外圆磨削质量缺陷原因分析与排除措施
影响深沟球轴承外圆磨削质量的因素及解决方法

影响深沟球轴承外圆磨削质量的因素及解决方法姜景滨,于秀丽(哈尔滨轴承集团公司小型球轴承分厂,黑龙江哈尔滨150036)摘 要:分析了影响深沟球轴承外圆磨削质量的常见原因并提出相应的解决办法,以轻系列61909轴承为例,说明薄壁套圈外圆磨削的注意事项,对轴承加工具有借鉴作用。
关键词:深沟球轴承;外圆磨削;圆度;棱圆度中图分类号:TG581+.1,TH133.33文献标识码:B 文章编码:1672-4582(2012)01-0038-03Factors of effect on deep groove ball bearing outer circlegrinding quality and solving methodsJiang Jingbin,Y u Xiuli(Small Ball Bearing Branch,Harbin Bearing Group Corporation ,Harbin 150036,China)Abstract:The common reasons of effecting on deep groove ball bearing outer circle grinding quality are analyzed and the corresponding solution is put forward,to light series 61909bearing as an example,the points for attention of thin-walled ring cylindrical grinding are explained ,it has reference to bearing processing.Key words:deep groove ball bearing ;cylindrical grinding ;roundness ;prismatic roundness第33卷 第1期2012年3月Vo l.33No.1Mar.2012哈 尔 滨 轴 承JOU RN AL OF HA RBIN BEARIN G收稿日期:作者简介:2011-08-10.姜景滨(1963-),女,工程师.1 前言 轴承外径通常采用无心贯穿磨削,这种加工方式批量大效率高,在加工中分粗磨、细磨、修磨才能达到成品零件要求。
外圆磨削中常见缺陷的产生原因及消除方法

9、砂轮主轴轴承间隙过大
10、卡盘装夹磨削外圆时, 头架主轴径向圆跳动过 大。
5、修整砂轮
6、保证充足的切削液
7、背吃刀量不能太大,并应随着余 量减少而逐步减少,最后多做几次
“光磨”行
8磨削前事先加以平衡
9、调整主轴轴承间隙
10、调整头架,主轴轴承间隙
工件有锥度
1、工作台未调整好
2、工件和机床的弹性变形 发生变化
2、注意润滑,如已磨损需重新修磨 顶尖
3、重新调节尾座顶尖压力
4、把顶尖卸下,擦净后重新装上
锥孔内配合不紧密
5、砂轮过钝
6、切削液不充分或供应不 及时
7、工件刚性较差而毛坯形 状误差又大,磨削余量不 均匀而引起背吃力量变 化,使工件弹性变形,发 生相应变化,结果磨削后 的工件表面部分地保留着 毛坯形状误差。
2、装夹时加平衡物,做好平衡,检 修机床
3、合理选用砂轮的粒度、硬度,仔 细修整砂轮,增加光修次数
4、适当减少背吃刀量和纵向进给 量,提高砂轮圆周速度
5、加大切削液,更换不清洁切削液
6、减小工件塑性变形,最后多作几 次光磨
3、修整砂轮
4、把金刚石装夹牢固,如金刚石有 松动,需重新焊接
5、加大或加浓切削液
6、调整轨润滑油的压力
7、打开放气阀,排除液压系统中的 空气,或检修机床
8检修机床
工件表面有 烧伤现象
1、砂轮太硬或粒度太细
2、砂轮修得过细不锋利。
3、砂轮太钝
4、背吃刀量、纵向进给量 过大或工件的圆周速度过 低。
5、切削液不充足。
2、正确调整撑块和支块对工件的压 力
工件弯曲
1、磨削用量太大
2、切削液不充分,不及时
磨削缺陷分析与解决

磨削缺陷分析与解决1.产生原因及影响因素零件的磨削精度指零件在磨削加工后,其形状、尺寸及表面相互位置三方面与理想零件的符合程度。
一般说来,形状精度高于尺寸精度,而位置精度也应高于尺寸精度。
磨削加工中的误差主要来源与两方面。
一是磨床-夹具-砂轮组成的工艺系统本身误差;二是磨削过程中出现的载荷和各种干扰:包括力变形、热变形、振动、磨损等引起的误差。
而在磨削过程中,使砂轮与工件位置改变以降低磨削精度的主要原因有:⑴.由磨削力引起的磨床和工件弹性变形;⑵.磨床和工件的热变形;⑶.磨床和工件的振动;⑷.砂轮磨损后其形状、尺寸变化;⑸.工装、夹具的损坏或变形;⑹.导轨、轴承和轴等部件的非弹性变形。
其中磨削过程中的弹性变形是主要的影响因素,它会使砂轮的实际切入深度与输入切入深度不一致,这一变化是由“砂轮架—砂轮轴承-砂轮轴-工件-工件支承”的弹性系统刚性决定。
一般为消除这种原因带来的误差常在行程进给磨削后,停止相互间的进给,仅依靠弹性回复力维持磨削,即光磨阶段(又叫清火花磨削),从而消除残留余量。
当然造成磨削误差的其它因素液很多如:工件磨削形状误差,工件热变形,磨粒切刃引起的塑性变形,砂轮的磨损等。
2.对工件的影响:降低工件使用寿命;降低工件抗疲劳强度;特殊特性的尺寸精度误差易影响工件使用,如轴承孔尺寸的控制,尺寸过小,安装不到轴上;过大,易引起振动,影响轴承使用寿命等。
3.解决方法:增加系统刚性;减少上工序加工留量,以减小磨削厚度,从而减小磨削力降低残留应力;增加光磨时间;及时修整砂轮,及时检查工装、夹具、轴承完好性及电主轴的振动性等;精细的选择砂轮,如挑选细粒度,硬度较大,组织稍紧密的砂轮;选用导热性好的砂轮(如CBN 砂轮);采用冷却性能优良的磨削液以减少因热变形引起的误差。
二、工件表面粗糙度1.产生原因及影响因素表面粗糙度指加工表面具有较小间距和峰谷所组成微观几何形状特征。
它是大量磨粒在工件表面进行切削后留下的微观痕迹的集合。
外圆磨削加工的质量缺陷分析与控制

外圆磨削加工的质量缺陷分析与控制作者:张光普焦禹萃张艳兵来源:《科技资讯》 2014年第27期张光普焦禹萃张艳兵(郑州工业应用技术学院河南郑州 451100)摘要:目前,外圆磨削技术已广泛应用于各种零件的加工中,但在磨削过程中经常出现一些有质量缺陷的零件,如加工过的零件常常会出现表面烧伤、划伤等现象。
因此,为了保证磨削后的产品的质量,在加工时就要有足够高的加工精度的磨床。
该文将从外圆磨削加工的质量缺陷分析以及控制方法进行阐述。
