光刻技术的发展概要
光刻技术的现状和发展
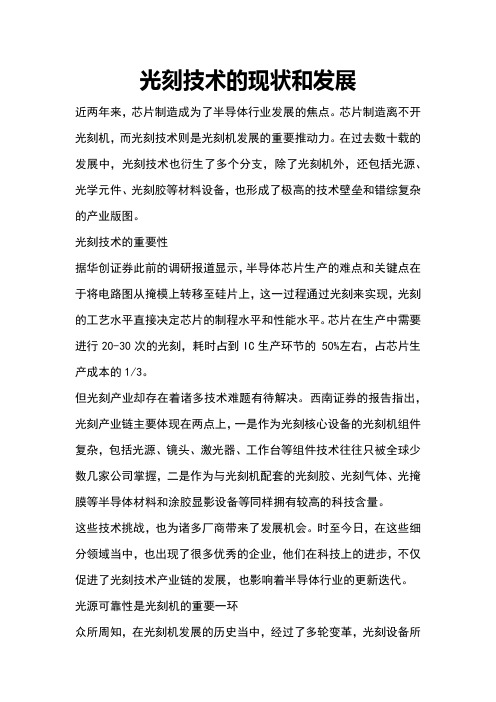
光刻技术的现状和发展近两年来,芯片制造成为了半导体行业发展的焦点。
芯片制造离不开光刻机,而光刻技术则是光刻机发展的重要推动力。
在过去数十载的发展中,光刻技术也衍生了多个分支,除了光刻机外,还包括光源、光学元件、光刻胶等材料设备,也形成了极高的技术壁垒和错综复杂的产业版图。
光刻技术的重要性据华创证券此前的调研报道显示,半导体芯片生产的难点和关键点在于将电路图从掩模上转移至硅片上,这一过程通过光刻来实现,光刻的工艺水平直接决定芯片的制程水平和性能水平。
芯片在生产中需要进行20-30次的光刻,耗时占到IC生产环节的 50%左右,占芯片生产成本的1/3。
但光刻产业却存在着诸多技术难题有待解决。
西南证券的报告指出,光刻产业链主要体现在两点上,一是作为光刻核心设备的光刻机组件复杂,包括光源、镜头、激光器、工作台等组件技术往往只被全球少数几家公司掌握,二是作为与光刻机配套的光刻胶、光刻气体、光掩膜等半导体材料和涂胶显影设备等同样拥有较高的科技含量。
这些技术挑战,也为诸多厂商带来了发展机会。
时至今日,在这些细分领域当中,也出现了很多优秀的企业,他们在科技上的进步,不仅促进了光刻技术产业链的发展,也影响着半导体行业的更新迭代。
光源可靠性是光刻机的重要一环众所周知,在光刻机发展的历史当中,经过了多轮变革,光刻设备所用的光源,也从最初的g-line,i-line发展到了KrF、ArF,如今光源又在向EUV方向发展。
Gigaphoton是在全球范围内能够为光刻机提供激光光源的两家厂商之一(另外一家是Cymer,该公司于2012年被ASML收购)。
Gigaphoton的Toshihiro Oga认为,光源是一项专业性较强的领域,并需要大规模的投资去支撑该技术的发展,而光源又是一个相对小众的领域,尤其是用于光刻机的光源有别于用于其他领域的光源——其他领域所用光源多为低频低功率,而光刻机所用光源则为高频高功率,这也让许多企业对该领域望而却步。
光刻机的历史发展与前景展望
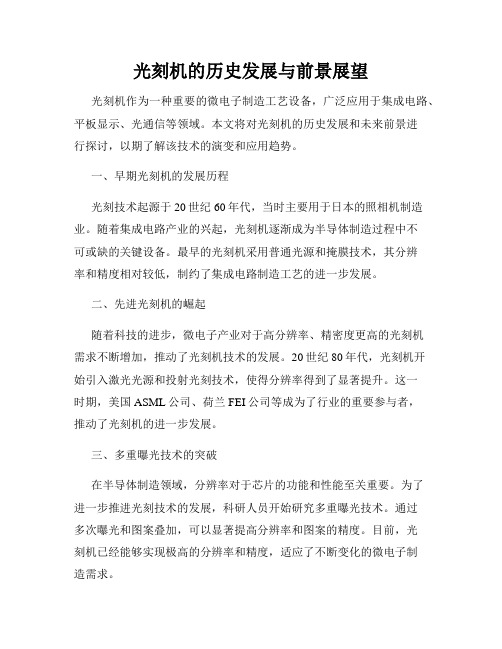
光刻机的历史发展与前景展望光刻机作为一种重要的微电子制造工艺设备,广泛应用于集成电路、平板显示、光通信等领域。
本文将对光刻机的历史发展和未来前景进行探讨,以期了解该技术的演变和应用趋势。
一、早期光刻机的发展历程光刻技术起源于20世纪60年代,当时主要用于日本的照相机制造业。
随着集成电路产业的兴起,光刻机逐渐成为半导体制造过程中不可或缺的关键设备。
最早的光刻机采用普通光源和掩膜技术,其分辨率和精度相对较低,制约了集成电路制造工艺的进一步发展。
二、先进光刻机的崛起随着科技的进步,微电子产业对于高分辨率、精密度更高的光刻机需求不断增加,推动了光刻机技术的发展。
20世纪80年代,光刻机开始引入激光光源和投射光刻技术,使得分辨率得到了显著提升。
这一时期,美国ASML公司、荷兰FEI公司等成为了行业的重要参与者,推动了光刻机的进一步发展。
三、多重曝光技术的突破在半导体制造领域,分辨率对于芯片的功能和性能至关重要。
为了进一步推进光刻技术的发展,科研人员开始研究多重曝光技术。
通过多次曝光和图案叠加,可以显著提高分辨率和图案的精度。
目前,光刻机已经能够实现极高的分辨率和精度,适应了不断变化的微电子制造需求。
四、未来光刻机发展趋势展望随着人工智能、物联网、5G等新兴技术的快速发展,对于光刻机技术的需求也在不断增加。
未来,光刻机有望在以下几个方面取得新的突破。
1. 高分辨率和高精密度随着集成电路制造工艺的不断进步,对于光刻机的分辨率和精密度要求越来越高。
科研人员将致力于开发更高分辨率的投影光刻技术,并通过材料和工艺的创新,提高芯片制造的精度。
2. 多模态光刻技术的发展多模态光刻技术可以同时处理不同尺寸、不同结构的图案,提高生产效率和灵活性。
未来光刻机有望引入多模态技术,满足不同制造需求的变化。
3. 绿色环保制造随着环保意识的不断提升,未来光刻机将更加注重节能减排和环境友好。
研究人员将寻找更加环保的曝光光源和材料,减少对环境的影响。
光刻技术及发展前景讲解

b、通过对准标志,位于切割槽 上。另外层间对准,即套刻精度, 保证图形与硅片上已经存在的图 形之间的对准。
6、曝光Exposure
曝光方法: a、接触式曝光(Contact Printing)掩膜 板直接与光刻胶层接触。 b、接近式曝光(Proximity Printing)掩 膜板与光刻胶层的略微分开,大约为 10~50μm。 c、投影式曝光(Projection Printing) 。在掩膜板与光刻胶之间使用透镜聚集 光实现曝光。 d、步进式曝光(Stepper)
其实各大厂商已经开始为EUV布局!
IMEC开发的EUV alpha demonstration tool
其实各大厂商已经开始为EUV布局!
