@叠层实讲义体快速成型工艺
叠层实体快速原型制造工艺的基本原理

叠层实体快速原型制造工艺的基本原理一、引言叠层实体快速原型制造工艺是一种快速制造技术,它可以通过层层堆叠材料来构建三维实体模型。
该技术的优点是快速、灵活、经济,因此在工业设计、医疗器械、航空航天等领域得到了广泛应用。
本文将详细介绍叠层实体快速原型制造工艺的基本原理。
二、基本原理1. 快速成型技术概述快速成型技术(Rapid Prototyping,RP)是指利用计算机辅助设计(CAD)系统将设计模型转化为数字化的三维模型,并通过控制设备对材料进行逐层堆积或逐点加工的方式,直接制造出物理模型或零件的一种现代化制造技术。
2. 叠层实体快速原型制造工艺流程叠层实体快速原型制造工艺流程包括:CAD建模、STL文件生成、切片处理、机器参数设置和加工过程控制等步骤。
3. STL文件生成STL(STereoLithography)文件是一种三角面片格式文件,它描述了一个三维对象表面的几何形状。
在CAD软件中,用户可以将设计模型导出为STL格式文件。
4. 切片处理切片处理是将STL文件分割成多层二维图形的过程,每一层都代表着三维模型的一个截面。
切片厚度的大小决定了最终模型的精度和表面光滑度。
5. 机器参数设置机器参数设置包括材料选择、加工速度、温度控制等参数设置。
不同材料需要不同的加工参数,这些参数会影响到最终模型的质量和性能。
6. 加工过程控制加工过程控制是指通过计算机程序对设备进行控制,使其按照预定路径进行加工。
该过程需要保证设备在加工过程中稳定运行,并及时检测和纠正可能存在的误差。
7. 层层堆积原理叠层实体快速原型制造工艺通过将材料逐层堆积来构建三维实体模型。
在每一层堆积完成后,需要对其进行固化或热塑处理,以保证其稳定性和可操作性。
常用的堆积方式有激光束烧结、喷墨技术、熔融沉积等。
8. 激光束烧结原理激光束烧结是通过高能量激光束将粉末材料进行局部熔化和固化的一种加工方式。
在加工过程中,激光束按照预定路径扫描,将粉末材料逐层烧结成实体模型。
叠层实体快速成型工艺课件(PPT 39页)

第3章 叠层实体快速成型工艺
3.3
LOM工艺原型制作实例
工 艺 过 程
用SSM-800成型机来制作一个原型样件。该件为一个标准测试件, 其外形尺寸为200 mm x 150 mm x 20 mm,单个制作过程大约需 要3--4h。
第3章 叠层实体快速成型工艺
3.3
LOM工艺原型制作实例
1. 数据准备
①运动速度 ②路径参数 ③工作台参数 ④热压参数
⑤激光功率匹配
第3章 叠层实体快速成型工艺
3.3
工
1、 CAD模型及STL文件
艺
2、模型的切片处理
前处理
过
3、原型制造过程
程 4、后处理
3.3
工 艺 过 程
第3章 叠层实体快速成型工艺
原型制造过程 1、基底制作
实现原型与工作台之间的连接 避免起件时破坏原型
2、原型制作
关键参数
激光切割速度( ∝ 原型表面质量、制作时间) 激光能量(∝切割速度,切割纸材的的厚度) 加热辊温度与压力 切碎网格尺寸(∝余料去除的难易,原型表面质量)
第3章 叠层实体快速成型工艺
3.3
后处理
工
1、去除余料
艺
过
2、修补、打磨、抛光、表面涂覆
程
提高原型表面质量和机械强度,
保证原型尺寸稳定性、精度等方面的要求
3.2
2、热熔胶
材 料 要求:
1)良好的热熔冷固性 。
与 2)在反复“熔融—固化”条件下,具有较好的物理化学 设稳
定性 。
备 3)与纸具有足够的粘结强度 。
4)良好的废料分离性能 。
第3章 叠层实体快速成型工艺
3.2
材 料 与 设 备
四大快速成型工艺和优缺点

.
的粘结在前一层上,如此重复不已,直到整个产品成型完毕。最后升降台升出液体树脂表面,即可取出工 件,进行清洗和表面光洁处理。 光敏树脂选择性固化快速成型技术适合于制作中小形工件,能直接得到塑料产品。主要用于概念模型的原 型制作,或用来做装配检验和工艺规划。它还能代替腊模制作浇铸模具,以及作为金属喷涂模、环氧树脂 模和其他软模的母模,使目前较为成熟的快速原型工艺。 SLA 快速原型技术的优点是: 1、 系统工作稳定。系统一旦开始工作,构建零件的全过程完全自动运行,无需专人看管,直到整个工艺 过程结束。 2、 尺寸精度较高,可确保工件的尺寸精度在 0.1mm 以内。 3、 表面质量较好,工件的最上层表面很光滑,侧面可能有台阶不平及不同层面间的曲面不平。 4、 系统分辨率较高,因此能构建复杂结构的工件。 SLA 快速原型的技术缺点: 1、 随着时间推移,树脂会吸收空气中的水分,导致软薄部分的弯曲和卷翅。 2、 氦-镉激光管的寿命仅 3000 小时,价格较昂贵。同时需对整个截面进行扫描固化,成型时间较长,因 此制作成本相对较高。 3、 可选择的材料种类有限,必须是光敏树脂。由这类树脂制成的工件在大多数情况下都不能进行耐久性 和热性能试验,且光敏树脂对环境有污染,使皮肤过敏。 4、 需要设计工件的支撑结构,以便确保在成型过程中制作的每一个结构部位都能可靠定位。
粉末材料选择性烧结快速成型工艺适合于产品设计的可视化表现和制作功能测试零件。由于它可采用各种 不同成分的金属粉末进行烧结、进行渗铜等后处理,因而其制成的产品可具有与金属零件相近的机械性能, 故可用于制作 EDM 电极、直接制造金属模以及进行小批量零件生产。 SLS 快速成型技术的优点是:
;..
