7Dow化学指数法
DOW火灾、爆炸危险指数法(第七版)
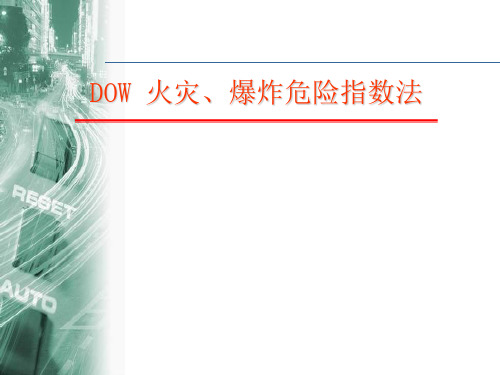
第19页
五、混合物的物质系数求取
如果存在由多种物质组成的混合物,当这些物质的含量基本相同, 但物质系数不同时,如果其中物质系数最大的物质浓度在5%以上(质 量浓度),可将最大物质系数作为工艺单元的物质系数。
在工艺单元中,虽然存在由多种物质组成的混合物,但其中某种物 质的浓度足够高,一旦发生泄漏,引起火灾、爆炸事故,工艺单元 中混合物的性质与高浓度物质的性质十分相似,这时可以用该高浓 度物质的物质系数作为工艺单元的物质系数。
110μm,试确定在这种情况下该单元的
粉尘爆炸危险系数。
第36页
5、 压力释放
本项系数用于操作压力高于大气压, 由于高压可能会引起高速率的泄漏的场 合。
试确定在下述两种情况下的压力释 放危险系数:
操作压力为800 磅/英寸2(表压)
第37页
6、 低温
本项主要考虑碳钢或其他金属在其 展延或脆化转变温度以下时可能存在的 脆性问题。
且其反应为间歇反应,试确定该单元 的泄漏危险系数。
第43页
10、 明火设备的使用
当易燃液体、蒸气或可燃性粉尘 泄漏时,工艺中明火设备的存在额外增 加了明引火起设引备燃设的置可在能工性艺。单元中;
明火设备附近有各种工艺单元。
第44页
11、 热油交换系统
大多数交换介质可燃且操作温度
经常在闪点火沸点以上,因此增加了危 险性热。交换介质的使用温度;
某低温冷冻单元装置结构为碳钢, 其操作温度为 -10℃,试确定在该情况下本单元的低温
第38页
7、 易燃物质和不稳定物质的数量
本项主要讨论单元中易燃物质和不 稳定物质的数量与危险性的关系。
工艺过程中的液体或气体;
DOW化学火灾

道(DOW)化学火灾\爆炸指数评价法1 概述DOW化学火灾\爆炸指数评价法属于危险指数评价法。
使用危险指数评价法的目的是确定与研究所考虑的最重要的工艺区域和操作,用于危险分析的危险等级方法原理依据3个要素:1)可能出现什么错误;2)可能性如何;3)有哪些影响因素。
危险指数评价是从安全角度出发,对所要分析的问题,确定其工艺及操作有关危险性,通过对工艺属性进行分析、比较和计算,进而确定哪一个区域的相对危险性更大,对重点关键的区域单元(危险性大的单元)进行进一步的安全评价补偿。
具有以下特点:1)鉴别出预期综合危险最大和易发生事故的各个单元;2)鉴别出单个单元或工厂中预期综合危险最大或最易引发事故的关键物料特性、工艺条件或工艺特点;3)利用预期的危险和事故特性去判定不同的设计、场址或操作选择方案;4)用单元或装置预期危险性表征事故特性比用其它特性更明了。
2 资料要求危险指数评价所需要的资料主要有:1)按照国家标准GB16483-2000《化学品安全技术说明书编写规定范围》编写的所用物料的安全技术说明书(MSDS,material safety data sheets)2)工艺图纸、物料的最大存量、装置工艺的条件、物料储存区的平面布置方面的资料;3)操作规程及有关法律、法规等资料;4)设计和操作数据资料及所选用的指数法的方法说明书等。
道化学火灾、爆炸指数评价法1 概述美国道化学公司于1964年开发了“火灾、爆炸危险指数评价法”,是其第一版。
在实际应用中,不断修改,并于1993年推出了第七版,也就是现在使用的DOW七版。
DOW法以以往的事故统计资料及物质的潜在能量和现行安全措施为依据,定量地对工艺装置及所含物料的实际潜在火灾、爆炸的反应危险性进行分析评价。
经过30多年的应用,DOW法已得到了全世界的广泛认可,并被作为一种标准性的方法,在危险化学品安全评价中得到了最为广泛的应用。
2 目的有以下四项目的:1)量化潜在火灾、爆炸和反应性事故的预期损失;2)确定可能引起事故发生或事故扩大的装置;3)向有关部门通报潜在的火灾、爆炸危险性;4)使有关人员有工程技术人员了解到各工艺部门可能造成的损失,以此确定减轻事故严重性的有效、经济的途径。
道(Dow)化学危险指数分析
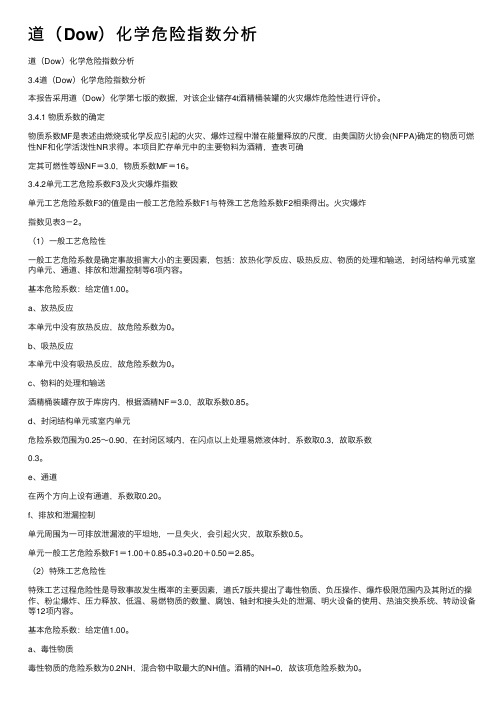
道(Dow)化学危险指数分析道(Dow)化学危险指数分析3.4道(Dow)化学危险指数分析本报告采⽤道(Dow)化学第七版的数据,对该企业储存4t酒精桶装罐的⽕灾爆炸危险性进⾏评价。
3.4.1 物质系数的确定物质系数MF是表述由燃烧或化学反应引起的⽕灾、爆炸过程中潜在能量释放的尺度,由美国防⽕协会(NFPA)确定的物质可燃性NF和化学活泼性NR求得。
本项⽬贮存单元中的主要物料为酒精,查表可确定其可燃性等级NF=3.0,物质系数MF=16。
3.4.2单元⼯艺危险系数F3及⽕灾爆炸指数单元⼯艺危险系数F3的值是由⼀般⼯艺危险系数F1与特殊⼯艺危险系数F2相乘得出。
⽕灾爆炸指数见表3-2。
(1)⼀般⼯艺危险性⼀般⼯艺危险系数是确定事故损害⼤⼩的主要因素,包括:放热化学反应、吸热反应、物质的处理和输送,封闭结构单元或室内单元、通道、排放和泄漏控制等6项内容。
基本危险系数:给定值1.00。
