棕化、层压实用工艺要求规范
内层棕化工艺流程

内层棕化工艺流程
内层棕化工艺流程是PCB制作流程中的一种,其步骤为:
1.对内层铜面进行清洁处理,去除表面的油脂、氧化物等杂质。
2.使用棕化液对内层铜面进行浸泡或喷涂处理,使其表面发生化学反应,生成一层棕色的化合物。
3.对棕化后的内层铜面进行清洗,去除表面的棕化液残留物。
4.对内层铜面进行烘干处理,使其表面干燥,以便进行后续的层压等工艺。
内层棕化的目的是增加内层铜与胶片(玻璃纤维)的键结能力,提高PCB的层间结合力和耐热性。
层压黑化和棕化的区别
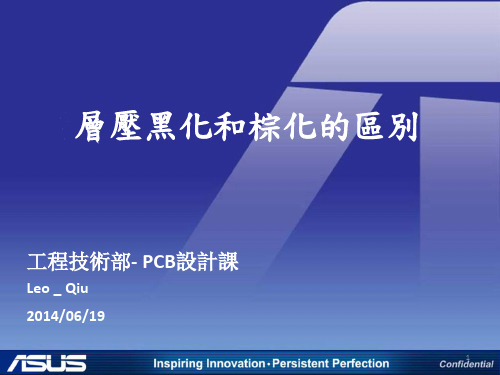
化學反應: 4Cu+NaClO2=2Cu2O + NaCl 2Cu2O+NaClO2 = 4CuO + NaCl
4
黑化流程
鹼洗 酸浸 微蝕 預浸 氧化 還原 抗氧化
1. 去除油脂、污垢等; 2. 銅層表面親水處理。
調整板面PH至酸性操作環境。 提高銅表面粗糙度。 1. 2. 酸鹼中和,達到鹼性操作環境; 使氧化層顏色均勻。
14
黑化和棕化優缺點比對
項目 速度 黑化 棕化 棕化速度快,棕化膜本身特別薄, 黑化的速度較慢,板子在藥水浸泡 不帶溪水基因,板在藥液中浸泡 在60分鐘左右,且需加烤30分鐘以 時間短,經過90± 5℃的烘乾,可 保證板面乾燥。 保證板面乾燥,無需外加烘乾。
黑化藥水帶入帶出較多,且黑化槽 液溫度較高(70± 2℃),濃度變化大, 棕化藥水帶入帶出少,槽液易管 藥水管控 製 黑化槽的氧化劑和還原劑容易分層, 控。 作 給品質帶來隱患。 差 棕化微蝕量控制在60~80µ"之間, 異 黑化微蝕量控制在40~60µ"之間,板 板面的清潔較好,不易產生露銅 製作 面潔淨度難以管控,容易產生露銅。 現象,但重工次數要求嚴格,特 別是內層為H/H銅箔。 刮傷 黑化為插框架作業,對較薄板子容 棕化製作為水平式,板面容易受 易產生刮傷,雖用鐵氟龍網框,但 機台刮傷。 仍有刮傷。
黑化和棕化優缺點比對
黑化結合力不及棕化,且有電性問題
黑化層因液中存有高鹼度而雜有Cu2O,此物容易形成長針 狀或羽毛狀結晶。此種亞銅之長針在高溫下容易折斷而大 大影響銅與樹脂間的附著力,並隨流膠而使黑點流散在板 中形成電性問題,而且也容易出現水分而形成高熱後局部 的分層爆板。 棕化層則呈碎石狀瘤狀結晶貼銅面,其結構緊密無疏孔, 與膠片間附著力遠超過黑化層,不受高溫高壓的影響,成 為聚亞醯胺多層板必須的製程。
棕化--压板工艺原理及控制要点
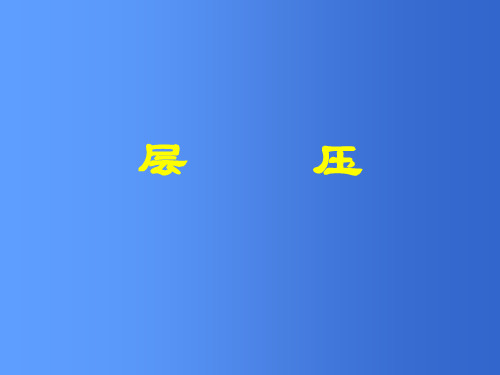
目前公司常用半固化片IT158特性及参数 目前公司常用半固化片IT158特性及参数 IT158
項目 規格 7628 7628 7628 2116 2116 2116 1080 1080 1080 1080 106 106 106 106
布重(g/ (g/㎡ 布重(g/㎡) Glass Fiber Weight 樹脂含量 Resin Content (%):R/C± (%):R/C±2 樹脂流量 Resin Flow(%): R/F±5 R/F± 膠化時間( 膠化時間(秒) Gel Time(sec) G/T±20 ± (拉絲法) 拉絲法) G/T±20 ± (脫盤法) 脫盤法) 脫盤法 揮發物含量 Volatile Content(%) V/C 壓合 光板厚度 (mil) Thickness
2.3 常见多层板(以六层板为例)结构 常见多层板(以六层板为例)
--Foil Prepreg
-- Core(C/C) -- Prepreg -- Core(C/C) -- Prepreg -- Foil
2.5 压板方式
------MASS LAM ------MASS ------PIN ------PIN LAM
压板生产步骤: 2.2 压板生产步骤: 排板---------将内层板与半固化片及铜 A、排板-----将内层板与半固化片及铜 箔以钢板分隔排好。 箔以钢板分隔排好。 压板---------通过压板机将排好的多层 B、压板-----通过压板机将排好的多层 book)压合成整体。 板(book)压合成整体。
3.2 Prepreg
