铝合金汽车车门冲压成形工艺研究
车用铝合金中铝板冲压的设计及生产的关键技术

车用铝合金中铝板冲压的设计及生产的关键技术随着汽车工业的发展与普及,车用铝合金中铝板冲压技术日渐成熟,成为了汽车制造领域中不可或缺的一部分。
车用铝合金中铝板冲压技术能够大幅度减轻汽车的整体重量,提高车辆的燃油经济性和性能,同时也对汽车的外观设计起到了很大的提升作用。
本文将围绕车用铝合金中铝板冲压的设计及生产的关键技术展开探讨。
一、铝合金中铝板冲压的设计1. 材料选择:在车用铝合金中铝板冲压的设计中,首先需要选择合适的材料。
一般来说,车身冲压零部件所采用的铝合金材料要求具有高强度、高塑性、良好的焊接性、优异的表面质量和成型性能。
目前常用的车用铝合金材料有6系、5系和7系铝合金,其中6系铝合金具有良好的塑性和强度综合性能,被广泛应用于车身冲压零部件的制造。
2. 模具设计:冲压模具是车用铝合金中铝板冲压中至关重要的工艺设备。
模具设计直接影响着产品的成型质量和生产效率。
冲压模具主要包括上模、下模和冲头等部分,其中冲头是决定产品成型质量和表面质量的重要部件。
在车用铝合金中铝板的冲压模具设计中,需要考虑到材料的流动性、成形难度、成形是否均匀等因素,合理设计模具结构和尺寸参数,以确保产品成型质量和生产效率。
3. 工艺流程设计:在车用铝合金中铝板冲压的设计中,需要合理确定冲压的工艺流程。
工艺流程设计需要考虑到产品的结构形状、尺寸精度要求、表面质量要求等因素,以确保产品的成型质量和工艺效率。
1. 强化处理技术:为了提高车用铝合金中铝板的机械性能,常常需要进行强化处理。
强化处理技术主要包括固溶处理和时效处理两种。
固溶处理是指将合金加热到固溶温度,然后经过适当的保温时间后,迅速冷却到室温。
时效处理是指在固溶处理后,通过加热保温一定时间,再经过适当的冷却处理。
通过合理的强化处理技术,可以显著提高车用铝合金中铝板的强度和硬度,满足汽车零部件的使用性能要求。
2. 成形工艺技术:在车用铝合金中铝板的冲压成形过程中,需要考虑到材料的成形性能和成形工艺的合理性。
铝合金冲压成形工艺研究

铝合金冲压成形工艺研究近年来,随着制造业的飞速发展,铝合金成为了广泛应用的材料之一,其优良的耐腐蚀性、机械性能以及良好的导电性和导热性等特点受到了极大的重视。
铝合金冲压成形作为制造铝合金零部件的主要工艺之一,其制造工艺及技术发展变得越来越重要。
首先,铝合金冲压成形生产过程中,需要考虑很多因素,比如冲裁工艺、模具设计、材料性能等问题。
冲裁生产的质量和数量都是冲裁生产是否具备可行性的重要因素。
在冲压过程中,材料要承受很大的应变,因此材料的损伤程度也会影响零件的质量。
为了在冲压成形中保证零件质量,需要遵循标准的冲裁过程和模具设计原则。
其次,铝合金冲压成形工艺需要严格控制模具制造和加工工艺。
模具制造过程中如果出现问题,可能会导致生产困难和生产成本上升。
因为模具制造是成本的重要组成部分,而模具的生产精度、耐磨性以及寿命的好坏会直接影响到零件的质量,也会对生产力产生影响。
因此,为了获得好的模具,需要对制造和冷却工艺进行严格控制。
而在加工和组装过程中也都需要使用严格的工艺标准和设备工具,并且需要进行清洁、检查和保养。
最后,在铝合金冲压成形工艺中还需要对材料本身的特性进行深入研究。
铝及其合金的物理和力学性质随着变型的增加而发生相应的变化,而这些变化将直接影响到成形工艺中铝合金材料的应变、应力、发热和变形等方面。
因此,在冲压成形中,需要进行一系列预分析和实验研究,包括材料性能的表征、应变测试、成形过程的模拟和分析等等。
只有对铝合金成形过程中的各种因素全部考虑清楚,才能在生产中获得高效、低成本同时高质量的铝合金零件。
总之,铝合金冲压成形工艺在现代制造业中具有广泛的应用前景。
通过对冲压生产过程中的各种因素进行深度研究,结合制定严格的冲裁工艺和模具设计制造原则,以及材料性能的预判和实验研究,将能够大大提高铝合金零件的生产效率和生产质量。
汽车车身的冲压成形技术分析

汽车车身的冲压成形技术分析汽车车身是汽车的重要组成部分,其外形设计和制造工艺直接影响着汽车的外观、性能和安全性。
而汽车车身的冲压成形技术是目前最常用的车身制造技术之一,本文将对汽车车身的冲压成形技术进行深入分析。
一、冲压成形技术概述冲压成形技术是利用冲压设备和模具将金属板料加工成所需形状的一种制造方法,其特点是高效、精度高、成本低。
冲压成形技术在汽车制造领域得到了广泛应用,尤其是汽车车身的制造中,冲压成形技术的作用尤为突出。
二、冲压成形技术在汽车车身制造中的应用1.冲压成形工艺汽车车身的冲压成形工艺主要包括下料、模具设计、冲床冲压、清洗、组装等环节。
首先是通过下料设备将金属板料剪切成所需大小。
然后根据车身的设计要求设计并制造冲压模具。
接着使用冲床对金属板料进行冲压成形,通过模具的设计和冲床的运行,将金属板料冲压成车身需要的各种零部件。
最后对冲压成形后的零部件进行清洗、去毛刺等处理,然后进行组装,形成完整的车身结构。
2.冲压成形技术的优势冲压成形技术在汽车车身制造中具有高效、精度高、生产成本低等优势。
冲压成形可以使金属板料在较短的时间内完成成形,提高了生产效率。
由于模具的精密设计和冲床的高速运动,可以实现对车身零部件的高精度冲压,保证其尺寸和形状的准确度。
由于冲压成形生产线的自动化程度较高,相对于传统的手工制造工艺,冲压成形技术降低了人工成本,使得汽车的生产成本得到了有效控制。
1.高强度材料的应用随着汽车安全性能的不断提高,对车身材料的要求也越来越高。
传统的冷轧钢板在一定程度上已经无法满足汽车车身材料的需求。
高强度材料如高强度钢、铝合金等开始在汽车车身制造中得到应用。
这些新材料的应用对冲压成形技术提出了更高的要求,需要冲压设备和模具能够更好地处理这些高强度材料,以保证车身零部件的成形质量。
2.多工位冲压设备的应用为了提高生产效率和节约生产成本,汽车车身制造中开始使用多工位冲压设备。
多工位冲压设备可以在一次加工中完成多道工序,实现一次性成形多个零部件,提高了生产效率和降低了生产成本。
【技术帖】浅谈车身铝合金板冲压工艺和模具注意事项

