全厂生产及工艺介绍分解
瓷砖生产工艺流程介绍怎么写的呢

瓷砖生产工艺流程介绍怎么写的呢
瓷砖是一种常见的建筑材料,被广泛应用于室内装饰中,其生产过程涉及多个工艺环节。
下面将从原料准备、研磨成型、干燥、装炉烧成和包装出厂等方面介绍瓷砖的生产工艺流程。
首先,瓷砖的生产需要准备各种原料,包括瓷土、石英砂、长石和粘土等。
这些原料需按一定比例混合,经过一系列处理后得到瓷砖的坯体。
接下来是研磨成型的过程。
在这个环节中,原料经过研磨、混合、加水制浆等工序,最终形成了瓷砖的坯体。
坯体经过模具成型后,需要进行干燥处理,以去除多余的水分。
随后是装炉烧成阶段。
坯体放入炉内进行烧结,经过高温处理,使瓷砖坯体结晶硬化,形成坚硬的瓷质。
烧成过程需要控制好温度和时间,确保瓷砖的质量。
最后是包装出厂环节。
烧成后的瓷砖需要经过检查和质量验收,合格的产品进入包装环节。
通常瓷砖会根据规格、颜色等分类包装,并在外包装上标明产品信息和商标。
总的来说,瓷砖生产工艺流程相对复杂,需要严格按照要求操作,保证产品质量。
只有经过每个环节的精心处理,才能生产出质量过硬的瓷砖产品。
希望通过以上介绍,您对瓷砖的生产工艺流程有了更进一步的了解。
1。
本钢冷轧厂生产流程和产品介绍

敬请关注的地方
Diagram
冷轧板
冷轧产品涵盖CQ、DQ、DDQ、 EDDQ、SEDDQ和低合金高强 等各个级别,采用全氢罩式退火工艺实现再结晶光亮退 火,退火炉温均匀,退火后产品机械性能优良、均匀, 可以灵活安排生产,满足小批量特殊品种需求
TIPS:本钢冷轧家电板产品 具有机能优势;2010年底四 期炉台投产后,能够稳定生 产SEDDQ和低合金高强钢;为 确保产品的性能优势,2011 年不提高机组产能,通过增 加保温时间、优化再结晶退 火曲线,进一步发挥罩退 DC01\DC03\DC04产品的机能 优势 规格:0.5-2.5*700-1525mm
产品类型 DC01~05、Q195、Q215、Q235、SPCC、SPCD、 SPCE、ST37、NH295、BGD、05CuPCrNi等系列产品。
工艺流程 钢卷准备→装炉,扣内罩→密封测试→预吹扫→扣 加热罩,点火→H2吹扫,加热,保温→冷却→后吹扫→出炉→ 二次冷却。
Company Logo
Company Logo
罩式炉退火机组简介
罩式炉退火机组主要是通过罩式退火炉对冷轧后的钢卷进行 再结晶光亮退火,以保证最终冷轧产品的质量要求,是冷轧板 卷生产的一个重要环节。罩式退火炉机组的设计生产能力 882267吨,主要退火普通板、深冲板、低合金高强度钢板,及 少量的镀锌特深冲板。按生产设计能力,需罩式退火炉45座, 一期工程引进德国 L01公司 HUGF220-520HPH 罩式退火炉 24座, 二期工程引进该公司罩式退火炉 12 座,三期工程引进奥地利 EBNER公司HICON/H2罩式退火炉9座,其中主体设备共包括炉台 45个,加热罩24个,冷却罩21个,内罩45个,分流冷却系统36 套,最终冷却台33个。附属设备包括一套钢卷运输链,二台平 板运输车。退火过程由计算机自动控制。
炼厂物料平衡及生产工艺简介讲解
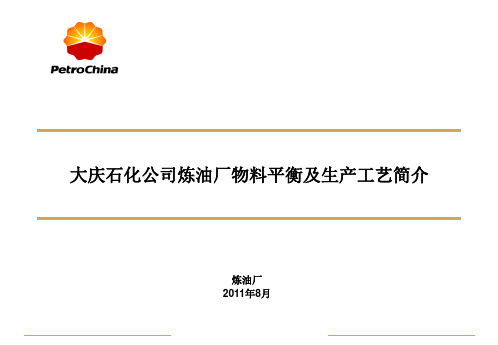
2020/9/25 (11)
炼油物料平衡
项目 一、原油原料量
1 原油加工量 2 外购原料
乙烯氢气 炼油自产氢气 做燃料用天然气 乙烯MTBE 乙烯甲苯 乙烯二甲苯 化三粗甲苯 化三乙苯 外购乙苯 外购MTBE 外售污油 外购二甲苯 外购甲苯
全厂物料平衡表
2010年(吨) 6766646 6583166 183480 3553 8270 18156 37705 28401 8732 1635 22041 8572 2025 -21147 23052 42485
2020/9/25 (8)
炼油物料平衡
炼油企业物料分析
✓ 综合商品量 报告期内生产的可供销售的石油制品资源总和。 报告期内生产的除燃料油(气)之外的所有石油制品产量。 炼油装置产出的化工产品的商品量。如丙烯、硫磺、苯等。
✓ 石油综合自用量 供所有炼油装置作燃料的燃料油、燃料气和做溶剂用的产品。 催化裂化装置的烧焦量。 企业自备电站、锅炉用的燃料油、燃料气。
比例(%) 100.00 97.29
2.71
2020/9/25 (12)
炼油物料平衡
项目 二、综合商品量
1 液化气 2 干气商品量 3 丙烯 4苯 5 化工轻油
其中:轻烃 石脑油 尾油
6 汽油 其中:90# 93# 97#
7 航煤
全厂物料平衡表
2010年(吨) 6358716 300410 11428 140542 8697 786137 115149 428833 242155 1508765 67011 1107142 334611 279317
2020/9/25 (4)
炼油物料平衡
指炼油生产由原料(原料油及外购原料油)投入,各装置 加工、精制、调合到产品交库的整个过程中,原料投入到产品 产出之间的平衡关系。 分阶段物料平衡:根据炼油产品生产顺序进行的,包括炼油装 置物料平衡、炼油产成品、半成品物料平衡 。 总平衡:炼油企业内部总的物料平衡,即炼油企业物料分析。
车间生产工艺流程
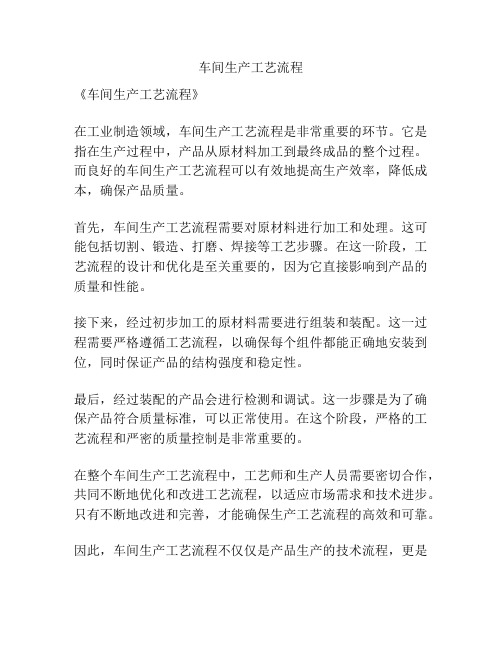
