影响机床部件刚度的因素
影响机械加工精度因素与降低加工误差的措施
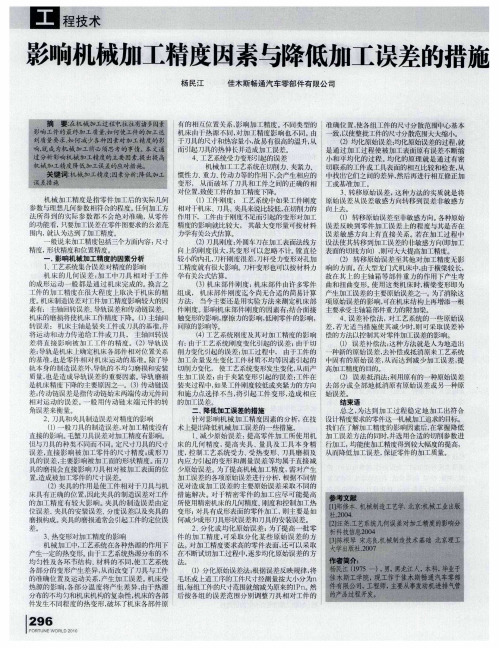
一
法。
( 分化原始误差法: 1 ) 根据误差反映规律 , 将 毛坯或上道工序的工件尺寸经测量按大 小分为n 『 组, 每组工件的尺寸范 围就缩减 为原来的I n 然 P 。 后按各 组的误差 范围分别调整刀具 相对工件的 f
机 械加工精度是指零 件加 工后的实际几何 参数与理想几何参数相符合的程度。 任何加工方 法所 得到的实 际参数都 不会绝 对准确 , 从零件
的功能看, 只要 加 工误 差 在零 件 图要 求 的 公差 范
围内, 就认为达到 了 加工精度。 般说来加工精 度包括三个方面内容: 尺寸 精度, 形状精度和位置精度 。 影响机械加工精度的因素分析 1 工艺系统集合误差对精度的影响 、 机 床的 几何 误 差: 加工中刀具 相对 于工件 的成形运 动一般 都是通 过机床 完成的。 换言之 工件的加工精度在很大程 度上取决于机 床的精 度。 机床制造误差对工件加工精度影响较大的因 素有:主轴回转误差、 导轨误差和传动链误差。 机床的磨损将使机床工作精度下降 。() 1 主轴 回 转误差: 机床主轴 是装夹工件或 刀具 的基准 , 并 将运动 和动 力传递 给 【 件或 刀具 , 主轴 同转误 差将 直接影 响被 加 』 。件 的精度。( )导轨误 =I : 2 差: 导轨是机床上确定机 床各部 件相对位置关系 的基准 , 也是零件 相对机床运 动的基准 。 除了导 轨本身的制造误差外, 的不均 匀磨损和安装 导轨 质量, 也是造 成导轨 误差的重要因素。 导轨 磨损 是机床精度下降的主要原因之一。() 3 传动链误 差: 传动链误差是指 传动链始末两端传动元件间 相对运 动的误差 。 一般 用传动链 末端元件 的转 角误差来衡量。 2 刀具和夹具制造误差对精度的影 响 、 ( 一般 刀 的制造误 差, 工精度没有 1 ) 具 对加 直接的影 响。 毛蟹 刀具误 差对加工精度有影响。 但与刀具的种类不同而不同。 定尺寸刀具 的尺寸 误差 , 直接影 响被加 工零件的尺寸精度 ; 成形 刀 具的误 差, 主要影 响被加 工面的形状精 度。 刀 而 具的磨损会直接影 响刀具 相对波加 工表面的位 置, 造成被加工零件的尺寸误差。 () 2 夹具的作用是使工件相对于 刀具与机 床具有正确的位置, 夹具 的制造误 差对工件 因此 的加工 精度 有较大 影响 。 夹具 的制造误 差由定 位误差、 夹具的安装误差、 分度误差以及夹具的 磨损构成 。 夹具 的磨损通常会引起工件 的定位误
影响机械加工精度的几个重要因素
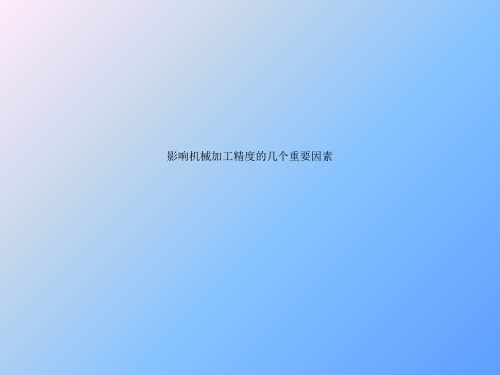
误差复映系数:加工前后误差之比值,称
为误差复映系数,它代表误差复映的程度。
分析式(4-11)可知ε与
k
成反比;
系
这表明工艺系统刚度愈大,误差复映系数愈小,
加工后复映到工件上的误差值就愈小。
尺寸误差和形位误差都存在复映现象。如
果我们知道某加工工序的复映系数,就可以通
过测量待加工表面的误差统计值来估算加工后
三、工艺系统受力变形引起的误差 (一)工艺系统刚度 图 1.工艺系统刚度 机械加工中,工艺系统在切削力、夹紧
力、传动力、惯性力和重力等的作用下,将 产生相应变形, 使工件产生加工误差。工艺系 统在外力作用下产生变形的大小,不仅取决 于作用力的大小,还取决于工艺系统的刚度。
垂直作用于工件加工表面的背向力与工
四、工艺系统受热变形引起的误差 工艺系统在热作用下产生的局部变形,
会破坏刀具与工件的正确位置关系,使工件 产生加工误差。热变形对加工精度影响较大, 特别是在精密加工和大件加工中,热变形所 引起的加工误差通常会占到工件加工总误差 的40%-70%。随着高精度、高效率及自动 化加工技术的发展,工艺系统热变形问题日 益突出。
不同而不同。采用定尺寸刀具(例如钻头、铰 刀、键槽铣刀、圆拉刀等)加工时,刀具的尺 寸误差和磨损将直接影响工件尺寸精度。采用 成形刀具(例如成形车刀、成形铣刀、齿轮模 数铣刀、成形砂轮等)加工时,刀具的形状误 差和磨损将直接影响工件的形状精度。对于一 般刀具(例如车刀、健刀、铣刀等),其制造 误差对工件加工精度无直接影响。
薄弱环节的刚度。
2.机床刚度 机床结构较为复杂,它由许多零、部件 组成,其刚度值迄今尚无合适的简易计算方 法,目前主要还是用实验方法进行测定。
测得机床部件刚度 k 主轴 、k 尾座 、k 刀架
数控机床精度影响原因及改进措施

数控机床精度影响原因及改进措施作者:张厚来来源:《市场周刊·市场版》2020年第05期摘要:首先,文章提出了影响数控机床精度的原因,其次,并对各影响原因提出对应的改进措施和改善方向,对数控机床结构设计和机床使用稳定性的维护有一定的参考意义。
