橡胶生产工艺介绍
橡胶生产工艺流程

橡胶生产工艺流程
《橡胶生产工艺流程》
橡胶是一种重要的工业原料,广泛应用于轮胎、橡胶制品、胶水等领域。
橡胶的生产工艺流程经过多道工序,包括橡胶树的采胶、橡胶的加工和成型等步骤。
首先是橡胶树的采胶。
橡胶树的树干上有一层薄薄的橡胶乳液,这就是我们常说的橡胶树胶。
工人们会用特制工具在橡胶树的树干上划上几道口,让橡胶乳液自然流出。
采胶一般在清晨进行,因为此时橡胶乳液的含水量相对较低,采得的橡胶更加纯正。
接下来是橡胶的加工。
采集到的橡胶乳液需要经过凝固、干燥等工序,变成实心的橡胶块。
首先将橡胶乳液倒入模具中,然后放入蒸汽锅中进行加热,使橡胶乳液凝固成块状。
接着将凝固后的橡胶块放置在干燥室中进行干燥,使橡胶块的含水量达到标准。
这样处理后的橡胶块就可以作为原料,用于生产橡胶制品。
最后是橡胶的成型。
经过加工的橡胶块会被送入成型机器中,经过一系列的模具和工序,变成各种橡胶制品,如轮胎、橡胶管、胶水等。
这些橡胶制品最终会被用于各种行业和领域。
总的来说,橡胶的生产工艺流程包括橡胶树的采胶、橡胶的加工和成型。
这些工序都需要精准的操作和高效的机器设备,以确保产出的橡胶品质优良。
随着技术的发展和工艺的改进,橡
胶生产的效率和质量也在不断提升,为各个行业提供更好的橡胶原料。
橡胶生产工艺流程
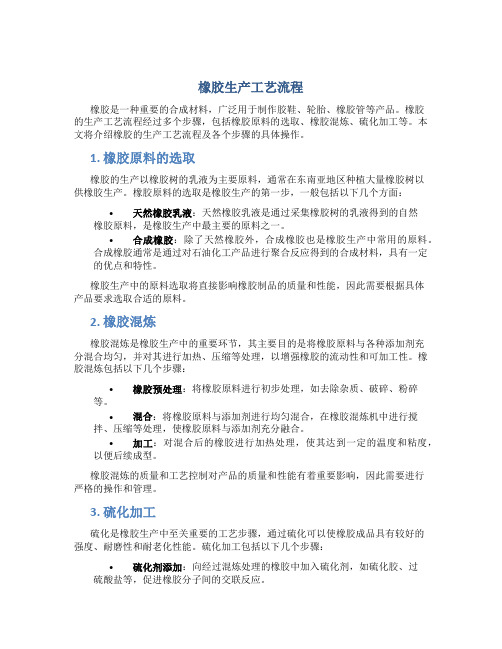
橡胶生产工艺流程橡胶是一种重要的合成材料,广泛用于制作胶鞋、轮胎、橡胶管等产品。
橡胶的生产工艺流程经过多个步骤,包括橡胶原料的选取、橡胶混炼、硫化加工等。
本文将介绍橡胶的生产工艺流程及各个步骤的具体操作。
1. 橡胶原料的选取橡胶的生产以橡胶树的乳液为主要原料,通常在东南亚地区种植大量橡胶树以供橡胶生产。
橡胶原料的选取是橡胶生产的第一步,一般包括以下几个方面:•天然橡胶乳液:天然橡胶乳液是通过采集橡胶树的乳液得到的自然橡胶原料,是橡胶生产中最主要的原料之一。
•合成橡胶:除了天然橡胶外,合成橡胶也是橡胶生产中常用的原料。
合成橡胶通常是通过对石油化工产品进行聚合反应得到的合成材料,具有一定的优点和特性。
橡胶生产中的原料选取将直接影响橡胶制品的质量和性能,因此需要根据具体产品要求选取合适的原料。
2. 橡胶混炼橡胶混炼是橡胶生产中的重要环节,其主要目的是将橡胶原料与各种添加剂充分混合均匀,并对其进行加热、压缩等处理,以增强橡胶的流动性和可加工性。
橡胶混炼包括以下几个步骤:•橡胶预处理:将橡胶原料进行初步处理,如去除杂质、破碎、粉碎等。
•混合:将橡胶原料与添加剂进行均匀混合,在橡胶混炼机中进行搅拌、压缩等处理,使橡胶原料与添加剂充分融合。
•加工:对混合后的橡胶进行加热处理,使其达到一定的温度和粘度,以便后续成型。
橡胶混炼的质量和工艺控制对产品的质量和性能有着重要影响,因此需要进行严格的操作和管理。
3. 硫化加工硫化是橡胶生产中至关重要的工艺步骤,通过硫化可以使橡胶成品具有较好的强度、耐磨性和耐老化性能。
硫化加工包括以下几个步骤:•硫化剂添加:向经过混炼处理的橡胶中加入硫化剂,如硫化胶、过硫酸盐等,促进橡胶分子间的交联反应。
•硫化处理:将橡胶制品放入硫化罐中进行硫化处理,通常在高温高压下进行,使橡胶形成交联结构,提高其强度和耐磨性。
硫化加工是橡胶生产的关键环节,对产品的质量和性能具有重要的影响,需要进行严格控制和管理。
橡胶制品的基本生产工艺过程

橡胶制品的基本生产工艺过程橡胶制品的生产工艺是一个包含多个步骤的复杂过程。
以下是橡胶制品的基本生产工艺过程:1. 原材料准备:橡胶制品的主要原材料是天然橡胶和合成橡胶。
原材料需要进一步加工,以便在后续的工艺过程中使用。
这包括清洗、切割和破碎等步骤。
2. 配方调配:根据产品要求,制定合适的橡胶配方。
不同类型的橡胶制品需要不同的橡胶配方,以确保产品具有所需的物理性能和特性。
在配方中,可能需要添加硫化剂、防老化剂、增塑剂和填充剂等助剂。
3. 混炼:将橡胶原料和各种助剂混合在一起,形成混炼胶料。
这个过程可以使用混炼机完成,混炼机能够把原料均匀地混合在一起,并产生适当的热量以促进反应。
4. 成型:将混炼好的胶料放入模具中,并通过压力或挤压等方式进行成型。
成型过程根据产品的不同可以使用不同的技术,例如压延、注射、挤出和压痕等。
成型完成后,需要进行烘干或固化以确保产品的硬度和形状。
5. 处理和整理:对成型后的产品进行修整和整理,以确保产品的质量和外观。
这包括去除多余的边角料、刷洗和打磨等处理过程。
6. 检测和检验:对制造完成的橡胶制品进行检测和检验,以确保产品符合预定的标准和要求。
这可以包括物理性能、化学性质、外观和尺寸等方面的测试。
不合格的产品将进行返工或退货。
7. 包装和储存:将合格的产品进行包装,并标明产品的规格、批次和生产日期等信息。
然后将产品储存到仓库或发往销售渠道。
总的来说,橡胶制品的生产工艺包含了原料准备、配方调配、混炼、成型、处理和整理、检测和检验,以及最后的包装和储存。
其中每个步骤都需要精确的操作和控制,以确保最终产品的质量和效果。
橡胶制品的生产工艺是一个精细而复杂的过程,需要严格的控制和技术实力。
接下来将继续介绍橡胶制品的详细生产工艺过程以及一些常见的应用。
8. 二次加工:某些橡胶制品需要进行二次加工,以达到特定的要求和功能。
例如,橡胶密封件可能需要进行模切和槽口切割,橡胶管道可能需要进行穿刺和加强带的固定等。
橡胶的工艺流程
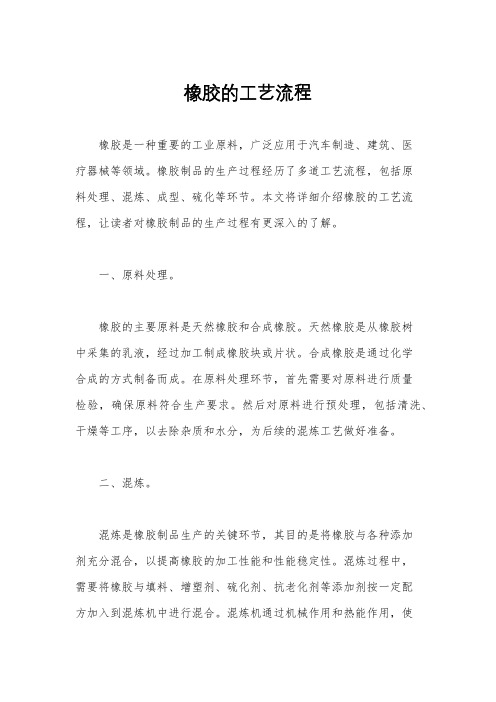
橡胶的工艺流程橡胶是一种重要的工业原料,广泛应用于汽车制造、建筑、医疗器械等领域。
橡胶制品的生产过程经历了多道工艺流程,包括原料处理、混炼、成型、硫化等环节。
本文将详细介绍橡胶的工艺流程,让读者对橡胶制品的生产过程有更深入的了解。
一、原料处理。
橡胶的主要原料是天然橡胶和合成橡胶。
天然橡胶是从橡胶树中采集的乳液,经过加工制成橡胶块或片状。
合成橡胶是通过化学合成的方式制备而成。
在原料处理环节,首先需要对原料进行质量检验,确保原料符合生产要求。