【技术帖】浅谈车身铝合金板冲压工艺和模具注意事项摘要:汽车车身用铝合金板与传统汽车低碳钢板比,具有弹性模量小易回弹、质地软、成形窗口窄、切口敏感度高等特点。
通过分析铝合金板的特点对冲压和产品质量的影响,结合经验数据阐述和总结了铝合金板在冲压工艺设计和模具开发方面需要注意的事项。
关键词:弹性模量铝合金冲压工艺1、前言近年来,汽车工业快速发展,全球汽车保有量急剧攀升。
随之而来的是能源危机和环境污染日趋严峻,减少能源消耗已经成为汽车工业发展客观面临的严峻挑战。
汽车轻量化无疑是解决以上问题的重要方法之一。
有研究表明,小轿车车重每减轻10%,燃油效率可提高6%~8%,排放降低约4%。
而车身系统质量占整备质量的比例约在40%~50%之间,所以汽车车身轻量化就尤为重要。
铝合金材料具有密度小、强度高、抗腐蚀性强、可回收循环利用等诸多优点。
另外,铝合金弹性性能高,安全性高,发生碰撞时吸能效果好,铝合金吸能约是钢的1.5倍。
采用铝合金板材替代传统低碳钢板作为车身材料是目前车身实现轻量化的重要方法之一。
2、车身用铝合金板材种类及特点目前,在汽车车身上应用的铝合金板材主要有5000系和6000系两个系列。
5000系是Al-Mg系铝合金,是目前在汽车车身上应用最为广泛用量最大的系类,主要合金元素是镁元素,镁元素含量在3%~5%之间。
主要优点有:强度高、延伸率高、较好的冲压成形性、优异的焊接性和抗腐蚀性。
主要应用在车身内板等结构相对复杂的零件。
其缺点是易产生吕德斯线和延迟屈服,主要用在车身内板等成形复杂的结构件上。
6000系是Al-Mg-Si系铝合金,主要含有镁和硅两种合金元素,拥有4000系和5000系两者的优点。
属于热处理后可强化的合金,热处理可强化铝合金的过饱和铝基固溶体具有时效强化特性,即在室温或加热到某一温度时,其强度和硬度随时间的延长而增高,尤其是零件在经涂装185℃烘烤20 min后,强度有大幅提升,但塑性降低。
铝合金汽车车门冲压成形分析与设计
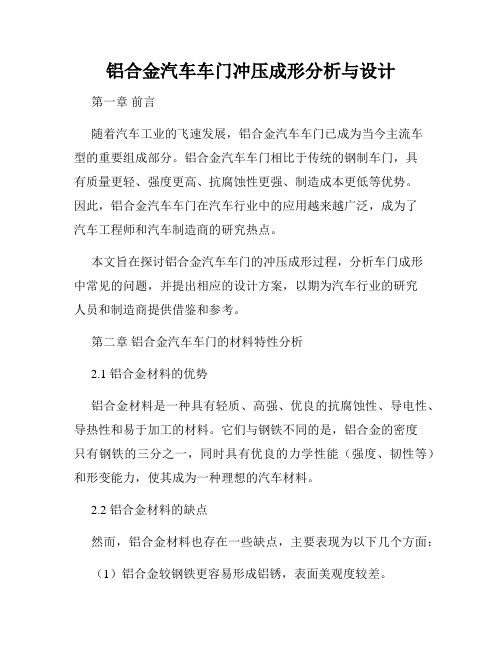
铝合金汽车车门冲压成形分析与设计第一章前言随着汽车工业的飞速发展,铝合金汽车车门已成为当今主流车型的重要组成部分。
铝合金汽车车门相比于传统的钢制车门,具有质量更轻、强度更高、抗腐蚀性更强、制造成本更低等优势。
因此,铝合金汽车车门在汽车行业中的应用越来越广泛,成为了汽车工程师和汽车制造商的研究热点。
本文旨在探讨铝合金汽车车门的冲压成形过程,分析车门成形中常见的问题,并提出相应的设计方案,以期为汽车行业的研究人员和制造商提供借鉴和参考。
第二章铝合金汽车车门的材料特性分析2.1 铝合金材料的优势铝合金材料是一种具有轻质、高强、优良的抗腐蚀性、导电性、导热性和易于加工的材料。
它们与钢铁不同的是,铝合金的密度只有钢铁的三分之一,同时具有优良的力学性能(强度、韧性等)和形变能力,使其成为一种理想的汽车材料。
2.2 铝合金材料的缺点然而,铝合金材料也存在一些缺点,主要表现为以下几个方面:(1)铝合金较钢铁更容易形成铝锈,表面美观度较差。
(2)铝合金材料的成本相对较高,价格比钢铁高出50%左右。
(3)铝合金车门在高速碰撞事故中可能受到更严重的损坏。
(4)铝合金材料更容易变形,且易于钝化。
2.3 材料选择的原则在选择材料时,需要根据车门的性能要求和压力要求进行选择。
较轻的铝合金车门在碰撞事故中可能会变形或破裂。
高强度钢制品对于碰撞的力量会有更好的抵抗,但比铝合金重许多。
因此,材料的选择应根据设计要求,针对不同需求进行权衡和取舍,并在实际制造中试验和验证。
第三章车门冲压成形的设计流程3.1 设计流程如图1所示,车门冲压成形的设计流程主要分为以下几个环节:(1)制定车门的设计要求和技术规范。
(2)通过数值模拟和实际制造验证车门材料的选择。
(3)设计车门的造型和尺寸,通过数值模拟和实际制造验证其可行性。
(4)运用数值模拟软件对车门进行成形模拟,并根据模拟结果进行设计验证和优化。
(5)制造车门,并进行质量检验和性能测试。
铝合金板材冲压成形技术

