原料药生产管理
原料药管理

原料药管理
原料药管理是指对用于生产药品的活性药物成分(API)进行的一系列管理活动。
以下是原料药管理的一些关键方面:
1. 质量控制:原料药的质量是确保药品质量的关键。
因此,原料药管理涉及严格的质量控制程序,包括对原料药的采购、检验、储存和使用进行监控和控制,以确保其符合质量标准。
2. 供应商选择与评估:选择可靠的原料药供应商是原料药管理的重要环节。
这包括对供应商的质量体系、生产能力、合规性和信誉进行评估,以确保所采购的原料药质量可靠。
3. 法规合规:原料药管理必须符合相关的法规要求,如药品生产质量管理规范(GMP)和药品注册法规。
这包括确保原料药的生产、储存和运输符合法规标准,并进行必要的文件记录和申报。
4. 供应链管理:有效的供应链管理对于原料药的及时供应和质量保证至关重要。
这包括与供应商建立良好的合作关系,监控供应的可靠性和稳定性,以及管理库存水平。
5. 变更管理:当原料药的生产工艺、质量标准或供应商等发生变更时,需要进行严格的变更管理。
这包括评估变更对药品质量的潜
在影响,并采取适当的措施来确保变更的可控性和合规性。
6. 风险管理:原料药管理涉及识别和管理与原料药相关的风险。
这包括对潜在的质量问题、供应中断、法规合规性等进行风险评估,并制定相应的风险缓解策略。
7. 质量体系:建立和维护有效的质量体系是原料药管理的基础。
这包括制定质量手册、标准操作程序(SOP),并进行内部审计和培训,以确保原料药管理的一致性和有效性。
原料药管理制度
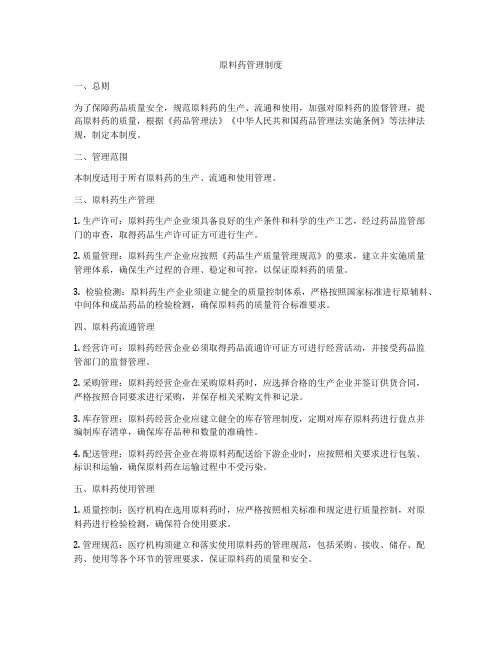
原料药管理制度一、总则为了保障药品质量安全,规范原料药的生产、流通和使用,加强对原料药的监督管理,提高原料药的质量,根据《药品管理法》《中华人民共和国药品管理法实施条例》等法律法规,制定本制度。
二、管理范围本制度适用于所有原料药的生产、流通和使用管理。
三、原料药生产管理1. 生产许可:原料药生产企业须具备良好的生产条件和科学的生产工艺,经过药品监管部门的审查,取得药品生产许可证方可进行生产。
2. 质量管理:原料药生产企业应按照《药品生产质量管理规范》的要求,建立并实施质量管理体系,确保生产过程的合理、稳定和可控,以保证原料药的质量。
3. 检验检测:原料药生产企业须建立健全的质量控制体系,严格按照国家标准进行原辅料、中间体和成品药品的检验检测,确保原料药的质量符合标准要求。
四、原料药流通管理1. 经营许可:原料药经营企业必须取得药品流通许可证方可进行经营活动,并接受药品监管部门的监督管理。
2. 采购管理:原料药经营企业在采购原料药时,应选择合格的生产企业并签订供货合同,严格按照合同要求进行采购,并保存相关采购文件和记录。
3. 库存管理:原料药经营企业应建立健全的库存管理制度,定期对库存原料药进行盘点并编制库存清单,确保库存品种和数量的准确性。
4. 配送管理:原料药经营企业在将原料药配送给下游企业时,应按照相关要求进行包装、标识和运输,确保原料药在运输过程中不受污染。
五、原料药使用管理1. 质量控制:医疗机构在选用原料药时,应严格按照相关标准和规定进行质量控制,对原料药进行检验检测,确保符合使用要求。
2. 管理规范:医疗机构须建立和落实使用原料药的管理规范,包括采购、接收、储存、配药、使用等各个环节的管理要求,保证原料药的质量和安全。
3. 监测反馈:医疗机构应建立原料药使用监测制度,定期对原料药使用情况进行监测和分析,并及时反馈问题,及时采取措施,确保原料药使用的安全和有效性。
六、监督管理1. 监督检查:药品监管部门对原料药生产企业、经营企业和使用单位进行定期和不定期的检查,对不合格的原料药进行处罚和整改,确保原料药的质量和安全。
原料药生产车间现场管理质量保证的实践要点及方案研究

原料药生产车间现场管理质量保证的实践要点及方案研究原料药生产车间现场管理是保证药品质量的重要环节,实施有效的质量保证方案对于提高原料药质量、降低生产风险、保障患者安全具有重要意义。
在这篇文章中,我们将就原料药生产车间现场管理质量保证的实践要点和方案进行深入研究,为提升药品质量和生产效率提供有益的参考。
1. 强化质量管理意识在原料药生产车间,所有员工都应该具备严格的质量管理意识,深刻理解质量对药品安全、生产效率和企业声誉的重要性。
只有把质量放在首位,才能保证原料药的质量和安全性。
2. 严格执行生产管理规定原料药生产车间要根据国家相关法律法规和企业内部制定的生产管理规定,全面推行GMP管理制度,确保生产过程符合规范要求,严格执行生产计划和操作规程,提高生产质量和效率。
3. 确保生产设备清洁和维护生产设备的清洁和维护是保证原料药质量的重要环节,对设备进行定期的清洗、消毒和维护,避免设备污染对产品质量的影响,并做好设备的验收和记录工作。
4. 严格控制原料和辅料的质量原料药生产车间要对进厂原料和辅料进行严格的质量控制,严格执行验收标准,确保原料的质量符合要求,防止劣质原料影响产品质量。
5. 强化检验和监控在原料药生产车间,要加强对生产过程各个环节的检验和监控,采用先进的检测设备和技术手段,确保各项指标符合规定标准,保证产品的质量稳定可靠。
6. 做好记录和档案管理在生产过程中,要做好生产记录和档案管理,对每一批产品的生产过程进行全面记录和归档,确保数据完整、真实、可追溯,便于对产品质量进行追溯和分析。
7. 强化人员培训和技能提升员工是原料药生产的重要环节,要加强对员工的岗前培训和技能提升,提高员工的专业素养和操作技能,增强员工的责任感和使命感。
1. 建立健全的质量管理体系原料药生产车间要建立健全的质量管理体系,明确生产过程中各个环节的责任和要求,确保生产过程符合质量管理要求,提高产品质量和生产效率。
