树脂工艺品摆件怎样去除气孔
树脂工艺品生产中常见的问题及处理技巧

有易燃有易燃、、易爆气体进入会引起爆炸易爆气体进入会引起爆炸,,造成严重后果造成严重后果。
所以所以,
,空压机的进气口应选择在车间外面,空气新鲜,流通好的地方。
总之,工艺品厂生产区域中,应严禁烟火,尤其是流动吸烟危害极大总之,工艺品厂生产区域中,应严禁烟火,尤其是流动吸烟危害极大,
,务必要认真管理到位,一点点疏忽就有可能酿成大祸,千万不可麻痹大意必要认真管理到位,一点点疏忽就有可能酿成大祸,千万不可麻痹大意。
树脂工艺品制作流程
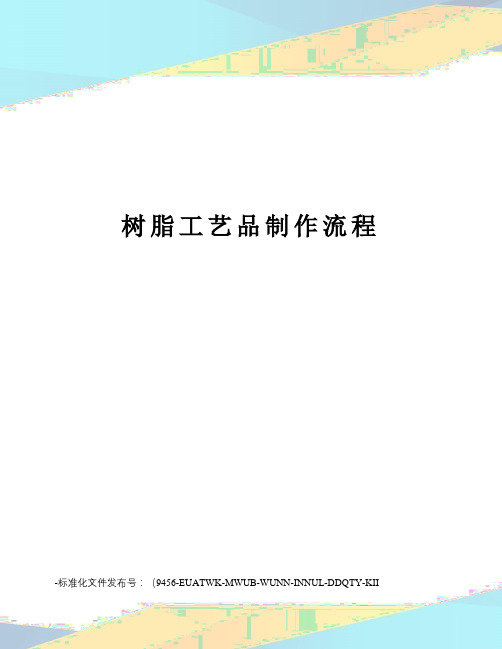
树脂工艺品制作流程-标准化文件发布号:(9456-EUATWK-MWUB-WUNN-INNUL-DDQTY-KII
树脂工艺品制作流程
1.搅拌
根据模具大小、产品数量,先将不饱和树脂称量出来,倒入调料桶,先将固化剂加入不饱和树脂内,进行充分搅拌,再加促进剂进行搅拌,充分混合。
2.倒模
模具应摆放在(水平状态)工作台面上,把模具内模面应清洗干净,用小勺舀料浆一勺一勺的缓缓倒入,不可倾倒,要从高点倒进,使其自然流淌.
3.抽气
把已经灌注满的模具搬移至强力真空压缩机,把树脂料浆里面因搅拌时产生的多余气泡挤走,否则,成品后会有气孔。
4.脱模
料浆倒入模具后经1-2小时即可凝固,凝固后即可脱模
5.打磨
脱模后的毛(粗)胚,需要经人手在砂带机上磨平进浆水口;用小型机械工具修整合模线;然后用240号砂纸对整个产品表面进行打磨。
再重复用600号砂纸细磨平滑。
防止气孔产生的措施

防止气孔产生的措施气孔是指在材料或工件中由于冷却过程中产生的气体无法完全排出而形成的孔洞。
气孔对材料的性能和工件的质量都会产生负面影响,因此在工业生产中需要采取一系列的措施来防止气孔的产生。
本文将介绍几种常用的防止气孔产生的措施。
1. 合理设计模具和工艺在工业生产中,模具的设计和工艺的选择对防止气孔产生起着决定性的作用。
首先,模具的设计应该考虑材料的流动性和气体的排出。
合理的模具设计可以在充填过程中顺利排出气体,从而避免气孔的产生。
其次,适当的工艺参数,如注塑温度、压力和速度等也应该合理选择,以确保材料在充填和冷却过程中的性能稳定,从而降低气孔的产生。
2. 控制材料的含气量材料中的含气量是产生气孔的主要因素之一。
因此,在工业生产中需要采取一些措施来控制材料的含气量。
首先,可以通过提前热处理材料来去除大部分的气体。
其次,在原材料的配料和搅拌过程中要保持材料的均匀性,避免产生空隙和气泡。
最后,在材料的加工过程中,如挤出、压缩和注塑等,也需要控制材料的温度和压力,以防止气体的产生和混入。
3. 采取适当的排气措施在材料充填的过程中,必须排除材料中的气体,以避免气孔的产生。
为了实现这一目标,可以采取多种适当的排气措施。
首先,可以在模具中设置气孔或导流槽,以便气体可以顺利排出。
其次,可以通过调整注塑机的速度和压力来促使气体的被压出。
另外,还可以使用真空排气系统来加速气体的排出。
综合运用这些排气措施可以最大限度地降低气孔的产生。
4. 控制冷却过程冷却过程是决定工件质量的关键环节之一。
如果冷却不均匀或过快,就容易产生气孔。
因此,在工业生产中应该控制冷却过程,以保证工件的均匀冷却。
首先,可以通过合理设置冷却水的流量和温度来控制冷却速度。
其次,在冷却过程中可以采取多种方式,如喷水冷却、液氮冷却等来加快冷却速度。
此外,还可以合理设计冷却时间和冷却方式,以确保冷却的充分性和均匀性。
5. 质量控制和检测质量控制和检测是防止气孔产生的必要手段。
铸造气孔解决方法

铸造气孔解决方法一、背景介绍铸造是一种常见的制造工艺,但在铸造过程中,气孔是一个常见的缺陷。
气孔会降低铸件的强度和密封性,影响其使用寿命和品质。
因此,解决气孔问题对于提高铸件质量至关重要。
二、气孔的成因1.金属液中溶解氧过多2.熔融金属流动速度过快3.模具表面粗糙或有杂质4.金属液中含有挥发性物质三、预防措施1.减少金属液中溶解氧含量:可通过加入还原剂、增加保温时间等方法来实现。
2.控制熔融金属流动速度:可通过调整浇注系统设计、增加浇注口数量等方法来实现。
3.改善模具表面状态:可通过精密加工模具表面、清洁模具表面等方法来实现。
4.减少挥发性物质:可通过改变熔融金属组成、使用合适的保护剂等方法来实现。
四、处理方法1.机械处理法:包括打磨和修补。
打磨可通过砂轮、砂带等工具进行,修补则可采用填充剂填充气孔。
2.热处理法:包括退火和时效。
退火可使气孔内部的氧分子扩散到金属液中,使气孔逐渐消失;时效则是利用金属在高温下的再结晶过程来消除气孔。
3.化学处理法:包括浸泡、电解和喷涂等方法。
浸泡可将含有铝的溶液浸泡在铸件表面,形成一层保护膜以防止氧化;电解则是利用阳极溶解作用来填补气孔;喷涂则是将特定材料喷涂在铸件表面,形成一层密封膜。
五、常见问题及解决方法1. 气孔数量较多:应从预防措施入手,加强金属液净化、控制熔融金属流动速度等。
2. 气孔回火后仍存在:应采取机械处理法或化学处理法进行修复。
3. 铸件表面存在小气孔:可采用电解或喷涂等化学处理法进行修复。
六、结论气孔是铸造过程中常见的缺陷,但通过预防措施和处理方法,可以有效地减少或消除气孔问题。
在实际生产中,应根据具体情况采取不同的解决方法,以提高铸件质量和使用寿命。
气孔问题如何解决,你可了解?