关键词:机床精度;机床结构;动态响应一、对数控机床加工精度的影响原因主要包括如下几个方面(一)变形包括由于本身结构不合理等因素导致的弹性变形和机床运转过程中的发热传递给机床造成的变形,热变形是影响机床加工精度的最主要因素,最高可达机床总加工误差的70%。
(二)间隙由于制造和装配误差、弹性变形以及磨损都会产生间隙,间隙会造成定位精度变差和响应滞后,在闭环系统中会造成系统超调,产生振荡制造。
(三)磨损包括局部磨损、正常使用磨损本来就不可避免,只能通过措施减少磨损带来的影响。
一般机械设备中约有80%的零件因磨损而失效报废,材料、装配、变形、润滑不好等情况均会导致磨损加剧,从而造成设备精度丧失。
(四)动态响应是所有机械结构和机床状况的最终反映,决定了机床的加工精度和稳定性。
且受温度、润滑情况、加工负载等情况的影响比较大。
二、针对以上导致机床精度变差甚至丧失的情况,可以有针对性的采用一定的措施来提高机床的精度(一)变形:通过机床结构的合理布局和优化,减少变形的产生1. 合理布局以镗铣床为例,针对不同加工零件的要求采用不同的床身布局结构。
工作台有十字形布局和T形床身布局,其中T形布局的工作台与床身分离,刚性好,承载能力强适用于较重的零件。
对于主轴箱悬挂于立柱对于精度要求高的机床一般采用框式立柱,避免采用單侧悬挂。
框式立柱结构对称,受力和温度变化的变形小,有利于提高加工精度。
其他类型的机床如卧车尽量采用斜床身结构,不仅结构稳定且有利于排屑排水。
对于大型重型零件的铣削加工多采用天车式龙门结构,结构稳定精度高。
2. 优化结构对于立柱、横梁、床身、底座等采用变形小热稳定性好的铸铁作为材料,内部合理布置隔板和筋条,减小应力变形的同时又能提高刚性,且内空的结构易于散热,一些精度要求特别高的场合内部可增加强制冷却,进一步减小热变形。
分析机械设备装配精度的影响因素和控制措施

分析机械设备装配精度的影响因素和控制措施一、设备装配精度机械设备装配就是将一系列全部合格的零部件、设备组装成具有肯定生产力量的技术装备或生产线系统。
产品装配完成后需要进行各种检验和试验,以确保其装配质量和使用性能。
为了使机械设备具有正常工作性能,必需保证其装配精度。
设备装配精度包含各独立设备之间所需正确联动的位置精度、单台设备重现的制造精度和整台设备在使用中的运行精度。
二、设备安装协作精度的影响因素设备在装配时受到的精度影响因素不是单一的,应从多方面因素综合考虑和分析。
下面重点介绍了八种影响因素。
(一)基础的影响设备基础存在强度不够、沉降不匀称和抗振性能不足等一些缺陷对安装精度存在严峻的影响。
设备找平、找正、找标高及安装检验合格后,若基础强度不足、连续下沉,安装会存在偏差,造成设备安装精度降低。
因此,设备安装前,应检查和测试基础强度是否符合设计要求,应观测基础沉降是否稳定,确定都合格后作最终设备调整和固定安装。
设备运行过程中可能会产生较大的动载荷或冲击载荷,若设备基础抗振性能不足,也会影响设备安装精度。
(二)灌浆和垫铁的影响在垫铁和二次灌浆层上安装设备。
若垫铁本身的质量(表面不平整、有毛刺,尺寸误差大)、垫铁的接触质量(垫铁不平稳、接触不好,未焊牢)、二次灌浆质量(不密实、强度达不到)存在一些问题,会严峻影响设备装配精度。
应严格根据垫铁的设置和灌浆要求进行合理的施工和安装,使设备装配误差降到最低限度。
(三)地脚螺栓的影响地脚螺栓的位置、标高、垂直度和紧固力矩直接影响设备安装的质量。
有些设备(特殊是自动化程度高的联动设备)对标高、位置的精确性要求很严。
因此,必需在设备安装前,地脚螺栓埋设后对其进行检查和矫正。
当发生偏差时,应依据设备的详细状况采纳不同的处理方法。
地脚螺栓若安装不垂直,在浇灌混凝土时产生偏移,还可能产生局部间隙,造成设备与螺母的接触会倾斜不正,受力不均衡,影响设备的坚固安装固定;螺栓紧固力低于标准要求,装配连接存在松动,设备在工作运行中会产生振动和位移,造成设备安装精度降低。
影响机械零件加工精度的因素及改善对策论文

影响机械零件加工精度的因素及改善对策论文影响机械零件加工精度的因素及改善对策论文1 引言。
常用的衡量机械零件加工质量的指标包括加工精度和表面质量等数个方面,在实际的加工过程中,由于环境温度、工艺系统的几何误差、工件内应力重新分布引起的变形误差等因素的影响,导致加工工具和工件的正确位置可能会产生一定的程度的偏移,使得零件与理想情况下的定位位置存在差异,这种差异即会对零件的加工精度产生影响。
