振动切削加工技术
实用化振动切削技术——振动研磨去毛刺及表面光整
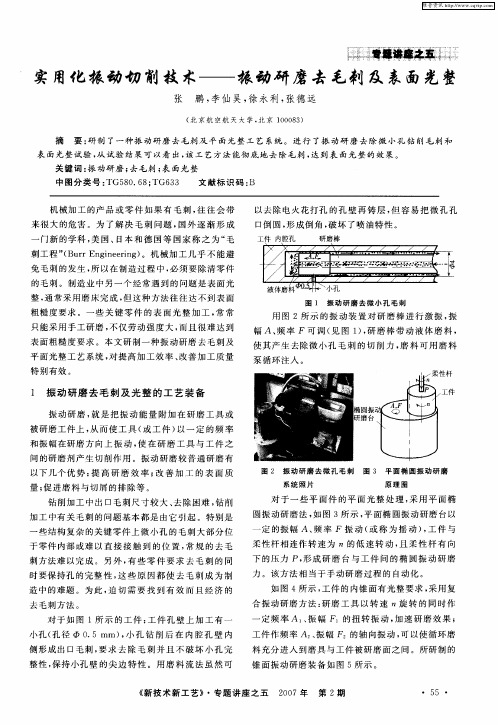
量 ; 进磨料 与切 屑 的排 除等 。 促
钻 削加工 中出 口毛 刺尺 寸较 大 、 除 困难 , 去 钻削 加 工 中有 关 毛刺 的问题 基本 都是 由它 引起 。特别 是
一
系统 照 片
原理 图
20 0 7年 第 2 期
・5 ・ 5
维普资讯
要求 。
环 液 磨 料 a 研 磨 前 1 b 研 磨 后 )
图 4 锥面振 动研 磨原 理 图 图 5 锥 面振 动研磨 系统照 片
图 7 椭 圆振 动研 磨 平 面 的前 后 对 比照 片
刺工 程” B r E gn eig 。机 械 加工 几乎 不 能避 ( u r n ier ) n
免 毛刺的 发生 , 以在 制造 过程 中, 所 必须要 除 清零件
的毛 刺 。制造业 中另 一个 经常遇 到 的 问题 是 表面光 整 , 常采用 磨床 完成 , 这种 方法往 往达 不 到表 面 通 但
图 1 振 动 研 磨 去 微 小 孑 毛 刺 L
粗糙度 要求 。一 些关 键 零 件 的 表 面光 整 加 工 , 常 常
只能采 用手 工研磨 , 不仅 劳 动强度 大 , 而且很 难 达到 表面粗 糙度要 求 。本文研 制 一种振 动研 磨 去毛刺 及 平 面光 整工艺 系统 , 对提 高加 工效 率 、 改善加 工质 量 特别有 效 。
2 振 动 研磨 去 微 小 孑 毛 刺及 平面 光 整 的 工 L
艺 效 果
采用 刺 进 行 研 磨 , 验 条 件 : 件 材 料 为 不 锈 钢 试 工 1 r8 9 ; 料 为 Alo 粉 , 水 凋合 ; 磨 棒 激 C 1 NiTi 磨 :。 加 研 振 的频 率 F=2 , 幅 A=0 4 mm; 件 研 磨 O Hz 振 . 单 ( 实用 系统 为批 量 研 磨 ) 间小 于 1 n 时 5mi 。研 磨 前 后 的孔 口毛刺 对 比照 片如 图 6所 示 , 磨后 的孔 口 研 毛刺 已完全 去除 , 且保持 了孔 口的锐 边 ( 无倒 角 ) 。
浅析机械加工中的切削加工及切削颤振

浅析机械加工中的切削加工及切削颤振切削制造是机器制造中的一种关键技术措施,切削制造品质针对机器制造的商品品质具有重大的作用。
切削颤振对切削制造商品品质以及措施有着严重的影响。
文章主要联合机器制造中切削制造的技术措施,从切削制造在机器制造中的用途和切削制造关注事项等,同时针对切削制造中的切削颤振及其带来的损坏、掌控技术等开展解析讨论,以完成针对机器制造中切削制造与切削颤振的解析探索,提升切削制造措施,确保切削制造商品品质。
标签:机械加工;切削加工;切削颤振;产品质量切削制造是机器制造业内一种关键的制造措施,切削制造不光在机器制作制造行业中有所使用,在电机还有电子等新式现代化设备的制造中也能够使用,同时其用途在这些行业的制造与行业前进都有着关键的用途。
在开展机器切削制造程序中,针对切削制造的措施与制造品质有着关键的用途,撇开开展切削制造使用的机器切削机床,开展切削制造运用的刀具同时也是切削制造的重点。
下面就联合机器切削制造的技术程序,重点的对切削制造中刀具的关键性与刀具的选用展开研究,同时对切削制造中会存在的切削颤振以及其带来的作用和掌控手段开展解析研究。
1 机械加工中的切削加工分析1.1 切削加工在机械加工生产中的重要作用在机器制造程序中,开展机器制造的零件商品,大都是生产行业制造中关键制造的配件。
一般来讲,开展机器零配件的制作程序中,针对机器零配件的制作技术方式,大多是铸造与锻造,亦或是焊接,这些机器制造技术方式关键是在机器零配件商品的半成品制作。
伴随着机器制造技术措施的持续提升,在开展机器商品的制造程序中,制造手段也随之前进,例如,精铸造与精锻造制造技术等,都能够采用来开展机器零配件商品毛坯的制作使用中。
除此之外,在机器制作制造中,迅速原型生产技术,也是开展机器零配件模子生产中经常使用的技术方式,一般来讲,经常和别的机器生产制作措施一起使用,在机器商品的制作制造中使用。
在开展机器商品的生产制作中,除了会运用到经常见的切削以及磨削技术,还能够运用到激光束、电化学、电子束等机器生产技术,在这些机器制造技术中,切削技术是机器生产制作中最经常使用到的同时也是最基本的制作措施之一。
切削加工以及切削颤振简述

切削加工以及切削颤振简述切削加工作为机械制造行业的传统生产加工工艺,是机械制造的流程中完成零件制作这一中心环节的重要生产技术,文章介绍了切削加工的基本方法,切削加工使用的刀具以及切削过程中产生的切削颤振和相应的控制方法。
标签:切削加工;切削;颤振切削加工是机械加工产品生产过程中必要而又值得信赖的技术手段,这一技术手段为了能够跟上市场需求的不停改变,对切削工具提出了新的要求,而切削刀具日新月异的发展又促使切削加工成为机械产品加工众多环节中备受关注的生产步骤。
