丰田仓库管理七原则
丰田:规则创造神奇—进取、改变、创新
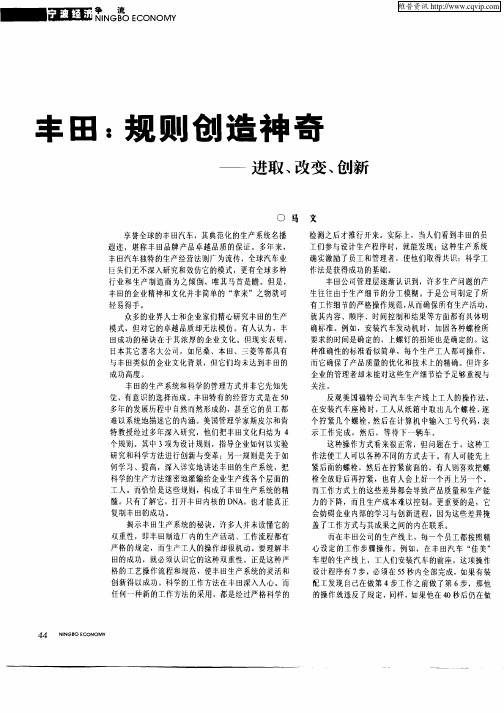
检测之后才推行开来。实际上,当人们看到丰田的员 工们参与设计生产程序时,就能发现;这种生产系统 确实激励了员工和管理者,使他们取得共识:科学工 作法是获得成功的基础。 丰田公司管理层逐渐认识到,许多生产问题的产 生往往由于生产细节的分工模糊。于是公司制定了所 有工作细节的严格操作规范, 从而确保所有生产活动, 就其内容、顺序、时间控制和结果等方面都有具体明 确标准。例如,安装汽车发动机时,加固各种螺栓所 要求的时间是确定的,上螺钉的扭矩也是确定的。这 种准确性的标准看似简单,每个生产工人都可操作。 而它确保了产品质量的优化和技术上的精确。 但许多 企业的管理者却未能对这些生产细节给予足够重视与
丰田的企业精神和文化并非简单的 “ 拿来”之物就可 轻易得手。 众多的业界人士和企业家们精心研究丰田的生产 模式,但对它的卓越品质却无法模仿。有人认为,丰 田成功的秘诀在于其浓厚的企业文化。但现实表明, 日本其它著名大公司,如尼桑、本田、三菱等都具有 与丰田类似的企业文化背景,但它们均未达到丰田的 成功高度。 丰田的生产系统和科学的管理方式并非它先知先 觉, 有意识的选择而成。 丰田特有的经营方式是在 5 0 多年的发展历程中自然而然形成的,甚至它的员工都 难以系统地描述它的内涵。美国管理学家斯皮尔和肯 特教授经过多年深入研究,他们把丰田文化归结为 4 个规则。其中3 项为设计规则,指导企业如何以实验 研究和科学方法进行创新与变革;另一规则是关于如 何学习、提高,深入详实地讲述丰田的生产系统,把 科学的生产方法细密地灌输给企业生产线各个层面的 工人。而恰恰是这些规则,构成了丰田生产系统的精 髓。 只有了解它,打开丰田内核的D A N ,也才能真正 复制丰田的成功。 揭示丰田生产系统的秘诀,许多人并未读懂它的 双重性,即丰田制造厂内却很机动。要理解丰 田的成功,就必须认识它的这种双重性。正是这种严 格的工艺操作流程和规范,使丰田生产系统的灵活和 创新得以成功。科学的工作方法在丰田深入人心。而 任何一种新的工作方法的采用,都是经过严格科学的
零部件库存管理
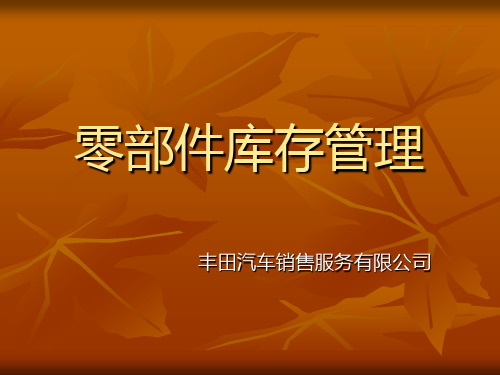
第二章 库存管理的目的
一、库存管理的目的 提高顾客满意度 CS NO.1
在顾客需要的时候, 在顾客需要的时候 及时供应零部件
以最合理的库存,获 以最合理的库存 获 取最大的经营收益
提供客户满意度:确保更高的供应率。 获取更多的利润:保持更低的库存量。
二、库存标准 1、供应率 是衡量库存供应率的指标,反映了库存满足客户 需求的水平。 2、库存度 是衡量库存效率的指标。 计算公式:库存度=库存数量/ 计算公式:库存度=库存数量/月均需求 ①为什么要减少库存量? ②供应率和库存率是一对矛盾的统一体 ③要保持适当的供应率(S/R)并减少库存度 ③要保持适当的供应率(S/R)并减少库存度 (S/M),需要回答两个问题: S/M),需要回答两个问题: ☆库存什么? ☆库存多少?
