冲裁件的工艺性分析
冲裁工艺与冲裁模冲裁工艺及冲裁件的工艺性

一、冲裁工艺及冲裁件的工艺性
1、概述
1)冲裁——利用装在压力机上的模具,将板料分离的冲压工 艺。 2)包括内容——冲孔、落料、修边、切口、切断等。 落料——从板料上冲下所需形状的零件或毛坯(要冲掉部分) 冲孔——从工件上冲出所需形状的孔(冲掉的部分是废料) 3)用途——可加工平板类零件;为弯曲、拉深、成形等工序 准备毛坯;在成形件上完成刨切、冲孔等。 4)模具
四、排样设计
排样:冲裁件在被冲材料上的布置方法。
在冲压生产中,零件的材料费用占制造成本 的60%以上,所以合理的排样不仅能提高冲 裁件的质量、提高模具寿命,而且时节约使 用材料降低成本的有效措施 。
冲裁工艺与冲裁模冲裁工艺及冲裁 件的工艺性
搭边:排样时零件与零件之间、零件与条料侧 边留下的工艺废料。
)配合加工法中凸、凹模刃口尺寸计算
对于形状复杂冲裁件,为保证凸、凹模 之间的合理间隙值,必须采用配 合加工方式。即首先加工凸、凹模中的一件作为基准件,然后以选定的间 隙配合加工另一件。
冲裁工艺与冲裁模冲裁工艺及冲裁 件的工艺性
冲裁工艺与冲裁模冲裁工艺及冲裁 件的工艺性
配合加工的计算公式
冲裁工艺与冲裁模冲裁工艺及冲裁 件的工艺性
冲裁工艺与冲裁模冲裁工艺及冲裁 件的工艺性
落料与冲孔:
冲裁工艺与冲裁模冲裁工艺及冲裁 件的工艺性
冲裁工艺与冲裁模冲裁工艺及冲裁 件的工艺性
模具图
冲裁工艺与冲裁模冲裁工艺及冲裁 件的工艺性
2、冲裁件的工艺性
冲裁件的工艺性: 指冲裁件在工艺上的适应性,即加工难易程度。良好的工艺性能使材
料消耗少、工序数量少、模具结构简单且使用寿命长、产品质量稳定。
冲裁时,搭边过大,会造成材料浪费,搭边太 小,则起不到搭边应有的作用,过小的搭边, 导致板料被拉进凸、凹模间隙,加剧模具的磨 损,甚至会损坏模具刃口。
第2章6-7节(冲裁工艺及冲裁模设计)
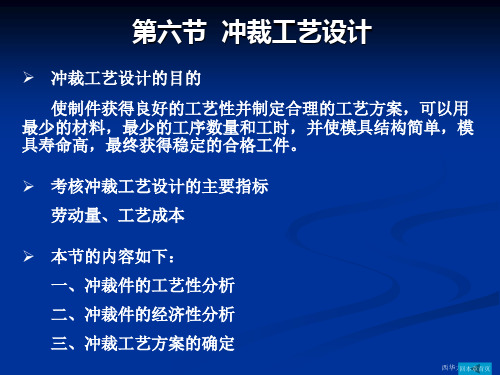
用途 薄件、平整要求高的零件、 薄件、平整要求高的零件、易分层的非金属件
西华大学 张晓洪
2、冲孔模 、
普通板坯冲孔模结构与落料模相似。 普通板坯冲孔模结构与落料模相似。 冲孔的多样性导致冲孔模有更多自己的特点。 冲孔的多样性导致冲孔模有更多自己的特点。
典型的冲孔模有: 典型的冲孔模有: (1)冲侧孔模 ) (2)单工序多凸模冲孔模 ) (3)导板式冲小孔模 )
西华大学 张晓洪
倒装复合模
冲制垫圈的复合冲裁模 适用条件 0.3mm以上低平直度要求件(刚性推件未压紧制件部分,卸 以上低平直度要求件(刚性推件未压紧制件部分, 以上低平直度要求件 料板也未压紧条料) 料板也未压紧条料) 特点 卸料板兼承料平面, 卸料板兼承料平面,冲前无法预压 凸凹模若直刃段长,则胀裂力大,须控制其最小壁厚 凸凹模若直刃段长,则胀裂力大, 条料废料部分: 条料废料部分:冲裁时有上下动作 改进 若上部改为弹性推件,则可加工 若上部改为弹性推件,则可加工0.3mm以下的冲件 以下的冲件
西华大学 张晓洪
… … …冲裁件的形状和尺寸 冲裁件的形状和尺寸
6、孔径不能太小; 、孔径不能太小; 自由凸模的最小尺寸 带护套凸模的最小尺寸 最小孔间距
西华大学 张晓洪
