水泥厂方案.
水泥厂技改项目工程方案

水泥厂技改项目工程方案一、项目概况随着我国经济的快速发展,建筑行业的需求不断增长,对水泥产品的需求量也在不断增加。
然而,传统的水泥生产工艺已经不能满足市场需求,而且存在着一系列的环保隐患。
因此,对水泥厂进行技改是当务之急。
本项目选择对某水泥厂进行技改,主要包括提高生产效率、降低能耗、改善产品质量、加强环保措施等内容,旨在使水泥厂达到国际先进水平,推动水泥工业的可持续发展。
二、技改目标1. 提高生产效率:通过更新设备、改进工艺、优化管理等措施,提高生产效率,降低生产成本。
2. 降低能耗:引进节能设备、优化能源结构、改进工艺等措施,降低能耗,提高能源利用率。
3. 改善产品质量:提高产品品质,满足市场需求,提升企业竞争力。
4. 加强环保措施:减少排放物、改善环境质量,达到国家环保标准。
三、技改内容1. 更新设备:更新煤磨、窑炉、磨机等关键设备,提高设备先进化程度,确保设备运行的稳定性和可靠性。
2. 改进工艺:优化生产工艺,提高原料燃烧效率,减少二氧化碳排放,改进熟料烧成工艺,降低能耗,提高生产效率。
3. 引进新技术:引进新型水泥生产技术,例如新型磨煤设备、高效环保型窑炉、高性能磨机等,提高生产效率,降低能耗,改善产品质量。
4. 环保设施建设:增加除尘设备、脱硫脱硝设备等环保设施,减少大气污染物排放量,改善环境质量。
5. 优化管理:建立科学的生产管理体系,提高工人操作水平,提高生产效率,降低人为因素造成的损耗。
四、实施方案1. 技改前期准备(1)确定技改项目的总体方案、投资规模、建设期限等(2)进行现场勘查,了解已有设备及工艺流程(3)编制技改项目实施的可行性研究报告,明确技改内容和目标(4)进行技术比选,确定更新设备和引进新技术的方案(5)进行环境影响评价,确定环保设施建设的内容和规模(6)编制技改项目施工图纸和施工方案2. 技改实施阶段(1)更新设备:根据技术比选结果选购更新设备,并由专业人员进行设备安装和调试。
水泥厂工程改造施工方案
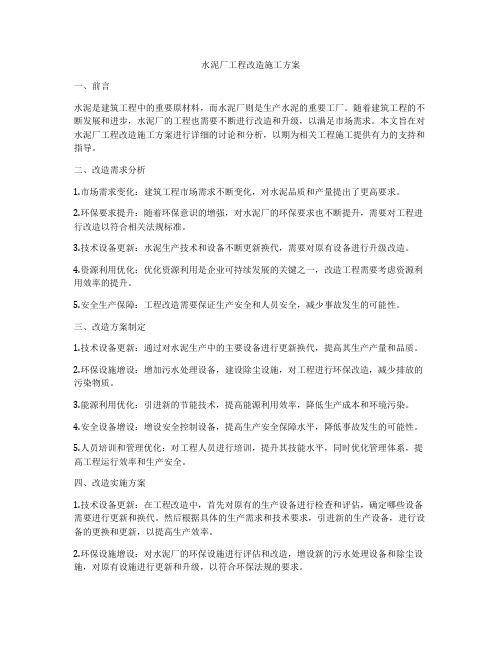
水泥厂工程改造施工方案一、前言水泥是建筑工程中的重要原材料,而水泥厂则是生产水泥的重要工厂。
随着建筑工程的不断发展和进步,水泥厂的工程也需要不断进行改造和升级,以满足市场需求。
本文旨在对水泥厂工程改造施工方案进行详细的讨论和分析,以期为相关工程施工提供有力的支持和指导。
二、改造需求分析1.市场需求变化:建筑工程市场需求不断变化,对水泥品质和产量提出了更高要求。
2.环保要求提升:随着环保意识的增强,对水泥厂的环保要求也不断提升,需要对工程进行改造以符合相关法规标准。
3.技术设备更新:水泥生产技术和设备不断更新换代,需要对原有设备进行升级改造。
4.资源利用优化:优化资源利用是企业可持续发展的关键之一,改造工程需要考虑资源利用效率的提升。
5.安全生产保障:工程改造需要保证生产安全和人员安全,减少事故发生的可能性。
三、改造方案制定1.技术设备更新:通过对水泥生产中的主要设备进行更新换代,提高其生产产量和品质。
2.环保设施增设:增加污水处理设备,建设除尘设施,对工程进行环保改造,减少排放的污染物质。
3.能源利用优化:引进新的节能技术,提高能源利用效率,降低生产成本和环境污染。
4.安全设备增设:增设安全控制设备,提高生产安全保障水平,降低事故发生的可能性。
5.人员培训和管理优化:对工程人员进行培训,提升其技能水平,同时优化管理体系,提高工程运行效率和生产安全。
四、改造实施方案1.技术设备更新:在工程改造中,首先对原有的生产设备进行检查和评估,确定哪些设备需要进行更新和换代。
然后根据具体的生产需求和技术要求,引进新的生产设备,进行设备的更换和更新,以提高生产效率。
2.环保设施增设:对水泥厂的环保设施进行评估和改造,增设新的污水处理设备和除尘设施,对原有设施进行更新和升级,以符合环保法规的要求。
3.能源利用优化:通过引进新的节能技术和设备,实现水泥生产过程中能源利用效率的提升,降低生产成本和环境污染。
4.安全设备增设:对工程的安全设备进行评估和改造,增设新的安全控制设备,提高生产安全保障水平,降低事故发生的可能性。
2024年水泥厂安全生产实施方案范文(2篇)
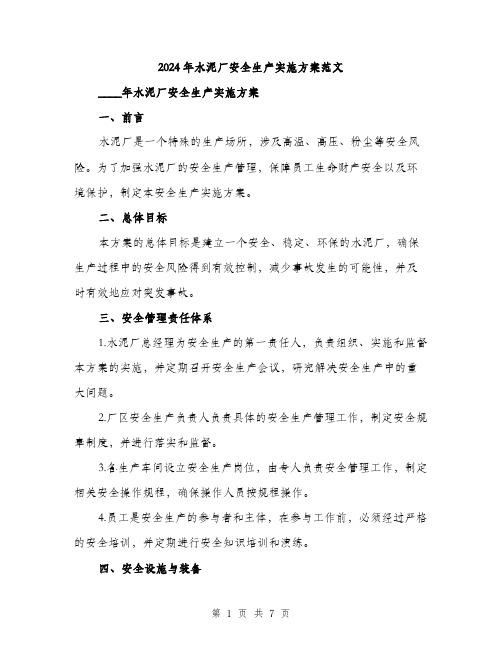
2024年水泥厂安全生产实施方案范文____年水泥厂安全生产实施方案一、前言水泥厂是一个特殊的生产场所,涉及高温、高压、粉尘等安全风险。
为了加强水泥厂的安全生产管理,保障员工生命财产安全以及环境保护,制定本安全生产实施方案。
二、总体目标本方案的总体目标是建立一个安全、稳定、环保的水泥厂,确保生产过程中的安全风险得到有效控制,减少事故发生的可能性,并及时有效地应对突发事故。
三、安全管理责任体系1.水泥厂总经理为安全生产的第一责任人,负责组织、实施和监督本方案的实施,并定期召开安全生产会议,研究解决安全生产中的重大问题。
2.厂区安全生产负责人负责具体的安全生产管理工作,制定安全规章制度,并进行落实和监督。
3.各生产车间设立安全生产岗位,由专人负责安全管理工作,制定相关安全操作规程,确保操作人员按规程操作。
4.员工是安全生产的参与者和主体,在参与工作前,必须经过严格的安全培训,并定期进行安全知识培训和演练。
四、安全设施与装备1.厂区周界设立安全围栏,并设置安全出入口,进行严格的管理和监控。
2.生产车间内设置清晰的安全警示标志,标明危险区域和安全通道,提醒员工注意安全。
3.安全通道和应急出口保持畅通,定期进行检查和维护,保证在紧急情况下能够迅速疏散人员。
4.按照国家标准配置消防设备,将消防器材摆放在易于取用的位置,并定期进行消防器材使用演练和检查。
5.生产车间内设置安全监控系统,实时监测生产环节,及时发现异常情况。
五、安全生产规章制度1.制定《水泥厂安全生产规定》,明确各岗位的安全责任和操作规程,员工必须严格遵守。
2.制定《水泥厂事故应急预案》,包括火灾、爆炸、泄漏等突发事件的预案,明确人员疏散、报警、救援等相关措施。