到货周期
安全库存周期
■MAD 是月平均需求量(单位:个/月),其确定要素: 是月平均需求量(单位:个/ ①按照所接订单 ②按照B/O的需求 ②按照B/O的需求 ③考虑L/S的需求 ③考虑L/S的需求 ④无论是B/O还是L/S需求,在统计计算MAD时要视具体情 ④无论是B/O还是L/S需求,在统计计算MAD时要视具体情 况而定。
二、大— 二、大—小订货原则 前提:按照既定订货机制订货 特点:阶段性的订货和发货 定义:在既定订货时机,实际库存量小于等于最小库存 量时,订货补充库存到最大订货量。 最小库存量可以自行设定,但是不能小于MAD× O/C+ 最小库存量可以自行设定,但是不能小于MAD×(O/C+ L/T) L/T)
三、大—大订货和大— 三、大—大订货和大—小订货原则比较 ○使用大— ○使用大—小订货原则进行零件库存补充管理,需 要在每次订货时点,实际库存小于等于库存最小 值时发出订货单,造成单次订货的数量较大,而 且需要较深的安全库存。订货周期不规律。 ○使用大— ○使用大—大订货原则进行零件库存补充管理,需 要在每次订货时点发出订货单。减少零件库存深 度。 ●结论:大— ●结论:大—大订货原则好,管理精度高 ☆减少安全库存天数 ☆均匀的订货和发货 ☆较少的每单订货数量,易于操作管理
TPS管理

TPS ,即丰田生产方式是Toyota Production System的缩写。
TPS的特点有以下四个方面:1、拉动式准时化生产要求以最终用户的需求为生产起点,强调物流平衡,追求零库存,要求上一道工序加工完的零件立即进入下一道工序。
生产线依靠看板传递信息。
生产节拍由人工干预、控制,重在保证生产中的物流平衡(对于每一道工序来说,均要保证对后道工序供应的准时化)。
由于采用拉动式生产,生产中的计划与调度实质上是由各个生产单元来完成,在形式上不采用集中计划,但操作过程中生产单元之间的协调则极为重要。
2、全面质量管理强调质量是生产出来而非检验出来的,由生产中的质量管理来保证产品的最终质量。
在每道工序进行时均注意质量的检测与控制,保证及时发现质量问题,培养每位员工的质量意识。
如果发现问题,立即停止生产,直至解决,从而保证不出现对不合格产品的失效加工。
3、团队工作方法(Team Work)每位员工在工作中不仅仅是执行上级的命令,更重要的是积极地参与,起到决策与辅助决策的作用。
组织团队的原则并不完全按行政组织来划分,而主要根据业务的关系来划分。
团队成员强调一专多能,工作的氛围是信任,以一种长期的监督控制为主,而避免对每一步工作的稽核,提高工作效率。
团队的组织是变动的,针对不同的事物,建立不同的团队,同一个人可能属于不同的团队。
4、并行工程(Concurrent Engineering)在产品设计开发期间,将概念设计、结构设计、工艺设计、最终需求等结合起来,保证以最快的速度按要求的质量完成。
TPS的另一大理念--零库存,就是随时反馈订货信息,实现生产与销售的并行化。
TPS最终目标是企业利润的最大化。
管理中的具体目标是通过消灭一切生产中的浪费来实现成本的最低化。
TPS通过准时化生产、全面质量管理、并行工程等一系列方法来消除一切浪费,实现利润最大化。
TPS最具特色的方法是,在组织生产时对消灭物流浪费的无限追求,即对物流环境的需求和内部的分权决策。
精益生产7个零目标
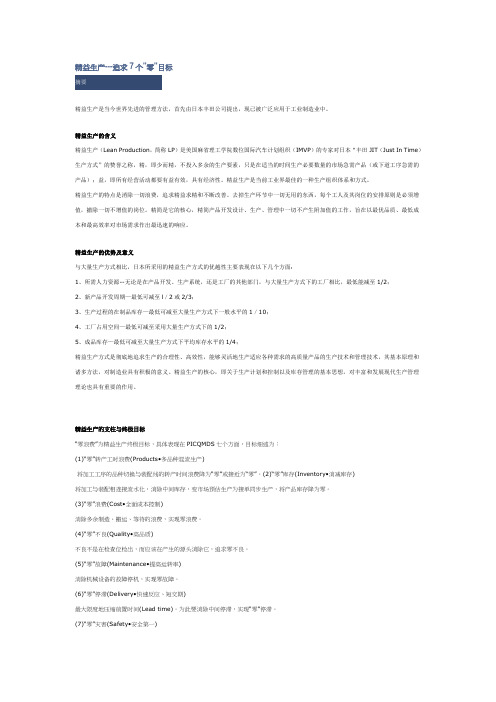
精益生产---追求7个"零"目标精益生产是当今世界先进的管理方法,首先由日本丰田公司提出,现已被广泛应用于工业制造业中。
精益生产的含义精益生产(Lean Production,简称LP)是美国麻省理工学院数位国际汽车计划组织(IMVP)的专家对日本“丰田JIT(Just In Time)生产方式”的赞誉之称,精,即少而精,不投入多余的生产要素,只是在适当的时间生产必要数量的市场急需产品(或下道工序急需的产品);益,即所有经营活动都要有益有效,具有经济性。
精益生产是当前工业界最佳的一种生产组织体系和方式。
精益生产的特点是消除一切浪费,追求精益求精和不断改善。
去掉生产环节中一切无用的东西,每个工人及其岗位的安排原则是必须增值,撤除一切不增值的岗位。
精简是它的核心,精简产品开发设计、生产、管理中一切不产生附加值的工作,旨在以最优品质、最低成本和最高效率对市场需求作出最迅速的响应。
精益生产的优势及意义与大量生产方式相比,日本所采用的精益生产方式的优越性主要表现在以下几个方面:1、所需人力资源--无论是在产品开发、生产系统,还是工厂的其他部门,与大量生产方式下的工厂相比,最低能减至1/2;2、新产品开发周期—最低可减至l/2或2/3;3、生产过程的在制品库存—最低可减至大量生产方式下一般水平的1/10;4、工厂占用空间—最低可减至采用大量生产方式下的1/2;5、成品库存—最低可减至大量生产方式下平均库存水平的1/4;精益生产方式是彻底地追求生产的合理性、高效性,能够灵活地生产适应各种需求的高质量产品的生产技术和管理技术,其基本原理和诸多方法,对制造业具有积极的意义。
精益生产的核心,即关于生产计划和控制以及库存管理的基本思想,对丰富和发展现代生产管理理论也具有重要的作用。
