【汽车专业文献翻译】汽车后底板的冲压模具设计分析
汽车垫片冲压工艺分析及模具设计本科毕业设计论文

摘要冲压技术是一门具有极高实用价值的基础制造技术,在生产生活的各个方面都有广泛地应用。
冲压工艺与模具设计是冲压技术中的主要内容,世界上许多经济发达的国家把它列为重点发展的应用科学技术,被誉为企业效益的放大器,金属加工的帝王。
本次毕业设计是通过对汽车垫片进行工艺分析,确定工艺方案及模具结构形式,设计出适合的模具结构。
本次设计的主要内容包括落料、冲孔、弯曲工艺的分析以及模具的设计。
通过对比法找出最佳的排样、送料等方式,确定工艺参数。
模具采用落料、冲孔、弯曲的级进模,然后根据零件及查阅资料设计出模具的各零件及选用标准件,用Solidworks三维建模软件绘制出最后的模具。
关键词:冲压;模具;落料;冲孔;弯曲AbstractStamping technology is a very high practical value based manufacturing technology in the production of all aspects of life are widely used. Stamping process and die design stamping technology is the main content of many of the world economically developed countries take it as a key development in applied science and technology, known as enterprise efficiency amplifiers, metal processing emperors. The graduation project is through the automobile gaskets for process analysis, process solutions and determine the form of the mold structure, the final design of a suitable mold structure and draw nonstandard parts diagram.This design mainly involves blanking, punching, bending process analysis and design of mold related parts. The end result of the requirement to design the optimal stamping die parts. The design of the mold is the use of blanking, punching, bending progressive die, by comparing the method to find the optimal nesting, feeding, etc., then the parts and access to information design and selection of the various parts of mold standard parts , final assembly tooling and verify complete this design.Keyword:Stamping;Mold;Blanking;Punching;Bending目录第1章绪论 (1)1.1模具发展现状 (1)1.2未来冲压模具制造技术发展趋势 (1)1.3研究主要内容 (3)第2章零件的冲压工艺性分析和工艺方案 (4)2.1冲裁件工艺性 (4)2.2弯曲件的工艺性 (7)2.3工艺方案的确定 (12)第3章工艺计算和零部件设计 (16)3.1冲裁件毛坯计算 (16)3.2弯曲件毛坯计算 (18)3.3毛坯的尺寸计算 (19)3.4冲裁工序总力的计算 (19)3.5弯曲力的计算 (20)3.6压力中心的计算 (20)3.7工作零部件的计算 (21)第4章模具的装配和调试 (30)4.1装配图 (30)4.2压力机的选择与校核 (30)4.3模具的装配 (31)4.4模具的调试 (31)结论 (33)致谢 (35)I第1章绪论1.1 模具发展现状改革开放以来,随着国民经济的高速发展,市场对模具的需求量不断增长。
浅析汽车覆盖件冲压模具的结构优化

浅析汽车覆盖件冲压模具的结构优化
汽车覆盖件冲压模具的结构优化是为了满足汽车制造业对零部件轻量化、成本降低等
需求提出的一项重要挑战。
优化冲压模具的结构可以提高模具使用寿命、减少成本和时间,并提高产品质量和生产效率。
本文将从模具结构设计、制造材料、工艺参数等方面进行浅析。
首先,通过优化模具设计来提高模具的刚度和强度,达到减少振动和变形的目的。
在
模具结构设计中,应考虑到零件的形状、尺寸、厚度以及冲压工艺等因素。
针对不同的工
件类型和材料,采用不同的材料和加工方式,以达到合理的模具强度。
此外,还可以在设
计制造过程中,采用仿真分析模拟以及CAD三维设计软件,利用优化算法来优化零部件和
模具结构设计参数,减少变形和提高精度。
其次,选择合适的制造材料可以在提高模具强度和精度的同时,降低制造成本。
首先,对于高强度、高耐磨性的零部件,可以采用耐磨性好、硬度高的合金钢等材料制造;对于
中小型压件则可以采用一些具有较好加工性的低合金钢,并进行表面硬化等处理。
其次,
应根据模具所需的寿命和承载力选取合适的导向材料,并进行热处理,以达到较好的硬度
和耐磨性,防止零件损坏和模具破坏。
最后,加工工艺参数优化可以提高模具的使用寿命和加工精度。
首先,必须对模具的
加工过程进行全面的评估,包括工件形状、材料种类、模具结构和压力等因素。
