真空热蒸镀法制备介质膜
真空蒸镀非金属薄膜工艺
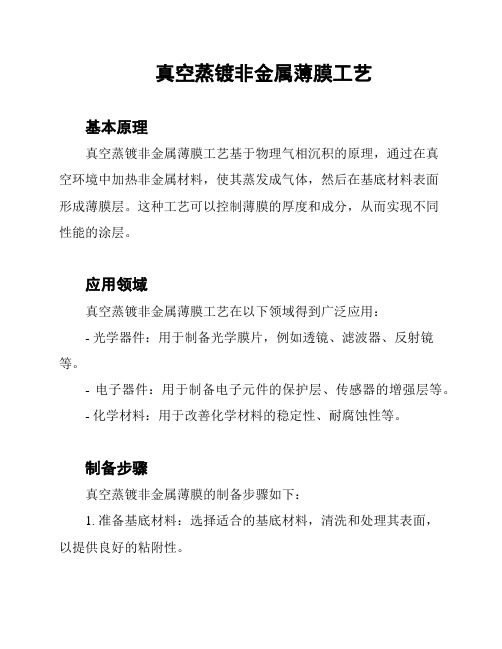
真空蒸镀非金属薄膜工艺
基本原理
真空蒸镀非金属薄膜工艺基于物理气相沉积的原理,通过在真
空环境中加热非金属材料,使其蒸发成气体,然后在基底材料表面
形成薄膜层。
这种工艺可以控制薄膜的厚度和成分,从而实现不同
性能的涂层。
应用领域
真空蒸镀非金属薄膜工艺在以下领域得到广泛应用:
- 光学器件:用于制备光学膜片,例如透镜、滤波器、反射镜等。
- 电子器件:用于制备电子元件的保护层、传感器的增强层等。
- 化学材料:用于改善化学材料的稳定性、耐腐蚀性等。
制备步骤
真空蒸镀非金属薄膜的制备步骤如下:
1. 准备基底材料:选择适合的基底材料,清洗和处理其表面,
以提供良好的粘附性。
2. 准备蒸发源:选择适合的非金属材料作为蒸发源,将其加热至蒸发温度。
3. 建立真空环境:将制备系统放入真空腔室中,泵出大部分空气,以建立高真空环境。
4. 沉积薄膜:通过控制蒸发源的温度和时间,将蒸发的非金属材料沉积在基底材料表面,形成薄膜层。
5. 测量和分析:对所制备的薄膜进行性能测试和分析,以确保其满足要求。
总结
真空蒸镀非金属薄膜工艺是一种重要的表面涂层技术,具有广泛的应用领域。
通过了解其基本原理和制备步骤,我们可以更好地理解和应用该工艺。
在实际应用中,我们需要根据具体需求选择合适的非金属材料和工艺参数,以实现所需的涂层效果。
薄膜制备方法
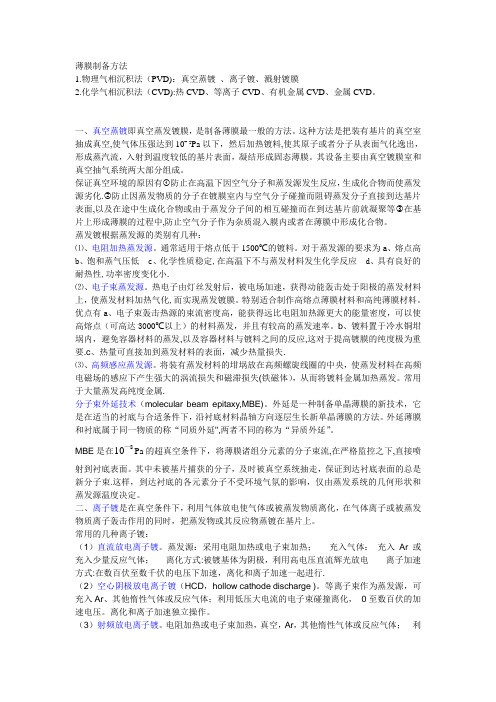
薄膜制备方法1.物理气相沉积法(PVD):真空蒸镀、离子镀、溅射镀膜2.化学气相沉积法(CVD):热CVD、等离子CVD、有机金属CVD、金属CVD。
一、真空蒸镀即真空蒸发镀膜,是制备薄膜最一般的方法。
这种方法是把装有基片的真空室抽成真空,使气体压强达到10¯²Pa以下,然后加热镀料,使其原子或者分子从表面气化逸出,形成蒸汽流,入射到温度较低的基片表面,凝结形成固态薄膜。
其设备主要由真空镀膜室和真空抽气系统两大部分组成。
保证真空环境的原因有①防止在高温下因空气分子和蒸发源发生反应,生成化合物而使蒸发源劣化.②防止因蒸发物质的分子在镀膜室内与空气分子碰撞而阻碍蒸发分子直接到达基片表面,以及在途中生成化合物或由于蒸发分子间的相互碰撞而在到达基片前就凝聚等③在基片上形成薄膜的过程中,防止空气分子作为杂质混入膜内或者在薄膜中形成化合物。
蒸发镀根据蒸发源的类别有几种:⑴、电阻加热蒸发源。
通常适用于熔点低于1500℃的镀料。
对于蒸发源的要求为a、熔点高b、饱和蒸气压低c、化学性质稳定,在高温下不与蒸发材料发生化学反应d、具有良好的耐热性,功率密度变化小.⑵、电子束蒸发源。
热电子由灯丝发射后,被电场加速,获得动能轰击处于阳极的蒸发材料上,使蒸发材料加热气化,而实现蒸发镀膜。
特别适合制作高熔点薄膜材料和高纯薄膜材料。
优点有a、电子束轰击热源的束流密度高,能获得远比电阻加热源更大的能量密度,可以使高熔点(可高达3000℃以上)的材料蒸发,并且有较高的蒸发速率。
b、镀料置于冷水铜坩埚内,避免容器材料的蒸发,以及容器材料与镀料之间的反应,这对于提高镀膜的纯度极为重要.c、热量可直接加到蒸发材料的表面,减少热量损失.⑶、高频感应蒸发源。
将装有蒸发材料的坩埚放在高频螺旋线圈的中央,使蒸发材料在高频电磁场的感应下产生强大的涡流损失和磁滞损失(铁磁体),从而将镀料金属加热蒸发。
常用于大量蒸发高纯度金属.分子束外延技术(molecular beam epitaxy,MBE)。
3.真空蒸镀、溅射制膜的原理

真空蒸镀和溅射制膜是现代材料制备领域中常用的薄膜沉积工艺。
它们通过将材料加热至高温并在真空环境下进行薄膜沉积,可以制备出具有特定性能和特征的薄膜材料。
本文将对真空蒸镀和溅射制膜的原理进行详细介绍。
1. 真空蒸镀的原理真空蒸镀是一种将固态材料加热至其蒸发温度并在真空环境中进行沉积的工艺。
其原理如下:1) 加热源:真空蒸镀加热源通常为电阻加热或电子束加热。
当材料加热至其蒸发温度时,固态材料会逐渐转变为气态,形成蒸气。
2) 蒸镀材料:蒸镀材料通常以固态块状形式置于加热源附近,通过加热源使其升温并蒸发。
蒸镀材料的选择对于薄膜的成分和性能具有重要影响。
3) 沉积物质传输:蒸气在真空腔体中扩散并沉积到基底表面上,形成所需的薄膜。
沉积过程受到气体分子的影响,需要在高真空环境下进行以确保薄膜的纯净性和均匀性。
4) 控制薄膜厚度:通过控制蒸镀时间和材料的蒸发速率,可以实现对薄膜厚度的精确控制。
旋转或倾斜基底也可影响薄膜的均匀性和结构。
2. 溅射制膜的原理溅射制膜是一种利用离子轰击固体材料表面,将其溅射成粒子并沉积在基底表面上的工艺。
其原理如下:1) 离子轰击:在真空环境中,通过加速器使惰性气体(如氩气)成为离子,并将其加速至高能量。
这些离子以高速撞击固体材料表面,将固体材料溅射成细小粒子。
2) 溅射材料:溅射材料通常为固态块状形式,其固体材料会被离子轰击成粒子,并在基底表面上形成薄膜。
3) 质量选择:通过选择离子轰击的惰性气体、溅射材料的种类和形状,可以实现对薄膜成分和结构的调控。
不同的溅射条件可以实现对薄膜的特定性能要求。
4) 控制薄膜厚度:通过控制溅射时间和离子轰击能量,可以实现对薄膜厚度的精确控制。
旋转或倾斜基底也可影响薄膜的均匀性和结构。
3. 比较与应用真空蒸镀和溅射制膜是两种常用的薄膜沉积工艺,在各自领域具有独特的优势和应用。
真空蒸镀工艺适用于加热蒸发易挥发材料的制备,例如金属薄膜和氧化物薄膜的制备。
溅射制膜工艺适用于制备高纯度金属薄膜、合金薄膜和复合薄膜等。
薄膜制备方法
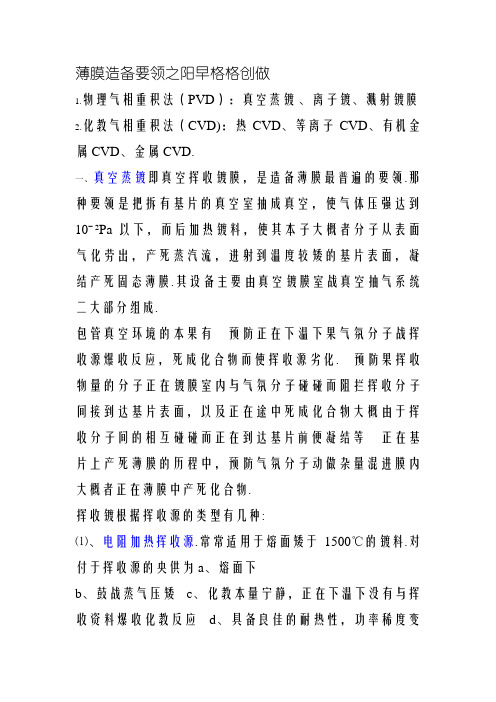
薄膜造备要领之阳早格格创做1.物理气相重积法(PVD):真空蒸镀、离子镀、溅射镀膜2.化教气相重积法(CVD):热CVD、等离子CVD、有机金属CVD、金属CVD.一、真空蒸镀即真空挥收镀膜,是造备薄膜最普遍的要领.那种要领是把拆有基片的真空室抽成真空,使气体压强达到10¯²Pa以下,而后加热镀料,使其本子大概者分子从表面气化劳出,产死蒸汽流,进射到温度较矮的基片表面,凝结产死固态薄膜.其设备主要由真空镀膜室战真空抽气系统二大部分组成.包管真空环境的本果有预防正在下温下果气氛分子战挥收源爆收反应,死成化合物而使挥收源劣化.预防果挥收物量的分子正在镀膜室内与气氛分子碰碰而阻拦挥收分子间接到达基片表面,以及正在途中死成化合物大概由于挥收分子间的相互碰碰而正在到达基片前便凝结等正在基片上产死薄膜的历程中,预防气氛分子动做杂量混进膜内大概者正在薄膜中产死化合物.挥收镀根据挥收源的类型有几种:⑴、电阻加热挥收源.常常适用于熔面矮于1500℃的镀料.对付于挥收源的央供为a、熔面下b、鼓战蒸气压矮c、化教本量宁静,正在下温下没有与挥收资料爆收化教反应d、具备良佳的耐热性,功率稀度变更小.⑵、电子束挥收源.热电子由灯丝收射后,被电场加速,赢得动能轰打处于阳极的挥收资料上,使挥收资料加热气化,而真止挥收镀膜.特天符合创造下熔面薄膜资料战下杂薄膜资料.便宜有a、电子束轰打热源的束流稀度下,能赢得近比电阻加热源更大的能量稀度,不妨使下熔面(可下达3000℃以上)的资料挥收,而且有较下的挥收速率.b、镀料置于热火铜坩埚内,预防容器资料的挥收,以及容器资料与镀料之间的反应,那对付于普及镀膜的杂度极为要害.c、热量可间接加到挥收资料的表面,缩小热量益坏.⑶、下频感触挥收源.将拆有挥收资料的坩埚搁正在下频螺旋线圈的中央,使挥收资料正在下频电磁场的感触下爆收强盛的涡流益坏战磁滞益坏(铁磁体),从而将镀料金属加热挥收.时常使用于洪量挥收下杂度金属.分子束中延技能(molecular beam epitaxy,MBE).中延是一种造备单晶薄膜的新技能,它是正在符合的衬底与符合条件下,沿衬底资料晶轴目标逐层死少新单晶薄膜的要领.中延薄膜战衬底属于共一物量的称“共量中延”,二者分歧的称为“同量中延”.MBE是正在810—Pa的超真空条件下,将薄膜诸组分元素的分子束流,正在庄重监控之下,间接喷射到衬底表面.其中已被基片捕获的分子,即时被真空系统抽走,包管到达衬底表面的经常新分子束.那样,到达衬底的各元素分子没有受环境气氛的效率,仅由挥收系统的几许形状战挥收源温度决断.二、离子镀是正在真空条件下,利用气体搁电使气体大概被挥收物量离化,正在气体离子大概被挥收物量离子轰打效率的共时,把挥收物大概其反应物蒸镀正在基片上.时常使用的几种离子镀:(1)曲流搁电离子镀.挥收源:采与电阻加热大概电子束加热;充进气体:充进Ar大概充进少量反应气体;离化办法:被镀基体为阳极,利用下电压曲流辉光搁电离子加速办法:正在数百伏至数千伏的电压下加速,离化战离子加速所有举止.