3.制定《水泥厂职业卫生管理办法》,建立健全职业卫生管理体系,确保员工的身体健康。
六、安全生产培训与演练1.新员工入职前必须进行安全培训,包括安全操作规程、应急逃生等内容。
2.定期组织员工进行安全知识培训,加强员工的安全意识和应急处理能力。
水泥厂主体工程施工方案

一、工程概况本工程为某水泥厂主体工程,主要包括水泥磨房、原料库、成品库、熟料库、窑炉及辅助设施等。
工程总投资XX亿元,工期为XX个月。
二、施工组织设计1. 施工队伍根据工程特点,组建一支具有丰富经验、技术过硬、责任心强的施工队伍。
施工队伍应包括项目经理、施工员、质量员、安全员、材料员等。
2. 施工工艺(1)水泥磨房:采用钢筋混凝土框架结构,基础采用独立基础,屋面采用钢屋面。
(2)原料库、成品库、熟料库:采用钢筋混凝土框架结构,基础采用独立基础,屋面采用钢屋面。
(3)窑炉及辅助设施:采用钢筋混凝土框架结构,基础采用独立基础,屋面采用钢屋面。
3. 施工进度计划根据工程特点和施工队伍实际情况,制定合理的施工进度计划,确保工程按期完成。
三、施工方法及技术措施1. 施工准备(1)施工现场的平整、排水、供电、供水等基础设施。
(2)施工材料的采购、运输、验收、储存等。
(3)施工人员的培训、考核。
2. 施工工艺(1)基础施工:采用人工挖土,机械吊装,混凝土浇筑。
(2)主体结构施工:采用钢筋混凝土框架结构,先进行柱、梁、板的钢筋绑扎,然后进行混凝土浇筑。
(3)屋面施工:采用钢屋面,先进行屋面板安装,然后进行屋面防水。
3. 施工质量控制(1)施工过程中,严格控制原材料的质量,确保施工质量。
(2)严格按照施工图纸和施工规范进行施工,确保施工质量。
(3)加强施工过程中的质量检查,发现问题及时整改。
4. 施工安全措施(1)施工现场设置安全警示标志,明确安全操作规程。
(2)施工人员必须佩戴安全帽、安全带等防护用品。
(3)施工现场设置安全通道,确保人员安全通行。
(4)加强施工现场的安全管理,防止安全事故发生。
四、施工进度安排1. 第一阶段:基础施工,工期为2个月。
2. 第二阶段:主体结构施工,工期为4个月。
3. 第三阶段:屋面施工,工期为1个月。
4. 第四阶段:辅助设施施工,工期为1个月。
5. 第五阶段:竣工验收,工期为1个月。
水泥成品厂房施工方案
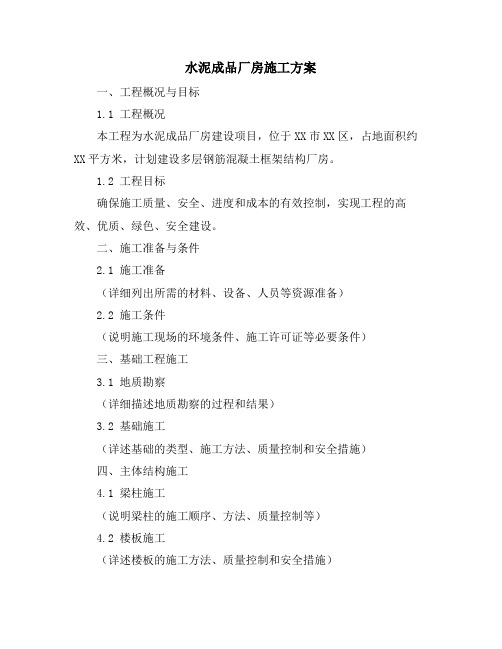
水泥成品厂房施工方案一、工程概况与目标1.1 工程概况本工程为水泥成品厂房建设项目,位于XX市XX区,占地面积约XX平方米,计划建设多层钢筋混凝土框架结构厂房。
1.2 工程目标确保施工质量、安全、进度和成本的有效控制,实现工程的高效、优质、绿色、安全建设。
二、施工准备与条件2.1 施工准备(详细列出所需的材料、设备、人员等资源准备)2.2 施工条件(说明施工现场的环境条件、施工许可证等必要条件)三、基础工程施工3.1 地质勘察(详细描述地质勘察的过程和结果)3.2 基础施工(详述基础的类型、施工方法、质量控制和安全措施)四、主体结构施工4.1 梁柱施工(说明梁柱的施工顺序、方法、质量控制等)4.2 楼板施工(详述楼板的施工方法、质量控制和安全措施)五、屋面与防水工程5.1 屋面施工(说明屋面的材料选择、施工方法、质量控制等)5.2 防水工程(详述防水层的施工方法、质量控制和安全措施)六、装饰与保温工程6.1 内外装饰(说明内外装饰的材料选择、施工方法、质量控制等)6.2 保温工程(详述保温材料的选择、施工方法、质量控制和安全措施)七、设备安装与调试7.1 设备选型与采购(说明设备的选型原则、采购流程等)7.2 设备安装与调试(详述设备的安装方法、调试流程、质量控制和安全措施)八、质量与安全管理8.1 质量管理(详述质量管理体系、质量控制措施、质量检查流程等)8.2 安全管理(说明安全管理体系、安全培训、安全措施等)九、工程验收与交付9.1 工程验收(详述验收流程、验收标准、验收记录等)9.2 工程交付(说明交付流程、交付标准、交付文件等)以上是水泥成品厂房施工方案的主要内容,具体施工细节需要根据实际情况进行调整和完善。
在施工过程中,应严格遵守国家相关法规和规范,确保工程的高质量、高效率、高安全性。
水泥厂安全生产攻坚三年行动方案范文
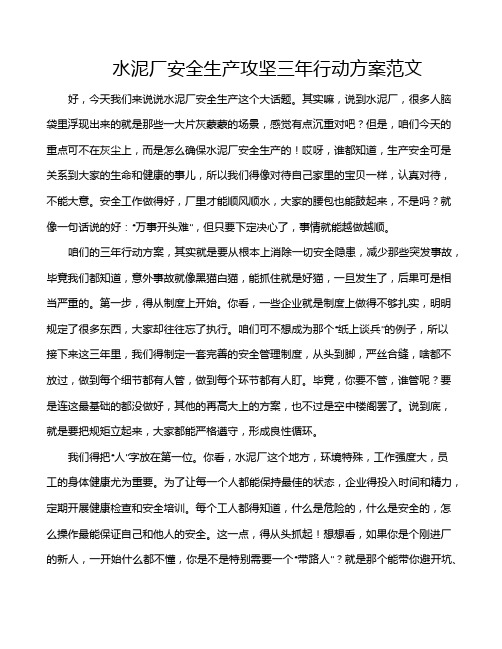
水泥厂安全生产攻坚三年行动方案范文好,今天我们来说说水泥厂安全生产这个大话题。
其实嘛,说到水泥厂,很多人脑袋里浮现出来的就是那些一大片灰蒙蒙的场景,感觉有点沉重对吧?但是,咱们今天的重点可不在灰尘上,而是怎么确保水泥厂安全生产的!哎呀,谁都知道,生产安全可是关系到大家的生命和健康的事儿,所以我们得像对待自己家里的宝贝一样,认真对待,不能大意。
安全工作做得好,厂里才能顺风顺水,大家的腰包也能鼓起来,不是吗?就像一句话说的好:“万事开头难”,但只要下定决心了,事情就能越做越顺。
咱们的三年行动方案,其实就是要从根本上消除一切安全隐患,减少那些突发事故,毕竟我们都知道,意外事故就像黑猫白猫,能抓住就是好猫,一旦发生了,后果可是相当严重的。
第一步,得从制度上开始。
你看,一些企业就是制度上做得不够扎实,明明规定了很多东西,大家却往往忘了执行。
咱们可不想成为那个“纸上谈兵”的例子,所以接下来这三年里,我们得制定一套完善的安全管理制度,从头到脚,严丝合缝,啥都不放过,做到每个细节都有人管,做到每个环节都有人盯。
毕竟,你要不管,谁管呢?要是连这最基础的都没做好,其他的再高大上的方案,也不过是空中楼阁罢了。
说到底,就是要把规矩立起来,大家都能严格遵守,形成良性循环。
我们得把“人”字放在第一位。
你看,水泥厂这个地方,环境特殊,工作强度大,员工的身体健康尤为重要。
为了让每一个人都能保持最佳的状态,企业得投入时间和精力,定期开展健康检查和安全培训。
每个工人都得知道,什么是危险的,什么是安全的,怎么操作最能保证自己和他人的安全。
这一点,得从头抓起!想想看,如果你是个刚进厂的新人,一开始什么都不懂,你是不是特别需要一个“带路人”?就是那个能带你避开坑、少走弯路的师傅。