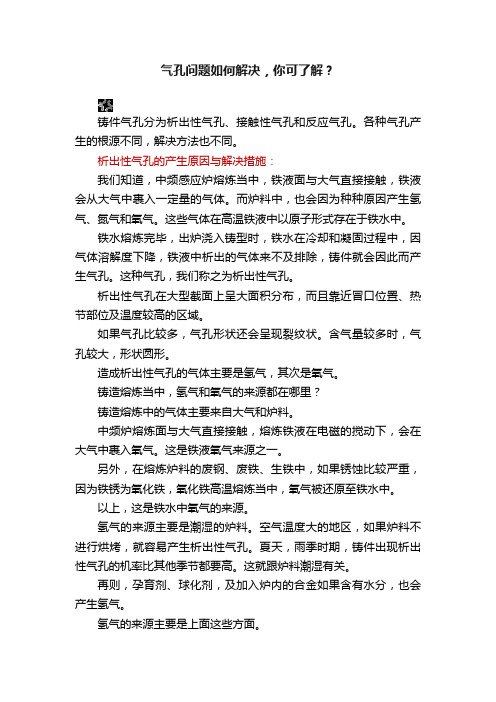
气孔问题如何解决,你可了解?铸件气孔分为析出性气孔、接触性气孔和反应气孔。
各种气孔产生的根源不同,解决方法也不同。
析出性气孔的产生原因与解决措施:我们知道,中频感应炉熔炼当中,铁液面与大气直接接触,铁液会从大气中裹入一定量的气体。
而炉料中,也会因为种种原因产生氢气、氮气和氧气。
这些气体在高温铁液中以原子形式存在于铁水中。
铁水熔炼完毕,出炉浇入铸型时,铁水在冷却和凝固过程中,因气体溶解度下降,铁液中析出的气体来不及排除,铸件就会因此而产生气孔。
这种气孔,我们称之为析出性气孔。
析出性气孔在大型截面上呈大面积分布,而且靠近冒口位置、热节部位及温度较高的区域。
如果气孔比较多,气孔形状还会呈现裂纹状。
含气量较多时,气孔较大,形状圆形。
造成析出性气孔的气体主要是氢气,其次是氧气。
铸造熔炼当中,氢气和氧气的来源都在哪里?铸造熔炼中的气体主要来自大气和炉料。
中频炉熔炼面与大气直接接触,熔炼铁液在电磁的搅动下,会在大气中裹入氧气。
这是铁液氧气来源之一。
另外,在熔炼炉料的废钢、废铁、生铁中,如果锈蚀比较严重,因为铁锈为氧化铁,氧化铁高温熔炼当中,氧气被还原至铁水中。
以上,这是铁水中氧气的来源。
氢气的来源主要是潮湿的炉料。
空气温度大的地区,如果炉料不进行烘烤,就容易产生析出性气孔。
夏天,雨季时期,铸件出现析出性气孔的机率比其他季节都要高。
这就跟炉料潮湿有关。
再则,孕育剂、球化剂,及加入炉内的合金如果含有水分,也会产生氢气。
氢气的来源主要是上面这些方面。
所以,要避免产生析出性气孔,我们就要在源头上进行控制。
炉料选择,合金选择时,尽量避免多锈材料。
夏天,或空气湿度高的地区,对炉料和合金进行必要的烘烤。
这样就能在源头上杜绝氧气和氢气的来源。
材料上防范是一方面。
除了在材料上面防范,在熔炼过程及浇注过程中,还需要采取其他一些措施,才能杜绝析出性气孔产生。
一、如果铁液含气量高,在熔炼时,就要适当延长铁液高温静置时间,以利于铁液中气体排除。
树脂工艺品需要的材料及相关工艺问题解决方法
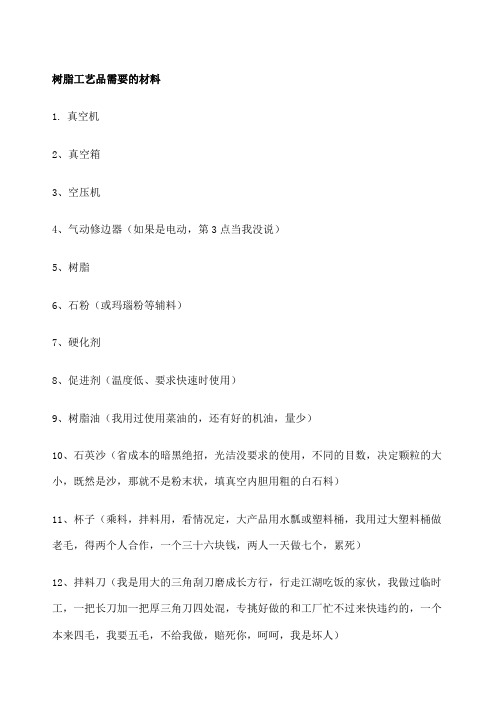
树脂工艺品需要的材料1.真空机2、真空箱3、空压机4、气动修边器(如果是电动,第3点当我没说)5、树脂6、石粉(或玛瑙粉等辅料)7、硬化剂8、促进剂(温度低、要求快速时使用)9、树脂油(我用过使用菜油的,还有好的机油,量少)10、石英沙(省成本的暗黑绝招,光洁没要求的使用,不同的目数,决定颗粒的大小,既然是沙,那就不是粉末状,填真空内胆用粗的白石料)11、杯子(乘料,拌料用,看情况定,大产品用水瓢或塑料桶,我用过大塑料桶做老毛,得两个人合作,一个三十六块钱,两人一天做七个,累死)12、拌料刀(我是用大的三角刮刀磨成长方行,行走江湖吃饭的家伙,我做过临时工,一把长刀加一把厚三角刀四处混,专挑好做的和工厂忙不过来快违约的,一个本来四毛,我要五毛,不给我做,赔死你,呵呵,我是坏人)13、色浆(看需要)14、油漆(看需要)15、天那水16、松节水17、仿古油18、亮油(配金粉)19、喷漆器(大产品无要求的,喷底色用大号的,小产品喷脸用小号的)20、美工刷、美工笔(视产品大小结构要求