熔体纺丝成型
第六章-2-熔融纺丝

图
(3)影响取向的因素
①聚合物分子量:M ②卷绕速度 纺程上不结晶时:VL↑,使σxx Δn ↑ 纺程上结晶时:VL↑,使σxx ↑ 微晶取向↑ 进一步使VL↑↑,Δn 变化缓慢 ③熔体泵供量(细度不变):W ↑ Δn↓ ④ 纤维细度(泵供量不变) :d↓ Δn ↑ ⑤环境介质温度的影响:Ts ↑ Δn↓ ⑥熔体温度的影响:To ↑ Δn↓ ηe ↑ σxx ↑ Δn ↑
两个重要的结论: (1)在横吹风时(Vx =0, V y=a)的传热系数为纵向吹风(Vx=a, Vy=0)时的两倍
(2)在纺丝线上丝条冷却的控制因素是变化的
=0.428A-0.3332Vy0.334 =0.428A-0.333Vx0.334 在纺程上部, Vx<<8Vy(Vy/ Vx >>0.125)时 在纺程下部, Vx>>8Vy( Vy/ Vx << 0.125)时
卷曲,上油,切断和打包整个工序。
长丝的后加工-拉伸
拉伸加捻示意图 1—筒子架 2—卷绕丝筒 3,8—导 丝棒 4—喂入辊 5—上拉伸盘 6—加热器 7—下拉伸盘 9—钢领 10—筒管 11—废丝轴 12—钢丝圈
拉伸加捻流程
POY丝假捻变形的加工
POY丝假捻变形的加工原理
利用纤维的热塑性,经 过“变形”和热定型而制得 的高度卷曲蓬松的弹力丝。 加捻、热定型、解捻这 三个过程在同一台机器上完 成。
②表面张力Fs
纺丝液的拉伸流动使流体比表面积增大,但表面张力 要使液体表面趋于最小, Fs是一种抗拒拉伸的作用力 。 Fs=2π(R0-Rx) λ Fs仅在液态区域内起作用;熔纺中一般很小,除了纺 低分子量物料外可忽略。
③摩擦力Ff
熔体纺丝(meltspinning)工艺原理
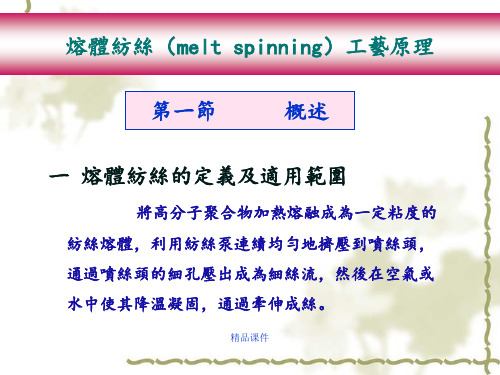
第三節 熔體紡絲過程中纖維結構的形成
❖ 初生纖維結構的形成和發展主要是指紡絲線上聚合物的取 向和結晶。
❖ 一 熔體紡絲過程中的取向作用
紡絲過程中發生取向是纖維製造中重要的結構
形成過程之一。對成品纖維的取向貢獻最大的不是 紡絲工序,而是拉伸工序。在紡絲過程中得到的取向 度,即預取向度,對拉伸工序和成品纖維的取向度有很
於絲條的方向上吹送調溫調濕氣流。
精品课件
初生纖維的後處理主要有拉伸、熱定型、捲曲 和假撚。
拉伸可改變初生纖維的內部結構,提高斷裂強度和
耐磨性,減少產品的伸長率。熱定型可調節紡絲過程帶
來的高聚物內部分子間作用力,提高纖維的穩定性和其
他物理-機械性能、染色性能。卷曲是改善合成纖維的
加工性(羊毛和棉花纖維都是捲曲的),克服合成纖維
❖ 二 熔體紡絲過程中的結晶
熔體紡絲線上的結晶是控制絲條固化的 一個極重要的動力學過程。紡絲線上的結晶對捲繞絲 的結構和性能起決定作用。 ❖ (一)熔體紡絲中纖維結晶的主要特徵
熔體紡絲中纖維結晶的特徵包括兩個方面 ,一是捲繞絲本身的晶態結構,二是熔體紡絲中聚合 物結晶過程的發展。
精品课件
捲繞絲的結晶特性主要包括:晶格結構 、結晶度、結晶形態和結晶取向等,它們對纖
大的影響,對結晶動力學和晶體形態也有一定的影響。
精品课件
精品课件
❖ 兩種取向機理:
(1)處於熔體狀態下的流動取向機理:包括噴絲孔 中切變流場中的流動取向和出噴絲孔後熔體細流在 拉伸流場中的流動取向
T高,τ小,取向小,可忽略
控制取向的速度場:軸向
精品课件 速度梯度,主要
(2)纖維固化之後的形變機理
1)紡絲線上的任何一點上,高聚物的流動是“穩態”的和連 續的。
熔体纺丝工艺原理
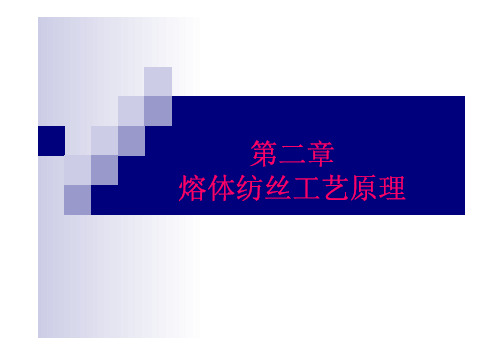
σ 12 ηγ̇ γ = = = τγ̇ = N Re,el G G
PP比PET纺丝流体的非牛顿性强,弹性 显著,τ值和ψ值越大,总法向应力差和 胀大比越大。因此流体的粘弹本质是决定 胀大比的内因。 � 适当提高纺丝温度,控制适宜的分子量, 适当增大喷丝孔径(0.4mm),以及增大 喷丝孔长径比(L/D值大于2)和降低剪切 速率。都是可以减小细流的胀大比,改善 PP的可纺性能。
�
1.简述影响纺丝流体弹性的因素及其对成形的影响。 2. 什么是孔口胀大?纺丝流体产生孔口胀大的原因是 什么?并说明欲提高纺丝产量会遇到哪些问题?怎样 克服? 3. 纺丝流体出现不稳定流动的原因是什么? 4. 什么是纺丝流体的可纺性?表征可纺性的方法有哪 些?纺丝中如何避免出现毛细断裂和内聚断裂? 5. 简述纺丝流体的挤出类型及其影响因素。
dmax时, d= d=d
dv x ̇x = ε =0 dx
X<10mm 弹性释放。
1.PA6,2.PET,3.PS
Ⅱ形变(细化)区: 丝条拉伸流动, 拉长变细。 Vx ↑, d ↓, 出现极大值, X=50-150cm 2 dv d vx a Ⅱ : x > 0, >0
dx dx 2
̇ ( X ) ↑ x ≈ 10cm T高, η 小,形变大。 ε V(x)增加快,大部分形变在此发生。
�
原则上,这两种断裂机理都能独立地对丝条的断裂 起作用。 两种断裂机理起控制作用的条件: η、 V0 较小时毛细破坏起控制作用 η、 V0 较大时内聚破坏起控制作用 在某一中间范围χ* 有极大值,可纺性最好
