热轧卷取机夹送辊对板带表面质量影响
热轧质量缺陷及产生原因
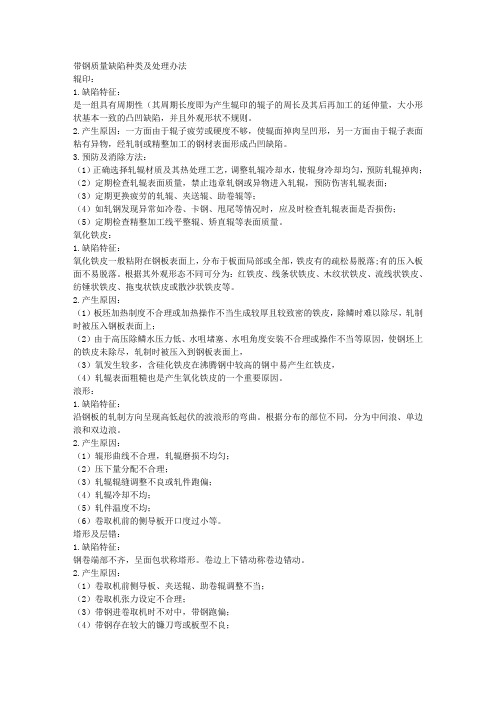
带钢质量缺陷种类及处理办法辊印:1.缺陷特征:是一组具有周期性(其周期长度即为产生辊印的辊子的周长及其后再加工的延伸量,大小形状基本一致的凸凹缺陷,并且外观形状不规则。
2.产生原因:一方面由于辊子疲劳或硬度不够,使辊面掉肉呈凹形,另一方面由于辊子表面粘有异物,经轧制或精整加工的钢材表面形成凸凹缺陷。
3.预防及消除方法:(1)正确选择轧辊材质及其热处理工艺,调整轧辊冷却水,使辊身冷却均匀,预防轧辊掉肉;(2)定期检查轧辊表面质量,禁止违章轧钢或异物进入轧辊,预防伤害轧辊表面;(3)定期更换疲劳的轧辊、夹送辊、助卷辊等;(4)如轧钢发现异常如冷卷、卡钢、甩尾等情况时,应及时检查轧辊表面是否损伤;(5)定期检查精整加工线平整辊、矫直辊等表面质量。
氧化铁皮:1.缺陷特征:氧化铁皮一般粘附在钢板表面上,分布于板面局部或全部,铁皮有的疏松易脱落;有的压入板面不易脱落。
根据其外观形态不同可分为:红铁皮、线条状铁皮、木纹状铁皮、流线状铁皮、纺锤状铁皮、拖曳状铁皮或散沙状铁皮等。
2.产生原因:(1)板坯加热制度不合理或加热操作不当生成较厚且较致密的铁皮,除鳞时难以除尽,轧制时被压入钢板表面上;(2)由于高压除鳞水压力低、水咀堵塞、水咀角度安装不合理或操作不当等原因,使钢坯上的铁皮未除尽,轧制时被压入到钢板表面上,(3)氧发生较多,含硅化铁皮在沸腾钢中较高的钢中易产生红铁皮,(4)轧辊表面粗糙也是产生氧化铁皮的一个重要原因。
浪形:1.缺陷特征:沿钢板的轧制方向呈现高低起伏的波浪形的弯曲。
根据分布的部位不同,分为中间浪、单边浪和双边浪。
2.产生原因:(1)辊形曲线不合理,轧辊磨损不均匀;(2)压下量分配不合理;(3)轧辊辊缝调整不良或轧件跑偏;(4)轧辊冷却不均;(5)轧件温度不均;(6)卷取机前的侧导板开口度过小等。
塔形及层错:1.缺陷特征:钢卷端部不齐,呈面包状称塔形。
卷边上下错动称卷边错动。
2.产生原因:(1)卷取机前侧导板、夹送辊、助卷辊调整不当;(2)卷取机张力设定不合理;(3)带钢进卷取机时不对中,带钢跑偏;(4)带钢存在较大的镰刀弯或板型不良;(5)卷取机卸卷时将钢卷头部拽出。
热轧卷板生产工艺流程及常见缺陷辨识及原因

缺陷介绍(表面类) 铁皮灰轧入
产生原因:精轧经长期生产,大量堆积金属粉尘、水、油等物质的混合物, 当积累到一定程度,掉落至轧件表面,经过后续轧制碾压嵌入轧件表面。 宏观特征:多呈彗星状(有颜色较淡的“尾巴”),目视可观测到嵌入 的金属颗粒及黑色油脂残留物。
35
缺陷介绍(表面类) 红铁皮
产生原因:加热炉中生成的氧化亚铁(FeO)与析出的硅(SiO2),在高 温环境结合生成红褐色的硅酸亚铁(Fe2SiO4),黏附于板坯表面; 宏观特征:呈条带状分布,缺陷呈红褐色。
440、SPFH540-590、QStE340-700TM、S355MC-S700MC酸洗热轧钢带、汽
车用高强钢;420L-700L汽车大梁钢、330CL-590CL车轮钢等汽车结构钢热 轧钢带及管线钢、石油套管钢、焊瓶钢、低合金结构钢及花纹板热轧钢
带等。
铁素体贝氏体高扩孔钢等先进高强钢( AHSS )热轧钢带和屈服强度 550MPa以上超高强钢带,已批量投放市场。
产生原因:成分中含有P 等促进氧化的元素、高温环境轧制等原因,造成 轧件表面金属快速氧化; 宏观特征:呈云雾状,目视可观察到氧化金属浮于表面。
33
缺陷介绍(表面类) 氧化铁皮(板道系)
产生原因:轧件在高温、高速轧制过程中,由于辊道被动转、辊道死辊、 辊道弯曲变形、辊面磨损等原因,表面造成划伤、挫伤缺陷,轧件表面破 损,氧化铁颗粒堆积在破损处,在后续轧制变形过程中,被碾压入轧件。 宏观特征:缺陷位置基本固定,形貌类似划伤、挫伤。
卷取机 (全液压三助卷辊地下卷取机)
全流程监控仪表
进口美国 NDC 公司设备,生产 全程宽度监控,检测精度偏差 0.05mm。另外在宽度控制方面粗轧 运 用 立 辊 控宽 调宽 , 采 用 AWC 及 SSC宽度控制功能。
地卷夹送辊对钢卷卷形质量的影响与改进

求 。在最后道 次带 钢经层 流冷却后 ,通过 输 出辊道 、 地 卷对 中导 位进入 地卷 夹送辊 ,由夹送辊 对带 头进
2 l年第4 0O 期
张智 :地卷夹送辊对钢卷卷形质量 的影 响与 改进
行牵引 和夹持 ,将带头送 人地卷 芯轴与助卷 辊之 间,
1欢 不 o
完成带钢的穿带动作 ;此后夹送辊按穿带压力对带钢
热 轧炉 卷 轧机 为紧凑 型双 机架 可逆 式轧 机 次往返轧制 。
第 六 道次地 卷设 备进 人设置 状态 ,夹送 辊从最 大辊 缝 7m 2 m关闭到穿带设 定位 置 ( 常夹送辊 的辊缝按 通 带 钢 目标 厚度的 8 % 给定 ) 5 ,以满足地卷机 的穿带要
2 地 卷 夹送辊 控 制 工 艺及 设 备 组成
21 地 卷 夹 送 辊 控 制 工 艺 .
的重要设备 , 主要 功能是与地卷对 中导位 、助卷辊 其
配合 完成 带钢 在地卷 机 的穿带 、卷 取及 协助 钢卷 带 尾定 位等 。在 地上 卷取 机穿 带和 卷取过 程 中 ,如果 地卷夹送辊 位置 、压力 、速 度偏 差较大 或设置不 当 ,
图 1 地 卷 工 艺 流 程 图
Fi gur Pr es i r m f pc e1 oc sD ag a o U oHe r
带钢卷取 时就会 因失张而导致钢卷 出现错层 、塔形或
松卷 ,直接影响钢卷 的卷形质量 ,不 利于产 品运输 和 后续生产 。为了解决 出现 的问题 ,对 地卷夹送辊 的位 置控制 、压力设定 、速度控制的精度 等关键影 响因素 进行研究 ,并提 出了解决措施 。
进行夹 持 ,在地卷芯 轴与夹送辊 之间建立卷 取张力 ,
22 设备组成及控 制原理 .
卷取夹送辊转矩和张力