.
1、 与其他工艺相比,能生产最硬的模具。 2、 可以采用多种原料,例如绝大多数工程用塑料、蜡、金属、陶瓷等。 3、 零件的构建时间短,可达到 1in/h 高度。 4、 无需对零件进行后矫正。 5、 无需设计和构造支撑。 选择性烧结的最大优点是可选用多种材料,适合不同的用途、所制作的原型产品具有较高的硬度,可进行 功能试验。 SLS 快速原型技术缺点是: 1、 在加工前,要花近 2 小时的时间将粉末加热到熔点以下,当零件构建之后,还要花 5-10 小时冷却, 然 后才能将零件从粉末缸中取出。 2、 表面的粗糙度受到粉末颗粒大小及激光点的限制。 3、 零件的表面一般是多孔性的,为了使表面光滑必须进行后处理。 4、 需要对加工室不断充氮气以确保烧结过程的安全性,加工的成本高。 5、 该工艺产生有毒气体,污染环境。
四大快速成型工艺和优缺点

四大快速成型工艺和优缺点目前世界上的快速成型工艺主要有以下几种:一、FDM –熔融堆积工艺丝状材料选择性熔覆(Fused Deposition Modeling)快速原型工艺是一种不依靠激光作为成型能源、而将各种丝材加热溶化的成型方法,简称FDM。
丝状材料选择性熔覆的原理是,加热喷头在计算机的控制下,根据产品零件的截面轮廓信息,作X-Y平面运动。
热塑性丝状材料(如直径为1.78mm的塑料丝)由供丝机构送至喷头,并在喷头中加热和溶化成半液态,然后被挤压出来,有选择性的涂覆在工作台上,快速冷却后形成一层薄片轮廓。
一层截面成型完成后工作台下降一定高度,再进行下一层的熔覆,好像一层层"画出"截面轮廓,如此循环,最终形成三维产品零件。
这种工艺方法同样有多种材料选用,如ABS塑料、浇铸用蜡、人造橡胶等。
这种工艺干净,易于操作,不产生垃圾,小型系统可用于办公环境,没有产生毒气和化学污染的危险。
但仍需对整个截面进行扫描涂覆,成型时间长。
适合于产品设计的概念建模以及产品的形状及功能测试。
由于甲基丙烯酸ABS(MABS)材料具有较好的化学稳定性,可采用伽马射线消毒,特别适用于医用。
但成型精度相对较低,不适合于制作结构过分复杂的零件。
FDM快速成型技术的优点是:1、制造系统可用于办公环境,没有毒气或化学物质的危险。
2、工艺干净、简单、易于材作且不产生垃圾。
3、可快速构建瓶状或中空零件。
4、原材料以卷轴丝的形式提供,易于搬运和快速更换。
5、可选用多种材料,如可染色的ABS和医用ABS、浇铸用蜡和人造橡胶。
FDM快速原型技术的缺点是:1、精度较低,难以构建结构复杂的零件。
2、垂直方向强度小。
3、速度较慢,不适合构建大型零件。
二、SLA –树脂光固化工艺光敏树脂选择性固化是采用立体雕刻(Stereolithography)原理的一种工艺,简称SLA,也是最早出现的、技术最成熟和应用最广泛的快速成型技术。
常用快速成型基本方法简介

1前言快速成型(Rapid Prototyping)是上世纪80年代末及90 年代初发展起来的高新制造技术,是由三维CAD模型直接驱动的快速制造任意复杂形状三维实体的总称。
它集成了CA D技术、数控技术、激光技术和材料技术等现代科技成果,是先进制造技术的重要组成部分。
由于它把复杂的三维制造转化为一系列二维制造的叠加,因而可以在不用模具和工具的条件下生成几乎任意复杂的零部件,极大地提高了生产效率和制造柔性。
与传统制造方法不同,快速成型从零件的CAD几何模型出发,通过软件分层离散和数控成型系统,用激光束或其他方法将材料堆积而形成实体零件。
通过与数控加工、铸造、金属冷喷涂、硅胶模等制造手段相结合,已成为现代模型、模具和零件制造的强有力手段,在航空航天、汽车摩托车、家电等领域得到了广泛应用。
2 快速成型的基本原理快速成型技术采用离散/堆积成型原理,根据三维CAD模型,对于不同的工艺要求,按一定厚度进行分层,将三维数字模型变成厚度很薄的二维平面模型。