4. 纺丝中可能发生的断裂
表面张力(达因/cm2) PP.PE PA.PET 30-50 30-80
)=
熔体纺丝纤维成型原理
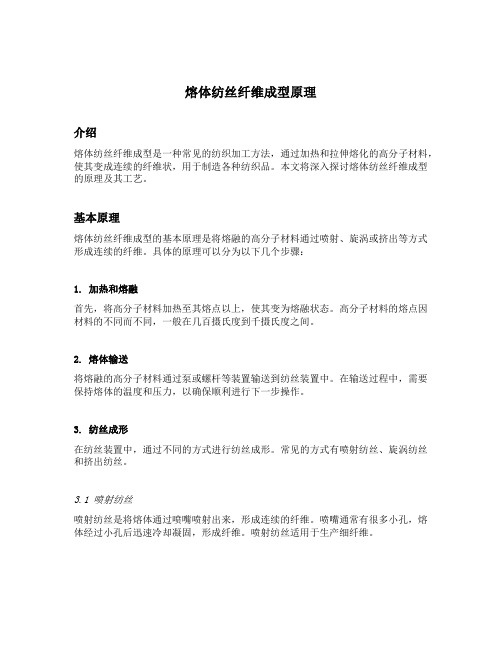
熔体纺丝纤维成型原理介绍熔体纺丝纤维成型是一种常见的纺织加工方法,通过加热和拉伸熔化的高分子材料,使其变成连续的纤维状,用于制造各种纺织品。
本文将深入探讨熔体纺丝纤维成型的原理及其工艺。
基本原理熔体纺丝纤维成型的基本原理是将熔融的高分子材料通过喷射、旋涡或挤出等方式形成连续的纤维。
具体的原理可以分为以下几个步骤:1. 加热和熔融首先,将高分子材料加热至其熔点以上,使其变为熔融状态。
高分子材料的熔点因材料的不同而不同,一般在几百摄氏度到千摄氏度之间。
2. 熔体输送将熔融的高分子材料通过泵或螺杆等装置输送到纺丝装置中。
在输送过程中,需要保持熔体的温度和压力,以确保顺利进行下一步操作。
3. 纺丝成形在纺丝装置中,通过不同的方式进行纺丝成形。
常见的方式有喷射纺丝、旋涡纺丝和挤出纺丝。
3.1 喷射纺丝喷射纺丝是将熔体通过喷嘴喷射出来,形成连续的纤维。
喷嘴通常有很多小孔,熔体经过小孔后迅速冷却凝固,形成纤维。
喷射纺丝适用于生产细纤维。
3.2 旋涡纺丝旋涡纺丝是将熔体喷射到旋转的输送气流中,通过离心力的作用将其拉伸成纤维。
旋涡纺丝适用于生产中纤纤维。
3.3 挤出纺丝挤出纺丝是将熔体通过挤出机的挤出口挤出,形成连续的纤维。
挤出纺丝适用于生产粗纤维。
4. 冷却和拉伸成形的熔体纤维需要经过冷却和拉伸处理。
冷却可以固化纤维,拉伸可以提高纤维的强度和拉伸性能。
5. 收集和卷绕最后,完成的纤维被收集起来,并通过卷绕装置进行卷绕。
卷绕的方式通常根据需要选择,可以是平板卷绕、筒形卷绕或其他形式。
工艺参数熔体纺丝纤维成型的工艺参数对成品的质量有重要影响。
以下是一些常见的工艺参数:1.温度:熔体的温度对纤维的形成和性能有影响,需要根据具体材料选择合适的温度。
2.压力:熔体的压力决定了纤维的形状和尺寸,过高或过低的压力都会影响纤维的质量。
3.拉伸速度:纤维的拉伸速度会影响纤维的强度和拉伸性能,需要根据要求进行调节。
4.冷却方式:不同的冷却方式会导致纤维的结构和性能产生变化,可以选择气体冷却、水冷却等方式。
熔体纺丝(melt spinning)工艺原理

冷卻速率增加,結晶所需時間降低,結晶速率隨
紡速提高而增加。
取向使結晶速率大大增加的原因,可以概括為兩類: 一,從結晶理論的角度看,大分子取向區域越大, 生成晶核的臨界溫度也越高,因此,在熔體冷卻的 過程中,取向高的體系能夠在較高的溫度下形成晶
核,取向低的體系則相反,必須有較大的過冷度才
能形成晶核。
取向度的測定:一般用取向因數f 表徵。
該式用於表徵單軸取向中結構單元的取向,υ
表示單元晶胞某晶軸與纖維軸的平均夾角,當
結構單元完全平行于纖維軸時,υ=0,f=1;
垂直于纖維軸時,υ=90度,f=0.5 。
二 熔體紡絲過程中的結晶
熔體紡絲線上的結晶是控制絲條固化的一個極
重要的動力學過程。紡絲線上的結晶對捲繞絲的結構
流一經固化,就有巨大的抗張能力,所以熔紡的捲繞速
度比濕紡為高,一般在1000~1500米/分,噴絲頭拉伸 比(捲繞速度與熔體從噴絲孔噴出速度之比)也比濕紡 時高。
三、上油
熔紡纖維剛成形時幾乎是幹的,容易積聚靜電,纖
維間的抱合力差,與設備的摩擦力大,因此在捲繞前要 經過給油、給濕處理。
對於吸水性較大的聚醯胺纖維還可以防止繞在筒 管上的絲條再度吸水,以致發生縱向膨脹而出現松圈 和塌邊等現象。 化學纖維在紡絲和紡織加工過程中因不斷摩擦而 產生靜電,必須使用助劑以防止或消除靜電積累,,同 時賦於纖維以柔軟、平滑等特性,使其順利通過後道
熔體紡絲過程中的參數可以歸為三類
第二節 熔體紡絲過程的運動學和動力學
紡絲線上直徑的變化和速度的分佈
從速度分佈,可求出拉 伸應變速率(軸向速度 梯度)
根據拉伸應變速率的 不同,把整個紡絲線 分成三個區域
熔融纺丝法简介

熔体制备(螺杆挤压机) 含水率较高的成纤高聚物在熔融纺丝前要经过干燥处 理,以防止由于水分引起的高聚物熔体分子降解。高聚物 切片受热熔融过程中微细结构发生如下变化:非晶区从玻 璃态转变为高弹态,再变为粘流态;结晶区发生晶体的融 化,也成为粘流态,最后高聚物形成熔体。
纺丝工艺过程 熔融挤压→过滤→静态混和→计量→熔体分配→挤出 成形→冷却 过滤可去除聚合物熔体中一些凝胶和细小的固体粒子。 静态混和是指聚合物熔体输送管道中静态混和器对聚 合物熔体的均匀混和作用。 计量和熔体分配可精确控制产量和纤维细度的一致性。
一般,喷丝孔直径越大,所纺纤维直径越大,纤维 双折射越低。喷丝孔直径越大,可以减缓熔体在喷丝孔 中流动时的径向剪切速度梯度,降低毛细粘性流动的切 应变速率,减少出口时的熔体膨大现象。喷丝孔越长, 熔体弹性形变能松弛越多,将来出口处熔体膨大越小。 通常,喷丝孔直径和长度大一些,纺丝比较稳定,尤其 是对高粘度熔体的纺丝有利。一般长径比大些,有利于 熔体松弛,减小出口膨大;但当长径比大到某一数值时, 膨大系数不再随长径比变化。