台积电公司订购ASML公司极紫外光刻系统Twinscan NXE3100
EUV技术在Intel的实战中取得成果
光刻技术面临的困难与挑战
≥32纳米
光学掩膜版图形分辨率加强 技术的研发和后光学成像技 术掩膜版的制造
Photoresist Spin Coating
Edge Bead Removal
Ready For Soft Bake
4、前烘 Soft Bake
蒸发光刻胶中的溶剂
溶剂能使涂覆的光刻胶更薄 但吸收热量且影响光刻胶的黏附 性 过多的烘烤使光刻胶聚合,感光 灵敏度变差 烘烤不够影响黏附性和曝光
Baking Systems
但一切还远没有结束!
据Intel表示,11nm制程节点上该公司的光 刻技术将采用多种光刻工艺互补混搭的策略, 将193nm沉浸式光刻技术与EUV,无掩模光刻 (maskless)等技术混合在一起来满足11nm 制程的需求。
光刻机的发展历程
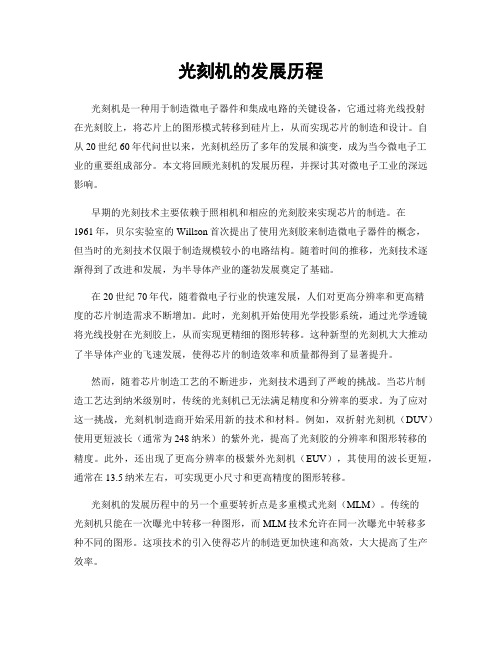
光刻机的发展历程光刻机是一种用于制造微电子器件和集成电路的关键设备,它通过将光线投射在光刻胶上,将芯片上的图形模式转移到硅片上,从而实现芯片的制造和设计。
自从20世纪60年代问世以来,光刻机经历了多年的发展和演变,成为当今微电子工业的重要组成部分。
本文将回顾光刻机的发展历程,并探讨其对微电子工业的深远影响。
早期的光刻技术主要依赖于照相机和相应的光刻胶来实现芯片的制造。
在1961年,贝尔实验室的Willson首次提出了使用光刻胶来制造微电子器件的概念,但当时的光刻技术仅限于制造规模较小的电路结构。
随着时间的推移,光刻技术逐渐得到了改进和发展,为半导体产业的蓬勃发展奠定了基础。
在20世纪70年代,随着微电子行业的快速发展,人们对更高分辨率和更高精度的芯片制造需求不断增加。
此时,光刻机开始使用光学投影系统,通过光学透镜将光线投射在光刻胶上,从而实现更精细的图形转移。
这种新型的光刻机大大推动了半导体产业的飞速发展,使得芯片的制造效率和质量都得到了显著提升。
然而,随着芯片制造工艺的不断进步,光刻技术遇到了严峻的挑战。
当芯片制造工艺达到纳米级别时,传统的光刻机已无法满足精度和分辨率的要求。
为了应对这一挑战,光刻机制造商开始采用新的技术和材料。
例如,双折射光刻机(DUV)使用更短波长(通常为248纳米)的紫外光,提高了光刻胶的分辨率和图形转移的精度。
此外,还出现了更高分辨率的极紫外光刻机(EUV),其使用的波长更短,通常在13.5纳米左右,可实现更小尺寸和更高精度的图形转移。
光刻机的发展历程中的另一个重要转折点是多重模式光刻(MLM)。
传统的光刻机只能在一次曝光中转移一种图形,而MLM技术允许在同一次曝光中转移多种不同的图形。
这项技术的引入使得芯片的制造更加快速和高效,大大提高了生产效率。
除了技术的改进,光刻机在制造工艺上的不断进步也对微电子行业产生了深远影响。
光刻机的发展使得芯片制造成本大幅降低,更多的人能够享受到电子产品的便捷。
光刻机生产助力智能手机领域的创新

光刻机生产助力智能手机领域的创新随着科技的不断进步和人们对智能手机的需求增加,智能手机制造领域迅速发展。
其中,光刻技术在智能手机生产中起到关键作用,为其带来了创新和突破。
本文将讨论光刻机生产如何助力智能手机领域的创新。
一、光刻技术概述光刻技术是一种将芯片电路图案转移到硅片上的核心制造工艺。
在智能手机生产中,光刻机是保证芯片制造精度和稳定性的重要设备。
它通过对光刻胶的敏感性实现对图案的转印,使得芯片上的电路能够准确无误地制造出来。
二、光刻技术在智能手机领域的应用1. 精细图案制造光刻技术可以制造出微小且复杂的电路图案。
在智能手机芯片制造中,各种集成电路以及传感器都需要进行精细图案制造,光刻技术通过其高精度和高分辨率的特点,使得这些芯片能够实现更快、更安全、更稳定的运行。
2. 提高制造效率随着智能手机市场竞争的加剧,制造效率的提升成为制造商们迫切需要解决的问题。
光刻技术通过大幅提高芯片制造的速度和效率,使得智能手机的生产周期大幅缩短,从而更快地满足市场需求。
3. 创新产品的打开方式光刻技术在智能手机制造中的应用,为创新产品的打开方式提供了巨大的可能性。
例如,在曲面屏、柔性显示器等新型手机屏幕技术中,光刻技术能够实现对非常规形状的图案进行制备,推动了智能手机屏幕领域的创新和突破。
三、光刻技术的潜在挑战和解决方案1. 制造成本光刻技术的设备和材料成本较高,给智能手机制造商带来一定压力。
然而,随着技术的成熟和发展,光刻机制造商正在寻找降低设备成本的解决方案,同时,材料供应商也在不断提供性价比更高的材料。
2. 制造精度智能手机中的芯片制造需要高精度的图案转印,而光刻技术在这方面的限制是制造商们需要面对的挑战之一。
为了解决这个问题,制造商们正不断投入更多的研发资源,提高光刻机的精度,保证制造质量。
3. 新材料适应性随着新材料的不断涌现,光刻技术需要不断适应新的材料特性,以满足智能手机制造的需求。
制造商们正在加强与材料供应商的合作,持续改进和适应新材料的光刻工艺流程。
光刻技术及其应用的状况和未来发展
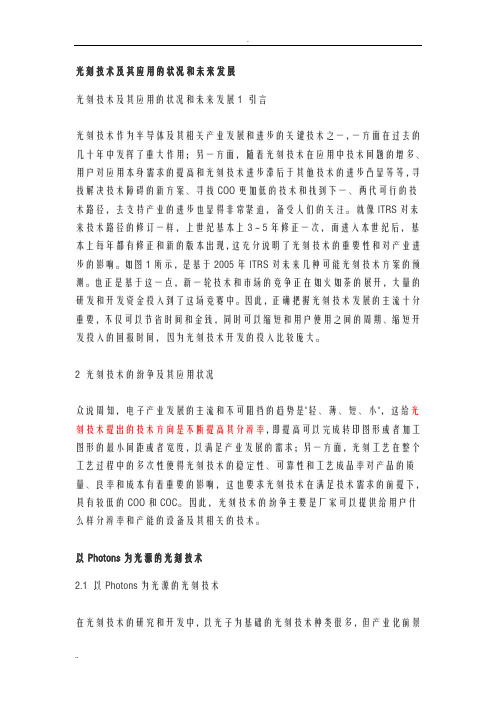
光刻技术及其应用的状况和未来发展光刻技术及其应用的状况和未来发展1 引言光刻技术作为半导体及其相关产业发展和进步的关键技术之一,一方面在过去的几十年中发挥了重大作用;另一方面,随着光刻技术在应用中技术问题的增多、用户对应用本身需求的提高和光刻技术进步滞后于其他技术的进步凸显等等,寻找解决技术障碍的新方案、寻找COO更加低的技术和找到下一、两代可行的技术路径,去支持产业的进步也显得非常紧迫,备受人们的关注。
