硅胶硫化剂添加比例
硅胶的一些数据
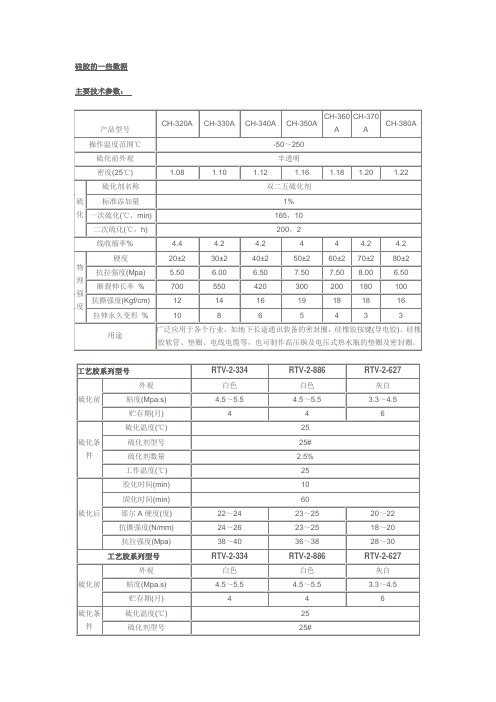
使用方法:
1、称取一定量的硅胶后,再按硅胶量的2-3%加入固化剂,并做到现用现配,在短时间内必须用完。
2.将加入固化剂的胶料充分搅拌,再将胶料放入真空箱内抽3-5分钟,排气泡后便可以制模。
3.本系列产品硫化速度与环境温度、湿度有密切关系,温度越高,湿度越大,硫化速度越快。
用户可根据天气情况,选择固化剂,调整固化剂用量,从而获得适当的硫化速度。
包装、储运及注意事项:
1.本系列产品基胶用200kg、25kg、5kg、1kg每铁桶包装,固化剂用0.75L/塑料瓶包装。
2.本系列产品应密封贮存,并放在阴凉的地方,防止雨淋,日光曝晒。
3.本系列产品贮存期为半年,如有粘度增大现象,搅拌均匀后再使用,性能不变。
4.复制型为玻璃、陶瓷、树脂、木器等产品或涂有涂料时,原型表面用表面活性剂(如洗洁精、洗发水或肥皂水)均匀涂一遍,待水分挥发后,再灌注或刷涂硅橡胶,有利于更好地脱模。
5.本系列产品为非危险品,但要注意使用过程中,尽量避免固化剂与皮肤和眼睛接触。
一旦接触,立即用适量的洗涤剂和水清洗,如溅入眼睛,用流动的水清洗至少15分钟,并咨询医生。
硅胶硫化剂知识

硅胶硫化剂知识 The latest revision on November 22, 2020学习之路一、中级双二四XC-224XC-224双二四:硫化速度快,喷霜小,气味小,形状硬朗,便于添加混炼,利于生产,硅胶制品一次硫化成型黄变小,适用做透明或彩色,黑白硅制品,无气泡.绿色环保性可达ROHS 标准,广泛用于医疗,餐具及电线,电缆,硅胶管,片,条型硅制品生产(硅制品厚薄成型无限制)。
用途:硅橡胶挤出或压廷成型热空气硫化.主要成份:A、过氧化物B、有机硅聚合物 C、有机硅分散剂D、气相法白炭黑添加比例:1.0 - 1.5 %外观:白色或浅黄色膏体包装:20 kg/桶保存:不拆密封桶的情况下可存放两年.贮存方法:贮存场所严禁明火,远离热源,防止静电、阳光直射(爆晒)及猛烈撞击;应有良好的通风,常温存放,30oC以下存贮;大量存放该产品时,严禁产品接触还原剂、铁锈、重金属离子及酸、碱性物质和易燃性材料。
粘接剂CX-801适用于未硫化硅橡胶与金属、树脂、玻璃纤维、陶瓷热硫化粘接。
一、物理性能外观:无色透明或略带浅黄色液体密度:0.84-0.88色度:30MAX沸点:大于200闪点:13二、特点1、单组分,使用方便。
2、适用不同的硫化工艺(平板硫化、真空硫化、注射硫化)3、活性强,粘接强度高,耐高温及稳定性好(通过拉力剥离测试)4、不含有毒成分(通过SGS检测)三、使用方式1、骨架处理:骨架处理的好坏直接影响产品的粘接效果,能喷砂的金属尽量喷砂。
经机械处理的金属骨架一定要先除油渍(乙醇),铜件、铝材不可用稀酸处理,喷砂后的骨架用乙醇清洗。
不能喷砂的小零件用手工砂磨。
碳钢、不锈钢可用稀硫酸或稀盐酸浸泡处理,一定要冲洗晾干。
陶瓷、环氧树脂包覆材料表面应打毛,再用乙醇清洗。
喷砂后的金属骨架不能长期存放,避免二次生锈氧化。
2、涂胶:较小的骨架可采用浸泡涂胶法,不能浸泡的大型基材可采用喷涂和刷涂(一是要细致,二是要均匀,涂胶不宜太厚,否则容易产生气泡)。
硫化剂配比对硅橡胶泡沬材料发泡效果的影响
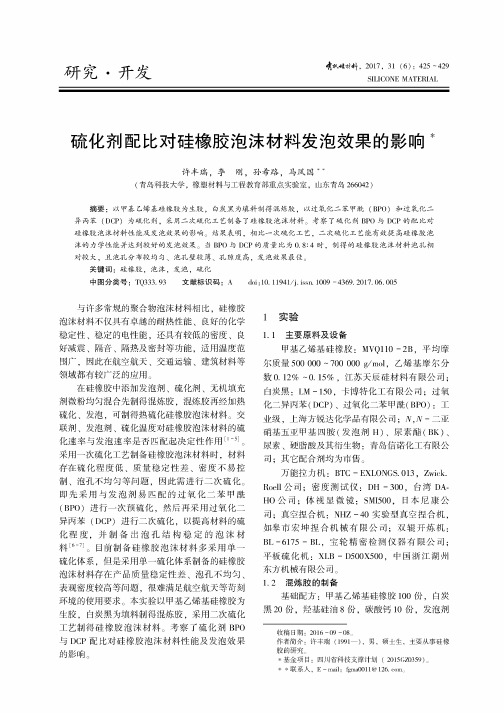
研究•开发咬机片封科,2017,31 (6):425耀429SILICONE MATERIAL 硫化剂配比对硅橡胶泡沬材料发泡效果的影响#许丰瑞,李刚,孙希路,马凤国鄢鄢(青岛科技大学,橡塑材料与工程教育部重点实验室,山东青岛266042)摘要:以曱基乙烯基硅橡肢为生肢,白炭黑为填料制得混炼肢,以过氧化二苯曱酰(B P O)和过氧化二异丙苯(D C P)为硫化剂,采用二次硫化工艺制备了硅橡肢泡沫材料。
