最佳化模具设计方案_完整版
模具工艺方案

模具工艺方案引言模具工艺方案是指在零件加工过程中,为了实现零件的形状、尺寸、表面粗糙度等复杂要求,使用模具进行加工的工艺方案。
在模具加工过程中,需要考虑材料选择、模具设计、加工工艺等多个因素,以确保模具的准确度和加工效果。
本文将介绍一套完整的模具工艺方案。
1. 材料选择选择适合的材料对于模具的加工效果起着重要作用。
通常,模具材料需要具备以下特点:•高硬度:能够保持在高温、高压下不变形。
•耐磨性:能够承受长时间摩擦磨损而不失效。
•耐蚀性:能够抵抗酸碱腐蚀。
•良好的热稳定性:能够在高温环境下使用,不受气候变化影响。
•可加工性好:易于加工、切削和刻蚀。
常见模具材料包括钢材(如工具钢、合金钢)、铝合金等。
根据具体的加工要求和零件特性,我们可以选择合适的材料。
2. 模具设计模具设计是模具制造的重要环节。
合理的模具设计能够确保模具的精度和寿命,提高加工效率。
在模具设计过程中,需要考虑以下关键因素:•零件结构:根据零件的形状、尺寸等特点,设计模具的结构,确保模具能够完整复制出零件的形状。
•模具材料选择:根据需要冷却、加热的区域,选择合适的模具材料,以满足加工要求。
•零件脱模:设计合理的脱模方式,确保零件能够顺利脱离模具。
•模具寿命:考虑模具的使用寿命,选择合适的表面处理方式以提高模具的耐磨性和耐腐蚀性。
模具设计需要结合具体的加工要求和材料特性,通过CAD等设计软件进行建模和优化,以确保设计的合理性和准确性。
3. 加工工艺加工工艺是指模具制造过程中的操作步骤和技术要求。
合理的加工工艺能够提高生产效率,保证模具的精度和质量。
3.1 切削加工切削加工是模具制造过程中的关键环节。
切削加工包括车削、铣削、镗削、钻削等,根据模具的形状和要求选择不同的切削方式。
切削加工需要注意以下几点:•选择合适的刀具:根据加工要求和工件材料选择合适的刀具,确保切削效果和刀具寿命。
•控制切削速度和进给速度:根据材料硬度和加工要求,合理控制切削速度和进给速度,以免损坏刀具或工件。
模具结构设计方案

模具结构设计方案模具是工业生产中常用的工具之一,广泛应用于塑料、金属、陶瓷等制品的生产过程中。
模具的结构设计对产品的成型质量、生产效率以及模具寿命等都有着重要的影响。
下面将以塑料模具为例,详细介绍模具结构设计的几个方面。
首先是模具的整体结构设计。
模具一般由上、下两部分组成,上模和下模之间通过模具螺栓连接。
上模通常由进料口、固定板、移动板、顶针等部分组成,下模则由底板、定位销、导向板等部分组成。
在整体结构设计中,需要注意上、下模的对位准确、顶出机构的稳定性以及模具的可拆卸性等。
其次是注塑模具中的流道系统设计。
流道系统是塑料模具中最关键的部分,直接影响产品的成型质量。
在流道系统的设计中,需要考虑塑料的充填速度、压力和温度等因素,合理选择流道的截面形状和尺寸。
同时,还需要设计出合适的喷嘴和冷却系统,以确保塑料在流道中充分流动和冷却。
第三是模具的冷却系统设计。
冷却系统对于模具寿命和产品质量有着重要的影响。
在冷却系统的设计中,需要合理设置冷却通道,并确保冷却通道与模具表面的距离足够近,以提高冷却效果。
同时,还需要注意冷却通道的位置和布局,以保证整个模具受热均匀,避免产生应力集中和变形等问题。
另外还需要考虑模具的顶出机构设计。
顶出机构主要用于将成型的产品从模具中弹出,避免产品粘模。
在顶出机构的设计中,需要确保顶出机构的稳定性和可靠性,同时考虑到产品的形状、材料和尺寸等因素,设计合适的顶出机构形式和数量。
最后是模具材料的选择。
模具材料的选择直接影响到模具的使用寿命和成本。
一般而言,模具材料要求具有较高的硬度、强度和耐磨性,同时还需具备一定的耐腐蚀性和导热性等特点。
在选择模具材料时,需要根据具体的生产需求和经济因素综合考虑,选择合适的模具材料。
综上所述,模具结构设计是一个复杂的工作,需要考虑多个方面的因素。
合理的模具结构设计可以提高产品的成型质量和生产效率,延长模具的使用寿命,减少生产成本。
因此,在进行模具结构设计时,需要充分考虑以上几个方面的原则和要点,以保证模具的性能和质量。
模 具 设 计 方 案

模具设计方案一、零件生产纲领和技术要求1.生产纲领:大批量生产。
2.产品技术要求(冲压件的特性及及尺寸的精度要求)(1)产品特性(2)零件形状,尺寸的精度要求(3)产品设计基准及其他要求二、工艺、经济效益分析及模具类型方案确定1.工艺分析2.经济效益分析3.冲压方案确定:通过艺、经济效益和生产纲领综合分析采用级进模具不论在零件精度、生产效率、寿命都有明显的优势。
因此确定采用级进模。
三、级进模设计主要参数计算(1)料片展开(2)排样图设计:确定步距、条料宽度、搭边量(方案1/2)、工位1要冲出定位孔和边侧检测曹为以后冲压保证定位的精度孔位要求精度高的尽可能一次冲出,不能一次冲出的,要在相邻两位完成。
在成型阶段有无法保证模块强度的要加孔位。
最重要是保证送料顺畅。
保证送料和冲压不能出现弯曲。
工位2(3)计算材料利用率(4)冲压力计算工位11)冲裁力F=LKt材料抗剪切强度(MPa);K—系数。
一般取K=1.3。
2)卸料力3)顶件力工位1冲压力:等于上述力总和同理可算工位2冲压力:工位3冲压力:工位4冲压力:工位5冲压力:工位6冲压力:工位7冲压力:工位8冲压力:工位9冲压力:总冲压力等于上述力总和加上上述力总和30%=四、冲压设备选择根据总冲压力和由排样图推出模具大概尺寸确定采用250吨五、模具设计1.模具闭合高度根据250吨设备最大和最小装模高度是350到510确定模具高度且根据现有送料机送料高度在1000-1100 250吨工作台面高度在750左右为保证排样送料机送料高度在1000-1100范围,确定排样料带距工作台面的高度250-350的范围,选择为料带距工作台面的高度330,模具高,490,计模具料片距模具上面160,距模具下面330.2.模具结构的组成1)模具送料托举定位机构2)压料导正机构3)下模块组:包括下安装板、垫板、固定板、送料托举定位机构用的导套,模块材料及热处理下模块安装固定形式:所有模块都向安装板方向固定4)上模块组:包括上安装板、垫板、固定板、压料导正机构用的导套,模块材料及热处理模块及冲子固定形式:所有模块及冲子都向安装板方向固定冲子尽可能采用带台肩的形式,细小冲子采用快换结构。