即半固化片,由玻璃纤维布和树脂组成。 即半固化片,由玻璃纤维布和树脂组成。其 中的树脂呈半固化状态-----称 ;业界 中的树脂呈半固化状态-----称 B-Stage ;业界 ----常称“树脂片”,“半硬化材料”,“半固化片” 常称“树脂片” 半硬化材料” 半固化片” 等。
工艺技术棕化层压工艺规范教材(DOC37页)

1、目的:规范层压工序制程能力的管控。
2、范围:适用于层压工序制程能力的管控。
3、职责:层压工序工艺工程师按规范要求管控该工序制程能力;技术中心负责该规范的编制与更新。
5、制程目标产品能力:详见附件三《层压工序产品能力参数表》设备能力:详见附件二《层压工序设备能力参数表》制程能力:详见附件四《层压工序制程能力参数表》6、工序资源设备资源:详见附件六《层压工序设备列表》物料资源:详见附件五《层压工序物料列表》7、基本原理棕化内层芯板经过棕化处理后,在铜面形成一层均匀的棕色有机金属膜,可增强铜面与半固化片的结合力,同时在高温压合过程中,阻止铜与半固化片的氨基发生反应。
产品实现的基本原理有药水作用原理、设备作用原理等。
棕化反应机理酸洗酸洗的主要作用是去除铜表面氧化物,中和残余退膜液,粗化铜面,保证稳定的微蚀、成膜及着色。
酸洗段的主要成分为过硫酸钠(NaPS)、H2SO4。
其反应机理如下:Cu+CuO+H2SO4+Na2S2O8→2CuSO4+Na2SO4+H2O碱洗碱洗的主要作用是去除铜表面的油污、手指印、轻微氧化物及抗蚀剂残渣。
碱式除油剂主要成分为NaOH和H2O。
其反应过程是利用热碱溶液对油脂的皂化作用和乳化作用来进行除油。
水洗棕化线在酸洗、碱洗、棕化之后均有水洗段,主要目的是去除酸洗、碱洗、棕化缸在板面残留的药水,避免污染下一道工序。
序号影响因素具体影响1 DI水电导率水洗用水必须具备一定的纯净度,即对电导率有要求,当电导率超过一定范围,则会带来离子污染。
2 水洗时间水洗需要一定的时间去作用,水洗时间不够,则无法去除板面残留药水,从而引起缸与缸之间的药水污染。
3 喷淋压力采用喷淋水洗主要是为了全面去除板面各个位置的残留药水,若水洗压力不当,则会导致局部区域水洗效果不佳,引发污染。
预浸预浸的主要作用是活化铜表面以利于棕化处理快速均匀,增强结合力。
预浸段的主要成分为活化剂(成分为苯并三唑,乙二醇单异丙基醚和水)。
棕化层压工艺设计规范
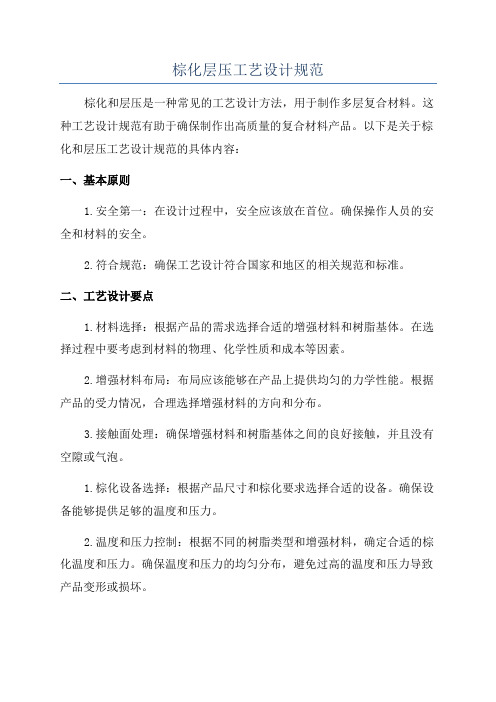
棕化层压工艺设计规范棕化和层压是一种常见的工艺设计方法,用于制作多层复合材料。
这种工艺设计规范有助于确保制作出高质量的复合材料产品。
以下是关于棕化和层压工艺设计规范的具体内容:一、基本原则1.安全第一:在设计过程中,安全应该放在首位。
确保操作人员的安全和材料的安全。
2.符合规范:确保工艺设计符合国家和地区的相关规范和标准。
二、工艺设计要点1.材料选择:根据产品的需求选择合适的增强材料和树脂基体。
在选择过程中要考虑到材料的物理、化学性质和成本等因素。
2.增强材料布局:布局应该能够在产品上提供均匀的力学性能。
根据产品的受力情况,合理选择增强材料的方向和分布。
3.接触面处理:确保增强材料和树脂基体之间的良好接触,并且没有空隙或气泡。
1.棕化设备选择:根据产品尺寸和棕化要求选择合适的设备。
确保设备能够提供足够的温度和压力。
2.温度和压力控制:根据不同的树脂类型和增强材料,确定合适的棕化温度和压力。
确保温度和压力的均匀分布,避免过高的温度和压力导致产品变形或损坏。
3.加热和冷却过程控制:根据产品的尺寸和要求,确定合适的加热和冷却速率。
避免温度过快变化引起应力集中或变形。
1.板材准备:确保板材表面干净,无油脂和杂质。
对于一些需要特殊处理的板材,如镀铜板或金属板,要进行特殊的处理。
2.压力和温度控制:根据树脂类型和板材厚度,确定合适的层压温度和压力。
确保温度和压力的均匀分布,避免过高的温度和压力导致产品变形或损坏。
3.层压时间控制:根据产品的尺寸和层数,确定合适的层压时间。
避免层压时间过长或过短导致产品质量不稳定。
综上所述,棕化和层压工艺的设计规范对于确保制作高质量的复合材料产品非常重要。
遵循这些规范可以提高工艺过程的可控性和稳定性,减少产品的不良率,提高产品的性能和可靠性。
同时,合理的工艺设计规范还可以降低生产成本,提高生产效率。
压合技术全套

5.材料-----------------------------------------------------------4