然后对原料进行预处理,包括清洗、干燥等工序,以去除杂质和水分,为后续的混炼工艺做好准备。
二、混炼。
混炼是橡胶制品生产的关键环节,其目的是将橡胶与各种添加剂充分混合,以提高橡胶的加工性能和性能稳定性。
混炼过程中,需要将橡胶与填料、增塑剂、硫化剂、抗老化剂等添加剂按一定配方加入到混炼机中进行混合。
混炼机通过机械作用和热能作用,使各种添加剂均匀分散在橡胶中,形成均匀的橡胶混合料。
三、成型。
混炼后的橡胶混合料需要进行成型,以得到所需的橡胶制品。
成型过程根据不同的制品要求,可以采用压延、挤出、注塑等不同的成型方法。
在成型过程中,需要根据产品的形状和尺寸,选择合适的模具和成型设备,将橡胶混合料加工成所需的形状,如轮胎、密封圈、橡胶管等。
四、硫化。
硫化是橡胶制品生产中的重要工艺环节,通过硫化可以使橡胶获得良好的物理性能和耐热耐老化性能。
硫化过程是将成型后的橡胶制品放入硫化炉中,加热并加入硫化剂,使橡胶分子间发生交联反应,从而增强橡胶的强度和弹性。
硫化时间和温度根据不同的橡胶制品和硫化体系有所不同,需要根据实际情况进行调整。
五、检验与包装。
最后,经过硫化的橡胶制品需要进行质量检验,包括外观质量、尺寸精度、物理性能等方面的检测。
合格的橡胶制品经过检验后,将进行包装和存储,待出厂销售或使用。
总结,橡胶制品的生产过程经历了原料处理、混炼、成型、硫化等多道工艺流程,每道工艺环节都对最终产品的质量和性能有着重要的影响。
橡胶生产工艺简介

橡胶生产工艺简介橡胶生产工艺简介1 综述橡胶制品的主要原料是生胶、各种配合剂、以及作为骨架材料的纤维和金属材料,橡胶制品的基本生产工艺过程包括塑炼、混炼、压延、压出、成型、硫化6个基本工序。
橡胶的加工工艺过程主要是解决塑性和弹性矛盾的过程,通过各种加工手段,使得弹性的橡胶变成具有塑性的塑炼胶,在加入各种配合剂制成半成品,然后通过硫化是具有塑性的半成品又变成弹性高、物理机械性能好的橡胶制品。
2 橡胶加工工艺2.1塑炼工艺生胶塑炼是通过机械应力、热、氧或加入某些化学试剂等方法,使生胶由强韧的弹性状态转变为柔软、便于加工的塑性状态的过程。
生胶塑炼的目的是降低它的弹性,增加可塑性,并获得适当的流动性,以满足混炼、亚衍、压出、成型、硫化以及胶浆制造、海绵胶制造等各种加工工艺过程的要求。
掌握好适当的塑炼可塑度,对橡胶制品的加工和成品质量是至关重要的。
在满足加工工艺要求的前提下应尽可能降低可塑度。
随着恒粘度橡胶、低粘度橡胶的出现,有的橡胶已经不需要塑炼而直接进行混炼。
在橡胶工业中,最常用的塑炼方法有机械塑炼法和化学塑炼法。
机械塑炼法所用的主要设备是开放式炼胶机、密闭式炼胶机和螺杆塑炼机。
化学塑炼法是在机械塑炼过程中加入化学药品来提高塑炼效果的方法。
开炼机塑炼时温度一般在80℃以下,属于低温机械混炼方法。
密炼机和螺杆混炼机的排胶温度在120℃以上,甚至高达160-180℃,属于高温机械混炼。
生胶在混炼之前需要预先经过烘胶、切胶、选胶和破胶等处理才能塑炼。
几种胶的塑炼特性:天然橡胶用开炼机塑炼时,辊筒温度为30-40℃,时间约为15-20min;采用密炼机塑炼当温度达到120℃以上时,时间约为3-5min。
丁苯橡胶的门尼粘度多在35-60之间,因此,丁苯橡胶也可不用塑炼,但是经过塑炼后可以提高配合机的分散性顺丁橡胶具有冷流性,缺乏塑炼效果。
顺丁胶的门尼粘度较低,可不用塑炼。
氯丁橡胶得塑性大,塑炼前可薄通3-5次,薄通温度在30-40℃。
橡胶制品的基本生产工艺过程
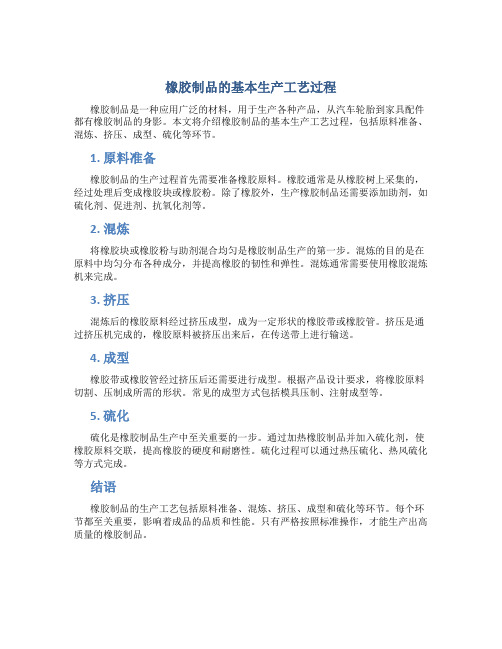
橡胶制品的基本生产工艺过程
橡胶制品是一种应用广泛的材料,用于生产各种产品,从汽车轮胎到家具配件都有橡胶制品的身影。
本文将介绍橡胶制品的基本生产工艺过程,包括原料准备、混炼、挤压、成型、硫化等环节。
1. 原料准备
橡胶制品的生产过程首先需要准备橡胶原料。
橡胶通常是从橡胶树上采集的,经过处理后变成橡胶块或橡胶粉。
除了橡胶外,生产橡胶制品还需要添加助剂,如硫化剂、促进剂、抗氧化剂等。
2. 混炼
将橡胶块或橡胶粉与助剂混合均匀是橡胶制品生产的第一步。
混炼的目的是在原料中均匀分布各种成分,并提高橡胶的韧性和弹性。
混炼通常需要使用橡胶混炼机来完成。
3. 挤压
混炼后的橡胶原料经过挤压成型,成为一定形状的橡胶带或橡胶管。
挤压是通过挤压机完成的,橡胶原料被挤压出来后,在传送带上进行输送。
4. 成型
橡胶带或橡胶管经过挤压后还需要进行成型。
根据产品设计要求,将橡胶原料切割、压制成所需的形状。
常见的成型方式包括模具压制、注射成型等。
5. 硫化
硫化是橡胶制品生产中至关重要的一步。
通过加热橡胶制品并加入硫化剂,使橡胶原料交联,提高橡胶的硬度和耐磨性。
硫化过程可以通过热压硫化、热风硫化等方式完成。
结语
橡胶制品的生产工艺包括原料准备、混炼、挤压、成型和硫化等环节。
每个环节都至关重要,影响着成品的品质和性能。
只有严格按照标准操作,才能生产出高质量的橡胶制品。
橡胶生产工艺简介
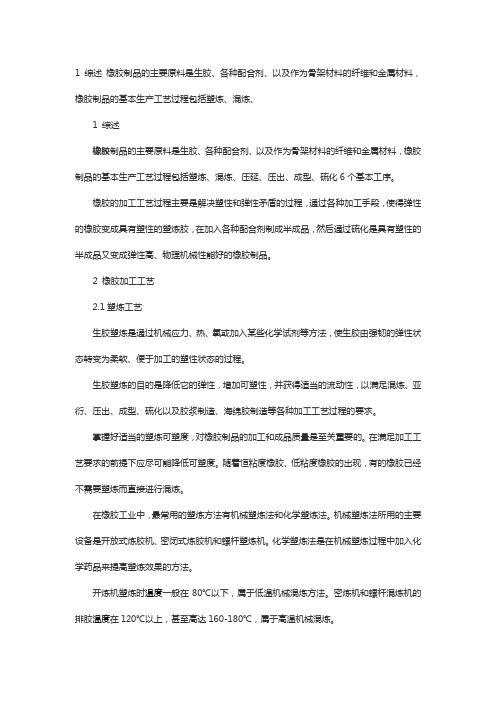
1 综述橡胶制品的主要原料是生胶、各种配合剂、以及作为骨架材料的纤维和金属材料,橡胶制品的基本生产工艺过程包括塑炼、混炼、1 综述橡胶制品的主要原料是生胶、各种配合剂、以及作为骨架材料的纤维和金属材料,橡胶制品的基本生产工艺过程包括塑炼、混炼、压延、压出、成型、硫化6个基本工序。
橡胶的加工工艺过程主要是解决塑性和弹性矛盾的过程,通过各种加工手段,使得弹性的橡胶变成具有塑性的塑炼胶,在加入各种配合剂制成半成品,然后通过硫化是具有塑性的半成品又变成弹性高、物理机械性能好的橡胶制品。
2 橡胶加工工艺2.1塑炼工艺生胶塑炼是通过机械应力、热、氧或加入某些化学试剂等方法,使生胶由强韧的弹性状态转变为柔软、便于加工的塑性状态的过程。
生胶塑炼的目的是降低它的弹性,增加可塑性,并获得适当的流动性,以满足混炼、亚衍、压出、成型、硫化以及胶浆制造、海绵胶制造等各种加工工艺过程的要求。