考察了硫化剂B P O与D C P的配比对硅橡肢泡沫材料性能及发泡效果的影响。
结果表明,相比一次硫化工艺,二次硫化工艺能有效提高硅橡肢泡沫的力学性能并达到较好的发泡效果。
当BP O与D CP的质量比为0.8:4时,制得的硅橡肢泡沫材料泡孔相对较大,且泡孔分布较均匀、泡孔壁较薄、孔隙度高,发泡效果最佳。
关键词院硅橡肢,泡沫,发泡,硫化中图分类号:TQ333.93 文献标识码: A doi 院 10.11941/j.issn.1009 -4369.2017.06. 005与许多常规的聚合物泡沫材料相比袁硅橡胶 泡沫材料不仅具有卓越的耐热性能、良好的化学 稳定性、稳定的电性能,还具有较低的密度、良好减震、隔音、隔热及密封等功能,适用温度范 围广,因此在航空航天、交通运输、建筑材料等 领域都有较广泛的应用。
在硅橡胶中添加发泡剂、硫化剂、无机填充 剂微粉均匀混合先制得混炼胶,混炼胶再经加热 硫化、发泡,可制得热硫化硅橡胶泡沫材料。
交 联剂、发泡剂、硫化温度对硅橡胶泡沫材料的硫 化速率与发泡速率是否匹配起决定性作用[1-5]。
采用一次硫化工艺制备硅橡胶泡沫材料时,材料 存在硫化程度低、质量稳定性差、密度不易控 制、泡孔不均匀等问题,因此需进行二次硫化。
即先采用与发泡剂易匹配的过氧化二苯甲酰(B P O)进行一次预硫化,然后再采用过氧化二 异丙苯(D C P)进行二次硫化,以提高材料的硫 化程度,并制备出泡孔结构稳定的泡沫材料咱6-7]。
硅胶硫化剂配方

硅胶硫化剂配方
硅胶硫化剂配方是指用于制造硅胶制品的化学配方,其中硫化剂是至关重要的一部分。
硅胶硫化剂配方的制定需要考虑到硅胶的性质和用途,以及硫化剂的种类和用量等因素。
硅胶是一种高分子化合物,具有优异的耐高温、耐寒、耐腐蚀、耐老化等特性,因此被广泛应用于电子、医疗、食品、化工等领域。
硅胶硫化剂配方的制定需要根据不同的用途和要求来确定硫化剂的种类和用量。
硫化剂是硅胶制品中的重要组成部分,它能够促进硅胶分子间的交联反应,使硅胶变得更加坚固和耐用。
常用的硫化剂有过氧化物、硫醇、硫酸铵等。
不同的硫化剂对硅胶的硬度、弹性、耐热性等性能有不同的影响,因此需要根据具体情况来选择合适的硫化剂。
硅胶硫化剂配方的制定还需要考虑到硫化剂的用量。
过量的硫化剂会导致硅胶变得过硬,影响其弹性和柔韧性,而过少的硫化剂则会导致硅胶的硬度和耐用性不足。
因此,需要根据硅胶的性质和用途来确定合适的硫化剂用量。
硅胶硫化剂配方的制定需要考虑到硅胶的性质和用途,以及硫化剂的种类和用量等因素。
只有制定合理的硅胶硫化剂配方,才能生产出具有优异性能的硅胶制品,满足不同领域的需求。
硅胶硫化技术要求
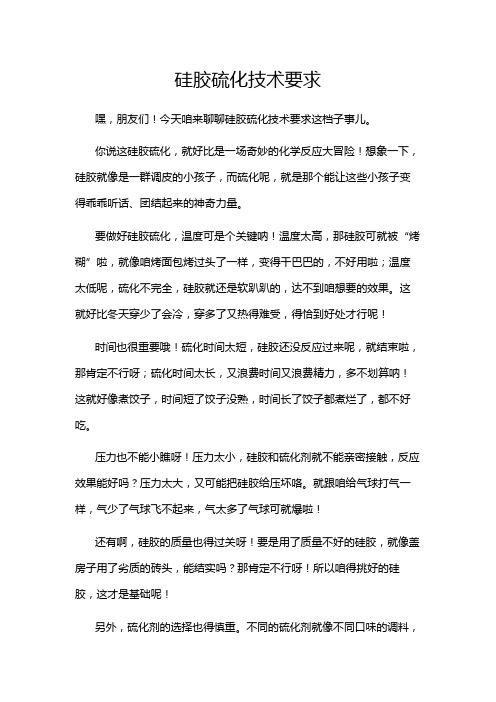
硅胶硫化技术要求嘿,朋友们!今天咱来聊聊硅胶硫化技术要求这档子事儿。
你说这硅胶硫化,就好比是一场奇妙的化学反应大冒险!想象一下,硅胶就像是一群调皮的小孩子,而硫化呢,就是那个能让这些小孩子变得乖乖听话、团结起来的神奇力量。
要做好硅胶硫化,温度可是个关键呐!温度太高,那硅胶可就被“烤糊”啦,就像咱烤面包烤过头了一样,变得干巴巴的,不好用啦;温度太低呢,硫化不完全,硅胶就还是软趴趴的,达不到咱想要的效果。
这就好比冬天穿少了会冷,穿多了又热得难受,得恰到好处才行呢!时间也很重要哦!硫化时间太短,硅胶还没反应过来呢,就结束啦,那肯定不行呀;硫化时间太长,又浪费时间又浪费精力,多不划算呐!这就好像煮饺子,时间短了饺子没熟,时间长了饺子都煮烂了,都不好吃。
压力也不能小瞧呀!压力太小,硅胶和硫化剂就不能亲密接触,反应效果能好吗?压力太大,又可能把硅胶给压坏咯。
