注塑制品内应力分析及控制
注塑制件内应力影响因素分析

注塑制件内应力影响因素分析文章详细对注塑制件内应力的产生因素进行了分析,并针对其不同的影响因素提出了针对性的解决措施,从实践中证实热处理对于消除或降低注塑制件内应力的有效性,通过该种方式有效稳定热塑制件内部结构,从而保证热塑制件结构质量。
标签:注塑制件;内应力;因素;成型工艺;热处理塑料的加工成型特点优良,因而在加工行业得到了广泛的使用,其最主要的优势在于比强度高、电性能好、质量相对较强,且相比其他材料塑料耐磨性良好,能够消音减震,最重要的是加工方便。
但是注塑制件仍旧存在一个无法避免的缺陷——内应力。
热塑制件会因为内应力而出现翘曲变形现象,严重者会导致制件开裂,另外还会对制件的光学、电学、物理学等性能造成影响,表观质量也同样会受到内应力的影响。
所以寻找对热塑制件内应力影响因素,从而针对性的提出解决措施,是保证热塑制件质量的重要前提,通过有效措施使得热塑制件内应力能够均匀分布。
尤其在使用热塑制件时环境恶劣,例如需要直接接触高热、有机溶剂以及其他腐蚀性介质时,降低内应力可以保证热塑制件结构的稳定性。
1 影响因素分析影响注塑制件内应力大小的因素有很多,具体分析包括以下几点。
1.1 造型设计1.1.1 圆角。
注塑制件其表面相交之处应当采用圆弧进行过度,而其使用上则要求使用尖角。
这是因为注塑制件在注塑过程中截面、形状发生变化的过程中在尖角的位置容易产生极大的应力,并始终无法消除,一旦受到外界的冲击以及超出其能够承受的荷载时就会生生破裂,有些在脱膜过程中就会由于其内应力而出现开裂现象,特别在内角位置。
该类问题可以通过尖角改圆角的方式予以消除,采用0.5mm圆角就能够改善应力集中现象消除内应力的产生,从而改善制件的结构特性,避免由于冲击造成材料不满模腔或形成波纹等问题。
将注塑制件过度位置设计成圆角,那么模型内部也呈圆角,因而磨具也同样具有坚固特性。
由于制件圆角对应模型圆角,因而在热塑过程中不会造成应力过于几种,不但提高了制件的质量,还提升了模具的使用寿命。
影响注塑制件内应力的因素

影响注塑制件内应力的因素注塑制件是一种经济高效和具备多种形状及功能的重要制造技术,但是其内部应力却受到来自注塑工艺及其他外部因素的影响,使得注塑制件内应力产生变化,从而影响了其功能性能、使用寿命。
因此,探究影响注塑制件内部应力的因素和机理,对于改进注塑工艺及优化注塑制件的使用性能及使用寿命具有重要的意义。
首先,注塑参数是影响注塑制件内应力的重要因素之一。
注塑参数主要包括注塑温度、塑料填充量、熔料压力、射出速度等。
随着参数调整,注塑过程中塑料的塑形、熔料流动和成型性能以及塑料凝固动态特性发生明显变化,从而使得熔体在凝固过程中产生应力,由此导致注塑制件内部应力发生变化。
其次,注塑成型模具结构是影响注塑制件内应力的重要因素之二。
一般来说,注塑成型模具结构的设计会影响注塑的流植分布,而分布的不均衡会使得冷却水或空气在不同地方冷却速度不一,从而导致注塑件表面张力的不均匀,从而导致注塑制件内应力发生变化。
同时,模具中心热对流也会对注塑制件内应力产生影响。
此外,注塑材料也是影响注塑制件内应力的因素之一。
目前,注塑材料的选择一般是根据制件的用途来确定的,其受到多种因素的影响,例如熔点、熔体流动性、熔体弹性模量、收缩率等等。
这些因素的变化都会对注塑制件的内部应力产生影响。
另外,不良工艺及装配技术也是影响注塑制件内应力的因素之一。
如果在注塑过程中,采用了不合理的工艺操作,会使得塑料不均匀地冷却,而导致注塑制件内应力出现变化,从而影响制件的使用性能和使用寿命。
此外,注塑件装配时如果采用不正确的技术,也会导致注塑件内部应力发生变化。
综上所述,注塑参数、注塑模具结构、注塑材料、不良工艺及装配技术等多种因素都会影响注塑制件的内部应力,从而影响注塑制件的使用性能和使用寿命。
因此,在注塑工艺的设计和应用过程中,应该充分考虑这些因素,通过优化参数来改善注塑制件的内部应力,并采用合理的模具结构设计、优良的注塑材料,以及正确的装配技术,最大程度地降低注塑制件内部应力,提高其功能性能及使用寿命。
注塑制品内应力分析及控制

注塑制品内应力分析及控制注塑制品是指利用注塑成型技术制造的各类塑料产品。
在注塑制品的生产过程中,由于塑料的热胀冷缩以及流动性等特性,会产生内应力。
这些内应力如果不得到合理的控制和处理,将会导致注塑制品的变形、开裂等问题。
因此,注塑制品内应力的分析和控制非常重要。
首先,注塑制品内应力的分析应从材料的选择和设计的角度来考虑。
不同的塑料材料在注塑成型过程中,由于热胀冷缩的差异以及流动性的不同,会产生不同程度的内应力。
因此,在选择塑料材料时,应考虑其热胀冷缩系数和流动性等因素。
同时,在产品设计中,应尽量避免或减少注塑制品的复杂形状和薄壁结构,这样可以减少塑料在注射和冷却过程中的内应力。
其次,注塑制品内应力的控制主要通过优化注塑工艺参数来实现。
注塑工艺参数包括注射压力、注射速度、保压时间和冷却时间等。
在注射过程中,应控制注射压力和速度,避免塑料在注射过程中产生过大的内应力。
在保压过程中,应根据具体产品的形状和尺寸,适当延长保压时间,以提高塑料的流动性和均匀性,减少内应力。
在冷却过程中,应控制冷却时间和冷却速度,避免快速冷却引起的内应力。
此外,还可以采用一些工艺改进的方法来控制注塑制品内应力。
例如,合理设计模具结构,采用多点定位和多级冷却等方式,可以均匀分布注塑制品内应力,减少应力集中。
另外,还可以采用预应力或热处理等后处理方式来消除或降低注塑制品的内应力。
总之,注塑制品内应力的分析和控制是注塑制品生产过程中非常重要的问题。
通过选择合适的塑料材料、优化注塑工艺参数以及合理设计模具结构等方式,可以有效减少注塑制品的内应力,并提高产品的质量和性能。
影响注塑制件内应力的因素
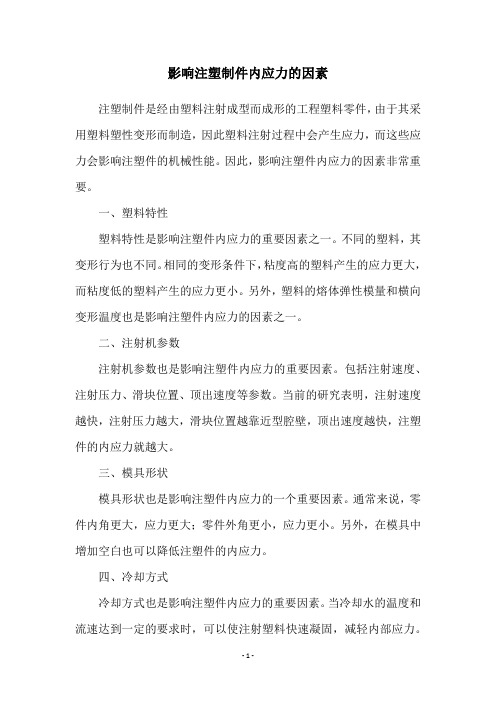
影响注塑制件内应力的因素
注塑制件是经由塑料注射成型而成形的工程塑料零件,由于其采用塑料塑性变形而制造,因此塑料注射过程中会产生应力,而这些应力会影响注塑件的机械性能。
因此,影响注塑件内应力的因素非常重要。
一、塑料特性
塑料特性是影响注塑件内应力的重要因素之一。
不同的塑料,其变形行为也不同。
相同的变形条件下,粘度高的塑料产生的应力更大,而粘度低的塑料产生的应力更小。
另外,塑料的熔体弹性模量和横向变形温度也是影响注塑件内应力的因素之一。
二、注射机参数
注射机参数也是影响注塑件内应力的重要因素。
包括注射速度、注射压力、滑块位置、顶出速度等参数。
当前的研究表明,注射速度越快,注射压力越大,滑块位置越靠近型腔壁,顶出速度越快,注塑件的内应力就越大。
三、模具形状
模具形状也是影响注塑件内应力的一个重要因素。
通常来说,零件内角更大,应力更大;零件外角更小,应力更小。
另外,在模具中增加空白也可以降低注塑件的内应力。
四、冷却方式
冷却方式也是影响注塑件内应力的重要因素。
当冷却水的温度和流速达到一定的要求时,可以使注射塑料快速凝固,减轻内部应力。
另外,控制模具的冷却水的流向也是影响注塑件内应力的一个重要因素。
五、其他因素
此外,塑料的流量、型腔尺寸公差控制、型腔表面光洁度、模具温度等因素也会影响注塑件内部应力。
综上所述,影响注塑件内应力的因素有很多,包括塑料特性、注射机参数、模具形状、冷却方式和其他因素。
因此,对于注塑件来说,控制其内应力非常重要,以保证其质量和可靠性。
塑胶产品内应力研究报告及消除方法

