汽车制造工艺学-第三版-期末复习总结
汽车制造工艺学复习资料
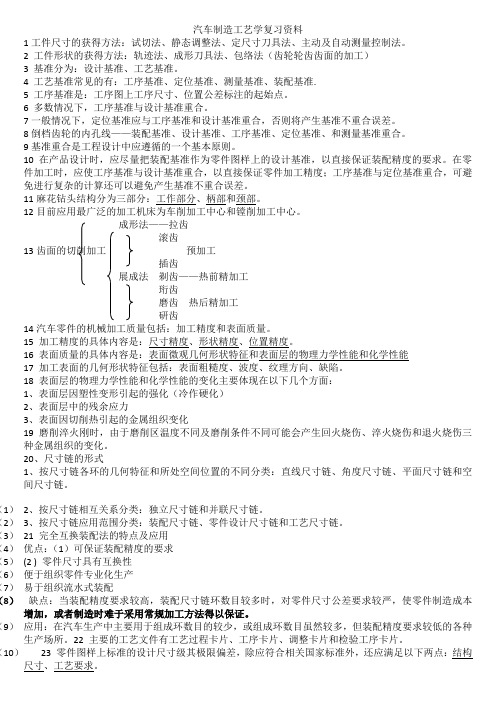
汽车制造工艺学复习资料1工件尺寸的获得方法:试切法、静态调整法、定尺寸刀具法、主动及自动测量控制法。
2 工件形状的获得方法:轨迹法、成形刀具法、包络法(齿轮轮齿齿面的加工)3 基准分为:设计基准、工艺基准。
4 工艺基准常见的有:工序基准、定位基准、测量基准、装配基准.5 工序基准是:工序图上工序尺寸、位置公差标注的起始点。
6 多数情况下,工序基准与设计基准重合。
7一般情况下,定位基准应与工序基准和设计基准重合,否则将产生基准不重合误差。
8倒档齿轮的内孔线——装配基准、设计基准、工序基准、定位基准、和测量基准重合。
9基准重合是工程设计中应遵循的一个基本原则。
10 在产品设计时,应尽量把装配基准作为零件图样上的设计基准,以直接保证装配精度的要求。
在零件加工时,应使工序基准与设计基准重合,以直接保证零件加工精度;工序基准与定位基准重合,可避免进行复杂的计算还可以避免产生基准不重合误差。
11麻花钻头结构分为三部分:工作部分、柄部和颈部。
12目前应用最广泛的加工机床为车削加工中心和镗削加工中心。
成形法——拉齿滚齿13齿面的切削加工预加工插齿展成法剃齿——热前精加工珩齿磨齿热后精加工研齿14汽车零件的机械加工质量包括:加工精度和表面质量。
15 加工精度的具体内容是:尺寸精度、形状精度、位置精度。
16表面质量的具体内容是:表面微观几何形状特征和表面层的物理力学性能和化学性能17 加工表面的几何形状特征包括:表面粗糙度、波度、纹理方向、缺陷。
18 表面层的物理力学性能和化学性能的变化主要体现在以下几个方面:1、表面层因塑性变形引起的强化(冷作硬化)2、表面层中的残余应力3、表面因切削热引起的金属组织变化19 磨削淬火刚时,由于磨削区温度不同及磨削条件不同可能会产生回火烧伤、淬火烧伤和退火烧伤三种金属组织的变化。
20、尺寸链的形式1、按尺寸链各环的几何特征和所处空间位置的不同分类:直线尺寸链、角度尺寸链、平面尺寸链和空间尺寸链。
汽车制造工艺-期末复习与总结

期末复习与总结一、判断题:(83)一)工序、安装、工步、走刀(10)1、在一道工序中只能有一次安装;(×)2、一组工人在同一个工作地点加工一批阶梯轴,先车好一端,然后调头再车这批轴的另一端,即使在通一台车床上加工,也应算作两道工序。
(×)3、用同一把外圆车刀分三次车削阶梯轴的同一个台阶,因切削用量变化,故称为三个工步;(×)4、一组工人在一个工作地点同时对几个工件连续进行加工,只能算作一道工序。
(√)5、生产纲领是指企业在计划期内应当生产的产品产量和进度计划。
(√)6、在加工表面、切削刀具和切削用量不变的情况下,所连续完成的那一部分称为工步。
(×)7、汽车制造企业试制车间的生产属于单件生产。
(√)8、重型货车和特种车辆多为中批生产。
(√)9、一道工序只能在一台设备上完成。
(√)10、因为一道工序可有多次安装,一次安装可有多个工步,一个工步可有多次走刀,因此工艺过程的最基本单元是走刀。
(×)二)基准(22)1、加工高精度表面时所用的定位基准称为精基准; (× )2、因为球心、轴线等是看不见摸不着的,他们客观上并不存在,所以只能以球面和圆柱面为定位基准。
(× )3、所谓基准统一原则就是选择定位基准是应尽可能统一选用某一个表面既作为粗基准又作为精基准原则; (× )4、所谓基准重合原则就是工序基准、定位基准、测量基准必须重合。
( ×)5、当某些精加工加工余量小且余量均匀时,可以选择加工表面本身作为定位基准。
( √ )6、机械制造过程中,加工工件和装配机器时所采用的各种基准,称为工艺基准。
√7、定位基准是用以确定加工表面与刀具相互关系的基准。
(√)8、测量基准只限于测量工件各表面的相互位置。
( × )9、测量工件形状和尺寸时通常不需要基准。
(× )10、装配时用来确定零件或部件在产品中的相对位置所采用的基准,称为定位基准。
汽车制造工艺学复习
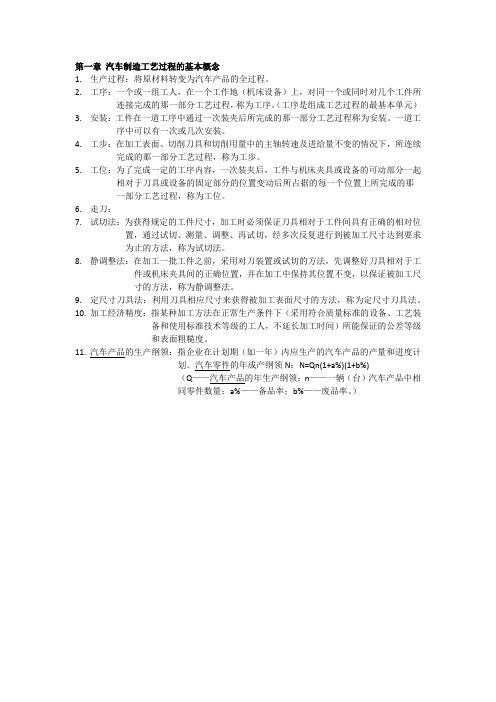
第一章汽车制造工艺过程的基本概念1.生产过程:将原材料转变为汽车产品的全过程。
2.工序:一个或一组工人,在一个工作地(机床设备)上,对同一个或同时对几个工件所连接完成的那一部分工艺过程,称为工序。
(工序是组成工艺过程的最基本单元)3.安装:工件在一道工序中通过一次装夹后所完成的那一部分工艺过程称为安装。
一道工序中可以有一次或几次安装。
4.工步:在加工表面、切削刀具和切削用量中的主轴转速及进给量不变的情况下,所连续完成的那一部分工艺过程,称为工步。
5.工位:为了完成一定的工序内容,一次装夹后,工件与机床夹具或设备的可动部分一起相对于刀具或设备的固定部分的位置变动后所占据的每一个位置上所完成的那一部分工艺过程,称为工位。
6.走刀:7.试切法:为获得规定的工件尺寸,加工时必须保证刀具相对于工件间具有正确的相对位置,通过试切、测量、调整、再试切,经多次反复进行到被加工尺寸达到要求为止的方法,称为试切法。
8.静调整法:在加工一批工件之前,采用对刀装置或试切的方法,先调整好刀具相对于工件或机床夹具间的正确位置,并在加工中保持其位置不变,以保证被加工尺寸的方法,称为静调整法。
9.定尺寸刀具法:利用刀具相应尺寸来获得被加工表面尺寸的方法,称为定尺寸刀具法。
10.加工经济精度:指某种加工方法在正常生产条件下(采用符合质量标准的设备、工艺装备和使用标准技术等级的工人,不延长加工时间)所能保证的公差等级和表面粗糙度。
11.汽车产品的生产纲领:指企业在计划期(如一年)内应生产的汽车产品的产量和进度计划。
汽车零件的年成产纲领N:N=Qn(1+a%)(1+b%)(Q——汽车产品的年生产纲领;n——一辆(台)汽车产品中相同零件数量;a%——备品率;b%——废品率。
)第二章整车企业典型制造工艺1.冲压工艺及其特点冲压是利用冲模使板料产生分离或变形的加工方法。
