BP德克萨斯炼油厂爆炸事故案例分析
BP德克萨斯炼油厂事故分析
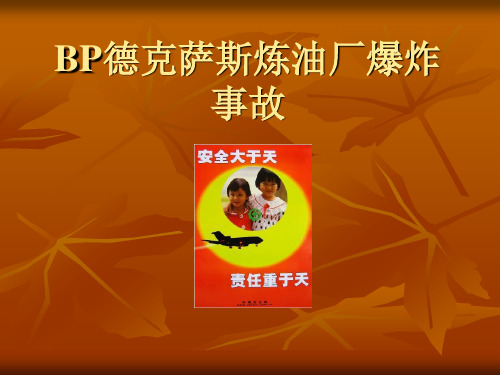
1、管理原因 (1)尽管炼油厂的许多基础设施和工艺设备已经 年久 失修,但BP公司继续削减成本,造成安全投入不 足。 尽管早先已报告该塔的液位计、液位观察孔和压 力控 制阀出现故障,但装置仍按原计划开车。
2)BP公司和德州炼厂的管理人员没有履行有效 的领 导和监督责任。对集团公司的安全文化和重大事 故预 防体系没有给予足够的关注,BP公司管理层安全 监督 不力,没有提供足够的人力和财力,也没有建立 一套 安全管理模式对安全法规和操作规程执行情况进 行监 督与考核。
2005年3月23日上午,BP美国德克萨斯州炼油厂的 一套异构化装置的抽余油塔在经过2周的短暂维修后, 重新开车。开车过程中,操作人员将可燃的液态烃原 料不断抽入余油塔。抽余油塔是一个垂直的蒸馏塔, 内径3.8 m,高51.8 m,塔内有70块塔板,用于将抽 余油分离成轻组分和重组分。在3个多小时的进料过 程中,因塔顶馏出物管线上的液位控制阀未开,而报 警器和控制系统又发出了错误的指令,使操作者对塔 内液位过高毫不知情。液体原料装满抽余油塔后,进 入塔顶馏出管线。塔顶的管线连通距塔顶以下45.1 m 的安全阀。(下续)
(5)不注重更新安全操作规程,为操作者 违反操作规 程提供了条件。没有制定有效的安全操作 限值。 (6)人手不足,对操作人员的培训不到位, 没有特别 强调开车期间的危险性。
(7)BP公司没有建立良好的事故调查管理系统。 1994~2004年,BP公司这套加氢装置的放空罐已 经发 生了8次严重的事故,但只对3起事故进行了调查。 (8)未熄火的汽车距离有燃爆危险性的装置太近。 BP 公司德州炼厂的管理人员没有遵从安全要求,未 将无 关人员从附近区域撤出。
2005年BP德克萨斯州炼油厂爆炸事故
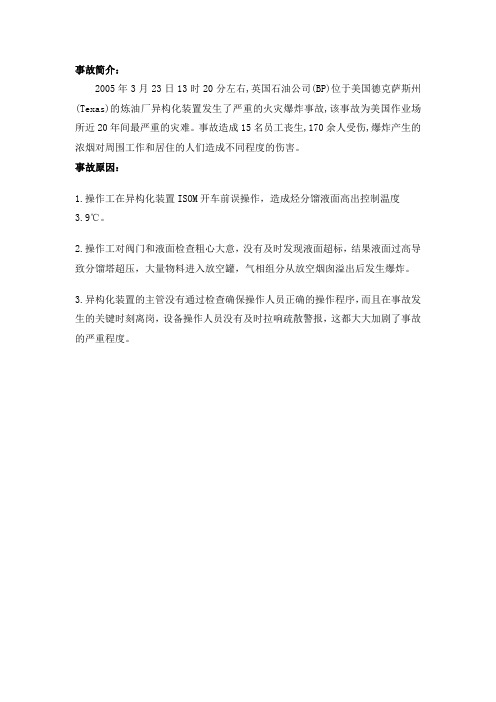
事故简介:
2005年3月23日13时20分左右,英国石油公司(BP)位于美国德克萨斯州(Texas)的炼油厂异构化装置发生了严重的火灾爆炸事故,该事故为美国作业场所近20年间最严重的灾难。
事故造成15名员工丧生,170余人受伤,爆炸产生的浓烟对周围工作和居住的人们造成不同程度的伤害。
事故原因:
1.操作工在异构化装置ISOM开车前误操作,造成烃分馏液面高出控制温度
3.9℃。
2.操作工对阀门和液面检查粗心大意,没有及时发现液面超标,结果液面过高导致分馏塔超压,大量物料进入放空罐,气相组分从放空烟囱溢出后发生爆炸。
3.异构化装置的主管没有通过检查确保操作人员正确的操作程序,而且在事故发生的关键时刻离岗,设备操作人员没有及时拉响疏散警报,这都大大加剧了事故的严重程度。
BP德克萨斯炼油厂爆炸事故案例学习(教学版)分析
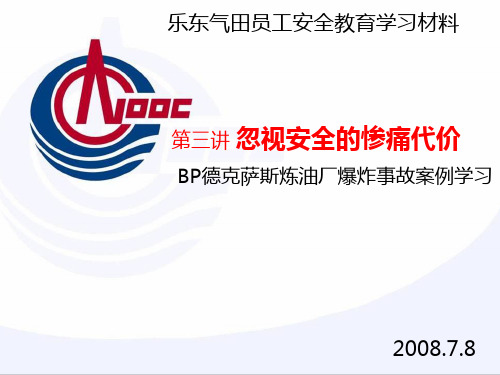
后果:由于削减成本,得克萨斯州炼厂很多设备年久失修, 无法更新;员工雇佣成本和设备更新维护方面的预算被大 量削减。这些削减对生产安全产生了负面影响。
第一章
概述
2005 年3 月23 日13 时20 分左右,英国石油公 司(BP)位于美国德克萨斯州(Texas)的炼油厂 异构化装置发生了严重的火灾爆炸事故,该事故为 美国作业场所近20年间最严重的灾难。事故造成15 名员工丧生,170 余人受伤,爆炸产生的浓烟对周围 工作和居住的人们造成不同程度的伤害。
第一章
概述
1999年之前,得克萨斯城炼油厂属于阿莫科石油公司。在 属于阿莫科石油公司管理期间的1994年,管理层决定减 少得克萨斯炼厂的人数以不断削减人力成本。
第一章
概述
根据当时被各大公司竞相追捧的一个用人原则,减少 18%的员工,就能节省2200万到3300万美元的人力成 本投资。如果减少31%的员工,就能节约4200万到 6100万美元的花销。 1999年,BP收购阿莫科石油公司 在得克萨斯城炼油厂的人员管理和设备投资方面,低 成本的战略得以维持并被BP公司继续维持下去。
第一章
概述
低成本的战略在得克萨斯城炼油厂人员管理方面所产 生的影响:
人手不足 相关机构的研究发现,在过去的四年里,得克萨斯 炼厂的操作工和维护人员加班时间占总工作时间的 27%,有些员工甚至高达68%。这么高的加班比率 远远超出正常水平,这是得克萨斯炼厂员工人数不 足的一种表现。
第一章
概述
