结晶器设计计算
高盐废水蒸发结晶设计方案

高盐废水蒸发结晶设计方案1.设计条件:1.处理量:每小时处理量3000Kg/h。
2.湿盐产量:240Kg/h;湿盐含水量按8%计算3.设备蒸发水量:2800Kg/h。
4.蒸发出的水洁净程度能达到污水管网排放标准,可用于生产。
2.设备选型2.1 选择依据(1)溶液在蒸发过程中有结晶产生并分离出结晶。
(2)溶液从8%浓缩到饱和状态(27.3%)并结晶。
2.2 工艺及设备1.蒸发工艺:考虑到蒸发能耗大,因此选用采用并流三效蒸发工艺。
由于原料浓度较大,需要蒸发少量水份,到饱和时才能产生结晶.第二、三效采用强制外循环OSLO结晶蒸发器形式,物料经过三效蒸发,溶液在末效达到饱和并产生结晶,温度在70℃左右。
晶浆经过泵输送到结晶罐,在罐内冷却到40~45℃并进一步结晶,然后出料进入离心机进行固液分离,母液则返回蒸发器。
2.设备形式:外循环三效蒸发器,第二、三效采用强制外循环OSLO结晶蒸发器形式,出料采用泵送方式,晶浆送入结晶罐内降温结晶,然后经过离心机分离晶体和母液,母液则返回第三效蒸发器内蒸发。
3.流程:顺流(并流)方式,即原料由第一效进入,经过第二效再到第三效。
与加热蒸汽及二次蒸汽的流动方向相同。
4.预热:第三效二次蒸汽进入冷凝器之前先经过原料预热器,作为原料的第一级预热。
第一效加热蒸汽产生的冷凝水作为原料的第二级预热。
原料经过两次预热后,原料温度大约可以上升到72℃左右。
5.OSLO结晶蒸发器属于强制外循环蒸发结晶器。
操作时,料液自循环管下部加入,与离开结晶室底部的晶浆混合后,由泵送往加热室。
晶浆在加热室内升温(通常为2~3℃),但不发生蒸发。
OSLO是制盐行业中常用的一种典型的结晶器。
蒸发式OSLO结晶器是由外部加热器对循环料液加热进入真空闪蒸室蒸发达到过饱和,再通过垂直管道进入悬浮床使晶体得以成长,由OSLO结晶器的特殊结构,体积较大的颗粒首先接触过饱和的溶液优先生长,依次是体积较小的溶液;因此OSLO结晶器生产出的晶体具有体积大、颗粒均匀、生产能力大。
我对碳化和结晶过程的探索与研究(周光耀)

分级结晶器的数学模型:为了减轻肥料结块,便于施肥,农业上希望化学肥料能造粒。
工业上由于各种肥料性质及生产方法不同,采用的造粒方法也不同,如有的采用大型造粒塔造粒,有的采用造粒机械进行造粒,有的直接在结晶器内制造大粒结晶肥料。
对于氯化铵,我国曾于1963~1965年进行过分级悬浮结晶器制造粒状氯化铵的中试,试验表明采用这种结晶器,氯化铵冷析结晶器可以制造出粒度达2mm以上的粒状结晶。
但盐析结晶器要制造粒状氯化铵难度较大。
此后化工部第八设计院曾设计过这种分级悬浮的冷析结晶器在生产厂试用,试车时曾生产出粒状氯化铵结晶,但当时由于市场上纯碱紧缺,生产厂都追求产量,如结晶器采用分级悬浮作业,结晶器生产强度要大幅下降,影响产量,此外要生产粒状氯化铵,还要控制晶核数量,操作比较麻烦,再加上当时市场上对粒状氯化铵并无需求,所以长期以来结晶器都强化生产粉状氯化铵,因此,用结晶器直接生产粒状氯化铵,在国内一直未能实现。
由于国际市场需求以及近年国内部份市场开始有了对粒状氯化铵的需求,有的厂采用挤压法生产一部份粒状氯化铵。
我认为随着我国经济的发展,尤其是农业生产技术的发展,对粒状化肥的需求量一定会越来越大。
用结晶器造粒,虽然降低了结晶器的生产强度,需要加大结晶器容积,增加建设费用,但结晶器属常压容器类设备,增加投资是不多的,比增设挤压机、粉碎机、筛分机等一系列机械造粒设备投资要少得多,此外结晶器获得的粒状氯化铵呈球形,流动性好,机械强度高,而且由于结晶粒度增大,离心机能力提高,漏网结晶大大减少,分离后水份降低,干燥费用减少,所以综合技术经济比较是有利的。
目前盐析结晶器生产粒状氯化铵技术还不成熟,我认为可采用冷析生产粒铵,盐析生产粉铵供制复合肥,并采用半母液二洗涤流程代替目前普遍采用的逆料流程,这样既在冷析结晶器生产了粒状氯化铵,又能确保盐析产品的盐份。
冷析结晶器要生产粒状氯化铵,中试时遇到的主要困难是如何控制好晶核的数量,目前已经有简单易行的技术可以解决,所以我认为用冷析结晶器直接生产粒状氯化铵应提到日程上来。
DTB结晶器

工艺设计要点工艺设计要点之九:罐式容器1。
液体罐通常是卧式的,气液分离罐通常是立式的。
2。
适宜的长度/直径比为3,范围在2.5 ~ 5。
3。
半充满回流罐的停留时间为5 分钟;气液分离罐进料到另一个塔之间的设计停留时间为5 ~ 10 分钟。
4。
炉前进料罐的停留时间最好是30 分钟。
5。
压缩机前气液分离罐的设计停留时间应该为每分钟液体体积通量的10 倍。
6。
液液分离器的设计停留时间应该维持沉降速度为0.85 ~ 1.3 mm/s7。
气液分离罐中气体临界速度 = 0.048 (液体密度/气体密度-1)0.5密度为kg/m3,临界速度为m/s8。
除沫器中丝网层厚度通常为150 mm。
9。
对于正压分离系统,丝网层之前的分离空间为150~450 mm,丝网层之后的分离空间为300 mm。
工艺设计要点之十:蒸发器1、最常见的类型是垂直长管自然或强制循环蒸发器。
管径在19~63 mm之间,管长在3.6~9.1 m之间。
2、强制循环速度一般在4.5~6 m/s范围内。
3、溶液沸点温度升高(BoilingPointRise或B.P.Elevation)是由于溶液中存在不挥发溶质的作用,而导致溶液温度与饱和蒸汽温度的差别。