• 液滴型不能成为连续细流,纤维无法成形;液滴型出现的 条件首先与纺丝流体的性质有关。流体表面张力α越大, 则细流缩小其表面积成为液滴的倾向也越大。此外,粘度 η的下降也促使液滴的生成。 • 漫流型虽已形成连续细流,但纺丝流体在流出喷丝孔后, 迅即沿喷丝板表面漫流。这种细流很不稳定,纺丝往往因 而中断;为避免漫流型细流的出现,应设法提高η和R0 或 降低界面张力
• 聚合物熔体从喷丝孔挤 出成形,经历入流、孔 流、出流、变形和稳定 的流变过程,其物理形 态和几何形态均发生变 化。 • 高聚物流体通过喷丝孔 的流动有明显的流场变 化,而包括毛细孔入口 区的收敛流场,毛细孔 区的管道流动,以及毛 细孔出口区向拉伸流动 的流场过渡
熔融纺丝工艺流程

熔融纺丝工艺流程熔融纺丝工艺是一种将高分子材料通过熔融加工成纤维的方法。
该工艺被广泛应用于纤维素、聚酯、聚酰胺等高分子材料的制备。
下面将详细介绍熔融纺丝工艺的流程。
一、准备工作1.1 原料准备首先需要准备好所需的高分子材料,如聚酯、聚酰胺等。
这些高分子材料通常以粉末或颗粒的形式存在。
1.2 设备准备熔融纺丝设备包括熔体供给系统、挤出机、旋转收卷器等部件。
在进行熔融纺丝之前,需要对这些设备进行检查和调整,确保其正常运行。
二、挤出加工2.1 熔体供给系统首先将高分子材料放入熔体供给系统中,通过加热和搅拌使其变成流动状态。
这个过程中需要控制温度和压力,以确保高分子材料能够顺利地进入挤出机。
2.2 挤出机接下来,在挤出机的作用下,将熔体推出并拉伸成细丝。
挤出机的主要部件包括螺杆、筛网和模头。
螺杆通过旋转将熔体向前推进,筛网则用于过滤杂质,模头则用于控制纤维的形状和尺寸。
2.3 拉伸在挤出机的作用下,高分子材料被拉伸成细丝。
这个过程中需要控制温度和速度,以确保纤维的质量和性能。
三、收卷3.1 冷却在拉伸完成后,纤维需要进行冷却处理。
这个过程中需要控制温度和速度,以确保纤维能够顺利地进行收卷。
3.2 收卷最后,将冷却后的纤维送入旋转收卷器中进行收卷。
这个过程中需要控制张力和速度,以确保纤维能够均匀地分布在收卷器上。
四、检验与包装4.1 检验在完成收卷之后,需要对纤维进行检验。
这个过程中需要检查纤维的外观、尺寸、强度等指标,并对不合格品进行处理。
4.2 包装最后,将合格的纤维进行包装。
通常将纤维卷成一定长度和重量的卷筒,并进行标记和记录。
总结:熔融纺丝工艺是一种将高分子材料通过熔融加工成纤维的方法。
该工艺包括准备工作、挤出加工、收卷和检验与包装等步骤。
在进行熔融纺丝之前,需要对设备进行检查和调整,确保其正常运行。
在挤出机的作用下,高分子材料被拉伸成细丝,并经过冷却和收卷处理后进行检验和包装。
熔体纺丝定义

熔体纺丝定义熔体纺丝定义熔体纺丝是一种制备纤维的方法,它利用高分子材料的熔融状态将其挤出成细丝,并在空气中冷却和固化。
该方法广泛应用于纤维、薄膜、管材等领域,并有着广泛的应用前景。
一、熔体纺丝的基本原理熔体纺丝是利用高分子材料在加热条件下从固态转变为液态,经过特定的挤出系统将其挤出成细丝,然后通过空气或其他方式进行冷却和固化。
这个过程主要包括以下几个步骤:1.高分子材料加热:将高分子材料放入挤出机中,在一定的温度和压力下加热。
2.挤出成形:在加热条件下,高分子材料从机头中挤出成细丝。
3.冷却固化:将挤出来的细丝通过空气或其他方式进行冷却和固化,使其变得坚硬并具有所需的物理性能。
二、熔体纺丝的分类根据不同的加工方式和设备类型,熔体纺丝可以分为以下几种:1.单丝熔体纺丝:将高分子材料从单一的机头中挤出成细丝。
2.多丝熔体纺丝:将高分子材料从多个机头中挤出成多根细丝,然后通过特定的方式进行合并。
3.微纳米级熔体纺丝:利用电场、气流等特定条件对高分子材料进行加工,制备出微小尺寸的纤维或薄膜。
三、熔体纺丝的应用由于熔体纺丝具有制备成本低、生产效率高、产品性能优良等优点,因此在许多领域都有广泛的应用。
以下是几个典型的应用领域:1. 纤维制备:利用熔体纺丝技术可以制备各种类型的合成和天然纤维,如聚酯、聚酰胺、聚乙烯等。
2. 薄膜制备:通过控制挤出速度和冷却方式,可以制备各种类型的薄膜,如聚乙烯薄膜、聚氨酯薄膜等。
3. 医疗器械:熔体纺丝技术可以制备出具有良好生物相容性的材料,用于制备医用敷料、人工血管等医疗器械。
4. 环保材料:利用可降解高分子材料进行熔体纺丝制备,可以制备出可降解的环保材料,如可降解塑料袋、餐具等。
四、熔体纺丝的优缺点1. 优点:(1)生产效率高,可以大批量生产;(2)生产成本低,适合大规模生产;(3)产品性能优良,具有较高的强度和耐磨性;(4)可以制备出各种类型的高分子材料。
2. 缺点:(1)对原始材料要求较高;(2)设备成本较高;(3)对操作人员技术要求较高。
第2章化学纤维成型原理精品PPT课件

三、熔体纺丝的运动学和动力学
1、熔体纺丝线上的速度分布:
熔体从喷丝孔挤出后,熔体丝条逐渐被拉细,运动速度逐步加大
2、熔体纺丝线上的力平衡:
Fp+Fg=Fr+Fi+Ff+Fs 式中卷绕张力Fp可用张力计在纺丝线上直接测定,重力Fg、惯性力Fi、摩擦力Ff及表面张力Fs可根据理论 计算得到,从而可求出流变阻力Fr
传热过程:热效应不大(传质过程中温度差别不大)
四、湿法纺丝中纤维结构的形成
1、初生纤维溶胀度:
取向度:溶胀度↓→高聚物含量↑→分子间作用力↑→取向度↑→ 断裂强度↑ 序态和染色饱和值:溶胀度↑→较高的碘溶胀度(低序态)和高的染色饱和值 干燥收缩率:溶胀度↑→纵向收缩率↑
2、形态结构:
横截面形状:强烈凝固→非圆形横截面 缓慢凝固→圆形横截面
大分子链结构:分子间作用力强、刚性分子链、化学交联→溶解度↓ 超分子结构:结晶高聚物→溶解度↓ 溶剂:极性溶剂(成纤高聚物是极性高聚物)
3、溶剂的选择:
高分子~溶液相互作用参数χ1: χ1< 1/2 →大分子和溶剂分子间作用能↑→溶解 χ1<1/2 →大分子和溶剂分子间作用能↑→不溶解
相似相溶:结构 内聚能密度或溶度参数相近 :溶解
四、成型过程中的热量变化
热量变化:熔体细流不断向周围介质释出热量,温度逐渐下降。 手段:强制对流传热(环形吹风、侧吹风)
五、熔体纺丝中纤维结构的形成
1、取向:
机理:熔体状态下的流动取向机理(喷丝孔中切变流场中的流动取向和出喷丝孔后熔体细流在拉伸流场 中的流动取向);纤维固化之后的形变取向机理
表示:双折射Δn,Δn↑→纤维取向度↑ 大小:流动形变区:该区在喷丝板以下0~70cm范围,解取向主要(高温),取向很小
熔体纺丝纤维成型原理

熔体纺丝纤维成型原理
熔体纺丝纤维成型是一种常见的制造纤维和材料的方法。
它是通过将高分子材料加热到其熔点,然后将其通过细孔或喷嘴挤出来形成连续的纤维。
这种方法可以用于制造各种不同类型的纤维,包括聚酯、尼龙、聚丙烯等。
在熔体纺丝过程中,高分子材料首先被加热到其熔点以上的温度,使其变成液态。
然后,液态高分子材料通过喷嘴或细孔挤出,并在空气中冷却和固化。
这个过程称为拉伸固化。
拉伸固化是整个过程中最重要的步骤之一。
在拉伸固化期间,挤出的液态高分子材料会被拉伸成一个非常细小的直径,并在空气中迅速冷却和固化。
这种快速冷却和固化使得纤维具有优异的强度和耐久性。
在熔体纺丝过程中,控制喷嘴或细孔大小以及拉伸速度非常重要。
如果喷嘴或细孔太大,那么挤出的液态高分子材料将会过于厚重,导致纤维质量下降。
相反,如果喷嘴或细孔太小,那么挤出的液态高分子材料将会过于细小,难以拉伸和固化。
另外,拉伸速度也非常重要。
如果拉伸速度太慢,那么纤维将会变得过于粗糙和不均匀。
相反,如果拉伸速度太快,那么纤维将会变得过
于脆弱和易碎。
总之,在熔体纺丝纤维成型中,控制好喷嘴或细孔大小以及拉伸速度是非常重要的。
这种方法可以制造出各种不同类型的纤维,并被广泛应用于各种领域,包括服装、家居用品、医疗器械等。
熔体纺丝纤维成型原理

熔体纺丝纤维成型原理熔体纺丝纤维成型是一种常见的纤维成型工艺,广泛应用于纺织、塑料、化工等行业。
它通过将高分子材料加热至熔化状态,然后将熔融的高分子材料通过模具或喷丝孔口挤出,经过冷却固化后形成纤维的过程。
本文将详细介绍熔体纺丝纤维成型的原理及其基本流程。
一、熔体纺丝纤维成型的原理熔体纺丝纤维成型的原理主要涉及高分子材料的熔化、挤出和冷却固化过程。
具体而言,其原理如下:1. 高分子材料的熔化:将固态的高分子材料通过加热使其达到熔化状态。
高分子材料通常是聚合物或聚合物混合物,如聚酯、聚酰胺等。
加热温度通常高于材料的熔融温度,使其分子链断裂,形成熔融状态。
2. 熔融高分子材料的挤出:将熔融的高分子材料通过模具或喷丝孔口挤出。
模具或喷丝孔口的形状决定了挤出物的截面形状。
挤出过程中,高分子材料受到挤出机的压力驱动,从而形成连续的纤维。
3. 冷却固化:挤出的熔融高分子材料在空气中迅速冷却,并逐渐固化成为纤维状。
冷却速度和温度对纤维的性能有重要影响,通常需要通过控制冷却气流或其他冷却方式来实现。
二、熔体纺丝纤维成型的基本流程熔体纺丝纤维成型的基本流程包括材料准备、熔化、挤出和冷却固化等步骤。
具体而言,其流程如下:1. 材料准备:选择适合的高分子材料,并按照一定的配比将其准备好。
通常需要将高分子材料切碎成小颗粒,以便于后续的加热和熔化。
2. 熔化:将高分子材料加入熔体纺丝设备中,通过加热使其熔化。
加热温度和时间需要根据不同的材料和设备来确定,以保证材料充分熔化且不发生分解。
3. 挤出:将熔融的高分子材料通过模具或喷丝孔口挤出。
挤出机通过控制压力和速度来控制纤维的直径和速度。
挤出口的形状决定了纤维的截面形状,可以是圆形、扁平形或其他形状。
4. 冷却固化:挤出的熔融高分子材料在空气中迅速冷却,并逐渐固化成为纤维状。
冷却速度和温度需要根据材料的特性和要求来控制。
冷却后的纤维可以通过拉伸、卷绕等处理方式进行进一步加工。
熔融纺丝法

熔融纺丝法(Melt spinning)是一种常见的纺丝工艺,用于将高分子材料(如聚合物)从熔融状态转变为纤维的过程。
该工艺常用于合成纤维的生产,例如聚酯纤维、聚酰胺纤维等。
以下是熔融纺丝法的一般步骤和关键要点:
原料准备:将所需的高分子材料(聚合物)加工成颗粒状或片状形式,以便于后续的熔融处理。