BP低成本的战略在设备投资方面的表现: 1999年,BP收购阿莫科后削减了得克萨斯炼厂25%的固定 资产投资,两年后固定资产投资又削减了25%。
2.2 事故过程描述
2005 年3 月23 日凌晨2 时左右,异构化装置的操作人员将 液态烃原料导入分馏塔中。 凌晨3 时30 分,开始进料,当时液位计指示塔内液位在距离 塔底3.0 m 处。 9 时50 分左右,操作员开始将液态原料进行循环,并将更 多的液体打入液位已经过高的塔中,
TAPLINE-HSECASE-1BP德克萨斯P炼油厂爆炸事故教训2012-10-24
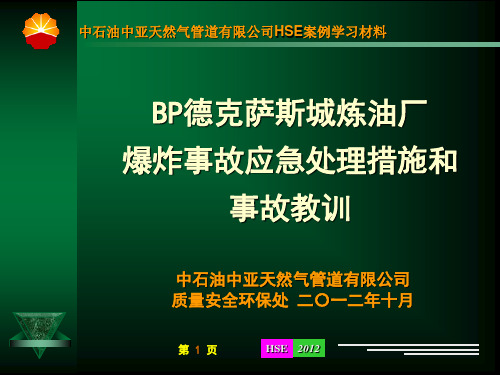
HSE 2012
四、事故调查情况
5月17日,BP事故调查小组公布了初步调查报告,
称因BP相关人员在异构化装置开车前和开车过程中 的一系列失误,导致BP得克萨斯州炼油厂发生火灾 和爆炸事故。如“装置主管的失职和值班工人没有 遵循书面程序规定是事故发生的根本原因,主管没 有通过检查确保操作人员正确的操作程序,而且在 事故发生的关键时刻离岗,设备操作人员也没有及 时拉响疏散警报。
中石油中亚天然气管道有限公司HSE案例学习材料
BP德克萨斯城炼油厂
爆炸事故应急处理措施和
事故教训
中石油中亚天然气管道有限公司 质量安全环保处 二〇一二年十月
第 1 页 HSE 2012
一、事故情况
2005年3月23日,BP位于美国得克萨斯州休斯敦 南部地区的得克萨斯城炼油厂异构化装置在开车过程 中发生爆炸着火,造成15人死亡、170多人受伤。
第 9 页
HSE 2012
四、事故调查情况
调查中发现诸多问题,如:
Байду номын сангаас●异构化装置开车时,没有积极的监控;
●印制了启动程序操作人员没有执行;
●关于以前事故的文件不完备; ●没人察觉危险,比如说,放置的拖车与炸毁的
烟囱近在咫尺;
●没有做出更多的努力,调整在员工调查中发现
的士气低落和对站点管理的不信任。
第 10 页
富有人情味的补救措施。BP在事故当天即开辟
了事故专栏,发布与事故相关的消息,各级管理 人员对员工和媒体的讲话均放在网上,并随时公 布事故调查进展情况。首席执行官约翰布朗公开 向公众道歉,他说“德州炼油厂的爆炸事故是
BP近年来最糟糕的一起悲剧,我们将竭尽所能,
确保不再发生”
第 5 页
BP炼油厂重大事故调查报告

重建与提升
针对事故原因,改进和提升生 产设施和安全性能。
04
事故调查
调查组织与程序
调查组织
BP炼油厂重大事故发生后,当地政府成立了专门的事故调查组,由相关部门 和专家组成,对事故进行全面调查。
调查程序
事故调查组制定了详细的调查计划,包括现场勘查、取证和技术鉴定等步骤 ,同时对相关人员进行问询和调查。
加强安全生产培训与教育
对员工进行定期的安全生产培训,提高员工的安 全意识和操作技能。
开展多种形式的安全教育活动,加强员工的安全 意识培养。
对安全生产培训和教育效果进行评估和反馈,不 断改进和提高培训教育质量。
完善安全生产责任制考核机制
建立和完善安全生产责任制 考核机制,明确各级管理人 员和员工的安全生产职责。
加强领导干部安全意识
加强领导干部的安全意识培养,使其能够起到表率作用,并 将安全生产纳入到企业整体战略中。
安全生产管理体制不健全
建立健全安全生产管理体系
建立完善的安全生产管理体系,明确各级管理人员在安全生产中的职责和权 限,形成科学有效的管理机制。
加强安全检查和隐患排查
定期进行安全检查和隐患排查,发现并解决存在的安全隐患,确保生产过程 的安全。
损失
BP炼油厂被迫关闭,周边企业生产受到不同程度的影响。
事故等级与性质
等级
美国国家应急管理局(NRC)将事故定为“重大”级别。
性质
爆炸、火灾、有毒化学物质泄漏等多种因素交织的复杂事故 。
02
事故原因分析
直接原因分析
操作失误
操作人员在进行催化剂注入时,未能按照规定步骤进行,导致催化剂注入量 过大。
EHS课程_事故分析

EHS常用网站
EHS常用网站(公众环境研究中心IPE)
Thanks !
加工工艺流程图
事故经过
START 03:30
09:50
12:40
13:0013:20 Nhomakorabea开始进料, 当时液位计 指示塔内液 位距离塔底 3.0m处
操作员开始将液态原 料进行循环,并将更 多的液体打入液位已 经过高的塔中。点燃 火嘴开始加热。液位 计仍然将液位指示在 3m一下并不断下降。 (液位计失灵!)