优点:(1)在模具的作用下,可以批量获得精度高度一致的产品,提高零件制造的互换性,易于组织后续制造工艺;(2)材料利用率高,可冲压形状复杂的零件;(3)冲压产品具有足够高的精度和较低的表面粗糙度;(4)能够在结构和工艺条件允许情况下,获得较高强度和刚度的零件;(5)冲压操作简单,工艺过程便于机械化和自动化,生产率很高,故零件成本低。
汽车制造工艺学期末复习知识点

汽车制造工艺学期末复习知识点1.汽车制造装备分为整车制造装备和零部件制造装备两大类。
2.整车制造的“四大工艺装备”是指整车自动装配线、车身焊接和装配生产线、喷涂生产线、冲压生产线。
3.激光加工设备:包括激光切割设备、激光焊接设备。
4.汽车生产的工艺过程:工序、安装、工位、工步、走刀。
5.生产类型是指企业(或车间、工段、班组、工作地)生产专业化程度的分类。
一般分为大量生产、成批生产和单件生产三种类型。
6.汽车铸件特性的主要要求是:铸件形状复杂,常需使用砂芯;尺寸精度高;采用薄壁铸件以减小质量;材质稳定;具有足够的耐压性和抗压性。
7.习惯上将铸造分为砂型铸造和特种铸造两大类。
汽车铸件生产中,砂型铸造所生产的铸件占整个汽车铸件的90%以上。
8.金属型铸造:金属型分为整体式、垂直分形式、水平分形式和复合分形式。
9.选择分型面:应尽量使铸件位于同一铸型内;尽量减少分型面;尽量使分型面平直;尽量使型腔和主要型芯位于下砂箱。
10.铸件结构工艺性:铸件壁厚要合理;铸件壁厚要均匀;铸件内壁应薄于外壁;铸件壁链接要合理;避免铸件收缩受阻;防止铸件翘曲变形。
11.锻造按所用工具与模具的安置情况的不同可分为自由锻、胎膜锻、摸锻等类型;按模锻加工可分为温度热锻、温锻、冷锻、等温锻等类型。
12.根据作用与变形要求不同,自由锻的工序分为基本工序、铺助工序和精整工序三类。
13.焊接的分类方法很多,若按焊接过程中金属所处的状态不同,可把焊接方法分为熔焊、压焊和钎焊三大类。
14.焊接结构件种类各式各样,在其材料确定以后,对焊接结构件进行工艺设计主要包括三方面内容:焊缝布置、焊接方法选择和焊接接头设计等。
15.板料冲压的基本工序有冲裁、弯曲、拉深、成形等。
16.冲裁是使板料沿封闭的轮廓线分离的工序,包括冲孔和落料。
17.在切削加工形成零件需要表面的全过程中,刀具和工件间的相对运动,按作用的不同分为切削运动和铺助运动。
18.常用刀具标注角度参考系有正交平面参考系、法平面参考系和假定工作平面参考系三种。
汽车制造工艺学复习资料
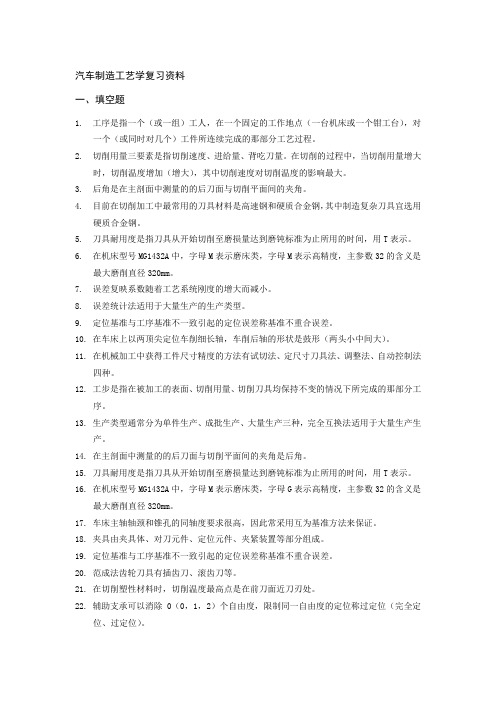
汽车制造工艺学复习资料一、填空题1.工序是指一个(或一组)工人,在一个固定的工作地点(一台机床或一个钳工台),对一个(或同时对几个)工件所连续完成的那部分工艺过程。
2.切削用量三要素是指切削速度、进给量、背吃刀量。
在切削的过程中,当切削用量增大时,切削温度增加(增大),其中切削速度对切削温度的影响最大。
3.后角是在主剖面中测量的的后刀面与切削平面间的夹角。
4.目前在切削加工中最常用的刀具材料是高速钢和硬质合金钢,其中制造复杂刀具宜选用硬质合金钢。
5.刀具耐用度是指刀具从开始切削至磨损量达到磨钝标准为止所用的时间,用T表示。
6.在机床型号MG1432A中,字母M表示磨床类,字母M表示高精度,主参数32的含义是最大磨削直径320mm。
7.误差复映系数随着工艺系统刚度的增大而减小。
8.误差统计法适用于大量生产的生产类型。
9.定位基准与工序基准不一致引起的定位误差称基准不重合误差。
10.在车床上以两顶尖定位车削细长轴,车削后轴的形状是鼓形(两头小中间大)。
11.在机械加工中获得工件尺寸精度的方法有试切法、定尺寸刀具法、调整法、自动控制法四种。
12.工步是指在被加工的表面、切削用量、切削刀具均保持不变的情况下所完成的那部分工序。
13.生产类型通常分为单件生产、成批生产、大量生产三种,完全互换法适用于大量生产生产。
14.在主剖面中测量的的后刀面与切削平面间的夹角是后角。
15.刀具耐用度是指刀具从开始切削至磨损量达到磨钝标准为止所用的时间,用T表示。
16.在机床型号MG1432A中,字母M表示磨床类,字母G表示高精度,主参数32的含义是最大磨削直径320mm。
17.车床主轴轴颈和锥孔的同轴度要求很高,因此常采用互为基准方法来保证。
18.夹具由夹具体、对刀元件、定位元件、夹紧装置等部分组成。
19.定位基准与工序基准不一致引起的定位误差称基准不重合误差。
20.范成法齿轮刀具有插齿刀、滚齿刀等。
21.在切削塑性材料时,切削温度最高点是在前刀面近刀刃处。
汽车制造工艺学总结
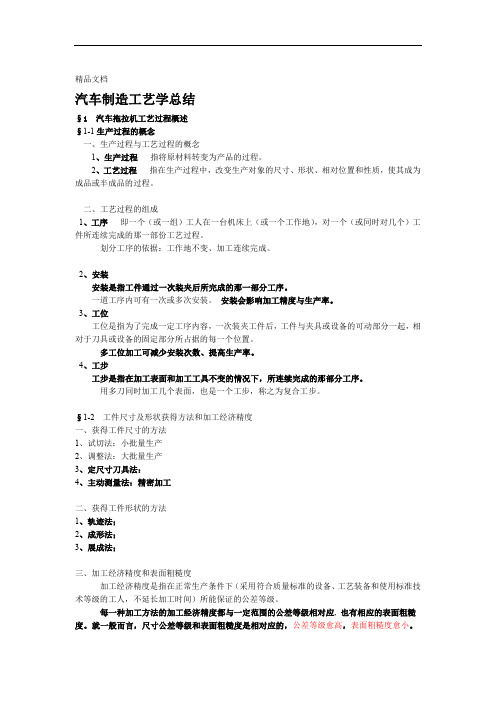
精品文档汽车制造工艺学总结§1 汽车拖拉机工艺过程概述§1-1生产过程的概念一、生产过程与工艺过程的概念1、生产过程指将原材料转变为产品的过程。
2、工艺过程指在生产过程中,改变生产对象的尺寸、形状、相对位置和性质,使其成为成品或半成品的过程。
二、工艺过程的组成1、工序即一个(或一组)工人在一台机床上(或一个工作地),对一个(或同时对几个)工件所连续完成的那一部份工艺过程。
划分工序的依据:工作地不变、加工连续完成。
2、安装安装是指工件通过一次装夹后所完成的那一部分工序。
一道工序内可有一次或多次安装。
安装会影响加工精度与生产率。
3、工位工位是指为了完成一定工序内容,一次装夹工件后,工件与夹具或设备的可动部分一起,相对于刀具或设备的固定部分所占据的每一个位置。
多工位加工可减少安装次数、提高生产率。
4、工步工步是指在加工表面和加工工具不变的情况下,所连续完成的那部分工序。
用多刀同时加工几个表面,也是一个工步,称之为复合工步。
§1-2 工件尺寸及形状获得方法和加工经济精度一、获得工件尺寸的方法1、试切法:小批量生产2、调整法:大批量生产3、定尺寸刀具法:4、主动测量法:精密加工二、获得工件形状的方法1、轨迹法;2、成形法;3、展成法;三、加工经济精度和表面粗糙度加工经济精度是指在正常生产条件下(采用符合质量标准的设备、工艺装备和使用标准技术等级的工人,不延长加工时间)所能保证的公差等级。
每一种加工方法的加工经济精度都与一定范围的公差等级相对应, 也有相应的表面粗糙度。
