?投影机-掩膜版对准标记(Retical Alignment,RA)在投影掩膜版的左右两侧,与安装在步进机机身上的对准标记对准。
整场对准标记(Global Alignment,GA)在第一次曝光时被光刻在硅片左右两边,被用于每个硅片的粗对准。
精对准标记(Fine Alignment,FA)每个场曝光时被光刻,用于每个硅片曝光场和投影掩膜版的对准调节。
3.什么是光刻胶的对比度?它对曝光图形产生什么样的影响?光刻胶的对比度()是对光刻胶完全曝光所需要的最小剂量和光刻胶不发生曝光效果所允许的最大剂量比例的函数,表征的是曝光并显影后从曝光区域到非曝光区域的图形侧壁陡峭程度。
对比度越大,显影后光刻胶侧壁越陡峭,图形越明晰。
4.什么是光刻中常见的表面反射和驻波效应?如何解决?穿过光刻胶的光会从晶圆片表面反射出来,从而改变投入光刻胶的光学能量。
当晶圆片表面有高度差时,表面反射会导致线条缺失,无法控制图形,这就是表面反射和驻波效应。
解决方法:改变沉积速率以控制薄膜的反射率;避免薄膜表面高度差,表面平坦化处理(CMP);光刻胶下涂覆抗反射的聚合物(Anti-reflect coating,ARC)5.简述电子束光刻的光栅扫描方法和矢量扫描方法有何区别。
光刻工艺 光刻对准

NIKON工艺一、对位概述对光刻而言,其最重要的工艺控制项有两个,其一是条宽控制,其二是对位控制。
随着产品特征尺寸的越来越小,条宽和对位控制的要求也越来越高。
目前0.5um的产品,条宽的要求一般是不超过中心值的10%,即条宽在0.5±0.05um之间变化;对位则根据不同的层次有不同的要求,一般而言,在多晶和孔光刻时对位的要求最高,特别是在孔光刻时,由于孔分为有源区和多晶上的孔,对位的要求更高,部分产品多晶上孔的对位偏差甚至要求小于0.14um。
在现在的IC电路制造过程中,一个完整的芯片一般都要经过十几到二十几次的光刻,在这么多次光刻中,除了第一次光刻以外,其余层次的光刻在曝光前都要将该层次的图形与以前层次留下的图形对准。
对位的过程存在于上版和圆片曝光的过程中,其目的是将光刻版上的图形最大精度的覆盖到圆片上已存在的图形上。
它包括了以下几部分:光刻版对位系统、圆片对位系统(又包括LSA、FIA等)。
对于NIKON的步进重复曝光机(Step & Repeat)而言,对位其实也就是定位,它实际上不是用圆片上的图形与掩膜版上的图形直接对准来对位的,而是彼此独立的,即,确定掩膜版的位置是一个独立的过程,确定圆片的位置又是另一个独立的过程。
它的对位原理是,在曝光台上有一基准标记,可以把它看作是定位用坐标系的原点,所有其它的位置都相对该点来确定的。
分别将掩膜版和圆片与该基准标记对准就可确定它们的位置。
在确定了两者的位置后,掩膜版上的图形转移到圆片上就是对准的。
光刻版对位系统略。
圆片对位系统圆片对位系统中,根据特定的应用或为解决依赖于圆片工艺(如铝层)而产生的对位错误,发展了各种各样对位系统:LSA、LIA、FIA。
这里先作一个比较:这三种方式的最大差异是处理对位过程中遇到问题的侧重点不同,特别是在铝上,高温溅射的铝在填充对位标记的台阶时,由于铝表面构造粗糙和铝对对位标记的填充不对称等原因,对位的精度往往要比其它层次差很多。
光刻机中的自动对位与校准技术
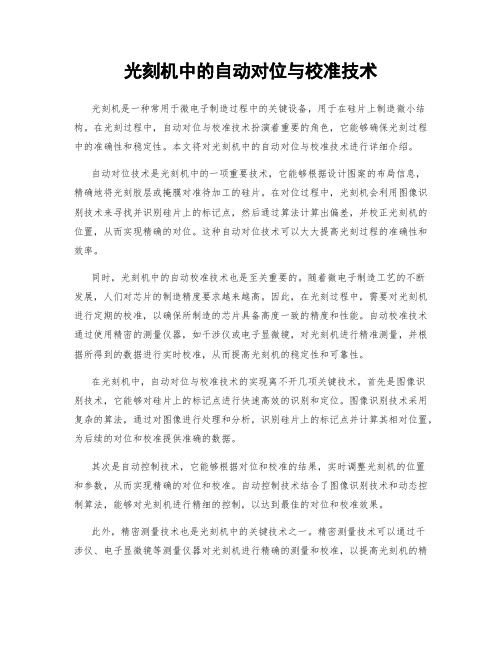
光刻机中的自动对位与校准技术光刻机是一种常用于微电子制造过程中的关键设备,用于在硅片上制造微小结构。
在光刻过程中,自动对位与校准技术扮演着重要的角色,它能够确保光刻过程中的准确性和稳定性。
本文将对光刻机中的自动对位与校准技术进行详细介绍。
自动对位技术是光刻机中的一项重要技术,它能够根据设计图案的布局信息,精确地将光刻胶层或掩膜对准待加工的硅片。
在对位过程中,光刻机会利用图像识别技术来寻找并识别硅片上的标记点,然后通过算法计算出偏差,并校正光刻机的位置,从而实现精确的对位。
这种自动对位技术可以大大提高光刻过程的准确性和效率。
同时,光刻机中的自动校准技术也是至关重要的。
随着微电子制造工艺的不断发展,人们对芯片的制造精度要求越来越高。