关键词:磨削加工质量缺陷分析控制中图分类号:TG581 文献标识码:A 文章编号:1672-3791(2014)09(c)-0049-01Quality defects analysis and controlling of grindingZhang Guangpu Jiao Yucui Zhang Yanbing(The Industrial Applied Technology College of Zhengzhou,Zhengzhou Henan,451100 China)Abstract:at present, the external cylindrical grinding technology has been widely used in various kinds of parts processing, but often appear some quality defects in the process of grinding parts, such as processed parts often appear burns, scratches and other surface phenomenon. Therefore, in order to guarantee the quality of the products after grinding, during processing need to be high enough to machining precision grinding machine. This article will from external circular grinding quality defects analysis and elaborates the control approach.Key Words:Grinding;Analysis of Quality Defects;Control磨削是指用磨料、磨具等工具来加工比较精确零件的加工方法。
磨削加工常见问题与处理方法
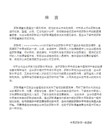
3)细长轴刚性差,承受不了磨削时的径向力
1)适当减小磨削用量,保持充足的磨削液
2)改小砂轮工作面,选用较软的砂轮,及时修整砂轮
3)使用中心托架,增强工件的刚性
工件表面烧伤
1)砂轮太硬或粒度太细或修整砂轮时修得过细;磨削液不充足
2)横向进给量过大,砂轮转速过高
1)普遍磨削时选中软以下的砂轮,修整砂轮时加快行程,保持充足的磨削液
1)换用硬度较高的砂轮
2)采用更先进的过滤装置,使磨削液更干净
工件有圆度误差
1)工件中心孔形状不正确,或中心孔内有铁屑、尘埃等
2)工件顶得过松或过紧
3)顶尖在主轴或尾架套筒锥孔内贴合不紧密或有磨损
4)砂轮主轴轴承间隙过大
5)用卡盘装夹磨削外圆时,头架主轴径向跳动过大
6)工件刚性差而磨前的形状误差又大,磨削时余量不均匀而引起背吃刀量变化,工件弹性变形也相应变化,磨后工件保留着磨前的形状误差
1)修整中心孔,重打中心孔或擦净中心孔
2)重新调节尾架顶尖压力
3)把顶尖卸下,擦净后重新装上或修磨顶尖
4)调整主轴轴承间隙或更换轴承
5)调整头架主轴轴承间隙或更换轴承
6)背吃刀量不能太大,并应随着余量减少而逐步减小,最后多作几次“光磨”行程,误差可以减小
工件弯曲
1)磨削用量太大,磨削液不充足,不及时
2)工作台导轨润滑油浮力过大使工作台浮起,在运行中产生摆动或运行时有爬行现象
3)修整砂轮时,冷却不够,使金刚石发热膨胀速度是一致的
4)砂轮主轴有轴向窜动;磨削液太少或浓度太低
5)砂轮磨损,母线不直;纵、横向进给量过大
1)如金刚石笔有松动,应重新焊牢,同时将其装夹牢固
外圆磨床磨削圆跳动超差的原因分析及维修研究

外圆磨床磨削圆跳动超差的原因分析及维修研究摘要:数控外圆磨床是端面大轴类零件精密磨削加工中不可缺少的重要工具之一,其应用范围十分广泛,能够很好的确保零件的磨削效率及加工质量。
但是在长期运行使用后,却很容易出现磨削外圆表面跳动超差问题,这在一定程度上就会给零件加工带来较大困扰,进而无法保证最终的零件加工质量,因此,要想改善现状,就要寻找一条便捷有效的途径针对该故障问题进行解决和处理。
本文也会对外圆磨床磨削期间所产生的圆跳动超差故障进行着重研究,进而根据具体产生原因,提出科学合理的维修策略,以便相关人士参考借鉴。
关键词:外圆磨床;磨削圆跳动超差故障;原因分析;维修策略现今,数控外圆磨床在汽车发动机及其它行业中有着很高的利用率,其虽然可以很好地确保零件磨削加工质量,但是在运行使用过程中仍存有一定的缺陷和不足,尤其是在磨削期间,很容易出现圆跳动超差问题,进而影响到零件加工质量,因此,要想避免这种故障问题的发生,就要通过全面的检测和维修,来挖掘出故障问题的诱发因素,并制定针对性的防控措施,这样才能最大化发挥外圆磨床的应用性能,满足端面大轴类零件磨削加工需求。
1.故障产生的具体原因分析1.1初步分析与判断在故障初步分析阶段,相关工作人员考虑主要是由以下原因所致:第一,由于磨床车轴顶尖孔加工精度不达标所致;第二,磨床拨盘结构为三拨叉结构,但在实际操作时,操作人员只采用双拨叉,这样就会导致磨床在磨削加工时因拨叉不均匀而出现旋转摆动情况,从而诱发圆跳动超差故障的发生;第三,由于磨床后轴承间隙过大,从而使得磨床运行期间出现不规律的径向跳动,进而诱发圆跳动超差故障的发生[1]。
针对这些故障原因,工作人员进行了相应的调整,得出以下结论:首先,重新修正车轴顶尖孔后,发现磨削圆跳动超差现象依然存在;其次,调整拨盘结构后,发现磨床磨削精度略有改善,可以初步判断拨叉分布的不均匀是导致该故障发生的原因之一,但不是主因;最后,对磨床头架主轴拨盘装置进行拆卸,并在夹持状态下对其头架主轴顶尖径向跳动情况进行全面检测,发现千分表指针顶尖锥端和锥尾最大跳动值分别为0. 014 mm、0. 011 mm,随后又将顶尖拆除,发现工件头架主轴的内外锥面径向跳动及前端面旋转轴向跳动分别为0. 011 mm、0. 007 mm、0. 006mm,均已超出设备最大精度允差,所以可以初步判定,头架主轴的跳动是导致故障发生的主要原因。
外圆磨削中常见的缺陷及防止措施
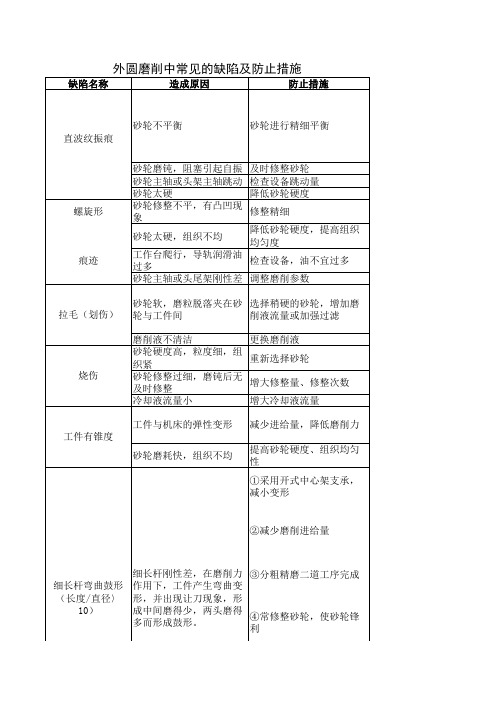
烧伤
工件有锥度 砂轮磨耗快,组织不均
②减少磨削进给量
细长杆刚性差,在磨削力 ③分粗精磨二道工序完成 细长杆弯曲鼓形 作用下,工件产生弯曲变 (长度/直径〉 形,并出现让刀现象,形 10) 成中间磨得少,两头磨得 ④常修整砂轮,使砂轮锋 多而形成鼓形。 利