选,画眉毛要求较高)21、烧碱(洗产品用,不知道叫不叫烧碱,好象是,忘了看学名,自己去考证)22、四方塑料框(装产品用)23、推车(转移用)24、一种补坯用的粉末,我叫它轻粉25、硅胶(模具用的,当我没解释)26、硅胶固化剂27、医用纱布(蒙模具用的,位于硅胶中心层,增加抗拉强度,防止撕裂)28、橡皮泥(开模用的)29、板料(开模用的)30、石膏(具体叫什么不清楚,一种像水泥一样的东西,不是水泥,做外模用的,有点重,小东西用,大东西还如果一个老毛的像用石膏做外模,我可没那么强壮)31、纤维(树脂外模用,增加强度)32、筷子(或木条,石膏外模用,增加强度)33、锋利的刀片(模具难点切口用)34、胶水(将原坯固定在板料上)出现水纹的原因1、新模具。
一半新模具要放在太阳下晒晒,当然石膏外模也要,如果没有太阳,那就用点吹风,别吹烧了,冷天气,每天早上预热一次,别太热了哦!2、硬化剂。
非常实用的树脂工艺品制作步骤
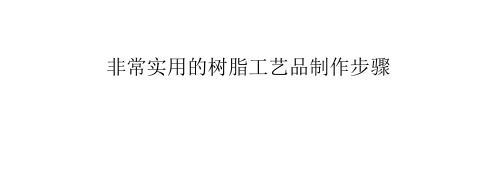
zfc0e 树脂工艺品厂
树脂工艺品成型:按照产品的实际重量称好需
要调配的树脂分量,再加入同比例的固化剂搅拌均
匀,然后把大约三分之一调配好的树脂倒入干净的
模具内,连同剩余没有倒入模具的树脂的容器同时
放到真空箱内抽真空,这里需要注意抽空完后放气
务必要缓慢,从真空箱的透视镜中看到模具内的树
Байду номын сангаас
脂气泡慢慢消失,直到模具内气泡完全消失殆尽后
才能把进气阀完全打开,放完最后的空气。然后把
模具从真空箱中取出来,放在凭证的台上,再把剩
余抽空完的树脂缓慢的倒入模具中。如果这样操作
产品固化后还是有小气孔,那么可以在树脂内加入
一定比例的苯乙烯稀释树脂。
胚体的表面处理:抛光是树脂工艺品的一个非
常关键工艺,产品从模具取出后,需要等到完全固
化,然后用碱水清洗表面的污垢,泡碱清洗干净后。
取出后再用目数较细的砂纸把整个产品表面打砂,
模线的地方需要处理仔细,要求产品表面光滑。最
后用光机进行产品表面的抛光处理。
产品表面喷亮油上光:在抛光好的产品上用喷
枪在产品表面照喷一层亮光漆(可以用亮光清漆或
者是亮光的金油)待油漆完全固化后,检查产品有
没有遐思,如果有遐思的地方需要返工处理。检查
没有问题后就可以进入组装和包装环节。
环氧树脂气泡消除方法
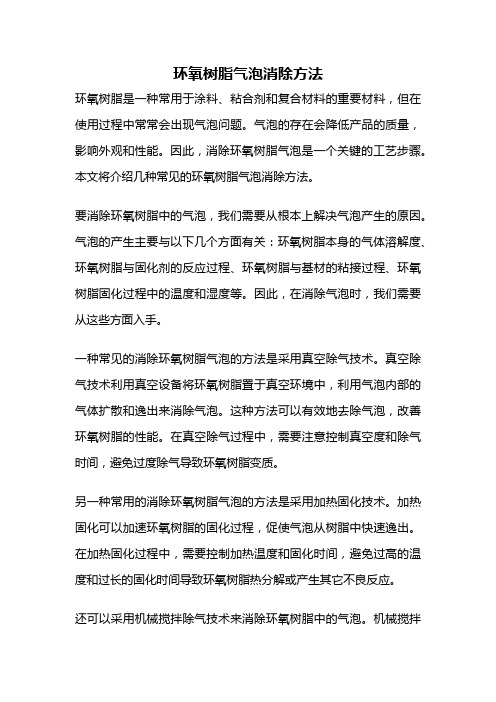
环氧树脂气泡消除方法环氧树脂是一种常用于涂料、粘合剂和复合材料的重要材料,但在使用过程中常常会出现气泡问题。
气泡的存在会降低产品的质量,影响外观和性能。
因此,消除环氧树脂气泡是一个关键的工艺步骤。
本文将介绍几种常见的环氧树脂气泡消除方法。
要消除环氧树脂中的气泡,我们需要从根本上解决气泡产生的原因。
气泡的产生主要与以下几个方面有关:环氧树脂本身的气体溶解度、环氧树脂与固化剂的反应过程、环氧树脂与基材的粘接过程、环氧树脂固化过程中的温度和湿度等。
因此,在消除气泡时,我们需要从这些方面入手。
一种常见的消除环氧树脂气泡的方法是采用真空除气技术。
真空除气技术利用真空设备将环氧树脂置于真空环境中,利用气泡内部的气体扩散和逸出来消除气泡。
这种方法可以有效地去除气泡,改善环氧树脂的性能。