精益生产的支柱与终极目标“零浪费”为精益生产终极目标,具体表现在PICQMDS七个方面,目标细述为:(1)“零”转产工时浪费(Products•多品种混流生产)将加工工序的品种切换与装配线的转产时间浪费降为“零”或接近为“零”。
浅析丰田精益管理模式的本质
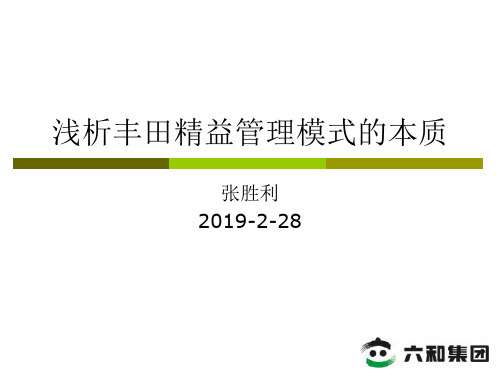
一、丰田精益管理的核心理念:(识别并消除浪费)
丰田公司之所以能成为世界顶级企业、其成功的 答案就是:
--精益生产管理。
他们认识到传统的生产经营管理中,存在着大量 的对最终产品和客户没有一点意义的行为:
--这就是浪费
效率驱动效益 · 包容提速增长
一、丰田精益管理的核心理念:(识别并消除浪费)
“无管理”状态,使企业浪费大、成本高、利润低。目前
困扰我们发展的最大瓶颈正在于“管理技术缺乏”、“管 理体系束缚技术、设备和人力的能力发挥”
效率驱动效益 · 包容提速增长
丰田生产模式(TBS):
丰田生产方式(TPS)已经成为全世界公认的先进管理模
式。“只要杜绝浪费,生产效率就有可能提高10倍。”
效率驱动效益 · 包容提速增长
二、精益管理中的---“流”
“时间流”的管理和坚决执行是丰田管理的灵魂。
时间管理就是用技巧、技术和工具帮助人们完成工作,实 现目标。
时间管理并不是要把所有事情做完,而是更有效的运用时 间。
时间管理的目的除了要决定你该做些什么事情之外,另一 个很重要的目的也是决定什么事情不应该做;
一、丰田精益管理的核心理念:(识别并消除浪费)
库存:
定义:任何超过客户或后道工序需求的供应; 表现:需要额外的进货区域、停滞不前的物流移动、
发现问题后需要进行大量返工、需要额外资 源进行物料搬运(人员、场地、货架、车辆) 对客户要求的变化不能及时反应; 起因:生产能力不稳定、不必要的停机、生产换型 时间长、生产计划不协调、市场把握不准确
1、库存不合理; 2、计划不周; 3、不合格品; 4、过度生产; 5、物料过度搬动; 6、等待; 7、动作不合理;
精益生产(丰田生产模式)专业用语解释说明
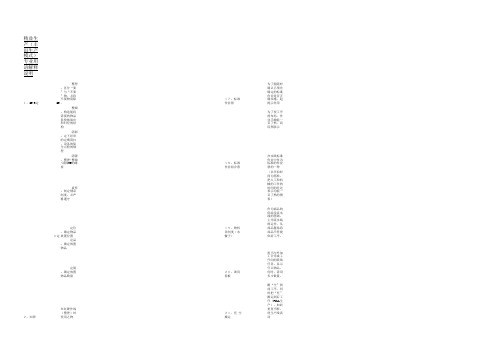
精益生产(丰田生产模式)专业用语解释说明1、5S・3定5S 整理 :区分“要”与“不要”物,并将不要物清除。
17、标准作业票为了能随时确认已预先确定的标准作业是否正确实施、起提示作用 整頓 :构造能将需要的物品很快地取出和归位的结构为了使工序的布局,作业手顺能一目了然,而用图表示 清掃 :定下经常的定期清扫、设备的保全点检的规程 清潔 :整理・整頓・清掃3S的維持18、标准作业组合票在实践标准作业中作为标准的作业票的一种 素养 :制定规章制度、并严格遵守(以节拍时间为基准、把人工和机械的工作的时间的经过表示为能一目了然的图表)3定 定位 :确定物品放置位置19、物料员制度(水鳖子)作为部品的供給及流水线的基础,主司流水线的运作,从部品置场将部品不停提供给工序。
定品 :确定放置物品 定量 :确定放置物品数量20、领用看板担当与外加工公司或工序间的联络任务、显示什么物品、何时、需用多少数量。
2、红牌在红牌作战(整理)时使用之物21、充 空搬运搬“空”到前工序,同时把“充”搬运到后工序(PULL生产),如此重复不断,使生产线流动组织红牌委员会,在剩余品上贴红牌、作成剩余品表单,扔掉不要的物品22、稼动率(稼働时间/工作时间)×100%3、看板表示的道具(在哪里<场所表示>什么<品名表示>多少<量表示>)把物品的放置方法规范化、整顿放置场所的道具23、可动率<1个产品的C/T×后工序要求数额>/(完成后工序要求数额所需要时间)×100%例:工作场所看板、工程看板、设备看板、3定看板、放置场所看板等→包含作业阻害要因(经常性暂停、准备时间、等)4、T/T一个数值,表示顾客要求的物品一个应在几秒内完成时较合理24、半成品看板主要用于表示工序的作业指示(遵从半成品看板的指示,方可开始操作)(节拍时间)計算式=一日的作业時间/顾客要求数25、停滞保管,工序等待中的半成品状态5、C/T生产一个制品所必要的时间(周期时间)26、标准保有量操作中、必要最低限的工序的半成品的个数6、S/T估计了作业阻害要因(经常性暂停、上洗手间、维修、准备时间等)而算出的标准时间。
七大浪费

丰田生产方式认为:“不产生附加价值的一切作业都是浪费”。
它把生产过程中的浪费问为以下七种(见下表):
1、生产过程的浪费。
一心想要多销售而大量生产,结果是人员、设备、材料、能源等方面都产生了浪费。
在没有需求的时候提前生产而产生浪费。
2、产生不合格品的浪费。
在生产过程中出现不合格品(次品、废品),会在原材料、零部件、返工或返修所需工时等生产不合格品所消耗的资源方面而产生浪费。
3、停工待产的浪费。
在进行机械加工时,机器发生故障不能正常作业,或因缺少零部件而停工等活等,在这样的状态下所产生的浪费都是停工待产的浪费。
4、动作的浪费。
不产生附加价值的动作、不合理的操作、效率低下的姿势和动作都是浪费。
5、搬运的浪费。
除去准时化生产所必须的搬运,其他任何搬运都是一种浪费。