车间生产工艺流程
《车间生产工艺流程》
在工业制造领域,车间生产工艺流程是非常重要的环节。
它是指在生产过程中,产品从原材料加工到最终成品的整个过程。
而良好的车间生产工艺流程可以有效地提高生产效率,降低成本,确保产品质量。
首先,车间生产工艺流程需要对原材料进行加工和处理。
这可能包括切割、锻造、打磨、焊接等工艺步骤。
在这一阶段,工艺流程的设计和优化是至关重要的,因为它直接影响到产品的质量和性能。
接下来,经过初步加工的原材料需要进行组装和装配。
这一过程需要严格遵循工艺流程,以确保每个组件都能正确地安装到位,同时保证产品的结构强度和稳定性。
最后,经过装配的产品会进行检测和调试。
这一步骤是为了确保产品符合质量标准,可以正常使用。
在这个阶段,严格的工艺流程和严密的质量控制是非常重要的。
在整个车间生产工艺流程中,工艺师和生产人员需要密切合作,共同不断地优化和改进工艺流程,以适应市场需求和技术进步。
只有不断地改进和完善,才能确保生产工艺流程的高效和可靠。
因此,车间生产工艺流程不仅仅是产品生产的技术流程,更是
一种管理方法和质量保证体系。
只有严格遵守工艺流程,才能保证产品质量,提高生产效率,增强企业竞争力。
史上最全化妆品生产工艺介绍!

史上最全化妆品生产工艺介绍!史上最全化妆品生产工艺介绍---1. 引言随着化妆品行业的不断发展,人们对化妆品的需求也越来越高。
化妆品的生产工艺是保证产品质量和安全性的重要环节。
本文将介绍史上最全化妆品生产工艺,从原料选取到成品包装,详细解析整个生产过程。
---2. 原料选择化妆品的原料选择是化妆品生产的第一步。
原料的质量直接影响最终产品的品质。
通常,原料主要包括基础油、活性成分、防腐剂、稳定剂等。
在选择原料时,需要考虑原料的来源、纯度、稳定性以及对皮肤的影响等因素。
---3. 配方调配根据产品的类型和功能,化妆品厂商需要合理配制化妆品的配方。
在配方调配过程中,需要考虑原料的配比、物相稳定性、防腐剂的使用量等。
此外,根据市场需求和消费者的反馈,还可以调整配方,提升产品的效果和用户体验。
---4. 生产工艺化妆品的生产工艺包括混合溶解、精细混合、热熔、乳化和灭菌等步骤。
4.1 混合溶解将特定比例的原料按照一定的顺序加入搅拌槽中,进行混合溶解。
通过搅拌和加热的方式,使得原料充分溶解,并得到均匀的混合物。
4.2 精细混合将混合溶解后的物料进行进一步的精细混合。
通过高剪切搅拌设备,将混合物分散均匀,确保各种原料充分融合。
4.3 热熔对于一些固体原料,需要通过热熔的方式使其溶解。
通过加热设备,将固体原料加热至液态,再与其他原料进行混合。
4.4 乳化乳化是化妆品生产工艺的关键步骤之一。
在乳化过程中,需要加入乳化剂,并通过高速搅拌将油性物质和水性物质充分乳化,使化妆品形成乳状或凝胶状。
4.5 灭菌为了确保化妆品的安全性和防腐效果,还需要进行灭菌过程。
常用的灭菌方法有高温灭菌和辐射灭菌。
---5. 包装与质检化妆品生产完成后,需要进行包装与质检。
包装通常包括瓶子、管状、喷雾器等。
包装应符合卫生、安全和环保要求。
同时,对成品进行质检,检测产品的外观、气味、质地等指标,确保产品符合标准。
---6. 结论本文详细介绍了史上最全化妆品生产工艺。
家具厂工艺流程

家具厂工艺流程
《家具厂工艺流程》
家具制造是一个非常复杂的工艺过程,需要经过多道工序才能完成一件精美的家具。
在家具厂,工艺流程通常包括设计、原材料选购、加工制作、质量检验和包装等环节。
首先是设计环节,设计师根据市场需求和客户要求,设计出符合潮流和实用的家具款式。
设计好的图纸将作为制作的依据。
接下来是原材料选购。
在家具制作中,木材、板材、五金配件、油漆等原材料都是必不可少的。
家具厂通常会选择质量良好、环保的原材料,以保证家具的质量和安全。
加工制作是家具制造的重要环节。
木工师傅根据设计图纸,进行原木的切割、打磨、组装等工序。
五金师傅负责五金配件的安装,油漆师傅进行家具表面的喷涂和打磨。
每一个环节都需要工人们精湛的技艺和细心的操作,以确保家具的质量和外观。
质量检验是家具制造中不可或缺的一环。
经过制作完成的家具需要进行严格的质量检验,包括结构稳固性、外观完美度、使用安全性等方面。
只有通过检验的家具才能被包装出厂。
最后是包装环节。
家具在出厂前需要进行包装,以保护家具免受损坏。
一般家具的包装包括泡沫塑料、纸箱、防震膜等方式,确保家具在运输过程中不受损坏。
综上所述,家具制造的工艺流程非常繁琐,需要各个环节精准配合和高标准操作。
只有这样才能制作出优质的家具产品。
史上最全PBAT生产工艺介绍

史上最全PBAT生产工艺介绍PBAT是一种生物降解性塑料,在目前的环境保护和可持续发展的背景下,受到了广泛的关注和研究。
本文将对PBAT的生产工艺进行详细介绍,以帮助读者更好地了解和应用这种材料。
首先,PBAT的生产工艺可以分为原料准备、控制发酵、高分子聚合、加工成型等几个主要步骤。
原料准备阶段,主要包括对生物基原料的选择和预处理工作。
PBAT的主要成分是聚丁二酸丁二醇酯和一些添加剂,如增塑剂、稳定剂等。
在选择原料时,要保证其质量稳定和生物降解性能。
控制发酵阶段,需要在恰当的温度和湿度条件下,加入合适的微生物发酵剂,通过微生物的代谢进行聚合反应。