a、放热反应本单元中没有放热反应,故危险系数为0。
b、吸热反应本单元中没有吸热反应,故危险系数为0。
c、物料的处理和输送酒精桶装罐存放于库房内,根据酒精NF=3.0,故取系数0.85。
d、封闭结构单元或室内单元危险系数范围为0.25~0.90,在封闭区域内,在闪点以上处理易燃液体时,系数取0.3,故取系数0.3。
e、通道在两个⽅向上设有通道,系数取0.20。
f、排放和泄漏控制单元周围为⼀可排放泄漏液的平坦地,⼀旦失⽕,会引起⽕灾,故取系数0.5。
单元⼀般⼯艺危险系数F1=1.00+0.85+0.3+0.20+0.50=2.85。
(2)特殊⼯艺危险性特殊⼯艺过程危险性是导致事故发⽣概率的主要因素,道⽒7版共提出了毒性物质、负压操作、爆炸极限范围内及其附近的操作、粉尘爆炸、压⼒释放、低温、易燃物质的数量、腐蚀、轴封和接头处的泄漏、明⽕设备的使⽤、热油交换系统、转动设备等12项内容。
基本危险系数:给定值1.00。
a、毒性物质毒性物质的危险系数为0.2NH,混合物中取最⼤的NH值。
DOW火灾爆炸指数评价法在油库中的应用 (1)
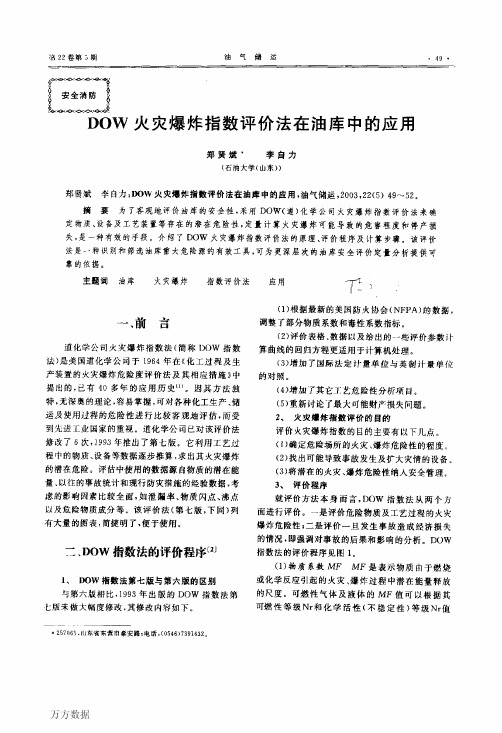
5.钱新明等;化工储罐瞳安全评价的比较研究,j、北大日期:200,1
2 01)
m+lll●…+…I●iI P+lII[+lII m+11[I●…+…m.-lllI+111 m●fl
m+…●¨|…III¨¨+…._ll
编辑:陈桂明
m._ll m●…●…+¨●i
调整了部分物质系数和毒性系数指标。 (2)评价表格、数据以及给出的一些评价参数计 算曲线的回归方程更适用于计算机处理。 (3)增加了国际法定计量单位与英制计量单位 的对照。 (4)增加,其它]:艺危险性分析项目。 (5)重新讨论了最大可能财产损失问题。 2、火灾爆炸指数评价的目的 评价火灾爆炸指数的目的主要有以下几点。 (I)确定危险场所的火灾、爆炸危险性的程度。 (2)找出可能导致事故发生及扩大灾情的设备。 (3)将潜在的火灾、爆炸危险性纳入安全管理。 3、评价程序 就评价方法本身而言,DOW指数法从两个方 面进行评价。一是评价危险物质及工艺过程的火灾 爆炸危险性;二是评价~旦发生事故造成经济损失 的情况,即强调对事故的后果和影响的分析。DOW 指数法的评价程序见图1。 (1)物质系数MF MF是表示物质由于燃烧 或化学反应引起的火灾、爆炸过程中潜在能量释放 的尺度。可燃性气体及液体的MF值可以根据其 可燃性等级Nr和化学活性(不稳定性)等级Nr值
险物质能量释放造成火灾或爆炸事故的综合效应。 单元危害系数DF是F。和MF的非线性函数,可查
图得到。
蓬
图1
确定危害景擞DF
确定8『
火灾、爆炸指数评价程序图
(7)确定暴露半径R在所评价的单元内发生 火灾爆炸时往往产生立体的同心圆柱型破坏,因此, 在考虑影响区域时,一般计算影响区域半径(即裸
露半径)R: R一0.256×F&E1(m)
道化学简介

道(DOW)化学公司火灾、爆炸危险指数法简介美国道化学公司自1964年开发“火灾、爆炸危险指数评价法”(第一版)来,历经29年,不断修改完善。
在1993年推出了第七版,以已往的事故统计资料及物质的潜在能量和现行安全措施为依据,定量地对工艺装置及所含物料的实际潜在火灾、爆炸和反应危险性行分析评价,可以说更趋完善、更趋成熟。
其目的是:量化潜在火灾、爆炸和反应性事故的预期损失;确定可能引起事故发生或使事故扩大的装置;向有关部门通报潜在的火灾、爆炸危险性;使有关人员及工程技术人员了解到各工艺部门可能造成的损失,以此确定减轻事故严重性和总损失的有效、经济的途径。
DOW化学公司火灾爆炸指数法也称为道氏指数法,其根据单元物质系数MF、工艺条件(一般工艺危险系数F1和特殊工艺危险系数F2),通过一系列系数计算(单元火灾爆炸指数F&EI 、影响区域、破坏系数DF计算)确定单元火灾爆炸危险程度,并与安全指标比较、判定事故损失能否被接受的评价方法。
其评价程序如下图3-1所示。
图1-1 DOW化学法评价程序图1.计算流程下图是F&EI计算流程图,给出了与本次评价有关的F&EI计算基本流程,该流程图对理解F&EI的计算过程很有帮助。
需要说明的是,这个流程并不是F&EI计算流程的全部,只是其中的一部分,其他部分因在本次评价中未用到而略去。
图1-2 火灾爆炸指数计算流程2.物质系数MF物质系数MF是计算F&EI的基本数据。
所谓的物质系数,是物质在由燃烧或其他化学反应引起的火灾和爆炸中,潜在能量释放速率的度量。
在与该方法配套的《火灾爆炸危险指南》中详细介绍了MF 的求取方法,并在其附录A中给出了部分常用的化合物和物质系数MF值。
3.一般工艺危险因素值(F1)一般工艺危险因素是在确定火灾爆炸事故损失时起主要作用的因素,这些因素被分为六个方面,每个方面均有各自的取值范围。