1.注塑制品一个普遍存在的缺点是有应力。
应力的存在不仅是制件在储存和使用中浮现翘曲变形和开裂的重要原因,也是影响制件光学性能、电学性能、物理力学性能和表观质量的重要因素。
因此找出各种成型因素对注塑制品应力影响的规律性,以便采取有效措施减少制件的应力,并使其在制件断面上尽可能均匀地分布,这对提高注塑制品的质量具有重要意义。
特殊是在制件使用条件下要承受热、有机溶剂和其他能加速制件开裂的腐蚀介质时,减少制件的应力对保证其正常工作具有更加重要的意义。
此外,掌握注塑制品应力的消除方法和测试方法也很有必要2 应力的种类高份子材料在成型过程中形成的不平衡构象,在成型之后不能即将恢复到与环境条件相适应的平衡构象,是注塑制品存在应力的主要原因。
此外,外力使制件产生强迫高弹形变也会在其中形成应力。
根据起因不同,通常认为热塑性塑料注塑制件中主要存在着四种不同形式的应力。
对注塑制件力学性能影响最大的是取向应力和体积温度应力。
2.1 取向应力高份子取向使制件存在着未松弛的高弹形变,主要集中在表层和浇口的附近,使这些地方存在着较大的取向应力,用退火的方法可以消除制件的取向应力。
试验说明,提高加工温度和模具温度、降低注射压力和注射速度、缩短注射时间和保压时间都能在不同程度上使制件的取向应力减小。
2.2 体积温度应力体积温度应力是制件冷却时不均匀收缩引起的。
因外收缩不均而产生的体积温度应力主要靠减少制件外层冷却降温速率的差异来降低。
这可以通过提高模具温度、降低加工温度来到达。
加工结晶塑料制件时,往往因各局部结晶构造和结晶度不等而浮现结晶应力。
模具温度是影响结晶过程的最主要的工艺因素,降低模具温度可以降低结晶应力。
带金属嵌件的塑件成型时,嵌件周围的料层由于两种材料线膨胀系数不等而浮现收缩应力,可通过预热嵌件降低应力。
这两种应力主要是由于收缩不均而产生的,也属于体积温度应力。
2.3 与制件体积不平衡有关的应力高份子在模腔凝固时,甚至在极其缓慢的条件下要使制件在脱模后即将到达其平衡体积,在实际上是不可能的。
《塑料注塑成型内应力研究》

《塑料注塑成型内应力研究》塑料注塑成型是一种常用于制造塑料制品的方法,它可以通过将加热熔化的塑料材料注入到模具中,然后冷却固化来制造各种形状的产品。
然而,在注塑成型过程中,塑料制品会产生内部应力,这可能对产品的性能和质量产生不良影响。
因此,研究塑料注塑成型内应力具有重要的意义。
首先,塑料注塑成型内应力的研究可以帮助我们了解注塑成型过程中塑料材料的变形和形状保持能力。
在注塑成型过程中,塑料材料会经历加热、熔化、注入、冷却和固化等阶段。
在这些过程中,塑料材料会因为温度变化和形状变化而产生内部应力。
通过研究这些内应力的产生机制和分布规律,我们可以更好地理解塑料材料的变形特性,从而提高产品的成型质量和性能。
其次,塑料注塑成型内应力的研究对于改善产品的外观和尺寸稳定性也具有重要作用。
塑料制品在注塑成型后,由于内部应力的存在,可能出现缩水、翘曲、变形等问题,从而影响产品的外观和尺寸稳定性。
通过研究内应力的分布规律,我们可以针对性地优化模具结构和成型工艺,控制塑料制品的变形,从而得到更好的外观和尺寸稳定性。
此外,塑料注塑成型内应力的研究还可以为改善塑料制品的力学性能提供指导。
塑料制品的力学性能包括强度、刚度、韧性等方面。
内应力的存在会影响塑料材料的分子结构和链层结构,从而对力学性能产生影响。
通过研究内应力与力学性能的关系,我们可以优化成型工艺和后处理工艺,提高塑料制品的力学性能。
需要注意的是,塑料注塑成型内应力的研究是一个复杂的课题,其中涉及到温度场、应力场、流动场等多个因素的相互作用。
因此,进行这方面的研究需要综合运用力学、热学、流体力学等多个学科的知识,并结合实验和数值模拟等方法进行。
只有通过深入研究和理解塑料注塑成型内应力的机理和规律,我们才能更好地控制塑料制品的成型过程,提高产品的质量和性能。
综上所述,《塑料注塑成型内应力研究》是一个有益且有挑战性的研究课题。
通过深入研究内应力的产生机制、分布规律和对塑料制品性能的影响,我们可以为改善塑料制品的成型质量、外观和力学性能提供重要的理论指导和实践应用。
注塑件内部应力消除策略

注塑件内部应力消除策略注塑件内部应力消除策略注塑件内部应力消除是注塑工艺中一个非常重要的环节。
当注塑件从模具中取出后,常常会出现内部应力过大的情况,这对于产品的性能和质量都会产生不良影响。
因此,我们需要采取一些策略来消除这些内部应力。
首先,选择合适的注塑工艺参数是消除内部应力的基础。
注塑工艺参数包括注塑温度、注塑速度、保压时间等。
通过合理地调整这些参数,可以使注塑件在注塑过程中获得均匀的内部结构,减少应力集中的情况发生。
其次,注意模具的设计和制造。
模具的设计和制造质量会直接影响注塑件的内部应力。
一个合理的模具设计应该考虑到塑料材料的流动性、收缩率等因素,以及注塑件的形状和结构。
同时,模具的制造精度也非常重要。
如果模具存在偏差或者不良加工,会导致注塑件在注塑过程中受到不必要的应力。
此外,适当的后处理也是消除内部应力的有效手段之一。
常见的后处理方式包括退火、加热和冷却等。
通过这些方法,可以使注塑件的内部结构重新排列,减少应力的积累。
需要注意的是,后处理的温度和时间需要控制得当,以免对注塑件的性能产生不良影响。
最后,定期进行内部应力测试也是非常重要的。
通过测试,可以及时发现注塑件内部应力的情况,以便及时采取相应的措施进行调整。
常用的内部应力测试方法有压力测试、拉伸测试和弯曲测试等。
总之,注塑件内部应力消除是注塑工艺中一项重要的任务。
通过选择合适的工艺参数、注意模具设计和制造、进行适当的后处理以及定期进行内部应力测试,可以有效地消除注塑件的内部应力,提高产品的性能和质量。
这需要注塑工程师具备丰富的经验和专业的知识,同时也需要相关的设备和技术支持。
只有综合运用各种策略,才能更好地解决注塑件内部应力的问题,确保产品的质量和可靠性。
注塑件内应力的产生及解决对策

注塑件内应力的产生及解决对策注塑件内应力的产生是由于注塑过程中的热胀冷缩效应引起的。
具体而言,注塑过程中,塑料在高温下进入模具中,然后在冷却过程中,塑料会收缩并形成注塑件。
然而,由于注塑过程中塑料的不均匀收缩,以及与模具之间的附着力,注塑件内部会形成应力。
1.外观缺陷:注塑件可能会出现翘曲、扭曲、脱模或开缺等问题,从而影响其外观质量。
2.尺寸变化:由于应力会导致塑料变形,从而导致注塑件的尺寸变化。
3.力学性能下降:注塑件的内应力可能导致其力学性能下降,使得产品更容易断裂或失效。
以下是一些解决注塑件内应力的对策:1.优化模具设计:合理的模具设计可以减少内应力的产生。
例如,通过增加模具冷却通道和增加射胶点的数量和位置等方式,可以加快注塑件的冷却速度,减少应力的产生。
2.优化材料选择:选择合适的塑料材料也可以减少内应力的产生。
一些塑料材料具有更低的热胀冷缩系数,可以减少注塑件的收缩程度和应力水平。
3.控制注塑工艺参数:合理控制注塑工艺参数也可以减少内应力的产生。
例如,调整注射速度、保压时间和冷却时间等,可以减少塑料的不均匀收缩,并减少应力的产生。
4.使用预应力技术:预应力技术可以在注塑过程中施加一定的压力,以减小注塑件形成后的应力水平。
这可以通过在注塑模具上加装压力缸或在模具关闭之前施加辅助压力等方式实现。
5.热处理和退火:对于内应力较高的注塑件,可以通过热处理或退火等热处理方法,来减小或消除部分内应力。
总之,在注塑件生产中,必须重视注塑件内应力的产生和解决。
通过合理的模具设计、优化材料选择、控制工艺参数、使用预应力技术以及热处理和退火等方法,可以有效减少内应力的产生,并优化注塑件的性能和外观质量。
注塑应力形成的原理及消除方案

