声表面波器件工艺原理-9倒装焊工艺原理
超声波焊机工作原理
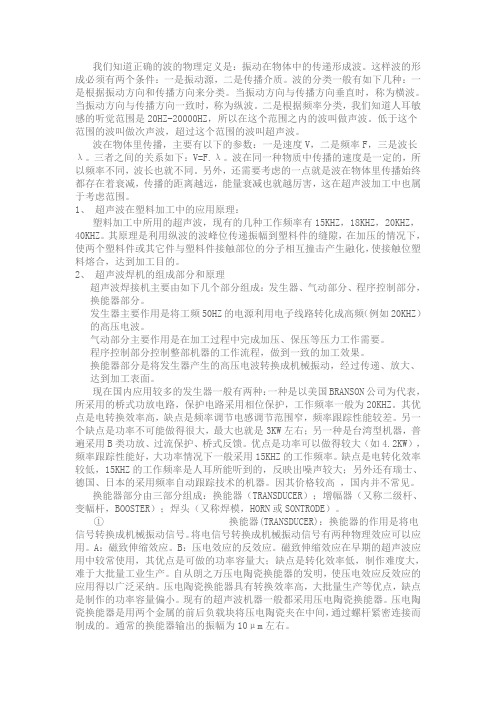
我们知道正确的波的物理定义是:振动在物体中的传递形成波。
这样波的形成必须有两个条件:一是振动源,二是传播介质。
波的分类一般有如下几种:一是根据振动方向和传播方向来分类。
当振动方向与传播方向垂直时,称为横波。
当振动方向与传播方向一致时,称为纵波。
二是根据频率分类,我们知道人耳敏感的听觉范围是20HZ-20000HZ,所以在这个范围之内的波叫做声波。
低于这个范围的波叫做次声波,超过这个范围的波叫超声波。
波在物体里传播,主要有以下的参数:一是速度V,二是频率F,三是波长λ。
三者之间的关系如下:V=F.λ。
波在同一种物质中传播的速度是一定的,所以频率不同,波长也就不同。
另外,还需要考虑的一点就是波在物体里传播始终都存在着衰减,传播的距离越远,能量衰减也就越厉害,这在超声波加工中也属于考虑范围。
1、超声波在塑料加工中的应用原理:塑料加工中所用的超声波,现有的几种工作频率有15KHZ,18KHZ,20KHZ,40KHZ。
其原理是利用纵波的波峰位传递振幅到塑料件的缝隙,在加压的情况下,使两个塑料件或其它件与塑料件接触部位的分子相互撞击产生融化,使接触位塑料熔合,达到加工目的。
2、超声波焊机的组成部分和原理超声波焊接机主要由如下几个部分组成:发生器、气动部分、程序控制部分,换能器部分。
发生器主要作用是将工频50HZ的电源利用电子线路转化成高频(例如20KHZ)的高压电波。
气动部分主要作用是在加工过程中完成加压、保压等压力工作需要。
程序控制部分控制整部机器的工作流程,做到一致的加工效果。
换能器部分是将发生器产生的高压电波转换成机械振动,经过传递、放大、达到加工表面。
现在国内应用较多的发生器一般有两种:一种是以美国BRANSON公司为代表,所采用的桥式功放电路,保护电路采用相位保护,工作频率一般为20KHZ。
其优点是电转换效率高,缺点是频率调节电感调节范围窄,频率跟踪性能较差。
另一个缺点是功率不可能做得很大,最大也就是3KW左右;另一种是台湾型机器,普遍采用B类功放、过流保护、桥式反馈。
超声波焊接机的工作原理

超声波焊接机的工作原理超声波焊接机是一种常用于塑料焊接的设备,它利用超声波振动产生的热能来实现材料的熔接。
下面将详细介绍超声波焊接机的工作原理。
1. 超声波发生器:超声波焊接机的核心部件是超声波发生器。
超声波发生器通过电能转换为机械振动,产生频率在20kHz至70kHz之间的超声波。
2. 换能器:超声波发生器将电能转换为机械振动后,通过换能器将机械振动转换为超声波振动。
换能器由压电陶瓷材料制成,当施加电压时,压电陶瓷会发生机械振动。
3. 振动焊头:超声波振动通过焊头传递到工件上。
焊头通常由钛合金制成,具有良好的导热性能和机械强度。
焊头的形状和尺寸根据焊接材料和焊接要求进行设计。
4. 工件准备:要进行超声波焊接,首先需要将要焊接的工件准备好。
通常需要清洁工件表面,确保无油污和杂质。
接下来,将工件放置在焊接夹具中,以确保工件的位置和稳定性。
5. 焊接过程:当超声波振动通过焊头传递到工件时,工件表面的分子开始振动,并因摩擦产生热能。
这种热能使工件表面温度升高,直到材料熔化。
然后,焊头施加一定的压力,将熔化的材料压合在一起。
随着焊接时间的增加,熔化的材料逐渐冷却固化,形成焊接接头。
6. 控制系统:超声波焊接机配备了先进的控制系统,可以实现焊接过程的自动化和精确控制。
控制系统可以调节焊接参数,如振幅、焊接时间和压力,以适应不同材料和焊接要求。
超声波焊接机的工作原理基于超声波振动产生的热能,通过将材料熔化并压合在一起来实现焊接。
它具有焊接速度快、焊接强度高、无需使用焊接材料和填充剂等优点,广泛应用于汽车制造、电子产品制造、医疗器械等领域。
第四讲微系统封装技术-倒装焊技术
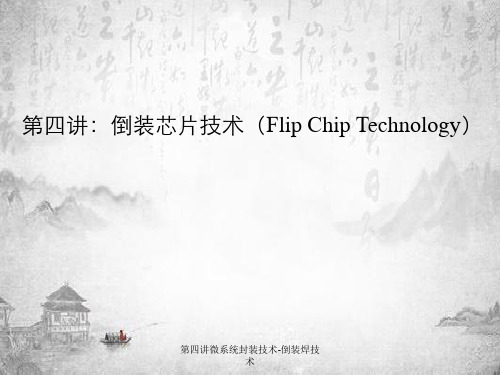