卷取夹送辊是轧钢厂精轧机组的重要组成部件之一,它的主要作用是控制带钢的张力,保证带钢在卷取过程中的形状和质量。
卷取夹送辊的转矩和张力是卷取夹送辊的两个重要参数,下面将对这两个参数进行详细介绍。
一、卷取夹送辊转矩卷取夹送辊转矩是指在卷取过程中,卷取夹送辊电机所输出的转矩。
卷取夹送辊转矩的大小直接影响到带钢的卷取效果和形状质量。
在轧钢生产过程中,如果卷取夹送辊转矩不足,会导致带钢在卷取过程中出现松卷、层间错位等问题,严重影响带钢的质量和形状。
因此,在轧钢生产过程中,需要根据实际情况调整卷取夹送辊电机的输出转矩,保证带钢的卷取效果和质量。
卷取夹送辊转矩的控制方法主要有两种:一种是通过调节卷取夹送辊电机的电流来控制转矩;另一种是通过调节卷取夹送辊的液压系统来控制转矩。
其中,通过调节电机电流来控制转矩的方法比较常用。
在调节电机电流时,需要根据实时的轧制力和转矩反馈来进行调整,以保证带钢的卷取效果和质量。
卷取夹送辊张力是指在卷取过程中,带钢在卷取夹送辊之间所承受的拉力。
卷取夹送辊张力的大小直接影响到带钢的形状和质量。
在轧钢生产过程中,如果卷取夹送辊张力不足,会导致带钢在卷取过程中出现波浪、层间错位等问题,严重影响带钢的质量和形状。
因此,在轧钢生产过程中,需要根据实际情况调整卷取夹送辊的张力大小,以保证带钢的形状和质量。
卷取夹送辊张力的控制方法主要有两种:一种是通过调节卷取机的速度来控制张力;另一种是通过调节卷取夹送辊的液压系统来控制张力。
其中,通过调节卷取机速度来控制张力是比较常用的方法。
在调节卷取机速度时,需要根据实时的张力反馈和轧制力来进行调整,以保证带钢的形状和质量。
在实际轧钢生产过程中,卷取夹送辊的转矩和张力是相互影响的。
如果转矩不足,会导致张力不稳定;如果转矩过大,会导致带钢在卷取过程中出现压痕等问题。
因此,在轧钢生产过程中,需要对卷取夹送辊的转矩和张力进行协调控制,以保证带钢的卷取效果和质量。
三、总结本文对卷取夹送辊的转矩和张力进行了详细介绍,并阐述了它们在轧钢生产过程中的重要性。
薄板热轧工艺对不锈钢表面质量的影响及优化

薄板热轧工艺对不锈钢表面质量的影响及优化不锈钢是一种耐腐蚀性能优异的钢种,广泛应用于食品加工、化工装备、医疗设备等领域。
而薄板热轧工艺对不锈钢表面质量的影响及优化,则是确保不锈钢制品质量的关键。
薄板热轧工艺对不锈钢表面质量的影响主要体现在以下几个方面:首先,轧辊温度的控制。
轧辊温度是指轧辊与板材接触的温度,过高或过低的轧辊温度会导致不锈钢表面质量下降。
如果轧辊温度过高,会引起板材表面烧结或者出现凹凸不平;如果轧辊温度过低,则会导致板材表面较粗糙。
其次,轧制压力和过程控制。
轧制压力是指轧机施加在板材上的压力,合理的轧制压力可以使板材表面均匀光洁。
同时,合理的过程控制也能够影响不锈钢表面质量,如加热温度、保温时间等。
此外,润滑剂的选择和使用也对不锈钢表面质量有很大的影响。
润滑剂主要起到减少轧制过程中的摩擦和损耗的作用,合适的润滑剂能够有效地提高不锈钢表面的光洁度和平整度。
最后,冷却过程的控制。
冷却过程是将轧制后的热板材迅速冷却到室温,合理的冷却过程可以控制不锈钢表面组织的形成,进而影响不锈钢表面质量。
如果冷却速度过快,会导致板材内部组织不均匀;如果冷却速度过慢,会使不锈钢表面出现晶间腐蚀等问题。
针对薄板热轧工艺对不锈钢表面质量的影响,我们可以从以下几个方面进行优化:首先,合理选择合适的工艺参数,如轧辊温度、轧制压力、润滑剂的使用量等。
可以通过试验和实践,不断调整这些参数,以达到最佳的不锈钢表面质量。
其次,加强对冷却过程的控制。
可以通过改变冷却介质和冷却速度来优化不锈钢表面的质量。
同时,在冷却过程中,可以适当增加板材的延展性,以提高表面光洁度。
此外,合理使用润滑剂,选择适合的润滑剂类型和使用方法,以减少摩擦和损耗,并提高不锈钢表面的光洁度和平整度。
最后,定期对生产设备进行维护和保养,确保设备处于良好的工作状态。
并且,加强监测和检验工作,及时发现和解决潜在问题,以保证不锈钢表面质量的稳定和可靠。
总之,薄板热轧工艺对不锈钢表面质量有着重要的影响,通过合理选择工艺参数、加强对冷却过程的控制、合理使用润滑剂以及设备的维护和保养等措施,可以有效地提高不锈钢表面质量,确保制品符合质量标准,满足使用需求。
三判断题(轧钢工)

三判断题A级试题:1.轧件的变形抗力越大,轧辊辊缝的弹跳值越小。
( × )2.在板带钢轧制时,前后张力的加大,使宽展减小。
( √ )3.浪板是钢板表面的长度方向或宽度方向呈现高低起伏的波浪形弯曲。
( √ )4.轧机机架抵抗弹性变形的能力称为轧机刚性。
( √ )5.轧辊硬度通常指轧辊工作表面的硬度,它决定轧辊的耐磨性。
( √ )6.当测量厚度较厚时,采用β射线测厚仪。
(×)7.精轧机组间活套越高越好控制。
(×)8.热轧后的层流冷却过程相当于热处理工艺的淬火过程。
(×)9.在一个换辊周期内,一般是先轧窄规格,后轧宽规格。
(×)10.退火的目的是降低硬度,提高塑性,减小残余应力,消除钢中的组织缺陷。
(√)11.铁碳相图是研究碳素钢的相变过程,以及制定热加工及热处理等工艺的重要依据。
( √ )12.退火是将钢加热到一定温度,保温后再快速冷却的热处理工艺。
( × )13.导板用来引导轧件正确进出孔型,使轧件在水平方向不致左右偏斜和歪扭。
(√)14.变形抗力越大,其塑性越低。
( × )15.轧制生产实践表明,所轧制的钢越软,则其塑性就越好。
( × )16.热电偶是参与温度控制的基本元件。
( √ )17.合格的轧制产品数量占总检验量的百分数是成材率。
( × )18.孔洞、气泡、裂纹(发纹、龟纹)、结疤、拉裂、折叠、表面夹杂和分层等质量缺陷一旦在带钢上发现就坚决判为废品。
( √ )19.轧制节奏是指轧制一块钢所用的总时间。
( × )20.热连轧活套的作用是对张力进行补偿。
(√)21.带钢宽度由窄变宽时可以不换辊就直接轧制。
(×)22.常规板带轧机是以轧辊直径来标称的。
(×)23.带钢中S含量过高要产生冷脆,p含量过高要产生热脆。
( √ )24.当应力小于金属的屈服极限δs时,金属发生塑性变形。
攀钢热连轧卷取机夹送辊稳定性分析