它们包括:Ⅰ.放热的化学反应,取值范围:0.30~1.25;Ⅱ.吸热的工艺过程,取值范围:0.20~0.40;Ⅲ.物质加工和运输,取值范围:0.25~1.05;Ⅳ.室内或密闭的工艺过程单元,取值范围:0.25~0.90;Ⅴ.紧急出入通道,取值范围:0.20~0.35;Ⅵ.对排泄和溢出的控制,取值范围:0.25~0.50;上述六个方面的数值求和,再加上基数1,即可得到一般工艺危险因素值F1。
道化学法

F.排放和泄露控制
0.20~0.50
一般工艺危险系数(F1) 2.特殊工艺危险系数
基本系数
1.00
1.00
A.毒性物质
0.20~0.80
B.负压<500mmHg=66661Pa
0.50
C.接近易燃范围的操作:惰性化、未惰性化
a.罐装易燃液体
0.50
b.过程失常和吹扫故障
0.30
c.一直在燃烧范围内
0.80
地区/国家: 位置: 评价人: 工艺单元 物质 主要物质 系数
表 4:生产单元危险分析汇总表
部门:
场所:
生产单元:
操作类型:
生产单元总替换价值:
日期:
火灾、爆炸 影响区内 基本 实际 停工天数
指数 F&EI 财产价值 MPPD MPPD MPDO
停工损失 BI
4、DOW 方法计算说明
4.1、选择工艺单元 确定评价单元:进行危险指数评价的第一步是确定评价单元,单元是装置的
J.热油、热交换系统
0.15~1.15
K.转动设备
0.50
特殊工艺危险系数(F2) 3.工艺单元危险系数(F3=F1×F2) 4.火灾、爆炸指数(F&EI=F3×MF)
*无危险系数时用 0.00
表 2:安全措施补偿系数表
项目
补偿系数范围
1.工艺控制
a.应急电源
0.98
b.冷却装置
0.97~0.99
g.泡沫灭火装置
0.92~0.97
h.手提式灭火器和喷水枪
0.93~0.98
i.电缆防护
0.94~0.98
防火设施安全补偿系数C3**
安全补偿系数=C1×C2×C3。
氯乙酸甲酯、甲醇、甲苯、多聚甲醛、甲醇钠-甲醇溶液、二恶氯乙烷火灾、爆炸危险指数法评价与衡量
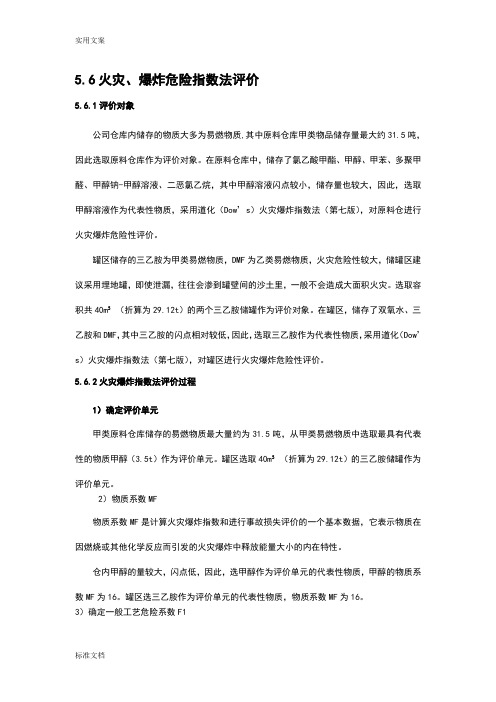
5.6火灾、爆炸危险指数法评价5.6.1评价对象公司仓库内储存的物质大多为易燃物质,其中原料仓库甲类物品储存量最大约31.5吨,因此选取原料仓库作为评价对象。
在原料仓库中,储存了氯乙酸甲酯、甲醇、甲苯、多聚甲醛、甲醇钠-甲醇溶液、二恶氯乙烷,其中甲醇溶液闪点较小,储存量也较大,因此,选取甲醇溶液作为代表性物质,采用道化(Dow’s)火灾爆炸指数法(第七版),对原料仓进行火灾爆炸危险性评价。
罐区储存的三乙胺为甲类易燃物质,DMF为乙类易燃物质,火灾危险性较大,储罐区建议采用埋地罐,即使泄漏,往往会渗到罐壁间的沙土里,一般不会造成大面积火灾。
选取容积共40m³(折算为29.12t)的两个三乙胺储罐作为评价对象。
在罐区,储存了双氧水、三乙胺和DMF,其中三乙胺的闪点相对较低,因此,选取三乙胺作为代表性物质,采用道化(Dow’s)火灾爆炸指数法(第七版),对罐区进行火灾爆炸危险性评价。
5.6.2火灾爆炸指数法评价过程1)确定评价单元甲类原料仓库储存的易燃物质最大量约为31.5吨,从甲类易燃物质中选取最具有代表性的物质甲醇(3.5t)作为评价单元。
罐区选取40m³(折算为29.12t)的三乙胺储罐作为评价单元。
2)物质系数MF物质系数MF是计算火灾爆炸指数和进行事故损失评价的一个基本数据,它表示物质在因燃烧或其他化学反应而引发的火灾爆炸中释放能量大小的内在特性。
仓内甲醇的量较大,闪点低,因此,选甲醇作为评价单元的代表性物质,甲醇的物质系数MF为16。
罐区选三乙胺作为评价单元的代表性物质,物质系数MF为16。
3)确定一般工艺危险系数F1一般工艺危险系数是确定事故危险程度的主要因素,包括:放热反应、吸热反应、物料处理与输送、封闭单元及室内单元、通道、排放和泄漏控制六项内容。
一般工艺危险性考虑那些和事故相关的最基本的影响因素。
本评价工艺单元的一般工艺危险系数取值如下:1.放热反应:无2.吸热反应:无3.物质处理与输送:桶装易燃液体存放于库房,系数取0.85。
道化学公司火灾、爆炸危险指数评价法
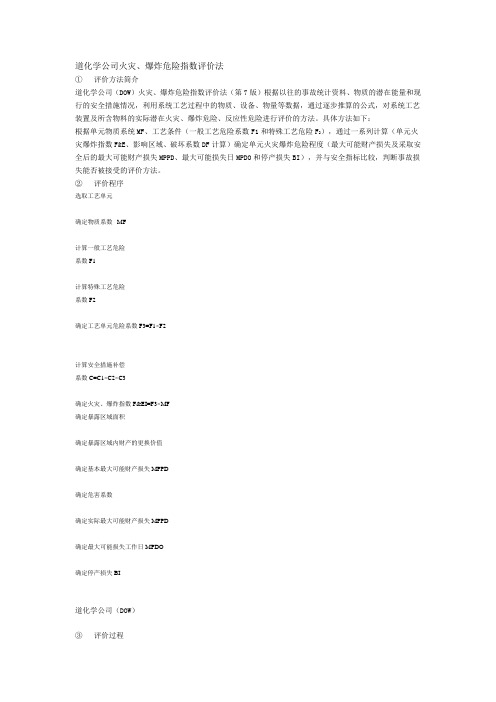
道化学公司火灾、爆炸危险指数评价法①评价方法简介道化学公司(DOW)火灾、爆炸危险指数评价法(第7版)根据以往的事故统计资料、物质的潜在能量和现行的安全措施情况,利用系统工艺过程中的物质、设备、物量等数据,通过逐步推算的公式,对系统工艺装置及所含物料的实际潜在火灾、爆炸危险、反应性危险进行评价的方法。
具体方法如下:根据单元物质系统MF、工艺条件(一般工艺危险系数F1和特殊工艺危险F2),通过一系列计算(单元火灾爆炸指数F&E、影响区域、破坏系数DF计算)确定单元火灾爆炸危险程度(最大可能财产损失及采取安全后的最大可能财产损失MPPD、最大可能损失日MPDO和停产损失BI),并与安全指标比较,判断事故损失能否被接受的评价方法。