就一般而言,尺寸公差等级和表面粗糙度是相对应的,公差等级愈高,表面粗糙度愈小。
但是,加工经济精度对应的公差等级并不是一成不变的;它将随着机械加工水平的不断提高、设备和工艺装备的改进而逐渐提高。
§1-3 生产类型与工艺特征一、生产纲领与生产类型(一)生产纲领指企业计划期内应当生产的产品产量和年度计划。
精品文档.精品文档(二)生产类型1、生产类型的概念生产类型,是指企业(或车间、工段、班组、工作地)生产专业化程度的分类。
汽车制造工艺学考点整理

l −l பைடு நூலகம் l0
。
2、均匀延伸率:指试样在拉伸试验中,达到强度极限,即试样开始出现局部颈缩时的延伸 率。 Ch1: 1、 冲裁是指冲压分离工序, 板料受力是从弹性变形开始, 经过塑性变形, 以断裂分离结束。 2、 冲裁分为哪几个阶段: (1)弹性变形阶段 凸模接触板料后,开始向下压缩材料,使材料产生弹性压缩和弯曲变形。板料与 凸模和凹模的接触处形成很小的圆角。随着凸模的继续压入,材料的内应力达到弹性极 限。此时,凸模下的材料略有弯曲,凹模上的材料则向上翘。 (2)塑性变形阶段 当凸模继续下行、材料的内应力达到屈服极限时,材料除了有剪切变形外,还同 时伴有弯曲和拉伸变形。 随着凸模挤入材料的深度逐渐增大, 即塑性变形程度逐渐增大。 材料内部的拉应力和弯矩也都增大,变形区材料硬化加剧。直至凸、凹模刃口附近的材 料应力集中,在拉应力作用下出现裂纹时,塑性变形阶段即告结束。此时冲裁变形力达 到最大值。 (3)断裂分离阶段 断裂分离阶段从材料在模具刃口附近出现微裂纹开始。随着凸模继续压下,已形 成的上、下两面的微裂纹逐渐扩大,并向材料内延伸。当上下两条裂纹相遇重合时,材 料便被剪断分离。 3、 冲裁断面的区域性特征:塌角、光亮带、剪裂带和毛刺等四个部分。 塌角:在凸模压入材料时,刃口附近的材料被牵连拉入变形而形成。 光亮带:表面光滑,表面质量最佳,它是在塑性变形过程中由凹、凸模挤压切入材料所 形成的。 剪裂带:表面较粗糙,带斜度而不与板平面垂直.它是材料剪断分离时所形成的。 毛刺:材料出现微裂纹时形成,随凸模的下行被拉长,并残留在冲裁件上。 4、冲裁模间隙 Z:指凸、凹模之间的间隙,其对冲裁件的质量影响极大,同时影响:冲裁 力、模具寿命。 1、 对冲裁件质量的影响 1)对冲裁件断面的影响 冲裁模间隙较大时,材料中的拉应力也较大,容易产生裂纹,塑性变形阶段结束 较早,因此光亮带较小,而剪裂带、塌角和毛刺都较大,冲裁件的翘曲也较显著。 间隙较小,情况刚好相反。 间隙过大或过小均导致上、下两面的剪裂纹不能相交重合于一线。 2)对冲裁件尺寸精度的影响(受拉,回弹收缩;受挤,恢复伸张) 冲裁模间隙较大时,材料受拉伸作用大,冲裁后材料的弹性恢复也较大,因此,使 落料尺寸小于凹模尺寸,冲孔孔径大于凸模直径。另一方面,冲裁模间隙较大使翘曲严重,
汽车制造工艺学期末考试重点
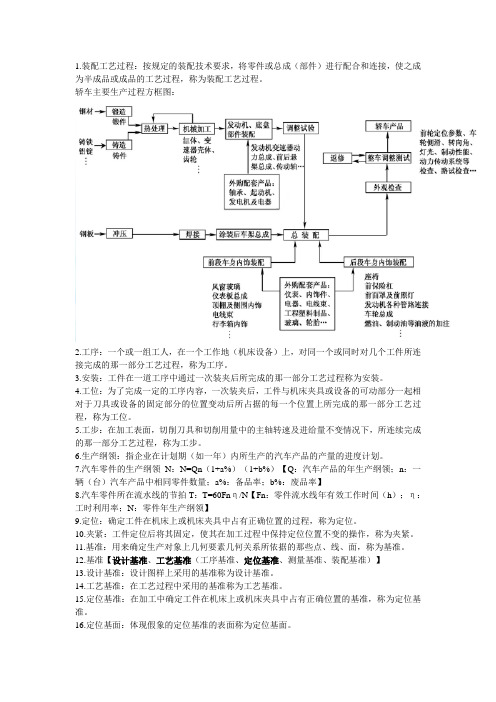
1.装配工艺过程:按规定的装配技术要求,将零件或总成(部件)进行配合和连接,使之成为半成品或成品的工艺过程,称为装配工艺过程。
轿车主要生产过程方框图:2.工序:一个或一组工人,在一个工作地(机床设备)上,对同一个或同时对几个工件所连接完成的那一部分工艺过程,称为工序。
3.安装:工件在一道工序中通过一次装夹后所完成的那一部分工艺过程称为安装。
4.工位:为了完成一定的工序内容,一次装夹后,工件与机床夹具或设备的可动部分一起相对于刀具或设备的固定部分的位置变动后所占据的每一个位置上所完成的那一部分工艺过程,称为工位。
5.工步:在加工表面,切削刀具和切削用量中的主轴转速及进给量不变情况下,所连续完成的那一部分工艺过程,称为工步。
6.生产纲领:指企业在计划期(如一年)内所生产的汽车产品的产量的进度计划。
7.汽车零件的生产纲领N:N=Qn(1+a%)(1+b%)【Q:汽车产品的年生产纲领;n:一辆(台)汽车产品中相同零件数量;a%:备品率;b%:废品率】8.汽车零件所在流水线的节拍T:T=60Fnη/N【Fn:零件流水线年有效工作时间(h);η:工时利用率;N:零件年生产纲领】9.定位:确定工件在机床上或机床夹具中占有正确位置的过程,称为定位。
10.夹紧:工件定位后将其固定,使其在加工过程中保持定位位置不变的操作,称为夹紧。
11.基准:用来确定生产对象上几何要素几何关系所依据的那些点、线、面,称为基准。
12.基准【设计基准、工艺基准(工序基准、定位基准、测量基准、装配基准)】13.设计基准:设计图样上采用的基准称为设计基准。
14.工艺基准:在工艺过程中采用的基准称为工艺基准。
15.定位基准:在加工中确定工件在机床上或机床夹具中占有正确位置的基准,称为定位基准。
16.定位基面:体现假象的定位基准的表面称为定位基面。
17.定位误差:指由于定位的不准确性原因使工件工序基准偏离理想位置,引起工序尺寸变化的加工误差。
大学汽车制造工艺学复习资料

大学汽车制造工艺学复习资料汽车制造工艺学复习资料(加工质量)1.什么是工序、安装、工位、工步、走刀?工序:一个(组)工人,在一台机床(某个地方),对一个(多个)工件所连续完成那部分工艺过程。
安装:工件通过一次装夹后所完成的那一部分工序。
工位:一次安装内,工件在机床上所占的每一个位置。
工步:在加工表面、加工工具、切削用量中的转速、进给量不变的情况下,所连续完成的那一部分工序。
走刀:在一个工步内,由于有些表面加工余量太大,需用同一把刀具以及同一切削用量对其多次切削。
这样的每一次切削就称为一次走刀。
2.说明加工精度、加工误差、公差的概念及区别。
加工精度:零件在加工以后的几何参数(尺寸、形状和位置)的实际值与理想值的符合程度。
加工精度包括:(1)尺寸精度(2)形状精度(3)位置精度加工误差:零件加工后的几何参数的实际值与理想值的偏离程度。
公差:实际参数的允许变动量。
区别:加工精度和加工误差都是从不同的角度在描述误差,但是加工误差的大小由零件的实际测量的偏离量来衡量,而加工精度的高低由公差等级或者公差值来衡量,并由加工误差的大小来控制。