第四讲微系统封装技术-倒装焊技 术
电镀凸点横截面示意图
第四讲微系统封装技术-倒装焊技 术
电
镀
凸
点
步
骤
示
意
图
第四讲微系统封装技术-倒装焊技 术
步骤
1、硅片清洗(方法和目的与蒸镀中清洗相同) 2、UBM沉积( TiW-Cu-Au ,溅射到整个硅片上。理论上讲, UBM 层提供了一个平均电流 分布以利于一致的电镀。图(a)是硅片覆盖了TiW的情形,为了形成微球或者图钉帽结构,施 加掩模(b),沉积一定高度的Cu和Au(c)凸点总体高度为85μm to 100 μm。 3、焊料的电镀: 再次施加掩模,以电镀凸点(d)。当凸点形成之后,掩模被剥离(e)。 暴露在外的UBM刻蚀掉。 4、回流成球见图(f) 。
3%的圆片用于倒装芯片凸点。几年后可望超过20%。
第四讲微系统封装技术-倒装焊技 术
第四讲微系统封装技术-倒装焊技 术
C4:Controlled Collapse Chip Connection 可控塌陷芯片连接
优点: 1.工艺简单,倒装焊时易于熔化回流 2.熔化的焊料可以弥补凸点的高度不一致或基板不平而引起的高度差 3.对凸点金属所加的焊接压力小,从而不易损坏芯片和焊点 4.熔化时有较大的表面张力,具有“自对准”效果。
– Lift off photoresist – Reflow into spheres
• Characteristics
– Variation of previous method – Higher pitch
第四讲微系统封装技术-倒装焊技 术
蒸镀凸点步骤示意图
第四讲微系统封装技术-倒装焊技 术
超声波焊接机原理
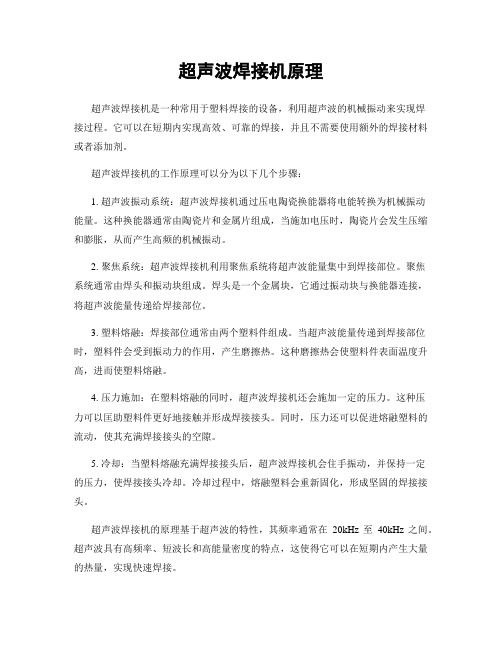
超声波焊接机原理超声波焊接机是一种常用于塑料焊接的设备,利用超声波的机械振动来实现焊接过程。
它可以在短期内实现高效、可靠的焊接,并且不需要使用额外的焊接材料或者添加剂。
超声波焊接机的工作原理可以分为以下几个步骤:1. 超声波振动系统:超声波焊接机通过压电陶瓷换能器将电能转换为机械振动能量。
这种换能器通常由陶瓷片和金属片组成,当施加电压时,陶瓷片会发生压缩和膨胀,从而产生高频的机械振动。
2. 聚焦系统:超声波焊接机利用聚焦系统将超声波能量集中到焊接部位。
聚焦系统通常由焊头和振动块组成。
焊头是一个金属块,它通过振动块与换能器连接,将超声波能量传递给焊接部位。
3. 塑料熔融:焊接部位通常由两个塑料件组成。
当超声波能量传递到焊接部位时,塑料件会受到振动力的作用,产生磨擦热。
这种磨擦热会使塑料件表面温度升高,进而使塑料熔融。
4. 压力施加:在塑料熔融的同时,超声波焊接机还会施加一定的压力。
这种压力可以匡助塑料件更好地接触并形成焊接接头。
同时,压力还可以促进熔融塑料的流动,使其充满焊接接头的空隙。
5. 冷却:当塑料熔融充满焊接接头后,超声波焊接机会住手振动,并保持一定的压力,使焊接接头冷却。
冷却过程中,熔融塑料会重新固化,形成坚固的焊接接头。
超声波焊接机的原理基于超声波的特性,其频率通常在20kHz至40kHz之间。
超声波具有高频率、短波长和高能量密度的特点,这使得它可以在短期内产生大量的热量,实现快速焊接。
超声波焊接机广泛应用于汽车、电子、医疗器械、家电等行业,可以用于焊接塑料零件、组装电子元件、封装器件等。
它具有焊接速度快、焊接质量高、无需额外材料等优点,因此被广泛使用。
总结起来,超声波焊接机利用超声波的机械振动和磨擦热原理,通过施加压力将塑料件熔融并形成焊接接头。
它是一种高效、可靠的焊接方法,广泛应用于各个领域。
超声波焊接机的工作原理
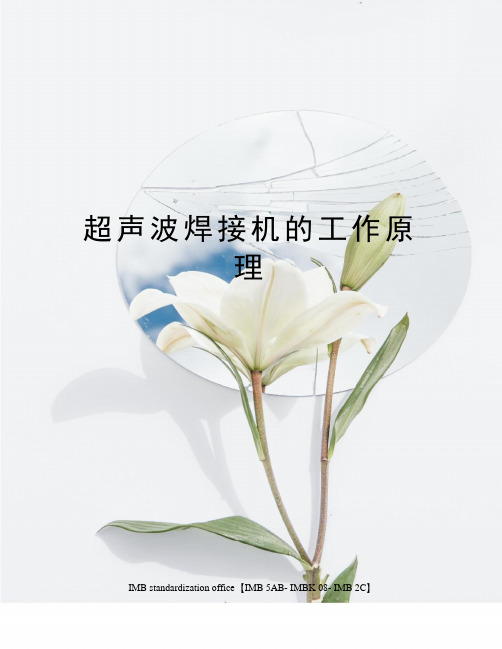
超声波焊接机的工作原理IMB standardization office【IMB 5AB- IMBK 08- IMB 2C】超声波焊接机的工作原理超音波焊接机的工作原理是:是通过振荡电路振荡出高频信号由换能器转化成机械能(即频率超出人耳听觉阈的高频机械振动能),该能量通过焊头传导到塑料工件上,以每秒上几十万次的振动加上压力使塑料工件的接合面剧烈摩擦后熔化。