6.工艺流程图-----------------------------------------------------5
压合技术指导
d.下列情况的需返工: 棕化颜色不良、不均匀; 严重擦花、擦伤(返工前先用 300#砂纸打磨擦花处); 棕化 后有辘痕; 棕化后超过一个星期未层压的板; 露铜。
7.2.1.4.8 关机: a.当确认机器内无任何生产板后方可关机。 b.依次关闭各缸体控制开关(棕化缸除外)。 c.关掉酸洗缸、促进缸(预浸缸)的冷却开关。 d.排放掉水洗缸中的水,以备第二天开工用。
35±3℃
10-20
每周
40-60
板面颜色浅, 蚀铜率低于 1.0µm/min Cu2+>30g/L 药水产量: 2.0-3.0m2/L
压合技术指导
水洗 烘干
保持循环流动 温度:80-90℃
室温 0.7kg/cm2
85-89
7.2.1.7 维护和保养:
7.2.1.7.1 药水缸保养项目,周期及责任人:
压合技术指导
芯)过滤棉芯的使用:使用前先用 5%左右的 H2SO4 浸泡 30 分钟左右。(注意 H2SO4 溶液需 用 DI 水配取),然后用 DI 水冲洗,方可使用。 7.2.1.3 工艺流程:
酸洗→水洗→水洗→水洗→脱膜(碱洗)→DI 水洗→DI 水洗→热水(DI 水)洗 →预浸→铜面剂(棕化)→DI 水洗→DI 水洗→DI 水洗→强风吹干→热风吹干 →出板 7.2.1.4 作业标准 7.2.1.4.1 打开总电源开关至“ON”,按启动键启动机器。 7.2.1.4.2 依次打开输送辘、各缸体循环泵、加热开关(试实际情况)。 7.2.1.4.3 启动后检查: a.检查各过滤器、泵等设备是否正常运作。 b.检查传输辘是否正常运作,药水缸或水缸等运输辘有否不转、跳离等情况。 c.检查棕化缸、预浸缸上槽液是否合适,否则进行调整(一般药水位以不超过挡水辘为宜, 以免生产时药水沿着板面倒流回预浸缸或进入水洗缸)。 d.检查警报指示灯,“绿灯”为正常,“红灯”或“黄灯”要查明原因并将其清除。 e.检查控制柜显示温度(红色数字)是否在作业范围内,输送速度是否在 2.0-3.0m/min,否 则,要调整。 7.2.1.4.5 试板: a.用 2 片方形铜板(尺寸为 10ⅹ10cm 左右)分别进行酸洗、棕化蚀铜率测试,保证其在要 求范围内。 b.放 3-5PNL 生产板作首板检查,无不良品质问题则可生产,有则通知工程师解决。 7.2.1.4.6 注意: a.经常察看棕化缸上槽的药水位,过高或过底要进行调整。 b.经常察看棕化缸各传动辘运行情况及 DI 水和冷却水供应情况。 c.每做一种料号的板依工卡估算有效铜面积,生产过程中棕化缸按每 50m2(有效铜面积)生 产板加 400ml H2O2 及时进行药水补加,下班前统计做板面积(开料面积)及药水补加量 并填写在《棕化生产记录及药水添加记录表》中。 d.放板距离间隔大于 10cm,不可放得太近,以免叠板、卡板。 e.接板人要戴干净的手套,接板处要干净、干燥。 f.每连续做 200-300 m2 板,须更换棕化缸后的三个 DI 水缸中的 DI 水。 7.2.1.4.7 生产板返工: a.返工板须先查明原因,并确认通过返工能改善的可返工,否则另行处理。 b.凡有返工的板返工次数不得多于三次(特别是细线路的板),若超过三次仍无效果,通知 工程师处理。 c.凡一批板中一次性超过 50PNL 需返工,须及时通知工程师。
棕化

1.0目的:1.1建立棕化的作业规范,指导员工正确操作与控制机器,以保证产品的质量与机器的维护。
1.2光滑内层铜面在多层板内层压板后结合力不足,因此在生产加工后容易产生爆板,分层等缺陷;因此在加工过程中要进行表面的微粗化(微蚀MICRO-ETCH)以增强内层铜箔表面积,提高结合力。
铜面不经氧化处理在高温高压状态下内层铜面会与半固化片(粘结片)固化过程中的的有机物(在高温高压下多官能团有机物均具有很强的氧化效果)和挥发性气体(水和其他小分子物质)发生反应,造成内层铜面的颜色不均,明显的色差和次表面缺陷,采用棕化处理即可有效防止该类缺陷的发生。
2.0适用范围:我公司垂直棕化生产线以及棕化后烤板。