4、当BPR大于4 oC时,较经济的做法是采用4~6 效串联蒸发器设计。
温差愈小,采用取决于蒸汽消耗成本的串联设计,其经济效果愈加明显。
5、增加多效之间的蒸汽压力,可以采用喷射器(20~30%效率),或者机械压缩机(70~75%效率)。
工艺设计要点之十一:过滤器1。
通常依据实验室真空滤叶试验的形成滤饼时间来分类的,0.1~10 cm/s为快速;0.1~10 cm/min为中速;0.1~10 cm/hr为慢速;2。
如果5分钟之内不能形成3 mm厚的滤饼,则不应采用连续过滤方法。
3。
对于需要快速过滤的场合,最好选择带卸料、顶加料的转鼓过滤机和加压式离心过滤机。
4。
对于需要中速过滤的场合,最好选择带真空鼓式和边沿式离心过滤机。
常规板坯连铸机结晶器技术

常规板坯连铸机结晶器技术【保护视力色】【打印】【进入论坛】【评论】【字号大中小】2006-12-0711-07杨拉道刘洪王永洪刘赵卫邢彩萍田松林 (西安重型机械研究所)结晶器是连铸机中的铸坯成型设备, 是连铸机的核心设备之一。
其作用是将连续不断地注入其内腔的钢液通过水冷铜壁强制冷却,导出钢液的热量,使之逐渐凝固成为具有所要求的断面形状和一定坯壳厚度的铸坯,并使这种芯部仍为液相的铸坯连续不断地从结晶器下口拉出.为其在以后的二冷区域内完全凝固创造条件。
在钢水注入结晶器逐渐形成一定厚度坯壳的凝固过程中.结晶器一直承受着钢水静压力、摩檫力、钢水热量的传递等诸多因素引起的的影响.使结晶器同时处于机械应力和热应力的综合作用之下.工作条件极为恶劣.在此恶劣条件下结晶器长时间地工作.其使用状况直接关系到连铸机的性能.并与铸坯的质量与产量密切相关。
因此.除了规范生产操作、选择合适的保护渣和避免机械损伤外.合理的设计是保证铸坯质量、减小溢漏率、提高其使用寿命的基础和关键。
板坯连铸机一般采用四壁组合式(亦称板式)结晶器.也有一个结晶器浇多流铸坯的插装式结构。
结晶器主要参数的确定1 结晶器长度H结晶器长度主要根据结晶器出口的坯壳最小厚度确定。
若坯壳过薄.铸坯就会出现鼓肚变形.对于板坯连铸机.要求坯壳厚度大于10~15mm。
结晶器长度也可按下式进行核算:H=(δ/K)2Vc+S1+S2 (mm)式中δ——结晶器出口处坯壳的最小厚度.mmK——凝固系数.一般取K=18~22 mm/min0.5Vc——拉速.mm/minS1——结晶器铜板顶面至液面的距离.多取S1=100 mmS2——安全余量.S=50~100 mm对常规板坯连铸机可参考下述经验:当浇铸速度≤2.0m/min时.结晶器长度可采用900~950mm。
当浇铸速度2.0~3.0m/min时.结晶器长度可采用950~1100mm。
当浇铸速度≥3.0m/min时.结晶器长度可采用1100~1200mm。
连铸机

第4章方坯连铸机总体设计及计算4.1 总体方案的确立钢水凝固成型有两种方法:传统的模铸法或连续铸钢法。
传统的模铸法分为脱模、整模、钢锭均热与开坯等工序。
基建投资大,能耗大,生产成本很高。
连续铸钢法的出现从根本上一个世纪以来占统治地位的钢锭初扎工艺,节省了工序,缩短了流程,提高了金属的收得率,降低的能耗。
本设计的主要工序流程是:钢水从钢水包中流出,先注入中间包,然后进入弧形结晶器,在结晶器中形成弧形铸坯沿着弧形辊道向下运动,运动中受喷水冷却,直至完成或部分凝固,然后铸坯到水平切点处进入拉矫机,然后用火焰切割车把铸坯切割成定尺,从水平方向出坯。
4.2 弧形连铸机总体设计计算与确定弧形连铸机总体参数包括:铸坯断面尺寸、冶金长度、拉坯速度、铸机半径以及连铸机的流数。
这些参数是确定铸即性能和规格的基本要素,也是设备选型和设计的主要依据。
4.2.1 铸坯断面连铸的坯型有:板坯、方坯、矩形坯、圆坯、六角或八角坯等。
以生产的铸坯断面尺寸和坯形如表4-1所示:确定铸坯断面尺寸时,应根据轧才的需要和轧制时的压缩比。
还应考虑炼钢炉的容量和铸机的生产能力。
对大型炼钢炉一般配置大断面和多流连铸机。
轧制的压缩比可取6~10。
对不锈钢和耐热钢最小取8,对高速钢和工具钢最小取10,对碳素钢和低合金钢可取6。
铸坯断面越大,对加杂物上浮越有利,同时铸机生产能力越大,但铸坯断面尺寸超过最大压缩比的要求时,就会相对得多消耗能量。
在选择铸坯断面形状和尺寸时,还应考虑与轧机能力的合理配合,可参照表4-2选用。
4.2.2 冶金长度从结晶器液面到铸坯全部凝固为止,铸坯中线距离称为液心长度或称冶金长度,因此液心长度与铸坯冷凝有关。
冷凝公式:铸坯凝壳厚度δ与冷凝强度和冷凝时间有关,冷凝强度用单位热流表示,即每单位时间单位面积上流出的热量,用0H 表示,单位为Kj/m 2·min,0H 越大表明冷凝强度越大,凝壳越厚。
由实验知,有如下关系:δ∝5.05.00τH (mm )或者 δ=ξ5.05.00τH(4.1)式中 τ——冷凝时间(min )ξ——系数(mm ·m/k 5.0J ),与铸坯形状和材质有关,由实验知ξ=0.0758式中(4.1)中( ξ5.00H )称冷凝系数,用K 表示,即K=ξ5.00H (mm ·5.0min -) (4.2)则冷凝皮可厚度δ为:δ=K 5.0τ(mm ) (4.3)式(4.3)称冷凝公式。
真空制盐蒸发结晶器的设计与实践

+
蒸发结晶器的沿革 盐的生产主要是通过对卤水进行 加 热 " 使 其 蒸 发 浓 缩 结