(2)空心阳极搁电离子镀(HCD,hollow cathode discharge ).等离子束动做挥收源,可充进Ar、其余惰性气体大概反应气体;利用矮压大电流的电子束碰碰离化, 0至数百伏的加速电压.离化战离子加速独力支配.(3)射频搁电离子镀.电阻加热大概电子束加热,真空,Ar,其余惰性气体大概反应气体;利用射频等离子体搁电离化, 0至数千伏的加速电压,离化战离子加速独力支配.(4)矮压等离子体离子镀.电子束加热,惰性气体,反应气体. 等离子体离化, DC大概AC 50V离子镀是一个格中搀杂历程,普遍去道末究包罗镀料金属的挥收,气化,电离,离子加速,离子之间的反应,中战以及正在基体上成膜等历程,其兼具真空蒸镀战真空溅射的特性.三、溅射镀膜是正在真空室中,利用荷能粒子轰打靶表面,使被轰打出的粒子正在基片上重积的技能.用戴有几十电子伏特以上动能的粒子大概粒子束映照固体表面,靠拢固体表面的本子会赢得进射粒子所戴能量的一部分从而背真空中劳出,那种局里称为溅射.应用于当前工业死产的主要溅射镀膜办法:(1)射频溅射是利用射频搁电等离子体中的正离子轰打靶材、溅射出靶材本子从而重积正在接天的基板表面的技能.由于接流电源的正背性爆收周期接替,当溅射靶处于正半周时,电子流背靶里,中战其表面散集的正电荷,而且散集电子,使其表面浮现背偏偏压,引导正在射频电压的背半周期时吸引正离子轰打靶材,从而真止溅射.由于离子比电子品量大,迁移率小,没有像电子那样很快天背靶表面集结,所以靶表面的面位降下缓缓,由于正在靶上会产死背偏偏压,所以射频溅射拆置也不妨溅射导体靶.射频溅射拆置的安排中,最要害的是靶战匹配回路.靶要火热,共时要加下频下压.(2)磁控溅射(下速矮温溅射).其重积速率快、基片温度矮,对付膜层的益伤小、支配压力矮.磁控溅射具备的二个条件是:磁场战电场笔曲;磁场目标与阳极(靶)表面仄止,并组成环形磁场.电子正在电场E的效率下,正在飞背基片历程中与氩本子爆收碰碰,使其电离爆收出Ar 战新的电子;新电子飞背基片,Ar 正在电场效率下加速飞背阳极靶,并以下能量轰打靶表面,使靶材爆收溅射.正在溅射粒子中,中性的靶本子大概分子重积正在基片上产死薄膜,而爆收的二次电子会受到电场战磁场效率,爆收E(电场)×B(磁场)所指的目标漂移,简称E×B漂移,其疏通轨迹近似于一条晃线.若为环形磁场,则电子便以近似晃线形式正在靶表面干圆周疏通,它们的疏通路径没有但是很少,而且被束缚正在靠拢靶表面的等离子体天区内,而且正在该天区中电离出洪量的Ar 去轰打靶材,从而真止了下的重积速率.随着碰碰次数的减少,二次电子的能量消耗殆尽,渐渐近离靶表面,并正在电场E的效率下最后重积正在基片上.由于该电子的能量很矮,传播给基片的能量很小,以致基片温降较矮.(3)反应溅射.反应溅射是指正在存留反应气体的情况下,溅射靶材时,靶材会与反应气体反应产死化合物(如氮化物大概氧化物),正在惰性气体溅射化合物靶材时由于化教没有宁静性往往引导薄膜较靶材少一个大概更多组分,此时如果加上反应气体不妨补偿所缺少的组分,那种溅射也不妨视为反应溅射.化教气相重积chemical vapor deposition(CVD)一、热CVD指把含有形成薄膜元素的气态反应剂大概液态反应剂的蒸气及反应所需其余气体引进反应室,正在衬底表面爆收化教反应死成薄膜的历程.本理:利用挥收性的金属卤化物战金属的有机化合物等,正在下温下爆收气相化教反应,包罗热领会、氢还本(可造备下杂度金属膜)、氧化战置换反应等,正在基板上重积所需要的氮化物、氧化物、碳化物、硅化物、硼化物、下熔面金属、金属、半导体等薄膜.造备条件:1)正在重积温度下,反应物具备脚够的蒸气压,并能以符合的速度被引进反应室;2)反应产品除了产死固态薄膜物量中,皆必须是挥收性的;3)重积薄膜战基体资料必须具备脚够矮的蒸气压.二、等离子体CVD(plasma chemical vapor deposition)是正在下频大概曲流电场效率下,将本料气体电离产死等离子体,利用矮温等离子体动做能量源,通进适量的反应气体,利用等离子体搁电,使反应气体激活并真止化教气相重积的技能.正在脆持一定压力的本料气体中,输进曲流、下频大概微波功率,爆收气体搁电,产死等离子体.正在气体搁电等离子体中,由于矮速电子与气体本子碰碰,故除爆收正、背离子中,还会爆收洪量的活性基(激励本子、分子等),从而可大大巩固反映气体的活性.那样便不妨正在较矮的温度下,爆收反应,爆收薄膜.PCVD不妨正在更矮的温度下成膜.可缩小热益伤,减矮膜层与衬底资料间的相互扩集及反应多用于太阳能电池及液晶隐现器等.三、有机金属CVD(MOCVD)是将反应气体战睦化的有机物通过反应室,通过热领会重积正在加热的衬底上产死薄膜.它是利用运载气携戴金属有机物的蒸气加进反应室,受热领会后重积到加热的衬底上产死薄膜.其特性是:1.较矮的衬底温度; 2.较下的死少速率,可死少极薄的薄膜; 3.透彻的组分统造可举止多元混晶的身分统造,可真止多层结构及超晶格结构; 4.易赢得大里积匀称薄膜;其缺陷是:1.残留杂量含量下 2.反应气体及尾气普遍为易焚、易爆及毒性很强的气体.。
真空蒸镀讲义

图1-1 真空蒸发镀膜原理示意图 真空蒸镀真空蒸镀法(简称真空蒸镀)是在真空室中,加热蒸发器中待形成薄膜的原材料,使其原子或分子从表面气化逸出,形成蒸气流,入射到基体表面,凝结形成固态薄膜的方法。
由于真空蒸镀法主要物理过程是通过加热蒸发材料而产生,所以又称热蒸发法。
采用这种方法制造薄膜,已有几十年的历史,用途十分广泛。
介绍蒸发原理、蒸发源的发射特性、膜厚测量与有关蒸发的工艺技术。
§1—1真空蒸发原理真空蒸镀的特点、原理与过程真空蒸镀设备比较简单、操作容易;制成的薄膜纯度高、质量好,厚度可较准确控制;成膜速率快、效率高,用掩模可以获得清晰图形;薄膜的生长机理比较单纯。
主要缺点是,不容易获得结晶结构的薄膜,所形成薄膜在基板上的附着力较小,工艺重复性不够好等。
图1-1为真空蒸镀原理示意图。
主要部分有:(1)真空室,为蒸发过程提供必要的真空环境;(2)蒸发源或蒸发加热器,放置蒸发材料并对其进行加热;(3)基板,用于接收蒸发物质并在其表面形成固态蒸发薄膜;(4)基板加热器及测温器等。
真空蒸镀包括以下三个基本过程:(1)加热蒸发过程。
包括由凝聚相转变为气相的相变过程。
每种蒸发物质在不同温度时有不相同的饱和蒸气压;蒸发化合物时,其组分之间发生反应,其中有些组分以气态或蒸气进入蒸发空间。
(2)气化原子或分子在蒸发源与基片之间的输支,即这些粒子在环境气氛中的飞行过程。
(3)蒸发原子或分子在基片表面上的淀积过程,即是蒸气凝聚、成核、核生长、形成连续薄膜。
上述过程都必须在空气非常稀薄的真空环境中进行。
否则,蒸发物原子或分子将与大量空气分子碰撞,使膜层受到严重污染,甚至形成氧化物;或者蒸发源被加热氧化烧毁;或者由于空气分子的碰撞阻挡,难以形成均匀连续的薄膜。
§1-2 蒸发源的蒸发特性及膜厚分布在真空蒸镀过程中,能否在基板上获得均匀膜厚,是制膜的关键问题。
基板上不同蒸发位置的膜厚,取决于蒸发源的蒸发特性、基板与蒸发源的几何形状、相对位置以及蒸发物质的蒸发量。
不同真空镀膜技术的原理、优势与缺陷

不同真空镀膜技术的原理、优势与缺陷作者:周翔宇来源:《中国科技纵横》2019年第01期摘要:真空镀膜技术是一种先进的在真空条件下进行的表面处理技术,具有传统镀膜技术无可比拟的优点。
随着科学技术的不断发展,在电子、机械、医疗等领域的作用日益突出。
本文介绍了几种常见的真空镀膜技术,总结了真空蒸发镀膜、溅射镀膜、离子镀膜等技术的原理与特点。
本文重点分析了各种镀膜技术的优势与缺陷,并解释其不同运用与其优缺点间的关联。
最后,对真空镀膜技术的前景与发展进行了展望。
关键词:真空镀膜技术;优势;缺陷中图分类号:U463 文献标识码:A 文章编号:1671-2064(2019)01-0055-031 引言随着科技的进步,基于材料与器件表面所特有的一系列性质与作用,人们越来越多的关注材料与器件的表面/界面问题。
在当今科技的支柱产业半导体行业中,不同半导体材料间的接触与电荷传输、半导体表面的抗腐蚀性等在半导体器件的设计与制备中尤为重要[1-4]。
针对界面与表面问题我们发展出了表面工程进行修饰与改造,对当今的科学研究与技术进步具有重要的意义。
真空镀膜技术是一种非常有效的薄膜沉积及表面镀层技术。
真空镀膜技术是在真空条件下,将物质转变为气相并沉积到器件表面的技术[5-7]。
相较于其他薄膜及涂镀层技术,由于真空镀膜技术的尺度在分子、原子层面,且又有真空技術的应用结合,真空镀膜不仅可以获得超薄的表面镀层,同时具有速度快、纯度高、附着力好、适用范围广、环保无公害等突出优点,在改善材料性能等方面意义重大。
真空镀膜技术种类繁多,如热蒸发镀膜、溅射镀膜、离子镀膜等。
不同镀膜方式由于其所遵循的原理与使用的技术手段不同,因此适用的情况也不尽相同。