・ 带钢头尾异常 , 造成夹送辊进入故障模式 ; ・ 夹送辊两侧压力或辊缝偏差大 , 造成卷形很
差;
攀 钢 15 4 0毫米 热 轧板 厂三 、 四号 地下 卷取 机 建 成 于 20 03年 5月 , 是该 厂 为 了改 善产 品结 构和 扩 大 生 产能力 而 新建 的 。夹送 辊 的控 制 由 G E公 司 生产 的 IN V TO N O A IN控 制器 来完 成 , 控 制分 为 液 压 和 其
取机背后的交流异 步电机传动。众所周知 , 在地下
卷 取机 区域 , 夹送 辊 的作 用 就 是 对 来 自于精 轧 机 的
带 钢进 行 “ ” “ ” “ ” 意 思 是对 带 钢 施 加 夹 和 送 :夹 的
夹 持力 ; 送 ”的意 思 是 将 带 钢 送 进 卷 取 机 进 行 卷 “
g n tS rp Mi a g Ho ti l l,i a e n i to u e e wa o c n ue t. s th s b e nr d c d t y t o q ri Alo,i ha e n r s a c e e sa h t s b e e e r h d t t — h b lt fp n h r l. ii o i c o1 y
大行 程动 作 以后 , 液压 缸 实 际动 作 行 程 偏 移 和 超 对 出水平 范 围之 外进行 保 护 。
在压力模式 , 液压压力传感器被用于测量和控 制带钢接触压力。第一种压力调节模式使用两侧液 压缸独立的压力传感器 , 来保证夹送 辊的压 力均匀 的分布在传动侧和操作侧夹送辊上。然而使用这种 模式 , 当楔形带钢卷取时会 造成夹送辊倾斜 。第二 种压力调节模式是使用合压力模式 和一个微分的位
钢铁加工业中热轧工艺对板材表面质量和界面粗糙度的影响研究

钢铁加工业中热轧工艺对板材表面质量和界面粗糙度的影响研究热轧是钢铁加工业中常用的一种工艺,其通过加热钢坯至较高温度,然后在辊道上进行辗压变形,最终得到所需的板材。
热轧工艺对板材的表面质量和界面粗糙度都有一定的影响,下面将从这两个方面对其进行研究。
首先,热轧工艺对板材的表面质量有重要影响。
在热轧过程中,钢坯的表面会受到来自辊道的力和热能的作用,从而产生各种变形和损伤,进而影响最终的表面质量。
一方面,辊道上的辊道力会使钢坯的表面出现压痕和划痕,同时还会导致板材的变形和扭曲。
另一方面,热轧过程中的高温会使钢材表面氧化,产生氧化皮或锈蚀,进而降低表面的光洁度和美观度。
此外,热轧过程中的冷却速度也会影响板材的表面质量,较快的冷却速度会导致板材表面出现裂纹和麻点。
其次,热轧工艺对板材的界面粗糙度也有一定的影响。
热轧过程中,钢坯和辊道之间的相互作用会产生界面的微观变形和摩擦,从而在板材表面形成一定的界面粗糙度。
辊道的压力和温度等工艺参数会直接影响界面的摩擦和变形程度,进而决定界面粗糙度的大小。
同时,辊道表面的加工质量和润滑条件等也会对界面粗糙度产生影响。
界面粗糙度的增大会导致板材的接缝部分出现裂纹和断层,进而降低板材的强度和可靠性。
为了研究热轧工艺对板材表面质量和界面粗糙度的影响,需要采用实验方法进行定量分析。
首先,可以选择不同的工艺参数,如辊道的压力、温度和冷却速度等,来进行实验。
通过调整这些工艺参数,可以得到不同的热轧条件下的板材,并对其表面质量和界面粗糙度进行测量和评估。
其次,还可以采用不同的表征方法,如光学显微镜观察、扫描电子显微镜观测和表面粗糙度仪测量等,来对板材的表面质量和界面粗糙度进行分析。
最后,可以根据实验结果,确定不同工艺参数下的最佳热轧条件,以得到具有良好表面质量和界面粗糙度的板材。
综上所述,热轧工艺对板材的表面质量和界面粗糙度都有一定的影响。
实验研究可以进一步揭示热轧工艺对板材的影响机制,并为优化工艺参数提供科学依据。
热轧带钢表面质量缺陷原因分析

热轧带钢表面质量缺陷原因分析【摘要】热轧带钢表面质量缺陷是影响产品质量的重要因素之一。
本文通过分析研究发现,造成热轧带钢表面质量缺陷的主要原因包括热轧工艺参数调整不当、原料质量问题、轧辊磨损和松动、冷却系统故障以及设备设施不良等。
为解决这些问题,加强热轧带钢生产工艺控制尤为重要,调整工艺参数、提高原料质量管理水平、定期检查设备设施并进行及时维护保养是关键措施。
只有通过全面的措施,才能有效提高热轧带钢表面质量,确保产品的质量稳定性和生产效益。
【关键词】热轧带钢、表面质量缺陷、工艺参数、原料质量、轧辊磨损、冷却系统、设备设施、生产工艺控制、原料质量管理、设备维护。
1. 引言1.1 热轧带钢表面质量缺陷原因分析热轧带钢表面质量缺陷是指在热轧生产过程中,带钢表面出现的各种瑕疵和缺陷,会影响带钢的使用性能和外观质量。
热轧带钢表面质量缺陷的原因分析是热轧生产过程中非常重要的一环,只有找准表面质量缺陷的根本原因,才能有效地采取相应的措施进行改进和解决。
热轧带钢表面质量缺陷的原因主要可以分为以下几个方面:首先是热轧工艺参数调整不当导致表面缺陷,比如轧制过程中温度控制不当、轧辊间隙不合适等,都会直接影响带钢表面的质量;其次是原料质量问题引起的表面缺陷,如果原料本身质量不合格或存储条件不当,也有可能导致带钢表面出现缺陷;轧辊磨损和松动、冷却系统故障、设备设施不良等因素也会对热轧带钢表面质量造成影响。
加强热轧带钢生产工艺控制的重要性不言而喻。
提高原料质量管理水平、定期检查设备设施并及时维护保养也是预防和解决热轧带钢表面质量缺陷的有效途径。
通过分析各种可能的原因,找出问题所在并及时处理,才能确保热轧带钢表面质量的稳定和提升。
2. 正文2.1 热轧工艺参数调整不当导致表面缺陷热轧工艺是影响热轧带钢表面质量的重要因素之一。
如果工艺参数调整不当,很容易导致表面缺陷的产生。
热轧工艺参数包括轧制温度、轧制速度、轧制力等多个方面的参数,这些参数之间存在一定的相互关系,如果一个参数调整不当,就会对其他参数造成影响,导致表面质量缺陷的出现。
热轧带钢表面质量缺陷原因分析