模具设计方案

模具设计方案模具设计方案1. 引言在制造业中,模具设计是非常重要的环节之一。
模具是用于生产具有特定形状的工业产品的工具。
优质的模具设计能够提高生产效率、降低成本,并且保证产品的质量。
本文将介绍模具设计方案的基本流程和关键步骤。
2. 模具设计流程模具设计通常包括几个关键步骤,如下所示:2.1. 确定产品要求在开始模具设计之前,首先需要明确产品的要求。
这包括产品的形状、尺寸、材料等信息。
通过与客户或生产部门的沟通,确定清楚产品的需求。
2.2. 制定设计方案根据产品的要求,设计师需要制定一个合适的设计方案。
设计方案应考虑到模具的结构、材料、加工工艺等因素。
设计师需要综合考虑多个方面,以确保最佳的设计效果。
2.3. 3D建模和分析在设计方案制定完成后,设计师将进行3D建模和分析。
通过使用CAD软件,设计师可以将设计方案转化为三维模型,并进行各种分析,如强度分析、装配分析等。
这些分析能够帮助设计师发现潜在的问题并进行优化。
2.4. 制造模具当模具设计通过3D建模和分析验证后,设计师将开始制造模具。
这通常涉及到使用机床、数控机床等设备进行数控加工。
制造过程需要严格按照设计图纸进行操作,以确保模具的准确性和质量。
2.5. 模具调试和测试当模具制造完成后,需要进行调试和测试。
设计师和生产部门将一起合作,验证模具在实际生产中的效果。
调试和测试的目的是确保模具能够按照设计要求正常运行,并且生产出符合要求的产品。
2.6. 优化和改进根据模具的调试和测试结果,设计师将根据实际情况进行优化和改进。
这可能包括调整模具的结构、材料和加工工艺。
通过不断的优化和改进,模具的性能和效率可以进一步提高。
3. 模具设计的关键要素模具设计的成功与否,取决于以下几个关键要素:3.1. 结构设计良好的模具结构设计能够提高模具的使用寿命和稳定性。
设计师需要考虑到模具的强度、刚度、冷却性能等因素,并进行相应的分析和优化。
3.2. 材料选择模具的材料选择直接影响到模具的耐磨性、抗腐蚀性以及热传导性能。
模具设计方案
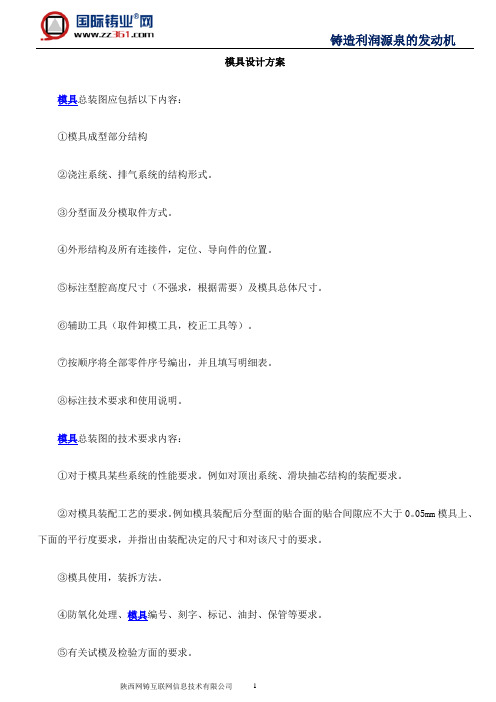
模具设计方案模具总装图应包括以下内容:①模具成型部分结构②浇注系统、排气系统的结构形式。
③分型面及分模取件方式。
④外形结构及所有连接件,定位、导向件的位置。
⑤标注型腔高度尺寸(不强求,根据需要)及模具总体尺寸。
⑥辅助工具(取件卸模工具,校正工具等)。
⑦按顺序将全部零件序号编出,并且填写明细表。
⑧标注技术要求和使用说明。
模具总装图的技术要求内容:①对于模具某些系统的性能要求。
例如对顶出系统、滑块抽芯结构的装配要求。
②对模具装配工艺的要求。
例如模具装配后分型面的贴合面的贴合间隙应不大于0。
05mm模具上、下面的平行度要求,并指出由装配决定的尺寸和对该尺寸的要求。
③模具使用,装拆方法。
④防氧化处理、模具编号、刻字、标记、油封、保管等要求。
⑤有关试模及检验方面的要求。
模具总装图拆画零件图的顺序应为:①图形要求:一定要按比例画,允许放大或缩小。
视图选择合理,投影正确,布置得当。
为了使加工专利号易看懂、便于装配,图形尽可能与总装图一致,图形要清晰。
②标注尺寸要求统一、集中、有序、完整。
标注尺寸的顺序为:先标主要零件尺寸和出模斜度,再标注配合尺寸,然后标注全部尺寸。
在非主要零件图上先标注配合尺寸,后标注全部尺寸。
③表面粗糙度。
把应用最多的一种粗糙度标于图纸右上角,如标注"其余3。
2。
"其它粗糙度符号在零件各表面分别标出。
④其它内容,例如零件名称、模具图号、材料牌号、热处理和硬度要求,表面处理、图形比例、自由尺寸的加工精度、技术说明等都要正确填写。
校对的内容:①模具及其零件与塑件图纸的关系,模具及模具零件的材质、硬度、尺寸精度,结构等是否符合塑件图纸的要求。
②塑料制件方面塑料料流的流动、缩孔、熔接痕、裂口,脱模斜度等是否影响塑料制件的使用性能、尺寸精度、表面质量等方面的要求。
图案设计有无不足,加工是否简单,成型材料的收缩率选用是否正确。
③成型设备方面注射量、注射压力、锁模力够不够,模具的安装、塑料制件的南芯、脱模有无问题,注射机的喷嘴与哓口套是否正确地接触。
青华模具分享一套经典的模具设计方案
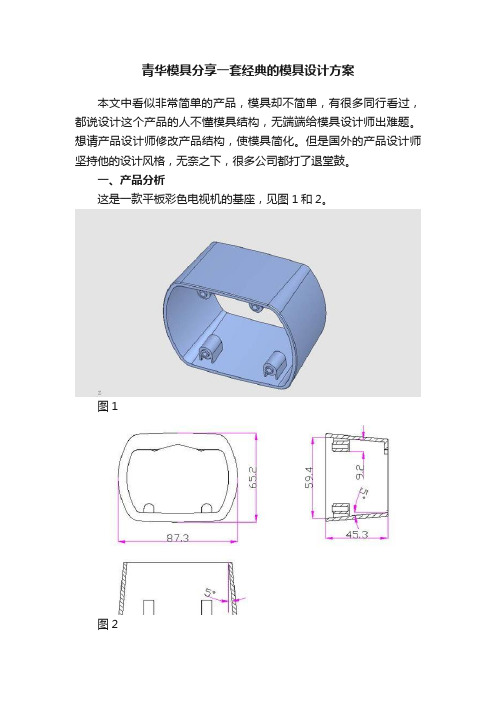
青华模具分享一套经典的模具设计方案本文中看似非常简单的产品,模具却不简单,有很多同行看过,都说设计这个产品的人不懂模具结构,无端端给模具设计师出难题。
想请产品设计师修改产品结构,使模具简化。
但是国外的产品设计师坚持他的设计风格,无奈之下,很多公司都打了退堂鼓。
一、产品分析这是一款平板彩色电视机的基座,见图1和2。
图1图2产品材质为PC,造型比较简洁,初看产品好像非常简单,其实不然,这套模具是非常地复杂,甚至有无从入手的感觉。
由于产品内测是有5°斜度的,横置内壁的4个螺丝柱阻碍了模芯的脱出,对于注塑模具来说,出模方法极为繁复。
由于外壳四周也均为5°的倒斜,4个螺丝柱的脱模受到严重的限制。
考虑到模具结构的复杂性,客户又要求一模二穴,所以,浇口形式的选择受到很多因素的限制。
我一拿到产品3D,基本可以肯定是要用前模内缩芯的结构,所以,点浇口和热流道的形式是被排除的。
经过Moldex 3D公司的模流分析,用潜伏式浇口的效果比较好,只有这种形式的浇口可以实现前模内缩芯结构的布置。
具体分析结果见图3。
图3二、模具结构的初步设想对于这类的产品,做“斜顶块”是最直接的想法,见图4。
图4从图4可以看到,由于4个螺丝柱的脱模是用推管来实现的,然而,从上图可以看到,斜顶块与推管是相互干涉的,假如在斜顶块上开一个缺口,避开推管,原理上是成立的,但是做成具体的零件并不合理。
因为斜顶块在脱模时要水平移动9.2mm,推管外侧的凸模将被开通。
另外,由于产品的下部沿周有一圈R0.5的圆角,所以斜顶块上必然有凹下0.5的造型,当斜顶块向上顶起时,一定会有一个向内的水平移动,但是这个凹下的0.5的部位当充满了塑料(PC)后就会阻挡斜顶块的的水平运动。
