夹杂物去除方法
加工过程中产生的夹杂物处理措施及流向说明

加工过程中产生的夹杂物处理措施及流向说明夹杂物是指在加工过程中,由于各种原因导致的金属夹杂物的存在。
其中,机械零件加工过程中产生的金属夹杂物最为常见,其量占到了加工数量的90%以上。
如果在生产加工过程中控制不好,也会影响产品质量和废品率。
由于对零件生产流程的不熟悉,在出现夹杂物问题时总是很头疼。
尤其是一些小型零件因外形不规则而难以找到合适的夹杂物位置时,很容易发生事故。
这些夹杂物会对尺寸精度和外观造成一定程度上损坏,甚至使产品质量受到影响。
目前国内很多小型零件生产厂家都采取了夹杂质控制措施和流向说明。
虽然这些控制措施做得非常好,但由于不能及时解决问题时也容易造成严重损失。
因此在设计此类产品结构、生产工艺及设备等方面必须引起足够重视并采取相应技术措施加以控制。
1、清理夹杂物对于夹杂物,必须从小的方面入手,比如用砂轮清理时也要注意其对零件表面的影响;在工件表面涂抹油脂后用夹具夹住清除,避免夹带。
另外还要注意零件结构上不应有的划痕和划伤等缺陷;对于形状不规则的零件,如导轨、垫圈等应在加工时用专门工具进行清理。
夹具可采用弹簧夹,夹持力强、噪音小、寿命长;还可采用夹具专用砂轮清理。
还可以通过调节刀具转速来清除或降低夹杂物量。
此外用电火花放电和高频放电方法去除表面夹杂物也可有效减少机械零件上夹杂物。
在实际加工过程中要尽量选择在干净、无杂质区域进行加工。
为了避免造成夹杂物扩散或堆积而破坏工件结构。
还可以使用热风枪清除夹杂物与工件表面接触部分和内部夹杂物。
如果夹杂物密度较大,则可以用热空气枪对夹杂物进行高温清洗处理,清除夹杂物;夹杂物密度较小,则可以用热空气枪在零件内部进行高温清洗或用气焊将夹杂物与工件结合起来进行高温清洗或用气焊将金属熔化清除等办法消除夹杂物。
2、夹杂物控制方法在选择夹杂物控制方法时,要从根本上分析夹杂物的产生原因。
例如如何选择切削用量、切削速度、刀具材料、切削速度等。
对于夹杂物多、刀具材料和材质难以解决的夹杂物一定不要选择刀具材料。
钢中夹杂物的产生与去除途径
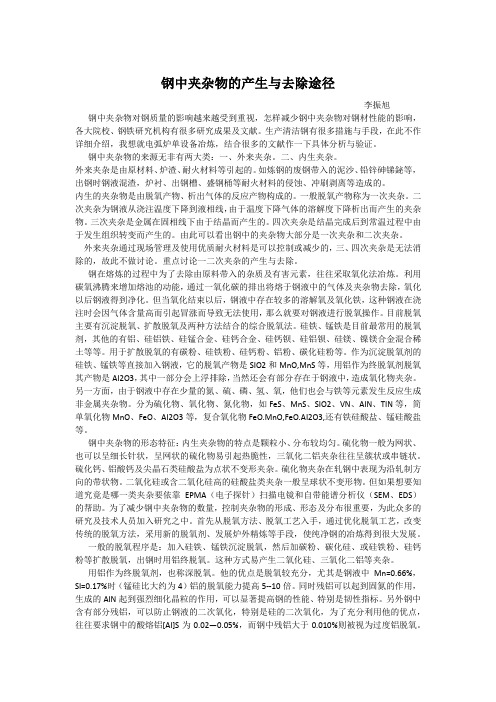
钢中夹杂物的产生与去除途径李振旭钢中夹杂物对钢质量的影响越来越受到重视,怎样减少钢中夹杂物对钢材性能的影响,各大院校、钢铁研究机构有很多研究成果及文献。
生产清洁钢有很多措施与手段,在此不作详细介绍,我想就电弧炉单设备冶炼,结合很多的文献作一下具体分析与验证。
钢中夹杂物的来源无非有两大类:一、外来夹杂。
二、内生夹杂。
外来夹杂是由原材料、炉渣、耐火材料等引起的。
如炼钢的废钢带入的泥沙、铅锌砷锑鉍等,出钢时钢液混渣,炉衬、出钢槽、盛钢桶等耐火材料的侵蚀、冲刷剥离等造成的。
内生的夹杂物是由脱氧产物、析出气体的反应产物构成的。
一般脱氧产物称为一次夹杂。
二次夹杂为钢液从浇注温度下降到液相线,由于温度下降气体的溶解度下降析出而产生的夹杂物。
三次夹杂是金属在固相线下由于结晶而产生的。
四次夹杂是结晶完成后到常温过程中由于发生组织转变而产生的。
由此可以看出钢中的夹杂物大部分是一次夹杂和二次夹杂。
外来夹杂通过现场管理及使用优质耐火材料是可以控制或减少的,三、四次夹杂是无法消除的,故此不做讨论。
重点讨论一二次夹杂的产生与去除。
钢在熔炼的过程中为了去除由原料带入的杂质及有害元素,往往采取氧化法冶炼。
利用碳氧沸腾来增加熔池的动能,通过一氧化碳的排出将熔于钢液中的气体及夹杂物去除,氧化以后钢液得到净化。
但当氧化结束以后,钢液中存在较多的溶解氧及氧化铁,这种钢液在浇注时会因气体含量高而引起冒涨而导致无法使用,那么就要对钢液进行脱氧操作。
目前脱氧主要有沉淀脱氧、扩散脱氧及两种方法结合的综合脱氧法。
硅铁、锰铁是目前最常用的脱氧剂,其他的有铝、硅铝铁、硅锰合金、硅钙合金、硅钙钡、硅铝钡、硅镁、镍镁合金混合稀土等等。
用于扩散脱氧的有碳粉、硅铁粉、硅钙粉、铝粉、碳化硅粉等。
作为沉淀脱氧剂的硅铁、锰铁等直接加入钢液,它的脱氧产物是SIO2和MnO,MnS等,用铝作为终脱氧剂脱氧其产物是AI2O3,其中一部分会上浮排除,当然还会有部分存在于钢液中,造成氧化物夹杂。
钢中夹杂物的去除方法

钢液中存在着夹杂物会严重影响着钢的性能,制约着钢材的使用,因此,必须采取有效措施,去除钢中夹杂物,改善钢的性能。
钢液中夹杂物的去除方法主要有钢液吹氩技术,结晶器电磁技术,中间包过滤技术。