2. 推行6S管理原料药生产车间要推行6S管理,即“整顿、整理、清扫、清洁、清除隐患、培养习惯”,通过对车间环境、设备、工具等进行整顿和清洁,营造良好的生产环境,提高生产效率和产品质量。
原料药生产管理
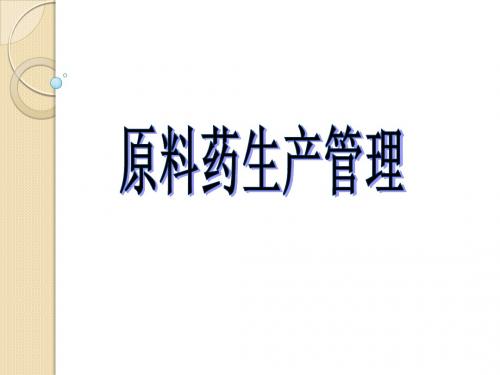
6.物料平衡检查
☆物料平衡:产品或物料实际产品或实际用量及收集到
的损耗之和与理论产量或理论用量之间的比较,并考
虑可允许的偏差范围。
☆理论产量:按照实际所用的原辅料、包装材料、中间
产品量,在生产中无任何损失或差错的情况下得出的
最大中间产品或成品的数量。
☆实际产量:生产过程中实际产出的中间产品或成品的
附注
原 料 药
混合前的产品必须按同一 生产工艺生产并符合质量 标准,且有可追踪的记录
4.批生产记录的管理
☆批生产记录是该批药品生产全过程(包括中 间产品检验)的完整记录,它由生产指令、
有关岗位生产原始记录、清场记录、偏差调
查处理情况、检验报告单等汇总而成。此记 录应具有质量的可追踪性;
批生产记录可由操作工分工段填写,班长复核, 生产车间技术人员汇总,生产车间主任审核并 签字。跨车间的产品,各车间分别填写、审核 并签字后送质量部; 批生产记录要保持整洁,不得撕毁和任意涂改。 若发现填写错误,应按规定程序更改(用横线 划掉,使原数据仍可辨认,旁边写上正确数据, 并签上姓名和日期)。 批生产记录应按批号归档,保存5年。
(4)对生产用计量容器、度量衡器以及测定、测试仪器、 仪表,进行必要的检查(或校正),超过计量周检 期限的计量仪器不得使用; (5)检查与生产品种相适应的工艺规程、岗位操作法、 BPR等生产管理文件是否齐全; (6)设备、工具、容器清洗是否符合标准; (7)按领料单或配料、核料单对所用原辅料、半成品 (中间产品)进行核对。
7.原料药或中间产品的混合
混合是指将符合同一质量标准的原料药或中 间产品合并,以的到均一产品的工艺过程。 将来自同一批次的各部分产品(如同一结晶 批号的中间产品分数次离心)在生产中进行 合并,或将几个批次的中间产品合并在一起 作进一步加工,可生产工艺的组成部分,不 视为混合。
原料药生产质量管理和原料药检测管理

原料药生产质量管理和原料药检测管理摘要:在原料药的生产过程中,为了保证原料药的生产质量,必须对质量管理给予足够的重视。
认真分析原料药的生产过程,合理设置质量检查点。
通过分析API的生产过程中,如果你想做好杂质剖面散装药品生产质量管理,质量保证体系和无菌API进行检查,以确保API杂质剖面是准确的,完整的,确保质量保证体系能发挥积极作用,提高活性药物成分的无菌性,避免API被二次污染。
因此,我们要明确质量管理在原料药生产中的重要性,积极检查各质量控制点。
关键词:原料药;生产质量管理;检查要点;原料药作为制剂的重要组成部分,其质量至关重要。
原料药的质量得不到保证,将直接影响后续药品的质量。
因此,在原料药生产过程中,应注意原料药的质量管理。
根据原料药的生产过程,合理设置质量检查点。
原材料的质量控制是保证原材料生产质量符合相应标准和要求,从而提高原料药质量的关键。
因此,有必要明确原料药生产的质量控制和检验要点,做好原料药的质量控制和检验工作,提高原材料的质量管理水平。
一、原料药生产的质量控制1.人为因素的控制。
药品质量问题是药品生产企业生产控制、质量检验检测一体化程度的综合体现。
在众多影响药品质量的因素中,占有重要地位的是对药品问题的认知,作为一个药品生产企业,企业中的每个人,包括:企业的领导人和生产工人,技术人员有资格药物产品质量都发挥着至关重要的作用,不仅制药企业内部全体员工的生产高,控股的使命负责药物开发过程和生产过程的严格要求,将会有更多的热情和身体完成药品的生产,只有这样,员工才能熟悉药品生产的各个方面,才能熟练操作。
只有这样,才能保证药品生产的质量和数量。
2.加强对生产设备、设备和检验仪器的管理。
制药公司试图提高药品的质量,必须要有良好的硬件条件,生产车间,相应的生产设备相应的规定要求满足GMP的要求,保证生产高质量医药先决条件,此外,应不定期的检查生产设备和陈旧设备的及时维修或更换,以及那些对药品生产质量检验仪器进行检验的请正规学校相关部门和团队进行整合,使检验仪器始终处于良好的运行状态,从而保证所生产药品的质量。
原料药生产质量管理和检查要点
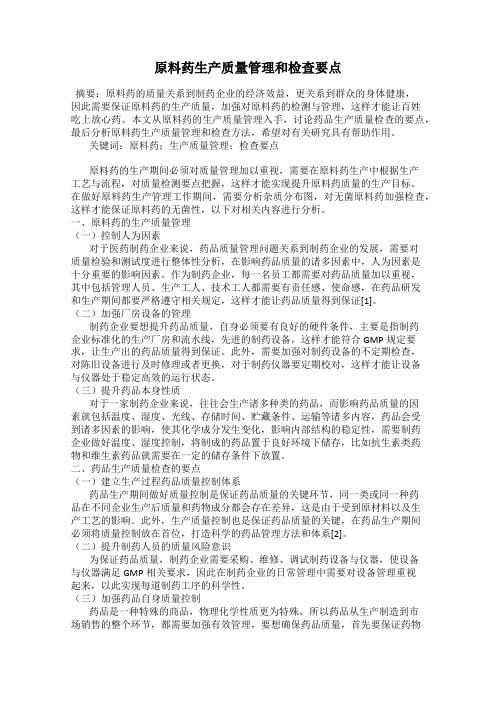
原料药生产质量管理和检查要点摘要:原料药的质量关系到制药企业的经济效益,更关系到群众的身体健康,因此需要保证原料药的生产质量,加强对原料药的检测与管理,这样才能让百姓吃上放心药。
本文从原料药的生产质量管理入手,讨论药品生产质量检查的要点,最后分析原料药生产质量管理和检查方法,希望对有关研究具有帮助作用。
关键词:原料药;生产质量管理;检查要点原料药的生产期间必须对质量管理加以重视,需要在原料药生产中根据生产工艺与流程,对质量检测要点把握,这样才能实现提升原料药质量的生产目标。
在做好原料药生产管理工作期间,需要分析杂质分布图,对无菌原料药加强检查,这样才能保证原料药的无菌性,以下对相关内容进行分析。
一、原料药的生产质量管理(一)控制人为因素对于医药制药企业来说,药品质量管理问题关系到制药企业的发展,需要对质量检验和测试度进行整体性分析,在影响药品质量的诸多因素中,人为因素是十分重要的影响因素。
作为制药企业,每一名员工都需要对药品质量加以重视,其中包括管理人员、生产工人、技术工人都需要有责任感、使命感,在药品研发和生产期间都要严格遵守相关规定,这样才能让药品质量得到保证[1]。
