埋弧焊问题及解决
焊接中出现的问题和解决方案
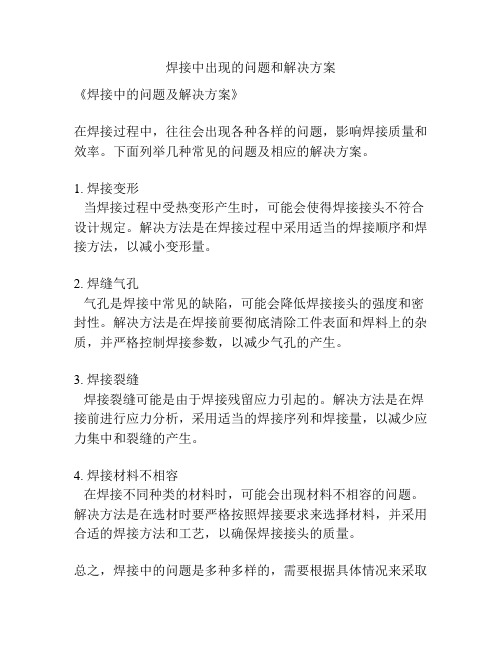
焊接中出现的问题和解决方案
《焊接中的问题及解决方案》
在焊接过程中,往往会出现各种各样的问题,影响焊接质量和效率。
下面列举几种常见的问题及相应的解决方案。
1. 焊接变形
当焊接过程中受热变形产生时,可能会使得焊接接头不符合设计规定。
解决方法是在焊接过程中采用适当的焊接顺序和焊接方法,以减小变形量。
2. 焊缝气孔
气孔是焊接中常见的缺陷,可能会降低焊接接头的强度和密封性。
解决方法是在焊接前要彻底清除工件表面和焊料上的杂质,并严格控制焊接参数,以减少气孔的产生。
3. 焊接裂缝
焊接裂缝可能是由于焊接残留应力引起的。
解决方法是在焊接前进行应力分析,采用适当的焊接序列和焊接量,以减少应力集中和裂缝的产生。
4. 焊接材料不相容
在焊接不同种类的材料时,可能会出现材料不相容的问题。
解决方法是在选材时要严格按照焊接要求来选择材料,并采用合适的焊接方法和工艺,以确保焊接接头的质量。
总之,焊接中的问题是多种多样的,需要根据具体情况来采取
相应的解决方法。
只有不断积累经验、改进技术,才能够提高焊接质量和效率。
焊接过程中容易出现的问题及产生原因

焊接过程中易出现的问题及原因分析;焊接缺陷所谓焊接缺陷,就是使焊接接头金属性能变坏。
手工电弧焊在压力容器的焊接过程中,容易出现的缺陷有有尺寸偏差、咬边、气孔、未焊透、夹渣、裂纹、焊瘤等。
在知道其产生原因后,我们找出了相应的方法,尽量减少这些缺陷所带来的危害。
尺寸偏差焊缝宽度、余高、焊脚尺寸等焊缝尺寸过大或过小。
产生原因:焊条直径及焊接规范选择不当;坡口设计不当;运条手势不良。
危害:尺寸过小,强度降低;尺寸过大,应力集中,疲劳强度降低防止措施:正确选用焊接规范,良好运条。
咬边由于焊接参数选择不当,或操作方法不正确,沿焊趾的母材部位产生的沟槽或凹陷。
产生咬边的原因:操作方法不当,焊接规范选择不正确,如焊接电流太大、电弧过长、运条方式与角度不当、坡口两侧停留时间太长或太短均有产生咬边的可能。
咬边的危害:咬边将减少母材的有效截面积、在咬边处可能引起应力集中、特别是低合金高强钢的焊接,咬边的边缘组织被淬硬,易引起裂纹。
防止措施:正确选用焊接规范,不要使用过大的焊接电流,要采用短弧焊,坡口两边运条稍慢、焊缝中间稍快,焊条角度要正确。
气孔气孔产生原因:焊件表面氧化物、锈蚀、污染未清理;焊条吸潮;焊接电流过小,电弧过长,焊速太快;药皮保护效果不佳,操作手势不良。
危害:减小焊缝有效截面,降低接头致密性,减小接头承载能力与疲劳强度。
防止措施1、清除焊丝,工作坡口及其附近表面的油污、铁锈、水分与杂物。
2、采用碱性焊条、焊剂,并彻底烘干。
3、采用直流反接并用短电弧施焊。
4、焊前预热,减缓冷却速度。
5、用偏强的规范施焊。
未焊透产生原因:坡口、间隙设计不良;焊条角度不正确,操作手势不良;热输入不足,电流过小,焊速太快;坡口焊渣、氧化物未清除。
危害:形成尖锐的缺口,造成应力集中,严重影响接头的强度、疲劳强度等。
防止未焊透的措施:加大焊接电流,加焊盖面焊缝。
夹渣产生原因:焊件表面氧化物,层间熔渣没有清除干净;焊接电流过小,焊速太快;坡口设计不当;焊道熔敷顺序不当;操作手势不良。
埋弧焊机常见的故障和排除方法

焊接电流小
1.二次电缆导线接触不良
2.导电嘴间隙太大,导电不良
3.送丝电动机转速提不高
1.清理接触面并拧紧
2.更换导电嘴
3.检修电动机及供电系统
气体保护不良
1.气瓶内气体不足甚至没气
2.气路堵塞或接头漏气
3.预热气断电造成减压器冻结
4.电磁气阀或电磁电源故障
5.喷嘴内被飞溅堵塞
6.工作场地空气对流大
7.气体流量不足
1.更换新瓶
2.检修气路,紧固接头
3.检修预热器,接通电路
4.检修
5.清理喷嘴
6.设挡风板
7.加大流量
未按送丝按钮红灯亮,导电嘴碰到焊件短路
交流接触器触点常闭
更换或修理接触器
5.更换导电嘴,清理焊丝上的脏物
启动小车不动活在焊接过程小车突然停止
1.离合器未接上
2.行车速度旋钮在最小位置
3.空载焊接开关在空载位置
1.合上离合器
2.将行车速度调到需要位置
3.拨到焊接位置
焊丝没有与焊件接触,焊接回路即带电
焊接小车与焊件之间绝缘不良或损坏
1.检查小车车轮绝缘
2.检查焊车下面是否有金属与焊件短路
埋弧焊机常见的故障和排除方法
故障特征
产生原因
排除方法
按焊丝向下或向上按钮时,送丝电机不逆转
1.送丝电机有故障
2.电动机电源线接点断开或损坏
1.修理送丝电动机
2.检查电源线路接点并修复
按启动按钮后,不见电弧产生,焊丝将机头顶起
焊丝与焊件没有导电接触
清理接触部分
按启动按钮,线路工作正常,但引不起弧
1.焊接电源未接通
2.电源接触器接触不良
初学者在埋弧自动焊操作实验中遇到的问题及解决办法

初学者在埋弧自动焊操作实验中遇到的问题及解决办法马磊锋;王玉安;蒋应田;史旭龙;房中华【摘要】由于埋弧自动焊的焊接质量好、效率高以及操作环境好等特点在工业生产中得到广泛使用.因此该项技术在焊接专业教学中占据重要地位,相应地埋孤焊操作技术成为本科焊接专业实验教学中的一项必修内容.在本科生的埋弧自动焊接实验教学操作训练中,由于学生学习时间短和缺乏操作经验原因,时常会出现引弧不成功现象.在介绍埋弧焊机的工作原理和设备组成基础上,针对本科学生在埋弧焊操作过程中常出现的一些技术问题为讨论对象,从学生对存在问题的认识与理解以及解决问题所获得心得出发,阐述了引弧粘丝、顶丝等导致引孤不成功现象进行了技术问题,提出了问题的解决办法.对于广大同学快速掌握埋孤自动焊操作技术将起到积极作用.