在真空除气过程中,需要注意控制真空度和除气时间,避免过度除气导致环氧树脂变质。
另一种常用的消除环氧树脂气泡的方法是采用加热固化技术。
加热固化可以加速环氧树脂的固化过程,促使气泡从树脂中快速逸出。
在加热固化过程中,需要控制加热温度和固化时间,避免过高的温度和过长的固化时间导致环氧树脂热分解或产生其它不良反应。
还可以采用机械搅拌除气技术来消除环氧树脂中的气泡。
机械搅拌可以通过剧烈的搅拌运动来破坏气泡的表面张力,使气泡快速破裂和逸出。
在机械搅拌过程中,需要注意搅拌速度和时间的控制,避免过高的速度和过长的时间导致环氧树脂的过度剪切和变质。
还可以采用添加消泡剂的方法来消除环氧树脂中的气泡。
消泡剂是一种能够降低液体表面张力的物质,可以有效地破坏气泡的表面张力,使气泡快速破裂和逸出。
在使用消泡剂时,需要注意添加剂的种类和用量的选择,避免过量添加剂导致环氧树脂性能的下降。
消除环氧树脂中的气泡是一个关键的工艺步骤。
我们可以采用真空除气、加热固化、机械搅拌和添加消泡剂等多种方法来消除气泡。
在具体操作中,需要根据环氧树脂的特性和工艺要求选择合适的方法,并注意控制各个参数,避免产生其它问题。
树脂砂铸造铸件产生气孔的原因及防止

树脂砂铸造铸件产生气孔的原因及防止概述:面对不断增长着的生产优质铸件的压力,同时又面临缺少有专长的劳动力的局面。
时至今日,国内越来越多的公司(或企业)选择由粘土砂干型铸造工艺转为呋喃树脂砂铸造工艺。
与粘土砂干型铸造工艺相比,呋喃树脂砂铸造工艺具有下述优点:铸件表面质量好、尺寸精度高、废品率低,适用范围广、对工人技术水平要求低,大大减轻了工人的劳动强度和改善工作环境,生产率提高40-60%。
但在生产过程中,也存在着一些问题,如果不加以重视和解决,势必会带来不必要的经济损失。
因此,我们在树脂砂生产技术方面,作了一些工作与探索,为我铸造车间进一步扩大业务,拓宽产品范围,作出了努力,本文主要论述的是树脂砂铸造铸件产生气孔的原因及防止。
关键词:呋喃树脂砂气孔防止气孔是树脂砂铸造中最常见的缺陷之一,采用自硬树脂砂造型工艺尽管铸件气孔缺陷大为减少,但如果工艺、熔炼、浇注等措施不当,气孔缺陷也时有发生。
气孔(气眼、气泡、呛火)主要在铸件内部、表面或近于表面处于有大大小小不等的光滑孔眼,形状有圆的、长的及不规则的、有单个的、也有聚集片的,颜色为白色或带一层暗包,有时覆有一层氧化皮。
目前,比较常用树脂砂铸造灰铸、球铁、合金铸铁、碳钢以及低碳合金钢,都会产生气孔,从铸件的气孔来看,主要有侵入性气孔、析出性气孔、反应性气孔等,它们对铸件的质量有不同的影响,但影响大多比较的大,甚至造成铸件的报废,因此,我们要想方设法的去防止、控制、阻止它的产生。
1 气体的来源在树脂砂铸造铸件中,铸件产生气孔是比较常见的,主要是由各种气体形成的,想要更好的去防止、控制、阻止它的产生,就必须找到气体的来源,它的来源主要在熔炼、铸型、材料、浇注等过程中产生。
1.1 熔炼过程[1]熔炼过程中气体的来源,如表一所示,主要来自各种炉料的锈湿以及周围气氛中的水分、氮、氧、以及Co2、Co、So2、H2及有机物燃烧产生的碳氢化合物等。
表一熔炼过程中气体的来源气体种类气体来源氢1、炉料中的水分、氢氧化合物、有机物。
教你一招对付压铸件气孔的办法!