⑤采用新磨料,如CBN、 SG等,增加切削能力
外圆磨削中常见的缺陷及防止措施
缺陷名称 造成原因 防止措施
砂轮不平衡 直波纹振痕 砂轮磨钝,阻塞引起自振 砂轮主轴或头架主轴跳动 砂轮太硬 砂轮修整不平,有凸凹现 象 砂轮太硬,组织不均 痕迹
砂轮进行精细平衡
及时修整砂轮 检查设备跳动量 降低砂轮硬度 修整精细 降低砂轮硬度,提高组织 均匀度
螺旋形
工作台爬行,导轨润滑油 检查设备,油不宜过多 过多 砂轮主轴或头尾架刚性差 调整磨削参数 砂轮软,磨粒脱落夹在砂 选择稍硬的砂轮,增加磨 轮与工件间 削液流量或加强过滤 磨削液不清洁 砂轮硬度高,粒度细,组 织紧 砂轮修整过细,磨钝后无 及时修整 冷却液流量小 工件与机床的弹性变形 更换磨削液 重新选择砂轮 增大修整量、修整次数 增大冷却液流量 减少进给量,降低磨削力 提高砂轮硬度、组织均匀 性 ①采用开式中心架支承, 减小变形
常见磨削缺陷的产生原因及消除方法
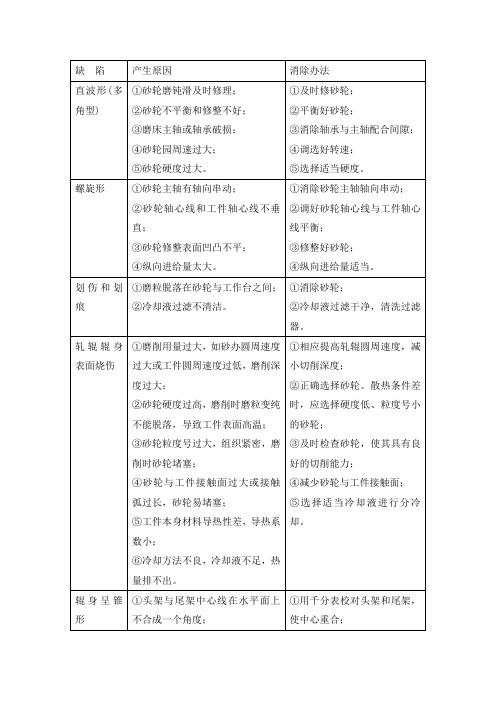
⑤选择适当冷却液进行分冷却。
辊身呈锥形
①头架与尾架中心线在水平面上不合成一个角度;
②轧辊轴线没有调整好,与砂轮轴线不垂直;
③砂轮太软,使砂轮由工件端走到另一端时产生磨耗。
①用千分表校对头架和尾架,使中心重合;
②调整好轧辊,使其轴线与顶针中心线重合;
③合理选择砂轮。
辊身呈细腰形
①头架尾架中心线在垂直平面内不重合成一个角度;
②轧辊轴线没调整好,在垂直平面内成一个角度。
①校正头架与尾架,使中心线重合;
②调整好轧辊,使其轴线与顶针中心重合。
外圆磨削中常见的缺陷及防止措施
缺陷
产生原因
消除办法
直波纹振痕
砂轮不平衡
砂轮进行精细平衡
砂轮磨钝,阻塞引起自振
及时修整砂轮
砂轮主轴或头架主轴跳动
缺陷
产生原因
消除办法
直波形(多角型)
①砂轮磨钝滑及时修理;
②砂轮不平衡和修整不好;
③磨床主轴或轴承破损;
④砂轮园周速过大;
⑤砂轮硬度过大。
①及时修砂轮;
②平衡好砂轮;
③消除轴承与主轴配合间隙;
④调选好转速;
⑤选择适当硬度。
螺旋形
①砂轮主轴有轴向串动;
②砂轮轴心线和工件轴心线不垂直;
③砂轮修整表面凹凸不平;
③砂轮粒度号过大,组织紧密,磨削时砂轮堵塞;
④砂轮与工件接触面过大或接触弧过长,砂轮易堵塞;
⑤工件本身材料导热性差,导热系数小;
⑥冷却方法不良,冷却液不足,热量排不出。
①相应提高轧辊圆周速度,减小切削深度;
②正确选择砂轮。散热条件差时,应选择硬度低、粒度号小的砂轮;
③及时检查砂轮,使其具有良好的切削能力;
磨削外经质量问题及解决措施
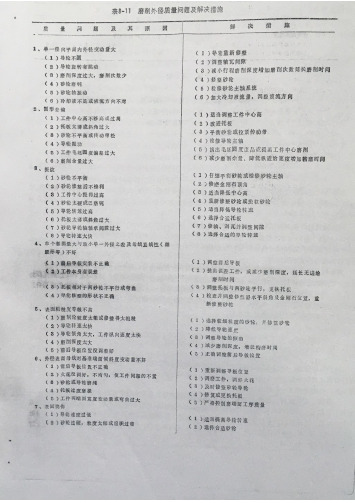
(3)减小行程磨削深度增如次数延长时问 |8减少形余量、降低纵过给速增加精时闻 (4)检查扑调整修当器水平角及金刚石位置,重 (5)搞出毛坏圆度品或贫测工件中心磨削 (2)换出误差工作,成减少磨M深度延长无进培| 决攒 (1)导轮重新修整(2)调整轴瓦间默- (4)修整砂轮(5)检修砂轮主桩系统(6)加大冷却液流量,预整方自 (1)适当调维工作中心高(2)改进托板(3)平衡砂轮或拉紧传动带(4)检修导轮主辅 (1)仔细平衡砂轮或检修主(2箱)修座金照石顶角(3)适当降低中心高( 4)重新修整砂轮或换软论(5)适当释低导轮载遇(6)选择合近托板(7)修轴、刮瓦并训整间霞(8)选择合孟的导轮转汕| (1)翼变前后导板削时间(3)调整托板与两砂轮平行,三铁新修整砂轮(1)选择校细粒度的砂伦,并(修3签)沙袋降低导轮逐庄(3)调整导轮的(损4)减少略削限度,增长粒察5时正间确词整前后导板位置(1)重新词骆导板位(2置)页络工件,诅好(8火)花及时修签砂轮导(4)复或更换礼(板5) 严格控创磨端面工序质】(1)滥当提高导轮载(浊2) 选择合适砂轮
浅析外圆磨削常见缺陷及其消除方法

浅析外圆磨削常见缺陷及其消除方法作者:焦玉来源:《商情》2012年第48期[摘要]在外圆磨削加工过程中,在工件表面经常会产生各种各样的表面缺陷,常见的如表面存在波纹、表面划伤、烧伤、鱼鳞状痕迹等。
为了保证磨削的质量,不仅要保证磨床有较高的加工精度,还要保证砂轮有较好的磨削性能。
我们从检查的角度对外圆磨削这些质量缺陷,进行分析并给出相应的解决措施。
[关键词]磨削;缺陷;消除一、工件表面产生多角形波纹此缺陷是在工件表面沿母线方向有一条条直线痕迹。
自工件横剖面来看,周边呈近似正=波的曲线。
产生的原因1、振动机L电机无隔振装置或失灵、皮带卸C装置失灵、横向进给导轨磨损,使抗=性能变差等。
9轮的不平衡或工件的r周速度太高,會引起振动。
此外,在磨削过程中,如果工件与顶尖系统刚性较差,当9轮变。
或修整得不够锋利时,9轮与工件间的磨Q加剧,也会引起振动,整个工艺系统产生的=动,就会使工件表面出现多角形波纹;2、9轮磨损不均匀,9轮r周面不平;3、9轮或工件支承松动。
多角形波纹的消除方法1、平衡9轮,新9轮要经粗精两次平衡,使用后磨损较多时应再作平衡;2、及时修整9轮,保证其具有良好的切削性能;3、确保磨头有关减振装置健全、有效;4、修整中心一及机L顶尖,高速尾架顶尖的预紧力,使其大小适中。
5、9轮也是一个主要的原因,9轮的退出时间在初磨和精磨中是有区别的。
在初磨中,9轮在工件毛7磨削成r时退出,而在精磨时,9轮接触到工件后即可退出,具体磨削效果可根据实际情况来微调。
二、工件表面产生螺旋形波纹螺旋形波纹是指工件表面上出现螺旋状很浅的波纹痕迹。
产生的原因1、9轮工作表面凸h不平;2、机L刚性影响;3、其他因素:磨削深度太大,纵向进给量太大,或9轮主q有q向:动,都有可能产生螺旋形波纹。
此外,工作台导轨润滑油压过大,使用使工作台纵向移动时产生Q浮和摆动,也会造成工件表面的螺旋形波纹。
螺旋形波纹的消除方法1、仔细修整9轮,使g轮工作面光整无凸出点;2、适当减少磨削深度及纵向进给量,降低磨削力,以减小机L刚度的影响;3、调整导轨润滑油压力,排除液压系统中的空气。
外圆磨削常见的工件缺陷
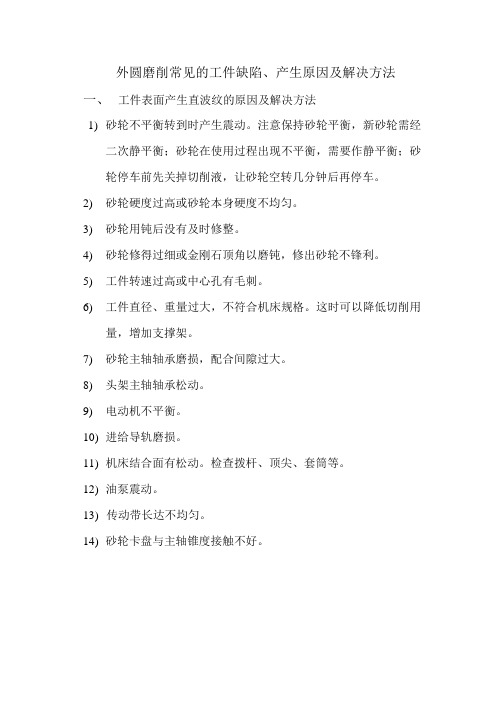
外圆磨削常见的工件缺陷、产生原因及解决方法一、工件表面产生直波纹的原因及解决方法1)砂轮不平衡转到时产生震动。
注意保持砂轮平衡,新砂轮需经二次静平衡;砂轮在使用过程出现不平衡,需要作静平衡;砂轮停车前先关掉切削液,让砂轮空转几分钟后再停车。
2)砂轮硬度过高或砂轮本身硬度不均匀。
3)砂轮用钝后没有及时修整。
4)砂轮修得过细或金刚石顶角以磨钝,修出砂轮不锋利。