(二)冲裁件的尺寸精度和表面粗糙度要求
冲裁件的经济精度:一般不高于 冲裁件的经济精度:一般不高于IT11,冲孔比落料高一级 , 1、冲裁件外形与内孔尺寸公差表 、 2、冲裁件两孔孔心距公差表 、 3、冲裁件断面表面粗糙度表 、 4、冲裁件断面允许的毛刺高度表 、
第六节
冲裁工艺设计的目的
冲裁工艺设计
使制件获得良好的工艺性并制定合理的工艺方案, 使制件获得良好的工艺性并制定合理的工艺方案,可以用 最少的材料,最少的工序数量和工时,并使模具结构简单, 最少的材料,最少的工序数量和工时,并使模具结构简单,模 具寿命高,最终获得稳定的合格工件。 具寿命高,最终获得稳定的合格工件。 考核冲裁工艺设计的主要指标 劳动量、 劳动量、工艺成本 本节的内容如下: 本节的内容如下: 一、冲裁件的工艺性分析 二、冲裁件的经济性分析 三、冲裁工艺方案的确定
冲裁件结构工艺性

冲裁件结构工艺性
(1)外形与圆角半径
• 冲裁件的外形与内孔尽量避免尖角, 宜用适当的圆角,一般圆角半径R大 于或等于板厚t的一半,同种材料相同 的条件下,外形上的圆角半径值可以 比内形的半径值小10内形应优先选用圆孔。冲孔的最小尺寸与 孔的形状、材料的力学性能和板材厚度t有 关,自由凸模冲孔的直径d或方孔的边长、 长方形孔的宽b(参见图标)
(3)凸出和凹入尺寸
• 冲裁件上应避免窄长的悬臂和凹槽。一般 凸出和凹入部分的宽度B应取B≥1.5t。当板 的厚度t≤1mm时,悬臂长L与凹槽B应有 L≤5B
(3)凸出和凹入尺寸
• 冲裁件的孔与边缘的距离A、孔与孔之间 的距离B均不应过小,应有A≥2t和B≥2t
• 应尽量避免在成形件的圆弧或斜边部件 上冲孔,但球形零件底部中心孔或斜边为 先冲孔后成形着例外。
冲裁工艺性分析及间隙的选择问题的探讨

现多位化 、 多功 能化 , 并且随着计算机信息技术的引进, 模 具 2 . 2 冲裁 间隙对冲裁件 的影响 技术发展越来越依靠精度化 、 信息化 , 并 以此 为 基 础 , 吸 引 大
( 1 ) 间隙过小时, 由凹模刃 口处产生的裂纹在继续 加压 的
量 的市 场 投 资者 与 消 费者 对 于 模 具 设 计 的 技 术 来 言 , 现今 情 况下将产生二次剪切, 继而被挤入凹模 。这样 , 制件端面 中 个科研机构 、 学 校 实 验 室 正在 大 力 的应 用 C A D/ C AE / C A M 技 部 留下 撕 裂 面 , 而 两 头 出现 光 亮 带 , 在端 面 出现 挤 长 的 毛刺 。
的 模 具 具 有 多功 能 、 多位 阶 , 这些模具显然在生产过程中, 需 问隙有单面间隙和双面间隙之分。 根据冲裁件尺寸精度 、 剪切
求量依然 巨大, 并且有着非常好的发展前景。
质 量、 模具寿命和力能消耗等主要 因素 , 将金属材料冲裁间隙
从市场对模 具需求分析 ,我 国的模具技术的发展水平呈 分成三种类型: I 类( 小间隙) , l I 类( 中等间隙) , I I I 类( 大问隙) 。
2 冲裁 工 艺 性 分 析 及 间 隙 的 选 择 冲 裁 件 的工 艺 性 分 析 是 指 冲 裁 件对 冲 裁 的适 应 性 , 即冲
冲裁件的工艺性ppt
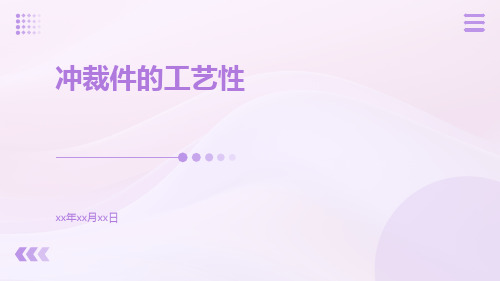
