固定床移动床的特点
固定床、移动床、流化床反应器区别详解

固定床、移动床、流化床反应器,这三种反应器被誉为是工业生产中不可或缺的重要设备。
它们虽然都是制造工业生产中的设备,但它们各有所长,各有其优缺点。
一、首先,“床”指的是什么?大量固体颗粒堆积在一起,便形成了具有一定高度的颗粒床层,这就是名称里的"床"。
这些固体颗粒可以是反应物,也可以是催化剂。
二、如何区分固定床、移动床、流化床反应器如果这个颗粒床层是固定不动的,就叫固定床。
如果这个颗粒床层是整体移动的,固体颗粒自顶部连续加入,又从底部卸出,颗粒相互之间没有相对运动,而是以一个整体的状态移动,叫做移动床。
当流体(气体或液体)通过颗粒床层时,进行反应。
如果将流体通过床层的速度提高到一定数值,固体颗粒已经不能维持不变的状态,全部悬浮于流体之中,固体颗粒之间进行的是无规则运动,整个固体颗粒的床层,可以像流体一样流动,这即是流动床。
下面,小七为大家详细的介绍这三种反应器。
三、固定床反应器又称填充床反应器,内部装填有固体催化剂或固体反应物,以实现多相反应。
固体物通常呈颗粒状,堆积成一定高度(或厚度)的床层,床层静止不动,流体通过床层进行反应。
固定床反应器主要用于实现气固相催化反应,如氨合成塔、二氧化硫接触氧化器、烃类蒸汽转化炉等。
用于气固相或液固相非催化反应时,床层则填装固体反应物。
涓流床反应器也可归属于固定床反应器,气、液相并流向下通过床层,呈气液固相接触。
1、优点•催化剂机械磨损小。
•床层内流体的流动接近于平推流,与返混式的反应器相比,可用较少量的催化剂和较小的反应器容积来获得较大的生产能力。
•由于停留时间可以严格控制,温度分布可以适当调节,因此特别有利于达到高的选择性和转化率。
•可在高温高压下操作。
2、缺点•固定床中的传热较差。
•催化剂的再生、更换均不方便,催化剂的更换必须停产进行。
•不能使用细粒催化剂,但固定床反应器中的催化剂不限于颗粒状,网状催化剂早已应用于工业上。
目前,蜂窝状、纤维状催化剂也已被广泛使用。
移动床

实际的SMB设备中,在程序 控制下,通过旋转阀RV的步 进,同步改变进料位置,和流 体流过床层方向抽出的位置, 实际上固体吸
…… 生物发酵 早期成功应用在石油的轻组 分分离和果葡糖浆的纯化中。 SMB 食品
的应用
手性药物
由于具有设备结构小、产 率高、溶剂消耗少、分离能力 强、污染少以及便于连续化生 产和自动控制等优点,在生物 分离和手性拆分中备受关注。
水质特点
I区: 洗脱液进口与抽取液出 口之间——解吸强吸附组份 II区: 抽取液出口与进料口 之间———解吸弱吸附组份 III区: 进料口与抽余液出口 之间——吸附强吸附组份 IV区: 抽余液与洗脱液进口 之间——吸附弱吸附组份
每经过一个切换周期物料进出口管线沿液相流动方向移动一个色谱柱, 通过周期性开启、关闭进出口阀门来模拟固定相吸附剂与流动相液体的逆流 接触移动
切换时间 进料液流量 洗脱液流量 萃取液流量 萃余液流量 循环液流量
参数设计
安全边界因子法、 Massimo三角形理论法 驻波分析法
①
ISMB (Improved SMB):即改进的模拟移动床技术,只需要少量 的柱数,但却可以实现比传统SMB系统更好的分离效果 。
② SMBR (SMB reactors):模拟移动床反应器是一种化学反应器,把反应和相应 产品的分离综合在一起,减少设备,提高工艺性能。对有平衡限制的反应,通过打 破平衡,一边反应一边把产物分离出去,最终实现彻底地转化。
一种吸附操作单元
模拟移动床( SMB )
一. 什么是移动床?