此外,还
需要根据零件材料的流变特性和成形工艺要求,调整加工工艺参数,如加工速度、压力、
温度等。
根据模具结构和零件特性,采用合理的磨料和切削工艺,以减小切屑和表面粗糙度,提高零件成型的质量和几何精度。
浅析汽车覆盖件冲压模具的结构优化

浅析汽车覆盖件冲压模具的结构优化1. 引言1.1 研究背景汽车是现代社会中不可或缺的交通工具,而汽车覆盖件则是汽车外观设计中不可或缺的一部分。
汽车覆盖件冲压模具作为汽车生产过程中不可或缺的工艺装备,直接影响着汽车覆盖件的质量和生产效率。
随着汽车工业的发展,对汽车覆盖件的质量要求越来越高,传统的冲压模具在面对复杂形状的汽车覆盖件时往往存在挑战。
对汽车覆盖件冲压模具进行结构优化,以提高冲压件的精度和质量,已成为当前研究的热点之一。
通过优化冲压模具的结构,可以提高冲压件的成型精度、降低生产成本、提高生产效率。
研究汽车覆盖件冲压模具的结构优化具有重要的理论和实际意义。
在本文中,将对汽车覆盖件冲压模具的结构优化进行深入探讨,以期为汽车生产提供更高效、更精准的制造工艺。
1.2 研究意义汽车覆盖件冲压模具是汽车制造中不可或缺的重要工具,其结构的优化对于提高汽车生产效率和产品质量具有重要意义。
通过对冲压模具的结构进行优化,可以提高冲压过程中的生产效率和产品质量,减少生产成本,延长模具的使用寿命,同时也能够满足不断变化的市场需求和客户需求。
优化冲压模具的结构还有利于减少对环境的影响,降低能耗和资源消耗。
随着汽车工业的快速发展和环保意识的提高,对于汽车生产过程中的节能减排要求也越来越高,而优化冲压模具结构正是一种有效的节能减排手段。
研究汽车覆盖件冲压模具的结构优化具有重要的实践意义和研究价值。
通过不断优化冲压模具的结构,可以提高汽车制造的整体竞争力,推动汽车工业的持续发展,实现经济效益、社会效益和环境效益的有机统一。
.2. 正文2.1 汽车覆盖件冲压模具的结构优化概述汽车覆盖件冲压模具的结构优化是指通过对汽车覆盖件冲压模具的结构进行改进和优化,以提高其性能和效率。
冲压模具在汽车制造过程中起着至关重要的作用,它直接影响到汽车零部件的质量和生产效率。
因此,对汽车覆盖件冲压模具进行结构优化具有重要意义。
结构优化包括对模具的各个部分进行设计和调整,以确保模具在使用过程中能够稳定、高效地运行。
对汽车冲压模具设计制造及其维修分析

对汽车冲压模具设计制造及其维修分析伴随着社会经济的增长,国民生活水平的提升,越来越多的人购买了汽车作为出行的交通工具。
在此基础上,社会公众对于汽车本身的制造水平与售后维修的关注度逐渐升高。
鉴于此,本文对汽车冲压模具设计制造及其维修进行分析,通过阐述制造及维修内容着手,提出了几点维修制造的建议。
此次研究的主要目的是为了更好的提升现今汽车冲压模具设计制造及其维修工作质量。
标签:汽车制造;冲压模具;模具制造;模具设计前言汽车行业发展愈加迅速的当前阶段,我国汽车模具行业的制造技术方面也相继取得了诸多突破,此时的市场竞争更加炽热化起来。
在多样化的汽车模具制造技术种类中,计算机辅助技术、特种冲压成型等技术在汽车模具制造领域中的应用频率较高,其中特种冲压成型技术的应用最为广泛。
基于此,针对汽车冲压模具设计制造及其维修分析这一话题进行深入的研究分析相当有必要。
1 汽车冲压模具简介冲压模具制造是现代汽车生产行业中极其重要的一种模具加工方式。
运用该种模具制造方法生产出来的车身零件,具备自重轻、高强度、硬度高、在一定程度上节省生产成本的优点。
实际的汽车零件生产制造过程中,该种加工方式非常符合时代的发展,能够适应现代生产批量化以及机械自动化的生产方式[1]。
相对于其他汽车零件加工方式的运用,冲压模具加工方式的使用拥有能够提升成产效率的优势,此种优势是其他汽车模具制造技术所不具备的。
经过多年的摸索研发,我国当前在汽车冲压模具技术的研发方向上,逐渐倾向于模具的覆盖与多功能精冲的研发目标上面。
在信息传播迅速、网络智能化的时代背景下,将汽车模具的研发工作紧贴时代的发展,实现生产与销售一体化的发展模式,记忆一定要在详细的生产应用方法更新,积极的集成化计算机处理技术、模具数字化制造技术、模具系统化等方式,最终达到提升整个汽车制造行业生产水平的目标。
2 汽车冲压模具的设计与制造汽车制造中,最为重要的因素就是汽车产品的质量。
据相关调查研究表明,目前汽车冲压模具的着呢广场使用寿命普遍处于万-万次范围内。
汽车冲压模具的技术分析
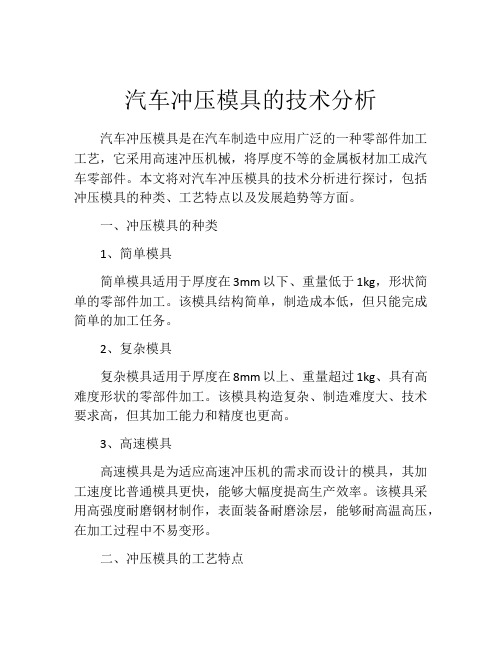
汽车冲压模具的技术分析汽车冲压模具是在汽车制造中应用广泛的一种零部件加工工艺,它采用高速冲压机械,将厚度不等的金属板材加工成汽车零部件。
本文将对汽车冲压模具的技术分析进行探讨,包括冲压模具的种类、工艺特点以及发展趋势等方面。
一、冲压模具的种类1、简单模具简单模具适用于厚度在3mm以下、重量低于1kg,形状简单的零部件加工。
该模具结构简单,制造成本低,但只能完成简单的加工任务。
2、复杂模具复杂模具适用于厚度在8mm以上、重量超过1kg、具有高难度形状的零部件加工。
该模具构造复杂、制造难度大、技术要求高,但其加工能力和精度也更高。
3、高速模具高速模具是为适应高速冲压机的需求而设计的模具,其加工速度比普通模具更快,能够大幅度提高生产效率。
该模具采用高强度耐磨钢材制作,表面装备耐磨涂层,能够耐高温高压,在加工过程中不易变形。
二、冲压模具的工艺特点1、高精度汽车零部件通常要求高精度,要求冲压模具能够准确地切割和成型材料。
因此,模具的设计和制造需要考虑工艺流程、材料特性和产品质量要求等因素。
目前,采用CAD/CAM设计和制造技术的冲压模具的精度能够达到微米级别。
2、高效率高效率是汽车冲压模具的又一重要特征。
随着汽车工业的发展,节约时间成了工业生产的一个绝对要素,冲压模具须有着一定的加工速度和生产率。
为了提高加工效率和生产率,采用高速冲压机和高速钢材制造模具是目前常用的方法。