所以,用斜顶块的方案是行不通的,见图5。
图5第二个思路是做“内缩滑块”,见图6。
图6如图6所示,假如二个内缩滑块向中间移动,给4个螺丝柱让出位置,产品就可以正常脱模,但是这个方案也将面对二个问题,第一是产生二个内缩滑块的斜铲块必须布置在定模一边,假如放在动模一边将无法安排动模芯的冷却水路。
模具结构设计方案

模具结构设计方案模具是生产制造工具、零件的重要设备,其结构设计方案直接关系到产品的质量和生产效率。
下面给出一个模具结构设计方案的简要描述,共700字。
该模具结构设计方案针对一种塑料零件的生产制造。
根据该零件的形状和尺寸要求,以及生产批量的要求,设计了一个适用的模具结构。
首先,该模具结构设计方案采用了三板式开模结构,即上模板、移动模板和下模板。
上模板由模具的顶部组成,用于支撑和固定塑料零件。
移动模板是模具的核心部分,通过传动装置可以在模具壳体内移动,用于塑料的注塑成型和脱模。
下模板用于支撑和固定整个模具结构,以及固定底部的冷却系统。
其次,该模具结构设计方案将模具壳体采用了整体式结构,以保证模具的稳定性和刚性。
模具壳体采用优质的合金钢材料制作,经过多道工艺处理,以提高模具的耐用性和使用寿命。
模具壳体内部采用了优化设计的冷却系统,以快速冷却塑料材料,并保证零件的尺寸稳定性。
此外,该模具结构设计方案还采用了特殊的辅助装置,以提高模具的操作性和生产效率。
其中,一种辅助装置是自动脱模装置,通过气动或液压装置,可以实现零件的自动脱模,提高生产速度和减少工人劳动强度。
另一种辅助装置是自动喷油装置,通过喷油系统可以在每次注塑成型前对模具进行喷油,以减少零件的粘模现象,保证零件的质量。
最后,该模具结构设计方案还考虑了模具的维护和保养问题。
模具的维护和保养对于模具的使用寿命和生产效率至关重要。
因此,在模具的设计中考虑了易于拆卸和更换的零部件,并设置了清洗和保养的通道。
同时,也对模具的使用要求进行了培训,以保证模具的正常使用。
综上所述,该模具结构设计方案采用了三板式开模结构,整体式模具壳体,优化的冷却系统,辅助装置以及易于维护和保养的设计。
这个设计方案有效地满足了该塑料零件的生产要求,提高了生产效率,保证了产品质量,具有广泛的应用前景。
模具实施方案

模具实施方案一、背景介绍模具是制造工业中常用的一种生产工具,它的质量和性能直接影响着产品的成型质量和生产效率。
因此,制定一套科学的模具实施方案对于企业的生产至关重要。
二、目标和意义1. 目标:建立高效、稳定的模具实施方案,提高产品的质量和生产效率。
2. 意义:通过实施科学的模具方案,降低生产成本,提高产品的市场竞争力,实现企业的可持续发展。
三、实施步骤1. 模具选型:根据产品的特点和要求,选择适合的模具类型,包括材料、结构、尺寸等。
2. 模具设计:由专业的设计师进行模具的结构设计和工艺设计,确保模具的精度和稳定性。
3. 模具制造:选择有资质和经验的模具制造厂家进行生产,确保模具的质量和交货周期。
4. 模具调试:在生产线上进行模具的调试和优化,确保模具的稳定性和适应性。
5. 模具保养:建立健全的模具保养制度,定期对模具进行检查、清洁和维护,延长模具的使用寿命。
四、关键问题和解决方案1. 模具选型:根据产品的特点和要求,进行全面的市场调研和技术评估,选择性能优良、价格合理的模具。
2. 模具设计:引入先进的设计软件和技术,提高设计效率和精度,确保模具的合理性和可制造性。
3. 模具制造:建立健全的供应商管理体系,选择优质的材料和零部件,严格控制生产过程,确保模具的质量和交货周期。
4. 模具调试:配备专业的技术人员和先进的检测设备,快速定位和解决模具调试中的问题,确保生产的顺利进行。
5. 模具保养:建立健全的模具管理制度,培训员工掌握模具保养的技能,延长模具的使用寿命,降低生产成本。
五、实施效果评估1. 生产效率:通过模具实施方案的优化,提高生产效率,降低生产成本,提高产品的市场竞争力。
2. 产品质量:优化模具方案可以提高产品的成型精度和表面质量,提高产品的合格率和一致性。
3. 资源利用:科学的模具实施方案可以减少资源的浪费和损耗,提高企业的资源利用效率。
六、总结通过科学的模具实施方案,可以提高产品的质量和生产效率,降低生产成本,提高企业的市场竞争力。
模具设计方案

模具设计方案一、介绍模具是工业生产中常用的工具,用于制造复杂的零部件和产品。
好的模具设计方案可以提高产品质量和生产效率,因此在工业制造中具有重要的地位。
本文将探讨模具设计的几个关键方面,包括材料选择、结构设计和制造工艺等。
二、材料选择模具材料的选择对于模具设计至关重要。
一般而言,模具材料应具备高强度、抗磨损、抗腐蚀和耐高温等特性。
常用的模具材料包括工具钢、硬质合金和高速钢等。
在选择模具材料时,需要考虑到生产工艺、使用环境和成本等因素。
三、结构设计模具的结构设计直接影响产品的质量和生产效率。
合理的结构设计可以提高模具的使用寿命和加工精度。
例如,在注塑模具设计中,需要考虑产品的收缩率,并合理设计模具的尺寸。
此外,对于大型模具而言,还需要考虑模具的拆卸、组装和运输等因素。
四、制造工艺制造工艺是模具设计过程中不可忽视的一环。
精密的模具制造需要采用先进的加工设备和工艺。
常见的加工工艺包括数控加工、电火花加工和线切割等。
此外,还需要进行表面处理,以提高模具的耐磨性和抗腐蚀性。
一般而言,模具的制造过程需要经过修模、组装、调试和试模等多个阶段。
五、模具设计的创新随着科学技术的进步和工业生产的需求变化,模具设计也需要不断创新。
现代模具设计已经开始引入计算机辅助设计和仿真技术,以提高设计效率和预测模具性能。
例如,通过有限元分析可以评估模具的强度和刚度,并优化设计方案。
此外,三维打印技术的应用也为模具设计提供了新的思路,可以实现复杂结构的制造。
六、模具设计的案例以下是一个汽车零部件模具设计的案例,以说明模具设计的具体过程。
假设需要设计一个汽车车灯的注塑模具。
首先,根据产品要求和材料特性,选择适合的模具材料。
然后,根据产品的形状和尺寸,设计模具的结构,包括模仁、模座和定位系统等。
接下来,确定制造工艺,选择合适的加工设备和工艺,进行模具的加工和组装。
最后,进行模具的调试和试模,检验产品的质量和精度。