根据冲裁件的材料、厚度、尺寸和精度要求的不同,可以将 冲裁件分为多种类型,如普通冲裁件、硬质合金冲裁件、非 金属冲裁件、复杂形状冲裁件等。
冲裁件的应用范围
汽车制造
汽车车身、发动机、底盘等部件制 造。
家电制造
电视、冰箱、洗衣机、空调等家电 部件制造。
金属制品
钢桶、罐头盒、金属管件等金属制 品加工。
电子电器
电脑、手机、平板等各种电子电器 产品的零件制造。
冲裁件的设计原则
合理选择材料
优化零件结构
根据使用要求选择适当的材料,以满足使用 性能和工艺性能的要求。
考虑冲压工艺的特点,优化零件的结构设计 ,以简化模具结构,提高生产效率。
统一模数尺寸
标注清晰准确
尽量采用统一的模数尺寸,以简化模具制造 和降低生产成本。
详细描述:冲裁件的 结构工艺性主要考虑 以下几个方面
零件外形和结构是否 符合冲压模具的加工 特点,如模具的开模 距离、凹凸模间隙等 ;
零件的定位和导向是 否准确可靠,以保证 模具的精度和生产效 率;
零件的形状和结构是 否便于冲裁后的分离 和排出,如侧向抽芯 机构的设计等。
冲裁件的精度和表面质量分析
冲裁件精度高
冲裁件的精度通常较高,可达到IT10级以上,适 合于制造高精度的零件和制品。
适合大批量生产
冲裁件适合于大批量生产,生产效率高,生产成 本低,经济效益好。
材料的利用率高
冲裁件可利用材料的利用率较高,废料少,降低 了材料成本。
冲裁件工艺性的未来发展趋势
发展高精度冲裁技术
随着制造业的发展,对冲裁件的精度要求越来越高,因此,发展高精度冲裁技术是未来的 发展趋势。
冲裁件表面粗糙度是否 满足要求,如表面是否 有毛刺、划痕等缺陷。
冲裁工艺与模具设计-冲裁模设计步骤及实例
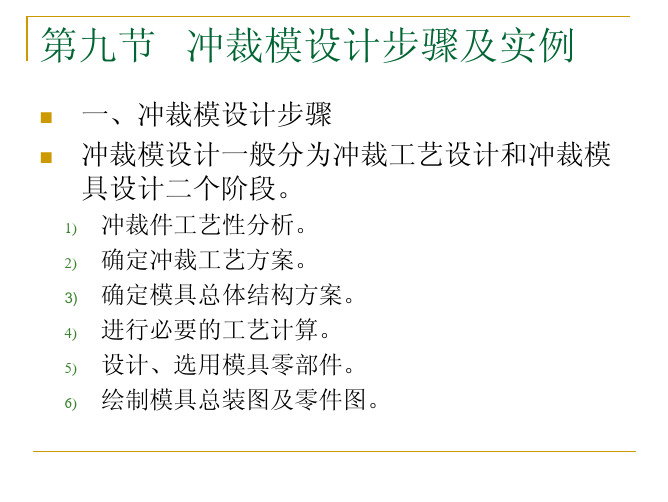
第2章 冲裁工艺及冲裁模设计
实际确定冲裁工艺方案时,通常可以先拟定出 几种不同的工艺方案,然后根据冲件的生产批 量、尺寸大小、精度高低、复杂程度、材料厚 度、模具制造、冲压设备及安全操作等方面进 行全面分析和研究,从中确定技术可行、经济 合理、满足产量和质量要求的最佳冲裁工艺方 案。
或级进冲裁; 冲件尺寸较大时,料薄时可用复合冲裁或单工序冲裁,料厚时受
压力机压力限制只宜采用单工序冲裁; 冲件上孔与孔之间或孔与边缘之间的距离过小时,受凸凹模强度
限制,不宜采用复合冲裁而宜用级进冲裁,但级进模轮廓尺寸受 压力机台面尺寸限制,所以级进冲裁宜适应尺寸不大、宽度较小 的异形冲件; 形状复杂的冲件,考虑模具的加工、装配与调整方便,采用复合 冲裁比级进冲裁较为适宜,但复合冲裁时其出件和废料清除较麻 烦,工作安全性和生产率不如级进冲裁。
《冲压工艺及模具设计》
第2(章1冲)裁模具工类艺型及冲裁模设计
模具类型主要是指单工序模、复合模、级进模三种。有些单件试 制或小批量生产的情况下,也采用简易模或组合模。
模具类型应根据生产批量、冲件形状与尺寸、冲件质量要求、材 料性质与厚度、冲压设备与制模条件、操作与安全等因素确定。
(2)操作与定位方式
《冲压工艺及模具设计》
第2章 冲裁工艺及冲裁模设计
4 进行必要的工艺计算 在冲裁工艺与模具结构方案确定以后,为了进
一步设计模具零件的具体结构,应进行以下有 关工艺与设计方面的计算:
《冲压工艺及模具设计》
第2(章1冲)裁排工样艺设及计冲与裁计模算设计 根据冲件形状特征、质量要求、模具类型与结构方 案、材料利用率等方面因素进行冲件的排样设计。设 计排样时,在保证冲件质量和模具寿命的前提下,主 要考虑材料的充分利用,所以,对形状复杂的冲件, 应多列几种不同排样方案 (特殊形状件可用纸板按冲 件比例作出样板进行实物排样),估算材料利用率, 比较各种方案的优缺点,选择出最佳排样方案。 排样方案确定以后,查出搭边值,根据模具类型和定 位方式画出排样图,计算条料宽度、进距及材料利用 率,并选择板料规格,确定裁板方式 (纵裁或横 裁),进而确定条料长度,计算一块条料或整块板料 的材料利用率。
冲压零件分析报告范文
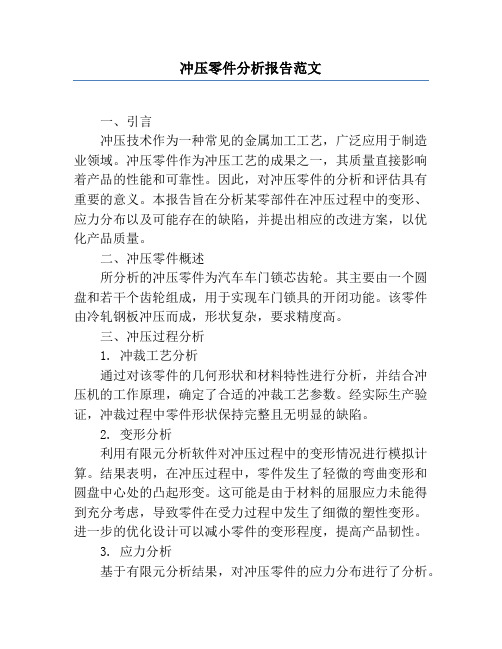
冲压零件分析报告范文一、引言冲压技术作为一种常见的金属加工工艺,广泛应用于制造业领域。
冲压零件作为冲压工艺的成果之一,其质量直接影响着产品的性能和可靠性。
因此,对冲压零件的分析和评估具有重要的意义。
本报告旨在分析某零部件在冲压过程中的变形、应力分布以及可能存在的缺陷,并提出相应的改进方案,以优化产品质量。
二、冲压零件概述所分析的冲压零件为汽车车门锁芯齿轮。
其主要由一个圆盘和若干个齿轮组成,用于实现车门锁具的开闭功能。
该零件由冷轧钢板冲压而成,形状复杂,要求精度高。
三、冲压过程分析1. 冲裁工艺分析通过对该零件的几何形状和材料特性进行分析,并结合冲压机的工作原理,确定了合适的冲裁工艺参数。
经实际生产验证,冲裁过程中零件形状保持完整且无明显的缺陷。
2. 变形分析利用有限元分析软件对冲压过程中的变形情况进行模拟计算。
结果表明,在冲压过程中,零件发生了轻微的弯曲变形和圆盘中心处的凸起形变。
这可能是由于材料的屈服应力未能得到充分考虑,导致零件在受力过程中发生了细微的塑性变形。
进一步的优化设计可以减小零件的变形程度,提高产品韧性。
3. 应力分析基于有限元分析结果,对冲压零件的应力分布进行了分析。
结果显示,零件中心以及齿轮与圆盘连接处的应力较大,且存在较大的应力集中现象。
这可能导致零件在工作过程中发生断裂或变形。
为了提高零件的抗拉强度和承载能力,建议加强连接处的设计,并考虑材料的抗拉性能。
四、缺陷分析根据冲压过程分析的结果,对可能存在的缺陷进行了评估: 1. 裂纹由于冲压过程中可能存在的应力过大和应力集中,零件表面可能出现微小的裂纹。
这些裂纹可能会扩展并最终导致零件的失效。
应在生产过程中加强品质控制,尽量减少零件表面的缺陷。
2. 翘曲受冲压过程中的变形影响,零件可能发生翘曲现象。
这会导致零件的装配困难,降低产品的可靠性。
建议采用合适的退火工艺,降低零件的内应力,减少翘曲的可能性。
五、改进方案基于对冲压过程的分析和缺陷评估,提出以下改进方案: 1. 优化工艺参数通过进一步分析和实验验证,调整冲裁工艺的参数,提高零件的精度和一致性,减少变形和缺陷的产生。
第2章-冲裁工艺

B类尺寸,随凹模磨损,尺寸↓:
C类尺寸,随凹模磨损,尺寸不变:
34
2.3 冲裁模刃口尺寸计算
3)冲孔
第 2 章
冲
冲孔件
裁
工
艺
A类尺寸,随凸模磨损,尺寸↑:
B类尺寸,随凸模磨损,尺寸↓: C类尺寸,随凸模磨损,尺寸不变:
冲孔凸模刃口轮廓
35
2.3 冲裁模刃口尺寸计算
4)总之
第
2
第
2
非圆形工件x值
圆形工件x值
材料
章
厚度
1
0.75
0.5
0.75
0.5
t/mm
工 件 公 差 Δ/mm
冲
裁
1 <0.16 0.17~0.35 ≥0.36 <0.16 ≥0.16
工
1~2 <0.20 0.21~0.41 ≥0.42 <0.20 ≥0.20
艺
2~4 <0.24 0.25~0.49 ≥0.50 <0.24 ≥0.24
1、冲裁时的力态分析
第 普通冲裁示意图
2
模具工作部分有两个基
章
本特征:
冲
凸、凹模有锋利刃口
裁
凸、凹模有间隙
工
C - 单面间隙
艺
Z - 双面间隙
冲裁板料受力图
6
2.1 冲裁工艺分析
第
2
变形区位置
章
冲
裁
工
艺
变形区的应力状态
7
2.1 冲裁工艺分析
2、冲裁变形过程
第
2
1)弹性变形阶段
第2章 冲裁工艺
第
2.1 冲裁工艺分析
冲压件工艺性分析与计算
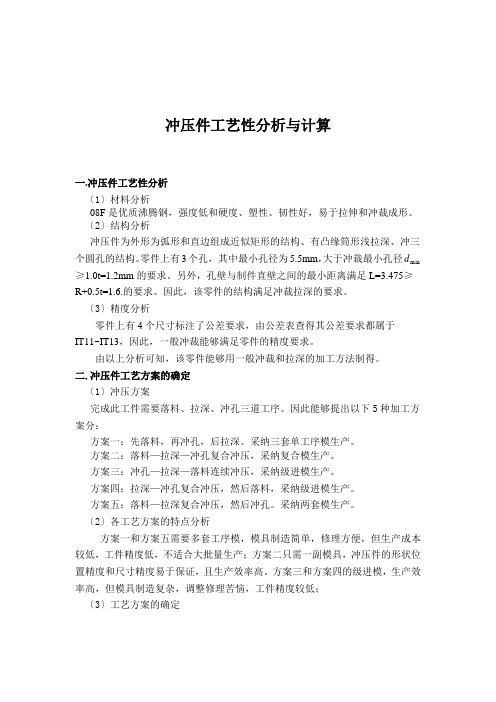
冲压件工艺性分析与计算一.冲压件工艺性分析〔1〕材料分析08F是优质沸腾钢,强度低和硬度、塑性、韧性好,易于拉伸和冲裁成形。
〔2〕结构分析冲压件为外形为弧形和直边组成近似矩形的结构、有凸缘筒形浅拉深、冲三个圆孔的结构。
零件上有3个孔,其中最小孔径为5.5mm,大于冲裁最小孔径dmin ≥1.0t=1.2mm的要求。
另外,孔壁与制件直壁之间的最小距离满足L=3.475≥R+0.5t=1.6.的要求。
因此,该零件的结构满足冲裁拉深的要求。
〔3〕精度分析零件上有4个尺寸标注了公差要求,由公差表查得其公差要求都属于IT11~IT13,因此,一般冲裁能够满足零件的精度要求。
由以上分析可知,该零件能够用一般冲裁和拉深的加工方法制得。
二.冲压件工艺方案的确定〔1〕冲压方案完成此工件需要落料、拉深、冲孔三道工序。
因此能够提出以下5种加工方案分:方案一:先落料,再冲孔,后拉深。
采纳三套单工序模生产。
方案二:落料—拉深—冲孔复合冲压,采纳复合模生产。
方案三:冲孔—拉深—落料连续冲压,采纳级进模生产。
方案四:拉深—冲孔复合冲压,然后落料,采纳级进模生产。
方案五:落料—拉深复合冲压,然后冲孔。
采纳两套模生产。
〔2〕各工艺方案的特点分析方案一和方案五需要多套工序模,模具制造简单,修理方便,但生产成本较低,工件精度低,不适合大批量生产;方案二只需一副模具,冲压件的形状位置精度和尺寸精度易于保证,且生产效率高。
方案三和方案四的级进模,生产效率高,但模具制造复杂,调整修理苦恼,工件精度较低;〔3〕工艺方案的确定比较三个方案,采纳方案五生产更为合理。
尽管模具结构较其他方案复杂,但 由于零件的几何形状简单对称,模具制造并不困难。
因此,在本设计中,将采纳落料、拉深复合模的设计方案。
三.冲压工艺运算〔1〕凸、凹模刃口尺寸的运算依照零件形状特点,刃口尺寸运算采纳分开制造法。
落料件尺寸的运算,落料差不多运算公式为A 0max A )(δ+-=X ΔD D0min max 0min A T T T )()(δδ----=-=Z X ΔD Z D D尺寸44mm ,经查得该零件凸、凹模最小间隙Z min =0.126mm ,最大间隙Z max =0.180mm ;凸模制造公差m m 02.0T =δ,凹模制造公差m m 03.0A =δ。