固定床:间歇操作,非吸附分 离的时间比较长,若处理细胞浆 或发酵液会堵塞床层
流化床:吸附效率虽高,但返 混严重 ,吸附剂有磨损
特点:连续逆流循环 基于色谱分离技术的原理 流动相在床层内通 过循环泵不断自下而上 循环流动,而吸附剂颗 粒依靠重力向下移动, 与进料逆流接触。床层 中部连续进料,弱吸附 组分从床层顶部流出, 而强吸附组分在固定相 作用下从床层底部流出, 逐步完成吸附、精制和 解吸的过程 真实移动床原理图
反应器

制造加氢反应器的常用材料 制造加氢反应器的常用材料一般为Cr-Mo钢系, 因为这些钢材既具有优良的抗高温氢腐蚀性能, 又有良好的短时和长时高温力学性能。根据不同 的温度和压力,一般都选用 1Cr-0.5Mo; 1.25Cr-0.5Mo; 2.25Cr-1Mo; 2.25Cr-1Mo 0.25V; 3Cr-1Mo 0.25V;
热壁加氢反应器的 主要损伤形式
热壁加氢反应器由于器壁直接与高温、 高压含氢或氢与硫化氢介质接触,操作条 件相当苛刻,可能引起下列损伤: 1)高温氢腐蚀 2)氢脆 3)硫化物应力腐蚀开裂 4)铬-钼钢回火脆性破坏 5)奥氏体不锈钢堆焊层的氢致剥离现象
1)高温氢腐蚀 一是表面脱碳。表面产生裂纹,一般影响 很轻; 二是内部脱碳与开裂。它是由于氢侵入扩 散到钢中与固溶碳或不稳定的碳化物发生 化学反应,生成甲烷 Fe3C + 2H2 → CH4 + 3Fe 。 而甲烷不能逸出钢外,就聚集在晶界空 穴和夹杂物附近,形成很高的局部应力, 导致钢材产生龟裂、裂纹和鼓泡,并使强 度、延性和韧性显著下降。
2)氢脆 氢脆是氢残留在钢中所引起的脆化现象。 产生了氢脆的钢材,其延伸率和断面收缩 率显著下降。这是由于侵入钢中的原子氢 使结晶的原子结合力变弱,或者作为分子 状在晶界或夹杂物周边上析出的结果。但 是,对于已经产生氢脆现象的钢材,当给 予特定的条件时,氢仍可从钢中释放出来, 使钢的性能得到恢复,所以氢脆是可逆的, 也称为一次脆化现象。
防治措施: 1、用合适的材料是有效的方法之一; 2、要尽量消除或减轻由于冷加工和焊接引 起的残余应力,并希望能够加工成不形成 应力集中或尽可能小的结构; 3、使用上应采取缓和环境条件的措施,如 抑制连多硫酸生成,采取用干燥氮气吹扫, 除去空气和防止水蒸汽析出。或碱洗方法, 中和可能生成的连多硫酸,值得注意的是 碱洗后不能再用水冲洗。
固定床、流化床、移动床、浆态床比较

四种反应器形式比较一、固定床反应器(一)概念凡是流体通过不动的固体物料形成的床层面进行反应的设备都称为固定床反应器。
而其中尤以利用气态的反应物料,通过由固体催化剂所构成的床层进行反应的气固相催化反应器在化工生产中应用最为广泛。
例如石油炼制工业中的加氢裂化、歧化、异构化、加氢精制等;无机化学工业中的合成氨、硫酸、天然气转化等;有机化学工业中的乙烯氧化制环氧乙烷、乙烯水合制乙醇、乙苯脱氧制苯乙烯、苯加氢制环己烷等。
(二)特点结构简单、操作稳定、便于控制、易实现大型化和连续化生产等优点,是现代化工和反应中应用很广泛的反应器。
1、优点主要表现在以下几个方面:1)在生产操作中,除床层极薄和气体流速很低的特殊情况外,床层内气体的流动皆可看成是理想置换流动,因此在化学反应速度较快,在完成同样生产能力时,所需要的催化剂用量和反应器体积较小。
2)气体停留时间可以严格控制,温度分布可以调节,因而有利于提高化学反应的转化率和选择性。
3)催化剂不易磨损,可以较长时间连续使用。
4)适宜于高温高压条件下操作。
2、由于固体催化剂在床层中静止不动,相应地产生一些缺点:1)催化剂载体往往导热性不良,气体流速受压降限制又不能太大,导致床层中传热性能较差,也给温度控制带来困难。