结论模具设计是一个综合性的工程,需要考虑材料选择、结构设计和制造工艺等多个因素。
较佳模具结构设计范例word文档

目的:1. 提供設計人員參考2. 提供新進人員認識結構及設計內容:1.入子(植入式成型)須由手工組裝至模具中的定位機構2.模仁入子須先抽退或公模側有內縮SIide機構3.雙色模控制第二色GATE4.二段頂出順序機構5.模內剪膠機構6.同SLIDE不同距離,方向的設計機構(成品側邊有倒勾)7.同方向,HOOK PIN與HooK PlN間距離小,作動空間小機構8.母模側HOOK PIN機構1:此機構適用於入子須由手工組裝至模具中的定位機構2:資料來源:0305133:作動方式:為將入子置入模具內經由氣壓缸作動使入子固定模具中(如第二頁所示)可裝卸入子,組裝前避免作動延遲1:此機構適用於模仁入子須先抽退或公模側有內縮Slide 時2:資料來源:0305133:作動方式:為頂出桿作用於頂出板上一頂出板往上移使得公模仁同時作動而往 上移,在移動一段距離後BLOCK 會脫離橘色BLOCK 約束而偏轉一角度此時公模板 因無往前移之動力而停留原處只剩頂岀板作頂出動作*RP 沈頭孔深度 / \須正確不可加深1:此機構適用於雙色模控制第二色GATE 2:資料來源:0209203:作動方式:合模時一色母模PL面會將綠色頂針往下壓而造成BLOCK旋轉使紅色頂針往上而造成二色GATE閉鎖二色GATE 閉鎖□UBLOCK3:作動方式:開模時因無壓迫力量利用彈簧的力量將頂針往上頂而造成BLOCK 旋轉將紅色頂針往下帶Q運動方向旋轉軸1:二段頂出順序機構2:資料來源:02092OMT3:作動方式:下頂出板往上頂出亦同時帶動上頂出板作動(BLOCK頂住SLlDE BLOCK)→頂出至SLlDE BLOCK與GUlDE PlX碰觸後SLlDE CLOCK會往運動方向移動(GUIDE PlN與SLIDE BLOCK的孔不同中心)SLIDE BLOCK當GUlDE PIN與SLlDE BLOCK同中心時則下頂出板可單獨作頂出動作(如圖示(BLOCK 與SLIDE BLOCK 無干涉)*GUIDE PIN偏心距離需大於BLOCK與SLIDE BLOCK 的干涉距離(如左圖所示)1:模內剪膠機構2:作動方式:保壓結束後(合模狀態)做頂岀動作(1:需配合射出機台2:只有下頂出板作動)*RP 需置於上頂出板上,VrT--Iη5IL J8."E≡≡L LLSJ-T・ I ∙√頂出距離剪切距離Or・/HH N N H P √----1-- -----I丄VJL此機構適用於同SLlDE不同距離,方向的設計2.資料來源:030506MT&030808MT3.此種設計的重點在於,小空間裡有幾個不同方向滑動,且其退出的行程也不相同.4.注意事項:1 •帶動件與倒勾件角度設計上,(因線割無法加工大於10°以上),所以角度設計上,以10°以內設計為準.帶動件倒勾件帶動件相同設計的結合,在030506MT的設計時如左圖所示,在030808MT時作些許修, 正,如圖右所示,如此修正,帶動件強度較佳.1.此機構適用於同方向,HOOK PlN與HoOK PlN間距離小,作動空間小.2.資料來源:030308MT3.作動方式:BLOCK與上頂出板固定,HOOK PlN滑動於BLOCK上,形成頂岀動作其作動狀態如圖B所示.圖A 上頂出板BLOCK1.此機構用在母模側HooK PlN2.資料來源:03018OMT3.作動方式:當公母模板作動時,彈簧跳開,帶動HooK PIN退開行程,完成動作.母模板'作動方向。
模具立体造型设计方案
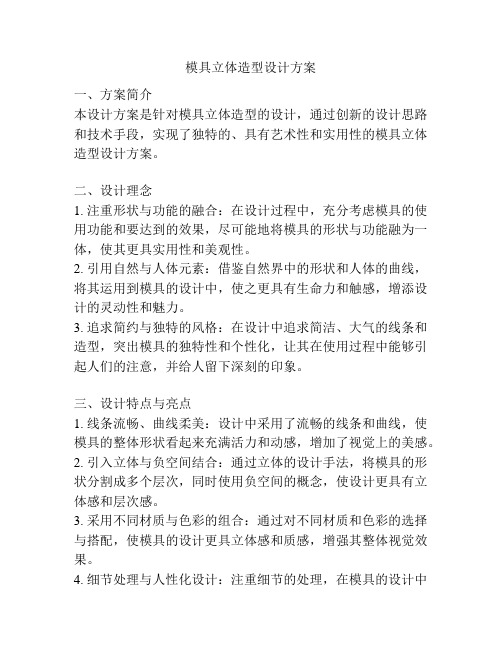
模具立体造型设计方案一、方案简介本设计方案是针对模具立体造型的设计,通过创新的设计思路和技术手段,实现了独特的、具有艺术性和实用性的模具立体造型设计方案。
二、设计理念1. 注重形状与功能的融合:在设计过程中,充分考虑模具的使用功能和要达到的效果,尽可能地将模具的形状与功能融为一体,使其更具实用性和美观性。
2. 引用自然与人体元素:借鉴自然界中的形状和人体的曲线,将其运用到模具的设计中,使之更具有生命力和触感,增添设计的灵动性和魅力。
3. 追求简约与独特的风格:在设计中追求简洁、大气的线条和造型,突出模具的独特性和个性化,让其在使用过程中能够引起人们的注意,并给人留下深刻的印象。
三、设计特点与亮点1. 线条流畅、曲线柔美:设计中采用了流畅的线条和曲线,使模具的整体形状看起来充满活力和动感,增加了视觉上的美感。
2. 引入立体与负空间结合:通过立体的设计手法,将模具的形状分割成多个层次,同时使用负空间的概念,使设计更具有立体感和层次感。
3. 采用不同材质与色彩的组合:通过对不同材质和色彩的选择与搭配,使模具的设计更具立体感和质感,增强其整体视觉效果。
4. 细节处理与人性化设计:注重细节的处理,在模具的设计中考虑到用户的使用需求和体验感,使其更符合人体工程学原理,提供更便捷、舒适的使用体验。
四、设计应用领域本方案的模具立体造型设计适用于各种工业和民用领域,如汽车制造、家居用品、日用品等。
具体应用于模具生产与使用中,可以提高产品质量、提升品牌形象和用户满意度。
五、总结通过对模具立体造型设计方案的独特理念和创新性的设计思考,可以实现模具在形状、结构、色彩等方面的立体化,为产品的研发和生产提供更多可能性,以满足不同行业领域的需求,并为模具设计带来全新的发展机遇。
模具方案格式

模具方案格式引言模具是工业生产中不可或缺的一部分,而模具技术也在不断发展。
模具方案是指根据工件的特性和客户需求,选择合适的加工工艺和设计模具的过程。
制定一个科学、规范的模具方案能够有效提高生产效率和产品质量,减少生产成本。
模具方案格式好的模具方案需要包含以下方面的内容(以文本形式呈现):1.工件零件图纸及技术要求在一份完整的模具方案中,首先应该包含工件的零件图纸和技术要求。
工件的图纸应该包括外观尺寸、基准尺寸等信息,技术要求应该包括加工工艺、精度要求等。
2.模具结构图模具结构图应该详细描述模具的结构和组成部件。
包括上模、下模、侧板、压痕板、精修模等部件。
