分布式控制系统PLC
DCS与PLC的区别

DCS与PLC的区别控制类产品名目繁多,各家叫法不一。
通常使用的控制类产品包括DCS、PLC两大类。
我们又将DCS的概念拓展到FCS。
DCS(Distributed Contorl System),集散控制系统,又称分布式控制系统。
PLC(Program Logic Control ),可编程逻辑控制器。
FCS(FieldBus Contorl Syestem),现场总线控制系统●发展到现在,DCS和PLC之间没有一个严格的界线,在大多数人看来,大的系统就是DCS,小的系统就叫PLC。
当然,这么说也不是不可以,但是还不对。
现在我们来重新建立这个观念。
●首先,DCS和PLC 之间有什么不同?1、从发展的方面来说:DCS从传统的仪表盘监控系统发展而来。
因此,DCS从先天性来说较为侧重仪表的控制,比如我们使用的YOKOGAWACS3000DCS系统甚至没有PID数量的限制(PID,比例微分积分算法,是调节阀、变频器闭环控制的标准算法,通常PID的数量决定了可以使用的调节阀数量)。
PLC从传统的继电器回路发展而来,最初的PLC甚至没有模拟量的处理能力,因此,PLC从开始就强调的是逻辑运算能力。
2、从系统的可扩展性和兼容性的方面来说:市场上控制类产品繁多,无论DCS还是PLC,均有很多厂商在生产和销售。
对于PLC系统来说,一般没有或很少有扩展的需求,因为PLC系统一般针对于设备来使用。
一般来讲,PLC也很少有兼容性的要求,比如两个或以上的系统要求资源共享,对PLC来讲也是很困难的事。
而且PLC一般都采用专用的网络结构,比如西门子的MPI总线性网络,甚至增加一台操作员站都不容易或成本很高。
DCS在发展的过程中也是各厂家自成体系,但大部分的DCS系统,比如横河YOKOGAW A、霍尼维尔、ABB等等,虽说系统内部(过程级)的通讯协议不尽相同,但操作级的网络平台不约而同的选择了以太网络,采用标准或变形的TCP/IP协议。
dcs与plc的区别

1、名称不同DCS:分散控制系统(distributedcontrol systems)。
PLC:可编程逻辑控制器(Programmable Logic Controller),只是一种控制“装置”。
2、侧重点不同DCS更侧重于过程控制领域(如化工、冶炼、制药等)主要是一些现场参数的监视和调节控制。
PLC则侧重于逻辑控制(机械加工类)。
当然现在的PLC也能很好的处理过程控制问题,但是没有DCS专业。
3、模拟量不同模拟量大于100个点以上的,一般采用DCS模拟量在100个点以内的,一般采用PLC。
4、网络形式不同DCS网络是整个系统的中枢神经,DCS系统通常采用的国际标准协议 TCP/IP。
它是安全可靠双冗余的高速通讯网络,系统的拓展性与开放性更好。
PLC因为基本上都为单个小系统工作,在与别的PLC或上位机进行通讯时,所采用的网络形式基本都是单网结构,网络协议也经常与国际标准不符。
5、出现故障不同DCS系统所有I/O模块都带有CPU,可以实现对采集及输出信号品质判断与标量变换,故障带电拔,随机更换。
而PLC模块只是简单电气转换元,没有智能芯片,故障后相应单元全部瘫痪。
扩展资料:可编程逻辑控制器是种专门为在工业环境下应用而设计的数字运算操作电子系统。
它采用一种可编程的存储器,在其内部存储执行逻辑运算、顺序控制、定时、计数和算术运算等操作的指令,通过数字式或模拟式的输入输出来控制各种类型的机械设备或生产过程。
集散控制系统是以微处理器为基础,采用控制功能分散、显示操作集中、兼顾分而自治和综合协调的设计原则的新一代仪表控制系统。
集散控制系统简称DCS,也可直译为“分散控制系统”或“分布式计算机控制系统”。
它采用控制分散、操作和管理集中的基本设计思想,采用多层分级、合作自治的结构形式。
其主要特征是它的集中管理和分散控制。
目前DCS在电力、冶金、石化等各行各业都获得了极其广泛的应用。
SCADA、DCS与PLC之间的区别
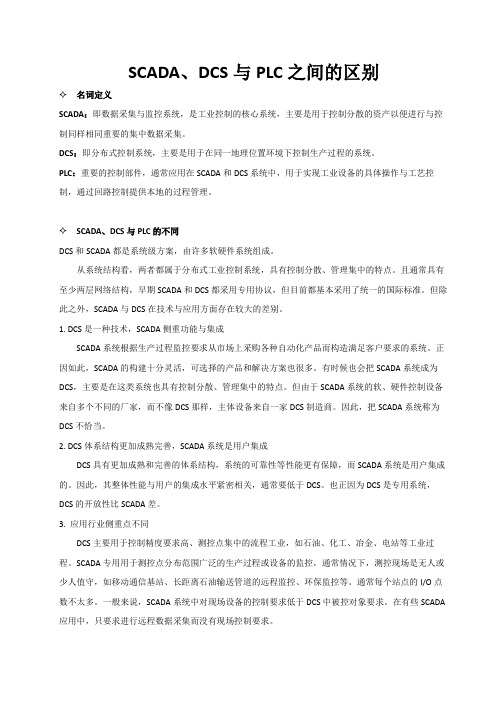
SCADA、DCS与PLC之间的区别✧名词定义SCADA:即数据采集与监控系统,是工业控制的核心系统,主要是用于控制分散的资产以便进行与控制同样相同重要的集中数据采集。
DCS:即分布式控制系统,主要是用于在同一地理位置环境下控制生产过程的系统。
PLC:重要的控制部件,通常应用在SCADA和DCS系统中,用于实现工业设备的具体操作与工艺控制,通过回路控制提供本地的过程管理。
✧SCADA、DCS与PLC的不同DCS和SCADA都是系统级方案,由许多软硬件系统组成。
从系统结构看,两者都属于分布式工业控制系统,具有控制分散、管理集中的特点。
且通常具有至少两层网络结构,早期SCADA和DCS都采用专用协议,但目前都基本采用了统一的国际标准。