如在不同仓库间移动、转运、长距离运输、运输次数过多和运输方法不档等。
6、加工本身的浪费。
把与工程的进展情况和产品质量没有任何关系的加工当作必要的加工而进行操作所产生的浪费。
7、库存的浪费。
因原材料、零部件、各道工序的半成品过多而产生的浪费。
这些产品过度积压还会引起库存管理费用的增加。
丰田七种浪费对策表。
日本本田汽车公司S和安全卫生管理手册

日本本田汽车公司S和安全卫生管理手册Document number【AA80KGB-AA98YT-AAT8CB-2A6UT-A18GG】丰田汽车5S和安全卫生管理手册目录1.XXXX的基本方针:提供顾客100%满意的服务,创建员工100%满意的公司。
2.XXXX企业基础:危机管理体制,人才培养,环境安全以及5S的推行3.5S方针的策略重点:3.1建立使顾客100%满意的质量保证体制3.2改进业务流程、削减在库、遵守交期3.3强化成本竞争力3.4积累与提高生产技术力3.5提高新技术的推广速度3.6构筑企业基础4.5S与环境安全的目标4.1提高生产性4.2提高服务水平和维修产品质量4.3提高速度4.4提高人员素质4.5提高安全性5.5S的定义5.1整理:工作现场,区别要与不要的东西,只保留有用的东西,撤除不需要的东西;5.2整顿:把要用的东西,按规定位置摆放整齐,并做好标识进行管理;5.3清扫:将不需要的东西清除掉,保持工作现场无垃圾,无污秽状态;5.4清洁:维持以上整理、整顿、清扫后的局面,使工作人员觉得整洁卫生;5.5修养:通过进行上述4S的活动,让每个员工都自觉遵守各项规章制度,养成良好的工作习惯,做到“以厂为家、以厂为荣”的地步。
6.5S活动的职责6.1办公室负责组织整个公司的5S及安全卫生的检查6.2各部门负责按5S管理要求对本部门的5S及安全卫生进行检查6.3责任部门负责对5S及安全卫生检查中发现的问题进行改进7.5S活动的要求7.1良好的仪表及礼仪:统一规范的着装要求,良好的坐姿、站姿,电话礼仪,整洁、明亮、大方、舒适的接待环境7.2单一整洁的办公室:台面整洁,文具单一化管理,公用设施责任人标识7.3生产工具管理:单一化管理7.4现场管理:分区划线,员工工作井然有序,工作环境清洁明亮7.5工作速度和效率:最佳的速度和零不良率7.6空间效率:对现场分区划线,对各场地的利用率予于分析,增加有限空间的利用价值7.7严明的小组督导:上班前经理、班组长对员工进行检查督导,工作过程中,对发现的问题及时开展小组督导,下班前对全天的工作进行总结7.8工作评估:自我评估与综合考核评价相结合8.5S对应的措施8.1整理的措施8.1.1清除不用物品的措施a)进行整理,首先要根据情况,分清什么需要,什么不需要。
丰田模式管理的14项原则

丰田模式的14项原则【第一类】长期理念原则1:管理决策以长期理念为基础,即使因此牺牲短期财务目标也在所不惜。
⏹企业应该有一个优先于短期决策的目的概念,使整个企业的运作与发展能够相互呼应,朝向这个比赚钱更重要的共同的目的迈进。
了解你公司的历史地位,设法使公司迈向下一个阶段。
公司理念的使用使所以其他原则的基石。
⏹起始点应该是顾客、社会、经济创造价值。
评估公司每个部门实现此目的的能力。
⏹要有责任感。
努力决定自己的命运,依靠自己,相信自己的能力。
对自己的行为、保持与提高创造价值的技能等负起责任。
【第二类】正确的流程方能产生正确成果原则2:建立连续的作业流程以使问题浮现⏹重新设计工作流程,使其变成创造高附加价值的连续流程。
尽力把所有计划中闲置或等候他人的工作时间减少到零。
⏹建立快速输送材料与信息的流程,使流程与人员紧密的联结在一起,以便立即浮现问题。
⏹使整个企业文化重视流程,这是促成真正的持续改善及员工发展的关键原则3:使用拉动式生产方式以避免生产过剩。
⏹在你生产流程下游的顾客需求的时候供应给他们正确数量的正确东西。
材料的补充应该由消费量决定,这是准时生产的基本原则。
⏹使在制品及仓库存货减少至最少,每项产品只维持少量存货,根据顾客实际领取的数量,经济的补充存货。
⏹按顾客的需求每天变化,而不是依靠计算机的时间表与系统来追踪浪费的存货。
原则4:使工作负荷平均(生产均衡化),工作应该像龟兔赛跑中的乌龟一样。
⏹杜绝浪费只是实现精益所必须做的1/3,。
避免员工与设备的工作负荷过重,以及生产安排的不均匀,也同等重要,但多数试图实行精益原则的企业并不了解这些。
⏹尽量使所有制造与服务流程的工作负荷平均化,以取代大多数公司实行的批量生产方法中经常启动、停止、停止、启动的做法。
原则5:建立立即暂停已解决问题、从一开始就重视质量控制的文化。
⏹为顾客提供的品质决定着你的定价。
⏹使用所有确保品质的现代方法。
⏹使生产设备具有发现问题及一发现问题就停止生产的能力。
丰田的7种浪费
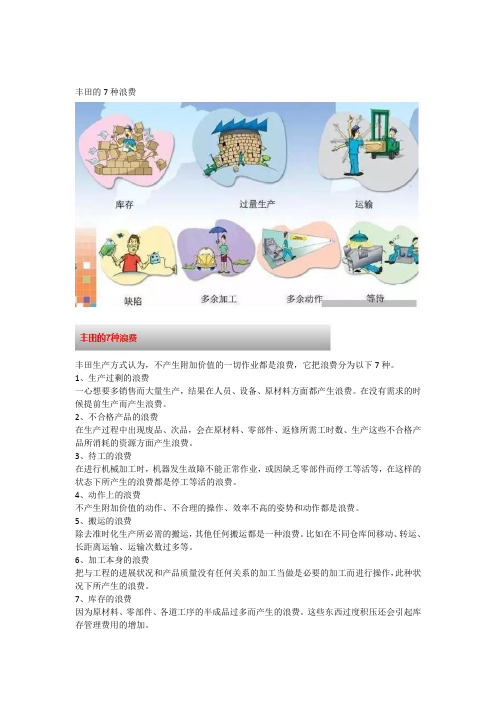
丰田的7种浪费丰田生产方式认为,不产生附加价值的一切作业都是浪费,它把浪费分为以下7种。
1、生产过剩的浪费一心想要多销售而大量生产,结果在人员、设备、原材料方面都产生浪费。
在没有需求的时候提前生产而产生浪费。
2、不合格产品的浪费在生产过程中出现废品、次品,会在原材料、零部件、返修所需工时数、生产这些不合格产品所消耗的资源方面产生浪费。