3.模具设计图和技术要求模具设计图应该详细描述模具的设计,包括模具的加工准备、制作过程、零件拼装等。
在设计阶段,还应该确定模具的技术要求,包括材料、热处理要求等。
4.加工工艺卡加工工艺卡是对整个模具制作过程进行规范管理的重要工具。
加工工艺卡应该按照制作工艺流程,明确每个环节的加工工序、设备要求和质量控制要求。
5.模具零件检验记录在模具制作的各个环节,需要对零件进行严格的检验和测试,保证零件质量符合要求。
模具零件检验记录需要详细记录每个零件的检验过程、结果和结论。
6.模具整体检验记录模具整体检验需要对制作完成后的模具进行全面的检测。
记录每个零部件的加工精度和装配精度,检验结果要符合技术要求。
结论模具方案的制定对于保证模具的质量和生产效率有着重要的作用。
一个好的模具方案不仅需要各个方面的要求都得到满足,而且还需要注重每个细节,保证每个零件的质量都得到保证,从而保证最终的产品质量。
模具开发模具设计方案

模具开发模具设计方案
模具开发是指根据产品的加工工艺要求和设计要求,利用CAD、CAM等软件工具对模具进行全面、系统的设计。
模具开发的设计方案应包括以下几个方面:
1.产品分析:对产品进行全面的分析,了解产品的形状、尺寸、材料等特性,并根据产品的用途和需求确定模具的设计要求。
2.模具结构设计:根据产品分析的结果,确定模具的结构形式
和工作原理。
模具的结构包括上模、下模、导柱、导套、顶杆、顶针、卡板、模板等,需要确定每个零件的形状、尺寸和材料。
3.零件设计:对模具各个零件进行细节设计,包括上模、下模、导柱、导套、顶杆、顶针、卡板、模板等各个零部件。
在设计过程中需要考虑到零件的材料、加工工艺和装配方式。
4.模具工艺设计:确定模具的制造工艺,包括模具的加工方法、装配顺序、加工精度等。
在设计过程中需要考虑到模具的制造成本、生产周期和制造工艺的可行性。
5.模具试制方案:制定模具试制方案,包括模具的试制计划、
试制流程、试制工艺和试制设备等。
在试制过程中需要对模具进行试模和试产,检验模具的加工精度、装配性能和产品质量。
6.模具改进方案:根据模具试制过程中的问题和产品生产中的
需求,提出模具改进方案。
模具的改进包括结构改进、材料改
进、加工工艺改进等,旨在提高模具的加工精度、生产效率和产品质量。
总之,模具开发的设计方案需要综合考虑产品的加工工艺要求和设计要求,确定模具的结构形式、零件设计、工艺设计、试制方案和改进方案。
通过合理的设计方案,可以提高模具的加工精度、生产效率和产品质量,从而有利于产品的生产和发展。
模具设计优化思路与方法总结
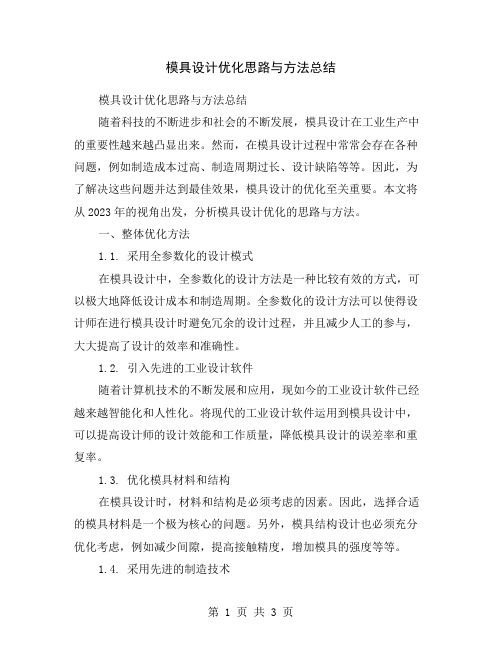
模具设计优化思路与方法总结模具设计优化思路与方法总结随着科技的不断进步和社会的不断发展,模具设计在工业生产中的重要性越来越凸显出来。
然而,在模具设计过程中常常会存在各种问题,例如制造成本过高、制造周期过长、设计缺陷等等。
因此,为了解决这些问题并达到最佳效果,模具设计的优化至关重要。
本文将从2023年的视角出发,分析模具设计优化的思路与方法。
一、整体优化方法1.1. 采用全参数化的设计模式在模具设计中,全参数化的设计方法是一种比较有效的方式,可以极大地降低设计成本和制造周期。
全参数化的设计方法可以使得设计师在进行模具设计时避免冗余的设计过程,并且减少人工的参与,大大提高了设计的效率和准确性。
1.2. 引入先进的工业设计软件随着计算机技术的不断发展和应用,现如今的工业设计软件已经越来越智能化和人性化。
将现代的工业设计软件运用到模具设计中,可以提高设计师的设计效能和工作质量,降低模具设计的误差率和重复率。
1.3. 优化模具材料和结构在模具设计时,材料和结构是必须考虑的因素。
因此,选择合适的模具材料是一个极为核心的问题。
另外,模具结构设计也必须充分优化考虑,例如减少间隙,提高接触精度,增加模具的强度等等。
1.4. 采用先进的制造技术制造技术也是模具设计优化的一个重要环节。
通过采用先进的制造技术,例如数控加工、电火花加工等,可以提高模具的生产效率和质量。
此外,规范和完善制造流程,也是提高制造效益和降低制造成本的有效措施。
二、细节优化方法2.1. 优化材料的选择材料的选择对于模具设计的效果和质量有着至关重要的影响。
一方面,合理选择材料,可以大大提高模具的使用寿命和精度;另一方面,不合理的材料选择则会导致模具质量变差、使用寿命缩短等不良后果。
因此,在模具设计中需要根据具体的制造要求和使用环境,选择合适材料,尽可能地实现材料的最佳匹配。
2.2. 优化产品的合理性在进行模具设计时,产品的合理性与制造效率和制造成本息息相关。
模具工程规划方案

模具工程规划方案一、绪论模具是制造行业中的重要工具,它直接影响着产品的设计和生产周期。
现代工业中,模具的制作技术和质量要求越来越高,因此模具工程规划至关重要。
通过对模具工程的规划,可以有效提高模具制造效率,降低成本,提高产品质量,实现生产数字化、智能化。
本文将针对模具工程规划方案进行详细的分析和阐述。
二、模具工程规划的目标和意义1. 目标(1)提高模具制造效率通过规划和优化制造流程,提高模具的制造效率和产能,缩短制造周期。
(2)降低成本通过优化资源配置,提高生产效率,降低模具制造成本。
(3)提高产品质量通过完善的生产过程和质量控制,提高产品质量,减少次品率。
(4)实现数字化、智能化生产引入先进的制造技术和智能设备,实现模具制造的数字化、智能化。
2. 意义模具工程规划的意义在于提高模具制造效率,降低成本,提高产品质量,实现生产数字化、智能化。
这不仅对企业生产效率和产品质量有重要意义,也对整个产业的发展具有重要的推动作用。
三、模具工程规划的内容和方法1. 规划内容(1)制定模具制造流程根据产品特性和工艺要求,制定模具制造的详细流程和计划。
(2)资源配置和技术引进根据生产需求,配置生产设备和人员,并引进先进的制造技术和设备。
(3)制定质量控制计划确定合理有效的质量控制标准和检测手段,保证产品质量。
(4)实施数字化、智能化生产引入数字化制造和智能制造技术,实现模具制造的数字化、智能化。
2. 规划方法(1)调研分析对企业现有的模具制造情况进行调研和分析,找出存在的问题和瓶颈。