冲裁模设计(doc10)

冲裁模设计冲裁模设计一.冲裁件的工艺性冲裁件的工艺性是指零件对冲裁加工工艺的适应性,即加工的难易程度。
良好的冲压工艺性,是指在满足零件使用要求的前提下,能以生产率高最经济的方式加工出来。
由冲裁变形的过程分析可知,材料除剪切变形外,刃口附近的程序还存在拉伸、弯曲、横向挤压等变形,冲裁件断面具有明显的区域性特征。
所以在拟定冲裁件的工艺规程或设计冲裁件时,必须从制件结构形状、材料性能、尺寸精度及模具强度等方面分析零件的结构工艺性。
1.对结构的基本要求1) 冲裁件的形状应力求简单、规则、使排样时废料最少。
2) 制件内、外形转角处应避免设计成尖角,一般在圆角处应使R≥0.5t。
3) 冲孔制件的孔不能太小。
冲裁可冲出的最小孔径见教材。
4) 制件上孔与孔之间的距离,制件孔与边缘之距离c值不宜太小,一般要求c≥2t,并保证应大于3~4mm,连续模且对制件精度要求不高使,可适当减小但不小于板厚。
5) 制件外形应避免有长悬臂,或过窄的凹槽,悬臂和凹槽的宽度要大于料厚的1.5~2倍。
2.裁件的尺寸精度和粗糙度制件的尺寸精度以不高于IT12 级为宜。
如无特殊的要求,外形尺寸应低于IT10级,内形尺寸精度应低于IT9级。
对精度要求高于IT10级的冲裁件,应在模具结构设计方面采取措施,如提高定位精度,采用弹压卸料顶件装置,提高模具制造精度或采用精冲技术等。
制件的断面要求质量不高时,材料厚度和硬度的影响尤甚。
通常材料厚度t<1mm的制件,断面粗糙度可达Ra6.3um。
二.冲裁间隙1.冲裁间隙冲裁模的凸模横断面,一般小于凹模孔,凸、凹模刃口部分,在垂直于冲裁力方向的投影尺寸之差,称为冲裁间隙。
间隙有两种含义:一般指凸模与凹模间每侧空隙的数值,称为单边间隙;另一种指凹模与凸模间两侧空隙之和,成为双面间隙。
对于圆形刃口的凸、凹模来说,双面间隙是两者直径之差,常用C来表示。
2.间隙对冲裁的影响实践证明,间隙的大小,分布是否均匀等,对冲裁件的断面质量、尺寸精度、冲裁力和模具寿命有直接的影响。
2.2冲裁件的工艺性

硬钢,
软钢及黄铜
铝,锌.
d≧1.3t
d≧1.0t
d≧0.8t
a≧1.2t
a≧0.9t
a≧0.7t
a≧0.9t
a≧0.7t
a≧0.5t
a≧1.0t
a≧0.8t
a≧0.6t
表2.2-4采用凸模所套冲孔的最小尺寸
硬钢
软钢及黄铜
铝锌.
圆形孔d
0.5t
0.35t
2.普级冲裁为导向部分零件按IT8级精度制造.
3.高级冲裁为导向部分零件按IT7级精度制造.
表2.2-6同时冲出两孔之间中心距公差
冲模形式
材料厚度(mm)
公差(mm)
孔中距尺寸(mm)
≦1
1~2
2~4
4~6
一般冲模
<50
±0.10
±0.12
±0.15
±0.20
50~150
±0.15
±0.20
±0.25
0.30T
0.24T
0.45T
0.50T
0.35T
0.70T
0.35T
0.20T
0.50T
0.60T
0.45T
0.90T
(3)冲裁件凸出臂和凹槽的宽度不宜过小.其合理数值见下表2.2-2.