就像ITRS对未来技术路径的修订一样,上世纪基本上3~5年修正一次,而进入本世纪后,基本上每年都有修正和新的版本出现,这充分说明了光刻技术的重要性和对产业进步的影响。
如图1所示,是基于2005年ITRS对未来几种可能光刻技术方案的预测。
也正是基于这一点,新一轮技术和市场的竞争正在如火如荼的展开,大量的研发和开发资金投入到了这场竞赛中。
因此,正确把握光刻技术发展的主流十分重要,不仅可以节省时间和金钱,同时可以缩短和用户使用之间的周期、缩短开发投入的回报时间,因为光刻技术开发的投入比较庞大。
2 光刻技术的纷争及其应用状况众说周知,电子产业发展的主流和不可阻挡的趋势是"轻、薄、短、小",这给光刻技术提出的技术方向是不断提高其分辨率,即提高可以完成转印图形或者加工图形的最小间距或者宽度,以满足产业发展的需求;另一方面,光刻工艺在整个工艺过程中的多次性使得光刻技术的稳定性、可靠性和工艺成品率对产品的质量、良率和成本有着重要的影响,这也要求光刻技术在满足技术需求的前提下,具有较低的COO和COC。
因此,光刻技术的纷争主要是厂家可以提供给用户什么样分辨率和产能的设备及其相关的技术。
以Photons为光源的光刻技术2.1 以Photons为光源的光刻技术在光刻技术的研究和开发中,以光子为基础的光刻技术种类很多,但产业化前景较好的主要是紫外(UV)光刻技术、深紫外(DUV)光刻技术、极紫外(EUV)光刻技术和X射线(X-ray)光刻技术。
光刻机发展史
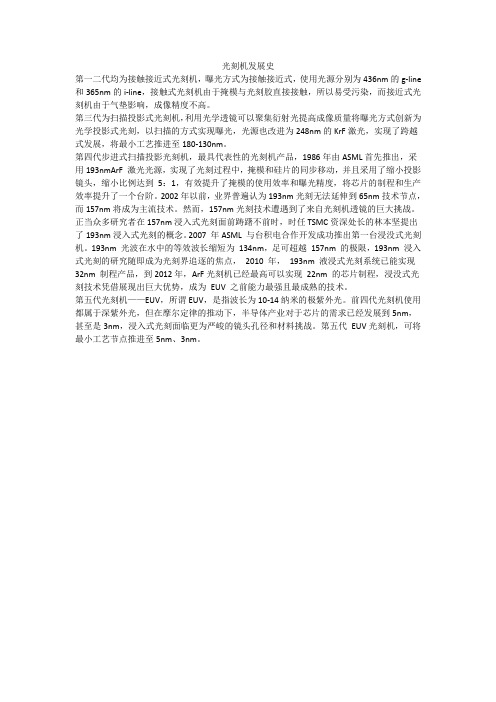
光刻机发展史第一二代均为接触接近式光刻机,曝光方式为接触接近式,使用光源分别为436nm的g-line 和365nm的i-line,接触式光刻机由于掩模与光刻胶直接接触,所以易受污染,而接近式光刻机由于气垫影响,成像精度不高。
第三代为扫描投影式光刻机,利用光学透镜可以聚集衍射光提高成像质量将曝光方式创新为光学投影式光刻,以扫描的方式实现曝光,光源也改进为248nm的KrF激光,实现了跨越式发展,将最小工艺推进至180-130nm。
第四代步进式扫描投影光刻机,最具代表性的光刻机产品,1986年由ASML首先推出,采用193nmArF 激光光源,实现了光刻过程中,掩模和硅片的同步移动,并且采用了缩小投影镜头,缩小比例达到5:1,有效提升了掩模的使用效率和曝光精度,将芯片的制程和生产效率提升了一个台阶。
2002年以前,业界普遍认为193nm光刻无法延伸到65nm技术节点,而157nm将成为主流技术。
然而,157nm光刻技术遭遇到了来自光刻机透镜的巨大挑战。
正当众多研究者在157nm浸入式光刻面前踌躇不前时,时任TSMC资深处长的林本坚提出了193nm浸入式光刻的概念。
2007 年ASML 与台积电合作开发成功推出第一台浸没式光刻机。
193nm 光波在水中的等效波长缩短为134nm,足可超越157nm 的极限,193nm 浸入式光刻的研究随即成为光刻界追逐的焦点,2010 年,193nm 液浸式光刻系统已能实现32nm 制程产品,到2012年,ArF光刻机已经最高可以实现22nm 的芯片制程,浸没式光刻技术凭借展现出巨大优势,成为EUV 之前能力最强且最成熟的技术。
第五代光刻机——EUV,所谓EUV,是指波长为10-14纳米的极紫外光。
前四代光刻机使用都属于深紫外光,但在摩尔定律的推动下,半导体产业对于芯片的需求已经发展到5nm,甚至是3nm,浸入式光刻面临更为严峻的镜头孔径和材料挑战。
第五代EUV光刻机,可将最小工艺节点推进至5nm、3nm。
光刻技术的发展趋势
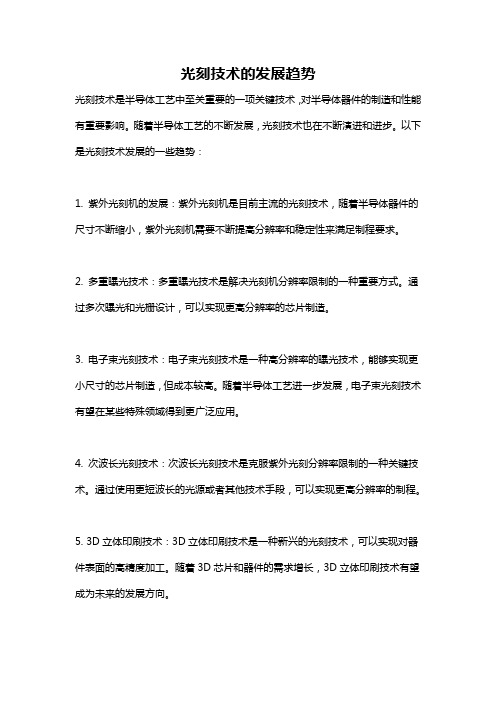
光刻技术的发展趋势
光刻技术是半导体工艺中至关重要的一项关键技术,对半导体器件的制造和性能有重要影响。
随着半导体工艺的不断发展,光刻技术也在不断演进和进步。
以下是光刻技术发展的一些趋势:
1. 紫外光刻机的发展:紫外光刻机是目前主流的光刻技术,随着半导体器件的尺寸不断缩小,紫外光刻机需要不断提高分辨率和稳定性来满足制程要求。
2. 多重曝光技术:多重曝光技术是解决光刻机分辨率限制的一种重要方式。
通过多次曝光和光栅设计,可以实现更高分辨率的芯片制造。
3. 电子束光刻技术:电子束光刻技术是一种高分辨率的曝光技术,能够实现更小尺寸的芯片制造,但成本较高。
随着半导体工艺进一步发展,电子束光刻技术有望在某些特殊领域得到更广泛应用。
4. 次波长光刻技术:次波长光刻技术是克服紫外光刻分辨率限制的一种关键技术。
通过使用更短波长的光源或者其他技术手段,可以实现更高分辨率的制程。
5. 3D立体印刷技术:3D立体印刷技术是一种新兴的光刻技术,可以实现对器件表面的高精度加工。
随着3D芯片和器件的需求增长,3D立体印刷技术有望成为未来的发展方向。
总体来说,光刻技术的发展趋势是朝着更高分辨率、更快速度和更低成本的方向发展。
随着新一代半导体工艺的引入和应用需求的变化,光刻技术会继续不断演进和创新。
光刻技术的发展史
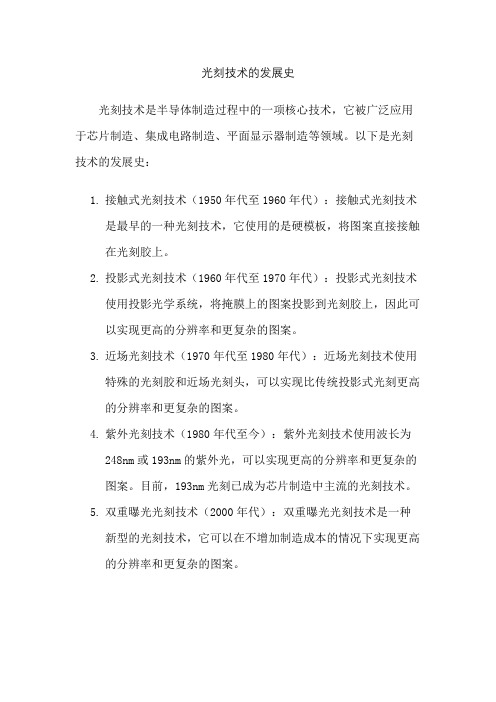
光刻技术的发展史
光刻技术是半导体制造过程中的一项核心技术,它被广泛应用于芯片制造、集成电路制造、平面显示器制造等领域。
以下是光刻技术的发展史:
1.接触式光刻技术(1950年代至1960年代):接触式光刻技术
是最早的一种光刻技术,它使用的是硬模板,将图案直接接触在光刻胶上。
2.投影式光刻技术(1960年代至1970年代):投影式光刻技术
使用投影光学系统,将掩膜上的图案投影到光刻胶上,因此可以实现更高的分辨率和更复杂的图案。
3.近场光刻技术(1970年代至1980年代):近场光刻技术使用
特殊的光刻胶和近场光刻头,可以实现比传统投影式光刻更高的分辨率和更复杂的图案。
4.紫外光刻技术(1980年代至今):紫外光刻技术使用波长为