一般来说,只有加工误差小于公差时才能保证加工精度。
3.加工质量的两大指标是?加工精度:尺寸精度、形状精度、位置精度。
表面质量:1、表面微观几何形状特征:1)表面粗糙度2)波度3)纹理方向4)缺陷2、表面物理、化学性能:1)冷作硬化2)残余应力3)金相组织变化4.何为原始误差,他与加工误差有何关系?原始误差:工艺系统本身的误差。
原始误差通过加工过程直接反映到工件上就成为加工误差。
5.原始误差包括哪些内容?1、机床误差2、刀具误差3、工艺系统受力变形引起的加工误差4、工艺系统热变形引起的加工误差5、工件残余应力引起的加工误差6.车床导轨误差怎么影响加工精度?水平面内的直线度误差:在纵向切削过程中,刀尖的运动轨迹相对工件轴线之间的距离会发生变化,引起工件半径的尺寸变化,即产生圆柱度误差。
汽车制造工艺学复习
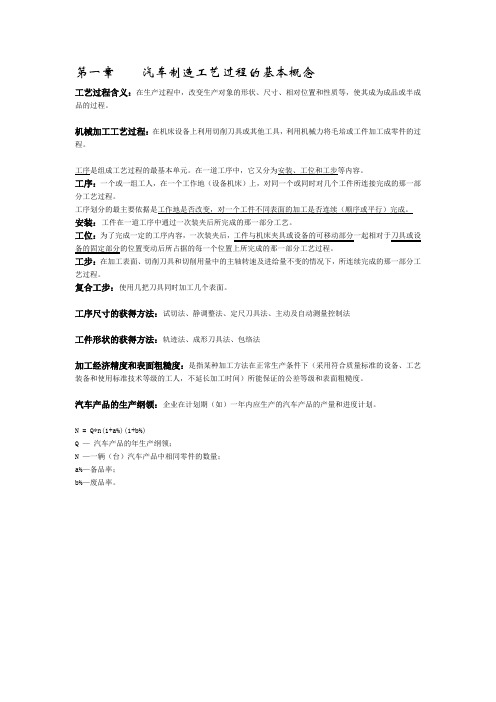
第一章汽车制造工艺过程的基本概念工艺过程含义:在生产过程中,改变生产对象的形状、尺寸、相对位置和性质等,使其成为成品或半成品的过程。
机械加工工艺过程:在机床设备上利用切削刀具或其他工具,利用机械力将毛培或工件加工成零件的过程。
工序是组成工艺过程的最基本单元。
在一道工序中,它又分为安装、工位和工步等内容。
工序:一个或一组工人,在一个工作地(设备机床)上,对同一个或同时对几个工件所连接完成的那一部分工艺过程。
工序划分的最主要依据是工作地是否改变,对一个工件不同表面的加工是否连续(顺序或平行)完成。
安装:工件在一道工序中通过一次装夹后所完成的那一部分工艺。
工位:为了完成一定的工序内容,一次装夹后,工件与机床夹具或设备的可移动部分一起相对于刀具或设备的固定部分的位置变动后所占据的每一个位置上所完成的那一部分工艺过程。
工步:在加工表面、切削刀具和切削用量中的主轴转速及进给量不变的情况下,所连续完成的那一部分工艺过程。
复合工步:使用几把刀具同时加工几个表面。
工序尺寸的获得方法:试切法、静调整法、定尺刀具法、主动及自动测量控制法工件形状的获得方法:轨迹法、成形刀具法、包络法加工经济精度和表面粗糙度:是指某种加工方法在正常生产条件下(采用符合质量标准的设备、工艺装备和使用标准技术等级的工人,不延长加工时间)所能保证的公差等级和表面粗糙度。
汽车产品的生产纲领:企业在计划期(如)一年内应生产的汽车产品的产量和进度计划。
N = Q*n(1+a%)(1+b%)Q —汽车产品的年生产纲领;N —一辆(台)汽车产品中相同零件的数量;a%—备品率;b%—废品率。
第二章工件的装夹和机床夹具定位:确定工件在机床上或机床夹具中占有正确位置的过程。
夹紧:工件定位后将其固定,使其在加工过程中保持定位位置不变的操作。
装夹:将工件在机床上或机床夹具中定位、夹紧的过程。
工艺基准包括:工序基准、定位基准、测量基准、装配基准。
工序基准:在工序图上用来确定本道工序被加工件表面加工尺寸、位置公差的基准,工序尺寸:联系加工表面和工序基准间的加工尺寸,是本道工序应直接保证的尺寸。
汽车制造工艺 期末复习重点
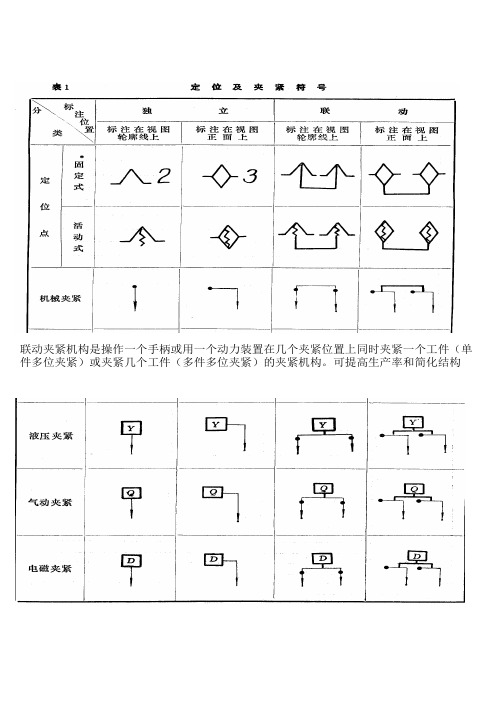
件多位夹紧)或夹紧几个工件(多件多位夹紧)的夹紧机构。
可提高生产率和简化结构表1-9 定位及夹紧符号(续)汽车制造工艺学一、填空题1. 主轴回转作纯径向跳动及漂移时,所镗出的孔是_椭圆__形。
2. 零件的加工质量包括_加工精度_和_加工表面质量__。
3. 零件光整加工的通常方法有_珩磨_、研磨、超精加工及_抛光_等方法。
4. 机械加工工艺规程实际上就是指规定零件机械加工工艺过程和操作方法等的_工艺文件5. 工艺过程是指生产过程中,直接改变生产对象形状、尺寸、相对位置、及性质的过程。
6. 零件的几何(尺寸,形状,位置)精度、表面质量、物理机械性能是评定机器零件质量的主要指标。
7. 加工经济精度是指在正常加工条件下(采用符合标准的设备,工艺装备和标准技术等级的工人,不延长加工时间)所能保证的加工精度。
8. 轴类零件加工中常用两端中心孔作为统一的定位基准。
9. 零件的加工误差指越小(大),加工精度就越高(低)。
10. 10.粗加工阶段的主要任务是获得高的生产率。
11.精加工阶段的主要任务是使各主要表面达到图纸规定的质量要求。
12.工艺系统的几何误差包括加工方法的原理误差、制造和磨损所产生的机床几何误差和传动误差,调整误差、刀具、夹具和量具的制造误差、工件的安装误差。
13. 13.零件的加工误差值越小(大),加工精度就越高(低)。
14.机械产品的质量可以概括为__实用性____、可靠性和__经济性____三个方面。
15.通过切削加工方法获得工件尺寸的方法有试切法、静调整法、_定尺寸刀具法__、主动及自动测量控制法16、表面质量:是指机械加工后零件表面的状况。
17、形状精度:是指零件表面或线的实际形状与理想形状的接近程度。
18、工艺系统:在机械加工时,机床、机床夹具、刀具和工件形成了一个完整的加工系统。
粗基准:用未经加工过的表面作为定位基准称为粗基准。
19、工艺系统刚度:在外力作用下,工艺系统抵抗变形的能力。
汽车制造工艺学复习重点汇总
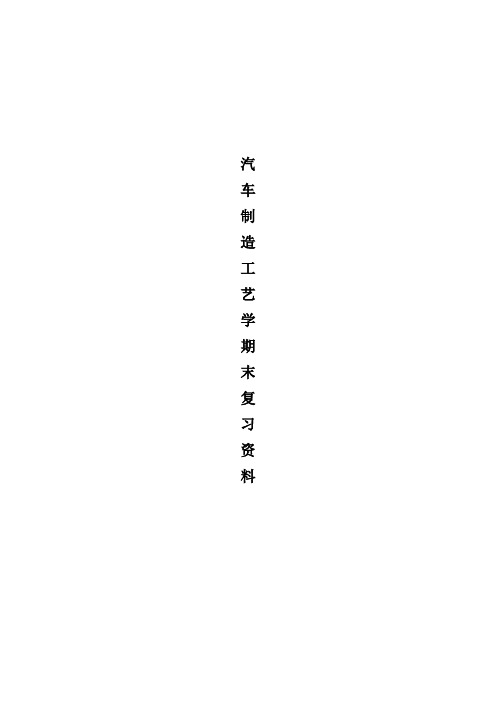
尺寸链:由相互连接的尺寸形成的封闭尺寸组,称为尺寸链。
尺寸链中的每一个尺寸或位置公差,简称为环。
尺寸链包括组成环和封闭环,组成环是对封闭环有影响的全部环,封闭环是在装配和加工过程中间接获得的环。
增环:指该环的变化引起封闭环作同向变化的组成环、即该环增大(减小)时,封闭环也随之增大(减小)。
定位误差:由于定位的不准确原因是工件工序偏离理想位置,引起工序尺寸变化的加工误差。
定位误差
夹紧装置的组成:力源装置、夹紧元件、中间传力机构
夹紧力作用方向选择原则: 夹紧力的方向应垂直于主要定位基面,以保证加工精度; 夹紧力方向应与工件刚度最大的方向一致,以减小工件的夹紧变形; 夹紧力方向应尽量与切削力、重力等力方向一致,以减小夹紧力。
生产节拍/min
大量生产
1~2
5以下
大批生产