这个阶段是PBAT的重要步骤,发酵过程需要进行严格的控制,以保证聚合反应的效率和产品质量。
高分子聚合阶段是整个工艺的核心步骤,主要是将发酵得到的聚合物进行进一步反应,提高分子量和聚合度。
这个过程中,需要选择合适的反应条件和催化剂,以促进聚合反应的进行。
同时,控制反应时间和温度,以确保聚合反应的彻底和高效。
加工成型阶段是将高分子聚合物加工成所需的产品形式。
PBAT可以通过挤出、注塑、吹塑等方式进行成型。
在这个阶段,需要根据具体需求选择合适的成型设备和工艺参数,以获得所期望的产品性能。
除了上述的主要工艺步骤,PBAT的生产还需要进行质量检测和后处理。
质量检测主要包括对原料和成品进行物理性能、降解性能等方面的测试,以确保产品的质量符合要求。
后处理工作主要是对成品进行包装、储存和运输等操作,以确保产品的保存和交付。
需要注意的是,PBAT的生产工艺是一个复杂的过程,需要丰富的经验和专业知识。
同时,随着环保意识的加强和技术的不断进步,PBAT的生产工艺也在不断完善和优化,以提高产品质量和生产效率。
综上所述,PBAT的生产工艺包括原料准备、控制发酵、高分子聚合、加工成型等几个主要步骤。
通过合理的工艺参数和设备选择,可以获得高质量的PBAT产品,为环境保护和可持续发展做出贡献。
企业生产工艺流程说明
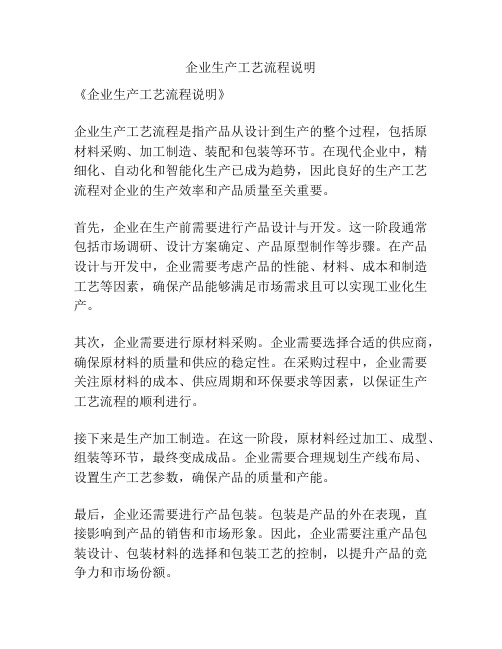
企业生产工艺流程说明
《企业生产工艺流程说明》
企业生产工艺流程是指产品从设计到生产的整个过程,包括原材料采购、加工制造、装配和包装等环节。
在现代企业中,精细化、自动化和智能化生产已成为趋势,因此良好的生产工艺流程对企业的生产效率和产品质量至关重要。
首先,企业在生产前需要进行产品设计与开发。
这一阶段通常包括市场调研、设计方案确定、产品原型制作等步骤。
在产品设计与开发中,企业需要考虑产品的性能、材料、成本和制造工艺等因素,确保产品能够满足市场需求且可以实现工业化生产。
其次,企业需要进行原材料采购。
企业需要选择合适的供应商,确保原材料的质量和供应的稳定性。
在采购过程中,企业需要关注原材料的成本、供应周期和环保要求等因素,以保证生产工艺流程的顺利进行。
接下来是生产加工制造。
在这一阶段,原材料经过加工、成型、组装等环节,最终变成成品。
企业需要合理规划生产线布局、设置生产工艺参数,确保产品的质量和产能。
最后,企业还需要进行产品包装。
包装是产品的外在表现,直接影响到产品的销售和市场形象。
因此,企业需要注重产品包装设计、包装材料的选择和包装工艺的控制,以提升产品的竞争力和市场份额。
总之,企业生产工艺流程涉及到产品设计与开发、原材料采购、加工制造和产品包装等环节。
良好的生产工艺流程能够提高企业的生产效率和产品质量,从而增强企业的竞争力。
随着科技的不断进步,企业需要不断优化和改进生产工艺流程,以适应市场的需求和企业的发展。
比较全的PCB生产工艺流程介绍

比较全的PCB生产工艺流程介绍PCB(Printed Circuit Board)是现代电子产品中不可或缺的一部分,它起到了组织电子元件、连接电路的作用。
下面是一个较全的PCB生产工艺流程介绍。
1.原料准备:PCB生产的原材料主要包括基板材料、导电层材料、覆盖层材料以及焊接材料等。
各种材料需要经过质量检验和筛选。
2.设计:PCB的设计一般是通过电脑辅助设计(CAD)软件进行的。
在设计过程中,需要考虑电路布局、元件安装位置、线路走向等因素。
3.版图制作:根据PCB设计图,进行版图制作。
版图制作包括各种工艺参数的设置,如层间距、线宽、线间距等。
4.印制制作:通过光刻工艺,将设计的电路图形透过掩膜映射到基板上,涂覆光敏化剂,并暴光照射,形成导电图形。
5.蚀刻:将覆盖着光敏化剂的基板浸入蚀刻液中,通过化学反应去除未曝光的光敏化剂,暴露出需要保留的导电层。
6.电镀:在蚀刻后的导电层上进行金属电镀,一般使用铜。
铜层的厚度和均匀性对PCB的性能有重要影响。
7.钻孔:根据PCB设计要求,在特定位置进行钻孔。
钻孔通常使用电脑控制的机械钻床进行。
8.电镀:进行表面处理,保护导电层不被氧化。
常用的表面处理方法包括阻焊、镀金、喷锡等。
9.特殊工艺:一些PCB可能需要特殊的工艺,如层压、压线、贴膜等。
这些工艺的目的是提高PCB的性能和可靠性。
10.组件装配:将PCB上的元件进行焊接,通常使用锡膏和热风或烙铁进行。
11.测试:对PCB进行测试,确保其正常工作。
常见的测试方法有连通性测试、功能性测试等。
12.包装和发货:将已经测试过的PCB进行包装,并按照订单要求进行发货。
总结:以上是一个较全的PCB生产工艺流程介绍。
PCB生产工艺复杂,需要多个环节的配合和准确的操作。
每个环节都非常重要,影响着PCB的质量和可靠性。
随着技术的不断进步,PCB生产工艺也在不断改进,以满足不断变化的市场需求。
棋盘井洗煤厂工艺简介(改造后)

棋盘井选煤厂生产系统及工艺介绍生产系统介绍棋盘井选煤厂是一座设计年入选原煤4.0Mt/a的矿区型焦煤选煤厂。
全厂生产系统可分为:原煤入仓系统、原煤分选系统及成品煤运输系统三部分。
分选系统采用无压给料三产品重介旋流器主选+煤泥重介+直接浮选的联合工艺流程。