248nm或193nm的紫外光,可以实现更高的分辨率和更复杂的图案。
目前,193nm光刻已成为芯片制造中主流的光刻技术。
5.双重曝光光刻技术(2000年代):双重曝光光刻技术是一种
新型的光刻技术,它可以在不增加制造成本的情况下实现更高的分辨率和更复杂的图案。
6.多重图案光刻技术(2010年代):多重图案光刻技术可以同
时实现多个图案的制造,从而大大提高了芯片制造的效率和成本效益。
中国古代光刻机发展历程

中国古代光刻机发展历程
中国古代光刻机的发展历程可以追溯到唐朝时期。
以下是中国古代光刻机发展历程的概述:
1. 唐代(618-907年):在唐代,出现了最早的光刻机原型。
这种机器由一个旋转的圆盘、槽和活字组成,可以将文字刻在木板上。
2. 宋代(960-1279年):宋代时,光刻技术得到了进一步发展。
出现了一种叫做“簿照法”的技术,可以用来复制文稿。
这种技术使用了光照,可以在纸上复制文字和图案。
3. 元代(1271-1368年):在元代时期,光刻机的技术进一步改进。
光刻机的构造更加复杂,可以制作更精细的复制品。
4. 明代(1368-1644年):明代时期,光刻技术得到了进一步的改进。
出现了一种新的光刻机构造,可以更准确地刻印文字和图案。
5. 清代(1644-1912年):在清代,光刻技术继续发展。
光刻机的操作变得更加简便,可以制作更大规模的刻版。
总体来说,中国古代的光刻机发展历程经历了从简单的机械设备到复杂的光刻技术的演变。
这些技术对书籍印刷和文物保护起到了重要作用,并对后来的光刻技术的发展产生了影响。
光刻机的技术原理和技术发展趋势PDF
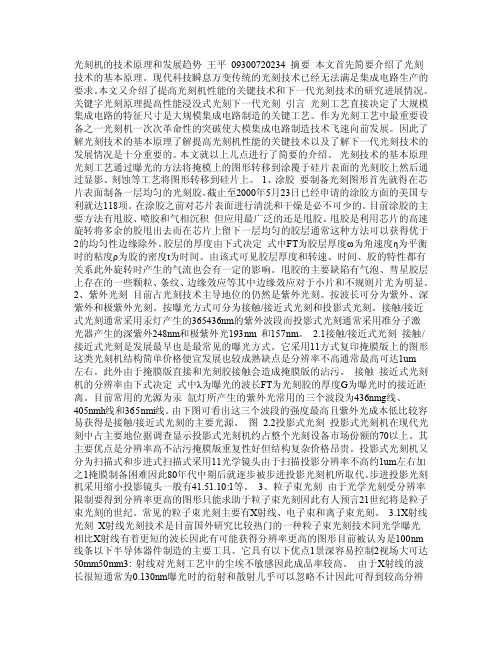
光刻机的技术原理和发展趋势王平0930******* 摘要本文首先简要介绍了光刻技术的基本原理。
现代科技瞬息万变传统的光刻技术已经无法满足集成电路生产的要求。
本文又介绍了提高光刻机性能的关键技术和下一代光刻技术的研究进展情况。
关键字光刻原理提高性能浸没式光刻下一代光刻引言光刻工艺直接决定了大规模集成电路的特征尺寸是大规模集成电路制造的关键工艺。
作为光刻工艺中最重要设备之一光刻机一次次革命性的突破使大模集成电路制造技术飞速向前发展。
因此了解光刻技术的基本原理了解提高光刻机性能的关键技术以及了解下一代光刻技术的发展情况是十分重要的。
本文就以上几点进行了简要的介绍。
光刻技术的基本原理光刻工艺通过曝光的方法将掩模上的图形转移到涂覆于硅片表面的光刻胶上然后通过显影、刻蚀等工艺将图形转移到硅片上。
1、涂胶要制备光刻图形首先就得在芯片表面制备一层均匀的光刻胶。
截止至2000年5月23日已经申请的涂胶方面的美国专利就达118项。
在涂胶之前对芯片表面进行清洗和干燥是必不可少的。
目前涂胶的主要方法有甩胶、喷胶和气相沉积但应用最广泛的还是甩胶。
甩胶是利用芯片的高速旋转将多余的胶甩出去而在芯片上留下一层均匀的胶层通常这种方法可以获得优于2的均匀性边缘除外。
胶层的厚度由下式决定式中FT为胶层厚度ω为角速度η为平衡时的粘度ρ为胶的密度t为时间。
由该式可见胶层厚度和转速、时间、胶的特性都有关系此外旋转时产生的气流也会有一定的影响。
甩胶的主要缺陷有气泡、彗星胶层上存在的一些颗粒、条纹、边缘效应等其中边缘效应对于小片和不规则片尤为明显。
2、紫外光刻目前占光刻技术主导地位的仍然是紫外光刻。
按波长可分为紫外、深紫外和极紫外光刻。
按曝光方式可分为接触/接近式光刻和投影式光刻。
接触/接近式光刻通常采用汞灯产生的365436nm的紫外波段而投影式光刻通常采用准分子激光器产生的深紫外248nm和极紫外光193nm 和157nm。
2.1接触/接近式光刻接触/接近式光刻是发展最早也是最常见的曝光方式。
光刻机的发展历史与技术创新
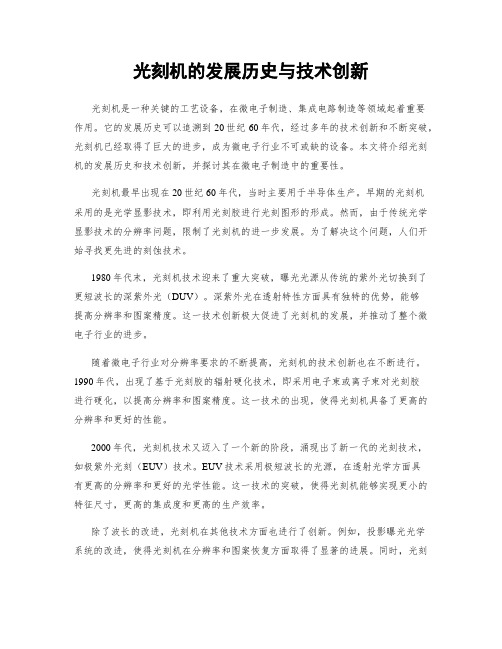
光刻机的发展历史与技术创新光刻机是一种关键的工艺设备,在微电子制造、集成电路制造等领域起着重要作用。
它的发展历史可以追溯到20世纪60年代,经过多年的技术创新和不断突破,光刻机已经取得了巨大的进步,成为微电子行业不可或缺的设备。
本文将介绍光刻机的发展历史和技术创新,并探讨其在微电子制造中的重要性。
光刻机最早出现在20世纪60年代,当时主要用于半导体生产。
早期的光刻机采用的是光学显影技术,即利用光刻胶进行光刻图形的形成。
然而,由于传统光学显影技术的分辨率问题,限制了光刻机的进一步发展。
为了解决这个问题,人们开始寻找更先进的刻蚀技术。
1980年代末,光刻机技术迎来了重大突破,曝光光源从传统的紫外光切换到了更短波长的深紫外光(DUV)。
深紫外光在透射特性方面具有独特的优势,能够提高分辨率和图案精度。
这一技术创新极大促进了光刻机的发展,并推动了整个微电子行业的进步。
随着微电子行业对分辨率要求的不断提高,光刻机的技术创新也在不断进行。
1990年代,出现了基于光刻胶的辐射硬化技术,即采用电子束或离子束对光刻胶进行硬化,以提高分辨率和图案精度。
这一技术的出现,使得光刻机具备了更高的分辨率和更好的性能。
2000年代,光刻机技术又迈入了一个新的阶段,涌现出了新一代的光刻技术,如极紫外光刻(EUV)技术。
EUV技术采用极短波长的光源,在透射光学方面具有更高的分辨率和更好的光学性能。
这一技术的突破,使得光刻机能够实现更小的特征尺寸,更高的集成度和更高的生产效率。
除了波长的改进,光刻机在其他技术方面也进行了创新。
例如,投影曝光光学系统的改进,使得光刻机在分辨率和图案恢复方面取得了显著的进展。
同时,光刻机的自动化程度也不断提高,通过引入先进的控制系统和软件,实现了更高的精度和更快的操作速度。
光刻机在微电子制造中的重要性不言而喻。
