铝合金压铸端盖的模具设计
铝合金盖体挤压铸造工艺与模具设计

田福祥
["] 保压时间
在保证制件成形密致和完全结晶凝固条件下, 保压 时间愈短愈好。一般挤压铸造的保压时间大约是金属 模重力浇注的 ’ 7 %。保压时间与铸件的断面最大厚度 有关, 一般为 & " + , ’ 8 7 66。例如制件最大壁厚为 !& 最大保压时间不超过 !& 8, 最小保压时间不低于 ’! 66, 此件需保压 %1 , 91 8。 8。按图 ’ 铸件的最大壁厚计算, !"% 浇注温度 通常根据金属的液相线温度和凝固范围确定合适 的浇注温度。在挤压铸造铝镁合金 #$%&’ 时, 浇注温度 选择在 +1& , :&& ; 较合适。 !"&
3.期刊论文 郭国文.陈维平.李元元.罗宗强 新型高强韧铝铜系合金的挤压铸造 -特种铸造及有色合金2003,""(z1)
为实现某种重载车辆负重轮的"以铸代锻",进行了负重轮简约化缩小模型挤压铸造的试验研究.采用自行研制的一种新型铝铜合金,结合挤压铸造工艺,制得了负 重轮模型铸件.挤压铸造工艺参数为:比压50 MPa,浇注温度720~730 ℃,摸具温度250~350 ℃,开始加压时间7~10 s,保压时间8~15 s.热处理后铸件的组织、性 能和断口形貌的检测结果表明,挤压铸件的晶粒更为细小,组织更加致密,T5和T6热处理的力学性能分别为抗拉强度428、440 MPa,屈服强度360、395 MPa,伸长率 13.1%、11.3%.与重力金属型铸造相比,挤压铸造使铸件的力学性能得到明显提高.
规定的温度。为了稳定工艺参数, 保证产品质量, 组合 凹模设有冷却水道, 通过调节水流大小把模具温度控制 在一定的范围内。 冲头由型芯、 顶杆和模套组合而成, 以形成铸件的 复杂内腔。 对图 # 所示模具, 模套、 顶杆和凹模采用 ’FG#H-I 钢, 热处理硬度 JKF$$ L $-; 型芯采用 H(-FG$I。为了 提高模具的使用寿命, 模具的工作表面进行氮化处理。 氮化 层 厚 度 一 般 为 + & ’) 11、 氮化后硬度 + & $+ 11, JKF). L .+。 模具工作过程: 调整好模具, 模具工作表面充分润 滑后, 将熔化的合金液用浇勺浇入凹模, 下降上模进行 模压, 机床压力升至缺陷临界值压力时进行保压。保压 完成后, 上模抬起, 组合冲头带着铸件升至一定高度以 后, 扳动副油缸控制管路上的操纵阀, 使高压油进入油 缸上部, 通过活塞杆、 顶板、 顶杆和模套, 将铸件推离组 合模芯。将上下模工作部分润滑后, 扳回控制阀手把,
铝压铸件的设计

铝合金压铸件的结构设计经验1。
考虑壁厚的问题,厚度的差距过大会对填充带来影响2。
考虑脱模问题,这点在压铸实际中非常重要,现实中往往回出现这样的问题,这比注塑脱模讨厌多了,所以拔模斜度的设置和动定模脱模力的计算要注意些,一般拔模斜度为1到3度,通常考虑到脱模的顺利性,外拔模要比内拔模的斜度要小些,外拔模也就1度,而内拔模要2~3度左右3。
设计时考虑到模具设计的问题,如果有多个位置的抽心位,尽量的放两边,最好不要放在下位抽心,这样时间长了下抽心会容易出问题4。
有些压铸件外观可能会有特殊的要求,如喷油、喷粉等,这时就要时结构避开重要外观位置便于设置浇口溢流槽5。
在结构上尽量的避免出现导致模具结构复杂的结构出现,如,不得不使用多个抽心或螺旋抽心等6。
对于需进行表面加工的零件,注意,需要在零件设计时给适合的加工留量,不能太多,否则加工人员会骂你的,而且会把里面的气孔都暴露出来的,不能太少,否则粗精定位一加工,得,黑皮还没干掉,你就等再在模具上打火花了,那给多少呢,留量最好不要大于0。
8mm,这样加工出来的面基本看不到气孔的,因为有硬质层的保护。
7。
再有就是注意选料了,是用ADC12还是A380等,要看具体的要求了8。
铝合金没有弹性,要做扣位只有和塑料配合。
9。
一般不能做深孔!在开模具时只做点孔,然后在后加工!10。
如果是薄壁零件与不能太薄,而且一定要用加强肋,增加抗弯能力!由于铝铸件的温度要在800摄氏度左右!模具寿命一般比较短一般做如电机外壳的话只有80K左右就再见了!1.压铸件的设计与塑胶件的设计比较相似,塑胶件的一些设计常规也适用于压铸件。
铝合金支承盖压铸模的设计
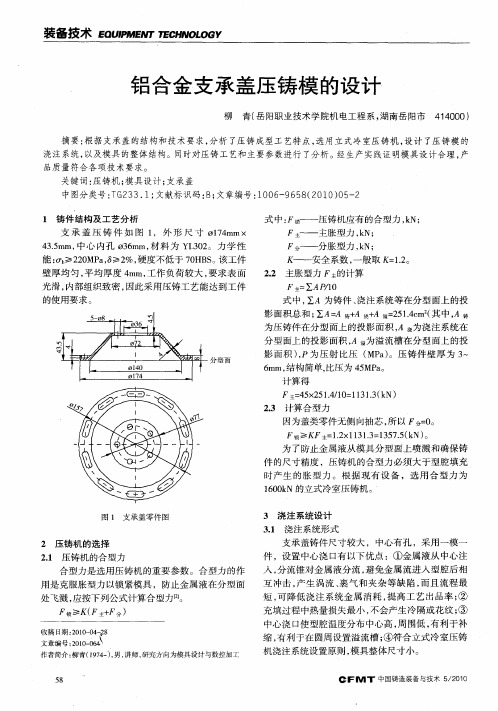
安 全 系数 , 般 取 K= .。 一 I 2
壁厚均匀 , 均厚度 4 m, 平 m 工作负荷较大 , 要求表面 光滑 , 内部 组织 致密 , 因此采 用 压铸 工艺 能 达 到工件 的使用要 求 。
22 主胀 型力 F{ . 的计算
} :∑A /O P I
式中 , ∑A为 铸件 、 浇注 系 统等 在 分 型面 上 的投
31 浇 注系统形 式 .
2 压铸 机 的选择
支 承盖 铸件 尺 寸较 大 ,中心 有孔 ,采 用 一模 一
21 压 铸机 的合 型力 .