但除此之外,SCADA与DCS在技术与应用方面存在较大的差别。
1. DCS是一种技术,SCADA侧重功能与集成SCADA系统根据生产过程监控要求从市场上采购各种自动化产品而构造满足客户要求的系统。
正因如此,SCADA的构建十分灵活,可选择的产品和解决方案也很多。
有时候也会把SCADA系统成为DCS,主要是在这类系统也具有控制分散、管理集中的特点。
但由于SCADA系统的软、硬件控制设备来自多个不同的厂家,而不像DCS那样,主体设备来自一家DCS制造商。
因此,把SCADA系统称为DCS不恰当。
2. DCS体系结构更加成熟完善,SCADA系统是用户集成DCS具有更加成熟和完善的体系结构,系统的可靠性等性能更有保障,而SCADA系统是用户集成的。
因此,其整体性能与用户的集成水平紧密相关,通常要低于DCS。
也正因为DCS是专用系统,DCS的开放性比SCADA差。
3. 应用行业侧重点不同DCS主要用于控制精度要求高、测控点集中的流程工业,如石油、化工、冶金、电站等工业过程。
SCADA专用用于测控点分布范围广泛的生产过程或设备的监控,通常情况下,测控现场是无人或少人值守,如移动通信基站、长距离石油输送管道的远程监控、环保监控等。
DCS和PLC区别及优缺点

plc和dcs在工业自动化控制中占有举足轻重的地位,而工业自动化控制是国家工业发展战略的核心。
PLC以及DCS在工业控制的各个环节中不断的升级、完善,已经成为现代工业生产制造中不可或缺的工具。
1、DCS和PLC的定义DCS控制系统,在国内自控行业又称之为集散控制系统。
即所谓的分布式控制系统,是相对于集中控制系统而言的一种新型计算机控制系统,它是在集中控制系统的基础上发展、演变而来的。
DCS作为一个集过程控制和过程监控为一体的计算机综合系统,在通信网络的不断带动下,DCS系统已经成为了一个综合计算机,通信、显示和控制等4C技术的完整体系。
其主要特点是分散控制、集中操作、分级管理、配置灵活以及组态方便。
现如今的DCS系统可以广泛地用于工业装置的生产控制和经营管理,在化工、电力、冶金等流程自动化领域的应用已经十分普及。
PLC,即逻辑可编程控制器,是一种数字运算操作的电子系统,专为在工业环境应用而设计的。
它采用一类可编程的存储器,用于其内部存储程序,执行逻辑运算、顺序控制、定时、计数与算术操作等面向用户的指令,并通过数字或模拟式输入/输出控制各种类型的机械或生产过程,是工业控制的核心部分。
2、DCS和PLC控制器的差别DCS和PLC控制器的主要差别是在开关量和模拟量的运算上,即使后来两者相互有些渗透,但是仍然有区别。
80年代以后,PLC除逻辑运算外,也增加了一些控制回路算法,但要完成一些复杂运算还是比较困难,PLC用梯形图编程,模拟量的运算在编程时不太直观,编程比较麻烦。
但在解算逻辑方面,表现出快速的优点。
而DCS使用功能块封装模拟运算和逻辑运算,无论是逻辑运算还是复杂模拟运算的表达形式都非常清晰,但相对PLC来说逻辑运算的表达效率较低。
3、DCS和PLC在火电厂的应用在火电厂热工自动化领域,DCS和PLC是两个完全不同而又有着千丝万缕联系的概念。
DCS和PLC都是计算机技术与工业控制技术相结合的产物,火电厂主机控制系统用的是DCS,而PLC主要应用在电厂辅助车间。
PCS FCS DCS PLC 区别
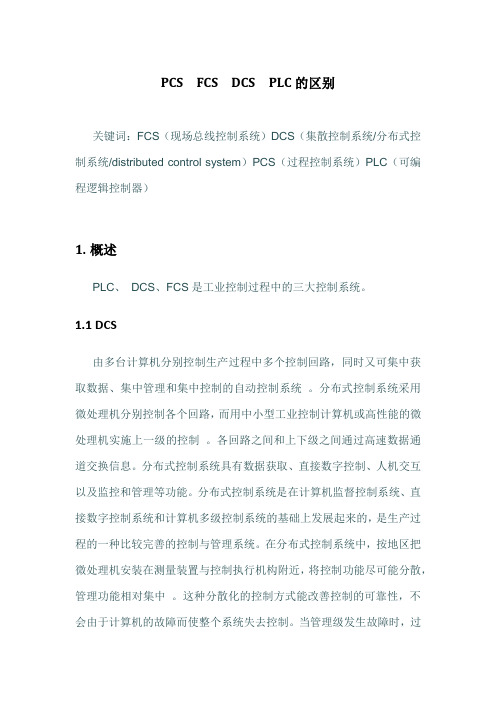
PCS FCS DCS PLC的区别关键词:FCS(现场总线控制系统)DCS(集散控制系统/分布式控制系统/distributed control system)PCS(过程控制系统)PLC(可编程逻辑控制器)1.概述PLC、DCS、FCS是工业控制过程中的三大控制系统。
1.1 DCS由多台计算机分别控制生产过程中多个控制回路,同时又可集中获取数据、集中管理和集中控制的自动控制系统。
分布式控制系统采用微处理机分别控制各个回路,而用中小型工业控制计算机或高性能的微处理机实施上一级的控制。
各回路之间和上下级之间通过高速数据通道交换信息。
分布式控制系统具有数据获取、直接数字控制、人机交互以及监控和管理等功能。
分布式控制系统是在计算机监督控制系统、直接数字控制系统和计算机多级控制系统的基础上发展起来的,是生产过程的一种比较完善的控制与管理系统。
在分布式控制系统中,按地区把微处理机安装在测量装置与控制执行机构附近,将控制功能尽可能分散,管理功能相对集中。
这种分散化的控制方式能改善控制的可靠性,不会由于计算机的故障而使整个系统失去控制。
当管理级发生故障时,过程控制级(控制回路)仍具有独立控制能力,个别控制回路发生故障时也不致影响全局。
与计算机多级控制系统相比,分布式控制系统在结构上更加灵活、布局更为合理和成本更低。
分散型控制系统(DCS)是以微处理机为基础,以危险分散控制,操作和管理集中为特性,集先进的计算机技术、通讯技术、CRT技术和控制技术即4C技术于一体的新型控制系统。