对于放热反应,在换热式反应器的入口处,因为反应物浓度较高,反应速度较快,放出的热量往往来不及移走,而使物料温度升高,这又促使反应以更快的速度进行,放出更多的热量,物料温度继续升高,直到反应物浓度降低,反应速度减慢,传热速度超过了反应速度时,温度才逐渐下降。
所以在放热反应时,通常在换热式反应器的轴向存在一个最高的温度点,称为“热点”。
如设计或操作不当,则在强放热反应时,床内热点温度会超过工艺允许的最高温度,甚至失去控制而出现“飞温”。
此时,对反应的选择性、催化剂的活性和寿命、设备的强度等均极不利。
2)不能使用细粒催化剂,否则流体阻力增大,破坏了正常操作,所以催化剂的活性内表面得不到充分利用。
第六章_固定床反应器详解

3.熔盐:温度范围300℃~400℃,由无机熔
盐KNO3、NaNO3、NaNO2按一定比例组成, 在一定温度时呈熔融液体,挥发性很小。但 高温下渗透性强,有较强的氧化性。 4.烟道气:适用于600~700℃的高温反应。
26
6.2 固定床的传递特性
• 气体在催化剂颗粒
之间的孔隙中流动,
较在管内流动更容
补充水
产物
4. 自热式反应器
采用反应放出的热量来预热新鲜的进料,
达到热量自给和平衡,其设备紧凑,可用
于高压反应体系。
但其结构较复杂,操作弹性较小,启动反
应时常用电加热。
24
6.1.3 传热介质
•传热介质的选用根据反应的温度范围决定, 其温度与催化床的温差宜小,但又必须移走 大量的热,常用的传热介质有: 1.沸腾水:温度范围100~300℃。使用时需注 意水质处理,脱除水中溶解的氧。 2.联苯醚、烷基萘为主的石油馏分:粘度低 ,无腐蚀,无相变,温度范围200~ 350℃
如图 (b) 所示。径向反应器的结构较轴向 反应器复杂,催化剂装载于两个同心圆构 成的环隙中,流体沿径向流过床层,可采 用离心流动或向心流动。
径向反应器的优点是流体流过的距离较短
,流道截面积较大,床层阻力降较小。
轴向反应器与径向反应器
(a)
(b)
2.多段绝热式固定床反应器
热效应大,常把催化剂床层分成几段(层), 段间采用间接冷却或原料气(或惰性组分)
8
原料气
绝热式
催化剂
固定床 反应器
产物
9
绝热式固定床反应器可分为轴向反应器和
径向反应器。 (1)轴向绝热式固定床反应器
移动床技术

实际的SMB设备中,在程序 控制下,通过旋转阀RV的步 进,同步改变进料位置,和流 体流过床层方向抽出的位置, 实际上固体吸附剂是不移动的 。
中试设备图
SMB技术现已广泛用于分离和提纯
……
生物发酵
食品
SMB 的应用
手性药物
精细化学品
早期成功应用在石油的轻组 Fra bibliotek分离和果葡糖浆的纯化中。
由于具有设备结构小、产 率高、溶剂消耗少、分离能力 强、污染少以及便于连续化生 产和自动控制等优点,在生物 分离和手性拆分中备受关注。
移动床技术的发展
一种吸附操作单元
真实移动床( TMB )
模拟移动床( SMB )
什么是移动床?
固定床:间歇操作,非吸附分 离的时间比较长,若处理细胞浆 或发酵液会堵塞床层 流化床:吸附效率虽高,但返 混严重 ,吸附剂有磨损
? 移动床分离技术也称色谱分离技术,与传统的制 备色谱技术相比,现在移动床多采用连续操作的 手段,利于实现自动化,制备效率高,制备量大。
II 区: 抽取液出口与进料口 之间———解吸弱吸附组份
III 区: 进料口与抽余液出口 之间——吸附强吸附组份
IV区: 抽余液与洗脱液进口 之间——吸附弱吸附组份
每经过一个切换周期物料进出口管线沿液相流动方向移动一个色谱柱, 通过周期性开启、关闭进出口阀门来模拟固定相吸附剂与流动相液体的逆流
接触移动
除了pH、温度、吸附剂和吸附质的性质、床层空隙率、 颗粒空隙率、吸附等温线和传质参数外,与操作参数有关如:
切换时间 进料液流量 洗脱液流量 萃取液流量 萃余液流量 循环液流量
参数设计
安全边界因子法、 Massimo三角形理论法 驻波分析法
① ISMB (Improved SMB):即改进的模拟移动床技术,只需要少量 的柱数,但却可以实现比传统SMB系统更好的分离效果 。
催化重整技术问答
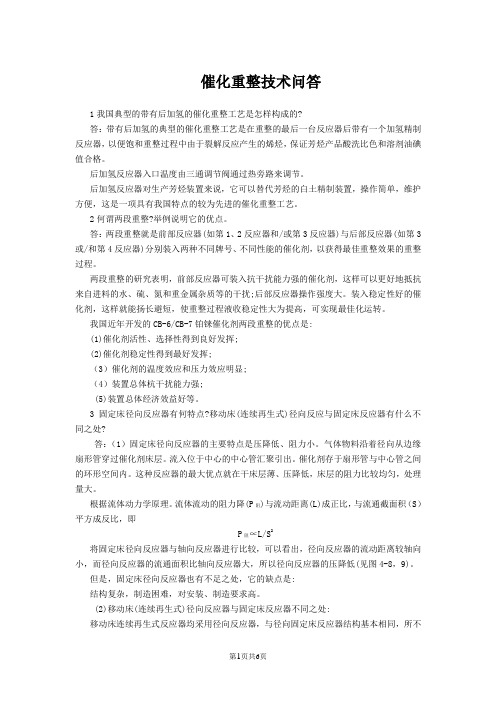
催化重整技术问答1我国典型的带有后加氢的催化重整工艺是怎样构成的?答:带有后加氢的典型的催化重整工艺是在重整的最后一台反应器后带有一个加氢精制反应器,以便饱和重整过程中由于裂解反应产生的烯烃,保证芳烃产品酸洗比色和溶剂油碘值合格。
后加氢反应器入口温度由三通调节阀通过热旁路来调节。
后加氢反应器对生产芳烃装置来说,它可以替代芳烃的白土精制装置,操作简单,维护方便,这是一项具有我国特点的较为先进的催化重整工艺。
2何谓两段重整?举例说明它的优点。
答:两段重整就是前部反应器(如第1、2反应器和/或第3反应器)与后部反应器(如第3或/和第4反应器)分别装入两种不同牌号、不同性能的催化剂,以获得最佳重整效果的重整过程。
两段重整的研究表明,前部反应器可装入抗干扰能力强的催化剂,这样可以更好地抵抗来自进料的水、硫、氮和重金属杂质等的干扰;后部反应器操作强度大。
装入稳定性好的催化剂,这样就能扬长避短,使重整过程液收稳定性大为提高,可实现最佳化运转。
我国近年开发的CB-6/CB-7铂铼催化剂两段重整的优点是:(1)催化剂活性、选择性得到良好发挥;(2)催化剂稳定性得到最好发挥;(3)催化剂的温度效应和压力效应明显;(4)装置总体杭干扰能力强;(5)装置总体经济效益好等。
3固定床径向反应器有何特点?移动床(连续再生式)径向反应与固定床反应器有什么不同之处?答:(1)固定床径向反应器的主要特点是压降低、阻力小。
气体物料沿着径向从边缘扇形管穿过催化剂床层。
流入位于中心的中心管汇聚引出。
催化剂存于扇形管与中心管之间的环形空间内。
这种反应器的最大优点就在干床层薄、压降低,床层的阻力比较均匀,处理量大。
根据流体动力学原理。
流体流动的阻力降(P阻)与流动距离(L)成正比,与流通截面积(S)平方成反比,即P阻∝L/S2将固定床径向反应器与轴向反应器进行比较,可以看出,径向反应器的流动距离较轴向小,而径向反应器的流通面积比轴向反应器大,所以径向反应器的压降低(见图4-8,9)。
几种固定床

几种固定床(移动床)气化炉的特点2009-02-21 10:05:37| 分类:默认分类|举报|字号订阅移动床(固定床)气化移动床气化又称固定床气化,属于逆流操作。
分为常压与加压两种。
常压法比较简单,但要求用块煤,低灰熔点的煤难以使用。
加压法是常压法的改进和提高,常用O2与水蒸气为气化剂,对煤种适应性大大提高。
属于这类炉型的气化炉有UGI炉、鲁奇(Lurgi)炉和液态排渣鲁奇(BGL)炉等。
(1) UGI炉固定床气化炉常压UGI炉以块状无烟煤或焦炭为原料,以空气和水蒸气为气化剂,在常压下生产合成原料气或燃料气。
该技术是20世纪30年代开发成功的,设备容易制造、操作简单、投资少。
但是,在日益重视规模化、环境保护和能源利用率的今天,这种常压煤气化技术设备能力低、三废量大以及必须使用无烟块煤等缺点变得日益突出。
①UGI炉单炉生产能力小。
即使是最大的3.6m炉,单炉的产气量也只有12000m3/h(标)左右,使得气化炉数量增多,布局十分困难。
②UGI炉生产现场操作环境恶劣。
一层潮湿,二层闷热,三层升腾的蒸汽让人难以忍受。
③一个制气循环分为吹风、上吹、下吹、二次上吹、空气吹净5个阶段。
气化过程中大约有1/3的时间用于吹风和倒换阀门,有效制气时间少,气化强度低。