发出了高压警 报,火嘴被关 闭以降低物料 温度。
换热器出现 异常。原料 温度升至 150。液体 膨胀塔出现 溢流。
液体由烟囱口
溢出,落到地 上迅速形成极 易燃烧的蒸汽 云,停在附近 的货卡未关闭 引擎,引发爆 炸。
END
事故详细经过
正常情况下,塔底分馏液位 只有1.98m,塔底设有1个液位计, 可以检测塔内液位并将数据传送 给控制室。同时,塔内设有两个 报警器,超出规定液位时,控制 室将声音报警。但是晚班工作人 员在液位超过2.5m,报警器报 警时将其关闭,且声称过度进料 不但可以节省时间,还能避免加 满的不便。事故发生时,液位已 超出3.0m,操作人员无法正确 读取数据,而备用报警器早已失
事故回顾
➢ 2005年3月23日中午1点20分左右,英国石油公司(BP)在美 国德克萨斯州的炼油厂碳氢化合物车间发生系列爆炸。15名工人 死亡,170余人受伤。在周围工作和居住的许多人成为爆炸燃烧中 产生的浓烟的受害者。
➢ 爆炸发生后,美国化学品安全与危险调查局随即于3月26日组 成了专题调查组,并于4月1日进驻BP在德州的炼油厂。此次CSB公 布的调查结果表明,该公司明知该车间的一些警报器和一个液位 变送器失效,却仍然启动了设备,结果发生爆炸。
事故案例分析2013.1
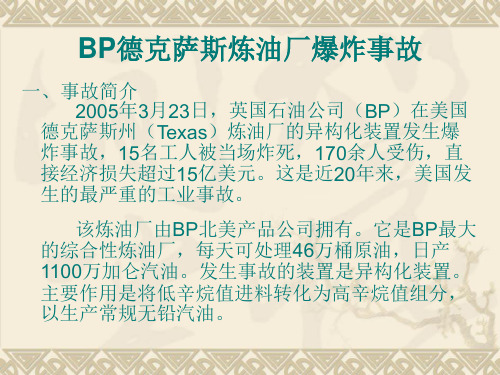
二、事故原因 1)912号储罐的自动测量系统(ATG)失灵,储罐装满时,液位计停止在储罐的 2/3液位处, ATG报警系统没能启动,储罐独立的高高液位开关也未能自动开启 切断储罐的进油阀门,致使油料从罐顶溢出,从罐顶泄漏的油料外溢,油料挥发, 形成蒸气云,遇明火发生爆炸、起火。 2)尽管邦斯菲尔德油库进行了三级设防,由于一级设防的缺陷使外溢的油料形成多 处瀑布,加速了蒸气云的形成,二级和三级设防主要是用于保护环境的,但由于 泄漏的油料形成大面积池火,高温破坏了防火堤,致使防火堤围墙倒塌和断裂, 同时殃及了第三级设防,大量的油料和消防泡沫流出库区。 3)部分储罐和管道系统的电子监控器以及相关的报警设备处在非正常工作状态。 4)储罐和管道系统附近的可燃气体检测仪器不灵敏。 5)对于某些处于非正常工作状态设备的检查不及时,响应迟钝,诸如储罐入口的自 动切断阀和管线入口的控制阀等。 6)储罐的结构设计(如罐顶的设计)不尽合理,这在一定程度上加剧了油料蒸气云 形成的可能性。 7)罐区应急设施(如消防泵房等)的选址和保护措施不合理。 三、 教训与启示 此次邦斯菲尔德油库事故除设计和操作的原因外,油库选址存在安全隐患也 是教训之一。英国健康安全署(HSE)在过去审批过程中,对油库选址与周围发 展问题考虑不够,只考虑储罐油料泄漏在防火堤内形成池火,未充分考虑油料蒸 气云爆炸的潜在危害性;只对汽车罐车装卸站台可能发生油料蒸气云爆炸的风险 在应急预案中作了相应的准备。邦斯菲尔德油库事故提示我们应对油库罐区和选 址的安全评估标准进行新的修改。
由于喷出的油气量比较大,油气从放空罐顶部的放空管喷 出(放空管直接排大气,高度34.4米左右),大量汽油流向罐 周围并迅速气化。在第一次小的爆炸后,在13:20发生大爆炸。 由于放空罐附近的临时活动房(为另一套检修装置服务)内仍 有很多人,在油气大量喷出并迅速气化的情况下也没有组织疏 散,导致事故伤亡人数大大增加。
BP德克萨斯炼油厂爆炸事故案例分析

B P德克萨斯炼油厂爆炸事故案例分析2005年3月23日13时20分左右,英国石油公司(BP)位于美国德克萨斯州(Texas)的炼油厂异构化装置发生了严重的火灾爆炸事故,该事故为美国作业场所近20年间最严重的灾难。
事故造成15名员工丧生,180余人受伤,爆炸产生的浓烟对周围工作和居住的人们造成不同程度的伤害,直接经济损失超过15亿美元。
炼油过程中主要的操作装置为蒸馏塔,重新启动过程长达12小时,蒸馏塔的主要功能就是蒸馏生燃料,分离较重与较轻的成分,液态生燃料进入蒸馏塔的途中由加热炉加温,较轻的成分会蒸发,蒸汽升到塔顶,再由管子排送出去,蒸汽经过冷凝器液化接着便被抽走,提高汽油效能,此时抽取留在塔底的较重残余物,这些成分用来制造沥青等产品,如果蒸馏过程制造出太多蒸汽,操作员应排放多余气体降压,这些气体最终抵达安全出口即排放烟囱。
此为炼油厂主要的加工工艺过程。
从视频中可以看出,进料、开关阀门等操作过程均由电脑控制、人为操作,多数程序必须由手动操作完成,因此人是该厂最最重要的安全因素,任何的人为操作失误都有可能引起重大安全事故。
蒸馏塔进行了数年一次例行检修,蒸馏塔中油位高度由电脑读取控制,人为操控。
备用警报器经后期检查已经损坏,起不到警报作用,而后最重要的排液控制阀未开启,导致过量的夜料排不掉被迫进去排气管,最后充满35米高的烟囱爆出,导致爆炸的发生。
视频中多处显示出人为操作失误,夜班操作员无视蒸馏塔进料超过标准将警报关掉,并继续进料15分钟;日班领班在接到儿子摔伤的电话后离去,擅离职守,请同事代为控制监督;开入的白色小货卡未关闭引擎司机离去久未归,这些人为原因都直接或间接的导致了爆炸的发生。