随着现代计算机和通讯网络技术的高速发展,DCS正向着多元化、网络化、开放化、集成管理方向发展,使得不同型号的DCS可以互连,进行数据交换,并可通过以太网将DCS系统和工厂管理网相连,实现实时数据上网,成为过程工业自动控制的主流。
DCS的构成方式十分灵活,可由专用的管理计算机站、操作员站、工程师站、记录站、现场控制站和数据采集站等组成,也可由通用的服务器、工业控制计算机和可编程控制器构成。
DCS、FCS、PLC的区别

DCS系统采用一个统一的开发环境,工程师站(过程管理层)用于现场控制站的组态,控制算 法的开发以及流程图画面的开发。采用一个统一数据库!而PLC用于过程控制需要不同的开发 环境,首先要对PLC(相当于DCS的现场控制站层)进行逻辑开发,建立相应的数据库,然后再通 过相应的上位机软件,例如GE FANUC 的PROFICY HMI/SCADA - IFIX 或 CIMPLICITY PLANT EDITION软件,建立与PLC相对应的数据库,然后进行流程图画面的开发。 DCS开发控制算法采用仪表技术人员熟悉的风格,仪表人员很容易将P&I图转化成DCS提 供的控制算法,而PLC采用梯形图逻辑来实现过程控制,对于仪表人员来说相对困难。尤其是 复杂回路的算法,不如DCS实现起来方便。 DCS系统通常提供完整的系统给用户,包括机柜,电源,工程师站,操作员站,用户只需 在现场简单的安装。而PLC则需要系统集成。 DCS实现顺序连锁功能相对于PLC来讲是弱势,且逻辑执行速度不如PLC, 也不如PLC编程 方便。 DCS的现场控制站层‘通常采用集中式控制,尽管支持远程分布式I/O, 但由于成本原 因, 很少采用。而PLC基于现场总线的远程分布式I/O更灵活易用,能有效的节省接线成本。 —— GE FANUC全球自动化解决方案中国区总经理贲志刚
—— 贝加莱负责APROL产品应用开发的技术经理陈志平
分析DCS与PLC的区别,最关键的是两点,一是DCS是分布式 控制,拥有全局数据库;二是PLC是顺序扫描机制,DCS是以 时间为基准的控制。我们的系统符合第一点,例如一个I/O标签 的修改,在HMI也可以同步体现。 ——罗克韦尔自动化过程市场产品经理 王广野
我们下面的比较将是针对现场级DCS与FCS的比较
现场总线控制系统
DCS与PLC的区别与联系

DCS与PLC的区别与联系DCS(分散控制系统)和PLC(可编程逻辑控制器)是在工业自动化领域中常用的控制系统。
它们在设计、功能和应用方面存在一些区别和联系。
本文将探讨DCS与PLC之间的区别与联系,旨在帮助读者更好地理解这两种控制系统。
一、DCS与PLC的定义和概述DCS是一种分层结构的控制系统,它通常由多个分布在不同位置的控制单元组成,这些控制单元可以通过网络进行通信。
每个控制单元都可以独立地执行控制任务,并与其他控制单元共享信息。
DCS广泛用于大型工业过程控制系统,例如发电厂、化工厂和石油炼厂等。
PLC是一种用于自动控制的专用计算机,它可以根据预先编写的程序来控制各种设备和过程。
PLC通常用于小型或中型控制系统,例如自动化生产线、机械设备和建筑物自动化系统等。
虽然DCS和PLC具有不同的定义和概述,但它们都能够实现工业自动化控制的目标,并在不同的应用场景中发挥重要作用。
接下来将详细讨论DCS与PLC的具体区别与联系。
二、DCS与PLC的区别1. 结构与组成DCS的结构更加复杂,由多个控制单元组成,这些单元可以相互通信和共享信息。
每个单元都具有独立的性能和功能,可以实现高度分布式和协作控制。
相比之下,PLC通常是一个单独的设备,它独立执行控制任务。
2. 网络通信DCS的控制单元通过网络进行通信,可以实现异地操作和远程监控。
这使得DCS适用于大型的、分布式的控制系统。
PLC通常通过本地连接进行通信,适用于较小规模的控制系统。
3. 灵活性和可扩展性DCS具有较高的灵活性和可扩展性,可以根据需要灵活地增加或减少控制单元,并实现系统的动态调整。
相比之下,PLC相对独立,扩展性较低。
4. 编程语言和功能DCS通常使用高级编程语言进行控制和编程,具备更为复杂的功能和逻辑。
PLC则使用简化的Ladder Diagram(梯形图)等编程语言,功能相对较简单。
这使得DCS适用于需要更复杂控制逻辑的应用,而PLC则适合于一些简单的控制任务。
ESDPLCDCS三大控制系统介绍
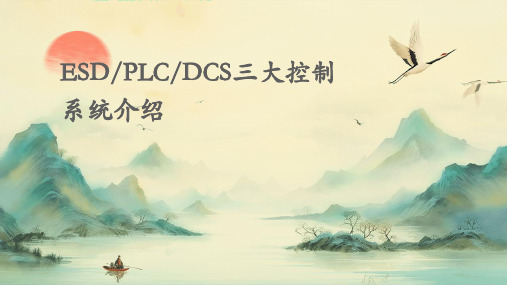
05
三大控制系统比较
性能比较
01
响应速度
ESD系统具有最快的响应速度,能够在毫秒级别内完成控制动作,而
PLC和DCS系统的响应速度通常在秒级别。
02
控制精度
DCS系统的控制精度最高,能够实现精确的模拟量控制,而ESD和PLC
系统的控制精度相对较低,主要用于开关量控制。
03
可靠性
PLC系统的可靠性最高,因为其结构简单,且对环境要求较低,而ESD