再将数据进行一定的处理,加入加工参数,产生数控代码,在数控系统控制下以平面加工方式连续加工出每个薄层,并使之粘结而成形。
实际上就是基于“生长”或“添加”材料原理一层一层地离散叠加,从底至顶完成零件的制作过程。
快速成型有很多种工艺方法,但所有的快速成型工艺方法都是一层一层地制造零件,所不同的是每种方法所用的材料不同,制造每一层添加材料的方法不同。
快速成型的基本原理图快速成型的工艺过程原理如下:(1)三维模型的构造:在三维CAD设计软件中获得描述该零件的CAD文件。
一般快速成型支持的文件输出格式为STL模型,即对实体曲面做近似的所谓面型化(Tessellation)处理,是用平面三角形面片近似模型表面。
以简化CAD模型的数据格式。
便于后续的分层处理。
由于它在数据处理上较简单,而且与CAD系统无关,所以很快发展为快速成型制造领域中CAD系统与快速成型机之间数据交换的标准,每个三角面片用四个数据项表示。
快速成型

四种快速成型方法的特点及常用材料 零件
成型方法
大小
熔融堆积 成型 中小件
复杂 程度
中等
精度
较低
0.1~石墨、塑料、 低熔点金属等
较慢 快
较低 低
叠层实体成型
中小件
简单 或 中等
较高
0.02~0.2mm
纸、金属箔、 塑料薄膜 热固性光敏树 脂等
石蜡、塑料、 金属、陶瓷等 粉末
(2)叠层实体制造(Laminated Object Manufacturing,LOM)
它是将单面涂有热溶胶的箔材(涂覆纸-涂有粘结剂覆层的纸、 涂敷陶瓷等)通过加热辊加热粘结在一起,使激光束在片材平 面内沿确定轨迹扫描而形成平面模型。 平面模型逐层堆 叠并在滚压辊的滚压 下粘结逐步形成整体 物理模型,去除废料 后即成型。废料部分 切成网络是为了便于 消除。
(2)制造者
制造者在产品设计的初级阶段,也能拿到实在的产品样品、甚至 试制用的工模具及少量产品,这使得他们能及时地对产品设计提出 意见,做好原材料、标准件、外协加工件、加工工艺和批量生产用 工模具等的准备,最大限度地减少失误和返工,大大节省工时、降 低加工成本和提高产品质量。
(3)推销者
推销者在产品设计最初阶段,也可拿到产品样品、甚至少量产品, 这使得他们能据此及早、实在地向用户宣传,征求意见,以及进行 比较准确的市场需求预测,而不是仅凭抽象的产品描述或一张图纸、 一份样本来推销。所以,快速成型技术的应用可以显著的降低新产 品的销售风险和成本,大大缩短其投放市场时间和提高竞争能力。
立体光 固化成型
中小件
中等
较高
0.02~0.2mm
较快
较高
选择性激光烧结 成型 中小件
四种常见快速成型技术

四种常见快速成型技术FDM丝状材料选择性熔覆(Fus ed Dep osi tion Mod eling)快速原型工艺是一种不依*激光作为成型能源、而将各种丝材加热溶化的成型方法,简称FDM。
丝状材料选择性熔覆的原理室,加热喷头在计算机的控制下,根据产品零件的截面轮廓信息,作X-Y平面运动。
热塑性丝状材料(如直径为1.78m m的塑料丝)由供丝机构送至喷头,并在喷头中加热和溶化成半液态,然后被挤压出来,有选择性的涂覆在工作台上,快速冷却后形成一层大约0.127mm厚的薄片轮廓。
一层截面成型完成后工作台下降一定高度,再进行下一层的熔覆,好像一层层"画出"截面轮廓,如此循环,最终形成三维产品零件。
这种工艺方法同样有多种材料选用,如ABS塑料、浇铸用蜡、人造橡胶等。
这种工艺干净,易于操作,不产生垃圾,小型系统可用于办公环境,没有产生毒气和化学污染的危险。
但仍需对整个截面进行扫描涂覆,成型时间长。
适合于产品设计的概念建模以及产品的形状及功能测试。