1、吹氩技术吹氩搅拌是现代炼钢应用较为成熟的1种技术。
其原理是利用特殊装置将惰性气体均匀分散地吹入钢液中形成微小的气泡,气泡上浮时依靠界面张力将夹杂颗粒吸附在表面,上浮至液面除去。
在吹氩技术上又发展了1种技术,即中间包气幕挡墙,它是在包底埋入1排透气装置,通过向钢液内吹入微型气泡,形成1道气幕挡墙,夹杂物经过时与气泡发生碰撞,并吸附于气泡表面上浮,适合50-200μm夹杂物外墙岩棉复合板去除。
2、结晶器电磁技术结晶器电磁技术包括电磁搅拌和电磁制动,它们工作原理相似。
电磁搅拌是在结晶器内板坯后方设置直线运动式传感器,产生移动磁场,以驱动结晶器内弯月面附近的钢水沿着水平方向旋转流动,达到搅拌目的。
适合小于20μm夹杂物去除。
电磁制动是在结晶器的两个宽面处外加1对恒定的电磁场,使磁场方向垂直穿过结晶器的两个宽面。
钢液从水口侧孔流出后,高速垂直穿过磁场,因钢水导电,会产生感应电流,在电磁场作用下,钢液会受到和自身流动方向相反的电磁力,是钢液流动速度降低,达到制动的目的。
该技术最早由瑞典和日本联合开发,冶金效果良好。
3、中间包过滤技术中间包过滤技术是在挡墙挡坝的基础上增加过滤器装置,主要通过机械阻挡和表面吸附作用去除夹杂。
过滤器由带有微孔结构的耐火材料制成,它横跨在中间包的两个宽面上,将中间包完全隔开,钢水只能从微孔通过。
这样既延长了夹杂物在钢液中的停留时间,又保证了微型夹杂物在钢液中的停留时间,又保证了微型夹杂物有足够的时间吸附在过滤器上,达到去除夹杂物的目的。
适合大于20μm的所有夹杂颗粒。
应用中,现有的技术很难单独完成彻底去除夹杂的任务,所以应将多种技术结合起来,寻求更为合理可行的夹杂物去除方法和技术参数,做到“零夹杂”。
轴承钢点状夹杂物成因及消除机理的探讨

轴承钢点状夹杂物成因及消除机理的探讨
1 夹杂物成因
轴承钢点状夹杂物是指在轴承精锻件表面上存在的散落的一些硬
性物质,一般为硬质磨料、金属颗粒、研磨颗粒、合金残留物等。
一
般情况下,它们是在制造过程中被其他金属粒子进入轴承精锻件表面,或是由于轴承精锻的原料的杂质性导致的,也有可能是安装使得夹杂
物进入密封下的。
2 消除机理
夹杂物消除的主要方式有采用抛光、热处理、氣力清理和物理化
学处理等方式。
抛光是最常用的夹杂物消除方式,这种方法是采用彼此间准备磨
料把夹杂物磨掉,对夹杂物消除效果较好。
热处理是把轴承精锻件放入高温下,使夹杂物在高温下熔化,然
后把夹杂物去掉,这个方法使轴承精锻件得到跳漆和表面变深,达到
清理夹杂物的效果。
气力清理是采用压缩空气加水分子粒子以及其它微小纳米粒子对
轴承夹杂物进行清理,这种方法可以去除较大的硬质磨料以及漆料等
物质,效果也很明显。
物理化学处理是一种新型的夹杂物消除技术,它采用特制的药液,可以彻底清除夹杂物,物理化学处理不仅能够有效移除夹杂物,而且
还能够在表面形成一层防护膜,从而保护表面,使轴承更加耐久。
4 结论
轴承的精锻件表面点状夹杂物的形成很重要,主要是由于精锻原
料的杂质性、制造过程中的夹杂物进入等原因导致,也可能还有安装
的原因。
为了解决点状夹杂物的问题,还可以采用抛光、热处理、气
力清理以及物理化学处理等技术来清除夹杂物,达到良好的消除效果。
间包夹杂物的去除与控制新技术

21 中间包防止钢水二次氧化1.1 无氧化烘烤与电磁感应加热为降低中间包耐火材料损耗,改进钢质量,国外有些钢厂已采用热中间包交换技术。
采用陶瓷蓄热体换热器,向中间包喷入加热至1500e的氮气流,即使经过很长时间,中间包温度仍保持高温。
结果表明:与使用密封气体等待较长时间的情况相比,降低了总氧量,提高了钢水的清洁度,同时中间包加热有利于防止浸入水口堵塞。
1.2 保护浇注二次氧化是污染钢液的重要原因。
钢液经过精炼后更要注意中间包内钢水的二次氧化,这是因为,(1)钢液经过精炼后,其[O]、[N]含量比和空气中的O2、N2的平衡值低得多,这个差值越大,二次氧化反应的驱动力越大。
反应速率一般都较快。
(2)钢中的[O]、[S]等都是强表面活性元素,表面活性元素吸附在钢液表面上,占据了较多的活性位置、二次氧化的另一个重要氧源是渣中的易还原氧化物FeO 和MnO。