合型力是选用压铸机 的重要参数 。合型力 的作
用是 克 服胀 型力 以锁 紧模 具 ,防止 金属 液 在分 型 面 处 飞溅 , 按下 列公 式计算 合 型力[ 应 2 1 。
F丰 — 主胀 型力 ,N; — k
支 承 盖 压 铸 件 如 图 1 外 形 尺 寸 o7m , 14 m× 4. 3 mm, 心 内孔 o 6 5 中 3 mm, 料 为 YL 0 。力 学 性 材 32
F钋 —分 胀 型力 ,N; — k
— —
能 : b 2 MP ,>2 硬 度不 低于 7 H S 该工 件 ( ≥20 a6 %, r t 0B。
环 形 连 接 , 厚 为 2 m,2的环 形 截 面 与 — 且 m a t 处 相 等, 这有 利 于平稳 充填 , 排气 畅通 。
而 七
1 8 l 9 2 0 2 1 22 23
—。
_
。
-
●
●
_
_
●
图 2 直 浇 道 不 意 图
蛊
亡
33 溢 流槽设 计 .
o F M 3" 1中NNN装备 与技术 5 2 1 / 00
铝合金壳体压铸模具设计
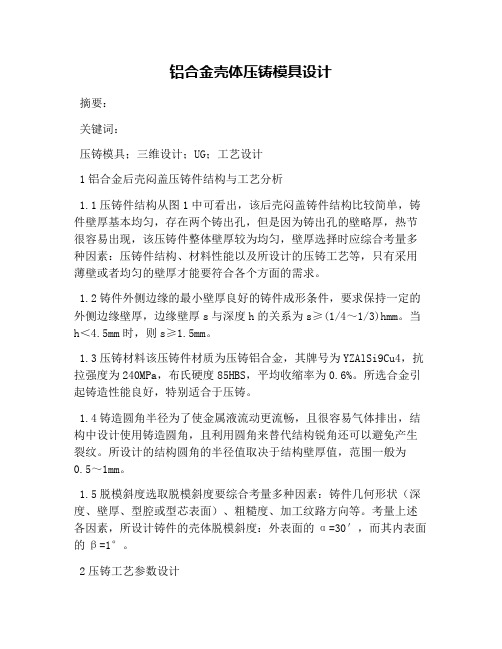
铝合金壳体压铸模具设计摘要:关键词:压铸模具;三维设计;UG;工艺设计1铝合金后壳闷盖压铸件结构与工艺分析1.1压铸件结构从图1中可看出,该后壳闷盖铸件结构比较简单,铸件壁厚基本均匀,存在两个铸出孔,但是因为铸出孔的壁略厚,热节很容易出现,该压铸件整体壁厚较为均匀,壁厚选择时应综合考量多种因素:压铸件结构、材料性能以及所设计的压铸工艺等,只有采用薄壁或者均匀的壁厚才能要符合各个方面的需求。
1.2铸件外侧边缘的最小壁厚良好的铸件成形条件,要求保持一定的外侧边缘壁厚,边缘壁厚s与深度h的关系为s≥(1/4~1/3)hmm。
当h<4.5mm时,则s≥1.5mm。
1.3压铸材料该压铸件材质为压铸铝合金,其牌号为YZAlSi9Cu4,抗拉强度为240MPa,布氏硬度85HBS,平均收缩率为0.6%。
所选合金引起铸造性能良好,特别适合于压铸。
1.4铸造圆角半径为了使金属液流动更流畅,且很容易气体排出,结构中设计使用铸造圆角,且利用圆角来替代结构锐角还可以避免产生裂纹。
所设计的结构圆角的半径值取决于结构壁厚值,范围一般为0.5~1mm。
1.5脱模斜度选取脱模斜度要综合考量多种因素:铸件几何形状(深度、壁厚、型腔或型芯表面)、粗糙度、加工纹路方向等。
考量上述各因素,所设计铸件的壳体脱模斜度:外表面的α=30′,而其内表面的β=1°。
2压铸工艺参数设计2.1压铸机选择选择压铸机必须先确定锁模力。
锁模力作用有二:一个是用来平衡反压力,以达到锁紧分型面的目的;一个是用来阻止飞溅的金属液,以达到获得目标尺寸精度的目的。
设计的铸件不存在分胀型力,因为此模具是没有侧抽芯的(压铸件无侧孔与侧凹)。
因此F 锁≥KF主=1.25×1288.352=1610.44kN根据上述计算得到锁模力的值还有铸件重量,根据这两个主要因素进行压铸机选择,最后选用机型为:卧式冷室压铸机(2500kN)———J1125型,主要参数:①最大金属浇注量———3.2Kg,②模具厚度———250~650mm,③动模座板行程———400mm,④压射力———143~280kN。
铝合金压铸工艺中的模具设计
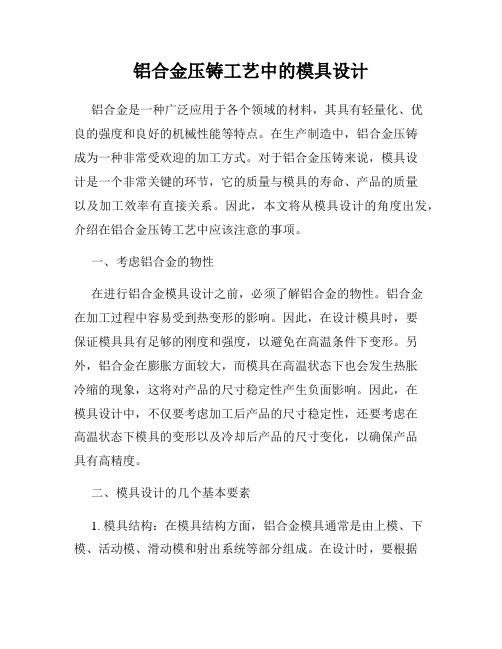
铝合金压铸工艺中的模具设计铝合金是一种广泛应用于各个领域的材料,其具有轻量化、优良的强度和良好的机械性能等特点。
在生产制造中,铝合金压铸成为一种非常受欢迎的加工方式。
对于铝合金压铸来说,模具设计是一个非常关键的环节,它的质量与模具的寿命、产品的质量以及加工效率有直接关系。
因此,本文将从模具设计的角度出发,介绍在铝合金压铸工艺中应该注意的事项。
一、考虑铝合金的物性在进行铝合金模具设计之前,必须了解铝合金的物性。
铝合金在加工过程中容易受到热变形的影响。
因此,在设计模具时,要保证模具具有足够的刚度和强度,以避免在高温条件下变形。
另外,铝合金在膨胀方面较大,而模具在高温状态下也会发生热胀冷缩的现象,这将对产品的尺寸稳定性产生负面影响。
因此,在模具设计中,不仅要考虑加工后产品的尺寸稳定性,还要考虑在高温状态下模具的变形以及冷却后产品的尺寸变化,以确保产品具有高精度。
二、模具设计的几个基本要素1. 模具结构:在模具结构方面,铝合金模具通常是由上模、下模、活动模、滑动模和射出系统等部分组成。
在设计时,要根据铝合金的物性和加工要求来确定模具结构和形状,以达到高效生产的目的。
2. 模具材料:在模具材料的选择方面,应根据铝合金的物性进行选择。
通常,适合用于铝合金模具的材料应具有高强度、高耐磨性和高温耐受性等特点。
目前,常用的模具材料有SKD61、H13和CRM等。
3. 考虑注塑工艺:在进行模具设计时,必须考虑到注塑工艺。
这意味着必须根据注塑工艺的参数来设计模具。
例如,应根据化学成分和温度参数来确定注塑机的射出系统和出口形状,以确保正常的注塑过程。
三、注塑机的选择在进行铝合金压铸加工时,注塑机的选择是非常关键的环节。
不同的注塑机具有不同的投影面积和射程,这会对产品的尺寸稳定性、成型速度和加工效率产生直接影响。
因此,在选择注塑机时,不仅要考虑加工数量和生产周期,还要考虑产品的几何形状、尺寸和质量要求。
四、模具维护模具在长期使用过程中,需要进行定期维护和保养。
浅谈铝合金压铸生产中模具的设计制造

浅谈铝合金压铸生产中模具的设计制造摘要:铝合金压铸模具是进行压铸生产的重要工艺装备,同时,也是铝合金压铸生产中三大必备因素之一。
文章首先分析了铝合金压铸模具设计制造技术,其次,就铝合金压铸模具设计制造中需要注意的几个技术问题进行了深入的探讨,具有一定的参考价值。
关键词:铝合金;压铸模具;制造技术铝合金压铸模具是进行压铸生产的重要工艺装备,同时,也是铝合金压铸生产中三大必备因素之一。