热轧带钢表面质量缺陷原因分析【摘要】本文主要对热轧带钢表面质量缺陷的原因进行了分析。
带钢表面氧化是造成质量缺陷的重要因素之一,其主要导致表面出现氧化物,影响产品表面质量。
带钢表面夹杂物也是一个常见问题,会使产品表面出现不良痕迹。
轧辊表面缺陷和卷取过程中的质量缺陷也会对表面质量造成影响。
涂油不均匀也容易引起质量缺陷。
热轧带钢表面质量缺陷的原因是多方面的,需要通过合理的生产技术和工艺控制来减少和避免。
通过深入分析这些原因,可以帮助生产厂家改进工艺,提高产品质量,从而提升市场竞争力。
【关键词】热轧带钢、表面质量缺陷、原因分析、氧化、夹杂物、轧辊表面缺陷、卷取过程、涂油不均匀、生产技术、工艺控制。
1. 引言1.1 热轧带钢表面质量缺陷原因分析带钢表面氧化是导致质量缺陷的一个重要因素。
在热轧过程中,带钢表面会与空气中的氧气发生氧化反应,形成氧化膜,使表面出现氧化斑点、氧化皮等缺陷。
带钢表面还存在着夹杂物,如硫化物、磷化物等,会导致表面不平整、坑洞等问题。
轧辊表面的缺陷也是一个常见原因,轧辊表面的不洁净、磨损不均匀等问题都会直接影响带钢表面的质量。
在卷取过程中,也容易引起质量缺陷。
卷取张力不均匀、卷取速度过快等因素都会导致带钢表面出现皱纹、印痕等问题。
涂油不均匀也是一个常见问题,涂油不足或涂油过多都会导致表面质量不佳。
热轧带钢表面质量缺陷的原因是多方面的,需要生产厂家通过合理的生产技术和工艺控制来减少和避免这些问题,提高产品的质量和市场竞争力。
2. 正文2.1 带钢表面氧化带钢表面氧化是热轧带钢表面质量缺陷中常见的一种现象。
其主要原因包括以下几个方面:带钢在高温轧制过程中易受氧化影响,尤其是在轧制过程中的高温区域,带钢表面易与空气中的氧气发生化学反应而产生氧化膜。
带钢在冷却过程中容易因表面残余的热量造成局部高温,使得表面氧化的速度增加,从而形成氧化层。
带钢在运输、堆放等过程中也容易受到空气中的氧气和水分的影响,导致表面氧化。
本钢热连轧厂平整分卷机组常见表面质量缺陷产生原因及控制措施

本钢热连轧厂平整分卷机组常见表面质量缺陷产生原因及
控制措施
本钢热连轧厂平整分卷机组是一种关键设备,用于对热轧钢卷进行平整分卷,以满足客户对钢材尺寸和表面质量的要求。
然而,在生产过程中,常常会出现表面质量缺陷,给产品质量和客户满意度带来不良影响。
本文将分析本钢热连轧厂平整分卷机组常见的表面质量缺陷产生原因及控制措施。
1. 钢卷表面出现夹杂物
钢卷表面出现夹杂物是由于钢坯表面存在杂质或氧化皮等原因导致的。
为了避免这种情况的发生,应尽可能在热轧过程中削减或清除钢坯表面的杂质和氧化皮,以确保钢卷表面的质量。
2. 钢卷表面出现划伤
钢卷表面出现划伤是由于钢卷在运输、卷取或加工过程中受到的外力损伤而导致的。
为了避免这种情况的发生,应在运输、卷取和加工过程中尽可能减小外力的影响,同时对钢卷表面进行定期检查和维护。
3. 钢卷表面出现皱纹
钢卷表面出现皱纹是由于在轧制过程中,辊缝不平或轧制参数不当导致的。
为了避免这种情况的发生,应对辊缝进行检查和维护,确保辊缝平整。
同时,在轧制过程中应根据钢材尺寸和硬度调整轧制参数,以确保钢卷表面的质量。
4. 钢卷表面出现烧伤
钢卷表面出现烧伤是由于轧制过程中过度加热或冷却不当导致的。
为了避免这种情况的发生,应根据钢材的热处理要求和硬度调整轧制温度和速度,并在过程中对钢卷进行冷却控制,以确保钢卷表面的质量。
综上所述,保证本钢热连轧厂平整分卷机组表面质量的关键在于对生产过程中可能出现的问题进行及时的检查和维护,并根据钢材尺寸和质量要求调整轧制参数和控制温度和速度。
只有这样才能确保钢卷表面的质量,满足客户需求,并提高产品质量和客户满意度。
浅析热轧带钢表面质量控制

浅析热轧带钢表面质量控制作者:薛彦珍来源:《科学导报·学术》2020年第36期摘;;要:现代化建设当中,钢铁行业的竞争压力日渐加大,如何减少钢铁生产过程中的成本投入与质量问题开始成为行业关注的热点。
本文将主要讨论热轧带钢表面常见的质量问题与控制措施,仅供参考。
关键词:热轧带钢;质量控制;措施1.热轧带钢表面常见质量缺陷与发生原因(1)麻面麻面是指带钢热轧过程中表面形成较多无规则凹坑现象,原因主要以下三点:其一,氧化铁皮压入。
轧件表面覆盖的氧化铁皮未去除干净,经过轧制后被压入其中。
其二,轧辊的轧制量过大造成辊面老,轧制量过多是造成热轧带钢麻面的重要原因。
其三,轧辊的冷却方法不正确或冷却能力不够,导致轧辊表面严重磨损。
(2)裂纹热轧带钢表面也容易出现裂纹,原因有:连铸坯浇筑过程未有效把握浇筑过程中的速度,影响钢凝固与冷却导致钢表面出现气孔、接痕等。
轧制时应力过于集中造成表面裂纹,比如划痕、划伤等。
钢中含有游离态氮元素,加速裂纹的拓展,甚至可能引起钢材断裂。
(3)压痕压痕是热轧带钢一常见质量问题。
一方面轧辊或者夹送辊的冷却不良造成表面明显凸起,机组运行时产品表面就会出现规律性压痕。
另一方面成品或前面道次轧辊表面掉块也会造成产品不同程度规律性压痕。
(4)划痕就划痕而言,其可能是接触了尖锐的棱角,钢带表面产生了一条或者多条划痕,具体原因有:轧线沉头螺丝冒出、过渡板或间隙处有废钢片残留、活套辊/自由辊转动不灵活或活套角度过大、三角区滚动体或卷取输送辊堵转等。
在卧式卷取系统中,输送轨道未正常运转,使得轧件堆叠等也会造成表面划伤,影响热轧带钢表面质量。
(5)氧化铁皮压入氧化铁皮可以被划分为一次氧化与二次氧化铁皮,其中一次氧化铁皮不规则分布于带钢之上,在炉内就已形成,一次氧化铁皮主要由四氧化三铁构成,该种物质为暗红色固体,被轧入钢材中很难彻底清除,导致钢带呈现翘皮等表面缺陷。
二次氧化铁皮发生于初次除鳞后,氧化铁皮的厚度与氧化时间和反应温度相关。
热轧板带表面质量缺陷原因及相关控制措施初探