如何检验塑胶件的应力如何去除应力A 、内应力产生的机理塑料内应力是指在塑料熔融加工过程中由于受到大分子链的取向和冷却收缩等因素而产生的一种内在应力..内应力的本质为大分子链在熔融加工过程中形成的不平衡构象;这种不平衡构象在冷却固化时不能立刻恢复到与环境条件相适应的平衡构象;这种不均衡构象的实质为一种可逆的高弹形变;而冻结的高弹形变平时以位能情势储存在塑料制品中;在合适的条件下;这种被迫的不稳定的构象将向自在的稳固的构象转化;位能改变为动能而开释..当大分子链间的作用力和相互缠结力蒙受不住这种动能时;内应力平衡即受到破坏;塑料制品就会产生应力开裂及翘曲变形等现象..B、塑料内应力产生的起因1取向内应力取向内应力是塑料熔体在流动充模和保压补料过程中;大分子链沿流动方向排列定向构象被冻结而产生的一种内应力..取向应力产生的详细过程为:近流道壁的熔体因冷却速度快而造成外层熔体粘度增高;从一而使熔体在型腔核心层流速远高于表层流速;导致熔体内部层与层之间受到剪切应力作用;产生沿流动方向的取向..取向的大分子链解冻在塑料制品内也就象征着其中存在未松弛的可逆高弹形变;所以说取向应力就是大分子链从取向构象力求过渡到无取向构象的内力..用热处理的方式;可降低或排除塑料制品内的取向应力..塑料制品的取向内应力分布为从制品的表层到内层越来越小;并呈抛物线变化..2冷却内应力冷却内应力是塑料制品在熔融加工过程中因冷却定型时收缩不均匀而产生的一种内应力..尤其是对厚壁塑料制品;塑料制品的外层首先冷却凝固收缩;其内层可能仍是热熔体;这徉芯层就会限度表层的收缩;导致芯层处于压应力状况;而表层处于拉应力状态..塑料制品冷却内应力的分布为从制品的表层到内层越来越大;并也呈抛物线变更...另外;带金属嵌件的塑料制品;因为金属与塑料的热胀系数相差较大;容易形成收缩不一平匀的内应力..除上述两种重要内应力外;还有以下多少种内应力:对结晶塑料制品而言;其制品内部各部位的结晶构造跟结晶度不同也会发生内应力..另外还有构型内应.力及脱模内应力等;只是其内应力听占比重都很小..C、影响塑料内应力产生的因素1分子链的刚性分子链刚性越大;熔体粘度越高;聚合物分子链运动性差;因而对于产生的可逆高弹形变恢复性差;易产生残余内应力口例如;一些分子链中含有苯环的聚合物;如PC、PPO、PPS等;其相应制品的内应力偏大..2分子链的极性一分子链的极性越大;分子间相互吸引的作用力越大;从而使分子间互相挪动艰苦增大;恢复可逆弹性形变的程度减小;导致残余内应力大..例如;一些分子链中含有羰基、酯基、睛基等极性基团的塑料种类;其相应制品的内应力较大..3代替基团的位阻效应大分子侧基取代基团的体积越大;则妨害大分子链自由活动导致残余内应力加大..例如;聚苯乙烯取代基团的苯基体积较大;因而聚苯乙烯制品的内应力较大.. 几种常见聚合物的内应力大小次序如下:PPO>PSF>PC>ABS>PA6>PP>HDPED、塑料内应力降低与疏散的把持1原料配方设计①选取分子量大、分子量分布窄的树脂聚合物分子量越大;大分子链间作用力和缠结程度增添;其制品抗应力开裂能力较强;聚合物分子量分布越宽;其中低分子量成分越大;轻易首先造成微观撕裂;造成应力集中;便制品开裂..②选取杂质含量低的树脂聚合物内的杂质等于应力的集中体;又会降低塑料的原有强度;应将杂质含量减少到最低程度..③共混改性易出现应力开裂的树脂与适宜的其它树脂共混;可降低内应力的存在程度..例如;在PC中混入适量PS;PS呈近似珠粒状分散于PC连续相中;可使内应力沿球面分散缓解并禁止裂纹扩大;从而达到降低内应力的目的..再如;在PC中混入适量PE ; PE球粒外沿可形成关闭的空化区;也可适当降低内应力..④加强改性用增强纤维进行增强改性;可以降低制品的内应力;这是因为纤维缠结了良多大分子链;从而提高应力开裂能力..例如;30%GFPC的耐应力开裂能力比纯PC提高6倍之多..⑤成核改性在结晶性塑料中参加相宜的成核剂;可以在其制品中形成很多小的球晶;使内应力降低并得到分散..2成型加工前提的节制在塑料制品的成型过程中;凡能减小制品中聚合物分子取向的成型因素都可能降低取向应力;但凡能使制品中聚合物均匀冷却的工艺条件都能降低冷却内应力;凡有助于塑料制品脱模的加工方法都有利于降低脱模内应力..对内应力影响较大的加工条件主要有如下几种..①料筒温度较高的料筒温度有利于取向应力的降低;这是因为在较高的料筒温度;熔体塑化均匀;粘度降落;流动性增加;在熔体充斥型腔过程中;分子取向作用小;因而取向应力较小..而在较低料筒温度下;熔体粘度较高;充模过程中分子取向较多;冷却定型后残余内应力则较大..但是;料筒温度太高也不好;太高容易造成冷却不充足;脱模时易造成变形;固然取向应力减小;但冷却应力和脱模应力反而增大..②模具温度模具温度的高下对取向内应力和冷却内应力的影响都很大..一方面;模具温度过低;会造成冷却加快;易使冷却不均匀而引起收缩上的较大差异;从而增大冷却内应力;另一方面;模具温度过低;熔体进入模其后;温度降低加快;熔体粘度增加迅速;造成在高粘度下充模;形成取向应力的程度明显加大..模温对塑料结晶影响很大;模温越高;越有利于晶粒堆砌严密;晶体内部的缺点减小或消除;从而减少内应力..另外;对于不同厚度塑料制品;其模温请求不同..对于厚壁制品其模温要适当高一些..③注射压力注射压力高;熔体充模进程中所受剪切作使劲大;产生取向应力的机遇也较大..因而;为了降低取向应力和打消脱模应力;应适当降低打针压力...④保压压力保压压力对塑料制品内应力的影响大于注射压力的影响..在保压阶段;跟着熔体温度的降低;熔体粘度敏捷增加;此时若施以高压;必定导致分子链的逼迫取向;从而形成更大的取向应力..⑤注射速度注射速度越快;越容易造成分子链的取向程度增加;从而引起更大的取向应力..但注射速渡过低;塑料熔体进入模腔后;可能先后分层而形成熔化痕;产生应力集中线;易产生应力开裂..所以注射速度以适中为宜..最好采用变速注射;在速度逐步减小下停止充模..⑥保压时间保压时间越长;会增大塑料熔体的剪切作用;从而产生更大的弹性形变;冻结更多的取向应力..所以;取向应力随保压时间延长和补料量增长而明显增大..⑦开模残余压力应适当调剂注射压力和保压时间;使开模时模内的残余压力濒临于大气压力;从而避免产生更大的脱模内应力..⑶塑料制品的设计①塑料制品的形状和尺寸在具体设计塑料制品时;为了有效地分散内应力;应遵守这样的准则:制品形状应尽可能坚持持续性;防止锐角、直角、缺口及忽然扩展或缩小..对于塑料制品的边沿处应设计成圆角;其中内圆角半径应大于相邻两壁中薄者厚度的70%以上;外圆角半径则根据制品形状而肯定..对于壁厚相差较大的部位;因冷却速度不同;易产生冷却内应力及取向内应力..因此;应设计成壁厚尽可能匀称的制件;如必需壁厚不平均;则要进行壁厚差别的渐变过渡..