随着半导体器件尺寸的不断缩小和集成度的提高,光刻机在芯片制造的分辨率限制中发挥着至关重要的作用。
光刻机的发展历程与技术突破
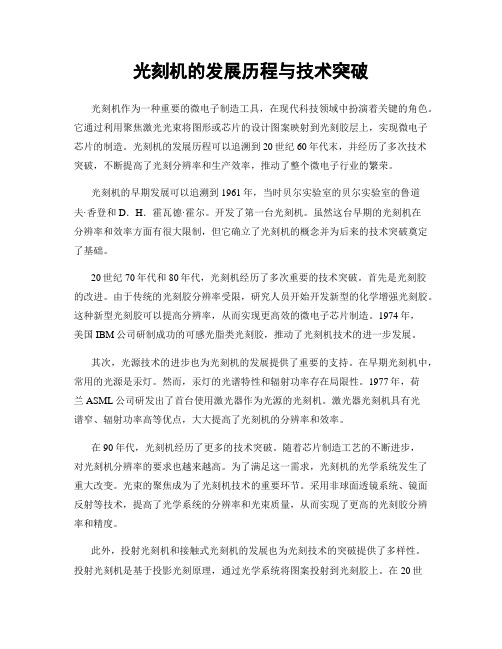
光刻机的发展历程与技术突破光刻机作为一种重要的微电子制造工具,在现代科技领域中扮演着关键的角色。
它通过利用聚焦激光光束将图形或芯片的设计图案映射到光刻胶层上,实现微电子芯片的制造。
光刻机的发展历程可以追溯到20世纪60年代末,并经历了多次技术突破,不断提高了光刻分辨率和生产效率,推动了整个微电子行业的繁荣。
光刻机的早期发展可以追溯到1961年,当时贝尔实验室的贝尔实验室的鲁道夫·香登和D.H.霍瓦德·霍尔。
开发了第一台光刻机。
虽然这台早期的光刻机在分辨率和效率方面有很大限制,但它确立了光刻机的概念并为后来的技术突破奠定了基础。
20世纪70年代和80年代,光刻机经历了多次重要的技术突破。
首先是光刻胶的改进。
由于传统的光刻胶分辨率受限,研究人员开始开发新型的化学增强光刻胶。
这种新型光刻胶可以提高分辨率,从而实现更高效的微电子芯片制造。
1974年,美国IBM公司研制成功的可感光脂类光刻胶,推动了光刻机技术的进一步发展。
其次,光源技术的进步也为光刻机的发展提供了重要的支持。
在早期光刻机中,常用的光源是汞灯。
然而,汞灯的光谱特性和辐射功率存在局限性。
1977年,荷兰ASML公司研发出了首台使用激光器作为光源的光刻机。
激光器光刻机具有光谱窄、辐射功率高等优点,大大提高了光刻机的分辨率和效率。
在90年代,光刻机经历了更多的技术突破。
随着芯片制造工艺的不断进步,对光刻机分辨率的要求也越来越高。
为了满足这一需求,光刻机的光学系统发生了重大改变。
光束的聚焦成为了光刻机技术的重要环节。
采用非球面透镜系统、镜面反射等技术,提高了光学系统的分辨率和光束质量,从而实现了更高的光刻胶分辨率和精度。
此外,投射光刻机和接触式光刻机的发展也为光刻技术的突破提供了多样性。
投射光刻机是基于投影光刻原理,通过光学系统将图案投射到光刻胶上。
在20世纪90年代初,荷兰ASML公司首次将投射光刻机商业化。
投射光刻机相较于接触式光刻机,具有更高的分辨率和制造效率,成为了微电子制造的主流技术。
光刻机发展史
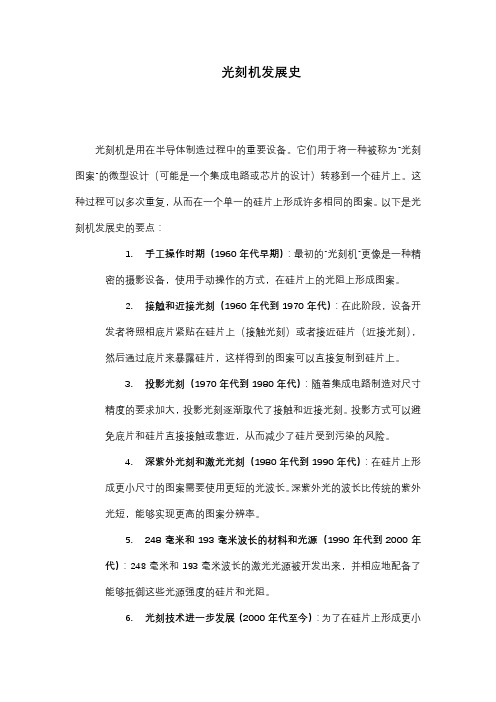
光刻机发展史光刻机是用在半导体制造过程中的重要设备。
它们用于将一种被称为“光刻图案”的微型设计(可能是一个集成电路或芯片的设计)转移到一个硅片上。
这种过程可以多次重复,从而在一个单一的硅片上形成许多相同的图案。
以下是光刻机发展史的要点:1.手工操作时期(1960年代早期):最初的"光刻机"更像是一种精密的摄影设备,使用手动操作的方式,在硅片上的光阻上形成图案。
2.接触和近接光刻(1960年代到1970年代):在此阶段,设备开发者将照相底片紧贴在硅片上(接触光刻)或者接近硅片(近接光刻),然后通过底片来暴露硅片,这样得到的图案可以直接复制到硅片上。
3.投影光刻(1970年代到1980年代):随着集成电路制造对尺寸精度的要求加大,投影光刻逐渐取代了接触和近接光刻。
投影方式可以避免底片和硅片直接接触或靠近,从而减少了硅片受到污染的风险。
4.深紫外光刻和激光光刻(1980年代到1990年代):在硅片上形成更小尺寸的图案需要使用更短的光波长。
深紫外光的波长比传统的紫外光短,能够实现更高的图案分辨率。
5.248毫米和193毫米波长的材料和光源 1990年代到2000年代):248毫米和193毫米波长的激光光源被开发出来,并相应地配备了能够抵御这些光源强度的硅片和光阻。
6.光刻技术进一步发展( 2000年代至今):为了在硅片上形成更小的图案,人们开发了全息光刻、离子束光刻和电子束光刻等新技术。
其中电子束光刻尤其受到关注,因为它的波长远比光波短,能够实现非常高的分辨率。
7.极紫外光刻(EUV) 2010年代至今):极紫外光刻使用13.5毫米的波长,比现有的193毫米敏光化学品技术要短得多,降低了芯片制造的复杂性,是目前市场上最新的硅光刻技术。
8.纳米光刻技术(2225年~): 面对纳米级别光刻的挑战,研发者正在探索使用多种新式的光刻技术来实现制造需要,诸如电子束光刻、离子束光刻、X射线光刻、电介质纳米阵列光刻等。
光刻机技术的进展与创新

光刻机技术的进展与创新光刻机是一种高精密度的制造设备,对于半导体行业来说具有至关重要的作用。
它使用光刻工艺将芯片设计图案转移到硅片上,从而实现集成电路的制造。
随着半导体技术的迅猛发展,光刻机技术也在不断进步和创新,以满足更高的制造要求和应用需求。
一、光刻机技术的进展1. 分辨率的提升:随着芯片制造工艺的不断演进,对于微小特征图案的制造要求越来越高,分辨率的提升成为关键。
光刻机技术通过使用更短波长的紫外光和改进的光刻胶材料,能够实现更高的分辨率。
目前,最先进的光刻机已经实现了10纳米级的分辨率,为芯片制造提供了更大的空间。
2. 全息光刻技术:全息光刻技术是一种新型的光刻技术,它通过使用干涉图案生成非常复杂的芯片图案。
与传统的投影光刻技术相比,全息光刻技术具有更高的分辨率和更大的制造灵活性。
它能够实现更高的芯片集成度,提高芯片的性能和功能。
3. 多层次光刻技术:多层次光刻技术是一种将多个层次的图案在同一个硅片上制造的技术。
通过使用多个刻蚀和光刻步骤,可以实现不同层次的互连结构和器件。
这种技术能够大大提高芯片制造的效率和准确性。
二、光刻机技术的创新1. 设备体积的减小:传统的光刻机设备通常体积庞大,不便于移动和操作。
新一代的光刻机设备致力于减小设备的体积,增加灵活性和便携性。
采用新型材料和设计理念,使得光刻机设备更加轻巧、紧凑,能够适应不同场景的需求。