因此,在光刻过程中,需要对光刻机进行定期的校准,以确保所制造的芯片具备高度一致的精度和性能。
自动校准技术通过使用精密的测量仪器,如干涉仪或电子显微镜,对光刻机进行精准测量,并根据所得到的数据进行实时校准,从而提高光刻机的稳定性和可靠性。
在光刻机中,自动对位与校准技术的实现离不开几项关键技术。
首先是图像识别技术,它能够对硅片上的标记点进行快速高效的识别和定位。
图像识别技术采用复杂的算法,通过对图像进行处理和分析,识别硅片上的标记点并计算其相对位置,为后续的对位和校准提供准确的数据。
其次是自动控制技术,它能够根据对位和校准的结果,实时调整光刻机的位置和参数,从而实现精确的对位和校准。
自动控制技术结合了图像识别技术和动态控制算法,能够对光刻机进行精细的控制,以达到最佳的对位和校准效果。
此外,精密测量技术也是光刻机中的关键技术之一。
精密测量技术可以通过干涉仪、电子显微镜等测量仪器对光刻机进行精确的测量和校准,以提高光刻机的精度和稳定性。
测量结果可以作为反馈信号,用于自动控制系统对光刻机进行实时调整。
总之,光刻机中的自动对位与校准技术是现代微电子制造过程中的重要环节。
它可以提高光刻过程的准确性和效率,保证芯片的制造精度和性能。
双面光刻对准过程
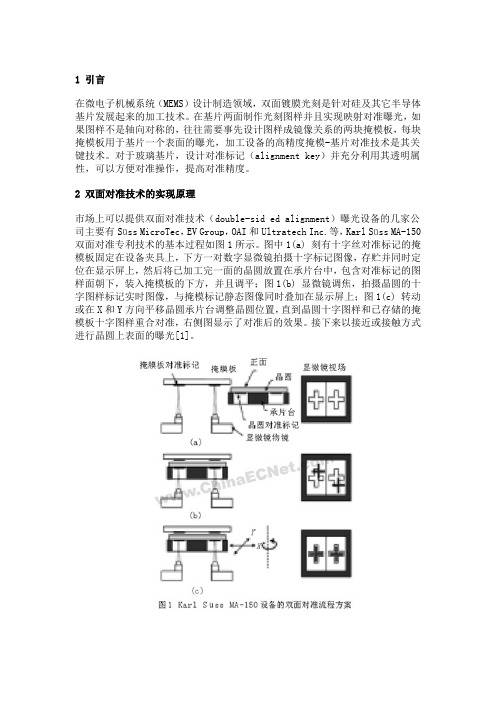
1 引言在微电子机械系统(MEMS)设计制造领域,双面镀膜光刻是针对硅及其它半导体基片发展起来的加工技术。
在基片两面制作光刻图样并且实现映射对准曝光,如果图样不是轴向对称的,往往需要事先设计图样成镜像关系的两块掩模板,每块掩模板用于基片一个表面的曝光,加工设备的高精度掩模-基片对准技术是其关键技术。
对于玻璃基片,设计对准标记(alignment key)并充分利用其透明属性,可以方便对准操作,提高对准精度。
2 双面对准技术的实现原理市场上可以提供双面对准技术(double-sid ed ali gnment)曝光设备的几家公司主要有Süss MicroTec,EV Group,OAI和Ultratech Inc.等,Karl Süss MA-150双面对准专利技术的基本过程如图1所示。
图中1(a) 刻有十字丝对准标记的掩模板固定在设备夹具上,下方一对数字显微镜拍摄十字标记图像,存贮并同时定位在显示屏上,然后将已加工完一面的晶圆放置在承片台中,包含对准标记的图样面朝下,装入掩模板的下方,并且调平;图1(b) 显微镜调焦,拍摄晶圆的十字图样标记实时图像,与掩模标记静态图像同时叠加在显示屏上;图1(c) 转动或在X和Y方向平移晶圆承片台调整晶圆位置,直到晶圆十字图样和已存储的掩模板十字图样重合对准,右侧图显示了对准后的效果。
接下来以接近或接触方式进行晶圆上表面的曝光[1]。
但这里存在一个问题,存储的掩模十字标记的图像位置是以显微镜物镜为参照系的图 1 (b) 中的调焦过程不可避免会导致物镜的抖动,而且两个目镜都需要重新调焦,如果物镜侧移则必然会带来对准误差,如图 2所示。
因此EVG公司的设备调整了对准工艺流程,极力避免物镜的重新调焦。
其做法是把焦平面固定在晶圆承片台的表面,首先安置掩模板,接触到承片台的表面,拍摄并存储对准标记的数字图像,然后平稳地垂直提升掩模板,接下来在承片台上放置晶圆,晶圆的已加工面朝下,由于标记仍然在承片台表面,不需重新调焦,因此避免了可能导致的目镜侧移带来的对准误差 [2],这也是EVG最新的NanoAlign对准技术的主要保证措施之一。
14 nm工艺光刻对准之异常问题与对策分析

集成电路应用 第 36 卷 第 10 期(总第 313期)2019年10月 252.2 晶圆预对准技术晶圆预对准系统(Pre-Alignment Unit)主要保证晶圆传输系统的精度,就是所谓的一级定位系nm 节点,甚至在 10~7 nm 工艺虽然已在世界先进 Fab 投入量产,但是在实际工厂生产制造过程中,会遇到各种工程技术问题需要解决。
本文主要探讨了 14 nm 晶圆在光刻曝光工艺时,晶圆对准之异常问题以及改善措施。
上海市经济和信息化委员会软件和集成电路产业发展专项基金(1500204)。
郑华明,上海华力集成电路制造有限公司,研究方向:集成电路制造。