(二)加强厂房设备的管理制药企业要想提升药品质量,自身必须要有良好的硬件条件,主要是指制药企业标准化的生产厂房和流水线,先进的制药设备,这样才能符合GMP规定要求,让生产出的药品质量得到保证。
此外,需要加强对制药设备的不定期检查,对陈旧设备进行及时修理或者更换,对于制药仪器要定期校对,这样才能让设备与仪器处于稳定高效的运行状态。
(三)提升药品本身性质对于一家制药企业来说,往往会生产诸多种类的药品,而影响药品质量的因素就包括温度、湿度、光线、存储时间、贮藏条件、运输等诸多内容,药品会受到诸多因素的影响,使其化学成分发生变化,影响内部结构的稳定性,需要制药企业做好温度、湿度控制,将制成的药品置于良好环境下储存,比如抗生素类药物和维生素药品就需要在一定的储存条件下放置。
原料药生产车间管理制度
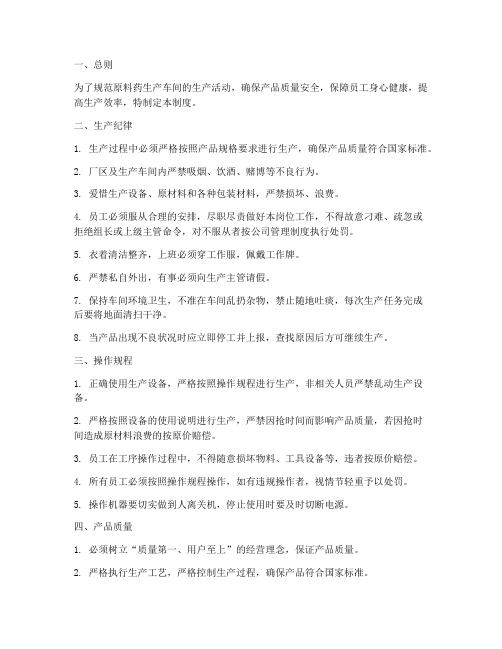
一、总则为了规范原料药生产车间的生产活动,确保产品质量安全,保障员工身心健康,提高生产效率,特制定本制度。
二、生产纪律1. 生产过程中必须严格按照产品规格要求进行生产,确保产品质量符合国家标准。
2. 厂区及生产车间内严禁吸烟、饮酒、赌博等不良行为。
3. 爱惜生产设备、原材料和各种包装材料,严禁损坏、浪费。
4. 员工必须服从合理的安排,尽职尽责做好本岗位工作,不得故意刁难、疏忽或拒绝组长或上级主管命令,对不服从者按公司管理制度执行处罚。
5. 衣着清洁整齐,上班必须穿工作服,佩戴工作牌。
6. 严禁私自外出,有事必须向生产主管请假。
7. 保持车间环境卫生,不准在车间乱扔杂物,禁止随地吐痰,每次生产任务完成后要将地面清扫干净。
8. 当产品出现不良状况时应立即停工并上报,查找原因后方可继续生产。
三、操作规程1. 正确使用生产设备,严格按照操作规程进行生产,非相关人员严禁乱动生产设备。
2. 严格按照设备的使用说明进行生产,严禁因抢时间而影响产品质量,若因抢时间造成原材料浪费的按原价赔偿。
3. 员工在工序操作过程中,不得随意损坏物料、工具设备等,违者按原价赔偿。
4. 所有员工必须按照操作规程操作,如有违规操作者,视情节轻重予以处罚。
5. 操作机器要切实做到人离关机,停止使用时要及时切断电源。
四、产品质量1. 必须树立“质量第一、用户至上”的经营理念,保证产品质量。
2. 严格执行生产工艺,严格控制生产过程,确保产品符合国家标准。
3. 加强对原材料、中间产品、成品的质量检验,确保产品质量。
4. 发现质量问题,立即采取措施,防止不合格产品流入市场。
五、安全生产1. 员工必须参加定期安全教育培训,提高安全意识。
2. 严格遵守安全操作规程,防止事故发生。
3. 定期对生产设备、安全设施进行检查、维护,确保设备正常运行。
4. 发生安全事故,立即上报,及时处理。
六、附则1. 本制度适用于原料药生产车间全体工作人员。
2. 本制度由生产车间负责解释和实施。
《药品生产质量管理规范(修订)》附录2原料药

《药品生产质量管理规范(2010年修订)》附录2:原料药附录2:原料药第一章范围第一条本附录适用于非无菌原料药生产及无菌原料药生产中非无菌生产工序的操作。
第二条原料药生产的起点及工序应当与注册批准的要求一致。
第二章厂房与设施第三条非无菌原料药精制、干燥、粉碎、包装等生产操作的暴露环境应当按照D级洁净区的要求设置。
第四条质量标准中有热原或细菌内毒素等检验项目的,厂房的设计应当特别注意防止微生物污染,根据产品的预定用途、工艺要求采取相应的控制措施。
第五条质量控制实验室通常应当与生产区分开。
当生产操作不影响检验结果的准确性,且检验操作对生产也无不利影响时,中间控制实验室可设在生产区内。
第三章设备第六条设备所需的润滑剂、加热或冷却介质等,应当避免与中间产品或原料药直接接触,以免影响中间产品或原料药的质量。
当任何偏离上述要求的情况发生时,应当进行评估和恰当处理,保证对产品的质量和用途无不良影响。
第七条生产宜使用密闭设备;密闭设备、管道可以安置于室外。
使用敞口设备或打开设备操作时,应当有避免污染的措施。
第八条使用同一设备生产多种中间体或原料药品种的,应当说明设备可以共用的合理性,并有防止交叉污染的措施。
第九条难以清洁的设备或部件应当专用。
第十条设备的清洁应当符合以下要求:(一)同一设备连续生产同一原料药或阶段性生产连续数个批次时,宜间隔适当的时间对设备进行清洁,防止污染物(如降解产物、微生物)的累积。
如有影响原料药质量的残留物,更换批次时,必须对设备进行彻底的清洁。
(二)非专用设备更换品种生产前,必须对设备(特别是从粗品精制开始的非专用设备)进行彻底的清洁,防止交叉污染。
(三)对残留物的可接受标准、清洁操作规程和清洁剂的选择,应当有明确规定并说明理由。
第十一条非无菌原料药精制工艺用水至少应当符合纯化水的质量标准。
第四章物料《药品生产质量管理规范(2010年修订)》附录2:原料药第十二条进厂物料应当有正确标识,经取样(或检验合格)后,可与现有的库存(如储槽中的溶剂或物料)混合,经放行后混合物料方可使用。
原料药生产管理

生产管理的重要性:药品生产质量管理规范以生产为基础,有生产才有质量。
药品的质量是生产出来的,而不是检验出来的。
因此说,生产管理是相当重要的。
依照GMP进行生产管理。
批生产记录批生产记录是一批药品生产各工序全过程(包括中间控制)的完整记录,应具有质量的可追踪性。
一、批批的概念:在规定限度内具有同一性质和质量,并在同一连续生产周期中生产出来的一定数量的药品为一批。
1. 大、小容量注射剂一般以同一配液罐一次所配制的药液所生产的均质产品为一批。
2.粉针剂一般以同一批原料药在同一连续生产周期内生产的均质产品为一批。
3.冻干粉针剂以同一批药液使用同一台冻干设备在同一生产周期内生产的均质产品为一批。