5)工件转速过高或中心孔有毛刺。
6)工件直径、重量过大,不符合机床规格。
这时可以降低切削用量,增加支撑架。
7)砂轮主轴轴承磨损,配合间隙过大。
8)头架主轴轴承松动。
9)电动机不平衡。
10)进给导轨磨损。
11)机床结合面有松动。
检查拨杆、顶尖、套筒等。
12)油泵震动。
13)传动带长达不均匀。
14)砂轮卡盘与主轴锥度接触不好。
二、工件表面产生横波纹1)砂轮硬度过高或砂轮两边硬度高修得过细,而磨削深度过大。
2)纵向进给量过大。
3)砂轮磨损,母线不直。
4)修整砂轮和磨削时切削液供应不足。
5)工作台导轨润滑油过多,使台面运行产生摆动。
6)工作台运行有爬行现象。
可打开放气阀排除液压系统中的空气或检修机床。
7)砂轮主轴轴向窜动超差。
8)砂轮主轴与头架轴线不平行。
9)修整时金刚石运动中心与砂轮中心线不平行。
三、工件表面产生烧伤1)砂轮太硬或粒度太细。
2)砂轮修得过细,不锋利或砂轮太钝。
3)切削用量过大或工件速度过低。
4)切削液不充分。
四、圆柱度超差1)工件产生锥度A.工件旋转轴线与工作台运动方向不平行。
B.工件和机床的弹性变形发生变化。
校正锥度时,砂轮一定要锋利,工作过程也要保持砂轮锋利状态。
C.工作台导轨润滑油过多。
2)工件产生鼓形A.工件刚度差,磨削时产生让刀现象,减少工件的弹性变形;减少磨削深度,增加光磨次数;砂轮经常保持良好的切削性能;应使用中心架。
B.中心架调整不适当,正确调整支承块的压力。
C.机床导轨水平面内直线度超差。
3)工件产生鞍形A.磨细长轴时顶尖顶得太紧工件弯曲变形。
外圆磨常见故障排除
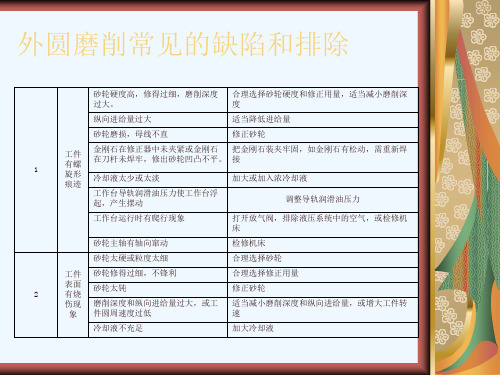
冷却液太少或太淡
工作台导轨润滑油压力使工作台浮 起,产生摆动 工作台运行时有爬行现象 砂轮主轴有轴向窜动 砂轮太硬或粒度太细
加大或加入浓冷却液
调整导轨润滑油压力 打开放气阀,排除液压系统中的空气,或检修机 床 检修机床 合理选择砂轮 合理选择修正用量 修正砂轮 适当减小磨削深度和纵向进给量,或增大工件转 速
4
磨削深度不能太大。并应随着余量减小而逐步减 小,最后多次几次光磨行程,
工作有不平衡重量时,由于离心 事先加以平衡 力作用,会在重的那边磨去 较多金属,使工件有椭圆度。 砂轮主轴轴承间隙过大。 用卡盘装夹磨削外圆时,头架主 轴径向跳动过大 调整主轴轴承间隙 调整头架主轴轴承间隙
外圆磨削常见的缺陷和排除
工作台导轨润滑油压过大,运 行中产生波动 头架和尾座中心不重合 工 6 工件刚性差,磨削时产生弹性 弯曲变型 件 有 鼓 中心架调整不适当 型
外圆磨削常见的缺陷和排除
序号 缺陷 内容 缺陷产生原因 缺陷消除方法 砂轮超出工件端面台小或过大 工件 两端 尺寸 过大 或过 小 阶台 旁外 圆尺 寸大 阶台 轴各 外圆 表面 不同 轴 工作台换向时停留时间太长或太短 调整时间 调整换向撞块位置,使砂轮超出工件端面1/3-1/2 个砂轮宽度
外圆磨削常见的缺陷和排除
砂轮硬度高,修得过细,磨削深度 过大。 纵向进给量过大 砂轮磨损,母线不直 合理选择砂轮硬度和修正用量,适当减小磨削深 度 适当降低进给量 修正砂轮
1
工件 有螺 旋形 痕迹
金刚石在修正器中未夹紧或金刚石 把金刚石装夹牢固,如金刚石有松动,需重新焊 在刀杆未焊牢,修出砂轮凹凸不平。 接
3
工件 表面 出现 直波 形振 痕
调整轴承间隙 注意保持砂轮平衡;(1)新砂轮需经俩次静平衡。 (2)砂轮使用一段时间后,如果又出现不平衡, (3)砂轮停车前,先关掉冷却液。使砂轮空转进 行脱水,以免冷却液聚集在下部引起不平衡, 根据工件材料性质,选择合适的砂轮 修正砂轮 合理选择修正用量或翻身金刚石,或得金刚石磨 修尖。
车削外圆的常见问题及解决方法
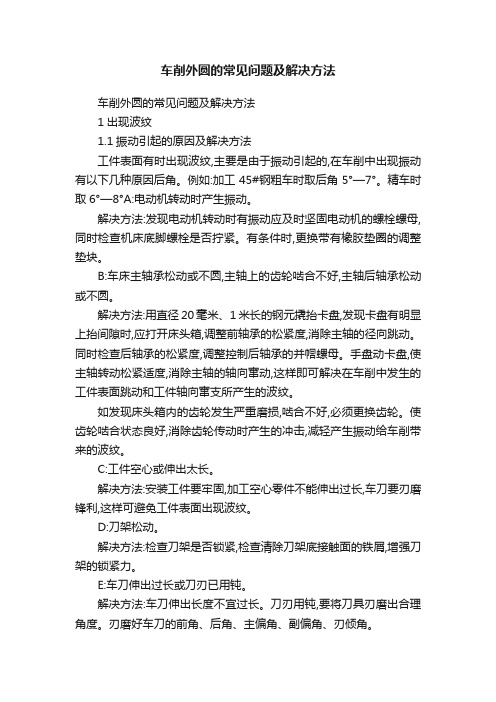
车削外圆的常见问题及解决方法车削外圆的常见问题及解决方法1出现波纹1.1振动引起的原因及解决方法工件表面有时出现波纹,主要是由于振动引起的,在车削中出现振动有以下几种原因后角。
例如:加工45#钢粗车时取后角5°—7°。
精车时取6°—8°A:电动机转动时产生振动。
解决方法:发现电动机转动时有振动应及时坚固电动机的螺栓螺母,同时检查机床底脚螺栓是否拧紧。
有条件时,更换带有橡胶垫圈的调整垫块。
B:车床主轴承松动或不圆,主轴上的齿轮啮合不好,主轴后轴承松动或不圆。
解决方法:用直径20毫米、1米长的钢元撬抬卡盘,发现卡盘有明显上抬间隙时,应打开床头箱,调整前轴承的松紧度,消除主轴的径向跳动。
同时检查后轴承的松紧度,调整控制后轴承的并帽螺母。
手盘动卡盘,使主轴转动松紧适度,消除主轴的轴向窜动,这样即可解决在车削中发生的工件表面跳动和工件轴向窜支所产生的波纹。
如发现床头箱内的齿轮发生严重磨损,啮合不好,必须更换齿轮。
使齿轮啮合状态良好,消除齿轮传动时产生的冲击,减轻产生振动给车削带来的波纹。
C:工件空心或伸出太长。
解决方法:安装工件要牢固,加工空心零件不能伸出过长,车刀要刃磨锋利,这样可避免工件表面出现波纹。
D:刀架松动。
解决方法:检查刀架是否锁紧,检查清除刀架底接触面的铁屑,增强刀架的锁紧力。
E:车刀伸出过长或刀刃已用钝。
解决方法:车刀伸出长度不宜过长。
刀刃用钝,要将刀具刃磨出合理角度。
刃磨好车刀的前角、后角、主偏角、副偏角、刃倾角。
前角:增大前角可以减少切削变形和切削力。
使切削轻快,提高加工精度和降低表面粗糙度。
工件材料的强度、硬度高,前角应选小一些,工件材料的强度硬度低前角应大一些。
一般硬质合金刀具前角为15°—20°为宜。
后角:要求切削刃强固,应取较小的后角。
精加工时应取较大的。
1.2辐射状波纹产生原因及消除方法用车床车削端面,有时会产生辐射状波纹。
数控外圆磨床常见缺陷及其解决方法

数控外圆磨床常见缺陷及其解决方法
1.加工精度不稳定
当使用数控外圆磨床进行加工时,可能会出现加工精度不稳定的情况,即在不同时间或不同工件上,加工精度会有所变化。
这可能是由于刀具磨
损或磨具磨损不均匀引起的。
解决方法是及时检查和更换磨具和刀具。
同时,定期检查磨床的工作状态和润滑情况,保证磨床正常工作。
2.磨削表面质量差
数控外圆磨床在进行磨削加工时,可能会出现磨削表面质量差的情况,即磨削后的工件表面粗糙度较高。
这可能是由于磨削参数设置不当、磨具
选择不当或磨削液不符合要求等原因造成的。
解决方法是合理设置磨削参数,选择适当的磨具,并使用符合要求的磨削液进行加工。
3.自动化程度不高
数控外圆磨床在自动化程度方面可能存在一定的缺陷。
在传统的数控