生产过程能否顺利进行,铸件质量是否有保证,在很大程度上取决于模具结构的合理性和技术上的先进性。
铝合金压铸模设计制造的优劣,直接影响压铸件的形状、尺寸、强度、表面质量等方面。
而压铸件的质量和稳定性,反映出整个压铸生产过程和压铸模制造过程的技术水平和经济效益。
1铝合金压铸模具设计在铝合金压铸模具设计过程中必须全面分析压铸件结构,熟悉压铸机操作过程,了解压铸机及工艺参数得以调整的可能性及范围,掌握在不同压铸条件下的金属液填充特性和流动特性,并考虑到经济因素,才能设计出切合实际并满足生产要求的压铸模。
铝合金压铸模设计前,设计人员应对所提供的设计依据,包括压铸产品图和生产纲领进行工艺分析,并进行如下必要准备:①根据产品图,对所选用的压铸合金、压铸件的形状、结构、精度和技术要求进行工艺性分析,确定机械加工部位、加工余量和机械加工时所要采取的工艺措施以及定位基准等。
②根据产品图和生产纲领,确定压射比压,计算锁模力:估算压铸件所需的开模力和推出力,以及压铸机的开模距离;选定压铸机的型号和规格。
③根据产品和压铸机的型号和规格,对模具结构进行初步分析,选择分型面和确定型腔数量;选择内浇口进口位置,确定浇注系统和溢流槽、排气槽朗总体布置方案;对带嵌件的压铸件,要考虑嵌件的装夹和固定方式;确定功模和定模镶块,动模和定模套板外形尺寸,以及导核、导套的位置和尺寸;确定冷却和加热管道的位置和尺寸,控制压铸过程的热平衡等。
④绘制压铸件毛坯图。
包括分型面位置、浇注系统、溢流槽和排气槽,推出元件的位置和尺寸以及机械加工余量、加工基准等数值。
铝合金压铸模具的制作

铝合金压铸模具的制作铝合金压铸模具的制作刘氏模具铝合金压铸模具的制作一般可以分为这几个步骤:审图—备料—加工—模架加工—模芯加工—电极加工—模具零件加工—检验—装配—飞模—试模—生产;A:模架加工:1打编号,2 A/B板加工,3面板加工,4顶针固定板加工,5底板加工;模架加工细节:1,打编号要统一,模芯也要打上编号,应与模架上编号一致并且方向一致,装配时对准即可不易出错;2, A/B板加工即动定模框加工,a:A/B板加工应保证模框的平行度和垂直度为,b :铣床加工:螺丝孔,运水孔,顶针孔,机咀孔,倒角c:钳工加工:攻牙,修毛边;3,面板加工:铣床加工镗机咀孔或加工料嘴孔;4,顶针固定板加工:铣床加工:顶针板与B板用回针连结,B板面向上,由上而下钻顶针孔,顶针沉头需把顶针板反过来底部向上,校正,先用钻头粗加工,再用铣刀精加工到位,倒角;5,底板加工:铣床加工:划线,校正,镗孔,倒角;注:有些模具需强拉强顶的要加做强拉强顶机构,如在顶针板上加钻螺丝孔B:模芯加工:1飞边,2粗磨,3铣床加工,4钳工加工,5CNC粗加工,6热处理,7精磨,8CNC精加工,9电火花加工,10省模模芯加工细节:1粗加工飞六边:在铣床上加工,保证垂直度和平行度,留磨余量2粗磨:大水磨加工,先磨大面,用批司夹紧磨小面,保证垂直度和平行度在,留余量双边铣床加工:先将铣床机头校正,保证在之内,校正压紧工件,先加工螺丝孔,顶针孔,穿丝孔,镶针沉头开粗,机咀或料咀孔,分流锥孔倒角再做运水孔,铣R角;4钳工加工:攻牙,打字码5CNC粗加工6发外热处理HRC48-527 精磨;大水磨加工至比模框负,保证平行度和垂直度在之内8CNC精加工9电火花加工10省模,保证光洁度,控制好型腔尺寸;11加工进浇口,排气,锌合金一般情况下浇口开,排气开,铝合金浇口开排气开,塑胶排气开,尽量宽一点,薄一点;C:模具零件加工:1滑块加工,2压紧块加工,3分流锥浇口套加工,4镶件加工铝合金压铸模具的制作注意事项压铸件加工是一种利用高压强制将金属溶液压入形状复杂的金属模具内的一种精密铸造法,为了更好的保证压铸件的特点,对于铝合金压铸加工中的一些事项还是需要引起注意的:要知道,日常所用的合金金属的散热较好,很难形成瞬间难却的时候局部先后冷却的现象,而且合金的收缩率也相对较小,很难导致塑料产品缩水的现象,所以在压铸件加工设计的时候,不需要严格的厚度,但是要保证相对均匀;另外,对于压铸设备的选择根据合金的不同选用的设备也不尽相同,基本上可以分为两类,一类是冷室机,另一类是热室机;冷室机适合铜、镁、铝等高温合金,而锌、、锡、铅等一般使用热室机;。
压铸端盖设计说明书

目录摘要Abstract1.序言2.压铸模设计概述3设计任务及要求4压铸件的工艺性分析5分型面的选择6压铸机设备的选择和校核7浇注系统及排溢系统的设计8推出机构的设计9模具成型零件的设计10模架及其零件的设计11 模具零件的机加工工艺设计12心得体会参考文献文献综述摘要压铸是制造业的一种工艺,能够成型复杂的高精度的金属制品,多用于汽车制造,机械制造等。
本课题是对端盖进行模具设计并分析加工工艺。
本文介绍了现代模具制造技术的现状及其发展方向,重点说明了铝合金零件压铸模具的设计过程。
它主要从产品左端盖的工艺分析(主要包括脱模斜度、壁厚、孔、尺寸精度和表面粗糙度、收缩率等),成型方案的确定,压铸机的选用与确定,有色金属压铸模具的几大系统(浇注系统、成型零部件、冷却系统、排气系统、导向系统等)的分析与设计,各种技术数据的校核等方面出发,详细的介绍了压铸模具设计过程中的若干问题,并简要的介绍了压铸模具零件加工过程中的相关问题。
关键词:压铸工艺分析压铸成型设备模具结构加工1序言近年,模具增长十分迅速,高效率、自动化、大型、微型、精密、高寿命的模具在整个模具产量中所占的比重越来越大。
模具是利用其特定形状去成型具有一定的形状和尺寸制品的工具。
在各种材料加工工业中广泛的使用着各种模具。
例如金属铸造成型使用的砂型或压铸模具、金属压力加工使用的锻压模具、冷压模具等各种模具。
对模具的全面要求是:能生产出在尺寸精度、外观、物理性能等各方面都满足使用要求的公有制制品。
以模具使用的角度,要求高效率、自动化操作简便;从模具制造的角度,要求结构合理、制造容易、成本低廉。