热轧板带表面质量缺陷原因及相关控制措施初探作者:刘伟潘腾来源:《中国科技博览》2017年第27期[摘要]随着社会经济飞速发展,我国热轧板带掀起了一阵建设热潮,自动化水平的提升也为热轧板带的发展提供了基础。
决定钢板整体质量的重要因素之一就是热轧板带表面的质量,因此,要想保证钢板的产品质量和生产效率,就必须保证热轧板带表面的质量。
热轧板带表面质量会受到很多因素的影响,而且热轧板带的生产环境极其恶劣,所以造成热轧板带表面质量缺陷的原因有很多。
基于此,本文就热轧板带表面质量缺陷原因及相关控制的措施进行探讨,希望可以降低因热轧板带表面质量造成的损失,从而提高企业的经济效益。
[关键词]板带热轧;表面质量缺陷;措施中图分类号:TG335.5 文献标识码:A 文章编号:1009-914X(2017)27-0117-01引言:热轧板带表面质量的好坏和钢板产品的质量和生产线的生产效率有直接关系,因此要想保证企业的效益,就必须保证热轧板带表面的质量。
造成热轧板带表面质量缺陷的因素不仅有高温、水汽、粉尘,还会因为精轧末机架导板较高、精轧末机架过渡倒板磨损严重、螺杆凸出和轧线辊道出现自由辊或转速过慢等原因造成热轧板带表面刮伤,给企业造成经济损失。
基于此,本文对热轧板带表面质量缺陷的原因进行具体的分析,并提出相关控制的措施,希望可以给相关技术人员提供一些有价值的参考意见,从而有效的提高热轧板带表面的质量。
一、研究背景根据检查研究,压入的氧化铁皮基本属于精轧过程中和精轧后、卷取前生成的“三次氧化铁皮”从板坯加热到粗轧、精轧及之后的冷却,整个热轧带钢生产过程一直伴随着氧化。
按热轧带钢生产流程,将不同工序产生的氧化铁皮分为4种:加热炉内生成的为“一次氧化铁皮”,粗轧过程中和粗轧完成后生成的为“二次氧化铁皮”,精轧过程中和精轧后、卷取前生成的为“三次氧化铁皮”,带钢卷取及随后冷却至室温表面生成的为“四次氧化铁皮”[1]。
二、热轧板概述热轧板卷是以板坯(主要为连铸坯)为原料,经加热后由粗轧机组及精轧机组制成带钢。
探讨卷取设备功能精度检测与调整方法,改善卷型

探讨卷取设备功能精度检测与调整方法,改善卷型【摘要】根据首钢迁钢最近推行的设备功能精度,详细介绍了热连轧生产线卷取设备的检测与调整方法 , 明确提出了一些重要的安装精度要求标准。
为热连轧生产线卷取设备提供了一套可行的设备精度管理方法。
尤其通过对夹送辊、卷筒及助卷辊的使用磨损状况分析,确定在当前状况下,如何快速准确对设备重要部位进行检测、调整和记录,对研究辊型,改善板型,寻求最佳辊型来弥补对卷型的影响,起到至关重要的作用。
此外,通过寻求最佳辊型对夹送辊和助卷辊的修复提供重要依据。
【关键词】卷取机 ; 检测与调整 ; 设备精度 ; 方法;辊型0 引言卷取机设备系统是热连轧生产线的关键设备之一 , 其主要由侧导板、夹送辊、卷筒、助卷辊等设备组成。
在自动化水平较高的热连轧生产线上 , 产品卷形质量对卷取机设备系统的安装精度要求非常高 , 一旦出现安装或使用维护精度偏差 , 就会造成产品卷形超差 , 严重影响下道工序正常使用。
目前首钢迁钢热轧卷取机设备助卷辊和卷筒在轧制过程中磨损严重,其中卷筒、助卷辊在规定的使用期限内 , 中部1100mm 左右磨损严重。
另外 , 由于中间磨损而造成间隙 , 使得进行零调压靠时 , 中间辊缝实际值与显示值有较大偏差 , 对卷型影响严重 , 而且产品规格越薄越明显。
因此 , 有必要对热连轧卷取设备检测与调整方法进行探讨,以求更好的记录和及时掌握和了解卷筒及助卷辊的磨损状况,对辊型进行研究 , 寻求最佳辊型来弥补对卷型的影响。
因此 , 搞好卷取设备安装精度检测工作并明确提供一些安装精度要求的数值对提高设备安装精度非常重要。
1 侧导板检测项目侧导板设备安装于卷取机夹送辊之前 , 侧导板的移动方向垂直于轧制方向 , 侧导板起预先对中和侧向引导带钢的作用。
侧导检测项目有 : 侧导板对中度 , 侧导板与辊道的相对间隙值。
1.1 侧导板对中度将标定块放置在侧导板中央 , 在侧导上方架好 0.5mm 钢丝 , 首先挂线坠校核标定块中心与轧制中心线是否重合 , 重合度应小于 1 mm; 其次检查侧导板相对中心线是否对中 , 对中度应小于 1 mm。
热轧卷缺陷对冷轧产品影响(62页)

钢接触 磨损后产生沟槽而对带钢表面产生损伤。 3 、精轧导卫件异常磨损造成局 部不平对带钢下表面
产生损伤。
三 、表面缺陷形貌
黑皮卷划伤
白皮卷划伤
连续划伤
3 、划伤缺陷发生在400系钢种较多。
三 、表面缺陷与产生原因
4 、热轧氧化铁皮 定义与形态 带钢表面上存在沿轧制方向具有一定连续
性条状 、呈疏松针状 、散沙状或片状的氧化铁皮压入 。有 时亦会出现一至两条断断续续压入 。不同不锈钢钢种均可 发生 , 以304与430钢种居多。
主要产生原因 1 、主要是板坯的除鳞效果不好 , 一次氧化皮没有被除鳞 去除 ,经 酸洗后氧化皮被洗掉所呈现的状态。 2 、过程温度控制过高 , 次生氧化铁皮在轧制时又被压入 到钢卷的 表面上 , 。 3 、机架内除尘效果不好 ,板道不干净 , 异物压入带钢 表面。
目前不锈钢分公司生产的铁素体不锈钢SUS430 、半马 氏体不锈钢如410S存在边裂问题 ,410S的边裂率约10% , 纵观宝钢铁素体钢和半马氏体钢较短的生产历史 , 前一 阶 段410S边裂问题比较严重 ,通过攻关 ,边裂率明显下降; 可见高温和常温存在两相组织的400系不锈钢 , 其生产难 度和主要质量瓶颈就是边裂问题。
如果狭缝控制过大 ,用户在使用中无法剪切 除干净 ,使带钢成材率受到影响 ,不锈带钢卷通 过冷轧后一般用在制管行业上较多 。
三 、表面缺陷与产生原因
3 、热轧划伤 定义与形态 在酸洗或未酸洗时发现的 带钢上下表面的机械损伤 ,
平行于轧制方向分布 ,连续 或断续性的产生的锋利的线 状伤痕 ,程度严重的酸洗过 后在伤痕部位上咬入氧化铁 皮,大多在带钢下表面全长上 连续发生 ,有时是发亮的划 伤 , 也有时是暗划伤 ,在整 个轧线任意可能与带钢接触 的部位均可发生 。所有钢种 均可能发生。
带钢轧制时产生的主要缺陷与分析