七、XXX轿车铝合金零件开发应用: 红旗H7后副车 架
2.铝合金后副车架零件
名称: 支架 材料: 5754-H22 料厚: 3.5
谢谢!
毛坯边界
凸模
40
压边圈
5.退料
由于铝板较轻, 压完件后易带件, 上模加顶料销, 排气 孔加大。
二、铝合金零件拉延工艺特点
6.模具材料: 一般使用ENZF2070 。
7.拉延模具热处理 型面渗氮, 圆角激光淬火)。
8.油漆 非工作表面刷浅色的漆, 脏了能看出来, 及时清理。
三、铝合金零件修边工艺特点
8.废料输送: 铝板废料和钢板废料必须分开输送。
七、XXX轿车铝合金零件开发应用: 红旗H7后副车
架
1.铝合金后副车架总成
七、XXX轿车铝合金零件开发应用: 红旗H7后副车 架
2.铝合金后副车架零件
名称: 后副车架前横梁 材料: 6063 料厚: 4
七、XXX轿车铝合金零件开发应用: 红旗H7后副车 架
三、铝合金零件修边工艺特点
7.热处理
8.废料滑道: 角度最小30°,并且选用网纹板。 9.定位: 一定要有定位板(2孔定位+四周定位板)
四、铝合金零件压弯翻边工艺特点
1.内圆角半径R: 最小1,5t。
四、铝合金零件压弯翻边工艺特点
龟裂
四、铝合金零件压弯翻边工艺特点
2.热处理: 硬度HRC58+2
无法消除。
a
二、铝合金零件拉延工艺特点
2.拉延凹模圆角半径R: 最小3t,平面圆角区域比直线区域 R
更大。
二、铝合金零件拉延工艺特点
3. 拉延筋: 侧修边的地方,不做拉延筋,断开,拉延筋过渡要平
缓。
铝合金汽车车门冲压成形工艺研究

铝合金汽车车门冲压成形工艺研究发表时间:2019-02-13T09:45:53.813Z 来源:《电力设备》2018年第25期作者:张健沙佳辰[导读] 摘要:随着社会经济的发展,人们的环保意识越来越强,在汽车行业中,已经开始利用铝合金材料,通过大幅减轻自身车体重量,达到减少油耗和尾气排放量的目的。
(长城汽车股份有限公司河北保定 071000)摘要:随着社会经济的发展,人们的环保意识越来越强,在汽车行业中,已经开始利用铝合金材料,通过大幅减轻自身车体重量,达到减少油耗和尾气排放量的目的。
对此,针对铝合金材料的车门冲压工艺进行优化,对铝合金车门形成特点进行综合分析。
关键词:铝合金材料;车门冲压;工艺优化近年来,我国的汽车行业有了飞速的发展,其对环境的污染问题也越来越突出,节约资源和减少污染成为汽车行业亟待解决的两大问题。
着眼于可持续发展,减轻汽车质量,降低燃油消耗及减少排放污染的任务显得尤为迫切,汽车轻量化技术是解决这些问题的重要途径之一。
研究结果表明,汽车质量每减少10%就可以降低6%~8%的燃油消耗。
铝合金具有密度小、强度高、耐腐蚀性强、抗冲击性能好和再回收能力强等一系列优良特性,并且资源相对丰富,将成为汽车工业中最具竞争的轻质材料。
但是铝合金在室温条件下,其成形性能较差,总伸长率小,且弹性系数仅为钢板的1/3,成形时金属流动困难,从而其应用受到一定的限制。
在高温下铝合金塑性好、变形抗力低、成形难度低,因此,铝合金的热冲压成形技术受到人们的广泛关注。
1工艺方案的制定(1)拉延工序工艺方案的制定:拉延工序是覆盖件冲压成形的关键工序,覆盖件的大部分形状是在此工序形成,拉延成形的好坏将直接影响覆盖件质量。
该工序一方面成形出零件的大部分形状,同时在拉延过程中还将对坯料进行切角,减少落料模具,降低成本。
结合零件的工艺性,在拉延工序中对零件的某些部分做如下处理。
◎第一方案,增大模具圆角,以减小材料流动阻力,再对相应部分进行整形;第二方案,利用在窗框的适当部位冲切工艺切口的方法,使容易破裂的区域从相邻区域里得到材料补充,从而改善该区域的变形情况,避免破裂的产生。
汽车车门外板冲压工艺

汽车车门外板冲压工艺随着汽车工业的迅速发展,汽车车门外板的质量和外观要求越来越高。
而冲压工艺作为汽车车门外板加工的主要方法,对于保证车门质量、提高生产效率和降低成本起着至关重要的作用。
本文将介绍汽车车门外板冲压工艺的整体流程、工艺参数及对车门外板质量的影响。
一、汽车车门外板冲压工艺的整体流程汽车车门外板冲压工艺一般分为以下几个步骤:材料切割、冲孔、弯曲、成形和涂装。
首先,车门外板所需材料经过切割工艺,将大板材切割成适合冲压的小板材。
然后,根据车门外板的设计要求,在小板材上进行冲孔,以便后续的安装和组装。
接下来,利用专用的冲压模具对冲孔后的小板材进行弯曲和成形,使其形状与车门外板设计相符。
最后,经过涂装工艺,将成形后的车门外板进行表面处理,使其具备防腐蚀性和美观性。
二、汽车车门外板冲压工艺的工艺参数1. 冲压力和冲压速度:冲压力和冲压速度是决定冲压质量和效率的关键参数。
冲压力过大会导致小板材变形和裂纹,冲压速度过快会影响冲压精度。
因此,冲压力和冲压速度需要根据车门外板材料的性质和冲压模具的特点进行合理调整。
2. 冲孔模具和弯曲模具:冲孔模具和弯曲模具是冲压工艺中的关键工具。
冲孔模具的设计需要考虑到冲孔位置、孔径和孔距等因素,以确保冲孔的准确性和一致性。
弯曲模具的设计需要考虑到弯曲角度和弯曲半径等因素,以确保车门外板的形状和尺寸符合要求。
3. 材料选择和热处理:汽车车门外板通常使用高强度钢板或铝合金板材。
材料的选择需要综合考虑强度、韧性、成本和可加工性等因素。
同时,通过热处理可以改善材料的机械性能,提高冲压质量和寿命。
三、汽车车门外板冲压工艺对车门外板质量的影响汽车车门外板冲压工艺的参数设置和工艺流程对车门外板的质量有着直接影响。
1. 尺寸精度和表面质量:冲压工艺中的冲压力、冲压速度和模具设计等因素会影响车门外板的尺寸精度和表面质量。
合理控制这些参数可以避免尺寸偏差和表面缺陷,保证车门外板的装配和外观质量。
汽车铝合金车身冲压工艺