(2)制定规划方案根据调研结果,制定模具工程规划方案,明确制造流程、资源配置、质量控制计划和数字化、智能化生产方案。
(3)实施和监控根据规划方案,逐步实施,并定期进行监控和评估,及时调整和优化。
四、模具工程规划的实施步骤1. 调研分析(1)对企业现有的模具制造情况进行调研和分析,明确问题和瓶颈。
(2)分析市场需求和竞争情况,制定发展战略。
最佳冲压模具设计
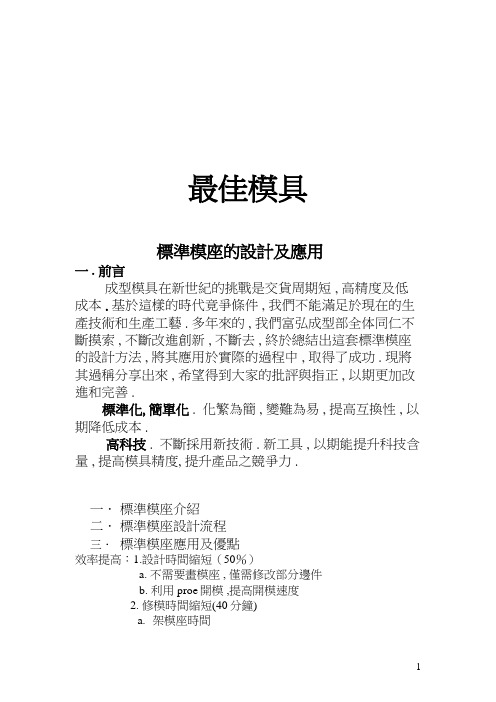
最佳模具標準模座的設計及應用一 . 前言成型模具在新世紀的挑戰是交貨周期短 , 高精度及低成本 . 基於這樣的時代竟爭條件 , 我們不能滿足於現在的生產技術和生產工藝 . 多年來的 , 我們富弘成型部全体同仁不斷摸索 , 不斷改進創新 , 不斷去 , 終於總結出這套標準模座的設計方法 , 將其應用於實際的過程中 , 取得了成功 . 現將其過稱分享出來 , 希望得到大家的批評與指正 , 以期更加改進和完善 .標準化, 簡單化. 化繁為簡 , 變難為易 , 提高互換性 , 以期降低成本 .高科技 . 不斷採用新技術 . 新工具 , 以期能提升科技含量 , 提高模具精度, 提升產品之競爭力 .一.標準模座介紹二.標準模座設計流程三.標準模座應用及優點效率提高:1.設計時間縮短(50%)a. 不需要畫模座 , 僅需修改部分邊件b. 利用 proe開模 ,提高開模速度2. 修模時間縮短(40分鐘)a.架模座時間b.插頂針時間3.簡單化 , 提高效率a.教學簡單 , 新人易上手b.減少出錯率成本降低:1.節省模座費用, 節省模座存放空間 , 便於模具管理2.大量採用標準件 ,提高互換性 , 節省成本3.合理布置多模穴生產4.減小料頭大小提高精度方面:1.利用PROE拆模不易出錯2.E01.E02較小 , 減輕重量 , 減小變形標準模座結構的豐富1.斜滑塊裝置2.簡易二次頂出裝置3.自動吹氣裝置一.模座介紹該標準模座分為兩部份: 模座部份和block部份.其中block部份自成一體 , 可以抽出 . 通過楔塊定位在模座上 , 用螺絲鎖緊 . 又相當於一個小的模具 , 自有頂針板 . 回位銷 . 輔助柱 . 定位銷等 . 我們的模具設計只需完成black里面空腔的部份 . 每個空腔大小為:小標準模座25*90mm , 大標準模座22.5*160mm ,這樣尺寸可以把我們絕大多數產品包容在內 .block公模座母模座block 公模 block母模autocad 裝配圖二. 標准模座設計流程1.拿到制工的產品圖面進行design review,進行模流分析2.在 proe 中開出一穴模仁 . 該穴大小由它在block所空間決定3.將整穴模仁和單個模仁分別轉到autocad4.將整穴模仁圖貼到標準模座的layout圖上,補出分流道5.將每個模仁插入圖框, 稍作修改(如靠肩插破面等)6.將layout圖上的頂針孔位置copy到M05A(公模底板)E02A(上頂板) 修改頂針孔大小,7.最后將它們全部標上尺寸即可. (見下面范例)產品圖一穴公母模仁模仁proe圖轉到autocad檔填進layout圖 , 補出流道標注尺寸三.標準模座應用及優點(一)效率提高:1.設計時間的縮短A . 不需要畫模座 , 邊件部分只需要部分修改 .以前模具設計時 ,模座及邊件的圖紙量有 26張 ,一般需要2~3天 . 現在2到3個小時就可以完成 .B . 利用 proe開模 , 提高開模速度(1) . 以前用atuocad設計模仁時 , 需將產品計算縮水率 ,重新繪制產品放大圖 , 現在利用PROE來開模 , 在計算縮水率時 ,只需輸入三個方向的縮水率比例 , 並不需要重要重新繪制 .(2) . atuocad設計模仁時 , 需要有很深厚的視圖能力和空間想象能力 , PROE是三D視圖 , 容易理解模具的具體結構 ,能迅速而准確的找出分模面的位置(3) . atuocad設計模仁時 , 利用剖面視圖一條一條線的反向補出模仁圖 , 因為PROE是將一個體積塊中挖去產品 , 然后利用分模面將其公母模分開 , 所以不存在模仁結構上的缺一或多一塊 , 不會帶來人為的計算錯誤 , 提高其精度 .總體來說 : 以前我們一套模需要設計5到8天 , 現在2到4天就能完成 , 可以節省50%的時間 .3 . 降低修模時間A.減少架模座時間以前的模具在機台上生產公模發現問題 , 因為結構問題必需將公模座吊下來 . 修完后再重新吊上去 . 這樣至少需要30分鍾時間 , 而現在只須要用撬杆將楔塊打出 , 即可取出block部分 , 下模與上模僅需約10分鍾時間 . 這樣由於減少架模時間 , 即可減少修模時間約20分鐘 .切換不同模具時 ,也不需要架模座 ,更換block就可以 . 可節省換公母模座時間約 30分鐘從機台上直接將block取出B. 減少插頂針時間以前模具插頂出須將公模底板打開 , 預裝公模block , 然后再插頂針 , 因模座較大 , 增加了插頂針的難度 , 費時又費力 , 而現在block較小 , 插頂針比較容易 , 這樣易可節省時間約20分鍾 .以前的插頂針方法現在在block上直接插頂針(二) 標准化 , 簡單化教學簡單 , 新人易上手.在教學上 , 每一塊模板 , 每一個件號都固定下來 , 使得我們的以后在稱呼上形成統一 . 能與成型自己編定的《塑模圖面規範》 .《模具設計基礎》.《PROE開模流程》等教材相統一 , 形成一整套培訓體系 , 使得新人能在最短的時間內上手 , 目前生產模修人員在開發實習中,已有3名同仁在2個多月的時間內上手,並開發出新模 .模座部分容易出錯 , 以標準的形式固定下來 , 可以集中精力在模仁拆分方式上的精進 , 從面提高品質 , 提升效率 .(三)降低成本1.節省模座費用a .模座能共用 , 那麼只需有安全模座存量 , 不同模具在上面切換block就行了, 而不像以前每套模具有專用模座 , 光發包模座就得十幾二十幾萬台幣 .b .節省模座存放空間 , 便於模具管理 .非標準模座所佔空間大標準block所佔空間小2.標準邊件互換性模具可以共用 , 不需要新發包 , 那麼邊件呢 ? 我們的邊件也是標准化了的 , 一次發包多套 ,不僅降低生產成本 , 而且以后有新模時 , 直接拿來使用 , 縮短鴻准的加工周期 , 如果萬一有損壞的 , 易可作備品更換使用 .