带钢轧制时产生的主要缺陷与分析在热带轧机上轧制带钢所形成的缺陷最主要有下列几种:(1)结疤。
在板坯清理时对裂口及裂纹没有全部清除干净,结果在轧制时形成结疤;板坯加热时过热,特别是铬不锈钢,轧制时在带钢上形成结疤。
带钢坯表面大量集结的非金属夹杂物,也是产生结疤的原因。
(2)裂边。
板坯侧面缺陷未全面清除干净,这是带钢裂边的原因。
(3)过热。
板坯在过高温度下长时间停留会引起过热。
过热板坯轧制时会产生大裂口和剥落;邻近过热的部分出现细裂纹,细裂纹在进一步轧制时会变成结疤。
为防止板坯过热必须严格遵守规定的加热制度,尤其是高温下的均热时间。
加热铁素体类钢时,温度超过850℃后必须快速加热。
(4)机械损伤。
轧入碎屑、压痕、划痕是热轧不锈带钢表面最有特征的缺陷。
轧人碎屑和压痕缺陷是由于坯料上的结疤块、裂边在导卫上摩擦时有碎片落到带钢表面上以及其他东西被轧辊或矫直机辊子压人而形成的。
划痕大部分是在带钢运动时,下表面与不光滑的导卫、辊面不平的辊子及被动辊相接触时形成的。
上表面划痕通常是在未卷紧运送时卷层间摩擦造成的。
在卷取中,带钢与卷取机成形辊和喂料辊之间发生摩擦时,带钢表面上会产生很多短条状划伤。
(5)带钢厚薄不均。
带钢长度上的厚度不均匀与沿板坯长度加热的均匀性及带钢在机架间张力值有关。
带钢的前端和后端一般比中部厚一些,这是因为在连续式精轧机组中带钢端部没有张力的缘故。
带钢后端一般比前端厚,这是温度不同所致热轧带钢开裂的改进热轧带钢生产的工艺流程:铁液一铁液预处理一顶底复吹转炉一脱氧合金化一吹氩一板坯连铸一铸坯检验一加热一粗轧高压水除鳞一立辊轧一可逆式粗轧一中轧一热卷箱一精轧高压水除鳞一精轧一层流冷却一卷取一入库。
热轧带钢在生产检验及用户使用过程中常出现的开裂现象,并对开裂带钢进行了化学成分及低倍和金相检验分析。
结果表明,化学成分符合要求,铸坯存在皮下气泡、带钢存在非金属夹杂及游离渗碳体是带钢出现开裂主要原因,针对以上情况给你针对性改进建议,具体如下。
2012年第九届热轧轧钢工题库(总计510题)(1)
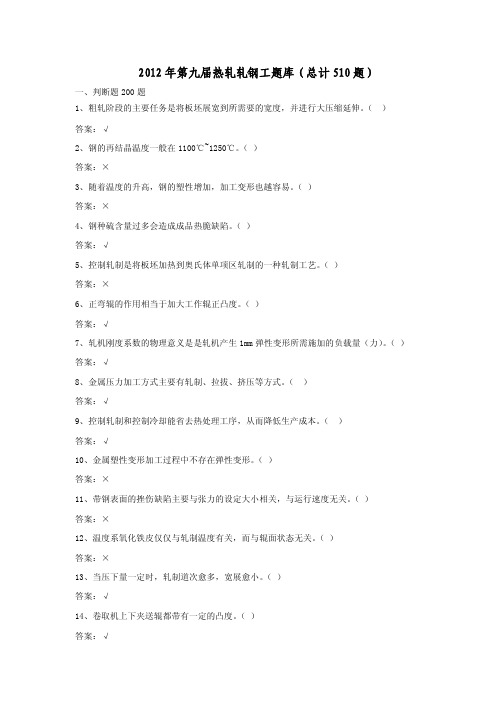
2012年第九届热轧轧钢工题库(总计510题)一、判断题200题1、粗轧阶段的主要任务是将板坯展宽到所需要的宽度,并进行大压缩延伸。
()答案:√2、钢的再结晶温度一般在1100℃~1250℃。
()答案:×3、随着温度的升高,钢的塑性增加,加工变形也越容易。
()答案:×4、钢种硫含量过多会造成成品热脆缺陷。
()答案:√5、控制轧制是将板坯加热到奥氏体单项区轧制的一种轧制工艺。
()答案:×6、正弯辊的作用相当于加大工作辊正凸度。
()答案:√7、轧机刚度系数的物理意义是是轧机产生1mm弹性变形所需施加的负载量(力)。
()答案:√8、金属压力加工方式主要有轧制、拉拔、挤压等方式。
()答案:√9、控制轧制和控制冷却能省去热处理工序,从而降低生产成本。
()答案:√10、金属塑性变形加工过程中不存在弹性变形。
()答案:×11、带钢表面的挫伤缺陷主要与张力的设定大小相关,与运行速度无关。
()答案:×12、温度系氧化铁皮仅仅与轧制温度有关,而与辊面状态无关。
()答案:×13、当压下量一定时,轧制道次愈多,宽展愈小。
()答案:√14、卷取机上下夹送辊都带有一定的凸度。
()答案:√15、钢表面的氧化铁皮按照厚度方向剖面金额分成三种,其中紧靠钢基体的一层最薄,成分是FeO,是很难通过酸洗除去的。
()答案:×16、张力可以起到降低轧制力和缓解带钢跑偏的作用。
()答案:√17、轧机的钢度系数K越大,轧机弹跳越小,产品的控制精度越好。
()答案:√18、所谓“自由轧制”就是轧制计划的编排不受带钢宽度和厚度的限制。
()答案:×19、轧辊辊面氧化膜剥落与轧制负荷相关,轧制负荷大氧化膜就容易剥落。
()答案:×20、氧化铁皮会使带钢表面粗糙,因此轧制时摩擦系数会增加。
()答案:×21、活套量的形成是由于钢在两相邻机架的轧制中金属秒流量差的积累的结果。
提高热轧卷取机夹送辊表面堆焊质量及使用寿命措施

118研究与探索Research and Exploration ·工艺流程与应用中国设备工程 2021.03 (下)热轧带钢卷取机夹送辊及助卷辊是热轧带钢生产线上的重要装备之一,担负着将轧制好的钢板导向、夹送的任务,夹送辊及助卷辊的辊面质量的好坏将直接影响钢板的质量。
目前,为了提高夹送辊的使用寿命,较经济的方法是在辊面堆焊一层具有特殊性能的材料,形成复合材料的工程结构,而特殊性能的焊接材料是其中的关键技术。
本课题重点针对夹送辊的失效形式进行分析,并有针对性地制定改进措施,以实现在线的正常使用。
1 夹送辊失效形式及改进措施夹送辊及助卷辊在线使用过程中的问题主要集中在气孔、夹渣、焊点问题、裂纹问题、辊面黏钢、压痕及焊道印问题,这些问题是直接影响热轧作业部生产顺畅和产品质量的突出问题,也是修复厂家必须严肃对待和解决的课题。
1.1 气孔、夹渣、焊点问题产生原因:焊丝、焊剂受潮,或堆焊过程中脱渣不彻底,导致辊面容易产生气孔、夹渣等缺陷。
对局部缺陷进行点焊后,上线使用会出现焊点问题。
解决措施:第一,堆焊前,对所用的焊材进行烘干处理,避免堆焊过程中气孔的产生。
第二,堆焊过程中发现气孔时,及时用角磨机进行打磨处理。
第三,每堆焊一遍,采用角磨机彻底对辊面进行打磨,确保两个焊道搭接位置的焊渣清理彻底。
第四,增加探伤环节,一是堆焊之前进行探伤,避免辊子因带缺陷堆焊导致堆焊后辊面存在气孔等缺陷;二是热处理缓冷后车削第一刀进行探伤处理,发现缺陷时,对缺陷位置进行打磨或车削,确定缺陷尺寸,需要堆焊时,重新对辊子进行预热、堆焊、热处理工序;三是辊子打磨前进行探伤,检查辊面是否存在缺陷。
第五,不允许对辊面进行任何局部的点焊处理,当出现气孔、夹渣等缺陷时,进行车削后再对缺陷位置整体堆焊,确保整个辊面的质量。
1.2 裂纹问题产生原因:(1)母材本身有裂纹,在堆焊过程中容易产生气孔或裂纹。
(2)焊接过程中不能保证层间温度,对于高硬度的辊子,在焊接过程中容易出现冷裂纹。
热轧带钢表面质量