汽车铝合金车身冲压工艺
随着汽车工业的不断发展,汽车铝合金车身的应用越来越广泛。
铝合金车身具有重量轻、强度高、耐腐蚀等优点,可以提高汽车的燃油经济性和安全性能。
而汽车铝合金车身的制造过程中,冲压工艺是其中非常重要的一环。
汽车铝合金车身冲压工艺是指将铝合金板材通过模具进行冲压成形的过程。
这个过程需要经过多道工序,包括模具设计、板材切割、冲压成形、表面处理等。
其中,模具设计是冲压工艺的关键,模具的设计质量直接影响到冲压件的质量和生产效率。
因此,模具设计需要考虑到铝合金板材的特性,如强度、韧性、塑性等,以及冲压件的形状、尺寸等因素。
在冲压成形过程中,铝合金板材需要经过多次冲压,每次冲压都会使板材发生变形,因此需要进行多次校正。
同时,铝合金板材的塑性较差,容易出现裂纹和变形,因此需要控制冲压力度和速度,以避免板材的损坏。
冲压成形完成后,还需要进行表面处理,以提高铝合金车身的耐腐蚀性和美观度。
表面处理包括喷涂、阳极氧化等工艺,其中阳极氧化是一种常用的表面处理方法,可以形成一层氧化膜,提高铝合金车身的耐腐蚀性和硬度。
汽车铝合金车身冲压工艺是汽车制造过程中非常重要的一环,需要
经过多道工序,包括模具设计、板材切割、冲压成形、表面处理等。
在冲压成形过程中,需要控制冲压力度和速度,以避免板材的损坏。
同时,表面处理也是非常重要的一步,可以提高铝合金车身的耐腐蚀性和美观度。
5_系铝合金车门内板冲压成形及回弹研究

精 密 成 形 工 程第15卷 第12期106 JOURNAL OF NETSHAPE FORMING ENGINEERING2023年12月收稿日期:2023-07-22 Received :2023-07-22基金项目:重庆市教委科技项目重点项目(KJZD-K202101101)Fund :Key Project of Science and Technology Project of Chongqing Municipal Education Commission (KJZD-K202101101) 引文格式:陈俊, 张玉成, 王博, 等. 5系铝合金车门内板冲压成形及回弹研究[J]. 精密成形工程, 2023, 15(12): 106-115. CHEN Jun, ZHANG Yu-cheng, WANG Bo, et al. Stamping Forming and Springback of 5 Series Aluminum Alloy Door Inner Panel[J]. Journal of Netshape Forming Engineering, 2023, 15(12): 106-115.5系铝合金车门内板冲压成形及回弹研究陈俊1,张玉成1,王博1,甘贵生2,彭波1,郑雪勇1,马相3(1.重庆赛力斯新能源汽车设计院有限公司,重庆 401335;2.重庆理工大学 材料科学与工程学院,重庆 401135;3.挪威科技工业研究院,奥斯陆 0314) 摘要:目的 在整体式车门内板上应用质量较轻的5系铝合金材质以达到新能源汽车的轻量化要求。
方法 在工艺设计阶段,采用AutoForm 数值分析软件及CAE 数值仿真分析技术预测零件的成形难点及回弹趋势;分析整体式车门内板的深度,并提出几种改善零件成形性的方案;根据回弹结果对模具型面进行回弹补偿;对模具加工、调试等重要环节进行深度管控。
汽车车门内板冲压成形工艺分析

缺陷检测ห้องสมุดไป่ตู้针对常见的冲压成形缺陷,采用特定的检测方法和技术手段,及时发现并处理缺 陷,避免批量质量问题。
质量追溯:建立完善的质量追溯体系,对每个环节进行记录和追踪,确保产品质量可追溯, 便于问题排查和解决。
冲压成形中的应力应变分析:板料在冲压过程中,会发生应力应变,其分布和大小对成形质量 有重要影响。
冲压成形中的缺陷分析:如起皱、开裂、回弹等,与材料性质、模具设计、工艺参数等因素有 关。
材料在冲压过程中的流动与变形规律 材料的应力应变行为 材料屈服准则和本构方程 材料硬化特性对冲压成形的影响
冲压速度:根据 材料厚度和成形 要求选择合适的 冲压速度,以保 证成形质量和效
轻量化材料:如高强度钢、铝合金等,可有效降低车身重量,提高燃油经济性和 动力性能。
新型成形工艺:如热冲压、温冲压等,可提高材料成形极限和零件强度,降低生 产成本。
复合材料:如碳纤维复合材料,具有高强度、轻量化和可设计性等优点,是未来 汽车车门内板冲压成形工艺的重要发展方向。
智能化技术:如人工智能、大数据等,可实现冲压成形工艺的智能化控制和优化, 提高生产效率和产品质量。
模具刚度与强度:确保模具在冲压 过程中具有足够的刚度和强度,避 免变形和损坏。
添加标题
添加标题
添加标题
添加标题
模具结构设计:采用易于加工、装 配和维修的结构,降低制造成本。
模具冷却系统:优化冷却系统设计, 提高冷却效果,减少模具温度波动 和热疲劳损伤。
研发背景:传统冲压成形工艺存在局限性,新型工艺应运而生 主要技术:激光冲压成形、热冲压成形等 应用领域:汽车制造、航空航天等 优势与效果:提高材料利用率、减少生产成本、提高产品性能等
全铝车身的冲压成型工艺

全铝车身的冲压成型工艺冲压加工是借助于常规或专用冲压设备的动力,使板料在模具里直接受到变形力并进行变形,从而获得一定形状,尺寸和性能的产品零件的生产技术。
板料,模具和设备是冲压加工的三要素。
按冲压加工温度分为热冲压和冷冲压。
前者适合变形抗力高,塑性较差的板料加工;后者则在室温下进行,是薄板常用的冲压方法。
它是金属塑性加工(或压力加工)的主要方法之一,也隶属于材料成型工程技术。
冲压所使用的模具称为冲压模具,简称冲模。
冲模是将材料(金属或非金属)批量加工成所需冲件的专用工具。
冲模在冲压中至关重要,没有符合要求的冲模,批量冲压生产就难以进行;没有先进的冲模,先进的冲压工艺就无法实现。
冲压工艺与模具、冲压设备和冲压材料构成冲压加工的三要素,只有它们相互结合才能得出冲压件。
当前全铝车身越来越吃香,会不会最终取代钢铁呢?答案是肯定的,但短时间内无法做到。
据美国市场研究机构Ducker的一份报告称,目前仅有1%的汽车为全铝车身,预计到2025年,这一数字将达到18%。
奥迪R8采用全铝车身设计,R8车身的高性能复合材料被称为Audi Space Frame(AFS),其总重量只有 210 公斤,不到钢铁车架的一半重,但是强度和抗冲击性能都十分出色。
整个车体成分里,70%是铝合金、13%是增强碳纤维(CFRP)。
用奥迪自己的话来说就是:「把正确的材料以正确的数量放在正确的位置」。
视频1:AUDI R8的冲压(铝材)成型车间▼视频2:液压成型工艺的结构原理和应用(3D动画)▼TESLA特斯拉Model S 97%车身为轻质铝合金打造,一卷铝材的费用是3万美元,打造全车需要50-60种不同的铝卷材,全铝合金车身的重量仅为190kg。
TESLA使用的串联式液压冲压生产线(SchulerSMG hydraulic tandem stamping press lines)是全北美最大,世界第六大的冲压生产线,总吨位达到11,000吨,每6秒出一件铝材冲压件,每天可生产出5,000件。
车用铝合金中铝板冲压的设计及生产的关键技术