作为模具专业的学生,综合检测理论在实际应用中的能力,除了平时的考试、实验测试外,更重要的是理论联系实际,即此次设计的课题为左端盖压铸模具。
本次毕业设计课题来源于生活,应用广泛,但成型难度大,模具结构较为复杂,对模具工作人员是一个很好的考验。
它能加强对压铸模具成型原理的理解,同时锻炼对压铸成型模具的设计和制造能力。
铝合金压铸模具结构剖析

铝合金压铸模具结构剖析
铝合金压铸模具结构剖析
铝合金压铸模具,是如何设计的?如题,产品图如下,有很多的薄片小筋板,分型面是平整的;学习参考就来下载图纸吧。
模具设计思路:
1.压铸模具设计,铝合金压铸模产品的三维外观,平面较于规则,对于新手模具设计师来说,都可以搞定模具设计;
2.压铸模具图纸产品后模侧的结构会有凸起特征,分型面直接用坐标拆分即可;
3.压铸模具设计-拔模检测,以正负0.5为分析值,其符合开模要求;
4.压铸模具图纸-内厚分析,两端有装配结构孔,其结构较厚,上面有装配的螺丝孔;
5.压铸模具图纸,其模具的外观整体结构,压铸模具不带工字板,要开码模槽;
6压铸模具图纸,滑块位置结构剖面线,其铲基原身留,斜导柱尽量做到16;
7.压铸模具图纸,分流锥剖面图,整体来说,压铸模具结构相对于简单,分流锥图解流道不好设计;
8.压铸模具设计教程,前模仁平面有凸起台阶,流道的对面是渣包,用UG拆分体一次可以把分型面设计好,渣包要拉伸、拔模、倒R 角;
9.压铸模具设计,后模结构设计,一般设计压铸模具,都需要用模流分析软件跑一跑,然后再画进胶流道,流道是压铸模具设计的一大难点;
10.压铸模具设计,滑块入子原身结构设计,侧孔用滑块抽芯,双螺丝固定在行位座上。
铝合金压铸模具设计论文

铝合金压铸模具设计论文1结构分析及分型面的确定铝合金连接套压铸件三维图,其形状特点是圆筒形零件,零件上部外形最大直径Φ99mm、长28mm处最大壁厚3mm有11处。
最小壁厚仅1mm共有10处,约12mm宽,28mm长。
这样的压铸件在顶出时极易顶碎,顶出极困难。
零件中部有12个方孔,需要12个侧抽芯。
下部最大壁厚6.25mm,在内孔Φ93mm与Φ80mm孔台阶处有12处小平台上设有顶杆。
E-E剖视图中设在零件中部尺寸25处。
此处上部外形由11段Φ99mm和12段Φ95mm圆弧构成),下部外形由12段Φ93.5mm和12段Φ92.6mm圆弧构成。
12个方孔内40°斜面内孔、槽宽42.5mm和槽宽12.5mm及槽宽8.2mm由动模型芯成形[3-4]。
2模具设计结构及原理2.1模具结构模具结构如图3所示。
此模具是安装在J1116压铸机上,模具厚度320mm、宽度580mm、高度520mm。
动模把模板1通过8个长螺钉2将支撑块3与中板15连接,中板与动模框16通过8个短螺钉37将动模镶件14和动模型芯29连接。
通过导向轴4将调整垫5、导向套6、复位杆8、顶杆9、顶杆压板10、推管11、顶杆固定板12连接并导向。
螺钉13连接顶杆压板10和顶杆固定板12。
动模框16上分别安装12对限位块21、斜滑块22、侧型芯23。
侧型芯与定模上的斜导柱18配合。
定模框25、斜导柱18、定模镶件27、浇口套28、直导柱33和定模把模板30由螺钉24连接固定。
模具分型面在动模镶件14和定模镶件27之间合模接触平面上。
2.2工作原理图3为模具合模状态,压铸机锤头压射、铝液充满型腔、凝固冷却、开模。
开模瞬间由于斜导柱18和斜滑块22孔上面有间隙,所以定模先脱模,然后斜导柱带动斜滑块及侧型芯23脱模。
在侧型芯完全脱模后,动模在开模的过程中2个顶出轴7对顶杆压板10有作用力同时传递给顶杆9和推管11将零件顶出,然后检查清理铸件、模腔、喷涂料、合模。
铝合金压铸模具浇排设计方案
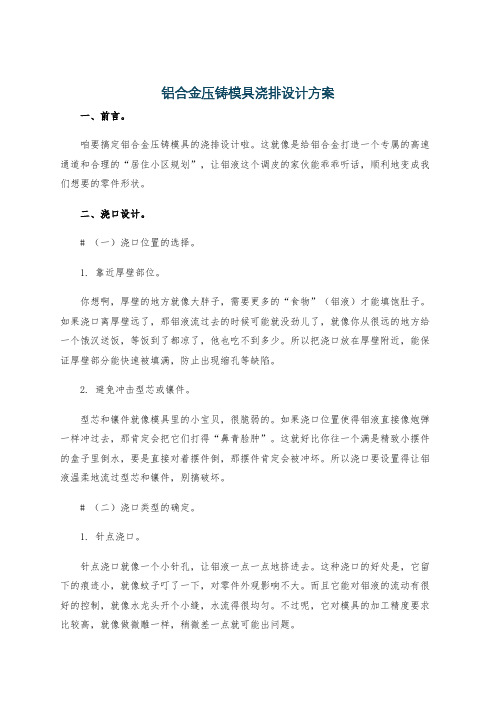
铝合金压铸模具浇排设计方案一、前言。
咱要搞定铝合金压铸模具的浇排设计啦。
这就像是给铝合金打造一个专属的高速通道和合理的“居住小区规划”,让铝液这个调皮的家伙能乖乖听话,顺利地变成我们想要的零件形状。
二、浇口设计。
# (一)浇口位置的选择。
1. 靠近厚壁部位。
你想啊,厚壁的地方就像大胖子,需要更多的“食物”(铝液)才能填饱肚子。
如果浇口离厚壁远了,那铝液流过去的时候可能就没劲儿了,就像你从很远的地方给一个饿汉送饭,等饭到了都凉了,他也吃不到多少。
所以把浇口放在厚壁附近,能保证厚壁部分能快速被填满,防止出现缩孔等缺陷。
2. 避免冲击型芯或镶件。
型芯和镶件就像模具里的小宝贝,很脆弱的。
如果浇口位置使得铝液直接像炮弹一样冲过去,那肯定会把它们打得“鼻青脸肿”。
这就好比你往一个满是精致小摆件的盒子里倒水,要是直接对着摆件倒,那摆件肯定会被冲坏。
所以浇口要设置得让铝液温柔地流过型芯和镶件,别搞破坏。
# (二)浇口类型的确定。
1. 针点浇口。
针点浇口就像一个小针孔,让铝液一点一点地挤进去。
这种浇口的好处是,它留下的痕迹小,就像蚊子叮了一下,对零件外观影响不大。
而且它能对铝液的流动有很好的控制,就像水龙头开个小缝,水流得很均匀。
不过呢,它对模具的加工精度要求比较高,就像做微雕一样,稍微差一点就可能出问题。
2. 侧浇口。
侧浇口就比较实在,像个小侧门。
铝液从侧面流进去,比较简单直接。
它适合一些形状不是特别复杂的零件。
这种浇口加工起来比较容易,就像盖个普通的小房子,不需要太多的技巧。
但是它可能会在零件表面留下比较明显的浇口痕迹,就像脸上有个小疤一样,影响美观。
三、流道设计。
# (一)主流道设计。
1. 尺寸确定。
主流道就像高速公路的主干道,要足够宽敞才能让铝液大军顺利通过。
一般来说,主流道的直径要根据零件的大小和所需铝液的量来确定。
如果零件大,需要的铝液多,主流道就得粗一点,就像大货车要走大路一样。
要是主流道太细了,铝液就会堵在那里,就像一群人挤在小胡同里,谁也走不动。
铝合金箱体压铸模具设计说明书