外圆磨床中,往往需要人工干预进行工件的夹紧和调整等操作。
解决方法
是引入更高级别的数控系统和自动化装置,实现工件的自动夹紧和自动调整,提高磨床的自动化程度。
4.能耗较高
5.磨削噪音大
6.润滑不良
数控外圆磨床在加工过程中需要进行润滑,以减少摩擦和磨损。
然而,有时润滑不良可能会导致磨床的工作效率下降和磨具寿命缩短。
解决方法
是定期检查润滑系统的工作状态,确保润滑剂的供应充足和均匀。
同时,定期清洗和更换润滑系统中的油液,保证润滑效果良好。
总之,数控外圆磨床常见的缺陷包括加工精度不稳定、磨削表面质量差、自动化程度不高、能耗较高、磨削噪音大和润滑不良等。
通过合理的操作和维护,可以解决这些缺陷,提高磨床的加工效率和加工质量。
车削外圆的常见问题及解决方法
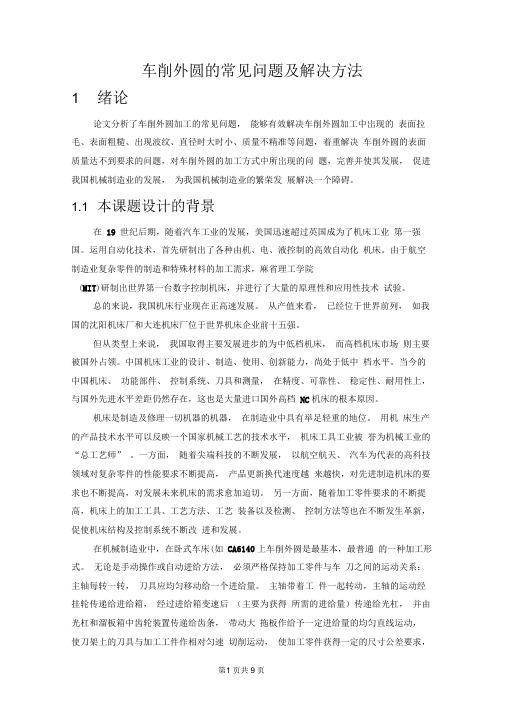
车削外圆的常见问题及解决方法1 绪论论文分析了车削外圆加工的常见问题,能够有效解决车削外圆加工中岀现的表面拉毛、表面粗糙、出现波纹、直径时大时小、质量不精准等问题,着重解决车削外圆的表面质量达不到要求的问题,对车削外圆的加工方式中所岀现的问题,完善并使其发展,促进我国机械制造业的发展,为我国机械制造业的繁荣发展解决一个障碍。
1.1 本课题设计的背景在19 世纪后期,随着汽车工业的发展,美国迅速超过英国成为了机床工业第一强国。
运用自动化技术,首先研制出了各种由机、电、液控制的高效自动化机床。
由于航空制造业复杂零件的制造和特殊材料的加工需求,麻省理工学院(MIT)研制出世界第一台数字控制机床,并进行了大量的原理性和应用性技术试验。
总的来说,我国机床行业现在正高速发展。
从产值来看,已经位于世界前列,如我国的沈阳机床厂和大连机床厂位于世界机床企业前十五强。
但从类型上来说,我国取得主要发展进步的为中低档机床,而高档机床市场则主要被国外占领。
中国机床工业的设计、制造、使用、创新能力,尚处于低中档水平。
当今的中国机床、功能部件、控制系统、刀具和测量,在精度、可靠性、稳定性、耐用性上,与国外先进水平差距仍然存在,这也是大量进口国外高档NC机床的根本原因。
机床是制造及修理一切机器的机器,在制造业中具有举足轻重的地位。
用机床生产的产品技术水平可以反映一个国家机械工艺的技术水平,机床工具工业被誉为机械工业的“总工艺师” 。
一方面,随着尖端科技的不断发展,以航空航天、汽车为代表的高科技领域对复杂零件的性能要求不断提高,产品更新换代速度越来越快,对先进制造机床的要求也不断提高,对发展未来机床的需求愈加迫切。
另一方面,随着加工零件要求的不断提高,机床上的加工工具、工艺方法、工艺装备以及检测、控制方法等也在不断发生革新,促使机床结构及控制系统不断改进和发展。
在机械制造业中,在卧式车床(如CA6140上车削外圆是最基本,最普通的一种加工形式。
车削外圆的常见问题及解决方法1
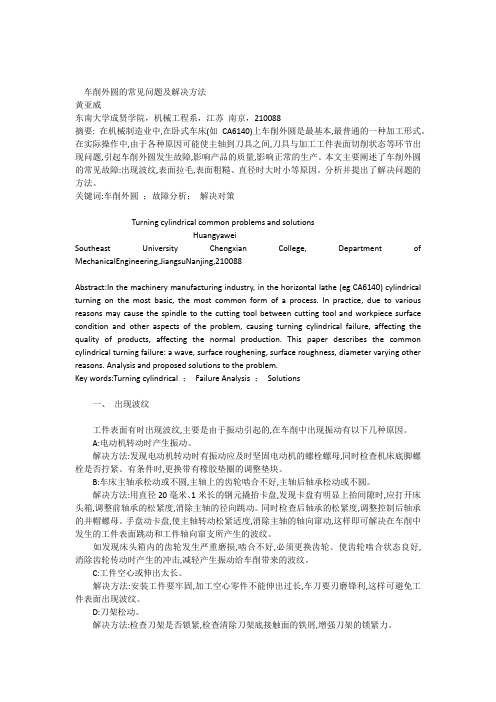
车削外圆的常见问题及解决方法黄亚威东南大学成贤学院,机械工程系,江苏南京,210088摘要: 在机械制造业中,在卧式车床(如CA6140)上车削外圆是最基本,最普通的一种加工形式。
在实际操作中,由于各种原因可能使主轴到刀具之间,刀具与加工工件表面切削状态等环节出现问题,引起车削外圆发生故障,影响产品的质量,影响正常的生产。
本文主要阐述了车削外圆的常见故障:出现波纹,表面拉毛,表面粗糙、直径时大时小等原因。
分析并提出了解决问题的方法。
关键词:车削外圆;故障分析;解决对策Turning cylindrical common problems and solutionsHuangyaweiSoutheast University Chengxian College, Department of MechanicalEngineering,JiangsuNanjing,210088Abstract:In the machinery manufacturing industry, in the horizontal lathe (eg CA6140) cylindrical turning on the most basic, the most common form of a process. In practice, due to various reasons may cause the spindle to the cutting tool between cutting tool and workpiece surface condition and other aspects of the problem, causing turning cylindrical failure, affecting the quality of products, affecting the normal production. This paper describes the common cylindrical turning failure: a wave, surface roughening, surface roughness, diameter varying other reasons. Analysis and proposed solutions to the problem.Key words:Turning cylindrical ;Failure Analysis ;Solutions一、出现波纹工件表面有时出现波纹,主要是由于振动引起的,在车削中出现振动有以下几种原因。
外圆磨床磨削圆跳动超差的原因分析及维修