成品煤运输系统可实现汽车短倒运输和铁路系统运输。
生产工艺的介绍:矿井来煤和外调原煤分别经运输皮带和配煤刮板,分配至四个原煤仓。
入仓原煤经仓下24台给煤机将原煤按要求比例给入准备车间。
原煤在准备车间经分级、捡矸、除杂、破碎后输至主厂房。
进入厂房的原煤由刮板机平均分配给两台无压给料三产品重介旋流器进行重介分选,选后的精煤、中煤、矸石分别经弧形筛、脱介筛脱介脱水后,矸石脱介筛筛上物运至矸石仓;精煤、中煤脱介筛筛上物分别进入精煤、中煤卧式离心机进一步脱水,最终卸入各自的产品皮带。
重介分选工艺中,六台精煤脱介筛合格介质段增设喷水,合介段筛下物经分流部分物料进入煤泥重介分选系统,分选后的溢流进入精煤稀介桶,底流进入中矸稀介桶。
介质回收系统中,精煤稀介和中矸稀介单独回收。
精煤稀介经六台精煤磁选机回收介质,磁旋尾矿通过六台击打弧形筛实现截粗后,筛上粗粒精煤经煤泥离心脱水机脱水后进入精煤皮带;筛下物给入一段浮选入料桶,再经泵给入一段浮选机;一段浮选尾煤进入二段浮选缓冲桶,再经泵打入二段浮选机进行分选。
二段浮精和一段浮选精煤混合,经三台精煤加压过滤机脱水后,卸入精煤产品皮带。
二段浮选的尾煤连同中矸稀介磁选尾矿进入一段斜管浓缩池。
一段斜管浓缩浓底流经卧式沉降离心脱水机脱水后卸入中煤皮带,溢流进入二段耙式浓缩沉降池。
二段浓缩底流由快开式板框压滤机脱水后,形成最终成品——煤泥,二段浓缩溢流连同加压过滤机滤液、板框压滤滤液汇至浓缩池。
由三台多级离心空压机提供的压缩空气,经风包连接至精煤加压过滤机和快开式压滤机。
循环水池的水经循环水泵打入精煤、中煤、矸石脱介筛,用作筛上喷水及各处生产补水、清扫卫生使用。
化肥厂生产过程及工艺流程

化肥厂生产过程及工艺流程This model paper was revised by the Standardization Office on December 10, 2020化肥厂生产过程及工艺流程煤制合成氨、尿素 C+ O 2 → CO C+ O 2 → CO 2 CO + H 2O →CO 2+ H 2H 2+N 2→NH 3CO 2 + 2NH 3 → CO (NH 2)2 1 全厂流程简介2 过程工艺描述(1)水煤浆气化制合成气装置由水煤浆制备工序来的水煤浆送入煤浆槽储存待用。
浓度约为63%的水煤浆通过煤浆给料泵加压输送到气化炉顶部工艺烧嘴,并与空分装置来的纯氧分别进入气化炉在(G),约1400℃工艺条件下,水煤浆与纯氧进行部分氧化反应,生成粗合成气。
反应后的粗合成气和溶渣进入气化炉下部的激冷室。
在激冷室中,粗合成气经冷却、洗涤,将粗合成气中的大部分碳黑洗去,并和粗渣分开。
出激冷室的粗合成气直接进入文丘里洗涤器和碳洗塔进一步洗涤,除去粗合成气中残留的碳黑,然后将水蒸汽/干气比约~的合成气送至变换工序。
溶渣被激冷室底部通过破渣机进入锁斗,定期排入渣池,渣池设有捞渣机将粗渣捞出,装车运往园区免烧砖项目。
渣池中含细渣的灰水通过渣池泵送至真空闪蒸器。
碳洗塔的液位通过控制进入塔内的灰水量来维持,碳洗塔内的黑水分两股排出,一股黑水去高压闪蒸器;另一股由灰水循环泵送至气化炉也进入高压闪蒸器,黑水经减压,闪蒸出黑水中溶解的气体并通过变换冷凝液加热器回收闪蒸汽的热量,通过高压闪蒸分离器,闪蒸出的气体至变换或火炬,水送入脱氧水槽。
(2)净化装置a. 变换变换工序主要反应式为:COS+H2O——CO2+H2S+QCO+H2O——CO2+H2+Q由气化送来粗煤气经煤气水分离器分离掉少量的冷凝液及灰尘后,经中温换热器温度升高至250℃,进第一中温变换炉。
第一中温变换炉分上、下两段,炉内装有两段三层耐硫变换触媒,层间配有煤气激冷管线调温,出第一中温变换炉变换气CO含量为24%(干),温度为420℃左右。
装配式建筑PC构件厂简介及生产工艺流程全解

思考:预压应力怎样施加?
2.1.2 机组流水法
机组流水法也称为流水线工艺,特点是操作人员位置相对固定,而加工对象按顺 序和一定的时间节拍在各个工位上行走的生产工艺。
2.2 车间工艺布置
示范工厂总平面图
搅拌站进料
搅拌站
苯板连接件仓库
示范工厂介绍
原材料/构件运输出口
自动化流水线
主要生产各种叠合板(叠合 楼板、叠合双皮墙、叠合带 保温层双皮墙)、外墙板 (三明治外挂墙板、三明治 剪力墙板)、内墙(内隔墙、 剪力墙)等板类构件
异型构件生产线
传统预制构件多采用该形式。 手工作业,可按照流水生产组 织形式。主要生产梁、柱、屋 顶板材、阳台、楼梯、看台、 飘窗等异形构件
混凝土挤压机
3、 预应力工艺
滑动式混凝土压模机,可以生产6-60mm的预应力混凝土预制板、基桩、排水沟 以及带有隔热功能的预制楼板。
模机行进在导轨上,沿台座纵向行进,边 滑行边灌筑边振动加压,形成一条混凝土板 带,然后按构件要求的长度切割成材。这种 工艺具有投资少,设备简单,生产效率高等优 点。
混凝土压模机
为什么要使用预应力混凝土?
• 混凝土的抗拉极限应变值只有0.0001~0.00015㎜,要保证混凝土不开 裂,钢筋的应力只能达到20~30N/mm2;即使允许出现裂缝的构件, 当裂缝宽度限制在0.2~0.3㎜时,钢筋应力也只能达到150~ 250N/mm2,使高强钢筋的强度无法充分利用。
预应力混凝土的基本原理?