毕业设计(论文)任务书 2015 届机械工程及自动化专业题目:铝合金箱体压铸模具的设计子题:学生姓名:班级学号:指导教师:职称:所在系(教研室):机电与信息工程系下达日期:2014年7月4日完成日期:2015年5月8日摘要压铸模具是铸造液态模锻的一种方法,一种在专用的压铸模锻机上完成的工艺。
它的基本工艺过程是:金属液先低速或高速铸造充型进模具的型腔内,模具有活动的型腔面,它随着金属液的冷却过程加压锻造,既消除毛坯的缩孔缩松缺陷,也使毛坯的内部组织达到锻态的破碎晶粒。
毛坯的综合机械性能得到显著的提高。
本文运用大学所学的知识,了解压铸模具的工作原理,在此基础上,设计一款铝合金箱体压铸模具。
通过查找相关资料,了解铝合金箱体压铸模具的内部结构和工作原理,构建了铝合金箱体压铸模具组成结构的总的指导思想,从而得出了该铝合金箱体压铸模具的优点是高效,经济,并且运行效果好,运行平稳的结论。
关键词:铝合金箱体压铸模具;型腔;效率;模具AbstractThe environment of global economic development, China industries affected by other countries advanced technology at the same time, foreign enterprises and brand spread to more and more Chinese has become an opportunity. Cap pressing machine in industry through a variety of ways have been working with the relevant technology, and constantly improve their own strength and core competitiveness, and narrow the gap with developed countries.In the new market demand, update the sleeve pressing machine is a pressing matter of the moment. The production of pipe pressing machine equipment manufacturing enterprises to fully tap the potential of the market, vigorously develop the sleeves of large low cost pressing special machinery and equipment, plays a positive role in the evolution of automatic assembly, the assembly of mechanical equipment. There is a large pipe equipment on equipment safety index has strict requirements of production. In the production equipment of enterprises, give full consideration to the possible problems in the operation of the equipment, so as to reduce the noise pollution caused by vibration or improper operation of equipment phenomenon and manufacturing of domestic pipe pressing equipment with global appeal, economic, security and stability of the theme consistent. Increase and production pipe pressing equipment of new energy saving.Key word:pneumatic manipulator;cylinder;pneumatic loop;Fout degrees of freedom.目录摘要 (1)Abstract (2)第一章绪论 (3)1.1 模具介绍 (4)1.2 模具在加工工业中的地位................... 错误!未定义书签。
压铸模设计压铸件结构设计及压铸工艺

压铸模设计、压铸件结构设计及压铸工艺引言压铸是一种常用的金属零件制造方法,其通过将熔化的金属注入到预先加工好的模具中,通过压力将金属冷却固化成型。
在压铸过程中,压铸模具的设计、压铸件结构的设计以及压铸工艺的选择都是至关重要的。
本文将分别介绍压铸模设计的相关要点、压铸件结构设计的原则以及压铸工艺的选择。
压铸模设计要点压铸模具是进行压铸加工的关键工具,其设计的合理与否直接影响到产品质量和生产效率。
下面是一些压铸模设计的要点:1.模具材料选择:常见的模具材料有钢、铝合金等,根据压铸件的要求和使用场景选择合适的模具材料,以确保模具具有足够的强度和耐磨性。
2.结构设计:模具的结构要合理,与压铸件的形状相匹配,避免出现脱模困难、变形等问题。
同时,要考虑到模具的拆卸和维护,方便进行清理和更换模具零部件。
3.冷却系统设计:在模具中设置合适的冷却系统,以提高压铸件的凝固速度并避免产生缺陷。
冷却系统的设计要考虑到冷却介质的流动性、冷却效果以及与压铸件形状的匹配等因素。
4.压铸模表面处理:对模具表面进行适当的处理,如喷涂涂层、表面硬化等,以延长模具的使用寿命和提高模具的抗腐蚀性能。
压铸件结构设计原则压铸件结构设计的目标是在满足产品功能和外观要求的前提下,尽量减少结构复杂性和提高生产效率。