②评价程序选取工艺单元确定物质系数MF计算一般工艺危险系数F1计算特殊工艺危险系数F2确定工艺单元危险系数F3=F1×F2计算安全措施补偿系数C=C1×C2×C3确定火灾、爆炸指数F&EI=F3×MF确定暴露区域面积确定暴露区域内财产的更换价值确定基本最大可能财产损失MPPD确定危害系数确定实际最大可能财产损失MPPD确定最大可能损失工作日MPDO确定停产损失BI道化学公司(DOW)③评价过程●确定评价单元。
包括评价单元的确定和评价设备的选择。
●求取单元内重要物质的物质系数MF。
重要物质是指单元中以较多数量(5%以上)存在的危险性潜能较大的物质。
物质系数(MF)是表述物质由燃烧或其它化学反应引起的火灾、爆炸过程中释放能量大小的内在特性,它由物质可燃性Nf和化学活泼性(不稳定性)Nr求得。
●根据单元的工艺条件,采用适当的危险系数,求得单元一般工艺危险系数F1和特殊工艺危险系数F2。
一般工艺危险系数F1是确定事故损害大小的主要因素。
特殊工艺危险系数F2是影响事故发生概率的主要因素。
●求工艺单元危险系数F3。
F3=F1×F2。
DOW火灾、爆炸危险指数法分析
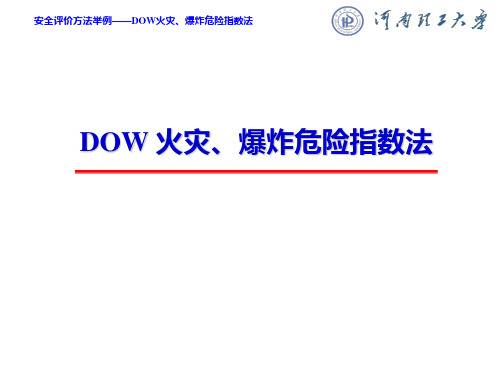
•储存、处理、生产易燃易爆、可燃、活性物质的操作过程 •污水处理设备(设施)、公用工程系统、管道系统、变压 器、发电设备、热氧化器等工艺单元
安全评价方法举例——DOW火灾、爆炸危险指数法
三、评价程序
十大步骤
•1、确定单元。 •2、求取单元内的物质系数MF。 •3、按单元的工艺条件,选用适当的危险系数。 •4、用一般工艺危险系数和特殊工艺危险系数相乘求出工艺单元危险系数。 •5 、 将 工 艺 单 元 危 险 系 数 与 物 质 系 数 相 乘 , 求 出 火 灾 、 爆 炸 危 险 指 数 (F&EI)。 •6、用火灾、爆炸指数查出单元的暴露区域半径,并计算暴露面积。 •7、查出单元暴露区域内的所有设备的更换价值,并确定危害系数,求出基 本最大可能财产损失MPPD。 •8、应用安全措施补偿系数乘以基本MPPD,确定实际MPPD。 •9、根据实际最大可能财产损失,确定最大损失工作日(MPDO)。 •10、用停产损失工作日MPDO确定停产损失。
MF由NF和NR求得。 NF —— 物质可燃性 NR —— 化学活泼性(不稳定性)
安全评价方法举例——DOW火灾、爆炸危险指数法
• Nr=0 在燃烧条件下仍能保持稳定的物质。 不与水反应的物质;在温度300 ℃以下时用差示扫描
量热(DSC)测定不显示温升的物质。 • Nr=1 自身通常稳定但在加温加压条件下就变得不稳 定的物质。
二、选择恰当工艺单元的重要参数
• 物质的潜在的化学能(物质系数); • 工艺单元中危险物质的数量; • 资金密度; • 操作压力与操作温度; • 导致火灾、爆炸事故的历史资料; • 对装置操作起关键作用的设备。
11
安全评价方法举例——DOW火灾、爆炸危险指数法
道(DOW)化学公司火灾、爆炸危险指数评价法(第7版):应用实例

道(DOW)化学公司火灾、爆炸危险指数评价法(第7版):应用实例1 评价项目概述本书选取某化学工业公司年产12万t聚苯乙烯项目作为评价对象,该公司的12万t聚苯乙烯项目由三套聚苯乙烯生产装置组成。
聚苯乙烯生产工艺流程包括配料、预聚合、聚合、脱挥、造粒等工序和循环真空、导热油等辅助系统。
聚苯乙烯工艺流程示意图如图11所示。
图11 聚苯乙烯工艺流程简图2 选择评价单元该公司主要分为生产区和贮罐区两大部分。
现有的12万t聚苯乙烯项目共有3条生产线,每条生产线均由多个工艺系统组成,包括配料、聚合、脱挥、循环回收、真空、造粒和粉末脱除等部分。
依据对聚苯乙烯生产工艺过程的分析,可初步确定苯乙烯聚合阶段是整个生产过程中最具危险性的阶段,因此,生产主装置区应选取预聚合车间为代表性工艺单元。
此外,苯乙烯罐区和日用罐区也是该公司内主要的火灾、爆炸危险场所,应以此为危险单元进行事故后果评价。
各评价单元基本情况如下:(1) 聚苯乙烯生产装置区:由于3条生产线的布置相对独立,可选取其中一条生产线为代表性评价单元,本书选取3号生产线进行评价。
评价时考虑苯乙烯(SM)进入预聚釜进行聚合时的情况。
(2) 贮罐区:该公司球罐区有两组贮罐,其中一组包含2个6 000m3的液化石油气球罐、1个600m3的柴油贮罐和1个864m3的矿物油贮罐;另一组为2个1 000m3的乙二醇贮罐,两组贮罐用防火堤隔开。
罐区的火灾爆炸危险主要来自苯乙烯,故选取苯乙烯罐组为单元进行评价,考虑罐内填充系数为0〃85时的情况。
(3) 日用罐区:罐区内的主要危险物质是苯乙烯,一般存放量约为150t。
3 各单元火灾、爆炸事故经济损失评价3〃1 物质系数的确定以生产装置区为例,单元内存在的物质有苯乙烯、矿物油、聚丁二烯橡胶和抗氧剂等。
根据评价指南的规定,应选取火灾危险性较大或储运量较大的物质作为代表性物质,故代表物选定为苯乙烯,其物质系数为24。
考虑苯乙烯进入预聚合釜聚合时的温度为90~200℃,远超过其闪点(32℃)温度,应进行温度修正,所得物质系数仍为24。
DOW化学火灾爆炸指数法在某采油平台安全评价中的应用 孙红栋