车用铝合金中铝板冲压的设计及生产的关键技术随着社会的发展和科技的进步,车用铝合金中铝板冲压技术在汽车制造行业中得到了越来越广泛的应用。
车身板件作为汽车的重要组成部分,其设计制作直接关系到汽车的外观和性能,因此对车用铝合金中铝板冲压的设计及生产的关键技术有着非常高的要求。
一、设计1. 材料选择车用铝合金中铝板冲压的首要任务是选用合适的材料。
在选择材料时需要考虑到铝合金的强度、硬度、延展性等性能指标,以及对汽车整体质量的影响。
常用的铝合金有5052、6061、7075等,设计师需要根据具体的使用场景和要求选择合适的材料。
2. 模具设计模具设计是车用铝合金中铝板冲压中至关重要的一环,直接决定了冲压成型的精度和质量。
在模具设计中需要考虑到产品的结构特点,合理设计模具结构,保证产品的冲压成型质量和生产效率。
3. 工艺设计车用铝合金中铝板冲压的工艺设计包括了冲压过程的工艺路线、冲压工序的顺序、冲压机的选型等内容。
合理的工艺设计能够使得产品的成型过程更加顺畅、精准,提高生产效率和产品质量。
二、生产1. 冲压设备冲压设备是车用铝合金中铝板冲压生产中的关键设备,对产品的成型质量和生产效率有着直接的影响。
目前常用的冲压设备有液压冲床、机械冲床等,工厂需要根据生产需求选择合适的冲压设备。
2. 精密控制在车用铝合金中铝板冲压生产中,需要进行精密的控制来确保产品的质量和精度。
包括对冲压负荷、速度、温度等参数进行准确控制,以及对冲压模具的使用和维护进行严格管理。
3. 质检与改进在整个车用铝合金中铝板冲压的生产过程中需要进行严格的质量检测和控制,及时发现问题并进行改进。
例如采用成型试验来验证模具设计的可行性和合理性,以及对成品进行全面的检查和测试等。
三、关键技术1. 材料成型技术原料的成型质量对最终产品的成形质量有着直接的影响,控制原料的成型技术是车用铝合金中铝板冲压的关键技术之一。
需要对原料的厚度、宽度、形状等进行严格控制,确保原料的均匀性和一致性。
汽车车门制造冲压工艺分析

汽车车门制造冲压工艺分析摘要:在对汽车车门进行制造时,所使用的材料以及制造工艺都会影响车门的强度与钢度。
大部分汽车车门的制造过程是冲压,焊装,涂装最后与车身其他部件总装为一个白车身。
汽车车门的制造工艺是整车工艺的一个缩影,从小见大,了解它也就能帮助我们了解整车制造工艺。
笔者介绍了一种冲压工艺方法在汽车车门内板上的具体应用,降低了拉延模具制造难度,降低了制造成本。
关键词:车门材料;冲压工艺;分析一、制件冲压工艺概述冲压件一般需经过拉延/修边+冲孔/整形(或翻边)+冲孔等工序才能得到合格产品。
对于稍微复杂的钣金件,通过拉延仅能得到冲压件大概轮廓,经过后序的修边冲孔,再配合整形翻边等工序才能得到最终零件。
整形翻边等工艺可以降低拉延深度,简化拉延模面的形状,提高成形性,也就是提高了模具制造的可实现性及易操作性。
以常见的车门外板为例,展示普通冲压外覆盖件的工艺流程。
车门外板采用4步工序实现了零件的制造过程,因车门外板拉延深度较小,型面相对简单,因此采用的是一次拉延成形的方法,配合后面的修边、冲孔、翻边工序而成,这种一次拉延的冲压工艺方案是通过拉延得到基本的零件轮廓,后期的整形、翻边等都是对R角的微小型面进行小范围改变,这种工艺方法在实际生产中广泛应用,但同时也存在如下缺点和不足:(1)一次拉延工序得到几乎整个零件的全部形状特征,后工序主要是修边、冲孔、翻边,以及对局部的(小面积的)难以一次成形的型面做整形,得到零件。
此工艺比较死板,灵活变动的空间较小,限制了工艺设计的多样性。
(2)因为是一次拉延得到了零件的基本形状,所以拉延深度是固定的,零件的造型决定了拉延深度的大小,也就决定了成形的可实现性。
对于拉延深度较大的零件就存在拉延状态不稳定及拉延开裂的风险。
(3)拉延深度较大的零件拉延工序存在拉毛风险,为减少拉毛的概率,对于拉延模质量要求较高,比如硬度、光洁度都要提升一个等级,同时也要加强模具的日常保养维护,增加了制造成本。
车用铝合金中铝板冲压的设计及生产的关键技术

车用铝合金中铝板冲压的设计及生产的关键技术车用铝合金中的铝板冲压技术是指通过将铝板材料放置在冲压机上,并利用冲压机的力量将其塑性变形成为所需的形状,完成汽车零部件的制造过程。
铝合金具有良好的强度和韧性,同时具备较低的密度,因此广泛应用于汽车制造领域。
下面将介绍车用铝合金中铝板冲压的设计及生产的关键技术。
一、设计1. 材料选择:合适的铝合金材料是冲压设计的首要考虑因素。
需要考虑材料的强度、韧性、耐蚀性、可焊性等性能,以及成本因素。
还需根据零部件的功能和要求选择合适的铝合金材料。
2. 结构设计:在进行铝板冲压零部件的结构设计时,需要考虑到零件的形状、尺寸、壁厚以及各个结构部分的布局。
通过对零件的合理设计,可以降低冲压过程中的应力集中和变形,提高零件的强度和稳定性。
3. 港口:港口的设计是决定零部件冲压成形与加工质量的重要因素。
港口的形状和尺寸需要根据材料的性质和冲压工艺要求进行选择,并考虑到冲压过程中的引导和变形。
4. 成型模具设计:成型模具是铝板冲压的重要工具,它的设计直接影响到产品的形状、尺寸和表面质量。
模具的设计应考虑到零件的冲裁、下料、成形等工艺要求,并注意模具的耐用性和加工精度等要求。
二、生产1. 材料预处理:铝合金材料在冲压加工之前需要进行预处理,包括材料的去氧化处理、清洗和涂层等。
预处理可以提高材料的表面质量和降低其在冲压过程中的焊粘、卡料等问题。
2. 冲压工艺参数控制:在进行铝板冲压加工时,需要控制好冲压工艺参数,如冲程、冲头冲速、冲头冲量等,以保证零部件的加工质量和成形精度。
还需对冲压机进行维护和调整,以确保设备的正常运行。
3. 冲压润滑:冲压过程中的润滑对于减少摩擦和热量、提高材料的流动性和延展性十分重要。
常用的冲压润滑方式包括油润滑、干润滑和液体润滑等,根据具体情况选择适合的润滑方法。
4. 质量控制:在铝板冲压加工过程中,需要进行质量控制,包括对材料和成形零部件的尺寸、形状、表面质量等进行检测和评估。
铝合金汽车覆盖件冲压成形回弹的仿真研究