掌握好适当的塑炼可塑度,对橡胶制品的加工和成品质量是至关重要的。
在满足加工工艺要求的前提下应尽可能降低可塑度。
随着恒粘度橡胶、低粘度橡胶的出现,有的橡胶已经不需要塑炼而直接进行混炼。
在橡胶工业中,最常用的塑炼方法有机械塑炼法和化学塑炼法。
机械塑炼法所用的主要设备是开放式炼胶机、密闭式炼胶机和螺杆塑炼机。
化学塑炼法是在机械塑炼过程中加入化学药品来提高塑炼效果的方法。
开炼机塑炼时温度一般在80℃以下,属于低温机械混炼方法。
密炼机和螺杆混炼机的排胶温度在120℃以上,甚至高达160-180℃,属于高温机械混炼。
生胶在混炼之前需要预先经过烘胶、切胶、选胶和破胶等处理才能塑炼。
几种胶的塑炼特性:天然橡胶用开炼机塑炼时,辊筒温度为30-40℃,时间约为15-20min;采用密炼机塑炼当温度达到120℃以上时,时间约为3-5min。
丁苯橡胶的门尼粘度多在35-60之间,因此,丁苯橡胶也可不用塑炼,但是经过塑炼后可以提高配合机的分散性顺丁橡胶具有冷流性,缺乏塑炼效果。
橡胶生产六大工艺
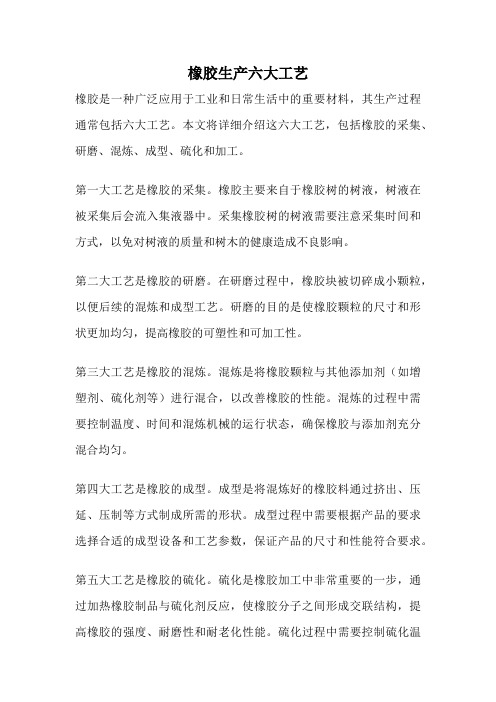
橡胶生产六大工艺橡胶是一种广泛应用于工业和日常生活中的重要材料,其生产过程通常包括六大工艺。
本文将详细介绍这六大工艺,包括橡胶的采集、研磨、混炼、成型、硫化和加工。
第一大工艺是橡胶的采集。
橡胶主要来自于橡胶树的树液,树液在被采集后会流入集液器中。
采集橡胶树的树液需要注意采集时间和方式,以免对树液的质量和树木的健康造成不良影响。
第二大工艺是橡胶的研磨。
在研磨过程中,橡胶块被切碎成小颗粒,以便后续的混炼和成型工艺。
研磨的目的是使橡胶颗粒的尺寸和形状更加均匀,提高橡胶的可塑性和可加工性。
第三大工艺是橡胶的混炼。
混炼是将橡胶颗粒与其他添加剂(如增塑剂、硫化剂等)进行混合,以改善橡胶的性能。
混炼的过程中需要控制温度、时间和混炼机械的运行状态,确保橡胶与添加剂充分混合均匀。
第四大工艺是橡胶的成型。
成型是将混炼好的橡胶料通过挤出、压延、压制等方式制成所需的形状。
成型过程中需要根据产品的要求选择合适的成型设备和工艺参数,保证产品的尺寸和性能符合要求。
第五大工艺是橡胶的硫化。
硫化是橡胶加工中非常重要的一步,通过加热橡胶制品与硫化剂反应,使橡胶分子之间形成交联结构,提高橡胶的强度、耐磨性和耐老化性能。
硫化过程中需要控制硫化温度和时间,以及硫化剂的种类和用量,确保橡胶制品的质量。
最后一大工艺是橡胶的加工。
加工是指对硫化好的橡胶制品进行后续处理,包括修整边角、打磨表面、安装配件等。
加工的目的是使橡胶制品的外观更加美观,尺寸更加精确,以满足客户的需求。
通过以上六大工艺,橡胶从采集到最终成品的过程得以完整实现。
这些工艺相互衔接,每个环节都至关重要,对橡胶制品的质量和性能有着重要影响。
因此,在橡胶生产过程中,需要严格控制每个工艺的参数和操作方法,确保橡胶制品达到设计要求,并具有优良的性能和可靠的质量。
总结起来,橡胶生产的六大工艺包括采集、研磨、混炼、成型、硫化和加工。
这些工艺环环相扣,每个环节都不可或缺。
只有在每个工艺环节都严格把控,才能生产出优质的橡胶制品。
橡胶生产工艺流程
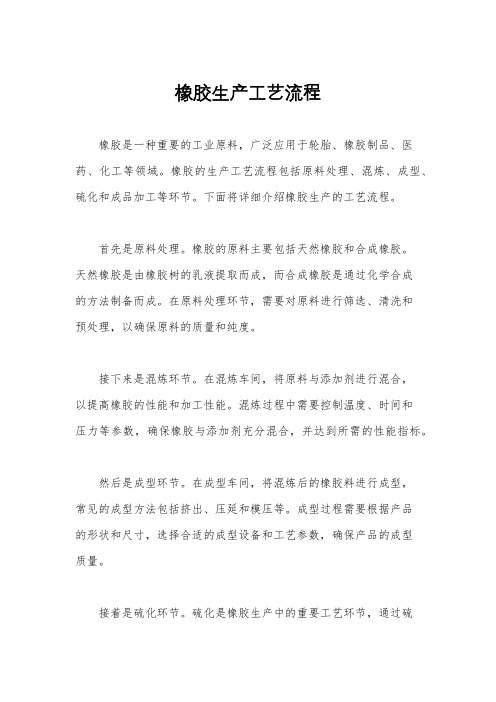
橡胶生产工艺流程橡胶是一种重要的工业原料,广泛应用于轮胎、橡胶制品、医药、化工等领域。
橡胶的生产工艺流程包括原料处理、混炼、成型、硫化和成品加工等环节。
下面将详细介绍橡胶生产的工艺流程。
首先是原料处理。
橡胶的原料主要包括天然橡胶和合成橡胶。
天然橡胶是由橡胶树的乳液提取而成,而合成橡胶是通过化学合成的方法制备而成。
在原料处理环节,需要对原料进行筛选、清洗和预处理,以确保原料的质量和纯度。
接下来是混炼环节。
在混炼车间,将原料与添加剂进行混合,以提高橡胶的性能和加工性能。
混炼过程中需要控制温度、时间和压力等参数,确保橡胶与添加剂充分混合,并达到所需的性能指标。
然后是成型环节。
在成型车间,将混炼后的橡胶料进行成型,常见的成型方法包括挤出、压延和模压等。
成型过程需要根据产品的形状和尺寸,选择合适的成型设备和工艺参数,确保产品的成型质量。
接着是硫化环节。
硫化是橡胶生产中的重要工艺环节,通过硫化可以使橡胶材料具有良好的弹性和耐磨性。
硫化过程中需要控制硫化温度、时间和压力等参数,确保橡胶材料的硫化度和性能达到要求。
最后是成品加工环节。
在成品加工车间,对硫化后的橡胶制品进行修整、检验和包装等工序,最终将成品交付给客户。
成品加工环节需要严格控制产品的质量,确保产品符合客户的要求。
总的来说,橡胶生产工艺流程包括原料处理、混炼、成型、硫化和成品加工等环节,每个环节都需要严格控制工艺参数,确保产品的质量和性能。
随着科技的发展,橡胶生产工艺也在不断创新,以适应市场对橡胶制品的不断需求。
希望本文的介绍能够对橡胶生产工艺有所帮助,谢谢阅读!。
橡胶制品生产工艺

橡胶制品生产工艺简要介绍一、基本工艺流程橡胶制品种类繁多,但生产工艺过程,却基本相同;以一般固体橡胶生胶为原料的橡胶制品的基本工艺过程包括:塑炼、混炼、压延、压出、成型、硫化6个基本工序;当然,原材料准备、成品整理、检验包装等基本工序也少不了;橡胶的加工工艺过程主要是解决塑性和弹性性能这个矛盾的过程,通过各种工艺手段,使得弹性的橡胶变成具有塑性的塑炼胶,再加入各种配合剂制成半成品,然后通过硫化使具有塑性的半成品又变成弹性高、物理机械性能好的橡胶制品;二、原材料准备:1.橡胶制品的主要原料是以生胶为基本材料,而生胶就是生长在热带,亚热带的橡胶树上通过人工割开树皮收集而来;2.各种配合剂:是为了改善橡胶制品的某些性能而加入的辅助材料;3.