晶析出固体 (B%H 的过程 $ 随着社会发展和科学技术进步 " 盐 作为人们食用所占比例 越来越小 " 而是大量作为基础化学工
图 ! 蒸发结晶器简图 !"外热式强制正循环切向进料蒸发结晶器 !#" 外热式强制正循环轴向进料蒸发结晶器 ! $"外热式逆循环径向出料蒸发结晶器 !%" 外挂式逆循环轴向出料蒸发结晶器 "
作者简介 ’ 罗大忠 (&’(’) )$ 男 $ 四川峨眉山市人 $ 高级工程师 $ 原副总工程师 $ 长期从事盐化工及真空制盐工程设计与研究工作 %
!""# 年 ! 月第 " 期
,
罗大忠 !真空制盐蒸发结晶器的设计与实践
业和其它工业部门的原料 ! 盐的品种由古老的雪花盐 " 筒盐 " 锅巴盐 # 发展到今天的各种特殊要求用途的特种盐 ! 制 盐 设 备 也 由 古 老 的 作 坊 式 手 工 操 作 的 园 锅 "镶 锅 "小 方 锅 "小 平 锅 "大 平 锅 #至 近 代 制 盐 工 业 用 的 内 热 式 强 制 循 环 $ 标 准 式 % 蒸发结晶器和现代外热式强制正循环 $ 又分为切向进 料 和 轴 向 进 料 两 种 %蒸 发 结 晶 器 及 外 热 式 逆 循 环 $分 为 径 向 出 料 和 轴向出料两种 % 蒸发结晶器 ! 这也是目前制盐企业应 用 最 多 的蒸发结晶器 $ 如图 & 所示 %! 若为了获得粒径更大的结晶盐 可在上述蒸发结晶器上增设奥斯陆 $’()$ % 育晶器 ! * & & + ,型 育晶器或倒园锥型育晶器 # 这 样 可 获 得 粒 径 在 &-- 至 数 毫 米的结晶盐产品 ! ** 溶液的过饱和度 $# . / %’ 式中 (!/* ** 溶液在同一温度下的平衡饱和浓度 $56)7 ’ /&* ** 溶液的实际过饱和浓度 856)7 ! /1* 要 使 结 晶 成 长 #必 须 使 溶 液 达 到 过 饱 和 #并 控 制 在 介 稳 区内 # 溶液的过饱和度完全用于晶种成长而 消 失 ! 在 实 际 的 运行过程中溶液的实际过饱和度远比其最大的过饱和浓度 低 ! 一 般 情 况 下 溶 液 的 实 际 过 饱 和 浓 度 !/ 值 宜 控 制 在
方坯结晶器铜管锥度的测量与分析

方坯结晶器铜管锥度的测量与分析摘要:铜管锥度有两种表示方法,一是每米长度上的锥度,二是铜管上下口两相对面的尺寸偏差。
采用电子锥度测量仪和百分表对实际铜管锥度的测量表明,因制作精度差,铜管长度方向存在负锥度和锥度不变以及弯月面处的锥度变化不合理问题。
分析认为,生产螺纹钢时,弯月面处的锥度应不低于0.7%/m;生产低碳包晶钢时,弯月面锥度应不低于0.9%/m。
关键词:结晶器铜管;锥度测量;弯月面锥度相关博文:结晶器相关知识集锦1 结晶器铜管锥度结晶器铜管的断面必须随铸坯断面不断收缩而变化,铜管锥度大小必须合适。
锥度过大会造成结晶器对坯壳的挤压,拉矫机拉坯困难,增加坯壳与铜管内壁的摩擦,加剧铜管内壁的磨损,铸坯表面增铜,严重时会出现拉断、拉漏等事故。
在铜管弯月面以下,由于角部冷却强度大于面部,因此角部最先离开结晶器内壁,而产生气隙,在该区域气隙的作用下会形成热点,致使同一横截面上的温度梯度不同,在收缩应力的作用下,造成坯壳裂纹。
锥度过小,气隙增大,导出的有效热流少,坯壳减薄,容易发生漏钢事故;另外,锥度过小会使角部转动加剧,易诱发角部裂纹和纵向凹陷。
倒锥度主要取决于铸坯断面、拉速和钢的高温收缩性。
由于气隙厚度的不均匀性及纵向气隙形成的不规则,单锥度结晶器不能完全消除由气隙带来的影响,在生产低碳包晶钢时尤其突出。
随着连铸技术的发展,出现了双锥度、三锥度、多锥度及抛物线锥度的结晶器。
抛物线锥度结晶器在纵向上更加符合坯壳的凝固收缩形状,从而消除了气隙带来的不良影响,增加结晶器的传热效果,为高效连铸奠定了基础。
1.1 锥度计算表示方法方坯结晶器铜管锥度可由下式计算[1]:Ta=(B1-B2/B1*Lm)*100% 或Ta=(B1-B2/B2*Lm)*100%式中:Ta为铜管每米长度的倒锥度,%/m;Lm为结晶器铜管的长度,m;B1 为结晶器下口两相对面之间的距离,mm;B2为结晶器上口两相对面之间的距离,mm。
东华氯化铵结晶工艺6.15
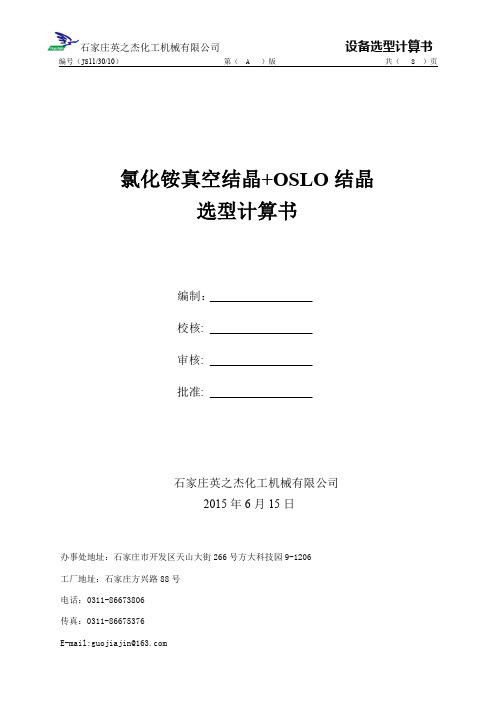
功率:4kW
1台
氟塑料
FPSWJ-280 功率:15kW
容积:15m3
1台
塑料喷射泵机组
1台
搪瓷
11
稠厚器
12
结晶出料泵
13
外冷器冲洗泵
容积:5m3
2台
流量:25m3/h
扬程:20m
2
功率:5.5KW
流量:25m3/h
扬程:20m
2
功率:5.5KW
搪瓷 2205 不锈钢 2205 不锈钢
7
石家庄英之杰化工机械有限公司
195.5526
6
石家庄英之杰化工机械有限公司
编号(JS11/30/10)
第( A )版
五、设备清单如下:
序 货物名称
号
规格、型号
数量
1
真空结晶室
2800×4000
1台
设备选型计算书
共( பைடு நூலகம் )页
备注 2205 不锈钢
2
卧式外置除沫器
Φ2000×3500mm
1台
2205 不锈钢
3
真空结晶冷凝器
4
真空结晶循环泵
37t/h
进料液浓度
50﹪
进料温度:
125℃
冷却水进口温度: 32℃(设定)
冷却水出口温度: 38℃(设定)
氯化铵溶解度表
氯化铵溶解度列表
温度℃