因此,为了在不增加制造成本的情况下,尽可能提升机械零件的加工精度,相关的工艺人员需要结合产品的具体设计要求和实际生产条件,采取诸如更换较高精度加工设备和工装夹具、制定合理的加工工艺、降低加工误差等一系列方式,以期在保证加工过程经济性的同时得到较高的加工精度。
2 主轴回转误差对机械零件加工精度的影响及改进措施。
2.1 主轴回转误差概述。
机床几何误差是整个机械零件加工中决定系统误差的主要因素,主轴回转误差和导轨误差均属于主轴回转误差。
在加工过程中,由于主轴部件中轴承、轴颈、轴承座孔等的制造误差和配合质量、润滑条件、以及回转时的动力因素的影响,往往瞬时回转轴线的空间位置都在周期性地变化,造成实际回转中心与理论回转中心不重合而产生回转误差。
如图 1 所示,主轴回转误差包括径向圆跳动、倾角摆动、端面圆跳动三种形式,常见的成因包括轴承本身系统误差、轴承间隙过大、各段轴颈、轴孔的同轴度误差、温度过高引起热变形等等。
2.2 对加工精度的影响。
根据影响主轴回转精度的因素不同,其对于工件加工精度往往也具有不同的影响,具体表现在以下几个方面:当机床主轴回转误差为径向圆跳动时,工件会产生圆度误差;当机床主轴回转误差为倾角摆动时,车削时工件径向截面仍然会呈一圆形,而轴向截面则是一梯形,镗孔时由于主轴的角度摆动形成的回转轴线与工作台导轨不平行,镗出的孔将为椭圆形。
当机床主轴回转误差为端面圆跳动时,虽然加工圆柱面的情况不会受到影响,但加工端面时,左右螺旋面可能会形成垂直度误差,被加工的端面与圆柱面也可能不垂直。
提高机床刚度的有效措施

提高机床刚度的有效措施
提高机床刚度是提高加工精度和工件表面质量的关键因素之一。
以下是一些有效的措施可
以提高机床的刚度:
1. 使用高刚性材料:选择高刚性的铸铁或钢材作为机床的结构材料,能够增加机床的整体刚度。
2. 加强机床结构设计:通过合理设计机床结构,增加机床的刚性。
例如,在承受力的部位增加
加强筋或支撑件,这样可以使机床更加坚固。
3. 增加机床的重量:增加机床的重量可以提高其刚度。
可采用增加床身或增加床身和工作台的
重量等方式。
4. 加强机床的支撑和固定:将机床牢固地固定在地面上,使用合适的支撑方式,避免机床在加
工过程中出现振动。
5. 提高导轨和传动系统的刚度:导轨是机床最关键的部件之一,选用高刚度的导轨和精密的传
动系统,可以有效提高整个机床的刚度。
6. 补偿机床变形:根据机床变形规律,采用合适的补偿方法,如预应力调整、补偿环技术等,
降低机床变形对刚度的影响。
7. 优化加工过程:通过合理的切削参数、工艺规程和工件夹持方式,减轻切削力对机床的影响,提高机床的稳定性和刚度。
总之,提高机床刚度需要多方面的措施综合应用,从材料、结构设计、支撑固定、导轨传动系
统和加工过程等方面入手,以达到提高机床刚度的目的。
机械制造工艺学课后习题及参考答案讲解学习
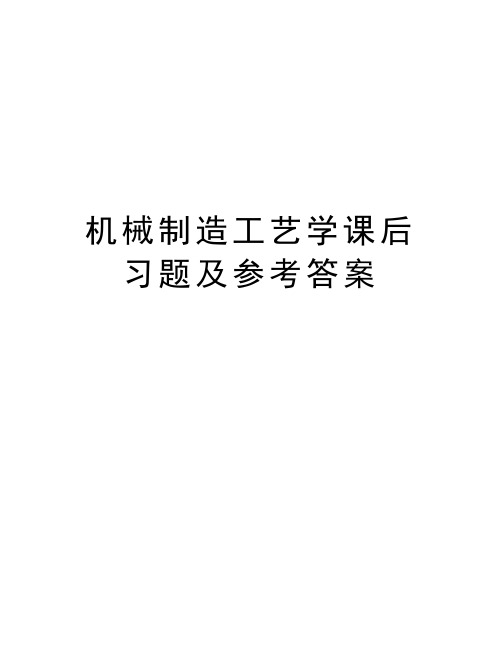
机械制造工艺学课后习题及参考答案机械制造工艺学复习题及参考答案第一章1.1什么叫生产过程、工艺过程、工艺规程?生产过程是指从原材料变为成品的劳动过程的总和。
在生产过程中凡属直接改变生产对象的形状、尺寸、性能及相对位置关系的过程,称为工艺过程。
在具体生产条件下,将最合理的或较合理的工艺过程,用文字按规定的表格形式写成的工艺文件,称为机械加工工艺规程,简称工艺规程。
1.2、某机床厂年产CA6140 卧式车床2000 台,已知机床主轴的备品率为15%,机械加工废品率为5%。
试计算主轴的年生产纲领,并说明属于何种生产类型,工艺过程有何特点?若一年工作日为280 天,试计算每月(按22 天计算)的生产批量。
解:生产纲领公式 N=Qn(1+α)(1+β)=(1+15%)(1+5%)=2415 台/年查表属于成批生产,生产批量计算:定位?各举例说明。
六点定位原理:在夹具中采用合理布置的6个定位支承点与工件的定位基准相接触,来限制工件的6个自由度,就称为六点定位原理。
完全定位:工件的6个自由度全部被限制而在夹具中占有完全确定的唯一位置,称为完全定位。
不完全定位:没有全部限制工件的6个自由度,但也能满足加工要求的定位,称为不完全定位。
欠定位:根据加工要求,工件必须限制的自由度没有达到全部限制的定位,称为欠定位。
过定位:工件在夹具中定位时,若几个定位支承重复限制同一个或几个自由度,称为过定位。
(d)一面两销定位,X,两个圆柱销重复限制,导致工件孔无法同时与两销配合,属过定位情况。
7、“工件在定位后夹紧前,在止推定位支承点的反方向上仍有移动的可能性,因此其位置不定”,这种说法是否正确?为什么?答:不正确,保证正确的定位时,一定要理解为工件的定位表面一定要与定位元件的定位表面相接触,只要相接触就会限制相应的自由度,使工件的位置得到确定,至于工件在支承点上未经夹紧的缘故。