Re e c n s r g a k n me ia i ua in o h e t 0 m ig s ar h o p i b c u n r l m lt fs e tme al r n c s o f
第 2期 21 0 1年 2月
文章 编号 :0 1 3 9 ( 0 )2 0 0 — 3 10 — 9 7 2 1 0 — 19 0 1
机 械 设 计 与 制 造
M a hi e y De i n c n r sg & Ma u a tr n fcu e 19 0
铝 合金 汽 车覆 盖 件 冲压 成 形 回 弹 的仿 真研 究
s l , o igta ep rmeesa h e e r v i bea dc nb s dt ud ep a t aprd cin ut prvn th aa tr c iv daea al l n a eu e g iet r i l o u t . s h t a o h c c o :
;cos mb r a e a a a pete rc se o i fr n ,i igp n hn n r g akaes 一 ; rs me e p n l ne m l, oess t omi tmm n ,u c iga ds i bc r i s x hp s f gr pn mu
: r ynou dn t nas utn oeoaool a l e ndT i e n rd be td e a ee r li df t be n p s t ant d b y: i ir c dhg eli aom rum ip ei ree kgh u e o l f m s  ̄
汽车铝合金车身冲压工艺

汽车铝合金车身冲压工艺一、引言汽车铝合金车身冲压工艺是一种重要的汽车制造工艺,它能够生产出轻量化、高强度、低油耗的汽车车身。
本文将从材料选择、模具设计、冲压过程等方面详细介绍汽车铝合金车身冲压工艺。
二、材料选择1. 铝合金材料铝合金是一种轻量化、高强度的材料,常用于汽车零部件制造中。
目前市场上常用的铝合金有6系列和7系列两种,其中6系列常用于外壳和结构件,7系列则常用于发动机部件。
2. 板厚选择板厚是影响冲压质量和效率的重要因素。
对于复杂形状的零部件,板厚应适当增加以提高强度和稳定性;对于平面形状简单的零部件,则可以适当减小板厚以降低成本。
三、模具设计1. 模具结构设计模具结构应根据零部件形状和尺寸进行设计。
为了避免产生应力集中现象,模具应采用圆弧过渡方式。
同时,在模具结构设计中应注意加强支撑和加强板的刚度,以确保冲压过程中的稳定性和精度。
2. 模具材料选择模具材料应具有高硬度、高强度和高耐磨性。
常用的模具材料有工具钢、硬质合金和陶瓷等。
其中工具钢是最常用的模具材料,其硬度和强度较高,同时价格相对较低。
四、冲压过程1. 冲压准备在进行冲压前,应先进行准备工作。
首先需要根据零部件形状和尺寸选择合适的模具,并将模具安装到冲床上。
然后需要对铝合金板材进行切割、清洗和涂油等处理,以确保冲压质量。
2. 冲压操作在进行冲压操作时,应注意以下几点:(1)控制进给速度:进给速度过快会导致变形不均匀或产生裂纹;进给速度过慢则会影响生产效率。
(2)控制冲头力量:力量过大会导致零部件变形或损坏;力量过小则会影响成型精度。
(3)控制冲压次数:过多的冲压次数会导致零部件变形或损坏;过少的冲压次数则会影响成型精度。
3. 冲压后处理在完成冲压后,需要对零部件进行后处理。
首先需要对零部件进行清洗和去毛刺等处理,然后再进行热处理或喷涂等表面处理。
五、结论汽车铝合金车身冲压工艺是一种重要的汽车制造工艺。
在材料选择、模具设计和冲压过程等方面都需要注意细节,以确保生产出高质量、高强度、低油耗的汽车车身。
车用铝合金中铝板冲压的设计及生产的关键技术

车用铝合金中铝板冲压的设计及生产的关键技术
1. 铝合金板材的选择:铝合金板材具有良好的塑性和可锻性,能够满足复杂形状的
冲压需求。
在车辆制造中常用的铝合金板材有5系、6系和7系。
5系铝合金具有良好的耐腐蚀性和可焊接性,适用于车身外板等部位;6系铝合金具有较高的强度和热处理性能,
适用于车架等高强度部件;7系铝合金具有超高强度和疲劳寿命,适用于重载部件例如承
力梁等。
2. 冲压工艺的设计:冲压工艺的设计是实现车用铝合金中铝板冲压的关键。
首先需
要根据所需的零件形状和尺寸,通过计算和模拟分析确定冲床的压力、速度和行程等参数。
还需要设计合适的冲头和模具,以确保冲压过程中铝板的变形和切削达到预期的要求。
3. 衬板和垫块的应用:在车用铝合金中铝板冲压过程中,为了避免铝板的变形和划伤,常常需要在冲头和模具之间插入衬板和垫块。
衬板通常由聚酰亚胺(PI)或聚四氟乙
烯(PTFE)等材料制成,具有良好的耐磨损和耐高温性能;垫块通常由橡胶或塑料材料制成,能够减小冲压过程中的冲击力和振动。
4. 表面处理技术:车用铝合金中铝板冲压后,常常需要进行表面处理,以提高零件
的耐腐蚀性和装饰效果。
常见的表面处理技术包括阳极氧化、电泳涂装、喷涂和电镀等。
这些技术能够形成一层保护膜,防止铝板与外界环境发生化学反应,提高零件的使用寿
命。
车用铝合金中铝板冲压的设计及生产需要考虑铝合金板材的选择、冲压工艺的设计、
衬板和垫块的应用以及表面处理技术等关键技术。
通过合理的设计和生产控制,能够实现
高质量和高效率的车用铝合金中铝板冲压生产。
汽车用6016铝合金板材预时效工艺研究及冲压成形数值模拟