3、待工的浪费在进行机械加工时,机器发生故障不能正常作业,或因缺乏零部件而停工等活等,在这样的状态下所产生的浪费都是停工等活的浪费。
4、动作上的浪费不产生附加价值的动作、不合理的操作、效率不高的姿势和动作都是浪费。
5、搬运的浪费除去准时化生产所必需的搬运,其他任何搬运都是一种浪费。
比如在不同仓库间移动、转运、长距离运输、运输次数过多等。
6、加工本身的浪费把与工程的进展状况和产品质量没有任何关系的加工当做是必要的加工而进行操作,此种状况下所产生的浪费。
7、库存的浪费因为原材料、零部件、各道工序的半成品过多而产生的浪费。
这些东西过度积压还会引起库存管理费用的增加。
消除7种浪费的步骤从哪里开始消除这7种浪费为好呢?在像丰田一样积累了50年以上的改善经验和没有这些改善经验的企业中,在生产体制上存在着很大差异。
在此让我们以问题比较多的企业为对象,来思考一下处理7种浪费的基本顺序。
步骤①:在需要的时候适时生产需要的产品可以排除生产过剩的浪费,这需要具备严格管理的思想。
步骤②:如果经常产生不合格产品,抑制生产过剩是很困难的。
我们要消除不合格产品,消除制造不合格产品的浪费。
步骤③:对于停工等活,只要明白其要点就很容易改善。
消除停工等活的浪费,有效利用人力资源。
步骤④~⑥可以根据消除浪费的着眼点从可以实施的部分开始实施。
步骤④:对于动作的浪费,如果减少工时数(人数×时间)将会对消除浪费产生很大影响。
但是,即使是进行动作分析,清除了一些细小的浪费,也会被其他的问题所掩盖,所以必须注意。
仓库JIT库存管理方法
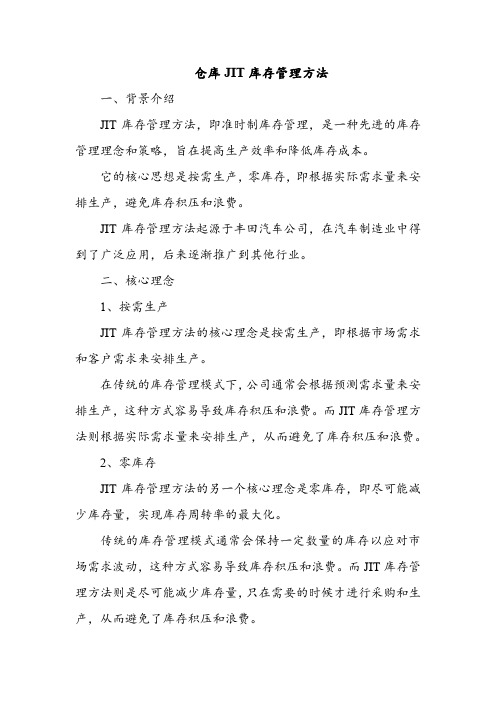
仓库JIT库存管理方法一、背景介绍JIT库存管理方法,即准时制库存管理,是一种先进的库存管理理念和策略,旨在提高生产效率和降低库存成本。
它的核心思想是按需生产,零库存,即根据实际需求量来安排生产,避免库存积压和浪费。
JIT库存管理方法起源于丰田汽车公司,在汽车制造业中得到了广泛应用,后来逐渐推广到其他行业。
二、核心理念1、按需生产JIT库存管理方法的核心理念是按需生产,即根据市场需求和客户需求来安排生产。
在传统的库存管理模式下,公司通常会根据预测需求量来安排生产,这种方式容易导致库存积压和浪费。
而JIT库存管理方法则根据实际需求量来安排生产,从而避免了库存积压和浪费。
2、零库存JIT库存管理方法的另一个核心理念是零库存,即尽可能减少库存量,实现库存周转率的最大化。
传统的库存管理模式通常会保持一定数量的库存以应对市场需求波动,这种方式容易导致库存积压和浪费。
而JIT库存管理方法则是尽可能减少库存量,只在需要的时候才进行采购和生产,从而避免了库存积压和浪费。
3、持续改进JIT库存管理方法强调持续改进和不断优化。
在生产过程中,公司需要不断关注生产流程、产品质量、交货时间等方面的问题,并及时采取措施进行改进。
通过持续改进,公司可以提高生产效率、降低成本、提高产品质量,从而获得更大的竞争优势。
三、与传统库存管理的区别JIT库存管理与传统库存管理的主要区别体现在以下几个方面。
1、库存水平JIT库存管理通过采用准时制生产方式,将库存水平降低到最低限度,以避免库存积压和浪费。
而传统库存管理通常会维持一定水平的库存,以应对需求波动和不确定性。
2、质量管理JIT库存管理强调高质量的产品和零部件,通过减少缺陷和故障来降低维修成本和产品退货率。
传统库存管理可能更注重在成本控制和质量可接受性之间找到平衡。
3、供应链管理JIT库存管理注重与供应商建立紧密的合作伙伴关系,通过信息共享和协同计划来提高供应链的效率和灵活性。
传统库存管理可能更侧重于与多个供应商合作,以分散风险并获得更好的采购谈判力量。
丰田零件业务管理简述

丰田零件业务管理简述概述(一)、零件部门的使命(方针目标)(二)、库存管理不是单纯追求效率化,而是需要实现统一化、管理化、综合化、信息化l 统一化——供应链管理(JIT理念运用到丰田零件供应体系中)l 管理化——形成经营管理周期(plan·do·see)系统1、计划(plan)——丰田的Just In Time库存计划管理方式(对市场预测及库存设定、订货原则等)2、实施(do)——订货业务、到货索赔及入库业务、出库业务、零件报价、保管原则和方式等日常性工作3、审核(see)——盘库业务、供应率和周转率的确定与分析、Phase-in(建库零件)和Phase-out(呆滞零件)管理等l 综合化——是统一化的供应链纵向管理与管理化的横向经营管理周期有机的结合l 信息化——库存管理的统一化、管理化和综合化需要有高效的计算机统计系统支持(TACT丰田业务标准系统、EPC丰田零件电子目录的应用)(三)、零件部其他内容(丰田零件基础知识、丰田对Tass零件业务考评及价格体系、零件主管工作职责、5S效果等)____________________________________________(一)零件部门的使命和库存管理方针就是通过最大限度的及时满足客户需求(高供应率→高CS客户满意率),和优化库存带来的低库存金额,以获得良好的营业收益(高库存效率)。