表2.2-2
材料
宽度B
硬钢
(1.5~2.0)
黄铜,软钢
(1.0~2.0)
紫铜,铝
(0.8~0.9)
(4)冲孔时,孔径不宜过小.其最小孔径与孔的形状,材料的机械性能.材料的厚度等有关.见表2.2-3,表2.2-4
10~50
0.03/0.04
0.04/0.04
冲压件的结构工艺性

B>2s
B>2s
pressing
上一页
下一页
冲孔尺寸不能太小, 3. 冲孔尺寸不能太小,最小孔径或最小边长要大于 1.5) (0.5 ~ 1.5)s 。 孔间距离或孔与边缘距离不能太小,一般a 4. 孔间距离或孔与边缘距离不能太小,一般a ≥ 2s , 但要保证a > 3 ~ 4 mm 。 但要保证a
§2 冲压件的结构工艺性
一、冲裁件的结构工艺性 形状应尽量简单, 1. 形状应尽量简单,最好由直线 与圆弧组成。应避免过长的悬臂和 与圆弧组成。 窄槽,它们的宽度b应大于料厚s 窄槽,它们的宽度b应大于料厚s 的两倍。 的两倍。 外转角处应用圆弧连接, 2. 内、外转角处应用圆弧连接,圆 角半径应大于料厚的一半。 角半径应大于料厚的一半。(参见表 3-6)
第 4 页
pressing
上一页
下一页Biblioteka 结 束aaa
a
第 2 页
pressing
上一页
下一页
二、弯曲件的结构工艺性 1. 弯曲半径不能小于材料允许的最小弯曲半径。 弯曲半径不能小于材料允许的最小弯曲半径。
弯曲边过短不易成形,故应使弯曲边的平直部分H 2. 弯曲边过短不易成形,故应使弯曲边的平直部分H > 2S 。 S H L R
孔的位置不能离弯曲线太近,一般S 3. 孔的位置不能离弯曲线太近,一般S < 2mm 时, 2mm时 L ≥ S; S ≥ 2mm时 , L ≥ 2S 。
第 3 页
pressing
上一页
下一页
三、拉深件的结构工艺性 形状应简单、对称,尽量避免深度大的拉深件, 1. 形状应简单、对称,尽量避免深度大的拉深件, 以减少拉深次数。 以减少拉深次数。 2. 为避免角部产生裂纹,侧壁与底面间圆角半径 为避免角部产生裂纹, 侧壁与凸缘间圆角半径r r1、侧壁与凸缘间圆角半径r2以及矩形件四壁间圆 角半径r 应尽可能大些。一般应满足: 角半径r3应尽可能大些。一般应满足: r1 ≥ S , 3S。 r2 ≥ 2S , r3 ≥ 3S。 S r1 r2 r1 r3
冲裁件的质量分析

冲裁件的质量分析
冲裁件质量及其影响因素
冲裁件质量:指断面状况、尺寸精度和形状误差。
垂直、 光洁、 毛刺小
图纸规定 的公差范 围内
外形满足图纸 要求;表面平 直,即拱弯小
冲裁工艺与模具设计
冲Байду номын сангаас件的质量分析
一、尺寸精度
1.冲裁模的制造精度: 冲模精度高,冲裁件精度高。
2. 材料性质: 软材料冲裁后回弹小,精度高。
冲裁件的质量分析
二、冲裁件断面质量及其影响因素
断面特征
圆角带a:刃口附近的材料产生弯曲和伸长变形。 光亮带b:塑性剪切变形。质量最好的区域。 断裂带c:裂纹形成及扩展。 毛刺区d: 间隙存在,裂纹产生不在刃尖,毛刺不可避免。
此外,间隙不正常、刃口不锋利,还会加大毛刺。
冲裁工艺与模具设计
冲裁件的质量分析
冲裁工艺与模具设计
冲裁区应力、变形和冲裁件正常的断面状况
a)冲孔件
b)落料件
冲裁工艺与模具设计
冲裁变形过程
三、毛刺
正常毛刺高度:表2-2 间隙过大:产生明显拉伸毛刺。 间隙过小:产生尖锐的挤出毛刺。 间隙合理且分布不均匀:产生局部毛刺。 凸、凹模磨钝后的毛刺: 凸模磨钝,则在落料件上端产生毛刺。 凹模磨钝,则在冲孔件的孔口下断产生毛刺。