2、手控生产线
热电车间工艺简介

1、各车间生产关系
企业所属车间有哪些?各车间上下游关系用文字简单描述;用关系图明确的标示;
2、全厂生产工艺介绍
用文字概括介绍整体生产工艺是什么样的?然后用工艺流程图表示出来,并在图中标出三废;(要求:1、工艺图能反应出整个生产的主体流程是怎样的即可,不必和各车间简介中的工艺图一样详细;2、如果企业各车间是分别独立的,为避免与下内容重复全厂生产工艺介绍可不写;)公司共有4个生产车间,分别是:电解车间、氯乙烯车间、热电车间、装备车间,
下表为公司各生产车间成立时间及主要原料和来源及产品情况:
表2-3 公司所属车间情况说明表
企业生产车间包括电解车间、氯乙烯车间、热电车间和装备车间:
热电车间生产关系如下图所示:
水
图2-4 热电车间生产关系图
2、热电车间生产工艺介绍
干煤棚中的燃料煤在通过带式输送机送入主厂房煤仓,由给煤皮带送入炉内燃烧,燃烧释放的热量经热传递和辐射将炉内水管里的水(锅炉补充水经化水处理装置处理后由除氧器除氧后送入)加热至过饱和蒸汽状态,化学能转化为热能,产生的蒸汽通过汽轮机做功带动发电机组发电,电能由输变线路送往各用电单位,蒸汽做功后排入凝汽器经热交换后冷凝为水,经冷凝水处理装置处理后再送入锅炉循环利用,与此同时,送入汽轮机的蒸汽经过分汽缸送至各用热单位,蒸汽进入凝汽器,经冷却水变成凝结水,凝结水经处理装置处理后回用。
炉内燃烧产生的烟气经脱硝装置(氨水)脱硫塔(石灰浆)脱硫及布袋除尘器、静电除尘器除尘后由引风机引入烟囱高空排放。
除尘器分离下来的灰尘与炉渣运至砖厂制砖。
山东实华化工有限公司热电车间工艺流程图见图2-5。
图2-5 热电车间工艺流程图
3
5。
炼油厂的构成和工艺流程

炼油厂的构成和工艺流程炼油厂主要由两大部分组成,即:炼油过程和辅助设备。
从原油生产出各种石油产品一般需经过多个物理的及化学的炼油过程。
通常,每个炼油过程相对独立的组成一个炼油生产装置。
第一节炼油厂构成一、炼油生产装置按生产目的分为以下几类:原油分离装置 (龙头装置、加工能力)原油加工的第一步是把原油分离为多个馏分油和残渣油,因此,每个炼油厂都有原油常压蒸馏装置或原油常减压蒸馏装置。
在此装置中,还设有原油脱盐脱水设施。
重油轻质化装置为了提高轻质油收率,需将部分或全部减压馏分油和渣油转化为轻质油,这一任务主要由裂化反应过程来完成,如催化裂化、加氢裂化、焦化等。
油品改质及油品精制装置此类装置的作用是提高油品的质量已达到质量指标要求,如催化重整、加氢精制、电化学精致、溶剂精致、氧化沥青等。
加氢处理、减粘裂化等也归入此类。
油品调合装置为了达到产品质量要求,通常需要进行馏分油直接的调合,并且加入各种提高油品性能的添加剂。
油品调合方案的优化对提高现代炼厂的效益也能起到重要作用。
气体加工装置如气体分离、气体脱硫、烷基化、C5/C6异构化、合成甲基叔丁基醚(MTBE)等。
制氢装置在现代炼厂,由于加氢过程的耗氢量大,催化重整装置的副产氢气不敷使用,有必要建立专门的制氢装置。
化工产品生产装置如芳烃分离、含H2S气体制硫、某些聚合物单体的合成等。
产品分析中心为了保证产品的出厂质量。
由于生产方案不同,炼厂中所包含的炼油过程的种类和多少,或者说复杂程度都有所不同。
一般来说,规模大的炼厂其复杂程度会高些,但也有一些大规模的炼厂的复杂程度并不高。
二、辅助设施辅助设施是维持炼厂正常运转生产所必需的,主要的辅助设施有:供电系统供水系统供水蒸气系统原油和产品储运系统三废处理系统第二节炼油装置工艺流程一个炼厂或一个炼油装置的构成和生产程序是用工艺流程图来描述的。
炼油生产是自动化程度较高的连续生产过程,正确设计的工艺流程不仅对保障日常生产,而且对提高效益具有重要的作用。
硝酸生产工艺技术简介
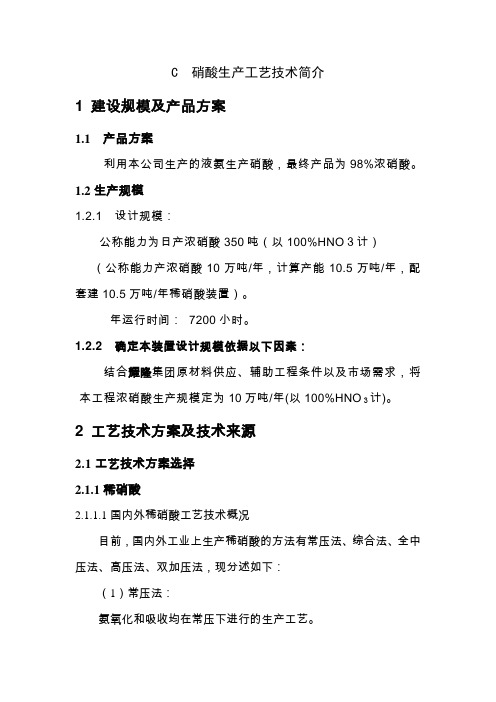
C 硝酸生产工艺技术简介1 建设规模及产品方案1.1 产品方案利用本公司生产的液氨生产硝酸,最终产品为98%浓硝酸。
1.2生产规模1.2.1 设计规模:公称能力为日产浓硝酸350吨(以100%HNO3计)(公称能力产浓硝酸10万吨/年,计算产能10.5万吨/年,配套建10.5万吨/年稀硝酸装置)。
年运行时间:7200小时。
1.2.2 确定本装置设计规模依据以下因素:结合耀隆集团原材料供应、辅助工程条件以及市场需求,将本工程浓硝酸生产规模定为10万吨/年(以100%HNO3计)。
2 工艺技术方案及技术来源2.1工艺技术方案选择2.1.1稀硝酸2.1.1.1国内外稀硝酸工艺技术概况目前,国内外工业上生产稀硝酸的方法有常压法、综合法、全中压法、高压法、双加压法,现分述如下:(1)常压法:氨氧化和吸收均在常压下进行的生产工艺。
早期硝酸生产多采用这种方法,该工艺流程的特点为系统压力低,设备结构简单,工艺操作稳定,氨氧化率高,铂耗较低。