8、根据六点定位原理,分析图中各工件需要限制哪些的自由度,指出工序基准,选择定位基准并用定位符号在图中表示出来。
CNC机床加工中的夹具刚度与变形分析
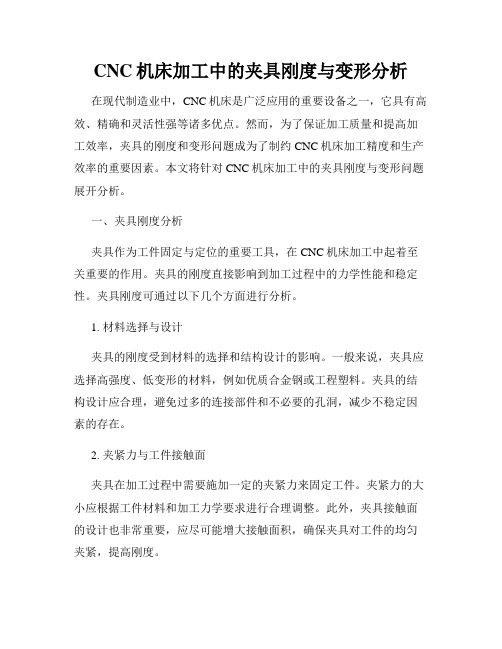
CNC机床加工中的夹具刚度与变形分析在现代制造业中,CNC机床是广泛应用的重要设备之一,它具有高效、精确和灵活性强等诸多优点。
然而,为了保证加工质量和提高加工效率,夹具的刚度和变形问题成为了制约CNC机床加工精度和生产效率的重要因素。
本文将针对CNC机床加工中的夹具刚度与变形问题展开分析。
一、夹具刚度分析夹具作为工件固定与定位的重要工具,在CNC机床加工中起着至关重要的作用。
夹具的刚度直接影响到加工过程中的力学性能和稳定性。
夹具刚度可通过以下几个方面进行分析。
1. 材料选择与设计夹具的刚度受到材料的选择和结构设计的影响。
一般来说,夹具应选择高强度、低变形的材料,例如优质合金钢或工程塑料。
夹具的结构设计应合理,避免过多的连接部件和不必要的孔洞,减少不稳定因素的存在。
2. 夹紧力与工件接触面夹具在加工过程中需要施加一定的夹紧力来固定工件。
夹紧力的大小应根据工件材料和加工力学要求进行合理调整。
此外,夹具接触面的设计也非常重要,应尽可能增大接触面积,确保夹具对工件的均匀夹紧,提高刚度。
3. 夹具支撑与加固夹具的刚度还与其支撑和加固方式有关。
夹具支撑部位应选择强度高、稳定性好的结构,避免在加工过程中产生振动和变形。
在必要的情况下,可以采用加固辅助支撑手段,提高夹具的整体刚度。
二、夹具变形分析夹具在加工过程中容易发生变形,这种变形可能会导致工件加工精度降低和尺寸偏差产生。
下面将从几个方面分析夹具的变形问题。
1. 刚性分析夹具的变形主要受到其自身刚度和荷载的影响。
荷载产生的内力和外力会使得夹具发生弯曲、扭转和拉伸等变形。
因此,夹具的刚性是解决这一问题的关键。
利用有限元分析等方法,可以评估夹具在不同荷载情况下的刚性表现,并在设计中作出相应的调整。
2. 热变形分析加工过程中,热量的积累和热膨胀会导致夹具产生热变形。
尤其是在高温环境下,夹具的热变形问题更加突出。
为解决这一问题,可以在夹具设计中引入冷却系统,及时降低夹具温度并减小热变形。
数控机床主轴的抗扭刚度分析

数控机床主轴的抗扭刚度分析1. 引言数控机床主轴是机床的核心部件之一,承担着传动力和工件加工的重要任务。
主轴的扭转刚度是其性能评价的关键指标之一。
本文将对数控机床主轴的抗扭刚度进行详细分析和探讨。
2. 数控机床主轴的结构和工作原理数控机床主轴一般由主轴轴承、主轴箱、主轴电机等部分组成。
其工作原理是通过主轴轴承和主轴箱中的传动装置将电机传来的动力转化为主轴的旋转动力,用于工件的加工。
3. 数控机床主轴的受力分析在机床加工过程中,主轴受到来自切削力和惯性力的作用。
切削力引起的扭矩会导致主轴发生弯曲变形,而惯性力则引起主轴的振动。
这些力对主轴的扭转刚度提出了很高的要求。
4. 数控机床主轴的抗扭刚度计算主轴的抗扭刚度可以通过有限元分析方法进行计算。
通过建立主轴的有限元模型,确定主轴材料的物理参数和边界条件,可以得到主轴在工作过程中的变形情况,并进而计算出主轴的抗扭刚度。
5. 影响数控机床主轴抗扭刚度的因素数控机床主轴抗扭刚度的大小受到多种因素的影响。
主要包括主轴箱的结构设计、主轴轴承的选型和装配精度、主轴的刚度设计等。
只有在这些因素都得到合理的处理和控制,才能确保数控机床主轴的抗扭刚度满足要求。
6. 提高数控机床主轴抗扭刚度的方法为了提高数控机床主轴的抗扭刚度,可以采取多种方法。
例如,选择合适的主轴轴承和材料,提高主轴箱的刚度和精度,合理设计主轴结构等。
这些方法都可以有效地提高数控机床主轴的抗扭刚度。
7. 数控机床主轴抗扭刚度的优化设计在数控机床主轴的设计过程中,应充分考虑主轴的抗扭刚度要求,并进行相应的优化设计。
通过使用优化设计方法,可以最大限度地提高数控机床主轴的抗扭刚度,提升机床的加工精度和效率。
8. 结论数控机床主轴的抗扭刚度是影响机床性能的重要指标之一。
通过对主轴受力分析、抗扭刚度计算和相关因素的分析,可以有效地提高数控机床主轴的抗扭刚度。
在数控机床主轴的设计中,优化设计方法的应用可以进一步提升主轴的性能和机床的加工效率。
机床刚度概念及部件刚度概念、特点
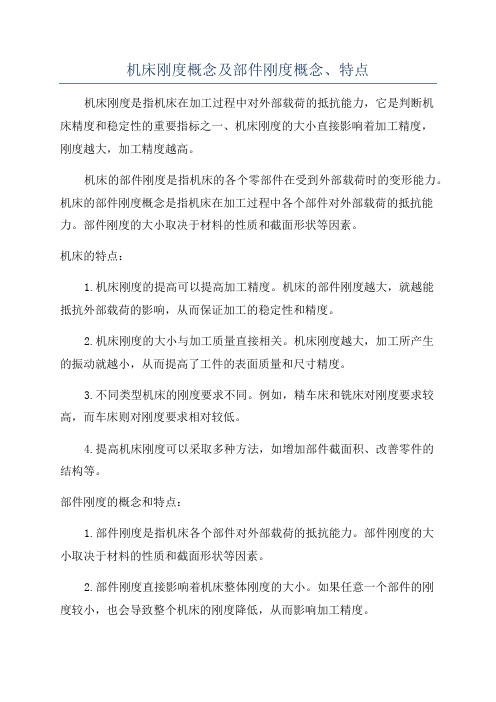
机床刚度概念及部件刚度概念、特点机床刚度是指机床在加工过程中对外部载荷的抵抗能力,它是判断机床精度和稳定性的重要指标之一、机床刚度的大小直接影响着加工精度,刚度越大,加工精度越高。
机床的部件刚度是指机床的各个零部件在受到外部载荷时的变形能力。
机床的部件刚度概念是指机床在加工过程中各个部件对外部载荷的抵抗能力。