即用最少的零件库存确保最大的供应性。
这是企业成为在激烈竞争中能否生存下去的关键之一。
(二)库存管理不是单纯追求效率化,而是需要实现统一化、管理化、综合化、信息化要达到CS和库存效率化这两个相互矛盾的目标,库存管理实现上述“四化”是首要条件。
一、统一化——应把库存管理作为构成供应链纵向统一系统的一环加以定位。
1、丰田的零件供应体系是建立在JIT零件供应理论基础上的,即卖一买一原则,就是零件的物流按要求的步调沿供应线流动。
2、TASS经销店是丰田整个零件供应链中的重要一环。
丰田5S管理制度
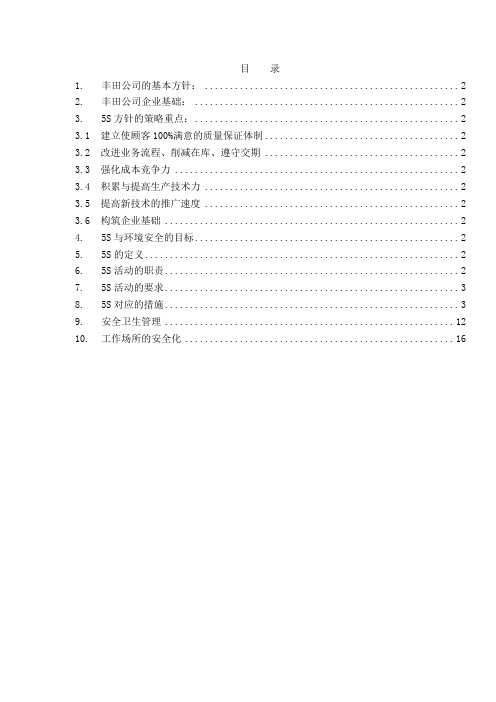
目录1. 丰田公司的基本方针: (2)2. 丰田公司企业基础: (2)3. 5S方针的策略重点: (2)3.1 建立使顾客100%满意的质量保证体制 (2)3.2 改进业务流程、削减在库、遵守交期 (2)3.3 强化成本竞争力 (2)3.4 积累与提高生产技术力 (2)3.5 提高新技术的推广速度 (2)3.6 构筑企业基础 (2)4. 5S与环境安全的目标 (2)5. 5S的定义 (2)6. 5S活动的职责 (2)7. 5S活动的要求 (3)8. 5S对应的措施 (3)9. 安全卫生管理 (12)10. 工作场所的安全化 (16)1.丰田公司的基本方针:提供顾客100%满意的服务,创建员工100%满意的公司。
2.丰田公司企业基础:危机管理体制,人才培养,环境安全以及5S的推行3.5S方针的策略重点:3.1建立使顾客100%满意的质量保证体制3.2改进业务流程、削减在库、遵守交期3.3强化成本竞争力3.4积累与提高生产技术力3.5提高新技术的推广速度3.6构筑企业基础4.5S与环境安全的目标4.1提高生产性4.2提高服务水平和维修产品质量4.3提高速度4.4提高人员素质4.5提高安全性5.5S的定义5.1整理:工作现场,区别要与不要的东西,只保留有用的东西,撤除不需要的东西;5.2整顿:把要用的东西,按规定位置摆放整齐,并做好标识进行管理;5.3清扫:将不需要的东西清除掉,保持工作现场无垃圾,无污秽状态;5.4清洁:维持以上整理、整顿、清扫后的局面,使工作人员觉得整洁卫生;5.5修养:通过进行上述4S的活动,让每个员工都自觉遵守各项规章制度,养成良好的工作习惯,做到“以厂为家、以厂为荣”的地步。
6.5S活动的职责6.1办公室负责组织整个公司的5S及安全卫生的检查6.2各部门负责按5S管理要求对本部门的5S及安全卫生进行检查6.3责任部门负责对5S及安全卫生检查中发现的问题进行改进7.5S活动的要求7.1良好的仪表及礼仪:统一规范的着装要求,良好的坐姿、站姿,电话礼仪,整洁、明亮、大方、舒适的接待环境7.2单一整洁的办公室:台面整洁,文具单一化管理,公用设施责任人标识7.3生产工具管理:单一化管理7.4现场管理:分区划线,员工工作井然有序,工作环境清洁明亮7.5工作速度和效率:最佳的速度和零不良率7.6空间效率:对现场分区划线,对各场地的利用率予于分析,增加有限空间的利用价值7.7严明的小组督导:上班前经理、班组长对员工进行检查督导,工作过程中,对发现的问题及时开展小组督导,下班前对全天的工作进行总结7.8工作评估:自我评估与综合考核评价相结合8.5S对应的措施8.1整理的措施8.1.1清除不用物品的措施a)进行整理,首先要根据情况,分清什么需要,什么不需要。
丰田的核心竞争力解析——从七个方面看供应链体系
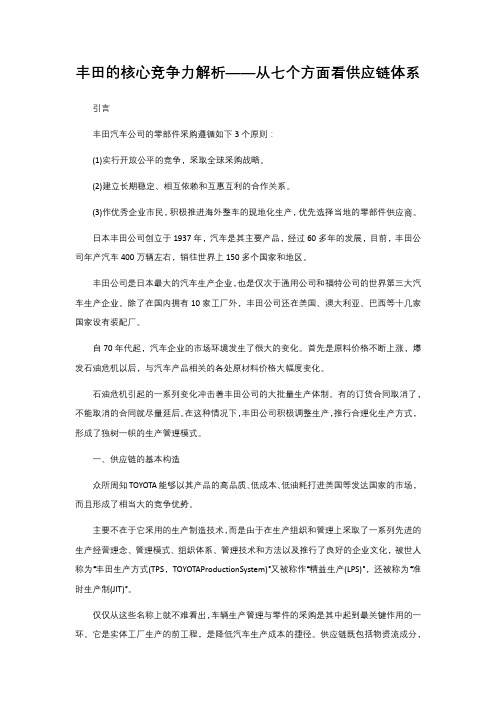
丰田的核心竞争力解析——从七个方面看供应链体系引言丰田汽车公司的零部件采购遵循如下3个原则:(1)实行开放公平的竞争,采取全球采购战略。
(2)建立长期稳定、相互依赖和互惠互利的合作关系。
(3)作优秀企业市民,积极推进海外整车的现地化生产,优先选择当地的零部件供应商。
日本丰田公司创立于1937年,汽车是其主要产品,经过60多年的发展,目前,丰田公司年产汽车400万辆左右,销往世界上150多个国家和地区。
丰田公司是日本最大的汽车生产企业,也是仅次于通用公司和福特公司的世界第三大汽车生产企业。
除了在国内拥有10家工厂外,丰田公司还在美国、澳大利亚、巴西等十几家国家设有装配厂。
自70年代起,汽车企业的市场环境发生了很大的变化。
首先是原料价格不断上涨,爆发石油危机以后,与汽车产品相关的各处原材料价格大幅度变化。
石油危机引起的一系列变化冲击着丰田公司的大批量生产体制。
有的订货合同取消了,不能取消的合同就尽量延后。
在这种情况下,丰田公司积极调整生产,推行合理化生产方式,形成了独树一帜的生产管理模式。
一、供应链的基本构造众所周知TOYOTA能够以其产品的高品质、低成本、低油耗打进美国等发达国家的市场,而且形成了相当大的竞争优势。
主要不在于它采用的生产制造技术,而是由于在生产组织和管理上采取了一系列先进的生产经营理念、管理模式、组织体系、管理技术和方法以及推行了良好的企业文化,被世人称为“丰田生产方式(TPS,TOYOTAProductionSystem)”又被称作“精益生产(LPS)”,还被称为“准时生产制(JIT)”。