2. 自动化和智能化:随着工业自动化和人工智能技术的发展,光刻机也在努力实现自动化和智能化。
通过引入先进的传感器和机器学习算法,光刻机能够实现自动调整和优化制造过程,提高生产效率和一致性。
3. 多层次刻蚀技术:在芯片的制造过程中,刻蚀是不可或缺的一步。
传统的刻蚀技术通常只能实现单层的刻蚀,而多层次刻蚀技术能够同时处理多个不同材料的层次。
这种创新技术能够大大简化生产过程,提高芯片制造的效率和可靠性。
4. 增强现实辅助制造:随着增强现实技术的兴起,光刻机制造过程中的操作也得到了改进。
光刻机的起源与发展

光刻机的起源与发展光刻机是一种用于微电子制造中的关键设备,它在现代科技中起着举足轻重的作用。
本文将详细探讨光刻机的起源与发展,并分析其在电子制造领域中的重要性。
光刻机最早的起源可以追溯到20世纪50年代,当时光刻机主要用于摄影行业。
然而,随着半导体技术的迅速发展,光刻机逐渐被引入到电子制造领域。
最早的光刻技术使用硬底片来将图案投射到光刻胶上,然后通过化学蚀刻的方式进行图案转移。
然而,这种方法非常繁琐且不精确,因此需要更加先进的技术来满足制造需求。
20世纪70年代,以美国为代表的科学家们开始研发光刻机的新技术。
他们发现,将光刻胶和图案进行光刻曝光后,再使用化学蚀刻的方式可以得到更加精确的图案。
这种光刻技术被称为光刻曝光技术,它的出现极大地推动了光刻机的发展。
在光刻曝光技术的基础上,光刻机的发展得以加速。
传统的光刻机使用紫外线光源进行曝光,而现代的光刻机则使用更高精度的深紫外光源。
这种深紫外光源可以提供更高的分辨率和更短的曝光时间,从而使得制造微小元件成为可能。
在20世纪90年代,光刻机迎来了一个重要的里程碑:双层光刻技术的出现。
双层光刻技术使得曝光光刻胶层和下方的反射层之间形成更大的折射率差,从而提高了光刻图案的分辨率和精度。
这项技术的引入为高密度集成电路的制造提供了巨大的便利。
随着科技的不断进步,光刻机的性能得到了进一步提升。
光刻机的曝光分辨率已经达到了亚微米级别,而曝光时间也大大缩短,从而提高了生产效率。
此外,纳米级别的光刻技术正在不断发展,为制造尺寸更小、性能更优的微电子元件铺平了道路。
光刻机在电子制造领域扮演着重要的角色。
它是集成电路制造的核心工艺之一,用于制造芯片中的电路图案。
利用光刻机,可以将复杂的电路图案准确地转移到硅片上,从而实现电子元件的制造。
光刻机的精度决定了整个电子元件的性能,因此它在电子制造工业中的重要性不可忽视。
除了电子制造领域,光刻机还被广泛应用于其他行业。
例如,光刻机可以用于制造光学元件,如激光器、光通信设备等。
光刻机的起源与发展

光刻机的起源与发展光刻机是半导体工业中至关重要的一种制造设备,它被广泛应用于集成电路和微电子器件的制造过程中。
本文将探讨光刻机的起源与发展,介绍其核心技术和在半导体工业中的应用。
一、光刻机的起源光刻机的起源可以追溯到1930年代的光学技术领域。
当时,科学家开始研究如何利用光线对物体进行图案的投射和复制。
这项研究成果奠定了光刻机的基础。
二战后,半导体工业迅速发展,对于更高密度和更精确的芯片制造要求也越来越高。
1960年代,光刻机在半导体工业中得到了广泛的应用。
这些早期的光刻机主要采用了光掩膜的方式进行图案的投射,其复杂性和制造成本较高。
二、光刻机的发展随着半导体工业的不断进步,对于更小尺寸、更高分辨率的芯片需求不断增长,光刻机也在技术和性能上得到了长足的发展。
下面将从光刻机的核心技术和应用两方面进行介绍。
1. 核心技术(1)光源技术:光刻机中的光源是生成光线的装置,早期使用的是汞灯等传统光源,后来发展出了激光光源和X射线光源等新型光源。
新型光源具有更高的光强度和更小的光斑尺寸,可以实现更高分辨率的图案投射。
(2)光刻胶技术:光刻机中使用光刻胶作为图案形成层。
光刻胶的选择和优化对于图案的精确复制至关重要。
随着技术的进步,新型的光刻胶不断涌现,具有更好的光敏特性和更低的副产物产生。
(3)投射光学系统:光刻机中的投射光学系统负责将光源发出的光线投射到光刻胶上,形成所需的图案。
投射光学系统的设计和精确度对于芯片的分辨率、精度和成像质量有着重要影响。
2. 应用领域光刻机在半导体工业中的应用非常广泛。
它被用于制造集成电路、微处理器、存储器芯片、显示面板等各种微电子器件。
其中,在集成电路制造中,光刻机扮演了关键角色。
通过光刻机将芯片表面的材料进行曝光、显影等处理,形成微细的图案结构。
这些图案结构决定了芯片功能和性能,对于半导体工艺的发展具有重要意义。
随着技术的不断进步,光刻机的分辨率不断提高,从最初的微米级到现在的纳米级。
光刻技术原理全解
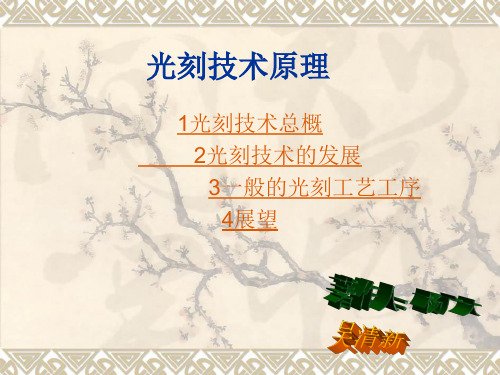
1光刻技术总概 2光刻技术的发展 3一般的光刻工艺工序 4展望
1光刻技术总概
光刻技术是指集成电路制造中利用光学- 化学反应原理和化学、物理刻 蚀方法,将电路图形传递到单晶表面或介质层上,形成有效图形窗口或 功能图形的工艺技术。随着半导体技术的发展,光刻技术传递图形的尺 寸限度缩小了2~3个数量级(从毫米级到亚微米级),已从常规光学技 术发展到应用电子束、 X射线、微离子束、激光等新技术;使用波长已 从4000埃扩展到 0.1埃数量级范围。光刻技术成为一种精密的微细加工 技术。常规光刻技术是采用波长为2000~4500埃的紫外光作为图像信息 载体,以光致抗蚀剂为中间(图像记录)媒介实现图形的变换、转移和 处理,最终把图像信息传递到晶片(主要指硅片)或介质层上的一种工艺 (图1)。在广义上,它包括光复印和刻蚀工艺两个主要方面。 ①光复 印工艺:经曝光系统将预制在掩模版上的器件或电路图形按所要求的位 置,精确传递到预涂在晶片表面或介质层上的光致抗蚀剂薄层上。 ②刻 蚀工艺:利用化学或物理方法,将抗蚀剂薄层未掩蔽的晶片表面或介质 层除去,从而在晶片表面或介质层上获得与抗蚀剂薄层图形完全一致的 图形。集成电路各功能层是立体重叠的,因而光刻工艺总是多次反复进 行。例如,大规模集成电路要经过约10次光刻才能完成各层图形的全部 传递 在狭义上,光刻工艺仅指光复印工艺,即图1中从④到⑤或从③到⑤ 的工艺过程。光复印工艺的主要流程如图2。 曝光方式 常用的曝光方 式