图 1 ASML NXT 系列光刻机图 3 晶圆的量测图 2 晶圆的传输当晶圆放置在 Pre-alignment 系统放置台时,LED 光源将入射光照射在 wafer边缘,同时 wafer 通过 P-chuck 的旋转装置(Rotation Unit)旋转 wafer。
然后,由下方的 Edge senor 感应器收集光信号。
通过 Edge2.3 预对准温控单元(TSU)Pre-alignment系统中的温控单元(TSU)主要功能是为了保证 wafer 在进入曝光前提前进入更然后,实际上 wafer 与 Pre-alignment中的温控单元(TSU)并不是完全接触的,wafer 之间存在一定的间距(20~30 μm)。
同时,当 wafer 放置在 TSU P-chuck 放置台时,TSU 盘面很多圈状的小孔内是在同时进行真空(Vacuum)和纯净空气(CDA)作业控制,都是为了保证都到最佳的温度控制效果。
图 7 所示为 wafer 在 TSU 时的状态情况。
3 异常问题及改善方案3.1 问题描述3.3.2 鱼骨分析图从以下几个方面分析晶圆在光刻机的对准异常情况,如图 9 所示。
3.3.3 验证分析光刻机只是针对 14 nm 工艺产品会产生对准误差过大的问题,其余正常工艺产品都未见异常,所图 4 预对准系统图 5 Edge sensor 与 wafer rotation 关系曲线图 6 预对准系统中的温控单元(TSU)图 7 wafer 在温控单元(TSU)中的侧视图图 8 晶圆在预对准时失效模型图图 9 晶圆对准偏差问题鱼骨分析图通过测试 14 nm 工艺晶圆的翘曲度数据和正常产品比对,也未见明显异常,说明 14 nm 产品晶圆翘曲度状况良好。
半导体工艺与制造技术习题答案(第五章)

第五章图形转移1.典型的光刻工艺主要有哪几步?简述各步骤的作用。
涂胶:在衬底上涂布一层光刻胶前烘:蒸发光刻胶中的溶剂对准:保证图形与硅片上已经存在的图形之间的对准曝光:使光刻胶产生化学反应而变性曝光后烘烤:减少驻波效应;激发化学增强光刻胶的PAG产生的酸与光刻胶上的保护基团,发生反应并移除基团使之能溶解于显影。
显影:显影液溶剂溶解掉光刻胶中软化部分,将图形从掩膜版转移到光刻胶上坚膜:完全蒸发掉光刻胶里面的溶剂,提高光刻胶在离子注入或刻蚀中保护下表面的能力,进一步增强光刻胶与硅片表面之间的粘附性,减少驻波效应显影检查:检查图形是否对准,临界尺寸及表面是否良好2.光刻对准标记中RA,GA,FA分别是什么?它们有什么用?投影机-掩膜版对准标记(Retical Alignment,RA)在投影掩膜版的左右两侧,与安装在步进机机身上的对准标记对准。
整场对准标记(Global Alignment,GA)在第一次曝光时被光刻在硅片左右两边,被用于每个硅片的粗对准。
精对准标记(Fine Alignment,FA)每个场曝光时被光刻,用于每个硅片曝光场和投影掩膜版的对准调节。
3.什么是光刻胶的对比度?它对曝光图形产生什么样的影响?光刻胶的对比度()是对光刻胶完全曝光所需要的最小剂量和光刻胶不发生曝光效果所允许的最大剂量比例的函数,表征的是曝光并显影后从曝光区域到非曝光区域的图形侧壁陡峭程度。
对比度越大,显影后光刻胶侧壁越陡峭,图形越明晰。
4.什么是光刻中常见的表面反射和驻波效应?如何解决?穿过光刻胶的光会从晶圆片表面反射出来,从而改变投入光刻胶的光学能量。
当晶圆片表面有高度差时,表面反射会导致线条缺失,无法控制图形,这就是表面反射和驻波效应。
解决方法:改变沉积速率以控制薄膜的反射率;避免薄膜表面高度差,表面平坦化处理(CMP);光刻胶下涂覆抗反射的聚合物(Anti-reflect coating,ARC)5.简述电子束光刻的光栅扫描方法和矢量扫描方法有何区别。
alignment工艺技术

alignment工艺技术Alignment(对准)是一种常用的工艺技术,广泛应用于光学仪器、半导体制造、电子装备和精密机械等领域。
它的作用是确保工作目标相互之间或与参考标准之间的位置和方向的准确度,从而实现高精度和高质量的加工和组装工作。
Alignment工艺技术主要包括光学对准、机械对准和电子对准三种类型。