2~10
5~15Hale Waihona Puke 中批生产10~20
15~60
小批生产
20~40
60以上
大量生产:一台机床设备上常年进行某一零件的某1~2个固定工序内容的加工,这样的生产类型称为大量生产。
单件生产:每台机床设备上常年不重复或很少重复制造同一种零件或进行相同工序内容的加工,这样的生产类型称之为单件生产。
机械加工工序卡片:在卡片上绘有工序简图,图上注明定位基准符号、各加工表面的工序尺寸、表面粗糙度和其他技术要求等,并详细写明各工步的顺序和内容、使用的设备及工艺装备,以及规定的切削用量和时间定额等;它是用以指导操作工人进行生产的文件。
调整卡片:是对自动、半自动机床或某些齿轮加工机床等进行调整用的一种工艺文件;调整卡片的格式因机床而异。
汽车制造工艺学复习整理1.doc

汽车制造工艺学汽车制造工艺过程中的基本概念工艺过程:是指在生产过程中,改变生产对象的形状、尺寸、相对位置和性质等,使其成为成品或半成品的过程。
生产过程指将原材料转变为产品的过程。
机械加工工艺过程:在机床设备上利用切削刀具或其它工具易用机械力将毛坯或工件加工成零件的过程。
工序:一个或一组工人在一个机床设备上对同一个或同时对几个工件所连续完成那一部分工艺过程。
工序是组成工艺过程的最基本单元安装:同一道工序中,零件在加工位置上装夹一次所完成的那一部分工序。
P4 工位:零件在每个位置上完成的那一部分加工过程。
P4 工步:在一次安装中,在加工表面、加工刀具、切屑用量不变的情况下,所连续完成的那一部分工艺过程。
几把刀同时加工几个表面叫(一个)复合工步工件尺寸的获得方法①试切法:通过试切、测量、调整、再试切,经多次反复进行到被加工尺寸达到要求为止的方法适用于单件货几件工件的加工②静调整法:在加工一批工件之前,采用对刀装置或试切的方法,先调整好刀具相对于工件或机床夹具间的正确位置,并在加工中保持其位置不变,以保证被加工尺寸的方法适合产量较大的场合广泛用于半自动机床和自动线上的生产;③定尺寸刀具法:利用刀具相应尺寸来获得被加工表面尺寸的方法适用于孔沟槽等表面的加工适用于各种产量的场合;④主动及自动测量控制法;在加工过程中,利用测量装置、进给机构及控制系统保证被加工表面尺寸的方法产量大的汽车制造企业。
工件形状的获得方法①轨迹法:依靠刀具运动轨迹来获得所需工件形状的方法用于产量较大较大工件形状较为复杂的零件形状的切削加工;②成型刀具法:使用成形刀具获得工件形状的方法生产率高;③包络法;在刀具与工件相对运动过程中,由刀具切削刃连续运动的轨迹包络成工件形状的方法加工经济精度:是指某种加工方法在正常生产条件下不延长加工时间所能保证的公差等级和表面粗糙度。
P83 •汽车零件表面的尺寸公差与表面粗糙度具有何种关系?答: 一般被加工表面的尺寸公差值小表面粗糙度值也一定较小o但是有些被加工表面要求的表面糙度值较小不一定尺寸公差值也必须小。
汽车制造工艺学复习总结

第一章汽车制造过程概论1.工艺过程:改变原材料(或毛坯)的形状、尺寸、相对位置和材料性能,使其成为成品或半成品的那部分过程。
包括铸造、锻造、热处理、机械加工和装配等工艺过程。
2机械加工工艺过程:工序、安装、工位、工布、走刀工序:工艺过程的基本组成单元,指一个(或一组)工人在一台设备上对一个或同时对几个零件所连续完成的那一部分加工过程。
区分的依据:分析零件加工过程中工作的场地或设备是否发生变化,加工过程是否连续。
供需划分的好处:1、零件表面具有不同的形状、精度,这些工件不可能在一台机床上加工完成。
2、可以提高生产率降低生产成本。
安装:同一道工序中,零件在加工位置上装夹一次所完成的那一部分工序。
同一工序中为了提高生产效率和零件位置精度,应尽量减少安装次数。
工位:零件在每个位置上完成的那一部分加工过程。
多工位零件加工方法减少了安装次数,提高了生产效率,特别适合汽车零件的加工。
工步:零件在一次安装中,在加工表面、加工刀具、切削用量(转速及进给量)不变的情况下所连续完成的那一部分工序。
复合工步,在一次安装条件下,利用多个刀具同时加工多个待加工表面,作为一个工步(提高生产效率)。
走刀:零件一次安装后,在一个工步内,被加工表面余量较大时,需要进行多次切削,每次称为一次走刀。
3生产纲领:一个汽车制造厂根据市场需要,销售和本企业生产能力制定的年产量和进度计划就是该厂的生产纲领T。
对于汽车零件的生产车间或协作厂的生产纲领P=Tμ(1+α)(1+β)μ:每台汽车中的该零件的所需量α:批次中备件的百分率β:废品百分率4.汽车产品的销售与工厂的能力→工厂的生产纲领→生产类型(生产规模)5.生产类型;单件生产,成批生产,大量生产单件生产:一台或少量,不重复或很少重复。
通用设备,组合夹具成批生产:小批生产,中批生产,大批生产,成批的,周期性的大量生产:重复的专用机床。
第三章1.产品的质量不仅取决于装配质量,而且还与零件的加工质量直接相关2.机械加工质量;①机械加工精度。
汽车制造工艺期末复习

1、金属材料在使用过程中应具备的力学性能包括强度,硬度,塑性,冲击韧性,疲劳强度等性能指标。
2、_强度是指金属材料在载荷作用下,抵抗塑性变形或断裂的能力。
作为最基本的指标有_抗拉强度,屈服强度塑性。
3、塑性__ 是指金属材料在载荷作用下,产生塑性变形而不被破坏的能力。
常用的指标有_伸长率A ,_断面伸缩率Z __。
4、采用适当的方法将钢在固态_ 态下进行加热.保温和冷却,以改变其内部组织,从而获得所需性能的一种工艺方法叫热处理_5、钢的热处理工艺有_退火,正火,淬火,回火_等。
6、在汽车上常用的非金属材料有塑料,橡胶,复合材料_等。
7、汽车是由许多零件、部件、分总成等装配而成的。
把将原料转变为成品的全过程称为生产过程。
8、在加工中作定位的基准,称为_定位基准_ 。
9、汽车覆盖件件是覆盖汽车发动机、底盘、驾驶室和车身的薄板异形类表面零件和内部零件。
10、加工精度的具体内容有尺寸精度,形状精度,位置精度___、形状精度、位置精度。
11、金属材料性能包括__使用性能__和__工艺性能__性能。