3.1、硅片清洗烘干
方法:湿法清洗+去离子水冲洗+脱水烘焙
(热板150~2500C,1~2分钟,氮气保护) 目的:a、除去表面的污染物(颗粒、有机 物、工艺残余、可动离子);b、除去水蒸气, 是基底表面由亲水性变为憎水性,增强表面 的黏 附性(对光刻胶或者是HMDS-〉六甲基 二硅胺烷)。
光刻技术综述

刻 技 术 ,不 少 国家 先后 建 造 丁同步 辐 射装 置 。例 如 , 我 国 的 同步 辐 射装 置 , 可 获 得高 强度 光
源;具 有范 尉广 的连 续单 色光 光谱 ,从X射线刘红外 ,主要 集 中在软X射线}辐射出的光偏 振性好 ,在 电子运动 轨道 平面 内,1 0 0 嘶水 平偏 振光,其 它方 向为 椭圆偏 振光; 准直性高 , 在
4 新 的领域应 用:
1 8 年 , 在 美 团的 密 执 安 州 的 底特 律 专 业 博 览会 上 ,首 次 展 出 了立 体 光 刘新 技 术 。该 技 97
术是当今光刻技术的一种新发展 ,使光刻技 术走 出两维光刻领域 ,步人三 维空间 。立体 光刻 技 术集 光化学 、激光技术 、计算机 C / A 和数 控技 术于 一体 , 因而 可 以说该技 术是光 AD C M
感光层的分辨 率和抗蚀 性将直接 影响光刻 图形 的质 量,因而 是光刻技术研究 的另一个重
点 。用高 分 子 材料 做 的 感 光 层 的 光 化 学 反应 ,主 要 原 理 在 于 光 交 联 反 应 。近 年 来 不 少 研 究 集
光刻机研发历史

光刻机研发历史光刻机是一种用于微电子制造中的关键设备,它的出现极大地推动了半导体工业的发展。
本文将从光刻机的研发历史出发,介绍光刻机的发展过程及其对半导体工业的影响。
20世纪50年代,随着集成电路的诞生,人们意识到需要一种能够将电路图案精确地复制到硅片上的技术。
于是,光刻机应运而生。
最早的光刻机是通过将电路图案投射到硅片上,再使用化学方法进行刻蚀的方式来进行制造。
然而,这种方法存在着很多缺点,如分辨率低、成本高等问题,限制了电子制造工艺的进一步发展。
为了克服这些问题,人们开始研发新型的光刻机。
1965年,美国贝尔实验室的科学家发明了一种新的光刻技术——接触式光刻。
这种技术利用光刻胶来代替直接在硅片上进行刻蚀,大大提高了分辨率和效率。
接触式光刻机的出现,使得集成电路制造工艺迈上了一个新的台阶。
然而,随着集成电路的不断发展,接触式光刻技术也逐渐暴露出了一些问题。
首先,接触式光刻机所使用的光学系统无法实现更高的分辨率,限制了集成电路的密度。
其次,接触式光刻机的工作接触方式容易造成硅片的损伤,影响了生产效率和产品质量。
为了解决这些问题,人们开始研发非接触式光刻技术。
1974年,日本理化学研究所的科学家发明了一种新的光刻技术——投影式光刻。
投影式光刻利用光学投影系统将电路图案投射到硅片上,避免了接触式光刻中的硅片损伤问题。
投影式光刻机的问世,使得集成电路的制造工艺实现了质的飞跃。
随着半导体工业的不断发展,对光刻机的要求也越来越高。
为了提高分辨率和生产效率,人们开始研发更先进的光刻技术。
1980年代,光刻机开始采用深紫外光(DUV)作为光源,大大提高了分辨率。
1990年代,光刻机开始采用精密光学系统和自动化控制技术,使得光刻机的精度和稳定性得到了进一步的提高。
如今,随着半导体工艺的不断进步,光刻机也在不断演化。
现代光刻机已经实现了纳米级的分辨率,为微电子制造提供了强有力的支持。
同时,光刻机的速度和生产效率也大大提高,推动了半导体工业的快速发展。
- 1、下载文档前请自行甄别文档内容的完整性,平台不提供额外的编辑、内容补充、找答案等附加服务。
- 2、"仅部分预览"的文档,不可在线预览部分如存在完整性等问题,可反馈申请退款(可完整预览的文档不适用该条件!)。
- 3、如文档侵犯您的权益,请联系客服反馈,我们会尽快为您处理(人工客服工作时间:9:00-18:30)。
摘要:
光刻在半导体集成电路制造工艺中,无论是从占用的资金、技术还是人员来看,都有举足轻重的地位。
光刻工艺的发展历史就是集成电路的发展历史,光刻技术的发展现状就是集成电路的发展现状,不论是最低端的,还是今天最为先进的集成电路制造,光刻技术水平始终决定着集成电路的生产水平。
关键词:光刻曝光分辨率
引言:
30多年以来,集成电路技术的发展始终是随着光学光刻技术的不断创新所推进的。
在摩尔定律的驱动下,光学光刻技术经历了接触/接近(Aligner)、等倍投影、缩小步进投影(Stepper)、步进扫描投影(Scanner)曝光方式的变革(见图l所示),曝光波长由436nm的h线向365nm的i线、继而到248nm的KrF0.5 m、0.35 m、0.1 m、90 nnl、65 nm、45 nnl等节点。
光刻技术始终为摩尔定律的不断向前推进而孜孜不懈地努力着,目前已迈向了32 nn]节点的开发阶段。
一.推动光刻技术和设备发展的动力
经济利益是si片直径由200ram向300mm转移的主要因素。
Canon于1995年着手300ram曝光机,推出了EX3L和[5L步进机,于1997~1998年提供日本半导体超前边缘技术(SELETE)集团使用,ASML公司的300ram步进扫描曝光机使用193nm波长,型号为FPA2500,也于1999年提供给SELETE集团使用。