3、高坚固性冲压模具的坚固性和刚度是关系到加工质量和寿命的重要组成部分。
汽车模具在工作过程中所承受的高压和高速冲击力是巨大的,因此要求模具所使用的钢材具有足够的抗压性和耐磨性。
4、低成本冲压模具的制造成本直接关系到企业的生存和竞争力。
因此,为了降低制造成本,应尽量采用先进的CAD/CAM技术,大幅度减少模具的设计和制造周期,应用先进的模具制造技术,提高模具加工的收益率。
三、冲压模具的发展趋势1、高速为了应对市场竞争,汽车工业需要提高生产效率和质量,而高速化是势必趋势。
冲压模具设计毕业外文翻译 中英文翻译 外文文献翻译

冲压模具设计毕业外文翻译中英文翻译外文文献翻译毕业设计(论文)外文资料翻译系部:专业:姓名:学号:外文出处: The Pofessional English of DesignManufacture for Dies & Moulds附件: 1.外文资料翻译译文,2.外文原文。
指导教师评语:签名:年月日附件1:外文资料翻译译文冲压模具设计对于汽车行业与电子行业,各种各样的板料零件都是有各种不同的成型工艺所生产出来的,这些均可以列入一般种类“板料成形”的范畴。
板料成形(也称为冲压或压力成形)经常在厂区面积非常大的公司中进行。
如果自己没有去这些大公司访问,没有站在巨大的机器旁,没有感受到地面的震颤,没有看巨大型的机器人的手臂吧零件从一个机器移动到另一个机器,那么厂区的范围与价值真是难以想象的。
当然,一盘录像带或一部电视专题片不能反映出汽车冲压流水线的宏大规模。
站在这样的流水线旁观看的另一个因素是观看大量的汽车板类零件被进行不同类型的板料成形加工。
落料是简单的剪切完成的,然后进行不同类型的加工,诸如:弯曲、拉深、拉延、切断、剪切等,每一种情况均要求特殊的、专门的模具。
而且还有大量后续的加工工艺,在每一种情况下,均可以通过诸如拉深、拉延与弯曲等工艺不同的成形方法得到所希望的得到的形状。
根据板料平面的各种各样的受应力状态的小板单元体所可以考虑到的变形情形描述三种成形,原理图1描述的是一个简单的从圆坯料拉深成一个圆柱水杯的成形过程。
图1 板料成形一个简单的水杯拉深是从凸缘型坯料考虑的,即通过模具上冲头的向下作用使材料被水平拉深。
一个凸缘板料上的单元体在半径方向上被限定,而板厚保持几乎不变。
板料成形的原理如图2所示。
拉延通常是用来描述在板料平面上的两个互相垂直的方向被拉长的板料的单元体的变形原理的术语。
拉延的一种特殊形式,可以在大多数成形加工中遇到,即平面张力拉延。
在这种情况下,一个板料的单元体仅在一个方向上进行拉延,在拉长的方向上宽度没有发生变化,但是在厚度上有明确的变化,即变薄。
汽车零件冲压模具设计及其发展分析

汽车零件冲压模具设计及其发展分析摘要:本文介绍了汽车覆盖件冲压模的设计要点,针对冲压模具的发展和现状以及冲压新技术的应用,根据一个冲压模具的实例,对汽车覆盖件在冲压过程中容易出现的问题进行了分析,从工艺分析、模具结构设计等几个方面详细说明了冲压模设计的重要性,为结构模具优化设计分析奠定了基础。
关键词:汽车;覆盖件;冲压模;设计引言冲压成型在汽车制造中是一种十分重要的制造技术,而汽车覆盖件大都采用冲压而成,其模具制造周期影响汽车的制造成本以及新产品开发的周期。
目前,国外汽车界提出缩短产品的市场化周期、降低产品开发费用和减轻汽车的质量的了3R 战略,其中的一个重要环节就是降低车身覆盖件模具的制造费用和减少生产周期,因此在车身覆盖件模具的研发方面各个国家都投入了大量的资金。
本文就是通过介绍汽车覆盖件冲压模的设计要点,针对冲压模具的发展和现状以及冲压新技术的应用,根据一个冲压模具的实例,对汽车覆盖件在冲压过程中容易出现的问题进行了分析,从工艺分析、模具结构设计等几个方面详细说明了冲压模设计的重要性。
1模具冲压技术在制造行业中的应用1.1冲压模具的发展和现状随着与国际接轨的脚步不断加快,市场竞争的日益加剧,人们已经越来越认识到产品质量、成本和新产品的开发能力的重要性。
在冲压模具发展方面,主要表现在以下几个方面:第一,模具CAD/CAM/CAE技术是模具设计制造的发展方向。
计算机和网络的发展正使CAD/CAM/CAE技术跨地区、跨企业、跨院所地在整个行业中推广成为可能,实现技术资源的重新整合,使虚拟制造成为可能[1]。
第二,模具“逆向工程”的飞速发展。
高速扫描机和模具扫描系统提供了从模型或实物扫描到加工出期望的模型所需的诸多功能,大大缩短了模具的在研制制造周期。
有些快速扫描系统,可快速安装在已有的数控铣床及加工中心上,实现快速数据采集、自动生成各种不同数控系统的加工程序、不同格式的CAD数据,模具逆向工程已在汽车、摩托车、家电等行业得到成功应用。
冲压模具的设计与制造分析

冲压模具的设计与制造分析冲压模具是机械加工中比较常见的模具形式之一,它通常用于汽车、电子、家电等领域中的零部件生产。
冲压模具的制造和设计对于产品的质量和生产效率有着非常重要的影响,因此需要在制造中加强分析和优化。
冲压模具的设计和制造主要包括以下几个方面:第一,工件的形状和材料。
冲压模具的设计需要结合工件的形状和材料进行考虑。
不同形状的工件需要不同的冲压模具来适应,同时工件的材料也需要做出相应的选取,以便冲压过程不会出现异常情况,提高产品的质量。
第二,模具的结构设计。
冲压模具的结构设计需要充分考虑冲裁时的压力、角度和导向。
同时需要考虑工件的形状要素,采用合理的加工方式,提高加工精度和效率,保证生产稳定性。
第三,零部件的加工和装配。
在冲压模具的制造过程中,需经过多道工序,包括铣削、钻孔、线切割、硬化等。
在零部件装配时应该注意每个零部件的与模具的充分匹配,保证模具的稳定性和可靠性。
第四,模具性能测试。
在冲压模具制造完成后,还需要进行性能测试,包括模具的光洁度、运转稳定性、耐磨性等等。
通过性能测试可以评估模具的品质,进一步优化冲压模具的设计和制造。