12、组成铁碳合金组织的基本相有__铁素体F,奥氏体A,渗碳体Fe3C,珠光体P,莱氏体Ld__等。
13、通过加热或加压(或两者并用),使被接金属原子之间互相溶解与扩散,从而实现永久连接的一种工艺方法是焊接。
14、硬度___ 是衡量金属材料软硬程度的指标。
它是指金属表面抵抗局部塑性变形的能力。
衡量指标有:____布氏硬度HBW HBS,洛氏硬度HRB HRC,维氏硬度HV _。
15、在汽车上常用的有色金属材料有_铜铝钛_ 等16、工艺过程是指改变生产对象的形状、尺寸、相对位置和性质等,使其成为成品或半成品的过程。
17、冲压工艺中常见的变形工序有__弯曲,拉伸,翻边.18、加工精度的具体内容有_尺寸精度,形状精度,位置精度。
19、碳的质量分数是0.0218%﹤WC﹤2.11%的铁碳合金称为_钢_。
20、找正定位可分为直接找正定位_ 、划线找正定位和组合表面定位。
汽车制造工艺学(吉大第3版)期末考试知识点总结

【名词解释】1.生产过程:指将原材料转变为汽车产品的全过程。
2.工艺过程:在生产过程中,改变生产对象的形状、尺寸、相对位置和性质等,使其成为成品或半成品的过程。
3.机械加工工艺过程:在机床设备上利用切削刀具或其他工具,利用机械力将毛坯或工件加工成零件的过程。
4.切削加工:利用切削刀具从生产对象(工件)上切除多余材料的加工方法。
5.装配工艺过程:按规定的装配技术要求,将零件或总成(部件)进行配合和连接,使之成为半成品或成品的工艺过程。
6.工序:一个或一组工人,在一个工作地(机械设备上)对同一个或同时对几个工件所连续完成的那一部分工艺过程。
7.安装:工件在一道工序中通过一次装夹后所完成的那一部分工艺过程。
8.工位:在某一工序中,工件在机床所占的每一个位置上所完成的那一部分工艺过程。
9.工步:在一次安装或工位中,加工表面、加工工具和切削用量中的主轴转速及进给量不变的情况下,所连续完成的那一部分工序,称为工步。
(填空题)10.试切法:通过试切、测量、调整、再试切,经过多次反复进行到被加工尺寸达到要求为止的方法。
11.加工经济精度:在正常生产条件下,每种加工方法所能保证的公差等级。
12.生产纲领:指企业在计划期内应生产的汽车产品的产量和进度计划。
13.定位:通常将确定工件在机床上或机床夹具中占有正确位置的过程。
14.夹紧:工件定位后将其固定,使其在加工过程中保持定位位置不变的操作。
15.装夹:将工件在机床或机床夹具中定位和夹紧的过程称为装夹。
16.机床夹具:用以装夹工件或引导刀具的装置。
17.基准:用以确定生产对象上几何要素间几何关系所依据的那些点线面。
18.设计基准:设计图样上采用的基准。
19.工艺基准:工艺过程中采用的基准。
20.工序基准:在工序图上用以确定本道工序被加工表面的加工尺寸、位置的基准。
21.定位基准:在加工中确定工件在机床或机床夹具中占有正确位置的基准。
22.测量基准:测量时所采用的基准,用来确定被测量尺寸、形状和位置的基准、23.装配基准:装配时用来确定零件或部件在产品中相对位置的基准。
汽车制造工艺学复习资料(精品)

汽车制造工艺学期末复习资料(精品)一、填空题1.按制造的自动化程度主要分为刚性制造自动化、柔性制造自动化、集成制造自动化、智能制造自动化四个阶段。
2. 要使工件加工后尺寸达到规定要求,可采用以下四种方法:试切法、调整法、定尺寸刀具法、主动测量法。
3. 工件形状的获得方法:轨迹法、成形法、展成法。
4. 生产类型:单件生产、成批生产、大量生产。
5. 工件的安装方式:直接找正安装、划线找正安装、采用夹具安装。
6. 夹具的分类:通用夹具、专用夹具、成组夹具、组合夹具7. 夹具的组成:定位元件、夹紧元件、引导元件、夹具体、其他元件。
8. 对夹紧装置的基本要求:夹得稳、夹得好、夹得快。
9. 零件的机械加工质量包括两个方面:加工精度和表面质量。
10. 尺寸链按各环所处的空间位置分类:线性尺寸链、平面尺寸链、空间尺寸链、、角度尺寸链。
11. 冲压生产的三大要素:板料、模具和冲压设备。
12. 按加工后板料分离与否,冲压工序可以分为分离工序和成形工序。
冲压常见的分离工序:落料、冲孔、剪切、切开、切舌、修边。
冲压常见的成形工序:弯曲、拉深、内孔翻边、外缘翻边、胀形、整形。
13. 冲裁既可以直接冲制出成品零件,也可为其他成形工序准备坯料或在已成形的零件上进行修边、切口和冲孔等工作。
在冲裁过程中,冲裁凸凹模组成上、下刃口,板料放在凹模上,在压力机(或冲床)压力作用下,凸模逐步下降使板料发生变形,直至全部分离,完成冲裁。
14. 将板料毛坯、棒料、管材和型材弯成具有一定曲率、一定角度和形状的冲压成形工序称为弯曲。
15.弯曲变形过程及变性特点:弯曲变形过程,板料由开始阶段为自由弯曲,随着凸模的下压,板料直角边与凹模的V形表面逐渐靠近,板料曲率半径逐渐减小,与凹模接触点形成的弯曲力臂也逐渐减小,直到与凸模形成三点接触,直到终止,这时凹模对板料进行校正,使圆角和直角边与凸模全部接触。
16. 拉深:利用拉深模将平面毛坯压制成各种形状的开口空心零件,或将已压制的开口空心毛坯进一步制成其他形状和尺寸的开口空心零件的冲压成形工序称为拉深,拉深又称为拉延或压延。
汽车制造工艺学总结
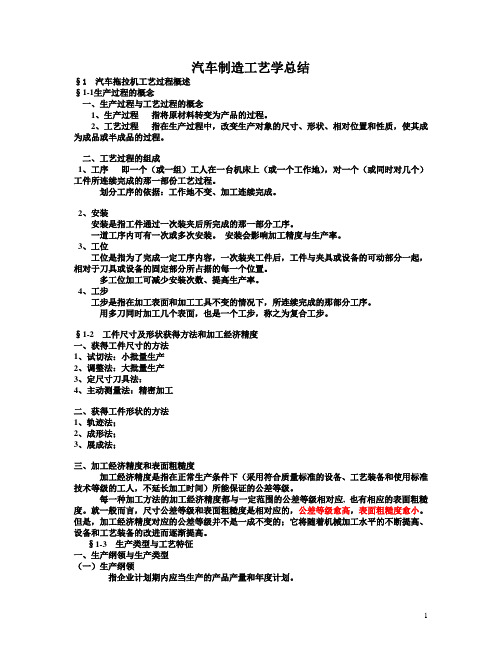
汽车制造工艺学总结§1 汽车拖拉机工艺过程概述§1-1生产过程的概念一、生产过程与工艺过程的概念1、生产过程指将原材料转变为产品的过程。
2、工艺过程指在生产过程中,改变生产对象的尺寸、形状、相对位置和性质,使其成为成品或半成品的过程。
二、工艺过程的组成1、工序即一个(或一组)工人在一台机床上(或一个工作地),对一个(或同时对几个)工件所连续完成的那一部份工艺过程。
划分工序的依据:工作地不变、加工连续完成。
2、安装安装是指工件通过一次装夹后所完成的那一部分工序。
一道工序内可有一次或多次安装。
安装会影响加工精度与生产率。
3、工位工位是指为了完成一定工序内容,一次装夹工件后,工件与夹具或设备的可动部分一起,相对于刀具或设备的固定部分所占据的每一个位置。
多工位加工可减少安装次数、提高生产率。