3.0工序流程:酸洗水洗*2碱洗水洗*2预浸棕化水洗*2热水洗烘干4.0化验合格配槽化验补充药水加温IPQC首样换槽量产首样工艺流程:5.0工艺参数:6.0操作规程:6.1配槽步骤及方法见表:6.2补充液位与药水:6.2.1检查各水洗槽放水阀是否关闭,将各水槽放满水,放满后进水阀不要完全关闭,保持一定了溢流量,以保证水洗槽清洁;6.2.2每班上班半小时内检查各药水槽液位是否过低,低了先补充纯水,补充也不宜过高,需留有适当空间共补充药水,淹没挂篮5cm左右较为合适。
液位补充完成后待化验室化验;6.2.3药水槽每班化验一次,化验时间为上班后1小时内,未化验前不得生产;6.2.4根据《溶液分析报告》分析结果添加药水;6.2.5若化验单下来液位还没有补充,则重新补液位,化验,添加药水。
6.3加温:下图为电源控制柜,生产前打开酸洗、碱洗、预浸、棕化、热水洗温控开关,待显示温度加到设定值才可以生产。
设定值显示值温控开关顺着箭头方向为开6.4插板:6.4.1棕化板很容易擦伤,为防止板与板,板与挂篮碰触,造成的划伤。
必须使用专用挂篮,且不同板厚插板间距也不同。
板厚≤0.5mm芯板每间隔两个槽插一块板,芯板到挂篮筐也须间隔两个槽。
PCB工艺流程之棕化工序培训教材
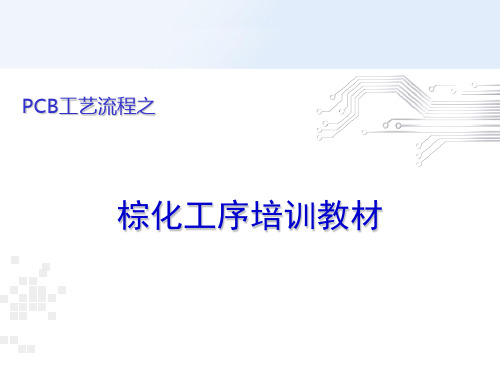
棕化的工艺流程、原理及其作用
1:CU金属遭受微蚀攻击而氧化 2:氧化铜与有机物形成有机物层沉积 3:微蚀/沉积持续进行
11
棕化的工艺流程、原理及其作用
1:CU金属遭受微蚀攻击而氧化 2:氧化铜与有机物形成有机物层沉积 3:微蚀/沉积持续进行 4:反应达到平衡
12
棕化的工艺流程、原理及其作用
去离子水(DI水) BondFilm Activator
内层键合活化剂
BondFilm Part A Plus 内层键合剂A Plus
硫酸(50%) 双氧水(50%) 去离子水(DI水)
操作浓度 30ml/L 20g/L 510L/hr
100ml/L
510L/hr 20ml/L
100ml/L
50ml/L 21.5ml/L 510L/hr
a:装机要求
1.机器运行良好,所有的机械部分运作良好,无损坏,无异常磨损。 2.机器不漏水,所有的药水缸无药水泄露,包括所有的进水管道、排水管道、
加药泵、加药桶和加药盒。 3.设备运转时无尖锐的噪音,噪音低于国家标准65分贝。 4.机器无不正常的震动 5.所有的马达运转正常 6.所有的电线连接正确,不发生过热现象,不发生裸露铜线。 7.所有的电气信号正确
六、棕化设备
a:Schmid(迅德)棕化线
22
棕化工艺控制及设备要求
b:UCE(宇宙)棕化线
23
棕化工艺控制及设备要求
六、棕化设备能力
1.板厚:0.05~3.2MM(含铜,以H/HOZ铜作标准) 2.板大小尺寸:最大620*622mm,最小180*180mm 3.孔径比:10:1
七、棕化设备要求
二、棕化颜色不均匀
29
棕化主要缺陷及其成因和改善对策
棕化--压板工艺原理及控制要点 层压
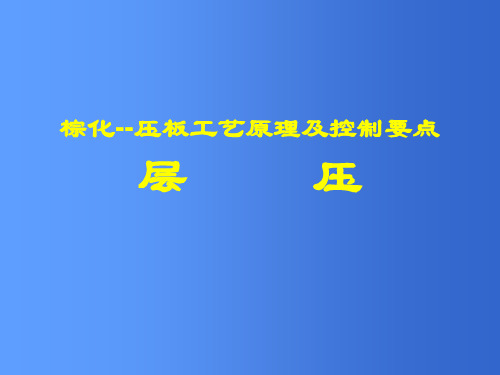
3337℃
2次/班
处理方式:药水浸入处理。
水洗: 作用:清洗上一步反应的残存药水,以利下一步反应的进行。 处理方式:喷淋处理,溢流水洗
DI水洗: 作用:降低制板表面离子含量,最终清洁制板。 处理方式:喷淋处理,逐级溢流水洗。 烘干: 作用:去除棕化膜表面水份,为排压板做准备。 处理方式:风刀热风吹干
钻孔工序制作
2.1 压板的原理及目的:
利用半固化片(B-Stage树脂)受高温高压 而完全固化使多层板各层结合在一起,保证多 层板的电气性能和机械性能。
2.2 压板生产步骤:
A、排板-----将内层板与半固化片及铜 箔以钢板分隔排好。
B、压板-----通过压板机将排好的多层 板(book)压合成整体。
半固化片的特性指标各项并非孤立存在,而是相互 影响。
例如: a、Gel Time长则树脂流失多; b、挥发份含量高则树脂流失多; c、树脂含量高则树脂流量高。
选择半固化片的原则:
在层压时树脂能填满内层线路间隙,排除叠片间的气 体和挥发物,并保证制板要求的厚度及电气性能,而且 需考虑客户的特殊要求、制板尺寸、布线密度、层数等。
水平棕化工艺的优点:
工艺简单、容易控制;棕化膜抗酸性好,不 易出现粉红圈故障;
生产制板质量稳定一致。
2. 工艺流程:
棕化用化学药水: 碱性除油剂 内层键合活化剂 双氧水(H2O2)30% 硫酸(H2SO4)98% MS100
工艺流程图:
AOI制板清洁