纤维材料有棉、麻、毛及各种人造纤维、合成纤维和金属材料钢丝、铜丝是作为橡胶制品的骨架材料,以增强机械强度、限制制品变型;在原材料准备过程中,配料必须按照配方称量准确;为了使生胶和配合剂能相互均匀混合,需要对材料进行加工:生胶要在60--70℃烘房内烘软后,再切胶、破胶成小块;配合剂有:块状的,如石蜡、硬脂酸、松香等要粉碎;粉状的若含有机械杂质或粗粒时需要筛选除去;液态的,如松焦油、古马隆需要加热、熔化、蒸发水分、过滤杂质;配合剂要进行干燥,不然容易结块、混炼时若不能分散均匀,硫化时产生气泡,会影响产品质量;三、塑炼生胶富有弹性,缺乏加工时必需的可塑性性能,因此不便于加工;为了提高其可塑性,所以要对生胶进行塑炼;这样,在混炼时配合剂就容易均匀分散在生胶中;同时,在压延、成型过程中也有助于提高胶料的渗透性渗入纤维织品内和成型流动性;将生胶的长链分子降解,形成可塑性的过程叫做塑炼;生胶塑炼的方法有机械塑炼和热塑炼两种;机械塑炼是在不太高的温度下,通过塑炼机的机械挤压和摩擦力的作用,使长链橡胶分子降解变短,由高弹性状态转变为可塑状态;热塑炼是向生胶中通入灼热的压缩空气,在热和氧的作用下,使长链分子降解变短,从而获得可塑性;四、混炼为了适应各种不同的使用条件、获得各种不同的性能,也为了提高橡胶制品的性能和降低成本,必须在生胶中加入不同的配合剂;混炼就是将塑炼后的生胶与配合剂混合、放在炼胶机中,通过机械拌合作用,使配合剂完全、均匀地分散在生胶中的一种过程;混炼是橡胶制品生产过程中的一道重要工序,如果混合不均匀,就不能充分发挥橡胶和配合剂的作用,影响产品的使用性能;混炼后得到的胶料,人们称为混炼胶,它是制造各种橡胶制品的半成品材料,俗称胶料,通常均作为商品出售,购买者可利用胶料直接加工成型、硫化制成所需要的橡胶制品;根据配方的不同,混炼胶有一系列性能各异的不同牌号和品种,提供选择;五、成型在橡胶制品的生产过程中,利用压延机或压出机预先制成形状各式各样、尺寸各不相同的工艺过程,称之为成型;成型的方法有:1.压延成型:适用于制造简单的片状、板状制品;它是将混炼胶通过压延机压制成一定形状、一定尺寸的胶片的方法叫压延成型;有些橡胶制品如轮胎、胶布、胶管等所用纺织纤维材料,必须涂上一层薄胶在纤维上涂胶也叫贴胶或擦胶,涂胶工序一般也在压延机上完成;纤维材料在压延前需要进行烘干和浸胶,烘干的目的是为了减少纤维材料的含水量以免水分蒸发起泡和提高纤维材料的温度,以保证压延工艺的质量;浸胶是挂胶前的必要工序,目的是为了提高纤维材料与胶料的结合性能;2.压出成型:用于较为复杂的橡胶制品,象轮胎胎面、胶管、金属丝表面覆胶需要用压出成型的方法制造;它是把具有一定塑性的混炼胶,放入到挤压机的料斗内,在螺杆的挤压下,通过各种各样的口型也叫样板进行连续造型的一种方法;压出之前,胶料必须进行预热,使胶料柔软、易于挤出,从而得到表面光滑、尺寸准确的橡胶制品;3.模压成型也可以用模压方法来制造某些形状复杂如皮碗、密封圈的橡胶制品,借助成型的阴、阳模具,将胶料放置在模具中加热成型;六、硫化把塑性橡胶转化为弹性橡胶的过程叫做硫化,它是将一定量的硫化剂如硫磺、硫化促进剂等加入到由生胶制成的半成品中在硫化罐中进行,在规定的温度下加热、保温,使生胶的线性分子间通过生成“硫桥”而相互交联成立体的网状结构,从而使塑性的胶料变成具有高弹性的硫化胶;由于交联键主要是由硫磺组成,所以称为“硫化”;随着合成橡胶的迅速发展,现在硫化剂的品种很多,除硫磺外,还有有机多硫化物、过氧化物、金属氧化物等;因此,凡是能使线状结构的塑性橡胶,转化为立体网状结构的弹性橡胶的工艺过程都叫硫化,凡能在橡胶材料中起“搭桥”作用的物质都称为“硫化剂”;硫化后的弹性橡胶叫硫化橡胶,又叫软橡胶,俗称“橡胶”;硫化是橡胶加工的一个最为重要的工艺过程,各种橡胶制品必须经过硫化来获得理想的使用性能;未经硫化的橡胶,在使用上是没有什么使用价值的,但欠硫硫化程度不够,硫化时间不够,未能达到最佳状态和过硫硫化时间超过、性能显着下降都使橡胶性能下降;所以生产过程中一定要严格控制硫化时间,以保证硫化后的橡胶制品具有最好的使用性能和最长久的使用寿命;七、辅助措施为了达到使用性能,还应在生产工艺中增加辅助措施:1.增加强度——配用硬质碳黑,掺用酚醛树脂;2.增加耐磨性——配用硬质碳黑;3.气密性要求高——少用挥发性高的组分;4.增加耐热性——采用新的硫化工艺;5.增加耐寒性——通过生胶的解枝镶嵌,降低结晶倾向,使用耐低温的增塑剂;6.增加耐燃性——不用易燃助剂、少用软化剂、使用阻燃剂如:三氧化锑;7.增加耐氧性、耐臭氧性——采用对二胺类防护剂;8.提高电绝缘性——配用高结构填充剂或金属粉,配用抗静电剂;9.提高磁性——采用锶铁氧粉,铝镍铁粉,铁钡粉等作填充剂;10.提高耐水性——采用氧化铅或树脂硫化体系,配用吸水性较低的填充剂如硫酸钡、陶土;11.提高耐油性——充分交联、少用增塑剂;12.提高耐酸碱度——多用填充剂;13.提高高真空性——配用挥发性小的添加剂;14.降低硬度——大量填充软化剂;八、橡胶制品的分类橡胶制品应用广泛,品种也很多;按照用途来分,通常分为工业用和民用两大类;工业用橡胶制品主要有:轮胎、胶带、胶管、胶版、胶布及胶布制品、密封件、减振件、胶乳制品、硬质橡胶制品、橡胶绝缘制品、胶辊以及橡胶衬里等;九、橡胶制品硫化的有关问题:1.橡胶制品硫化时产生哪些有毒气体橡胶的硫化过程中,采用烘箱半封闭式硫化,有的橡胶会有微量的有毒气体排出,能闻到很重的橡胶味;比如:一氧化硫、二氧化硫、三氧化硫、硫化氢气体,虽剧毒的东西基本上没有,但对人体肯定有害,有的产品硫化会产生致癌的东西,或者本身硫化前的橡胶就有致癌成分,最好少接触为好;橡胶硫化所采用的有机试剂或多或少对人体都是有害的;如二甲基苯等2. 一般橡胶的硫化温度是多少一般为115度到180度,看什么橡胶品种而定;而200度的温度则为高温硫化;3.二氧化硫的危害有哪些危险性类别:三星级侵入途径:通过呼吸系统健康危害:易被湿润的粘膜表面吸收生成亚硫酸、硫酸;对眼及呼吸道粘膜有强烈的刺激作用;大量吸入可引起肺水肿、喉水肿、声带痉挛而致窒息;急性中毒:轻度中毒时,发生流泪、畏光、咳嗽,咽、喉灼痛等;严重中毒可在数小时内发生肺水肿;极高浓度吸入可引起反射性声门痉挛而致窒息;皮肤或眼接触发生炎症或灼伤;慢性影响:长期低浓度接触,可有头痛、头昏、乏力等全身症状以及慢性鼻炎、咽喉炎、支气管炎、嗅觉及味觉减退等;环境危害:对大气可造成严重污染;。
天然橡胶生产工艺