所以说,安全培训这一块,咱得做得细致入微,不怕麻烦,不怕重复,只有大家都成为安全小能手,咱厂的安全生产才能有保障。
然后嘛,咱们还得重视设备的维护保养。
现在很多企业的设备其实都很先进,可要是平时不注意保养,那也是“空中楼阁”。
水泥厂施工组织设计方案

水泥厂施工组织设计方案1. 引言该施工组织设计方案旨在针对水泥厂的施工过程,提供合理且高效的组织设计,确保施工项目的顺利进行。
本方案包括施工组织设计的原则、流程、人员配置、安全措施等内容。
2. 施工组织设计原则- 安全原则:以人员安全为首要考虑,保障施工过程中的安全性。
- 高效原则:通过精细化的组织设计,提高施工效率,确保项目进度。
- 经济原则:合理配置人力、物力资源,最大限度降低成本。
- 环保原则:采取环保措施,减少对环境的影响。
- 合规原则:遵守相关法律法规和建设工程规范,确保施工合规。
3. 施工组织设计流程3.1 资料准备- 收集水泥厂施工相关的设计文件、图纸及技术规范要求。
- 确认施工所需的人力、物力资源及工期要求。
3.2 施工工序划分- 对水泥厂施工过程进行合理的工序划分,确定施工的先后顺序和依赖关系。
3.3 人员配置- 根据施工工序和工期,合理配置各个工种的施工人员和管理人员。
- 确保施工人员具备相应的资质和技能。
3.4 施工组织图制定- 制定水泥厂施工组织图,明确各个施工部门、作业区域和通道的位置布置。
- 确定施工现场的分区划分,确保作业区域的安全与顺畅。
3.5 安全措施- 根据水泥厂施工特点和法律法规要求,制定相应的安全措施和应急预案。
- 落实施工现场的安全管理,确保人员和设备的安全。
4. 人员安排- 施工项目经理:负责整个施工过程的组织、协调和管理。
- 施工工长:负责具体施工工序的实施和工艺控制。
- 施工人员:根据工序要求,负责具体施工作业。
5. 建设期安全管理- 确保施工现场的安全警示标识和告示牌的设置。
- 开展安全教育培训,提高工作人员的安全意识和技能。
- 加强施工现场的巡查和监督,及时发现和解决安全问题。
6. 环保措施- 严格遵守环境保护法律法规和水泥厂环保要求。
- 控制施工现场的噪声、粉尘、废水等污染物的排放,采取相应的治理措施。
7. 总结通过合理的施工组织设计,可以保障水泥厂施工项目的顺利进行,确保施工安全、高效、经济和环保。
水泥厂工程改造方案范本

水泥厂工程改造方案范本一、前言随着我国工业化进程的加快和建筑业的高速发展,对水泥的需求量也在持续增加。
然而,随着环保意识的提高和环境保护法规的日益严格,传统水泥厂在生产过程中所产生的固体废弃物、废气、废水等对环境造成的污染也引起了广泛关注。
因此,对水泥厂进行工程改造,提高其环保水平和生产效率,已成为一个迫切的需求。
在这种情况下,我公司受到了水泥厂一家企业的委托,要求为其提供一份水泥厂工程改造方案,以提升其生产效率和环保水平。
本方案旨在对水泥厂的生产工艺、设备和环保设施等进行全面改造和升级,确保其达到符合国家相关环保标准的要求,提高公司的竞争力和市场地位。
二、项目背景1. 企业概况委托方是一家地处工业园区的大型水泥生产企业,拥有自己的矿山、生产线和销售渠道。
公司年产水泥量达到1000万吨,市场份额较大,是当地的领军企业。
2. 项目背景随着国家环保政策的不断加强,水泥生产行业也面临着严峻的环保压力。
当前,公司所使用的生产工艺和设备已经落后,废气处理设施和废水处理设备也跟不上环保要求的提升。
此外,由于原有工艺设备的老化,生产效率不高,资源利用率也比较低。
因此,公司迫切需要对其水泥生产线进行改造和升级。
三、项目目标本项目的主要目标是对水泥生产线进行全面改造和升级,以达到以下目标:1. 提高生产效率:通过更新和优化生产设备和工艺流程,提高水泥生产效率,降低能耗和原材料消耗。
2. 提升产品质量:通过引进先进的生产技术和设备,提高水泥产品的品质和稳定性,满足市场对高标准水泥产品的需求。
3. 增强环保设施:更新废气处理、废水处理等环保设施,确保排放达到国家相应标准,减少对环境的污染。
4. 提高企业竞争力:通过改造升级,提高企业的生产水平和产品质量,增强企业在市场上的竞争力,获得更多的市场份额。
5. 降低生产成本:通过新设备的投资和生产效率的提高,降低水泥生产成本,增加企业的盈利能力。
四、项目内容1. 生产设备的更新和改造通过引进先进的水泥生产设备,如垂直磨机、回转窑等,来替代原有的老旧设备,提高生产效率,降低能耗和原材料消耗。
水泥厂精细化管理方案
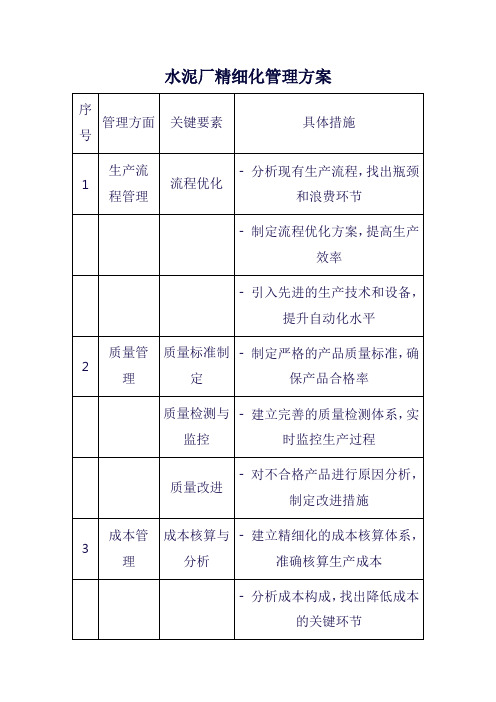
- 建立环保监测体系,定期报告环保状况
绩效考核
- 建立公正的绩效考核体系,激发员工积极性
5
安全管理
安全规章制度制定
- 制定完善的安全生产规章制度
安全培训与传
- 开展安全培训和宣传活动,提高员工安全意识
安全检查与整改
- 定期进行安全检查,及时整改安全隐患
6
环保管理
环保政策落实
- 严格执行国家和地方的环保政策
排污治理
- 投入资源,加强排污治理,减少环境污染
水泥厂精细化管理方案
序号
管理方面
关键要素
具体措施
1
生产流程管理
流程优化
- 分析现有生产流程,找出瓶颈和浪费环节
- 制定流程优化方案,提高生产效率
- 引入先进的生产技术和设备,提升自动化水平
2
质量管理
质量标准制定
- 制定严格的产品质量标准,确保产品合格率
质量检测与监控
- 建立完善的质量检测体系,实时监控生产过程
质量改进
- 对不合格产品进行原因分析,制定改进措施
3
成本管理
成本核算与分析
- 建立精细化的成本核算体系,准确核算生产成本
- 分析成本构成,找出降低成本的关键环节
成本控制
- 制定成本控制措施,降低生产过程中的浪费
4
人力资源管理
人员培训与提升
- 定期开展员工培训和技能提升活动
- 建立激励机制,鼓励员工创新和改进
水泥厂建筑工程方案

水泥厂建筑工程方案一、前言随着城市化进程的加速和工业化水平的不断提高,水泥作为建筑材料的需求量也随之增加。
水泥厂建筑工程是现代化工业制造的重要组成部分,其规模、设备和技术水平直接关系到生产效率、产品质量和环境保护。