光学对准是利用光束的传输和检测功能来对准目标的位置和方向。
这种方法需要使用激光仪或光学传感器来发射和接收光束,通过反射、折射、衍射等原理来确定目标是否对准。
光学对准广泛应用于光学元件的精密定位和组装过程中,例如光学纤维的对准、镜头组件的校准等。
机械对准是利用机械传动装置对准目标的位置和方向。
这种方法适用于需要进行精确定位和组装的机械系统,如加工中心、机器人和精密测量设备等。
机械对准的关键是通过传动机构和控制系统实现对目标位置的微调和调整。
常用的机械对准方法包括螺旋状位移机构、精密导轨和气压定位系统等。
电子对准是利用电子传感器和控制系统对准目标的位置和方向。
这种方法适用于电子器件和电子装备的组装和维修过程中,如印刷电路板的组装、芯片对准和焊接等。
电子对准主要依靠电子传感器对物体的位置、位移和方向进行检测和反馈控制。
常见的电子对准技术包括电容式、电感式和压阻式传感器等。
在使用Alignment工艺技术时,需要注意以下几点:1.选择适当的对准方法。
根据工作目标的特点和工艺要求,选择合适的对准方法,确保能够满足精度和质量要求。
2.调整对准参数。
根据实际情况,调整对准系统的参数,如灵敏度、灵活度和稳定性等,以获得最佳的对准效果。
3.考虑环境因素。
在进行对准过程中,需注意环境因素对对准的影响,如温度、湿度、振动等,避免对准误差的产生。
4.定期检查和校准。
对准系统需要定期检查和校准,以确保其准确度和可靠性。
通过定期保养和维修,延长对准系统的使用寿命。
Alignment工艺技术在现代制造业中起着不可或缺的作用,它可以提高工作效率和产品质量,并降低生产成本和时间。
active alignment原理

active alignment原理Active Alignment原理什么是Active AlignmentActive Alignment是一种用于组装光学元件的技术。
在光学元件的组装过程中,需要确保不同的光学元件之间的光轴之间存在准确的对准,以达到最佳的光学性能。
Active Alignment技术通过使用反馈机制对光学元件进行微小调整,从而实现高精度的光轴对准。
Active Alignment的原理1. 光学元件的几何参数测量在开始组装之前,首先需要测量每个光学元件的几何参数,例如光学中心、光学轴和光学面。
这些几何参数是进行对准的基础。
常用的测量方法包括探针测量和机器视觉测量。
2. 光学元件的初始位置粗调在进行精细的光轴对准之前,需要对光学元件进行初步的位置调整。
这可以通过机器人手臂或者其他自动化装置来实现。
粗调时,需要尽量使光学元件的几何中心和光轴与理想位置接近。
3. 光学元件的反馈对准利用反馈机制对光学元件进行微小调整是Active Alignment的核心步骤。
这可以通过调整光学元件的位置或者姿态来实现。
常用的反馈机制包括光强度反馈、干涉信号反馈和像差反馈。
4. 光学元件的固定当光学元件的光轴调整到预定位置后,需要对其进行固定,以保证调整不会受到外界干扰。
常用的固定方法包括胶粘、机械夹持和热压等。
Active Alignment的应用领域Active Alignment技术在许多光学元件组装的领域中得到了广泛应用,特别是对要求高精度对准的光学系统。
以下为几个常见的应用领域:•光通信:在光通信系统中,Active Alignment可以用于组装激光二极管、光纤连接器和光学波导等元件。
•显示技术:在液晶显示器、有机发光二极管显示器和激光显示器等显示技术中,Active Alignment可用于组装透镜、滤光片和光纤光栅等光学元件。
•光学传感器:在光学传感器中,Active Alignment 可以用于组装透镜、光栅和光学滤波器等元件。
光刻操作步骤

光刻操作步骤光刻操作步骤1.提前准备a)检查氮气是否充足:如果氮气量较少,请及时通知徐化勇老师购买氮气。
尤其是使用氮气量小的普通钢瓶时。
b)检查超净间的环境是否适合实验:检查超净间湿度和正负压情况。
如果超净间湿度不在所用光刻胶的容许的湿度范围内,则停止实验,并通知徐化勇老师;如果超净间负压,通知本周值日人员换纱网。
c)如果是使用大的Hot plate,请提前大约2 h设到所需温度。