酸洗
二级逆流水洗
除油
三级逆流DI水洗
强风吹干 四级逆流DI水洗
保持 /min
8 7 1 100 15 15
斜率 /min
5 0 0 15 0 20
棕化

1.0目的:1.1建立棕化的作业规范,指导员工正确操作与控制机器,以保证产品的质量与机器的维护。
1.2光滑内层铜面在多层板内层压板后结合力不足,因此在生产加工后容易产生爆板,分层等缺陷;因此在加工过程中要进行表面的微粗化(微蚀MICRO-ETCH)以增强内层铜箔表面积,提高结合力。
铜面不经氧化处理在高温高压状态下内层铜面会与半固化片(粘结片)固化过程中的的有机物(在高温高压下多官能团有机物均具有很强的氧化效果)和挥发性气体(水和其他小分子物质)发生反应,造成内层铜面的颜色不均,明显的色差和次表面缺陷,采用棕化处理即可有效防止该类缺陷的发生。
2.0适用范围:我公司垂直棕化生产线以及棕化后烤板。
3.0工序流程:酸洗水洗*2碱洗水洗*2预浸棕化水洗*2热水洗烘干4.0化验合格配槽化验补充药水加温IPQC首样换槽量产首样工艺流程:5.0工艺参数:6.0操作规程:6.1配槽步骤及方法见表:6.2补充液位与药水:6.2.1检查各水洗槽放水阀是否关闭,将各水槽放满水,放满后进水阀不要完全关闭,保持一定了溢流量,以保证水洗槽清洁;6.2.2每班上班半小时内检查各药水槽液位是否过低,低了先补充纯水,补充也不宜过高,需留有适当空间共补充药水,淹没挂篮5cm左右较为合适。
液位补充完成后待化验室化验;6.2.3药水槽每班化验一次,化验时间为上班后1小时内,未化验前不得生产;6.2.4根据《溶液分析报告》分析结果添加药水;6.2.5若化验单下来液位还没有补充,则重新补液位,化验,添加药水。
6.3加温:下图为电源控制柜,生产前打开酸洗、碱洗、预浸、棕化、热水洗温控开关,待显示温度加到设定值才可以生产。
设定值显示值温控开关顺着箭头方向为开6.4插板:6.4.1棕化板很容易擦伤,为防止板与板,板与挂篮碰触,造成的划伤。
必须使用专用挂篮,且不同板厚插板间距也不同。
板厚≤0.5mm芯板每间隔两个槽插一块板,芯板到挂篮筐也须间隔两个槽。
棕化层压工艺规范

棕化层压工艺规范1. 引言本文档旨在规范棕化层压工艺的操作步骤、关键参数和注意事项,以确保最终产品的质量和可靠性。
2. 工艺流程棕化层压工艺的基本流程包括材料准备、层压成型、压力和温度控制、冷却和固化等环节。
2.1 材料准备在进行棕化层压前,需要准备以下材料:•树脂胶粘剂•纤维材料(如玻璃纤维布)•预制基材(如金属板或塑料板)2.2 层压成型层压成型是棕化层压工艺的关键步骤,它包括以下几个基本步骤:1.准备工作台面,并确保表面平整清洁。
2.将预制基材放置在工作台上,并仔细检查其表面质量。
3.将纤维材料逐层铺设在预制基材上,确保每一层之间均匀覆盖树脂胶粘剂。
4.在每一层纤维材料上均匀涂布树脂胶粘剂,注意控制涂布量,以免造成浸渍不均。
5.叠加完所有层次后,在最上层铺设一层纤维材料,并涂布适量的树脂胶粘剂以封闭工件。
6.对于大型工件,可在层压过程中使用夹具进行固定。
7.检查一遍各层纤维材料是否平整、无空隙,并调整需要。
8.开始层压成型,使用合适的设备对工件进行压力施加。
2.3 压力和温度控制在层压过程中,合理的压力和温度控制是确保工件质量的关键。
1.压力控制:根据工件的大小和形状,合理选择施加的压力。
通常,压力越大,层压效果越好。
2.温度控制:通过控制加热设备的温度,使树脂胶粘剂在合适的温度下固化。
温度过高会导致胶粘剂退化或烧焦,温度过低则会影响固化效果。
2.4 冷却和固化层压完成后,需要进行冷却和固化步骤以确保工件的稳定性和强度。
1.先将工件从加热设备中取出,并放置在冷却设备中进行快速冷却。
冷却时间根据工件大小和厚度来确定。
2.在完成冷却后,取出固化的工件。
固化时间根据树脂胶粘剂的特性来确定。
3. 注意事项在进行棕化层压工艺时,需注意以下事项:•操作时需佩戴防护手套和眼镜,避免材料对皮肤和眼睛的刺激。
•根据不同材料的性质和特点,合理选择树脂胶粘剂,以确保黏合效果。
•控制涂布量,避免树脂胶粘剂过多或过少影响工件的质量。
棕化、层压工艺规范标准[详]
![棕化、层压工艺规范标准[详]](https://img.taocdn.com/s3/m/38dab272647d27284b7351a9.png)