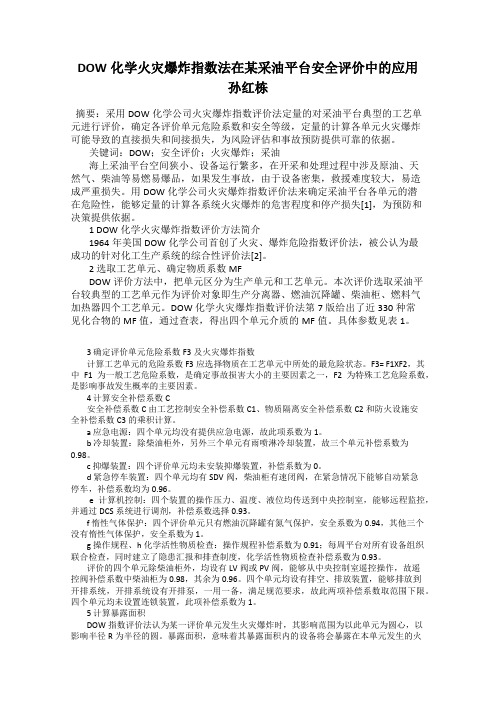
DOW化学火灾爆炸指数法在某采油平台安全评价中的应用孙红栋摘要:采用DOW化学公司火灾爆炸指数评价法定量的对采油平台典型的工艺单元进行评价,确定各评价单元危险系数和安全等级,定量的计算各单元火灾爆炸可能导致的直接损失和间接损失,为风险评估和事故预防提供可靠的依据。
关键词:DOW;安全评价;火灾爆炸;采油海上采油平台空间狭小、设备运行繁多,在开采和处理过程中涉及原油、天然气、柴油等易燃易爆品,如果发生事故,由于设备密集,救援难度较大,易造成严重损失。
用DOW化学公司火灾爆炸指数评价法来确定采油平台各单元的潜在危险性,能够定量的计算各系统火灾爆炸的危害程度和停产损失[1],为预防和决策提供依据。
1 DOW化学火灾爆炸指数评价方法简介1964年美国DOW化学公司首创了火灾、爆炸危险指数评价法,被公认为最成功的针对化工生产系统的综合性评价法[2]。
2 选取工艺单元、确定物质系数MFDOW评价方法中,把单元区分为生产单元和工艺单元。
本次评价选取采油平台较典型的工艺单元作为评价对象即生产分离器、燃油沉降罐、柴油柜、燃料气加热器四个工艺单元。
DOW化学火灾爆炸指数评价法第7版给出了近330种常见化合物的MF值,通过查表,得出四个单元介质的MF值。
具体参数见表1。
3 确定评价单元危险系数F3及火灾爆炸指数计算工艺单元的危险系数F3应选择物质在工艺单元中所处的最危险状态。
F3= F1XF2,其中F1为一般工艺危险系数,是确定事故损害大小的主要因素之一,F2为特殊工艺危险系数,是影响事故发生概率的主要因素。
4 计算安全补偿系数C安全补偿系数C由工艺控制安全补偿系数C1、物质隔离安全补偿系数C2和防火设施安全补偿系数C3的乘积计算。
a 应急电源:四个单元均没有提供应急电源,故此项系数为1。
b 冷却装置:除柴油柜外,另外三个单元有雨喷淋冷却装置,故三个单元补偿系数为0.98。
c 抑爆装置:四个评价单元均未安装抑爆装置,补偿系数为0。
DOW火灾、爆炸危险指数法(第七版)

2、创立时间
1964年(第1版) 1993年(第7版)
3、定量依据
以往事故的统计资料、物质的潜在能量和现行安全防灾措 施的状况。
国家安全生产监督管理总局安全生产科学研究院
第4页
风险评价培训课程-2006
二、评价目的及适用范围
1、评价目的
• 客观地量化潜在火灾、爆炸和反应性事故的预期损失; • 找出可能导致事故发生或使事故扩大的设备; • 向管理部门通报潜在的火灾、爆炸危险性; •使工程技术人员了解各部分可能的损失和减少损失的途径。
国家安全生产监督管理总局安全生产科学研究院
第25页
风险评价培训课程-2006
2、 吸热反应
• 反应器中的吸热反应 —— 系数0.2;
• 煅烧 —— 系数0.4; • 电解 —— 系数0.2; • 热解或裂化:间 接 加 热 —— 系数0.2; 直接火加热 —— 系数0.4。
国家安全生产监督管理总局安全生产科学研究院
F3 = F1 ¡ È · ¶ ¨ ¹ ¤ Ò Õ µ ¥ Ô ª Î £ Ï Õ Ï µ Ê ý Á F2 ¼ Æ Ë ã ° ² È « ´ ë Ê © ² ¹ ³ ¥ Ï µ Ê ý Ê =ý =C ¡ Á C Á C3 1 2¡ È · ¶ ¨ » ð Ô Ö ¡ ¢ ± ¬ Õ ¨ Ö ¸ Ê ý ï Ö Ê Ï µ Ê ý F£ ¦ EI = F 3 ¡ Á Î È · ¶ ¨ ± © Â ¶ Ã æ » ý È · ¶ ¨ ± © Â ¶ Ç ø Ó ò Ä Ú ² Æ ² ú µ Ä ¸ ü » » ¼ Û Ö µ È · ¶ ¨ » ù ± ¾ MPPD È · ¶ ¨ Ê µ ¼ Ê MPPD È · ¶ ¨ MPDO È · ¶ ¨ BI È · ¶ ¨ Î £ º ¦ Ï µ Ê ý
DOW道化法 火灾

DOW道化法火灾、爆炸指数危险性定量评价分析一、评价单元对拟建项目评价分割单元;二、分析计算程序框图内之间关系。
三、各单元火灾爆炸危险指数评价(1)物质系数的确定根据(DOW第七版)的规定,应选用火灾危险性较大或含量较大的物质作为代表物,汽油物质系数为16。
(2)确定一般工艺危险系数F基本危险系数:给定值为1物料处理与运输:(DOW)中规定:对NF=3或NF=4的易燃液或气体,存放于库房或露天时的系数取0.85,汽油易燃性NF=3,故汽油罐槽车的危险系数选0.85。
汽油罐槽车选0.2。
排放和泄漏控制:汽油罐槽车四周设有护堤、拦沟隔油池防止泄漏液流到其他区域,故选危险系数为0.5。
一般工艺危险系数F1为基本危险系数与所有选了危险系数之和,F1值如表4—1所示。
(3)确定特殊工艺危险系数F2基本危险系数:1.00毒性物质:毒性物质的危险系数为0.2×NH汽油NH=1 故选危险系数为0.2燃烧范围或其附近的操作,选危险系数为0.3压力释放:汽油罐槽车总容量为600m3×0.74=444吨查出危险系数为1.2特殊工艺危险系数F2等于基本危险系数与各项选取危险系数之和。