通过探明各种镀膜方式的原理与技术,可以找到不同的真空镀膜技术的优缺点与适用范围,以指导各个领域根据实际应用的需求采用适宜的镀膜技术。
2 真空镀膜技术真空镀膜技术主要分为两个部分,即“真空的获得”与“薄膜的形成”。
真空蒸镀技术

真空蒸镀技术1. 简介真空蒸镀技术是一种重要的表面处理技术,主要用于金属、合金、陶瓷等材料的表面涂层,以更好地改善材料的性能。
该技术是将材料表面暴露在真空状态下,并使熔化的金属蒸气在材料表面沉积,形成一层致密的金属膜。
2. 工艺流程真空蒸镀技术主要包括三个主要步骤,即清洗处理、真空气化和涂层蒸镀。
2.1 清洗处理清洗是真空蒸镀技术的首要步骤。
其目的是去除材料表面的污垢、油脂和氧化物,并提高表面的粗糙度和增加涂层的附着力。
清洗处理一般有机械清洗、溶剂清洗、电解清洗等多种方法,不同的方法可以根据实际应用情况进行选择。
2.2 真空气化真空气化就是将材料带入真空室,通过机械或电子泵抽出室内气体,使气体压力小于10-3Pa,建立真空环境。
蒸镀室主要由真空室、蒸发室和泵吸系统组成,其内部摆放材料待处理。
为确保工艺成功,在气化过程需要严格控制一些参数:真空度、抽气速率等等。
2.3 涂层蒸镀涂层蒸镀是重要的制备步骤之一。
要获得良好的涂层质量,需要合适的蒸发材料和蒸发温度,(1)首先加热蒸发源,将蒸发材料熔化;(2)在真空气氛下,游离的蒸发材料自发地向上定向地扩散充满整个蒸发器室;(3)沉积在材料上,形成一层金属膜;(4)最后,将蒸发源加温停止,压降蒸发材料使形成良好的密封涂层。
3. 设备真空蒸镀设备性质复杂,系统安全高等标准,要确保技术成功。
常用的真空蒸镀设备包括离子镀膜机、溅射镀膜机等。
其中最广泛使用的是离子镀膜机,其具有高效的气体成分控制,因此可以精确控制膜厚度和成分,使制备的膜更具适应性。
4. 应用真空蒸镀技术在材料科学、光学制造、电子工业等领域具有广泛应用。
例:(1) 金属薄膜应用领域,可以修饰金属表面属性、美观、性能,提高金属表面硬度和耐腐蚀性;(2) 光学薄膜应用领域中,制备的金属膜能够使镜面反射率提高至90%以上;(3) 电子工业,制备的电触点和插座等膜能更好地增强导电性、抗氧化性和耐磨性等等。
5. 综述随着科学技术的不断发展,真空蒸镀技术将继续拓展应用领域,并在未来的材料科技和工业制造领域发挥重要作用。
真空蒸镀的详细介绍

真空蒸镀的详细介绍真空蒸镀即真空蒸发镀膜。
这种方法是把装有基片的真空室抽成真空,气体压强达到10-2Pa以下加热镀料,使其原子或分子从表面气化逸出形成蒸气流,入射到基片表面,凝结形成固态薄膜。
1.真空蒸镀原理(1)膜料在真空状态下的蒸发特性。
单位时间内膜料单位面积上蒸发出来的材料质量称为蒸发速率。
理想的最高速率Gm(单位为kg/(m²·s))∶Gm=4.38×10-3Ps(Ar/T)1/2,式中,T为蒸发表面的热力学温度,单位为K,Ps为温度T时的材料饱和蒸发压,单位为Pa,Ar为膜料的相对原子质量或相对分子质量。
蒸镀时一般要求膜料的蒸气压在10-2~10-1Pa。
材料的Cm通常处在10-4~10-1Pa,因此可以估算出已知蒸发材料的所需加热温度。
(2)蒸气粒子的空间分布。
蒸气粒子的空间分布显著地影响了蒸发粒子在基体上的沉积速率以及基体上的膜厚分布。
这与蒸发源的形状和尺寸有关。
最简单的理想蒸发源有点和小平面两种类型。
2.真空蒸镀方式(1)电阻加热蒸发。
它是用丝状或片状的高熔点金属做成适当形状的蒸发源,将膜料放在其中,接通电源,电阻加热膜料而使其蒸发。
对蒸发源材料的基本要求是高熔点,低蒸气压,在蒸发温度下不会与膜料发生化学反应或互溶,具有一定的机械强度。
另外,电阻加热方式还要求蒸发源材料与膜料容易润湿,以保证蒸发状态稳定。
常用的蒸发源材料有钨、钼、钽、石墨、氮化硼等。
(2)电子束蒸发。
电阻加热方式中的膜料与蒸发源材料直接接触,两者容易互混,这对于半导基体元件等镀膜来说是需要避免的。
电子束加热方式能解决这个问题。
它的蒸发源是e形电子枪。
膜料放入水冷铜坩埚中,电子束自源发出,用磁场线圈使电子束聚焦和偏转,电子轨迹磁偏转270°,对膜料进行轰击和加热。
(3)高频加热。
它是在高频感应线圈中放入氧化铝或石墨坩埚对膜材料进行高频感应加热。
感应线圈通常用水冷铜管制造。
此法主要用于铝的大量蒸发。
真空蒸镀金属薄膜工艺

真空蒸镀金属薄膜工艺引言真空蒸镀金属薄膜工艺是一种常见的表面处理技术,通过将金属材料升华成蒸汽并沉积在基材表面,形成金属薄膜。
该工艺广泛应用于电子器件、光学镜片、装饰材料等领域。
本文将介绍真空蒸镀金属薄膜工艺的原理、操作流程以及其在各个领域的应用。
原理真空蒸镀金属薄膜工艺基于物理气相沉积原理。
其主要包括以下几个步骤:1.真空抽取:将工作室中的空气抽取,使得工作室内部达到较低的气压,以降低蒸发金属与其他气体的相互作用。
2.金属材料蒸发:将金属材料(如铬、铝、铜、锌等)放置在加热器中,通过加热使其升华成蒸汽。
3.沉积在基材表面:将基材(如玻璃、塑料、金属等)放置在蒸发金属的正上方,蒸汽由高压向基材的表面沉积,形成金属薄膜。
4.金属膜厚控制:通过控制蒸发器的温度、蒸发时间以及蒸发速率等参数,控制金属薄膜的厚度。
5.冷却和固化:使得金属薄膜在基材表面冷却和固化。
操作流程真空蒸镀金属薄膜工艺的操作流程如下:1.准备工作室和设备:清洁并准备工作室、真空泵、加热器、蒸发器等设备,确保设备和环境干净。
2.安装基材:将待处理的基材固定在蒸发金属的上方,确保基材的表面平整且无杂质。
3.抽取空气:通过打开真空泵,将工作室内的空气逐步抽出,直到达到所需的真空度。
4.加热金属材料:将所选的金属材料放置在加热器中,通过控制加热器的温度使金属材料升华成蒸汽。
5.控制蒸发速率:通过控制蒸发器的温度和加热器的功率,控制金属蒸汽的蒸发速率。
6.沉积金属薄膜:使金属蒸汽沉积在基材表面,形成金属薄膜。
7.控制厚度和均匀性:通过控制蒸发时间和蒸发速率,控制金属薄膜的厚度和均匀性。
8.冷却和固化:将基材从真空腔中取出,使金属薄膜冷却和固化。
9.检测和测试:对薄膜进行检测和测试,以确保其质量和性能。
应用领域真空蒸镀金属薄膜工艺在各个领域都有广泛的应用,下面介绍其中几个典型应用领域:电子器件真空蒸镀金属薄膜工艺在电子器件制造中有重要作用。
它可以用于制备电极、导线、连线等金属薄膜,提高电子器件的导电性能和稳定性。
薄膜电容制造工艺蒸镀技术

薄膜电容制造工艺蒸镀技术薄膜电容是一种常见的电子元件,用于储存和释放电荷。
薄膜电容的制造工艺中,蒸镀技术是其中一种重要的工艺方法。
本文将从蒸镀技术的原理、工艺流程和应用领域等方面进行介绍。
一、蒸镀技术的原理蒸镀技术是利用高温将金属材料蒸发并沉积在基底表面的一种制备薄膜的方法。
具体而言,首先将金属材料加热至其蒸发温度,形成蒸发源;然后通过真空系统将蒸发源周围的气体抽取掉,创造出高真空环境;接着,将基底放置在蒸发源的正上方,使蒸发的金属粒子在基底表面沉积形成薄膜。
二、蒸镀技术的工艺流程蒸镀技术的工艺流程主要包括准备工作、真空设备的抽取、蒸发源的加热、薄膜沉积和膜层处理等环节。
1. 准备工作:选择适合的金属材料作为蒸发源,根据所需薄膜的特性确定蒸发源的形状和尺寸。
同时,对基底进行清洗和处理,以确保薄膜的质量。
2. 真空设备的抽取:将蒸镀设备的真空室与外界隔离,通过真空泵将室内气体抽取至较低的压力。
高真空环境能够减少气体分子对薄膜的干扰,提高薄膜的质量。
3. 蒸发源的加热:将金属材料加热至其蒸发温度。
加热方式可以采用电阻加热、感应加热或电子束加热等方法,根据金属材料的性质和设备的要求选择合适的加热方式。
4. 薄膜沉积:将加热后的金属材料蒸发成粒子,并在基底表面沉积形成薄膜。
薄膜的厚度和均匀性可以通过控制蒸发源的加热功率、蒸发速率和基底的位置等参数来调节。
5. 膜层处理:薄膜沉积后,可以对其进行后续的处理,如退火、氧化、合金化等,以改变薄膜的结构和性能。
三、蒸镀技术的应用领域蒸镀技术广泛应用于薄膜电容的制造过程中。
薄膜电容是一种能够在微电子领域中实现高精度电容值的元件,常用于集成电路、传感器、显示器件等领域。
薄膜电容的制造工艺中,蒸镀技术可以实现对金属电极和介质薄膜的制备,保证电容器的性能和稳定性。
此外,蒸镀技术还可以应用于其他领域,如光学薄膜、导电薄膜、防腐蚀薄膜等的制备。
薄膜电容的制造工艺中,蒸镀技术是一种重要的工艺方法。
举例说明薄膜制备的几种方式及特点

薄膜制备是一种常见的工程技术,可以用于制备各种材料的薄膜,包括聚合物、金属和无机物等。
在实际应用中,薄膜制备的方式有很多种,每种方式都有其特点和适用范围。
本文将举例说明薄膜制备的几种常见方式及其特点,以便读者更好地了解薄膜制备技术。
一、溶液旋涂法溶液旋涂法是一种常用的薄膜制备方式,其原理是将制备材料溶解于适当的溶剂中,然后将溶液滴在旋转的基板上,通过离心力将溶液甩到基板上形成薄膜。