教你一招对付压铸件气孔的办法!产品含空气?产生气孔的原因有以下几点:一,氢气,原材料里面还有氢气,坩埚及环境还有湿气,导致气体加热产生氢气夹裹在原材料里面,容易产生针状气孔。
二:压射室充满度不高,导致压射室内含空间过大,铝汤在压射前,出现回流撞击,产生涡流。
气泡是模具温度及铝温太高,容易产生气泡。
氢气,压射缸卷起,流道卷起,型腔内压力卷起,水蒸气产生气孔这些都是模具气孔的主因。
产生原因:1、金属液在压射室充满度过低(控制在45%~70%),易产生卷气,初压射速度过高。
2、模具浇注系统不合理,排气不良。
3、熔炼温度过高,含气量高,熔液未除气。
4、模具温度过高,留模时间不够,金属凝固时间不足,强度不够过早开模,受压气体膨胀起来。
5、脱模剂、注射头油用量过多。
6、喷涂后吹气时间过短,模具表面水未吹干。
解决压铸件气孔的办法:先分析出师什么原因导致的气孔,再来取相应的措施。
(1)干燥、干净的合金料。
(2)控制熔炼温度,避免过热,进行除气处理。
(3)合理选择压铸工艺参数,特别是压射速度。
调整高速切换起点。
(4)顺利填充有利于型腔气体排出,直浇道和横浇道有足够的长度(>50mm),有利于合金液平稳流动和气体有机会排出。
可改变浇口厚度、浇口方向、在形成气孔的位置设置溢流槽、排气槽。
溢流品截面积总和不能小于内浇口截面积总和的60%,否则排渣效果差。
(5)选择性能好的涂料及控制喷涂量。
预防措施:1、调整压铸工艺参数、压射速度和高压射速度的切换点。
2、修改模具浇道,增设溢流槽、排气槽。
3、降低缺陷区域模温,从而降低气体的压力作用。
4、调整熔炼工艺、5、延长留模时间,调整喷涂后吹气时间。
6、调整脱模剂、压射油用量。
本文来源:第一压铸,由“易模网”整理发布,版权归原作者所有,内容为作者个人观点,并不代表本公众号赞同其观点和对其真实性负责。
如涉及作品版权问题,请与我们联系,我们将在第一时间删除内容!。
树脂砂铸件气孔及防止措施

一、侵入性气孔及防止气孔的来源:黏结剂呋喃树脂、固化剂分解,浇注系统型腔内气体(空气、水汽等),涂料、铸型中发气物、有机物受高温而气化等。
树脂因其含氮量和水分及有机物量多少及固化剂种类、用量不同,其发气量的多少也不同,在1050℃左右发气进出,短时间内产生N2,H2,O2,CmHn等,此时,砂型、砂芯中气体压力增大而侵入金属液,形成侵入性气孔,针对这一情况,一方面要设法阻止气体侵入金属液,另一方面设法让已侵入的气体排出、逸出。
侵入性气孔防止措施如下:①减少树脂和固化剂加入量,选用发气量小的树脂,控制其他强化剂(如硅烷)等加入量。
②控制涂料的含水量,醇基涂料酒精的含水量。
砂型、泥芯充分干燥后,再刷涂料,最好合箱前用喷灯(枪)烘烤去潮气。
③旧砂再生去除型砂中的尘埃、微粉,以免阻碍通气,注意铸型及泥芯的出气孔和出气通道设置,保证使浇注时产生的气体顺利排气,砂箱四壁要有出气孔。
④浇注系统和浇注工艺有利于排气或抑制外来气体侵入。
a.加快铸型内金属液面上升速度,使型腔中的气体压力增大,有助于抑制界面外气体的侵入;同时也会因型腔内的气体来不及逸出,导致铸件顶部产生浇不足的缺陷。
一般树脂砂浇注系统内浇道总面积要比黏土砂造型的大20%~30%,才能抑制或排除树脂发气量较大,不致使铸件出现侵入性气孔。
b.便于排气。
浇注系统加大和浇注时间的控制,除考虑金属液的特性、浇注系统对型腔内的金属液流动,必须便于气体逸出,在最高处设置集渣包或气冒口或冒口。
比如,长条状机床床身、圆桶体等应采用反雨淋式自下向上便于金属液型腔上面气体向上顶面逸出或排除,平板类应平做斜浇。
c.使已经侵入型腔内金属液的气体尽快形成气泡,从金属液中排出。
d.设置型腔内铸件前端、顶端的溢流冒口或集渣包,使其能容纳混有气泡、夹杂物、渣滓的冷金属液,将其汇集纳入溢流冒口,其主要作用是排除它的气泡、夹杂物、冷金属液于铸件之外。
二、卷裹入气孔及防止浇注时,浇注系统中的金属液流卷携带气泡,气泡随流股进入型腔,或液流冲刷型腔内金属液流动产生湍流、条流、涡流,将气泡卷带人金属流股中,当气泡不能从型腔金属液中排除时,就会使铸件产生气孔,称卷入裹携气孔。
特种印制电路板树脂塞孔及去除工序改善汇总

特种印制电路板树脂塞孔及去除工序改善汇总王劲公司PCB部门5年前在市场和产品方面启动转型,市场主要在军工客户,产品主要在HDI、射频微波、高速等特种印制板,目前基本跨上这个台阶。
公司经营打造以好和快为品牌,生产部门必须围绕这两个字开展所有工作,最终好和快是体现在产品上的质量好、交付快。
特种印制板是过去的叫法,相对于我公司以前没有的材料和工艺来确定,如:(局部)厚金工艺、厚铜蚀刻、厚铜压合、复合介质混压、背钻工艺(数控、蚀刻)、减铜工艺、真空树脂塞孔工艺、树脂去除工艺、填孔电镀工艺、埋器件工艺、台阶工艺、激光切割工艺等,目前我公司特种印制板基本由FR4、高频高速材料和这些工艺的组合加工而成。
按照公司安排对生产现场开展改善活动的要求,本人从生产质量问题最多、最不可控、最不稳定的工艺工序,特种产品基本上都会用到的工艺工序、工艺时间长的工艺工序入手,从年前一周到今天(2022年2月25日)用时20来天,对树脂塞孔、树脂去除、背钻孔清洁、铜浆塞孔、减铜工艺等进行了阶段性较为彻底的改善(目前没有文件化和标准化),仍有许多继续改善的空间。
一、该工序存在的质量问题及带给下工序的质量问题:板面大量凹坑、印制板尺寸变化大并且不一致、铜箔打穿造成局部无铜、铜箔厚度不一导致腐蚀报废、塞孔凹陷明显、塞孔树脂上部分无铜、塞孔周边铜层起泡、铜浆塞孔不平整等。
因该工序质量问题带来的整体交期无法确定、交期延误、影响其他工序质量及加工时间(侧腐蚀、腐蚀不干净等报废,因板材形变带来的一种印制板做成了几种印制板给工程、数控、丝印、文字、成型等工序增加了较多的工作量和质量隐患);质量问题带来的现场人员士气低落(质量不可控,不能做、不愿做、不敢做的心态较为明显,产品因此在现场出现停顿等待情况明显,管理人员对交期无法确定并且不能承诺);成本的增加(材料、能源、工时等没有统计,客户的信心)等。
材料供应商多次到厂未能解决问题,结合自己对我们的人机料法环测等特性的了解,改善活动主要围绕人、机、料、法、测来开展,并且会涉及到上下工序的一部分改善活动(关联工序改善会继续,如数控背钻、压合等),其改善的机理及要求在改善活动中对相关人员进行了培训,每一个改善背后的机理会在以后的文章中阐述,同时部分改善可以申请专利、可以为工厂二期建设提供参考和指导。
分析注塑中产生的气泡-空洞-水纹解决方案

分析注塑中产生的气泡,空洞,水纹解决方案The appearance of bubbles, voids, sinks or blisters on an injection-molded part make up the most significant causes for part rejects due to cosmetic requirements. These troublesome "features", although not the most common of problems wheninjection-molding parts, can inhibit part performance and are problematic to solve.Bubbles are either pockets of trapped gas or vacuum voids. It is important to determine which type of bubble exists in your part to more quickly pinpoint the source and determine the correct adjustment to make. A simple test of warming the part area containing the bubble until it softens can be used to determine its bubble type as trapped air or void. With the test, if there is gas trapped in the bubble, the gas will warm up and want to expand the bubble