就跟咱给气球打气一样,气少了气球飞不起来,气太多了气球可就爆啦!还有啊,硅胶的质量也得过关呀!要是用了质量不好的硅胶,就像盖房子用了劣质的砖头,能结实吗?那肯定不行呀!所以咱得挑好的硅胶,这才是基础呢!另外,硫化剂的选择也得慎重。
不同的硫化剂就像不同口味的调料,得搭配对了,才能做出美味的“硅胶大餐”。
而且添加量也要合适,多了少了都不行,得像大厨放盐一样精准。
在操作过程中,可得仔细认真,不能马虎。
就像走钢丝一样,得小心翼翼的,稍有不慎,可能就前功尽弃啦!咱得把每一个环节都当成宝贝一样对待,这样才能做出高质量的硅胶制品。
总之呢,硅胶硫化技术要求可不少,每一个环节都得用心去对待。
这可不是闹着玩的事儿,咱得认真,认真,再认真!只有这样,才能让硅胶在硫化的魔法下变得棒棒的,为我们的生活带来便利和美好呀!大家说是不是这个理儿?。
硅橡胶配方以及硫化工艺

硅橡胶常用硫化剂②乙烯基硅橡胶硫化剂BP膏状物用量(膏状物内含硫化剂BP为50%)。
硅橡胶常用补强剂的用量和性能硅橡胶的着色剂乙烯基硅橡胶和氟硅橡胶基本配方和物理机械性能开炼机混炼双辊开炼机辊筒速比为1.2~1.4:为宜,快辊在后,较高的速比导致较快的混炼,低速比则可使胶片光滑。
辊筒必须通有冷却水,混炼温度宜在40℃以下,以防止焦烧或硫化剂的挥发损失。
混炼时开始辊距较小(1~5mm),然后逐步放大。
加料和操作顺序:生胶(包辊)—→补强填充剂—→结构控制剂—→耐热助剂—→着色剂等—→薄通5次—→下料,烘箱热处理—→返炼—→硫化剂—→薄通—→停放过夜—→返炼—→出片。
胶料也可不经烘箱热处理,在加入耐热助剂后,加入硫化剂再薄通,停放过夜返炼,然后再停放数天返炼出片使用。
混炼时间为20~40分钟(开炼机规格为φ250mm ×620mm)。
如单用沉淀白炭黑或弱补强性填充剂(二氧化钛、氧化锌等)时,胶料中可不必加入结构控制剂。
应缓慢加入填料,以防止填料和生胶所形成的球状体浮在堆积胶的顶上导致分散不均。
如果要加入大量的填料,最好是分两次或三次加入,并在其间划刀,保证良好的分散。
发现橡胶有颗粒化的趋势,可收紧辊距以改进混炼。
落到接料盘上的胶粒应当用刷子清扫并收集起来,立即返回炼胶机的辊筒上,否则所炼胶料中含有胶疙瘩而导致产品外观不良。
增量性填料应当在补强性填料加完之后加入,可采用较宽的辊距。
装胶容量(混炼胶):φ160mm×320mm炼胶机为1~2 kg;φ250mm×620mm炼胶机为 3~5kg。
硅橡胶在加入炼胶机时包慢辊(前辊),混炼时则很快包快辊(后辊),炼胶时必须能两面操作。
由于硅橡胶胶料比较软,混炼时可用普通赋子刀操作,薄通时不能象普通橡胶那样拉下薄片,而采用钢、尼龙或耐磨塑料刮刀刮下。
为便于清理和防止润滑油漏入胶内,应采用活动挡板。
气相白炭黑易飞扬,对人体有害,应采取相应的劳动保护措施。
硅橡胶的硫化剂
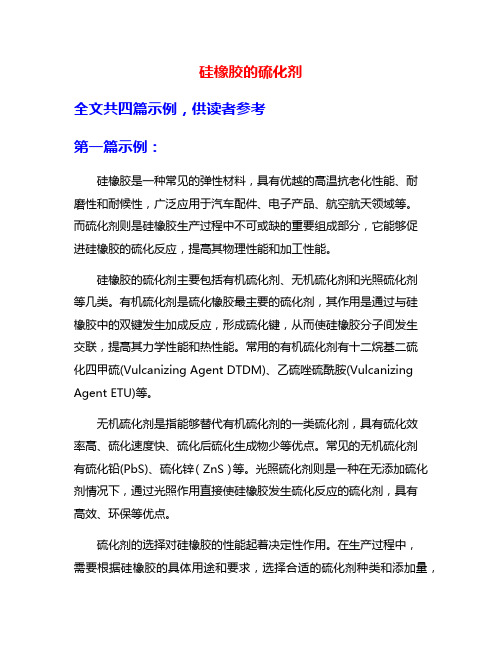
硅橡胶的硫化剂全文共四篇示例,供读者参考第一篇示例:硅橡胶是一种常见的弹性材料,具有优越的高温抗老化性能、耐磨性和耐候性,广泛应用于汽车配件、电子产品、航空航天领域等。
而硫化剂则是硅橡胶生产过程中不可或缺的重要组成部分,它能够促进硅橡胶的硫化反应,提高其物理性能和加工性能。
硅橡胶的硫化剂主要包括有机硫化剂、无机硫化剂和光照硫化剂等几类。
有机硫化剂是硫化橡胶最主要的硫化剂,其作用是通过与硅橡胶中的双键发生加成反应,形成硫化键,从而使硅橡胶分子间发生交联,提高其力学性能和热性能。
常用的有机硫化剂有十二烷基二硫化四甲硫(Vulcanizing Agent DTDM)、乙硫唑硫酰胺(Vulcanizing Agent ETU)等。
无机硫化剂是指能够替代有机硫化剂的一类硫化剂,具有硫化效率高、硫化速度快、硫化后硫化生成物少等优点。
常见的无机硫化剂有硫化铅(PbS)、硫化锌(ZnS)等。