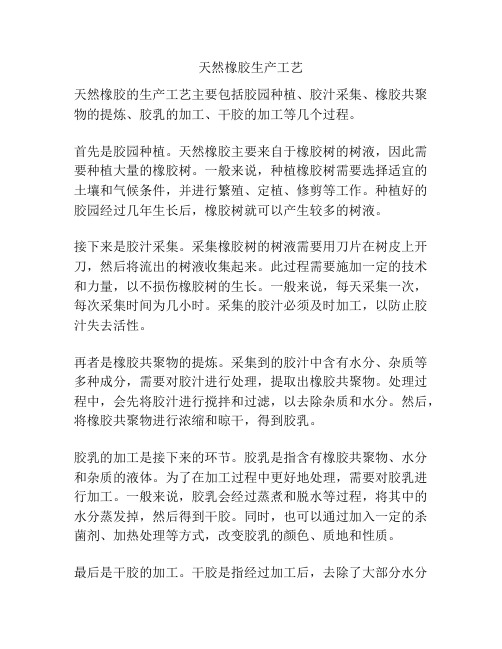
天然橡胶生产工艺天然橡胶的生产工艺主要包括胶园种植、胶汁采集、橡胶共聚物的提炼、胶乳的加工、干胶的加工等几个过程。
首先是胶园种植。
天然橡胶主要来自于橡胶树的树液,因此需要种植大量的橡胶树。
一般来说,种植橡胶树需要选择适宜的土壤和气候条件,并进行繁殖、定植、修剪等工作。
种植好的胶园经过几年生长后,橡胶树就可以产生较多的树液。
接下来是胶汁采集。
采集橡胶树的树液需要用刀片在树皮上开刀,然后将流出的树液收集起来。
此过程需要施加一定的技术和力量,以不损伤橡胶树的生长。
一般来说,每天采集一次,每次采集时间为几小时。
采集的胶汁必须及时加工,以防止胶汁失去活性。
再者是橡胶共聚物的提炼。
采集到的胶汁中含有水分、杂质等多种成分,需要对胶汁进行处理,提取出橡胶共聚物。
处理过程中,会先将胶汁进行搅拌和过滤,以去除杂质和水分。
然后,将橡胶共聚物进行浓缩和晾干,得到胶乳。
胶乳的加工是接下来的环节。
胶乳是指含有橡胶共聚物、水分和杂质的液体。
为了在加工过程中更好地处理,需要对胶乳进行加工。
一般来说,胶乳会经过蒸煮和脱水等过程,将其中的水分蒸发掉,然后得到干胶。
同时,也可以通过加入一定的杀菌剂、加热处理等方式,改变胶乳的颜色、质地和性质。
最后是干胶的加工。
干胶是指经过加工后,去除了大部分水分的胶乳。
这种胶乳在加工过程中,会进一步挤压、浸泡、烘干等处理,得到最终的生胶产品。
同时,也可以对干胶进行筛分和干燥,以得到符合要求的天然橡胶。
以上就是天然橡胶的生产工艺的一般步骤。
当然,不同厂家和地区可能会有一些细微的差别,但整体的生产过程是相似的。
经过这一系列的加工工艺,最终可以得到质量优良、性能稳定的天然橡胶产品。
橡胶工艺流程
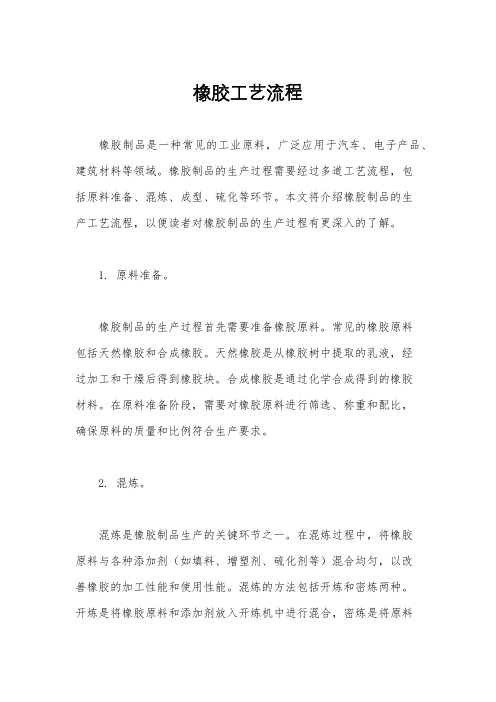
橡胶工艺流程橡胶制品是一种常见的工业原料,广泛应用于汽车、电子产品、建筑材料等领域。
橡胶制品的生产过程需要经过多道工艺流程,包括原料准备、混炼、成型、硫化等环节。
本文将介绍橡胶制品的生产工艺流程,以便读者对橡胶制品的生产过程有更深入的了解。
1. 原料准备。
橡胶制品的生产过程首先需要准备橡胶原料。
常见的橡胶原料包括天然橡胶和合成橡胶。
天然橡胶是从橡胶树中提取的乳液,经过加工和干燥后得到橡胶块。
合成橡胶是通过化学合成得到的橡胶材料。
在原料准备阶段,需要对橡胶原料进行筛选、称重和配比,确保原料的质量和比例符合生产要求。
2. 混炼。
混炼是橡胶制品生产的关键环节之一。
在混炼过程中,将橡胶原料与各种添加剂(如填料、增塑剂、硫化剂等)混合均匀,以改善橡胶的加工性能和使用性能。
混炼的方法包括开炼和密炼两种。
开炼是将橡胶原料和添加剂放入开炼机中进行混合,密炼是将原料放入密炼机中进行混合。
混炼过程需要控制时间、温度和压力,确保橡胶混合均匀。
3. 成型。
成型是将混炼后的橡胶料加工成所需形状的过程。
常见的成型方法包括挤出、压延和模压。
挤出是将橡胶料挤出成型,压延是将橡胶料通过压延机加工成片状,模压是将橡胶料放入模具中进行成型。
成型过程需要根据产品要求选择合适的成型方法,并控制温度、压力和速度,确保成型品质量符合要求。
4. 硫化。
硫化是橡胶制品生产的最后一个环节。
在硫化过程中,将成型后的橡胶制品放入硫化炉中进行硫化处理,使橡胶分子间发生交联,提高橡胶的强度和弹性。
硫化过程需要控制温度、压力和硫化时间,确保橡胶制品硫化均匀,达到设计要求的性能指标。
总结。
橡胶制品的生产工艺流程包括原料准备、混炼、成型和硫化四个主要环节。
每个环节都需要严格控制生产参数,确保橡胶制品的质量和性能符合要求。
同时,随着科技的进步,橡胶制品的生产工艺也在不断创新和改进,以满足不同领域对橡胶制品的需求。
希望本文能为读者对橡胶制品的生产工艺有所了解,并对橡胶制品的应用和发展有所启发。
橡胶制品生产工艺
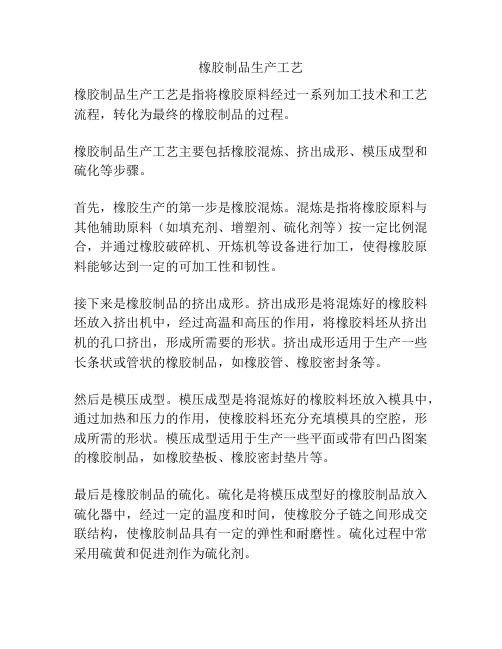
橡胶制品生产工艺
橡胶制品生产工艺是指将橡胶原料经过一系列加工技术和工艺流程,转化为最终的橡胶制品的过程。
橡胶制品生产工艺主要包括橡胶混炼、挤出成形、模压成型和硫化等步骤。
首先,橡胶生产的第一步是橡胶混炼。
混炼是指将橡胶原料与其他辅助原料(如填充剂、增塑剂、硫化剂等)按一定比例混合,并通过橡胶破碎机、开炼机等设备进行加工,使得橡胶原料能够达到一定的可加工性和韧性。
接下来是橡胶制品的挤出成形。
挤出成形是将混炼好的橡胶料坯放入挤出机中,经过高温和高压的作用,将橡胶料坯从挤出机的孔口挤出,形成所需要的形状。
挤出成形适用于生产一些长条状或管状的橡胶制品,如橡胶管、橡胶密封条等。
然后是模压成型。
模压成型是将混炼好的橡胶料坯放入模具中,通过加热和压力的作用,使橡胶料坯充分充填模具的空腔,形成所需的形状。
模压成型适用于生产一些平面或带有凹凸图案的橡胶制品,如橡胶垫板、橡胶密封垫片等。
最后是橡胶制品的硫化。
硫化是将模压成型好的橡胶制品放入硫化器中,经过一定的温度和时间,使橡胶分子链之间形成交联结构,使橡胶制品具有一定的弹性和耐磨性。
硫化过程中常采用硫黄和促进剂作为硫化剂。
在整个橡胶制品生产工艺中,还需要进行一些后续工序,如去毛刺、修整、细修等,以确保橡胶制品的质量和外观。
总的来说,橡胶制品生产工艺涉及到橡胶混炼、挤出成形、模压成型和硫化等多个步骤,每个步骤都需要通过相应的设备和工艺流程进行加工。
橡胶生产工艺流程介绍
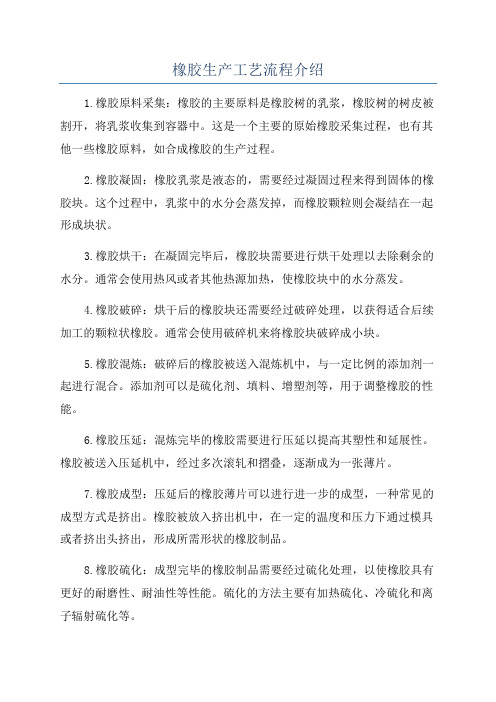
橡胶生产工艺流程介绍1.橡胶原料采集:橡胶的主要原料是橡胶树的乳浆,橡胶树的树皮被割开,将乳浆收集到容器中。
这是一个主要的原始橡胶采集过程,也有其他一些橡胶原料,如合成橡胶的生产过程。
2.橡胶凝固:橡胶乳浆是液态的,需要经过凝固过程来得到固体的橡胶块。
这个过程中,乳浆中的水分会蒸发掉,而橡胶颗粒则会凝结在一起形成块状。
3.橡胶烘干:在凝固完毕后,橡胶块需要进行烘干处理以去除剩余的水分。