本文将针对水泥厂建筑工程方案进行详细的分析和论述,从场地选址、建筑设计、设备配置以及环境保护等方面综合考虑,提出一套全面、科学的水泥厂建筑工程方案。
二、场地选址1. 场地选址的原则:(1)选址应考虑到原材料、水源、电源、交通等基础设施的便利性,降低原材料运输成本,提高生产效率。
(2)选址应考虑到环境保护、生态平衡等因素,避免对周边环境产生不良影响。
(3)选址应考虑到未来的发展空间和规划用地的合理性,以便进行适度的扩建和改造。
2. 场地选址建议:(1)地理位置:尽量选择距离原材料矿区、水源、电源、交通枢纽等基础设施较近的地块,便于原材料、水电等资源的供应和运输。
(2)地块面积:考虑到未来的扩建和改造,建议选择较大面积的地块,以便进行合理布局和规划。
(3)环境因素:应避免选址在人口密集区、生态保护区、迁移流动人口集中地等区域,以避免对周边环境和生态产生不良影响。
三、建筑设计1. 厂房布局设计:(1)厂区布局:应将原料库、破碎区、煤磨煤粉系统、烧成系统、电机房等相关区域合理布局,确保原材料、燃料、电力等资源的供应和输送畅通无阻。
(2)车间布局:按生产线流程和工艺要求,合理布置设备和生产线,确保生产效率和产品质量。
(3)生活区布局:应合理布置员工宿舍、食堂、办公楼等区域,提供良好的工作生活环境。
2. 厂房建筑设计:(1)建筑结构:应根据厂房用途和荷载要求,确定合适的建筑结构形式和材料,保证厂房的安全性和耐久性。
(2)建筑风格:应考虑到区域文化和环境特点,注重建筑外观的美观性和风格的统一性。
(3)绿化景观:在厂区的各个角落布置绿植,打造绿色环保的厂区环境。
四、设备配置1. 生产设备选择:(1)原料破碎:选用高效节能的破碎设备,如锤式破碎机、颚式破碎机等,确保原料破碎粒度的均匀性和稳定性。
水泥厂工程改造方案
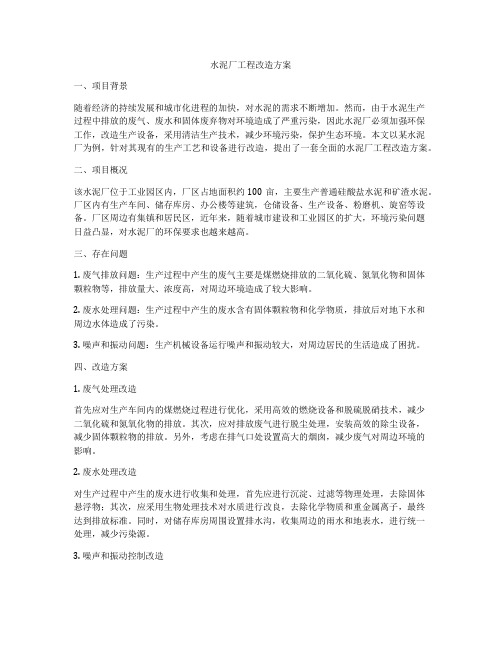
水泥厂工程改造方案一、项目背景随着经济的持续发展和城市化进程的加快,对水泥的需求不断增加。
然而,由于水泥生产过程中排放的废气、废水和固体废弃物对环境造成了严重污染,因此水泥厂必须加强环保工作,改造生产设备,采用清洁生产技术,减少环境污染,保护生态环境。
本文以某水泥厂为例,针对其现有的生产工艺和设备进行改造,提出了一套全面的水泥厂工程改造方案。
二、项目概况该水泥厂位于工业园区内,厂区占地面积约100亩,主要生产普通硅酸盐水泥和矿渣水泥。
厂区内有生产车间、储存库房、办公楼等建筑,仓储设备、生产设备、粉磨机、旋窑等设备。
厂区周边有集镇和居民区,近年来,随着城市建设和工业园区的扩大,环境污染问题日益凸显,对水泥厂的环保要求也越来越高。
三、存在问题1. 废气排放问题:生产过程中产生的废气主要是煤燃烧排放的二氧化硫、氮氧化物和固体颗粒物等,排放量大、浓度高,对周边环境造成了较大影响。
2. 废水处理问题:生产过程中产生的废水含有固体颗粒物和化学物质,排放后对地下水和周边水体造成了污染。
3. 噪声和振动问题:生产机械设备运行噪声和振动较大,对周边居民的生活造成了困扰。
四、改造方案1. 废气处理改造首先应对生产车间内的煤燃烧过程进行优化,采用高效的燃烧设备和脱硫脱硝技术,减少二氧化硫和氮氧化物的排放。
其次,应对排放废气进行脱尘处理,安装高效的除尘设备,减少固体颗粒物的排放。
另外,考虑在排气口处设置高大的烟囱,减少废气对周边环境的影响。
2. 废水处理改造对生产过程中产生的废水进行收集和处理,首先应进行沉淀、过滤等物理处理,去除固体悬浮物;其次,应采用生物处理技术对水质进行改良,去除化学物质和重金属离子,最终达到排放标准。
同时,对储存库房周围设置排水沟,收集周边的雨水和地表水,进行统一处理,减少污染源。
3. 噪声和振动控制改造在生产车间内,应进行噪声和振动的源头控制,采用隔音设备和减振设备,减少噪声和振动的传播;另外,在厂区周边设置隔离带和隔音墙,减少噪声对周边环境的影响。
水泥生产工厂建设实施方案

水泥生产工厂建设实施方案1. 概述本文档详细介绍了水泥生产工厂建设的实施方案,包括项目背景、目标、关键步骤和时间表等内容。
2. 项目背景水泥市场需求稳步增长,为满足市场需求,建设一座水泥生产工厂是必要的。
本项目所在地具备充足的原材料和便利的交通条件,是建设水泥工厂的理想选择。
3. 项目目标本项目的主要目标是建设一座高效、环保的水泥生产工厂,确保生产能力满足市场需求,并遵守环境保护相关法规。
同时,确保项目完成后能够持续盈利并提供就业机会。
4. 关键步骤和时间表下面是本项目的关键步骤和预计时间表:步骤1:项目准备阶段(1个月)- 寻找合适的土地,并进行评估和选址。
- 完成市场调研,分析市场需求和竞争状况。
- 确定项目预算和资金筹措计划。
步骤2:工厂设计和建设阶段(12个月)- 聘请专业工程师进行工厂设计和设备选择。
- 完善工程设计和设备采购计划,并进行招标。
- 开展工厂建设,确保施工进度和质量控制。
步骤3:设备调试和生产准备阶段(2个月)- 安装所需生产设备,并进行调试和测试。
- 提前准备原材料和生产配方。
- 培训工厂员工,提高生产技能和安全意识。
步骤4:试生产和产品质量控制阶段(3个月)- 开展试生产,确保生产线正常运行。
- 建立完善的质量控制系统和标准。
- 对产品进行检测和评估,确保产品质量达标。
步骤5:运营和市场推广阶段- 开始正式生产并销售产品。
- 加强市场推广和销售渠道建设。
- 持续改进生产工艺和产品质量。
5. 风险管理本项目的风险主要包括市场需求波动、环保合规风险和成本控制风险等。
在项目实施过程中,需设立专门的风险管理机制,及时应对和控制各种风险。
6. 结论本文档提供了水泥生产工厂建设的实施方案,明确了项目目标、关键步骤和时间表,并提出了风险管理建议。
根据该方案的实施,相信能够成功建设一座高效、环保的水泥生产工厂,为市场提供优质的水泥产品。
水泥厂建设施工方案

水泥厂建设施工方案一、前言水泥厂是以生产水泥为主要目的的工业建筑物,其施工既需要考虑生产工艺的要求,也要兼顾工程的稳定性和安全性。