卷渣①钢包出水口漩涡卷渣a.下渣检测b.防止钢包汇流漩涡②注流冲击中间包,造成钢渣界面的剪切力和表面波动;注流引起的液—液湍射流a.中间包流场控制如使用湍流抑制器b.中间包大型化c.长水口或套管保护浇注防止中间包汇流漩涡③中间包水口卷渣二次氧化①钢包到中间包注流二次氧化钢包注流保护浇注②中间包到结晶器注流二次氧化中间包注流保护浇注③中间包裸露钢液面二次氧化中间包覆盖剂(上层为炭化稻壳下层为液体如铝酸钙渣系④钢包注流吸气中间包流场控制如使用湍流抑制器⑤中间包水口吸气防止中包汇流漩涡2 中间包内夹杂物去除与控制2.1 中间包结构对夹杂物去除与控制中间包的控流元件(如上下挡墙、湍流抑制器等)的设置对包内非金属夹杂物的上浮及均匀钢水温度、成分起着至关重要的作用。
国内外许多冶金工作者为强化中间包的冶金作用建立了许多中间包流场模型,但其对于满足当前生产高质量钢种要求是否具有实际意义尚无定论,因此本研究在对湍流抑制器的作用进行了深入研究的同时,采用中间包刺激响应曲线、中间包去除夹杂实验、流场观测实验对比不同中间包结构对流体流动特性的影响得到:(1)无控流条件下和单独使用湍流抑制器均不是理想的流场,应进行流场控制。
铝合金熔炼过程中常见夹杂及净化技术研究
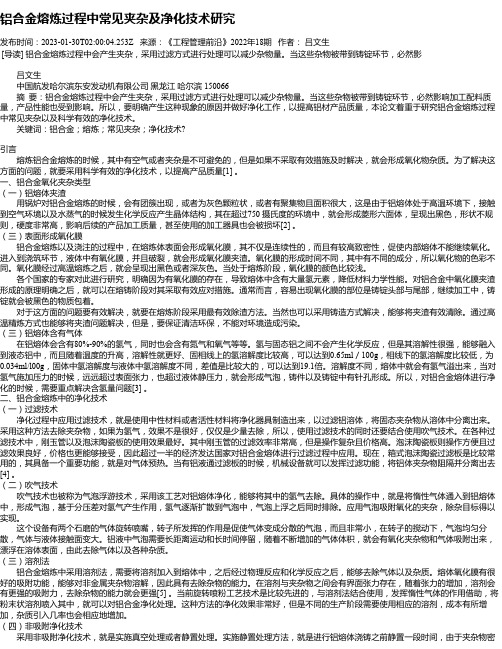
铝合金熔炼过程中常见夹杂及净化技术研究发布时间:2023-01-30T02:00:04.253Z 来源:《工程管理前沿》2022年18期作者:吕文生[导读] 铝合金熔炼过程中会产生夹杂,采用过滤方式进行处理可以减少杂物量。
当这些杂物被带到铸锭环节,必然影吕文生中国航发哈尔滨东安发动机有限公司黑龙江哈尔滨 150066摘要:铝合金熔炼过程中会产生夹杂,采用过滤方式进行处理可以减少杂物量。
当这些杂物被带到铸锭环节,必然影响加工配料质量,产品性能也受到影响。
所以,要明确产生这种现象的原因并做好净化工作,以提高铝材产品质量,本论文着重于研究铝合金熔炼过程中常见夹杂以及科学有效的净化技术。
关键词:铝合金;熔炼;常见夹杂;净化技术?引言熔炼铝合金熔炼的时候,其中有空气或者夹杂是不可避免的,但是如果不采取有效措施及时解决,就会形成氧化物杂质。
为了解决这方面的问题,就要采用科学有效的净化技术,以提高产品质量[1] 。
一、铝合金氧化夹杂类型(一)铝熔体夹渣用锅炉对铝合金熔炼的时候,会有团簇出现,或者为灰色颗粒状,或者有聚集物且面积很大,这是由于铝熔体处于高温环境下,接触到空气环境以及水蒸气的时候发生化学反应产生晶体结构,其在超过750 摄氏度的环境中,就会形成菱形六面体,呈现出黑色,形状不规则,硬度非常高,影响后续的产品加工质量,甚至使用的加工器具也会被损坏[2] 。
(三)表面形成氧化膜铝合金熔炼以及浇注的过程中,在熔炼体表面会形成氧化膜,其不仅是连续性的,而且有较高致密性,促使内部熔体不能继续氧化。
进入到浇筑环节,液体中有氧化膜,并且破裂,就会形成氧化膜夹渣。
氧化膜的形成时间不同,其中有不同的成分,所以氧化物的色彩不同。
氧化膜经过高温熔炼之后,就会呈现出黑色或者深灰色。
当处于熔炼阶段,氧化膜的颜色比较浅。
各个国家的专家对此进行研究,明确因为有氧化膜的存在,导致熔体中含有大量氢元素,降低材料力学性能。
对铝合金中氧化膜夹渣形成的原理明确之后,就可以在熔铸阶段对其采取有效应对措施。
简述炼钢过程中产生夹杂物去除方法

简述炼钢过程中产生夹杂物去除方法原则上,炼钢过程中产生的夹杂物能够通过向钢液/气体、钢/渣或钢/耐火材料界面移动而得到去除。
然而,必须同时采取措施防止钢液二次氧化、卷渣和使夹杂物重新回到钢液中,避免夹杂物的去除速度小于夹杂物生成的速度的情况。
对于从钢液中去除到钢液/气体、钢/渣界面的夹杂物必须能够脱离钢液进入界面,然后再从界面上脱离。
只有当夹杂物和气泡的接触角为180°时,才能通过钢液/气体界面将夹杂物去除,因此这种几率很小。
然而,如果钢液表面有覆盖渣,覆盖渣就能够吸收夹杂物粒子,即使接触角较小也能够将夹杂物脱除。
总的来说,由于没有足够的上浮时间,钢包(或中间包、结晶器)中小颗粒的一次脱氧产物只有少部分得到了上浮去除,斯托克斯方程决定了上浮力的大小。
例如,直径为100 μm的三氧化二铝夹杂物从钢液表面下2.5 m上浮到钢液表面需要4.8 min,对于直径为20 μm 的夹杂物,上浮时间增加到119min,对于去除夹杂物来说显然上浮是效率很低的。
通过气体或电磁搅拌钢液,增加夹杂物之间的碰撞能够使周态夹杂物聚集,液态夹杂物聚合为大颗粒夹杂物,从而提高夹杂物去除速率。
因此搅拌钢液是生产洁净钢的一个重要操作。
当通过吹氩搅拌钢液时,气体吹入点要尽可能地在钢包底部从而获得最大的搅拌能和搅拌区域,使气泡捕获更多的夹杂物。