以下是一些常用的压铸件结构设计原则:1.壁厚均匀:保持压铸件的壁厚均匀,避免厚度过大或过薄导致不均匀收缩和应力集中。
2.避免尖角和过度薄壁结构:减少压铸件中的尖角和过度薄壁结构,因为这些部分容易引起变形和缺陷。
3.引导放料设计:在压铸件结构中设置合适的引导放料设计,以确保熔融金属能够充分填充整个模腔,并避免产生气孔和冷却不均。
4.滑动方向和出料设计:考虑到模具的拆卸和压铸件的出料,结构中应合理设置滑动方向和出料设计,以方便模具的安装和压铸件的脱模。
压铸工艺选择在确定了压铸模具设计和压铸件结构设计后,还需要选择适合的压铸工艺。
以下是一些常用的压铸工艺选择要点:1.压铸机选择:根据压铸件的尺寸和形状,选择合适的压铸机型号和规格。
铝合金压铸模具设计论文

铝合金压铸模具设计论文铝合金压铸是目前工业界中应用广泛的一种铸造方法,其在汽车、航空航天、电子等诸多领域都有着重要的应用。
铝合金压铸模具设计则是铝合金压铸过程中一个不可或缺的环节,对于产品的质量、生产效率以及成本控制都有着至关重要的影响。
本文旨在探讨铝合金压铸模具设计的相关知识。
一、铝合金压铸模具设计的流程铝合金压铸模具的设计流程通常包括以下几个步骤:1.产品设计阶段在产品设计阶段,需要考虑铝合金产品的外形、尺寸、重量、材料等因素,并确定产品的加工精度、表面质量和使用要求,为后续模具设计提供基础和限制条件。
2.模具结构设计模具结构设计是铝合金压铸模具设计的重要环节,主要包括模具类型、结构形式、工作方式、各部件的尺寸和形状等方面。
一般情况下,铝合金压铸模具结构应具有良好的刚度和稳定性,合理的材料利用率,以及方便维修和调整等特点。
3.模具零部件设计模具零部件设计是铝合金压铸模具设计的细节部分。
它涉及到各种紧固件、导向构件、卡块、注流口等部件的设计和选型。
在设计这些零部件时,需要考虑它们的材料选择、可靠性、加工精度、耐磨性以及易于更换等因素。
4.模具加工模具加工是将设计好的模具结构和零部件加工成一整个模具的过程。
它包括各种加工工艺和设备的选择和操作,如钳工、磨床、铣床、数控加工中心等。
加工质量的好坏将直接影响到模具的性能和使用寿命。
二、铝合金压铸模具设计的注意点在进行铝合金压铸模具设计时,要注意以下几点:1.设计合理的铸件缩孔铝合金压铸过程中,铸件总会产生一定的缩孔和气孔,这将影响铸件的力学性能和表面质量。
因此,在模具设计中,需要合理地设计铸件的缩孔位置和大小,以便减少铸件缩孔和气孔的产生。
2.合理设置注流系统和冷却系统注流系统和冷却系统是铸造中非常重要的两个方面。
注流系统应能够保证铝合金液体的顺利进入铸型腔内,并恰当地分流、润滑、冷却。
冷却系统则是为了保证铸件的制品周期和产品合格率而设置,以便加快铝合金的凝固速度,提高产品的表面质量和尺寸精度。
铝合金轮毂压铸模具设计
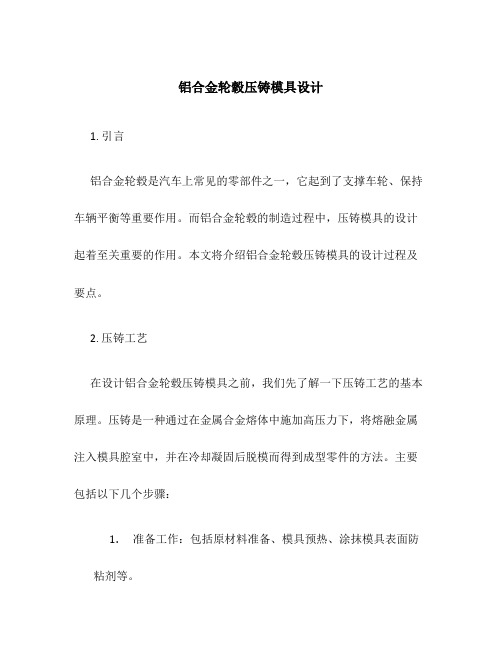
铝合金轮毂压铸模具设计1. 引言铝合金轮毂是汽车上常见的零部件之一,它起到了支撑车轮、保持车辆平衡等重要作用。
而铝合金轮毂的制造过程中,压铸模具的设计起着至关重要的作用。
本文将介绍铝合金轮毂压铸模具的设计过程及要点。
2. 压铸工艺在设计铝合金轮毂压铸模具之前,我们先了解一下压铸工艺的基本原理。
压铸是一种通过在金属合金熔体中施加高压力下,将熔融金属注入模具腔室中,并在冷却凝固后脱模而得到成型零件的方法。
主要包括以下几个步骤:1.准备工作:包括原材料准备、模具预热、涂抹模具表面防粘剂等。
2.注射:将熔融金属注入模具中,填充整个腔室。
3.压实:在金属熔池注入后,通过高压将其压实,确保填充均匀。
4.冷却固化:通过冷却水或其他冷却介质,使金属迅速冷却凝固。
5.脱模:将压铸件从模具中取出,并进行后续加工。
3. 铝合金轮毂压铸模具的设计要点在设计铝合金轮毂压铸模具时,需要考虑以下几个关键要点:3.1 模具材料选择常用的模具材料包括工具钢、合金钢、硬质合金等。
在选择模具材料时,需要考虑到铝合金液态腐蚀性强的特点,以及模具需要承受高压力和高温的环境。
因此,通常选择耐磨性好、耐腐蚀性强的材料。
3.2 模具结构设计模具的结构设计必须考虑到成型零件的形状和尺寸。
在设计铝合金轮毂压铸模具时,需要注意以下几点:•模具应该具有良好的填充性能,确保熔融金属在注射过程中能够充分填满模具腔室,并保持均匀分布。
•模具应该考虑到压实过程中可能产生的应力和变形情况,避免模具破裂或变形。
•模具应该具有良好的冷却系统,通过冷却水或其他冷却介质,使熔融金属迅速冷却凝固,减少缩孔和气孔等缺陷的产生。
3.3 模具表面处理铝合金轮毂表面的光洁度要求较高,因此压铸模具的表面处理至关重要。
常见的表面处理方法包括抛光、电镀、喷涂等,通过这些方法可以得到光洁度较高、质量较好的铝合金轮毂。
4. 总结铝合金轮毂压铸模具的设计是铝合金轮毂制造过程中的重要一环。
本文介绍了铝合金轮毂压铸模具设计的基本原理和要点,包括模具材料选择、模具结构设计和模具表面处理等。
端盖铸造工艺设计

端盖铸造工艺设计
端盖作为汽车发动机的重要零部件之一,扮演着重要的连接和密封作用。
而其制作的工艺和质量也直接关系到发动机的安全和性能。
下面我们就来讲解一下端盖铸造工艺设计的相关知识。
1、材料选择
用于制作端盖的材料有很多种,例如铝合金、铸铁等。
根据每种材料的物理特性和机械性能,可选用不同的材质来进行端盖铸造。
2、模具设计
制作端盖需要一个模具来进行铸造成型。
模具设计应根据实际需要来进行,包括模具尺寸、结构设计、冷却系统设计等。
3、溶液准备
铸造前需要将金属材料加热至一定温度,并在其中加入一定比例的合金元素,制成铸造用的溶液。
溶液熔化后应该经过过滤,并去除其中的杂质。
4、浇注方式
对于铸造的材料不同,其浇注方式也是不同的。
一般铝合金使用重力浇注法,铸铁则采用压铸法或振动拍捣法。