光照硫化剂则是一种在无添加硫化剂情况下,通过光照作用直接使硅橡胶发生硫化反应的硫化剂,具有高效、环保等优点。
硫化剂的选择对硅橡胶的性能起着决定性作用。
在生产过程中,需要根据硅橡胶的具体用途和要求,选择合适的硫化剂种类和添加量,以确保硅橡胶达到预期的性能指标。
硫化剂的添加也需要在一定的温度和时间条件下进行,以保证硅橡胶充分硫化,提高其综合性能。
除了硫化剂的选择,硫化条件也是影响硅橡胶硫化效果的重要因素之一。
在硫化过程中,温度和时间是影响硫化速度和硫化程度的主要因素。
通常情况下,硫化剂的硫化温度在140℃-180℃之间,硫化时间一般在10分钟到2小时不等。
通过合理控制硫化条件,可以在保证硅橡胶硫化程度的提高生产效率和降低成本。
第二篇示例:硅橡胶是一种广泛应用于工业领域的高性能弹性材料,它具有优异的耐热性、耐候性、化学稳定性和机械性能,被广泛应用于汽车制造、电子产品、建筑材料等领域。
硅橡胶的硫化剂是制备硅橡胶的关键成分之一,它能够加速硅橡胶的硫化反应,提高其硫化速度和硬度,改善其物理性能,使硅橡胶具备更广泛的应用领域和更优异的性能表现。
硫化剂cbs标准

硫化剂cbs是一种常用的橡胶硫化剂,它具有高效、环保、使用方便等特点,被广泛应用于橡胶制品的生产中。
硫化剂cbs的标准使用方法如下:
1. 确保cbs硫化剂的品质稳定,符合生产要求。
在使用前应检查硫化剂的包装是否完好,确认生产日期等信息。
2. 根据橡胶制品的种类、性能和生产工艺,选择合适的硫化剂用量。
一般来说,cbs硫化剂的用量在0.5-2phr(硫化剂重量百分比范围内)。
3. 将cbs硫化剂与基础橡胶混合均匀,保证硫化反应的均匀性。
在混合过程中,应避免硫化剂与基础橡胶发生化学反应,导致混合不均匀。
4. 根据生产条件和设备,选择合适的硫化条件,如温度、压力和时间等。
在硫化过程中,应密切关注设备的运行情况,确保安全和产品质量。
5. 硫化完成后,应对橡胶制品进行质量检测和性能测试,确保产品符合预期要求。
如果出现质量问题或性能不符合要求的情况,应及时查明原因并采取相应的措施。
在使用硫化剂cbs时,需要注意以下几点:
1. cbs硫化剂具有一定的毒性,使用时应遵守相关安全规定,避免直接接触和吸入其粉尘。
2. 在使用过程中,应保持工作场所的整洁和卫生,及时清理废料和废弃物。
3. 不同种类的橡胶对硫化剂的适应性不同,应根据生产需要选择合适的橡胶类型。
4. 在使用过程中,应定期对设备和工艺进行检查和维护,确保设备的正常运行和产品的质量。
总之,硫化剂cbs的标准使用方法需要结合实际情况和相关规定进行操作,以确保产品的质量和安全。
在使用过程中,应注意遵守安全规定和保持工作场所的整洁卫生。
橡胶硫化剂配比表
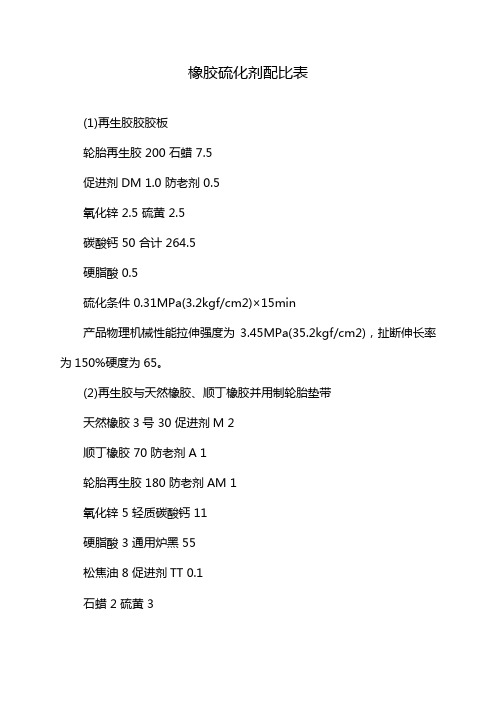
橡胶硫化剂配比表(1)再生胶胶胶板轮胎再生胶 200 石蜡 7.5促进剂DM 1.0 防老剂 0.5氧化锌 2.5 硫黄 2.5碳酸钙 50 合计 264.5硬脂酸 0.5硫化条件0.31MPa(3.2kgf/cm2)×15min产品物理机械性能拉伸强度为3.45MPa(35.2kgf/cm2),扯断伸长率为150%硬度为65。
(2)再生胶与天然橡胶、顺丁橡胶并用制轮胎垫带天然橡胶3号 30 促进剂M 2顺丁橡胶 70 防老剂A 1轮胎再生胶 180 防老剂AM 1氧化锌 5 轻质碳酸钙 11硬脂酸 3 通用炉黑 55松焦油 8 促进剂TT 0.1石蜡 2 硫黄 3合计 371.1硫化条件0.3MPa(3kgf/cm2)×10min产品物理机械性能拉伸强度为7.8MPa(80kgf/cm2),扯断伸长率为500%,硬度为55,相对密度为1.16。