固态夹杂物例如Al20、S102和Mg0等能够通过粘附到小气泡上,再上浮到钢渣界面。
夹杂物的直径越大,气泡越小,接触角越小,钢液表面张力越小,夹杂物去除的效率就越高。
普通液态夹杂物也是通过粘附到上浮的气泡去除的。
大多数的粘附方式为夹杂物成球形粘附到气泡内部。
有效去除夹杂物的最佳气泡直径为2—15 mm。
但是由于气泡在钢液中上浮过程迅速膨胀,因此很难达到最佳尺寸。
夹杂物可以随气泡尾流中上浮去除,尤其是小气泡,例如20 mm。
然而通过观察发现:到达钢/渣界面并破裂的气泡一般都明显大于这个尺寸,因此降低了辅助夹杂物上浮去除的能力。
钢液夹杂物的行为及去除

冶金熔体题目:钢液夹杂物的行为及去除 姓名: 王接喜 学号: 103511050 序号: 20 学院: 冶金科学与工程学院 专业: 有色金属冶金 完成时间: 2010- 12- 29Central South University钢液夹杂物的行为及去除王接喜(中南大学冶金科学与工程学院,长沙,410083)摘要:钢液中夹杂物的行为涉及的内容很广,其基本的物理过程大致包括:形核、生长、聚合、传递等,夹杂物去除可以视为传递过程的结果。
钢中夹杂物去除的主要环节为夹杂物的长大、上浮和分离。
钢中夹杂物去除技术有:气体搅拌-钢包吹氩、中间包气幕挡墙和RH-NK-RERM法;电磁净化-钢包电磁搅拌、中间包离心分离和结晶器电磁制动;渣洗技术;过滤器技术。
关键词:钢液;夹杂物;生长;去除;中间包;电磁场Behavior and removal of inclusions in molten steelWANG Jiexi, ZHOU Yongmao(School of Metallurgical Science and Engineering, Central South University, Changsha, China410083)Abstract:The behavior of inclusions in molten steel includes physical processes such as nucleation, growth, polymerization and transmission. The removal of inclusions can be seen as the result of transmission, which involves inclusion growth, floating and separating. The key progress on technique for removal of inclusions in steel is gas stirring-ladle argon blowing, gas shielding weir and dam in tundish, RH-NK-RERM method, electromagnetic cleaning-ladle electromagnetic stirring, tundish centrifugal separating and mold electromagnetic braking, slag washing and filter technique.Key words:molten steel, inclusions, growth, removal, tundish, electromagnetic field引言钢中非金属夹杂物事氧化物、硫化物、氮化物、硅酸盐等以及由它们组成的各种复杂化合物的统称[1]。
钢中氧化铝类夹杂的形成机理和去除效果的基础研究

钢中氧化铝类夹杂的形成机理和去除效果的基础研究钢中氧化铝类夹杂的形成机理和去除效果的基础研究随着工业化进程的不断推进,钢材作为一种重要的建筑和制造材料,其质量对于产品的性能和可靠性影响至关重要。
而钢中的夹杂物是影响钢材质量的主要因素之一。
尤其是在钢中出现的氧化铝类夹杂物对钢的性能及可靠性具有重要影响。
了解氧化铝类夹杂物的形成机理以及如何有效去除夹杂物,对于提高钢材质量至关重要。
1. 形成机理:1.1 氧化铝类夹杂物的来源:氧化铝类夹杂物主要由原料中的金属氧化物,包括铝氧化物(Al2O3)和其他氧化物(如FeO、MnO、SiO2等)等,通过不同的途径进入钢液中。
这些途径包括炼铁过程中的氧化物还原、原料中的氧化物溶解等。
金属氧化物还可能通过钢水接触管道材料或炉衬等形成和进入钢液中。