0 10 20 30 40 50 60 70 80 90 100
溶解度 g/100g 水
29.4 33.3 37.2 41.4 45.8 50.4 55.2 60.2 65.6 71.3 77.3
石家庄英之杰化工机械有限公司
常规板坯连铸机结晶器技术(知识学习)
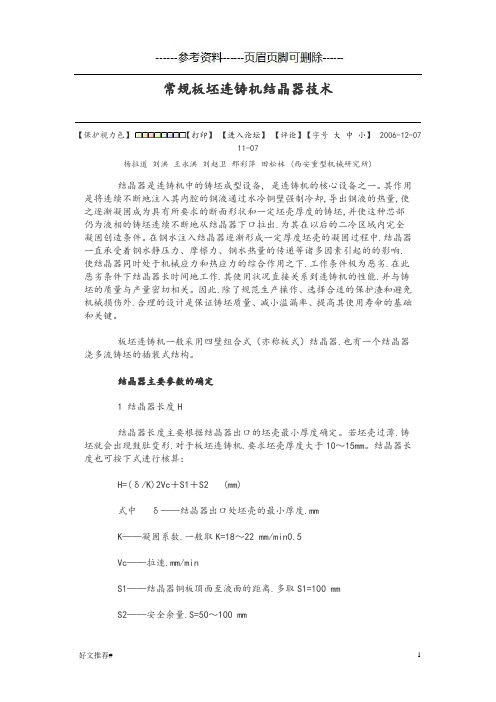
常规板坯连铸机结晶器技术【保护视力色】【打印】【进入论坛】【评论】【字号大中小】2006-12-0711-07杨拉道刘洪王永洪刘赵卫邢彩萍田松林 (西安重型机械研究所)结晶器是连铸机中的铸坯成型设备, 是连铸机的核心设备之一。
其作用是将连续不断地注入其内腔的钢液通过水冷铜壁强制冷却,导出钢液的热量,使之逐渐凝固成为具有所要求的断面形状和一定坯壳厚度的铸坯,并使这种芯部仍为液相的铸坯连续不断地从结晶器下口拉出.为其在以后的二冷区域内完全凝固创造条件。
在钢水注入结晶器逐渐形成一定厚度坯壳的凝固过程中.结晶器一直承受着钢水静压力、摩檫力、钢水热量的传递等诸多因素引起的的影响.使结晶器同时处于机械应力和热应力的综合作用之下.工作条件极为恶劣.在此恶劣条件下结晶器长时间地工作.其使用状况直接关系到连铸机的性能.并与铸坯的质量与产量密切相关。
因此.除了规范生产操作、选择合适的保护渣和避免机械损伤外.合理的设计是保证铸坯质量、减小溢漏率、提高其使用寿命的基础和关键。
板坯连铸机一般采用四壁组合式(亦称板式)结晶器.也有一个结晶器浇多流铸坯的插装式结构。
结晶器主要参数的确定1 结晶器长度H结晶器长度主要根据结晶器出口的坯壳最小厚度确定。
若坯壳过薄.铸坯就会出现鼓肚变形.对于板坯连铸机.要求坯壳厚度大于10~15mm。
结晶器长度也可按下式进行核算:H=(δ/K)2Vc+S1+S2 (mm)式中δ——结晶器出口处坯壳的最小厚度.mmK——凝固系数.一般取K=18~22 mm/min0.5Vc——拉速.mm/minS1——结晶器铜板顶面至液面的距离.多取S1=100 mmS2——安全余量.S=50~100 mm对常规板坯连铸机可参考下述经验:当浇铸速度≤2.0m/min时.结晶器长度可采用900~950mm。
当浇铸速度2.0~3.0m/min时.结晶器长度可采用950~1100mm。
当浇铸速度≥3.0m/min时.结晶器长度可采用1100~1200mm。
十种常见的工业结晶器结构原理
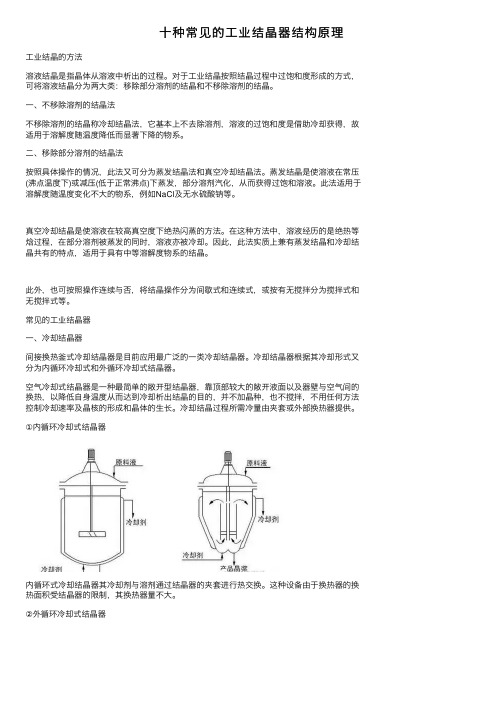
⼗种常见的⼯业结晶器结构原理⼯业结晶的⽅法溶液结晶是指晶体从溶液中析出的过程。
对于⼯业结晶按照结晶过程中过饱和度形成的⽅式,可将溶液结晶分为两⼤类:移除部分溶剂的结晶和不移除溶剂的结晶。
⼀、不移除溶剂的结晶法不移除溶剂的结晶称冷却结晶法,它基本上不去除溶剂,溶液的过饱和度是借助冷却获得,故适⽤于溶解度随温度降低⽽显著下降的物系。
⼆、移除部分溶剂的结晶法按照具体操作的情况,此法⼜可分为蒸发结晶法和真空冷却结晶法。
蒸发结晶是使溶液在常压(沸点温度下)或减压(低于正常沸点)下蒸发,部分溶剂汽化,从⽽获得过饱和溶液。
此法适⽤于溶解度随温度变化不⼤的物系,例如NaCl及⽆⽔硫酸钠等。
真空冷却结晶是使溶液在较⾼真空度下绝热闪蒸的⽅法。
在这种⽅法中,溶液经历的是绝热等焓过程,在部分溶剂被蒸发的同时,溶液亦被冷却。
因此,此法实质上兼有蒸发结晶和冷却结晶共有的特点,适⽤于具有中等溶解度物系的结晶。
此外,也可按照操作连续与否,将结晶操作分为间歇式和连续式,或按有⽆搅拌分为搅拌式和⽆搅拌式等。
常见的⼯业结晶器⼀、冷却结晶器间接换热釜式冷却结晶器是⽬前应⽤最⼴泛的⼀类冷却结晶器。
冷却结晶器根据其冷却形式⼜分为内循环冷却式和外循环冷却式结晶器。
空⽓冷却式结晶器是⼀种最简单的敞开型结晶器,靠顶部较⼤的敞开液⾯以及器壁与空⽓间的换热,以降低⾃⾝温度从⽽达到冷却析出结晶的⽬的,并不加晶种,也不搅拌,不⽤任何⽅法控制冷却速率及晶核的形成和晶体的⽣长。
冷却结晶过程所需冷量由夹套或外部换热器提供。
①内循环冷却式结晶器内循环式冷却结晶器其冷却剂与溶剂通过结晶器的夹套进⾏热交换。
这种设备由于换热器的换热⾯积受结晶器的限制,其换热器量不⼤。
②外循环冷却式结晶器外循环式冷却结晶器,其冷却剂与溶液通过结晶器外部的冷却器进⾏热交换。
这种设备的换热⾯积不受结晶器的限制,传热系数较⼤,易实现连续操作。
⼆、蒸发结晶器蒸发结晶器与⽤于溶液浓缩的普通蒸发器在设备结构及操作上完全相同。
结晶器铜管的设计和制造
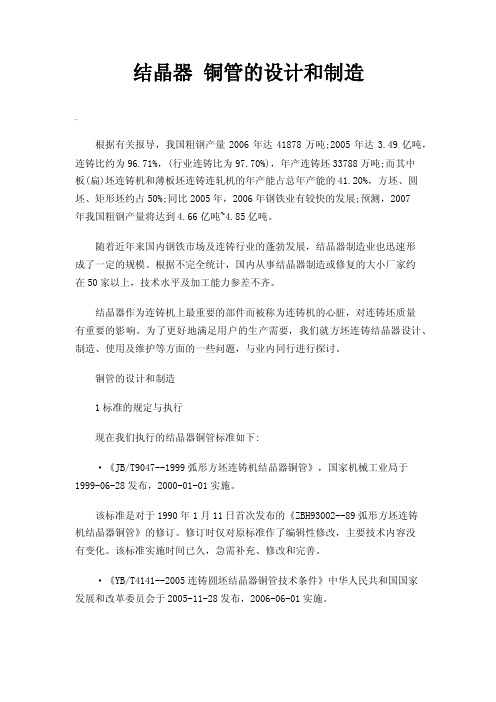
结晶器铜管的设计和制造根据有关报导,我国粗钢产量2006年达41878万吨;2005年达3.49亿吨,连铸比约为96.71%,(行业连铸比为97.70%),年产连铸坯33788万吨;而其中板(扁)坯连铸机和薄板坯连铸连轧机的年产能占总年产能的41.20%,方坯、圆坯、矩形坯约占50%;同比2005年,2006年钢铁业有较快的发展;预测,2007年我国粗钢产量将达到4.66亿吨~4.85亿吨。
随着近年来国内钢铁市场及连铸行业的蓬勃发展,结晶器制造业也迅速形成了一定的规模。
根据不完全统计,国内从事结晶器制造或修复的大小厂家约在50家以上,技术水平及加工能力参差不齐。
结晶器作为连铸机上最重要的部件而被称为连铸机的心脏,对连铸坯质量有重要的影响。