钢的成分控制和热轧控轧工艺的研究,其各项性能指标也已得到很大提
高。
目前,困扰热轧带钢产品质量进一步提高的问题之一是表面质量
问题,特别是随着热轧带钢产品直接应用于结构件外表面,如轿车的外
覆件等,对其表面质量提出了更为苛刻的要求。从目前热轧带钢厂的情
况看,热轧钢卷封锁量有80 %以上是由于带钢表面质量问题造成的。
了防止脱碳的发生,可采用专门的保护气体,避免加热温
度过高,保温时间过长,在高温区快速加热,炉气保持中
性或还原性气氛,避免空气吸入炉内。
钢的氧化:
当炉气中充满氧化性气体(O2、CO2、H2O、SO2)时, 钢坯表面就将氧化而形成氧化铁皮。 防止方法是采用快速加热的方法。使高温集中在加热 段,采用微正压操作,减少冷空气从出钢口的吸入;在均 热段要采取减少空气量,造成不完全燃烧,以获得还原性 或中性气氛。
纵向裂缝缺陷
2 周期性缺陷:面缺陷
重度氧化铁皮 中度氧化铁皮 红铁皮
(1)重度氧化铁皮
分布在带钢的上下表面 形态特征:表现为在大块表面上大面积的
压入氧化铁皮,有点状、条纹状、面状。 典型原因:除鳞机没有除尽轧件表面的全
部氧化铁皮
重度氧化铁皮图片
(2)中度氧化铁皮:
点状氧化铁皮 压入氧化铁皮 M型 椒盐型氧化铁皮 小舟型氧化铁皮
非金属夹杂:在脱氧过程中,由于切割产生的熔化物流到钢 的内部产生夹杂所造成的。
外 部 的 气 孔:主要由于潮湿而使切割时的焊剂与 熔化物的流出所造成的。
孔洞:主要由于钢的脱氧不充分造成的。
三常见热轧板带产品的质量缺陷:
首先,要区分清楚轧制中的缺陷与伪缺陷:伪缺陷是 在于正常表面差异大到足够被系统检测的目标,但它不是 一个真正的表面缺陷。如带钢表面的水滴或污垢,这两个 都不是表面缺陷。
- 1、下载文档前请自行甄别文档内容的完整性,平台不提供额外的编辑、内容补充、找答案等附加服务。
- 2、"仅部分预览"的文档,不可在线预览部分如存在完整性等问题,可反馈申请退款(可完整预览的文档不适用该条件!)。
- 3、如文档侵犯您的权益,请联系客服反馈,我们会尽快为您处理(人工客服工作时间:9:00-18:30)。
热轧卷取机夹送辊对板带表面质量影响分析与对策
邓经济
(江苏沙钢集团有限公司钢板总厂江苏张家港 215625)
摘要:本文对沙钢1450热卷板生产线卷取夹送辊辊印、振纹、划伤等的成因进行了分析,提出了相应的预防措施,取得了较好的效果。
关键词:卷取机夹送辊;辊印;划伤;排骨纹;振纹;亮带;工艺技术;管理
1.背景
当今,随着各行各业的发展,用户对热轧带钢的质量要求越来越高。
沙钢1450热卷板生产线主要生产厚度为1.2~20mm、宽度750-1350mm。
对于小于2.0mm 的薄料,轧制时带钢头尾波浪大、头部容易轧碎,尾部容易烂边,板型不稳定,卷取夹送辊的压力不稳等等,卷取夹送辊对我们的带钢表面质量产生很大的影响,严重影响产品质量和合同的完成,给厂里效益和声誉带来了重大的损失。
在如今钢铁业竞争白热化时期,解决好批量性的带钢表面质量问题对提高板带产品实物质量,打造精品产品,提高市场占有率和声誉有着十分重要的意义。
本文对沙钢1450热卷板生产线夹送辊辊印、划伤等缺陷的成因进行了分析,提出了相应的预防措施,取得了较好的效果。
2.夹送辊功能【1】
夹送辊安装在卷取机前的主要功能:(1)利用异径辊的错位布置迫使带钢头部产生大的弯曲,引导带钢头部沿着导向板顺利地进入卷取机;(2)带钢卷上芯棒,且带钢尾部未离开F7之前,在F7和夹送辊之间,在夹送辊和芯棒之间进行张力分配;(3)带钢尾部离开F7之后在夹送辊与芯棒之间建立后张力。
3.夹送辊设备组成及控制原理【1】
夹送辊的设备组成为:下夹送
辊、上夹送辊、机架、机架辊、摇
臂装置、压紧辊、换向辊、辊缝调
整机构、辊前上导板、辊前下导板、
辊后上导板、辊后下导板、活门导
板、液压缸等,如图一。
带钢头部从精轧F7轧出,头部
被热检(HMD)检测并跟踪,夹送辊
传动开始设置速度,调节装置获得
带钢数据求得压下力和设置卷取的
辊缝,当带钢穿带完成,就由位置
调节控制转换到压力调节控制,在
卷取过程中,根据操作侧(OS)和
传动侧(DS)的压力,适时调节辊缝,图一
是压力保持相对平衡,在带钢尾部离开精轧F7后,夹送辊与芯棒产生后张力;当带钢离开夹送辊后,由压力控制转换为位置控制。
此时,根据热检(HMD)和新的理论值传送给调节器,为卷取下一块钢做好准备。
4.夹送辊辊印、划伤等缺陷成因及预防措施
夹送辊表面的好坏对我们带钢表面质量起到关键作用,夹送辊损坏对带钢产生的缺陷有:辊印、划伤、亮带、排骨纹、振纹、堆焊纹等等;针对这些缺陷,我们从原辊、磨辊、生产技术和生产设备管理等方面对夹送辊进行控制,让一个个问题得到迎刃而解。
4.1原辊
4.1.1夹送辊材质
夹送辊表面硬度应为60-80(肖氏硬度)。
4.1.2夹送辊表面堆焊
夹送辊表面堆焊是夹送辊生产最重要的工序,堆焊的质量直接影响到夹送辊的使用性能。
堆焊速度过快,焊缝不能堆满,冷却不及时,导致交界处焊缝组织疏松,性能和硬度都有很大的差异;堆焊速度过慢,已经冷却的焊接层,重新加热,组织和性能都发生变化,相应的表面质量也不相同。
卷钢过程中在受到板带磨损后,由于辊面组织和性能不均,磨损程度不一,辊面上就会被磨损得凹凸不平。
如图二所示,由于夹送辊上堆焊纹路导致带钢表面也有堆焊纹路。
夹送辊上堆焊纹路带钢表面
图二
4.2磨辊
磨辊阶段对夹送辊表面产生的缺陷主要有振纹,振纹产生原因是在磨夹送辊时,辊子表面软硬不均,砂轮内部致密程度不一样,辊子与砂轮接触时打滑,砂轮振动,就产生了如图三所示的振纹。