振动停止后维持在工件上的短暂压力使两焊件以分子链接方式凝固为一体。
一般焊接时间小于1秒钟,所得到的焊接强度可与本体相媲美。
超声波塑料焊接机可用于热塑性塑料的对焊,也用于铆焊、点焊、嵌入、切除等加工工艺。
根据产品的外观来设计模具的大小、形状。
超声波塑料焊接机由气压传动系统、控制系统、超声波发生器、换能器及工具头和机械装置等组成。
1、气动传动系统包括有:过滹器、减压阀、油雾器、换向器、节流阀、气缸等。
工作时首先由空压机驱动冲程气缸,以带动超声换能器振动系统上下移动,动力气压在中小功率的超声波焊接中气压根据焊接需要调定。
2、控制系统控制系统由时间继电器或集成电路时间定时器组成。
主要功能是:一是控制气压传动系统工作,使其焊接时在定时控制下打开气路阀门,气缸加压使焊头下降,以一定压力压住被焊物件,当焊接完后保压一段时间,然后控制系统将气路阀门换向,使焊头回升复位;二是控制超声波发生器工作时间,本系统使整个焊接过程实现自动化,操作时只启动按钮产生一个触发脉冲,便能自动地完在本次焊接全过程。
整个控制系统的顺序是:电源启动一触发控制信号气压传动系统,气缸加压焊头下降并压住焊触发超声发生器工作,发射超声并保持一定焊接时间去除超声发射继续保持一定压力时间退压,焊头回升焊接结束。
3、超声波发生器(1)功率较大的超声波塑料焊接机,发生器信号采用锁相式频率自动跟踪电路,使发生器输出的频率基本上与换能器谐振频率一致。
(2)功率在500W以上的超声波塑料焊接机所用发生器采用自激式功率振荡器,也具有一定的频率跟踪能力。
超声波塑料焊接机工作原理

超声波塑料焊接机工作原理
===========
1. 塑料表面制备
----------
在进行超声波塑料焊接之前,首先需要对塑料表面进行制备。
这个步骤主要是为了去除塑料表面的杂质和污染物,提高表面的粗糙度,以及增强塑料表面的粘合力。
常用的方法包括机械打磨、化学处理和激光刻蚀等。
2. 表面熔合
-------
在塑料表面制备完成后,下一步就是进行表面熔合。
这个过程主要是通过超声波振动产生的热量,使塑料表面熔化,然后通过压力使两个塑料表面紧密结合。
熔合过程中需要注意控制温度和压力,以避免过度加热导致塑料变形或者过压导致塑料破裂。
3. 冷却
---
在完成表面熔合后,需要立即进行冷却。
这个步骤主要是为了将塑料从熔化状态冷却下来,使其恢复到固态,并固定在一起。
冷却通常是通过自然冷却或者强制风冷来实现的。
在冷却过程中,需要注意控制冷却速度,以避免冷却过快导致内部应力产生或者冷却过慢导致塑料变形。
以上就是超声波塑料焊接机的工作原理。
整个过程包括塑料表面制备、表面熔合和冷却三个主要步骤。
通过这个过程,我们可以将两个或者多个塑料制品牢固地连接在一起,而不会对它们的形状和结构产生影响。
这种焊接技术广泛应用于电子、汽车、医疗等领域,为我们的日常生活带来了很多便利。
超声波焊接机的工作原理

超声波焊接机的工作原理超声波焊接机的工作原理:超声波焊接机是一种利用超声波振动产生的热能来实现材料的焊接的设备。
它主要由超声波发生器、振动系统、焊接头和控制系统组成。
1. 超声波发生器:超声波发生器是超声波焊接机的核心部件,它能够将电能转化为超声波振动能。
在超声波发生器中,电能首先被转化为高频电能,然后通过压电陶瓷换能器将电能转化为机械振动能。
2. 振动系统:振动系统由压电陶瓷换能器和振动增幅器组成。
压电陶瓷换能器接收到超声波发生器产生的机械振动能后,将其转化为超声波振动能。
振动增幅器将超声波振动能进行放大,并传递到焊接头。
3. 焊接头:焊接头是超声波焊接机焊接材料的关键部件。
它通常由焊接头块和焊接头角组成。
焊接头块负责传递超声波振动能到焊接材料上,而焊接头角则用于集中能量和控制焊接过程。
4. 控制系统:控制系统是超声波焊接机的智能化部份,它能够监测和控制焊接过程中的各项参数,以确保焊接质量。