由于甲基丙烯酸ABS(M AB S)材料具有较好的化学稳定性,可采用加码射线消毒,特别适用于医用。
但成型精度相对较低,不适合于制作结构过分复杂的零件。
FD M快速原型技术的优点是:1、操作环境干净、安全可在办公室环境下进行。
2、工艺干净、简单、易于材作且不产生垃圾。
3、尺寸精度较高,表面质量较好,易于装配。
可快速构建瓶状或中空零件。
4、原材料以卷轴丝的形式提供,易于搬运和快速更换。
5、材料利用率高。
6、可选用多种材料,如可染色的A BS和医用A BS、PC、PP SF等。
FDM快速原型技术的缺点是:1、做小件或精细件时精度不如SLA,最高精度0.127mm。
2、速度较慢。
SL A敏树脂选择性固化是采用立体雕刻(Stereo litho gra phy)原理的一种工艺,简称SLA,也是最早出现的、技术最成熟和应用最广泛的快速原型技术。
在树脂液槽中盛满液态光敏树脂,它在紫外激光束的照射下会快速固化。
叠层制造及其它快速成型工艺与设备
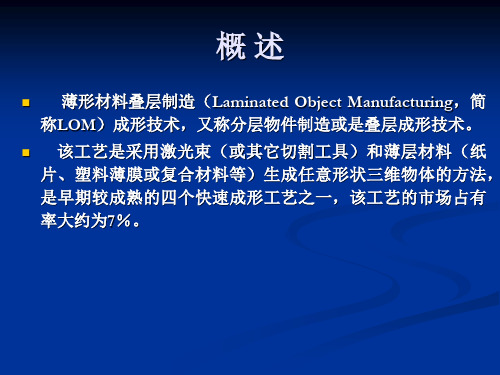
LOM快速原型工艺适合制作大中型原型件,翘曲变形较小,成型时间较短,激光器使用寿命长,制成件有良好的机械性能,适合于产品设计的概念建模和功能性测试零件,且由于制成的零件具有木质属性,特别适合于直接制作砂型铸造模。
面曝光快速成型
MPSL(Mask Projection Stereolithography)面曝光快速成型与扫描式固化快速成型最大的不同在于采用片层掩膜技术,一次曝光固化一个层面的实体。MPSL的关键技术之一是如何生成图形动态掩膜(Dynamic Mask)。 图形掩膜的生成方式有多种,早期是利用静电复印技术原理,在玻璃底版上生成图形掩膜。目前,比较典型的图形生成工艺是采用液晶显示技术(Liquid Crystal Display,LCD)和数字投影技术(Digital Light Processing,DLP)。下面对这两种技术分别进行简单地介绍,着重说明一下DLP的技术原理。
LOM快速成形技术的缺点
6. 表面比较粗糙,工件表面有明显的台阶纹,成型后要进行打磨;且纸制零件很容易吸潮,必须立即进行后处理、上漆。 7. 难以构建精细形状的零件,即仅限于结构简单的零件。 8. 由于难以(虽然并非不可能)去除里面的废料,该工艺不宜构建内部结构复杂的零件。 9. 当加工室的温度过高时常有火灾发生,因此,工作过程中需要专职人员职守。
MPSL技术基本原理
由分析可以看出,相比于LCD,DMD能更好地适应快速成型加工所需要的高精度、高可靠性以及对紫外光源能量较高的承受能力。因此将DLP技术应用到光固化快速成型技术的面曝光快速成型具有更好的发展前景。 它主要包括两大部分:固化成像器件即掩膜发生器和机械辅助装置即升降、涂覆系统等。掩膜发生器负责完成每层图像的生成,由紫外光照射投影到成像位置,即光敏树脂液面处,曝光固化一次树脂,再通过升降装置以及涂覆系统完成新一层树脂的准备工作,从而开始下一层的固化。
2.1第二章_快速成型制造工艺--I
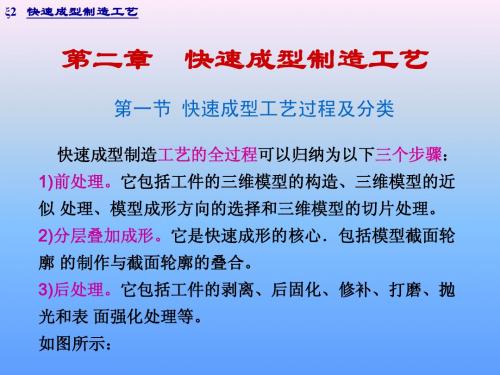
ξ2 快速成型制造工艺
支撑结构的作用和类型:
作用:支撑作用和减少翘曲变形。
类型:斜支撑
主要用于支撑悬臂结构部分,在 成型过程中为悬臂提供支承,同 时也约束悬臂的翘曲变形。
直支撑
主要用于支承腿部结构
ξ2 快速成型制造工艺
• 有时为了减少支撑量,以节省材料及方便后处理,也 经常采用倾斜摆放。确定摆放方位以及后续的施加支 撑和切片处理等都是在分层软件系统上实现。 • 对于上述的小扳手,由于其尺寸较小,为了保证 轴部外径尺寸以及轴部内孔尺寸的精度,选择直立摆
放,如图2-2c所示。同时考虑到尽可能减小支撑的批