(3)再生胶与天然橡胶、顺丁橡胶并用制皮鞋大底天然橡胶3号 70 促进剂DM 1.3顺丁橡胶 30 促进剂M 0.7轮胎再生胶 150 促进剂D 0.5硬脂酸 3 防老剂A 1氧化锌 5 松香 0,5高耐磨炉黑 20 石蜡 1半补强炉黑 25 液体古马隆 3陶土 20 硫黄 4轻质碳酸钙 20 合计 355硫化条件0.3MPa(3kgf/cm2)×8min物理机械性能拉伸强度为11.4MPa(116kgf/cm2),扯断伸长率为435%,硬度为68,相对密度为1.296,屈挠为43万次/E,磨耗为0.67cm3/1.64km。
配方是丁苯橡胶/顺丁橡胶/再生橡胶/低密度聚乙烯。
其中,丁苯橡胶 50份,顺丁橡胶 50份,再生橡胶 175份,低密度聚乙烯 25份,氧化锌 4份,硬脂酸 1.5份,防老剂A 2份,石蜡 1份,炭黑N330 35份,石粉 180份,古马隆树脂 4份,促进剂CZ 1.5份,促进剂TMTD 0.3份,硫磺 3份;合计:532.3份。
硅胶硫化剂知识
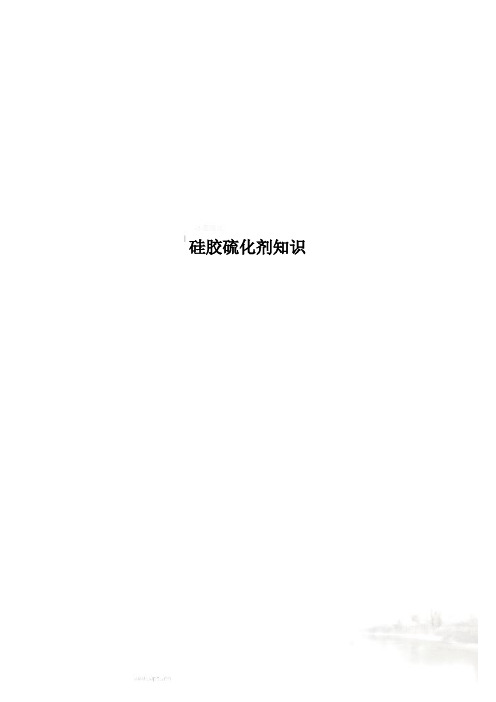
硅胶硫化剂知识学习之路一、中级双二四XC-224XC-224双二四:硫化速度快,喷霜小,气味小,形状硬朗,便于添加混炼,利于生产,硅胶制品一次硫化成型黄变小,适用做透明或彩色,黑白硅制品,无气泡.绿色环保性可达ROHS 标准,广泛用于医疗,餐具及电线,电缆,硅胶管,片,条型硅制品生产(硅制品厚薄成型无限制)。
用途:硅橡胶挤出或压廷成型热空气硫化.主要成份:A、过氧化物 B、有机硅聚合物 C、有机硅分散剂D、气相法白炭黑添加比例:1.0 - 1.5 %外观:白色或浅黄色膏体包装:20 kg/桶保存:不拆密封桶的情况下可存放两年.贮存方法:贮存场所严禁明火,远离热源,防止静电、阳光直射(爆晒)及猛烈撞击;应有良好的通风,常温存放,30oC以下存贮;大量存放该产品时,严禁产品接触还原剂、铁锈、重金属离子及酸、碱性物质和易燃性材料。
粘接剂CX-801适用于未硫化硅橡胶与金属、树脂、玻璃纤维、陶瓷热硫化粘接。
一、物理性能外观:无色透明或略带浅黄色液体密度:0.84-0.88色度:30MAX沸点:大于200闪点:13二、特点1、单组分,使用方便。
2、适用不同的硫化工艺(平板硫化、真空硫化、注射硫化)3、活性强,粘接强度高,耐高温及稳定性好(通过拉力剥离测试)4、不含有毒成分(通过SGS检测)三、使用方式1、骨架处理:骨架处理的好坏直接影响产品的粘接效果,能喷砂的金属尽量喷砂。
经机械处理的金属骨架一定要先除油渍(乙醇),铜件、铝材不可用稀酸处理,喷砂后的骨架用乙醇清洗。
不能喷砂的小零件用手工砂磨。
碳钢、不锈钢可用稀硫酸或稀盐酸浸泡处理,一定要冲洗晾干。
陶瓷、环氧树脂包覆材料表面应打毛,再用乙醇清洗。
喷砂后的金属骨架不能长期存放,避免二次生锈氧化。
2、涂胶:较小的骨架可采用浸泡涂胶法,不能浸泡的大型基材可采用喷涂和刷涂(一是要细致,二是要均匀,涂胶不宜太厚,否则容易产生气泡)。
涂胶后的骨架和基材要合理摆放,要有专用工具,避免汗手,油手触摸涂胶后的骨架。
硅胶铂金硫化操作流程

硅胶铂金硫化操作流程一、硅胶铂金硫化操作流程1. 准备工作得把硅胶原料准备好呀,就像做饭得先把食材找齐一样。
硅胶的种类可不少呢,要根据具体需求挑对硅胶哦。
铂金硫化剂也不能少,这可是让硅胶发生硫化反应的关键东西。
要确保硫化剂的质量没问题,要是硫化剂不好,那整个硫化过程可能就会出岔子。
还有设备呢,像硫化机之类的,要提前检查好设备有没有故障,能不能正常工作。
就像出门前要检查车子有没有问题一样。
2. 混合硅胶和硫化剂按照一定的比例把硅胶和硫化剂混合在一起。
这个比例很重要哦,如果比例不对,硫化出来的硅胶可能就不符合要求。
比如说,要是硫化剂放多了,硅胶可能会变得太硬;放少了呢,又可能硫化不完全。
这就像做菜放盐一样,盐放多放少都不行。