控制系统通常包括超声波发生器控制、振动系统控制、焊接头温度控制等功能。
超声波焊接机的工作原理如下:首先,超声波发生器产生高频电能,并将其转化为机械振动能。
然后,振动系统将机械振动能传递到焊接头。
焊接头将超声波振动能传递到焊接材料上,使其产生热能。
热能可以使焊接材料的表面温度升高,从而使其软化和熔化。
当焊接材料熔化后,焊接头施加一定的压力,将焊接材料连接在一起。
最后,焊接头住手振动,焊接材料冷却固化,完成焊接过程。
超声波焊接机的工作原理基于超声波的特性,超声波具有高频、高能量和高速传播等特点。
通过利用超声波的特性,超声波焊接机能够实现高效、快速、无污染的焊接过程。
它广泛应用于塑料、金属、纺织品等领域的焊接工艺中,具有焊接速度快、焊接强度高、焊接接头美观等优点。
倒装焊工艺简介

随着超导量子比特技术的进一步发展,实验上需要可以表面误码差校正以及更复杂的高保真量子电路[1-2]。
相关报道介绍了一些平面二维阵列的设计[3-5],但是这几种现行的设计方案中控制布线和读出电路往往使得量子比特数目与器件高保真度这二者与不能同时兼顾。
例如,二维阵列的X mon单量子位就需要利用电容耦合到四个最近量子比特和读出谐振腔,此外还要考虑XY驱动线的设计[6]。
多层膜加工工艺是解决这个问题的一种直观的方案[7],但是该方案中制备的量子比特基片上制备的绝缘层会造成额外的退相干,从而影响量子比特的特性[8]。
目前国际上解决上述困难的主流方法是通过将器件分离成两部分,其中一部分是密集的布线基片并在该基片上制备绝缘层,另一部分上制备量子比特而不生长大面积的绝缘层,随后将这两种基片通过倒装焊工艺结合起来形成一种同时满足多量子比特数目与高保真度的量子比特器件。
该种工艺已经在半导体工业中得到了广泛的应用,从手机到大型强子对撞机都有应用[9]。
而在低温技术中的应用还较少。
该工艺对两部分基片的连接部分提出了如下的要求:1.连接材料应是常规的量子比特制备工艺中常用的并可以与现有的量子比特制备工艺兼容。
2.谐振腔的可加工数量与质量必须达到高要求。
(在布线基片上需加工数百个高Q值的谐振腔)。
3.在极低温的条件下可以保证两部分的联通。
4.可以在不高的温度与大气压下进行两部分基片的连接,以避免退火改变约瑟夫森结临界电流[10]。
5.两部分基片的连接部分必须在测量条件下进入超导态,以保证芯片之间的无损连接与避免局部生热破坏测量条件。
6.相互连接偏置线临界电流应大于5nA,以保证可以进行实验测量。
铟的临界温度相对较高为3.4K,室温铟焊接工艺也是一种在半导体工业中较为成熟的技术[11],而在量子比特的加工工艺中高纯度的铟可以通过常用的热蒸发工艺生长在指定的位置,因此基片之间连接材料可选高纯铟。
但是,由于量子比特的基底金属常用铝,而铝和铟接触层会形成交叠层[12]影响量子比特的性能,因此热蒸发的时候必须在铝基底上生长氮化钛介质缓冲层以防止上述现象的出现,氮化钛的临界温度高达5.64K,并且是一种高相干性能的量子比特材料[13,14]。
超音波焊接机原理
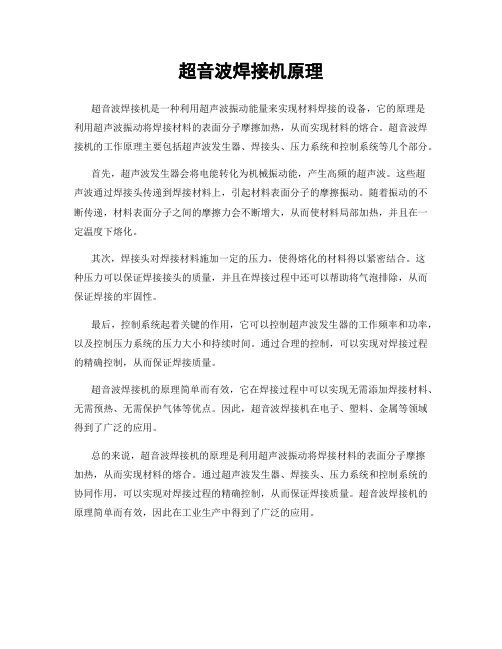
超音波焊接机原理
超音波焊接机是一种利用超声波振动能量来实现材料焊接的设备,它的原理是
利用超声波振动将焊接材料的表面分子摩擦加热,从而实现材料的熔合。
超音波焊接机的工作原理主要包括超声波发生器、焊接头、压力系统和控制系统等几个部分。
首先,超声波发生器会将电能转化为机械振动能,产生高频的超声波。
这些超
声波通过焊接头传递到焊接材料上,引起材料表面分子的摩擦振动。
随着振动的不断传递,材料表面分子之间的摩擦力会不断增大,从而使材料局部加热,并且在一定温度下熔化。
其次,焊接头对焊接材料施加一定的压力,使得熔化的材料得以紧密结合。
这
种压力可以保证焊接接头的质量,并且在焊接过程中还可以帮助将气泡排除,从而保证焊接的牢固性。
最后,控制系统起着关键的作用,它可以控制超声波发生器的工作频率和功率,以及控制压力系统的压力大小和持续时间。