3
PLC系统适用于对设备自动化程度要求较高的场 合,如智能制造、交通、仓储等领域,能够实现 设备的自动化控制。
优缺点比较
ESD系统的优点是响应速度快,能够迅速切断危险源,避免事故发生;缺点是过于敏感,可能会因为 误动作而导致生产过程受到影响。
DCS系统的优点是控制精度高,能够实现整个生产流程的精确控制;缺点是结构复杂,维护成本较高。
ESD系统可以根据特定工艺和安全要求进行定制, 适应不同的控制需求。
ESD系统应用场景
01
02
03
化工行业
在化工生产过程中,ESD 系统用于监控压力、温度、 液位等关键参数,确保安 全生产的需要。
制药行业
制药生产线上的ESD系统 用于确保在异常情况下迅 速停车,避免对产品和环 境造成损害。
食品加工
02
它通常由传感器、逻辑控制器和 执行机构组成,用于监控生产过 程中的关键参数,并在异常情况 下触发紧急停车。
ESD系统特点
快速响应
ESD系统能够在几毫秒内对紧急情况作出反应, 迅速停车设备以防止事故扩大。
安全可靠
ESD系统通常采用冗余设计,确保在单个组件故 障时仍能可靠地执行紧急停车操作。
灵活性高
自动化控制英文缩写解释
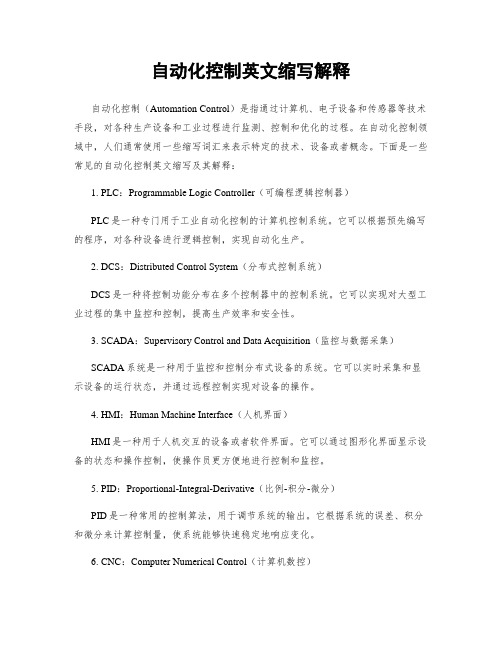
自动化控制英文缩写解释自动化控制(Automation Control)是指通过计算机、电子设备和传感器等技术手段,对各种生产设备和工业过程进行监测、控制和优化的过程。
在自动化控制领域中,人们通常使用一些缩写词汇来表示特定的技术、设备或者概念。
下面是一些常见的自动化控制英文缩写及其解释:1. PLC:Programmable Logic Controller(可编程逻辑控制器)PLC是一种专门用于工业自动化控制的计算机控制系统。
它可以根据预先编写的程序,对各种设备进行逻辑控制,实现自动化生产。
2. DCS:Distributed Control System(分布式控制系统)DCS是一种将控制功能分布在多个控制器中的控制系统。
它可以实现对大型工业过程的集中监控和控制,提高生产效率和安全性。
3. SCADA:Supervisory Control and Data Acquisition(监控与数据采集)SCADA系统是一种用于监控和控制分布式设备的系统。
它可以实时采集和显示设备的运行状态,并通过远程控制实现对设备的操作。
4. HMI:Human Machine Interface(人机界面)HMI是一种用于人机交互的设备或者软件界面。
它可以通过图形化界面显示设备的状态和操作控制,使操作员更方便地进行控制和监控。
5. PID:Proportional-Integral-Derivative(比例-积分-微分)PID是一种常用的控制算法,用于调节系统的输出。
它根据系统的误差、积分和微分来计算控制量,使系统能够快速稳定地响应变化。
6. CNC:Computer Numerical Control(计算机数控)CNC是一种通过计算机控制机床运动的技术。
它可以根据预先编写的程序,实现对机床的自动加工,提高加工精度和效率。
7. MES:Manufacturing Execution System(创造执行系统)MES是一种用于管理和控制创造过程的系统。
自动化控制英文缩写解释

自动化控制英文缩写解释自动化控制是指利用计算机技术和现代控制理论,对生产过程、设备和系统进行自动化监测、调节和控制的一种技术手段。
在自动化控制领域中,有许多常见的英文缩写,下面将对其中一些常见的英文缩写进行解释。
1. PLC (Programmable Logic Controller)PLC是可编程逻辑控制器的缩写。
它是一种专门用于工业自动化控制的计算机控制系统。
PLC能够根据预先设定的程序对输入信号进行逻辑运算和控制输出信号,从而实现对生产过程的自动化控制。
2. DCS (Distributed Control System)DCS是分布式控制系统的缩写。
它是一种用于监控和控制大型工业过程的自动化系统。
DCS系统由多个分布在不同地点的控制单元组成,这些控制单元通过网络连接,实现对整个生产过程的集中控制和监测。
3. SCADA (Supervisory Control and Data Acquisition)SCADA是监控与数据采集的缩写。
它是一种用于监控、采集和控制远程设备和系统的技术。
SCADA系统通过传感器和执行器与远程设备进行通信,将实时数据传输到监控中心,操作员可以通过监控中心对远程设备进行监测和控制。
4. HMI (Human Machine Interface)HMI是人机界面的缩写。
它是一种用于人机交互的技术,通过图形化界面和操作控制设备,使操作员能够直观地监控和控制自动化系统。
HMI通常包括触摸屏、键盘、指示灯等设备,操作员可以通过这些设备与自动化系统进行交互。