但吸收比容积大(20~25m3),酸吸收率较低(仅为92%左右)。
为减少对大气的污染并提高氨利用率,需附有碱吸收NOX尾气装置并副产硝盐,即便如此尾气中NOX浓度仍很高,不符合目前日益严格的环境要求。
加上设备相对台数较多,设备体积大,装置占地面积多,投资大,成品酸浓度低等因素,国家经贸委已明文规定禁止采用此种流程新建硝酸装置。
(2)综合法常压氨氧化和中压(0.25~0.5MPa)酸吸收的稀硝酸生产工艺。
这种方法在一定程度上弥补了常压酸吸收的缺点,我国在本世纪50年代末引进该流程进行稀硝酸的工业生产。
该方法主要缺点是常压氨氧化、设备庞大、占地多,需要配备较昂贵的不锈钢材质的氧化氮压缩机,其投资高于下面介绍的中压法,且吸收压力低仅0.35MPa(A),因此酸浓度低及尾气排放不能达到环保要求,不适用于规模较大的硝酸装置,国家经贸委也明文规定了不能采用此种流程建设硝酸装置。
(3) 全中压法氨氧化和酸吸收均在中压下进行的稀硝酸生产工艺。
原料车间及主要生产工艺
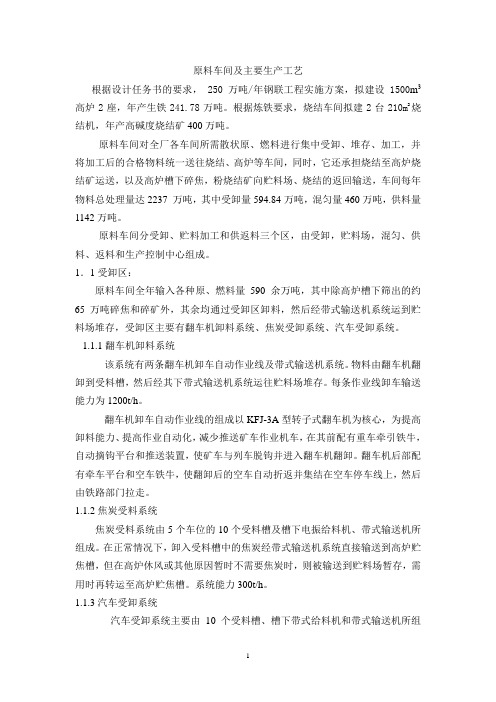
原料车间及主要生产工艺根据设计任务书的要求, 250万吨/年钢联工程实施方案,拟建设1500m3高炉2座,年产生铁241.78万吨。
根据炼铁要求,烧结车间拟建2台210m2烧结机,年产高碱度烧结矿400万吨。
原料车间对全厂各车间所需散状原、燃料进行集中受卸、堆存、加工,并将加工后的合格物料统一送往烧结、高炉等车间,同时,它还承担烧结至高炉烧结矿运送,以及高炉槽下碎焦,粉烧结矿向贮料场、烧结的返回输送,车间每年物料总处理量达2237 万吨,其中受卸量594.84万吨,混匀量460万吨,供料量1142万吨。
原料车间分受卸、贮料加工和供返料三个区,由受卸,贮料场,混匀、供料、返料和生产控制中心组成。
1.1受卸区:原料车间全年输入各种原、燃料量590余万吨,其中除高炉槽下筛出的约65万吨碎焦和碎矿外,其余均通过受卸区卸料,然后经带式输送机系统运到贮料场堆存,受卸区主要有翻车机卸料系统、焦炭受卸系统、汽车受卸系统。
1.1.1翻车机卸料系统该系统有两条翻车机卸车自动作业线及带式输送机系统。
物料由翻车机翻卸到受料槽,然后经其下带式输送机系统运往贮料场堆存。
每条作业线卸车输送能力为1200t/h。
翻车机卸车自动作业线的组成以KFJ-3A型转子式翻车机为核心,为提高卸料能力、提高作业自动化,减少推送矿车作业机车,在其前配有重车牵引铁牛,自动摘钩平台和推送装置,使矿车与列车脱钩并进入翻车机翻卸。
翻车机后部配有牵车平台和空车铁牛,使翻卸后的空车自动折返并集结在空车停车线上,然后由铁路部门拉走。
1.1.2焦炭受料系统焦炭受料系统由5个车位的10个受料槽及槽下电振给料机、带式输送机所组成。
在正常情况下,卸入受料槽中的焦炭经带式输送机系统直接输送到高炉贮焦槽,但在高炉休风或其他原因暂时不需要焦炭时,则被输送到贮料场暂存,需用时再转运至高炉贮焦槽。
系统能力300t/h。
1.1.3汽车受卸系统汽车受卸系统主要由10个受料槽、槽下带式给料机和带式输送机所组成。
车间生产工艺流程图
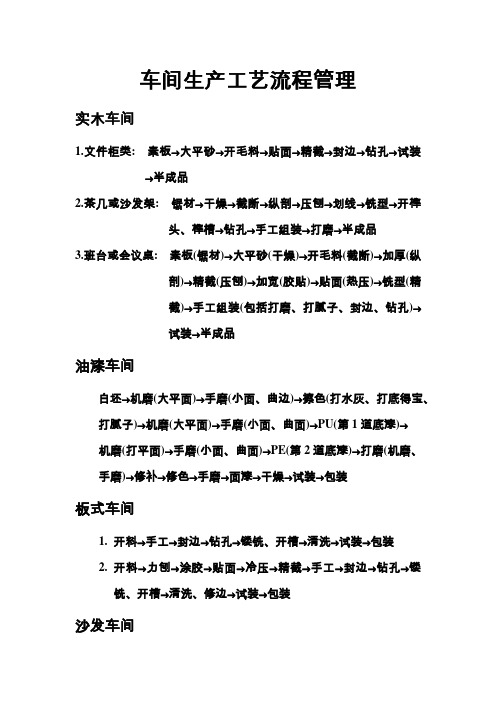
车间生产工艺流程管理实木车间1.文件柜类: 素板→大平砂→开毛料→贴面→精截→封边→钻孔→试装→半成品2.茶几或沙发架: 锯材→干燥→截断→纵剖→压刨→划线→铣型→开榫头、榫槽→钻孔→手工组装→打磨→半成品3.班台或会议桌: 素板(锯材)→大平砂(干燥)→开毛料(截断)→加厚(纵剖)→精截(压刨)→加宽(胶贴)→贴面(热压)→铣型(精截)→手工组装(包括打磨、打腻子、封边、钻孔)→试装→半成品油漆车间白坯→机磨(大平面)→手磨(小面、曲边)→擦色(打水灰、打底得宝、打腻子)→机磨(大平面)→手磨(小面、曲面)→PU(第1道底漆)→机磨(打平面)→手磨(小面、曲面)→PE(第2道底漆)→打磨(机磨、手磨)→修补→修色→手磨→面漆→干燥→试装→包装板式车间1.开料→手工→封边→钻孔→镂铣、开槽→清洗→试装→包装2.开料→力刨→涂胶→贴面→冷压→精截→手工→封边→钻孔→镂铣、开槽→清洗、修边→试装→包装沙发车间裁皮、开棉→打底(电车)→粘棉→扪皮(组装)→检验→包装转椅车间裁布(皮)、开棉→车位、粘绵→扪皮→组装→检验→包装屏风车间开料(铝材)→喷胶→贴绵→扪布(打钉)→组装→试装→包装五金车间1.椅架类: 开料→弯管→钻孔、攻牙→焊接→打磨→抛光→喷涂2.钢板类: 开料→冲板(圆孔、圆凸、方孔、方凸、小梅花、大梅花、网孔、菱凸)→折弯→焊接→打磨→喷涂3.台架类: 开料→冲弯→钻孔、攻牙→焊接→打磨→抛光→喷涂4.电镀类: 开料→开皮→冲弯→焊接→打磨→精抛→电镀总:开料(裁剪、剪板)→制造(冲床、弯管、钻孔、攻牙)→成型(焊接、打磨、抛光)→喷涂、电镀喷涂车间清洗→凉干→打磨→喷漆(喷粉)→电烤→包装。