%The automatic welding in an arc of welding of good quality and highly efficient production and operating environment for the industry is widely used.so the technology and professional teaching of the important position in an arc in welding operation technique in the teaching profession to be welded in a required item.at the undergraduate student in an arc automatic welding operation in the teaching, because the students study and lack of experience, and the arc is not successful.This article introduced in welding machine of arc in the works and facilities of the basis for the students are welding operation in an arc in the presence of some technical problems to discuss the object from students to know and understand the problem and solve the problem which platform, illustrated, arc down to the top of arc led to such success is not a technical problemand made an answer to the problem.this will be for the students to grasp quickly in an arc automatic welding equipment will exert positive effects.【期刊名称】《电焊机》【年(卷),期】2013(043)001【总页数】4页(P69-72)【关键词】埋弧自动焊;操作技术;短路回抽引弧【作者】马磊锋;王玉安;蒋应田;史旭龙;房中华【作者单位】辽宁石油化工大学材料学院,辽宁抚顺113001;辽宁石油化工大学材料学院,辽宁抚顺113001;辽宁石油化工大学材料学院,辽宁抚顺113001;辽宁石油化工大学材料学院,辽宁抚顺113001;辽宁石油化工大学材料学院,辽宁抚顺113001【正文语种】中文【中图分类】TG4450 前言埋弧自动焊是一种高效的自动焊接方法,因其焊接电流大、焊缝质量好、焊接效率高、焊工操作环境好[1],且对焊接操作者的具体操作技术要求不高而在现代大中型焊接生产制造企业得到了广泛的应用。
埋弧焊常见缺陷及处理方法.pdf

埋弧焊常见缺陷
埋弧焊常见缺陷及处理方法
宽度不均匀
产生原因:
1.焊接速度不均匀;2.焊丝给送速度不均匀;3.焊丝导电不良
防止方法:
1.找出原因排除故障;2.找出原因排除故障;3. 更换导电嘴衬套(导电块)
堆积高度过大
产生原因:
1.电流太大而电压过低;2.上坡焊时倾角过大;3.环缝焊接位置不当(相对于焊件的直径和 焊接速度)
产生原因:1.焊件、焊丝、焊等材料配合不当;2.焊丝中含碳、硫量较高;3.焊接区冷却速度过快而 致热影响区硬化;4.多层焊的第一道焊缝截面过小;5.焊缝成形系数太小;6.角焊缝熔深太 大;7.焊接顺序不合理;8.焊件刚度大 防止方法:
1.合理选配焊接材料;2.选用合格焊丝;3.适当降低焊速、焊前预热和焊后缓冷;4.焊前 适当预热或减小电流,降低焊速(双面焊适用);5.调整焊接参数和改进坡口;6.调整焊接参 数和改变极性(直流)7.合理安排焊接顺序;8.焊前预热及焊后缓冷 焊穿
产生原因:
焊接参数及其它工艺因素配合不当
防止方法:
选择适当焊接参数 咬边 产生原因: 1.焊丝位置或角度不正确;2.焊接参数不当 防止方法: 1.调整焊丝;2.调节焊接参数 未熔合 产生原因: 1.焊丝未对准;2.焊缝局部弯曲过甚 防止方法: 1.调整焊丝;2.精心操作 未焊透 产生原因: 1.焊接参数不当(如电流过小,电弧电压过高);2.坡口不合适;3.
中间凸起而两边凹陷
产生原因:
焊剂圈过低并有粘渣,焊接时熔渣被粘渣托压
防止方法:
提高焊剂圈,使焊剂覆盖高度达 30~40mm 气孔
产生原因:
1.接头未清理干净;2.焊剂潮湿;3.焊剂中混有垃圾;4.焊剂覆盖层厚度不当或焊剂斗阻 塞;5.焊丝表面清理不够;6.电压过高 防止方法:
埋弧焊常见缺陷的产生原因及防除方法

埋弧焊常见缺陷的产生原因及防除方法缺陷名称产生原因防除方法缺陷形状焊缝宽度不均匀1、焊接速度不均匀;2、送丝速度不均匀;3、焊丝导电不良;4、轮辐厚薄度不均匀,设备制造误差。
防止:1、找出原因排除故障。
2、更换导电块。
消除:酌情部分用手工焊修。
补并磨光。
余高过大1、焊接电流过大而电弧电压过低;2、上坡焊时倾角过大;3、环缝焊接位置不当。
防止:1、调整焊接工艺参数。
2、高速上坡倾角。
3、调节适当的焊接位置。
消除:去除表面多余部分并打磨。
咬边1、焊丝位置或角度不正确;2、焊接工艺参数不当。
防止:1、调整焊丝。
2、调整焊接工艺参数。
消除:去除夹渣补焊。
未熔合1、焊丝未对准焊缝;2、焊缝局部弯曲过甚。
防止:1、调整焊线。
2、精心操作。
消除:去除缺陷部分后补焊。
未焊透1、焊接工艺参数不当;2、坡口不合适;3、焊丝未对准。
防止:1、调整焊丝。
2、修正坡口。
3、调整焊接工艺参数。
操作:去除缺陷部分后补焊。
夹渣1、多层焊时,层间清渣不干净;2、多层分道焊时,焊丝位置不当。
防止:1、层间清渣彻底。
2、每层焊后发现咬边夹渣。
必须清除修复后再焊。
消除:去降缺陷补焊。
焊接常见缺陷的产生原因及防除方法焊缝表面成形不良气孔1、接头未清理干净;2、焊剂潮湿;3、焊剂中混有垃圾;4、电弧电压过高;5、焊接时焊剂覆盖不充分。
防止:1、接头必须清理干净。
2、焊剂按规定烘干,一般250度烘干。
烧穿焊接工艺参数及其它因素配合不当。
防止:选择适当工艺参数。
焊缝中间出现沟槽1、电流、电压不匹配,焊丝伸出长度不够;2、电流、电压过大,焊接间隙太大3、焊接位置不当,形成下坡焊。
1、调整电流电压。
2、调节焊接位置。
收弧弧坑过深1、收弧电流、电压太大;2、焊接长度不够;3、起弧时的焊渣未清干净、跳弧。
1、调节收弧电压2、增加焊接长度3、清干净,接头中的焊渣焊缝成型粗糙1、电压太小,电流偏大;2、焊接速度太快。