1、目的:规范层压工序制程能力的管控。
2、范围:适用于层压工序制程能力的管控。
3、职责:3.1层压工序工艺工程师按规范要求管控该工序制程能力;3.2技术中心负责该规范的编制与更新。
5、制程目标5.1产品能力:详见附件三《层压工序产品能力参数表》5.2设备能力:详见附件二《层压工序设备能力参数表》5.3制程能力:详见附件四《层压工序制程能力参数表》6、工序资源6.1设备资源:详见附件六《层压工序设备列表》6.2物料资源:详见附件五《层压工序物料列表》7、基本原理7.1棕化内层芯板经过棕化处理后,在铜面形成一层均匀的棕色有机金属膜,可增强铜面与半固化片的结合力,同时在高温压合过程中,阻止铜与半固化片的氨基发生反应。
产品实现的基本原理有药水作用原理、设备作用原理等。
7.1.1棕化反应机理7.1.1.1酸洗酸洗的主要作用是去除铜表面氧化物,中和残余退膜液,粗化铜面,保证稳定的微蚀、成膜及着色。
酸洗段的主要成分为过硫酸钠(NaPS)、H2SO4。
其反应机理如下:Cu+CuO+H2SO4+Na2S2O8→2CuSO4+Na2SO4+H2O影响酸洗效果的因素及影响趋势如下:7.1.1.2碱洗碱洗的主要作用是去除铜表面的油污、手指印、轻微氧化物及抗蚀剂残渣。
碱式除油剂主要成分为NaOH和H2O。
其反应过程是利用热碱溶液对油脂的皂化作用和乳化作用来进行除油。
7.1.1.3水洗棕化线在酸洗、碱洗、棕化之后均有水洗段,主要目的是去除酸洗、碱洗、棕化缸在板面残留的药水,避免污染下一道工序。
7.1.1.4预浸预浸的主要作用是活化铜表面以利于棕化处理快速均匀,增强结合力。
预浸段的主要成分为活化剂(成分为苯并三唑,乙二醇单异丙基醚和水)。
7.1.1.5棕化棕化的主要作用是粗化铜面并在铜表面形成一层均匀的棕色有机金属转化膜以增强多层板内层结合力。
棕化的主要成分为苯并三唑、硫酸和水。
其反应机理如下:2Cu+H2SO4+H2O2+nA+nB→CuSO4+2H2O+Cu[A+B]n有机物A为:乙二醇单异丙基醚;其作用机理:1、参与半固化片环氧树脂聚合; 2、与含N的杂环化合物B和金属铜形成化学键。
- 1、下载文档前请自行甄别文档内容的完整性,平台不提供额外的编辑、内容补充、找答案等附加服务。
- 2、"仅部分预览"的文档,不可在线预览部分如存在完整性等问题,可反馈申请退款(可完整预览的文档不适用该条件!)。
- 3、如文档侵犯您的权益,请联系客服反馈,我们会尽快为您处理(人工客服工作时间:9:00-18:30)。
1、目的:规层压工序制程能力的管控。
2、围:适用于层压工序制程能力的管控。
3、职责:3.1层压工序工艺工程师按规要求管控该工序制程能力;3.2技术中心负责该规的编制与更新。
5、制程目标5.1产品能力:详见附件三《层压工序产品能力参数表》5.2设备能力:详见附件二《层压工序设备能力参数表》5.3制程能力:详见附件四《层压工序制程能力参数表》6、工序资源6.1设备资源:详见附件六《层压工序设备列表》6.2物料资源:详见附件五《层压工序物料列表》7、基本原理7.1棕化层芯板经过棕化处理后,在铜面形成一层均匀的棕色有机金属膜,可增强铜面与半固化片的结合力,同时在高温压合过程中,阻止铜与半固化片的氨基发生反应。
产品实现的基本原理有药水作用原理、设备作用原理等。
7.1.1棕化反应机理7.1.1.1酸洗酸洗的主要作用是去除铜表面氧化物,中和残余退膜液,粗化铜面,保证稳定的微蚀、成膜及着色。
酸洗段的主要成分为过硫酸钠(NaPS)、H2SO4。
其反应机理如下:Cu+CuO+H2SO4+Na2S2O8→2CuSO4+Na2SO4+H2O影响酸洗效果的因素及影响趋势如下:7.1.1.2碱洗碱洗的主要作用是去除铜表面的油污、手指印、轻微氧化物及抗蚀剂残渣。
碱式除油剂主要成分为NaOH和H2O。
其反应过程是利用热碱溶液对油脂的皂化作用和乳化作用来进行除油。
7.1.1.3水洗棕化线在酸洗、碱洗、棕化之后均有水洗段,主要目的是去除酸洗、碱洗、棕化缸在板面残留的药水,避免污染下一道工序。
7.1.1.4预浸预浸的主要作用是活化铜表面以利于棕化处理快速均匀,增强结合力。
预浸段的主要成分为活化剂(成分为苯并三唑,乙二醇单异丙基醚和水)。
7.1.1.5棕化棕化的主要作用是粗化铜面并在铜表面形成一层均匀的棕色有机金属转化膜以增强多层板层结合力。
棕化的主要成分为苯并三唑、硫酸和水。