5. PID (Proportional-Integral-Derivative)PID是比例-积分-微分的缩写。
它是一种常用的控制算法,用于调节和控制自动化系统的输出。
PID控制器根据当前的偏差和变化率,计算出输出信号,从而实现对系统的精确控制。
6. CNC (Computer Numerical Control)CNC是计算机数控的缩写。
DCS系统与PLC系统的区别和联系

DCS系统与PLC系统的区别和联系DCS(分布式控制系统)和PLC(可编程逻辑控制器)是工业自动化领域中常见的两种控制系统。
它们在工业生产过程中起着至关重要的作用,并在许多方面有着相似之处,但也存在一些明显的区别。
本文将探讨DCS系统与PLC系统之间的区别和联系。
一、DCS系统的定义与特点DCS系统是指一种由多个分布式控制器组成的集中控制系统。
它将分散在不同位置的控制器通过网络进行连接,形成一个统一的整体控制系统。
DCS系统的特点如下:1. 高度分布式:DCS系统中的控制器可以分布在各个工艺单元或设备上,实现更加灵活的控制与监测。
2. 大规模处理能力:DCS系统支持处理大规模设备和复杂过程的能力,可以同时对多个设备进行控制和监控。
3. 强大的数据处理能力:DCS系统能够实时采集、处理和存储大量的工艺数据,为生产优化和故障诊断提供有力支持。
4. 开放性与可扩展性:DCS系统采用标准接口和协议,可以与其他系统进行互联互通,并可以根据实际需要进行扩展。
二、PLC系统的定义与特点PLC系统是一种特定用途的数字计算机,用于自动化控制过程中的逻辑和序列控制。
它通常通过编程来控制输出设备的状态,具有以下特点:1. 高度可编程性:PLC系统采用专门的编程语言(如Ladder Diagram)来编写控制逻辑,并可根据实际需求进行修改和调整。
2. 快速的响应时间:PLC系统具有低延迟和高实时性的特点,能够快速响应输入信号并进行逻辑判断和输出控制。
3. 简单可靠的硬件结构:PLC系统通常采用模块化的硬件结构,易于安装和维护。
其硬件组件包括中央处理器、输入/输出模块、电源模块等。
4. 适用于小规模控制:PLC系统通常适用于小规模的控制任务,如机械设备、自动化生产线等。
三、DCS系统与PLC系统的区别1. 应用领域不同:DCS系统主要应用于连续过程控制,如化工、电力、石油等;而PLC系统广泛应用于离散制造业,如机械加工、物流、制药等。
DCS与PLC

DCS与PLCDCS是分布式控制系统的英文缩写(Distributed Control System),在国内自控行业又称之为集散控制系统。
是相对于集中式控制系统而言的一种新型计算机控制系统,它是在集中式控制系统的基础上发展、演变而来的。
它是一个由过程控制级和过程监控级组成的以通信网络为纽带的多级计算机系统,综合了计算机,通信、显示和控制等4C技术,其基本思想是分散控制、集中操作、分级管理、配置灵活以及组态方便。
在特殊控制领域,如核电站控制系统,DCS 的含义被误叫做数字化控制系统(Digital control system),其实质仍为分布式操作系统。
国内DCS主要厂家有:上海新华、南京科远、杭州优稳、浙大中控、和利时、浙江威盛、自仪股份、鲁能控制、国电智深、上海华文、上海乐华、浙江中自等。
国外的有:西屋公司、艾默生、FOXBORO、ABB、西门子、霍尼韦尔、横河、罗克韦尔、山武-霍尼韦尔公司、FISHER-ROSEMOUNT公司等。
DCS的骨架——系统网络,它是DCS的基础和核心。
由于网络对于DCS整个系统的实时性、可靠性和扩充性,起着决定性的作用,因此各厂家都在这方面进行了精心的设计。
对于DCS的系统网络来说,它必须满足实时性的要求,即在确定的时间限度内完成信息的传送。
这里所说的“确定”的时间限度,是指在无论何种情况下,信息传送都能在这个时间限度内完成,而这个时间限度则是根据被控制过程的实时性要求确定的。
因此,衡量系统网络性能的指标并不是网络的速率,即通常所说的每秒比特数(bps),而是系统网络的实时性,即能在多长的时间内确保所需信息的传输完成。
系统网络还必须非常可靠,无论在任何情况下,网络通信都不能中断,因此多数厂家的DCS 均采用双总线、环形或双重星形的网络拓扑结构。
为了满足系统扩充性的要求,系统网络上可接入的最大节点数量应比实际使用的节点数量大若干倍。
这样,一方面可以随时增加新的节点,另一方面也可以使系统网络运行于较轻的通信负荷状态,以确保系统的实时性和可靠性。
dcs分散控制系统与plc可编程控制器的区别分析

dcs分散控制系统与plc可编程控制器的区别分析发布时间:2022-08-19T09:33:59.811Z 来源:《当代电力文化》2022年8期作者:周碧波[导读] dcs分散控制系统与plc可编程控制器皆为时代发展的产物,且推动了自动化水平的提升。