在切削加工过程中,也存在着大大小小的问题等待着我们去发现和总结,其中切削颤振就加工生产的主要问题之一,对切削颤振有一个细致的认识,进而采取一定的手段对其实施加工控制,是我们一直探索的科研课题。
1 切削加工概述1.1 切削加工概念在机械产品加工生产过程中,按照产品生产规格、质量、工艺等要求,技术人员需要利用合适的切削工具对选取材料进行切割塑形,这一加工生产程序被称作为切削加工。
1.2 切削加工的要素满足切削加工的要拥有生产的三个重要因素,切屑刀具、切削运动和切削角度。
简单的说,刀具就是进行机械生产加工的重要切割工具;刀具与被切割材料的相对运动,就是切削运动;刀具自身固有、安装以及切割金属时所参照的切割偏角数据,也就是切削角度。
由于刀具是直接接触产品表面的生产工具,产品的表面微观粗糙程度,大小精确程度和外形都主要取决于刀具,所以刀具自身材料的硬度、柔韧度、抗腐蚀能力以及生产加工质量工艺等一系列的问题都会对切削加工机床的生产速度、产品质量、以及机床的使用寿命造成不可忽视的影响,进而影响到机械生产加工行业的技术整体水平,还会涉及到生产厂家的刀具生产信誉和使用刀具造成的经济损失。
切削加工过程中,刀具对产品会产生一定的作用力,根据物体受力原理,会有相应的反作用力的产生,力的相互作用会给刀具带来一定的损耗,造成刀具固有角度的几何参数发生改变,从而对被加工产品产生影响。
振动切削加工技术

• 振动切削的分类
按振动质量:自激振动切削和强迫振动切削
按刀具振动方向:吃刀抗力方向、进给抗力 方向、主切削方向 按所加频率:高频振动和低频振动
• 普通切削与振动切削的对比
-------普通切削中,切削靠刀具与工具的相对 运动来完成。产生较大切削力,使刀具磨损、 产生切削振动的有害现象。 --------振动切削中,在切削刀具上施加某种有 规律的可控的振动,使切削速度、切削深度 产生周期性的改变,从而使切削力减小、切 削热降低。
• 振动切削的特点
1、切削力大大减小 2、切削温度明显降低 3、切削液的作用得到了充分发挥 4、可提高刀具使用寿命 5、可控制切屑的形状和大小 6、提高加工精度和表面质量 7、可提高已加工表面的耐磨性和耐蚀性
• 振动切削技术的应用
1、难切削材料的加工。如:不锈钢、钛合金、 陶瓷、玻璃等采用超声振动切削来大大降低加 工难度;加工石墨与氧化铝等材料只有采用超 声振动才能产生微粒式的切削分离得到整齐的 加工表面
金刚石刀具可以切削含铁工件
振动切削加工技术
振动加工技术是从20世纪60年代发展起来的 一种优于普通切削的先进的制造技术。
• 它通过在常规的切削刀具上施加高 频振动,使刀具和工件发生间断性 的接触。改变了工件与刀具之间的 时间与空间分配,从而改变了切削 加工机理达到了减小切削力和切削 热并提高加工质量和效率的目的。
2、难加工零件的切削加工
如易弯曲变形的细长杆类零件、薄壁零件、排屑断屑比较困难的切削加工 如用于钻孔、饺孔、攻丝、拉削等
Thank you!
超声加工及振动切削
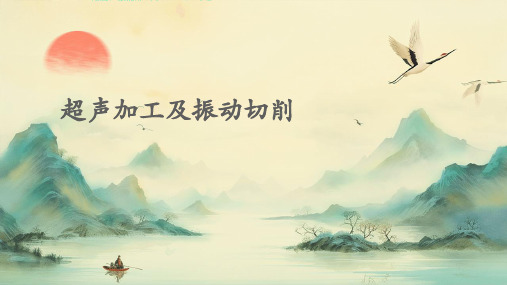
精密零件的加工
如微小型零件、复杂曲面 零件等需要高精度加工的 零件。
难加工环境的加工
如高温、高压、真空等极 端环境下的加工。
04
超声加工与振动切削的比较
工作原理的比较
超声加工
利用超声波的振动能量对工件进行加工,通过工具的快速振动,使工件表面材 料在工具的作用下产生局部高温、高压,使材料发生变形、破碎或去除。
应用领域的比较
超声加工
广泛应用于玻璃、陶瓷、石英等 硬脆材料的加工;在珠宝、钟表 制造等领域也有广泛应用。
振动切削
广泛应用于各种金属材料的加工 ,如汽车、航空、机械制造等领 域;在难加工材料的加工方面也 有一定应用。
05
超声加工与振动切削的发展趋势和未
来展望
超声加工的发展趋势和未来展望
高效化
随着工业生产对加工效率 的要求不断提高,超声加 工技术将不断优化,实现 更高效、更快速的生产。
振动切削的基本原理是利用振动系统产生的周期性弹性力,使刀具在切削过程中产生快速的 往复运动,从而实现对工件的加工。
振动切削过程中,刀具的振动频率和振幅对加工效果具有重要影响,需要根据不同的加工要 求进行合理选择。
振动切削的主要技术
超声振动切削
利用超声波的振动能量对工件进行加工,具有加工精度高、表面 质量好、适用于各种难加工材料等特点。
智能振动切削
结合人工智能和振动切削技术,实 现智能控制和自适应调整,提高加 工精度和效率。
多轴振动切削
研究多轴振动切削技术,实现复杂 形状和高精度零件的加工。
交叉学科的研究和应用前景
超声加工与振动切削的结合
01
研究超声加工与振动切削的结合技术,发挥各自的优势,提高
加工效率和精度。
切削加工振动及其控制技术

1
切削加工振动分类及其危害分析
2
强迫振动
3自激震动ຫໍສະໝຸດ 4切削加工振动控制技术
什么是强迫振动 强迫振动?