其反应机理如下:2Cu+H2SO4+H2O2+nA+nB→CuSO4+2H2O+Cu[A+B]n有机物A为:乙二醇单异丙基醚;其作用机理:1、参与半固化片环氧树脂聚合;2、与含N的杂环化合物B和金属铜形成化学键。
杂环化合物B为:苯并三唑其作用机理:1、与基体铜结合;2、通过有机物A的桥键与环氧树脂结合;3、化合物B分子之间通过Cu2+以配位键形式连接,增加了棕化层的厚度和平整性。
7.2烘板烘板的作用主要体现在以下两个方面:对于层经过电镀的板棕化前烘板的主要作用为去除水分,此阶段的温度和时间可以按参数上限设置。
对于棕化后烘板的主要作用为①去除水分,防止后续层压板因层芯板吸潮引起的7.3叠合(含预叠)棕化后需要对层芯板进行预叠和叠合,预叠是通过邦定或铆合等定位方式把层芯板、半固化片按ERP的叠层结构指示信息固定起来,防止后续压合过程滑动出现层间偏位。
铆合方式是通过铆钉将层芯板、半固化片固定起来,而邦定方式则通过高频电磁波穿透层铜网,加以邦定头施加的热量将半固化片熔合,在一定的压力下将层芯板与半固化片固定在一起,其中邦定方式的定位作用强于铆钉铆合方式。
对层芯板比较薄,对位精度要求高的板进行预叠时,优先采用邦定+铆合方式生产,而对超出邦定能力围的、对位精度要求不高的板则可采用铆合方式生产。
叠合是以钢质载板为底盘,放入一定数量的缓冲材料,中间一层分离钢板一层预叠板,预叠板与预叠板、钢板与钢板之间上下左右需对准,再放入牛皮纸及盖板即完成一个开口的组合。
叠合产品实现的控制点为层间对位、板面清洁,基本原理有物料作用原理、设备作用原理等。
7.3.1物料作用原理7.3.1.1铆钉7.3.1.2钢板钢板的主要作用在于防止铜箔皱褶凹陷及拆板容易,影响该作用的因素及趋势如下:7.3.1.3缓冲材料缓冲材料的主要作用在于均热均压、防滑。
一般的缓冲材料为牛皮纸。
特殊的缓冲材料有如:硅胶片(主要用于冷板压合,其可压缩性、均衡压力、温度的性能均优于牛皮纸)、pacopad(用于铝板厚度较大、形状较为复杂的冷板压合,可防止局部溢胶过多,其导热性及可压缩性均优于硅胶片)。
影响缓冲材料作用(主要为牛皮纸)7.3.1.4蜡布蜡布的主要作用在于清洁铜箔和钢板,避免出现层压杂物和铜箔起皱缺陷。
蜡布质量不佳,掉蜡在铜箔上,引入新的杂物,多次使用后蜡布变脏会影响清洁效果,需及时更换。
7.4压合压合是在高温高压条件下利用树脂(半固化阶段)的流变行为,完成对层线路空隙的填充,使各线路层粘结在一起,获得多层印制电路板。
产品的控制为层压板外观、厚度、层对位精度、热性能、翘曲度,基本原理有物料作用原理、设备作用原理、产品设计影响。
7.4.1物料作用原理7.4.1.1半固化片半固化片作用是粘结各层线路层,并起绝缘层的作用。
其主要成分是树脂、填充物和玻璃纤维布。
(1)树脂是热固性材料,应用到PCB主要有酚醛树脂、环氧树脂、聚四氟乙烯等,目前常用的是环氧树脂。
环氧树脂是泛指分子中有两个或两个以上环氧基团的有机高分子化合物,其环氧基团可以位于分子链的末端、中间或呈环状结构。
由于活泼环氧基团的存在,环氧树脂与固化剂在一定的条件下发生固化反应,生成立体网状结构的产物,从而显现出各种优良的性能。
最常用的环氧树脂是由溴化的丙二酚制成的耐燃性环氧树脂,称为FR-4环氧树脂。
其各组分的作用:①单体:常见的有双酚A、环氧氯丙烷等,与固化剂发生交联反应,成为固体聚合物。
如双酚A型单体结构如下:②固化剂:双氰胺、PN等固化剂,在有促进剂下和树脂发生固化反应。
常见的固化反应机理如下:双氰胺作为固化剂时:PN作为固化剂时:③促进剂:2-甲基咪唑等,加快单体与固化剂的交联反应④溶剂:二甲基甲酰胺、丙酮等.(2)填充物:碳酸钙、氢氧化铝等,其主要作用是增加阻燃效果、调整Tg和CTE值。
(3)玻璃纤维布:一种无机物经过高温融合后冷却成一种坚硬的非晶态物,然后由经纬纱纵横交织的补强材料。
一般采用的玻璃纤维布均是采用平纹布。
相比其它布(如斜纱、锻纹等组织)具有断裂强度大,尺寸稳定性好,不易变形,重量厚度均匀的优点。
玻璃纤维布的基本性能有:经纬纱种类、织布密度、厚度、单位面积重量及断裂强度等。
半固化片在压合过程中,存在三个阶段:整个压制升温过程,是B-stage树脂从难以流动的粘弹态逐渐变为胶凝状的变化过程。
在这个过程中,树脂于高温下进行熔融和流动,并同时完成对玻璃纤维空隙的进一步浸润且赶出气泡。