1.2 形成机制:氧化铝类夹杂物的形成机制与钢液中氧化还原反应和扩散过程有关。
其主要过程包括金属氧化物的溶解和形成夹杂物的水合反应。
2. 去除效果:2.1 传统的去除方法:传统的去除方法主要包括真空处理、浇注和渣化等。
真空处理可以通过增加钢液的气体溶解度,并通过气体从钢中释放的方式,达到去除夹杂物的效果。
浇注是通过改变钢液的流动状态,利用离心力等原理将夹杂物分离出去。
渣化则是通过加入适当的渣料,使夹杂物与渣料发生反应,形成易于分离的化合物,进而实现去除夹杂物的目的。
2.2 新的去除方法:近年来,随着科技的发展,一些新的去除方法也在不断涌现,包括磁场去除、超声波去除、激光去除等。
这些方法通过物理或化学的手段,对钢液中的夹杂物进行有效去除。
钢中氧化铝类夹杂的形成机理和去除效果的研究具有重要的意义。
通过深入了解氧化铝类夹杂物的形成机理,我们可以针对其形成机制采取相应的控制措施,从根本上减少夹杂物的产生。
研究新的去除方法有助于提高夹杂物去除的效率和质量。
这将对提高钢材的质量和性能,进而促进工业化进程产生积极的影响。
个人观点和理解:作为一名写手,通过撰写这篇文章,我对钢中氧化铝类夹杂的形成机理和去除效果有了更深入的了解。
钢中夹杂物得去除与控制
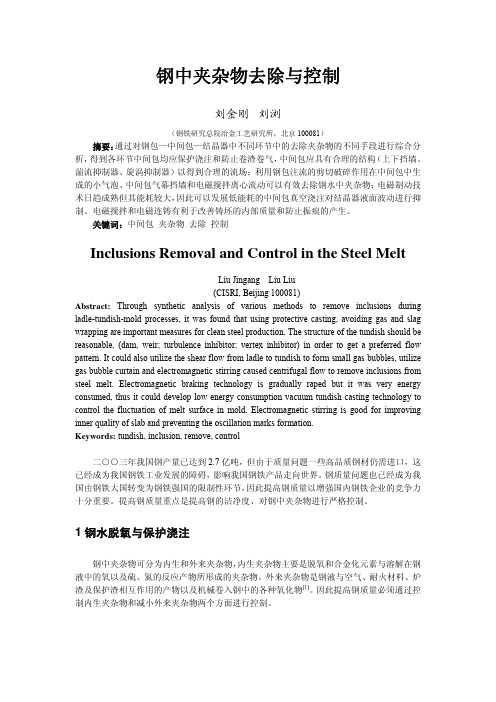
钢中夹杂物去除与控制刘金刚 刘浏(钢铁研究总院冶金工艺研究所,北京100081)摘要:通过对钢包—中间包—结晶器中不同环节中的去除夹杂物的不同手段进行综合分析,得到各环节中间包均应保护浇注和防止卷渣卷气,中间包应具有合理的结构(上下挡墙、湍流抑制器、旋涡抑制器)以得到合理的流场;利用钢包注流的剪切破碎作用在中间包中生成的小气泡、中间包气幕挡墙和电磁搅拌离心流动可以有效去除钢水中夹杂物;电磁制动技术日趋成熟但其能耗较大,因此可以发展低能耗的中间包真空浇注对结晶器液面波动进行抑制。
电磁搅拌和电磁连铸有利于改善铸坯的内部质量和防止振痕的产生。
关键词:中间包夹杂物去除控制Inclusions Removal and Control in the Steel MeltLiu Jingang Liu Liu(CISRI, Beijing 100081)Abstract: Through synthetic analysis of various methods to remove inclusions during ladle-tundish-mold processes, it was found that using protective casting, avoiding gas and slag wrapping are important measures for clean steel production. The structure of the tundish should be reasonable, (dam, weir; turbulence inhibitor; vertex inhibitor) in order to get a preferred flow pattern. It could also utilize the shear flow from ladle to tundish to form small gas bubbles, utilize gas bubble curtain and electromagnetic stirring caused centrifugal flow to remove inclusions from steel melt. Electromagnetic braking technology is gradually raped but it was very energy consumed, thus it could develop low energy consumption vacuum tundish casting technology to control the fluctuation of melt surface in mold. Electromagnetic stirring is good for improving inner quality of slab and preventing the oscillation marks formation.Keywords: tundish, inclusion, remove, control二○○三年我国钢产量已达到2.7亿吨,但由于质量问题一些高品质钢材仍需进口,这已经成为我国钢铁工业发展的障碍,影响我国钢铁产品走向世界。