要把它们搅拌均匀呀,不能有的地方硫化剂多,有的地方少。
可以用专门的搅拌设备来搅拌,搅拌的时候要耐心一点,多搅拌一会儿,确保混合得很充分。
3. 放入硫化机把混合好的硅胶放进硫化机里。
在放的时候要小心一点,不要把硅胶洒出来,不然既浪费材料,还可能弄脏硫化机呢。
根据硅胶的量和硫化机的大小,调整好硫化机的参数。
比如说硫化的温度、压力和时间等。
不同的硅胶可能需要不同的硫化参数,这就需要我们根据经验或者产品说明书来设置了。
4. 硫化过程在硫化机工作的时候,要在旁边看着哦。
就像守护小宝贝一样,虽然硫化机一般不会出什么大问题,但是万一有个小状况,我们可以及时处理呢。
注意硫化过程中的温度变化,要是温度突然升高或者降低太多,可能就表示有问题了。
这时候要检查一下硫化机是不是哪里出故障了,或者是不是硅胶和硫化剂的混合有问题。
5. 硫化完成当硫化时间到了之后,就可以把硫化好的硅胶从硫化机里取出来了。
取的时候要小心,因为刚硫化好的硅胶可能还很热呢。
检查硫化后的硅胶的质量,看看有没有硫化不完全的地方,或者有没有其他的缺陷。
如果有问题,要分析是哪个环节出了差错,以便下次改进。
硅胶硫化剂添加比例
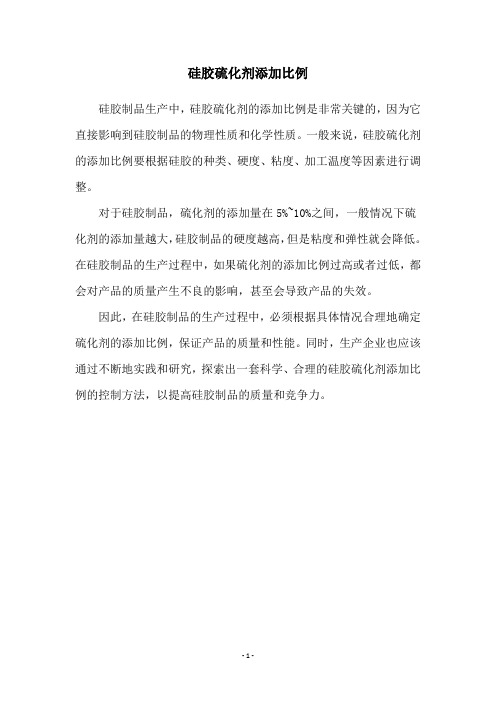
硅胶硫化剂添加比例
硅胶制品生产中,硅胶硫化剂的添加比例是非常关键的,因为它直接影响到硅胶制品的物理性质和化学性质。
一般来说,硅胶硫化剂的添加比例要根据硅胶的种类、硬度、粘度、加工温度等因素进行调整。
对于硅胶制品,硫化剂的添加量在5%~10%之间,一般情况下硫化剂的添加量越大,硅胶制品的硬度越高,但是粘度和弹性就会降低。
在硅胶制品的生产过程中,如果硫化剂的添加比例过高或者过低,都会对产品的质量产生不良的影响,甚至会导致产品的失效。
因此,在硅胶制品的生产过程中,必须根据具体情况合理地确定硫化剂的添加比例,保证产品的质量和性能。
同时,生产企业也应该通过不断地实践和研究,探索出一套科学、合理的硅胶硫化剂添加比例的控制方法,以提高硅胶制品的质量和竞争力。
- 1 -。
(最新)硅橡胶硫化剂
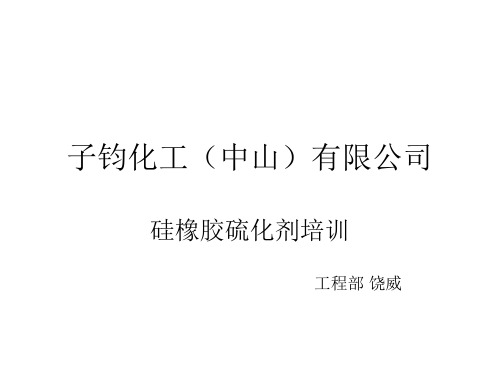
双2,4一般用在挤出压延工艺上,硫化温度一般在120度, 双2,5一般用于模压,硫化温度是170度; 另一个区别,双2,4是通用型硫化剂,而双2,5是乙烯基专用型硫化剂
• 焦烧时间(早期硫化时间):是加工安全性的度量; • 完全硫化转矩是胶料剪切模量或刚性的度量; • 硫化速度指数:是上升的硫化曲线的平均斜率;
硫化历程图
子钧化工(中山)有限公司
硅橡胶硫化剂培训
工程部 饶威
硅橡胶硫化剂
• 硫化剂
它能使硅胶分子链起交联反应,使线形分子形成立体网状 结构,可塑性降低,弹性剂强度增加的物质。除了某些热 塑性硅胶不需要硫化外,天然橡胶和各种合成橡胶都需配 入硫化剂进行硫化。硅胶经硫化后才具有宝贵的使用价值, 力学性能大大提高。
PTC-A PTC-A-25TS • 铂金交联剂
PTC-B PTC-B-25TS • 铂金抑制剂
PH 低温 HR 高温源自 过氧化物硫化剂区别双二四的优点是分解温度低,分解速度快,因此是挤出成型用混炼胶的 常用硫化剂。但由于分解温度低,所以焦烧性能不好,因此用量应尽 可能少。分解产物为2.4-二氯苯甲酸和2.4-二氯苯,有毒性,且影响 混炼胶制品的耐热性。
• 从硫化仪的硫化曲线可得到以下参数:
• 最小转矩 ML
最大转矩 MH
• 焦烧时间 ts1(分)=[ML+0.1NM]所对应的时间
• 正硫化时间 t90(分)=[ML+(MH-ML)x90%]所对应的时间
硫化剂DCBP和硫化剂DTBP的应用性能
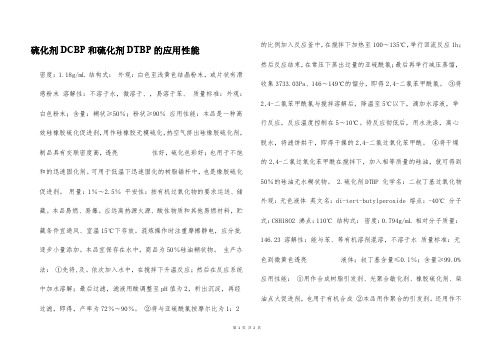