本文将从设计、土地准备、设备安装等方面,对水泥厂建设施工方案进行论述。
二、设计水泥厂的设计是保证生产效率和质量的关键。
在施工前,需由专业工程师进行综合评估和设计,确保建筑结构稳定,生产线布置合理,以及材料和人员的流线设计合理。
同时,还需考虑工艺流程改进、能耗控制、环保要求等因素,并制定相应的措施。
三、土地准备为了保证水泥厂的施工质量和效率,需进行土地准备工作。
这包括清理现场,平整地面,确保施工区域没有障碍物。
同时,还需进行地质勘察和土壤检测,以确定地基承载能力、地下水位和土壤稳定性等信息,为后续的土建工程提供支持。
四、土建工程1. 基础工程:水泥厂的基础工程是保证建筑物稳定性的关键。
需根据地质勘察结果,选择适当的基础形式,如浅基础或深基础,并进行相应的桩基工程。
同时,还需进行土壤处理,防止地基沉降。
2. 建筑工程:水泥厂的建筑工程主要包括厂房建设和办公楼建设。
在施工过程中,应遵循国家建筑规范和相关行业标准,确保建筑物的结构安全可靠。
此外,还需注意风险防范,采取相应的安全措施,保障工人和设备的安全。
3. 配套设施:水泥厂的施工还需要建设一些配套设施,如电力供应系统、水源供应系统、废水处理系统等。
这些设施的建设应考虑到工程的持续性和安全性,确保设备运行的稳定性和效率。
五、设备安装水泥厂的设备安装是水泥生产线的重要环节。
在设备安装前,在施工方案中应确定合适的起重设备和施工方案,并进行详细的施工图纸编制。
设备安装时,需按照标准操作程序,保证设备的正确安装和调试,以保证生产线的正常运行。
六、安全防护在水泥厂建设施工过程中,安全防护至关重要。
施工方案除了要考虑设备安装、土建工程等技术性问题,还应注重安全管理措施的制定和执行。
这包括工人的安全培训、工地的防护设施、施工现场的管理等方面,以确保施工过程的安全。
水泥厂工作计划格式及范文

水泥厂工作计划格式及范文一、管理目标1. 实施精益化管理,提高水泥生产效率和质量;2. 降低生产能耗和成本,提高水泥生产利润;3. 加强安全生产管理,确保员工安全。
二、生产计划1. 生产目标:根据市场需求和公司发展规划,制定年度生产目标,保证水泥生产量满足市场需求,实现销售收入目标。
2. 生产计划:制定每月、季度和年度生产计划,合理安排生产任务,确保生产目标的达成。
三、设备维护计划1. 设备维护目标:保证水泥生产设备正常运转,减少故障停机时间,提高设备利用率。
2. 设备维护计划:制定每月、季度和年度设备维护计划,包括设备检修、设备更新换代等内容,确保设备正常运转。
四、质量管理计划1. 质量管理目标:实施全面品质管理,确保水泥产品质量符合国家标准和客户要求。
2. 质量管理计划:建立质量管理体系,包括原材料采购、生产过程控制、产品检验等环节,确保水泥产品质量稳定、可靠。
五、能源管理计划1. 节能目标:降低水泥生产能耗,提高能源利用效率,减少能源消耗成本。
2. 节能措施:开展能源消耗分析,制定节能技术改造方案,加强能源管理,提高水泥生产能源利用效率。
六、安全生产计划1. 安全管理目标:确保水泥生产过程安全,避免事故发生,保护员工生命财产安全。
2. 安全生产措施:加强安全教育培训,建立安全生产管理制度,加强设备设施安全检查,加强现场作业安全管理。
七、环保治理计划1. 环保治理目标:加强对水泥生产工艺的环境监测和治理,减少对环境的污染。
2. 环保治理措施:制定环保目标,引进环保设施,对废气、废水、固体废物等进行治理,确保水泥生产过程环境污染达标排放。
八、后勤保障计划1. 后勤保障目标:为生产提供必需的后勤支持,确保生产顺利进行。
2. 后勤保障措施:充分利用后勤资源,完善后勤体系,包括供电、供水、交通、通信等后勤保障措施。
以上为水泥厂工作计划格式及范文,希望对您有所帮助。
水泥厂自动化实施方案

水泥厂自动化实施方案
为了实现水泥厂的自动化生产,以下是一个实施方案:
1. 分析需求:对水泥厂的生产流程进行全面的分析,了解每个环节的工作内容、操作流程和所需设备。
2. 设计系统架构:根据需求分析结果,设计自动化系统的整体架构。
包括硬件设备、软件系统和网络连接等方面。
3. 选购设备:根据系统架构设计,确定所需的硬件设备,包括传感器、执行器、PLC控制器等。
同时考虑设备的稳定性、
可靠性和适应性。
4. 开发软件:根据需求和系统架构,开发相应的软件系统。
软件系统需要能够实时监测生产过程、控制设备运行、进行数据分析和故障诊断等。
5. 设计网络连接:根据系统架构设计,建立设备之间的网络连接。
确保各个设备能够相互通信,实现信息的传输和共享。
6. 安装调试:对选购的硬件设备进行安装,并进行系统的调试。
确保设备能够正常运行,与软件系统和网络连接配合良好。
7. 实施验证:对实施的自动化系统进行验证。
通过对生产过程的模拟测试,验证系统的可行性和稳定性。
8. 员工培训:对水泥厂员工进行相关培训,使其能够熟练掌握
自动化系统的操作和维护。
9. 系统运维:确保自动化系统的正常运行和维护。
定期对设备进行检查和维修,及时解决系统故障和问题。
10. 持续改进:根据生产实际情况和反馈,对自动化系统进行持续改进和优化。
通过数据分析和技术更新,提高生产效率和质量。
以上是一个水泥厂自动化实施方案的概述,具体实施步骤还需根据实际情况进行调整和补充。
水泥厂工程改造方案模板

水泥厂工程改造方案模板一、项目背景随着中国经济的快速发展和城市化进程的加快,对水泥的需求量不断增加。
水泥作为建筑行业的基础材料,对城市建设和基础设施建设起着至关重要的作用。
然而,传统的水泥生产过程存在着能源消耗高、环境污染严重等问题。
为了适应未来发展需求,提高水泥厂的竞争力,有必要对水泥厂进行工程改造,提高生产效率,减少能源消耗和环境污染。
二、项目意义1. 提高生产效率:通过工程改造,优化生产流程,提高水泥生产效率,降低生产成本,提高产品质量。
2. 减少能源消耗:采用先进的生产技术和设备,减少能源消耗,降低生产成本,提高生产效率。
3. 减少环境污染:改造水泥厂,减少排放污染物,保护环境,提高企业的社会责任感,增强企业形象。