浇注时需注意溶液温度、浇注时间、流速等参数的控制。
5、冷却处理
铸造完成后,进行冷却处理可使材料有更好的抗拉强度。
此外,还可以通过机械加工和表面处理来达到理想的形态和性能。
端盖铸造工艺设计是非常重要的一环,需要设计师和工程师们的共同努力。
通过合理的材料选择、模具设计和浇注方式,以及严格的制品质量控制,才能保证端盖铸件的质量和可靠性。
端盖零件压力铸造工艺设计

目录目录 (1)一、前言 (2)二、压铸件工艺性分析及设计 (3)三、压铸机的选用 (8)四、压铸型设计 (11)五、压力铸造常规工艺的确定 (24)六、熔炼工艺 (26)总结 (40)参考文献 (41)一、前言1、压铸的基本概念压铸是将熔融状态或半熔融状态合金浇入压铸机的压室,在高压力的作用下,以极高的速度充填在压铸模(压铸型)的型腔内,并在高压下使熔融合金冷却凝固而形成的高效益、高效率的精密铸造方法。
2、压铸生产的特点及应用范围(1)压铸有如下的优点:1)铸件的尺寸精度和表面粗糙度要求很高2)铸件的强度和表面硬度较高3)可以压铸形状复杂的薄壁铸件4)生产率极高5)可省略装配操作和简化制造工序(2)压铸的应用范围压铸是近代金属加工工艺中发展较快的一种高效率、少无切削的金属成形精密铸造方法。
目前,压铸广泛应用于制造非铁合金的压铸件。
由于压铸工艺的特点,故使用的合金是结晶温度范围小、热裂倾向小以及收缩系数小的压铸铝、镁、及部铜的合金。
在非铁合金的压铸中,铝合金所占比例最高(约30%~60%)。
3、铝合金压铸业的发展及现状压力铸造工艺的诸多特点,使其在提高有色金属合金铸件的精度水平、生产效率、表面质量等方面显示出了巨大优势。
随着汽车、摩托车等工业的发展,以及提高压铸件质量、节省能耗、降低污染等设计要求的实现,有色金属合金压铸件、特别是轻合金(铝及铝合金)压铸件的应用范围在快速扩张。
有资料表明:工业发达国家用铝合金及铝合金铸件代替钢铁铸件正在成为重要的发展趋势。
目前压铸已成为汽车用铝合金成形过程中应用最广泛的工艺之一,在各种汽车成型工艺方法中占49%。
二、压铸件工艺性分析及设计压铸件工艺设计是压铸型设计前必须做的工作,此时应大致确定所使用的压铸机、合适的压射压力和压射速度。
与此同时,应精确地设计铸件的分型面、浇注排气系统,因为其对压铸件的生产和质量具有决定性的作用。
1、零件图图2-1为端盖零件图,材料为ZALSi12,合金代号为ZL102。
毕业设计任务书-铝合金端盖压铸工艺及模具设计
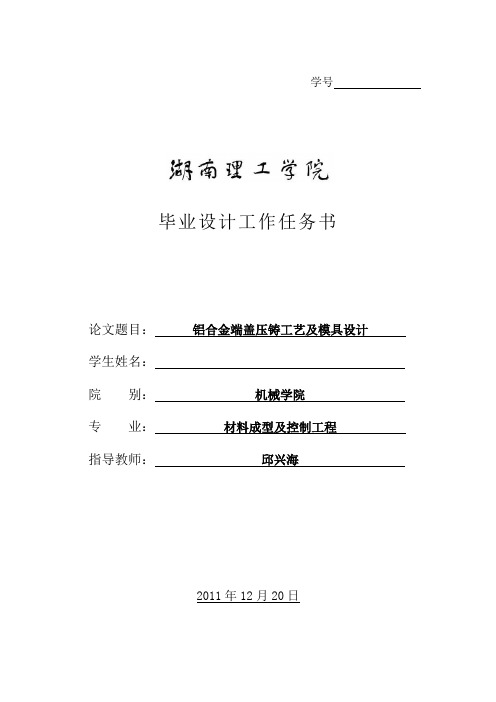
(3)模具设计方案应论证充分,做到结构合理、技术先进、工艺性好、经济耐用,工艺计算应正确无误,设计图样应尽量符合国家和行业相关技术标准,并基本达到工程应用目标。
(4)论文内容应不少于12000字(包括不少于300字的中英文摘要),并符合一般科技论文格式要求。论文叙述应条理清楚,论据充分,用语及符号应符合技术规范,尽量避免错别字和不通顺的语句。
通过毕业设计工作通过毕业设计工作通过毕业设计工作培养和训练学生正确运用所学专业培养和训练学生正确运用所学专业培养和训练学生正确运用所学专业理论知识解决实际工程问题理论知识解决实际工程问题理论知识解决实际工程问题掌握压铸模具设计的基本方法和步骤掌握压铸模具设计的基本方法和步骤掌握压铸模具设计的基本方法和步骤熟熟练练练autocadautocadautocad等软件的应用等软件的应用等软件的应用初步具备一般压铸件的工艺分析初步具备一般压铸件的工艺分析初步具备一般压铸件的工艺分析工艺计算工艺计算工艺计算及压铸模具总体和主要零部件结构设计的能力和撰写论文的能力
(2)2.27~3.25:加工整理技术资料,对零件图进行压铸工艺分析,合理选择压铸机和模具设计方案,完成各项理论计算工作。
(3)3.26~4.22:利用AutoCAD软件绘制零件图,完成模具装配图设计和成型部分的零件图设计,并完成撰写论文前的相关工作。
(4)4.23~13:完成毕业论文初稿,进行毕业设计中期检查。
(5)5.14~5.20:修改论文并装订。
(6)5.21以后:论文答辩。
教研室意见:
负责人签名:
注:本任务书一式三份,由指导教师填写,经教研室审批后一份下达给学生,一份交指导教师,一份留系里存档。
基于ProCAST的铝合金压铸模具设计PPT课件

压室直径/mm
40,50,60
项目名称 最大金属浇注量/Kg 铸件投影面积/cm2
压实压力(小~大)/Mpa
压射行程/mm 空循环周期/s 管路工作压力/Mpa 电动机功率/KW 机器重量/Kg 外形尺寸(长X宽X高)/mm
数值 (铝)1.4 94~374
30~118
320 7 12 11 5000 4550X1160X1800
◦ 水冷
冷却水道直径:
◦ 8mm
冷却水道示意图
2020/3/23
12
材料:
◦ 4Cr5MoV1Si
热处理:
◦ 退火 <229HB ◦ 淬火 56-58HRC ◦ 回火 43-47HRC
型芯镶块零件图
2020/3/23
13
材料:
◦ 4Cr5MoV1Si
热处理:
◦ 退火 <229HB ◦ 淬火 56-58HRC ◦ 回火 43-47HRC
流场
2020/3/23
8
将内浇口和主 流道平滑连接
设置溢流槽 增加内浇口宽
度
改进方法
浇注系统示意图
2020/3/23
9
温度
流场
2020/3/23
10
溢流槽:
◦ 半圆槽形,每个铸件 边缘设置三个
排气道
◦ 宽度10-15mm,深度 0.03mm
排溢系统示意图
2020/3/23
11
冷却方式:
50x100 动模套板螺钉 6xM12
205x25 推板螺钉
M8
205x16 模座螺钉
4xM16
压铸模架尺寸表
2020/3/23
15
2020/3/23
- 1、下载文档前请自行甄别文档内容的完整性,平台不提供额外的编辑、内容补充、找答案等附加服务。