通常会使用热风或者其他热源加热,使橡胶块中的水分蒸发。
4.橡胶破碎:烘干后的橡胶块还需要经过破碎处理,以获得适合后续加工的颗粒状橡胶。
通常会使用破碎机来将橡胶块破碎成小块。
5.橡胶混炼:破碎后的橡胶被送入混炼机中,与一定比例的添加剂一起进行混合。
添加剂可以是硫化剂、填料、增塑剂等,用于调整橡胶的性能。
6.橡胶压延:混炼完毕的橡胶需要进行压延以提高其塑性和延展性。
橡胶被送入压延机中,经过多次滚轧和摺叠,逐渐成为一张薄片。
7.橡胶成型:压延后的橡胶薄片可以进行进一步的成型,一种常见的成型方式是挤出。
橡胶被放入挤出机中,在一定的温度和压力下通过模具或者挤出头挤出,形成所需形状的橡胶制品。
8.橡胶硫化:成型完毕的橡胶制品需要经过硫化处理,以使橡胶具有更好的耐磨性、耐油性等性能。
硫化的方法主要有加热硫化、冷硫化和离子辐射硫化等。
9.橡胶终检:硫化后的橡胶制品需要进行终检,检查其外观质量、尺寸是否符合要求。
一般是通过目检、拉伸测试、硬度测试、水密度测试等方法进行。
10.橡胶包装和储存:通过终检合格的橡胶制品进行包装,常见的包装方式有纸箱、托盘和编织袋等。
包装完毕后,橡胶制品需要进行储存,储存条件对于橡胶制品的质量和使用寿命至关重要。
以上就是一种常见的橡胶生产工艺流程介绍。
橡胶的生产过程涵盖了原料采集、凝固、烘干、破碎、混炼、压延、成型、硫化、终检和包装储存等环节,每个环节都有其特定的工艺要求。
随着技术的进步,橡胶生产工艺也在不断演变和改进,以提高橡胶制品的质量和性能。
橡胶生产工艺流程

橡胶生产工艺流程橡胶生产工艺流程主要包括原料准备、混炼、模压、硫化等环节。
以下是一个大致的橡胶生产工艺流程。
首先是原料准备环节。
橡胶的主要原料有天然橡胶和合成橡胶,此外还需要添加剂如促进剂、防老化剂、增塑剂等。
原料需要按照一定的配方比例加入到生产设备中。
接下来是混炼环节。
混炼是指将原料进行机械拌和工艺,使其在一定温度条件下充分混合,同时提高橡胶的弹性和可塑性。
混炼一般分为开炼和密炼两个阶段。
开炼时将橡胶原料与一些添加剂加入到混炼机中,通过转动的刀叶将原料进行充分切割、破碎,使之达到均匀分散的目的。
密炼则是在开炼的基础上,进一步加入剂料进行混炼,使橡胶获得更好的塑胶性态。
然后是模压环节。
模压是将混炼好的橡胶放入到模具中,经过加热和压力作用,使橡胶在模具中变形成所需的形状。
模压通常采用加热板式压力机,通过加热板的加热和模具的压力,使橡胶在短时间内完成硫化反应,达到所需的硬度和强度。
最后是硫化环节。
硫化是指将已经成型的橡胶制品加热到一定温度,在一定时间内与硫化剂发生化学反应,使橡胶分子中的交联结构增加,从而提高橡胶的强度和耐磨性。
硫化过程一般分为热硫化和冷硫化两种形式。
热硫化是将橡胶制品放入加热箱中进行硫化,冷硫化则是在室温下进行硫化。
硫化时间和温度需要根据橡胶的种类和产品的要求进行调整。
整个橡胶生产工艺流程需要严格控制各个环节的参数和工艺要求,以确保橡胶制品的质量和性能。
同时,还需要注意生产中的环境保护和能源消耗,采取相应的措施减少污染和资源浪费。
总结起来,橡胶生产工艺流程主要包括原料准备、混炼、模压和硫化。
在这个流程中,需要控制好每个环节的参数和工艺要求,以确保橡胶制品的质量和性能。
橡胶使用的成型工艺有
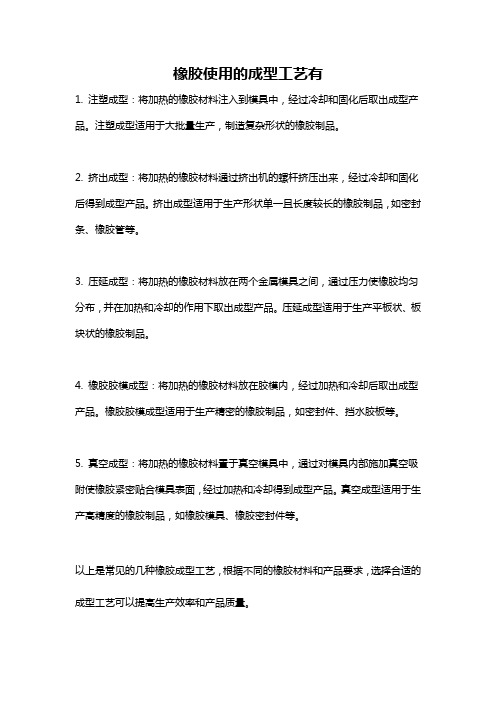
橡胶使用的成型工艺有
1. 注塑成型:将加热的橡胶材料注入到模具中,经过冷却和固化后取出成型产品。
注塑成型适用于大批量生产,制造复杂形状的橡胶制品。
2. 挤出成型:将加热的橡胶材料通过挤出机的螺杆挤压出来,经过冷却和固化后得到成型产品。
挤出成型适用于生产形状单一且长度较长的橡胶制品,如密封条、橡胶管等。
3. 压延成型:将加热的橡胶材料放在两个金属模具之间,通过压力使橡胶均匀分布,并在加热和冷却的作用下取出成型产品。
压延成型适用于生产平板状、板块状的橡胶制品。
4. 橡胶胶模成型:将加热的橡胶材料放在胶模内,经过加热和冷却后取出成型产品。
橡胶胶模成型适用于生产精密的橡胶制品,如密封件、挡水胶板等。
5. 真空成型:将加热的橡胶材料置于真空模具中,通过对模具内部施加真空吸附使橡胶紧密贴合模具表面,经过加热和冷却得到成型产品。
真空成型适用于生产高精度的橡胶制品,如橡胶模具、橡胶密封件等。
以上是常见的几种橡胶成型工艺,根据不同的橡胶材料和产品要求,选择合适的成型工艺可以提高生产效率和产品质量。
橡胶生产工艺流程介绍

橡胶生产工艺流程介绍首先,原料处理阶段,生产商需要将橡胶原料进行清洗和干燥处理,以确保原料的质量和干净程度。
接下来是混炼阶段,将橡胶和各种添加剂(例如硫化剂、填料、增塑剂等)混合在一起,通过橡胶研磨机或橡胶硫化机进行混合、研磨和加热,使各种添加剂充分分散,从而得到均匀的胶料。
然后是挤出和成型阶段,通过挤出机或压延机将混炼好的橡胶料挤出成所需的形状,或者放入模具中进行成型,以得到符合产品要求的各种橡胶制品。
接着是硫化阶段,橡胶制品需要在硫化炉中进行硫化处理,以使橡胶分子交联,提高产品的力学性能和耐热性能。
最后是包装阶段,经过严格的质量检验后,橡胶制品进入包装环节,以便于存储和运输。
总的来说,橡胶生产工艺流程是一个复杂的过程,需要严格控制各个环节的工艺参数和质量要求,才能生产出高质量的橡胶制品。
橡胶生产工艺流程是一个系统工程,需要严格控制原料的质量、混炼的工艺参数、硫化温度和时间等关键因素,才能确保最终产品的质量和性能。
下面我们来详细介绍一下橡胶生产的工艺流程。
首先是原料处理阶段。
橡胶的生产原料主要包括天然橡胶和合成橡胶。
天然橡胶是从橡胶树的橡胶乳中提取而来,合成橡胶是通过化学合成的方法获得。
在原料处理阶段,首先对原料进行清洗和干燥处理,以确保原料的质量和干净程度。
天然橡胶需要经过挤薄机、洗涤机等设备进行初步加工,去除杂质,保证原料的纯净度和质量。
合成橡胶在原料处理阶段主要进行物理或化学法的分散处理,以增加其可加工性和混炼性。
原料处理的环节需要控制原料的含水率、杂质含量和颗粒度,以确保后续生产的正常进行。