d)提前检查DI Water是否够实验使用,如果不够,提前用纯水机制备。
2.开启通风橱外围设备:打开维修走廊里的spin coater的CDA 阀门、氮气枪的阀门,并观察(禁止私自调动)气压是否处于正常数值范围(外围设备的正常数值由气压表上的标记给出)。
3.填写光刻机的使用记录表格上的使用人、开机时间等信息。
4.开启光刻机的外围设备a)打开光刻机后边墙上的CDA和氮气的阀门,并观察(禁止私自调动)气压是否处于正常数值范围(外围设备的正常数值由气压表上的标记给出)。
b)打开光刻机插排上的开关,真空泵会自己启动。
5.开启光刻机a)旋转光刻机前面左侧的红色旋钮,等待光刻机屏幕提示按on/off button时,摁一下on/off button(注意不要长摁)。
b)显示屏点击进入main menu,在main menu界面上,长时间按住mask vacuum is on直到变为mask vacuum is off。
c)片刻后请确保机身上面右侧的CDA、N2、VAC三个参数值为绿色,否则联系该设备负责人。
d)按一下光学平台下方的光源控制器的power on按钮,则光源控制器面板上的“350mW Hg”和“channel 1”两个绿色指示灯亮。
(注:channel 1是365 nm光源,channel2 是405 nm光源. 如需要切换光源,,点击change display可在两个channel之间切换。
)e)按光源控制器上的CP按钮(constant power模式—混合光),片刻后光源控制器上显示“=>> Start”.f)按光源控制器上的start 按钮,光源控制器会依次显示“Ignition”、“lamp cold”,同时“lamp life/power”红灯闪烁,数分钟后闪烁停止,显示数值“0.0 270”,Hg灯开启完毕。
应用不等栅距光栅的光刻对准系统
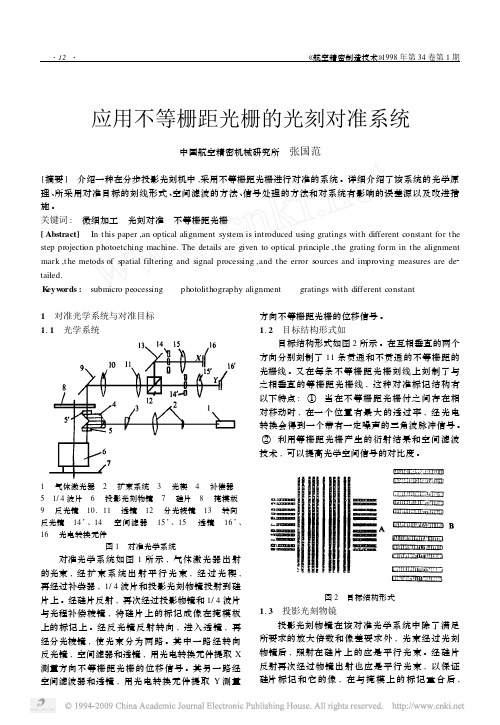
应用不等栅距光栅的光刻对准系统中国航空精密机械研究所 张国范[摘要] 介绍一种在分步投影光刻机中,采用不等栅距光栅进行对准的系统。
详细介绍了该系统的光学原理、所采用对准目标的刻线形式、空间滤波的方法、信号处理的方法和对系统有影响的误差源以及改进措施。
关键词: 微细加工 光刻对准 不等栅距光栅[Abstract] In this paper ,an optical alignment system is introduced using gratings with different constant for the step projection photoetching machine.The details are given to optical principle ,the grating form in the alignment mark ,the metods of spatial filtering and signal processing ,and the error sources and improving measures are de 2tailed.K eyw ords : submicro peocessing photolithography alignment gratings with different constant1 对准光学系统与对准目标1.1 光学系统1 气体激光器 2 扩束系统 3 光楔 4 补偿器5 1/4波片 6 投影光刻物镜 7 硅片 8 掩模板9 反光镜 10.11 透镜 12 分光棱镜 13 转向反光镜 14’、14 空间滤器 15’、15 透镜 16’、16 光电转换元件图1 对准光学系统对准光学系统如图1所示,气体激光器出射的光束,经扩束系统出射平行光束,经过光楔,再经过补尝器,1/4波片和投影光刻物镜投射到硅片上。
经硅片反射,再次经过投影物镜和1/4波片与光程补偿棱镜,将硅片上的标记成像在掩模板上的标记上。
【litho-man】光刻工艺中常见的对准技术
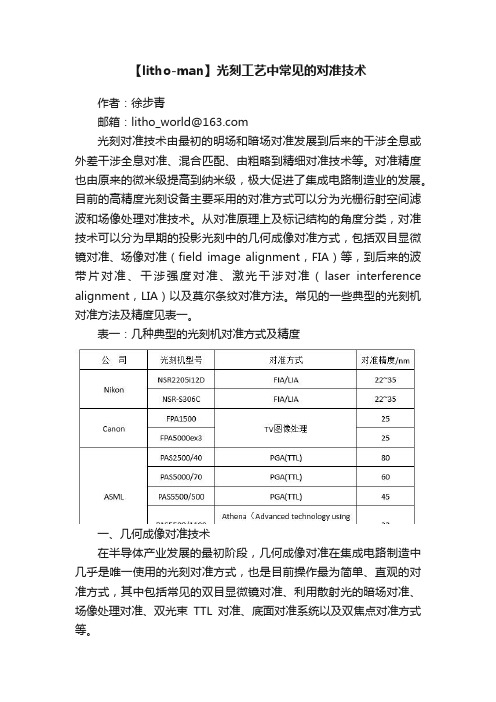