(四) 提高精度1.利用PROE不易出錯2.頂出改善a .以前因為頂針板和頂針墊板較大 , 對輔助的壓力很大,經過一段時間後 , 輕則頂針彎曲變短 , 造成產品外觀不良 . 重則回位銷卡死 , 而造成不能頂出 , 或者頂針頂短 .現在頂針板和頂針墊板減小 , 減輕了重量 , 減小巒形 ,很少再出現以上現象.b. 在大的標準模座上增加輔助柱 , 增加頂出平衡度(五) 標準模座結構的豐富1. 斜滑塊裝置該模于標準模座的區別是邊件不同,共用挖掉導滑槽後的標準模座.2. 簡易二次頂出裝置:如有一些如下面左圖陰影塑膠所示的產品結構 . 不能直接頂出 . 可以用下年面右圖所示模具結構 . 其原理是 : 當頂杆推動頂板前進時 , 件E05A靠彈簧E06A彈力與頂杆一起前進 , 將產品整個平衡頂出一部份 . 當件E05A頭部凸沿與底板M05A接觸后 , 件E05A不能前 , 壓縮彈簧E06A , 而頂針繼續前進 , 產品一側受力, 傾斜落下 .3. 自動吹氣裝置當合模時 , 件1抵住件2 , 壓縮彈簧件3 , 出氣孔B與進氣口A不通 ,開模后 , 彈簧彈力推動件2向上 , 氣孔通氣 , 經導向管向產品部位吹氣裝有吹氣裝置的標準模座總結:標準模座的應用雖然較之前提高了效率 , 節省了成本, 但我們不能就此止步 . 社會在發展 , 科學在進步 , 技術在更新 , 我們的模具 , 我們的技術也需要不斷的改進和完善 , 今後我們將沿著標準化 , 高科技的方向 , 謙虛好學 , 勇於創新 , 繼續前進 .。
模具设计方案

模具设计方案第1篇模具设计方案一、项目背景随着我国制造业的快速发展,模具行业在国民经济中的地位日益突出。
作为生产各种工业产品的基础工艺装备,模具在汽车、电子、家电、通讯等众多领域具有广泛应用。
为满足市场需求,提高产品质量,降低生产成本,本项目旨在设计一套合法合规的模具设计方案。
二、设计目标1. 满足产品功能需求,确保产品质量;2. 提高生产效率,降低生产成本;3. 合法合规,确保生产安全;4. 节能环保,降低资源消耗。
三、设计方案1. 产品分析与定位根据客户需求,对产品进行详细分析,明确产品结构、功能、尺寸等参数。
结合市场需求,对产品进行定位,确保设计方案符合产品发展方向。
2. 模具结构设计(1)根据产品结构特点,选择合适的模具类型;(2)采用模块化设计,提高模具的通用性和可维护性;(3)合理布局模具的冷却系统,确保产品成型过程中的温度控制;(4)优化模具的导向和定位系统,提高模具的运动精度。
3. 模具材料选择根据产品性能要求,选择具有良好机械性能、耐磨性和抗腐蚀性的模具材料。
同时,考虑材料成本和加工工艺,确保模具的经济性。
4. 模具制造与加工(1)采用先进的加工工艺,确保模具的制造精度;(2)加强模具加工过程中的质量检测,确保模具质量;(3)合理规划模具加工流程,提高生产效率。
5. 模具试模与优化(1)组织模具试模,验证模具结构、材料及工艺的合理性;(2)根据试模结果,对模具进行优化调整,确保产品质量;(3)跟踪模具生产过程,及时解决生产中出现的问题。
6. 模具验收与交付(1)按照相关法律法规,组织模具验收,确保模具符合国家标准;(2)提供完整的模具技术资料,包括模具结构图、模具零件清单等;(3)对客户进行模具操作和维护培训,确保客户正常使用模具。
四、质量保证与售后服务1. 质量保证(1)严格执行国家及行业标准,确保模具质量;(2)加强过程控制,对模具制造各环节进行质量把关;(3)提供模具质量保证书,承诺质量保证期限。
锻造模具造型设计方案

锻造模具造型设计方案设计方案一:设计理念:简洁、现代化1. 模具外形设计:采用流线型设计,外形光滑、简洁,呈现现代感。
2. 材质选择:选用高强度铝合金作为模具材质,既保证了模具强度,又减轻了模具自重。
3. 部件结构设计:通过分析模具的使用情况,采用可拆卸的模具结构设计,方便模具的维护和更换。
4. 贴合度优化:通过CAD技术对模具内外表面进行精确设计,确保模具各部件之间的贴合度,从而提高模具制造效率。
5. 细节设计:在模具的易损部位加入抗磨擦材料,延长模具寿命;同时,在模具表面进行喷砂处理,增加模具的使用稳定性。
6. 安全措施:在模具设计过程中,考虑到操作人员的安全,添加防护措施,如防滑手柄和自动关断装置,确保操作的安全性。
7. 技术创新:引入先进的热传导技术,提高模具制造过程中的加热效率,提高生产效率。
设计方案二:设计理念:经典、实用性强1. 模具外形设计:以整体稳定为设计理念,采用四方形结构,增加了模具的稳定性和刚性。
2. 材质选择:根据模具使用环境和使用寿命要求,选择耐磨、耐腐蚀、高强度的钢材作为模具材料。
3. 结构创新:通过应用仿生工程学原理,设计模具外形结构,提高了模具的抗压能力和抗疲劳能力。
4. 模具表面处理:采用高精度数控加工技术对模具表面进行精细处理,提高模具的平整度和表面质量。
5. 节能环保:在模具制造过程中,注重减少能量消耗,避免使用有害物质,保护环境。
6. 操作便捷性:通过模具内部结构的优化设计,确保模具的装拆过程简单方便,提高操作的便捷性。
7. 模具标识:在模具设计过程中,考虑到模具的管理和使用方便,添加模具标识,便于模具识别和跟踪。
设计方案三:设计理念:个性化、艺术性1. 模具外形设计:采用独特的造型设计,将模具打造成艺术品,增加模具的审美价值。
2. 材质选择:根据模具的艺术风格,选择质感好、色彩丰富的材料,如有机玻璃、陶瓷等,增加模具的观赏性。
3. 艺术元素融入:在模具的设计中融入艺术元素,如雕刻、图案等,增加模具的个性化和独特性。
- 1、下载文档前请自行甄别文档内容的完整性,平台不提供额外的编辑、内容补充、找答案等附加服务。
- 2、"仅部分预览"的文档,不可在线预览部分如存在完整性等问题,可反馈申请退款(可完整预览的文档不适用该条件!)。
- 3、如文档侵犯您的权益,请联系客服反馈,我们会尽快为您处理(人工客服工作时间:9:00-18:30)。
2
© 2003 PTC