Company Logo
由外界持续激振力引起和 维持的振动。当然除了激 振力,随着切削时间的变 化,位移、速度及加速度 也可以激起工艺系统的 振动
强迫振动特点
强迫振动特点
NUAA
强迫振动的稳态过程 为简谐振动
个简谐强迫振动。
其振动方 程
NUAA
目录
1
切削加工振动分类及其危害分析
2
刺激振动
3
自激震动
4
切削加工振动控制技术
什么是自激振动 自激振动?
Company Logo
在没有外力周期性的作用 下,由工艺系统内部激发 及反响的相互作用而产生 的周期性振动,称为自激 振动。
自激振动产生原理
Company Logo
NUAA
自激振动的控制方法
振动痕迹深而宽
自激振动
NUAA
高频振动
500—5000Hz 噪声锋利刺耳 振动痕迹细而密
NUAA
支持自激振动的三种力
1
2
3
车刀前面与切屑, 后面与加工外表间 的变动摩擦力
当车刀在波形外表 运动由于切去横断 面积周期性变化引 起的变动力。
当振动时刀具原有 几何形状改变引起 的变动力。
NUAA
索引
1
强迫振动的频率等于 激振力的频率。
强迫振动的振幅与激 振力的大小、系统的 刚度及阻尼系数有关
强迫振动产生原因
地基振动
机床传动机构 的缺陷
Company Logo
不平衡造成的 离心惯性力
超声振动切削报告

超声振动切削报告关键信息项:1、超声振动切削的原理和技术特点原理:____________________________技术特点:____________________________2、应用领域和优势应用领域:____________________________优势:____________________________3、设备和工具要求设备类型:____________________________工具规格:____________________________4、切削参数和工艺控制切削参数:____________________________工艺控制要点:____________________________ 5、质量检测和评估标准检测方法:____________________________评估标准:____________________________6、安全注意事项和防护措施安全风险:____________________________防护措施:____________________________11 超声振动切削的原理超声振动切削是一种在传统切削加工基础上引入超声振动的先进加工技术。
其原理是通过在刀具或工件上施加高频振动,使切削过程中的切削力、切削热等发生显著变化,从而改善切削性能。
具体来说,超声振动使得刀具与工件之间的接触状态发生周期性改变,实现了断续切削,减少了刀具与工件之间的摩擦和粘结,降低了切削力和切削温度。
111 技术特点超声振动切削具有以下显著特点:1111 降低切削力由于断续切削和摩擦的减少,切削力大幅降低,这有助于减少机床的负荷,提高加工精度和表面质量。
1112 减小切削热振动切削过程中的热量产生减少,有利于防止工件的热变形和热损伤,提高加工精度。
1113 改善表面质量能够获得更光滑、更低粗糙度的加工表面,提高零件的使用性能和寿命。
实用化振动切削技术——深孔振动铰削工艺及装备

的出油孔 排 出 , 接进人 切 削区 , 直 进行冷 却润 滑 , 并将切屑 由刀杆外部 排 出, 到强制 冷却 和排屑 达
的 目的 。
1 振 动铰 孔装 备
振动铰削就是在铰孔过程中, 铰刀与工件间在
普 通铰 削 时的旋转 运 动和进 给运 动 的基础 上又 附加
了轴向振动 ( 通常为正弦波振动 ) 以达到改变切削 , 机理 、 提高 工艺效 果 的 目的。 与普通 铰削相 比 , 振动 铰削具有断屑容易、 切削力小、 加工精度 高、 表面粗 糙度低 、 刀具寿命长等优点 , 尤其在难加工材料 的铰 削 中更 能显 示 出普通 铰削无 法 比拟 的优势 。 图1 是北航研制的深孔低频振动铰削系统在某 厂实际应用 的现场。深孔低频振动铰削系统主要由 三部分组成 : )深孔钻镗床 , 1 提供主运动和进 给运 动 ;)低频 振 动 驱 动 系统 , 出振 幅 和 频率 可控 的 2 输
m 。切削参数 : m 转速 n= 2 m n 进给速度 = 3 1r i, / l. m mn 振动频率 F= 74 z 振动振 幅 A 44m / i, 3.5H ,
=
切屑 , 而不是普通铰削产生 的螺旋状连续切屑。由
于普 通 铰削不 能 断 屑 , 生 的 螺旋 状 连 续 切 屑 非 常 产
0 1 m, .4m 进给量. 0 05m / 。切削液为高压 厂 .4 m r =
容易堵塞 , 特别是 当切屑缠绕在刀体上 时很容易将
刀体 扭 变形甚 至 扭ห้องสมุดไป่ตู้ 。
硫化油。表面粗糙度测量仪 M H ehm t 。 A RPr o e r t e M1 在上 述试 验条 件 下 , 通 铰 削 和振 动 铰 削 的表 普
超声振动切削加工

超声振动切削加工的研究现状及进展摘要:简述了超声振动切削技术的发展、优点及应用领域。
通过将超声振动切削与普通切削比较以及对振动切削过程特点的描述,探讨了超声振动切削的切削机理。
文章还分析了振动切削技术的最新发展, 认为超声振动切削是一项有发展前途的新型技术。