次,大端朝下摆放。
生聚合反应,选择时有局限性。
需要二次固化
经快速成型系统光固化后的原型树脂并未完 全被激光固化。
较脆,易断裂性能尚不如常用的工业塑料
ξ2 快速成型制造工艺
二、 光固化快速原型的工艺过程
光固化快速原型的制作一般可以分为前处理、原型制作和
后处理三个阶段。
(一)前处理
前处理阶段主要是对原型的CAD模型进行数据转换、摆放方位确定、 施加支撑和切片分层,实际上就是为原型的制作准备数据。下面以某一小 扳手的制作来介绍光固化原型制作的前处理过程。
成型方向选择
表面处理 表面处理
*****
切片处理
快速成型制作过程
ξ2 快速成型制造工艺
快速成型制造系统
快 速 成 型 产 品 造 型
产 品 原 型
ξ2 快速成型制造工艺
快速成型制造技术从广义上讲可以分成两类:材料叠加和材料去除。下 图给出了当前众多快速成型工艺根据材料和构建技术不同进行的分类。
ξ2 快速成型制造工艺
ξ2 快速成型制造工艺
快速成型技术的原理工艺过程及技术特点
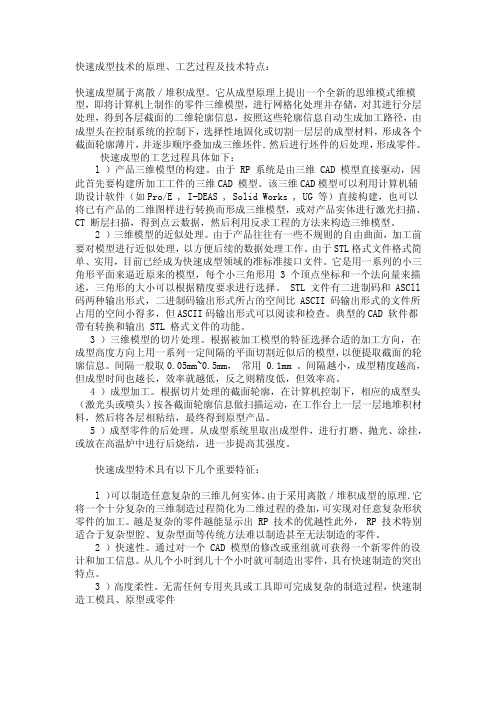
快速成型技术的原理、工艺过程及技术特点:快速成型属于离散/堆积成型。
它从成型原理上提出一个全新的思维模式维模型,即将计算机上制作的零件三维模型,进行网格化处理并存储,对其进行分层处理,得到各层截面的二维轮廓信息,按照这些轮廓信息自动生成加工路径,由成型头在控制系统的控制下,选择性地固化或切割一层层的成型材料,形成各个截面轮廓薄片,并逐步顺序叠加成三维坯件.然后进行坯件的后处理,形成零件。
快速成型的工艺过程具体如下:l )产品三维模型的构建。
由于 RP 系统是由三维 CAD 模型直接驱动,因此首先要构建所加工工件的三维CAD 模型。
该三维CAD模型可以利用计算机辅助设计软件(如Pro/E , I-DEAS , Solid Works , UG 等)直接构建,也可以将已有产品的二维图样进行转换而形成三维模型,或对产品实体进行激光扫描、CT 断层扫描,得到点云数据,然后利用反求工程的方法来构造三维模型。
2 )三维模型的近似处理。
由于产品往往有一些不规则的自由曲面,加工前要对模型进行近似处理,以方便后续的数据处理工作。
由于STL格式文件格式简单、实用,目前已经成为快速成型领域的准标准接口文件。
它是用一系列的小三角形平面来逼近原来的模型,每个小三角形用3 个顶点坐标和一个法向量来描述,三角形的大小可以根据精度要求进行选择。
STL 文件有二进制码和 ASCll 码两种输出形式,二进制码输出形式所占的空间比 ASCII 码输出形式的文件所占用的空间小得多,但ASCII码输出形式可以阅读和检查。
典型的CAD 软件都带有转换和输出 STL 格式文件的功能。
3 )三维模型的切片处理。
根据被加工模型的特征选择合适的加工方向,在成型高度方向上用一系列一定间隔的平面切割近似后的模型,以便提取截面的轮廓信息。
间隔一般取0.05mm~0.5mm,常用 0.1mm 。
间隔越小,成型精度越高,但成型时间也越长,效率就越低,反之则精度低,但效率高。
《逆向工程及快速成型原理》讲义12版——快速成形技术
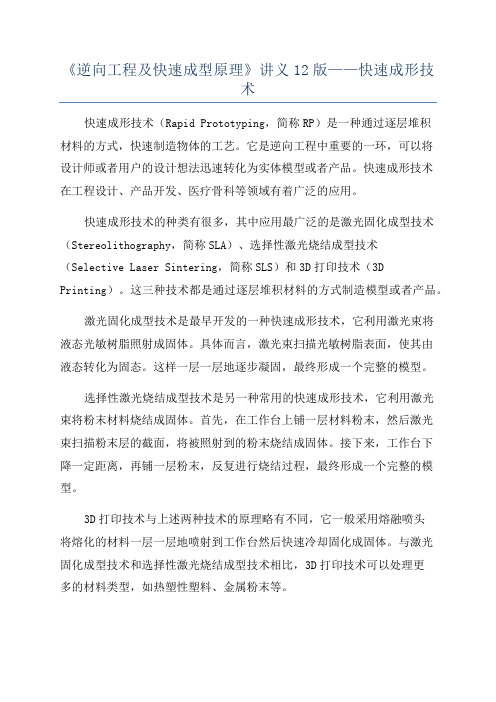
《逆向工程及快速成型原理》讲义12版——快速成形技术快速成形技术(Rapid Prototyping,简称RP)是一种通过逐层堆积材料的方式,快速制造物体的工艺。
它是逆向工程中重要的一环,可以将设计师或者用户的设计想法迅速转化为实体模型或者产品。
快速成形技术在工程设计、产品开发、医疗骨科等领域有着广泛的应用。
快速成形技术的种类有很多,其中应用最广泛的是激光固化成型技术(Stereolithography,简称SLA)、选择性激光烧结成型技术(Selective Laser Sintering,简称SLS)和3D打印技术(3D Printing)。