1 模具廠目前瓶頸 2 PTC解決方案藍圖 3 Case Study 1 : 最佳化模具設計方法 4 Case Study 2 : 模具廠無紙化方案 5 Case Study 3 : 設計導引系統介紹 ( 產品設計/ 模具設計) 6 Q&A
3
© 2003 PTC
模具廠目前瓶頸
最佳化模具設計方案
(PTC客戶導入經驗介紹)
Prepare By Anderson Tsai
Agenda
1 模具廠目前瓶頸 2 PTC解決方案藍圖 3 Case Study 1 : 最佳化模具設計方法 4 Case Study 2 : 模具廠無紙化方案 5 Case Study 3 : 設計導引系統介紹 ( 產品設計/ 模具設計) 6 Q&A
EMX is a problem for Implementation
❖The real expectation should be “331” ➢3 people to finish one project in 3 days !
❖EMX is one of the tools only ❖Methodology & Process are the critical successful factor
➢It can not to be part of the scope
11
© 2003 PTC
Implement Items for “331”
1. Construct the environment (Foundation) 2. Improve the Moldesign Skill 3. Implement Team work methodology (Integration) 4. Construct the library (Using Pro/E or EMX)
❖ XX has been using Pro/E more than 5 years , they are looking for quality & cycle time improvement
➢Long cycle time can not compete with the process of other moldshops ❖ XX decide to seek for PTC’s help to shorten design cycle time ➢The project initiated from Jun 2003. (China) ➢Whole team move back to Taiwan, then start project again ➢ Issue in initiated stage :
❖ 2D圖面花費太多時間
➢現場人員要求圖面尺寸需詳細標註,造成設計工程師需花費大量時間在2D圖面上
❖ 設計流程如何改善
➢改善設計流程,以提昇效率
4
© 2003 PTC
1 模具廠目前瓶頸 2 PTC解決方案藍圖 3 Case Study 1 : 最佳化模具設計方法 4 Case Study 2 : 模具廠無紙化方案 5 Case Study 3 : 設計導引系統介紹 ( 產品設計/ 模具設計) 6 Q&A
❖ 人員流動頻繁 , 花費太多教育訓練時間
➢人員流動頻繁對公司是一項重大的負擔,如何有效管理,應是模具廠重要的目標之一
❖ 設計經驗難以傳承
➢如何將設計經驗傳承,並建立Know-How資料庫,為RD部門重大,提昇能力以縮短設計時間 ?
❖ 溝通時間太多
➢由於圖面有時標示不清,設計工程師需要經常應付現場人員的溝通需求
9
© 2003 PTC
Bottleneck & Pain
❖ Old Process – Sequential process
1~2 day
Fix Model (1per.)
3 day
Moldesign (1per.)
2 day
Moldbase(1per.)
❖One project is almost 8 days
5
© 2003 PTC
PTC解決方案藍圖
Pro/E 基本訓練
Pro/E模仁設計 Pro/E基礎建設
模座設計
模具設計 3D化
Pro/E 2D
Pro/E設計基礎階段
提昇品質階段
6
人員等級分工
設計分工
Intralink 資料庫
引導系統
無紙化
流程改善階段
標準化階段
© 2003 PTC
1 模具廠目前瓶頸 2 PTC解決方案藍圖 3 Case Study 1 : 最佳化模具設計方法 4 Case Study 2 : 模具廠無紙化方案 5 Case Study 3 : 設計導引系統介紹 ( 產品設計/ 模具設計) 6 Q&A
7
© 2003 PTC
XX公司 Moldesign Solution
(331 Project)
Project Team: Name Anderson Tsai
Role PM,IC
Email atsai@
Voice mail 2494
XX Company Before Implementation
❖Experience : The mold design experience (PTC can not control)
❖Unexpected Factors : Bad quality of model from source
➢Bad quality of model will need time to fix(PTC can not control)
❖ Tool skill : ➢ Pro/E Modeling Skill , Moldesign Skill , 2D Skill ➢ Improve the design process (Team Work)
❖Environment Standardize : ➢ Library Should be constructed completely ➢ Build up the design environment (Mapkey,Icon……)
2~3 day
Drawing (1per.)
8 days
3 days
65% time saving: ???
10
© 2003 PTC
PTC’s Challenge for “331”
➢Tool Skill+Environment Standardize+Experience–Unexpected Factors