摘要6016铝合金板材主要制造汽车覆盖件,特别是乘用车内外罩、后行李箱和门框等汽车外板,是汽车轻量化的关键材料。
而目前国内的铝合金板材仍存在着成形性、抗凹性及零件成形后质量差等问题,无法满足使用要求。
因此开展6016铝合金板材关键的预时效工艺和冲压成形工艺研究,对提高板材的成形质量十分重要。
本文将545 o C固溶30 min的6016铝合金(Al-0.55%Mg-1.0%Si-0.18%Cu)板材水淬后,经60 o C~160 o C×5 min~30 min预时效,室温停放25天后,进行185 o C×20 min的模拟烤漆处理。
采用硬度、拉伸试验,结合示差扫描量热法(DSC)、扫描电子显微镜(SEM)等分析技术,研究预时效工艺对合金的力学性能及微观组织的影响规律。
通过数值模拟仿真实际的冲压过程,并预估零件成形后可能出现的质量缺陷,优化关键成形工艺参数。
结果表明:①固溶淬火后立即进行预时效可以抑制自然时效过程,T4P态合金的成形性和烘烤硬化性能都得到改善。
烤漆前后的硬度随着预时效温度升高,出现先缓慢增加后迅速增加的趋势。
预时效温度为100 o C,预时效时间为20 min合金烘烤前屈服强度低于120 MPa,延伸率在25%左右;烘烤后屈服强度高于180 MPa(预变形2%合金烘烤硬化值达到104 MPa),烘烤后的延伸率在22%左右,综合比较优于其他预时效工艺。
②结合DSC曲线对β”析出温度和激活能进行计算,研究发现,随预时效温度升高,β”析出峰左移,激活能也降低。
说明预时效可以抑制合金自然时效过程,提高合金T4P态成形性能,而且促进烘烤过程中β”的析出,增强烘烤硬化效果。
③以铝制汽车发动机罩内板为对象,建立冲压CAE模型,对板料冲压过程仿真,研究了不同成形工艺对成形后最大减薄率、最大增厚率及最大回弹量的影响规律。
④对多因素的优化问题,首先通过灰色关联分析法,获得较优的工艺参数为:压边力500 KN,摩擦系数0.1,凹凸模间隙1.1t(1.32 mm)、凸模速度3 m/s,仿真试验后出现了少量拉裂缺陷。
车用铝合金中铝板冲压的设计及生产的关键技术