(4)计算单元工艺危险系数F3单元工艺危险系数F3是一般工艺危险系数F1和特殊工艺危险系数F2的乘积,即F3=F1F2。
(5)计算火灾,爆炸指数F&EI火灾、爆炸指数用来估计生产过程中事故可能造成的破坏程度。
该指数是单元工艺危险系数F3和物质系数MF的乘积,即F&EI=F3MF。
(6)确定安全措施补偿系数建造任何一个化工装置(或化工厂)时,应该考虑一些基本设计要点,要符合各种规范。
除了这些基本的设计要求之外,根据经验提出的安全措施也已证明是有效的,它不仅能预防严重事故的发生,也能降低事故的发生概率和危害。
安全措施可以分为工艺控制、物质隔离、防火措施三类,其补偿系数分别为C1,C2,C3。
①工艺控制补偿系数(C1)a、冷却——贮罐上备有冷却喷散管道故补偿系数选为0.97。
道化学计算实例

道化学火灾、爆炸危险指数评价法美国道化学公司以已往的事故统计资料及物质的潜在能量和现行安全措施为依据,定量地对工艺装置及所含物料的实际潜在火灾、爆炸和反应危险性进行分析评价。
自1964年开发第一版以来,历经二十多年,在1993年推出了第七版。
在危险化学品评价上更臻完善、更趋成熟。
1)道化学分析评价的目的①量化潜在火灾、爆炸和反应性事故的预期损失;②确定可能引起事故发生或使事故扩大的装置;③向有关部门通报潜在的火灾、爆炸危险性;④使有关人员及工程技术人员了解到各工艺部门可能造成的损失,以此确定减轻事故严重性和总损失的有效、经济的途径。
2)选择工艺单元选择恰当工艺单元的重要参数有下列六个:①潜在的化学能(物质系数);②工艺单元中危险物质的数量;③资金密度(每平方米美元数);④操作压力和操作温度;⑤导致火灾、爆炸事故的历史资料;⑥对装置起关键作用的单元。
一般参数值越大,则该工艺单元就越需要评价。
该方法是假定工艺单元中所处理的易燃、可燃或化学活性物质的最低量为2270千克或2.27立方米。
因此,若单元内物料较少,则评价结果有可能被夸大。
一般,所处理的易燃、可燃或者化学活性物质的量至少为454千克或0.454立方米,评价结果才有意义。
3)评价计算①火灾、爆炸危险指数(F&EI)a.物质系数(MF)的选取物质系数是表述物质在燃烧或其他化学反应引起火灾、爆炸时释放能量大小的内在特性,是一个最基础的数值。
它是由美国消防协会规定的NF、NR(分别代表物质的燃烧性和化学活性)决定的。
b.一般工艺危险系数(F1)的选取选取项包括“基本系数、放热化学反应、吸热反应、物料处理与输送、封闭式或室内工艺单元、通道、排放、泄漏控制”等7个取值项。
基本系数取1.00,其它6项根据实际情况具体取值,无危险时系数用0.00。
一般工艺危险系数为7项取值之和。
c.特殊工艺危险系数(F2)的选取选取项包括“基本系数、毒性物质、负压操作、接近易燃范围的操作、粉尘爆炸、压力、低温、物质的量和燃烧热、腐蚀与磨损、泄漏、使用明火设备、热油热交换系统、传动设备”等13个取值项。
第四章(2)—DOW指数法

评价方法及评价程序
力学与工程科学学院
第3页
安全系统工程
一、概述
1、名称
道化学公司(Dow Chemical Company)火灾与爆炸危险指数
F&EI(Fire and Explosion Index),简称DOW法。
2、创立时间
1964年(第1版)
1993年(第7版)
3、定量依据
以往事故的统计资料、物质的潜在能量和现行安全防灾措 施的状况。
力学与工程科学学院
第7页
安全系统工程
火灾、爆炸危险指数 评价程序框图
选选选选选选 选选选选F 1
选选选选选选 选选选选选选
选选选选选选 选选选选F 2
选选选选选选选选选选
F3 = F1× F2
选选选选选选 选选选选??=C1×C2×C3
选选选选选选选选选 F选EI = F3 ×选选选选
选选选选选选
• 单元中虽然存在由多种危险性反应物和一种生成物组成的危险性 混合物,但由于发生化学反应且反应速度很快,危险性反应物存在 的时间足够短,单元危险主要来自生成物时,可把生成物的物质系 数作为工艺单元的物质系数。
力学与工程科学学院
第20页
安全系统工程
五、注意事项
• 确定混合物物质系数最好的办法是直接做混合物的燃烧性或反应 性试验。 •MF的温度修正。物质的MF只代表了常委成员环境下的危险性,如 果工艺单元温度高于60度,须按规定加以修正。如工艺单元是反应 器,对反应引起的温度升高可不修正。
力学与工程科学学院
第30页
安全系统工程
1. 一般工艺危险 基本系数 (1)放热化学反应 (2)吸热反应 (3)物料处理与输送 (4)密闭式或室内工艺单元 (5)通道 (6)排放和泄漏控制 一般工艺危险系数(F1)
道化学计算实例
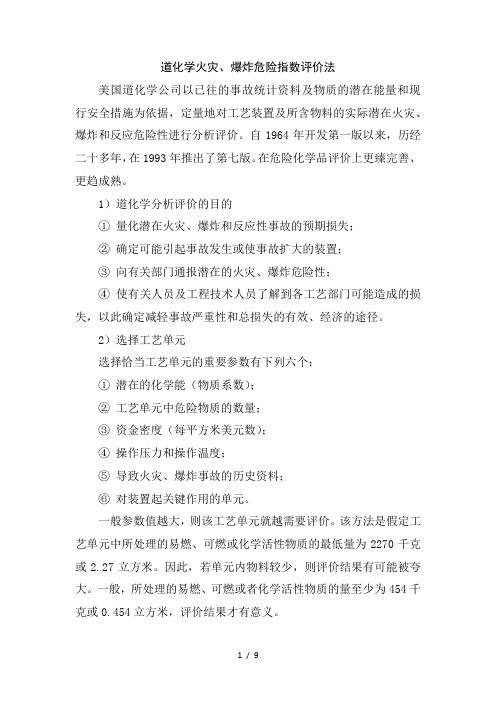
道化学火灾、爆炸危险指数评价法美国道化学公司以已往的事故统计资料及物质的潜在能量和现行安全措施为依据,定量地对工艺装置及所含物料的实际潜在火灾、爆炸和反应危险性进行分析评价。
自1964年开发第一版以来,历经二十多年,在1993年推出了第七版。
在危险化学品评价上更臻完善、更趋成熟。