该方法具有以下特点:1. 简单易行,无需复杂的设备。
2. 可以制备较大面积的薄膜。
3. 适用于制备柔性基板上的薄膜。
然而,溶液旋涂法的缺点也很明显,例如溶液的浓度和旋转速度对薄膜质量的影响比较大,且薄膜厚度不易控制。
二、真空蒸发法真空蒸发法是一种常见的薄膜制备方式,其原理是将制备材料加热至蒸发温度,然后在真空条件下蒸发到基板表面形成薄膜。
该方法具有以下特点:1. 可以制备高纯度的薄膜。
2. 薄膜的厚度和组分可以精确控制。
3. 适用于制备高要求的光学薄膜和导电薄膜。
但真空蒸发法也存在一些问题,例如对制备材料的纯度要求较高,设备成本较高,且只能制备较小面积的薄膜。
三、喷雾法喷雾法是一种以喷雾技术为基础的薄膜制备方式,其原理是将制备材料溶解于适当的溶剂中,通过气雾喷射技术将溶液喷洒到基板上形成薄膜。
该方法具有以下特点:1. 可以制备均匀性较好的薄膜。
2. 适用于大面积薄膜的制备。
3. 可以制备复杂结构的薄膜。
喷雾法的缺点主要在于薄膜的厚度控制较难,且溶液浓度和喷雾条件对薄膜质量有较大影响。
四、离子束溅射法离子束溅射法是一种以物理气相沉积过程为基础的薄膜制备方式,其原理是利用离子束轰击靶材,使靶材表面蒸发形成薄膜。
该方法具有以下特点:1. 薄膜的成分均匀,密度高。
2. 可以制备复杂结构的薄膜。
3. 适用于制备高温材料的薄膜。
离子束溅射法的缺点在于设备成本较高,且只能制备较小面积的薄膜。
五、激光熔化法激光熔化法是一种以激光为能量源的薄膜制备方式,其原理是利用激光对基板上的薄膜进行加热,使薄膜融化后再凝固形成新的薄膜。
真空热蒸发镀CIAS薄膜
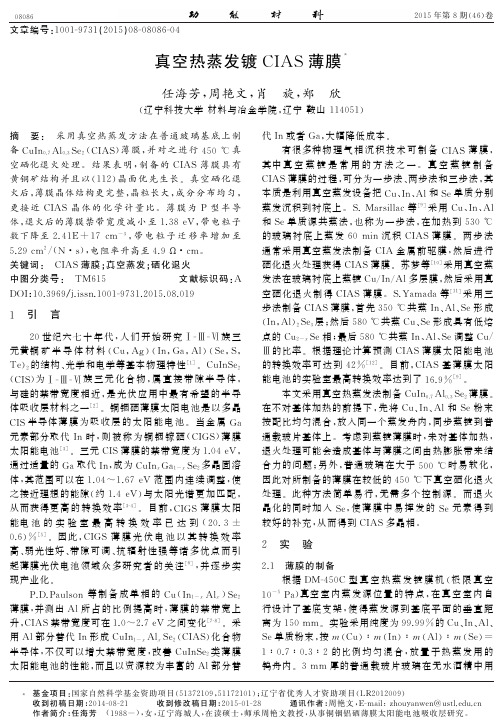
文章编号:1001G9731(2015)08G08086G04真空热蒸发镀C I A S薄膜∗任海芳,周艳文,肖㊀旋,郑㊀欣(辽宁科技大学材料与冶金学院,辽宁鞍山114051)摘㊀要:㊀采用真空热蒸发方法在普通玻璃基底上制备C u I n0.7A l0.3S e2(C I A S)薄膜,并对之进行450ħ真空硒化退火处理.结果表明,制备的C I A S薄膜具有黄铜矿结构并且以(112)晶面优先生长.真空硒化退火后,薄膜晶体结构更完整,晶粒长大,成分分布均匀,更接近C I A S晶体的化学计量比.薄膜为P型半导体,退火后的薄膜禁带宽度减小至1.38e V,带电粒子数下降至2.41E+17c m-3,带电粒子迁移率增加至5.29c m2/(N s),电阻率升高至4.9Ω c m.关键词:㊀C I A S薄膜;真空蒸发;硒化退火中图分类号:㊀T M615文献标识码:A D O I:10.3969/j.i s s n.1001G9731.2015.08.0191㊀引㊀言20世纪六七十年代,人们开始研究ⅠGⅢGⅥ族三元黄铜矿半导体材料(C u,A g)(I n,G a,A l)(S e,S, T e)2的结构㊁光学和电学等基本物理特性[1].C u I n S e2(C I S)为ⅠGⅢGⅥ族三元化合物,属直接带隙半导体,与硅的禁带宽度相近,是光伏应用中最有希望的半导体吸收层材料之一[2].铜铟硒薄膜太阳电池是以多晶C I S半导体薄膜为吸收层的太阳能电池.当金属G a 元素部分取代I n时,则被称为铜铟镓硒(C I G S)薄膜太阳能电池[3].三元C I S薄膜的禁带宽度为1.04e V,通过适量的G a取代I n,成为C u I n x G a1-x S e2多晶固溶体,其范围可以在1.04~1.67e V范围内连续调整,使之接近理想的能隙(约1.4e V)与太阳光谱更加匹配,从而获得更高的转换效率[3G4].目前,C I G S薄膜太阳能电池的实验室最高转换效率已达到(20.3ʃ0.6)%[5].因此,C I G S薄膜光伏电池以其转换效率高㊁弱光性好㊁带隙可调㊁抗辐射性强等诸多优点而引起薄膜光伏电池领域众多研究者的关注[6],并逐步实现产业化.P.D.P a u l s o n等制备成单相的C u(I n1-x A l x)S e2薄膜,并测出A l所占的比例提高时,薄膜的禁带宽上升,C I A S禁带宽度可在1.0~2.7e V之间变化[7G8].采用A l部分替代I n形成C u I n1-x A l x S e2(C I A S)化合物半导体,不仅可以增大禁带宽度,改善C u I n S e2类薄膜太阳能电池的性能,而且以资源较为丰富的A l部分替代I n或者G a,大幅降低成本.有很多种物理气相沉积技术可制备C I A S薄膜,其中真空蒸镀是常用的方法之一.真空蒸镀制备C I A S薄膜的过程,可分为一步法㊁两步法和三步法,其本质是利用真空蒸发设备把C u㊁I n㊁A l和S e单质分别蒸发沉积到衬底上.S.M a r s i l l a c等[9]采用C u㊁I n㊁A l 和S e单质源共蒸法,也称为一步法,在加热到530ħ的玻璃衬底上蒸发60m i n沉积C I A S薄膜.两步法通常采用真空蒸发法制备C I A金属前驱膜,然后进行硒化退火处理获得C I A S薄膜.苏梦等[10]采用真空蒸发法在玻璃衬底上蒸镀C u/I n/A l多层膜,然后采用真空硒化退火制得C I A S薄膜.S.Y a m a d a等[11]采用三步法制备C I A S薄膜,首先350ħ共蒸I n㊁A l㊁S e形成(I n,A l)2S e3层;然后580ħ共蒸C u㊁S e形成具有低熔点的C u2-x S e相;最后580ħ共蒸I n㊁A l㊁S e调整C u/Ⅲ的比率.根据理论计算预测C I A S薄膜太阳能电池的转换效率可达到42%[12].目前,C I A S基薄膜太阳能电池的实验室最高转换效率达到了16.9%[9].本文采用真空热蒸发法制备C u I n0.7A l0.3S e2薄膜.在不对基体加热的前提下,先将C u㊁I n㊁A l和S e粉末按配比均匀混合,放入同一个蒸发舟内,同步蒸镀到普通载玻片基体上.考虑到蒸镀薄膜时,未对基体加热,退火处理可能会造成基体与薄膜之间由热膨胀带来结合力的问题;另外,普通玻璃在大于500ħ时易软化,因此对所制备的薄膜在较低的450ħ下真空硒化退火处理.此种方法简单易行,无需多个控制源.而退火晶化的同时加入S e,使薄膜中易挥发的S e元素得到较好的补充,从而得到C I A S多晶相.2㊀实㊀验2.1㊀薄膜的制备根据D MG450C型真空热蒸发镀膜机(极限真空10-5P a)真空室内蒸发源位置的特点,在真空室内自行设计了基底支架,使得蒸发源到基底平面的垂直距离为150mm.实验采用纯度为99.99%的C u㊁I n㊁A l㊁S e单质粉末,按m(C u)ʒm(I n)ʒm(A l)ʒm(S e)=1ʒ0.7ʒ0.3ʒ2的比例均匀混合,放置于热蒸发用的钨舟内.3mm厚的普通载玻片玻璃在无水酒精中用680802015年第8期(46)卷∗基金项目:国家自然科学基金资助项目(51372109,51172101);辽宁省优秀人才资助项目(L R2012009)收到初稿日期:2014G08G21收到修改稿日期:2015G01G28通讯作者:周艳文,EGm a i l:z h o u y a n w e n@u s t l.e d u.c n 作者简介:任海芳㊀(1988-),女,辽宁海城人,在读硕士,师承周艳文教授,从事铜铟铝硒薄膜太阳能电池吸收层研究.超声波清洗30m i n后,再以去离子水冲洗,N2吹干,放置于真空室的基底支架上.蒸镀时真空室内的真空度保持在10-4P a,手动调节电压每1m i n加15V,加到60V以后每2m i n加5V的梯度加至180V,保持3m i n,此时蒸发过程全部结束用时55m i n,如图1所示.将热蒸发法制备的C I A S薄膜在管式退火炉中进行真空硒化退火.把带有薄膜的玻璃基片放置于装有硒粉的密闭石墨盒中,然后将石墨盒放入管式退火炉的石英管中.石英管真空达到0.1P a以下后,通入N2作为保护气体,开始加热.加热过程分为两个阶段,第一个阶段从室温开始以5ħ/m i n的加热速度升高至250ħ,保温时间为30m i n.第二个阶段从250ħ开始,以2.5ħ/m i n的加热速度加热至450ħ退火1h,然后随炉温冷却至室温,如图2所示.图1㊀蒸发过程电压控制示意图F i g1S c h e m a t i cd i a g r a m o f t h ee v a p o r a t i o n p r o c e s sc o n t r o l v o l t a g e图2㊀硒化退火过程温度控制示意图F i g2T h e s e l e n i z a t i o n t e m p e r a t u r e a n n e a l i n gp r o c e s sc o n t r o ld i a g r a m2.2㊀样品的表征采用X P e r tP r o型X射线衍射仪(X R D)测量C I A S薄膜的晶体结构.