在冲压模具设计和制造过程中,还需要注重一些具体的技术要点,如冲压模具的设计要充分考虑模具的寿命和使用寿命,同时对模具的材质和结构进行优化和改进,以提高模具运行的稳定性和可靠性。
此外,在模具的制造和加工过程中,还需要充分运用现代技术手段,如计算机辅助设计、数控加工等技术手段,进一步提高模具加工的准确性和效率。
总之,冲压模具的设计和制造对于产品的质量和生产效率起着非常重要的作用,需要加强分析和优化,以保证冲压模具的可靠性和稳定性,同时提高产品的品质和生产效率。
汽车零件冲压模具设计及其开展探析

汽车零件冲压模具设计及其开展探析摘要:随着国民经济的飞速开展,汽车行业不时提高,这使得效劳于汽车生产模具行业也越来越快的开展起来。
现今在汽车生产中运用额模具品种有很多,其中运用最多的两个模具就是冲压模具和塑料模具,除了这两种模具之外还有锻造模具、铸造模具、粉末冶金模具、橡胶模具和拉丝模具、无机模具等资料构成的模具等等。
本文主要引见汽车零件冲压模具的设计和开展的趋向,经过引见当前我国的汽车零件冲压模具的设计情况,针对冲压模具的开展现状和冲压技术在整个制造行业中的应用方面进行简单的引见,阐明了汽车零件冲压模具设计技术的重要性,以求更好的促进汽车生产技术的开展,生产出先进的汽车。
关键词:汽车零件冲压模具设计开展1前言在汽车制造中一个重要的制造技术即冲压成型技术,在汽车生产中所运用的汽车掩盖件大多是运用的冲压技术而构成的,冲压模具的制造周期影响到整个汽车制造所运用的本钱和新产品开发运用的周期长短。
当前,在国外的汽车生产中提出了新的技术战略,即可以合理的缩短整个市场化的周期、降低汽车产品生产的本钱等优势,在这个战略中的一个很重要的环节就是可以减少生产的周期,并且可以降低车身掩盖模具的制造运用的费用,所以需求在汽车零件的冲压模具设计中投入大量的资金和技术。
下文主要剖析模具冲压的技术在整个制造行业中的详细应用,并扼要的剖析当前我国的汽车冲压模具的技术情况。
2汽车零件冲压模具的技术情况2.1模具CAD/CAM/CAE技术我国自20世纪代以来逐步开端运用CAD/CAM技术,到了21世纪之后CAD/CAM技术逐步提高,当前汽车生产中具有一定生产才能的冲压模具企业,都曾经具有CAD/CAM技术,同时其中的很多企业中还具有CAE技术。
冲压模具CAD/CAM技术可以缩短模具的制造周期,大大的降低了生产本钱费用,逐步的提高产品的质量,越来越多的得到应用。
在我国进行八五九五期间,有很多企业逐步的提高了计算机进行绘图的技术,数控加工的运用技术越来越遭到关注,使得CAD/CAM技术被普遍的运用。
毕业设计——汽车零件冲压模设计
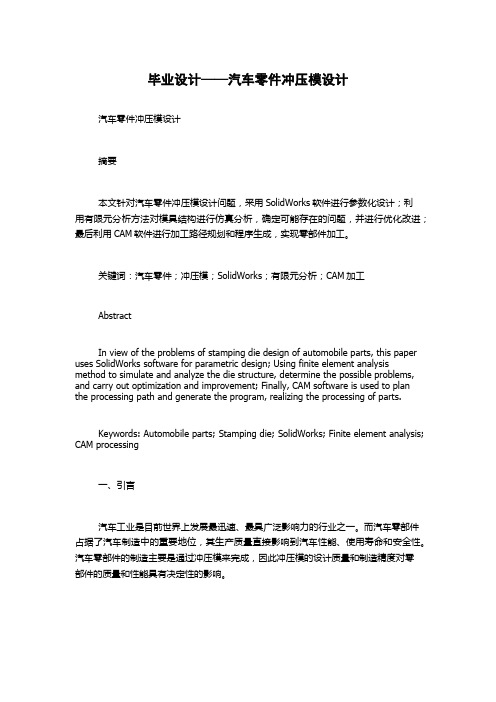
毕业设计——汽车零件冲压模设计汽车零件冲压模设计摘要本文针对汽车零件冲压模设计问题,采用SolidWorks软件进行参数化设计;利用有限元分析方法对模具结构进行仿真分析,确定可能存在的问题,并进行优化改进;最后利用CAM软件进行加工路径规划和程序生成,实现零部件加工。
关键词:汽车零件;冲压模;SolidWorks;有限元分析;CAM加工AbstractIn view of the problems of stamping die design of automobile parts, this paper uses SolidWorks software for parametric design; Using finite element analysis method to simulate and analyze the die structure, determine the possible problems, and carry out optimization and improvement; Finally, CAM software is used to plan the processing path and generate the program, realizing the processing of parts.Keywords: Automobile parts; Stamping die; SolidWorks; Finite element analysis; CAM processing一、引言汽车工业是目前世界上发展最迅速、最具广泛影响力的行业之一。
而汽车零部件占据了汽车制造中的重要地位,其生产质量直接影响到汽车性能、使用寿命和安全性。
汽车零部件的制造主要是通过冲压模来完成,因此冲压模的设计质量和制造精度对零部件的质量和性能具有决定性的影响。
本文以汽车零件冲压模设计为背景,综合运用SolidWorks、ANSYS Workbench和CAM软件等工具,分析了汽车零件冲压模的设计、分析和加工过程,并结合实际案例进行了实践操作与研究,为汽车零部件冲压模的设计与制造提供了一定的参考。
冲压模具的设计与制造分析
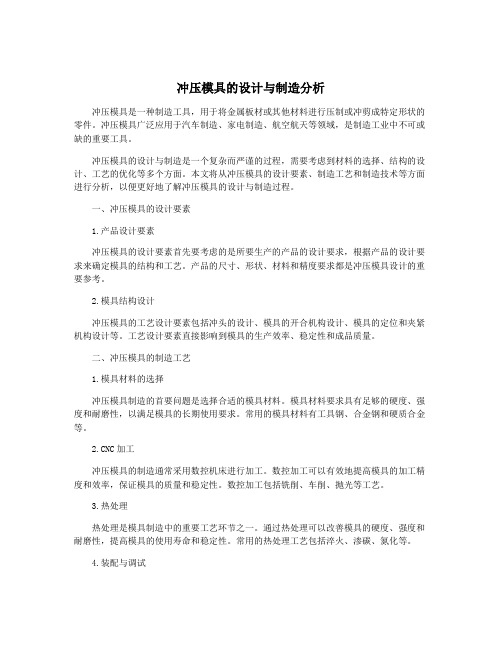
冲压模具的设计与制造分析冲压模具是一种制造工具,用于将金属板材或其他材料进行压制或冲剪成特定形状的零件。
冲压模具广泛应用于汽车制造、家电制造、航空航天等领域,是制造工业中不可或缺的重要工具。
冲压模具的设计与制造是一个复杂而严谨的过程,需要考虑到材料的选择、结构的设计、工艺的优化等多个方面。
本文将从冲压模具的设计要素、制造工艺和制造技术等方面进行分析,以便更好地了解冲压模具的设计与制造过程。
一、冲压模具的设计要素1.产品设计要素冲压模具的设计要素首先要考虑的是所要生产的产品的设计要求,根据产品的设计要求来确定模具的结构和工艺。
产品的尺寸、形状、材料和精度要求都是冲压模具设计的重要参考。
2.模具结构设计冲压模具的工艺设计要素包括冲头的设计、模具的开合机构设计、模具的定位和夹紧机构设计等。