仅仅从这些名称上就不难看出,车辆生产管理与零件的采购是其中起到最关键作用的一环。
它是实体工厂生产的前工程,是降低汽车生产成本的捷径。
供应链既包括物资流成分,也包括运营和计划流程。
(一)物资流供应商生产零件,并通过物流站将其运送至装配工厂。
在装配工厂,车辆在车身区成形,然后运向喷漆区,再经过然后装配区,最后进行质量检查。
丰田公司的物流解析

问题
• 丰田的召回事情很大程度上也是因为追求 高速率的生产和物流,它为了盲目追求速 度缩短时间,从而导致了汽车质量不过关 ,其中问题主要出现在它的供应链的管理 上。
1 质量管理是供应链管理的核心
无论哪一种供应链,无不强调一个相同的核心:质量。因此我们的建议是多注重质量
丰田汽车
公司简介
丰田是世界十大汽车工业公司之一,全球最大的汽车公 司,丰田喜一郎1933年在丰田自动织机制作所成立汽车部, 1937年汽车部正式从丰田自动织机制作所中独立出来,成立 丰田汽车工业公司。TOYOTA在汽车的销售量、销售额、知名 度方面均是世界三强公司之一。TOYOTA生产包括一般大众性 汽车、高档汽车、面包车、跑车、四轮驱动车、商用车在内的 各种汽车。
(1)零部件厂商对整车企业的实时物流供应
• 在实时物流中,取消了仓库的概念,丰田公司只设置场;临 时堆料,原材料和零配件只在此堆放几个小时,短的只要 几分钟,就被领用。在看板制度下,许多零件是等到下一 个制造过程需要的几个小时才上线生产。实时生产能发挥 作用,除了要求准时化生产;外,还需要零配件厂商的实时 物流做保障。零配件厂商大多位于同一个工业园区,这样 不仅降低了运输成本,使运送途中的损耗降低到最低程度 ,而且降低了所需的库存量。
的
实时物流供应
物
实时物流
实时物流服务
流
生产物流
持续改善
管理方式
出现的问题以及解决方案
准时化生产
• 准时化生产(Just In Time)--------服务主导的敏捷物流
• 就是仅仅在需要的时候,才为所需的地方按所需的数量和质量生产所需的产 品。JIT追求的目标为五个“零”, “零”纸张“零库存”零积压零等候零废品 ,从避免了各种浪费。JIT通过丰田汽车公司独创的均衡生产、牵引式系统、 连续工艺流程和生产节拍来实现
丰田模式的十四项原则

丰田模式的十四项原则自丰田公司创办以来,我们一直坚持通过制造高品质的产品与服务以贡献社会的核心理念,我们此核心理念的事业实务与活动所发展出来的价值观、信念、与事业方法在历经多年后,已经成为竞争优势的来源,这些管理的价值观与事业方法就是所谓的丰田模式。
丰田模式并非只是工具与方法其实,实行精益真正重要的工作现在才刚开始!员工不了解丰田生产制度背后的基础文化,他们并未对此生产制度的持续改善作出贡献,或是他们本身并未改善。
在丰田模式中,带给丰田生产制度生命的是员工:他们工作、沟通、解决问题、一起成长。
只要看一眼在日本实行精益生产方法而表现卓越的公司,就可以发现这些公司的员工主动积极于提出改善建议,但是,丰田模式还不仅于此,它鼓励、支持,且实际上是要求员工投入、参与。
我愈深入研究丰田生产制度与丰田模式,就愈了解这是一个提供员工工具、使他们能持续改善工作的制度,丰田模式代表更加倚重员工,而不是减少对员工的依赖。
丰田模式是一种文化,而非只是一套提升效率与改善的工具及方法,你必须仰赖员工减少存货,找出隐藏的问题,并解决问题,员工有紧迫感、目的、及团队合作的观念,因为他们若不能解决问题,就会发生存货不足的情形。
在日常作业中,工程师、技巧熟练的员工、品管专业人员、供应商、领班、及作业人员,全都参与解决问题与持续改善的工作,历经时日,人人都被训练成更擅长解决问题者。
促成及强化这种团队合作的精工益具之一是「5S」(整理、整顿、清扫、清洁与素养),这是一系列杜绝浪费的工作,避免因为浪费而造成错误、瑕疵品与伤害。
在这一系列工作的改善方法中,第五个S――素养,应该是最困难的部分,也是靠这项工作才能使前面四个S得以不断持续下去,欲做到素养工作,必须靠必要的教育、训练与奖励,以鼓励员工正确地维持及持续改善作业流程与工作场所环境。
这项工作必须结合管理阶层的信诺投入、适当的员工训练,以及使持续改善变成上至管理者、下至工厂员工之习惯行为的公司文化。
7S管理手册
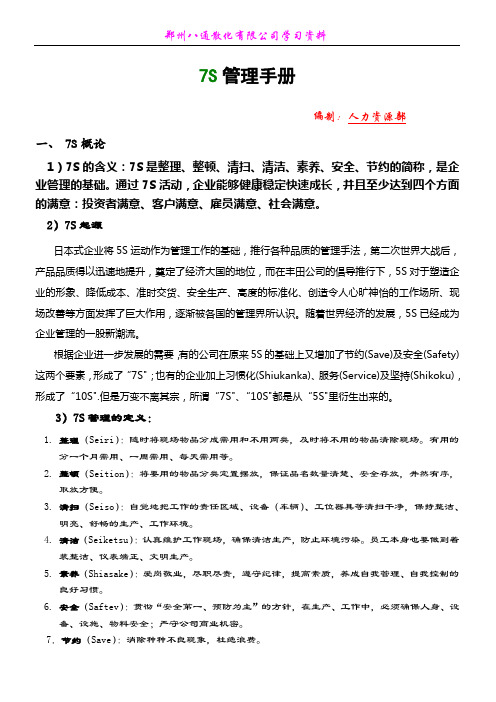
7S管理手册编制:人力资源部一、7S概论1)7S的含义:7S是整理、整顿、清扫、清洁、素养、安全、节约的简称,是企业管理的基础。
通过7S活动,企业能够健康稳定快速成长,并且至少达到四个方面的满意:投资者满意、客户满意、雇员满意、社会满意。
2)7S起源日本式企业将5S运动作为管理工作的基础,推行各种品质的管理手法,第二次世界大战后,产品品质得以迅速地提升,奠定了经济大国的地位,而在丰田公司的倡导推行下,5S对于塑造企业的形象、降低成本、准时交货、安全生产、高度的标准化、创造令人心旷神怡的工作场所、现场改善等方面发挥了巨大作用,逐渐被各国的管理界所认识。
随着世界经济的发展,5S已经成为企业管理的一股新潮流。