as the part softens. If there is no air in the bubble and a vacuum void exists, the bubble will collapse due to the atmospheric pressure pushing on the softened walls of the part. A hot air gun is best to heat the area, a small lighter is next, and a torch if you know what you are doing.Trapped Air IssueTrapped air is a root cause of bubbles as well as blisters. Trapped gas may stem from flow front issues such as converging fronts, or jetting, to equipment and production problems such as non-vented core pins, poor venting, too much decompression, or resin degradation. The air or gas may appear from water vapor, volatiles from the resin, or decomposing by-products. The air may be trapped in ribs, threads or non-ventedprojections off the nominal wall. Melt flow pattern is a major cause of bubbles. Processors should examine each parts flow pattern via short shots to see if the plastic flow front is coming around on itself. Note if there is a race-tracking effect or jetting that can cause air to become trapped in the polymer.Observe flow path for back flow or trapped air in blind ribs. Examine the part to determine if the rib or support areas of a part are covered before part is completely filled. If it is a flow pattern issue, run a short shot molding sequence, changing the transfer position or shot size to make various sized short shot parts ranging from 10 percent to 95 percent of the full part. Use this to find out where and how the bubble occurs. This test requires the process to be velocity controlled for the first stage (injection). This cannot be done if the first stage pressure and velocity is reduced.Other causes for trapped air leading to bubbles or blisters include inadequate venting, material flow pattern design, and gas traveling across the part surface during the fill or pack stage. Melt flow issues may indicate a need to change the gate location to avoid race tracking, trapping air or to promote uniform fillingEquipment can also be a cause for bubbles. If you are working with a hot runner tool it is possible that a venturi effect can suck air from between the plates into the hot runner, pulling air into the melt, forming a bubble. To check for this the tool must be disassembled, and a bluing agent is applied near the drops, being careful not to apply any in the flow path.If the bluing agent shows up in the part then you have found the source of the problem.One can also examine the purging of a normal shot to see if the bubble originates from the barrel or screw. General-purpose screws with dimensions of 18:1 L/D or lower can be the culprits for a bubble or blister. One solution is to raise the backpressure to 1000 to 1500 psi melt pressure. Another solution may be to pull a vacuum on the mold just before injection, so that air is pulled out. Moisture in the molding system can also be a source of trouble.Tool venting is another big issue, so vent properly or use a porous steel to eliminate gas traps. Check the number of vents as well as vent depth. Check vents with pressure sensitive paper. Clean all parting line and core vents. This can prevent the opportunity for trapping air.Avoiding Voids and SinksA void occurs during cooling, usually in thick sections of the part where there can be a significant cooling rate difference in the material forming the core and skin of the part. A sink is a depression impacting the surface of a part that does not mimic the mold steel surface.Voids and sinks are signs of internal stress and are warning signs that the part may not perform as required.Insufficient