1、调配好电流电压。
2、放慢焊接速度。
埋弧焊机常见的故障和排除方法

8.熔丝烧断
1.修复或更换
2.修复或更换
3.换新
4.检修控制线路,更换开关
5.调紧送丝轮压紧力
6.更换导电嘴
7.将焊丝退出剪掉一段
8.更换熔丝
送丝不均匀
1.送丝滚轮压紧力不足
2.送丝滚轮磨损
3.焊丝弯曲
4.导电嘴内孔过小
5.焊丝盘上的焊丝缠绕不好
2.调整电流、电压至合适值
线路工作正常,焊接工艺参数正确,但焊丝送给不均,电弧不稳
1.焊丝给送压紧轮磨损或压得太松
2.焊丝被卡住
3.焊丝给送机构有故障
4.网路电压波动太大
5.导电嘴导电不良,焊丝脏
1.调整压紧轮或更换焊丝给送滚轮
2.清理焊丝,使其顺畅送进
3.检查并修复送丝机构
4.使用专用焊机线路,保持网路电压稳定
2.电源接触器接触不良
3.焊丝与焊件接触不良
4.焊接回路无电压
1.接通焊接电源
2.检查并修复接触器
3.清理焊丝与焊件的接触点
启动后,焊丝一直向上
1.机头上电弧电压反馈引线未接断开
2.焊接电源未启动
1.接好引线
2.启动焊接电源
启动后焊丝粘住焊件
1.焊丝与焊件接触太紧
2.焊接电压太低或焊接电流太小
1.保证接触可靠,但不要太紧
5.找出脱焊并焊好
焊接电流小
1.二次电缆导线接触不良
2.导电嘴间隙太大,导电不良
3.送丝电动机转速提不高
1.清理接触面并拧紧
2.更换导电嘴
3.检修电动机及供电系统
气体保护不良
1.气瓶内气体不足甚至没气
2.气路堵塞或接头漏气
3.预热气断电造成减压器冻结
埋弧焊管焊接主要缺陷及防控措施
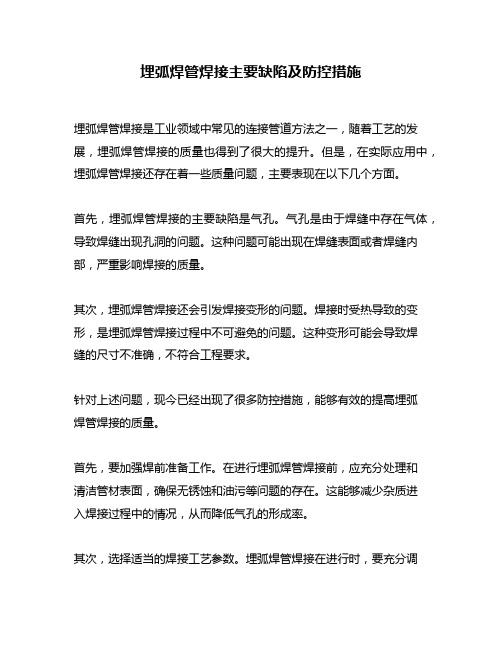
埋弧焊管焊接主要缺陷及防控措施
埋弧焊管焊接是工业领域中常见的连接管道方法之一,随着工艺的发展,埋弧焊管焊接的质量也得到了很大的提升。
但是,在实际应用中,埋弧焊管焊接还存在着一些质量问题,主要表现在以下几个方面。
首先,埋弧焊管焊接的主要缺陷是气孔。
气孔是由于焊缝中存在气体,导致焊缝出现孔洞的问题。
这种问题可能出现在焊缝表面或者焊缝内部,严重影响焊接的质量。
其次,埋弧焊管焊接还会引发焊接变形的问题。
焊接时受热导致的变形,是埋弧焊管焊接过程中不可避免的问题。
这种变形可能会导致焊
缝的尺寸不准确,不符合工程要求。
针对上述问题,现今已经出现了很多防控措施,能够有效的提高埋弧
焊管焊接的质量。
首先,要加强焊前准备工作。
在进行埋弧焊管焊接前,应充分处理和
清洁管材表面,确保无锈蚀和油污等问题的存在。
这能够减少杂质进
入焊接过程中的情况,从而降低气孔的形成率。
其次,选择适当的焊接工艺参数。
埋弧焊管焊接在进行时,要充分调
整好电流、电压等参数。
焊接过程中必须掌握好焊接时间,光弧稳定性等参数,确保在焊接过程中不会产生气孔等问题。
最后,要注意焊后处理工作。
焊母材在焊接过程中,受到了热应力的影响,需要对焊缝进行冷却,并给予一定的后续处理。
这能够避免出现松动、开裂等问题的发生,确保焊缝的质量和稳定性。
总之,焊接技术的推广和应用不仅需要具备良好的技术技能和操作能力,更需要以科学的思维和技术手段为支撑,不断进行改进和完善。
通过有效的防控措施,我们可以提高埋弧焊管焊接的质量,切实为工业发展提供有力保障。
高压管道埋弧自动焊的问题分析及处理措施
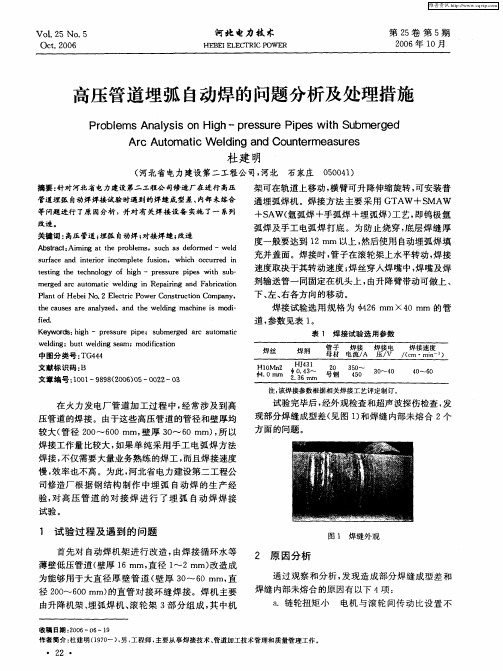
维普资讯
Vo - 5 NO 5 I2 .
Oc . 0 6 t2 0
河北 电力 技 术
H EBEIEL ECTRI P C OW ER
第 2 5卷 第 5期 20 0 6年 1 O月
高 压管道埋 弧 自动焊的问题分析及处理措施
P o lmsAn lsso g p e s r p s wi b r be ay i n Hih 。 r s u e Pie t Su me g d h re
t s i g t e t c n l g f h g ‘p e s r i e t u — e t h e h oo y o ih n r s u e p p s wih s b ・ me g r u o t l i g i p iig a d F b i t n r e a c a t ma i wed n n Re arn d c n a rc i ao Pln f He e . e ti o rC n t u t n C mp n , a t bi o No 2 Elcrc P we o s r c i o o a y
慢, 效率也不高 。为此 , 河北省电力建设第二工程公 司修造厂根据钢结构制作 中埋 弧 自动焊 的生产经 验 , 高 压 管 道 的对 接 焊 进 行 了埋 弧 自动 焊 焊 接 对
试验 。
1 试 验 过 程 及 遇 到 的 问题
首 先对 自动 焊机 架进 行 改造 , 由焊 接 循环 水 等 薄壁 低压 管道 ( 壁厚 1 6mm, 径 1- 直 -2mm) - - 改造 成 为能 够用 于大 直 径 厚 壁 管 道 ( 厚 3 ~ 6 壁 O 0mm, 直
较大 ( 径 2 0 6 0mm, 管 0  ̄ 0 壁厚 3 - 6 0 . 0 mm) 所 以  ̄ ,
埋弧焊机使用维护及常见故障教案.

教案【课题名称】:埋弧焊机使用维护常见故障【目标要求】:了解埋弧焊机的使用维护常识,掌握埋弧焊机常见故障的排除。
【主要内容】:焊机的使用维护及常见故障的排除为保证焊接过程顺利进行,提高生产效率和焊接质量,延长焊机寿命,应正确使用焊机并对焊机进行经常性的保养维护,使其处于良好的工作状态。
埋弧焊机安装时,要仔细研读使用说明书,严格按照说明书中的要求进行安装接线。
图为MZ-1000型埋弧焊机使用交流电源时的外部接线图。
要注意外接电网电压应与设备要求的电压一致。
外接电缆要有足够的容量和良好的绝缘。
连接部分的螺母要拧紧,尤其是地线连接的可靠性重要,否则可能危及人身安全。
通电前,应认真检查接线的正确性;通电后,应仔细观察设备的运行情况,如有无发热、声音异常等,并应注意运动部件的转向和测量仪表指示的方向是否正确无误等。
若发现异常,应立即停机处理。
电焊机制造厂生产的MZ-1000型埋弧焊机,一般是按交流电源接线出厂供货的,若要改用直流电源,需对焊机略加改装。