4.固体、半固体制剂在成型或分装前使用同一台混合设备一次混合量所生产的均质产品为一批。
固体制剂如采用多次混合后的产品作为一个批号,必须经过验证,证明产品质量的均一性后,在规定限度内所生产的产品为一批。
一般以最终所采用的混合设备如多维运动混合机混合一次的数量为一个批次。
5.液体制剂(包括膏滋、浸膏及流浸膏等)以灌封(装)前经最后混合的药液所生产的均质产品为一批。
6.连续生产的原料药,在一定时间间隔内生产的在规定限度内的均质产品为一批。
间歇生产的原料药,可由地定数理的产品经最后混合所得的在规定限度内的均质产品为一批。
混合前的产品必须按同一工艺生产并符合质量标准,且有可追踪的记录。
7.生物制品生产应按照«中国生物制品规程»中的“生物制品的分批规程”分批和编制批号。
应注意两台或两台以上的压片机(胶囊充填机)所压制出来的片子,必须分别做片重差异(装量差异)检查,确认在同一合格的范围之内并且符合其质量要求后才可作为一批。
二、批号批号的定义:用于识别“批”的一组数字或字母加数字,用以追溯和审查该批药品的生产历史。
生产中的每一个批次都必须要编制生产批号。
批号的编制方法1. 正常批号:年—月流水号,如011201批,即2001年12月的第1批。
原料药生产质量管理的特殊要求

原料药生产质量管理的特殊要求原料药生产质量管理是保障药品安全和质量的关键环节,它对药品生产企业起着至关重要的作用。
在国内外相关法律法规的指导下,原料药生产质量管理也有其特殊的要求。
本文将从国际质量管理体系、原料药的物理性质与化学性质、质量监控与控制等方面进行探讨。
首先,国际质量管理体系对原料药生产质量管理提出了一系列的特殊要求。
在国际上,药品的质量管理是遵循国际标准组织(ISO)的指南和要求的。
在ISO9001质量管理体系要求下,原料药生产企业必须建立完善的质量管理体系,通过严格执行国际标准化组织的各项规定,确保生产质量符合国际标准。
其次,原料药的物理性质与化学性质对其生产质量管理提出了特殊要求。
原料药作为药品的基本成分,其物理性质和化学性质直接影响到药品的质量和疗效。
因此,原料药生产企业必须通过严格的原料药采购、检验、储存和使用等措施,确保所采用的原料药符合规定的物理性质和化学性质要求。
另外,质量监控与控制也是原料药生产质量管理的重要环节。
质量监控的主要内容包括原料药的抽样检测、生产过程的监控、质量数据的记录和分析等。
这些措施可以帮助企业及时发现和解决生产过程中的问题,确保原料药的生产质量稳定可靠。
而质量控制则是通过建立科学合理的生产工艺和质量控制标准,对原料药的生产过程进行严格控制,确保其合格率和稳定性。
另外,原料药生产质量管理还需要注意一些特殊要求,如原料药的来源和品质可追溯性、药品安全风险评估、药品的溯源管理等。
原料药作为药品生产的关键环节,其来源和品质的可追溯性对于药品质量和安全至关重要。
因此,原料药生产企业应加强对原料药的采购管理,确保原料药的来源可靠,并能够准确追溯到具体的发货批次和供应商。
此外,药品安全风险评估也是原料药生产质量管理的重要内容。
随着药品市场的不断发展和竞争的加剧,药品的质量风险也在不断增加,为了保障患者的用药安全,原料药生产企业必须对药品质量风险进行全面评估,通过合理的风险控制措施,提高药品质量的可控性。
原料药生产管理34页PPT

混合前的产品必须按同一 生产工艺生产并符合质量 标准,且有可追踪的记录
4.批生产记录的管理
☆批生产记录是该批药品生产全过程(包括中 间产品检验)的完整记录,它由生产指令、 有关岗位生产原始记录、清场记录、偏差调 查处理情况、检验报告单等汇总而成。此记 录应具有质量的可追踪性;
批生产记录可由操作工分工段填写,班长复核, 生产车间技术人员汇总,生产车间主任审核并 签字。跨车间的产品,各车间分别填写、审核 并签字后送质量部;
批生产记录要保持整洁,不得撕毁和任意涂改。 若发现填写错误,应按规定程序更改(用横线 划掉,使原数据仍可辨认,旁边写上正确数据, 并签上姓名和日期)。
批生产记录应按批号归档,保存5年。
☆批包装记录是该批产品包装全过程的完整记 录。批包装记录可单独设置,也可作为批生 产记录的组成部分。其内容和管理要求与批 生产记录的管理相同。
5.不合格品的管理
☆凡不合格原辅料不准投入生产,不合格半成品不得流入 下工序,不合格成品不准出厂。
☆当发现不合格原辅材料、半成品(中间产品)和成品时 应按下列要求管理。
(1)立即将不合格品隔离于规定的存放区,挂上明显的不合格牌; (2)必须在每个不合格品的包装单元或容器上表明品名、规格、批
号、生产日期等; (3)填写不合格处理报告单,内容包括:品名、规格、批号、数量,
(6)设备、工具、容器清洗是否符合标准;
(7)按领料单或配料、核料单对所用原辅料、半成品 (中间产品)进行核对。
2.工艺管理
生产全过程必须严格做到“三按”即生产工 艺规程、岗位SOP、质量标准,不得任意更 改。
无菌药品的药液从配制到灭菌(或除菌过滤) 的时间间隔要有明确的规定,非无菌药品的 液体制剂的配制、过滤、灌封、灭菌等过程 也应在规定时间内完成。
原料药生产管理

生产管理的重要性:药品生产质量管理规范以生产为基础,有生产才有质量。
药品的质量是生产出来的,而不是检验出来的。
因此说,生产管理是相当重要的。
依照GMP进行生产管理。
批生产记录批生产记录是一批药品生产各工序全过程(包括中间控制)的完整记录,应具有质量的可追踪性。
一、批批的概念:在规定限度内具有同一性质和质量,并在同一连续生产周期中生产出来的一定数量的药品为一批。
1. 大、小容量注射剂一般以同一配液罐一次所配制的药液所生产的均质产品为一批。