综合人为因素、设备因素,导致了事故的发生。
在蒸馏塔三个多小时的进料过程中,因塔顶馏出物管线上的排液控制阀未开,而报警器和控制系统又发出了错误的指令,使操作者对塔内液位过高毫不知情。
液体原料装满蒸馏塔后,进入塔顶馏出管线。
重大安全事故案例分析
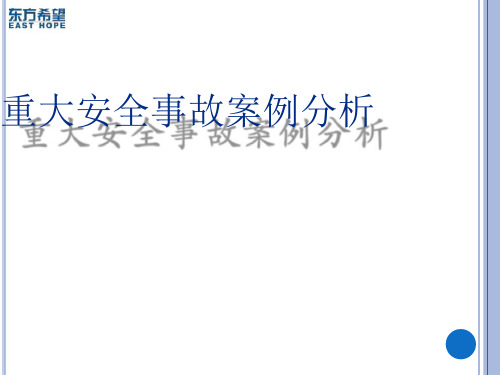
气被吸入到系统内,与T101塔内可燃气体形成爆炸性气
体混合物,引发硝基苯初馏塔和硝基苯精馏塔相继发生
爆炸。
二、事故原因
1、管理原因:
(1)中国石油天然气股份有限公司吉林石化分公司及
双苯厂对安全生产管理重视不够、对存在的安全隐
患整改不力,安全生产管理制度存在漏洞,劳动组
重要原因。
(3)未按本质安全的原则进行工厂操作。
内危险化学品的存储量。事故工厂MIC的储存量约为
171m3,有专家质疑储存如此大量危险物料的必要性。
事故发生时,实际液位是87%。
后,报警温度被设定在20℃(按规定,当温度超过
11℃时,就应该报警),实际的操作温度基本上在
15℃左右。
(4)应急反应效率低。在该工厂,少量的泄漏早已司
下降至正常值。
13时21分,在组织T101进料时,再一次错误操作,
没有按照“先冷后热”的原则进行操作,而是先开启进
料预热器的加热蒸汽阀,7分钟后,进料预热器温度再
次超过150℃量程上限。
13时34分启动了硝基苯初馏塔进料泵向进料预热器
输送粗硝基苯,当温度较低的26℃粗硝基苯进入超温的
进料预热器后,由于温差较大,加之物料急剧气化,造
3、需要对危害较大的工艺系统进行系统的工艺危害分析。
辨别工艺系统可能出现的偏离正常工况的情形,找出
相关的原因与后果,并提出消除或控制危害的改进措
施,从而提高系统的安全性能。
4、建立和切实执行工艺系统的变更管理制度,严肃对
待工艺系统和操作/维修程序的变更。工艺系统的
重要安全设施(如本案例中的冷冻系统和火炬)之
操作者,应该将抽余油产品导入储罐;夜班工作人员
BP德克萨斯炼厂爆炸事故的教训
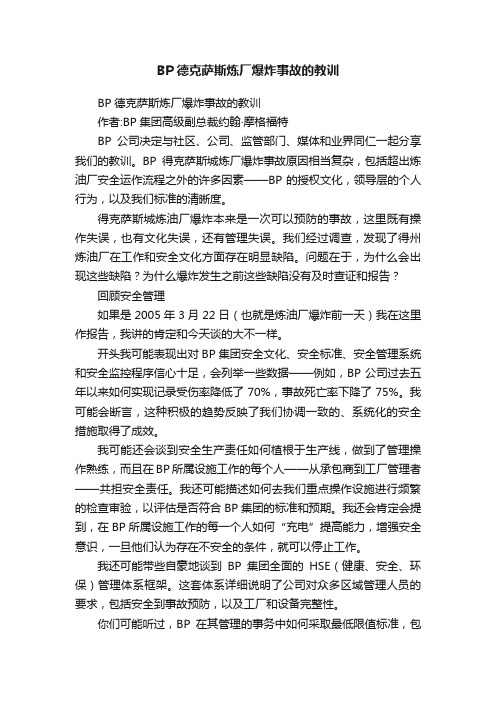
BP德克萨斯炼厂爆炸事故的教训BP德克萨斯炼厂爆炸事故的教训作者:BP集团高级副总裁约翰·摩格福特BP公司决定与社区、公司、监管部门、媒体和业界同仁一起分享我们的教训。
BP得克萨斯城炼厂爆炸事故原因相当复杂,包括超出炼油厂安全运作流程之外的许多因素——BP 的授权文化,领导层的个人行为,以及我们标准的清晰度。
得克萨斯城炼油厂爆炸本来是一次可以预防的事故,这里既有操作失误,也有文化失误,还有管理失误。
我们经过调查,发现了得州炼油厂在工作和安全文化方面存在明显缺陷。
问题在于,为什么会出现这些缺陷?为什么爆炸发生之前这些缺陷没有及时查证和报告?回顾安全管理如果是2005年3月22日(也就是炼油厂爆炸前一天)我在这里作报告,我讲的肯定和今天谈的大不一样。
开头我可能表现出对BP集团安全文化、安全标准、安全管理系统和安全监控程序信心十足,会列举一些数据——例如,BP公司过去五年以来如何实现记录受伤率降低了70%,事故死亡率下降了75%。
我可能会断言,这种积极的趋势反映了我们协调一致的、系统化的安全措施取得了成效。
我可能还会谈到安全生产责任如何植根于生产线,做到了管理操作熟练,而且在BP所属设施工作的每个人——从承包商到工厂管理者——共担安全责任。
我还可能描述如何去我们重点操作设施进行频繁的检查审验,以评估是否符合BP集团的标准和预期。
我还会肯定会提到,在BP所属设施工作的每一个人如何“充电”提高能力,增强安全意识,一旦他们认为存在不安全的条件,就可以停止工作。
我还可能带些自豪地谈到BP集团全面的HSE(健康、安全、环保)管理体系框架。
这套体系详细说明了公司对众多区域管理人员的要求,包括安全到事故预防,以及工厂和设备完整性。
你们可能听过,BP在其管理的事务中如何采取最低限值标准,包括允许工作、能源绝缘、地面干扰、限制区进入、工作高度、起重操作、安全驾驶和应变管理——从中得出有关公司事故和严重伤害的深入调查结论,用以鉴别行为方式差错。
BP德克萨斯炼油厂爆炸事故案例学习(教学版)分析
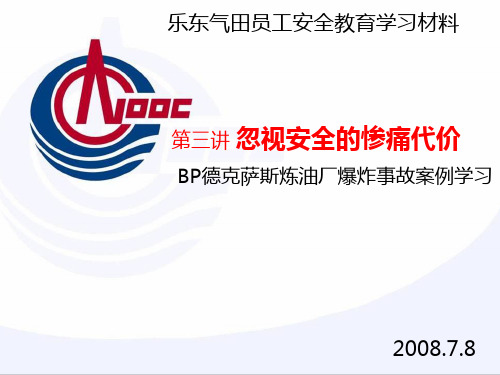
第二章
事故经过
13时左右,换热器出现异常,并且导致进入塔的原 料温度突然上升至150℃以上。 13 时5 分,进入塔中的液体开始膨胀并沸腾,导致 塔内的液位进一步上升; 13 时10 分左右,塔开始出现溢流,液体被排到塔 顶的排放管中; 13 时14 分,3 个应急泄压阀被打开,液体从异构 化装置流向放空罐,部分液体从放空罐溢出进入排污管 中。
同时,BP公司聘请外部专家对得克萨斯城炼油厂的 爆炸进行了模拟,测试关键成因。
第三章
事故调查
企业内部事故调查初步调查结果: 事故调查小组认为,爆炸的发生是由于BP 异构化装置的 操作人员向分馏塔中过量进料并过度加热分馏塔造成的, 分馏塔内的液位几乎超过正常值的20 倍。同时,装置开 车时异构化装置中的水蒸气或氮气的存在也可能导致塔内 的压力突然升高,使得大量烃类液体和蒸气进入临近的放 空塔,并很快超过放空塔上限,最终,形成的烃类蒸气云 被不明火源点燃从而引发了爆炸。