接下来是混炼阶段。
在混炼阶段,橡胶和各种添加剂(例如硫化剂、填料、增塑剂等)混合在一起,通过橡胶研磨机或橡胶硫化机进行混合、研磨和加热,使各种添加剂充分分散,从而得到均匀的胶料。
混炼的目的是使各种添加剂与橡胶充分融合,确保橡胶混合料具有一定的塑性和流动性,便于后续挤出和成型。
然后是挤出和成型阶段。
在这个阶段,混炼好的橡胶料通过挤出机或压延机进行挤出成所需的形状,或者放入模具中进行成型,以得到符合产品要求的各种橡胶制品。
橡胶生产工艺流程

橡胶生产工艺流程橡胶是一种重要的工业原料,广泛应用于汽车制造、建筑材料、医药等领域。
橡胶的生产工艺流程主要包括原材料采集、橡胶制备、混炼和成型四个步骤。
下面将详细介绍橡胶的生产工艺流程。
首先,原材料采集。
橡胶主要由橡胶树提供,并通过采集树液进行生产。
采集树液的过程被称为橡胶脱液,通常在早晨的时候进行。
工人会将树液从树干上切口处采集到集液器中,然后将橡胶脱水、净化并过滤。
然后是橡胶制备。
采集到的橡胶树液需要进行初步净化、干燥和固化,以去除杂质并变为固体状。
首先,将橡胶树液加热,使其变为胶态,并加入草木灰和石灰等材料进行固化。
然后,将固化后的橡胶进行蒸煮和搅拌,以增加其硫化性能和可塑性。
最后,经过冷却和干燥处理,得到成品橡胶。
接下来是混炼。
混炼是将橡胶与其他添加剂进行混合,以改善橡胶的性能和加工性。
首先,将橡胶放入混炼机中进行预热和破碎,使其变得柔软易塑。
然后,加入加工助剂、加硫剂、硫化剂等,进行搅拌和混合。
混炼的目的是使橡胶与添加剂充分融合,并达到所需的硬度、弹性和抗老化等性能。
最后是成型。
将混炼好的橡胶通过挤出机或压延机进行成型。
挤出机是将橡胶通过模具挤压成型,可以得到各种形状和尺寸的橡胶制品。
压延机是将橡胶通过辊筒压延成型,可以制造橡胶片、橡胶带等。
需要注意的是,橡胶的生产工艺还需考虑到橡胶的硫化。
硫化是橡胶加工的关键步骤,通过加热和加压使橡胶与硫化剂反应,形成交联结构,提高橡胶的强度、耐磨性和耐老化性能。
综上所述,橡胶的生产工艺流程包括原材料采集、橡胶制备、混炼和成型四个步骤。
每个步骤都起着重要的作用,决定了成品橡胶的质量和性能。
随着科技的进步,橡胶的生产工艺也在不断创新和改进,以提高生产效率和产品质量。
橡胶生产工艺介绍

橡胶生产工艺介绍橡胶是一种高分子合成材料,常用于制作各种工业、农业、医疗和消费品。
橡胶生产工艺是一个复杂的过程,需要经过多个步骤来实现。
这篇文章将介绍橡胶生产的工艺流程,包括橡胶的采集、质检、清洗、磨碎、加工、成型和包装等。
一、橡胶的采集橡胶是从橡胶树中获取的,主要产地包括东南亚、巴西和非洲。
在采集橡胶前,需要先确定合适的收割时间和方法。
一般情况下,待橡胶树树龄达到5-6年左右,橡胶树皮的厚度就足以支撑后续的产量,此时开始采集橡胶。
采集时,工人会在橡胶树的树干上切开一道深约5毫米的伤口,通过汁液自然流出的方式采集橡胶乳液。
一般需要在早晨采集,在下午之前完成采集工作,以保证橡胶树干恢复的时间。
二、橡胶的质检采集到橡胶之后,需要进行质检,以确定橡胶质量是否达到生产要求。
质检的主要方法是通过利用比重仪来测定橡胶和水的比重差异,进而计算出橡胶含量。
通常,含橡胶量在30%以上的橡胶乳液可以用于生产。
三、橡胶的清洗清洗橡胶的目的是去除掉污垢、树皮、杂质等杂物,以保证后续步骤的质量。
橡胶的清洗需要使用水和清洗剂。
清洗时,将橡胶放入清洗槽内,加入适量的清洗剂,并采用机械搅拌的方式,帮助去除杂质。
四、橡胶的磨碎橡胶磨碎是将橡胶乳液进行粉碎的过程,以便于后续加工。
通常采用的是球磨机、开放式磨机或密封式磨机进行磨碎。
在磨碎过程中,橡胶需要与磨球进行反复碾磨,直至粉碎成小颗粒。
五、橡胶的加工橡胶加工是将磨碎的橡胶小颗粒转变成橡胶制品的过程。
橡胶加工主要包括混炼、挤出、模压和酸洗等步骤。
1、混炼:混炼是将磨碎的橡胶颗粒与橡胶加工助剂(如硫化剂、促进剂和补强剂等)混合在一起的过程。
混炼可以使橡胶颗粒更好地分散,并加快硫化反应速度。
2、挤出:挤出是将混炼好的橡胶用挤出机进行挤压,形成一定的形状。
通常,挤压的形状是条形、圆形或方形等。
3、模压:模压是将挤压好的橡胶进行压制、成型的过程。
常用的压制方法包括挤压成型、注塑成型、压延成型等。
橡胶加工工艺流程

橡胶加工工艺流程橡胶加工是将天然橡胶或合成橡胶进行加工处理,制成各种橡胶制品的过程。
橡胶制品广泛应用于汽车、电子、医疗、建筑等领域,因此橡胶加工工艺的质量和效率对产品质量和生产成本有着重要影响。
下面将介绍橡胶加工的工艺流程。
1. 橡胶混炼。
橡胶混炼是橡胶加工的第一步,其目的是将橡胶与各种添加剂充分混合均匀。
混炼过程中需要将橡胶与填料、增塑剂、硫化剂等添加剂放入橡胶混炼机中,通过机械剪切和翻转,使各种添加剂均匀分散在橡胶中,形成均匀的混炼胶料。
2. 压延。
混炼后的橡胶胶料需要通过压延机进行压延,将其压成一定厚度的橡胶片。
压延机通过辊子的旋转将橡胶胶料不断压延,使其变得更加均匀、平整。
压延后的橡胶片可根据需要进行裁切或进一步加工。
3. 模压。
模压是将橡胶片通过模具加工成各种形状的橡胶制品的过程。
在模压过程中,橡胶片被放入模具中,经过一定的温度和压力作用下,形成所需的产品形状。
模压是橡胶加工中非常重要的一步,决定了最终产品的形状和尺寸精度。
4. 硫化。
硫化是橡胶加工中最关键的一步,通过硫化可以使橡胶获得良好的物理性能。
硫化过程中,橡胶制品放入硫化炉中,加热至一定温度,并在一定时间内进行硫化处理。
硫化可以使橡胶分子链发生交联,增强橡胶的强度、弹性和耐磨性。
5. 表面处理。
部分橡胶制品需要进行表面处理,以提高其外观质量和耐用性。
表面处理可以包括喷涂、印刷、抛光等工艺,使橡胶制品表面光滑、均匀,并且具有一定的装饰效果。
6. 检验与包装。
最后一步是对橡胶制品进行检验和包装。
检验包括外观质量、尺寸精度、物理性能等多个方面的检测,确保产品符合质量标准。
通过包装将橡胶制品进行包装,以便运输和销售。