关键词:超声振动切削;难加工材料:切削机理Research of vibration assisted turning cutting technology andIts developmentAbstract:Introduces the history, advantages and application field of the ultrasonic cutting technology(UCT). By compared with ordinary cutting and the characteristics description of the ultrasonic vibration cutting process, explored Ultrasonic vibration cutting of the cutting mechanism. The paper also analyzes an up- to- date vibrating cutting technology and summarizes that the ultrasonic vibration cutting is a promising new technology.Key Words: Ultrasonically vibrating cutting; Difficult - to - machine materials; Cutting Mechanism0 前言超声振动切削技术是把超声波振动的力有规律地加在刀具上,使刀具周期性地切削和离开工件的加工技术, 是结合超声波技术和传统切削工艺的一种新型切削技术。
振动切削技术特点及其应用研究

( . oeeo mm n ai ahnr n il ni en S uh e fr t nvrt, u mi un n 52 4 C i 1 Clg c u i t nm ci yadc iegn r g, otws o syu i sy K n n Y na 6 0 2 , hn l fo c o e v e i t er ei g a; 2 Sho o eh n a n p w r n i e n , e npl eh iu i rt, iou ea 4 4 0 , hn ) . colfm ca i l d o e gn r g H n o t n n esy J zoH n n 50 0 C i c a e ei a yc c v i a a
1 前
言
和摩擦 作用 , 将不 可 避 免 地产 生 较 大 的切 削 力 , 高 较
振 动 切削加 工 是 2 O世 纪 6 0年 代 发 展 起来 的一 种先进 制 造技术 , 通过 在常规 的切削刀 具上 施加 高 它
的切削温度, 使刀具产生磨损 和切削振动等有 害现 象 。普 通 切削 如图 1所示 。
Fe u e fv br i n a h n ng t c at r s o i ato m c i i e hnoog d e e r h o t plc to l y an r s a c f r is ap ia n i
W a ng— b a ,U u Chu n — s a ,Ya n —f ng Yi io a ho ng Yo g a
31振动切削的特点4振动切削技术的应用振动切削可以使切削力大幅度降低使摩擦热减振动切削技术是在研究切削加工本质的基础上小刀具耐用度提高已加工表面粗糙度减少它有以所提出的一种精密加工方法它弥补了普通切削加工下特点
震动刀切割机工作原理

震动刀切割机工作原理
震动刀切割机是一种利用高频震动刃刀进行切割的设备。
它的工作原理主要包括以下几个方面:
1. 电动机驱动:震动刀切割机内部有一台电动机,通常是交流电动机或直流电动机。
电动机会提供动力,驱动切割机的震动系统和切割刀片进行工作。
2. 震动系统:切割机的震动系统包括了电动机的转速调节装置、传动系统和震动刀片。
电动机的转速调节装置可以改变切割机的切割速度和切割深度。
传动系统将电动机的动力传递给切割刀片,使其产生高频震动。
3. 切割刀片:切割机的刀片通常是由高速钢、硬质合金等材料制成。
当传动系统将电动机的动力传递给刀片时,刀片会进行高频振动,产生较大的切割力。
4. 切割物体:在工作时,将需要切割的物体放置在切割机的工作平台上。
然后,通过控制手柄或按钮,将刀片轻轻地接触到工作物体的表面上。
刀片的高频震动能够迅速嵌入到物体中,并进行切割。
需要注意的是,震动刀切割机在工作时需要人员严格遵守操作规程,戴好所需的个人防护装备。
此外,切割机的刀片需要定时进行磨削和更换,以确保切割效果和工作效率。
振动切削技术的特点及其应用

引起人们 的重视而受 到世界各国的瞩目。
认, 认为它是传统加工技 术的一个飞跃。
2 普通切削与振动切削 .
在普通切削 中,切削是靠刀具与工件 的相对 运动来 完成的。切屑和 已加工表面 的形成过程 ,本质上 是工件 材料受 到刀具的挤压 ,产生弹性变形和塑性 变形 ,使切
屑与母体分离的过程 ( 图 1。在这种 刀具始终不离开 见 )
基于这种思想 ,在和有 害的 自 激振动 现象作斗争 中
产生了一种新 的切削方法——振动 切削。振 动切削即是
度降低 ,使摩擦热减小 、 刀具寿命提高 和已加工表 面粗
糙度值减少 ,即有 以下特点 :
囵 星 塑 旦 丝
WWW. mac n s . o . n hi i t c r c n
摩擦作用 ,将不可避免地产 生较大 的切 削力 ,较 高 的切 削温度 ,使 刀具磨损和产生切 削振动等有 害现象 。