硫化剂DCBP和硫化剂DTBP的应用性能密度:1.18g/mL 结构式:外观:白色至浅黄色结晶粉末,或片状有滑感粉末溶解性:不溶于水,微溶于、,易溶于苯、质量标准:外观:白色粉末;含量:糊状≥50%;粉状≥90%应用性能:本品是一种高效硅橡胶硫化促进剂,用作硅橡胶无模硫化,热空气挤出硅橡胶硫化剂,制品具有交联密度高,透亮性好,硫化色彩好;也用于不饱和的迅速固化剂。
可用于低温下迅速固化的树脂锚杆中,也是橡胶硫化促进剂。
用量:1%~2.5%平安性:按有机过氧化物的要求运送、储藏。
本品易燃、易爆。
应远离热源火源、酸性物质和其他易燃材料,贮藏条件宜通风、室温15℃下存放。
混炼操作时注重摩擦静电,应分批逐步小量添加。
本品宜保存在水中,商品为50%硅油糊状物。
生产办法:①先将,及。
依次加入水中,在搅拌下升温反应;然后在反应系统中加水溶解;最后过滤,滤液用酸调整至pH值为2,析出沉淀,再经过滤,即得,产率为72%~90%。
②将与亚硫酰氯按摩尔比为1:2的比例加入反应釜中,在搅拌下加热至100~135℃,举行回流反应1h;然后反应结束,在常压下蒸出过量的亚硫酰氯;最后再举行减压蒸馏,收集3733.03Pa、146~149℃的馏分,即得2,4-二氯苯甲酰氯。
③将2,4-二氯苯甲酰氯与搅拌溶解后,降温至5℃以下,滴加水溶液,举行反应,反应温度控制在5~10℃。
待反应彻低后,用水洗涤,离心脱水,将滤饼烘干,即得干操的2,4-二氯过氧化苯甲酰。
④将干燥的2,4-二氯过氧化苯甲酰在搅拌下,加入相等质量的硅油,就可得到50%的硅油无水糊状物。
2.硫化剂DTBP 化学名:二叔丁基过氧化物外观:无色液体英文名:di-tert-butylperoxide 熔点:-40℃分子式:C8H18O2 沸点:110℃结构式:密度:0.794g/mL 相对分子质量:146.23 溶解性:能与苯、等有机溶剂混溶,不溶于水质量标准:无色到微黄色透亮液体;叔丁基含量≤0.l%;含量≥99.0% 应用性能:①用作合成树脂引发剂、光聚合敏化剂、橡胶硫化剂、柴油点火促进剂,也用于有机合成②本品用作聚合的引发剂。
硅橡胶及硫化剂知识
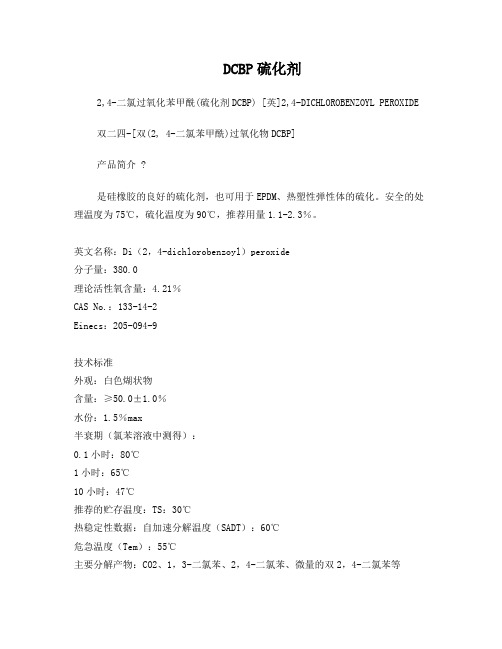
DCBP硫化剂2,4-二氯过氧化苯甲酰(硫化剂DCBP) [英]2,4-DICHLOROBENZOYL PEROXIDE 双二四-[双(2, 4-二氯苯甲酰)过氧化物DCBP]产品简介 ?是硅橡胶的良好的硫化剂,也可用于EPDM、热塑性弹性体的硫化。
安全的处理温度为75℃,硫化温度为90℃,推荐用量1.1-2.3%。
英文名称:Di(2,4-dichlorobenzoyl)peroxide分子量:380.0理论活性氧含量:4.21%CAS No.:133-14-2Einecs:205-094-9技术标准外观:白色煳状物含量:≥50.0±1.0%水份:1.5%max半衰期(氯苯溶液中测得):0.1小时:80℃1小时:65℃10小时:47℃推荐的贮存温度:TS:30℃热稳定性数据:自加速分解温度(SADT):60℃危急温度(Tem):55℃主要分解产物:CO2、1,3-二氯苯、2,4-二氯苯、微量的双2,4-二氯苯等包装:DCBP的标准包装是净重20公斤的纤维纸筒,内塑料袋包装。
也可按用户的要求的规格包装。
DCBP为D类固体有机过氧化物,货物分类:5.2,联合国编号:3106,二类危险货物包装。
安全注意事项:(1)远离火种、明火和热源。
(2)避免接触还原剂(如胺类)、酸、碱和重金属化合物(如促进剂、金属皂等)(3)请参照本产品的安全数据表(MSDS)。
贮存条件:保持包装密闭并处于良好通风状态下,最大贮存温度为30℃,避免和还原剂如胺类、酸、碱、重金属化合物(促进剂及金属皂),严禁在库房内分装及取用。