需要改动的主要有三处:一是直流电源的一极(应注意使用的极性)连接交流接触器的主触点,若触点面积不够时,可用两个触点并联使用;二是将互感器改为分流器;三是将交流电流表和电压表改为直流电流表和电压表。
只有熟悉焊机的结构、工作原理和使用方法,才能正确使用和及时排除各种故障,有效地发挥设备的正常功能。
在使用过程中应对设备经常进行清扫,严防异物落入电源或焊车的运动部件内,并应及时检查连接件是否因运动时的振动而使之松动。
运动部件响声异常、电路引线不正常地发热往往就是由于连接件松动而引起的。
若设备在露天工作,还要特别注意因下雨受潮而破坏焊机的绝缘等问题。
但是任何设备工作一段时间后,发生某些故障总是难免的,因此对焊接设备必须进行经常性的检查和维护。
埋弧焊机常见的故障和排除方法见表。
表埋弧焊机常见故障及排除方法故障产生的主要原因排除方法当按下焊丝“向上”、“向下”按钮时,焊丝动作不对或不动作1)控制线路中有故障(如控制变压器、整流桥损坏,按钮接触不良)2)感应电动机方向接反3)发电机或电动机电刷接触不好1)检查上述部件并修复2)改换三相感应电动机的输入接线焊接过程一切正常,而焊车突然停止行走1)小车离合器已脱开2)小车轮被电缆等物阻挡1)关紧离合器2)排除车轮的阻接物按下“起动”按钮后,继电器动作,而接触器不能正常动作1)中间继电器失常2)接触器线圈有故障3)接触器磁铁接触面生锈或污垢太多1)检修中间继电器2)检修接触器焊接过程中,机头与导电嘴的位置不时改变焊车有关部件有游隙检查消除游隙或更换磨损零件焊机起动后,焊丝末端周期地与工件“粘住”或常常断弧1)“粘住”是因为电弧电压太低,焊接电流太小或网路电压主太低2)常常断弧是因为电弧电压太高,焊接电流太大或网路电压太高1)增加电弧电压或焊接电流2)减小电弧电压或焊接电流3)改善网路负荷状态焊丝没有与工件接触,焊接回路有电焊接小车与工件之间的绝缘被破坏1)检查小车车轮绝缘情况2)检查小车下面是否有金属与工件短路焊丝在导电嘴里摆动,导电1)导电嘴磨损更换新导电嘴嘴以下的焊丝不时变红2)导电不良焊接电路接通时,电弧未引燃,而焊线粘结在工件上焊丝与工件之间接触太紧使焊丝与工件之间轻微接触导电嘴末端随焊一起熔化1)电弧太长或焊丝伸出长度太短2)焊丝给送和焊接小车皆已停止,电弧仍在燃烧3)焊接电流太大1)增加焊丝给送速度或焊丝伸出长度2)检查焊丝焊车停止原因3)减小焊接电流焊接停止后,焊丝与工件粘住1)“停止”按钮按下速度太快2)不经过“停止1”而直接按下“停止2”1)慢慢按下“停止”按钮2)先按下“停止1”待电弧自然熄灭后,再按“停止2”焊接过程中焊剂停止输送或输送不均匀1)焊剂箱阀门处被凝结成块的焊剂堵塞2)焊嘴未置于焊剂漏斗头中间1)清理焊剂箱2)检查并调整。
埋弧焊气孔等缺陷问题分析及预防
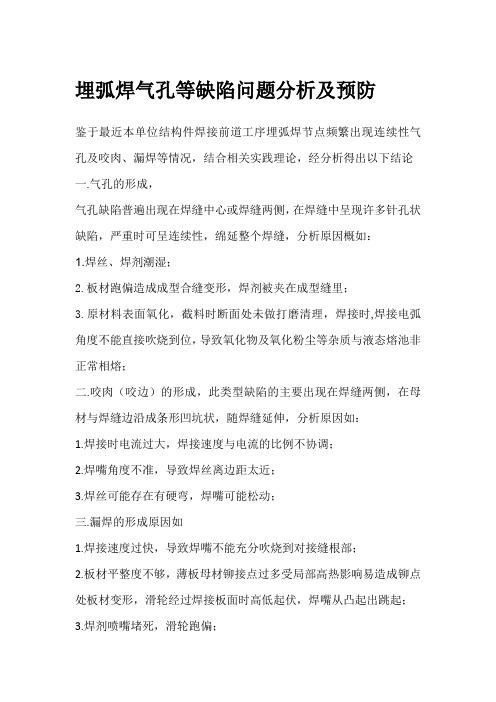
埋弧焊气孔等缺陷问题分析及预防鉴于最近本单位结构件焊接前道工序埋弧焊节点频繁出现连续性气孔及咬肉、漏焊等情况,结合相关实践理论,经分析得出以下结论一.气孔的形成,气孔缺陷普遍出现在焊缝中心或焊缝两侧,在焊缝中呈现许多针孔状缺陷,严重时可呈连续性,绵延整个焊缝,分析原因概如:1.焊丝、焊剂潮湿;2.板材跑偏造成成型合缝变形,焊剂被夹在成型缝里;3.原材料表面氧化,截料时断面处未做打磨清理,焊接时,焊接电弧角度不能直接吹烧到位,导致氧化物及氧化粉尘等杂质与液态熔池非正常相熔;二.咬肉(咬边)的形成,此类型缺陷的主要出现在焊缝两侧,在母材与焊缝边沿成条形凹坑状,随焊缝延伸,分析原因如:1.焊接时电流过大,焊接速度与电流的比例不协调;2.焊嘴角度不准,导致焊丝离边距太近;3.焊丝可能存在有硬弯,焊嘴可能松动;三.漏焊的形成原因如1.焊接速度过快,导致焊嘴不能充分吹烧到对接缝根部;2.板材平整度不够,薄板母材铆接点过多受局部高热影响易造成铆点处板材变形,滑轮经过焊接板面时高低起伏,焊嘴从凸起出跳起;3.焊剂喷嘴堵死,滑轮跑偏;四.埋弧焊防范注意事项1.气孔缺陷注意事项1.注意焊丝防水防锈,焊剂使用前的热烘干处理;2.保证截料时板材的平整度,铆接的准确性,避免接板处变形产生缝隙;3.务必清理原材料表面氧化物,截料时断面处必须做打磨除锈清理;2.咬肉(咬边)缺陷注意事项1.确保电流电压及焊接速度的合理性(电流一般是焊丝直径的100~200倍,焊接速度随板材厚度酌情而定);2.掌握好焊嘴角度,焊嘴与焊接根部的距离;3.操作人员应预先查验焊丝可能存在的硬弯,焊嘴可能出现的松动;3.漏焊缺陷注意事项1.注意焊接速度随着板材厚度调整,确保焊嘴能充分的吹烧到对接缝根部;2.原材料截料的板材轧制平整,决定了自动埋弧焊接时的流畅性,务必考虑薄板母材铆接处点数的合理性,以免发生滑轮经过焊接板面时高低起伏,焊嘴从凸起处跳起时,焊嘴偏离焊道引起漏焊,3.操作人员预先查验焊剂喷嘴通畅,滑轮螺丝是否松动,以防引起漏焊。
详解埋弧焊主要缺陷及防止措施方法,好好收藏!

详解埋弧焊主要缺陷及防止措施方法,好好收藏!埋弧焊时可能产生的主要缺陷,除了由于所用焊接工艺参数不当造成的熔透不足、烧穿、成形不良以外,还有气孔、裂纹、夹渣等。
本节主要叙述气孔、裂纹、夹渣这几种缺陷的产生原因及其防止措施。
1. 气孔埋弧焊焊缝产生气孔的主要原因及防止措施如下:1)焊剂吸潮或不干净焊剂中的水分、污物和氧化铁屑等都会使焊缝产生气孔,在回收使用的焊剂中这个问题更为突出。
水分可通过烘干消除,烘干温度与肘间由焊剂生产厂家规定。
防止焊剂吸收水分的最好方法是正确肋储存和保管6 采用真空式焊剂回、收器可以较有效地分离焊剂与尘土,从而减少回收焊剂在使用中产生气孔的可能性。
2)焊接时焊剂覆盖不充分由于电弧外露并卷入空气而造成气孔。
焊接环缝时,特别是小直径的环缝,容易出现这种现象,应采取适当措施,防止焊剂散落。
3)熔渣粘度过大焊接时溶入高温液态金属中的气体在冷却过程中将以气泡形式溢出。
如果熔渣粘度过大,气泡无法通过熔渣,被阻挡在焊缝金属表面附近而造成气孔。
通过调整焊剂的化学成分,改变熔渣的粘度即可解决。
4)电弧磁偏吹焊接时经常发生电弧磁偏吹现象,特别是在用直流电焊接时更为严重。
电弧磁偏吹会在焊缝中造成气孔。
磁偏吹的方向、受很多因素的影响,例如工件上焊接电缆的联接位置:电缆接线处接触不良、部分焊接电缆环绕接头造成的二次磁场等。