1)道化学分析评价的目的①量化潜在火灾、爆炸和反应性事故的预期损失;②确定可能引起事故发生或使事故扩大的装置;③向有关部门通报潜在的火灾、爆炸危险性;④使有关人员及工程技术人员了解到各工艺部门可能造成的损失,以此确定减轻事故严重性和总损失的有效、经济的途径。
2)选择工艺单元选择恰当工艺单元的重要参数有下列六个:①潜在的化学能(物质系数);②工艺单元中危险物质的数量;③资金密度(每平方米美元数);④操作压力和操作温度;⑤导致火灾、爆炸事故的历史资料;⑥对装置起关键作用的单元。
一般参数值越大,则该工艺单元就越需要评价。
该方法是假定工艺单元中所处理的易燃、可燃或化学活性物质的最低量为2270千克或2.27立方米。
因此,若单元内物料较少,则评价结果有可能被夸大。
一般,所处理的易燃、可燃或者化学活性物质的量至少为454千克或0.454立方米,评价结果才有意义。
3)评价计算①火灾、爆炸危险指数(F&EI)a.物质系数(MF)的选取物质系数是表述物质在燃烧或其他化学反应引起火灾、爆炸时释放能量大小的内在特性,是一个最基础的数值。
它是由美国消防协会规定的NF、NR(分别代表物质的燃烧性和化学活性)决定的。
b.一般工艺危险系数(F1)的选取选取项包括“基本系数、放热化学反应、吸热反应、物料处理与输送、封闭式或室内工艺单元、通道、排放、泄漏控制”等7个取值项。
基本系数取1.00,其它6项根据实际情况具体取值,无危险时系数用0.00。
一般工艺危险系数为7项取值之和。
c.特殊工艺危险系数(F2)的选取选取项包括“基本系数、毒性物质、负压操作、接近易燃范围的操作、粉尘爆炸、压力、低温、物质的量和燃烧热、腐蚀与磨损、泄漏、使用明火设备、热油热交换系统、传动设备”等13个取值项。
- 1、下载文档前请自行甄别文档内容的完整性,平台不提供额外的编辑、内容补充、找答案等附加服务。
- 2、"仅部分预览"的文档,不可在线预览部分如存在完整性等问题,可反馈申请退款(可完整预览的文档不适用该条件!)。
- 3、如文档侵犯您的权益,请联系客服反馈,我们会尽快为您处理(人工客服工作时间:9:00-18:30)。
对于危险程度为Ⅰ级的项目,最好用事故树和事件树 分析进行再评价。通过评价,如果发现有不完善之处,要 对设计进行修改,然后才能进行项目建设。
步骤
①
新建装置 安全性 基本政策 1有关法令收集 2 有关标准收集
② ③
用安全检查表检查 定量评价 潜在危险性评价 重要度分类
MR2 = MR1K1K2K3K4K5K6
概率安全评价法
是一种定量分析的方法。 先求系统发生事故的概率(FMECA、ETA、FTA等法) 在此基础上,进一步计算风险率的大小。 该方法认为系统危险性(风险率R )取决于两个方面: ① 事故发生的概率P (事故次数/单位时间)
② 造成后果严重程度S (事故损失/事故次数)
1级 ④ ⑤ ⑥ 安全对策 由事故情报评价 FTA评价 ETA评价
2级
3级 安全对策 由事故情报评价
4级
进行建设 运行 维修检查
化工六阶段法小结
评价 目标
方法特点 使用范围 也 可化 以工 推厂 广及 到有 相关 关装 应置 用。 领 域 。 应用条件 优缺点 准 确综 度合 较应 高用 ,几 工种 作办 量法 较反 大复 。评 价 ,
安 全 评 价 程 序 图
2、DOW 指数法评价程序
① 确定单元;
② 求取单元内的物质系数MF ;
P.68表3-11、P.228 附录
③ 求:“一般工艺危险系数F1 P.70表3-13”和“特殊工艺危险系数 F2 P.72表3-14”;(F=基本系数+所选系数的和) ④ 用F1×F2求出工艺单元危险系数F3;
② 再考虑工艺过程中其他因素的影响,来计算每个单
元的危险度数值(如操作方式、工艺条件、设备状况、物
料处理、安全装置情况等)
③ 然后按数值大小划分危险度级别。(分析时对管理因
素考虑较少,属静态分析)
④ 它主要是对化工生产过程中固有危险的度量。
1、DOW 指数法概述
① 道指数法开创了化工生产危险度定量评价的历史。 ② 1964年公布第一版,至今已作了 6 次修改,于1993年提出了 第 7 版。 ③ 道化学公司方法推出以后,各国竞相研究,在它的基础上提 出了一些不同的评价方法。 ④ 尤以英国ICI公司蒙德分部最具特色。他们根据化学工业的特 点,扩充了毒性指标,并对所采取的安全措施引进了补偿系 数的概念,把这种方法向前推进了一大步。 ⑤ 道化学公司又在吸收蒙德方法优点的基础上,进一步把单元 的危险度转化为最大可能财产损失,使该方法日臻完善。
P成=A1B1+A1B2C1
=0.855+0.0855 成功 =0.9405 P失 = 1-P成 =1-0.9405 失败 =0.0595 =A2+A1B2C2
系统成功的概率为0.9405,系统失败的概率为0.0595。
作业条件危险性分析法
一般作业的危险评价是一种简单易行的在有潜在危险
环境下作业的评价方法。
则:风险率(事故损失/单位时间)
R = S ·P
• 计算的风险率与安全指标比较,高则降,降至???