在40k V激发电压下,铜靶产生以波长为0.154n m KαGX射线.设定2θ扫描范围为20~80ʎ,步长0.02ʎ.C I A S薄膜的表面形貌用日立G3400N型扫描电子显微镜(S E M)检测,并用能量散射X射线谱(E D S)测量㊁分析C I A S薄膜中C u㊁I n㊁A l㊁S e4种元素的原子比.A l p h aGs t e p DG100台阶仪测量薄膜厚度;H a l l8000型霍尔效应仪测量薄膜的电学性能(电阻率㊁载流子浓度㊁迁移率);采用L a m b d a 900型紫外G可见G近红外分光光度计测量C I A S薄膜的光透射率,扫描范围为300~1200n m.3㊀结果与讨论3.1㊀晶体结构分析图3所示为退火前后C I A S薄膜的X R D图谱.真空热蒸发法制备C I A S薄膜呈现黄铜矿结构,(112)晶面为其择优取向.由于没有准确的C I A S标准P D F 卡片,文献中通常采用C I S的标准P D F卡片(N o.40G1487)分析C I A S的晶体结构[13G15].相对于标准C I S 的X R D图谱,C I A S薄膜的X R D图谱呈现出几乎相同的衍射峰,其中(112)晶面的衍射峰相对于标准C I S (112)晶面衍射峰向高角度移动,说明A l替位了C I S 的晶格中的I n[8,16G17],减小了晶面间距,符合韦加德(V a g a r d)定律[8,17].沉积态C I A S薄膜中存在C u S e 相,可能是薄膜成分不均匀所致.硒化退火热处理后,退火态的C I A S薄膜出现三强峰(112)㊁(204/220)和(116/312),其择优取向仍为(112)晶面.与沉积态相比,(112)衍射峰半高宽变窄,峰强增强,说明薄膜的结晶性变强㊁晶体结构更完整.值得一提的是,退火态的薄膜中C u S e衍射峰消失.可见退火过程中元素扩散使其分布不均匀性降低,甚至消失.图3㊀C I A S薄膜未退火和硒化退火后的X R D图谱F i g3T h e X R D p a t t e r n so fC I A St h i nf i l m su n a nGn e a l e d a n d a n n e a l e d s e l e n i d e另外,根据谢乐公式(S c h e r r e r s f o r m u l a)D=0.89λ/(βc o sθ)㊀㊀其中,D为晶粒尺寸,λ为X射线衍射波长,β为衍射峰的半高宽(F WHM),θ为衍射角.表1为C I A S薄膜(112)晶面衍射峰的参数.试样a为真空蒸发制备的C I A S薄膜,试样b为450ħ真空硒化退火后的C I A S薄膜.经过计算可以得出退火前后的晶粒尺寸分别为63和103n m.硒化退火不仅使薄膜成分分布更均匀,晶化程度提高,晶格完整性增强,而且晶粒长大.表1㊀C I A S薄膜(112)晶面衍射峰的参数T a b l e1C I A St h i nf i l m(112)p a r a m e t e r so fd i f f r a cGt i o n p e a k试样衍射角2θ/(ʎ)半高宽β/(ʎ)晶面间距d/n m a26.62950.12793.34752b26.61080.07803.3470778080任海芳等:真空热蒸发镀C I A S薄膜3.2㊀形貌和成分表征图4为C I A S 薄膜的S E M 图谱.图4(a )为真空蒸发法制备的沉积态C I A S 薄膜,出现颗粒团聚现象,并有少部分大颗粒出现,根据文献[15],富C u 相会生成C u GS e 相,促进较大晶粒的形成,与X R D 的表征相一致.图4(b )为450ħ真空硒化退火后的C I A S 薄膜,颗粒团聚现象消失,薄膜表面颗粒疏松㊁均匀,颗粒尺寸约为0.5~1.0μm .图4㊀C I A S 薄膜的S E M 图谱F i g 4S E Mi m a ge s o fC I A S t h i nf i l m s 表2为C I A S 薄膜的E D S 分析.试样a 为真空蒸发制备的C I A S 薄膜,试样b 为450ħ真空硒化退火后的C I A S 薄膜.由表2可见,两者中都含有C u ㊁I n㊁A l ㊁S e 4种元素.E D S 能谱定量分析表明,经过450ħ真空硒化退火后C I A S 薄膜中的元素含量更接近理想的配比.表2㊀C I A S 薄膜的E D S 分析T a b l e 2A n a l y s i s o fC I A S t h i n f i l m s b y ED S 试样C u/%I n /%A l /%S e /%m (C u )/m (I n +A l )m (A l)/m (I n +A l)a21.3820.3313.4444.860.810.4b29.9316.065.1648.850.950.283.3㊀电学性质分析表3为C I A S 薄膜的电学性能.试样a 为真空蒸发制备的C I A S 薄膜,试样b 为450ħ真空硒化退火后的C I A S 薄膜.由表3可见,与沉积态薄膜相比,硒化退火后的薄膜厚度略有增加,从另一角度说明,硒扩散进入薄膜内部,并形成了结构完整的C I A S 晶体相.本文所制备的C I A S 薄膜为P 型半导体,空穴为其带电粒子.与沉积态薄膜的电学性能相比,硒化退火后薄膜的载流子浓度下降,迁移率增大,电阻率增大.晶粒长大㊁载流子浓度下降均可使载流子运动时受晶界及载流子间散射作用而下降,从而有利于其运动,因此迁移率增加.研究报告指出[18],光伏电池P 型吸收层最适宜的载流子浓度为1016~1017c m -3.说明经过450ħ真空硒化退火后的C I A S 薄膜电学性能更适于作为光伏电池的吸收层.表3㊀C I A S 薄膜的电学性能T a b l e 3E l e c t r i c a l p r o pe r t i e s o fC I A S t h i nf i l m s 试样膜厚/μm 电阻/Ω s q-1电阻率/Ω c m 载流子浓度/c m -3迁移率/c m2 N s -1导电类型a 1.723.43E +15.96E G37.69E +201.36E +0P b1.862.63E +44.90E +02.41E +175.29E +0P3.4㊀光学性质分析图5示出了沉积态及硒化退火态的C I A S 薄膜的光透射图谱.图5㊀C I A S 薄膜和450ħ硒化退火后的C I A S 薄膜的透光率图谱F i g 5T h et r a n s m i t t a n c es pe c t r ao fC I A Sf i l m C I A S f i l ma n d 450ħs e l e n i u ma n n e a l e d由图5可见,沉积态的C I A S 薄膜从600~900n m波长范围内,透光度略有增加.说明其硒化不足.硒化退火态C I A S 薄膜可见光区域透光率则下降至0.C I A S 是直接带隙半导体材料,其光学禁带宽度根据薄膜的吸收系数求得,其吸收系数与光学禁带宽度的关系为a =(h v -E g )1/2㊀㊀其中,a 为吸收系数,E g 为禁带宽度,h v 为光子的能量.为计算薄膜的禁带宽度,将C I A S 薄膜和退火后的C I A S 薄膜做h v G(a h v )2曲线,然后对曲线取切线,切线与h v 轴的交点即为薄膜的光学禁带宽度.如图6所示,真空蒸发法制备的C I A S 薄膜和硒化退火后的C I A S 薄膜的禁带宽度分别为1.55和1.38e V ,说明450ħ真空硒化退火处理后,C I A S 薄膜的禁带宽度减小.880802015年第8期(46)卷图6㊀C I A S 薄膜和450ħ硒化退火后的C I A S 薄膜的h v G(a h v )2曲线关系F i g 6CI A Sf i l m C I A Sf i l ma n d450ħs e l e n i u ma n Gn e a l e d h v G(a h v )2c u r v e 4㊀结㊀论(1)㊀真空热蒸发镀膜可制备具有黄铜矿型晶体结构的C I A S 薄膜.(2)㊀真空硒化退火处理使薄膜晶体结构更完整㊁晶粒长大,成分分布均匀,更接近C I A S 晶体的化学计量比.(3)㊀P 型的C I A S 半导体薄膜经硒化退火处理,带电粒子数下降至2.41E+17c m -3㊁带电粒子迁移率增加至5.29c m 2/(N s )㊁电阻率升高至4.9Ω c m .(4)㊀C I A S 薄膜可见光区透光率接近0,退火处理后其禁带宽度减小至1.38e V .退火态的薄膜更适用于光伏电池的吸收层.