第5期(总第216期)2019年10月机械工程与自动化M E C HA N I C A L ㊀E N G I N E E R I N G㊀&㊀A U T OMA T I O NN o .5O c t .文章编号:1672G6413(2019)05G0174G02外圆磨床磨削圆跳动超差的原因分析及维修谭东升(太原重工轨道交通设备有限公司,山西㊀太原㊀030032)摘要:针对D A N O B A T 数控外圆磨床磨削过程中外圆表面跳动超差的问题,通过对磨削过程的现象和机床内部结构的分析㊁检查,对其进行了故障诊断和维修.在拆装和维修过程中,了解了主轴的机械结构㊁工作原理及轴承装配要求,为今后使用和维护设备提供了宝贵的资料.关键词:跳动超差;轴承装配;外圆磨床;磨削中图分类号:T G 581+1㊀㊀㊀文献标识码:A收稿日期:2019G05G24;修订日期:2019G08G03作者简介:谭东升(1990G),男,甘肃兰州人,助理工程师,本科,主要从事机械设备管理和维护工作.1㊀问题提出某公司有一台西班牙D A N O B A T 数控外圆磨床,型号为H G G91G3000G2A 2R ,带3轴数控倾角砂轮头架,西门子840DS L 控制.其主要结构特点是:①采用带静压轴承的双砂轮主轴;②主轴头架为装有活顶尖的带高精度角度滚柱轴承的主轴;③尾座为自动润滑套筒液压驱动,装有死顶尖.磨削某铁路车轴产品,外圆表面磨削尺寸要求184.15ʃ0.025m m ,圆柱度公差要求不大于0.02m m ,两径向圆跳动公差不大于0.015m m .外圆磨床按工艺要求进行磨削,检验外圆表面圆跳动公差值规律变化,最大处0.05m m ,不满足图纸要求.通过观察发现:在砂轮与工件刚接触且轴向和径向均不进刀的情况下火花时有时无;其次,磨削车轴不同部位,尤其是靠近头架方向上跳动加剧.2㊀故障原因分析2.1㊀初步分析和检测对磨削过程进行分析,考虑主要原因可能为:①车轴顶尖孔加工精度超差;②设计为均布三拨叉结构的拨盘,操作工只使用双拨叉而导致工件旋转摆动;③工件头架主轴前㊁后轴承间隙较大,运转过程中存在有不规律的径向跳动.对以上的故障原因进行检测和判断:①车轴重新修正顶尖孔后,磨削结果依然存在圆跳动超差现象;②恢复拨盘120ʎ分布的三拨叉结构,工件磨削精度稍有改善,可确定拨叉分布对加工精度有影响但不是主因;③拆除头架主轴拨盘装置,在夹持工件状态下检测头架主轴顶尖径向跳动,千分表指针规律变化,顶尖锥端和锥尾最大跳动值分别为0.015m m 和0.010m m ,拆除顶尖后,检测头架主轴的外锥面㊁内锥面的径向跳动及前端面旋转轴向跳动分别为0.010m m ㊁0.008m m ㊁0.007m m ,皆超出设备精度允差.综上可初步判定,头架主轴的跳动是造成磨削外圆面跳动超差的主要原因.2.2㊀头架主轴结构分析从头架主轴结构(见图1)来看,主要包括前端回转密封环㊁轴承前端盖(加防尘圈)㊁轴承后端盖(加防尘圈)㊁主轴旋转芯轴.其头架主轴旋转芯轴轴承采用英国G AM E T 超精密轴承的典型结构:前轴承为双列H 型结构(见图2(a)),其外环是一个加大宽度的外圈带法兰边的整体,作轴向定位,两轴承内环孔径和外环直径尺寸不一致,后内环孔径比前内环孔径大几微米,后外环直径比前外环直径小几微米,其作用主要是利用后内环受热膨胀的轴向移动量来调整轴承前㊁后环与外环滚道的工作状态,故轴承装配时与箱体孔的配合采用间隙配合,以便于轴承前㊁后支承中心的自动调准,也有利于轴承的装配和拆卸;用作后支承的为P型单列轴承(见图2(b)),外环前部环体内可安装最多24只小弹簧,通过对称地增加和减少弹簧的数量,能方便地改变轴承组预加负荷的大小,其轴承外环与箱体孔的配合亦采用间隙配合方式[1].图1㊀头架主轴结构图2㊀G AM E T 轴承结构示意图通过对主轴结构和轴承结构的分析可知,主轴旋转精度的好坏,关键在于H 型双列轴承轴向游隙的取值和P 型轴承预加载荷量的大小.G A M E T 轴承组结构中,预加载荷是通过主轴装入头架壳体后调整后轴承的弹簧预紧载荷,从而使前㊁后轴承同时预紧.前H 型轴承装配时,为使轴承处于最佳工作状态,预加载荷为零,且内环和外环之间预留有一定的轴向游隙.此值大小视主轴的最高转速值而定.最高转速值越高,预留轴向游隙值越大[2].在头架主轴(D A N O B A T 主轴转速为1r /m i n ~300r /m i n ,工作常用转速为20r /m i n~50r /m i n ,轴向游隙为0.002m m )中轴承的轴向游隙是通过在两内环(B 内环为后内环,A 内环为前内环)之间增加隔垫C 来保证(如图3所示).轴承使用一段时间后,可适当减少隔垫C 的厚度,对前轴承本身进行预紧,以调整因磨损而增加的轴向游隙量.P 型轴承是利用弹簧作轴向调整,使前㊁后轴承同时预紧.因此,弹簧的轴向压缩量决定了轴承预加载荷的大小.只要能准确地测量㊁计算出预载弹簧的轴向压缩量,便可知轴承的预加载荷.测量计算方法如下:根据测算出的弹簧与外环端面的高度差值H ,对后轴承进行轴向加载.加载时要缓慢进行,并且分载荷或档次随时测量并记录高度变化值ΔH 和加载力F的大小(见图4),这样就得到了轴承的预加载荷与弹簧压缩量对照表.在装配时,按照需要的载荷调整轴承弹簧的压缩量,就能得到对应的预加载荷.图3㊀H 型轴承装配示意图图4㊀P 型轴承载荷测算2.3㊀原因判定根据以上分析,解体头架主轴检查(注意严禁敲击,须做专用工装拆解)发现:①前端壳体底部排水槽被磨泥堵塞;②回转密封内表面有磨损;③轴承润滑脂污染失效,轴承滚道和滚子磨损.由此可判定故障的主要原因是:前端壳体内的排水孔被日常使用过程中磨削所带入主轴的磨泥堵塞,以致冷却液和磨泥排出受阻而进入轴承,致使轴承损伤,轴向游隙增大,最终导致头架主轴的内㊁外锥面的径向跳动及前端面旋转轴向跳动超差.3㊀解决问题(1)安装前准备.用煤油彻底清洗头架主轴㊁箱体内孔以及主轴附属零部件,用百洁布抛光冷却液锈蚀点,表面涂一层防锈油.(2)轴承装配和调整.G AM E T 双列H 型轴承的内㊁外环端面上标有不同字母,用来保证轴承准确地安装在主轴上.其主轴转速较低,采用油脂润滑,使轴承内圈感应加热至60ħ就可满足安装需求.装配时,把标有字母 A 的轴承内环感应加热至60ħ,滑装在主轴上,然后装上隔圈,再把轴承外环(法兰边朝向推入方向)推入.接着,用同样办法将标有字母 B 的内环感应加热到50ħ,然后滑装到主轴上.完成上述装配工作后,用锁紧丝圈将内环与隔圈压紧(锁紧丝圈时需使用专用钩型扳手,严禁敲击),压紧的同时应轻轻转动轴承外环.最后,添加润滑脂.但必须注意油脂不应封堵所有轴承空间(最多占1/2空间),以免过度发热和过多渗出外部.前轴承装配完毕后,将后轴承外环装入头架箱体后孔.装后轴承外环时,应注意12只预紧弹簧需均布,箱体孔内轴承弹簧垫圈与轴承外环端面的间隙均匀.上述工作完成后,将头架箱体倒立㊁架空,将主轴从上往下垂直装入箱体(由于采用间隙配合,调正后主轴靠自重滑入箱体).最后,将后轴承内环感应加热到40ħ后从底部滑装到主轴上.用锁紧丝圈把内环锁入至预紧弹簧刚受力,锁紧的同时应轻轻转动主轴,以防主轴不正,滚子大端面卡死,导致整个轴承损坏.翻转头架箱体至水平状态,按照测定的P 型预加载荷与弹簧压缩量对照表,用专用钩型扳手锁紧丝圈至选取的预紧载荷位置,锁紧的同时轻轻转动主轴.(3)轴承跑合试验.G A M E T 轴承采用脂润滑时,必须进行空运转,以使配合面磨合(滚道㊁滚子表面)到最佳配合状态,既保证润滑脂的均匀分布,又检查调整不适当的配合,防止过热损坏轴承的事件发生.