杆的左端是刀片 , 右端是振动驱动 中心 ,由换能器 和变 幅杆将纵 向振动转换为弯 曲刀杆的横 向振动 。
3 振动切削的特点及工艺效果分析 .
( )振动切削的特点 1 振动切削可 以使 切削力大 幅
削过程 。所以 ,作为精密加工和难加工材 料加工 中的一
到各个加工领域 ,出现 了各种复合加工方法 ,使传统 的
加工技术有了一 个飞跃 。研究表明 ,由于其在一定 范围 内能够有效地解决难切削材料的加工及其精密切削加工 方 面的问题并在 加工 中具有一 系列 的特点 ,因而越来 越
种新技术 ,它 的切 削效 果 已经得 到世 界 各 国 的一 致 公
( 切削)机理 ,达到减 小切 削力 、切削热 ,提高加 工质
量 和效率的 目的。振动切削按所加频率不 同可分为高频 振动 和低频振动 ,低频振动仅仅从量上改 变切屑的形成 条件 ,主要用来解 决断屑 问题以及与此相 关的一系列 问 题 。而超声振动 ( 高频振动 )切削 已经使 切屑形成机理 产 生重大变化 ,可 以提高被加工材料 的可加工性 ,提高 刀具 寿命和工件加工质量 。超声加工 的工 艺效果来 自刀 具和工件之间的分 离运动 ,即它是一种 脉冲式 的断续 切
超声椭圆振动切削技术
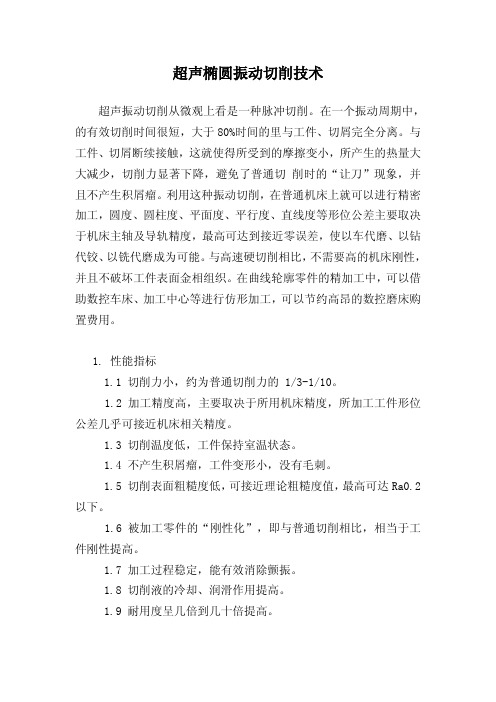
超声椭圆振动切削技术超声振动切削从微观上看是一种脉冲切削。
在一个振动周期中,的有效切削时间很短,大于80%时间的里与工件、切屑完全分离。
与工件、切屑断续接触,这就使得所受到的摩擦变小,所产生的热量大大减少,切削力显著下降,避免了普通切削时的“让刀”现象,并且不产生积屑瘤。
利用这种振动切削,在普通机床上就可以进行精密加工,圆度、圆柱度、平面度、平行度、直线度等形位公差主要取决于机床主轴及导轨精度,最高可达到接近零误差,使以车代磨、以钻代铰、以铣代磨成为可能。
与高速硬切削相比,不需要高的机床刚性,并且不破坏工件表面金相组织。
在曲线轮廓零件的精加工中,可以借助数控车床、加工中心等进行仿形加工,可以节约高昂的数控磨床购置费用。
1.性能指标1.1切削力小,约为普通切削力的1/3-1/10。
1.2加工精度高,主要取决于所用机床精度,所加工工件形位公差几乎可接近机床相关精度。
1.3切削温度低,工件保持室温状态。
1.4不产生积屑瘤,工件变形小,没有毛刺。
1.5切削表面粗糙度低,可接近理论粗糙度值,最高可达Ra0.2以下。
1.6被加工零件的“刚性化”,即与普通切削相比,相当于工件刚性提高。
1.7加工过程稳定,能有效消除颤振。
1.8切削液的冷却、润滑作用提高。
1.9耐用度呈几倍到几十倍提高。
1.10被加工表面呈压应力状态,零件疲劳强度、耐磨性、耐腐蚀性提高。
1.11切削后的工件表面呈彩虹效果。
2.应用范围由于超声振动切削有如此多的优点,所以可广泛应用于航空、航天、军工等领域各种难加工材料的切削加工。
2.1难加工材料切削:如耐热钢、钛合金、恒弹性合金、高温合金、不锈钢、冷硬铸铁、工程陶瓷、复合材料和花岗岩等。
2.2加工淬硬钢零件及超硬零件,能得到很高的加工精度和表面质量:用硬质合金可以很轻松地加工硬度达HRC60以上的淬硬钢零件,如高速钢、轴承钢等;用PCD加工硬质合金,可以大大提高的耐用度。
2.3成型切削:利用成型切削加工各种类型的轮廓曲面及内外球面、过度圆弧、锥面等。
实用化振动切削技术——振动攻丝工艺及装备

断 、 间和重 复 的脉 动 切 削 方式 。振 动攻 丝 丝 锥 切 瞬
削刃 的运动轨 迹如 图 1所示 。
目前 振 动 攻 丝 装 备 多 采 用 步 进 电机 作 为驱 动 力, 通过设定 电机正 、 反转 的脉 冲数 和发 送脉 冲的 频 率 来 控制攻 丝 的振 幅 和 频率 , 种 装 置 的攻 丝效 率 这 很 低 。为解决 这个 问题 , 本文 采 用 伺 服 电机替 代 步 进 电机 , 得 了 良好 的工 艺 效 果 。改 进 后 的新 型 振 取 动攻丝 机具 有如 下特 点 : 1 ( )巧 妙 安排 结 构设 计 , 使 得 主轴转 动惯 量较 小 , 提高 了电机 的动 态 响应能 力 ; ( )丝锥 自导 引进 给 , 2 机床 具 有 很 强 的 通 用性 ; 3 ()
命 。 以下 介 绍 研 制 的一 种 新 型 的低 频 振 动 攻 丝
机 , 实际应 用 中取得 了 良好 的 I 在 岂效果 。
I 振 动攻 丝装 备
通 常振动 攻丝 机 的工作 方式 是在 丝锥 上附加 一 个低 频 的扭转 振动 , 传 统 的连 续 切 削 过程 变 成 间 将
2 振 动 攻 丝 的工 艺效 果
2 1 降 低 攻 丝 扭 矩 .
支 撑方式 没计合 理 , 避 免 丝 锥 与被 加工 零件 焊 纹 能
‘
为验 证 振 动攻 丝 降 低 攻 丝扭 矩 的效 果 , 采用 表
1 所示 的试 验 条件 进行 了普 通 攻 丝 和振 动攻 丝 的对
7 ‘ 6
孔不 同轴 心 而 产 生 的 跳 动 , 用 于 精 密 螺 纹 加 工 。 适 系统 的实 物照 片 如 图 2所示 。
可能 使零件 报废 而造 成 巨大 的经济 损失 。振 动攻 丝
切削颤振综述.概要
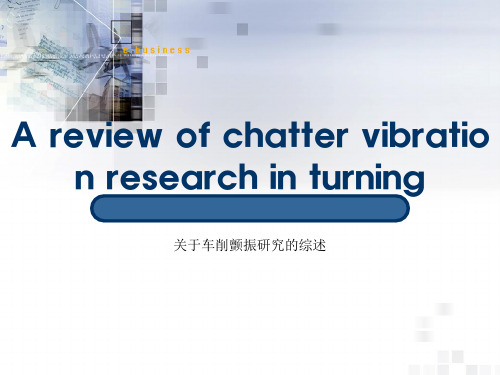
结论
• 刀具颤振以及刀具磨损能够通过分析切削力和从各 种传感器获得的振动信号来比较完整的估计出来。 刀具磨损可通过显微镜直接测量,刀具寿命可以通 过基于侧面磨损宽度的刀具寿命准则计算出来。最 大侧面磨损宽度0.2mm可应用于刀具寿命准则。