2.粉针剂一般以同一批原料药在同一连续生产周期内生产的均质产品为一批。
3.冻干粉针剂以同一批药液使用同一台冻干设备在同一生产周期内生产的均质产品为一批。
4.固体、半固体制剂在成型或分装前使用同一台混合设备一次混合量所生产的均质产品为一批。
固体制剂如采用多次混合后的产品作为一个批号,必须经过验证,证明产品质量的均一性后,在规定限度内所生产的产品为一批。
一般以最终所采用的混合设备如多维运动混合机混合一次的数量为一个批次。
5.液体制剂(包括膏滋、浸膏及流浸膏等)以灌封(装)前经最后混合的药液所生产的均质产品为一批。
6.连续生产的原料药,在一定时间间隔内生产的在规定限度内的均质产品为一批。
间歇生产的原料药,可由地定数理的产品经最后混合所得的在规定限度内的均质产品为一批。
混合前的产品必须按同一工艺生产并符合质量标准,且有可追踪的记录。
7.生物制品生产应按照«中国生物制品规程»中的“生物制品的分批规程”分批和编制批号。
应注意两台或两台以上的压片机(胶囊充填机)所压制出来的片子,必须分别做片重差异(装量差异)检查,确认在同一合格的范围之内并且符合其质量要求后才可作为一批。
二、批号批号的定义:用于识别“批”的一组数字或字母加数字,用以追溯和审查该批药品的生产历史。
生产中的每一个批次都必须要编制生产批号。
批号的编制方法1. 正常批号:年—月流水号,如011201批,即2001年12月的第1批。
原料药生产管理规程

原料药生产管理规程第一章总则第一条根据国家相关法律法规,为规范原料药生产管理行为,促进原料药生产质量稳定提高,制定本规程。
第二条本规程适用于原料药生产企业。
第三条原料药生产企业应当遵守国家有关生产管理制度,依法保障原料药生产的质量与安全。
第二章原料药生产管理组织第四条原料药生产企业应当设立专门的生产管理部门,负责原料药生产的组织与管理。
第五条原料药生产管理部门应当配备专业技术人员,具备相关生产管理经验和知识。
第六条原料药生产企业应当建立生产管理制度,明确生产过程中各个环节的职责和要求。
第三章原料药生产质量管理第七条原料药生产企业应当建立严格的原料药生产质量管理体系,确保生产过程中各项指标符合国家标准和要求。
第八条原料药生产企业应当对原料药的质量进行全面控制,确保所生产的原料药符合国家相关药品质量标准。
第九条原料药生产企业应当建立完善的原料药质量追溯体系,确保原料药的质量可追溯和溯源。
第四章原料药生产安全管理第十条原料药生产企业应当建立完善的生产安全管理制度,保障生产过程中的安全性。
第十一条原料药生产企业应当加强生产设备的维护和保养,确保设备运行正常、安全。
第十二条原料药生产企业应当进行生产过程中的安全培训,确保相关人员了解并遵守安全操作规程。
第五章原料药生产环境管理第十三条原料药生产企业应当对生产环境进行严格管理,确保生产场所卫生、整洁。
第十四条原料药生产企业应当建立完善的生产环境监测体系,定期对生产场所进行环境监测。
第十五条原料药生产企业应当保障生产环境符合国家相关卫生标准和要求。
第六章原料药生产质量记录与报告第十六条原料药生产企业应当建立原料药生产质量记录档案,记录生产过程中的各项数据和信息。
第十七条原料药生产企业应当定期向相关监管部门提交原料药生产质量报告,确保生产的原料药质量符合国家标准和要求。
第七章原料药生产质量监督检查第十八条原料药生产企业应当接受有关监管部门的质量监督检查,确保生产过程中各项指标符合国家相关标准和要求。
原料药生产管理PPT资料34页

用于识别一个特定批次的具有唯一性的数字和(或)字母的组 合。批号可用以追溯和审查该批药品的生产历史。
批号的划分原则:
所有生产药品必须按规定划分批号 批号的划分原则如下表:
分类
批次划分
附注
原
连续生产的原料 药
在一定时间间隔内生产的、 在规定限度内的均质产品 为一批
料
药
间歇生产的原料 药
由一定数量的产品经最后 混合所得的、在规定限度 内的均质产品为一批
☆重新加工
应当对重新加工的批次进行评估、检验及必 要的稳定性考察,并有完整的文件和记录, 证明重新加工后的产品与原工艺生产的产品 质量相同。可采用同步验证的方式确定重新 加工的操作规程和预期结果。
应当按照经验证的操作规程进行重新加工, 将重新加工的每个批次的杂质分布与正常工 艺生产的批次进行比较。常规检验方法不足 以说明重新加工批次特性的,还应当采用其 他的方法。
直接接触药品的包装材料、设备容器的清洗、 干燥、灭菌到使用时间应有规定。
计量、称量和投料要有人复查,操作人、复核 人均应签字。
生产过程中的半成品(中间产品)应按“工艺 规程”规定的质量标准作为上下工序交接验收 的依据。存放半成品(中间产品)的中转库, 亦应按“待验”、“合格”、“不合格”分别 堆放,“不合格品”不得流入下工序。
主要内容
一、生产过程的管理 二、防止生产过程中的污染和交叉污染
一、生产过程的管理
生产前准备 工艺管理 批号管理 批生产记录的管理 不合格品的管理 物料平衡检查 原料药或中间产品的混合
1.生产前准备
☆各工序向仓库、生产部门中间库或上工序领
取的原辅料、半成品(中间产品)、包装材 料时,应有专人验收、记录登帐并办理交接 手续。
原料药生产质量管理和检查要点

原料药生产质量管理和检查要点【摘要】考虑到原料药的特殊性,质量是关系到原料药生产的重要指标,如果不能保证原料药的质量,将直接影响后续药品的生产质量。
所以,在原料药生产过程中,应对质量管理工作引起足够的重视,应在原料药生产中积极做好质量管理工作,并根据原料药的生产工艺和流程,合理设置质量检查点,重点做好原料药的质量控制工作,保证原料药的生产质量满足实际要求,达到提高原料药质量的目的。