工艺设计要素直接影响到模具的生产效率、稳定性和成品质量。
二、冲压模具的制造工艺1.模具材料的选择冲压模具制造的首要问题是选择合适的模具材料。
模具材料要求具有足够的硬度、强度和耐磨性,以满足模具的长期使用要求。
常用的模具材料有工具钢、合金钢和硬质合金等。
C加工冲压模具的制造通常采用数控机床进行加工。
数控加工可以有效地提高模具的加工精度和效率,保证模具的质量和稳定性。
数控加工包括铣削、车削、抛光等工艺。
3.热处理热处理是模具制造中的重要工艺环节之一。
通过热处理可以改善模具的硬度、强度和耐磨性,提高模具的使用寿命和稳定性。
常用的热处理工艺包括淬火、渗碳、氮化等。
4.装配与调试冲压模具的装配与调试是模具制造的最后阶段。
在装配与调试过程中,需要对模具的各个零部件进行组装与调整,以保证模具的精度、稳定性和可靠性。
1.模具CAD/CAM技术模具CAD/CAM技术是现代模具制造的重要技术手段。
通过CAD/CAM技术可以实现模具的设计、工艺规划、数控加工程序生成等全过程数字化,提高设计效率和生产精度。
2.先进制造技术冲压模具的制造技术在不断发展与进步,涌现了许多新的制造技术。
冲压磨具结构设计案例分析成功案例的启示与借鉴

冲压磨具结构设计案例分析成功案例的启示与借鉴在冲压加工中,冲压磨具是非常重要的工具之一。
它不仅直接影响产品质量和生产效率,还关系到整个生产线的稳定性和成本控制。
本文通过分析一些成功的冲压磨具设计案例,总结出一些启示和借鉴,以提供给冲压工艺设计师和工装工程师参考。
一、案例一:汽车车身冲压件磨具设计该案例涉及到汽车车身冲压件的磨具设计。
为了实现高质量的冲压加工,并减少生产过程中的杂散变形和损伤,设计师采用了以下几点设计方案:1. 结构刚性优化:通过优化磨具结构,增加钢板厚度和加强磨具内部支撑结构,使磨具的整体刚性增强。
这样可以有效减少因冲击力而导致的磨具的扭曲和变形,保证冲压加工的稳定性。
2. 强化磨具表面处理:磨具的表面经过特殊处理,增加了硬度和耐磨性。
这样可以减少因摩擦而引起的磨损,延长磨具的使用寿命。
3. 优化导向系统:设计师对磨具的导向系统进行了优化,采用了高精度滑块导向和润滑系统。
这样可以确保冲压过程中的导向准确性,减少因导向偏差而导致的磨具损伤。
通过上述的设计方案,该案例中的冲压磨具提供了高质量的冲压加工,并且在长期使用中保持了较好的稳定性和寿命。
二、案例二:家用电器金属壳体冲压件磨具设计该案例涉及到家用电器金属壳体冲压件的磨具设计。
为了提高产品质量和生产效率,设计师采用了以下几点设计方案:1. 精确模具结构设计:通过精确的模具结构设计,确保金属壳体冲压件的尺寸和形状精度。
这可以避免冲压过程中产生的尺寸偏差和变形,保证产品的外观质量。
2. 合理分布冲孔:设计师根据冲压件的形状和结构特点,合理安排冲孔的位置和数量。
这样可以减少冲压过程中的扭力和应力集中,减少磨具的磨损和损伤。
3. 优化润滑系统:针对家用电器金属壳体冲压件的特点,设计师优化了润滑系统。
通过添加适当的润滑剂和优化润滑剂的供应方式,减少摩擦和热量,并提高冲压件的表面光洁度。
通过上述的设计方案,该案例中的冲压磨具实现了高效、稳定的冲压加工,提高了产品质量和生产效率。
后制动器底板冲压工艺分析及模具设计
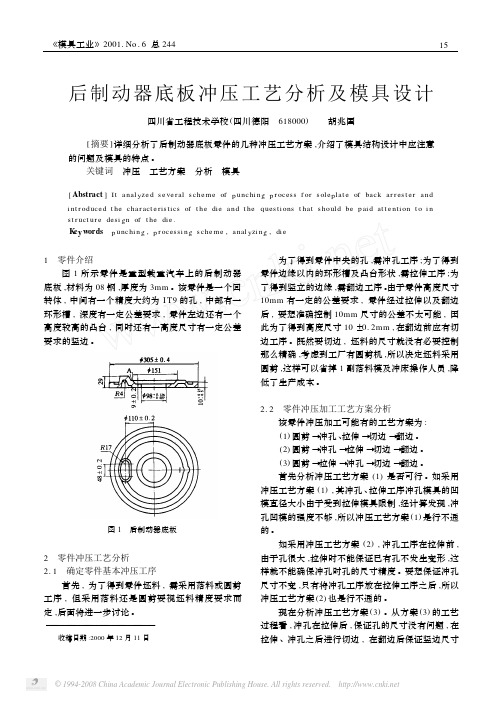
后制动器底板冲压工艺分析及模具设计四川省工程技术学校(四川德阳618000)胡兆国[摘要]详细分析了后制动器底板零件的几种冲压工艺方案,介绍了模具结构设计中应注意的问题及模具的特点。
关键词冲压工艺方案分析模具[Abstract]It a nal y ze d s e ve r al s che me of p unchi n g p r ocess f or s ole p lat e of back ar r es t e r a nd i nt r oduce d t he char act e ris tics of t he die a nd t he q ues tions t hat s houl d be p ai d at t e ntion t o i n s t r uct ur e desi g n of t he die.K e y words p unchi n g,p r ocessi n g s che me,a nal y zi n g,die1零件介绍图1所示零件是重型载重汽车上的后制动器底板,材料为08钢,厚度为3mm。
该零件是一个回转体,中间有一个精度大约为I T9的孔,中部有一环形槽,深度有一定公差要求,零件左边还有一个高度较高的凸台,同时还有一高度尺寸有一定公差要求的竖边。
图1后制动器底板2零件冲压工艺分析2.1确定零件基本冲压工序首先,为了得到零件坯料,需采用落料或圆剪工序,但采用落料还是圆剪要视坯料精度要求而定,后面将进一步讨论。
———————————————————收稿日期:2000年12月11日为了得到零件中央的孔,需冲孔工序;为了得到零件边缘以内的环形槽及凸台形状,需拉伸工序;为了得到竖立的边缘,需翻边工序。
由于零件高度尺寸10mm有一定的公差要求,零件经过拉伸以及翻边后,要想准确控制10mm尺寸的公差不太可能,因此为了得到高度尺寸10±0.2mm,在翻边前应有切边工序。
冲压模具的设计与制造分析

分析
综合分析冲压模具的设计与制造,可以发现存在以下问题和不足:
1、设计方面,对于复杂形状和特殊材料的成型加工工艺缺乏深入了解,导 致设计不合理,影响模具的性能和使用寿命;
2、制造方面,加工设备的精度和稳定性不足,影响模具的制造质量和进度, 同时材料选择不当也会导致模具的性能和使用寿命下降;
3、整体而言,冲压模具的设计与制造需要进一步实现标准化和数字化,以 提高模具的质量、降低成本并缩短研发周期。
对于设计师来说,需要掌握更多的数字化工具,并且紧密结合新的科技发展 趋势,以便更好地服务于制造业和社会发展。