通常需要对原料进行预处理,如干燥去除水分。
加热熔融:将预处理的高分子材料放入熔融设备中,如熔体挤出机或熔融纺丝机。
通过加热和机械搅拌,将高分子材料加热至熔融状态,形成可流动的熔体。
纺丝成型:将熔融的高分子熔体通过纺丝孔板或纺丝喷嘴,以合适的速度和压力喷出。
喷出的熔体会迅速冷却和固化,形成连续的纤维。
拉伸和冷却:在纺丝过程中,通过拉伸装置将形成的纤维拉伸,以改变其物理性质和尺寸。
同时,通过冷却装置将纤维迅速冷却,固化并增强其结构。
采集和收集:将拉伸冷却后的纤维通过辊筒或其他采集装置收集起来,形成卷曲的纤维束或纺线。
熔融纺丝法具有高效、连续和可控的特点,可以生产出各种不同性质的纤维。
该工艺可以根据不同的需求和应用,调整加热温度、拉伸速度、冷却方式等参数,以控制纤维的物理性质、直径和形态。
它广泛应用于纤维制造、纺织、塑料工业等领域。
熔体纺丝工艺原理
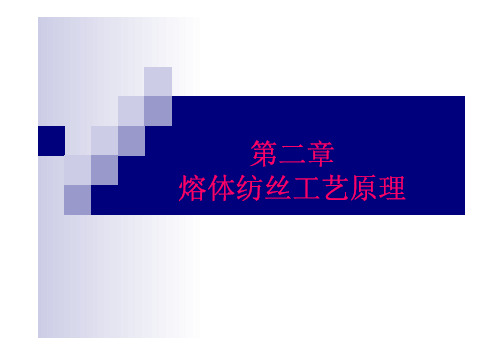
第二节 熔体纺丝原理 一、熔体纺丝工艺
聚合物熔体
熔体过滤及分配
纺丝
后加工
高聚物切片
熔体制备
纺丝箱体分配 组件过滤
喷丝板成型
纤维
螺杆熔融
熔体纺丝过程
熔纺纤维的纺丝成型
melt
solid
Melt-spinning sketch
直接纺:单体聚合
高聚物熔体
纺丝箱体 丝孔挤出
泵送至纺丝组件
由喷
切片纺:切片筛选干燥等处理 螺杆挤出机中熔融
dmax时, d= d=d
dv x ̇x = ε =0 dx
X<10mm 弹性释放。
1.PA6,2.PET,3.PS
Ⅱ形变(细化)区: 丝条拉伸流动, 拉长变细。 Vx ↑, d ↓, 出现极大值, X=50-150cm 2 dv d vx a Ⅱ : x > 0, >0
dx dx 2
̇ ( X ) ↑ x ≈ 10cm T高, η 小,形变大。 ε V(x)增加快,大部分形变在此发生。
表 口模材料对临界剪切应力的影响
̇↑ 临界 γ
̇↑ 临界 γ
3. 发生熔体破裂的条件的评定方法:
由临界剪切应力来评定:对大多数聚合物言, 约在105Pa左右。 � 由临界剪切速率来评定:105s � 由临界粘度来评定:ηcr=0.025ηo ̇ >5~8 � 由弹性雷诺准数来评定:Reel=τ γ τ:温度、浓度、分子量等 γ̇ :喷丝孔几何尺寸、泵供量、纺速等
(1)几何形态变化 (do dl) 喷丝孔(0.1~0.4mm) 纤维20~30μm 减小10倍 (2)物理形态变化 ①宏观状态米 几百米~几千米 增大百倍 50-100% Ci-X (浓度场) 20% P-X (应力场)
纤维的熔融纺丝
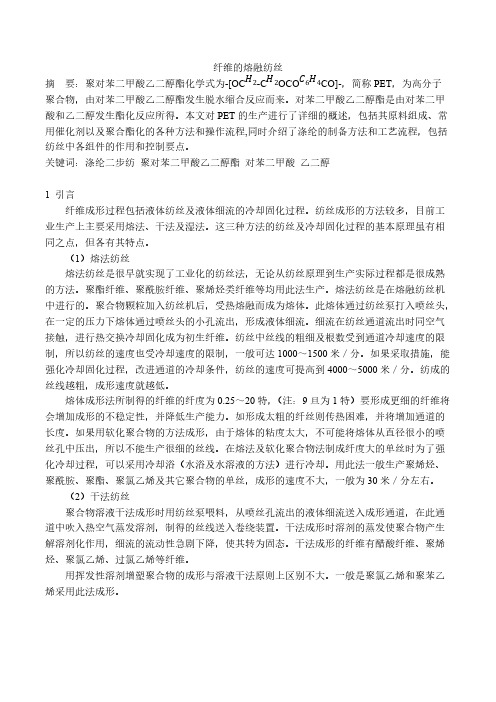
纤维的熔融纺丝H2H2C6H4摘要:聚对苯二甲酸乙二醇酯化学式为-[OC-C OCO CO]-,简称PET,为高分子聚合物,由对苯二甲酸乙二醇酯发生脱水缩合反应而来。
对苯二甲酸乙二醇酯是由对苯二甲酸和乙二醇发生酯化反应所得。
本文对PET的生产进行了详细的概述,包括其原料组成、常用催化剂以及聚合酯化的各种方法和操作流程,同时介绍了涤纶的制备方法和工艺流程,包括纺丝中各组件的作用和控制要点。
关键词:涤纶二步纺聚对苯二甲酸乙二醇酯对苯二甲酸乙二醇1 引言纤维成形过程包括液体纺丝及液体细流的冷却固化过程。
纺丝成形的方法较多,目前工业生产上主要采用熔法、干法及湿法。
这三种方法的纺丝及冷却固化过程的基本原理虽有相同之点,但各有其特点。
(1)熔法纺丝熔法纺丝是很早就实现了工业化的纺丝法,无论从纺丝原理到生产实际过程都是很成熟的方法。
聚酯纤维、聚酰胺纤维、聚烯烃类纤维等均用此法生产。
熔法纺丝是在熔融纺丝机中进行的。
聚合物颗粒加入纺丝机后,受热熔融而成为熔体。
此熔体通过纺丝泵打入喷丝头,在一定的压力下熔体通过喷丝头的小孔流出,形成液体细流。
细流在纺丝通道流出时同空气接触,进行热交换冷却固化成为初生纤维。
纺丝中丝线的粗细及根数受到通道冷却速度的限制,所以纺丝的速度也受冷却速度的限制,一般可达1000~1500米/分。
如果采取措施,能强化冷却固化过程,改进通道的冷却条件,纺丝的速度可提高到4000~5000米/分。
纺成的丝线越粗,成形速度就越低。
熔体成形法所制得的纤维的纤度为0.25~20特,(注:9旦为1特)要形成更细的纤维将会增加成形的不稳定性,并降低生产能力。
如形成太粗的纤丝则传热困难,并将增加通道的长度。
如果用软化聚合物的方法成形,由于熔体的粘度太大,不可能将熔体从直径很小的喷丝孔中压出,所以不能生产很细的丝线。
在熔法及软化聚合物法制成纤度大的单丝时为了强化冷却过程,可以采用冷却浴(水浴及水溶液的方法)进行冷却。
第三章熔体纺丝工艺原理总结
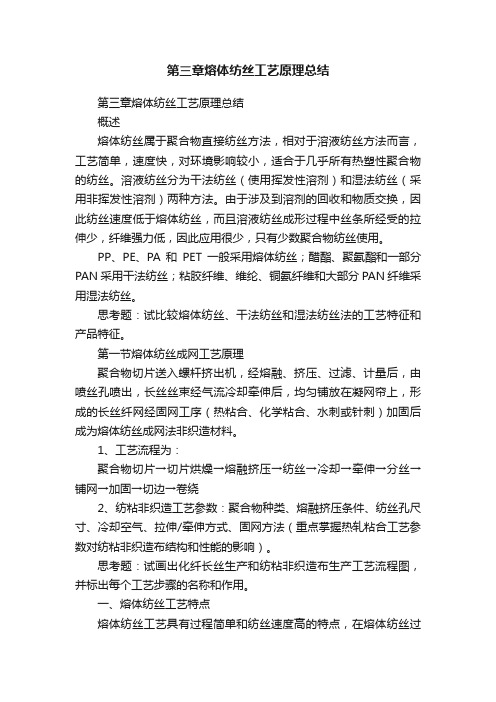
第三章熔体纺丝工艺原理总结第三章熔体纺丝工艺原理总结概述熔体纺丝属于聚合物直接纺丝方法,相对于溶液纺丝方法而言,工艺简单,速度快,对环境影响较小,适合于几乎所有热塑性聚合物的纺丝。
溶液纺丝分为干法纺丝(使用挥发性溶剂)和湿法纺丝(采用非挥发性溶剂)两种方法。