- 2、"仅部分预览"的文档,不可在线预览部分如存在完整性等问题,可反馈申请退款(可完整预览的文档不适用该条件!)。
- 3、如文档侵犯您的权益,请联系客服反馈,我们会尽快为您处理(人工客服工作时间:9:00-18:30)。
key words:Chassis Craft analysis Apparatus of shaping Mould structure Processing
摘要
Abstract
1.序言2.ຫໍສະໝຸດ 铸模设计概述3设计任务及要求
4压铸件的工艺性分析
5分型面的选择
6压铸机设备的选择和校核
7浇注系统及排溢系统的设计
关键词:压铸工艺分析压铸成型设备模具结构加工
Die-casting is a manufacturing process,it can mold the complex and high accurate metal product ,used in automobile manufacturing, machinery manufacturing and so on. The subject is about the design of Aluminum shell mold and process analysis.
由于金属压铸成型有不可比拟的突出优点,在工业技术快速发展的年代,必将得到越来越广泛的应用。特别是在大批量的生产中,虽然模具成本高一些,但总的说来,其生产的综合成本则得到大幅度的降低。在这个讲究微利的竞争时代,采用金属压铸成型技术,更有其积极和明显的经济价值。近年来,汽车工业的飞速发展给压铸成型的生产带来了机遇。处于可持续发展和环境保护的需要,汽车轻量化是实现环保、节能、节材、高速的最佳途径。因此,用压铸铝合金件代替传统的钢铁件,可使汽车质量减轻30%以上。同时,压铸铝合金件还有一个显著的特点是热传导性能良好,热量散失的快,提高了汽车的行车安全性。因此,金属压铸行业正面临着发展的机遇,其应用前景十分广阔。
作为模具专业的学生,综合检测理论在实际应用中的能力,除了平时的考试、实验测试外,更重要的是理论联系实际,即此次设计的课题为左端盖压铸模具。本次毕业设计课题来源于生活,应用广泛,但成型难度大,模具结构较为复杂,对模具工作人员是一个很好的考验。它能加强对压铸模具成型原理的理解,同时锻炼对压铸成型模具的设计和制造能力。
8推出机构的设计
9模具成型零件的设计
10模架及其零件的设计
11模具零件的机加工工艺设计
12心得体会
参考文献
文献综述
1序言
近年,模具增长十分迅速,高效率、自动化、大型、微型、精密、高寿命的模具在整个模具产量中所占的比重越来越大。模具是利用其特定形状去成型具有一定的形状和尺寸制品的工具。在各种材料加工工业中广泛的使用着各种模具。例如金属铸造成型使用的砂型或压铸模具、金属压力加工使用的锻压模具、冷压模具等各种模具。对模具的全面要求是:能生产出在尺寸精度、外观、物理性能等各方面都满足使用要求的公有制制品。以模具使用的角度,要求高效率、自动化操作简便;从模具制造的角度,要求结构合理、制造容易、成本低廉。
摘 要
压铸是制造业的一种工艺,能够成型复杂的高精度的金属制品,多用于汽车制造,机械制造等。本课题是对端盖进行模具设计并分析加工工艺。
本文介绍了现代模具制造技术的现状及其发展方向,重点说明了铝合金零件压铸模具的设计过程。它主要从产品左端盖的工艺分析(主要包括脱模斜度、壁厚、孔、尺寸精度和表面粗糙度、收缩率等),成型方案的确定,压铸机的选用与确定,有色金属压铸模具的几大系统(浇注系统、成型零部件、冷却系统、排气系统、导向系统等)的分析与设计,各种技术数据的校核等方面出发,详细的介绍了压铸模具设计过程中的若干问题,并简要的介绍了压铸模具零件加工过程中的相关问题。
This paper has introduced the current situation of the modern mould manufacturing technology and developing direction, have proved especially that the aluminum alloy chassis parts die casting design process of the mould . It mainly since products craft of chassis analysis (mainly including drawing of patterns slope, wall thick, hole, size precision and surface roughness , shrinking rate ,etc.), sureness of the shaping scheme, exertion and fixing of the injecting machine, Non-ferrous metal casting molds of several big analysis and design of system (pour system , shaping spare part , cooling system , exhaust system , guidance system ,etc.) of mould, the respects , such as check of different technical data ,etc. set out, the detailed introduction injects several questions in the design process of the mould , and the brief introduction axle seat injects the relevant problem in the part processing course of the mould .