高炉高铝渣问题的探索与解决
高炉炼铁中渣化反应的机理与优化措施
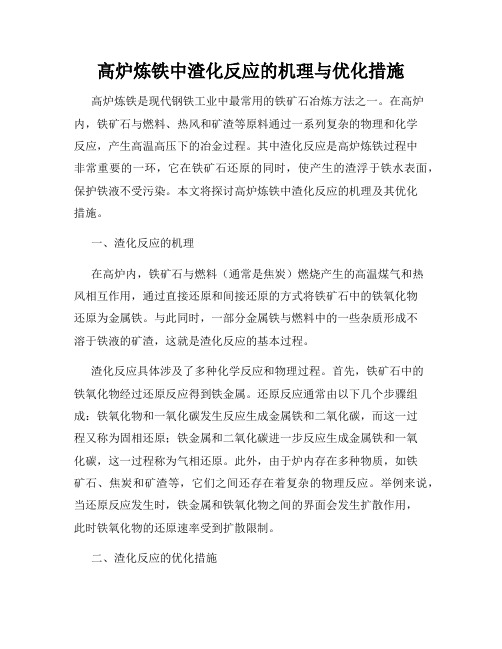
高炉炼铁中渣化反应的机理与优化措施高炉炼铁是现代钢铁工业中最常用的铁矿石冶炼方法之一。
在高炉内,铁矿石与燃料、热风和矿渣等原料通过一系列复杂的物理和化学反应,产生高温高压下的冶金过程。
其中渣化反应是高炉炼铁过程中非常重要的一环,它在铁矿石还原的同时,使产生的渣浮于铁水表面,保护铁液不受污染。
本文将探讨高炉炼铁中渣化反应的机理及其优化措施。
一、渣化反应的机理在高炉内,铁矿石与燃料(通常是焦炭)燃烧产生的高温煤气和热风相互作用,通过直接还原和间接还原的方式将铁矿石中的铁氧化物还原为金属铁。
与此同时,一部分金属铁与燃料中的一些杂质形成不溶于铁液的矿渣,这就是渣化反应的基本过程。
渣化反应具体涉及了多种化学反应和物理过程。
首先,铁矿石中的铁氧化物经过还原反应得到铁金属。
还原反应通常由以下几个步骤组成:铁氧化物和一氧化碳发生反应生成金属铁和二氧化碳,而这一过程又称为固相还原;铁金属和二氧化碳进一步反应生成金属铁和一氧化碳,这一过程称为气相还原。
此外,由于炉内存在多种物质,如铁矿石、焦炭和矿渣等,它们之间还存在着复杂的物理反应。
举例来说,当还原反应发生时,铁金属和铁氧化物之间的界面会发生扩散作用,此时铁氧化物的还原速率受到扩散限制。
二、渣化反应的优化措施为了提高高炉炼铁的效率和产能,必须优化渣化反应的过程。
以下是几种可行的优化措施:1. 选择合适的铁矿石:铁矿石的种类和质量对渣化反应有着重要影响。
选择具有较高还原性的铁矿石可以提高还原反应速率,从而加快渣化反应的进行。
此外,铁矿石中的含水和粉尘等杂质也会影响渣化反应的过程,因此在选择铁矿石时需要谨慎考虑。
2. 控制燃料的质量和供给:燃料是高炉炼铁中的重要组成部分,它不仅提供热量,还对渣化反应产生影响。
控制焦炭的质量和粒度可以影响还原反应的速率,进而影响渣化反应的进行。
此外,合理控制燃料的供给速度和方式也是重要的优化手段。
3. 优化高温煤气的利用:高温煤气中含有大量的一氧化碳和水蒸气等还原剂,可以与铁矿石中的氧化铁进行反应。
2024年高炉炉渣处理方法

____年高炉炉渣处理方法引言:高炉炉渣是一种由铁矿石在高温条件下熔化产生的废弃物,主要成分为氧化铁、氧化硅等。
传统的高炉炉渣处理方法主要是堆放和填埋,但这种处理方式存在着很多的问题,例如占地面积大、对环境造成污染等。
因此,研究和开发高效、环保的高炉炉渣处理方法非常重要。
本文将重点介绍____年高炉炉渣处理领域的新方法和技术。
一、循环利用炉渣制备建筑材料炉渣可以通过适当的处理方法用于制备建筑材料,例如水泥、混凝土等。
在____年,预计会有更多的研究和开发集高炉炉渣处理和建筑材料制备于一体的综合技术。
这种方法可以同时解决炉渣处理和建筑材料供需不平衡的问题,并且还可以减少原材料的使用,节约资源。
二、高炉炉渣的磁选处理高炉炉渣中的铁矿石矿物相对较多,通过磁选处理可以分离出其中的铁矿石,进一步回收利用。
____年,磁选处理技术将会更加高效和环保,能够在更短的时间内实现高炉炉渣的分离和回收。
这种方法可以大幅减少对铁矿石的需求,并且减少炉渣对环境的影响。
三、高炉炉渣的固化处理固化处理是指将高炉炉渣转化为无害、稳定的固体物质,以便安全地储存和处置。
____年,预计固化处理技术将有更大的突破,可以选择更环保的固化材料,提高固化处理的效果。
这种方法可以大大减少炉渣的体积,减少对土地资源的占用。
四、高炉炉渣的化学提取高炉炉渣中存在着一定的有价值金属元素,例如锌、锰等。
通过化学提取方法,可以将这些有价值的金属元素从炉渣中提取出来进行回收利用。
____年,随着化学提取技术的进步,将会有更多的高炉炉渣处理厂使用化学提取方法进行炉渣的资源化利用。
结论:综上所述,____年高炉炉渣处理方法将更加注重循环利用和资源化利用。
通过制备建筑材料、磁选处理、固化处理和化学提取等方法,可以实现高炉炉渣的有效处理和利用。
这不仅可以解决炉渣处理带来的环境问题,还可以减少对原材料的需求,节约资源。
同时,这也是对高炉技术发展的一种推动,使高炉产能得到更充分的利用。
济钢高炉高Al2O3炉渣渣系优化试验研究