通过合理的控制,可以实现对焊接过程的精确控制,从而保证焊接质量。
超音波焊接机的原理简单而有效,它在焊接过程中可以实现无需添加焊接材料、无需预热、无需保护气体等优点。
因此,超音波焊接机在电子、塑料、金属等领域得到了广泛的应用。
总的来说,超音波焊接机的原理是利用超声波振动将焊接材料的表面分子摩擦
加热,从而实现材料的熔合。
通过超声波发生器、焊接头、压力系统和控制系统的协同作用,可以实现对焊接过程的精确控制,从而保证焊接质量。
超音波焊接机的原理简单而有效,因此在工业生产中得到了广泛的应用。
超声波焊接原理

超声波焊接原理超声波焊接原理通过上焊件把超声能量传送到焊区,由于焊区即两个焊接的交界面处声阻大,因此会产生局部高温。
又由于塑料导热性差,一时还不能及时散发,聚集在焊区,致使两个塑料的接触面迅速熔化,加上一定压力后,使其融合成一体。
当超声波停止作用后,让压力持续,有些许保压时间,使其凝固成型,这样就形成一个坚固的分子链,达到焊接的目的,焊接强度能接近于原材料本体强度。
超声波焊接是如何工作的?超声波焊接原理是通过超声波发生器将50/60赫兹电流转换成15、20、30或40千赫兹电能。
被转换的高频电能通过换能器再次被转换成为同等频率的机械运动,随后机械运动通过一套可以改变振幅的调幅器装置传递到焊头。
焊头将接收到的振动能量传递到待焊接工件的接合部,在该区域,振动能量被通过摩擦方式转换成热能,将塑料熔化。
超声波不仅可以被用来焊接硬热塑性塑料,还可以加工织物和薄膜。
一套超声波焊接系统的主要组件包括超声波发生器,换能器/调幅器/焊头三联组,模具和机架线性振动摩擦是如何工作的?线性振动摩擦焊接利用在两个待焊工件接触面所产生的摩擦热能来使塑料熔化。
热能来自一定压力下,一个工件在另一个表面以一定的位移或振幅往复的移动。
一旦达到预期的焊接程度,振动就会停止,同时仍旧会有一定的压力施加于两个工件上,使刚刚焊接好的部分冷却、固化,从而形成紧密地结合。
轨道式振动摩擦是如何工作的?轨道式振动摩擦焊接是一种利用摩擦热能焊接的方法。
在进行轨道式振动摩擦焊接时,上部的工件以固定的速度进行轨道运动——向各个方向的圆周运动。
运动可以产生热能,使两个塑料件的焊接部分达到熔点。
一旦塑料开始熔化,运动就停止,两个工件的焊接部分将凝固并牢牢的连接在一起。
小的夹持力会导致工件产生最小程度的变形,直径在10英寸以内的工件可以用应用轨道式振动摩擦进行焊接。
应用范围超声波焊接机主要用于热塑性塑料的二次连接,相比其他传统工艺(如胶粘、电烫合或螺丝紧固等),具有生产效率高、焊接质量好、环保又节能等显著优点。
超声波金属焊接原理

超声波金属焊接原理超声波金属焊接是一种利用超声波振动能量来实现金属材料的焊接的技术。
它是利用超声波振动传递到工件表面,使得工件表面产生高频振动,从而产生摩擦热,将工件表面金属材料局部加热至熔点,然后在一定的压力下进行焊接,实现金属材料的连接。
超声波金属焊接技术具有焊接速度快、热影响区小、焊接接头强度高等优点,因此在航空航天、汽车制造、电子设备等领域得到了广泛应用。
超声波金属焊接的原理主要包括超声波振动传递、摩擦加热和压力焊接三个方面。
首先,超声波振动传递是通过超声波振动器将电能转换为机械能,产生高频振动,然后将振动能量传递到工件表面。
工件表面的金属材料在超声波振动作用下产生微小的振动,使得工件表面产生摩擦热。
摩擦加热是超声波金属焊接的关键步骤,它使得工件表面局部加热至熔点,形成熔池。
最后,在一定的压力下进行焊接,使得熔池充分融合,实现金属材料的连接。
超声波金属焊接技术的优点在于焊接速度快。
由于超声波振动传递的能量高效,使得工件表面局部加热速度快,从而实现了焊接速度的提高。
与传统的焊接方法相比,超声波金属焊接可以大大缩短焊接时间,提高生产效率。
另外,超声波金属焊接的热影响区小,这意味着在焊接过程中,工件周围的热影响范围较小,可以减少材料的变形和焊接接头的变质,保证焊接接头的质量。