这三种技术都是通过逐层堆积材料的方式制造模型或者产品。
激光固化成型技术是最早开发的一种快速成形技术,它利用激光束将液态光敏树脂照射成固体。
具体而言,激光束扫描光敏树脂表面,使其由液态转化为固态。
这样一层一层地逐步凝固,最终形成一个完整的模型。
选择性激光烧结成型技术是另一种常用的快速成形技术,它利用激光束将粉末材料烧结成固体。
首先,在工作台上铺一层材料粉末,然后激光束扫描粉末层的截面,将被照射到的粉末烧结成固体。
接下来,工作台下降一定距离,再铺一层粉末,反复进行烧结过程,最终形成一个完整的模型。
3D打印技术与上述两种技术的原理略有不同,它一般采用熔融喷头将熔化的材料一层一层地喷射到工作台然后快速冷却固化成固体。
与激光固化成型技术和选择性激光烧结成型技术相比,3D打印技术可以处理更多的材料类型,如热塑性塑料、金属粉末等。
与传统的手工模型制作相比,快速成形技术具有以下优势。
首先,它可以快速、准确地制造复杂形状的模型或者产品,减少了设计和制造的周期,加快了产品开发的速度。
其次,快速成形技术可以直接根据设计数据制造模型,减少了传统模具制造的过程和成本。
最后,快速成形技术可以提供可视化的实体模型便设计师和用户直观地评估设计效果。
虽然快速成形技术在设计和制造领域有着广泛的应用,但也存在一些挑战和限制。
四种常见快速成型技术

四种常见快速成型技术FDM丝状材料选择性熔覆(Fus ed Dep osi tion Mod eling)快速原型工艺是一种不依*激光作为成型能源、而将各种丝材加热溶化的成型方法,简称FDM。
丝状材料选择性熔覆的原理室,加热喷头在计算机的控制下,根据产品零件的截面轮廓信息,作X-Y平面运动。
热塑性丝状材料(如直径为1.78m m的塑料丝)由供丝机构送至喷头,并在喷头中加热和溶化成半液态,然后被挤压出来,有选择性的涂覆在工作台上,快速冷却后形成一层大约0.127mm厚的薄片轮廓。
一层截面成型完成后工作台下降一定高度,再进行下一层的熔覆,好像一层层"画出"截面轮廓,如此循环,最终形成三维产品零件。
这种工艺方法同样有多种材料选用,如ABS塑料、浇铸用蜡、人造橡胶等。
这种工艺干净,易于操作,不产生垃圾,小型系统可用于办公环境,没有产生毒气和化学污染的危险。
但仍需对整个截面进行扫描涂覆,成型时间长。
适合于产品设计的概念建模以及产品的形状及功能测试。
由于甲基丙烯酸ABS(M AB S)材料具有较好的化学稳定性,可采用加码射线消毒,特别适用于医用。
但成型精度相对较低,不适合于制作结构过分复杂的零件。
FD M快速原型技术的优点是:1、操作环境干净、安全可在办公室环境下进行。
2、工艺干净、简单、易于材作且不产生垃圾。
3、尺寸精度较高,表面质量较好,易于装配。
可快速构建瓶状或中空零件。
4、原材料以卷轴丝的形式提供,易于搬运和快速更换。
5、材料利用率高。
6、可选用多种材料,如可染色的A BS和医用A BS、PC、PP SF等。
FDM快速原型技术的缺点是:1、做小件或精细件时精度不如SLA,最高精度0.127mm。
2、速度较慢。
SL A敏树脂选择性固化是采用立体雕刻(Stereo litho gra phy)原理的一种工艺,简称SLA,也是最早出现的、技术最成熟和应用最广泛的快速原型技术。
在树脂液槽中盛满液态光敏树脂,它在紫外激光束的照射下会快速固化。
第三章_叠层实体快速成型工艺(专业课堂)
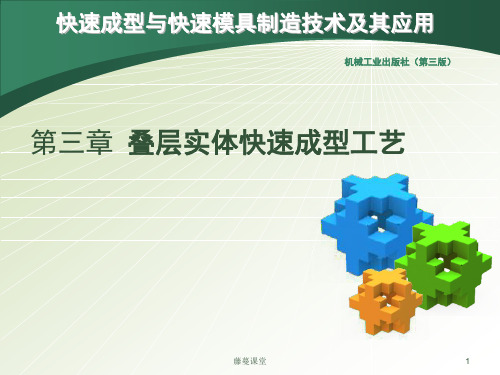
藤蔓课堂
12
第二节 叠层实体快速成型的材料和设备
图3-4 Solidimension 藤公蔓司课开堂发的SD 300 叠层打印机