为了更好地满足用户的生产需要,我们就方坯连铸结晶器设计、制造、使用及维护等方面的一些问题,与业内同行进行探讨。
铜管的设计和制造1标准的规定与执行现在我们执行的结晶器铜管标准如下:·《JB/T9047--1999弧形方坯连铸机结晶器铜管》,国家机械工业局于1999-06-28发布,2000-01-01实施。
该标准是对于1990年1月11日首次发布的《ZBH93002--89弧形方坯连铸机结晶器铜管》的修订。
修订时仅对原标准作了编辑性修改,主要技术内容没有变化。
该标准实施时间已久,急需补充、修改和完善。
·《YB/T4141--2005连铸圆坯结晶器铜管技术条件》中华人民共和国国家发展和改革委员会于2005-11-28发布,2006-06-01实施。
·《Q/SCJ4.01-2001方坯结晶器验收标准》作为首钢长白结晶器有限责任公司的企业标准于2001-02-20发布,2001-03-01实施。
该标准符合YB/T072-1995《方坯结晶器技术条件》和YB/T036.11-92冶金设备制造与通用技术条件要求。
值得注意的是,在国内钢铁企业中,连铸机种类繁多、千差万别,结晶器及铜管作为非标设备,虽然国家对于方坯和圆坯等先后制订了相关标准,但难以适应生产形势的发展,在这方面,希望相关设计单位及制造厂认识到应有的责任,共同努力作到产品规范统一。
OSLO结晶器

OSLO结晶器在工业上获得较广泛的应用,主要应用于味精、冶金、水产物加工、软水制造等。
OSLO结晶器为过饱和度产生的区域与晶体生长区分别设置在结晶器的两处,晶体在循环母液中流化悬浮,为晶体生长提供一个良好的条件。
OSLO结晶器厂家,江苏瑞达科技给大家介绍一下OSLO结晶器的结构型式及设计特点。
①育晶器底部为园弧形,这就改善了料液在育晶器内的流动状态,不致于形成死区;②育晶器上部扩大的断面可以使盐晶沉降下来,不参与循环,减少了二次成核的机会;③料液从蒸发室下部进料,上部管出料,减少了短路温差损失,同时料液在蒸发室内上升的过程中还有一个微粒溶解过程,料液由不饱和变成饱和,可以减少细晶的数量,从而保证盐的粒度;④设计时育晶器上锥部设置了母液排放管,它既可以排母液控制罐内Na2 SO4 含量,也可以将一些微细的盐晶排出系统,以保持罐内晶核相对稳定,有利盐粒长大;⑤在设计时还考虑了每次刷罐时保留育晶器内料液的刷罐方式,既只刷加热室,这样可避免育晶罐内大粒盐的损失,而且刷罐后恢复生产出合格盐的时间也可以缩短。
⑥循环泵电机采用可调电机,通过调节电机转速来调节循环泵流量,从而调节循环清液中盐晶粒径和排出系统的结晶数量;OSLO是制盐行业中常用的一种典型的结晶器。
其特点是溶液从结晶器上部流出,进入强制循环泵,通过可使溶液产生过饱和度的装置后进入结晶器降液管,逐渐形成结晶,长大后的结晶沉于结晶器底部,取出为产品。
在物料循环过程中,多采用清母液循环,晶体不参加循环因此不易被破碎,结晶自结晶器中部取出不受沉降限制,晶体生长环境好,所以晶体粒径大,可达6-20目,即3mm大。
结晶器内不需要搅拌。
江苏瑞达环保科技有限公司是一家以技术研发为先导的高科技环保公司,致力于为客户提供清洁生产、“三废”治理、资源综合利用等方面的技术咨询、研发、设计及工程总承包服务。
公司成立于2011年,厂区占地面积320000㎡,总注册资金16800万元。
年140万吨PTA的氧化反应-结晶系统工艺设计----氧化结晶器的设计【文献综述】

文献综述化学工程与工艺年140万吨PTA的氧化反应-结晶系统工艺设计----氧化结晶器的设计[前言]目前世界PTA生产厂家采用的技术虽有差异,但归纳起来,大致可分为以下两类:(1) 精PTA工艺此工艺采用催化氧化法将对二甲苯(PX)氧化成粗TA,再以加氢还原法除去杂质,将CTA精制成PTA,这种工艺在PTA生产中居主导地位。
(2) 优质聚合级对苯二甲酸(QTA、EPTA)工艺,此工艺采用催化氧化法将PX 氧化成粗TA,再用进一步深度氧化方法将粗TA精制成聚合级TA。
两种工艺路线产品质量有所差异,即两种产品所含杂质总量相当,但杂质种类不一样。
PTA产品中所含PT酸较高(200ppm左右),4-CBA较低(25ppm左右),而QTA(或EPTA)产品中所含杂质与PTA相反,4-CBA较高(250ppm左右),PT 酸较低(25ppm以下)。
我所研究的是PTA生产由粗对苯二甲酸制备(氧化单元)和粗对苯二甲酸精制(精制单元)组成,CTA氧化单元主要由工艺空气压缩机系统,催化剂调配系统。
氧化反应及冷凝系统,结晶,分离,干燥系统,溶剂脱水及MA回收,母液处理系统,尾气洗涤、处理及干燥系统和醋酸收集系统等组成。
反应过程中,原料对二甲苯和醋酸混合物在钴锰催化剂,以溴化氢为促进剂,与空气中氧化反应,生成对苯二甲酸,该反应为放热反应,生成的对苯二甲酸大部分在反映其中结晶出来形成浆料。
由此引出我研究的课题,自氧化反应器出来的浆料经过三个串联的结晶器降温、降压后,由泵送入旋转真空过滤器(RVF)进行固液分离。
结晶阶段的目的是为了减少反应产品的压力和温度,以便通过旋转真空分离器从母液中分离TA晶体。
此外结晶器还在反应段和产品回收段之间提供缓冲能力。
[主题]氧化结晶来自氧化反应器的浆料通过液位控制进入氧化第一结晶器内乙酸和水被闪蒸掉,蒸汽通过氧化第一CTA结晶器冷凝器冷冷凝。
蒸汽在氧化第一结晶器出口冷凝器中得到进一步的冷却。