• 为了抑制颤振,主轴转速变化应该非常快速,显然 主轴系统有着高动能,使之非常难以实现。 • SSV效率不高,因为一大部分能量用来加速或者加 速主轴而被消耗。另外,高速加工中,明显改变主 轴转速会造成主轴系统的不平衡和不稳定,导致加 工事故。 • 所以,SSV技术并不能在工厂普遍应用。
• 小结: 主动避振的优点:不需要模型系统,只需要配置传 感器和执行器,就可达到主动避振的效果;低稳定性 区域中,主动避振对于提高刀具稳定性更有效果。缺 点:主动系统需要第二振动源来增加振动波形的总能 量;许多主动颤振控制系统都会受到主轴转速不能太 高从而限制其应用;与被动系统相比,主动系统同事 也需要更加复杂的软件、硬件和昂贵的设备。 未来的避振方向:主动避振与被动避振相结合。
• 力和振动测量 在切削过程中,切削力是也是一个非常敏感的参数, 它会随着切削速度、切削深度以及工件硬度的变化而 变化。振动测量实施简单,但是会依赖于加工状况, 工件材料和机床结构。 对于切削力和振动的测量会用到测力计和加速度仪 这种比较昂贵的设备,但是在未来预测颤振的方向中, 它们依然具有较好的发展趋势,应用于刀具状况监视 系统中,依然会比较好的描述切削过程的动力学。 • 声音信号的测量 声音信号应用性不高,在测量时会受到其他噪声的 干扰。
• 主轴转速变化(SSV):通过不间断的改变主轴转速 来避免颤振产生的影响。实践证明这种方法比较有效。 然而,由于受到主轴动力学的限制,主轴转速变化在 实际加工中应用可能会有困难,因为这需要巨大的扭 矩来克服驱动系统的惯性力。 • 虽然SSV方法实施简单,但是其抑制颤振成功之局 限于短时操作加工,这时颤振还没有很明显。
机床切削加工及切削颤振
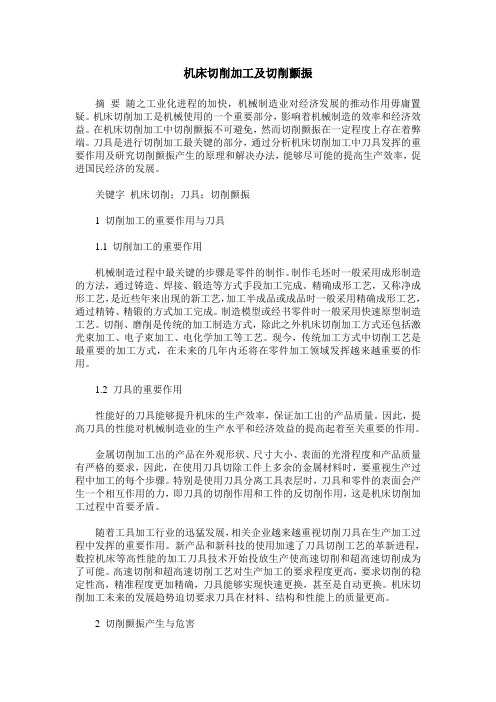
机床切削加工及切削颤振摘要随之工业化进程的加快,机械制造业对经济发展的推动作用毋庸置疑。
机床切削加工是机械使用的一个重要部分,影响着机械制造的效率和经济效益。
在机床切削加工中切削颤振不可避免,然而切削颤振在一定程度上存在着弊端。
刀具是进行切削加工最关键的部分,通过分析机床切削加工中刀具发挥的重要作用及研究切削颤振产生的原理和解决办法,能够尽可能的提高生产效率,促进国民经济的发展。
关键字机床切削;刀具;切削颤振1 切削加工的重要作用与刀具1.1 切削加工的重要作用机械制造过程中最关键的步骤是零件的制作。
制作毛坯时一般采用成形制造的方法,通过铸造、焊接、锻造等方式手段加工完成。
精确成形工艺,又称净成形工艺,是近些年来出现的新工艺,加工半成品或成品时一般采用精确成形工艺,通过精铸、精锻的方式加工完成。
制造模型或经书零件时一般采用快速原型制造工艺。
切削、磨削是传统的加工制造方式,除此之外机床切削加工方式还包括激光束加工、电子束加工、电化学加工等工艺。
现今,传统加工方式中切削工艺是最重要的加工方式,在未来的几年内还将在零件加工领域发挥越来越重要的作用。
1.2 刀具的重要作用性能好的刀具能够提升机床的生产效率,保证加工出的产品质量。
因此,提高刀具的性能对机械制造业的生产水平和经济效益的提高起着至关重要的作用。
金属切削加工出的产品在外观形状、尺寸大小、表面的光滑程度和产品质量有严格的要求,因此,在使用刀具切除工件上多余的金属材料时,要重视生产过程中加工的每个步骤。
特别是使用刀具分离工具表层时,刀具和零件的表面会产生一个相互作用的力,即刀具的切削作用和工件的反切削作用,这是机床切削加工过程中首要矛盾。
随着工具加工行业的迅猛发展,相关企业越来越重视切削刀具在生产加工过程中发挥的重要作用。
新产品和新科技的使用加速了刀具切削工艺的革新进程,数控机床等高性能的加工刀具技术开始投放生产使高速切削和超高速切削成为了可能。
高速切削和超高速切削工艺对生产加工的要求程度更高,要求切削的稳定性高,精准程度更加精确,刀具能够实现快速更换,甚至是自动更换。
切削加工振动及其控制技术

从计算得出,支持振动的变化力全部做功约为消耗在切去切屑的1~3%。大约这功 的15%为切屑形成时由物理过程(如摩擦力)所决定的变化力所作,其余85%由瞬 时切屑厚度所决定的变化力所作。
NUAA
自激振动
当存在振动时,在垂直于工件中心线的切削表面不是圆形而是在圆上的正弦曲线, 若刀尖所画曲线为: 前角与后角的数值可以由下式表示:
NUAA
自激振动
第二个支持振动的力为:刀具在前一转振动所留下波纹的轨迹上运动,过去所产生 切削力的变动部分。 实验中得知在下一转时的振动与上一转时的振动有70~120度的相位差,这样可以 设想,如果切削振动为谐振,被刀具切去金属层的厚度为二个有一定相位差的正弦 曲线所包括的厚度。这样切去层截面积将是周期性的,在相当范围内变化而产生切 削力的振动。
时,实际后角在周期中某一部分将小于
零,此时切削过程被破坏,因为车刀后面被加工表面挡住和推出来,切削厚度显著
减少,这种现象阻碍了振动的产生。
因此静止状的后角数值阻止振幅可能增加的范围。振幅增加达到的限值为 此后增加即停止。
NUAA
三种变化的力可以支持自激振动
1
2
3
车刀前面与切屑, 后面与加工表面间 的变动摩擦力
此处D为铣刀直径
切削速度
切削速度不直接影响振动的 振幅,但当一定的转速时( 或在一定直径铣刀到达一定 的切削速度)其中频率为nz 的振动的振幅突然增加,此 时,已发生共振现象,铣床 部件的自然振动频率一般在 30~80周之间或更高,当多 齿铣刀在中速铣切(此时由 于z)或高速铣切(此时由于 n)就会发生共振。平时常见 到铣切力与铣床工作台或立 柱发生共振现象。