在同一条焊缝的不同部位,磁偏吹的方向也不相同。
在接近端部的一段焊缝上,磁偏吹更经常发生,因此这段焊缝气孔也较多。
为了减少磁偏吹的影响,应尽可能采用交流电源;工件上焊接电缆的联接位置尽可能远离焊缝终端;避免部分焊接电缆在工件上产生二次磁场等。
5)工件焊接部位被污染焊接坡口及其附近的铁锈、油污或其他污物在焊接时将产生大量气体,促使气孔生成,焊接之前应予清除。
2. 裂纹通常情况下,埋弧焊接头有可能产生两种类型裂纹,即结晶裂纹和氢致裂纹。
前者只限于焊缝金属,后者则可能发生在焊缝金属或热影响区。
埋弧焊常见问题
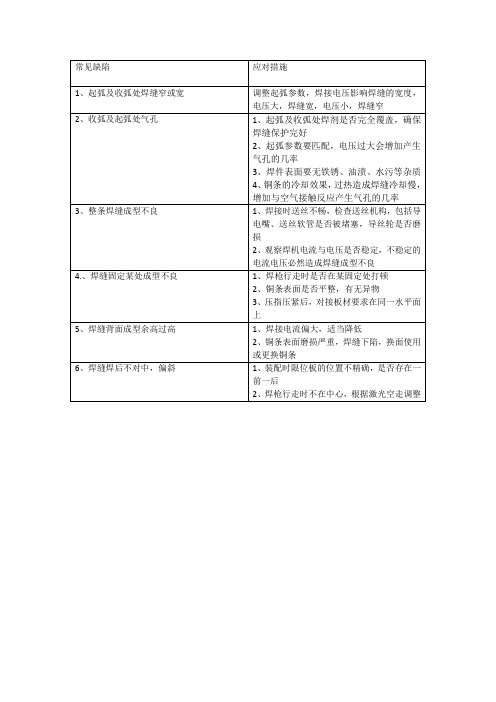
2、铜条表面磨损严重,焊缝下陷,换面使用或更换铜条
6、焊缝焊后不对中,偏斜
1、装配时限位板的位置不精确,是否存在一前一后
2、焊枪行走时不在中心,根据激光空走调整
3、整条焊缝成型不良
1、焊接时送丝不畅,检查送丝机构,包括导电嘴、送丝软管是否被堵塞,导丝轮是否磨损
2、观察焊机电流与电压是否稳定,不稳定的电流电压必然造成焊缝成型不良
4.、焊缝固定某处成型不良
1、焊枪行走时是否在某固定处打顿
2、铜条表面是否平整,有无异物
3、压指压紧后,对接板材要求在同一水平面上
5、焊缝背面成型余高过高
常见缺陷
应对措施
1、起弧及收弧处焊缝窄或宽
调整起弧参数,焊接电压影响焊缝的宽度,电压大,焊缝宽,电压小,焊缝窄
2、收弧及起弧处气孔
1、起弧及收弧处焊剂是否完全覆盖,确保焊缝保护完好
2、起铁锈、油渍、水污等杂质
4、铜条的冷却效果,过热造成焊缝冷却慢,增加与空气接触反应产生气孔的几率
碳钢板埋弧焊表面气孔问题的分析及对策
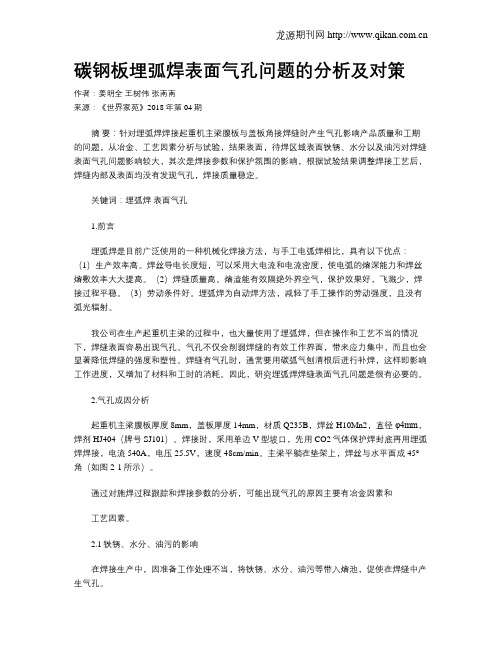
碳钢板埋弧焊表面气孔问题的分析及对策作者:姜明全王树伟张南南来源:《世界家苑》2018年第04期摘要:针对埋弧焊焊接起重机主梁腹板与盖板角接焊缝时产生气孔影响产品质量和工期的问题,从冶金、工艺因素分析与试验,结果表面,待焊区域表面铁锈、水分以及油污对焊缝表面气孔问题影响较大,其次是焊接参数和保护氛围的影响,根据试验结果调整焊接工艺后,焊缝内部及表面均没有发现气孔,焊接质量稳定。
关键词:埋弧焊表面气孔1.前言埋弧焊是目前广泛使用的一种机械化焊接方法,与手工电弧焊相比,具有以下优点:(1)生产效率高。
焊丝导电长度短,可以采用大电流和电流密度,使电弧的熔深能力和焊丝熔敷效率大大提高。
(2)焊缝质量高。
熔渣能有效隔绝外界空气,保护效果好,飞溅少,焊接过程平稳。
(3)劳动条件好。
埋弧焊为自动焊方法,减轻了手工操作的劳动强度,且没有弧光辐射。
我公司在生产起重机主梁的过程中,也大量使用了埋弧焊,但在操作和工艺不当的情况下,焊缝表面容易出现气孔。
气孔不仅会削弱焊缝的有效工作界面,带来应力集中,而且也会显著降低焊缝的强度和塑性。
焊缝有气孔时,通常要用碳弧气刨清根后进行补焊,这样即影响工作进度,又增加了材料和工时的消耗。
因此,研究埋弧焊焊缝表面气孔问题是很有必要的。
2.气孔成因分析起重机主梁腹板厚度8mm,盖板厚度14mm,材质Q235B,焊丝H10Mn2,直径φ4mm,焊剂HJ404(牌号SJ101)。
焊接时,采用单边V型坡口,先用CO2气体保护焊封底再用埋弧焊焊接,电流540A,电压25.5V,速度48cm/min。
主梁平躺在垫架上,焊丝与水平面成45°角(如图2-1所示)。
通过对施焊过程跟踪和焊接参数的分析,可能出现气孔的原因主要有冶金因素和工艺因素。
2.1铁锈、水分、油污的影响在焊接生产中,因准备工作处理不当,将铁锈、水分、油污等带入熔池,促使在焊缝中产生气孔。
铁锈主要成分为mFe2O3·nH2O,焊接时会析出大量的氧,增加氧化作用,促使生成CO2气孔。
埋弧焊常见焊接缺陷的成因分析及对策

埋弧焊常见焊接缺陷的成因分析及对策埋弧焊是一种常用的焊接方法,常见焊接缺陷包括气孔、夹渣、碳化物析出和裂纹等。
下面就这些常见焊接缺陷的成因进行分析,并提出相应的对策。
1.气孔气孔是由于焊口或焊丝表面含有气体、油污、水蒸汽等杂质进入焊缝内,而在焊接过程中被溶解在熔池中形成的孔洞。
气孔的成因主要有以下几个方面:1)焊接金属表面存在污染物;2)熔池热循环不充分,导致气体不能完全从焊缝中逸出;3)焊接材料或熔化金属中的气体含量过高。
对策:1)确保焊材和焊接母材的表面干净,需要进行预处理(如打磨、除油);2)控制焊接电流、电弧稳定,使熔池和热循环达到最佳状态;3)使用低气含量焊材,减少气体溶解在熔池中的机会。
2.夹渣夹渣是指焊缝中出现的包括焊渣在内的非金属夹杂物。
夹渣的成因主要是焊接过程中未能及时清理熔池中的渣滓,导致其残留在焊缝中。
对策:1)控制焊接参数,确保熔池的活动性足够高,便于渣滓从焊缝中浮出;2)焊缝宽度的设定要合理,以便焊工容易清理夹渣;3)确保焊缝两侧的金属表面干净,并采取适当的焊接技术措施,如倾斜角度、填充和推动方式等。
3.碳化物析出碳化物析出是在焊缝中由于熔化金属的冷却速度过慢,导致碳元素和金属元素结合形成的碳化物。
碳化物的成因主要有以下几个方面:1)金属元素成分不稳定,含有高碳或其他容易形成碳化物的合金元素;2)焊接过程中冷却速度过慢,导致碳和合金元素结合。
对策:1)控制焊接工艺参数,提高焊接速度,使熔池的冷却速度加快,减少碳化物的形成;2)选择含有稳定成分的焊接材料,避免含有高碳或其他容易形成碳化物的合金元素。
4.裂纹裂纹是焊接缺陷中最严重的一种,会导致焊接连接的失效。
1)焊接应力过大或应力集中,引发金属的应力超过其承受极限而发生破裂;2)低温下的氢致裂纹,由于焊材或焊接工艺中含氢元素的存在,使焊接过程中氢聚积在焊缝中导致裂纹形成。
对策:1)控制焊接应力,尤其是焊接位置的应力集中区域,采取合适的焊接顺序和焊接参数;2)确保焊接材料和焊接环境的干燥,避免氢聚积导致裂纹的形成。
埋弧焊问题及解决
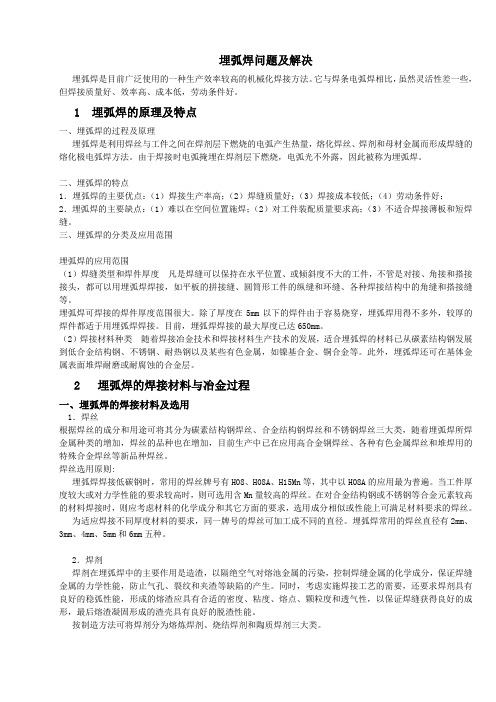
埋弧焊问题及解决埋弧焊是目前广泛使用的一种生产效率较高的机械化焊接方法。
它与焊条电弧焊相比,虽然灵活性差一些,但焊接质量好、效率高、成本低,劳动条件好。
1 埋弧焊的原理及特点一、埋弧焊的过程及原理埋弧焊是利用焊丝与工件之间在焊剂层下燃烧的电弧产生热量,熔化焊丝、焊剂和母材金属而形成焊缝的熔化极电弧焊方法。