冲裁工艺与冲裁模设计
冲裁工艺与模具设计
垫圈的落料与冲孔 a)落料 b)冲孔
冲裁工艺与模具设计
落 料 冲 孔 复 合 模
1-下模板 2-卸料螺钉 3-导柱 4-固定板 5-橡胶 6-导料销 7-落料凹模 8-推件块 9-固定板 10-导套 11-垫板 12、20-销钉 13-上模板 14-模柄 15-打杆
第二章冲裁工艺分析5-6
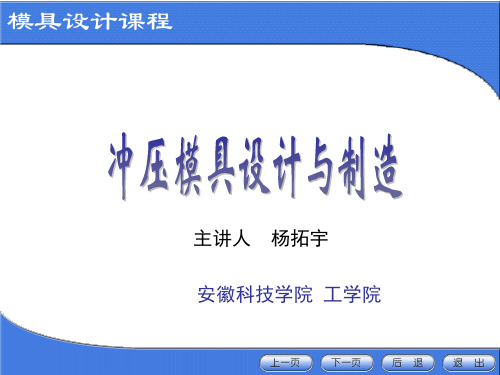
第二章 冲裁工艺与冲裁模
11导板,5凸模,在圆筒侧面冲孔。
导板式侧面冲孔模 1-摇臂2-定位销3-上模座4-螺钉5-凸模 6-凹模7-凹模体8-支架9-底座10-螺钉 11-导板12-销钉13-压缩弹簧
第二章 冲裁工艺与冲裁模
在筒形件的侧壁进 行冲孔,工作位置水 平。 斜楔1,随压力机向 下运动,推动滑块4和 凸模5向前运动,进行 冲孔,
补充:当采用弹压卸料板时,其凸模长度按下式计算:
L = H1 + H 2 + t + A '
第二章 冲裁工艺与冲裁模
第六节 冲裁模零部件结构设计
二、凹模结构设计
1.凹模结构形式 1)整体式:图2.29a 优点:结构简单,强度好;
缺点:整体采用模具刚成本高,适用于高精度小件。 刃口损坏如不能修补,需整体更换。
倒装式复合模
第二章 冲裁工艺与冲裁模
第二章 冲裁工艺与冲裁模
第六节 冲裁模零部件结构设计
第二章 冲裁工艺与冲裁模
第六节 冲裁模零部件结构设计
冲裁模零部件的分类:
工作零件
工艺零件 冲裁模零部件 结构零件 连接与固定零件 定位零件 卸料与推件零部件 模架
第二章 冲裁工艺与冲裁模
第六节 冲裁模零部件结构设计
全长导向结构的小孔冲模
第二章 冲裁工艺与冲裁模
局 部 放 大 图
第二章 冲裁工艺与冲裁模
第二章 冲裁工艺与冲裁模
1、9-定位板 2、3、4-小凸模 5-冲击块 7-小压板 8-大压板 10-侧压块 超 短 凸 模 的 小 孔 冲 模
第二章 冲裁工艺与冲裁模
局 部 放 大 图
第二章 冲裁工艺与冲裁模
第二章 冲裁工艺与冲裁模
冲裁件的工艺性

③ 冲孔时,孔径尺寸不宜过小,否则易损坏凸模。
采用和不采用护套的最小孔径见表2.19、表2.20。
④ 冲裁件的孔间距和 孔与边沿的距离不能 太小,否则凹模强度 和冲裁件的质量都不 易保证。
其间距和边距参考图 2.21所示
一般要求
b≥2t,并不能小于
3~4mm。
带一般在Ra12.5~50μm,具体数值见表2.22。
冷冲模具设计
图2.21 孔间距和孔边距
⑤ 在拉深和弯曲件上 冲孔时,孔与工件直 壁应有一定距离,孔 应在变形区外
如图2.22所示
L>R+0.5t。
图2.22 弯曲件和拉深件上的冲孔位置
注意:
拉深件底部的孔可以在拉深前、后冲出; 凸缘上的孔只能在拉深后冲出。
⑥ 要避免工件上有细长的悬臂和狭长的槽,以 防止凸模折断。
槽宽据材料而定,见表2.21。悬臂和窄槽的长
度L最大为5B。
⑦ 如果冲裁件端部带圆弧,应取R>B/2;
如图2.23所示。
图2.23 条料端部圆弧结构工艺性
1.2 冲裁件的尺寸精度和表面粗糙度
普通冲裁件的尺寸精度一般不高于IT11级 一般情况,冲孔精度比落料精度高一级。
冲裁件的断面粗糙度主要取决于切断面的光亮
冷冲模具设计
冲裁件的工艺性
冲裁件的工艺性 就是冲裁件对冲压工艺的适应性能,即冲裁件结构形 状、尺寸大小、工件精度等在冲裁时的难易程度。
1.1 冲裁件的结构和尺寸要采用圆、矩形这些规则形状或由它们组成
② 冲裁件的内、外形转角处要避免尖角 转角处的 圆角半径见表2.18