由于涉及到溶剂的回收和物质交换,因此纺丝速度低于熔体纺丝,而且溶液纺丝成形过程中丝条所经受的拉伸少,纤维强力低,因此应用很少,只有少数聚合物纺丝使用。
PP、PE、PA 和PET一般采用熔体纺丝;醋酯、聚氨酯和一部分PAN采用干法纺丝;粘胶纤维、维纶、铜氨纤维和大部分PAN纤维采用湿法纺丝。
思考题:试比较熔体纺丝、干法纺丝和湿法纺丝法的工艺特征和产品特征。
第一节熔体纺丝成网工艺原理聚合物切片送入螺杆挤出机,经熔融、挤压、过滤、计量后,由喷丝孔喷出,长丝丝束经气流冷却牵伸后,均匀铺放在凝网帘上,形成的长丝纤网经固网工序(热粘合、化学粘合、水刺或针刺)加固后成为熔体纺丝成网法非织造材料。
1、工艺流程为:聚合物切片→切片烘燥→熔融挤压→纺丝→冷却→牵伸→分丝→铺网→加固→切边→卷绕2、纺粘非织造工艺参数:聚合物种类、熔融挤压条件、纺丝孔尺寸、冷却空气、拉伸/牵伸方式、固网方法(重点掌握热轧粘合工艺参数对纺粘非织造布结构和性能的影响)。
思考题:试画出化纤长丝生产和纺粘非织造布生产工艺流程图,并标出每个工艺步骤的名称和作用。
一、熔体纺丝工艺特点熔体纺丝工艺具有过程简单和纺丝速度高的特点,在熔体纺丝过程中,成纤高聚物经历了两种变化,即几何形状的变化和物理状态的变化。
几何形状的变化是指成纤高聚物经过喷丝孔挤出和拉长而形成连续细丝的过程;物理变化即先将高聚物变为易于加工的流体,挤出后为保持已经改变了的几何形状和取得一定的化纤结构,使高聚物又变为固态。
原则上讲,分解温度高于熔点温度(或流动温度)的热塑性高聚物都可以采用熔体纺丝法。
二、熔体纺丝工艺过程(以纺粘法非织造布生产过程为例)主要步骤:―高聚物纺丝熔体的制备;―熔体自喷丝孔挤出/纺丝;―挤出的熔体细流的冷却和拉伸成形;―成形的纤维长丝铺网与固网。
熔体纺丝工艺要点

-熔体纺丝工艺原理-装置纺丝工艺流程及特点简介•附加和辅助设备简介弟一扁涤纶短纤维纺丝工艺部分合成纤维即用石油、天然气、煤及农副产品等为原料,经一系列的化学反应,制成合成高分子化合物,再经加工而制成的纤维。
其生产始于本世纪30年代中期,由于其性能优良,用途广泛,原料来源丰富,生产又不受气候或土壤条件的影响,所以合成纤维工业自建立以来,发展十分迅速。
在品种方面,占主导地位的是涤纶、锦纶和晴纶。
合成纤维的纺丝成型方法主要有熔体纺丝法和溶液纺丝法两不中。
溶液纺丝是化学纤维传统的成型工艺,根据纺丝原液细流的凝固方式不同,又分为湿法纺丝和干法纺丝。
湿法纺丝是指纺丝溶液经混合、过滤和脱泡等纺前准备,送至纺丝机,通过计量泵、过滤器、连接管,进入喷丝头,从喷丝头毛细孔中压出的原液细流进入凝固浴,原液细流中的溶剂向凝固浴扩散,浴中的沉淀剂向细流扩散,高聚物在凝固浴中析出而形成纤维。
湿法纺丝中的扩散和凝固是一些物理化学过程,但在某些化学纤维(如粘胶纤维)的湿法纺丝过程中,还同时发生化学变化,因此,湿法纺丝的成形过程是比较复杂的。
干法纺丝是指从喷丝头毛细孔中压出的原液细流不是进入凝固浴,而是进入纺丝甬道中。
由于通入甬道中的热空气流的作用,使原液细流中的溶剂快速挥发,挥发出来的溶剂蒸汽被热空气流带走。
在逐渐脱去溶剂的同时,原液细流凝固并伸长变细而形成初生纤维。
在干法纺丝过程中,纺丝原液与凝固介质(空气)之间只有传热和传质过程,不发生任何化学变化。
干法纺丝的成形过程与熔体纺丝有某些相似之处,它们都是在纺丝甬道中使高聚物液流的粘度达到某一极限值来实现凝固的,所不同的在于熔体纺丝时,这个过程是借温度下降而达到,而干法纺丝则是通过高聚物浓度的不断增大而完成的。
熔体纺丝是指成纤高聚物在高于其熔点10- 40 C的熔融状态下,形成较稳定的纺丝熔体,然后通过喷丝孔挤出成型,熔体射流在空气或液体介质中冷却凝固,形成半成品纤维,再经过拉伸、热定型等后处理工序,即成为成品纤维。
第2章化学纤维成型原理
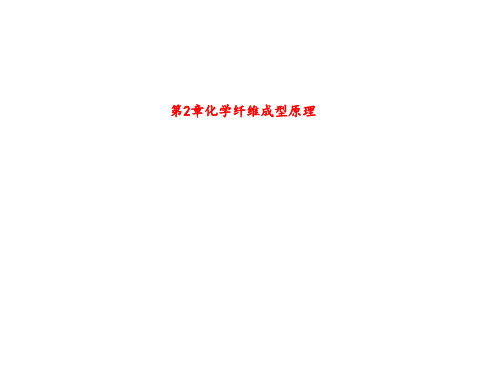
4、形变区 (膨化区之后与固化点之间 ):
离开喷丝板10~15cm的距离内,温度高,流动好→卷绕张力→熔体细流拉长变细、速度上 升→ 冷却风→细流从上到下温度降低→黏度增加→大分子取向度增加(双折射上升)、大 分子结晶→该区的终点即为固化点(离喷丝板板面约40~80cm )
5、稳定区 (固化点到卷绕筒 ):
Ⅲ区:纤维传质传热形成纤维结构的主要区域。纤维开始成形,溶剂从纤维中间层向表 面扩散,溶剂蒸发的速度更慢,浓度分布变得更大,随着蒸发强度的急剧降低,丝条表面 温度上升并接近热风温度。此时,纤维中的分子扩散速度又小,在此阶段开始除去使聚合 物分子溶剂化的那部分溶剂。在Ⅲ区内,溶剂的蒸发速度变小,以致聚合体与溶剂间的相 互作用加强,而且受内部扩散控制。Ⅲ区丝条的固化过程基本上完成,此时溶剂含量约为 30%~50%。从甬道出来的纤维溶剂含量为5%~25%。
结晶取向区:该区在喷丝板下80~130cm范围,结晶和取向加速 塑性形变区:接近固化的末端,距离喷丝板130cm,,部分变形取向
2、结晶:
晶格结构、结晶度、结晶形态和结晶取向
二、湿法纺丝的运动学和动力学
1、湿法成型过程中纺丝线上的速度分布:
喷丝头正拉伸:纺丝线的速度略大于喷丝速度,胀大区消失或部分消失,速度和速 度梯度沿纺程的分布情况和熔纺相类似。 零拉伸与负拉伸:胀大区的存在,刚进入凝固浴时,纺丝线的速度低于喷丝速度。
三、湿法纺丝中的传质过程
双扩散的传质过程: 液体细流中的溶剂及盐类向外扩散,而凝固剂向内扩散,结果 形成固相纤维。
传热过程:热效应不大(传质过程中温度差别不大)
四、湿法纺丝中纤维结构的形成
1、初生纤维溶胀度:
取向度:溶胀度↓→高聚物含量↑→分子间作用力↑→取向度↑→ 断裂强度↑ 序态和染色饱和值:溶胀度↑→较高的碘溶胀度(低序态)和高的染色饱和值 干燥收缩率:溶胀度↑→纵向收缩率↑
熔融纺丝工艺试验报告
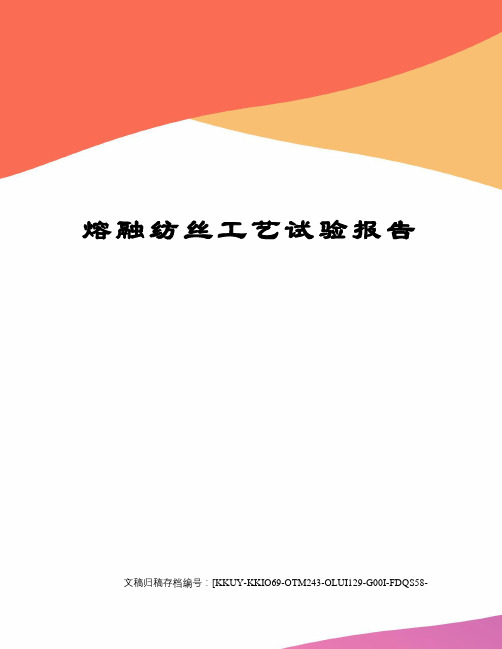
熔融纺丝工艺试验报告文稿归稿存档编号:[KKUY-KKIO69-OTM243-OLUI129-G00I-FDQS58-熔融纺丝工艺实验一,实验目的合成纤维的成形普遍采用高聚物的熔体或浓溶液进行纺丝,前者称为熔体纺丝,后者称为溶液纺丝。
本实验采用切片纺丝的方法,将聚合物熔体经过铸带,切粒等工序制成“切片”,然后在纺丝机上重新熔融成熔体并进行纺丝。
1.了解和掌握切片熔融纺丝的工艺路线和基本方法,通过熟悉并掌握常规纤维的成型条件和工艺参数。
2.了解熔融纺丝及牵伸设备的结构和各种部件的作用。
二,实验原理整个熔体纺丝过程包括纺丝熔体的制备,熔体自喷丝孔挤出,熔体细流拉长变细,冷却固化,丝条的上油和卷绕。
在切片熔融阶段,切片受热后结晶破坏,使其有一定结晶度的固体状态转变为均匀的粘流态,这是物理变化。
在冷却形成阶段聚合体发生的主要是物理变化,熔融后的聚合体在一定的压力下通过喷丝孔,形成熔体细流,熔体细流刚离开喷丝板时,由于熔体的弹性效应而出现膨胀现象,使熔体直径逐渐扩大,在纺程上细流受到卷绕拉力的作用,这时纤维直径急剧变细,同时丝条运动速度逐步加快,又由于空气冷却的作用,使聚合体温度下降,粘度增高,速度增加减慢,直径变化较小,再往下聚合体凝固并逐渐冷却至玻璃化温度以下,进入玻璃态,纤维固化,又由于固化后的纤维干燥而松散,以及纤维与设备,纤维与纤维之间相互摩擦产生静电,导致毛丝,给后加工带来困难,因此需经过给湿上油,增加纤维间抱合力,抗静电,使纤维变得柔软,平滑并获得良好的手感及弹性。
熔体纺丝过程的参数:指对纺丝过程的进行以及卷绕丝结构和性质起主导作用的参数。
这类参数有:成纤高聚物的种类;挤出温度;喷丝孔直径;喷丝孔长度;纺丝线的单纤维根数;质量流量;纺丝线长度,卷绕速度;冷却条件。
三,实验仪器及工艺过程1.纺丝工艺流程:切片、干燥、熔融挤出、冷却成形、上油、牵伸、卷绕。
2.切片干燥的目的:除去水分,提高切片的含水的均匀性,提高结晶度及软化点。
- 1、下载文档前请自行甄别文档内容的完整性,平台不提供额外的编辑、内容补充、找答案等附加服务。
- 2、"仅部分预览"的文档,不可在线预览部分如存在完整性等问题,可反馈申请退款(可完整预览的文档不适用该条件!)。
- 3、如文档侵犯您的权益,请联系客服反馈,我们会尽快为您处理(人工客服工作时间:9:00-18:30)。
熔体纺丝成型
一、实验目的
了解熔体纺丝机的各部分组成,掌握螺杆挤压机、计量泵的工作原理,了解纺丝工艺条件和工艺流程,设计出合理的纺丝工艺,纺制出合格的纤维
二、实验原理
一)螺杆挤压机的工作原理和结构
1、工作原理
物料从加料口进到螺杆的螺槽中,由于螺杆的转动,把切片向前推进。
切片不断吸收加热装置供给的热能;另一方面因切片和切片、切片与螺杆及套筒的摩擦及液层之间的剪切作用,而由一部分机械能转化成热能,切片在前进过程中温度不但升高而逐渐熔化成熔体。
熔化过程聚合物在温度、压力、粘度和形态等方面发生变化,由固态(玻璃态)转变为高弹态,随温度的进一步提高,出现塑性流动,成为粘流体(粘流态)。
粘流态的聚合物经螺杆的推进和螺杆出口的阻力作用,以一定的压力向熔体管道输送
2、挤压机的结构
螺杆挤压机主要由四部分组成(见图1)
高聚物熔融装置:主要由螺杆和套筒组成,其作用是将固体的物料挤压,外加热,使其熔融成均匀的熔体,并以一定的温度、压力和排出量从螺杆头部挤出,经过熔体管道送至纺丝装置进行纺丝。
按物料在螺杆中的输送、压缩和熔融等过程,一般将螺杆的的工作长度分为进料段、压缩段和计量段;根据物料在螺杆中的物理状态,将螺杆分为固体区、熔融区和熔体区。
加热和冷却系统:主要是由铝套加热器和水冷却夹套组成,其作用是通过对套筒的加热和冷却保证高聚物在工艺要求的温度范围内挤出。
传动系统:主要由变速电动机和齿轮箱组成,其作用是保证螺杆以需要的扭矩和转速稳定而均匀的工作。
电器控制系统:由温度、压力和转速控制系统构成,一方面通过熔体压力传感器控制电动机按所需要的转速运转,另一方面通过测温单元控制加热、冷却系统按设定温度工作。
二)计量泵的工作原理和结构
计量泵的作用是精确计量、连续输送成纤高聚物熔体或溶液,并于喷丝头组件结合产生预定的压力,保证纺丝流体通过滤层到达喷丝板,以精确的流量从喷丝孔喷出。
1、计量泵的结构
计量泵为外啮合齿轮泵,它由一对相等齿数的齿轮、三块泵板、两根轴和一副联轴器以及若干螺栓组成(见图2).