另外,需要经常维护气化区的适当位置,加上阀门开启频繁,部件容易损坏,因而操作与管理比较繁琐。
④来自洗气箱和洗气塔的大量含氰废水和吹风气,对河流和空气造成严重污染。
⑤UGI炉对煤质的要求极为严格,原料必须是25~80mm的无烟块煤,入炉煤必须经过筛选,筛选下来的粉煤和碎煤只能低价卖出或烧锅炉。
⑥UGI炉碳转化率低,渣中含碳量高达22%以上,造成煤的大量浪费。
⑦UGI炉出炉煤气中CO+H2只有70%左右,而且炉出口温度低,气体含有相当量的煤焦油,给气体净化带来困难。
UGI炉目前已属于落后的技术,国外早已不再采用。
我国的中小氮肥厂仍有3000多台UGI炉在运转。
- 1、下载文档前请自行甄别文档内容的完整性,平台不提供额外的编辑、内容补充、找答案等附加服务。
- 2、"仅部分预览"的文档,不可在线预览部分如存在完整性等问题,可反馈申请退款(可完整预览的文档不适用该条件!)。
- 3、如文档侵犯您的权益,请联系客服反馈,我们会尽快为您处理(人工客服工作时间:9:00-18:30)。
固定床移动床的特点
固定床:
固定床反应器又称填充床反应器,装填有固体催化剂或固体反应物用以实现多相反应过程的一种反应器。
固体物通常呈颗粒状,粒径2~15mm左右,堆积成一定高度(或厚度)的床层。
床层静止不动,流体通过床层进行反应。
它与流化床反应器及移动床反应器的区别在于固体颗粒处于静止状态。
固定床反应器主要用于实现气固相催化反应,如氨合成塔、二氧化硫接触氧化器、烃类蒸汽转化炉等。
用于气固相或液固相非催化反应时,床层则填装固体反应物。
涓流床反应器也可归属于固定床反应器,气、液相并流向下通过床层,呈气液固相接触。
1、分类
固定床反应器有三种基本形式:①轴向绝热式固定床反应器。
流体沿轴向自上而下流经床层,床层同外界无热交换。
②径向绝热式固定床反应器。
流体沿径向流过床层,可采用离心流动或向心流动,床层同外界无热交换。
径向反应器与轴向反应器相比,流体流动的距离较短,流道截面积较大,流体的压力降较小。
但径向反应器的结构较轴向反应器复杂。
以上两种形式都属绝热反应器,适用于反应热效应不大,或反应系统能承受绝热条件下由反应热效应引起的温度变化的场合。
③列管式固定床反应器。
由多根反应管并联构成。
管内或管间置催化剂,载热体流经管间或管内进行加热或冷
却,管径通常在25~50mm之间,管数可多达上万根。
列管式固定床反应器适用于反应热效应较大的反应。
此外,尚有由上述基本形式串联组合而成的反应器,称为多级固定床反应器。
例如:当反应热效应大或需分段控制温度时,可将多个绝热反应器串联成多级绝热式固定床反应器,反应器之间设换热器或补充物料以调节温度,以便在接近于最佳温度条件下操作。
2、特点
固定床反应器的优点是:①返混小,流体同催化剂可进行有效接触,当反应伴有串联副反应时可得较高选择性。
②催化剂机械损耗小。
③结构简单。
固定床反应器的缺点是:①传热差,反应放热量很大时,即使是列管式反应器也可能出现飞温(反应温度失去控制,急剧上升,超过允许范围)。
②操作过程中催化剂不能更换,催化剂需要频繁再生的反应一般不宜使用,常代之以流化床反应器或移动床反应器。
固定床反应器中的催化剂不限于颗粒状,网状催化剂早已应用于工业上。
目前,蜂窝状、纤维状催化剂也已被广泛使用。
数学模型固定床反应器是研究得比较充分的一种多相反应器,描述固定床反应器的数学模型有多种,大致分为拟均相模型(不考虑流体和固体间的浓度、温度差别)和多相模型(考虑到流体和固体间
的浓度、温度差别)两类,每一类又可按是否计及返混,分为无返混模型和有返混模型,按是否考虑反应器径向的浓度梯
度和温度梯度分为一维模型和二维模型。