- 1、下载文档前请自行甄别文档内容的完整性,平台不提供额外的编辑、内容补充、找答案等附加服务。
- 2、"仅部分预览"的文档,不可在线预览部分如存在完整性等问题,可反馈申请退款(可完整预览的文档不适用该条件!)。
- 3、如文档侵犯您的权益,请联系客服反馈,我们会尽快为您处理(人工客服工作时间:9:00-18:30)。
★
附属产品
固体硫磺
液氧 液氩 液氮
军品、民用四氧化二氮(N2O4)
国家卫星发射的推进剂 (航天标准 99.5%,我厂能达99.8%)
二、全厂的工艺介绍
1、合成氨厂 包括48000m³ /h空分装置和30万吨/年合成 氨装置。空分主要负责外供合成氨装置生 产所需的氧气、氮气、仪表空气,及生产液 氧、液氮、液氩。合成氨装置包括气化、 净化、合成三个工序。
3. 化肥厂:
化肥一车间(新尿素、10万吨/年食用二氧化碳、
3万吨二氧化碳)、化肥二车间(老尿素、 671#氨库)。
4. 硝盐化工厂: 硝酸一车间、 硝酸二车间(400st/d、450st/d双加压装置 + 三套间硝装置) 硝酸三车间(902t/d双加压装置+ 20万吨/年新硝铵+15万吨/年老硝铵置)。
合成氨厂生产流程
氮气 氧气 空分 气化炉(两开一备) 水煤浆 制浆 原料煤 煤场 皮带 671#氨库 煤仓
H2+N2
H2
粗煤气
CO、 H2
变换Leabharlann CO2低温甲醇洗CO2
H2
合成 液氨
液氮洗
1万立方氨罐
2、 合成氨二厂
主要包括 28000m³ /h空分装置+18万吨/年合成氨装置。 是淮化“1830”工程的生产的主体部分, 2000年投产,
急救:
迅速将患者移离中毒现场至通风处,松开衣领,注 意保暖,密切观察意识状态。
4、 硝酸
外观 :无色清澈液体 毒性及健康危害: 硝酸液及硝酸蒸气对皮肤和粘膜有强刺激和腐蚀作用。据 国外3例吸入硝酸烟雾的报道,吸入后短时间内无法呼吸道 症状,4~6小时后出现进行性呼吸困难。入院后均有发绀 及口、鼻流出泡沫液体。给机械通气及100%氧气吸入,在 24小时内死亡。 吸入硝酸烟雾可引起腐蚀性口腔炎和胃肠 炎,可出现休克或肾功能衰竭等。皮肤或眼睛接触硝酸可 引起灼伤。皮肤接触硝酸的部位呈褐黄色。一旦发生由硝 酸引发的事故,应立即使受伤害者脱离事故现场到空气新 鲜处。眼睛或皮肤被污染时应立即用大量清水冲洗15分钟 以上,口服后立即用清水漱口。
902T/D
60%稀酸
多孔 硝铵
● 硝酸生产粗流程
液氨气化 成气氨 氧化炉 氧化氮 浓硝酸 酸库
外销
吸收塔
稀硝酸
提浓装置
● 双加压工艺机组生产稀酸的优点
稀硝酸生产分为:常压法、综合法、中压法、 高压法、双加压法 5种工艺。其中双加压法是 国内外比较先进的硝酸生产工艺,与其它几种 工艺相比,具有: 1. 氨氧化率高达 2. 吨酸铂耗较低 3. 产酸浓度高 4. 尾气排放的NOX含量低,更环保。 (四合一机组,蒸汽透平、尾气透平、空压机、 NOX压缩机)
紧急处理:一氧化碳中毒后的紧急处理五步骤: 1.将门窗打开,勿碰触室内家电,以防爆炸。 2.将患者移到通风地,并松开衣服,保持仰卧姿势。 3.将患者头部后仰,使气道畅通。 4.患者如有呼吸,要以毛毯保温,迅速就医。 5.患者如无呼吸,要一面施行人工呼吸,一面呼叫救护车。
2、氨: 外观:具有非常刺鼻的气味的无色气体 氨中毒主要抑制中枢神经系统,正常情况下,中枢神 经系统能够抑制外周的低级中枢,当中枢神经系统受 抑制,使得其对外周低级中枢的抑制作用减弱甚至消 失,从而外周低级中枢兴奋,出现一系列如肌随意性 兴奋、角弓反射及抽搐等本能反应。 (1)、吸入的危害表现: 轻度吸入氨中毒表现有鼻炎、咽炎、喉痛、发音嘶哑。 氨进入气管、支气管会引起咳嗽、咯痰、痰内有血。 严重时可咯血及肺水肿,呼吸困难、咯白色或血性泡 沫痰,双肺布满大、中水泡音。患者有咽灼痛、咳嗽、 咳痰或咯血、胸闷和胸骨后疼痛等。 急性氨中毒主要表现为呼吸道粘膜刺激和灼伤。
既能生产多孔硝铵,也能生产普通硝铵
若生产多孔硝酸铵则加入 ①添加剂,以使颗粒形成多孔; ②包裹剂,以提高颗粒强度和均匀度,形成疏 水层、降低产品含水量,改变结晶习性等 。
硝改装置
27万吨稀硝装置(902T/D双加压稀硝) + 20万吨多孔硝铵
902T/D生产的稀酸
多孔硝铵 间硝(替代450t/d和400t/d 生产的酸)
全厂生产及工艺介绍
•
主讲 : 鲍玉贵
一、 淮化集团生产简介
淮化股份公司下辖六大生产分厂:包括合成氨厂、合成氨二厂、 化肥厂、硝盐化工厂、精细化工厂和热电厂,以及其它辅助车 间备煤、产成品库、电仪分厂等。
1. 合成氨厂 : 分空分、气化、净化、合成四个作业区 2. 合成氨二厂 :分空分、气化、净化、合成四个作业区。
5. 热电厂: 供水车间 热电车间(3台130t/h、2台75t/h锅炉; 3台3000kwh、2台6000kwh、 2台12000kwh汽轮发电机; 两个水处理班) 热电联供车间(2台240t/h锅炉、 1台 60000kwh汽轮发电机、 1个水处理班)