②合理设计金属嵌件塑料与金属的热膨胀系数相差5~10倍;因此带金属嵌件的塑料制品在冷却时;两者构成的收缩水平不同;因塑料的压缩比拟大而牢牢抱住金属嵌件;在嵌件四周的塑料内层受压应力;而外层受拉应力作用;产生应力集中景象..在详细设汁嵌件时;应留神如下几点;以辅助减小或消除内应力..a.尽可能抉择塑料件作为嵌件..b.尽可能取舍与塑料热膨胀系数相差小的金属材料做嵌件资料;如铝、铝合金及铜等..c.在金属嵌件上涂覆一层橡胶或聚氨酯弹性缓冲层;并保障成型时涂覆层不融化;可降低两者收缩差..d.对金属嵌件进行名义脱脂化处理;能够避免油脂加速制品的应力开裂..e.金属嵌件进行适当的预热处理..f.金属嵌件周围塑料的厚度要充分..例如;嵌件外径为D;嵌件周围塑料厚度为h;则对铝嵌件塑料厚度h≥0.8D;对于铜嵌件;塑料厚度h≥0.9 D..g.金属嵌件应设计成油滑形状;最好带精巧的滚花纹..③塑料制品上孔的设计塑料制品上孔的形状、孔数及孔的位置都会对内应力集中程度产生很大的影响.. 为避免应力开裂;切忌在塑料制品上开设棱形、矩形、方形或多边形孔..应尽可能开设圆形孔;其中卵形孔的效果最好;并应使椭圆形孔的长轴平行于外力作用方向..如开设圆孔;可增开等直径的工艺圆孔;并使相邻两圆孔的中央衔接线平行于外力作用方向;这样可以获得与椭圆孔相似的效果;还有一种方法;即在圆孔周围开设对称的槽孔;以分散内应力..⑷塑料模具的设计在设计塑料模具时;浇注系统和冷却系统对塑料制品的内应力影响较大;在具体设计时应注意如下几点..①浇口尺寸过大的浇口将须要较长的保压补料时间;在降温过程中的补料流动一定会冻结更多的取向应力;尤其是在补填冷料时;将给浇口附近造成很大的内应力..恰当缩小浇口尺寸;可缩短保压补料时光;下降浇口凝封时模内压力;从而降低取向应力..但过小的浇口将导致充模时间延伸;造成制品缺料..②浇口的地位浇口的位置决议厂塑料熔体在模腔内的流动情形、流动间隔和流动方向...当浇口设在制品壁厚最大部位时;可适当降低注射压力、保压压力及保压时间;有利于降低取向应力..当浇口设在薄壁部位时;宜适当增加浇口处的壁厚;以降低浇口附近的取向应力..熔体在模腔内流动距离越长;产生取向应力的几率越大..为此;对于壁厚、长流程且面积较大的塑料件;应适当分布多个浇口;能有效地降低取向应力;防止翘曲变形..另外;因为浇口四周为内.应力多发地带;可在浇口附近设汁成护耳式浇日;使内应力产生在护耳中;脱模后切除内应力较大的护耳;可降低塑料制品内的内应力..③流道的设计设计短而粗的流道;可减小熔体的压力丧失和温度降;相应降低注射压力和冷却速度;从而降低取向应力和冷却压力..④冷却体系的设计冷却水道的散布要公道;使浇口邻近、阔别浇口区、壁厚处、壁薄处都得到平均且迟缓的冷却;从而降低内应力;⑤顶出系统的设计要设计适当的脱模锥度;较高的型芯光洁度和较大面积的顶出部位;以预防强行脱模产生脱模应力..E、塑料应力的检测方法1.溶济法⑴醋酸沉浸所使用的乙酸CH3COOH必须是95%以上的乙酸且反复使用次数不得超过10次测试.①表面应力测试:将乙酸冰醋酸倒入玻璃器皿中;将产品完全浸在乙酸里;时间为30秒..30秒后用夹子将样品取出并马上用净水自来水即可冲刷清洁;察看样品表面有无发白及裂纹..断定:不得有任何开裂现象;容许表面有稍微发白..②内应力测试:将表面应力测试及格的样品擦干后完全浸在乙酸里;时间为2分钟..2分钟后将样品取出并当即用清水自来水即可冲洗干净;视察样品有无发白及裂纹..判断:不得有任何断裂现象;许可镶件处有轻微裂纹及表面发白现象..⑵甲乙酮 + 丙酮沉迷法:将整机完整浸入21摄氏度的1:1的甲乙酮 + 丙酮的混杂液中;掏出后即时甩干;依上法检讨.原理:根据介质应力决裂的现象;即溶济分子渗透到树脂的大分子之间后;降低了分子之间的彼此作用力..内应力大的地方在浸入前分子之间的作用力原来就有所削弱;浸入溶济后这些减弱了的处所进一步减弱;而引起开裂;内应力小的地方在短时间内不会开裂..因此;可以从待镀件表面开裂的时间和程度来断定镀件内应力的大小及其部位..从而断定塑料件是否进行电镀..2.仪器法用偏振光照耀塑料制件;视彩色光带多寡;剖析内应力的强弱;它只适用于透明的制件..偏振光法所要的仪器昂贵;操作庞杂;且正确度不高;因为制件处理前后变化不显着;光谱带上涌现的光带不一定都是内应力的影响;如制件表面的涟漪也会影响检验的成果..不外此法对制件的机能尚无任何影响;为无损检验;经检验过的制件可继承电镀和使用..3.温度骤变法这种方法是将塑料待镀件重复受冷受热;依据裂纹呈现的时间是非来评定内应力的大小..它实用于各类塑料成形件..温度骤变法所要的装备简略;然而测验时间较长..经检修后的塑料件已被损坏;不能持续应用..F、塑料制品应力的去除处理塑料制品的热处理是指将成型制品在必定温度下停留一段时间而消除内应力的办法..让制件在一定的温度下;恒温数小时;使其内局部子从新排列从而到达减少或清除内应力的目标.对制件进行热处理;可以使高聚物分子由不平衡构象向平衡构象转变;使强制冻结的处于不稳定的高弹形变取得能量而进行热松弛;从而降低或基础消除内应力..常采用的热处理温度高于制件使用温度10~20℃或低于热变形温度5~10℃..热处理时间取决于塑料品种、制件厚度、热处理温度和注塑条件..个别厚度的制件;热处理1~2小时即可;随着制件厚度增大;热处理时间应适当延长..提高热处理温度和延长热处理时间存在类似的效果;但温度的后果更显明些..热处理方法是将制件放入水、甘油、矿物油、乙二醇和液体石蜡等液体介质中;或放入空气轮回烘箱中加热到指定温度;并在该温度下停留一定时间;而后缓慢冷却到室温..试验表明;脱模后的制件立刻进行热处理;对降低内应力、改良制件性能的效果更明显..此外;提高模具温度;延长制件在模内冷却时间;脱模落后行保温处理都有相似热处理的作用..ABS塑料件在成形时;B粒子成不规矩的非球外形图4-151;引起残余应力;把这种塑料件放在80℃下热处置两个小时;B粒子变成球形状图4-152残余应力大大减少;还可进步镀层的结协力..4-15 1 塑料成形时B粒子成不规则的非球形状4-15 2 热处理80℃两个小时后B粒子变成球形状但是由于热处理时间较长;而且费电;所以国外对ABS塑料件的应力去除已不在用这种方法;采取的是另一种方法:水和丙酮的混合液..用水和丙酮为4:1的混合液;在室温下浸泡5分钟;便可消除应力;同时丙酮又有脱脂去油的才能;故把这种方法称为脱脂整面使B粒子变成球形状二合一..常用塑料件的热处理温度ABS塑料件 65-------75℃聚丙稀 80-----100℃氯化聚醚 80------120℃聚甲醛 90------120℃聚碳酸脂 110-----130℃聚砜 100-----120℃改性聚苯乙烯 50--------60℃聚苯醚 100-----120℃。
塑料内应力分析