钢中夹杂物的去除方法

钢中夹杂物的去除方法
钢中夹杂物的去除方法可以根据夹杂物的性质和形状来选择适当的方法。
以下是一些常用的方法:
1. 磁性夹杂物的去除:如果夹杂物是磁性的,可以使用磁铁或电磁铁来吸附和清除夹杂物。
将磁铁或电磁铁放在钢材附近,使用磁力将夹杂物吸附在磁铁上,然后将磁铁与夹杂物一起移除。
2. 熔炼剂的去除:对于含有氧化物或硫化物夹杂物的钢材,可以使用熔炼剂来与夹杂物反应形成渣滓,并将其从钢中分离出来。
熔炼剂可根据夹杂物的成分和特性选择不同的化学物质。
3. 精炼处理:通过加热和冷却的方式,利用夹杂物与钢的差异性,使夹杂物凝固或浮于钢液表面,然后进行分离。
精炼处理包括真空精炼、气体精炼和浸渣精炼等方法。
4. 超声波清洗:通过将钢材浸泡在特殊的清洗液中,利用超声波震荡,使夹杂物从钢材表面或内部脱离,并被清洗液带走。
5. 机械加工:对于较大的夹杂物或粗大的颗粒夹杂物,可以通过机械加工(如切割、磨削、铣削等)的方法将其从钢材中去除。
以上是一些常用的去除钢中夹杂物的方法,具体的方法选择应根据材料的要求和夹杂物的性质进行决定。
在进行夹杂物去除时,需遵循相关的操作规程和安全操作要求。
精炼过程中夹杂物的控制

精炼过程中夹杂物的控制发布时间:2009-04-02 14:34:54研究表明精炼过程可以去除钢液中80%左右的夹杂物。
1 真空吹氩气搅拌去除夹杂物真空可以进一步脱氧去除夹杂物。
钢包吹氩的精炼原理是:氩气泡的清洗作用;氩气泡上浮带动的钢水流动。
其作用主要有:使包中钢液成分均匀;使包中钢液温度均匀,便于正确掌握铸温;搅动的钢液增加了钢中非金属夹杂碰撞、聚集长大的机会,使上浮的氩气泡把钢液中的非金属夹杂物和气体一起带到钢液表面,并被渣层所吸收。
2 加入粉剂进一步去除钢中的杂质元素特别是在RH精炼过程中深脱硫,在RH精炼时以气粉两相流喷入石灰(CaO)、石灰(Ca0)/萤石(CaF2)+硅钙粉(CaSi)、石灰(Ca0),萤石(CaF2)、Ca、Mg等粉剂,这些粉剂在钢液循环流动的过程中可以作为吸附夹杂物的载体,将很快弥散于钢液内部,并与钢液中的硫在钢液与粉剂颗粒界面处发生脱硫反应。
正是由于RH精炼过程中钢液独特的流动和混合特性,使其具有一些显著的冶金效果:可使钢液的氧位降得更低,从而保证有效地脱硫;在脱硫的同时还可有效地脱气;可最大限度地消除顶渣对脱硫的影响;能为脱硫提供更好的动力学条件。
3 钢液中夹杂物的改性对钢中夹杂物MnS和A1203改性的原理是:钙与硫、氧均有很强的亲和力,其脱硫产物CaS和脱氧产物CaO易与钢中的A1203反应化合,形成低熔点的钙铝酸盐(mCaO·nA1203)复合夹杂物,这种夹杂物易于上浮,排出钢液进入顶渣,起到进一步净化钢水和对A1203夹杂物改性的作用。
当有A1203存在的条件下形成钙铝酸盐,它具有较高的硫容量,可以吸收脱硫后钢中剩余的硫。
随着钢液的冷却,硫在钙铝酸盐中溶解度的降低,硫化物以硫化钙的形式析出,抑制钢水在此过程中MnS的总量和聚集程度,并将MnS部分或全部改性为CaS,导致最后形成内部含钙铝酸盐、外壳包围着硫化钙层的复合夹杂物,或是CaS与Mn 的复合相,从而改善钢的各向异性,起到了钙作为硫的变性剂作用。
废铝重炼去除杂质的方法
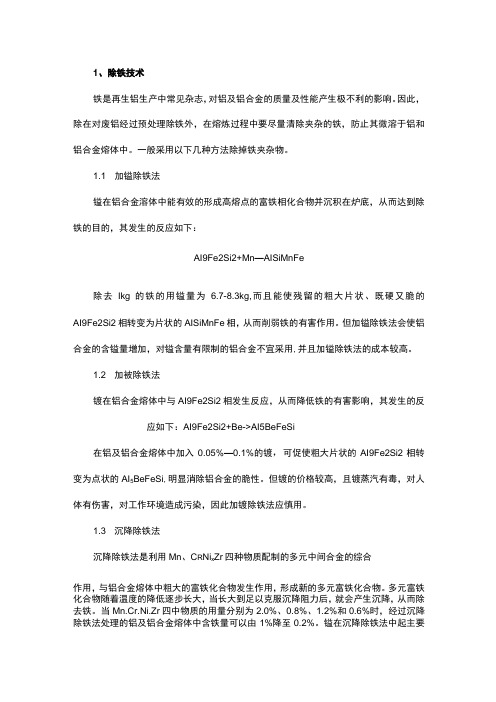
1、除铁技术铁是再生铝生产中常见杂志,对铝及铝合金的质量及性能产生极不利的影响。
因此,除在对废铝经过预处理除铁外,在熔炼过程中要尽量清除夹杂的铁,防止其微溶于铝和铝合金熔体中。
一般采用以下几种方法除掉铁夹杂物。
1.1 加镒除铁法镒在铝合金溶体中能有效的形成高熔点的富铁相化合物并沉积在炉底,从而达到除铁的目的,其发生的反应如下:AI9Fe2Si2+Mn—AISiMnFe除去Ikg的铁的用镒量为 6.7-8.3kg,而且能使残留的粗大片状、既硬又脆的AI9Fe2Si2相转变为片状的AISiMnFe相,从而削弱铁的有害作用。
但加镒除铁法会使铝合金的含镒量增加,对镒含量有限制的铝合金不宜采用,并且加镒除铁法的成本较高。