4. 提高竞争力:通过工程改造,提高产品质量,降低生产成本,提高企业的竞争力,开拓市场。
三、工程改造方案1. 技术改造(1)煤粉磨煤机部分改造采用新型的煤粉磨煤机,提高煤粉的磨细度和均匀度,降低能耗,提高生产效率。
(2)窑炉系统改造采用新型的窑炉系统,提高窑炉的使用效率,减少能源消耗,降低排放污染物。
(3)磨矿系统改造优化磨矿系统,提高磨矿效率,减少电能消耗,提高生产效率。
(4)配料系统改造改造配料系统,提高配料的准确性和稳定性,提高生产效率,降低能耗。
2. 设备改造(1)水泥粉磨机改造采用新型的水泥粉磨机,提高水泥的粉磨效率,减少电能消耗,降低生产成本。
(2)输送设备改造优化输送设备,提高输送效率,减少能耗,提高生产效率。
(3)除尘设备改造改造除尘设备,提高除尘效率,降低排放污染物,保护环境。
3. 资源循环利用(1)余热利用对窑炉排放的余热进行回收利用,用于生产和加热,降低能源消耗。
(2)固废处理对水泥生产过程中产生的固废进行分类处理和资源化利用,降低对环境的影响。
4. 管理体系完善(1)制定科学的生产计划,合理安排生产流程,提高生产效率。
(2)加强设备维护管理,延长设备寿命,降低维护成本。
水泥厂安全生产实施方案范本(2篇)
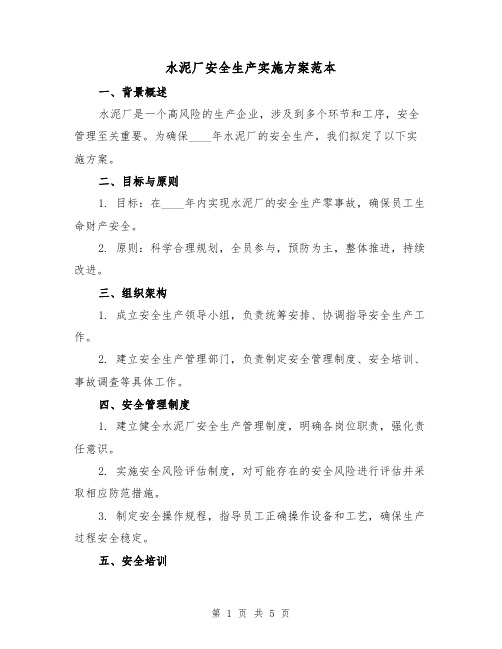
水泥厂安全生产实施方案范本一、背景概述水泥厂是一个高风险的生产企业,涉及到多个环节和工序,安全管理至关重要。
为确保____年水泥厂的安全生产,我们拟定了以下实施方案。
二、目标与原则1. 目标:在____年内实现水泥厂的安全生产零事故,确保员工生命财产安全。
2. 原则:科学合理规划,全员参与,预防为主,整体推进,持续改进。
三、组织架构1. 成立安全生产领导小组,负责统筹安排、协调指导安全生产工作。
2. 建立安全生产管理部门,负责制定安全管理制度、安全培训、事故调查等具体工作。
四、安全管理制度1. 建立健全水泥厂安全生产管理制度,明确各岗位职责,强化责任意识。
2. 实施安全风险评估制度,对可能存在的安全风险进行评估并采取相应防范措施。
3. 制定安全操作规程,指导员工正确操作设备和工艺,确保生产过程安全稳定。
五、安全培训1. 每位员工必须参加安全培训,确保其具备必要的安全防范意识和技能。
2. 建立定期安全培训制度,包括新员工培训、岗位技能培训、应急救援培训等。
3. 生产设备和工艺变更时,进行相应的安全培训,确保员工了解新工艺的操作要点和安全注意事项。
六、事故预防措施1. 加强设备检修和维护,确保设备安全运行。
2. 定期进行消防设施检查和火灾隐患排查,确保消防设备的完好,并采取适当的防火措施。
3. 对工作环境进行定期检测,保证员工的健康和安全。
4. 加强安全生产意识教育,强调员工的安全责任和安全行为。
七、应急救援1. 制定应急救援预案,明确各级应急救援组织与职责。
2. 配备完善的应急救援设备,进行定期演练和检查,确保设备的可用性和应急处置能力。
3. 安排专人负责事故的调查和分析,总结经验教训,及时改进应急预案。
八、安全监督与检查1. 建立健全安全监督与检查体系,通过日常巡查、专项检查、定期抽查等方式,全面了解生产安全状况。
2. 加强对承包商和供应商的安全管理,确保其遵守相关安全规定。
九、持续改进1. 定期组织安全生产工作交流和经验分享,推广先进的安全管理经验和技术。
水泥厂技术改造实施方案

水泥厂技术改造实施方案一、前言随着工业化进程的不断推进,水泥产业作为基础建设领域的重要支撑,也在不断发展壮大。
然而,随之而来的环境污染和资源浪费问题也日益突出,迫切需要对水泥厂进行技术改造,实现清洁生产,提高资源利用率,减少对环境的影响。
二、技术改造目标1. 提高生产效率:通过技术改造,提高水泥生产线的自动化程度,降低能耗,提高生产效率。
2. 减少排放:引入先进的环保设备,减少废气、废水排放,实现清洁生产。
3. 提高资源利用率:优化生产工艺,提高原材料利用率,减少资源浪费。
三、技术改造方案1. 更新生产设备:引进先进的水泥生产设备,提高生产线的自动化程度,减少人工操作,降低能耗,提高生产效率。
2. 完善废气处理系统:对水泥生产过程中产生的废气进行收集和处理,采用高效的除尘设备和脱硫脱硝技术,减少对大气的污染。
3. 强化废水处理工艺:对生产废水进行集中处理,采用生物处理、膜分离等技术,实现废水的循环利用,减少对水资源的消耗。
4. 优化原材料配比:对水泥生产中的原材料进行精细化管理,优化配比,提高原材料利用率,减少资源浪费。
5. 加强能源管理:推广节能技术,优化能源结构,降低生产过程中的能耗,减少对能源资源的消耗。
四、技术改造效益1. 生产效率提高:通过更新设备和优化工艺,生产效率得到提高,降低生产成本,提高市场竞争力。
2. 环境污染减少:完善的废气、废水处理系统,减少对环境的污染,实现清洁生产。
3. 资源利用率提高:优化原材料配比,加强能源管理,提高资源利用率,减少资源浪费。
五、技术改造实施步骤1. 制定技术改造计划:根据现有生产情况和技术水平,制定详细的技术改造计划,包括更新设备、改进工艺、完善环保设施等内容。
2. 落实技术改造方案:组织专业团队进行技术改造工作,确保设备更新、工艺优化、环保设施完善等工作按计划实施。
3. 进行运行调试:完成技术改造后,进行设备运行调试,确保生产线稳定运行,达到预期效果。
水泥厂专项方案

一、项目背景随着我国经济的快速发展,基础设施建设需求日益增长,水泥作为重要的建筑材料,在建筑、道路、桥梁等领域发挥着不可或缺的作用。
为满足市场需求,提高水泥生产效率,降低生产成本,提升产品质量,本项目拟建设一座现代化水泥厂。
为确保项目顺利实施,特制定本专项方案。
二、项目目标1. 提高水泥生产效率,实现年产水泥100万吨。
2. 降低生产成本,提高企业竞争力。
3. 优化生产工艺,提高产品质量。
4. 节能减排,实现绿色环保生产。
5. 加强企业内部管理,提高员工素质。
三、项目规模及布局1. 项目规模:年产水泥100万吨。
2. 布局:项目占地约1000亩,分为生产区、仓储区、办公区和生活区。