【litho-man】光刻工艺中常见的对准技术作者:徐步青邮箱:*******************光刻对准技术由最初的明场和暗场对准发展到后来的干涉全息或外差干涉全息对准、混合匹配、由粗略到精细对准技术等。
对准精度也由原来的微米级提高到纳米级,极大促进了集成电路制造业的发展。
目前的高精度光刻设备主要采用的对准方式可以分为光栅衍射空间滤波和场像处理对准技术。
从对准原理上及标记结构的角度分类,对准技术可以分为早期的投影光刻中的几何成像对准方式,包括双目显微镜对准、场像对准(field image alignment,FIA)等,到后来的波带片对准、干涉强度对准、激光干涉对准(laser interference alignment,LIA)以及莫尔条纹对准方法。
常见的一些典型的光刻机对准方法及精度见表一。
表一:几种典型的光刻机对准方式及精度一、几何成像对准技术在半导体产业发展的最初阶段,几何成像对准在集成电路制造中几乎是唯一使用的光刻对准方式,也是目前操作最为简单、直观的对准方式,其中包括常见的双目显微镜对准、利用散射光的暗场对准、场像处理对准、双光束TTL对准、底面对准系统以及双焦点对准方式等。
1、双光束TTL对准技术双光束TTL对准技术,主要通过在掩模一侧通过精缩物镜进行测量,该技术能允许连续的倍率控制,具有稳定性好、精度高、速度快等优点。
但是由于其使用的光学材料较为单一,投影物镜的镜头在对准波长较长时成像能力有限,且焦面漂移很大,因为这个原因在深紫外光刻中几乎不釆用此种对准方案。
2、场像对准技术这种方法也叫视频图像处理对准技术(field image alignment,FIA),是指在光刻套刻的过程中,掩模图样与硅片基板之间基本上只存在相对旋转和平移,充分利用这一有利条件,结合机器视觉映射技术,利用相机采集掩模图样与硅片基板的对位标记信号。
此种方法看上去虽然与双目显微镜对准有些类似,但是实质其实有所不同。
半导体overlay原理

半导体制造中的"overlay"是指在芯片制造过程中,对于每一层图案的对准精度。
它是一个非常关键的参数,因为芯片上的每一层图案都需要准确地对准前一层的图案,以确保整个芯片的功能和性能。
Overlay的原理和技术主要包括以下几个方面:
1. 曝光对准:在每一层的光刻过程中,需要将掩膜(Mask)上的图案对准前一层已经形成的图案。
曝光对准是通过对准标记(Alignment Marks)来实现的,光刻机会自动识别并将掩膜与前一层的图案对准。
2. 补偿对准:由于光刻过程中的误差和变化,有时需要进行补偿对准。
补偿对准是在曝光前根据前一层的图案和光刻机的特性进行调整,以达到更高的对准精度。
3. 特殊对准技术:对于一些特殊工艺,可能需要更高的对准精度。
在这些情况下,可能会使用额外的对准标记或采用先进的对准技术,如双向对准(Double Patterning)或多重对准(Multi-Patterning)等。
4. 对准测量和控制:为了保证对准精度,制造厂会进行对准测量和控制。
在芯片制造过程中,会定期测量对准误差,并根据测量结果调整光刻机的参数,以确保整个制造过程的对准精度满足要求。
半导体overlay是半导体制造中的重要技术之一,它直接影响到芯片的制造质量和性能。
随着芯片制造技术的进步,对准精度要求越来越高,因此,对于半导体制造厂来说,对准技术的研究和改进是一个不断进行的挑战。
光刻机对准原理
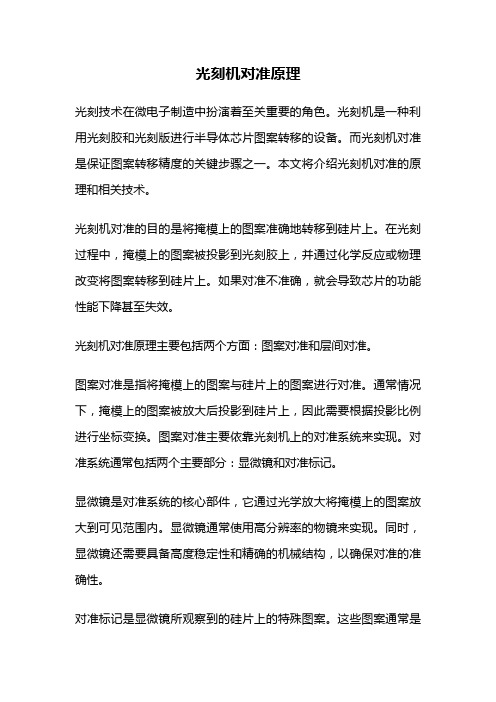
光刻机对准原理光刻技术在微电子制造中扮演着至关重要的角色。
光刻机是一种利用光刻胶和光刻版进行半导体芯片图案转移的设备。
而光刻机对准是保证图案转移精度的关键步骤之一。
本文将介绍光刻机对准的原理和相关技术。
光刻机对准的目的是将掩模上的图案准确地转移到硅片上。
在光刻过程中,掩模上的图案被投影到光刻胶上,并通过化学反应或物理改变将图案转移到硅片上。
如果对准不准确,就会导致芯片的功能性能下降甚至失效。
光刻机对准原理主要包括两个方面:图案对准和层间对准。
图案对准是指将掩模上的图案与硅片上的图案进行对准。