理想的跑合方法是在加载轴向力(一般在其1/3轴向载荷)和在轴承最大允许转速的1/10条件下分别进行正反向定时运转,然后改变轴向负荷的方向,再重复上述旋转.由于主轴转速限制,跑合方式采用另一种方式进行:总装后,先以1/10最高转速运行10h,停机,冷到自然状态,再提高一倍(1/5最高转速),再运行10h.(4)轴承配合安装完毕后,检测头架主轴的外锥面㊁内锥面的径向跳动及前端面旋转轴向跳动分别为0.004m m ㊁0.003m m ㊁0.004m m ,恢复到设备精度允差值.试加工工件,加工后产品表面质量满足要求.4㊀结语经过这次问题分析及维修,不仅了解了头架主轴的机械结构㊁工作原理及轴承装配要求,也从中发现了引起该故障的主要原因在于设备日常维护不到位.因此,像此类在设备说明书中未提及的维护部位,在设备投产及使用过程中,技术人员应详细了解设备结构和工作原理,尽可能地发现这类看似很简单却对设备精度乃至整体寿命有巨大影响的部位,做好日常维护和检修工作.参考文献:[1]㊀佚名.使你的机器达到世界等级的G a m e t 超高精度轴承[J ].机电信息,2001(9):94.[2]㊀张宏渊.G AM E T轴承及其在卧式坐标镗床上的应用[J ].装备机械,1986(1):34G37,18.C a u s eA n a l y s i s a n dM a i n t e n a n c e o fO u t o fT o l e r a n c e o fG r i n d i n g Ci r c l e R u n GO u t o fE x t e r n a l C y l i n d r i c a lG r i n d i n g Ma c h i n e T A ND o n g Gs h e n g(T a i y u a nH e a v y I n d u s t r y R a i l w a y T r a n s i tE q u i p m e n tC o .,L t d ,T a i yu a n030032,C h i n a )A b s t r a c t :I n v i e wo f t h e p r o b l e mt h a t t h e o u t e r s u r f a c e r u n Go u t o f t h eD A N O B A T C N Cc y l i n d r i c a l g r i n d i n g ma c h i n e i s o u t o f t o l e r a n c e ,t h e f a u l t d i a g n o s i s a n dm a i n t e n a n c e a r e c a r r i e d o u tb y a n a l y z i n g a n dc h e c k i n g t h e p h e n o m e n o n o f t h e g r i nd i n g pr o c e s s a n d t h e i n t e r n a l s t r u c t u r e o f t h em a c h i n e .D u r i n g t h e d i s a s s e m b l y a n d r e p a i r p r o c e s s ,t h em e c h a n i c a l s t r u c t u r e ,w o r k i n gp r i n c i p l e a n db e a r i n g a s s e m b l y r e qu i r e m e n t s o f t h e s p i n d l ew e r e u n d e r s t o o d ,w h i c h p r o v i d e d v a l u a b l e i n f o r m a t i o n f o r t h e f u t u r e u s e a n dm a i n t e n a n c e o f t h e e q u i pm e n t .K e y wo r d s :r u n Go u t o u t o f t o l e r a n c e ;b e a r i n g a s s e m b l y ;e x t e r n a l c y l i n d r i c a l g r i n d i n g m a c h i n e ;g r i n d i n g571 ㊀2019年第5期㊀㊀㊀㊀㊀㊀㊀㊀㊀谭东升:外圆磨床磨削圆跳动超差的原因分析及维修。
石墨材料零件外圆磨削难点及解决方法
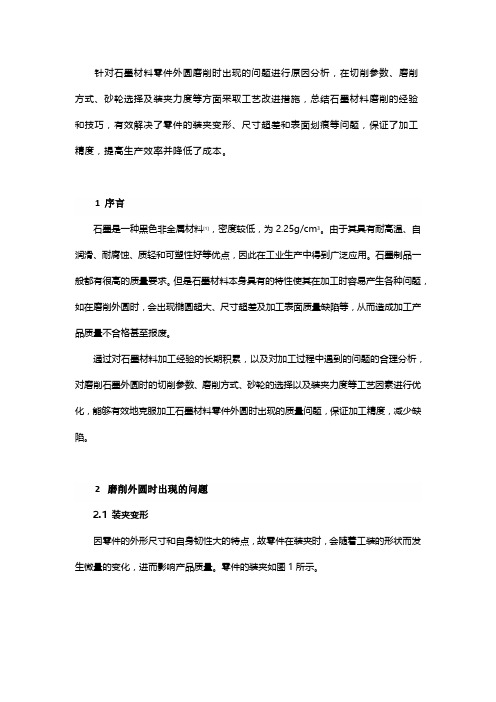
针对石墨材料零件外圆磨削时出现的问题进行原因分析,在切削参数、磨削方式、砂轮选择及装夹力度等方面采取工艺改进措施,总结石墨材料磨削的经验和技巧,有效解决了零件的装夹变形、尺寸超差和表面划痕等问题,保证了加工精度,提高生产效率并降低了成本。
1 序言石墨是一种黑色非金属材料[1],密度较低,为2.25g/cm3。
由于其具有耐高温、自润滑、耐腐蚀、质轻和可塑性好等优点,因此在工业生产中得到广泛应用。
石墨制品一般都有很高的质量要求。
但是石墨材料本身具有的特性使其在加工时容易产生各种问题,如在磨削外圆时,会出现椭圆超大、尺寸超差及加工表面质量缺陷等,从而造成加工产品质量不合格甚至报废。
通过对石墨材料加工经验的长期积累,以及对加工过程中遇到的问题的合理分析,对磨削石墨外圆时的切削参数、磨削方式、砂轮的选择以及装夹力度等工艺因素进行优化,能够有效地克服加工石墨材料零件外圆时出现的质量问题,保证加工精度,减少缺陷。
2 磨削外圆时出现的问题2.1 装夹变形因零件的外形尺寸和自身韧性大的特点,故零件在装夹时,会随着工装的形状而发生微量的变化,进而影响产品质量。
零件的装夹如图1所示。
图1 零件的装夹(1)影响零件的圆度和同轴度同轴度的两个加工基准是内孔与心轴,零件内孔与小锥度心轴过盈配合,心轴的磨损或顶尖与中心孔接触不良可能会引起跳动超差。
上一道工序的内孔采用车床加工,有装夹变形的情况发生,可能造成内孔呈椭圆状,从而影响外圆的加工精度。
(2)影响零件的尺寸石墨材料具有很大的韧性,当石墨零件装夹在心轴上时,由于心轴有锥度,因此零件会被心轴撑大,从而产生变形,进而使零件实际尺寸偏小,造成超差。