plastic can be a main reason for sinks or voids so packing more plastic into thecavity is recommended. Molders should have a consistent cushion on the press, making sure you are not bottoming out the screw. You should go for higher pressures in thehold/pack stage and longer stage time. To solve voids or sinks, trial slow fill rates, the use of gas counter-pressure, and increasing backpressure. You can open the gate for longer gate seal times to allow more packing during the second stage. Molders can also try reducing the melt temperature.Mechanically, you can increase the runner diameter. You should determine where the sink is. Is it near the gate or farther down the flow part? If near the gate, check the gate seal time. If it is farther down the flow part, increase injection speed to decrease viscosity and allow more packing pressure.Another approach to eliminating voids or sinks is to "thin-up" the nominal wall. Thicker is not always stronger in plastic parts. Thick nominal walls should be redesigned with ribs if strength is needed. This will save plastic and cycle time also. Molders can core out the thick section if possible. Changing the gate location to fill thicker areas in the mold first, this may allow more polymer into the part (before the gate freezes). Molders may also try raising the mold temperature significantly and/or ejecting the part sooner, which can avoid voids by allowing the outside walls to collapse during cooling.For sinks, users may try cooling the part in water or between aluminum sheets rather than air. Here, inner section of the thick-sectioned part can reheat or re-melt the outsidesurface of the part once ejected, allowing the surface to collapse. However, this may cause a vacuum void. You might be able to diminish the vacuum void by not cooling the part surface and keeping it warm by placing on wood or insulating foam. One should expect sinks with this approach.Be Aware of BlistersBlisters, a thin film of plastic that bubbles up from the part surface, can also ruin the aesthetics of a part. Like bubbles they can be caused by gas traveling across the surface during fill or pack, or due to trapped air issues (inadequate venting, melt flow pattern or screw L/D), and the solutions are the same. However, blisters can also originate from process problems or degradation of the resin or additive package. Delamination is a serious part defect.Excessively high injection rates can cause blisters, as they can develop a highly oriented thin layer or film on the surface of a molded part. Sometimes sticking tape to the part and lifting it pulls this layer off. Try injecting the melt at a slower rate. High temperatures of steel near the gate can cause blisters also and should be made lower if possible. If the decompression of the screw is excessive, it is possible that air will be pulled into the nozzle and remains trapped. This air pocket enters the melt stream during nozzle contact with the sprue. If using a hot runner system, at injection, the trapped air is moved through the hot runner system and can create the bubble. In a cold runner system the air is ahead of the flow front and gets vented.Gas can be created by the degradation of the resin or additive, so try a new lot of materialand/or use virgin material. It is best to check the melt temperature process rangerecommended by the resin supplier. Molders should minimize material residence time,and one way is to use the correct barrel size for the shot.Be sure that the plasticating screw be at least 20:1 L/D. If you are require longer cycletimes and higher backpressure to reduce the occurrence of blisters, then it is possibly ascrew design issue.消除气泡,空洞,水槽和水泡对注塑成型零件的气泡,空洞,水槽或水疱的出现弥补了部分因拒绝整容要求最显著的原因。