树脂的流动性逐渐增加,随着分子链的不断增长,随即发生交联作用,而随着交联程度的不断增加,它的流动性又成指数规律下降,最后达到不再流动的固化态。
多层板生产中,半固化片必须满足填隙充分,排除空气及挥发物,保留一定的介质层厚度,主要的影响因素7.4.1.2铜箔铜箔是生产多层印制线路板不可缺少的原材料,是外层图形制作的基础。
按制造方法分为压延铜箔与电解铜箔。
由于电解铜箔对基材的附着力较强,故刚性板一般使用电解铜箔。
1铜箔品质指标铜箔品质指标主要包括铜箔的剥离强度、粗糙度、延展性、耐化学腐蚀性及抗氧化性。
剥离强度低,线路易剥落,焊接过程焊盘易翘起甚至剥离;粗糙度太低,剥离强度难保证,粗糙度太高,信号传输损耗大;耐化学腐蚀性差,湿流程加工过程易受药水侵蚀导致剥离强度下降;延展性低,热涨冷缩过程铜箔与基材易分离或铜箔易断裂。
2 铜箔表面清洁铜箔的表面清洁状况决定压合后板面有无压痕、有无起皱等外观问题。
7.4.1.3离型膜离型膜是具有不粘性能和高温蠕动形变性能的塑料薄膜,其在压合过程中的主要作用是防粘、阻胶。
一般用于盲孔板、局部混压板及一些散热冷板的压合。
特殊离型膜如pacovia则用于局部混压,其阻胶性能优于一般的物料类型优点缺点离型膜1、阻胶性能好、盲孔板后续板面处理更容易;2、成本低。
耐温性能较铜箔差,不适宜Tg>210℃的高Tg板。
铜箔耐温性好,可用于高Tg板。
1、成本高;2、阻胶性能差,盲孔板后续板面处理需过除胶。
序号影响因素具体影响1 离型膜品质指标离型膜品质指标主要包括耐温性、阻胶效果,耐温性差,离型膜易熔化、破损导致流胶至钢板上,阻胶效果差,板面流胶量过多则对后续板面除胶难度大。
2 离型膜表面清洁离型膜的表面清洁状况决定压合后有无压痕等缺陷外观问题。
7.4.2设备作用原理压机大多都采用液压系统提供各开口的闭合与加压。
即压机顶部的热盘固定于压机的主体结构上,其它各开口的热盘由液压系统推动闭合与加压。
如下图所示:序号设备系统作用及影响1 机体系统机体系统是压合的场所,影响压机机体系统对压合作用的因素是热盘平整度,其直接影响压合板的厚度均匀性及翘曲度。
2 加热系统加热系统主要提供压机压板时所需要的热能,要求其满足材料固化反应的温度条件。
热煤油加热工作原理是在热盘中加设油管,先将热煤油在机外的加热交换器进行加7.4.3产品设计影响7.5钻靶、铣边钻靶、铣边的作用是利用基材和铜透光性能差异及X-Ray的穿透性原理(P3为CCD抓靶)进行钻靶,进而通过机械加工获得标准尺寸的层压板。
为了满足钻靶、铣边的不同要求和得到尺寸精度良好的层压板,必须选择合适的钻设备名称作用原理影响因素钻靶机利用基材和铜透光性能差异及X-Ray的穿透性原理(P3为CCD抓靶)进行钻靶,为铣边、钻孔提供定位孔。
光学靶标如图:1、钻靶精度,其影响定位孔精度。
定位孔精度不好,后续钻孔精度无法保证。
2、测量精度,其影响涨缩测试的准确性。
涨缩测试不准确,钻带准确性差,易致整板孔偏。
铣边机利用钻靶机钻的三个定位孔通过机械加工得到标准尺寸的层压板。
铣边转速、行速是影响铣边效果的主要因素。
铣边转速及行速控制不佳时,铣边精度差,铣边时容易滑板,导致铣边进图形,同时毛刺多,严重时引起沉铜孔铜瘤。
8、工艺原则8.1.参数设定原则(具体参数见附件一《层压工序生产参数表》)参数类别项目设定原则设备参数酸洗压力用棕化线最大制作尺寸的板,按正常参数过一遍,要求板面无氧化物。
碱洗压力用棕化线最大制作尺寸的板,按正常参数过一遍,要求板面无手指印等油迹。
水洗压力通过实验室对棕化线离子污染度测试结果设定,保证棕化后离子污染度合格。
烘干段温度用棕化线最大制作尺寸的板,按正常参数过一遍,要求板面无水迹。
药水参数浓度根据药水特性及反应速率来设定,保证实验室所测棕化线微蚀速率在标准围之。
温度操作参数传送速率保证微蚀量在标准围。
放板间距保证不叠板。
参数类别项目设定原则设备参数温度保证烘板后除水效果良好,且棕化膜不氧化。
操作参数时间保证烘板后除水效果良好,且棕化膜不氧化。
叠板高度保证各层均能达到要求的烘板温度。
参数类别项目设定原则设备参数铆钉机压力保证铆钉铆合时开花均匀且紧固,层间无滑移。
邦定机能量保证半固化片和层芯板熔融后紧固,无滑动。
磨钢板机电流参数通过用磨钢板机最大生产尺寸的覆铜板调整好磨痕标准围,再放入同等厚度的钢板检验磨刚板效果。