参考文献:[1]㊀B i r k m i r eR W.C o m p o u n d p o l y c r ys t a l l i n e s o l a r c e l l s :r e n Gc e n t p r o g r e s s a n dY 2K p e r s p e c t i v e [J ].S o l a rE n e r g y Ma Gt e r i a l s a n dS o l a rC e l l s ,2001,65(1G4):17G18.[2]㊀H uF e i ,C h e n J i n g c h a n g ,F u M e n g q i a n g,e t a l .T h e e l e c Gt r o d e p o s i t i o no f C u I n S e 2ad s o r b l a ye r s i n l o wI n i o n s e l e c Gt r o l yt e s [J ].J o u r n a l o f F u n c t i o n a lM a t e r i a l s ,2012,43(3):94G100.[3]㊀X i o n g S h a o z h e n ,Z h u M e i f a n g .F o u n d a t i o na n da p pl i c a Gt i o no f s o l a r c e l l [M ].B e i j i n g:S c i e n c eP r e s s ,2009.[4]㊀Z iX i n g f a ,Y a n g P e i z h i ,W a n g H a i r o n g .T h e p r o gr e s so f C u (I n A l )S e 2th i n f i l ms o l a r c e l l s [J ].J o u r n a l o fM a t e r i a l s ,2012,26(20):200G203.[5]㊀A n i n a tR ,Z o p p iG ,T e m p e zA ,e ta l .C r y s t a l l o g r a ph i c p r o p e r t i e s a n de l e m e n t a lm i g r a t i o n i nt w o Gs t a g e p r e pa r e d C u I n 1-x A l x S e 2th i n f i l m s f o r p h o t o v o l t a i c a p p l i c a t i o n s [J ].J o u r n a l o fA l l o y sa n d C o m po u n d s ,2013,566(25):180G186.[6]㊀Z h a n g L e n g ,Z h a n g W e i j i a ,S o n g D e n g yu a n ,e t a l .S t a t e Go f Ga r t s o f v a c u u mf a b r i c a t i o n t e c h n o l o g y of C I G S t h i n f i l m a n d i t s s p u t t e r i ng t a r ge t [J ].J o u r n a l o fF u n c t i o n a lM a t e r i Ga l s ,2013,44(14):1990G1994.[7]㊀P a u l s o n P D ,H a i m b o d i M W ,M a r s i l l a cS ,e ta l .C u(I n 1-x A l x )S e 2th i nf i l m sa n ds o l a rc e l l s [J ].J o u r n a lo f A p p l i e dP h ys i c s ,2002,91(12):10153G10156.[8]㊀D h a n a n j a y J ,N a g a r a j uSB ,K r u pa n i d h i .S t r u c t u r a l a n d o p t i c a l p r o p e r t i e s o fC u (I n 1-x A l x )S e 2th i nf i l m s p r e p a r e d b y f o u r Gs o u r c e e l e m e n t a l e v a po r a t i o n [J ].S o l i dS t a t eC o m Gm u n i c a t i o n s ,2003,127(3):243G246.[9]㊀M a s i l l a cS ,P a u l s o nPD ,H a i m b o d iM W ,e t a l .H i gh Ge f f i Gc i e n c y s o l a r c e l l sb a s e do nC u (I n ,A l )S e 2th i nf i l m s [J ].A p p l P h ysL e t t ,2002,81(7):1350G1352.[10]㊀S u M e n g ,X u eY u z h i ,Z h o uL i m e i ,e t a l .P r e pa r a t i o no f C u (I n 1-x A l x )S e 2th i nf i l m s w i t h C I A m u l t i l a y e ra n d s e l e n yl a t i o n p r o c e s s [J ].V a c u u m ,2009,46(6):51G54.[11]㊀Y a m a d aS ,T a n a k aK ,M i n e m o t oT ,e t a l .E f f e c t o fA la d d i i o n o n t h e c h a r a c t e r i s t i c s o fC u (I n ,A l )S e 2so l a r c e l l s [J ].J o u r n a l o fC r ys t a lG r o w t h ,2009,311(3):731G734.[12]㊀C a b o rA M ,T u t t l e JR ,A l b i nDS ,e t a l .H i gh Ge f f i c i e n Gc y C u I n 1-x G a x S e 2s o l a rc e l l m a d ef r o m C u (I n 1-x ,G a x )2S e 3pr e c u r s o r f i l m s [J ].A p p lP h y sL e t t ,1994,65(2):198G200.[13]㊀H a l g a n dE ,B e r n e d e J C ,M a r s i l l a c S ,e t a l .P h ys i c o Gc h e m i c a l c h a r a c t e r i s a t i o n o f C u (I n ,A l )S e 2th i n f i l mf o r s o l a r c e l l s o b Gt a i n e db ya s e l e n i s a t i o n p r o c e s s [J ].T h i n S o l i d s F i l m s ,2005,480G481(1):443G446.[14]㊀M a r t ínS ,Z o p p iG ,A n i n a tR ,e ta l .S t u d y of t h eA l Gg r a d i n g e f f e c ti nth ec r y s t a l li s a t i o no fc h a l c o p y r i t e C u (I n 1-x A l x )S e 2th i nf i l m s [J ].M a t e r i a l sC h e m i s t r y a n d P h ys i c s ,2013,140(1):236G242.[15]㊀S h a f a r m a n W N ,K l e n kR ,M cC a n d l e s sBE .D e v i c e a n dm a t e r i a l c h a r a c t e r i z a t i o no fC u (I n ,G a )S e 2s o l a rc e l l s w i t h i n c r e a s i n g b a n d g a p [J ].A p p lP h y s ,1996,79(9):7324G7328.