刺激振动
刺激振动最突出的特性为振动的频率与刺激力的频率相等(或为其倍数)
- 1、下载文档前请自行甄别文档内容的完整性,平台不提供额外的编辑、内容补充、找答案等附加服务。
- 2、"仅部分预览"的文档,不可在线预览部分如存在完整性等问题,可反馈申请退款(可完整预览的文档不适用该条件!)。
- 3、如文档侵犯您的权益,请联系客服反馈,我们会尽快为您处理(人工客服工作时间:9:00-18:30)。
振动切削加工技术姓名:宋大同班级:机械工程1105班学号:113085201149摘要:振动切削加工技术是机械振动有利一面的应用,这是一种优于普通切削的新技术,是先进制造方法的重要组成部分。
本文通过振动切削与普通切削的对比,分析了振动切削的原理、特点、工艺效果及在切削过程中的作用。
同时论述了振动切削加工技术在工业中的具体应用和仍需解决的问题。
关键词:振动切削低频振动超声振动工艺效果应用机械振动同许多事物一样具有两面性,有其不利的一面,也有其有利的一面。
振动切削加工技术就是机械振动有利一面的应用。
振动切削加工是20 世纪60 年代发展起来的一种先进制造技术,它通过在常规的切削刀具上施加高频振动,使刀具和工件发生间断性的接触,从而使传统切削模式发生了根本性的变化。
振动切削改变了工件与刀具之间的时间与空间的分配,从而改变了切削加工机理,达到了减小切削力和切削热,并且提高加工质量和效率的目的。
由于其在一定范围内能够有效地解决难切削材料的加工及其精密切削加工方面的问题,因而越来越引起人们的重视。
1.普通切削与振动切削在普通切削中,切削是靠刀具与工件的相对运动来完成的。
切屑与已加工表面的形成过程,本质上是工件材料受到刀具的挤压,产生弹性变形和塑性变形,使切屑与母体分离的过程。
在这种刀具始终不离开切削的普通切削中,刀具的作用包括两个方面:一个是刀刃的作用,一个是形成刀刃的刀面的作用。
由于刀刃与被切削物接触处局部压力很大,从而使被切物分离。
刀面则在切削的同时撑挤被切物,促进这种分离。
普通切削中,伴随着切屑的形成,由于切屑与刀具之间的挤压和摩擦作用,将不可避免产生较大的切削力,较高的切削温度,使刀具磨损和产生切削振动等有害现象。
基于这种思想,产生了一种新的切削方法——振动切削。
振动切削即通过在切削刀具上施加某种有规律的可控的振动,使切削速度、切削深度产生周期性的改变,从而得到特殊的切削效果的方法。
振动切削改变了工具和被加工材料之间的空间与时间存在条件,从而改变了加工机理,达到减小切削力、切削热,提高加工质量和效率的目的。
2.振动切削分类1)振动切削按振动质量分为自激振动切削和强迫振动切削。
自激振动切削是利用切削过程中产生的振动进行切削的。
强迫振动切削是利用专门设置的振动装置,使刀具或工件产生某种有规律的可控振动进行切削的方法。
2)振动切削按刀具振动方向分为吃刀抗力方向、进给抗力方向和主切削力方向三种振动切削。
3)振动切削按所加频率不同可分为高频振动和低频振动。
振动频率在200HZ 以下的振动切削称为低频振动切削,低频振动仅仅从量上改变切屑的形成条件,主要用来解决断屑问题以及与此相关的一系列问题。
一般来说,低频振动切削的振动主要是靠机械装置实现,机械振动切削装置的结构简单,造价低,使用维护都比较方便,振动参数受负载影响较小,所以应用比较广泛。
高频振动切削又称为超声波振动切削,高频振动切削是指振动频率在16KHZ以上,利用超声波发生器,换能器,变幅杆来实现的。
通常来自超声波发生器的正弦波形的电震荡通过换能器变成只有几个微米的机械振动,然后经过变幅杆将振幅放大到15μm以上,而连接在变幅杆前端的刀具就能以相同的频率进行振动。
高频振动切削已经使切屑形成机理产生重大变化,可以提高被加工材料的可加工性,提高刀具寿命和工件加工质量。
高频振动切削加工的工艺效果来自刀具和工件之间的分离运动,即它是一种脉冲式的断续切削过程。
所以作为精密加工和难加工材料加工中的一种新技术,它的切削效果已经得到世界各国的一致公认,认为它是传统加工技术的一个飞跃。
3.振动切削加工的特点振动切削可以是切削力大幅度降低,使摩擦热减小、刀具耐用度提高、已加工表面粗糙度减小,与传统切削相比,具有以下特点:1)切削力大大减小刀具与切屑间摩擦因数只有传统切削的1/10,所以切削力可以减小到传统切削的1/2~1/10,塑性材料减小得更多。
2)切削温度明显降低刀与切屑间接触出现间歇,切削热更难以传到切削区,易于冷却,所以平均切削温度降到与室温差不多,切屑不变色,用手摸不会烫手。
3)切削液的作用得到了充分发挥超声波振动切削时会在切削液内产生“空化”作用,一方面使切削液均匀乳化,形成均匀一致的乳化液微粒;另一方面切削液微粒获得了很大能量更容易进入切削区,从而提高了切削液的效果。
没有切削液时空气冷却,在10-8s内刀具前刀面上就可形成单分子层氧化膜,从而减小了刀具与切屑间的摩擦。
4)可提高刀具使用寿命5)可控制切屑的形状和大小,改善排屑状况6)提高加工精度和表面质量7)可提高已加工表面的耐磨性和耐蚀性4.工艺效果分析1)瞬间切削力增大根据连续弹性体动力分析理论,在普通切削中,切削力一直作用在工件上,使得周边的材料也参与抵抗变形,就使得切口处切削力降低。
在振动切削中,材料的破坏过程与普通切削不同,它由每次冲击产生细微破坏而完成切削。