知识篇——气孔常见问题多,了解气孔特征,10点入手解决铸件气孔

知识篇——气孔常见问题多,了解气孔特征,10点入手解决铸件气孔铸造网络平台 2022-02-23 11:49在铸件生产过程中都会出现各种各样的缺陷,影响铸件质量,甚至让铸件直接报废,气孔就是其中比较常见的,无论铸铁件、铸钢件还是合金铸件都可能出现气孔的问题。
气孔特征皮下气孔大多数情况下是由多个直径为1-3mm的小气孔,成串横列于铸件表面以下1-3mm处。
气孔内壁光滑,呈均匀分布在铸件上表面或远离内浇道的部位,但在铸件侧面和底部也偶尔存在。
一般为圆球形、团球形、泪滴形、长针形。
在铸态时,皮下气孔不易被发现;但是,铸件经热处理后,或是经机械加工后则显露。
图片形成的原因以及防治措施1、控制铁液质量(1)控制残留铝量湿型球墨铸铁件的危险残留铝量为0.03%-0.05%,此时会出现皮下气孔,小于0.03%时,一般不会出现。
在不影响金相组织的前提下,浇注前添加0.2%以上的铝,就可以消除皮下气孔。
但是铸铁中的铝主要来自孕育剂,湿型孕育的球墨铸铁件,在铁液中加入过多的硅铁孕育剂时,则是铸件产生皮下气孔的原因之一。
(2)控制钛量铸铁中残留铝和残留钛都有时,过量的残留钛会使铸铁产生严重的皮下气孔。
球墨铸铁件残留铝量小于0.03%时,一般不出现皮下气孔,若此时残留钛含量超过0.01%时,则会产生皮下气孔。
钛铝共同作用下,加剧界面水气还原,使得界面铁液含氢量更高,更易形成皮下气孔。
残留钛主要来自熔炼炉料生铁锭,应注意生铁锭的含钛量,含钛量高的与低的搭配使用,控制钛量。
(3)减少硫含量锰、硫对于湿型球墨铸铁件,从防止皮下气孔的角度来讲,硫元素是有害元素。
当硫元素含量超过0.094%时容易产生皮下气孔,硫含量越高,出现缺陷的情况越严重。
除此之外,产生的H2S可能会使缺陷更加严重。
球化处理之后产生的氧化物、硫化物渣,清理干净。
否则产生在界面处产生H2S气体也会形成皮下气孔,这种皮下气孔周围的石墨球化不良。
(4)添加稀土元素加入稀土元素能够脱氧、脱硫,提高铸铁液态的表面张力,能够有效的防止皮下气孔的产生。
树脂塞孔常见问题及其改进方法

树脂塞孔常见问题及其改进方法1 对于POFV产品1.1 常见的问题A、孔口气泡B、塞孔不饱满C、树脂与铜分层1.2 导致的后果A、孔口上面没有办法做出焊盘;孔口藏气,芯片贴装吹气,也叫out-gassingB、孔内无铜C、焊盘突起,导致贴不上元器件或元器件脱落1.3 预防改善措施A、选用合适的塞孔油墨,控制油墨的存放条件和保质期,B、规范的检查流程,避免贴片位孔口有空洞的出现。
即便能倚靠过硬的塞孔技术和良好的丝印条件来提高塞孔的良率,但是万分之一的几率也能导致产品报废,有时仅仅因为一个孔的空洞造成孔上没有焊盘而报废实在可惜。
这就只能通过检查来找出空洞的位置并进行修理的动作。
当然,检查树脂塞孔的空洞问题历来也被人们所探讨,但似乎目前还没有什么好的设备能解决这一问题。
而如何能让人工检查判断的准确性更高,也有许多不同的做法。
C、选择合适的树脂,尤其是材料Tg和膨胀系数的选择,合适的生产流程以及合适的除胶参数,方能避免焊盘与树脂受热后脱离的问题。
D、对于树脂与铜分层的问题,我们发现孔表面的铜厚厚度大于15um时,此类树脂与铜分层的问题可以得到极大的改善。
(如下图)2 内层HDI埋孔,盲孔塞孔树脂塞孔2.1 常见的问题A、爆板B、盲孔树脂突起C、孔无铜2.2 导致的后果不用说,以上的几个问题都直接导致产品的报废。
树脂的突起往往造成线路不平而导致开短路问题。
2.3 预防改善措施A、控制内层HDI塞孔的饱满度是预防爆板的必要条件;如果选用在线路以后进行塞孔,则要控制好塞孔到压合之间的时间和板面的清洁性。
B、树脂的突起控制需要控制好树脂的打磨和压平;3 、树脂塞孔技术的推广随着树脂塞孔技术应用的熟练度不断的提高,以及类似于气泡等顽固问题的有效解决,树脂塞孔技术在不断的被推广。
例如HDI盲孔进行树脂塞孔填胶,叠层HDI结构的内层HDI埋孔VIP工艺等等。
目前在行业通行的标准(IPC-650)里面,似乎还没有给出对于树脂塞孔的孔上面铜厚的要求,潜在的风险是,一旦树脂塞孔的孔上面电镀的铜厚偏薄,经过内层HDI线路的表面处理,棕化处理以后,孔口上面的薄薄的铜会有被激光钻孔钻穿的可能,而且在电测试时是无法判定其有问题的。
高档树脂工艺品摆件

高档树脂工艺品摆件
1、树脂工艺品摆件的清洗
很多人在发现树脂工艺品摆件蒙上了灰尘后,都习惯拿湿抹布进行擦拭,但如果经常拿湿抹布擦拭,会使抹布中的水分深入到树脂工艺品中,渐渐地就会损坏树脂的内部结构,使其中的缝隙受潮、变得松散。
所以,大家在清洁时可以用干棉布或鸡毛掸子将树脂工艺品上的灰尘掸去,这样的方式同样有清洁的效果。
2、树脂工艺品摆件的抛光
树脂工艺品摆件常年暴露在开放的居室中摆放,难免会出现光泽逐渐暗淡的情况,这时大家可以用刷子将上光蜡涂于树脂工艺品的表面,用干抹布擦一下抛光即可,或用含蜡质或含油脂的织品擦拭,就能使树脂工艺品光泽如新了。
3、树脂工艺品摆件的存放
由于树脂材料的不稳定性,因而树脂工艺万不可放置在是最怕阳光可直射的位置,否则时间久了可能会导致树脂工艺品开裂;其次,树脂工艺品也不宜放在极为潮湿的地方,在很潮湿的环境里,部分树脂因为材质的原因,会长“毛”发霉。
因此家中的树脂艺术品,可以把它放在客厅阴凉通风的位置上,才能使其在适宜的环境下得以长久的保存。
树脂工艺品摆件怎样去除气孔

树脂工艺品摆件怎样去除气孔
我们在常见较大件的树脂摆件和树脂卡通人物偶尔还是会出现不良,模具比较有利于抽真空,产品空间树脂的流动型比较好。
但树脂工艺品,有比较小的摆件相对结构特殊和太小件的产品,在转角等空心阻力大的拐角处,是最容易出现气孔的,有的气孔甚至露出了树脂制品的表面,有些不懂的人士就作为报废品处理了,这样既浪费又不节约,为了解决这些较小树摆件脂问题,深圳新艺源树脂工艺品总结了以下几种方法如下:
1、把已经灌注满的模具搬移至强力真空压缩机,把树脂料浆里面因搅拌时产生的多余气泡挤走。
2、查看一下真空抽取器有没有机械故障,要保证树脂工艺品在真空箱里的抽空速度很快达到0.2Mpa,这样才会把真空处理的很好,而有部分树脂工艺品厂家对大型的树脂工艺品产品则是采取真空度达到0.2Mpa后再减小到0.08Mpa,然后再回到0.1Mpa,这样的抽空效果也很不错。
3、在精细复杂的模具设计过程中要考虑到气孔的问题,要分型设计,在转角处要添加放气口,这样就方便了抽空效果,减少气孔发生的频率。
以上三点建议,希望可以帮助到大家。
- 1、下载文档前请自行甄别文档内容的完整性,平台不提供额外的编辑、内容补充、找答案等附加服务。
- 2、"仅部分预览"的文档,不可在线预览部分如存在完整性等问题,可反馈申请退款(可完整预览的文档不适用该条件!)。
- 3、如文档侵犯您的权益,请联系客服反馈,我们会尽快为您处理(人工客服工作时间:9:00-18:30)。
树脂工艺品摆件怎样去除气孔
我们在常见较大件的树脂摆件和树脂卡通人物偶尔还是会出现不良,模具比较有利于抽真空,产品空间树脂的流动型比较好。
但树脂工艺品,有比较小的摆件相对结构特殊和太小件的产品,在转角等空心阻力大的拐角处,是最容易出现气孔的,有的气孔甚至露出了树脂制品的表面,有些不懂的人士就作为报废品处理了,这样既浪费又不节约,为了解决这些较小树摆件脂问题,深圳新艺源树脂工艺品总结了以下几种方法如下:
1、把已经灌注满的模具搬移至强力真空压缩机,把树脂料浆里面因搅拌时产生的多余气泡挤走。
2、查看一下真空抽取器有没有机械故障,要保证树脂工艺品在真空箱里的抽空速度很快达到0.2Mpa,这样才会把真空处理的很好,而有部分树脂工艺品厂家对大型的树脂工艺品产品则是采取真空度达到0.2Mpa后再减小到0.08Mpa,然后再回到0.1Mpa,这样的抽空效果也很不错。
3、在精细复杂的模具设计过程中要考虑到气孔的问题,要分型设计,在转角处要添加放气口,这样就方便了抽空效果,减少气孔发生的频率。
以上三点建议,希望可以帮助到大家。