6. 精细化工厂:甲胺车间(新老甲胺各2万吨/年、新老 DMF各2万吨/年、小制气)+ 双氧水(4万吨/年)车 间。
硝酸+尿素+硝铵: 消耗液氨1500吨/天 富余120吨/天
3、化肥厂
主要装置生产能力为尿素50万吨/年,液体二氧化碳 13万吨/年。 尿素装置共有两套: 一套为15万吨/年老系统装置,采用水溶液全循 环法工艺,经2010年改造为700吨/天,但受 压缩机打气量限制,现产量只能达到430吨/天。 一套为30万吨/年的新系统装置,氨气提法,引进意大 利斯那姆技术,国际先进,国内领先。(液尿:一些电 厂用于烟气脱硫) 。
我厂水源 :
泵
加压后
厂区2#线
厂区生产用水
淮河水→供水车间的过滤池
泵
供水车间的加药间
厂区1#线
厂区生活用水
生活区 用水
三、新建项目
企业转型的标志项目 1. 乙二醇 2. 己内酰胺 3. 琥珀酸酐
四、其余相关
• 1.运输系统:铁路、水路、公路 • 2.实验装置:FMTP 乙二醇
五、有毒化学品
1、一氧化碳
7. 电仪分厂有两个车间:电气和仪表车间。
8. 备煤车间: 主要负责锅炉动力煤和气化 原料煤的存储与输送。 9. 产成品包装车间: 负责各种产品包装与发运。
二、 主要产品及其生产能力
★★ 主要产品 1、合成氨: 二厂18万吨/年,氨厂30万吨/年 2、浓硝酸: 50万吨/年 3、尿素: 50万吨/年 4、DMF(二甲基甲酰胺): 5万吨/年 5、混甲胺: 4万吨/年 6、双氧水: 4万吨/年 7、食用二氧化碳: 3万吨/年+10万吨/年 8、硝酸铵: (15+27)万吨/年
四氧化二氮: 此产品是直硝法工艺生产浓硝酸的一中间产 物,分为农用品和军品,产量是根据客户需要 来定的。
5、精细化工厂
甲胺:共有两套装置,4万吨/年混甲胺。原料是液 氨和甲醇。 DMF:共两套装置,5万吨/年。原料是一氧化碳、 二甲胺。 双氧水:4万吨/年。原料是氢气、空气。 两个氨厂的粗煤气(脱除H2S和CO2后) DMF的变 压吸附(分离出H2和CO),其中氢气供双氧水作为 原料气,一氧化碳供DMF合成作为原料气。
6、热电厂 主要负责供应全厂的生产用水,生产用汽,生产 用电。 现有供水装置一套,水处理装置三套(280吨/小时 软水处理,450吨/小时一级除盐水处理,400吨/小 时二级除盐水处理),总供蒸汽能力为780吨/小时 根据生产工艺需要,配备了12000KW抽凝汽轮发电机 两台,60000KW抽凝汽轮发电机一台(联供),背压式 汽轮发电机5台,总装机容量105000KW。
4、硝盐化工厂 主要产品浓硝酸,硝酸铵,四氧化二氮。 浓硝酸:年产量50万吨,共有四套浓硝酸装置. 一套为综合法稀硝机组,采用一次合成直硝 法,20万吨/年,分为稀硝和浓硝两个部分; 三套为双加压工艺机组,450ST/D、400ST/D、 315ST/D(315ST/D已拆至吉林康奈尔),每套都 配有稀酸提浓装置,叫做间硝,共年产浓酸30万 吨, 同时,部分稀硝酸用于生产硝酸铵。(1短 吨=0.907吨) 间硝 450st/d 60%稀酸 硝酸镁溶液提浓 成品浓硝酸 装置 400st/d
• 2009年投产,年产30万吨合成氨,是经国家发改委、国家环
保总局批准建设的淮河流域重点环境污染综合治理项目,是 安徽省861行动计划和安徽省“十一五”重点建设项目。
• 装置汇集了国内外先进成熟的工艺技术——大型空分、多元
料浆加压气化、耐硫变换、低温甲醇洗液氮洗净化、离心式 压缩、低压氨合成等,替代原技术落后、设备老化、成本高、 污染严重的炼焦炉、间歇造气、栲胶脱硫、热钾碱洗铜氨液 洗脱碳、高压合成的老合成氨系统,实现清洁生产。现负荷 已达到设计能力,极大地改善淮南市的大气质量和淮河水质, 企业的效益和竞争力显著增强。
外观与性状:无色、无嗅、无味的气体。 ‘ 危险特性:是一种易燃易爆气体。与空气混合能形成 爆炸性混合物,遇明火、高热能引起燃烧 爆炸;与空气混物爆炸限12%~75%。
中毒:亦称煤气中毒。 一氧化碳进入人体之后会和血液中的血红蛋白结合,由于 CO与血红蛋白结合能力远强于氧气与血红蛋白的结合能 力,进而使能与氧气结合的血红蛋白数量急剧减少,从而 引起机体组织出现缺氧,导致人体窒息死亡。
引进 法国液空公司双泵内压缩空分流程(空分)、 美国德士古水煤浆加压气化技术(气化)、
丹麦托普索氨合成回路技术(合成)等生产工艺,
DCS 控制,技术水平国际先进,国内领先。
合成氨二厂生产流程:
氮气
氧气
空分 气化炉(两开一备)
水煤浆
CO+ H2 O→ CO2 + H2 粗煤气
CO、 H2 CO2
变换
● 硝酸铵 1. 老硝酸铵:(常压中和法) 稀硝酸+气氨
包装
液体 硝铵
硝铵溶液(两段蒸发提浓后)
造粒塔 (纯度≥99.5的固体硝铵)