结晶器设计计算

通过结晶器的热流量通过结晶器放出热流,可用下列计算Q=LEVP{C1(Te-Tl)+lf+cs(Ts-To)}(3.1)式中:Q:结晶器钢水放出的热量,kj/min;L:结晶器横截面周长,4.012m;E:出结晶器坯壳厚度,0.012m;V:拉速,2.2m/min;。
为了防止出现水垢,水必须经过软化处理或脱盐处理[9]。
结晶器内冷却水的流量,一般按断面周长长度每毫米2-2.5每毫米计算。
经过净化及软处理的水一般都是循环使用。
采用封闭式供水系统。
充分利用回水系压有利于节能。
3.5.1结晶器的倒锥度钢水在结晶器内凝固是因坯壳收缩形成气隙,通常是将结晶器作成倒锥度,后者定义为:△ =(S上—S下)/S上×L(3.3)式中:△:结晶器的倒锥度%/m;S上,S下:结晶器的上边口,下边口长;L:结晶器长度。
倒锥度取值不能太小,也不能太大。
过小则作用不大,过大则增大了拉坯阻力,甚至卡钢而不能出坯[9]。
高碳钢的收缩量大,所以须用较大的倒锥度[7]。
高速拉坯时,应采用较小的倒锥度。
在此设计中,倒锥度可取0.96%/m,为了不致产生太大的拉坯阻力。
实际的倒锥度略小于上述值,约为0.4-0.8%/m。
3.5.2结晶器冷却水量的计算(3.4)3.5)即;W=Q/(△Q)=2468L/min=48.1m3/h=801L/min。
3.6结晶器的重要参数针对小方坯连铸机,结晶器设计为弧形结晶器,因为拉坯速度较高,结晶器的长度定为900毫米。
结晶器的材质查阅有关资料后,我们考虑到结晶器的热疲劳寿命,决定采用铜铬合金(含Gr0.5-0.9)。
3.6.1结晶器的构造结晶器的结构如图所示,其内管为冷拔异性无缝钢管。
外面套有刚制外壳,钢管与铜套之间有约7毫米的缝隙通以冷却水,即冷却水缝。
钢管与铜套制成弧形。
铜管的上口通过法兰用螺钉固定在钢制外壳上。
如图4-4所示,铜管的下口一般为自由端,允许热胀冷缩;但上下口都必须密封,防止漏水。
自动油润滑扁锭结晶器设计理论探讨

自动油润滑扁锭结晶器设计理论探讨发布时间:2022-11-27T08:39:29.215Z 来源:《科技新时代》2022年15期作者:赵朝杰[导读] 结晶器是半连续铸造用的锭模,俗称冷凝槽,它是铸锭成型和决定铸锭质量的关键部件,赵朝杰重庆西南铝机电设备工程有限公司,401326摘要:结晶器是半连续铸造用的锭模,俗称冷凝槽,它是铸锭成型和决定铸锭质量的关键部件,要求结构简单、安装方便,有一定的强度、刚度、耐冲击性、耐热性,还应该具有良好的导热性和好的耐磨性。
关键字:铸造工装结晶器冷凝槽模具前言:半连续铸造技术,是现在各国铝加工厂普遍采用的一种变形铝合金铸造的技术,现今普遍采用直接水冷立式半连续铸造,也被叫做 DC 铸造。
铝合金半连续铸造过程中,结晶器的设计质量决定了铸锭的质量及铸锭的成型率,其中结晶器侧壁的传热和结晶器的润滑情况对铝合金铸坯的表面质量具有重要的影响,结晶器收缩曲线决定了铸锭的厚差及铣面量的多少,较差的铸锭表面质量,需要较大的铣削量才能满足后续热变形的加工要求。
1、结晶器设计前基础数据的收集结晶器在开始设计前应和使用方进行详实的技术交流,了解清楚使用方铸造机形式,例如:内导式铸造机、外导式铸造机、钢丝绳铸造机以及铸造机的吨位,铸造(或控流)模式,常用的铸造铝合金牌号,期望的铸造速度。
选定适合的合金系列、合金牌号和铸造速度来作为结晶器的设计基准。
2、结晶器材料的选择选择结晶器的材质应该具有良好的导热性,这是因为良好的导热性可以提高结晶器与溶体的热交换能力,防止结晶器工作表面被烧损、融化,提高铸锭的一次冷却强度,缩短表面结晶区的高度,减少偏析瘤尺寸,提高铸造速度。
结晶器应具有足够的强度和刚度,确保结晶区在较高温度和压力下不变形,确保生产的铸锭不扭曲变形。
同时还应该具有良好的耐磨性,可以防止表面粗糙的铸锭将结晶器表面和人工打磨把结晶器工作面磨损,降低使用寿命。
通过以上分许我们可以选择锻件紫铜T2或铝合金锻件6061T652、轧制预拉伸板6061T651等材料作为我们的结晶器本体材料的选择,同时,还要选择相对较低的成本。
结晶器种类及主要特点

结晶器种类及主要特点 2010-9-27 9:09:27薄板坯和中薄板坯连铸技术的核心是结晶器。
对于结晶器的研究主要有以下种类:1、漏斗形结晶器1)几何形状德马克公司ISP工艺的第一代立弯式结晶器,上部是垂直段,下部是弧形段,侧板可调,上口断面是矩形,尺寸为(60-80)mm×(650-1330)mm。
意大利阿维迪厂采用了该工艺,并略作修改,上口断面形状,由原平行板形改为小漏斗形。
西马克公司CSP工艺所用的漏斗形结晶器,上口宽边两侧均有平行段,再与圆弧段相连接,上口断面较大。
这个漏斗形状在结晶器内保持到长700mm,结晶器出口处铸坯厚度为50-70mm。
2)主要特点漏斗形结晶器打破了传统板坯连铸结晶器在任意横截面均相同的限制,其结晶器腔内凝固壳的形状及大小按非矩形截面逐步缩小的规律变化。
但是,钢液在这种结晶器内凝固时要产生变形,特别是拉坯过程中机械变形产生的应力可能导致固液界面裂纹发生,并最终影响热轧带卷的质量。
因此,漏斗形结晶器的理想形状是尽量减小坯壳间两相区的弯曲变形率,使坯壳在固液变形率小于发生裂纹的临界应变率。
2、H2结晶器1)几何形状意大利达涅利公司FISC工艺是其代表FISC工艺优点是内部容积达,通过的钢液流量大,且有更好的钢液自然减速效应。