第二章
事故经过
爆炸后放空罐继续喷出烃类物质,装置持续燃烧。
第二章
事故经过
距离异构化装置数百 米远距离上拍摄的图 像-浓烟滚滚
第二章
事故经过
事故后的现场:异构化装置成为了废墟。
第二章
事故经过
2.4 学员观看事故录像
放映该事故的录像,该录像真实的还原了事故发生的 整个过程以及所造成的惨痛后果。
时间:35mintues
第二章
事故经过
个人记录区
5.从危险源辨识与风险分析来看
拓展: 乐东22-1气田隐患管理制度 拓展: 乐东22-1气田隐患管理制度 隐患:是指作业场所生产设备和设施的不安全状态, 人的不安全行为和管理上的缺陷,是潜藏或不易发现 的危险或祸患,是引发事故的直接原因。 一般隐患:是指生产装置通过努力在现场能自行整 改和解决的隐患。 重大隐患:是指生产装置不能自行解决,需分公司 协调整改和解决的隐患。
BP美国炼油厂爆炸事故

BP美国德克萨斯(Texas)炼油厂爆炸事故高前进赵建民1、事故简介2005年3月23日下午1点20分,一系列猛烈的爆炸发生在BP美国德克萨斯(Texas)炼油厂的一个正在开工的异构化装置。
爆炸造成15人死亡,180人受伤,在爆炸现场的工艺泄放烟囱旁边当时放置了一些检修用的可移动拖车,这些死伤人员中的大多数当时都是在拖车的里面或外面。
爆炸冲击波摧毁了附近的50个大型化学品储罐,震碎了3/4英里外的居民窗户玻璃,滚滚黑烟从工厂翻腾而出,当局指示约4万4千德克萨斯(Texas)市的居民呆在室内不要外出。
异构化装置被迫停工超过两年,BP公司为此爆炸损失数十亿美元。
图1:事故后的异构化装置的现场3月23日早上,炼油厂的异构化装置的萃取油分馏塔在检修后重新开工进料,操作员用泵连续向分馏塔内送可燃物料超过三个小时,在这三个小时的过程中没有将物料从塔内送出,这和操作开工指导是相矛盾的。
关键的报警和控制仪表显示假值,没能提醒操作员分馏塔内物料的液位已经很高。
结果,在操作员不清楚的的情况下,高170英尺(52米)的分馏塔进料过多,液体进料溢流到了塔顶部的管道中。
分馏塔顶部管道向下走,在约148英尺(45米)高的位置安装有三个安全阀。
当塔顶部的管道充满液体时,塔底部的压力迅速地从21psi升高到64psi,三个安全阀起跳打开持续了6分钟,排放了大量的可燃液体到下游的排放收集罐,这个排放收集罐通过一个泄放烟囱和大气相连通。
排放收集罐和泄放烟囱都相继溢流,大量的可燃液体从113英尺(34米)高的泄放烟囱顶部象喷泉一样地喷涌而出。
排放收集系统是一种陈旧的且不安全的设计,它是在19世纪50年代安装的,这个系统从来也没有和火炬系统相连通,不能安全地收集从工艺装置泄放的液体和可燃易燃的气体。
这些喷涌出的易挥发的液体,流到地面后形成了可燃蒸汽云。
在离排放收集罐约25英尺(7.6m)的地方停了一辆没有熄火发动机空转的皮卡车,扩散的可燃蒸汽随即被点燃,火焰迅速扩散,可燃蒸汽云被点燃,接下来在装置区发生了一系列的爆炸。
化工事故案例分析
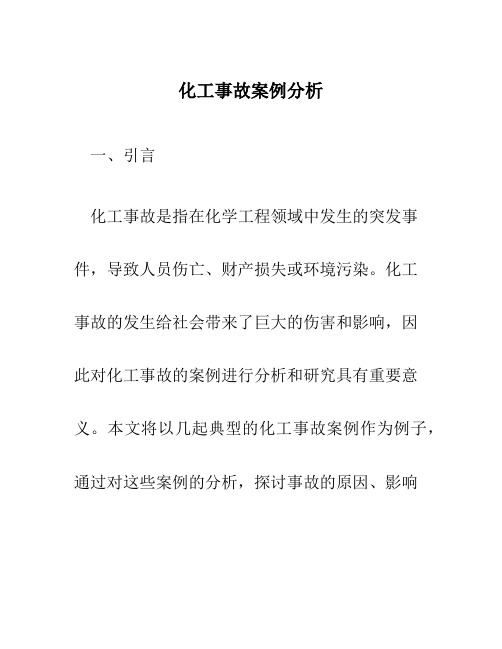
化工事故案例分析一、引言化工事故是指在化学工程领域中发生的突发事件,导致人员伤亡、财产损失或环境污染。
化工事故的发生给社会带来了巨大的伤害和影响,因此对化工事故的案例进行分析和研究具有重要意义。
本文将以几起典型的化工事故案例作为例子,通过对这些案例的分析,探讨事故的原因、影响以及相应的防范措施,以期提高人们对化工事故的认识和预防能力。
二、案例一:2005年美国得克萨斯州蒙塔瓦炼油厂爆炸1. 案例背景2005年3月23日,美国得克萨斯州蒙塔瓦炼油厂发生了一起严重的爆炸事故,该事故导致15人死亡,上百人受伤,造成巨大的财产损失。
该炼油厂是该地区最大的炼油厂,也是臭氧层破坏物质的主要制造商之一。
2. 事故原因分析经过调查,事故的原因主要有以下几个方面:(1)操作失误:操作人员未按照规定操作程序进行操作,导致了事故的发生。
操作人员在进行装载燃料过程中没有及时检查和修理卸油软管,最终导致了油气泄漏和爆炸。
(2)设备故障:事故中使用的设备存在一定的故障和缺陷。
在事故发生前,该炼油厂的监测系统未能及时发现油气泄漏,导致事故无法及时预警。
3. 事故影响及防范措施该次事故导致了严重的人员伤亡和财产损失,同时对环境产生了严重的污染。
为防止类似事故再次发生,可以从以下几个方面采取相应的防范措施:(1)加强操作培训:化工企业应加强对操作人员的培训,提高他们的操作能力和安全意识,确保操作规程得到严格执行。
(2)完善监测系统:加强对设备故障及时发现的能力,建立完善的监测系统,确保事故能够及时预警并进行相应的应对措施。
三、案例二:2015年中国天津港爆炸事故1. 案例背景2015年8月12日晚间,中国天津港发生了一起重大爆炸事故,该事故导致173人死亡,数百人受伤。
爆炸造成的巨大冲击波摧毁了大量附近的建筑物。