内应力控制塑料内应力是指在塑料熔融加工过程中由于受到大分子链的取向和冷却收缩等因素而响而产生的一种内在应力。
内应力的实质为大分子链在熔融加工过程中形成的不平衡构象,这种不平衡构象在冷却固化时不能立即恢复到与环境条件相适应的平衡构象,这种不平衡构象的实质为一种可逆的高弹形变,而冻结的高弹形变平时以位能形式贮存在塑料制品中,在适宜的条件下,这种被迫的不稳定的构象将向自由的稳定的构象转化,位能转变为动能而释放。
当大分子链间的作用力和相互缠结力承受不住这种动能时,内应力平衡即遭到破坏,塑料制品就会产生应力开裂及翘曲变形等现象。
几乎所有塑料制品都会不同程度地存在内应力,尤其是塑料注射制品的内应力更为明显。
内应力的存在不仅使塑料制品在贮存和使用过程中出现翘曲变形和开裂,也影响塑料制品的力学性能、光学性能、电学性能及外观质量。
为此,必须找出内应力产生的原因及消除内应力的办法,最大程度地降低塑料制品内部的应力,并使残余内应力在塑料制品上尽可能均匀地分布,避免产生应力集中现象,从而改善塑料制品的力学1热学等性能。
塑料内应力产生的原因产生内应力的原因有很多,如塑料熔体在加工过程中受到较强的剪切作用,加工中存在的取向与结晶作用,熔体各部位冷却速度极难做到均匀一致,熔体塑化不均匀,制品脱模困难等,都会引发内应力的产生。
依引起内应力的原因不同,可将内应力分成如下几类。
(1)取向内应力取向内应力是塑料熔体在流动充模和保压补料过程中,大分子链沿流动方向排列定向构象被冻结而产生的一种内应力。
取向应力产生的具体过程为:*近流道壁的熔体因冷却速度快而造成外层熔体粘度增高,从一而使熔体在型腔中心层流速远高于表层流速,导致熔体内部层与层之间受到剪切应力作用,产生沿流动方向的取向。
取向的大分子链冻结在塑料制品内也就意味着其中存在未松弛的可逆高弹形变,所以说取向应力就是大分子链从取向构象力图过渡到无取向构象的内力。
用热处理的方法,可降低或消除塑料制品内的取向应力。
塑胶制品如何去除内应力?