由于焊接时电弧掩埋在焊剂层下燃烧,电弧光不外露,因此被称为埋弧焊。
二、埋弧焊的特点1.埋弧焊的主要优点:(1)焊接生产率高;(2)焊缝质量好;(3)焊接成本较低;(4)劳动条件好;2.埋弧焊的主要缺点:(1)难以在空间位置施焊;(2)对工件装配质量要求高;(3)不适合焊接薄板和短焊缝。
三、埋弧焊的分类及应用范围埋弧焊的应用范围(1)焊缝类型和焊件厚度凡是焊缝可以保持在水平位置、或倾斜度不大的工件,不管是对接、角接和搭接接头,都可以用埋弧焊焊接,如平板的拼接缝、圆筒形工件的纵缝和环缝、各种焊接结构中的角缝和搭接缝等。
埋弧焊可焊接的焊件厚度范围很大。
除了厚度在5mm以下的焊件由于容易烧穿,埋弧焊用得不多外,较厚的焊件都适于用埋弧焊焊接。
目前,埋弧焊焊接的最大厚度已达650mm。
(2)焊接材料种类随着焊接冶金技术和焊接材料生产技术的发展,适合埋弧焊的材料已从碳素结构钢发展到低合金结构钢、不锈钢、耐热钢以及某些有色金属,如镍基合金、铜合金等。
此外,埋弧焊还可在基体金属表面堆焊耐磨或耐腐蚀的合金层。
2 埋弧焊的焊接材料与冶金过程一、埋弧焊的焊接材料及选用1.焊丝根据焊丝的成分和用途可将其分为碳素结构钢焊丝、合金结构钢焊丝和不锈钢焊丝三大类,随着埋弧焊所焊金属种类的增加,焊丝的品种也在增加,目前生产中已在应用高合金钢焊丝、各种有色金属焊丝和堆焊用的特殊合金焊丝等新品种焊丝。
焊丝选用原则:埋弧焊焊接低碳钢时,常用的焊丝牌号有H08、H08A、H15Mn等,其中以H08A的应用最为普遍。
当工件厚度较大或对力学性能的要求较高时,则可选用含Mn量较高的焊丝。
数字化埋弧焊常见故障及处理

1.数码管显示1-3分别对应第一,第二,第三相(U2,U3,U4对应的输入)。检查缺相可以根据些提示来检测,减少检修时间。
2.缺相故障通常是由同步变压器接线故障所引起的。
3.电压显示E07
热继电器故障。排查方法如下:
检查热继电器是否正常。
检查热继电器与电源面板间连接是否正常。
如果上述两步仍未发现故障源,检查电源面板上CON2-2是否对GND或5V短路,如无短路,检查CON2-2与IC12-25脚之间是否连通,如果不通,检查线路。如果正常接通,则单片机引脚损坏,需更换单片机。
4如果刹车电路正常,检查送丝触发引脚(IC12-11)在启动送丝期间有无15KHZ左右的方波信号,若无,检查此信号有无对其它引脚短路,若无,此I/O口损坏,需更换单片机。若有方波信号发出,顺着信号走向,检查后面的R11和推挽电路,若R11正常观察Q16(IRFP460)的栅极是否也有一个15KHZ的幅值为12V的方波,如果无,表明推挽电路有问题,此时如果波形衡为高,R44或Q32损坏,衡为低,检查Q31,Q24,及周围电阻。如果Q16栅极波形正常,检查Q16的漏极与CON4-1或CON4-2之间相连通。如果不通,检查继电器和相关连接线路;如果上述连接正常,再检查Q16源极与GND之前的通断,如果为断路,检查R301是否损坏、及相应焊点有无异常;如果此线路仍无异常,检查交流110V整流后的160V电压,及其到送丝继电器之间的线路通断。如果160V也正常,请查检送丝电机。
送丝电压不正常,排查方法如下:
1送丝电压与预设值相差太大。先检查R29上端是否与160V通路,R32上端与Q16漏极是否通路,若有断路,检查线路。如果线路正常,再检查送丝反馈采样电路,R29,R33,R32,R36的阻值是否精确。如果精确,请更换同阻值的精密电阻。如果电阻也正常,最后检查送丝保护电路。首先确定R301的阻值是否正确,若不正常,请更换;阻值正常,再检查比较电路,U11-2(LM358)的1V电是否正常。若不正常,检查1V产生的分压电路;如果1V正常,U11-1仍输出高电平(5V),则U11损坏。如果U11-1为低电平,D20直通,将送丝PWM拉低将会导致输出占空比达100%。
焊接常见问题及焊接返修工艺简析
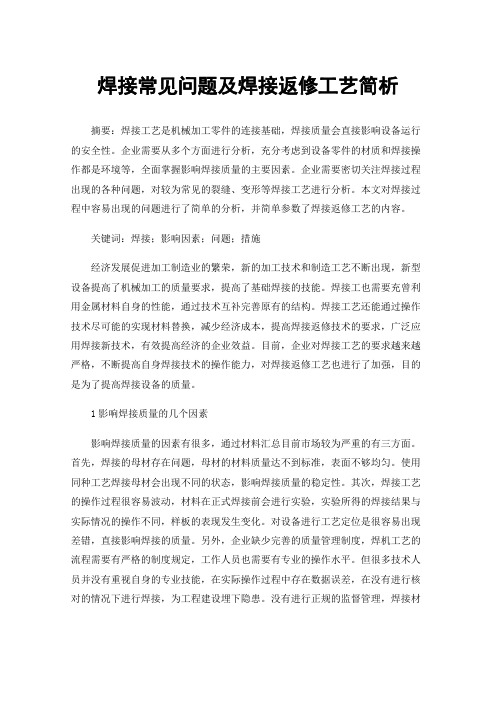
焊接常见问题及焊接返修工艺简析摘要:焊接工艺是机械加工零件的连接基础,焊接质量会直接影响设备运行的安全性。
企业需要从多个方面进行分析,充分考虑到设备零件的材质和焊接操作都是环境等,全面掌握影响焊接质量的主要因素。
企业需要密切关注焊接过程出现的各种问题,对较为常见的裂缝、变形等焊接工艺进行分析。
本文对焊接过程中容易出现的问题进行了简单的分析,并简单参数了焊接返修工艺的内容。
关键词:焊接;影响因素;问题;措施经济发展促进加工制造业的繁荣,新的加工技术和制造工艺不断出现,新型设备提高了机械加工的质量要求,提高了基础焊接的技能。
焊接工也需要充曾利用金属材料自身的性能,通过技术互补完善原有的结构。
焊接工艺还能通过操作技术尽可能的实现材料替换,减少经济成本,提高焊接返修技术的要求,广泛应用焊接新技术,有效提高经济的企业效益。
目前,企业对焊接工艺的要求越来越严格,不断提高自身焊接技术的操作能力,对焊接返修工艺也进行了加强,目的是为了提高焊接设备的质量。
1影响焊接质量的几个因素影响焊接质量的因素有很多,通过材料汇总目前市场较为严重的有三方面。
首先,焊接的母材存在问题,母材的材料质量达不到标准,表面不够均匀。
使用同种工艺焊接母材会出现不同的状态,影响焊接质量的稳定性。
其次,焊接工艺的操作过程很容易波动,材料在正式焊接前会进行实验,实验所得的焊接结果与实际情况的操作不同,样板的表现发生变化。
对设备进行工艺定位是很容易出现差错,直接影响焊接的质量。
另外,企业缺少完善的质量管理制度,焊机工艺的流程需要有严格的制度规定,工作人员也需要有专业的操作水平。
但很多技术人员并没有重视自身的专业技能,在实际操作过程中存在数据误差,在没有进行核对的情况下进行焊接,为工程建设埋下隐患。
没有进行正规的监督管理,焊接材料没有按照规定进行储存,直接影响材料接头处的应力情况,如果不加以控制,很可能会出现质量漏洞。
2焊接常见问题分析及处理2.1工件变形设备焊接过程中很容易出现工件变形的情况,焊接技术不过关和材料的问题都会造成工件变形。
钩舌埋弧焊的常见质量问题及改进建议
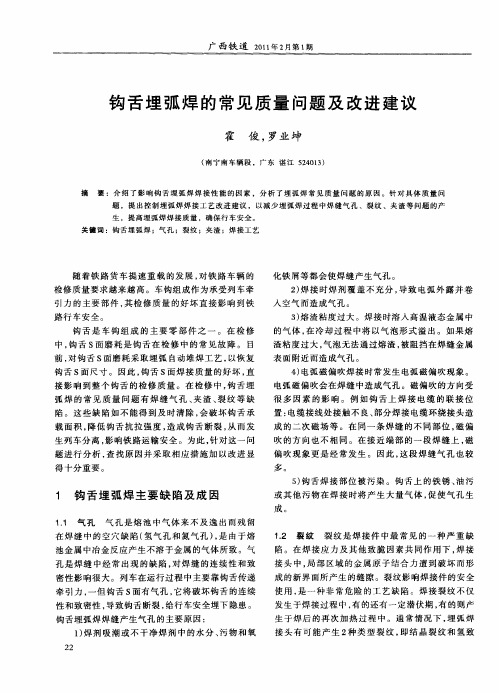