1.2 加被除铁法镀在铝合金熔体中与AI9Fe2Si2相发生反应,从而降低铁的有害影响,其发生的反应如下:AI9Fe2Si2+Be->AI5BeFeSi在铝及铝合金熔体中加入0.05%—0.1%的镀,可促使粗大片状的AI9Fe2Si2相转变为点状的AI5BeFeSi,明显消除铝合金的脆性。
但镀的价格较高,且镀蒸汽有毒,对人体有伤害,对工作环境造成污染,因此加镀除铁法应慎用。
1.3 沉降除铁法沉降除铁法是利用Mn、C R Ni x Zr四种物质配制的多元中间合金的综合作用,与铝合金熔体中粗大的富铁化合物发生作用,形成新的多元富铁化合物。
多元富铁化合物随着温度的降低逐步长大,当长大到足以克服沉降阻力后,就会产生沉降,从而除去铁。
当Mn.Cr.Ni.Zr四中物质的用量分别为2.0%、0.8%、1.2%和0.6%时,经过沉降除铁法处理的铝及铝合金熔体中含铁量可以由1%降至0.2%。
镒在沉降除铁法中起主要除铁作用,路虽然在除铁作用上不及镒,但其抗氧化烧损的性能较好,加入镇的主要目的是降低镒、珞残留所产生的脆性,加入错除了能起除铁的作用之外,还兼有细化晶粒的作用。
1.4 过滤除铁法过滤除铁法是利用铝合金熔体中的富铁相杂质在较低的温度和较长的保温时间下发生偏聚的原理,采用机械过滤的方法将聚集长大的富铁相物质除去。
夹杂物去除方法
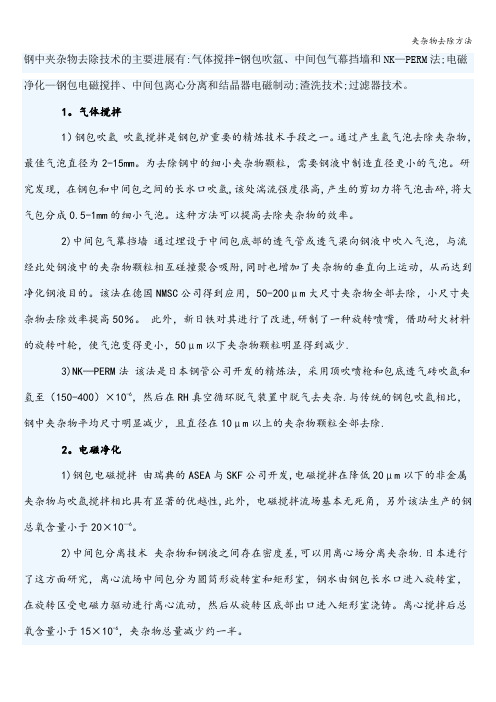
钢中夹杂物去除技术的主要进展有:气体搅拌-钢包吹氩、中间包气幕挡墙和NK—PERM法;电磁净化—钢包电磁搅拌、中间包离心分离和结晶器电磁制动;渣洗技术;过滤器技术。
1。
气体搅拌1)钢包吹氩吹氩搅拌是钢包炉重要的精炼技术手段之一。
通过产生氩气泡去除夹杂物,最佳气泡直径为2-15mm。
为去除钢中的细小夹杂物颗粒,需要钢液中制造直径更小的气泡。
研究发现,在钢包和中间包之间的长水口吹氩,该处湍流强度很高,产生的剪切力将气泡击碎,将大气包分成0.5-1mm的细小气泡。
这种方法可以提高去除夹杂物的效率。
2)中间包气幕挡墙通过埋设于中间包底部的透气管或透气梁向钢液中吹入气泡,与流经此处钢液中的夹杂物颗粒相互碰撞聚合吸附,同时也增加了夹杂物的垂直向上运动,从而达到净化钢液目的。
该法在德国NMSC公司得到应用,50-200μm大尺寸夹杂物全部去除,小尺寸夹杂物去除效率提高50%。
此外,新日铁对其进行了改进,研制了一种旋转喷嘴,借助耐火材料的旋转叶轮,使气泡变得更小,50μm以下夹杂物颗粒明显得到减少.3)NK—PERM法该法是日本钢管公司开发的精炼法,采用顶吹喷枪和包底透气砖吹氩和氢至(150-400)×10-6,然后在RH真空循环脱气装置中脱气去夹杂.与传统的钢包吹氩相比,钢中夹杂物平均尺寸明显减少,且直径在10μm以上的夹杂物颗粒全部去除.2。
电磁净化1)钢包电磁搅拌由瑞典的ASEA与SKF公司开发,电磁搅拌在降低20μm以下的非金属夹杂物与吹氩搅拌相比具有显著的优越性,此外,电磁搅拌流场基本无死角,另外该法生产的钢总氧含量小于20×10—6。
2)中间包分离技术夹杂物和钢液之间存在密度差,可以用离心场分离夹杂物.日本进行了这方面研究,离心流场中间包分为圆筒形旋转室和矩形室,钢水由钢包长水口进入旋转室,在旋转区受电磁力驱动进行离心流动,然后从旋转区底部出口进入矩形室浇铸。
离心搅拌后总氧含量小于15×10-6,夹杂物总量减少约一半。
采用var工艺对特殊钢枝晶细化及夹杂物去除的控制方法
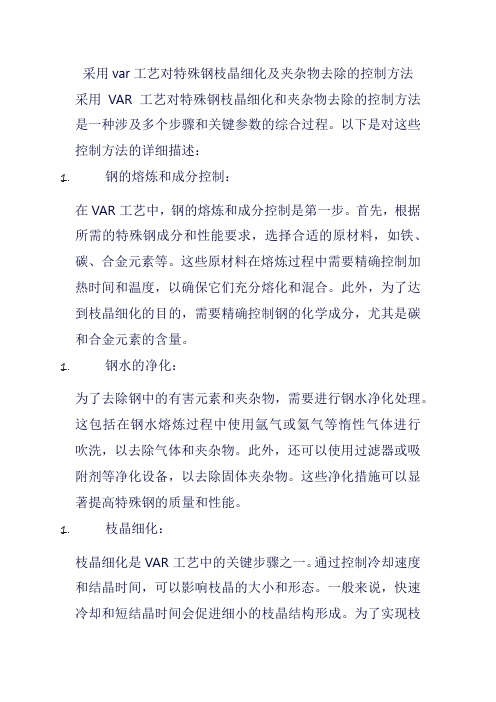
采用var工艺对特殊钢枝晶细化及夹杂物去除的控制方法采用VAR工艺对特殊钢枝晶细化和夹杂物去除的控制方法是一种涉及多个步骤和关键参数的综合过程。
以下是对这些控制方法的详细描述:1.钢的熔炼和成分控制:在VAR工艺中,钢的熔炼和成分控制是第一步。
首先,根据所需的特殊钢成分和性能要求,选择合适的原材料,如铁、碳、合金元素等。
这些原材料在熔炼过程中需要精确控制加热时间和温度,以确保它们充分熔化和混合。
此外,为了达到枝晶细化的目的,需要精确控制钢的化学成分,尤其是碳和合金元素的含量。
1.钢水的净化:为了去除钢中的有害元素和夹杂物,需要进行钢水净化处理。
这包括在钢水熔炼过程中使用氩气或氦气等惰性气体进行吹洗,以去除气体和夹杂物。
此外,还可以使用过滤器或吸附剂等净化设备,以去除固体夹杂物。
这些净化措施可以显著提高特殊钢的质量和性能。
1.枝晶细化:枝晶细化是VAR工艺中的关键步骤之一。
通过控制冷却速度和结晶时间,可以影响枝晶的大小和形态。