2. 事故原因分析经过调查,事故的原因主要有以下几个方面:(1)危险化学品储存不当:事故发生地点附近的仓库储存了大量危险化学品,包括硝酸铵等易燃易爆物品。
重大化学火灾事故案例分析
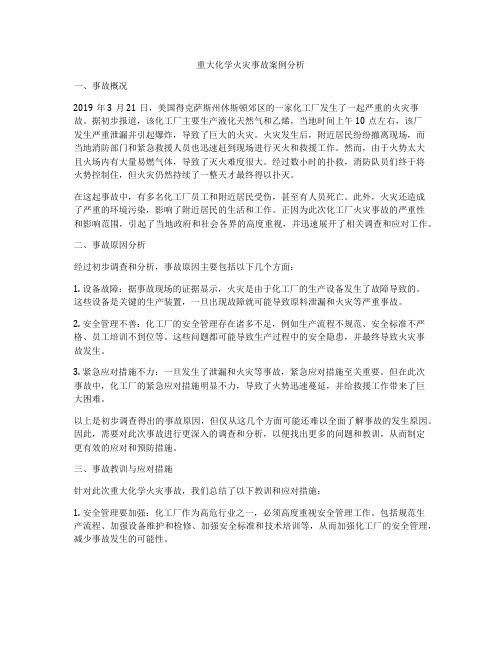
重大化学火灾事故案例分析一、事故概况2019年3月21日,美国得克萨斯州休斯顿郊区的一家化工厂发生了一起严重的火灾事故。
据初步报道,该化工厂主要生产液化天然气和乙烯,当地时间上午10点左右,该厂发生严重泄漏并引起爆炸,导致了巨大的火灾。
火灾发生后,附近居民纷纷撤离现场,而当地消防部门和紧急救援人员也迅速赶到现场进行灭火和救援工作。
然而,由于火势太大且火场内有大量易燃气体,导致了灭火难度很大。
经过数小时的扑救,消防队员们终于将火势控制住,但火灾仍然持续了一整天才最终得以扑灭。
在这起事故中,有多名化工厂员工和附近居民受伤,甚至有人员死亡。
此外,火灾还造成了严重的环境污染,影响了附近居民的生活和工作。
正因为此次化工厂火灾事故的严重性和影响范围,引起了当地政府和社会各界的高度重视,并迅速展开了相关调查和应对工作。
二、事故原因分析经过初步调查和分析,事故原因主要包括以下几个方面:1. 设备故障:据事故现场的证据显示,火灾是由于化工厂的生产设备发生了故障导致的。
这些设备是关键的生产装置,一旦出现故障就可能导致原料泄漏和火灾等严重事故。
2. 安全管理不善:化工厂的安全管理存在诸多不足,例如生产流程不规范、安全标准不严格、员工培训不到位等。
这些问题都可能导致生产过程中的安全隐患,并最终导致火灾事故发生。
3. 紧急应对措施不力:一旦发生了泄漏和火灾等事故,紧急应对措施至关重要。
但在此次事故中,化工厂的紧急应对措施明显不力,导致了火势迅速蔓延,并给救援工作带来了巨大困难。
以上是初步调查得出的事故原因,但仅从这几个方面可能还难以全面了解事故的发生原因。
因此,需要对此次事故进行更深入的调查和分析,以便找出更多的问题和教训,从而制定更有效的应对和预防措施。
三、事故教训与应对措施针对此次重大化学火灾事故,我们总结了以下教训和应对措施:1. 安全管理要加强:化工厂作为高危行业之一,必须高度重视安全管理工作。
包括规范生产流程、加强设备维护和检修、加强安全标准和技术培训等,从而加强化工厂的安全管理,减少事故发生的可能性。
BP德克萨斯州炼油厂火灾爆炸事故给我们的启示

BP 德克萨斯州炼油厂火灾爆炸事故给我们的启示唐彬 1 天津市居安企业管理咨询有限公司何琛 2 上海于睿商务咨询有限公司关键词 : 过程安全绩效指标(PSM KPI、过程安全管理、火灾、爆炸、美国化学品安全与危害调查委员会 (CSB摘要本文结合美国化学品安全与危害调查委员会对美国 BP 德克萨斯州炼油厂火灾爆炸事故的分析,从过程安全管理及过程安全绩效指标方面深刻分析产生爆炸事故的原因, 并提出改进措施。
1. 介绍目前很多企业都是执行 HSE 管理体系,把零伤亡作为企业安全管理的目标,所以我们管理的重点自然而然就变成对人身安全的管理, 但是对诸如操作工违反操作规程进行操作、报警的次数、联锁触发的次数、安全阀起跳的次数已经企业内出现的泄露事故关注的相对较少 , 但是这些看似微不足道的隐患往往最后导致了重大的过程安全事故的发生。
所以我们需要重视过程安全管理,重视过程安全管理的绩效。
本文通过美国化学品安全与危害调查委员会(CSB- Chemical Safety Board 对美国 BP 德克萨斯州炼油厂火灾爆炸事故的分析, 提出了企业应重视过程安全管理和过程安全管理绩效,并阐述过程安全管理绩效的划分和目的。
2. BP德克萨斯州炼油厂火灾爆炸事故经过2005年 3月 23日 13时 20分左右 , 英国石油公司 (BP位于美国德克萨斯州(Texas的炼油厂异构化装置发生了严重的火灾爆炸事故, 该事故为美国作业场所近 20年间最严重的灾难。
事故造成 15人死亡, 180余人受伤,爆炸产生的浓烟对周围工作和居住的人们造成不同程度的伤害, 直接经济损失超过 15亿美元。
德克萨斯州的炼油厂是 BP 公司最大和最复杂的炼油厂, 其每天生产汽油产量达 1000万加仑 (约占整个美国汽油销售总量的 2.5%。
此外 , 它还生产喷气式发动机燃料、柴油燃料和化学原料。
炼油厂有 29个炼油工艺装置和 4个化工装置 , 占地 1200英亩 , 拥有 1800名 BP 正式员工 ,事故发生时另外有大约 800名承包商员工在现场 , 正在进行检修作业。
BP德克萨斯炼油厂爆炸事故案例学习(学生预习版)
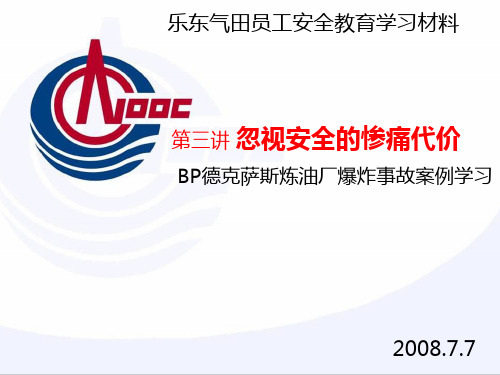
2.2 事故过程描述
2005 年3 月23 日凌晨2 时左右,异构化装置的操作人员将 液态烃原料导入分馏塔中。 凌晨3 时30 分,开始进料,当时液位计指示塔内液位在距离 塔底3.0 m 处。 9 时50 分左右,操作员开始将液态原料进行循环,并将更 多的液体打入液位已经过高的塔中,
第二章
事故经过
事故经过
个人记录区
4.从危险源辨识与风险分析来看
第二章
事故经过
个人记录区
5.你个人认为还需要改进的其他方面?