部件刚度的大小取决于材料的性质和截面形状等因素。
机床的特点:1.机床刚度的提高可以提高加工精度。
机床的部件刚度越大,就越能抵抗外部载荷的影响,从而保证加工的稳定性和精度。
2.机床刚度的大小与加工质量直接相关。
机床刚度越大,加工所产生的振动就越小,从而提高了工件的表面质量和尺寸精度。
3.不同类型机床的刚度要求不同。
例如,精车床和铣床对刚度要求较高,而车床则对刚度要求相对较低。
4.提高机床刚度可以采取多种方法,如增加部件截面积、改善零件的结构等。
部件刚度的概念和特点:1.部件刚度是指机床各个部件对外部载荷的抵抗能力。
部件刚度的大小取决于材料的性质和截面形状等因素。
2.部件刚度直接影响着机床整体刚度的大小。
如果任意一个部件的刚度较小,也会导致整个机床的刚度降低,从而影响加工精度。
3.部件刚度的提高可以通过多种方式实现,如增加部件的截面积、采用合适的材料、改善零件结构等。
4.部件刚度的大小对部件的稳定性和寿命也有一定的影响。
刚度较大的部件能够更好地抵抗外部载荷的作用,从而延长部件的使用寿命。
总之,机床刚度和部件刚度对于机床加工的精度和稳定性具有重要的影响。
提高机床和部件的刚度可以提高加工的精度和质量,从而满足不同加工要求。
影响机械加工精度因素浅析

影响机械加工精度因素在机械加工过程中,往往有很多因素影响工件的最终加工质量,如何使工件的加工达到质量要求,如何减少各种因素对加工精度的影响,就成为加工前必须考虑的事情,也就是要对影响机械加工精度的因素进行分析。
一、集合误差1.机床的几何误差:加工中刀具相对于工件的成形运动一般都是通过机床完成的,因此,工件的加工精度在很大程度上取决于机床的精度。
机床制造误差对工件加工精度影响较大的有:主轴回转误差、导轨误差和传动链误差。
机床的磨损将使机床工作精度下降。
1) 主轴回转误差,机床主轴是装夹工件或刀具的基准,并将运动和动力传给工件或刀具,主轴回转误差将直接影响被加工工件的精度。
2) 导轨误差,导轨是中国论文联盟整理机床上确定各机床部件相对位置关系的基准,也是机床运动的基准。
除了导轨本身的制造误差外,导轨的不均匀磨损和安装质量,也使造成导轨误差的重要因素。
导轨磨损是机床精度下降的主要原因之一。
3) 传动链误差,传动链误差是指传动链始末两端传动元件间相对运动的误差。
一般用传动链末端元件的转角误差来衡量。
2.刀具的几何误差:刀具误差对加工精度的影响随刀具种类的不同而不同。
采用定尺寸刀具成形刀具展成刀具加工时,刀具的制造误差会直接影响工件的加工精度;而对一般刀具(如车刀等),其制造误差对工件加工精度无直接影响。
3.夹具的几何误差:夹具的作用时使工件相当于刀具和机床具有正确的位置,因此夹具的制造误差对工件的加工精度(特别是位置精度)有很大影响。
二、定位误差1.基准不重合误差:定位基准与设计基准不重合时所产生的基准不重合误差,只有在采用调整法加工时才会产生,在试切法加工中不会产生。
2.定位副制造不准确误差:工件在夹具中的正确位置是由夹具上的定位元件来确定的。
基准不重合误差的方向和定位副制造不准确误差的方向可能不相同,定位误差取为基准不重合误差和定位副制造不准确误差的矢量和。
三、工艺系统受力变形引起的误差1.基本概念:机械加工工艺系统在切削力、夹紧力、惯性力、重力、传动力等的作用下,会产生相应的变形,从而破坏了刀具和工件之间的正确的相对位置,使工件的加工精度下降。
机械加工容易出现的九大误差

机械加工容易出现的九大误差1、机床的制造误差机床的制造误差主要包括主轴回转误差、导轨误差和传动链误差。
主轴回转误差是指主轴各瞬间的实际回转轴线相对其平均回转轴线的变动量,它将直接影响被加工工件的精度。
主轴回转误差产生的主要原因有主轴的同轴度误差、轴承本身的误差、轴承之间的同轴度误差、主轴绕度等。
导轨是机床上确定各机床部件相对位置关系的基准,也是机床运动的基准。
导轨本身的制造误差、导轨的不均匀磨损和安装质量是造成导轨误差的重要因素。
传动链误差是指传动链始末两端传动元件间相对运动的误差。
它是由传动链中各组成环节的制造和装配误差,以及使用过程中的磨损所引起的。
2、刀具的几何误差任何刀具在切削过程中都不可避免要产生磨损,并由此引起工件尺寸和形状地改变。
刀具几何误差对机械加工误差的影响随刀具种类的不同而不同:采用定尺寸刀具加工时,刀具的制造误差会直接影响工件的加工精度;而对一般刀具(如车刀等),其制造误差对机械加工误差无直接影响。
3、夹具的几何误差夹具的作用是使工件相当于刀具和机床具有正确的位置,因此夹具的几何误差对机械加工误差(特别是位置误差)有很大影响。
4、定位误差定位误差主要包括基准不重合误差和定位副制造不准确误差。