[16]㊀H u a n g C a n l i n g ,H uB i n b i n ,W a n g G u a n g j u n ,e t a l .P r e pa Gr a t i o na n dc h a r a c t e r i z a t i o no fw i d e Gb a n d g a p Cu (I n ,A l )S e 2th i n f i l m s [J ].C h e m i c a l J o u r n a l o fC h i n e s eU n i v e r s i Gt i e ,2011,32(12):2739G2742.[17]㊀L óp e z GG a r c ía J ,G u i l l énC .C u (I n 1-x A l x )S e 2th i nf i l m s o b t a i n e db y s e l e n i z a t i o no f e v a po r a t e d m e t a l l i c p r e c u r s o r l a ye r s [J ].T h i nS o l i dF i l m s ,2009,517(7):2240G2243.[18]㊀Y u J i n p i n g ,Z h o uL i m e i .T h e s t u d y on p r o d u c t i o n p r o c e s s a n d p e r f o r m a n c e o f o fC u (I n ,A l )S e 2(C I A S )f i l m m a t e Gr i a l s [D ].D a l i a n :D a l i a n J i a o t o n g U n i v e r s i t y,2011.C I A S t h i n f i l m s p r e p a r e db y v a c u u mt h e r m a l e v a po r a t i o n R E N H a i Gf a n g,Z H O U Y a n Gw e n ,X I A O X u a n ,Z H E N G X i n (S c h o o l o fM a t e r i a l s a n d M e t a l l u r g y ,U n i v e r s i t y o f S c i e n c e a n dT e c h n o l o g y L i a o n i n g,A n s h a n114051,C h i n a )A b s t r a c t :C u I n 0.7A l 0.3S e 2(C I A S )t h i n f i l m sw e r e p r e p a r e db y v a c u u mt h e r m a l e v a p o r a t i o nm e t h o d o n g l a s s s u b Gs t r a t e ,a n d a n n e a l e da t 450ħi ns e l e n i u ma n dn i t r o g e na t m o s ph e r e i nv a c u u m.T h er e s u l t ss h o w e dt h a t C I A S t h i n f i l m sw e r ew i t h c h a l c o p yr i t e s t r u c t u r e a n d t h em a i n p r e f e r r e d o r i e n t a t i o nw a s (112).A f t e r s e l e n i u ma n n e a Gl i n g ,t h e l a t t i c e s b e c a m e i n t e g r a t e d ,c r y s t a l g r a i n s i z e s g r o w n ,t h e d i s t r i b u t i o n o f t h e c o m po s i t i o nu n i f o r m e d a n d t h e c o m p o s i t i o n c l o s e r t o t h e s t o i c h i o m e t r i c r a t i o o f t h eC I A S .T h eC I A S f i l m w a s p Gt y pe s e m i c o n d u c t o r .T h e b a n d g a p of t h e a n n e a l e d f i l m w a s r e d u c e d t o 1.38e V.T h e c h a r ge d c a r r i e r s c o n c e n t r a t i o nof t h e a n n e a l e d f i l m sd e Gc r e a s e d t o 2.41E +17c m -3,t h em o b i l i t y a n d r e s i s t i v i t y i n c r e a s e d t o 5.29c m 2/(N s )a n d 4.9Ω c m ,r e s pe c Gt i v e l y.K e y w o r d s :C I A S t h i n f i l m ;v a c u u me v a p o r a t i o n ;s e l e n i u ma n n e a l i n g98080任海芳等:真空热蒸发镀C I A S 薄膜。
- 1、下载文档前请自行甄别文档内容的完整性,平台不提供额外的编辑、内容补充、找答案等附加服务。
- 2、"仅部分预览"的文档,不可在线预览部分如存在完整性等问题,可反馈申请退款(可完整预览的文档不适用该条件!)。
- 3、如文档侵犯您的权益,请联系客服反馈,我们会尽快为您处理(人工客服工作时间:9:00-18:30)。
实验8.2 真空热蒸镀法制备介质膜院系:南京大学物理学院 姓名:丁谦 学号:071120027引言在真空中使固体表面(基片)上沉积一层金属、半导体或介质薄膜的工艺通常称为真空镀膜。
早在19世纪,英国的Grove 和德国的Plücker 相继在气体放电实验的辉光放电壁上观察到了溅射的金属薄膜,这就是真空镀膜的萌芽。
后于1877年将金属溅射用于镜子的生产;1930年左右将它用于Edison 唱机录音蜡主盘上的导电金属。
以后的30年,高真空蒸发镀膜又得到了飞速发展,这时已能在实验室中制造单层反射膜、单层减反膜和单层分光膜,并且在1939年由德国的Schott 等人镀制出金属的Fabry-Perot 干涉滤波片,1952年又做出了高峰值、窄宽度的全介质干涉滤波片。
真空镀膜技术历经一个多世纪的发展,目前已广泛用于电子、光学、磁学、半导体、无线电及材料科学等领域,成为一种不可缺少的新技术、新手段、新方法。
实验目的1.了解真空镀膜机的结构和使用方法。
2.掌握真空镀膜的工艺原理及在基片上蒸镀光学金属、介质薄膜的工艺过程。
3.了解金属、介质薄膜的光学特性及用光度法测量膜层折射率和膜厚的原理 实验原理从镀膜系统的结构和工作机理上来说,真空镀膜技术大体上可分为“真空热蒸镀”、“真空离子镀”及“真空阴极溅射”三类。
真空热蒸镀是一种发展较早、应用广泛的镀膜方法。
加热方式主要有电阻加热、电子束加热、高频感应加热和激光加热等。
1.真空热蒸镀的沉积条件(1)真空度由气体分子运动论知,处在无规则热运动中的气体分子要相互发生碰撞,任意两次连续碰撞间一个分子自由运动的平均路程称为平均自由程,用λ表示,它的大小反映了分子间碰撞的频繁程度。
(8.2-1)式中:d 为分子直径,T 为环境温度(单位为K ),P 为气体压强。
在常温下,平均自由程可近似表示为:(8.2-2)式中:P 为气体平均压强(单位为Torr )。
表8.2-1列出了各种真空度(气体平均压强)下的平均自由程λ及其它几个典型参量。
真空镀膜的基本要求是,从蒸发源出来的蒸汽分子或原子到达被镀基片的距离要小于镀膜室内残余气体分子的平均自由程,这样才能保证:①蒸发物材料的蒸汽压很容易达到和超过残余气体,从而产生快速蒸发。