4、工步工步是指在加工表面和加工工具不变的情况下,所连续完成的那部分工序。
用多刀同时加工几个表面,也是一个工步,称之为复合工步。
§1-2 工件尺寸及形状获得方法和加工经济精度一、获得工件尺寸的方法1、试切法:小批量生产2、调整法:大批量生产3、定尺寸刀具法:4、主动测量法:精密加工二、获得工件形状的方法1、轨迹法;2、成形法;3、展成法;三、加工经济精度和表面粗糙度加工经济精度是指在正常生产条件下(采用符合质量标准的设备、工艺装备和使用标准技术等级的工人,不延长加工时间)所能保证的公差等级。
每一种加工方法的加工经济精度都与一定范围的公差等级相对应, 也有相应的表面粗糙度。
就一般而言,尺寸公差等级和表面粗糙度是相对应的,公差等级愈高,表面粗糙度愈小。
但是,加工经济精度对应的公差等级并不是一成不变的;它将随着机械加工水平的不断提高、设备和工艺装备的改进而逐渐提高。
§1-3 生产类型与工艺特征一、生产纲领与生产类型(一)生产纲领指企业计划期内应当生产的产品产量和年度计划。
(二)生产类型1、生产类型的概念生产类型,是指企业(或车间、工段、班组、工作地)生产专业化程度的分类。
- 1、下载文档前请自行甄别文档内容的完整性,平台不提供额外的编辑、内容补充、找答案等附加服务。
- 2、"仅部分预览"的文档,不可在线预览部分如存在完整性等问题,可反馈申请退款(可完整预览的文档不适用该条件!)。
- 3、如文档侵犯您的权益,请联系客服反馈,我们会尽快为您处理(人工客服工作时间:9:00-18:30)。
汽车制造工艺学第一章汽车制造工艺过程中的基本概念第一节汽车的生产过程和工艺过程2. 工艺过程:是指在生产过程中,改变生产对象的形状、尺寸、相对位置和性质等,使其成为成品或半成品的过程。
3. 生产过程指将原材料转变为产品的过程。
1、机械加工工艺过程:在机床设备上利用切削刀具或其它工具易用机械力将毛坯或工件加工成零件的过程。
2、工序:一个或一组工人在一个机床设备上对同一个或同时对几个工件所连续完成那一部分工艺过程。
工序是组成工艺过程的最基本单元3、安装:同一道工序中,零件在加工位置上装夹一次所完成的那一部分工序。
P44、工位:零件在每个位置上完成的那一部分加工过程。
P45、工步:再一次安装中,在加工表面、加工刀具、切屑用量不变的情况下,所连续完成的那一部分工艺过程。
几把刀同时加工几个表面叫(一个)复合工步第二节汽车零件尺寸即形状的获得方法和加工经济精度1. 工件尺寸的获得方法①试切法:通过试切、测量、调整、再试切,经多次反复进行到被加工尺寸达到要求为止的方法适用于单件货几件工件的加工②静调整法:在加工一批工件之前,采用对刀装置或试切的方法,先调整好刀具相对于工件或机床夹具间的正确位置,并在加工中保持其位置不变,以保证被加工尺寸的方法适合产量较大的场合广泛用于半自动机床和自动线上的生产;③定尺寸刀具法:利用刀具相应尺寸来获得被加工表面尺寸的方法适用于孔沟槽等表面的加工适用于各种产量的场合;④主动及自动测量控制法;在加工过程中,利用测量装置、进给机构及控制系统保证被加工表面尺寸的方法产量大的汽车制造企业。
2.工件形状的获得方法①轨迹法:依靠刀具运动轨迹来获得所需工件形状的方法用于产量较大较大工件形状较为复杂的零件形状的切削加工;②成型刀具法:使用成形刀具获得工件形状的方法生产率高;③包络法;在刀具与工件相对运动过程中,由刀具切削刃连续运动的轨迹包络成工件形状的方法6、加工经济精度:是指某种加工方法在正常生产条件下不延长加工时间所能保证的公差等级和表面粗糙度。
P83.汽车零件表面的尺寸公差与表面粗糙度具有何种关系?答:一般被加工表面的尺寸公差值小表面粗糙度值也一定较小。
但是有些被加工表面要求的表面糙度值较小不一定尺寸公差值也必须小。
例如抗腐蚀的零件表面具有高疲劳强度的零件表面都规定较小的表面粗糙度值但表面尺寸公差值却可以稍大些。
第三节汽车制造企业的生产类型及工艺特征1.生产纲领:生产厂家根据国家计划或用户订货和本企业的生产能力,在计划期内应生产的汽车产品的产量和进度计划。
2. 生产类型,是指企业(或车间、工段、班组、工作地)生产专业化程度的分类。
生产类型不同,零件加工工艺过程会有变化,工艺装备也不同。
2、生产类型的分类生产类型可以分为三大类,即:单件生产;成批生产:大批、中批、小批大量生产第二章工件的装夹和机床夹具1、定位:通常将确定工件在机床上或机床夹具中占有正确位置的过程。
P112、夹紧:工件定位后将其固定,使其在加工过程中保持定位位置不变的操作。
P113、装夹:将工件在机床上或机床夹具中定位、夹紧的过程。
P114. 机床夹具:用以装夹工件(和引导刀具)的装置第一节基准的概念1.基准:用来确定生产对象上几何关系所依据的那些点、线、面。
2.设计基准:设计图样上采用的基准3.设计尺寸:设计图样上标注的尺寸4.工艺基准:在工艺过程中采用的基准5.工序基准:在工序图上用来确定本道工序被加工表面加工尺寸、位置公差的基准。
工序卡上用以表示工件被加工表面加工要求及工件装夹情况的简图为工序图。
工序尺寸具有方向性6.定位基准:在加工中确定工件在机床上或机床夹具中占有正确位置的基准。
粗基准:未经加工的表面作为定位基准,精基准:用已加工的表面作为定位基准7.测量基准:用来确定被测量尺寸、形状和位置的基准8.装配基准:用来确定零件或部件在产品中的相对位置所采用的基准第二节工件的装夹方法工件装夹时,为了保证工序尺寸和位置公差,应满足的两项基本条件1.加工之前,工件必须正确定位,即工件相对于机床和刀具应占有正确位置2.加工过程中,工件必须合理夹紧,即保证作用于工件上的各种外力不被破坏定位。
工件的装夹方法1.找正装夹法直接找正装夹法:划线找正装夹法:2.专用机床夹具装夹法:为某种零件在某一道工序上的装夹而专门设计和制造的机床夹具特点:定位准确,装卸工件迅速,但设计与制造的周期长,费用较高。
主要适用于产品相对稳定而产量较大的成批和大量生产。
作用:保证加工精度,提高生产率,减轻工人的劳动强度,扩大机床的工艺范围第三节专用机床夹具的组成及其分类一、专用机床夹具的组成(1).定位元件:确定工件在夹具中位置的元件。