第三章
事故处理
事故发生后,BP 公司迅速做出反应,BP 首席执行官布 朗勋爵、BP 北美公司总裁罗斯- 费拉里等立即赶往德克萨斯 州,BP 网站也报道了关于事故的最新进展以及公司所采取 的应急措施。BP 公司成立了独立的事故调查小组对事故开 展调查,事故调查小组于2005 年5 月17 日公布了德州炼油 厂爆炸事故的初步调查报告。12 月又提出了最终报告,并通 过BP 公司全球网站向全世界发布。
第二章
事故经过
2.1 事故所处环境
炼油厂异构化装置
2.2 事故环境的工艺设施
1.异构化装置分馏塔 附属设施:来料流量控制阀,液位计,液位高高位报警系统,应急泄压阀BDV,溢流排放 管线,压力安全阀, 2.加热炉 3.换热器 4.放空罐,顶部有烟囱
第二章
2.3 事故背景
事故经过
操作工启动异构化装置
第五章
结束语
像这样一个有着良好安全业绩的世界级的大企业, 通过事故调查仍能发现在企业文化、领导层的个人行 为以及标准的准确度等诸多方面存在的问题。这也应 引起我们的思考,这起事故暴露的问题是不是我们的 企业也存在?
第二章
事故经过
BP炼油厂重大事故调查报告

事故经过与影响
事故经过
在炼油厂正常运营过程中,一个油罐突然发生爆炸,导致大 量原油泄漏。事故导致部分设备严重损坏,现场工作人员紧 急撤离。
影响
事故导致炼油厂部分区域被关闭,原油供应受到严重影响。 由于原油泄漏对环境和公共安全的影响,当地政府紧急启动 应急响应计划。
初步原因分析
原油泄漏的原因
初步分析表明,原油泄漏可能是由于油罐内部腐蚀导致。在油罐维护过程中,可 能存在一些不当操作导致内部腐蚀加剧。
现故障。
维护不到位
通过对设备进行检查和维护,发 现设备存在维护不到位的情况, 这也是导致事故发生的原因之一 。
管理问题
通过对公司管理流程的分析,发现 公司在设备维护和管理方面存在一 些问题,这也对事故的发生起到了 一定的影响。
验证过程与结果
模拟实验
通过对事故现场进行模拟实验,验证了操作不当和维护不到位是导致事故发生的主要原因。
环境的污染。
加强国际合作
炼油行业将加强国际合作,共 同应对全球能源和环境挑战。
感谢您的观看
THANKS
05
结论与展望
事故结论与设备维护不当,导致管道 破裂,大量原油泄漏。
影响范围
事故导致附近区域空气、 土壤和水质受到严重污染 ,部分动物栖息地受损。
人员伤亡
无人员伤亡,但附近居民 因环境污染受到不同程度 的影响。
安全措施改进建议
加强设备维护
定期对炼油厂设备进行检 查和维护,确保设备运行 正常。
BP炼油厂重大事故调查报 告
2023-11-06
contents
目录
• 引言 • 事故经过与初步分析 • 事故调查与验证 • 事故责任认定与教训 • 结论与展望
BP美国德州炼油厂火灾事故
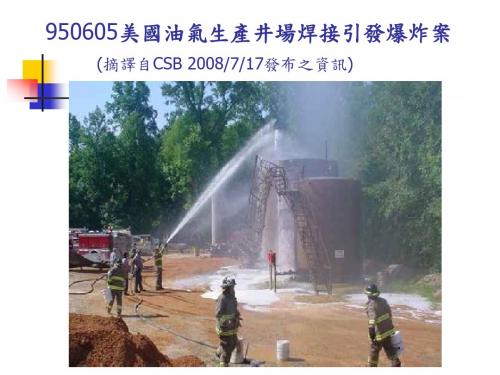
1.焊接前及作業中,未使用氣體偵測儀量測可燃性氣體濃 度。 2.動火作業前未將距離4英尺旁之鄰槽開口管線加帽蓋或 進行盲封隔離等。 3.四座儲槽內部連通,有些槽內仍有可燃性氣體及原油, 卻未先移除與清理,工作環境不安全。 4.將梯子橫置二儲槽作為焊接者的臨時工作平台,並由 維修人員站在槽頂協助穩定橫梯,不符高處作業之安全 程序。
事故原因分析
基本原因: 1.承商缺乏熱作之標準作業程序 承攬商未備製API規範之熱作SOP,以致
-在焊接前未先隔離含有可燃性蒸氣之#2與
#3槽。
-未移除#2號槽之原油。
-未將#3號槽之開口管線加帽蓋致油氣溢散。
-未偵測作業環境油氣濃度等。
事故原因分析
基本原因:
2.承商忽視高處作業之工作安全 未建造儲槽高處焊接之工作平台,僅以梯子橫放 #3及#4槽間以代替工作平台,致需有2名維修人 員在#3槽頂穩固梯子,而被爆炸波及死亡。
Partridge-Raleigh公司及其承攬商應 依API、NFPA提供之指引,並遵循OSHA 的規定執行熱作業,例如建立生產井場 熱作之SOP、工作手冊及製訂工作安全 計畫等,並落實執行。
Байду номын сангаас
3.Partridge-Raleigh及其承商均未建立工作許可 制度以管理動火作業
4.Partridge-Raleigh未建置井場員工之安全計 畫,亦未要求承商施工前應提出安全計畫並執行
改善措施
焊接區應與含可燃性液體(原油)、蒸氣之 儲槽及管線隔離,例如開口管線應設置管 帽或盲封或採取其他隔離措施。
950605美國油氣生產井場焊接引發爆炸案
(摘譯自CSB 2008/7/17發布之資訊)
事故摘要
2006年06月05日,位於美國密西西比州 Raleigh城的Partridge-Raleigh公司之生 產井場,有承攬商進行儲槽新設管線焊接 工作,欲將2個儲槽與第3個儲槽相接。當 天上午8時30分許,焊接火花引燃自鄰槽 未盲封管線溢散出的可燃性蒸氣(相對位 置參見圖示),導致兩個儲槽發生爆炸, 造成承攬商領班及維修人員3人死亡、焊 接工1人重傷的重大事故。
- 1、下载文档前请自行甄别文档内容的完整性,平台不提供额外的编辑、内容补充、找答案等附加服务。
- 2、"仅部分预览"的文档,不可在线预览部分如存在完整性等问题,可反馈申请退款(可完整预览的文档不适用该条件!)。