固定床反应器是一种被广泛采用的多相催化反应器,反应器内填充有固定不动的固体颗粒,可以是固体催化剂也可以是固体反应物.例如管式固定床反应器,管内装催化剂,管内装催化剂,反应物料自上而下通过床层,管间为载热体与管内反应物进行换热,以维持所需的温度条件.此外,固定床反应器也可用于气固及液固非催化反应。
当气体以较小的速度流过固定床时,流动气体的上升阻力不致使颗粒的运动状态发生变化,床高维持不变;床层压降随流速对数增大而增大。
流化床:
流化床:流体向上流过一个微细颗粒的床层(塔体),当流速低的时候流体只是穿过静止的颗粒之间的空隙,此时的床体称为固定床;随着流速的增加,颗粒互相离开,并可看到少量的颗粒在一定的区间进行震动和游动,称为膨胀床;速度再升高达到使全部颗粒都刚好悬浮在向上流动的气体或者液体中,此时的床层就是流化床起点。
固体颗粒可以像水等液体一样在设备内有明显的界面,即使设备倾斜,界面仍会保持水平;床层压降不随流速变化(基本不变)。
简单的说固体颗粒在流体作用下表现出类似流体状态的现象称为流态化。
流化床是流态化发生的设备。
流化床反应器中催化剂处于沸腾流化状态,被反应介质与提升介质带动快速通过反应器,如FCC的提升管反应器。
输送床:固体颗粒在设备内无明显界面;床层压力随流速增大而减小。
沸腾床是流化床的一种,固体在流化床反应器内流动,流体和固体颗粒所构成的床层犹如沸腾的液体. 沸腾床反应器下部设有分布板,板上放固体颗粒,流体自分布板下送入,当流体速度达到一定数值后,固体颗粒开始松动,再增大流速就进入流化状态.反应器内一般设有挡板,换热器,及流体与固体分离装置等内部部件. 沸腾床接触面大,传热传质效率高,时空产率高,但返混严重。
沸腾床因为固体处于运动状态,反应或传热效果好,但动力消耗大,而且在煤调湿中粉尘携带量大。
移动床:
移动床与固定床相似,不同的是固体颗粒自顶部连续加入,由底部卸出. 移动床(moving bed)离子交换树脂在交换器、再生器和清洗塔之间,周期性流动的离子交换装置。
移动床与固定固定床的差别在于反应过程中催化剂从反应器入口向出口缓慢运动,新鲜催化剂(或再生好的催化剂)从反应器入口进入,失活的催化剂从反应器出口移出,进行再生。
催化剂运动速度较慢,没有达到流化状态。
如U
OP与IFP连续重整工艺中的移动床反应器。
区别:
固定床可以处理高灰分,高灰熔点的煤,投资小,环保差……气流床产量最大,
但对煤种有一定要求;硫化床现在压力加不上去,推广受限。
这三种床最关键的就是设计床体,现在在国内设计床体大多数是一种经验估算和模拟实验,扩大到工业生产上往往存在很多缺点。
它们的主要区别还得看用途,物料的性质,既是物理过程还是化学反应过程。
固定床和移动床比较适合气-气、气-液和液-液反应,床层本身作为催化剂,优点是返混小,固相带出少,分离简单。
流化床的床型是设计中很重要的,与反应体系的匹配要求比较高。
此外,操作中的气速、带出量、与配套的旋风等分离设备设计比较严格。
流化床的传热和破汽泡、沟流措施也是研究比较多的。
流化床需要注意的是不能堵塞气体分布器,堵了很麻烦的。
固定床、移动床和沸腾床的区分是依据向床层内通气量的大小而定的,随着通气量的增加,一次是固定床、鼓泡床(沸腾床),湍动床,输送床。
移动床严格意义上属于流化床的范畴,是颗粒整理向下移动,床层高度不变,例如炼油中的催化重整工艺,是典型的移动床工艺。
至于应用范围和优缺点,相对而言流化床技术具有良好的传质、传热和各项均匀性,生产规模大,应用的最广泛,例如基于循环流化床开发的各种煤气化、燃烧工艺等等。
固定床和移动床受传质传热的限制,规模小,但是装置投资小,例如鲁奇的碎煤气化技术,就是典型的固定床,通常需要几台炉子一起交替生产,实现整个过程的连续。