周碧波广西投资集团北海发电有限公司北海市 536000摘要:dcs分散控制系统与plc可编程控制器皆为时代发展的产物,且推动了自动化水平的提升。
而二者之间有着一定区别,只有明确其差异,针对性地对dcs分散控制系统与plc可编程控制器加以应用,才可将最大限度发挥其技术优势。
但就目前情况而言,一些人员仍不明晰其区别,所以本文就二者的区别进行深入探究,以供参考。
关键词:dcs分散控制系统;plc可编程控制器;区别分析引言:dcs分散控制系统与plc可编程控制器的区别分析有利于其灵活运用。
因为二者虽然皆为自动化生产的“推进者”,但因各种差异发展方向略有不同,只有做到基于此进行相关系统软件的有效应用,才可推动各行业的可持续发展。
因此,下列就此进行研究,旨在使用二者的有效应用,并推动各行各业的发展。
一、dcs分散控制系统dcs分散控制系统出现于20世纪70年代中期,由于化工领域盛行,且其有仪表制造商制造而成,所以被广泛应用于化工行业。
其实现了先进技术的有机融合,且结合实际情况进行了多级计算机系统的构建。
通过这一控制系统的有效应用,可达到连续控制、逻辑顺序控制等目的。
dcs将分散仪表控制、集中式计算机控制系统的优势、好处进行了有机结合,且基于实际情况形成了相应结构,如:分布式、分支树状结构。
以垂直结构层面为依据进行分析,可发现其可分为三个层级,一为分散过程控制级,二为集中操作监控级,三为综合信息管理级,这三个层级之间有着密切联系。
且每一层级可进行水平分解,并形成相应子模块。
二、plc可编程控制器plc可编程控制器为一体化工业控制装置,做到了自动化技术、微机技术、通信技术的有效结合。
DCS、PLC、QCS介绍-dcs与plc的区别

跳转到第一页
DCS的发展
1975 年 70年代 80年代
90年代
美国 Honeyw ell (第一台DCS系统) 分散控制系统TDC—2000
以模拟量反馈为主,开关量为次,
各大公司推出的几十种型号的系统,
采用的都是专利网络,通用性差
随着计算机的发展与网络开发使各控制厂商更多地 采用商业计算机的技术, 80年代末许多公司推出新一 代的集散系统, 其主要特征是新系统的局部网络采用 MA P 协议; 引用智能变送器与现场总线结构; 在控制 软件上引入PLC 的顺序控制与批量控制, 使DCS 也 具有PLC 的功能。
第三代DCS,网络协议引入标准化,系统具有 开放性,可移植性,互操作性,应用速度及范 围更大。
跳转到第一页
DCS与PLC的区别
硬件 软件
运算
DCS 上位机、网络、控制器、 I/O接口、现场仪表等 上位机组态软件、 控制器编程软件、 通讯接口软件、 操作及设计画面人机接口软件等 周期相对长
PLC 单一的控制器 控制器编程软件
控制;而定量测得的数据
经A控BB制Q器C控S主制要上浆由泵三的 定大量部阀件大小构,成以:控制上
浆量达到定量要求。
1、扫描架
2、AC450控制器
3、上位机
跳转到第一页
AC450过程控制器
跳转到第一页
ABB扫 描 架
水分传感器是基于红外线吸收 原理而设计,是当物体被红外 光照射时,任何物质仅吸收一 定波长的辐射光,允许其它波 长的辐射光通过 ,纸张水分 测量选用对水不吸收的1.81微 米近红外光作为参比波长和处 于外吸 光收 作峰为中测心量水的波份长1传.,9感4利微器用米两近种红 波长的单色光轮水流份交灯替地透过 纸张,取其辐射强度的比值来 测定紙张水分
浅谈分散控制系统(DCS)与可编程控制系统(PLC)在火力发电厂中的应用与区别

浅谈分散控制系统(DCS)与可编程控制系统(PLC)在火力发电厂中的应用与区别【摘要】本文主要讨论了分散控制系统(DCS)与可编程控制系统(PLC)在火力发电厂中的应用与区别。
在DCS的应用方面,它主要用于对整个电厂的生产过程进行集中监控与控制;而PLC则更适用于对局部设备的单独控制。
两者在火力发电厂中的区别主要体现在控制范围、控制方式以及系统扩展性上。
本文分析了DCS和PLC的优缺点,提出了它们结合应用的必要性。
总结了两种系统在火力发电厂中的应用优势,并展望了未来它们在控制系统领域的发展方向。
【关键词】浅谈、分散控制系统、DCS、可编程控制系统、PLC、火力发电厂、应用、区别、优缺点、结合应用、总结分析、展望未来1. 引言1.1 背景介绍火力发电厂是我国能源领域中一个重要的组成部分,其在能源生产中扮演着至关重要的角色。
随着科技的不断发展和进步,火力发电厂的控制系统也在不断更新和完善。
分散控制系统(DCS)和可编程控制系统(PLC)作为现代控制系统中的两种主要形式,在火力发电厂中得到了广泛的应用。
DCS是一种以分布式控制器为核心的控制系统,其在火力发电厂中主要用于实时监测和控制各个子系统,如锅炉系统、汽轮机系统、发电系统等。
通过集中管理和监控各个子系统,DCS可以实现火力发电厂的高效运行和优化控制。
相比之下,PLC是一种基于可编程逻辑控制器的控制系统,其主要用于对火力发电厂的各种设备和机器进行逻辑控制。