- 3、如文档侵犯您的权益,请联系客服反馈,我们会尽快为您处理(人工客服工作时间:9:00-18:30)。
BP德克萨斯炼油厂爆炸事故案例分析
2005年3月23日13时20分左右,英国石油公司(BP)位于美国德克萨斯州(Texas)的炼油厂异构化装置发生了严重的火灾爆炸事故,该事故为美国作业场所近20年间最严重的灾难。
事故造成15名员工丧生,180余人受伤,爆炸产生的浓烟对周围工作和居住的人们造成不同程度的伤害,直接经济损失超过15亿美元。
炼油过程中主要的操作装置为蒸馏塔,重新启动过程长达12小时,蒸馏塔的主要功能就是蒸馏生燃料,分离较重与较轻的成分,液态生燃料进入蒸馏塔的途中由加热炉加温,较轻的成分会蒸发,蒸汽升到塔顶,再由管子排送出去,蒸汽经过冷凝器液化接着便被抽走,提高汽油效能,此时抽取留在塔底的较重残余物,这些成分用来制造沥青等产品,如果蒸馏过程制造出太多蒸汽,操作员应排放多余气体降压,这些气体最终抵达安全出口即排放烟囱。
此为炼油厂主要的加工工艺过程。
从视频中可以看出,进料、开关阀门等操作过程均由电脑控制、人为操作,多数程序必须由手动操作完成,因此人是该厂最最重要的安全因素,任何的人为操作失误都有可能引起重大安全事故。
蒸馏塔进行了数年一次例行检修,蒸馏塔中油位高度由电脑读取控制,人为操控。
备用警报器经后期检查已经损坏,起不到警报作用,而后最重要的排液控制阀未开启,导致过量的夜料排不掉被迫进去排气管,最后充满35米高的烟囱爆出,导致爆炸的发生。
视频中多处显示出人为操作失误,夜班操作员无视蒸馏塔进料超过标准将警报关掉,并继续进料15分钟;日班领班在接到儿子摔伤的电话后离去,擅离职守,请同事代为控制监督;开入的白色小货卡未关闭引擎司机离去久未归,这些人为原因都直接或间接的导致了爆炸的发生。
综合人为因素、设备因素,导致了事故的发生。
在蒸馏塔三个多小时的进料过程中,因塔顶馏出物管线上的排液控制阀未开,而报警器和控制系统又发出了错误的指令,使操作者对塔内液位过高毫不知情。
液体原料装满蒸馏塔后,进入塔顶馏出管线。
塔顶的管线连通塔顶以下的安全阀,管线中充满液体后,迫使安全阀打开,将大量可燃液体泄放到烟囱里,液体很快充满,像喷泉一样洒落到地面上。
泄露出来的可燃液体蒸发后,形成蒸汽云。
而附近停着的未关闭引擎的白色小货卡,引擎的火花点燃了可燃蒸汽云,引发了这场前所未有的大爆炸。
在此后介入的CBS的调查中,发现有多处的员工操作不当和失误,本应发挥安全作用的一连串安全装置却都未发挥其自身的作用,由于故障、被关闭、被忽视,夜班操作员违反安全规定的操作却被视为是很平常的做法,还有油位指示器本身存在着致命的设计缺陷,指示器的最高测量油位只到3米,3米在操作员的控制表上便是百分之百的高度,指示器无法侦测3米以上的高度,因为指示器有这种设计缺陷,油位如果超过3米,指示器甚至显示高度往下掉,这就严重混淆了操作员对塔内油位高度的判断。
在油位3米时还安有一个备用警报器,而在CBS调查时却发现该警报器在爆炸发生前就已经故障却一直没有进行维修,两个警报器一个遭到操作人员的关闭,另一个故障,这就为爆炸的发生埋下了巨大的隐患。
排液控制阀会自动调节油料的高度,如果油位过高,阀门会自动打开,将多余油料排出蒸馏塔,然而在随后的调查中发现,操作人员根本不知道要检查该阀门的开关,而且从未操控启动过程,因此并为主要由蒸馏塔排液的流量。
操作
不当,设备未及时维修,领班在重要时刻擅离职守,CBS调查员已经很确定有瑕疵的启动过程就是爆炸的肇因,在随后在现场中找到的蒸馏塔内控制的电脑硬盘证实了一切。
造成本次爆炸还有五个间接的原因:首先,历经多年的工作环境已被侵蚀到排斥变化的地步,而且缺乏信任、动力和目标。
监督和管理行为不清晰。
对条例的执行不彻底。
员工个人感觉没有提建议和进行改进的权力。
第二,管理者没有建立或强制实行流程安全、操作执行程序、系统的降低风险优先权等。
没有从BP其他事故中吸取教训。
第三,复杂组织内的众多变化,包括组织结构和人员的调整,导致了责任不明和沟通不畅。
结果造成员工对角色、职责和优先顺序迷惑不清。
第四,要归咎于对危险辨识不足,对站点流程安全的理解知之甚少——这些导致了人们承受了更大的风险。
最后,低水平的操作管理和炼油厂内由上至下缺乏沟通,意味着对于问题没有及时的早期警报系统。
而且缺乏独立的渠道,无法通过组织彻底的核查来了解这个工厂的水准下滑。
要预防此类事故,应该组建了一个新的管理团队进入德克萨斯城炼油厂,精简机构,促进沟通,不应该把责任归咎到基层员工。
明晰岗位角色和职责,并采取措施验证了遵守操作规程。
创建了项目组,以协调并跟踪最终事故调查报告中的建议。
在公司层面建立新的安全运行机构,促进交流与协作,共享相关经验教训。
强化独立的检查程序,确定系统与程序都被安排在适当的位置,并有效地工作。
建立新的标准,以促进更严格、更有连续性地掌握BP集团的工作和完整性管理。
在未来的5年投入10亿美元,对德克萨斯城炼油厂进行升级维修。
此外,将在关键装置上安装先进的过程控制系统,取消在轻度维修中使用放空烟囱,同时加强员工培训,说实话,这方面是有所欠缺的。
推行了新的工程技术实务规范,以管理炼厂和其他加工厂内临时建筑物的使用。
相信德克萨斯炼油厂经过这次劫难后,一定会痛改前非,有更加美好的明天。
加工工艺流程图:。