在机床上对工件进行加工时,须选择工件上若干几何要素作为加工时的定位基准,如果所选用的定位基准与设计基准(在零件图上用来确定某一表面尺寸、位置所依据的基准)不重合,就会产生基准不重合误差。
工件定位面与夹具定位元件共同构成定位副,由于定位副制造得不准确和定位副间的配合间隙引起的工件最大位置变动量,称为定位副制造不准确误差。
定位副制造不准确误差只有在采用调整法加工时才会产生,在试切法加工中不会产生。
5、工艺系统受力变形产生的误差工件刚度:工艺系统中如果工件刚度相对于机床、刀具、夹具来说比较低,在切削力的作用下,工件由于刚度不足而引起的变形对机械加工误差的影响就比较大。
刀具刚度:外圆车刀在加工表面法线(y)方向上的刚度很大,其变形可以忽略不计。
滚珠螺母的刚度

滚珠螺母的刚度
滚珠螺母的刚度是指其在受到外力作用时,抵抗变形的能力。
这是一个重要的性能指标,直接影响到滚珠丝杠传动系统的精度和寿命。
在自动化设备、精密机械以及各种工业应用中,高刚度的滚珠螺母可以确保传动系统的稳定性和可靠性。
滚珠螺母刚度的影响因素
1.材料特性:滚珠螺母和螺杆的材料特性,包括弹性模量、屈服强度等,都会影响其刚度。
2.结构设计:滚珠螺母的结构设计,如螺纹形状、接触角度、预紧力的大小等,也会对刚度产生影响。
3.装配和预紧力:通过适当的装配和调整预紧力,可以提高滚珠螺母的接触刚度,从而提高整个系统的刚度。
4.负载和速度:工作负载和运行速度也会影响滚珠螺母的刚度表现。
在高速或高负载条件下,滚珠螺母可能会出现更大的弹性变形。
刚度的测量
滚珠螺母的刚度通常通过实验方法测量,即在规定的条件下,测量其在一定负载作用下的位移量。
刚度(K)可以表示为:
[K=\frac{F}{\Delta L}]
其中,(F)是作用在滚珠螺母上的外力,(\Delta L)是滚珠螺母的位移量。
提高刚度的方法
提高预紧力:适当增加预紧力可以有效提高滚珠螺母的刚度,但
过高的预紧力会增加摩擦和磨损,降低系统的寿命。
优化设计:通过优化滚珠螺母和螺杆的结构设计,如改善螺纹形状、增加接触面积等,可以提高刚度。
使用高刚度材料:选择具有高弹性模量的材料制造滚珠螺母和螺杆,可以直接提高刚度。
组合使用:在某些情况下,可以通过组合使用多个滚珠螺母来分散负载,从而提高整体的刚度。
总之,滚珠螺母的刚度是一个复杂的性能指标,需要综合考虑材料特性、结构设计、装配状态以及工作条件等多种因素。
机械制造工艺复习题(含答案)
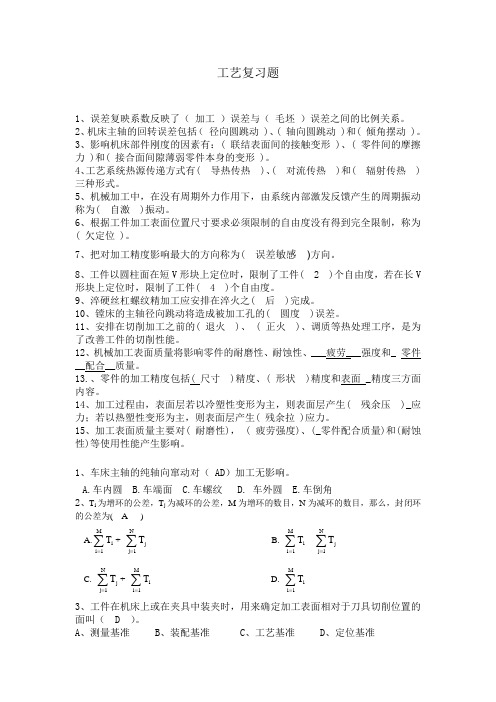
工艺复习题1、误差复映系数反映了( 加工 )误差与( 毛坯 )误差之间的比例关系。
2、机床主轴的回转误差包括( 径向圆跳动 )、( 轴向圆跳动 )和( 倾角摆动 )。
3、影响机床部件刚度的因素有:( 联结表面间的接触变形 )、( 零件间的摩擦力 )和( 接合面间隙薄弱零件本身的变形 )。
4、工艺系统热源传递方式有( 导热传热 )、( 对流传热 )和( 辐射传热 )三种形式。
5、机械加工中,在没有周期外力作用下,由系统内部激发反馈产生的周期振动称为( 自激 )振动。
6、根据工件加工表面位置尺寸要求必须限制的自由度没有得到完全限制,称为( 欠定位 )。
7、把对加工精度影响最大的方向称为( 误差敏感 )方向。
8、工件以圆柱面在短V 形块上定位时,限制了工件( 2 )个自由度,若在长V 形块上定位时,限制了工件( 4 )个自由度。
9、淬硬丝杠螺纹精加工应安排在淬火之( 后 )完成。
10、镗床的主轴径向跳动将造成被加工孔的( 圆度 )误差。
11、安排在切削加工之前的( 退火 )、 ( 正火 )、调质等热处理工序,是为了改善工件的切削性能。
12、机械加工表面质量将影响零件的耐磨性、耐蚀性、___疲劳___强度和_ 零件 __配合__质量。
13.、零件的加工精度包括( 尺寸 )精度、( 形状 )精度和表面 _精度三方面内容。
14、加工过程由,表面层若以冷塑性变形为主,则表面层产生( 残余压 )_应力;若以热塑性变形为主,则表面层产生( 残余拉 )应力。
15、加工表面质量主要对( 耐磨性), ( 疲劳强度)、(_零件配合质量)和(耐蚀性)等使用性能产生影响。
1、车床主轴的纯轴向窜动对( AD )加工无影响。
A.车内圆B.车端面C.车螺纹D. 车外圆E.车倒角2、T i 为增环的公差,T j 为减环的公差,M 为增环的数目,N 为减环的数目,那么,封闭环的公差为( A ) A.T i i M =∑1+ Tjj N=∑1B.T i i M =∑1- Tjj N=∑1C.T jj N =∑1+ T ii M=∑1 D. T ii M=∑13、工件在机床上或在夹具中装夹时,用来确定加工表面相对于刀具切削位置的面叫( D )。
详解机械加工容易出现的九大误差!