钩 舌 埋 弧 焊 的 常见 质 量 问题 及 改 进 建 议
霍 俊 , 罗业 坤
( 宁南 车辆 段 ,广 东 湛 江 5 4 1 ) 南 2 0 3
摘 要 :介 绍 了 影 响 钩 舌 埋 弧 焊 焊 接 性 能 的 因素 ,分 析 了埋 弧 焊 常 见 质 量 问 题 的 原 因 。针 对 具 体 质 量 问
性 和致 密性 , 致钩舌 断 裂 , 导 给行 车安 全埋 下 隐患 。 钩舌 埋 弧焊焊缝 产 生气孔 的主要 原 因 : 1 焊 剂 吸潮 或不 干 净焊 剂 中的水 分 、 物 和氧 ) 污
22
陷 。在 焊接 应 力及 其 他致 脆 因素 共 同作 用 下 , 焊接 接 头 中 , 部 区域 的金 属 原 子结 合力 遭 到破 坏 而 形 局 成 的新界 面所产 生 的缝隙 。裂纹 影响焊 接件 的安 全 使 用 , 一种 非 常危 险 的工 艺 缺陷 。 焊接 裂纹 不 仅 是 发生 于焊 接过 程 中 , 的还 有一 定潜伏 期 , 的则 产 有 有
题 , 提 出 控 制 埋 弧 焊 焊 接 工 艺 改 进 建 议 , 以减 少 埋 弧 焊 过程 中 焊 缝 气 孔 、裂 纹 、夹 渣 等 问题 的 产 生 ,提 高 埋 弧 焊 焊 接质 量 ,确 保 行 车 安 全 。 关 键 词 :钩 舌埋 弧 焊 ;气 孔 ;裂纹 ;夹 渣 ;焊 接 工艺
1 钩 舌 埋 弧 焊 主 要 缺 陷及 成 因
11 气 孔 . 气 孔 是 熔 池 中气 体 来 不及 逸 出而残 留
或 其 他 污物 在 焊接 时将 产 生 大量气 体 , 使 气孔 生 促
成。
在 焊缝 中 的空穴 缺 陷 ( 氢气 孔 和 氮气 孔 ) 是 由于熔 ,
- 1、下载文档前请自行甄别文档内容的完整性,平台不提供额外的编辑、内容补充、找答案等附加服务。
- 2、"仅部分预览"的文档,不可在线预览部分如存在完整性等问题,可反馈申请退款(可完整预览的文档不适用该条件!)。
- 3、如文档侵犯您的权益,请联系客服反馈,我们会尽快为您处理(人工客服工作时间:9:00-18:30)。
埋弧焊问题及解决埋弧焊是目前广泛使用的一种生产效率较高的机械化焊接方法。
它与焊条电弧焊相比,虽然灵活性差一些,但焊接质量好、效率高、成本低,劳动条件好。
1 埋弧焊的原理及特点一、埋弧焊的过程及原理埋弧焊是利用焊丝与工件之间在焊剂层下燃烧的电弧产生热量,熔化焊丝、焊剂和母材金属而形成焊缝的熔化极电弧焊方法。
由于焊接时电弧掩埋在焊剂层下燃烧,电弧光不外露,因此被称为埋弧焊。
二、埋弧焊的特点1.埋弧焊的主要优点:(1)焊接生产率高;(2)焊缝质量好;(3)焊接成本较低;(4)劳动条件好;2.埋弧焊的主要缺点:(1)难以在空间位置施焊;(2)对工件装配质量要求高;(3)不适合焊接薄板和短焊缝。
三、埋弧焊的分类及应用围埋弧焊的应用围(1)焊缝类型和焊件厚度凡是焊缝可以保持在水平位置、或倾斜度不大的工件,不管是对接、角接和搭接接头,都可以用埋弧焊焊接,如平板的拼接缝、圆筒形工件的纵缝和环缝、各种焊接结构中的角缝和搭接缝等。
埋弧焊可焊接的焊件厚度围很大。
除了厚度在5mm以下的焊件由于容易烧穿,埋弧焊用得不多外,较厚的焊件都适于用埋弧焊焊接。
目前,埋弧焊焊接的最大厚度已达650mm。
(2)焊接材料种类随着焊接冶金技术和焊接材料生产技术的发展,适合埋弧焊的材料已从碳素结构钢发展到低合金结构钢、不锈钢、耐热钢以及某些有色金属,如镍基合金、铜合金等。
此外,埋弧焊还可在基体金属表面堆焊耐磨或耐腐蚀的合金层。
2 埋弧焊的焊接材料与冶金过程一、埋弧焊的焊接材料及选用1.焊丝根据焊丝的成分和用途可将其分为碳素结构钢焊丝、合金结构钢焊丝和不锈钢焊丝三大类,随着埋弧焊所焊金属种类的增加,焊丝的品种也在增加,目前生产中已在应用高合金钢焊丝、各种有色金属焊丝和堆焊用的特殊合金焊丝等新品种焊丝。
焊丝选用原则:埋弧焊焊接低碳钢时,常用的焊丝牌号有H08、H08A、H15Mn等,其中以H08A的应用最为普遍。
当工件厚度较大或对力学性能的要求较高时,则可选用含Mn量较高的焊丝。
在对合金结构钢或不锈钢等合金元素较高的材料焊接时,则应考虑材料的化学成分和其它方面的要求,选用成分相似或性能上可满足材料要求的焊丝。
为适应焊接不同厚度材料的要求,同一牌号的焊丝可加工成不同的直径。
埋弧焊常用的焊丝直径有2mm、3mm、4mm、5mm和6mm五种。
2.焊剂焊剂在埋弧焊中的主要作用是造渣,以隔绝空气对熔池金属的污染,控制焊缝金属的化学成分,保证焊缝金属的力学性能,防止气孔、裂纹和夹渣等缺陷的产生。
同时,考虑实施焊接工艺的需要,还要求焊剂具有良好的稳弧性能,形成的熔渣应具有合适的密度、粘度、熔点、颗粒度和透气性,以保证焊缝获得良好的成形,最后熔渣凝固形成的渣壳具有良好的脱渣性能。
按制造方法可将焊剂分为熔炼焊剂、烧结焊剂和质焊剂三大类。
埋弧焊熔炼焊剂化学成分3.焊剂和焊丝的选用与配合焊剂和焊丝的正确选用及二者之间的合理配合,是获得优质焊缝的关键,也是埋弧焊工艺过程的重要环节。
所以必须按工件的成分、性能和要求,正确、合理地选配焊剂和焊丝。
在焊接低碳钢和强度等级较低的合金钢时,选配焊剂和焊丝通常以满足力学性能要求为主,使焊缝强度达到与母材等强度,同时要满足其它力学性能指标要求。
可选用下面两种配合方式中的任何一种:用高锰高硅焊剂(如HJ430、HJ431)配合低碳钢焊丝(如 H08A )或含锰焊丝(如 H08MnA );用无锰高硅或低锰中硅焊剂(如HJ130、HJ250)配合高锰焊丝(如H10Mn2)。
焊接低合金高强度钢时,除要使焊缝与母材等强外,要特别注意提高焊缝的塑性和韧性,一般选用中锰中硅或低锰中硅焊剂(如HJ350、HJ250)配合相应钢种焊丝。
焊焊接低温钢、耐热钢和耐蚀钢时,可选用中硅或低硅型焊剂与相应的合金钢焊丝配合。
焊接奥氏体不锈钢等高合金钢时,应选用合金含量比母材高的焊丝;焊剂要选用碱度高的中硅或低硅焊剂,如果只有合金成分较低的焊丝,也可以配用专门的烧结焊剂或质焊剂焊接,依靠焊剂过渡必要的合金元无法加入脱氧剂和铁合金水冷粒化、烘干、加入粘结剂调制湿料,再经烘~℃的较熔炼焊剂烧结焊剂素,同样可以获得满意的焊缝成分和性能。