参考内容
冲压工艺与冲压模具设计在制造业中具有重要地位,特别是在汽车、机械制 造等领域。本次演示将从冲压工艺和冲压模具设计的基本概念入手,深入探讨其 原理、特点和未来发展趋势。
一、冲压工艺基本原理及分类
五、结论
冲压工艺与冲压模具设计是制造业中的重要环节,对于汽车、机械制造等领 域的发展具有重要意义。本次演示对冲压工艺的基本原理及分类、冲压模具设计 流程及影响因素以及数字化模具设计的优势进行了简要探讨。随着科技的不断发 展,冲压工艺与冲压模具设计将不断进步,为制造业的发展注入新的动力。
感谢观看
冲压工艺在汽车制造业中具有广泛应用,如车身覆盖件、车轮、底盘等部件 的制作。在机械制造领域,冲压工艺可用于制作各种零件,如轴承、齿轮、活塞 等。这些零件对尺寸精度、表面质量的要求较高,冲压工艺能够满足这些严格的 技术要求。
三、冲压模具设计流程及影响因 素
冲压模具设计是冲压工艺中的关键环节,其设计水平直接影响着产品质量、 生产效率和制造成本。冲压模具设计流程可分为以下几个步骤:明确设计要求、 制定设计方案、进行结构设计、模拟分析、优化设计方案、出图等。
浅析汽车覆盖件冲压模具的结构优化

浅析汽车覆盖件冲压模具的结构优化1. 引言1.1 背景介绍汽车覆盖件是汽车外观设计中非常重要的一部分,对于汽车的整体美观性和aerodynamic performance 起着至关重要的作用。
而汽车覆盖件的生产离不开冲压模具,冲压模具是汽车覆盖件生产中的核心工具。
通过冲压模具,可以将金属板料冲压成各种形状的零部件,用于组装汽车覆盖件。
随着汽车产业的不断发展,市场对汽车覆盖件质量和生产效率的要求也越来越高。
如何优化汽车覆盖件冲压模具的结构,提高其使用寿命和生产效率,成为了当前研究的热点之一。
结构优化能够有效减少模具的磨损和变形,降低生产成本,提高生产质量,对于汽车覆盖件生产具有重要意义。
本文将对汽车覆盖件冲压模具的结构优化进行浅析,探讨其结构特点、常见问题以及优化方法,希望能够为汽车覆盖件生产领域的研究和实践提供一定的参考。
1.2 研究意义汽车覆盖件冲压模具作为汽车制造中不可或缺的重要工具,在汽车制造行业中扮演着至关重要的角色。
其结构设计的合理与否,直接影响着汽车覆盖件的加工质量、生产效率以及成本控制等方面。
进行汽车覆盖件冲压模具的结构优化研究具有重要意义。
通过对冲压模具结构的优化研究,可以提高冲压模具的使用性能和寿命,减少维护和更换成本,降低生产成本,提高汽车制造企业的竞争力。
结构优化可以有效解决汽车覆盖件冲压过程中常见问题,如产生裂纹、翻边、波纹等质量问题,提高冲压件的成品率和质量稳定性。
优化冲压模具的结构,还可以减小冲压过程的应力集中情况,降低模具的磨损和变形,延长模具的使用寿命。
对汽车覆盖件冲压模具的结构进行优化研究,对提高汽车制造行业的发展水平,推动制造业转型升级,具有重要的现实意义和战略意义。
希望通过本文的研究,能够为汽车覆盖件冲压模具的结构优化提供一定的理论依据和实践指导,进一步推动汽车制造行业的发展进程。
2. 正文2.1 汽车覆盖件冲压模具的结构特点1. 刚度和稳定性要求高:由于汽车覆盖件的形状复杂,对冲压模具的刚度和稳定性要求较高。
轿车后保险杠底座冲压工艺与模具设计

This topic by analyzing the car to the rear bumper of the forming process of the base sedan rear bumper structure of the base characteristics and technical requirements, design a punching off the material composite modulus. The focus of the design involved in the stamping process and die classification; common stamping equipment and works, the choice of principles; stamping the basic principles and laws; stamping formability and common stamping materials; types of mold material, performance, selection principles, and heat treatment; mold manufacturing characteristics, mold parts, processing methods and applications. Understanding of the blanking process technology program development anddiedesign, to determine the gap, the edge size calculation principles and methods, layout design, punching power on the basis of the analysis of blanking deformation process and blankingfactorsaffecting thequality center of pressure calculation, the blanking process analysis and process programming, the typical structure of the blanking, part design and mold standard applications, die design method and steps.