(1)生产区:包括原料堆场、破碎系统、磨粉系统、熟料烧成系统、水泥粉磨系统等。
(2)仓储区:包括原材料、半成品、成品的仓储设施。
(3)办公区:包括办公楼、食堂、宿舍等。
(4)生活区:包括员工宿舍、活动中心等。
四、生产工艺及设备选型1. 生产工艺:采用先进的干法水泥生产工艺,包括原料预均化、破碎、粉磨、生料均化、烧成、熟料粉磨等环节。
2. 设备选型:选用国内外知名品牌的先进设备,如:破碎机、球磨机、预热器、分解炉、回转窑、冷却机等。
五、节能减排措施1. 采用高效节能设备,降低能耗。
2. 优化生产工艺,减少废气、废水排放。
3. 加强余热利用,提高能源利用率。
4. 建立完善的环保设施,确保污染物达标排放。
六、项目实施进度1. 项目前期:可行性研究、环境影响评价、土地审批等,预计需6个月。
2. 工程建设:土建、设备安装、调试等,预计需18个月。
3. 试运行:进行生产调试,确保设备运行稳定,预计需3个月。
4. 正式投产:正式投入生产,预计需6个月。
七、项目投资估算1. 土地费用:1000亩,按每亩50万元计算,共计5000万元。
2. 建设投资:包括土建、设备购置、安装调试等,预计需5亿元。
3. 软件投资:包括环保设施、信息化建设等,预计需5000万元。
- 1、下载文档前请自行甄别文档内容的完整性,平台不提供额外的编辑、内容补充、找答案等附加服务。
- 2、"仅部分预览"的文档,不可在线预览部分如存在完整性等问题,可反馈申请退款(可完整预览的文档不适用该条件!)。
- 3、如文档侵犯您的权益,请联系客服反馈,我们会尽快为您处理(人工客服工作时间:9:00-18:30)。
1.2 主要建设内容、生产工艺、生产规模、建设周期和投资(包括环保投资)1.2.1 建设内容技改项目的工程建设内容包括:石灰石矿山开采及运输、石灰石破碎、石灰石预均化堆场、粘土破碎、辅助原料预均化堆场、原料配料站、原料粉磨及废气处理、生料均化库及生料入窑、烧成窑尾、烧成窑中、烧成窑头及废气处理、余热发电、熟料储存、石膏破碎及输送、水泥粉磨、水泥储存、水泥散装、袋装成品出厂等主生产线设施,以及必要的少量生产辅助设施如机电修车间、中央控制及室及化验室、材料库、空压机房、总配电房、电气室、水处理系统等,厂前区办公楼、宿舍、食堂等生活辅助设施。
1.2.2 生产规模、建设周期和投资(包括环保投资)项目总投资130820.9万元,其中环保投资为12841.09万元。
厂区占地面积327900m2,石灰石矿山占地面积2.02km2。
产品方案:年产熟料2×148.5万t。
产品分布为:商品熟料2×29.7万t;水泥2×152.74万吨,其中P.O42.5水泥2×122.19万t,P.C32.5水泥2×30.55万t。
其中散装水泥占80%,袋装水泥占20%。
公司定员294人,生产线年生产天数330天,矿山年工作天数290天。
项目技术经济表见表1.2-1。
1.2.3 技改项目生产工艺一、水泥熟料生产线具体工艺流程简述如下:(1)石灰石破碎石灰石破碎设于矿山,石灰石由装载机喂入卸车坑,或者运输石灰石的自卸汽车直接将石灰石卸入卸车坑,卸车坑下设有重型板喂机,石灰石经板喂机喂入石灰石破碎机。
重型板喂机的传动可变频调速,控制石灰石的喂料量。
当进料块度<1100mm,出料粒度≤75mm占90%时,生产能力为1200t/h。
破碎后的石灰石由胶带输送机输送至厂区石灰石预均化堆场。
在石灰石破碎机的下料点及转运点处设有袋收尘器。
(2)石灰石预均化堆场石灰石预均化堆场采用圆形预均化堆场,有效储量40000t。
出预均化堆场的石灰石经胶带输送机送至原料调配站。
(3)辅助原料破碎、堆存及输送辅助原料(粘土)汽车运输进厂,堆存在堆棚内。
粘土由装载机喂入卸车坑,或者运输粘土的自卸汽车直接将粘土卸入卸车坑,卸车坑下设有板喂机,粘土经板喂机喂入破碎机。
板喂机的传动可变频调速,控制粘土的喂料量。
粘土破碎采用辊式破碎机,当粘土进料粒度≤300mm,出料粒度≤50mm时,生产能力为200t/h。
破碎后的粘土由胶带输送机输送至原料调配站。
在粘土破碎机的下料点及转运点处设有袋收尘器。
辅助原料(砂土)汽车运输进厂,自卸汽车直接将砂土卸入卸车坑,卸车坑下设有板喂机,再由胶带输送机输送至辅助原料/原煤预均化堆场。
在各转运点处设有袋收尘器。
(4)辅助原料/原煤堆存、均化及输送原煤,硫酸渣车运输进厂,经胶带输送机送入辅助原料/原煤预均化堆场。
辅助原料和原煤共用一个长型预均化堆场,采用侧堆侧取方式.砂土储量11900t,硫酸渣储量1300t,原煤储量2×11700t。
堆料机堆料能力为400t/h ,取料机取料能力250 t/h。
原煤由取料机取出后经胶带输送机送至煤磨原煤仓。
辅助原料经胶带输送机送至原料调配站。
(5)原料调配原料调配站设四个配料仓,分别用于储存石灰石、砂土、粘土、硫酸渣。
各仓下设置卸料及计量、输送设备将每种物料按一定比例从配料库中卸出,送至原料粉磨系统进行粉磨。
(6)原料粉磨及废气处理系统原料粉磨采用二台辊式磨。
当原料入磨水分≤5%,进料粒度≤75 mm(占90%),产品细度为80 m筛筛余≤10~12%时,系统能力为380 t/h。
成品经斜槽与废气处理系统收集的窑灰一起由斗式提升机送入生料均化库。
原料粉磨利用出高温风机后的窑尾废气作为烘干热源。
出磨废气一部分做为循环风返回,剩余部分与增湿调质后的部分窑尾废气一起入窑尾袋收尘器,净化后的废气排入大气。
当原料磨不运行时,窑尾废气经增湿塔降温调质后,直接进入袋收尘器净化。
生料的自动取样装置设在进生料库提升机之前,试样由人工送至设在中央控制室的X射线荧光分析仪进行分析,并可根据其结果调整原料配比。
(7)生料均化库及窑喂料系统每条生产线均采用一座Φ18×50 m TP型生料均化库,有效储量为11000t,有效储期1.61d。
均化库底部为锥体,均化后的生料经库底多点流量控制阀、斜槽、送至带有荷重传感器、充气装置的生料搅拌计量仓。
仓下设有流量控制阀和流量计,经计量的生料由空气输送斜槽、斗式提升机等喂入窑尾预热器一、二级旋风筒上升管道。