根据企业进一步发展的需要,有的公司在原来5S的基础上又增加了节约(Save)及安全(Safety)这两个要素,形成了“7S";也有的企业加上习惯化(Shiukanka)、服务(Service)及坚持(Shikoku),形成了“10S".但是万变不离其宗,所谓“7S"、“10S"都是从“5S"里衍生出来的。
3)7S管理的定义:1. 整理(Seiri):随时将现场物品分成需用和不用两类,及时将不用的物品清除现场。
有用的分一个月需用、一周需用、每天需用等。
2. 整顿(Seition):将要用的物品分类定置摆放,保证品名数量清楚、安全存放,井然有序,取放方便。
3. 清扫(Seiso):自觉地把工作的责任区域、设备(车辆)、工位器具等清扫干净,保持整洁、明亮、舒畅的生产、工作环境。
4. 清洁(Seiketsu):认真维护工作现场,确保清洁生产,防止环境污染。
员工本身也要做到着装整洁、仪表端正、文明生产。
5. 素养(Shiasake):爱岗敬业,尽职尽责,遵守纪律,提高素质,养成自我管理、自我控制的良好习惯。
6. 安全(Saftev):贯彻“安全第一、预防为主”的方针,在生产、工作中,必须确保人身、设备、设施、物料安全;严守公司商业机密。
- 1、下载文档前请自行甄别文档内容的完整性,平台不提供额外的编辑、内容补充、找答案等附加服务。
- 2、"仅部分预览"的文档,不可在线预览部分如存在完整性等问题,可反馈申请退款(可完整预览的文档不适用该条件!)。
- 3、如文档侵犯您的权益,请联系客服反馈,我们会尽快为您处理(人工客服工作时间:9:00-18:30)。
第四章 仓库保管七原则
teachermyh@
3 综合评价 我们用以下表格说明库存保管七原则的优越性
评价内容
空间 质量
竖置存放
按类型存放
七
重物下置
原 一个零件号一个货位
则 存放在手可达到之处
异常品管理 按周转速度存放
作业效率
生产率 储存 安全性 学海无涯
作业区
为常流动件; 为慢流动件; 为出入库行走路线。
作业区
学海无涯
第四章 仓库保管七原则
teachermyh@
① 常流动件存放于远离作业区的货位,延长了出入库作业路线; ② 且存放在货架上不易取放的位置,大大降低了工作效率。
① 常流动件存放于靠近作业的货位,缩短了出入库作业路线; ② 存放在易于取放的位置,提高了工作效率。
货位上用向上的箭 头指示先从上方对 多的库存出库
过多的库存放在与该 零件货位相对应的货 架上方,以引起注意。
货架上方标有 红色警戒线
这样,当我们发现货架上方出现过多的库存时就应该及时同业务部门联系,确认是下 面哪种原因造成的:
① 订货错误; ② 市场需求增加,原来的货位已不能满足要求;
学海无涯
第四章 仓库保管七原则
1 仓库保管七原则
1 按周转速度存放; 2 重物下置; 3 竖置存放; 4 按类型存放; 5 异常品管理; 6 一个件号一个货位; 7 存放在手可达到之处。
teachermyh@
学海无涯
第四章 仓库保管七原则
2.1.按周转速度存放
* 常流动件远离作业区,效率低下。
teachermyh@ * 常流动件存放于作业区附近,作业方便。
学海无涯
第四章 仓库保管七原则
teachermyh@
2.2.重物下置
这是从出入库作业的安全性和高效率方面来考虑的。有些像半轴、缸体、轮毂等 重零件如存放在货架上方会产生如下问题:
① 重零件有落下伤人及损坏的危险; ② 上架、提取不便。
危险!
不便!
学海无涯
第四章 仓库保管七原则
teachermyh@
第四章 仓库保管七原则
2.4.按产品类型存放
teachermyh@
长形零件伸出至通 道影响出入库作业
空间严重浪费
中型零件如:空 滤、离合器片等 空间严重浪费
长零件如消声器
微小型零件(油 封、火花塞等)
大型零件如:缸体、 轮毂、水箱等
学海无涯
第四章 仓库保管七原则
2.5.异常管理
teachermyh@
货位已满
备用的货位有可 能被忽视,而不 能出库。
过多的库存 放至空货位
缺点:
① 容易因疏忽而忘记零件的临时存放位置; ② 有可能因疏忽了一种零件存放于两个位置而发生重复订货的事情; ③ 库存空间浪费; ④ 无法观察库存效率(不易发觉不良库存)。
学海无涯
第四章 仓库保管七原则
teachermyh@
所以一定要贯彻一个件号一个货位。
学海无涯
第四章 仓库效率角度考虑的。 如果零件存放在过高的地方,提取及上架时 不得不使用梯子,就会造成作业不方便、 效率低下。所以,应该将零件存放在 手能达到的位置。
teachermyh@
学海无涯
2.3.竖置存放
有些象车门、排气管、挡风玻璃等扁平或细长形状的零件如平放会产生如下问题: ① 上面零件的重量会损坏下面的零件; ② 此类零件平放会浪费很大空间; ③ 由于排气管一类的零件过长,如平放会从货架伸出至通道,从而影响通行且不安全; ④ 难以提取。
如图所示:
零件重且缠绕 不便出入库作业
学海无涯
2.6.一个零件号一个货位
teachermyh@
A01 A02 A03
出库票 A03-01-04
如上图所示,门市打出出库票,上面写明该零件的货位位于A区的A03号货架的由下向上 数第4段第一个货位即A03-01-04。这个货位里只保存我们要出库的这个零件,所以即使是 完全没有经验的人也可准确无误地找到。