2、工作原理
计量泵工作时,传动轴插在联轴器的槽中,带动主动轴转动,从而使一对齿轮在中泵板的“8”字形孔中啮合运转。
当齿轮啮合运转时,在吸入孔造成负压,流体被吸入泵内并填满两个齿轮的齿谷,齿谷间的熔体在齿轮的带动下紧贴着“8”字孔的内壁回转近一周后送至出口,由于出口容积的不断变化,而将流体排出。
图1 螺杆挤压机
图2 计量泵结构及工作图
三)纺丝组件与喷丝板
纺丝组件的主要作用是将计量泵送来的熔体进行最终过滤,混合均匀后分配到每个喷丝孔中,形成均匀的细流。
喷丝板的主要作用是将高聚物熔体通过微孔转变成具有特定截面的细流,经过冷却固化而形成丝条。
喷丝板的主要参数包括喷丝孔的直径和长径比、孔的排列和喷丝孔的加工精度。
四)热拉伸辊
热拉伸辊是用于纺牵一步法联合机上的主要部件,装在纺丝机和卷绕机之间,经过热拉伸辊后再卷绕,称为全拉伸丝(注:一般需要是高速纺或超高速纺才能够达到全拉伸)。
五)卷绕机构
卷绕机构的作用是把丝条按一定规律卷绕收集,形成一定形状和容量的卷装。
任何一种卷装形式都应当满足一定的要求,主要有:
1、形状稳定:不论卷装采取何种形状,丝层怎样分布,卷装应十分稳定,经久不变。
2、容量大:卷装的容量增大,意味着降低丝条街头,减少机器停台时间和提高效率。
3、丝条分布均匀:卷装上的丝条应分布均匀,密度一致,软硬适中。
不能有重叠,有重叠后将出现密集丝带;也不能有凸边,否则会擦伤丝条,损坏成形,增加退绕时的阻力。
4、张力均匀:卷绕过程一定要保持一定的张力,才能使丝条卷绕成结实的卷装。
张力过大,卷装端面会出现起皱和胀边现象,张力过小,则卷装松软,退绕时容易产生塌边和脱圈。
5、退绕容易:卷装上的丝层必须层次分明,在卷装端不能有蛛网丝。
卷绕机构由导丝机构和卷取机构两部分组成。
卷绕机构工作时,只能完成卷绕作用的称为单纯卷绕机构。
三、仪器和药品
纺丝牵伸一体小型熔体纺丝机(非标,临淄方辰母料厂),干燥好的成纤树脂切片
四、实验步骤
1、打开冷却水,打开机器电源,打开各控制柜,将螺杆各部分加热到设定温度
2、温度升到后,打开热拉伸辊,并将热拉伸辊的转速(低速档)和温度设定到指定参数。
计量泵及各辊频率设定原则:
1)计量泵频率的的设定(以PA6为例):
0()t dtex 10000()t 10000V Q V Q ⨯⨯=
⨯=一辊速度(线密度,)R (拉伸倍数)
(对应线密度的单位)卷绕(线密度)或 注:泵供量单位为:g/min ;线密度单位为分特时,分母为10000;为特时,分母为1000;为旦时,分母为9000。
本设备的计量泵电机50HZ 对应1400r/min ,减速机速比为40:1,则计量泵1HZ 对应1400/50/40=0.7r
假设V0=600r/min ,t=100dtex ,r=4,则
6001004=24g /min 10000
Q ⨯⨯= 而本设备计量泵的规格为2.4cm3/r ,PA6的密度为1.14g/cm3,用泵供量除以物料密度,可以得到泵供体积,以泵供体积除以计量泵规格,可以得到计量泵转速,进而得到频率。
24g /min f 12.51.14g/3 2.43/0.7/HZ cm cm r r HZ
=≈⨯⨯ 2) 热辊频率设定
热辊的电机频率为50HZ 对应1500r/mim ,辊子直径为0.24m ,则
1HZ 对应30r/min,热辊转一周的长度为πD=0.75m
热辊1HZ 对应的线速度为22.608m/min
卷绕棍1HZ 对应的线速度为14.13m/mim
3、当各工艺参数均达到指定参数时,开启空压机,开启螺杆主机,并将主机调到高速档,从螺杆进料口加入物料切片;打开油盘;开启卷绕装置;待纺丝细流稳定后,将主机调回低俗档,开始纺丝。
4、当开始纺丝后,用吸枪吸丝后,依次经过油盘,导丝钩,三道热辊,最后进入卷绕装置前。
5、当吸丝稳定后,将热拉伸辊调节到高速挡,转速达到后开始卷绕。
6、纺丝结束后,将剩余的物料挤空。
关闭温控单元及各传动单元,待温度降下后关掉冷却水,并将实验室打扫干净,关闭所有电源方可离开实验室。
五、思考题
1、何为环结阻料?采用哪些措施避免?
2、何谓螺杆的压缩比?为何不能过大或过小?
3、挤压机进料段为何加冷却装置?
4、上油装置可以起到哪些作用?
5、为了获得性能均匀的纤维,需要加强哪些工艺环节的控制?如何控制?
6、何谓卷绕比?纺丝过程如何控制卷绕比?。