为此,我们应明确原料药生产质量管理和检查要点,做好原料药生产质量管理和检查工作,提高原料药质量管理水平。
【关键词】原料药;生产质量管理;检查要点一、前言在原料药的生产过程中,为了保证原料药的生产质量,我们应对质量管理工作引起足够的重视,应认真分析原料药生产工艺流程,合理设置质量检查点。
通过对原料药的生产流程进行分析可知,要想做好原料药的生产质量管理工作,就要对杂质分布图、质量保证体系和无菌原料药进行检查,确保原料药的杂质分布图准确完整,保证质量保证体系能够发挥积极作用,提高原料药的无菌性,避免原料药被二次污染。
由此可见,我们应明确原料药生产中质量管理的重要性,应积极对各项质量控制点进行检查。
二、原料药在生产质量管理中应对杂质分布图进行检查与制剂要求一致。
每一种原料药都应有杂质分布图,用以描述常规产品中存在的已知和未知的杂质情况,这些产品应由受控的生产工艺制备得到。
杂质分布图应注明观察到的每一杂质的鉴别或其定量分析指标(如保留时间)、杂质范围,以及已确认杂质的类别(如有机杂质、无机杂质、溶剂)。
在原料药的生产过程中,杂质分布图能够反映出原料药的基本成分分布和杂质分布情况,对产品生产和整体质量产生了重要影响,为此,原料药在生产质量管理中应对杂质分布图进行检查。
具体应从以下几个方面进行:1、根据原料药的种类不同,区分杂质分布图的类别原料药生产中杂质分布图是与原料药相对应的,为了实现对原料药杂质分布图的有效检查,就要根据原料药的种类,区分杂质分布图的类别,做到正确分析。
原料药的生产质量管理和检查

原料药的生产质量管理和检查随着人们生活水平的提高,对于药品的要求也越来越高,药品的生产质量管理和检查显得尤为重要。
而在药品生产的过程中,原料药则是不可或缺的一部分,因此原料药的生产质量管理和检查也成为了药品生产中的重要环节。
一、原料药的定义和类型原料药是指用于生产药品的化学品或物质,原料药按照其来源和用途可分为天然药源和人工合成药源,天然药源包括动物、植物、菌类等,人工合成药源包括有机合成药源、无机合成药源等。
无论是天然药源还是人工合成药源,其质量都至关重要,原料药使用不合格或者低质量的原料药会影响到药品的质量和疗效,甚至会对人体产生不可逆的伤害。
二、原料药的生产质量管理原料药的生产质量管理包括原料药的采购、质量控制、流程管控和出厂检验等。
下面分别介绍各个环节。
1、原料药的采购原料药的采购需要寻求正规的供应商,要求供应商须具备合法身份、符合药品生产和质量标准的资质、具有生产能力、经验、资金等等。
采购过程需要明确合同内容,包括采购数量、质量标准、验收要求、价格、付款方式等等,保证双方达成共识。
2、质量控制质量控制是一项十分重要的工作,质量控制需要对原料药进行严格的检测和分析。
原料药的质量控制方案需要符合药品质量检测和管理规定,必须经过药品检测机构的批准和验收方可放行。
对于原料药的标准,其包括纯度、外观、成分、微生物限度、杂质等方面,必须得到相关检测机构批准。
3、流程管控原料药在生产过程中须得到严格的流程管控,包括生产记录、中间检验记录、不良品处理记录、产品发放记录等等。
在生产过程中还要保证实验室检测的严格监控,确保产品质量符合应用要求。
4、出厂检验出厂检验是保证原料药质量及药品生产质量的一个重要环节。
出厂检验涵盖了标准测试、微生物测试、重金属痕量测试、辐射污染测试等等多方面。
检验结果批准后方可进行下一步生产或出货。
三、原料药的检查原料药检查是药品生产监管中最关键的环节之一,分为进口药品的检验和国产药品的检验。
原料药生产质量管理:关键点解析

原料药生产质量管理:关键点解析在医药行业中,原料药生产质量管理是至关重要的环节。
原料药的质量直接关系到最终药品的疗效和安全性,因此严格的质量管理对于保障患者的健康至关重要。
本文将从原料药生产的关键环节出发,分析原料药生产质量管理的重要性和关键点。
原料采购原料药生产的第一步是原料采购。
选择合格可靠的原料供应商至关重要,供应商的信誉、资质、生产工艺等都会直接影响原料药的质量。
建立完善的原料采购管理制度,进行供应商评估和定期审核,保证原料的合格性和稳定性。
生产工艺控制生产工艺是影响原料药质量的关键因素之一。
生产过程中应严格执行工艺流程,确保每个步骤按照标准操作进行。
监控关键环节的生产参数,及时调整和校正,确保产品符合规定的质量标准。
质量控制质量控制是原料药生产中最核心的环节之一。
建立完善的质量管理体系,包括严格的质量控制标准、实验室检测方法和设备设施等。
对原料、在制品和成品进行全面检测和监控,确保产品质量符合相关法规和标准。
质量风险管理质量风险管理是原料药生产中不可忽视的方面。
建立健全的质量风险评估制度,对生产过程中可能影响产品质量的因素进行全面评估和控制。
及时发现和处理潜在的风险源,减少不合格品的风险。
产品追溯管理产品追溯管理是保障原料药质量的重要环节之一。
建立完善的产品追溯体系,对生产过程中的每一个环节进行记录和跟踪。
一旦发现质量问题,能够及时追溯到问题的原因和责任人,确保产品质量问题得到妥善解决。
结语原料药生产质量管理是一项综合性工作,需要各个环节的紧密配合和有效执行。
只有加强对原料药生产质量管理的重视,不断完善管理制度和技术手段,才能确保原料药的质量稳定、安全、有效,为患者提供高质量的医药产品。
愿每一位患者都能获得符合标准的原料药,早日康复。
原料药行业安全生产管理探讨

原料药行业安全生产管理探讨摘要:目前我国原料药行业在发展当中面临着越来越多的问题与挑战,其中安全生产方面的问题与挑战尤为突出。
虽然随着原料药装备技术管理水平在我国不断提升与进步,但有关原料药安全生产事故仍频繁发生,保障生产安全时刻牵动着所有从业人员的心。