机床的制造误差机床的制造误差主要包括主轴回转误差、导轨误差和传动链误差。
主轴回转误差是指主轴各瞬间的实际回转轴线相对其平均回转轴线的变动量,它将直接影响被加工工件的精度。
主轴回转误差产生的主要原因有主轴的同轴度误差、轴承本身的误差、轴承之间的同轴度误差、主轴绕度等。
导轨是机床上确定各机床部件相对位置关系的基准,也是机床运动的基准。
导轨本身的制造误差、导轨的不均匀磨损和安装质量是造成导轨误差的重要因素。
传动链误差是指传动链始末两端传动元件间相对运动的误差。
它是由传动链中各组成环节的制造和装配误差,以及使用过程中的磨损所引起的。
2刀具的几何误差任何刀具在切削过程中都不可避免要产生磨损,并由此引起工件尺寸和形状地改变。
刀具几何误差对机械加工误差的影响随刀具种类的不同而不同:采用定尺寸刀具加工时,刀具的制造误差会直接影响工件的加工精度;而对一般刀具(如车刀等),其制造误差对机械加工误差无直接影响。
3夹具的几何误差夹具的作用是使工件相当于刀具和机床具有正确的位置,因此夹具的几何误差对机械加工误差(特别是位置误差)有很大影响。
4定位误差定位误差主要包括基准不重合误差和定位副制造不准确误差。
在机床上对工件进行加工时,须选择工件上若干几何要素作为加工时的定位基准,如果所选用的定位基准与设计基准(在零件图上用来确定某一表面尺寸、位置所依据的基准)不重合,就会产生基准不重合误差。
工件定位面与夹具定位元件共同构成定位副,由于定位副制造得不准确和定位副间的配合间隙引起的工件最大位置变动量,称为定位副制造不准确误差。
定位副制造不准确误差只有在采用调整法加工时才会产生,在试切法加工中不会产生。
5工艺系统受力变形产生的误差工件刚度:工艺系统中如果工件刚度相对于机床、刀具、夹具来说比较低,在切削力的作用下,工件由于刚度不足而引起的变形对机械加工误差的影响就比较大。
刀具刚度:外圆车刀在加工表面法线(y)方向上的刚度很大,其变形可以忽略不计。
机床机械加工误差产生的原因剖析

机床机械加工误差产生的原因剖析机床机械加工误差是指在机床加工过程中,加工零件与理论轨迹或规格要求存在的偏离或差异。
机床机械加工误差会直接影响零件的质量和精度,因此对其原因进行剖析是非常必要的。
一、机床本身因素1.刚度不足:机床刚度不足会导致机床在加工过程中容易产生振动和变形,从而影响零件的精度。
2.导轨精度:机床导轨的精度直接影响机床的定位精度和运动精度,导轨精度不高会导致机床在加工过程中产生偏差。
3.传动系统误差:机床传动系统(如螺杆传动、齿轮传动等)的误差会直接影响机床的定位精度和运动精度。
4.刀具磨损:刀具在长时间使用后会出现磨损,导致加工出来的零件尺寸偏差增大。
二、加工过程因素1.切削力:切削力是机床加工中产生的力,切削力的大小和切削方向会直接影响加工零件的精度和形状。
2.切削温度:切削过程中产生的热量会引起刀具和工件的热膨胀,从而影响加工零件的精度。
3.冷却液不当:冷却液不当会导致切削区温度过高,从而加剧刀具磨损和工件变形,进而影响加工精度。
4.装夹力:工件在机床上的夹紧力不均匀会导致工件在加工过程中产生变形,影响加工零件的精度。
三、操作因素1.操作技术:操作人员的操作技术熟练程度不同会导致机床的使用不当,从而影响加工零件的精度。
2.操作误差:操作人员在操作过程中可能会发生误操作,如切削深度设置错误、切削速度过快等,进而影响加工结果。
3.测量误差:机床的定位精度和运动精度需要通过测量来确认,而测量误差会直接导致加工零件的尺寸偏差。
四、环境因素1.温度变化:环境温度的变化会导致机床零部件的热膨胀或收缩,从而影响机床的定位精度和运动精度。
2.湿度变化:环境湿度的变化会导致机床零部件的腐蚀和生锈,进而影响机床的使用性能和加工质量。
机床主轴部件静刚度研究与试验

机床主轴部件静刚度研究与试验机床主轴是机床的核心部件之一,是完成加工任务的关键部件。
因此,主轴的性能直接影响加工精度,主轴部件静刚度研究是机床研发中不可缺少的工作。
本文将从静刚度研究的必要性、静刚度的定义、影响因素、测试方法和多轴动态力试验台的应用等方面介绍机床主轴部件静刚度研究与试验。
一、静刚度研究的必要性机床主轴部件静刚度研究是机床研发中非常必要的一项工作。
一方面,如果主轴部件的静刚度较差,加工时会产生振动和位移,导致加工精度下降,降低了机床的生产效率和加工质量。
同时,主轴部件的静刚度还与加工质量、精度、效率和寿命等因素直接相关,对于提高生产效率、降低加工成本等方面都有重要的作用。
二、静刚度的定义静刚度是指结构在无外力作用下抵抗变形的能力,它是描述结构抵抗变形和保持初始形状的重要参数。
机床主轴部件静刚度是指主轴部件在负载情况下的刚度,它直接影响主轴的运行状态和机床的加工精度等参数。
三、影响静刚度的因素影响机床主轴部件静刚度的因素非常多,下面列举几个主要的因素:1、支撑结构的刚度支撑结构的刚度是影响机床主轴部件静刚度的关键因素之一。
支撑结构的刚度越大,就越能抵抗主轴部件的变形和振动,从而提高主轴部件的静刚度。
2、轴承的刚度机床主轴部件的轴承也是影响静刚度的因素之一。
轴承的刚度越大,就越能抵抗主轴部件的变形和振动,从而提高主轴部件的静刚度。
3、工件质量工件的质量也会对机床主轴部件的静刚度产生影响。
工件的质量越高,工件所产生的负载就越小,从而减小了主轴部件发生变形的可能性。
四、测试方法测量机床主轴部件静刚度的方法有很多,其中包括静载荷试验法、双向钻孔法、旋转转子-静态负载法、多点位移法等。
选择相应的测试方法需要根据具体的条件来确定,并且要注意测试仪器的稳定性和准确性。
五、多轴动态力试验台的应用多轴动态力试验台是一种能够模拟实际工况下机床轴承负载情况的试验设备,能够对各种机床部件进行静、动刚度等各种性能测试。