3 埋弧焊工艺一、埋弧焊工艺的容和编制1.埋弧焊工艺的主要容埋弧焊工艺主要包括焊接工艺方法的选择;焊接工艺装备的选用;焊接坡口的设计;焊接材料的选定;焊接工艺参数的制定;工件组装工艺编制;操作技术参数及焊接过程控制技术参数的制定;焊缝缺陷的检查方法及修补技术的制定;焊前预处理与焊后热处理技术的制定等容。
2.编制焊接工艺的原则和依据首先要保证接头的质量完全符合工件技术条件或标准的规定;其次是在保证接头质量的前提下,最大限度的降低生产成本,即以最高的焊接速度,最低的焊材消耗和能量消耗以及最少的焊接工时完成整个焊接过程。
编制焊接工艺的依据是工件材料的牌号和规格,工件的形状和结构,焊接位置以及对焊接接头性能的技术要求等。
3.埋弧焊工艺规程及实例埋弧焊工艺参数对焊缝成形的影响(用交流电焊接)2.工艺参数的选择方法(1) 工艺参数的选择依据焊接工艺参数的选择是针对将要投产的焊接结构施工图上标明的具体焊接接头进行的。
根据产品图纸和相应的技术条件,下列原始条件是已知的:1)工件的形状和尺寸(直径,总长度);接头的钢材种类与板厚;2)焊缝的种类(纵缝、环缝)和焊缝的位置(平焊、横焊、上坡焊、下坡焊);3)接头的形式(对接、角接、搭接)和坡口形式(“Y”形、“X”形、“U”形坡口);4)对接头性能的技术要求;5)焊接结构(产品)的生产批量和进度要求。
(2) 焊接工艺参数选择程序选定埋弧焊工艺方法:•选择适用的焊剂和焊丝的牌号•选定预热温度、层间温度、后热温度以及焊后热处理温度和保温时间•选定焊接参数(焊接电流、电弧电压和焊接速度)并配合其它次要工艺参数二、埋弧焊工艺1.坡口的选择与加工2.焊件的清理与装配4.焊机的检查与调试3.焊丝表面清理与焊剂烘干➢1—引弧板 2—工件 3—焊接试板 4—引出板(一)对接接头的焊接工艺1. 对接接头双面埋弧焊表3-17 不留间隙双面埋弧焊的焊接工艺预留间隙双面埋弧焊的焊接工艺焊剂垫结构a)软管式 b)橡皮膜式1—工件 2—焊剂 3—帆布 4—充气软管 5—橡皮膜 6—压板 7—气室临时工艺垫结构1—薄钢带垫 2—石棉绳垫 3—石棉板垫➢(3)开坡口双面焊➢(4)焊条电弧焊封底双面焊➢对无法使用衬垫或不便翻转的工件,也可采用焊条电弧焊先仰焊封底,再用埋弧焊焊正面焊缝的方法。
这类焊缝可根据板厚情况开或不开坡口。
保证封底厚度大于8mm,以免埋弧焊时烧穿。
由于焊条电弧焊熔深浅,所以在正面进行埋弧焊时必须采用较大的焊接参数,以保证焊件熔透。
➢厚板工件焊条电弧焊封底多层埋弧焊典型坡口厚板工件多层埋弧焊的焊接工艺2.对接接头单面埋弧焊在对接接头中采用单面埋弧焊,可用强迫成形的方法实现单面焊双面成形,因而可免除工件翻转带来的问题,大大提高生产率,减轻劳动强度,降低生产成本。
但用这种方法焊接时,电弧功率和线能量大,接头的低温韧性较差,通常适用于中、薄板的焊接。
(1)在铜衬垫上焊接➢铜衬垫截面尺寸固定式铜衬垫顶紧机构1—压板 2—工件 3—铜衬垫 4—顶杆 5—橡胶帆布移动式水冷铜铜滑块结构1—铜滑块 2—工件 3—拉片 4—拉紧滚轮架5—滚轮 6—夹紧调节装置 7—顶杆➢(2)在焊剂垫上焊接➢在电磁平台—焊剂垫上单面埋弧焊的焊接工艺热固化焊剂垫构造和装配示意图a)构造 b)装配示意图1—双面粘贴带 2—热收缩薄膜 3—玻璃纤维布 4—热固化焊剂 5—石棉布 6—弹性垫 7—工件 8—焊剂垫 9—磁铁 10—托板 11—调节螺钉➢热固化焊剂垫单面埋弧焊的焊接工艺➢(3)在永久性垫板或锁底上焊接对接用的永久钢垫板3.对接接头环缝埋弧焊环缝埋弧焊是制造圆柱形容器最常用的一种焊接形式,它一般先在专用的焊剂垫上焊接环缝,然后再在滚轮转胎上焊接外环缝。
由于筒体部通风较差,为改善劳动条件,环缝坡口通常不对称布置,将主要焊接工作量放在外环缝,环缝主要起封底作用。
焊接时,通常采用机头不动,让工件匀速转动的方法进行焊接,工件转动的切线速度环缝埋弧焊焊接示意图1—焊丝 2—工件 3—辊轮 4—焊剂垫 5—皮带➢环缝埋弧焊焊丝偏移位置示意图(二) T形接头和搭接接头的埋弧焊T形接头和搭接接头的焊缝均是角焊缝,用埋弧焊时可采用船形焊和横角焊两种形式。
小工件及工件易翻转时多用船形焊;大工件及不易翻转时则用横角焊。
船形焊的焊接工艺(交流电源)2.横角焊缝埋弧焊➢当采用T形接头和搭接接头工件太大,不便翻转或因其它原因不能进行船形焊时,可采用焊丝倾斜布置的横角焊来完成,横角焊时焊丝与工件的相对位置对焊缝成形影响很大,当焊丝位置不当时,易产生咬边或使立板产生未熔合。
为保证焊缝的良好成形,焊丝与立板的夹角α应保持在15°~45°围(一般为20°~30°)。
横角焊焊缝埋弧焊示意图a)示意图 b)焊丝与立板间距过大 c) 焊丝与立板间距过小横角焊焊的焊接工艺(交流电源)四、埋弧焊的常见缺陷及防止方法➢§6-4 埋弧焊的其它方法➢一、附加填充金属的埋弧焊附加填充金属的埋弧焊的基本做法是在坡口中预先加入一定数量的填充金属再进行埋弧焊,在常规埋弧焊中,只有10%一20%电弧能量用于填充焊丝的熔化,其余的能量消耗于熔化焊剂和母材以及使焊接熔池的过热。
因此,可以将过剩的能量用于熔化附加的填充金属,以提高焊接生产率。
是一种既能提高熔敷速度,又不使接头性能变差的一种有效方法,这种方法使用的焊接设备和焊接工艺与普通埋弧焊基本相同。
单丝埋弧焊时熔敷速度可提高60%~100%;深坡口焊接时,可减少焊接层数,减小热影响区,降低焊剂消耗。
附加填充金属的埋弧焊接法,由于熔敷率高,稀释率低,很适宜于表面堆焊和厚壁坡口焊缝的填充层焊接。
1-辅加填充金属2-熔池3-焊剂4-渣壳5-焊缝附加填充金属埋弧焊的焊接工艺➢二、多丝埋弧焊多丝埋弧焊是一种既能保证合理的焊缝成形和良好的焊接质量,又可以提高焊接生产率的有效方法。
采用多丝单道埋弧焊焊接厚板时可实现一次焊透,其总的热输入量要比单丝多层焊时少。
因此,多丝埋弧焊与常规埋弧焊相比具有焊速高、耗能省、填充金属少等优点。
主要用于厚板材料的焊接,通常采用在工件背面使用衬垫的单面焊双面成形的焊接工艺。
双丝埋弧焊示意图a)纵列式 b)横列式 c) 直列式纵列式双丝埋弧焊示意图a)单熔池 b)双熔池(分列电弧)双丝埋弧焊应用较多的是纵列式。
前列电弧可用足够大的电流以保证熔深;后随电弧则采用较小电流和稍高电压,主要用来改善焊缝成形。
这种方法不仅可大大提高焊接速度,而且还因熔他体积大,存在时间长,冶金反应充分而使产生气孔的倾向大大减小。