通常情况下,掩模上的图案被放大后投影到硅片上,因此需要根据投影比例进行坐标变换。
图案对准主要依靠光刻机上的对准系统来实现。
对准系统通常包括两个主要部分:显微镜和对准标记。
显微镜是对准系统的核心部件,它通过光学放大将掩模上的图案放大到可见范围内。
显微镜通常使用高分辨率的物镜来实现。
同时,显微镜还需要具备高度稳定性和精确的机械结构,以确保对准的准确性。
对准标记是显微镜所观察到的硅片上的特殊图案。
这些图案通常是由金属或硅等材料制成的,具有高反射率和较大的对比度。
对准标记的位置和形状是事先设计好的,可以根据标记的位置和形状来确定图案对准的偏差。
对准系统通过对准标记进行识别和分析,来计算出图案对准的偏差,并通过调整光刻机的参数来进行修正。
层间对准是指不同层次之间的图案对准。
在多层芯片制造过程中,不同层次的图案需要进行对准,以确保各层次之间的图案能够正确叠加。
层间对准通常通过参考点和对准标记来实现。
参考点是位于不同层次上的特殊图案,用于确定不同层次之间的相对位置。
参考点通常由金属或硅等材料制成,与对准标记类似。
对准系统通过识别和分析参考点的位置和形状,来计算出不同层次之间的图案对准偏差,并进行修正。
除了图案对准和层间对准,光刻机对准还需要考虑其他因素,如光源稳定性、机械振动和环境温度等。
这些因素都会对对准的精度和稳定性产生影响,需要在光刻机设计和操作过程中予以考虑和控制。
- 1、下载文档前请自行甄别文档内容的完整性,平台不提供额外的编辑、内容补充、找答案等附加服务。
- 2、"仅部分预览"的文档,不可在线预览部分如存在完整性等问题,可反馈申请退款(可完整预览的文档不适用该条件!)。
- 3、如文档侵犯您的权益,请联系客服反馈,我们会尽快为您处理(人工客服工作时间:9:00-18:30)。
University of California, Santa Barbara ME/ECE 141 B Alignment
In order to make useful devices the patterns for different lithography steps that belong to a single structure must be aligned to one another. The first pattern transferred to a wafer usually includes a set of alignment marks, which are high precision features that are used as the reference when positioning subsequent patterns, to the first pattern (as shown in figure 1). Often alignment marks are included in other patterns, as the original alignment marks may be obliterated as processing progresses. It is important for each alignment mark on the wafer to be labeled so it may be identified, and for each pattern to specify the alignment mark (and the location thereof) to which it should be aligned. By providing the location of the alignment mark it is easy for the operator to locate the correct feature in a short time. Each pattern layer should have an alignment feature so that it may be registered to the rest of the layers.