为了进一步优化我国原料药生产安全管理,从三方面出发,希望有效地促进原料药安全生产水平提升,合理进行分析,将安全生产事故的发生严重程度和概率降到最低,进一步促进原料药行业长远发展。
关键词:原料药;安全生产;管理探讨针对原料药行业的安全生产问题,安全管理一直是最为关键的方面之一。
由于原料药生产自身工艺繁琐流程复杂,多数生产环节需要在高温、高压环境中进行,而化工原料本身就具有非常大的危险性。
如果相关工作人员不能熟练掌握生产流程与操作规范,在工作中粗枝大叶,就会种下安全隐患的种子。
一方面可能对企业造成财产损失,另一方面工作人员的人身安全也会受到威胁。
为了避免安全事故的发生,企业各层级人员需要对原料药生产进行全方位、全流程安全管理。
横向到底纵向到边,方方面面考虑周全,制定更加完善的安全管理规章制度,促进原料药行业安全生产问题的解决。
一、明确目标管理加强对原料药安全生产重要性的认识,通过结合企业实际制定出更加明确的安全生产管理目标,让安全生产工作的开展更有针对性。
通过分析原料药生产的状况和管理的特征,确认原料药安全生产管理目标符合安全生产的标准,将原料药生产流程与管理目标相结合,设计出更加科学合理的安全管理计划。
同时对车间主任和相关岗位工作人员进行培训,让他们充分理解认识管理计划的内容,以便在不同层级上提升原料药生产效率,保证原料药生产安全管理目标得到进一步实现。
明确目标管理是新时代背景下,原料药安全生产工作管理工作开展的首要内容。
不同的生产目标和生产环境,需要配合开展的管理工作有非常大的区别,因此明确安全管理目标与具体生产工作流程非常重要,能够形成完善的安全管理流程系统,将实际工作内容从管理层真正落实到基层人员当中。
- 1、下载文档前请自行甄别文档内容的完整性,平台不提供额外的编辑、内容补充、找答案等附加服务。
- 2、"仅部分预览"的文档,不可在线预览部分如存在完整性等问题,可反馈申请退款(可完整预览的文档不适用该条件!)。
- 3、如文档侵犯您的权益,请联系客服反馈,我们会尽快为您处理(人工客服工作时间:9:00-18:30)。
原料药生产管理一、生产过程管理1.生产前准备☆各工序向仓库、生产部门中间库或上工序领取的原辅料、半成品(中间产品)、包装材料时,应有专人验收、记录登帐并办理交接手续。
☆特殊产品的主要原辅料,宜建立小样实验制度,凭小样实验结果决定是否投入使用。
当供货单位改变时,须进行验证。
☆生产操作前,操作人员必须对管理文件、工艺卫生、设备状况等进行检查。
检查内容如下:(1)检查生产场所是否符合该区域清洁卫生要求;(2)更换批号、品种及规格前是否清场过,清场者、检查者是否签字,未取得“清场合格证”不得进行另一个品种的生产;(3)对设备状况进行严格检查,检查确认无误后方可使用。
正在检修或停用的设备应挂上“故障”或“封存”的状态标志;(4)对生产用计量容器、度量衡器以及测定、测试仪器、仪表,进行必要的检查(或校正),超过计量周检期限的计量仪器不得使用;(5)检查与生产品种相适应的工艺规程、岗位操作法、BPR等生产管理文件是否齐全;(6)设备、工具、容器清洗是否符合标准;(7)按领料单或配料、核料单对所用原辅料、半成品(中间产品)进行核对。
2.工艺管理☆生产全过程必须严格做到“三按”即生产工艺规程、岗位SOP、质量标准,不得任意更改。
☆无菌药品的药液从配制到灭菌(或除菌过滤)的时间间隔要有明确的规定,非无菌药品的液体制剂的配制、过滤、灌封、灭菌等过程也应在规定时间内完成。
☆直接接触药品的包装材料、设备容器的清洗、干燥、灭菌到使用时间应有规定。
☆计量、称量和投料要有人复查,操作人、复核人均应签字。
☆生产过程中的半成品(中间产品)应按“工艺规程”规定的质量标准作为上下工序交接验收的依据。
存放半成品(中间产品)的中转库,亦应按“待验”、“合格”、“不合格”分别堆放,“不合格品”不得流入下工序。
☆生产过程应按工艺、质量监控要点进行工艺查证,及时预防、发现和消除事故差错并做好记录。
☆生产中发生事故,应按事故管理的有关规定及时处理。
3.批号管理☆批的含义:经一个或若干加工过程生产的具有预期均一质量和特性的一定数量的原辅料、包装材料或成品。
为完成某些生产操作步骤,可能有必要将一批产品分成若干亚批,最终合并成为一个均一的批。
在连续生产情况下,批必须与生产中具有预期均一特性的确定数量的产品相对应,批量可以是固定数量或固定时间段内生产的产品。
☆批号的含义:用于识别一个特定批次的具有唯一性的数字和(或)字母的组合。
批号可用以追溯和审查该批药品的生产历史。
☆批号的划分原则:所有生产药品必须按规定划分批号批号的划分原则如下表:4.批生产记录的管理批生产记录是该批药品生产全过程(包括中间产品检验)的完整记录,它由生产指令、有关岗位生产原始记录、清场记录、偏差调查处理情况、检验报告单等汇总而成。
此记录应具有质量的可追踪性;☆批生产记录可由操作工分工段填写,班长复核,生产车间技术人员汇总,生产车间主任审核并签字。
跨车间的产品,各车间分别填写、审核并签字后送质量部;☆批生产记录要保持整洁,不得撕毁和任意涂改。
若发现填写错误,应按规定程序更改(用横线划掉,使原数据仍可辨认,旁边写上正确数据,并签上姓名和日期)。
☆批生产记录应按批号归档,保存5年。
☆批包装记录是该批产品包装全过程的完整记录。
批包装记录可单独设置,也可作为批生产记录的组成部分。
其内容和管理要求与批生产记录的管理相同。
5.不合格品的管理☆凡不合格原辅料不准投入生产,不合格半成品不得流入下工序,不合格成品不准出厂。
☆当发现不合格原辅材料、半成品(中间产品)和成品时应按下列要求管理。