PLC可以根据预先设定的逻辑程序,实现对设备的自动控制和运行。
在火力发电厂中,DCS和PLC各有其应用优势和特点。
DCS在全局控制和监控方面具有优势,而PLC在局部设备控制和逻辑控制方面表现更为突出。
DCS和PLC的结合应用也可以进一步提高火力发电厂的运行效率和安全性。
DCS和PLC在火力发电厂中的应用是相辅相成的,它们的不同特点和优势可以为火力发电厂的控制系统提供更加全面和完善的解决方案。
随着技术的不断发展和更新,我们可以期待DCS和PLC在火力发电厂中的应用会更加普及和深入,为我国能源生产作出更大的贡献。
工业自动化控制产品分类
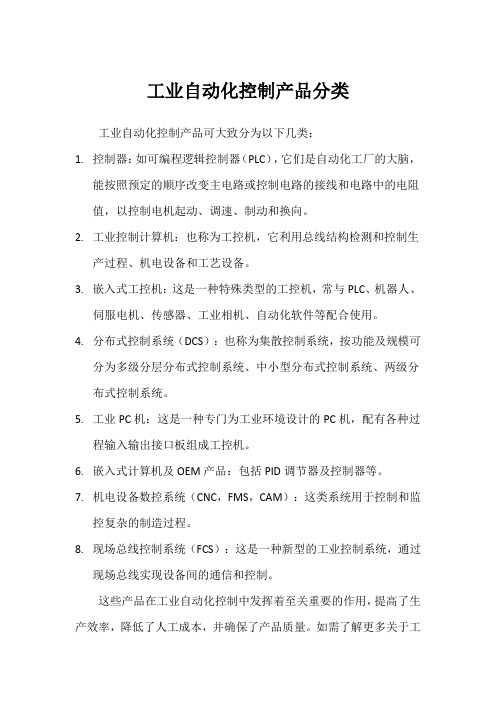
工业自动化控制产品分类
工业自动化控制产品可大致分为以下几类:
1.控制器:如可编程逻辑控制器(PLC),它们是自动化工厂的大脑,
能按照预定的顺序改变主电路或控制电路的接线和电路中的电阻值,以控制电机起动、调速、制动和换向。
2.工业控制计算机:也称为工控机,它利用总线结构检测和控制生
产过程、机电设备和工艺设备。
3.嵌入式工控机:这是一种特殊类型的工控机,常与PLC、机器人、
伺服电机、传感器、工业相机、自动化软件等配合使用。
4.分布式控制系统(DCS):也称为集散控制系统,按功能及规模可
分为多级分层分布式控制系统、中小型分布式控制系统、两级分布式控制系统。
5.工业PC机:这是一种专门为工业环境设计的PC机,配有各种过
程输入输出接口板组成工控机。
6.嵌入式计算机及OEM产品:包括PID调节器及控制器等。
7.机电设备数控系统(CNC,FMS,CAM):这类系统用于控制和监
控复杂的制造过程。
8.现场总线控制系统(FCS):这是一种新型的工业控制系统,通过
现场总线实现设备间的通信和控制。
这些产品在工业自动化控制中发挥着至关重要的作用,提高了生产效率,降低了人工成本,并确保了产品质量。
如需了解更多关于工
业自动化控制产品的信息,建议咨询自动化领域专业人士或查阅相关行业报告。
PLC控制系统的基本类型
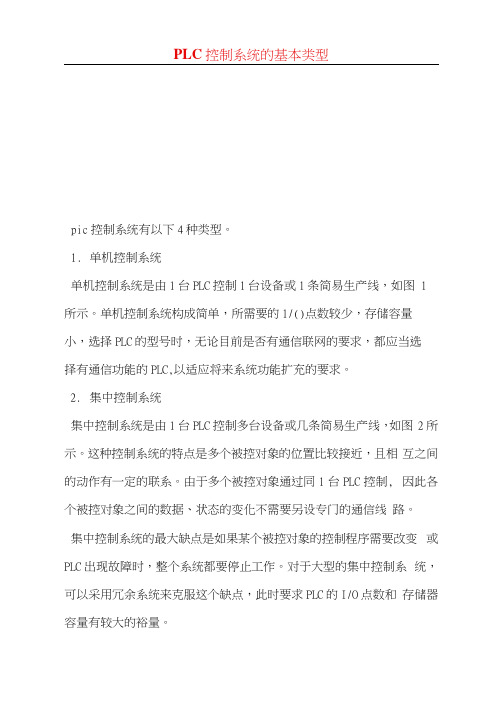
PLC控制系统的基本类型pic控制系统有以下4种类型。
1.单机控制系统单机控制系统是由1台PLC控制1台设备或1条简易生产线,如图1所示。
单机控制系统构成简单,所需要的1/()点数较少,存储容量小,选择PLC的型号时,无论目前是否有通信联网的要求,都应当选择有通信功能的PLC,以适应将来系统功能扩充的要求。
2.集中控制系统集中控制系统是由1台PLC控制多台设备或几条简易生产线,如图2所示。
这种控制系统的特点是多个被控对象的位置比较接近,且相互之间的动作有一定的联系。
由于多个被控对象通过同1台PLC控制, 因此各个被控对象之间的数据、状态的变化不需要另设专门的通信线路。
集中控制系统的最大缺点是如果某个被控对象的控制程序需要改变或PLC出现故障时,整个系统都要停止工作。
对于大型的集中控制系统,可以采用冗余系统来克服这个缺点,此时要求PLC的I/O点数和存储器容量有较大的裕量。
PLC输入/输出图1单机控制系统图72集中控制系统3.远程I/O 控制系统远程I/O 控制系统就是I/O 模块不是与PLC 放在一起,而是远距离 地放在被控对象附近。
远程1/()通道与PLC 之间通过同轴电缆连接传 递信息。
同轴电缆长度要根据系统的需要选用。
远程I/O 控制系统的 构成如图3所示。
其中使用3个远程1/()通道(A 、B 、D)和一本地1/()通道(0。
4.分布式控制系统分布式控制系统有多个被控对象,每个被控对象由1台具有通信功 能本地”①也逍图3远程I/O 控制系统的PLC控制。
分布式控制系统的特点是多个被控对象分布的区域较大,相互之间的距离较远,每台PLC可以通过数据通信总线与上位机通信,也可以通过通信线与其他的PLC交换信息。
分布式控制系统的最大好处是:某个被控对象或PLC出现故障时,不会影响其他的PLC。
PLC控制系统的发展非常快,在单机控制系统、集中控制系统、分布式控制系统之后,目前又提出了PLC的EIC综合化控制系统,即将电气控制(Electric),仪表控制(Instrumentation)和计算机(Computer)控制集成于一体,形成先进的EIC控制系统。
分布式控制系统(DCS)与可编程逻辑控制器(PLC)的区别

分布式控制系统(DCS)与可编程逻辑控制器(PLC)的区别李建民;位丽芯;李世梅;田金满;赵浩钧
【期刊名称】《现代工业经济和信息化》
【年(卷),期】2024(14)3
【摘要】在工业自动化发展、实施、应用过程中PLC和DCS必不可少.从PLC和DCS基础功能上来看,两者之间并没有形成严格意义上的区别.为了更加明确两者之间的区别,详细分析DCS和PLC两者之间在应用层面的区别,以便更好、更准确地选型应用.