Figure 1: Use of alignment marks to register subsequent layers
Depending on the lithography equipment used, the feature on the mask used for registration of the mask may be transferred to the wafer (as shown in figure 2). In this case, it may be important to locate the alignment marks such that they don't effect subsequent wafer processing or device
performance. For example, the alignment mark shown in figure 3 will cease to exist after a through the wafer DRIE etch. Pattern transfer of the mask alignment features to the wafer may obliterate the alignment features on the wafer. In this case the alignment marks should be designed to minimize this effect, or alternately there should be multiple copies of the alignment marks on the wafer, so there will be alignment marks remaining for other masks to be registered to.
Figure 2: Transfer of mask registration feature to substrate during lithography (contact aligner)
Alignment marks may not necessarily be arbitrarily located on the wafer, as the equipment used to perform alignment may have limited travel and therefore only be able to align to features located within a certain region on the wafer (as shown in figure 4). The region location geometry and size may also vary with the type of alignment, so the lithographic equipment and type of alignment to be used should be considered before locating alignment marks. Typically two alignment marks are used to align the mask and wafer, one alignment mark is sufficient to align the mask and wafer in x and y, but it requires two marks (preferably spaced far apart) to correct for fine offset in rotation.
Figure 3: Poor alignment mark design for a through the wafer etch (cross hair is released and lost)
Figure 4: Restriction of location of alignment marks based on equipment used.。