同时,由于焊接过程中局部加热,还可以减少材料的氧化和变质,提高焊接接头的质量和强度。
总的来说,超声波金属焊接技术是一种高效、快速、高质量的焊接方法,具有广泛的应用前景。
随着科学技术的不断发展,超声波金属焊接技术将在更多领域得到应用,为工业生产带来更多的便利和效益。
希望本文的介绍能够帮助读者更加深入地了解超声波金属焊接的原理和优点,为相关领域的工作者和研究人员提供一些参考和借鉴。
热压超声倒装焊工艺研究
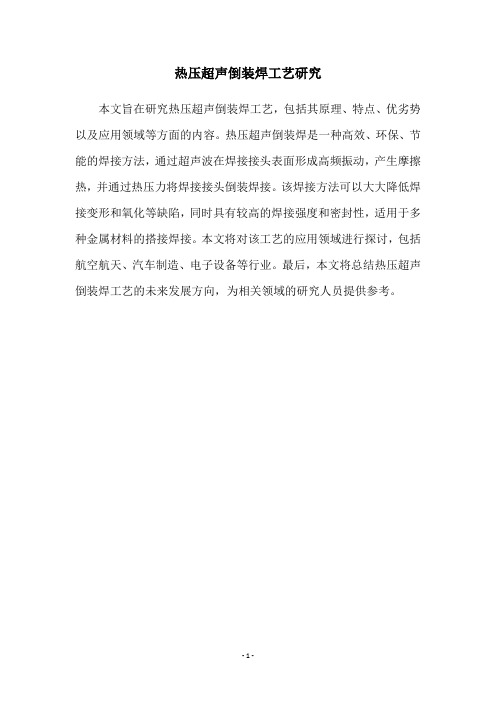
热压超声倒装焊工艺研究
本文旨在研究热压超声倒装焊工艺,包括其原理、特点、优劣势以及应用领域等方面的内容。
热压超声倒装焊是一种高效、环保、节能的焊接方法,通过超声波在焊接接头表面形成高频振动,产生摩擦热,并通过热压力将焊接接头倒装焊接。
该焊接方法可以大大降低焊接变形和氧化等缺陷,同时具有较高的焊接强度和密封性,适用于多种金属材料的搭接焊接。
本文将对该工艺的应用领域进行探讨,包括航空航天、汽车制造、电子设备等行业。
最后,本文将总结热压超声倒装焊工艺的未来发展方向,为相关领域的研究人员提供参考。
- 1 -。
- 1、下载文档前请自行甄别文档内容的完整性,平台不提供额外的编辑、内容补充、找答案等附加服务。
- 2、"仅部分预览"的文档,不可在线预览部分如存在完整性等问题,可反馈申请退款(可完整预览的文档不适用该条件!)。
- 3、如文档侵犯您的权益,请联系客服反馈,我们会尽快为您处理(人工客服工作时间:9:00-18:30)。
九,声表器件倒装焊工艺原理序:倒装芯片(FC)技术,是在芯片的焊接区金属上制作凸焊点,然后将芯片倒扣在外壳基座上,以实现机械性能和电性能的连接,由于FC是通过凸焊点直接与底座相连,因此与其它互连技术相比,FC具有最高的封装密度、最小的封装尺寸(线焊可焊的最小陶瓷外壳为3×3mm,而FC可以作到芯片级)、最好的高频性能(电感小)、最小的高度、最轻的重量,以及产品高可靠、生产高工效等。
倒装焊工艺:主要由UBM的形成、凸点的制作、倒装焊接三部分组成。
(一)UBM的形成:当凸焊点材料与芯片上的焊接区金属不能很好浸润粘附时(或接触电阻大,或热匹配差,或两种材料间易形成会导致键合强度降低的金属间化合物),需要在凸焊点与芯片压焊块之间置入一层既能与芯片焊接区金属良好粘附、又能与凸焊点良好浸润、还能有效阻挡两者之间相互反应扩散的金属膜(UBM),因我们无法找到可同时满足上述要求的材料,所以通常UBM由多层金属膜组成。
(说明:与凸点连接的还有底座上相应的焊接点,由于在底座制作时该部位已镀有多层金属,能满足要求,固在此不于讨论。
)1,对UBM的各层要求及材料选择:1)粘附层:要求与铝膜及钝化层间的粘附性好,低阻接触,热膨涨系数接近,热应力小。
常选用材料有:Cr、Ti、Ti-W、Al、V等,因它们与Al浸润性很好,固该层可较薄。
2)扩散阻挡层:能有效阻挡凸焊点材料与铝间的相互扩散,以免形成不利的金属间化合物,特别是金凸焊点,在高温下与铝可生成Al2Au、AlAu、AlAu2、Al2Au5等脆性金属间化合物及在接触处相互扩散形成空洞,导致键合强度降低甚至失效。
该层常用材料有:Ti、Ni、Cu、Pd、Pt、Ti-W等。
(当用软焊料如PbSn作凸点时,由于其回流时会吃掉浸润层,直接与阻挡层接触;此时阻挡层应足够厚,且与凸点相浸润,不反应产生有害物)3)浸润层:要求一方面能和凸焊点材料良好浸润,可焊性好,且不会形成不利于键合的金属间化合物;另一方面还能保护粘附层和阻挡层金属不被氧化、粘污。
该层常选用薄的金膜、金的合金膜或较厚的铜膜(用于焊料凸焊点)。
2,UBM的制作:1)UBM的组合选择:对于金凸焊点,常选用的UBM为:Cr/Ni/Au、Ti/Ni/Au、Ti/Pt/Au、Ti-W/Au等;对于PbSn凸焊点,常选用的UBM有:Ti-W/Cu、Ti-W/Au/Cu、Cr/Cr-Cu/Cu、Al/Ni-V/Cu、Ti/Cu、Ti-W/Cu/化学镀Ni等。