综上所述,橡胶加工工艺流程包括混炼、压延、模压、硫化、表面处理、检验与包装等多个环节。
每个环节都需要严格控制,以确保最终产品的质量和性能。
随着橡胶工艺技术的不断发展,橡胶制品的品种和质量将会得到进一步提升,满足不同行业的需求。
- 1、下载文档前请自行甄别文档内容的完整性,平台不提供额外的编辑、内容补充、找答案等附加服务。
- 2、"仅部分预览"的文档,不可在线预览部分如存在完整性等问题,可反馈申请退款(可完整预览的文档不适用该条件!)。
- 3、如文档侵犯您的权益,请联系客服反馈,我们会尽快为您处理(人工客服工作时间:9:00-18:30)。
一、老化胶现状:橡胶表面有明显的老化胶原因:1,模具行腔内飞边未清理干净
二、分层、胶料堆积
异常缺陷:
硫化后产品分型处胶料堆积、分层,且内孔烂泡
原因分析:
1,产品烂泡造成的原因
1)因为此产品烂泡部位是下端内孔,而下模恰恰没有可排气的孔,从而造成产品窝气。
2,产品分型处胶料堆积、分层的原因。
1)模具结构原因,因为此模具是内哈夫外加框(封闭)结构,注料时多余胶料不能充分流出;
2)堆积处的分型旁的余料槽过窄过浅,这样胶料过大极易造成胶料堆积到产品表面。
解决措施:
1,修理模具
2,减少胶料使用量
烫坏:产品表面有明显胶烧现象;
烫坏常见产生原因:
(1)骨架烫坏导致产品脱胶;
(2)平板机上料时间过长;
撕缺常见产生原因:
(1)脱模速度过快;导致产品带缺;
(2)胶料本身撕裂性较差;
(3)脱模器具及模具结构设计不当;
气泡产生的原因及解决方法
气泡:表现为减震器橡胶体表面存在体积较大的气泡。
原因分析
制品硫化不充分,导致橡胶制品表面有大气泡,割开其内部呈蜂窝海绵状
解决方法
①延长硫化时间,提高硫化温度
②保证硫化时有足够的压力
③调整配方,提高硫化速度
裂口:产品的内外表面或其它表面有明显裂纹;
老化胶:产品表面有明显似烫坏和烂泡现象的产品;
气泡:产品表面有明显突起呈线状
烂泡:产品表面有明显圆形疮状痕迹;
分层:产品橡胶部位不能形成一个整体,呈现出有层次的现象;
模脏:产品表面有明显的光洁度不够;
杂质:与胶料不融合,在产品上显出不同颜色或明显的异物
烫坏:产品表面有明显胶烧现象;
单边:产品表面除图纸要求外,对称部位出现倾斜,一边多、一边少或一边有一边无。
如切口的上端面有明显的一边宽大,一边宽度小,壁厚不均匀;
生锈:产品骨架表面有锈蚀现象;
尺寸不合格:产品尺寸明显不符合图纸要求,且不可以代用;
变形:产品形状发生变更,与图纸要求不一致;
撬坏:产品表面有明显脱模时产生的裂口,骨架变形等;
压坏:产品表面明显有受压痕迹;
脱胶:产品胶料与骨架分开,不能粘合在一起
缺陷1:内孔烂泡
缺陷2:烂泡
缺陷3:烫伤、老化胶
c:\iknow\docshare\data\cur_work\\showpic.html - blogid=674a94d90100i531&url=
缺陷4:磷化后表面挂灰
c:\iknow\docshare\data\cur_work\\showpic.html - blogid=674a94d90100i531&url=
缺陷5:模具结构不合理
c:\iknow\docshare\data\cur_work\.cn\showpic.html -
blogid=674a94d90100i531&url=/orignal/674a94d9t84dbf438b557
缺陷6:缺料
缺陷7:RC破坏-脱胶
缺陷8:脱胶-RC破坏
缺陷9:脱胶-MC破坏
c:\iknow\docshare\data\cur_work\\showpic.html - blogid=674a94d90100i531&url=缺陷10:粘合剂脱落
2222
异常现状:
RC破坏
原因分析:
1、模具压力不足温度不够;
2、硫化条件不当;
3、粘接剂太薄;
4、粘接剂选择不当;
5、稀释不当未搅拌均匀;
6.骨架、胶料污染;
7、胶料混炼不均匀;
下为堆积胶
异常缺陷:
硫化后产品分型处胶料堆积原因分析:
1,模具结构原因,
2,单耗大造成
产品橡胶内部气孔
1,现状:橡胶解剖后橡胶致密性差,呈现较多针孔状气孔
2,引起原因:
1)欠硫造成,即为硫化深度不透彻,或者温度低、或者硫化时间短造成
2)硫化压力小造成
工艺稳定性差、生产异常多;
管理思路:工艺验证、数据收集
产品的质量需要稳定的生产工艺支持,而稳定的生产工艺需要强有力的数据支持,而我们橡胶减震产品的主要特性是耐久、粘接和耐盐雾等,所以我们工艺其中的一大职责就是工艺验证:1)验证前处理粘接工艺(如骨架存放周期、粘合剂粘度及喷涂厚度等等,),其中涂完粘合剂的骨架存放周期验证工作正在进行,;2)加强产品的硫化工艺的验证,保证产品的性能和硫化深度;3)油漆附着力、耐盐雾效果验证,
橡胶表面发粘
橡胶表面发粘表现为产品橡胶部分表面存在海绵状或明显的粘性突起物。
其产生的原因及解决方法如下
原因分析解决方法
1 模具型腔局部滞留气体,从而影响传热和胶料受热硫化①对模具进行抽真空,
②增加j排气次数
③增加排气槽或余料槽
2 模具结构原因,硫化不充分延长硫化时间或提高硫化温度
3 某些橡胶过于正硫化点,反原重新验证硫化参数,找取合理的硫化点
产品:波纹管、进气管、排气管吊件等现状:产品脱模时易将产品脱破,或表面有明显裂开
原因分析:
1、易破处模具分型不会,分型处由毛刺
2、温度过高、硫化时间过长
3、脱模方法不当
脱胶原因
异常描述:
MC破坏
造成底胶脱的原因有:
1,骨架处理时,骨架表面污染;
2,底胶固化未彻底。
夹布溢出
异常描述:硫化后产品内部夹布溢出
原因分析:
1,模具结构原因
……………………………………………………………最新资料推荐…………………………………………………2,排气造成
3,操作原因
产品橡胶内部气孔
1,现状:橡胶解剖后橡胶致密性差,呈现较多针孔状气孔
2,引起原因:
1)欠硫造成,即为硫化深度不透彻,或者温度低、或者硫化时间短造成
2)硫化压力小造成
最新精品资料整理推荐,更新于二〇二一年一月二十二日2021年1月22日星期五19:23:23。