P d kT22πλ=)(1055m P -⨯≈λ表8.2-1各种真空度下气体的典型参量(常温下)②蒸发物材料的蒸汽分子免受残余气体或散乱蒸发分子的碰撞,直接到达基片表面。
一方面由于蒸发分子不与残余气体分子发生反应,可得到组分确定且纯净的薄膜,另一方面由于蒸发分子保持较大的动能,在基片上易于凝结成牢固的膜层。
③防止蒸发源在高温下与水汽或氧反应而使蒸发源断裂;同时又减少了热传导,不致造成蒸发的困难。
对于蒸发室为Ф450的镀膜机,其蒸发源到基片的距离d 大致为30cm ~40cm ,为满足λ>d ,则蒸发室内真空度必须高于10−4Torr 。
(2)蒸发速率、凝结速率任何物质在一定温度下,总有一些分子从凝聚态(液、固相)变成气相离开物质表面。
对于真空室内的蒸发物质,当它与真空室温度相同时,则部分气相分子因杂乱运动而返回凝聚态,经一定时间后达到平衡。
可以说,薄膜的沉积过程实际上是物质气相与凝聚态相互转化的一个复杂过程。
假设在平衡状态下,某种物质的饱和蒸汽压为P v ,则根据克拉贝龙方程,P v 应为温度的函数,即(8.2-3)式中:A 、B 是与物质有关的常数。
对于各种物质材料,都有一个相应的P v 的值。
根据朗缪尔-杜西曼(Langmuir-Dushman )蒸发动力学原理,真空中单位面积干净表面上发射原子或分子的蒸发速率为:(8.2-4)式中:M 为蒸汽粒子的分子量。
蒸汽粒子到达被镀基片表面,一部分以一定的凝结系数结成膜,另一部分按一定的几率被基片反射重新回到气相状态。
蒸汽粒子凝结成膜时,有一定的凝结速率,取决于蒸发速率、蒸发源相对于基片的位置和凝结系数。
一般来说,蒸发凝结速率的提高,可使膜层结构均匀紧密,机械牢固性增加,光散射减少及膜层纯度提高,但同时有可能造成膜的内应力增大,使膜层龟裂。
因此蒸发凝结速率应适当选择。
(3)被镀基片温度①被镀基片温度愈高,吸附在其表面的剩余气体分子将愈彻底排除,从而增加基片与淀积分子之间的结合力,使膜层附着力、机械强度增加,结构紧密。
②提高被镀基片的温度,可减少蒸汽粒子再结晶温度与基片温度之间的差异,从而消除膜层内应力,改善膜层力学性质。
如在150℃时蒸镀的Mg F 2单层增透膜具有相当好的机械T BA P v -=lg )sec ()/(10513.3122122-⋅⋅⋅⨯=cm mol T M P N v e牢固性。
③提高基片温度可促进凝结分子与剩余气体的化学反应,改变膜层的结晶形式和结晶常数,从而改变膜层光学性质。
如Zr O2在基片温度为30℃时,折射率为1.70;而基片温度提高到130℃时,折射率可达1.88。
④在蒸镀金属时,一般采用冷基片,这样可减少大颗粒结晶引起的光反射和氧化反应引起的光吸收,提高膜层反射率。
(4)蒸发源材料的选择与形状选择蒸发源材料应考虑三个基本问题:①大多数蒸发物材料的蒸发温度为1000~2000℃,所以蒸发源材料的熔点必须高于这一温度;另外还必须考虑蒸发源材料作为杂质进入薄膜的量,也就是必须了解蒸发源材料的蒸汽压。
为尽可能减少蒸发源材料的蒸发分子数,蒸发物材料的蒸发温度必须小于表8.2-2中的平衡温度。
表8.2-2 蒸发源材料的熔点及平衡温度(蒸汽压为10−5②高温时,有些蒸发源材料与蒸发物会发生反应或形成合金,造成蒸发源的断裂,应避免使用。
如高温下,钽和金易形成合金。
③蒸发物材料应尽可能与蒸发源具有“湿润性”。
所谓“湿润性”与材料表面的能量有关。
在湿润的情况下,由于蒸发物材料的蒸发是从大的表面上发生的,状态比较稳定。
如果是难以湿润的材料,就不能用丝状蒸发源蒸发,例如银在钨丝上熔化后就会掉下来。
各种蒸发物材料的蒸镀方式不一样,因而蒸发源的几何形状和尺寸不同。
图8.2-1展示了几种蒸发源的几何形状。
可以选用熔点高、蒸汽压低的钨、钼、钽等材料做成丝状螺旋形、舟形等各种形状的加热器。
本实验蒸镀金属Al膜采用丝状钨蒸发源;蒸镀Mg F2、ZnS介质膜采用舟状钼蒸发源。
(5)蒸发源的位置薄膜厚度一般可通过调节蒸发物的数量和时间以及基片和蒸发源的相对位置来控制。
令d0为刚好在蒸发源正上方的基片上沉积的厚度,d是任意位置的厚度,则点蒸发源和微小平面蒸发源相对厚度分布用下式表示:(点源)(8.2-5) (面源)(8.2-6)d/d 0和x/h 的关系曲线见图8.2-2。
(6)真空热蒸镀的基本工艺流程本实验采用真空热蒸镀法蒸镀金属或介质膜,其基本工艺流程图见图8.2-3。
其中离子轰击,又名辉光放电,进行时,真空室内电子获得很高速度,较之带正电的气体离子更高。
在镀件周围,因电子较大的迁移率,而迅速带有负电荷,在表面负电荷吸引力作用下,正离子轰击镀件表面,并可能在其上进行能量交换。
由于能量在污染表面被释放出来,故有洁净的功能,不仅能除去吸附气体层,还可除去表面氧化物。
利用离子轰击,还可粗略估计真空度。
烘烤的作用是可以加速镀件或夹具吸附气体的迅速逸出,有利于提高真空度,还可以提高膜层结合力。
预熔的作用是除去蒸发材料中的低熔点杂质以及蒸发源和材料中的吸附气体,有利于蒸发材料的顺利蒸发。
2.真空离子镀及真空阴极溅射镀真空离子镀可采用与真空热蒸镀相同的蒸发方式,只是在蒸发原子到达镀件表面前必须采取一定措施,让其离子化,同时可给镀件施加负偏压。
由此,镀件表面不断受到离子的轰击能提高膜层的结合力。
离子镀的缺点是,膜层的沉积速率下降。
要提高沉积速度,可增设电子发射电源,提高电子浓度,使之更易放电或减少镀件的自偏电压。
与真空热蒸镀相比,膜层厚度均匀,结合力好。
真空阴极溅射镀一般是导入一定量的氩气使之辉光放电,带正电子的氩离子轰击阴极,构成阴极的原子被溅射蒸镀到镀件表面形成膜层。
溅射出的原子,其膜的生成速度取决于溅射率和轰击氩气的流速,一般它比真空热蒸镀和离子镀的速度小得多,为,而热蒸镀和离子镀的沉积速度为。
3.几种光学薄膜的光学特性(1)单层介质膜的光学特性设入射光的振幅为1(图8.2-4),在n 0至n 1界面上反射所形成的反射光1的振幅为r 01,而透射光为t 01,该光再经n 1至n s 界面的反射及由n 1至n 0界面的透射而形成的反射光2,其振幅显然是t 01r 12t 10,同样可得其它各反射光3、4、…、m 的振幅分别为、…等。
此外将反射光1与2相比知,任意两相邻反射光由于光程差引起的位相差为:(8.2-7)其中:λ0为光在真空中的波长,θ1为折射角。
由于各光波是相干的,它们叠加后的合振幅为[]2/320)/(11h x d d +=[]220)//(11h x d d =min /1000025 A ~min /250000100A ~102121001t r t t 2103121001r r t t 1101121001--m m r r t t 1110cos 4θλπδd n=(8.2-8)由于,则 (8.2-9)单层膜的反射率为(8.2-10) 将相应的菲涅尔系数代入上式,则单层膜的反射率又可写成(8.2-11) 下面来确定反射率为极值时的光学厚度H =n 1d 1。
令dR dH =0,可求得当时,有极值。
①当k为奇数(在正入射)时,即H 值是下列数值中的任何一个:(8.2-12)②当k为偶数(在正入射)时,即H 值是下列数值中的任何一个: (8.2-13)和所镀膜的折射率无关。
单层介质膜的反射率随其光学厚度的变化关系见图8.2-5。
δδδδδδi i m i m m i i i e r r e r t t r e r r t t e r r t t e r r t t e r t t r r ----------+=++++++=1210120101)1(21011210013210312100121031210011210010111010012012101001111r r r r t t +=-=-=δδi i e r r e r r r --++=120112011δδcos 21cos 212012122011201212201*r r r r r r r r rr R ++++==2sin 2cos )(2sin 2cos )(2211022022110220δδδδ⎪⎪⎭⎫ ⎝⎛+++⎪⎪⎭⎫ ⎝⎛-+-=n n n n n n n n n n n n R s s s s ,45,43,4000λλλ=H ⎩⎨⎧><>>=⎪⎪⎭⎫ ⎝⎛+-=01max 01min 2210210n n n R n n n R n n n n n n R s s s s 如果如果 ,46,44,42000λλλ=H ⎩⎨⎧><>>=⎪⎪⎭⎫ ⎝⎛+-=01min 01max 200n n n R n n n R n n n n R s s s s 如果如果(2)增透膜的光学特性由单层介质膜的光学特性可知,若所镀膜层折射奇数倍率n1小于基底折射率n s,则当膜层光学厚度为λ04时,反射率在给定波长λ0处有极小值,即透射率极大,且满足式(8.2-12),可藉此做增透膜。