2.2 零件表面产生各种缺陷石墨材料零件在磨削过程中,由于质地较软[2],会受到砂轮颗粒和磨削方式等因素的影响,使零件表面产生各种缺陷:①多角形缺陷。
在零件表面沿轴线方向存在一条条等距的直线痕迹。
②螺旋形缺陷。
磨削表面呈现一条螺旋痕迹。
- 1、下载文档前请自行甄别文档内容的完整性,平台不提供额外的编辑、内容补充、找答案等附加服务。
- 2、"仅部分预览"的文档,不可在线预览部分如存在完整性等问题,可反馈申请退款(可完整预览的文档不适用该条件!)。
- 3、如文档侵犯您的权益,请联系客服反馈,我们会尽快为您处理(人工客服工作时间:9:00-18:30)。
外圆磨削质量缺陷原因分析与排除措施
摘要:在外圆磨削加工过程中,在工件表面经常会产生各种各样的表面缺陷,常见的如表面存在波纹、表面划伤、烧伤、鱼鳞状痕迹等。
为了保证磨削的质量,不仅要保证磨床有较高的加工精度,还要保证砂轮有较好的磨削性能。
我们从检查的角度对外圆磨削这些质量缺陷,进行分析并给出相应的解决措施。
关键词:外圆磨削质量缺陷原因分析
1.表面波纹缺陷
在磨削加工的过程中,工件表面或多或少的都会留下一些加工波纹,表面的波纹是磨削加工过程中最常见的缺陷,形成表面波纹的原因是由于磨削过程中,磨床存在机械的振动,使砂轮在磨削工件时,与工件表面的接触力不能保证时刻一致,从而在工件的表面会留下不同的加工痕迹,由于振动的随机性,因此会产生不同的波纹。
常见的有直线的条纹、多边形波纹、鱼鳞斑纹和斜纹、螺纹线等。
(1)直线条纹产生原因及排除措施
直线条纹的产生主要原因是由于磨削系统中存在的各种振动:①、由于砂轮的不平衡,在转动过程中产生的振动。
排除的方法:主要是在使用的过程中,保证砂轮的平衡质量,砂轮使用一段时间后,要对砂轮重新进行平衡性调整。
②、由于砂轮自身的硬度不均匀,在磨削的过程中引起振动。
排除方法:检查砂轮表面的硬度是否满足工艺的要求,如果硬度过高要更换硬度较软些的砂轮。
③、砂轮的修整量过大,或者是修整量不够。
排除的方法:对砂轮要进行合理的修整,修整量过大或不足同样会对工件的表面产生影响,根据要加工的工件进行合理的修整。
④、电机的振动引起的加工过程中砂轮的振动。
排除方法:电机要固定平衡,或者采用相应的隔振装置,如通过弹性零件吸收振动,消除电机的振动对磨削加工的影响。
⑤、砂轮的主轴与轴承这间的间隙过大,使砂轮在旋转时产生径向的跳动。
排除的方法:检查砂轮主轴与轴承间的间隙,按要求正确调整间隙。
(2)多边形波纹产生的原因及排除措施
①、由于工件细长,在磨削过程中,工件由于刚性不足,产生振动。
排除的方法:在工件中间增加支撑架,提高支承的刚性,同时稍微降低进给量和进给速度。
②、工件在旋转过程中不平衡,造成砂轮与工件的接触力的变化。
排除的方法:在工件的夹具上增加配重,以改善工件旋转过程中的平衡性,同时适当的降低工件的转速。
③、工件顶的过紧或过松,也会使磨削时砂轮与工件的接触力发生变化,产生多边形波纹。
排除的方法:调整工件的顶紧力,保证工件轴向推动不出现窜动,检查压紧弹簧的压力是否符合要求。
④、工件与支撑架未经磨合,在工件旋转过程中产生振动。
排除方法:提高要提高顶尖孔的质量,或者在工件与支撑架之间增加润滑。
⑤、顶尖孔有多边形,工件在旋转的过程中会沿着多边形轮廓滑动,从而在工件表面产生多边形波纹。
排除的方法:检查顶尖孔的质量,保证一定的圆周度,提高顶尖孔的加工质量。
(3)鱼鳞波纹和斜纹产生原因及排除措施
①、砂轮修整量不合适,并且表面不平滑。
排除方法:对砂轮重新进行修整,并且保证表面光滑。
②、砂轮的表面硬度不均匀,造成对工件的磨损不均匀,形成鱼鳞波纹。
排除方法:更换新的砂轮,保证砂轮表面硬度均匀。
或者对砂轮进行多次修整,使表面硬度达到均匀。
③、磨削液造成砂轮表面污染,从而影响磨削工件的表面质量。
排除方法:更换符合要求的磨削液,或者是对砂轮的表面清理,除去污染。
④、砂轮主轴轴向窜动,使磨削过程中,砂轮的轴向速度发生变化,对工件表面质量产生影响。
排除方法:严格控制砂轮的主轴只有旋转的自由度,调整止推轴承,保证砂轮的旋转精度。
(4)螺纹线产生原因及排除方法
①、由于在纵向磨削时,砂轮没有倒角,从而形成螺纹线。
排除方法:对砂轮增加倒角。
②、磨削加工的进给量大及进给的速度过快,在工件表面出现螺纹线。
排除方法:按照加工工艺的要求,对进给量及进给的速度进行调整。
③、砂轮主轴与工件轴线不平行,使砂轮不是整个面与工件接触,
在工件表面留下螺纹线。
排除方法:修整砂轮主轴,使主轴与工件轴线平行。
2.工件外形存在的缺陷
工件在磨削过程中,可能由于装夹或者砂轮质量的原因,磨削后的工件会存在外形上的一些缺陷,常见的如工件不圆、工件有锥度、工件弯曲变形、工件呈鼓形。
(1)工件不圆的原因及排除方法:
①、顶尖孔的形状不符合要求,造成工件不圆。
排除方法:对顶尖孔进行修圆处理,必要时还要对顶尖孔进行润滑。
②、顶尖已经磨损而未及时更换。
排除方法:要经常检查顶尖是的磨损程度,磨损严重时要及时更换。
③、中心架支承刚性差,或出现松动。
排除方法:提高支承的刚性,及时检查中心架是否松动,出现松动要及时的调整。
④、工件装夹不平衡,在旋转的过程中出现转速不均匀的现象。
排除方法:按照工艺要求,对工件合理装夹,降低工件旋转的速度。
⑤、由于工件的刚性较差,磨削过程中的变形量大。
排除方法:在磨削前对工件要先进行校直,消除因刚性差的原因带来的加工影响。
(2)工件有锥度的原因及排除方法
①、由于工件的轴线与工作台不平行,使工件的磨削量不一致。
排除方法:在磨削前要先对工作台进行调整,使工件轴线与工作台平行。
②、砂轮的母线方向与工件的轴线方向不平行,造成工件有锥度。
排除方法:调整砂轮修整器,按着锥度的方向进行调整。
③、机床自身的热变形导致工件有锥度。
排除方法:降低机床自身的热变形,适当降低进给量。
(3)工件弯曲变形的原因及排除方法
①、由于磨削深度大或者径向进给的速度过快,对工件的压力很大,使工件弯曲变形,排除方法:降低磨削的深度及径向进给的速度。
②、对于较长的工件没有采用中心架,或者是中心架的位置调整的不合适。
排除方法:对于刚性差的细长工件要采用中心架增加支承的刚性,中心架的位置要合理调整。
(4)工件呈鼓形的原因及排除方法
①、工件自身的刚性差,磨削过程产生弹性变形。
排除方法:减小磨削的深度,增加中心架以提高其刚性。
②、中心架调整不当,造成工件呈鼓形。
排除方法:固定中心架的支承中心应当与工件的轴线重合。
以上就是对外圆磨削常见的一些表面质量缺陷及外形的缺陷进
行分析并给出相应的排除措施,保证合理的磨削用量,合理的选择和修整砂轮,合理选择冷液对消除外圆磨削缺陷起到至关重要的作用。