2)UBM的制作方法:UBM的制作是凸焊点制作的关键工艺,其质量好坏直接影响凸焊点质量、倒装焊接的成功率和封装后凸焊点的可靠性。
由于UBM是多层金属,为防止薄膜间形成氧化膜夹层,对UBM的制作基本上都是采用溅射或电子束蒸发,在高真空腔内一次完成(当需要制作厚金属膜时,则采用电镀或化学镀)。
为防止多层金属腐蚀时造成凸点脱落,可采用剥离技术(电镀法制凸点除外),既可解决腐蚀不易控制,又可简化工艺,提高芯片凸点可靠性;这对换能器裸露于芯片表面的声表器件尤其适宜。
(二)凸焊点制作:1,凸焊点常用材料:要具有电阻率小、延展性好、化学性能稳定等特点,同时凸点(包括UBM)材料还要能承受器件在加工、使用、老化、可靠性实验等过程中所需承受的条件。
1)Au:由于金浸润性好,延展性好,内应力小,接触电阻小,化学性能稳定,因此是高频、高可靠器件常用的凸点材料。
现在已可作节距为20μ,直径为20μ,高为15μ的金凸点。
对小尺寸、高密度的金凸点的制作主要是用厚金电镀技术,低密度的金凸点可用金丝球焊切尾制作。
目前国内无氰电镀金凸点剪切强度已达11.8 mg/µm2,高度容差±1.4µm(优于美国公司标准:剪切强度>8.7mg/µm2,高度容差:管芯内±1.5µm,圆片内±2.5µm)。
有资料介绍,在有金参与的金属化系统中,Ti、Ni、Cr、Al不能与金直接接触,因为前三种金属与金接触时,在350-450℃烘焙数分钟其电阻就大大增加,而Al与Au在200℃以上易生成不利于键合的金属间化合物。
可作Ti、Ni、Cr与Au阻挡层的材料有Pd、Pt、Mo、W、Cu,通常用Mo或W。
提醒选材时予以注意。
2)Pb-Sn合金:属软焊料。
由于现阶段开发的无铅焊料仍存在浸润性差、熔点高、成本高、一些技术参数还难以实现等问题,因此Pb/Sn目前仍作为凸点材料使用。
铅锡焊球成分种类较多,主要分为用于陶瓷基板的高温高铅焊料如95Pb5Sn、97Pb3Sn(熔点为314-320℃),和用于有机基板的低温焊料如37Pb63Sn,熔点为183℃,其凸点剪切力> 3.1mg/µm2。
由于铅锡焊球体形较大(直径85-200μ),常采用电镀、模板印刷等法制作。
铅锡合金的缺点是:有容易形成晶须和热疲劳等可靠性问题(为提高焊料的抗热疲劳性,常在PbSn中加入少量的Ag或In);另外,PbSn在熔化状态易与金膜融解形成合金,会使结合质量产生隐患。
(有资料介绍,Au在PbSn中含量超过4%、Al在PbSn中含量超过0.001%,即会生成脆性金属间化合物)3)其它:* In:铟是低熔点(156℃)软焊料,应力小,有良好的塑性形变和浸润性。
采用蒸发- 剥离工艺制作的铟凸点均匀性好,工艺简单,UBM和凸点的制作可在镀膜机内一气哈成(在铟、铝之间仅须蒸发一层几千埃的钛即可)。
缺点是In易氧化,剪切力较低,有容易形成晶须和热疲劳等可靠性问题,及In价格昂贵等。
* Au/Sn合金:属硬焊料,无须助焊剂,有优良的物理和化学性能;具有浸润好,导热、导电性好,强度高等优点。
Au-Sn凸点常采用电镀-回流工艺制作(回流处理气氛:N2/H2(95/5),温度:300-325℃),Au-Sn(80/20)共熔合金的金相结构是在回流过程或焊接过程中锡、金反应形成,其凸点剪切力是铟凸点和铅锡凸点的两倍。
* 可作为凸点材料的还有:Al、SnAgCu、SnAg、SnCu、SnZn、SnCuNi等,我们须根据对器件性能的要求、对工艺的要求、以及对成本、效率的要求等,综合考虑选择。
* 说明:由于以上资料选自不同文章,难免有相互矛盾之处,如:“Ti、Ni、Cr、Al不能与金直接接触”与“对于金凸焊点,常选用的UBM为:Cr/Ni/Au、Ti/Ni/Au”即相矛盾。
因此在对一些材料选用时,要注意重实验、重实践。
2,凸焊点的制作方法:常用方法有:电镀、化学镀、蒸发、模板(丝网)印制、植球等。
1)电镀法:是最常用的方法,占市场份额80%。
优点是可以作到小的节距(25µ),且一致性好,质量稳定;缺点是费时费工。