13
第二节 叠层实体快速成型的材料和设备
图3-5 SD300 叠层打印机耗材配件及制作的模型
藤蔓课堂
14
第二节 叠层实体快速成型的材料和设备
图3-6 HRP系列薄材叠层快速成型机
藤蔓课堂
15
第二节 叠层实体快速成型的材料和设备
藤蔓课堂
16
第三章 叠层实体快速成型工艺
1 叠层实体制造工艺的基本原理和特点
2 叠层实体快速成型的材料与设备 3 叠层实体快速成型的工艺过程
4 提高叠层实体快速成型制作质量的措施
5 叠层实体制造工艺后置处理中的表面涂覆
6 新型叠层实体快速成型工艺方法
藤蔓课堂
17
第三节 叠层实体快速成型的工艺过程
前 处 STL文件
理
切片处理
分
设置工艺参数
层
叠
激光 加热 切片 切碎 切割 辊温 软件 网格
加
速度 度 精度 尺寸
基底制作
原型制作
后 处 余料去除 理
表面质量处理
提高强硬度处理
藤蔓课堂
18
第三章 叠层实体快速成型工艺
1 叠层实体制造工艺的基本原理和特点
藤蔓课堂
7
第二节 叠层实体快速成型的材料和设备
1.叠层实体快速成型材料
薄层材料:纸、塑料薄膜、金属箔等
粘结剂:热熔胶
制备工艺:涂布工艺
纸的性能要求:
1)抗湿性
2)良好的浸润性
3)抗拉强度
4)收缩率小
5)剥离性能好
四种常见快速成型技术

四种常见快速成型技术FDM丝状材料选择性熔覆(Fus ed Dep osi tion Mod eling)快速原型工艺是一种不依*激光作为成型能源、而将各种丝材加热溶化的成型方法,简称FDM。
丝状材料选择性熔覆的原理室,加热喷头在计算机的控制下,根据产品零件的截面轮廓信息,作X-Y平面运动。
热塑性丝状材料(如直径为1.78m m的塑料丝)由供丝机构送至喷头,并在喷头中加热和溶化成半液态,然后被挤压出来,有选择性的涂覆在工作台上,快速冷却后形成一层大约0.127mm厚的薄片轮廓。
一层截面成型完成后工作台下降一定高度,再进行下一层的熔覆,好像一层层"画出"截面轮廓,如此循环,最终形成三维产品零件。
这种工艺方法同样有多种材料选用,如ABS塑料、浇铸用蜡、人造橡胶等。
这种工艺干净,易于操作,不产生垃圾,小型系统可用于办公环境,没有产生毒气和化学污染的危险。
但仍需对整个截面进行扫描涂覆,成型时间长。
适合于产品设计的概念建模以及产品的形状及功能测试。
由于甲基丙烯酸ABS(M AB S)材料具有较好的化学稳定性,可采用加码射线消毒,特别适用于医用。
但成型精度相对较低,不适合于制作结构过分复杂的零件。
FD M快速原型技术的优点是:1、操作环境干净、安全可在办公室环境下进行。
2、工艺干净、简单、易于材作且不产生垃圾。
3、尺寸精度较高,表面质量较好,易于装配。
可快速构建瓶状或中空零件。
4、原材料以卷轴丝的形式提供,易于搬运和快速更换。
5、材料利用率高。
6、可选用多种材料,如可染色的A BS和医用A BS、PC、PP SF等。
FDM快速原型技术的缺点是:1、做小件或精细件时精度不如SLA,最高精度0.127mm。
2、速度较慢。
SL A敏树脂选择性固化是采用立体雕刻(Stereo litho gra phy)原理的一种工艺,简称SLA,也是最早出现的、技术最成熟和应用最广泛的快速原型技术。
在树脂液槽中盛满液态光敏树脂,它在紫外激光束的照射下会快速固化。
四种常见快速成型技术
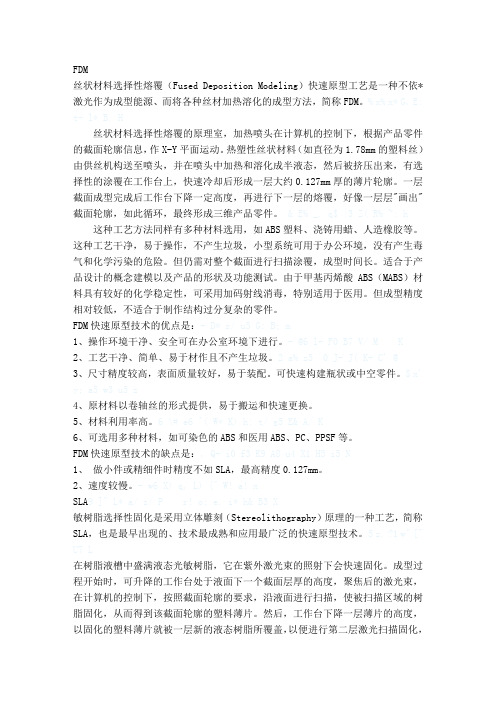
FDM丝状材料选择性熔覆(Fused Deposition Modeling)快速原型工艺是一种不依*激光作为成型能源、而将各种丝材加热溶化的成型方法,简称FDM。
% x% x* G, E: t- l* B. H丝状材料选择性熔覆的原理室,加热喷头在计算机的控制下,根据产品零件的截面轮廓信息,作X-Y平面运动。