该结晶器长度为1200mm,宽度为1220-1620mm,厚度为50、60、65、70mm。
2)主要特点该结晶器鼓肚形状由上至下贯穿整个铜板,并一直延续到扇形I 段的中部。
结晶器出口处为将铸坯鼓肚形状矫平而特别设计了一组带孔型的辊子,对铸坯鼓肚进行矫平的设备长度比仅用连铸机结晶器时长两倍,即与仅用结晶器来矫平坯壳的鼓肚相比,坯壳上所受应力大大降低。
并且H2结晶器内部体积增大,可以盛装更多的钢液。
同时,结晶器上部尺寸加大,可使水口形状设计更合理,保证结晶器内液面稳定,提高保护渣的润滑效果,改善热交换条件,提高拉速,减少裂纹倾向。
3、平行板形直结晶器1)几何形状奥钢联公司CONROLL工艺是其代表。
结晶器设计计算

通过结晶器的热流量通过结晶器放出热流,可用下列计算Q=LEVP{C1(Te-Tl)+lf+cs(Ts-To)} (3.1)式中:Q:结晶器钢水放出的热量,kj/min;L:结晶器横截面周长,4.012m;E:出结晶器坯壳厚度,0.012m;V:拉速,2.2m/min;P:钢水密度,7.4×10⒊kj/kg·℃;由此可得: Q=LEVP{C1(Te-Tl)+lf+cs(Ts-To)}=62218kj/min结晶器水缝面积计算结晶器的水缝面积与单位水流量(冷却强度)铸坯尺寸的大小以及冷却水流速有关,结晶器水缝面积可用下式计算:F=QkS×106/(3600V)(mm2)(3.2)式中:Qk:单位水流量m3/n·m,经验值取100-500m3/n·m;取100m3/n·m。
S:结晶器周边长度,4×120×103m;V:冷却水流速,取6-10m/s,实际取8m/s;即结晶器水缝面积为:F+QkS×106/(3600v)=1.67×103mm33.5 结晶器的冷却系统为使结晶器壁有较高的导热系数,在铜壁与冷却水之间不能产生水垢和沉淀物。
由于结晶器的热负荷很高,接触结晶器壁的冷却水有时会达到汽化的温度。
为了防止出现水垢,水必须经过软化处理或脱盐处理[9]。
结晶器内冷却水的流量,一般按断面周长长度每毫米2-2.5每毫米计算。
经过净化及软处理的水一般都是循环使用。
采用封闭式供水系统。
充分利用回水系压有利于节能。
3.5.1 结晶器的倒锥度钢水在结晶器内凝固是因坯壳收缩形成气隙,通常是将结晶器作成倒锥度,后者定义为:△ =(S上—S下)/S上×L (3.3)式中:△:结晶器的倒锥度 %/m;S上,S下:结晶器的上边口,下边口长;L:结晶器长度。
倒锥度取值不能太小,也不能太大。
过小则作用不大,过大则增大了拉坯阻力,甚至卡钢而不能出坯[9]。
连铸浸入式水口塞棒设计

连铸浸入式水口塞棒设计IMB standardization office【IMB 5AB- IMBK 08- IMB 2C】连铸结晶器是连铸机的关键部件之一,它的形状与尺寸,直接关系到浸入式水口和塞棒的设计。
在连铸耐火材料生产厂,在设计浸入式水口和塞棒时,往往要根据连铸结晶器的形状、大小和长度,确定浸入式水口插入结晶器部分的直径和长度;确定出钢口的数量、形状和尺寸。
还要根据结晶器振幅大小、渣线层厚度和双渣线操作位置确定浸入式水口的渣线位置和长度。
为了控制浸入式水口进入结晶器的钢水流量,还要确定浸入式水口的碗部(水口窝)形状和与其匹配的塞棒棒头。
最后还要根据钢厂连铸浇注的钢种、钢水处理的方式和连浇时间,确定浸入式水口和塞棒的材质。
浸入式水口的设计1 浸入式水口碗部浸入式水口碗部,如图1,A和B所示。
浸入式水口头部的外部形状有两种形式:图1-A为圆锥体;图1-B为圆柱体与圆锥体的组合。
为了叙述方便:命名φA为水口圆锥体或圆柱体上口面外径,即浸入式水口头部的外形尺寸,φB为碗部的开口度,φC为碗部圆弧与水口流钢中孔相切处的直径,该直线称为喉线,φD为水口圆锥体终端外径,R为水口碗部圆弧半径,h为圆锥体高度,h1为喉线深度,h2为水口碗部圆柱体高度,h为水口圆柱体与圆锥体的总高度。
图1 浸入式水口示意图对于大多数连铸耐火材料厂而言,要运用水力学模型和复杂的数学计算来设计浸入式水口,是一件非常困难的事。
因此,在浸入式水口的设计过程中,使用实践经验很重要,也很有效。
作者认为浸入式水口碗部的基本尺寸,源于水口流钢中孔的直径,一切从它开始。
首先要根据钢厂钢包的实际容量、中间包容量和流数、连浇炉数和单炉浇注时间等诸多因素,确定水口流钢中孔的直径φC。
在国内,大圆坯和板坯连铸所用的浸入式水口流钢中孔的直径φC,大多在50~85mm之间,其他类型为50~30mm,小方坯连铸则更小。
浸入式水口的喉线深度h1,无论流钢中孔的直径φC值在什麽范围,除小方坯连铸外,其喉线深度一般均在40~60mm之间。
- 1、下载文档前请自行甄别文档内容的完整性,平台不提供额外的编辑、内容补充、找答案等附加服务。
- 2、"仅部分预览"的文档,不可在线预览部分如存在完整性等问题,可反馈申请退款(可完整预览的文档不适用该条件!)。
- 3、如文档侵犯您的权益,请联系客服反馈,我们会尽快为您处理(人工客服工作时间:9:00-18:30)。
通过结晶器的热流量
通过结晶器放出热流,可用下列计算
Q=LEVP{C1(Te-Tl)+lf+cs(Ts-To)} (3.1)式中:Q:结晶器钢水放出的热量,kj/min;
L:结晶器横截面周长,4.012m;
E:出结晶器坯壳厚度,0.012m;