【总页数】3页(P137-138)
【作者】李建民;位丽芯;李世梅;田金满;赵浩钧
【作者单位】山东戴瑞克新材料有限公司
【正文语种】中文
【中图分类】TP273.5
【相关文献】
1.基于可编程逻辑控制器和分布式控制系统的医用电子直线加速器控制系统设计
2.分散控制系统(DCS)与可编程控制器(PLC)的主要区别
3.PLC可编程逻辑控制器在矿山机电控制系统中的应用研究
4.可编程控制器PLC及分布式控制系统简介
5.基于可编程逻辑控制器(PLC)的专用组合机床电气控制系统
因版权原因,仅展示原文概要,查看原文内容请购买。
- 1、下载文档前请自行甄别文档内容的完整性,平台不提供额外的编辑、内容补充、找答案等附加服务。
- 2、"仅部分预览"的文档,不可在线预览部分如存在完整性等问题,可反馈申请退款(可完整预览的文档不适用该条件!)。
- 3、如文档侵犯您的权益,请联系客服反馈,我们会尽快为您处理(人工客服工作时间:9:00-18:30)。
宋宇
第三章 DCS控制算法
工业生产中大量应用顺序控制,均已可编 程控制器PLC作为核心。
顺序控制:按照一定的逻辑关系,对各生 产阶段进行信息处理与控制。
传送带生产线控制 印刷机械
灌装及包装机械
木材加工
纺织机械
空调控制
电梯控制
第三章 DCS控制算法
3.12 PLC简介 PLC:可编程序控制器Programmable Logic
PLC的发展趋势
1)向高速度、大存储容量方向发展 (CPU处理速度nS级;内存2M字节)
2)向多品种方向发展和提高可靠性 (超大型和超小型)
3)产品更加规范化、标准化 (硬件、软件兼容的PLC)
4)分散型、智能型、与现场总线兼容的I/0 5)加强联网和通信的能力 6)控制的开放和模块化的体系结构
第三章 DCS控制算法
以上划分不包括模拟量I/0点数,且划分界限不是固定不 变的。
第三章 DCS箱体式。整体式PLC
是将电源、CPU、I/0部件都集中装在一个机箱 内。一般小型PLC采用这种结构。 模块式PLC:将PLC各部分分成若干个单独的模 块,如 CPU模块、I/0模块、电源模块和各种功 能模块。模块式PLC由框架和各种模块组成。模 块插在插座上。一般大、中型PLC采用模块式结 构,有的小型PLC也采用这种结构。 有的PLC将整体式和模块式结合起来,称为叠装 式PLC。
第三章 DCS控制算法
3.12 PLC简介 PLC的历史
✓ 1968年,美国最大的汽车制造商通用汽车公司 (GM),为了适应汽车型号不断更新的需要, 提出了十条技术指标在社会上公开招标,制造一 种新型的工业控制装置
✓ 以后,日本、德国、法国等国相继研制了各自的 PLC。
✓ 70年代中期,PLC进入了实用化阶段。
第三章 DCS控制算法
PLC的分类
(1)按 I/O点数分类 I/O点数小于 32为微型PLC; I/O点数在32~128为微小型PLC; I/O点数在128~256为小型PLC; I/O点九在256~1024为中型PLC; I/O点数大于1024为大型PLC; I/O点数在4000以上为超大型PLC。
第三章 DCS控制算法
3.12 PLC简介
✓ 辽宁无线电二厂引进德国西门子技术生产 PLC;
✓ 无锡电器和日本光洋合资生产的 PLC; ✓ 中美合资的厦门 A—B公司生产的PLC; ✓ 上海香岛机电公司引进技术生产的PLC; ✓ 上海OMRON公司; ✓ 西安Siemens公司等。
第三章 DCS控制算法
✓ 70年代末和 80年代初,PLC进入了成熟阶段。
第三章 DCS控制算法
3.12 PLC简介 美国PLC发展得最快: ✓ 1984年有48家,生产150多种PLC; ✓ 1987年有63家,生产243种PLC; ✓ 1996年有70余家,生产近300种PLC。 ✓ 著名厂家有A—B(Allen-Bradley)艾伦一布拉德利公
第三章 DCS控制算法
3.12 PLC简介
我国在 70年代末和 80年代初开始引进PLC。我国早期 独立研制PLC的单位有: ✓ 北京机械工业自动化研究所, ✓ 上海工业自动化仪表研究所, ✓ 大连组合机床研究所, ✓ 成都机床电器研究所, ✓ 中科院北京计算机所及自动化所, ✓ 长春一汽,上海起重电器厂,上海香岛机电公司, ✓ 上海自力电子设备厂 ✓ 等单位。 以上诸单位都没有形成规模化生产。
✓ 金钟默勒 AEG, ✓ 法国的施耐德 ✓ 瑞士的Selectron公司等。
第三章 DCS控制算法
3.12 PLC简介 1971年,日本从美国引进PLC技术,由日立公司研
制成功日本第一台PLC。 日本生产PLC的厂家有40余家: ✓ 三菱电机(MITSUBISHI) ✓ 欧姆龙(OMRON) ✓ 富士电机(Fuji Electric) ✓ 东芝(TOSHIBA), ✓ 光洋(KOYO),松下电工(MEW) ✓ 和泉(IDEC),夏普(SHARP) ✓ 安川等公司。
Controller 可编程序控制器的历史
60年代 继电接触控制系统 优点:简单 易懂 价格便宜
缺点:硬设备多 接线复杂 改变设计困难。
第三章 DCS控制算法
3.12 PLC简介 定义:
国际电工委员会( IEC)于 1982年11月和 1985年1月 对可编程序控制器作了如下的定义:“可编程序控制 器是一种数字运算操作的电子系统,专为在工业环境 下应用而设计。它采用可编程序的存储器,用来在其 内部存储执行逻辑运算、顺序控制、定时、计数和算 术运算等操作的命令,并通过数字式模拟式的输入和 输出,控制各种类型的机械或生产过程。可编程序控 制器及其有关设备,都应按易于与工业控制系统联成 一个整体,易于扩充功能的原则而设计”。
司,MODICON莫迪康公司,GE-FANUC公司,TI (Texas Instrument)德州仪器公司,WESTHOUSE Electric西屋电气公司, IPM(International Parallel Machines)国际并行机器公司等。
第三章 DCS控制算法
3.12 PLC简介 欧洲PLC的厂家有60余家: 西门子(Siemens)于1973年研制出第一台 PLC。
第三章 DCS控制算法
PLC著名品牌
根据美国 Automation Research Co.(ARC)的商 情调查,在1994年PLC市场上,最大的5家PLC制 造商是(80%):
✓ SIEMENS, ✓ Allen-Bradly,(Rockwell) ✓ AEG Schneider, ✓ 三菱电机, ✓ OMRON
4. PLC著名品牌 中国PLC市场排行榜上的世界十大厂家:
✓ 美国 A-B公司 (Allen-Bradley) ✓ 德国西门子公司(Siemens) ✓ 美国GE-Fanuc公司 ✓ 美国的莫迪康(Modicon)和法国的TE电器公司 ✓ 日本欧姆公司(OMRON) ✓ 日本三菱电机株式会社(MITSUBISHI) ✓ 日本富士电机株式会社(Fuji Electric) ✓ 日本东芝公司(TOSHIBA) ✓ 日本的光洋电子(KOYO) ✓ 日本松下电工株式会社(MEW)