机床导轨偏差对机械加工精度的影响与原因分析
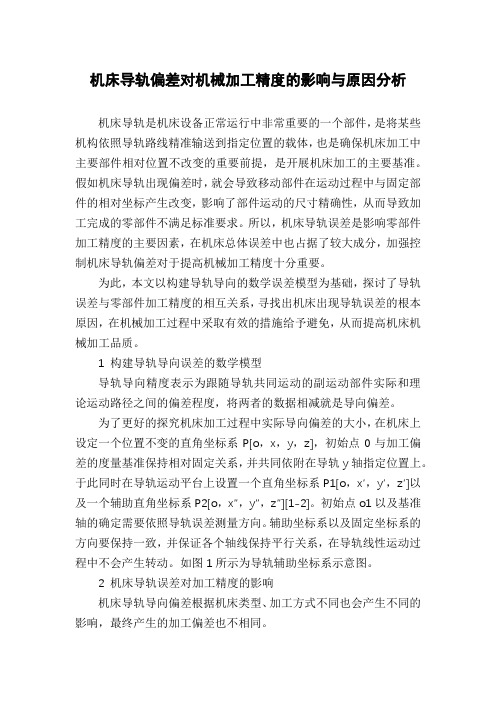
机床导轨偏差对机械加工精度的影响与原因分析机床导轨是机床设备正常运行中非常重要的一个部件,是将某些机构依照导轨路线精准输送到指定位置的载体,也是确保机床加工中主要部件相对位置不改变的重要前提,是开展机床加工的主要基准。
假如机床导轨出现偏差时,就会导致移动部件在运动过程中与固定部件的相对坐标产生改变,影响了部件运动的尺寸精确性,从而导致加工完成的零部件不满足标准要求。
所以,机床导轨误差是影响零部件加工精度的主要因素,在机床总体误差中也占据了较大成分,加强控制机床导轨偏差对于提高机械加工精度十分重要。
为此,本文以构建导轨导向的数学误差模型为基础,探讨了导轨误差与零部件加工精度的相互关系,寻找出机床出现导轨误差的根本原因,在机械加工过程中采取有效的措施给予避免,从而提高机床机械加工品质。
1 构建导轨导向误差的数学模型导轨导向精度表示为跟随导轨共同运动的副运动部件实际和理论运动路径之间的偏差程度,将两者的数据相减就是导向偏差。
为了更好的探究机床加工过程中实际导向偏差的大小,在机床上设定一个位置不变的直角坐标系P[o,x,y,z],初始点0与加工偏差的度量基准保持相对固定关系,并共同依附在导轨y轴指定位置上。
于此同时在导轨运动平台上设置一个直角坐标系P1[o,x′,y′,z′]以及一个辅助直角坐标系P2[o,x″,y″,z″][1-2]。
初始点o1以及基准轴的确定需要依照导轨误差测量方向。
辅助坐标系以及固定坐标系的方向要保持一致,并保证各个轴线保持平行关系,在导轨线性运动过程中不会产生转动。
如图1所示为导轨辅助坐标系示意图。
2 机床导轨误差对加工精度的影响机床导轨导向偏差根据机床类型、加工方式不同也会产生不同的影响,最终产生的加工偏差也不相同。
在使用车床进行轴类零部件加工时,Δz方向不会出现加工偏差,但是在Δx以及Δy方向会出现相对偏差,此时ΔRx=Δx、ΔRy≈(Δy)2/D,如图2所示为导向偏差对外圆周加工影响示意图。
机械制造技术基础B-第四章-第三节
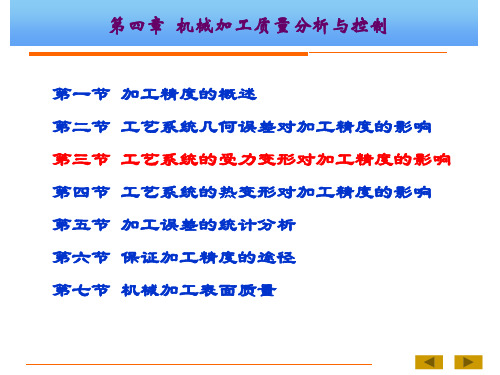
第三节 工艺系统的受力变形对加工精度的影响
切削过程中,增大走刀次数可不断减小工件的复映误差。设 ε1、ε2、 ε3分别为第一、第二、第三次走刀时的误差复映系数, 则
g1 1m, g22g112 m, g33g2123m
总误差复映系数: 总123
加工时:变形大的地方,切除的金 属层薄;变形小的地方,切除的金属 层厚。
结论:因机床受力变形,加工后的 工件呈两端粗,中间细的马鞍形。
第三节 工艺系统的受力变形对加工精度的影响
2. 工件的变形
用两顶尖车削细长轴时,不考虑机床和刀具的变形,工件在 切削点处的变形量 yB 为:
yB
FP(Lx)2x2 3EIL
k Fp y
第三节 工艺系统的受力变形对加工精度的影响
二、工艺系统刚度的计算
根据 k=Fy /y 得知,工艺系统在某一处的法向总变形位移y, 是系统的各个组成环节在同一处的法向变形的叠加:
yyjcyjjydyg
则机床刚度kjc、夹具刚度kjj、刀具刚度kd和工件刚度kg 为:
kjc Fp yjc, kd Fp yd , kjj Fp yjj, kg Fp yg,
得到:
11 111
k kjc kjj kd kg
第三节 工艺系统的受力变形对加工精度的影响
三、工艺系统刚度对加工精度的影响
(一)切削力作用点位置变化引起的工件形状误差 以在车床两顶尖间加工光轴为例,分析力作用点位置变化对
工件形状的影响。 1. 机床的变形 假定工件短而粗,车刀悬伸长度短,
从“提高工艺系统的刚度”和“减小载荷及其变化”两方面 采取措施,来减小工艺系统的受力变形。
(一)提高工艺系统的刚度 1. 合理的结构设计
- 1、下载文档前请自行甄别文档内容的完整性,平台不提供额外的编辑、内容补充、找答案等附加服务。
- 2、"仅部分预览"的文档,不可在线预览部分如存在完整性等问题,可反馈申请退款(可完整预览的文档不适用该条件!)。
- 3、如文档侵犯您的权益,请联系客服反馈,我们会尽快为您处理(人工客服工作时间:9:00-18:30)。
影响机床部件刚度的因素
1)连接表面间的接触变形
零件之间接合表面的实际接触面积只是理论接触面的一小部分,真正处于接触状态的,又只是一些凸峰。
当外力作用时,这些接触点处将产生较大的接触应力,并产生接触变形,其中有表面层的弹性变形,也有局部塑性变形。
图1所示为接触变形曲线。
试验表明,接触变形与接触表面名义压强的关系如下:
式中m —— 与连接面材料及表面状况有关的系数;
c —— 系数,由连接面材料,连接表面粗糙度、纹理方向等打算。
图1接触变形曲线
名义压强的增量dp与接触变形增量dx之比称为接触刚度kj。
明显有:
2)薄弱零件本身的变形
在机床部件中,薄弱零件受力变形对部件刚度的影响很大。
例如溜板部件中的楔铁,由于其结构瘦长,加工时又难以做到平直,以至装配后与导轨协作不好,简单产生变形。
3)零件表面间摩擦力的影响
机床部件受力变形时,零件间连接表面会发生错动,加载时摩擦力阻碍变形的发生,卸载时摩擦力阻碍变形的恢复,故表面间摩擦力
是造成加载和卸载刚度曲线不重合重要缘由之一。
4)接合面的间隙
部件中各零件间假如有间隙,那么只要受到较小的力(克服摩擦力)就会使零件相互错动。
假如载荷是单向的那么在第一次加载消退间隙后对加工精度的影响较小;假如工作载荷不断转变方向(如镗床、铣床的切削力),那么间隙的影响就不容忽视。
而且,因间隙引起的位移,在去除载荷后不会恢复。