贮存稳定性:按厂家提示的条件进行保存,产品在三个月内可保证出厂技术标准。
灭火:小的火灾需用干粉或二氧化碳灭火器灭火,同时用大量水喷洒,防止再燃。
大火需在安全距离之外用大量水喷射DTBP(引发剂A)(TPA)化学名过氧化二叔丁基CAS-No 110-05-4C8H18O2=146.22?安全数据闪点………………开口18℃、闭口12℃自加速分解温度(SADT) ………………80℃报警温度(Tem) …………………………75℃联合国编号(UN-No) (3107)中国危险化学品编号(CN-No) (52026)?理化特性状态………………………………………液态比重()………………………………~0.8折光指数()…………………………~1.39熔点 (40)沸点………………………………………111℃理论活性氧含量…………………………10.94%?主要质量指标外观…………………………浅黄色透明液体含量…………………………Min.98.5%色度…………………………Max.60黑曾Fe…………………………Max.0.0003%二叔丁基过氧化物(DTBP)98%MIN化学名:过氧化二叔丁基Cas NO. 110-05-4结构式:用途: DTBP为挥发性、微黄色透明液体,是一种二烷基有机过氧化物。
- 1、下载文档前请自行甄别文档内容的完整性,平台不提供额外的编辑、内容补充、找答案等附加服务。
- 2、"仅部分预览"的文档,不可在线预览部分如存在完整性等问题,可反馈申请退款(可完整预览的文档不适用该条件!)。
- 3、如文档侵犯您的权益,请联系客服反馈,我们会尽快为您处理(人工客服工作时间:9:00-18:30)。
硅胶硫化剂添加比例
硅胶是一种耐高温、耐寒、耐热、耐腐蚀等特性的弹性体材料,被广泛应用于医药、食品、机械等领域中。
所谓硅胶硫化剂,就是用于促进硅胶的交联反应,使其形成具有优异性能的网络结构的材料。
硅胶硫化剂的添加比例非常重要,直接影响到产品的质量和使用寿命。
一般来讲,在硅胶中添加硫化剂的比例会根据不同的使用环境、需要的硬度等因素来确定。
下面,我们就以硅胶密封圈为例,介绍硅胶硫化剂添加比例的相关知识。
硅胶密封圈通常要求具有较好的抗压弹性、耐高温、耐油耐酸碱等性能。
因此,在硅胶中添加硫化剂是必须的。
一般来讲,硅胶密封圈的硫化剂添加比例应根据以下几个方面来确定:
(1) 油性
在机械行业中,密封件在接触到油后容易出现膨胀或老化等现象,因此对于这类硅胶密封圈,硫化剂的添加比例应以硬度为主,一般而言添加比例在1.5%-3%之间。
(2) 温度
硅胶密封圈在高温条件下,容易熔化或损坏,因此对于高温场合的硅胶密封圈,硫化剂的添加比例往往高于其他环境下的添加比例,一般在3%左右。
(3) 压缩变形
在机械密封中,压盖力与硬度之间存在着一定关系,因此需要控制密封圈的硬度和压盖力的平衡。
通常硅胶密封圈在硫化剂的添加比例上可参考以下标准:
a. 硬度要求较低时,硫化剂添加比例控制在0.8%-1.4%之间。
通过以上几个方面,可以初步了解硅胶密封圈硫化剂的添加比例。
硅胶的硫化剂可以分为两种,一种是加热硫化剂,另一种是常温硫化剂。
(1) 加热硫化剂
加热硫化剂在加热后才能起到催化硅胶交联反应的作用,因此需要在生产过程中预热硫化剂。
具体操作方法如下:
a. 将硫化剂放入加热箱中,一般温度要控制在50℃-80℃之间。
将硫化剂加热15-20分钟,使其温度上升到60℃左右。
b. 将硫化剂加入到硅胶中,快速搅拌均匀,然后放置一段时间,等待硅胶硫化。
常温硫化剂在加入硅胶后可以直接起到交联反应的作用,因此操作方法比较简便。
以上就是硅胶硫化剂添加比例和添加方法的相关知识。
在硅胶制品的生产过程中,合理控制硫化剂添加比例和选用合适的硫化剂种类,不仅可以提高产品的质量和性能,还能够降低生产成本,提高生产效率,为企业的可持续发展打下良好基础。