(1)立即将不合格品隔离于规定的存放区,挂上明显的不合格牌;(2)必须在每个不合格品的包装单元或容器上表明品名、规格、批号、生产日期等;(3)填写不合格处理报告单,内容包括:品名、规格、批号、数量,查明不合格的日期、来源,不合格项目及原因、检验数据及负责查明原因的有关人员等,分送各有关部门;(4)由质量部会同技术部门查明原因,提出书面处理意见,负责处理的部门限期处理,质量部负责人批准后执行,并有详细的记录;(5)凡属正常生产中剔除的不合格产品,必须标明品名、规格、批号,妥善隔离存放,根据规定处理;(6)整批不合格产品,应由生产部门负责写出书面报告。
内容包括质量情况、事故或差错发生原因,应采取的补救方法,防止今后再发生的措施。
由质量部审核决定处理程序;(7)必须销毁的不合格产品应由仓库或生产部门填写销毁单,质量部批准后按规定销毁。
☆返工(1)不符合质量标准的中间产品或原料药可重复既定生产工艺中的步骤,进行重结晶等其它物理、化学处理,如蒸馏、过滤、层析、粉碎方法。
(2)多数批次都要进行的返工,应当作为一个工艺步骤列入常规的生产工艺中。
(3)除已列入常规生产工艺的返工外,应当对将未反应的物料返回至某一工艺步骤并重复进行化学反应的返工进行评估,确保中间产品或原料药的质量未受到生成副产物和过度反应物的不利影响。
(4)经中间控制检测表明某一工艺步骤尚未完成,仍可按正常工艺继续操作,不属于返工。
☆重新加工(1)应当对重新加工的批次进行评估、检验及必要的稳定性考察,并有完整的文件和记录,证明重新加工后的产品与原工艺生产的产品质量相同。
可采用同步验证的方式确定重新加工的操作规程和预期结果。
(2)应当按照经验证的操作规程进行重新加工,将重新加工的每个批次的杂质分布与正常工艺生产的批次进行比较。
常规检验方法不足以说明重新加工批次特性的,还应当采用其他的方法。
☆物料和溶剂的回收(1)回收反应物、中间产品或原料药(如从母液或滤液中回收),应当有经批准的回收操作规程,且回收的物料或产品符合与预定用途相适应的质量标准。
(2)溶剂可以回收。
回收的溶剂在同品种相同或不同的工艺步骤中重新使用的,应当对回收过程进行控制和监测,确保回收的溶剂符合适当的质量标准。
回收的溶剂用于其它品种的,应当证明不会对产品质量有不利影响。
(3)未使用过和回收的溶剂混合时,应当有足够的数据表明其对生产工艺的适用性。
(4)回收的母液和溶剂以及其它回收物料的回收与使用,应当有完整、可追溯的记录,并定期检测杂质。
6.物料平衡检查☆物料平衡:产品或物料实际产品或实际用量及收集到的损耗之和与理论产量或理论用量之间的比较,并考虑可允许的偏差范围。
☆理论产量:按照实际所用的原辅料、包装材料、中间产品量,在生产中无任何损失或差错的情况下得出的最大中间产品或成品的数量。
☆实际产量:生产过程中实际产出的中间产品或成品的数量。
包括:本工序产出合格品量、不合格品量、生产中抽检的样品量。
☆产品(或物料)的理论产量(或理论用量)与实际产量之间的比值应有可允许的正常偏差。
☆每批产品应在生产作业完成后,填写岗位物料结存卡并做物料平衡检查。
如有显著差异,必须查明原因,在得出合理解释、确认无潜在质量事故后,放可按正常品种处理。
☆偏差处理:(1)出现以下偏差之一时必须及时处理:a.物料平衡超出收率的正常范围;b.生产过程时间控制超出工艺规定范围;c.生产过程工艺条件发生偏移、变化;d.生产过程中设备突然异常,可能影响产品质量;e.产品质量(含量、外观、工序加工)发生偏移;f.跑料;g.标签实用数、剩余数、残损数之和与领用数发生差额;h.生产中其他异常情况。
(2)偏差处理程序:a.发生超限偏差时,须填写偏差处理单,写明品名、批号、规格、批量、工序、偏差内容、发生的过程及原因、地点、填表人签字、日期。
将偏差处理单交给生产部门管理人员;b.生产部门负责人及管理员会同有关人员进行调查,根据调查结果提出处理建议:继续加工,重新加工,回收或采取其他补救措施;如确认可能影响产品质量者,应报废或销毁;c.生产部门技术人员将上述处理建议(必要时应验证)写出书面报告(一式两份),生产部门负责人签字后连同偏差通知单报质量管理部门,由该部门负责人必要时会同有关负责人审核、批准;d.生产部门按批准的文件组织实施;同时将偏差报告单、调查报告、处理措施及实施结果归档备查;e.发现偏差批次与该批前后批次产品有关连时,必须立即通知质量部,作出相应的处理。
7.原料药或中间产品的混合☆混合操作可包括:(1)将数个小批次混合以增加批量。
(2)将同一原料药的多批零头产品混合成为一个批次。
二、防止生产过程中的污染和交叉污染☆严格按产品工艺要求在规定洁净度的生产场所生产,采取措施防止尘埃的产生和扩散,并定期监控生产环境的清洁及卫生情况。
☆不同产品品种、规格的生产操作不得在同一生产操作间同时进行;有数条包装线同时进行包装时,应采取隔离或其他有效防止污染或混淆的措施。
☆生产过程中应防止物料及产品所产生的气体、蒸汽、喷雾物或生物体等引起的交叉污染。
☆每一生产操作间或生产用设备、容器应有所生产产品的物料名称、批号、数量等状态标志。
☆做好清场管理工作,生产前应确认无上次生产遗留物,防止混淆。
附:清场管理的相关规定☆清场时间:生产结束、更换品种及规格或换批号前。
☆清场要求(1)地面无积灰、无结垢,门窗、室内照明灯、风管、墙面、开关箱外壳无积灰,室内不得存放与生产无关的杂品;(2)使用的器具、容器应清洁、无异物,无前次产品的遗留物;(3)设备内外无前次生产遗留的药品,无油垢;(4)非专用设备、管道、容器、工具应按规定拆洗或灭菌;(5)直接接触药品的机器、设备及管道工具、容器应每天或每批清洗或处理。
同一设备连续加工同一非无菌产品时,其清洗周期可按设备清洗的有关规定;(6)包装工序调换品种时,多余的标签及包装材料应全部按规定处理;(7)未领得“清场合格证”不得进入下一步的生产。