生料均化库的均化作用主要由库内重力切割和搅拌仓的搅拌来实现。
入窑生料CaCO3标准偏差控制在 0.25%。
生料入窑尾预热器系统斗式提升机前,设有生料取样装置,通过对生料的取样、制样、分析,可实现对烧成系统操作的指导。
(8)熟料烧成系统每条生产线的熟料煅烧均采用一台Φ4.8×72m的回转窑,窑尾带双系列低压损五级旋风预热器和TTF分解炉,生产能力4500t/d,熟料热耗3011kJ/kg(720kcal/kg)。
窑头和分解炉用煤比例为40%和60%,入窑物料的碳酸钙分解率大于90%。
回转窑采用三档支撑,窑头配有多通道的煤粉燃烧器。
熟料冷却采用一台第四代行进式稳流篦冷机篦冷机,熟料出冷却机的温度为环境温度+65℃。
为破碎大块熟料,冷却机出口处设有一台锤式破碎机,以保证出冷却机熟料粒度≤25 mm。
冷却后的熟料经槽式输送机送至熟料储存库。
冷却机排出的气体,一部分作为窑头二次风入窑,一部分经三次风管送往窑尾分解炉(三次风从窑头罩上抽取),一部分作为煤粉制备的烘干热源;其余经电收尘器净化后排入大气。
(9)煤粉制备煤粉制备采用代表目前先进水平的、成熟可靠、节约能源的新型立磨工艺系统。
煤磨设置在窑头,利用窑头废气作为烘干热源。
原煤由原煤仓下定量给料机喂入磨内烘干与粉磨,烘干并粉磨后的煤粉随同气流从立磨排出,细粉与废气一同进入袋收尘器,气体经袋收尘器净化后排入大气。
收下的煤粉经螺旋输送机分别送入窑及分解炉的煤粉仓。
分解炉及窑头采用两套喂煤计量系统,煤粉制备系统设置有严格的安全措施,如防爆阀、CO2灭火系统、消防水系统等。
(10)熟料储存及输送设置一座Φ60×40.5m的熟料储存库,储存量为100000t,储存期为22.22d。
熟料库底设卸料装置,熟料卸出后经胶带输送机送至水泥粉磨配料站。
根据业主要求两线熟料库总容量要求30万吨左右,故一两线共设置三座Φ60×40.5m的熟料储存库。
(11)石膏破碎、石灰石储存及输送石膏、混合材由分别由汽车运输进厂,储存于堆棚,石膏也可直接卸入卸车坑内,卸车坑下设有板喂机,石膏经板喂机喂入破碎机。
板喂机的传动可变频调速,控制石膏的喂料量。
石膏破碎采用锤式破碎机,当石膏进料粒度≤400mm,出料粒度≤50mm时,生产能力为70t/h。
破碎后的石膏由胶带输送机输送至水泥调配站。
粉煤灰由汽车运输进厂直接泵送入粉煤灰调配仓。
(12)矿渣烘干湿矿渣由汽车运输进厂区堆棚。
经卸车坑、胶带输送机喂入湿矿渣仓中,经仓底喂料机喂入矿渣烘干机。
矿渣烘干机为Φ3.0×25m,入料水份≤15%,出料水份≤1时,生产能力65~100 t/h。
烘干后的干矿渣经斗式提升机送至水泥调配站的干矿渣库。
烘干机排出的废气进入矿渣烘干专用的袋收尘器中,净化后的气体经烟囱排入大气,袋收尘器处理后的烟气正常排放浓度均满足国家规定排放浓度标准要求。
(13)水泥调配设四座水泥调配仓,分别储存熟料、矿渣、石膏及石灰石。
各仓下设定量给料机,各物料按一定比例计量配料送至水泥粉磨系统。
作为混合材使用的干粉煤灰,由车运进厂后直接卸入粉煤灰库。
粉煤灰库采用一座Φ15×25m库,出库粉煤灰经定量给料机进行定量给料,再由空气输送斜槽送入水泥磨房,其给料量由计算机控制系统按配比进行调控。
(14)水泥粉磨水泥粉磨系统设置二套由TRP140/140辊压机、V型选粉机、Φ4.2×13m球磨机、高效选粉机组成的联合粉磨系统。
当生产P.O42.5水泥,比表面积为350m2/kg时,系统产量为160t/h;当生产P.C32.5水泥,比表面积为330m2/kg时,系统产量为200t/h。
来自水泥调配站的混合料经胶带输送机、提升机、喂入V型选粉机,V型选粉机分选出来的细粉进入水泥磨系统的高效选粉机。
V型选粉机分选出来的粗粉经过中间仓稳流后进入辊压机,经辊压机挤压后的料饼随出调配库的物料进入V型选粉机。
管磨机粉磨后的物料经出磨空气输送斜槽、提升机喂入高效选粉机,选出的粗粉经斜槽返回到磨机中再次粉磨。
细粉随气体进入高效袋收尘器,收下的水泥成品经空气输送斜槽、提升机等送至水泥库。
气体经袋收尘器净化后排入大气。
(15)水泥储存、输送及水泥汽车散装设置六座Φ18×44.5 m水泥库,总储量为60000t,储存期12.96d。
来自水泥粉磨系统的水泥经斗式提升机、空气输送斜槽送入水泥库内。
水泥库底由罗茨鼓风机供气。
出库水泥经库底卸料装置、空气输送斜槽、斗式提升机送往水泥散装及包装系统。
水泥库顶及库下均设有袋收尘器,将含尘气体净化后排入大气。
每座库侧均设置有库侧水泥汽车散装,共计六套汽车散装系统,每台散装机能力200t/h。
(16)水泥包装及成品堆存设置3台八嘴回转式包装机,每台包装机的能力为100t/h。
出库水泥经提升机、空气输送斜槽,可同时分两路经三道阀进入包装中间仓。
水泥由中间仓送入八嘴包装机,包装好的袋装水泥(50kg标准袋),经卸袋输送系统送入袋装水泥成品库内储存。
也可直接由汽车装车机进行装车。
成品库内包装好的袋装水泥也可由火车装车机进行火车装车。
(17)熟料、水泥散装装车/原煤原料卸车原煤,硫酸渣车运输进厂,经胶带输送机送入辅助原料/原煤预均化堆场。
熟料、水泥经计量仓计量后装车出厂。
(18)压缩空气站设置两座空压机站,熟料烧成部分和水泥制成部分各选用三台螺杆式空压机,其中一台备用。
压缩后的气体经净化干燥,作为窑尾预热器吹堵,袋收尘器清灰,气动阀门,脉冲阀及仪表等的用气气源。
(19)辅助生产车间新建一座办公楼,包括总化验室,中控室、计量室,另设材料库、耐火砖库等辅助生产车间。
工艺流程及收尘点见图1.2-1,全水泥生产线主机设备情况见表1.2-2。
实线为物流方向图1.2-1 熟料水泥生产工艺流程及排污节点图二、矿山工程概况1、石灰石矿山概况根据物料平衡表,工厂年需要石灰石2×1955020t。
考虑矿山开采和运输损失5%,日生产不均衡系数1.1,生产采剥比1:0.1,矿山采矿规模及生产能力如表1.2-4所示。
2、矿山开采①采矿方法根据矿床赋存条件和矿山地形,本矿山为山坡露天矿,矿山开采采用自上而下的水平分层法开采。