(6)夹紧装置:在工件定位后将工件夹紧的装置(2).对刀导向元件:用以引导刀具或调整刀具相对于夹具的位置。
(3).夹具连接元件:用以确定夹具在机床上的位置并与机床相连接。
(4) .其他装置或元件:如分度机构。
(5).夹具体:用于连接夹具各元件及装置使之成为一个整体的基础件二、专用机床夹具的分类1.专用机床夹具:为某种工件在某道工序上的装夹而专门设计和制造的机床夹具。
特点:定位准确,装卸工件迅速,但设计与制造的周期长,费用较高。
主要适用于产品相对稳定而产量较大的成批和大量生产。
2.组合夹具:按一工件某道工序的加工要求,用预先制造的一套系列化标准零件及组件拼装而成的专用机床夹具。
特点:使用后可拆开,清洗和储存,以便多次重复使用。
主要应用与单件、小批生产3.成组夹具:在多平中、中小批生产中采用成组加工时,为每个工件组设计制造的专用机床夹具特点:针对性强,结构较为紧凑,弥补组合夹具结构刚性不足的缺点。
适用于多品种、中小批生产4.随行夹具:用于组合机床自动线上的可随工件通行的一种移动式专用机床夹具第四节、工件在机床夹具中的定位一、工件定位的六点定位规则六点定位规则:在工件的适当位置上布置六个支撑点,相应限制工件的六个自由度,从而确定工件唯一确定位置的规则三个移动,三个旋转。
二、正确确定工件位置应限制的自由度1. 第一类自由度:为保证加工要求应限制的自由度2. 第二类自由度:对加工要求无关的自由度三、机床夹具定位元件及其所限制的自由度定位元件必须满足的要求一定的精度,良好的耐磨性,足够的刚性,良好的工艺性(一)工件以平面为定位基准时常用的定位元件支承件:使用元件的平面支承工件的定位基准。
起定位作用的基本支承;不起限制自由度作用的辅助支承件。
支承钉,支承板,可调支承,辅助支承(二)工件以内孔为定位基面时常用的定位元件工件以内孔定位基面,常用的定位元件有心轴和定位销两种。
长心轴(销),限制4个自由度短心轴(销) ,限制2个自由度。
常用心轴定位形式①锥形心轴:定位时是依靠心轴的锥体定心和胀紧,可以限制五个自由度。
②过盈配合圆柱心轴:过盈配合心轴定心精度较高,可以限制四个自由度。
③间隙配合心轴:带有轴臂的间隙配合心轴可以限制五个自由度,其中心轴定位部分可以限制四个自由度。
(三)工件以外圆为定位基面时常用的定位元件工件以外圆定位基面,常用v形块、半圆定位块、定位套、定心夹紧机构。
固定v型块中的短v型块限制两个自由度;一个长v型块或两个短v型块的组合件限制四个自由度;活动v型块(浮动式与移动式)可以限制一个自由度。
定位套中的短定位套孔限制两个自由度;长定位套孔限制四个自由度;定位元件锥孔限制三个自由度。
(四)工件以组合表面定位的定位元件4、过定位:几个定位支承点,同时限制同一个自由度的定位。
5、欠定位:在加工中,如果定位元件限制的自由度少于工件应限制的自由度。
第五节定位误差的分析与计算1、定位误差:是指由于定位的不准确原因使工件工序基准偏离理想位置,引起工序尺寸变化的加工误差。
产生的原因:工件的定位基准与工序基准不重合,工件的定位基准(基面)与定位元件工作表面存在制造误差1.基准位移误差Δj,y:是由于定位基面(孔)和定位元件(心轴)制造不准确,而使定位基准在工序尺寸方向上产生最大位置变化,引起的加工误差)2.基准不重合误差Δj,b:是由于工序基准与定位基准不重合引起的,即工序基准在工序尺寸方向上产生的最大位置变化。
)3.定位误差ΔΔj,Δj,b注意:公差1d上偏差-下偏差≥0 ,定位误差Δd≥0 ,Δj,y≥0 ,Δj,b≥0 第六节工件的夹紧和夹紧装置一、夹紧装置的组成及夹紧的基本要求夹紧装置:将工件压紧夹牢的装置组成:力源装置,夹紧元件,中间传力机构夹紧装置的设计要求?夹紧力的三要素:大小、方向和作用点。
①确保工件的定位置不变。
②夹紧力的大小要适当。
③具有良好的自锁性。
④便于使用、操作简便。
⑤夹紧装置有良好的工艺性。
二、夹紧力的确定确定夹紧力作用点的原则①应正对夹具定位支承元件或位于支承元件所形成的稳定受力区域内,以免工件产生位移和偏转。
②应在工件刚性较好的部位上,以使夹紧变形尽可能少。
③应尽量靠近工件的加工表面,以保证夹紧的稳定性和可靠性、减小工件的夹紧力,防止加工过程产生振动。
确定夹紧力作用方向的选择原则?①应垂直于主要定位基面,以保证加工精度。
②应与工件刚度最大的方向一致,使工件的夹紧变形最小。
③应尽量与切削力、重力的方向一致,以减小工件的夹紧力。
三、常用的典型机构1.斜楔夹紧机构:适用于成批大量生产中,夹紧较大型工件的场合2.螺旋夹紧机构:螺旋夹紧结构简单,增力比大,自锁性好,夹紧可靠,所以在夹具中得到最广泛的应用。
螺旋夹紧的主要缺点安装、拆卸工件的辅助时间太长。
4.多位多件夹紧机构:加工时采取多件夹紧,可以大大提高生产率,尤其在小件加工时应用更为广泛。
5.定心夹紧机构1.机械式定心夹紧机构特点:结构简单工作行程较长通用性好。
但定心精度不高.适用于工件行程较长,定心精度要求不高的工件的装夹。
2.弹性变形式定心夹紧机构特点:定心精度高操作简便但夹紧力小因此多用于精加工。
第七节典型的专用机床夹具一、专用钻具夹具钻床夹具:使用钻头,铰刀等孔加工刀具进行孔加工的机床夹具,亦称钻模特点:具有引导钻头、铰刀等孔加工刀具的导向元件——钻套和安装钻套的钻模板钻套和钻模板是钻床夹具的特殊元件钻套:用来引导钻头、铰刀等孔加工刀具的导向元件。
功能是确定孔加工刀具相对于夹具定位元件间的位置和引导孔加工刀具,提高刀具的刚性,防止其加工中发生偏移。
钻模板二、专用铣床夹具对刀元件:专用铣床夹具上确定铣刀相对于夹具定位元件间正确位置的元件定位键:保证铣床夹具对铣床工作台间相对位置的连接件9、工序基准与定位基准不重合以及定位基准的位移误差是造成定位误差的两方面原因?p35①基准不重合误差由于工件的工序基准与定位基准不重合而引起的定位误差,为基准不重合误差。
②基准位移误差由于工件上的定位表面或夹具上的定位元件的制造误差和最小间隙配合的影响而引起的加工第三章汽车零件表面的加工方法1、切削用量或切削三要素:切削速度、进给量f、背吃刀量。