(2)嵌件周围的塑料应有足够的厚度,否则会由于存在收缩应力而开裂;
(3)嵌件的顶部也应有足够厚的塑料层,否则嵌件顶部塑件表面会出现鼓包或裂纹;
(4)嵌件不应带尖角、锐边,以减少应力集中;
(5)热塑性塑料注射成型时,将金属嵌件预热到接近物料温度,可减少由于金属与塑料热膨胀系数不同而产生的收缩应力;
3.5注塑成型工艺条件
注塑制品由于成型工艺特点不可避免的存在内应力,但工艺条件控制得当就会使塑件内应力降低到最小程度,能够保证制件的正常使用。相反,如果工艺控制不当,制件就会存在很大的内应力,不仅使制件强度下降,而且在储存和使用过程中出现翘曲变形甚至开裂。需要控制的工艺条件如嵌件预热、模具温度、加工温度、注射速度、注射压力、保压压力、注射时间、保压时间、冷却时间等。温度、压力、时间是塑料成型工艺的主要因素。
3.1.3金属嵌件
由于金属嵌件冷却时尺寸变化与塑料的热收缩值相差很大,使嵌件周围产生很大的内应力,而造成塑件的开裂。对某些高刚性的工程塑料更甚,如聚碳酸酯;但对于弹性和冷流动性大的塑料则应力值较低。当有金属嵌件存在时,应尽量避免制件开裂:
(1)如能选用与塑料线膨胀系数相近的金属作嵌件,内应力值可以降低;
2.1取向应力
高分子取向使制件内存在着未松弛的高弹形变,主要集中在表层和浇口的附近,使这些地方存在着较大的取向应力,用退火的方法可以消除制件的取向应力。试验表明,提高加工温度和模具温度、降低注射压力和注射速度、缩短注射时间和保压时间都能在不同程度上使制件的取向应力减小。
2.2体积温度应力
除相交表面的尖角外,尖锐的螺纹牙也是严重的应力集中源,采用倒圆角的螺纹可减少应力集中,提高螺纹强度。
3.1.2制品壁厚
制品壁厚是结构设计时所需要考虑的重要因素。不合理的壁厚会给制品带来很多缺陷。增加壁厚既可改善树脂的充模特性,又可降低取向应力,减少变形,提高制品强度。但同时收缩加大,保压和冷却时间加长,生产效率降低,消耗材料多。较大的收缩应力还将造成制品表面产生凹陷或内部出现缩孔与气泡,既影响外观又降低了强度。增加壁厚的同时也增加了制品的表面积,表面积与体积之比越大,表面冷却越快,取向应力和体积温度应力都随之增大。如果制品壁太薄,会降低强度,脱模时易破裂,还有碍于树脂的充模流动,造成填充不足或出现明显的熔合纹,严重影响制品质量。每种塑料根据充模能力都有一个最小壁厚。确定壁厚时在满足强度要求的前提下,壁厚尽量取薄些,可节省材料,减轻制品重量,降低成本,但不能小于最小壁厚。ABS常用的标准壁厚为1.2~3.5mm。壁厚设计还应注意均匀一致,否则将会由于收缩应力引起制品的翘曲变形。同一制品中,若必须存在壁厚相差较大的情况时,连接处应逐渐过渡,避免截面的突变。
注塑制品内应力的分析及控制

注塑制品内应力的分析及控制注塑成型是一种常见的塑料制品成型方法,其特点是成型周期短、生产效率高、成型精度高等。
然而,注塑制品在生产过程中往往会产生内应力,如果不及时进行分析和控制,会对产品的质量和性能造成不利影响。
本文将从注塑制品内应力的分析和控制两个方面进行详细探讨。
一、注塑制品内应力分析1.内应力形成原因:注塑制品在注塑过程中,由于塑料材料的热胀冷缩、固化收缩以及注塑工艺参数的变化等原因,会产生一定的内应力。
内应力存在的主要原因包括材料性能、注塑工艺参数、产品几何形态等。
2.内应力对产品的影响:内应力会直接影响注塑制品的力学性能、外观质量和尺寸稳定性。
例如,内应力过大会导致产品变形、开裂,甚至影响产品的使用寿命。
因此,分析注塑制品内应力,对产品质量的控制至关重要。
二、注塑制品内应力的控制1.材料选择:合理选择适合注塑成型的塑料材料,具有良好的流动性、热稳定性和机械性能。
材料的选择与产品的使用环境及要求有关,同时要考虑到产品的成本控制。
2.工艺参数控制:合理调整注塑工艺参数,包括注塑温度、注塑压力、注射速度等。
通过优化工艺参数,可以减小注塑过程中的温度梯度和压力差,减少内应力的产生。
3.产品设计优化:在注塑制品的产品设计阶段,考虑使用适当的加强件、结构设计等手段,使得产品的应力分布更加均匀,减少应力集中的区域。
4.合理模具设计:模具结构的设计对于控制注塑制品的内应力也非常重要。
合理的模具结构可以减小内应力的产生,减轻产品变形的风险。
5.后处理措施:包括产品的冷却、固化和放松等过程,都可以对内应力进行控制。
通过合理的冷却方式和固化条件,可以使注塑制品内部的应力得到释放和均衡。
6.检测与调整:对于关键零件和高要求的注塑制品,可以采用应力检测等方法,及时发现问题,进行调整和优化。
综上所述,注塑制品内应力的分析和控制对于改善产品质量、提高生产效率至关重要。
通过合理的材料选择、工艺参数控制、产品设计优化、模具设计、后处理措施以及检测和调整等综合手段,可以降低内应力的产生,保证产品的力学性能和外观质量。
塑料件应力开裂原因分析及检测方法简述

塑料件应力开裂原因分析及检测方法简述文稿归稿存档编号:[KKUY-KKIO69-OTM243-OLUI129-G00I-FDQS58-塑料件应力开裂原因分析及检测方法简述几乎所有塑料制品都会不同程度地存在内应力,尤其是塑料注射制品的内应力更为明显。
内应力的存在不仅使塑料制品在储存和使用过程中出现应力开裂和翘曲变形,也影响塑料制品的力学性能、光学性能、电学性能及外观质量等。
应力开裂的必要条件是试样或零件内存在应力,并存在某种应力集中因素如缺口、表面划伤等。
那么塑件应力从何而来呢?塑胶件内应力产生的原因依引起内应力的原因不同,可将内应力分成如下几类:(1)取向内应力取向内应力是塑料熔体在流动充模和保压补料过程中,大分子链沿流动方向排列定向构象被冻结而产生的一种内应力。
取向的大分子链冻结在塑料制品内也就意味着其中存在未松弛的可逆高弹形变,所以说取向应力就是大分子链从取向构象力图过渡到无取向构象的内力。
塑料制品的取向内应力分布为从制品的表层到内层越来越小,并呈抛物线变化。
(2)冷却内应力冷却内应力是塑料制品在熔融加工过程中因冷却定型时收缩不均匀而产的一种内应力。
尤其对厚壁塑料制品,塑料制品的外层首先冷却凝固收缩,其内层可能还是热熔体,这徉芯层就会限制表层的收缩,导致芯层处于压应力状态,而表层处于拉应力状态。
塑料制品冷却内应力的分布为从制品的表层到内层越来越大,并也呈抛物线变化。
另外,带金属嵌件的塑料制品,由于金属与塑料的热胀系数相差较大,容易形成收缩不一均匀的内应力。
(3)环境应力环境应力开裂是聚烯烃类塑料的特有现象,它是指当制品存在应力时,与某些活性介质接触,会出现脆性裂纹,最终可能导致制品破坏。
这些活性物质可以是洗涤剂、皂类、水、油、酸、碱、盐及对材料并无显着溶胀作用的有机溶剂。
原料混有其它杂质或掺杂不适当的或过量的溶剂或其它添加剂时,在某些应力集的位置就会导致裂纹。
有些塑料如ABS等,在受潮状况下加热会与水汽发生催化裂化反应,使制件发生大的应变从而开裂。
注塑件的应力变形分析及解决对策
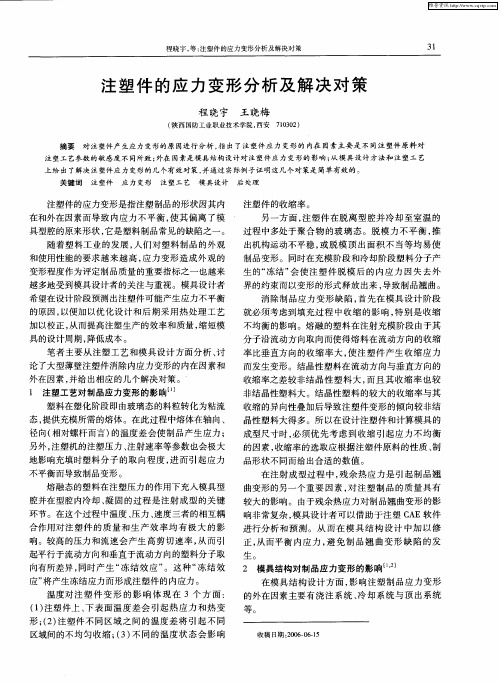
2 模 具结 构 对制 品应 力 变 形的 影 响 ¨ 在模 具 结 构 设 计 方 面 , 响注 塑 制 品应 力 变形 影
的外在因素主要有浇注系统 、 冷却 系统与顶 出系统
等。
收稿 日期 :0 6 0 -5 2 0 -61
形 ;2 注塑件不 同区域之间 的温度差将 引起不 同 ()
关 键 词 注 塑件 应 力 变 形 注 塑 工 艺 模 具设 计 后 处 理
注塑件 的应 力 变形 是指 注 塑制 品 的形 状 因其 内
注塑件 的收缩率。 另一方面 , 注塑件在脱离型腔并 冷却至室温的 过程中多处于聚合物的玻璃态。脱 模力不平衡 , 推 出机构运动不平稳 , 或脱模顶 出面积不 当等均易使 制品变形。同时在充模阶段和冷却阶段塑料分子产
较大的影响。由于残余热应力对制品翘 曲变形的影 响非常复杂 , 模具设计者可以借助于注塑 C E软件 A 进行分析和 预测。从 而在模 具结构 设计 中加 以修 正, 从而平衡 内应 力 , 避免制 品翘 曲变形缺 陷 的发
生。
腔并在型腔内冷却 、 固的过程是注射成型的关键 凝 环节 。在 这个过 程 中温 度 、 压力 、 速度 三 者 的相互 耦 合作用对注塑件 的质 量和生 产效率均 有极大 的影 响。较高的压力和流速会产生 高剪切速率 , 从而引
外在因素 , 并给出相应的几个解决对策。 1 注 塑工 艺对 制 品应力 变 形的 影响 …
塑 料 在塑化 阶段 即 由玻 璃态 的料 粒转 化 为粘 流 态 , 充模 所需 的熔体 。在此 过程 中熔 体在 轴 向 、 提供 径 向( 相对 螺杆 而言 ) 的温 度 差会 使 制 品产 生 应力 ;
变形 程度 作为评 定 制 品质量 的重要指 标之 一 也越 来 越多地 受 到模具 设 计者 的关 注与 重视 。模 具设 计者 希望在 设计 阶段 预 测 出注塑 件可 能产 生 应力不 平衡 的原 因 , 以便加 以优 化设 计 和 后 期 采 用 热 处 理 工 艺
注塑件内应力的产生及解决对策