V:拉速,2.2m/min;
P:钢水密度,7.4×10⒊kj/kg·℃;
由此可得: Q=LEVP{C1(Te-Tl)+lf+cs(Ts-To)}
=62218kj/min
结晶器水缝面积计算
结晶器的水缝面积与单位水流量(冷却强度)铸坯尺寸的大小以及冷却水流速有关,结晶器水缝面积可用下式计算:
F=QkS×106/(3600V)(mm2)(3.2)式中:Qk:单位水流量m3/n·m,经验值取100-500m3/n·m;取100m3/n·m。
S:结晶器周边长度,4×120×103m;
V:冷却水流速,取6-10m/s,实际取8m/s;
即结晶器水缝面积为:
F+QkS×106/(3600v)=1.67×103mm3
3.5 结晶器的冷却系统
为使结晶器壁有较高的导热系数,在铜壁与冷却水之间不能产生水垢
和沉淀物。
由于结晶器的热负荷很高,接触结晶器壁的冷却水有时会达到汽化的温度。
为了防止出现水垢,水必须经过软化处理或脱盐处理[9]。
结晶器内冷却水的流量,一般按断面周长长度每毫米2-2.5每毫米计算。
经过净化及软处理的水一般都是循环使用。
采用封闭式供水系统。
充分利用回水系压有利于节能。
3.5.1 结晶器的倒锥度
钢水在结晶器内凝固是因坯壳收缩形成气隙,通常是将结晶器作成倒锥度,后者定义为:
△ =(S
上—S
下
)/S
上
×L (3.3)
式中:△:结晶器的倒锥度 %/m;
S
上,S
下
:结晶器的上边口,下边口长;
L:结晶器长度。
倒锥度取值不能太小,也不能太大。
过小则作用不大,过大则增大了拉坯阻力,甚至卡钢而不能出坯[9]。
高碳钢的收缩量大,所以须用较大的倒锥度[7]。
高速拉坯时,应采用较小的倒锥度。
在此设计中,倒锥度可取0.96%/m,为了不致产生太大的拉坯阻力。
实际的倒锥度略小于上述值,约为0.4-0.8%/m。
3.5.2 结晶器冷却水量的计算
单位时间内通过结晶器冷却水缝(水槽)的水量对结晶器钢水热量传递和坯壳凝固有重要的参数影响。
结晶器冷切水量计算方法有:
结晶器热平衡法
假定结晶器钢水热量全部由冷却水带走,则结晶器钢水凝固放出的热量与冷却水带走的相等,即:
Q=W×C×△Q (3.4)
则 W=Q/(△Q)
式中: Q:结晶器内的钢水凝固放出热量,2218kj/min; W:结晶器全部水量,L/min;
C:水的比热容,4.2kj/kg×℃;
△Q:结晶器进出水量温度差6℃
即 W=Q/(△Q)=2468L/min
(1)从保证水缝内冷却水流速>6m/s来求结晶器水量得:
W1:36×S×V/10000(m3/h)(3.5)式中: S:水缝面积,1.67×103m m2
W1:冷却水量,m3/h;
V:冷却水流速,8m/s。
即;W=Q/(△Q)=2468L/min=48.1m3/h=801L/min。
3.6 结晶器的重要参数
针对小方坯连铸机,结晶器设计为弧形结晶器,因为拉坯速度较高,结晶器的长度定为900毫米。
结晶器的材质查阅有关资料后,我们考虑到结晶器的热疲劳寿命,决定采用铜铬合金(含Gr0.5-0.9)。
3.6.1 结晶器的构造
结晶器的结构如图所示,其内管为冷拔异性无缝钢管。
外面套有刚制外壳,钢管与铜套之间有约7毫米的缝隙通以冷却水,即冷却水缝。
钢管与铜套制成弧形。
铜管的上口通过法兰用螺钉固定在钢制外壳上。
如图4-4所示,铜管的下口一般为自由端,允许热胀冷缩;但上下口都必须密封,防止漏水。
结晶器外套是圆桶形的。
外套中部有底脚板,将结晶器固定在振动框加上。
结晶器铜板壁厚为10-15毫米磨损后可加工修复。
但最薄不能小于3-6毫米。
考虑到铸坯的热胀冷缩,在铜壁的角度应有一定的圆角过滤。
3.6.2 结晶器的断面尺寸
冷态铸坯的断面尺寸称为公称尺寸,结晶器的断面尺寸应根据公称尺寸(120×120mm)来定。
结晶器的内腔断面尺寸比铸坯尺寸略大些。
通常是根据经验公式来确定结晶器断面尺寸。
我们考虑以下公式,确定了方坯结晶器内腔尺寸厚度和宽度尺寸:
=(1+2.5%)Do=(1+2.5%)×120=123 (3.6)D
f
=(1+2.5%)Bo=(1+2.5%)×120=123 (3.7)B
f
管式结晶器内腔应有合适的圆角半径。
铸坯断面120*120mm2,参考有关公式,圆角半径为8毫米。
3.6.3 结晶器长度
确定结晶器长度的主要依据是出结晶器下口时的坯壳厚度。
若坯壳过薄。
铸坯就会出现鼓肚现象,甚至拉漏。
对于120×120mm方坯而言,出结晶器时铸坯坯壳厚度为8-10mm,根据现在大多数钢厂铸机的新倾向。
结晶器长度确定为900mm。
目的是与高速拉相配合。
理论计算标明,结晶器热量的50%是上部导出
的结晶器下部只是起支撑作用,因而过长的结晶器无益于坯壳的增厚,所以没有必要选用过长的结晶器。
结晶器长度因而决定用900mm。
3.6.4 水缝面积
结晶器水缝总面积通常根据下式计算:
Q结=360FV/1000 (3.8)则 F=10000Q结/36V
式中 Q:结晶器的耗水量,3m/h;
F:水缝总面积,2mm;
V:水缝内冷却水的流速,m/s。
方坯结晶器水流速确定为6m/s。
结晶器冷却水量也是根据经验,按结晶器周边长度计算。
对于本次设计的小方坯连铸机结晶器而言,周边供水量约为2.0-3.0L/min·mm。
冷却水进水压力为0.39-0.9Mpa,结晶器进出水温度为3-8度。