概率安全评价法故障概率
1
元件的故障概率一般可由试验获得(产品可靠性参数)。
并 不但 是是 一, 个许 稳多 定元 的件 数的 值故 。障 概 率
失 效
概率安全评价法
化工六阶段法(日本劳动省)
危险等级 危险分数Wd Ⅰ >16 Ⅱ 11~15 Ⅲ 1~10
危险评定 第四阶段:安全对策
高度
中等
低度
根据定量评价得出的危险等级和要求,拟定并实施有针 对性的安全措施(包括:技术、设备、组织管理等)。
化工六阶段法(日本劳动省)
第五阶段:用事故情报进行再评价
根据设计内容,参照同类设备和工艺的历史事故资料 进行再评价。如果有需要改进的地方,应按照上一步的要 求,重新进行讨论。 对于危险程度为Ⅲ级或Ⅱ级的项目,在以上的评价结 束之后,就可进行建设。
2
元件连接而成的系统,其故障概率求解
一、求串联系统概率(先确定成功的概率):
若元件A、B、C的成功概率分别为P(A)、 P(B)、 P(C),则系统的 成功概率P(S)为A、B、C均处于成功状态时的概率,即三事件的成功 概率积——可靠度。 成功概率 P( S ) P( A) P( B) P(C )
(工艺控制、物质隔离、防火措施P.80表3-16各项补偿系数的积);
⑨ 应用安全措施补偿系数C乘以基本最大可能财产损失 MPPD,确定实际MPPD=C×base MPPD ; ⑩ 据实际MPPD ,确定最大损失工作日MPDO P.87图3-23 ; 11 用MPDO确定停产损失BI =(MPDO /30 )× VPM × 0.7。
固 有 危 险 度 、 财 产 损 失
ICI 蒙德法简介
英国帝国化学公司(ICI)的蒙德(Mond)化工厂,根据道化学 公司评价方法的原则,提出了安全评价的蒙德方法。
该法详细规定了各种附加因素增加比例的幅度。
并根据不同的措施和条件,提出了补偿系数的概念,使评价结果 更符合实际。
采用蒙德答进行评价时,需要确定各评价要素的危险值。
DOW指数法及其它方法
张 东 胜
DOW火灾与爆炸指数法及其它
1
DOW指数法概述(ICI蒙德法)
2
DOW指数法评价程序(步骤)
3
概率法、作业条件危险性、化工六阶段法
4
机械工厂、工业管道、火力发电等评价法
1、DOW 指数法概述
美国DOW化学公司火灾、爆炸指数危险评价法,用 于对化工工艺过程及其生产装置的火灾、爆炸危险性 做出评价,并提出相应的安全措施。其原理如下: ① 它以物质系数为基础
3~40
(需要注意 ~ 极其危险)
作业条件危险性分析法小结
简单易行(打分、计算);
危险程度级别划分清晰、醒目;
3因素的分值及危险等级多凭经验,有局限;
是一种局部的评价,不具普遍适用性。
具体应用时,可按原则加以修正,但须有根据!
化工六阶段法(日本劳动省)
1976年,日本劳动省颁布了化工厂安全评价指南,提 出了六阶段评价法。是的评价方法。 方法集中了定性和定量评价的双重内容,考虑较周到 先从安全检查表入手 再根据各种条件评出表示危险性大小的分数 然后根据总的危险分数采取相应的安全对策。 除了在化工厂实施外,还扩大到其他行业。
作业条件危险性分析法
E-暴露于危险环境的频繁程度
分数值 暴露于危险环境的频繁程度 10 连续暴露
6
3 2 1 0.5
每天工作时间内暴露
每周一次,或偶然暴露 每月一次暴露 每年几次暴露 非常罕见地暴露
作业条件危险性分析法
C―发生事故产生的后果
分数值 100 40 15 7 3 1 发生事故产生的后果 大灾难,许多人死亡 灾难,数人死亡 非常严重,一人死亡 严重,严重伤害 重大,致残 引人注目,需要救护
一个油漆稀释剂生产车间,车间内有稀释剂原料 二甲苯、丙酮、乙酸乙酯等易燃易爆物品,工人全工
作时间暴露于车间内。 试用作业条件危险性分析法分析该车间的风险
现场状况判断 L 1)不经常但可能,2)相当可能 E 全工作时间暴露
取值 3或6 6
C 1)重大致残,2)严重伤害,3)致死
D = L E C = 54 ~ 1440
失败概率
F ( S ) 1 P( S )
二、求并联系统概率(先确定失败的概率) :
若元件A、B、C的成功概率分别为P(A)、 P(B)、 P(C),则系统的 失败概率F(S)为A、B、C均处于失败状态时的概率,即三事件的失败 概率积——故障率。 成功概率 P(S) = 1 – F(S)
失败概率 F(S) = [1-P(A)][1-P(B)][1-P(C)]
化工六阶段法(日本劳动省)
第一阶段:资料准备 这一阶段主要是搜集资料、熟悉政策和了解情况。所要搜 集的资料包括: 建厂条件、工厂总体布置、工艺流程及设备配置;原材 料、产品及中间产品的物理、化学性质;材料、产品的运 输和储存方式;安全装置的类别和位置,人员配备、操作 方式及组织机构等。 所要熟悉的政策包括有关法令、规程、标准及操作指南。 同时,要了解人、物、环境和管理等情况,为进一步的评价
作业条件危险性分析法
危险等级划分(D)
D 值 >320 160-320 70-160 20-70 <20 危 险 程 度 极其危险,不能继续作业 高度危险,要立即整改 显著危险,及时整改 一般危险,需要注意 稍有危险,可以接受
由以上表格和公式可以绘制危险性评价诺莫图 P.63 图3-14
作业条件危险性分析法小案例
工作作好准备。
化工六阶段法(日本劳动省)
第二阶段:定性评价 主要是用安全检查表进行检查和粗略评价。定性评价项目 包括:厂址选择、厂区布置、建筑物和构筑物、工艺设备、 材料及产品的储运、消防设备及事故预防计划等。
第三阶段:定量评价
进行定量评价时,首先将系统分为若干子系统及单元。对
于各单元,按物质、容量、温度、压力和操作五个项目进行 检查和评定,每一项又分为A,B,C,D四个类别,分别表 示10分,5分,2分,0分。然后,按照单元的总危险分数, 确定该单元的危险程度。 P.133 表3 - 40
元件串联系统示例
成功概率 P( S ) P( A) P( B) P(C ) 失败概率 F ( S ) 1 P( S )
系统成功的概率为0.7695,系统失败的概率为0.2305。
元件串并联系统示例
阀门B 泵A A1=0.95 启动 A2=0.05 B1=0.9 阀门C B2=0.1 C1=0.9 C2=0.1
DOW指数法工作前的资料准备
① 完整的工厂设计方案
② 详尽的工艺流程图
③ DOW 7 版火灾、爆炸指数评价法