注塑件内应力的产生及解决对策
一般射出成品定型前,存在成品内部的压力约为300kg/cm2 -500kg/cm2之间,如因调整不当造成射胶压力过高,射入模内虽经过浇道、浇口、成品之间的阻力以及成品逐渐冷却,压力逐渐之降低,而存在成品内部进胶口及远端之压力不同,成品经过一段时日于热接触,内应力渐渐释放出来而造成变形或破裂。
内应力太高时,可实施退火处理解决。
内应力的产生:
(1)过度充填。
(2)肉厚不均,gate开设在肉薄处。
(3)密度太商而造成脱膜困难。
(4)埋入件周围应变所致,易造成龟裂及冷热差距过大而使收缩不同所致,欲使埋入件周围充填饱模,需施加较大的射压,形成有过大的残留应力。
(5)直接浇口肉薄而又浅口者极易残留应力。
(6)结晶性塑胶、冷却太快内应力不易释放出来。
解决及对策:
(1)提高料温、模温,在各原料标准条件内设定。
(2)缩短保压时间。
(3)非结晶性塑胶,保压压力不需太高,乃因较不会缩水。
(4)肉厚设计要均匀gate开设在肉厚处。
(5)顶出要均匀。
(6)埋植件要预热(用夹子或手套塞入)。
(7)避免用新次料混合,如PC易加水分解,如需混合要彻底烘干。
(8)加大竖浇口、横浇道、浇口等,以减少流动阻力,成形品远处易于传达。
(9)已发生之产生可实施退火处理,依二及二-1之条件实施。
(10)加大射嘴射径,长射嘴需加热片控制。
(11)工程塑胶及加玻纤者需用模温60℃以上成型。
注塑零件的内应力分析及控制-精

注塑制品内注塑制品内应力应力应力的分析及控制的分析及控制在注塑加工过程中,注塑制品存在着一个内在的质量问题-内应力。
内应力的来源与所使用的塑料原料种类、注塑机的类型与塑化系统的结构、模具的结构及精度、塑料制品的结构、注塑成型的工艺参数的设定及控制、生产环境及操作者的状态等有关。
其中任何一项出现问题,都将影响到制品的质量。
而且,由于制品的表面质量是内在质量的反映,所以,凡是能引起制品内在质量的因素,都能同时引起制品的表面质量及其他质量问题,如引起制品的开裂、银纹、翘曲、变形、力学强度降低,甚至失去使用价值等问题。
由于注塑过程中,除了引起制品翘曲变形的内应力可以直观感觉到外,其它质量问题不但用肉眼看不到,而且在短时间内也没有表露出来。
所以注塑加工现场的工程人员对于这个问题一般不很重视,但是却可能存在着很大的质量隐患。
所以,本文针对内应力这个内在的质量问题展开分析,并提出控制的一些方法,希望对现场控制产品质量的工程人员有所帮助和启示。
一、内应力应力的种类及产生原因的种类及产生原因注塑制品的内应力主要有以下四种:1、温度应力:是制品冷却时温度不均产生的应力。
当熔体进入温度较低的模具时,靠近模腔壁的熔体迅速地冷却而固化。
由于凝固的聚合物层导热性很差,因而在制品厚度方向上产生较大的温度梯度。
先凝固的外层熔体要阻止后凝固的内层熔体的收缩,结果在外层产生压应力(收缩应力),内层产生拉应力(取向应力)。
另方面,因制品壁厚不均匀,冷却速度不一致,从而产生冷却温度不均现象。
2、取向应力:是制品内部大分子取向产生的应力。
对于线形树脂和纤维增强的塑料,在加工中最容易产生取向应力。
其结果,沿着流动方向的分子取向程度最大,在速冷条件下,如果被拉直的分子链来不及松弛,则在该方向上产生了取向应力。
3、收缩应力:注塑过程中,塑料分子本身的平衡状态受到破坏,并产生不平衡体积时的应力。
如结晶塑料的晶区与非晶区界面因收缩不均产生的内应力。
塑胶应力分析
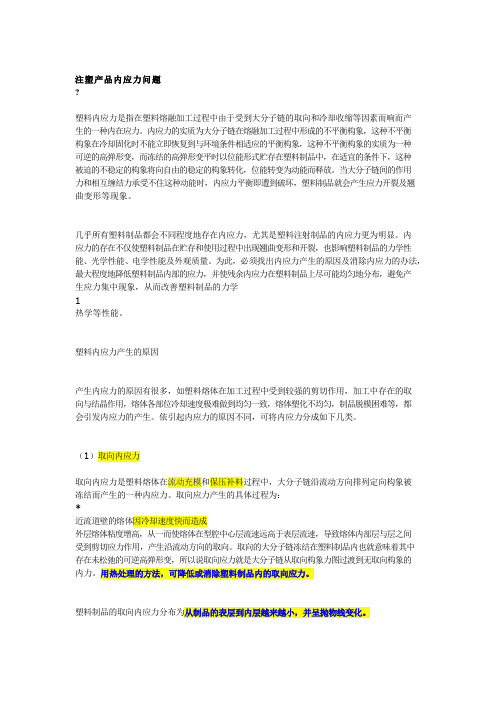
注塑产品内应力问题?塑料内应力是指在塑料熔融加工过程中由于受到大分子链的取向和冷却收缩等因素而响而产生的一种内在应力。
内应力的实质为大分子链在熔融加工过程中形成的不平衡构象,这种不平衡构象在冷却固化时不能立即恢复到与环境条件相适应的平衡构象,这种不平衡构象的实质为一种可逆的高弹形变,而冻结的高弹形变平时以位能形式贮存在塑料制品中,在适宜的条件下,这种被迫的不稳定的构象将向自由的稳定的构象转化,位能转变为动能而释放。
当大分子链间的作用力和相互缠结力承受不住这种动能时,内应力平衡即遭到破坏,塑料制品就会产生应力开裂及翘曲变形等现象。
几乎所有塑料制品都会不同程度地存在内应力,尤其是塑料注射制品的内应力更为明显。
内应力的存在不仅使塑料制品在贮存和使用过程中出现翘曲变形和开裂,也影响塑料制品的力学性能、光学性能、电学性能及外观质量。
为此,必须找出内应力产生的原因及消除内应力的办法,最大程度地降低塑料制品内部的应力,并使残余内应力在塑料制品上尽可能均匀地分布,避免产生应力集中现象,从而改善塑料制品的力学1热学等性能。
塑料内应力产生的原因产生内应力的原因有很多,如塑料熔体在加工过程中受到较强的剪切作用,加工中存在的取向与结晶作用,熔体各部位冷却速度极难做到均匀一致,熔体塑化不均匀,制品脱模困难等,都会引发内应力的产生。
依引起内应力的原因不同,可将内应力分成如下几类。
(1)取向内应力取向内应力是塑料熔体在流动充模和保压补料过程中,大分子链沿流动方向排列定向构象被冻结而产生的一种内应力。
取向应力产生的具体过程为:*近流道壁的熔体因冷却速度快而造成外层熔体粘度增高,从一而使熔体在型腔中心层流速远高于表层流速,导致熔体内部层与层之间受到剪切应力作用,产生沿流动方向的取向。
取向的大分子链冻结在塑料制品内也就意味着其中存在未松弛的可逆高弹形变,所以说取向应力就是大分子链从取向构象力图过渡到无取向构象的内力。
用热处理的方法,可降低或消除塑料制品内的取向应力。
塑料内应力形成的原理消除方案及检测方法
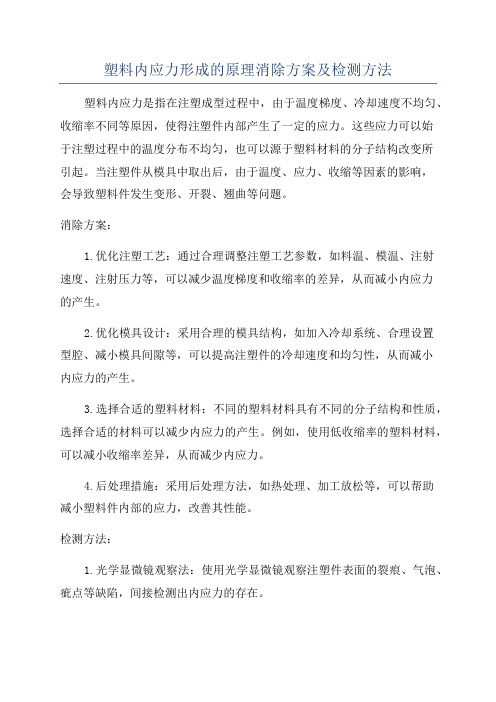
塑料内应力形成的原理消除方案及检测方法塑料内应力是指在注塑成型过程中,由于温度梯度、冷却速度不均匀、收缩率不同等原因,使得注塑件内部产生了一定的应力。
这些应力可以始于注塑过程中的温度分布不均匀,也可以源于塑料材料的分子结构改变所引起。
当注塑件从模具中取出后,由于温度、应力、收缩等因素的影响,会导致塑料件发生变形、开裂、翘曲等问题。
消除方案:1.优化注塑工艺:通过合理调整注塑工艺参数,如料温、模温、注射速度、注射压力等,可以减少温度梯度和收缩率的差异,从而减小内应力的产生。
2.优化模具设计:采用合理的模具结构,如加入冷却系统、合理设置型腔、减小模具间隙等,可以提高注塑件的冷却速度和均匀性,从而减小内应力的产生。
3.选择合适的塑料材料:不同的塑料材料具有不同的分子结构和性质,选择合适的材料可以减少内应力的产生。
例如,使用低收缩率的塑料材料,可以减小收缩率差异,从而减少内应力。
4.后处理措施:采用后处理方法,如热处理、加工放松等,可以帮助减小塑料件内部的应力,改善其性能。
检测方法:1.光学显微镜观察法:使用光学显微镜观察注塑件表面的裂痕、气泡、疵点等缺陷,间接检测出内应力的存在。
2.射线衍射法:通过使用射线衍射技术,对注塑件进行射线照射后,观察衍射图案的变化,可以判断出注塑件中的应力分布情况。
3.室温拉伸试验法:对注塑件进行拉伸试验,在试验过程中观察和记录试样的变形情况,通过分析变形程度和变形形状,可以间接推断出注塑件中的内应力程度。
4.热膨胀法:测量注塑件在不同温度下的尺寸变化,通过分析尺寸变化规律,可以推断出注塑件中的内应力分布情况。
总结:塑料内应力是注塑件常见的质量问题之一,可以通过优化注塑工艺、模具设计、选择合适的材料和后处理措施来减小或消除内应力的产生。
同时,通过光学显微镜观察、射线衍射、室温拉伸试验和热膨胀等检测方法,可以对注塑件的内应力进行检测和分析。
注塑制品内应力产生分析
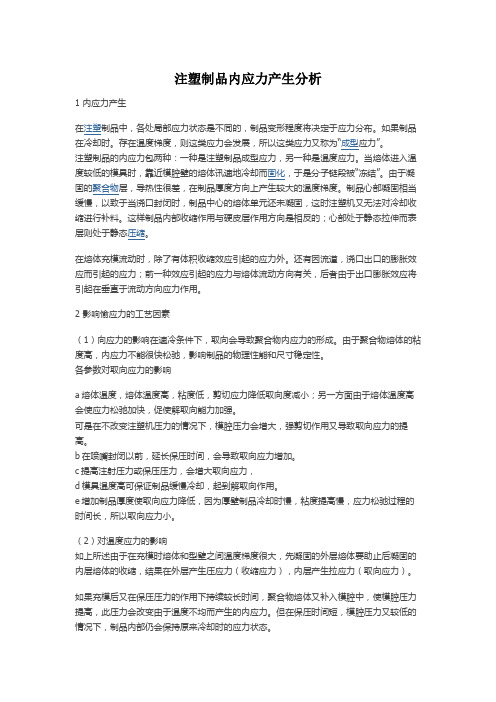
注塑制品内应力产生分析1 内应力产生在熔体充模流动时,除了有体积收缩效应引起的应力外。
还有因流道,浇口出口的膨胀效应而引起的应力;前一种效应引起的应力与熔体流动方向有关,后者由于出口膨胀效应将引起在垂直于流动方向应力作用。
2 影响愉应力的工艺因素(1)向应力的影响在速冷条件下,取向会导致聚合物内应力的形成。
由于聚合物熔体的粘度高,内应力不能很快松驰,影响制品的物理性能和尺寸稳定性。
各参数对取向应力的影响a熔体温度,熔体温度高,粘度低,剪切应力降低取向度减小;另一方面由于熔体温度高会使应力松驰加快,促使解取向能力加强。
可是在不改变注塑机压力的情况下,模腔压力会增大,强剪切作用又导致取向应力的提高。
b在喷嘴封闭以前,延长保压时间,会导致取向应力增加。
c提高注射压力或保压压力,会增大取向应力,d模具温度高可保证制品缓慢冷却,起到解取向作用。
e增加制品厚度使取向应力降低,因为厚壁制品冷却时慢,粘度提高慢,应力松驰过程的时间长,所以取向应力小。
(2)对温度应力的影响如上所述由于在充模时熔体和型壁之间温度梯度很大,先凝固的外层熔体要助止后凝固的内层熔体的收缩,结果在外层产生压应力(收缩应力),内层产生拉应力(取向应力)。
如果充模后又在保压压力的作用下持续较长时间,聚合物熔体又补入模腔中,使模腔压力提高,此压力会改变由于温度不均而产生的内应力。
但在保压时间短,模腔压力又较低的情况下,制品内部仍会保持原来冷却时的应力状态。
如果在制品冷却初期模腔压力不足时,制品的外层会因凝固收缩而形成凹陷;如果在制品已形成冷硬层的后期模腔压力不足时,制品的内层会因收缩而分离,或形成空穴;如果在浇口封闭前维持模腔压力,有利于提高制品密度,消除冷却温度应力,但是在浇口附近会产生较大的应力集中。
由此看来热塑性聚合物在成型时,模内压力越大保压时间越长,有助于温度所产生的收缩应力的减小反之会使压缩应力增大。
3内应力与制品质量的关系制品中内应力的存在会严重影响制品的力学性质和使用性能;由于制品内应力的存在和分布不均,制品在使用过程中会发生裂纹。
注塑产品内应力问题