目前还不是所有的焊料都可电镀。
下面结合声表器件工艺进行讨论:a)电镀法制金凸点:由于声表器件换能器裸露于芯片表面,不便于像IC那样用钝化层保护,在此采用光刻胶保护、隔离。
* 涂光刻胶0.5μm左右,光刻UBM窗口。
* 用溅射或电子束镀膜先后镀Ti、W各1500A°(镀前用等离子体打胶底膜)。
* 涂厚光刻胶(SU-8光刻胶,厚20-30µ,胶要高于所需凸点的高度,侧壁要陡直,侧壁角>85°);光刻出电镀窗口。
* 电镀厚金12-20µ(镀前要用等离子体打底膜)。
* 去厚胶, 剥离出金凸点。
依次腐蚀清除W、Ti金属膜层;去光刻胶。
(W腐蚀液:NaNO2:NaOH:H2O = 25g:4g:100ml,Ti腐蚀液:40%NH4F水溶液:48%HF=6:1)* 在400-450℃下退火15′,以降低其硬度。
b)电镀法制作SnPb凸点:工艺基本与上同。
* 采用光刻-真空镀膜制作UBM:Ti(200nm)/Cu(250nm)。
* 厚胶光刻。
按设计要求和SnPb合金比例,依次电镀一定厚度的Cu、Pb、Sn。
* 去厚胶,腐蚀清除凸点外UBM,对凸点进行高温回流处理。
c)讨论:电镀法制凸点应用于高频声表器件存在的问题:* 腐蚀清除UBM膜层时的问题:光刻胶的抗蚀能力;侧向钻蚀及酸碱对凸点的腐蚀。
* 回流时,来自焊料的焊滴很易扩散并粘附在芯片表面,引起短路或使特性变差。
* 退火(回流)时的高温对芯片的影响:压电晶片有很强的热电性,当被加热到250℃ 左右,表面会产生很高电压,不仅易造成裂片,还会在梳状电极间引起放电,击穿电极。
(具体温度多高会造成击穿,要根据工艺水平及指条间距而定)由此认为,电镀法制凸点不适宜高频声表器件。
(对熔点为183℃的37Pb63Sn,另议)2)化学镀法:化学镀不需外加直流电源设备,可在金属、非金属、半导体等各种不同基材上镀覆。
化学镀只局限在具有催化作用的工作表面上进行反应,如果被镀金属(如镍)本身是催化剂,那么这种化学镀的过程就具有自催化作用,使氧化还原反应能不断进行,而获得一定厚度的镀层;而对不具有催化表面的工件(如塑料等非金属),则需通过特殊予处理,使其表面活化,具有催化作用,才能进行化学镀。
目前用化学镀所得镀层有:Cu、Ni、Co、Au、Pb、Sn、Pd、Ag等和它们的合金。
化学镀因其镀液不稳定,镀层均匀性较差,有时不能满足凸焊点高度容差的要求。
化学镀制凸点工艺如下:a)光刻-蒸发-剥离制作UBM—厚胶光刻—化学镀凸点材料。
b)直接厚胶光刻,然后按厚度要求,依次化学镀Ni、Cu、Au、厚Au(做金凸点);依次化学镀Ni、Cu,然后按合金比例化学镀厚SnPb(做SnPb凸点)。
采用化学镀制凸点有时不需UBM,这是因为活化处理常使被镀基体表面具有UBM的性能。
在该工艺中镀液的组成和对被镀件表活化处理则是其技术要点。
由于化学镀制凸点需高温退火或回流,因此它不适用于高频声表面波器件。
3)蒸发法:用蒸发法制凸点可采用剥离技术,具有制做的凸点面积小,均匀性好,工艺简单(UBM和凸点的制作可在镀膜机内一气哈成)等优点;缺点是生产效率低。
另外当凸点材料昂贵、或对蒸发合金组分要求严格又不易控制时,可酌情选用。
a)一般工艺过程:(以SnPb凸点为例)* 厚胶光刻:负胶胶厚要高于所需凸点高度;光刻出蒸镀窗口,侧壁要陡直,侧壁角>85°。
* 蒸镀UBM和凸点材料:采用多源电子束镀膜机,蒸发前要用等离子体打底膜;然后依次按要求蒸镀UBM(如Ti/Cu)和凸点材料Pb、Sn(镀膜厚度按合金比例计算),蒸发入射角根据对凸点高度容差要求确定。
* 剥离形成凸点。
在N2/H2保护下进行回流处理。
利用其熔融时的张力形成半球状凸点。
b)采用蒸发法制铝凸点:即在厚胶光刻后直接蒸镀厚铝(不需UBM),然后剥离形成凸点,并在N2/H2保护下进行退火处理(350-400℃)。
需要注意的是,厚胶光刻后不仅要去底膜,还要去氧化铝膜,以确保两层铝间低欧姆接触;具体方法是蒸发前用氩离子轰击或在装片前用1:20稀HF溶液漂洗15″—20″。