辊子上的振纹图三带钢上的振纹
控制振纹的有效方法:降低砂轮速度,减少磨辊车架进给量,减少砂轮进给量,选择优质砂轮。
生产实践:正常磨轧辊的砂轮速度是40r/min,当磨夹送辊时,降低速度,采用36 r/min,正常磨轧辊的车架进给量是3000r/min,采用2000 r/min。
4.3生产技术
4.3.1产生夹送辊辊印的原因及相应的预防措施
夹送辊上辊印和带钢表面辊印形态如图四,产生夹送辊辊印的原因:
1)F7头部轧碎,头部撞夹送辊,造成辊子粘钢;
2)F7甩尾,尾部叠层和烂尾,当进入卷取机夹送辊后,会在夹送辊上撞击,产生夹送辊辊印;
3)带钢头部撞击,带钢头部冲击上夹送辊或夹送辊缝设定过小造成头部挤压夹送辊粘钢;
4)侧导板压力过大或侧导板焊接焊缝不良将侧导板磨损,导致侧导板拉丝后掉在板带上,进入卷取机后压入夹送辊造成辊印;
5)夹送辊冷却水异常带钢表面得不到有效地冷却,辊面氧化膜不易形成,当带钢进入时易产生辊印;
6)板带头部过冷产生与二次除磷和层流冷却,板带头部过冷,头部硬度急剧提高,当进入夹送辊时,撞击产生辊印。
夹送辊上辊印带钢表面辊印
图四
采取措施:
1)通过严格执行工艺、优化二级模型、提高操作工的业务技能,控制板形,同时实施薄规格生产时采用抛钢时活套小套及抬辊缝来控制甩尾;
2)每次利用检修时间,对飞剪前及精轧区侧导板进行标定及对中性测量并调整,来保证精轧板型稳定;
3)若精轧发生甩尾,同时轧线上已经抽出的钢采用其它卷取机卷取并取样检查,卷取甩尾卷的卷取机要进行打磨后方可投入使用,若表面有不满足技术协议要求的质量问题必须停车换辊;
4)减小侧导板的压力;
5)调整夹送辊前侧喷的角度,同时班中要加强对侧喷的检查;
6)严格执行侧导板更换规定即换,加强对侧导板堆焊质量检查;
7)加强对硬而薄的钢种外表面质量的检查,热检必须在卷取机下平台对每卷外表面质量进行检查,一旦发现问题,立即通知当班调度主任处理;
8)加大夹送辊缝设定补偿,适当增加夹送辊辊缝设定,降低咬钢时夹送辊压力;
9)除鳞时序进行调整,确保中间坯头部刚到时开除鳞,防止头部过冷,同时提高层流
冷却的头部温度补偿,让头部不要过冷;
10)增加飞剪切头长度。
如图五,2010年7月-2011年7月夹送辊辊印次品卷数图,辊印得到了很好的控制。
图五夹送辊辊印次品卷数图
4.3.2产生夹送辊划线的原因及相应的预防措施
6月中旬周修更换1#卷取机夹送辊,由于安装不到位,导致卷取机活门磨损上夹送辊,造成上夹送辊辊面有多条凹凸不平的沟槽,导致带钢表面产生多条划痕(如图六所示)。
措施:1)每一次换完夹送辊,测量活门与夹送辊的间距,按照图纸要求0-0.8mm,根据实际情况不能大于2.0mm;2)平时生产现场做好夹送辊表面质量的检查;3)平时生产现场做好带钢表面质量的检查。
夹送辊表面划线带钢表面划线
图六
4.3.3产生夹送辊亮带的原因及相应的预防措施
亮带表面形态表现为:在光的照射下,带钢表面出现一条一条发亮的纵向条纹,如图七为夹送辊和带钢上的亮带图;带钢出现亮带的实质是带钢在横向上出现厚度差。
亮带产生原因:亮带是带钢与卷取夹送辊的局部接触,在夹送辊压力、夹送辊与卷筒间的张力共同作用,
使接触区域的带钢发生塑性变形造成。
采取措施:1)对于薄、软带钢,在尾部卷取时,在保证卷形、避免带钢打滑的前提下,尽量减少夹送辊的压力和夹送辊与卷筒的张力,可以减少亮带;2)控制精轧带钢横断面形状、控制精轧带钢凸度,缩短夹送辊的使用周期。
【2】
夹送辊上亮带带刚上亮带
图七
4.3.4产生夹送辊横向振纹的原因及相应的预防措施
横向振纹与亮带的区别就在于它是横向的,如图八,夹送辊表面振纹和相应的带钢表面振纹。
横向振纹产生原因:1)带钢精轧轧制时,带钢进入卷取夹送辊中浪大导致夹送辊振动加剧;2)卷取上下夹送辊速度差,夹送辊与带钢产生相对滑动;3)夹送辊的压力过大,在卷取时夹送辊局部受力大,磨损严重,产生振纹;夹送辊压力过少,辊子与钢之间产生相对滑动,产生振纹。
采取措施:1)压下手调节好板型;2)调节好夹送辊与带钢接触部分的线速度;3)夹送辊压力适中。
夹送辊表面振纹带钢表面振纹
图八
4.4生产与设备管理
4.4.1生产管理
实行标准化作业,制定夹送辊更换和使用管理规定:
1)夹送辊更换标准为每台卷钢量最多不超过20万吨;
2)若发现夹送辊表面磨损严重对带钢表面质量产生影响要及时更换;
3)热检工在生产过程中要加强对夹送辊和带钢表面质量的检查;
4)发现问题要及时向车间反馈,同时做好对下一班的交接,同时跟班工艺员加强监督;
5)每次检修前一天,工艺条线负责对夹送辊表面质量检查,发现问题要及时反馈给车间相关领导;
6)更换夹送辊后,卷取技术员和后区钳工要对活门高度、入口上导板与夹送辊间隙、夹送辊冷却水等进行检查。
4.4.2设备管理
1)采购夹送辊时,对夹送辊材质(尤其是硬度),夹送辊辊面质量进行仔细检查,选择质量有保障的厂家购置夹送辊;
2)磨辊间做好夹送辊的磨辊工作,仔细跟中异常辊,磨辊严格按照工艺要求执行;
3)吊辊和更换辊子时,保护好辊面,防止辊面损伤。
5、结语
通过对原辊、磨辊、生产工艺和生产设备管理全面系统的分析,原辊组织性能和表面质量,夹送辊辊缝和压力,板带头尾板型是产生卷取机夹送辊辊印、排骨纹、亮带、振纹等的重要原因,卷取机活门是产生卷取机夹送辊划伤的重要原因;针对性的采取相应的预防措施,取得了较好效果。
【1】沙钢1450工艺资料
【2】刘跃华、阎东宇等热轧带钢纵向亮带分析辽宁鞍钢股份有限公司。