曝光是芯片制造中最关键的制造工艺,由于光学曝光技术的不断创新,一再突破人们预期的极限,使之成为当前曝光的主流技术。
1997年美国GCA公司推出了第一台分布重复投影曝光机,被视为曝光技术的一大里程碑,1991年美国SVC公司推出了步进扫描曝光机,它集分布投影曝光机的高分辨率和扫描投影机的大视场、高效率于一身,更适合 (<0125 m)线条的大规模生产曝光。
后来Nikon公司又推出了NSR2S204B,用KrF,使用变形照明(MBI)可做到0115 111的曝光。
ASML公司也推出PAS15500/750E,使用该公司的AERILAIJII 照明,可解决0113 in曝光。
但1999ITRS建议。
01l3 111曝光方案是用193nm或248nm加分辨率提高技术 (RET);0110 nl曝光方案是用157、193nm加RET、接近式x光曝光(PxL)或离子束投影曝光(IPL)。
目前,Ic加工中线宽在0.25 m 以上的大生产光刻设备,基本都采用i谱线光源,当线宽在0.25g.m--~0.18 m 时,将采用248nm DUV(远紫外)投影光刻技术,若将DUV 辅以提高光刻分辨率的诸多措施,将可用于0.15 m IC器件的研制,这种光源多采用KrF准分子激光器。
但到了0.18 m 以下时,人们还是认为光学光刻将会发展193nm 和157nmVUV(真空紫外/深紫外)准分子激光光刻技术。
193nm技术已比较成熟[4],商品化在即,只是还有些问题正在解决,比如抗蚀剂等问题。
157nm 的F。
准分子激光光刻技术,被认为是193nm 的后续技术,可用于0.10 m尺寸IC器件的加工,现已有工业级的F2激光器,由Lambda Physik 公司研制[5]。
不过,该技术要达到实用化,估计要到2010年左右。
用于0.10 m 以下尺寸器件~JnY_的光刻技术即EUV[极紫外(辅射)],或许会采用126nm 的Ar。
准分子激光氩灯源,但在目前看来,不能不说还处于想象阶段,除光源本身外,各种配套技术、原材料、全反射光学系统等等价格昂贵得将会难以承受。
也许,到了这个时候,非光学光刻技术才会真正成为这个技术领域的超微细加工技术的主流,比如采用X-ray曝光技术、电子束(EB—stepper)曝光技术、离子束曝光技术,尽管这种设备的价格也相当昂贵。
据了解,日本东京精密有限公司(ACCRETECH),正在联合日本十几家大公司,共同研制用于0.10 m 及以下尺寸器件加工的大型系统设备EB—stepper,有望于5年内问世,NIKON 公司也在开展相关研究,整个行业正拭目以待。
最后,以NIKON 公司光刻系统设备及技术为例。
9O年代以来,为适应IC集成度逐步提高的要求,微细加工的技术也迅速提高,相继出现了g谱线,h谱线、i谱线光源及KrF、ArF、F:、Ar:等准分子激光光源,x 射线、电子束、离子束等非光学曝光技术也得到了发展。
8O年代,普遍认为光学分辨率的极限只能达到0.5 m 左右,而现在的大多数业内人士则认为可以达到0.1 m 甚至以下[3]。
表1给出了不同光源波长的分辨率
二.光刻技术的发展前景
目前,Ic加工中线宽在0.25 m 以上的大生产光刻设备,基本都采用i谱线光源,当线宽在0.25g.m--~0.18 m 时,将采用248nm DUV(远紫外)投影光刻技术,若将DUV 辅以提高光刻分辨率的诸多措施,将可用于0.15 m IC器件的研制,这种光源多采用KrF准分子激光器。
但到了0.18 m 以下时,人们还是认为光学光刻将会发展193nm 和157nmVUV(真空紫外/深紫外)准分子激光光刻技术。
193nm技术已比较成熟[4],商品化在即,只是还有些问题正在解决,比如抗蚀剂等问题。
157nm 的F。
准分子激光光刻技术,被认为是193nm 的后续技术,可用于0.10 m尺寸IC器件的加工,现已有工业级的F2激光器,由Lambda Physik公司研制[5]。
不过,该技术要达到实用化,估计要到2010年左右。
用于0.10 m 以下尺寸器件~JnY_的光刻技术即EUV[极紫外(辅射)],或许会采用126nm 的Ar。
准分子激光氩灯源,但在目前看来,不能不说还处于想象阶段,除光源本身外,各种配套技术、原材料、全反射光学系统等等价格昂贵得将会难以承受。
也许,到了这个时候,非光学光刻技术才会真正成为这个技术领域的超微细加工技术的主流,比如采用X-ray曝光技术、电子束(EB—stepper)曝光技术、离子束曝光技术,尽管这种设备的价格也相当昂贵。
据了解,日本东京精密有限公司(ACCRETECH),正在联合日本十几家大公司,共同研制用于0.10 m 及以下尺寸器件加工的大型系统设备EB—stepper,有望于5年内问世,NIKON 公司也在开展相关研究,整个行业正拭目以待。
最后,以NIKON 公司光刻系统设备及技术为例,图示为这几年的法杖状况。
三,结束语
如上所述,光刻技术正在不断地发展,且会越走越艰难,现在正处于这样一个关键阶段,继i线和248nm DUV这一目前光刻技术的主流之后,193nm和157nmVUV 的发展既相当重要,又将会遇到很大的困难,抗蚀剂的问题,各种提高分辨率的技术问题、原材料的问题等等。
这些技术的发展情况及商品化成本等因素,决定了光学光刻技术的寿限。
至于EUV 及以后的光刻技术,目前似乎还没有人能说得清楚。
而非光学光刻技术目前来说,发展较快,到了0.1O>m 以下时电子束(EB)曝光技术极有可能成为超微细加工的主流。
四,参考文献
1.《光学光刻技术的发展历程及趋势》王相森 (东北微电子研究所,沈阳110032)
2.《浅谈半导体光刻技术的发展趋势》樊乡 (上海交通大学微电子学院,上海200030)
3.《光学光刻技术的历史演变》马建军 (长庆实业集团有限公司,西安710021)。