在振动切削中,因振动提高了实际的瞬间切削速度,并以动态冲击力作用于工件,使得局部变形减小,作用力集中,瞬间切削力增大。
从而获得较大的波前剪应力,有利于金属的塑性脆化。
减小塑性变形,利于切削。
在超硬材料的加工方面,这一优点更为突出。
2)摩擦因数减小振动切削可以是摩擦因数大大减小,因为振动可使相互接触材料间的静、动摩擦因数减小;振动切削可使切削液产生“空化”作用,使切削液充分发挥作用;此外,在无切削液作用的瞬间,前刀面生成了氧化膜,这同样可使摩擦因数减小。
3)剪切角增大振动切削时,刀具冲击被切材料产生的裂纹深度比实际切削长度长度大得多,在刀具前方会产生裂纹形成偏角,从而使实际剪切角增大。
4)工件刚性化当采用超声波振动切削时,整个系统的等效弹性系数比原系统弹性系数,在稳态切削条件下,一般增大3—10倍,所以我们可以看出采用振动切削能提高工件刚性。
5)应力和能量集中超声波振动使切削力的能量集中在切削刃前方工件材料很小范围内,工件材料原始晶格结构变化很微小,因此加工表面质量好,加工硬化和加工变质层均很小。
6)相对静切削时间小超声波振动切削时,在每个振动周期内只有短时间在切削,其余大部分时间里刀具与工件是分离的,所以振动切削的相对静切削时间短。
7)有利于冷却刀具的高速振动对刀具的散热十分有利,同时由于刀具的前面周期性脱离工件,使得冷却液更容易进入刀具和工件之间,也增加了系统的散热能力。
振动切削中,刀具在振动源驱动下周期性接触、离开工件。
刀具与切屑分离时,切削液产生空化作用,切削液充分进入切削区。
振动切削时刀具对工件的冲击作用,应力波的出现,有利于切削区裂纹的萌生和扩展。
刀具与切屑接触时,由于压力差出现,使得切削液渗透作用加强,充分发挥切削液的润滑和冷却作用。
这些都大大降低了前刀面与切屑间及后刀面与已加工工件表面间的摩擦。
5.振动切削技术的应用振动切削技术是在研究了切削加工本质的基础上所提出的一种精密加工方法,它弥补了普通切削加工的不足,但并不能完全取代普通切削加工而有一定的适用范围,主要有以下几个方面。
1)难切削材料加工不锈钢、淬硬钢、高速钢、钛合金、高温合金、冷硬铸铁以及陶瓷、玻璃、石料等非金属材料由于机械、物理、化学等特性而难以加工,如采用超声振动切削则可化难为易。
例如用硬质合金刀具振动车削淬硬钢(HRC35—45)外圆、端面、螺纹与镗孔时,不但提高了平行度、垂直度、与同心度,而且可达到“虹面”的表面光洁度,也可用金刚石刀具进行振动精密加工。
..此外,用普通切削加工石墨与氧化铝等材料时得不到平整的加工表面,只有采用超声振动才能产生微粒式的切削分离并得到整齐的加工表面。
2)难加工零件的切削加工如易弯曲变形的细长杆类零件,小径深孔,薄壁零件,薄盘类零件与小径精密螺纹以及形状复杂、加工精度与表面质量要求又较高的零件,用普通切削与磨削加工很困难,用振动切削,既可以提高加工质量,又可提高生产效率,例如用硬质合金车刀超声振动精车细长的退火调质铝棒(φ7.0mm,长220mm)的外圆,振动频率为F=21.5kHz,振幅为A=15μ,f=0.05mm/r,a p=0.01mm,用机械油作为切削液,加工后可获得工件直径精度为4μ,最大粗糙度为1μ。
又如超声振动精镗有特殊钢制成的薄壁圆筒(工件长70mm,孔径15mm,壁厚1mm),在镗过的50mm长度上可测出内孔精度为4μ,最大表面粗糙度为3μ。
3)高精度,高表面质量工件的切削加工与普通切削相比,振动切削时切屑变形与切削力小,切削温度低,加工表面上不产生积屑瘤、鳞刺与表面微裂纹,再加上表面硬化程度较大,表面产生残余压应力,切削过程稳定,容易加工出高精度与高表面质量的工件。
例如前述的超声振车软铝制成的细长轴(长200mm,φ7mm)时可得到圆度2μ,圆柱度3μ/170mm的加工精度。
超声车削φ5mm的电机整流器铜线时,可得到Ra=0.05μ的镜面,用其它加工方法是不可能达到的。
4)排屑断屑比较困难的切削加工钻孔、铰孔、攻丝、剖断、拉削等切削加工时,切屑往往处于半封闭或封闭状态,因而常不得不由于排屑断屑困难而降低切削用量,这时如果用振动切削则可比较顺利地解决排屑断屑问题而保证加工质量与提高生产效率。
例如利用超声波切削能顺利解决传统的钻孔工艺在排屑冷却等方面存在的困难,尤其适用于深孔和比较精密的小深孔加工。
主要表现如下:①切削效果明显提高。
由于切削过程中不必像麻花钻那样经常退刀排屑,一次走刀就可以成功地钻出整个孔,而且一次钻孔表面粗糙度可以达到0.63~0.2μm,尺寸精度可达IT7~ITS,完全可以达到较精密深孔的加工要求。
②排屑顺利,切削力、切削热明显降低。
加工过程中,切屑呈白色,与工件本体基本相同,一般为较薄的小带状切屑,比较容易随切削液排出,所以切削过程比较顺利。
③孔的表面质量大大提高,由于断屑排屑效果得到改善,同时又降低了切削力和切削温度,所以孔的表面质量得到较大的提高。
6.总结随着科学技术的进步和发展,振动切削加工作为精密机械加工和难加工材料加工中的一种新技术,它已经渗透到各个加工领域,出现了各种复合加工方法,使传统的加工技术有了一个飞跃。
目前世界各国虽然在振动切削某些现象的解释上,某些参数的选择上还有一些差别,但对它的工艺效果是一致公认的.。
目前我国在振动切削技术研究利用方面和国外相比有较大差距,大力加强振动切削技术的研究、推广和应用,这既是对切削技术的挑战,也是对切削行业陈旧体制的挑战。
同时也促进切削加工技术向复合方向发展,对提高我国机械制造业的加工水平和新产品开发具有十分重要的意义。