一般来说,快速冷却和短结晶时间会促进细小的枝晶结构形成。
为了实现枝晶细化,可以采用水冷或强制风冷等冷却方法,并精确控制冷却速度。
此外,通过添加适当的细化剂或变质剂,如铝、钛或硼等元素,可以进一步改善枝晶结构。
1.夹杂物去除:在VAR工艺中,夹杂物的去除也是重要的一步。
夹杂物对特殊钢的性能产生负面影响,因此需要尽可能减少它们的数量和大小。
通过控制熔炼和净化过程中的气氛和质量分数,可以减少夹杂物的生成。
此外,使用电磁搅拌或超声波振动等物理方法,可以促进夹杂物的浮出和去除。
为了更有效地去除夹杂物,还可以在钢水中添加吸附剂或过滤器等净化设备。
1.热处理和轧制:在VAR工艺中,热处理和轧制也是重要的步骤。
热处理可以改变钢的显微组织和性能,而轧制可以进一步细化组织结构并提高产品的尺寸精度。
通过控制热处理温度、时间和冷却速度,可以影响特殊钢的相变过程和显微组织结构。
在轧制过程中,采用控制轧制工艺参数和道次分配等方法,可以进一步细化组织结构并提高产品的机械性能。
- 1、下载文档前请自行甄别文档内容的完整性,平台不提供额外的编辑、内容补充、找答案等附加服务。
- 2、"仅部分预览"的文档,不可在线预览部分如存在完整性等问题,可反馈申请退款(可完整预览的文档不适用该条件!)。
- 3、如文档侵犯您的权益,请联系客服反馈,我们会尽快为您处理(人工客服工作时间:9:00-18:30)。
钢中夹杂物去除技术的主要进展有:气体搅拌-钢包吹氩、中间包气幕挡墙和NK-PERM法;电磁净化-钢包电磁搅拌、中间包离心分离和结晶器电磁制动;渣洗技术;过滤器技术。
1.气体搅拌
1)钢包吹氩吹氩搅拌是钢包炉重要的精炼技术手段之一。
通过产生氩气泡去除夹杂物,最佳气泡直径为2-15mm。
为去除钢中的细小夹杂物颗粒,需要钢液中制造直径更小的气泡。
研究发现,在钢包和中间包之间的长水口吹氩,该处湍流强度很高,产生的剪切力将气泡击碎,将大气包分成0.5-1mm的细小气泡。
这种方法可以提高去除夹杂物的效率。
2)中间包气幕挡墙通过埋设于中间包底部的透气管或透气梁向钢液中吹入气泡,与流经此处钢液中的夹杂物颗粒相互碰撞聚合吸附,同时也增加了夹杂物的垂直向上运动,从而达到净化钢液目的。
该法在德国NMSC公司得到应用,
50-200μm大尺寸夹杂物全部去除,小尺寸夹杂物去除效率提高50%。
此外,新日铁对其进行了改进,研制了一种旋转喷嘴,借助耐火材料的旋转叶轮,使气泡变得更小,50μm以下夹杂物颗粒明显得到减少。
3)NK-PERM法该法是日本钢管公司开发的精炼法,采用顶吹喷枪和包底透气砖吹氩和氢至(150-400)×10-6,然后在RH真空循环脱气装置中脱气去夹杂。
与传统的钢包吹氩相比,钢中夹杂物平均尺寸明显减少,且直径在10μm以上的夹杂物颗粒全部去除。
2.电磁净化
1)钢包电磁搅拌由瑞典的ASEA与SKF公司开发,电磁搅拌在降低20μm 以下的非金属夹杂物与吹氩搅拌相比具有显著的优越性,此外,电磁搅拌流场基本无死角,另外该法生产的钢总氧含量小于20×10-6。
2)中间包分离技术夹杂物和钢液之间存在密度差,可以用离心场分离夹杂物。
日本进行了这方面研究,离心流场中间包分为圆筒形旋转室和矩形室,钢水由钢包长水口进入旋转室,在旋转区受电磁力驱动进行离心流动,然后从旋转区底部出口进入矩形室浇铸。
离心搅拌后总氧含量小于15×10-6,夹杂物总量减少约一半。
3)结晶器电磁制动利用向上的电磁力阻止从浸入式水口流出的钢液并改变其方向,借此减小钢液的穿透深度,促使夹杂物上浮分离。
近年来,日本川崎公司开发出了全幅三段电磁制动技术,将下段磁场应用于二次制动,采用后,即使在2.5m/min以上的高速浇铸时,也不会有卷渣发生。
3.渣洗
电渣重熔是渣洗的典型代表,该技术已成为特钢行业必不可少的关键设备。
对于轴承钢GCr15,采用该技术后,其寿命提高到原来的3.5倍。
渣洗过程实际就
是转炉出钢后的钢渣变性处理!出钢时加入的各种造渣料!具体操作差不多是从出钢到1/3时开始加入造渣料及各种合金!钢水精炼渣洗也就是底吹氩加造渣料造渣的过程。
4.过滤器
主要通过机械拦截、表面吸附作用去除夹杂物。
美国SELEE钢铁研制的过滤器应用在中间包上,夹杂物去除效率提高了40-80%;日本千叶研制的陶瓷狭
孔过滤器,在最佳情况下能全部去除≥20μm的夹杂;国内宝钢在其中间包上也使用了CaO质过滤器。
但目前,过滤器比表面积有限,难以满足钢水连续过滤要求,仅限用于高纯净高价位钢材生产。
(成王)。