注塑产品内应力问题?塑胶产品在注塑得过程中往往会产生内应力,如不加以消除会对后序喷涂产生不良、有几个问题请高手赐1内应力就是怎么产生得,它与哪些因素有关?ﻫ2内应力如何检测,有什么直观且方便得方法?教:ﻫ3内应力如何消除,有没有方便快捷操作性强得方法?4内应力对喷涂到底还有哪些影响?内应力在其它方面还有什么危害?它有没有有利得一面呢?ﻫ下面就是回答请高手亮招所谓应力,就是指单位面积里物体所受得力,它强调得就是物体内部得受力状况;一般物体在受到外力作用下,其内部就会产生抵抗外力得应力;物体在不受外力作用得情况下,内部固有得应力叫内应力,它就是由于物体内部各部分发生不均匀得塑性变形而产生得。
按照内应力作用得范围,可将它分为三类:(一)第一类内应力(宏观内应力),即由于材料各部分变形不均匀而造成得宏观范围内得内应力;(二)第二类内应力(微观内应力),即物体得各晶粒或亚晶粒(自然界中,绝大多数固体物质都就是晶体)之间不均匀得变形而产生得晶粒或亚晶粒间得内应力;(三)第三类内应力(晶格畸变应力),即由于晶格畸变,使晶体中一部分原子偏离其平衡位置而造成得内应力,它就是变形物体(被破坏物体)中最主要得内应力。
塑料内应力就是指在塑料熔融加工过程中由于受到大分子链得取向与冷却收缩等因素而响而产生得一种内在应力。
内应力得实质为大分子链在熔融加工过程中形成得不平衡构象,这种不平衡构象在冷却固化时不能立即恢复到与环境条件相适应得平衡构象,这种不平衡构象得实质为一种可逆得高弹形变,而冻结得高弹形变平时以位能形式贮存在塑料制品中,在适宜得条件下,这种被迫得不稳定得构象将向自由得稳定得构象转化,位能转变为动能而释放.当大分子链间得作用力与相互缠结力承受不住这种动能时,内应力平衡即遭到破坏,塑料制品就会产生应力开裂及翘曲变形等现象.ﻫ几乎所有塑料制品都会不同程度地存在内应力,尤其就是塑料注射制品得内应力更为明显。
内应力得存在不仅使塑料制品在贮存与使用过程中出现翘曲变形与开裂,也影响塑料制品得力学性能、光学性能、电学性能及外观质量。
- 1、下载文档前请自行甄别文档内容的完整性,平台不提供额外的编辑、内容补充、找答案等附加服务。
- 2、"仅部分预览"的文档,不可在线预览部分如存在完整性等问题,可反馈申请退款(可完整预览的文档不适用该条件!)。
- 3、如文档侵犯您的权益,请联系客服反馈,我们会尽快为您处理(人工客服工作时间:9:00-18:30)。
注塑制品内应力的分析及控制在注塑加工过程中,注塑制品存在着一个内在的质量问题-内应力。
内应力的来源与所使用的塑料原料种类、注塑机的类型与塑化系统的结构、模具的结构及精度、塑料制品的结构、注塑成型的工艺参数的设定及控制、生产环境及操作者的状态等有关。
其中任何一项出现问题,都将影响到制品的质量。
而且,由于制品的表面质量是内在质量的反映,所以,凡是能引起制品内在质量的因素,都能同时引起制品的表面质量及其他质量问题,如引起制品的开裂、银纹、翘曲、变形、力学强度降低,甚至失去使用价值等问题。
由于注塑过程中,除了引起制品翘曲变形的内应力可以直观感觉到外,其它质量问题不但用肉眼看不到,而且在短时间内也没有表露出来。
所以注塑加工现场的工程人员对于这个问题一般不很重视,但是却可能存在着很大的质量隐患。
所以,本文针对内应力这个内在的质量问题展开分析,并提出控制的一些方法,希望对现场控制产品质量的工程人员有所帮助和启示。
一、内应力的种类及产生原因注塑制品的内应力主要有以下四种:1、温度应力:是制品冷却时温度不均产生的应力。
当熔体进入温度较低的模具时,靠近模腔壁的熔体迅速地冷却而固化。
由于凝固的聚合物层导热性很差,因而在制品厚度方向上产生较大的温度梯度。
先凝固的外层熔体要阻止后凝固的内层熔体的收缩,结果在外层产生压应力(收缩应力),内层产生拉应力(取向应力)。
另方面,因制品壁厚不均匀,冷却速度不一致,从而产生冷却温度不均现象。
2、取向应力:是制品内部大分子取向产生的应力。
对于线形树脂和纤维增强的塑料,在加工中最容易产生取向应力。
其结果,沿着流动方向的分子取向程度最大,在速冷条件下,如果被拉直的分子链来不及松弛,则在该方向上产生了取向应力。
3、收缩应力:注塑过程中,塑料分子本身的平衡状态受到破坏,并产生不平衡体积时的应力。
如结晶塑料的晶区与非晶区界面因收缩不均产生的内应力。
4、脱模应力:脱模时制品变形产生的应力。
这主要是模具加工精度较差和设计不合理造成,如脱模斜度不够,顶针数量不够或顶出不平衡等。
以上2至4类应力可以归纳为成型应力,是成型过程产生的应力。
一般注塑制品中同时都存在几种应力,制品的破坏,是由几种应力共同作用的结果。
二、内应力对注塑制品的影响制品中内应力的存在会严重影响到制品的力学性能和使用性能。
它的存在将降低了制品对光、热以及腐蚀介质的抵抗能力。
同时,制品在使用过程中将出现裂纹、不规则变形和翘曲,制品表面泛白、浑浊、光学性能下降等结果。
三、内应力的控制当注塑制品内的残余应力太高或应力分布不均时,塑件表面就会产生变形、泛白、裂纹及破裂等现象。
一般情况下,浇口附近最容易发生由残余应力引起的裂纹及破裂,因为浇口处的成型压力相对其他部位要高一些,尤其是主流道为直接浇口时更是如此。
当塑件的壁厚不均匀,熔料的冷却速度不一致时,由于厚薄部位的收缩量不同,也产生残余应力。
在速冷条件下,取向的分子链不能很快松驰会导致聚合物内应力的形成,等等。
由此,可以通过减少制品残余应力来防止或减小注塑制品产生以上缺陷。
减少残余应力的主要方法是改进浇注系统的结构形式和调整好塑件的成型条件。
1、减小取向应力的影响a、提高熔体温度,使剪切应力降低,分子取向度减小;另一方面会使应力松驰加快,促使解取向能力加强。
但有的材料成形温度范围窄,提高料温时可能出现分解,从而影响制品的抗衡力,会使制品开裂。
b、尽量减短保压时间,以减小取向应力。
c、减小注射压力或保压压力,会使取向应力减小。
因担心制品出现收缩凹陷或试图取得更好表面光泽而将注射压力、速度等调得过大,会造成制品内部产生大的应变。
结果,有些制品很快就开裂了,有些制品在存放一段时间后慢慢出现微裂或裂纹。
当中心浇口出现以浇口为中心的放射状开裂时,应考虑调节浇口尺寸,使型腔内的压力减少,减小取向应力。
有可能时,重新安排浇口的位置和形式,也可以增设必要的辅助浇口。
d、提高模具温度,使解取向作用加强。
虽然高的模温可减少聚合物的分子取向,但是,却使结晶性塑料结晶度提高,或因模温过高使塑料难以固化而造成脱模困难,所以要注意。
相反,如果模温太低,塑料过早冷却,熔接缝有可能产生,制品容易开裂。
e、有可能的话增加制品壁厚,使取向应力降低。
2、减小温度应力的影响如果在浇口封闭前维持模腔压力,有利于提高制品密度,消除冷却温度应力,但是在浇口附近会产生较大的应力集中。
设法降低浇口处温度,延长缓冷时间,有利于改善制品的应力不均,使制品的机械性能均一。
熔体温度的提高,不论对结晶型聚合物还是非结晶型聚合物都会导致拉伸强度的降低。
对非结晶型聚合物,拉伸强度会因浇口的位置而异。
当浇口与充模方向一致时,拉伸强度随熔体温度提高而降低;当浇口与充模方向垂直时,拉伸强度随熔体温度的提高而增加。
3、减小收缩应力的影响塑料制品如果在模内散热不好,冷热不均(尤其对大制品而言),可能会使制品出现收缩差异,产生较大的内应力,而使制品开裂。
因此,模具的冷却水道的布置应尽量平衡。
制品设计上,避免厚度相差很大的部位。
因厚度相差很大的部位必然是冷却速度不一,冷却过程的收缩和结晶情形的不同,力学状态也不同。
4、减小脱模应力的影响a、调整顶出装置,如顶板、顶杆等,使之平衡动作,避免作用力先后不一或倾斜歪曲顶出。
b、型腔、型芯要有适当的脱模斜度。
当斜度不够时,脱模困难,制品受的机械应力过大而开裂。
c、型腔脱模面要有足够的光洁度,甚至连抛光方向也应尽量与料流方向一致。
型芯部分的加强筋、柱子等应有足够的光洁度,使脱模顺畅。
d、采用小浇口,保压时间短,内应力小;用大流道,则注射压力低,注射时间短,内应力小;浇口设计在制品的厚壁处,则注射压力和保压压力低,内应力小。
e、调节好开模速度,避免高速拨模。
f、调节好模板的平行度及平稳性。
g、在模面上施加适当的脱模剂,使脱模顺畅。
h、制品在模内冷却时间太短,未充分硬化即开模顶出,可能在顶杆周围开裂。
但冷却时间过长,制品包贴在模芯上,顶出时由于脱模光洁度不够或斜度不够而发生顶白现象。
i、深腔制品应设置适当的进气孔道,以免脱模时产生过大的负压,影响塑料制品与模具的分离。
必要时,通过进气孔道向模具和制品之间吹入压缩空气有助于脱模。
5、制品设计上应注意问题:避免出现应力开裂的尖角、缺口或厚度相差很大的部位。
尖角和缺口是内应力集中的地方,而厚度相差很大的部位必然是冷却速度不一,冷却过程的收缩和结晶也不同。
总之,制品形状越复杂,尺寸愈大,愈容易开裂。
当塑料制品中带有金属嵌件时,嵌件最好是铜或铝,而且加工前应先预热嵌件。
由于金属和塑料的收缩率不一致,塑料的收缩率较大,而金属的收缩率相对较小,通过预热方法减小收缩差异。
对于聚苯乙烯,一般不宜设置金属嵌件。
制品设计上应注意平滑、缓过渡和匀称。
在制品造型上,应尽量采用曲面、双曲面,既美观又可减小变形。
6、材料方面的控制某些刚性大的塑料(如PC、PS塑料),本身不适合作脱模有困难的制品,而且容易出现应力开裂,所以应注意。
一般非结晶型树脂比结晶型树脂容易产生残余应力而引起裂纹,也应注意。
塑料再生次数太多或再生料含量太高,或料在料筒内加热时间太长,都会促使制品脆裂。
塑料分子量每成形一次,当降到某一数值下,其耐冲击强度急剧降低而变脆。
有些塑料在受潮状况下加热,会与水汽发生催化裂化反应,形成的降解产物和气态物质,除了影响制品外观外,还使制品发生大的应变,较小的残余应力就可以使出模后的制品产生开裂。
有些塑料本身质量不佳,例如分子量分布大,塑料受到污染,也是造成开裂的原因。
7、设备方面要注意的问题a、注塑机塑化容量要适中。
即使是相熔性良好的塑料,如果在机筒内未完全均匀混合,也即塑化不充分,成型的制品在受力时将使应变集中在未充分混合的部位而脆裂。
相反,若注塑机塑化容量太大,塑料在料筒中受剪切作用时间过长,也会老化降解,使制品变脆。
b、注塑机料筒内有障碍物,促使塑料降解而使制品变脆。
四、制品应力开裂检查和退火处理1、诊断方法:(1)、溶剂法:a. PS 在室温下用煤油处理。
b. 对PC、PS、聚砜、PPO等注塑制品,用四氯化硅溶剂处理,20秒内若制品开裂,说明内应力大。
c. POM 30%盐酸溶液中浸30min。
d. ABS 浸入冰醋酸溶液中。
e. PP 在80℃下,用63%(重量百分比)的三氧化铬与水的混合物处理。
f. HDPE 在80℃下,用2%的洗涤剂水溶液处理。
PC制品:1.四氯化碳60%+40%工业酒精配比放入容器中2.将成型产品放入容器中泡三分中3.取出产品放入清水中清洗4.清洗完毕后观察产品周围有无开裂缝隙(2)、仪器法:用偏振光方法可以检测制品的内应力。
2、热处理方法:有开裂倾向的塑料制品,可以用退火热处理方法来消除制品内应力,从而减小裂纹的生成。
POM 空气浴退火:140~150℃×壁厚每增5mm即增加40~60min;油浴退火:140~150℃×壁厚每增5mm即增加20~30min。
PBT 120℃×1~2h 。
PC 110~135℃×时间根据厚度定。
聚砜170~180℃×2~4h 。
PMMA 70~80℃×4h 。
ABS 70~80℃×2~4h 。
PS 介质为热空气或热水:60~70℃×30~60min(厚度≤6mm);70~80℃×120~300min(厚度≤6mm)。