热塑性丝状材料(如直径为1.78mm的塑料丝)由供丝机构送至喷头,并在喷头中加热和溶化成半液态,然后被挤压出来,有选择性的涂覆在工作台上,快速冷却后形成一层大约0.127mm厚的薄片轮廓。
一层截面成型完成后工作台下降一定高度,再进行下一层的熔覆,好像一层层"画出"截面轮廓,如此循环,最终形成三维产品零件。
& E% _. q$ |3 Z( R% ~: h这种工艺方法同样有多种材料选用,如ABS塑料、浇铸用蜡、人造橡胶等。
这种工艺干净,易于操作,不产生垃圾,小型系统可用于办公环境,没有产生毒气和化学污染的危险。
但仍需对整个截面进行扫描涂覆,成型时间长。
适合于产品设计的概念建模以及产品的形状及功能测试。
由于甲基丙烯酸ABS(MABS)材料具有较好的化学稳定性,可采用加码射线消毒,特别适用于医用。
但成型精度相对较低,不适合于制作结构过分复杂的零件。
FDM快速原型技术的优点是:- D* r/ u5 G: B; m1、操作环境干净、安全可在办公室环境下进行。
- @6 l- F0 B7 V/ M K2、工艺干净、简单、易于材作且不产生垃圾。
2 a% z5 `0 J- J( K+ C' @3、尺寸精度较高,表面质量较好,易于装配。
可快速构建瓶状或中空零件。
$ x' y; a5 w3 u5 z4、原材料以卷轴丝的形式提供,易于搬运和快速更换。
5、材料利用率高。
6 \# e6 ^( W* K) h: t/ g5 E& A/ K6、可选用多种材料,如可染色的ABS和医用ABS、PC、PPSF等。
叠层实体快速成型工艺
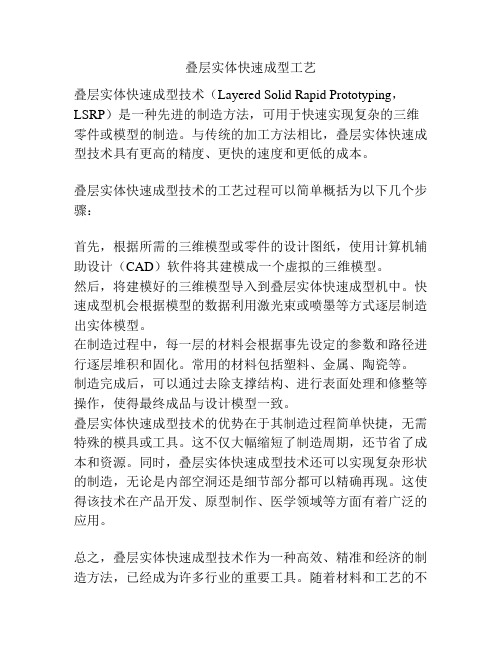
叠层实体快速成型工艺叠层实体快速成型技术(Layered Solid Rapid Prototyping,LSRP)是一种先进的制造方法,可用于快速实现复杂的三维零件或模型的制造。
与传统的加工方法相比,叠层实体快速成型技术具有更高的精度、更快的速度和更低的成本。
叠层实体快速成型技术的工艺过程可以简单概括为以下几个步骤:首先,根据所需的三维模型或零件的设计图纸,使用计算机辅助设计(CAD)软件将其建模成一个虚拟的三维模型。
然后,将建模好的三维模型导入到叠层实体快速成型机中。
快速成型机会根据模型的数据利用激光束或喷墨等方式逐层制造出实体模型。
在制造过程中,每一层的材料会根据事先设定的参数和路径进行逐层堆积和固化。
常用的材料包括塑料、金属、陶瓷等。
制造完成后,可以通过去除支撑结构、进行表面处理和修整等操作,使得最终成品与设计模型一致。
叠层实体快速成型技术的优势在于其制造过程简单快捷,无需特殊的模具或工具。
这不仅大幅缩短了制造周期,还节省了成本和资源。
同时,叠层实体快速成型技术还可以实现复杂形状的制造,无论是内部空洞还是细节部分都可以精确再现。
这使得该技术在产品开发、原型制作、医学领域等方面有着广泛的应用。
总之,叠层实体快速成型技术作为一种高效、精准和经济的制造方法,已经成为许多行业的重要工具。
随着材料和工艺的不断创新,相信叠层实体快速成型技术将会在未来有更加广泛的应用前景。
叠层实体快速成型(Layered Solid Rapid Prototyping,LSRP)技术是一种基于计算机辅助设计(CAD)的先进制造方法,通过逐层堆积和固化材料,快速制造出复杂的三维实体模型。
LSRP技术不仅可以用于原型制作,还可以直接应用于批量生产。
其工艺流程简单快捷,制造周期短,能够满足各类复杂形状和功能的需求,因此在众多领域得到了广泛的应用。
叠层实体快速成型技术最初由美国麻省理工学院在1980年代提出并发展起来。
随着计算机技术的不断进步和材料科学的发展,LSRP技术得以快速发展。