- 1、下载文档前请自行甄别文档内容的完整性,平台不提供额外的编辑、内容补充、找答案等附加服务。
- 2、"仅部分预览"的文档,不可在线预览部分如存在完整性等问题,可反馈申请退款(可完整预览的文档不适用该条件!)。
- 3、如文档侵犯您的权益,请联系客服反馈,我们会尽快为您处理(人工客服工作时间:9:00-18:30)。
汽车后底板的冲压模具设计分析Fuh-kuo Chen,Jia-Hong Liu台湾国立大学机械工程系,台北,台湾1994年10月10日接收摘要本文研究了客车后底板的冲压制造过程。
使用圆栅格分析和3-D有限元方法,对产生拉深开裂缺陷的最初的冲模设计进行了分析。
开裂缺陷是由于压边圈下大范围的金属限制了向杯状区域的流动。
优化的冲模设计,包括一个分离的冲模面和一个楔形机构组成的凹模结构,目的是在不添加工序的情况下,向杯状区域提供额外金属、消除开裂缺陷。
这种优化的冲模设计在第一次和第二次拉深的圆栅格分析结果中得到验证,获得了合格的拉深面板。
关键字:冲压模具;后底板;开裂;圆栅格分析1.绪论一般冲压过程中的主要缺陷是开裂,在最近的十年中,很多研究都使用了成型极限分析和有限元分析方法来研究开裂问题的起因和解决办法。
自Keeler和Backofen在1963年第一次引入成型极限图(FLDS),在冲压车间里它们就已经被广泛的使用在金属的结构分析中。
即使这个成型过程极快,FLDS也可以显示出应力并提供一个有用的工具去测定,同时有限元方法能够精确的计算冲压部分的分布应力,并且预知是否可能产生开裂缺陷。
一般来说,解决开裂问题的办法是在主要的拉深过程开始前,向危险地带提供更多的金属,这样可以通过减少压边圈的压力或是改善润滑条件而达到,但是为了输送更多的金属到危险区域,最好最直接的方法是增加一个额外的工序,然而,这个额外的工序会多增加一套模具和额外的劳力从而增加生产成本。
在目前的研究中,优化的模具设计,包括一个分离的冲模面和一个楔形机构组成的凹模结构,目的是为了消除发生在客车面板冲压过程中的开裂缺陷。
这种特殊的模具面和楔形结构能为发生开裂缺陷的危险区域提供额外的金属,而不增加额外的工序。
圆栅格分析和3-D有限元仿真能够完成开裂缺陷分析的任务。
2.问题描述客车后面板的设计通常是由两块冲压板焊合在一起,如图1所示。
之所以选择两块板设计是由于开裂往往是发生在拉深成杯状的壁上,使得冲压一块后底板很困难,如图2所示。
开裂的发生是由于在杯壁和压边圈之间有一段距离,如图3中A-B处,这限制了压边圈下的金属流入杯状区域,同时两块板的距离很短,有足够的金属能够轻易地流入杯中从而阻止杯缘的开裂,由于成本的考虑,一块后底板容易得到,因此开裂问题必须被攻克。
为了在冲压车间生产出一块后底板,最初的程序包括四步:拉深,再次拉深,清理焊缝,翻边。
第一次拉深操作仅仅能够产生杯状外形,如图3所示。
就杯子周围的肋板来说,这是在第二次拉深操作中形成的。
像大多数冲压过程一样,后底板的主要变形是在第一次拉深操作中完成的。
这种传统的拉深过程容许冲床从压边圈中拉出更多的金属到模腔中。
为了促进金属的流动,未被拉深的焊料贴在压边圈的表面。
然而,由于拉深很深和以上提及的几何学上的难点,在第一次拉深操作后开裂仍在靠近杯壁的底部被发现,如图2所示。
开裂缺陷的位置表明,在杯壁的一侧和压边圈之间有相当大的距离,这阻止了金属向杯状区域流动。
为了减少压边圈的应力,已经做的努力是帮助金属向杯状区域流动,但这致使在杯状区域底部出现更多起皱,也没有消除开裂,而改善薄金属的质量也被证明是徒劳的。
改变润滑条件能减弱开裂问题,然而这对大规模的生产并不节省成本。
同时大量的润滑油被用在冲压生产中可能会污染了车间。
因此更有效的方式是解决冲压形成杯状之前向杯状区提供更多金属的问题。
为了达到这个目的,改变压边圈表面的形状以便向杯状区域提供更多的金属。
然而由于同样的几何学原因,在杯与压边圈一侧有相当大的距离,优化的压边圈不容易获得。
最后,为第一次半自动拉深设计的分模面是通过特殊楔形机构安装在凹模里,它能为杯状区域提供更多的金属,并且激发了没有开裂缺陷产品的生产。
3.最初设计的分析开裂问题通常与危险区域的应力分布有关,在任何横截面的成形部分中,应力分布是由两方面决定的:一个是由金属流入压边圈的上方进行拉深而造成的,另一个是由冲床和模具之间接触所造成的延伸总量决定的。
为了在金属流动中考察几何学的效果,最初的设计是通过圆栅格分析CGA和有限元方法分析FEM。
3.1圆栅格分析圆栅格分析已被广泛用于冲压车间的测量应力分布当中,因此能够通过测绘成型极限图的有规则的应力来分析金属片的可冲压性。
圆栅格比其他类型的栅格例如方形栅格有主要的优势,因为它们没有任何的方向性,这种优势在于圆变形后会成为椭圆。
这两个主要的方向清晰地通过长轴与短轴展示出来。
通过在成型极限图上测量长轴与短轴的长度得出主张力的大小,就能够估计成形部分的区域。
在目前的研究中,底板的生产利用原来的模具设计,第一次使用圆栅格分析,生产厚0.7mm,DDQ品质的钢,如图4所示那样的材料,钢的供应者提供材料相应的成型极限图在图5中展示。
靠近这个弯曲面的残余应力使这个区域有开裂的趋势。
实际上成型极限弯曲如图在5中虚线所示,被移下来的10%作为设计弯曲。
在成型极限弯曲之上的区域被称作故障区域,在成型极限弯曲和设计弯曲之间的区域被称为边缘区域,在设计弯曲以下的区域被指定为安全区域。
一般来说,为了冲压过程的稳定,任何成形部分的应力分布应该下降到安全区域。