车用铝合金中铝板冲压的设计及生产的关键技术随着汽车轻量化的发展趋势,车用铝合金材料在汽车制造中的应用愈发广泛。
而在车身及零部件制造中,铝板冲压技术是一项关键的生产工艺。
本文将重点介绍车用铝合金中铝板冲压的设计及生产的关键技术。
设计阶段在车用铝合金中铝板冲压的设计阶段,需要考虑以下几个关键技术点:1. 材料选择:铝合金材料的选择对于冲压工艺至关重要。
一般而言,汽车中常用的铝合金材料有6系和7系两种。
6系铝合金具有良好的可加工性和韧性,适合用于一般冲压件的制造;而7系铝合金则具有较高的强度和硬度,适合用于制造要求更高的零部件,如车轮等。
2. 零部件设计:在设计车用铝合金中的铝板冲压零部件时,需要考虑其形状复杂度、厚度分布、变形特性等因素。
合理的设计可以降低冲压成本,减小材料浪费,提高产品质量。
3. 模具设计:模具是冲压工艺的关键,直接影响零部件的成型质量。
在设计模具时,需要考虑材料的选择、模具结构、冲压力的传递方式等因素。
生产阶段1. 材料处理:铝合金材料在冲压前需要进行预处理,包括氧化膜清除、表面处理、退火等工艺。
氧化膜的清除对于提高冲压质量至关重要。
2. 冲压工艺:车用铝合金中铝板冲压的工艺包括下料、模具装配、模具调试、冲压成型等环节。
在这个过程中,需要注意工艺参数的设定、模具的调整、冲压速度的控制等关键技术。
3. 质量控制:在冲压过程中,需要通过一系列的质量控制手段来保证产品的质量。
包括对材料的质量把控、对工艺参数的监控、对成品的检测等。
关键技术车用铝合金中铝板冲压的关键技术主要包括材料选择、零部件设计、模具设计、材料处理、冲压工艺、质量控制等方面。
这些技术点的合理运用能够提高产品的质量,降低成本,推动汽车轻量化的发展。
材料选择是车用铝合金中铝板冲压的第一步,选择合适的铝合金材料可以保证产品的成型质量和性能。
合理的零部件设计和模具设计也能够降低生产成本,提高生产效率。
材料处理和冲压工艺则是冲压生产过程中的关键环节,通过合理的处理和控制能够保证产品质量和工艺稳定性。
- 1、下载文档前请自行甄别文档内容的完整性,平台不提供额外的编辑、内容补充、找答案等附加服务。
- 2、"仅部分预览"的文档,不可在线预览部分如存在完整性等问题,可反馈申请退款(可完整预览的文档不适用该条件!)。
- 3、如文档侵犯您的权益,请联系客服反馈,我们会尽快为您处理(人工客服工作时间:9:00-18:30)。
铝合金汽车车门冲压成形工艺研究
发表时间:2019-02-13T09:45:53.813Z 来源:《电力设备》2018年第25期作者:张健沙佳辰
[导读] 摘要:随着社会经济的发展,人们的环保意识越来越强,在汽车行业中,已经开始利用铝合金材料,通过大幅减轻自身车体重量,达到减少油耗和尾气排放量的目的。
(长城汽车股份有限公司河北保定 071000)
摘要:随着社会经济的发展,人们的环保意识越来越强,在汽车行业中,已经开始利用铝合金材料,通过大幅减轻自身车体重量,达到减少油耗和尾气排放量的目的。
对此,针对铝合金材料的车门冲压工艺进行优化,对铝合金车门形成特点进行综合分析。
关键词:铝合金材料;车门冲压;工艺优化
近年来,我国的汽车行业有了飞速的发展,其对环境的污染问题也越来越突出,节约资源和减少污染成为汽车行业亟待解决的两大问题。
着眼于可持续发展,减轻汽车质量,降低燃油消耗及减少排放污染的任务显得尤为迫切,汽车轻量化技术是解决这些问题的重要途径之一。
研究结果表明,汽车质量每减少10%就可以降低6%~8%的燃油消耗。
铝合金具有密度小、强度高、耐腐蚀性强、抗冲击性能好和再回收能力强等一系列优良特性,并且资源相对丰富,将成为汽车工业中最具竞争的轻质材料。
但是铝合金在室温条件下,其成形性能较差,总伸长率小,且弹性系数仅为钢板的1/3,成形时金属流动困难,从而其应用受到一定的限制。
在高温下铝合金塑性好、变形抗力低、成形难度低,因此,铝合金的热冲压成形技术受到人们的广泛关注。
1工艺方案的制定
(1)拉延工序工艺方案的制定:拉延工序是覆盖件冲压成形的关键工序,覆盖件的大部分形状是在此工序形成,拉延成形的好坏将直接影响覆盖件质量。
该工序一方面成形出零件的大部分形状,同时在拉延过程中还将对坯料进行切角,减少落料模具,降低成本。
结合零件的工艺性,在拉延工序中对零件的某些部分做如下处理。
◎第一方案,增大模具圆角,以减小材料流动阻力,再对相应部分进行整形;第二方案,利用在窗框的适当部位冲切工艺切口的方法,使容易破裂的区域从相邻区域里得到材料补充,从而改善该区域的变形情况,避免破裂的产生。
◎在零件处,为了避免一次拉延可能产生的缺陷,考虑作二次拉延,从而降低第一次拉延的难度,拉延工序工艺的制定包括拉深方向的选择、工艺补充和压料面的设计等。
选择合理的拉延方向应考虑以下原则:保证能将拉延件的全部空间形状一次拉延出来,不产生负角;尽量使拉深深度浅且均匀;保证凸模有良好的接触状态;有利于防止表面缺陷;同时要考虑后工序内容和模具结构。
合理的压料面形状应遵循以下几个主要设计原则:压料面的形状应尽量简单;在拉延过程中压料面任一断面的展开长度要小于拉延件内部相应断面的长度;压料面应使成形深度小且各部分深度接近一致。
结合本零件的特点,压料面沿零件四周的变化趋势顺延成曲面。
在进行工艺补充时,应主要考虑以下几个原则:尽量简化拉延件结构形状;工艺补充部分尽量小,以提高材料利用率,降低成本;对后工序有利原则,如定位、修边等。
由于后工序全部有冲孔动作,出于模具结构简单化的目的考虑,窗框型面部分采用向下整形,并保证合适的切边角度,并将侧壁作了8°的拔模角。
其余部分顺着产品延伸出来。
(2)其余工序工艺方案该覆盖件部分孔和其他大部分孔的方向相差约10°,并且考虑到窗框型面弧度变化,第一工序和第二工序的冲压方向相同,后工序冲压方向与之相差10°,现将后工序进行简单介绍。
工序二为二次拉延+切边+冲孔,局部区域进行整形,切边时考虑了窗框内废料较大,将其分三块切掉,考虑模具结构强度的原因,本工序切出两端的两块。
工序三为切边+冲孔,将余下全周进行切边,同时冲出部分孔。
工序四为侧切+侧冲孔翻孔+冲孔+整形,窗框内边整形,侧向门锁安装孔在此工序全部完成,此部分内容的完成也是模具结构的难点,采用双动斜楔机构。
工序五为整形+冲孔,全周法兰边整形,冲切余下孔,因为零件的法兰边要与外板进行扣合,法兰边的平展度将直接影响扣合的质量,故在此工序安排了法兰边全周的整形[1]。
2铝合金板材影响因素分析及优化
2.1铝合金材料特性的影响
因为铝合金材料具有鲜明的立体结构,并且在车门冲压成型操作过程中,在车门铝合金半成件温度升高的条件下可以大幅度提升铝合金敏感度系数m值,从而可以对铝合金材料成形性等进行改善。
2.2模具压力边的影响
利用优化圆角模具,可以大大的改变铝合金表面的应变力,在进行铝合金车门受力拉深过程中,通过表面拉深力的作用,很容易发生塑形形变。
通过对车门常用的5754和6111型铝合金材料,进行拉深测试,结果发现优化的圆形模具使车门表面半径下降至少6mm,而且在拉抻过程中,模具自身对车门拉伸力的影响都比较小,车门表面成型时受到的拉伸力整体下降比较平缓。
2.3冲压速度对成形质量的影响
在相同温度下,随着冲压速度的提高,材料的应变率相应增大,高温下铝合金发生动态回复与动态再结晶受到限制,应变硬化得不到松弛,使得变形抗力增加。
当冲压速度为50mm/s时,铝合金能够较好的发生动态回复与动态再结晶,变形抗力小,压边区的材料能够顺利地通过传力区进入到成形区,从而使板料危险截面的最小厚度较大,成形质量较好;当冲压速度为100mm/s和200mm/s时,由于应变率较大,动态回复和动态再结晶都受到抑制,变形抗力较大,使成形区材料的流入受到一定的阻碍,从而板料危险截面的最小厚度较小[2]。
高温下,当冲压速度达到一定程度时,铝合金的动态回复与动态再结晶受抑制的程度基本上相同,此时,在其他条件不变的情况下,增加冲压速度对板料的成形质量影响较小。
3车门压力边加载模式优化
3.1恒定压力边加载模式
在铝合金材料成型过程中,一旦车门冲压形成的褶皱无法适应优化模具,就可以通过安装合适的压边进行直接设置。
现阶段在铝合金材料的车门冲压中,常用到的车门压边装置大多以刚性压边为主。
所谓刚性压边主要是指利用车门压力机上外设的动态滑块进行车门压边。
在实际车门压深过程中,车门四周受到的压边力处于恒定状态,整体拉深效果更好。
从压边实际操作上来看,在车门拉深过程中对进行适当的压边力和冲压控制可以有效调节冲压车门,从而直接控制车门成品质量。
对于铝合金材料车门冲压成型压边力优化技术的研究,是当今材料板材研究的重点,铝合金车本的边压力,在铝合金板材车门冲压力形成的过程中有着非常重要的作用[3]。
3.2破裂临界压边力
如果在车门冲压过程中,拉深力超过了铝合金最薄区域所能达到的最大应受力,整个车门的铝合金材料就会因为拉力过大而报废。
所以可以通过POER-LE软件,提交对铝合金车门胚件进行整体测评,划分交界面区域,对其最大受力性进行参数测评。
获取参数后,对拉抻
力进行综合优化,保证整体受力均匀,防止因为拉抻力过大导致的胚件损坏。
结语
综上所述,针对现阶段我国汽车行业来说,铝合金材料的应用技术和应用范围仍然还处在借鉴、研究的过程。
目前我国虽然已经成为世界第五大汽车生产国和第七大汽车出口国,但是我国应用铝合金材料的汽车总量占总生产量比例不超过15%,所以未来必须在充分了解铝合金冲压性的基础上,从模具的制造、拉抻力的分布以及压力边等多个方面,继续对铝合金的应用进行更深层优化。
参考文献
[1]吕萌萌,谷诤巍,徐虹,等.超高强度防撞梁热冲压成形工艺优化[J].吉林大学学报(工),2017,47(6):1834-1841.
[2]肖红波,蔡浩华.汽车前翼子板冲压成形工艺优化[J].锻压技术,2016(2):35-38.
[3]董娇,杨印安.基于稳健设计的冲压成形工艺参数多目标优化[J].模具工业,2017,43(9):22-26.。