冲压过程稳定是指对过程变化不敏感。
冲压之前模腔的危险区域被圆心间相距6mm,直径5mm的圆所标记。
为了标记模腔危险区域的圆,首先要使用一个特殊的清洁工具清洁,然后,有正确栅格的模板被放置在零件上,使用电解质作为指挥者,被模板覆盖的区域以栅格模式被标记。
为了阻止标记区域生锈,用一块湿清洁布把在标记中多余部分的电解质和残留的氧化物擦干净。
标记之后,开裂在杯壁靠近杯顶处被发现,如图2所示。
在裂缝周围不成形圆的主要和次要的应力如图6所示。
在成型极限图上的测量和规划如图7所示。
从图中可看出有规则的张力紧挨着成型极限曲线,因为主要和次要的应力是正应力,衰退是由延伸而造成的,所以应力非常接近水平应力方式,即接近次要应力为零的轴。
圆栅格分析的结果表明,原来的设计是非常不稳定的。
FLD也表明主要拉力太大,这是和目前作者的意见,即认为杯与压边圈之间的距离限制了金属向杯状区域流动这一结论是一致的,结果产生了大的拉力。
在前一部分讨论中最有效的减小主要拉力的方法是向杯状区域提供更多的金属。
3.2有限元分析为了帮助进一步了解冲压过程中毛坯的变形,3-D有限元分析完成最初设计的第一次拉深操作的任务。
明确了有限元是能够把任何3-D模具形状的PAM-STAMP 译成密码。
从3-D模具几何学起,只有冲床、模腔、压边圈未被简化,有限元程序能更准确模仿真实生产过程。
为了描述模具成分的几何学,一个商业的CAD 软件被用来构造这些成分的表面模型。
网孔系统要求把PAM-STAMP 作为几何学模具的输入数据,通过商业的CAD 系统产生,如图8所示。
在早些时期,简单的3-D 模型产生网孔系统是非常困难的,例如冲压模。
然而CAD 系统被越来越多地用在模具和模具工业中。
上述为模具几何学产生网孔系统的程序变得容易起来。
自PAM-STAMP 代码把模具成分当作其坚硬外壳以来,网孔系统仅仅被用来描述这些成分的几何学,而不是对应力进行分析。
在目前的调查中,3节点三角形和四节点矩形的原理被用来建造网孔系统,毛坯的网孔系统如图8所示。
从图中可以看出网孔密度在杯状区域比在其它地方高得多,因为杯状区域是开裂发生的位置。
许多在分析时使用的原理被总结如下:模具:9910,冲床:5499,压边圈:4411,薄片:4891,总计24711。
有限元的物质条件同前一部分一样,其他的操作条件是:压边圈的张力57KPa ,冲床速度10m/s ,冲击行程895mm ,摩擦力系数0.12,在一台SGI 工作站上展示仿真结果,一台HP735工作站单独工作CPU 需花费的时间是11100秒。
4.改进的模具设计开裂缺陷导致杯状周围的金属缺少,为了让更多的金属流向杯状,要改变杯状一侧的压边圈,如图12所示。
模具和压边圈的几何学仍与原来设计的一样,因此未被在图12中展示。
为了使这种修改有效,3-D有限元仿真完成代替重修模具的任务。
除了冲床和压边圈的几何学被改变以外,仿真条件与原来的设计是一样的,如图12所示。
整块板从有限元仿真为修改模具设计而得到主要和次要的应力分布,如图13所示。
从图中看出,由于大量的金属从不受限制的区域流向杯状,应力分布往下移了一点,但仍在边缘处。
图14展示了畸形的形状,观察到在不受限制的区域内有严重的起皱。
虽然在改进的设计中开裂问题可能避免,但严重的起皱是不能接受的。
因此,通过3-D有限元分析改进技术并不可行。
5.优化的模具设计正如前面部分所述,在生产面板中消除开裂缺陷的最有效的方法是为杯状区域提供更多的金属,为了达到这个目的已经作出了多次尝试,下面描述的模具设计已经被证明是可行和有效的。
在冲压车间,后底板通过两根氮柱为压边圈的单一冲压动作提供力量,为了在不增加额外工序的情况下向杯状区域提供更多的金属,凹模的形状被分为两部分,如图15所示。
模具形状的中间部分被楔形机构推动,并能够与固定的凹模进行相对的上下运动。
为了消除开裂缺陷设计改进的模具形状,活动部分的位置选择在杯状区域。
当压边圈关闭时,活动部分通过楔形机构向上驱动,把毛坯提高到一个特殊的高度。
当它在模具关闭过程期间与顶模接触时,倘若与原来的设计相比杯状区域有更多的金属,活动部分就被迫向下移动。
在模具关闭时,活动部分重新回到它的位置,加工成型完好部分。
6、结论为了使优化的模具设计有效,在上述相应计算基础上改进凹模结构。
结果,在试验期间使用改进的模具获得了优质量的后底板。
为了评估质量,圆栅格分析被又一次应用到成形过程中,与原来设计一样,圆被标记在同样的区域,开裂经常发生的杯壁周围,主要和次要应力被标注在成型极限图中,如图16所示。
从图中可看出,所有的标准应力在安全区域,其显示出用改进模具进行第一次拉深操作是非常稳定的,它对于处理变化并不敏感。
为了使它更完整,圆栅格分析也同样完成第二次拉深操作的任务。
除了在面板内形成肋骨之外,如图1所示,第二次拉深操作还在杯顶加大圆角半径。
因此,第二次拉深将有点拉长杯状区域。
在第一次拉深和第二次拉深中,测量杯状区域主要和次要应力在图17中展示。
在图17中很清楚的表明第二次拉深时拉力要大,尽管几个应力是在边缘区域,但大部分应力仍在安全区域。
因落入边缘区域的点数少并且它们的应力仍然接近设计弯曲,第二次拉深操作仍被认为是稳定的,至于第三次和以后的操作,只不过是修整和简单翻边操作。
因此,这两项操作不能够引起进一步的变形,也不需要分析。
译文原文出处:Journal of Materials Processing Technology 55 (1995) 408-416。