济钢 高炉 高 AI 炉渣渣 系优化试 验研究 2 O3
李 学付 , 贻 留, 方 杨金 福 , 马继 波 , 杨雄 文
( 济钢集团有限公司 , 山东 济南 20 0 ) 511 摘 要: 以济钢现场高炉 渣样为基 准 , 正交 设计方法 , 采用 设计 了2 组试验方案 , 5 研究 了w A , 1%~ 3 ( 1 ) 5 2 %的高炉炉渣 0 为
区 间 ( 图 3 、 ) 炉 渣 熔化 性 温 度影 响 不 大 。在 见 ab对 图 3 , A ,2 .%、 O 1 . c中 当 1 = 09 Mg = 32 O %为熔 化 性温 度
最低 。此时 , 降低 M O, 渣 的熔化性 温度将 升 g 炉
2 l 2 2 2 3 2 4
此, 必须采取合理的措施 , 降低高 A:, l 对炉渣黏度 O 的影 响 。研 究炉 渣 中铝 、 二元 碱度 对炉 渣黏 度和 熔
化性 温度 的影响 , 提出济钢 高炉合理 的渣 系组 成 。
1 1 1 1 l 3 50 9 0 .0 8 . 1 1 1 1 13 2 5 9 1 . 5 9 . 2 9 11 1 3 25 0 .5 9 . 2 1 12 140 . 0 0 .0 30 2 l 1 1 13 3 0 O 1 .0 9 . 21 1 1 1 13 0 0 3 .0 6 . 2l 1 1 1 l3 3 5 4 .5 9 .
1 1 11 138 . 7 O .5 14 1 1 1 2 1 3 9. 7 1 -O 8 3 1 9 1 1 l37 . 8 .O 28 1 1 1 1 l38 . 8 O .5 41
试验 号 A B c
1 4 1 5 1 6 1 7 l 8 l 9 2 O
2 1 l2 1 3 7 3 3 3 _0 9 . 2 l 1 1 13 5 0 3 2 .0 8 . 2 l 12 l3 90 l 2 .O 8 . 2 1 12 l3 80 2 4 -0 9 .
高炉渣铁持续排放不净的原因分析及改善措施

高炉渣铁持续排放不净的原因分析及改善措施摘要:柳州钢铁集团中金不锈钢有限公司炼铁厂2号1680m³高炉,于2021年5月10日正式建成投产,设计年产合格炼钢生铁146万吨,2021年5月开炉至今2022年2月,高炉多次持续的渣铁排放对高炉稳定构成严重威胁,本文从进气燃料质量、铁口运行状况、高炉运行状况等几个方面分析渣铁连续非净排放的原因,采取炉体局部灌浆等相应措施,延长铁口排放时间,改善高炉运行状况,炉渣排放明显改善,高炉冶炼强度明显提升,高炉运行稳定性增加。
关键词:高炉;铁口喷溅;渣铁;排放不净;点火开炉初始稳定生产指标,事故为零休风率。
由于焦炭价格上涨等国内外市场因素,日产铁水平均为5000t,平均系数2.97 t/(m3·d),焦、煤、燃料比,分别为358、150、510 kg/t,平均0.532%含硅。
但投产以来,炉前渣铁排放困难,喷溅严重,炉前工作量大,炉内压量关系紧张,高炉稳定平稳的趋势受到影响,风力萎缩,产量下降,生产计划难以保证稳步提升。
1.高炉渣铁持续排放不净原因分析1.铁口串煤气喷溅的影响。
柳钢中金2#高炉的铁口炉壳砌体是由微孔刚玉组合砖砌筑而成,过渡平稳,浇注料由超低水泥刚玉质浇注料浇筑而成,在冷凝过程中,在浇注料中不可避免的会出现小裂纹缝隙,与铁口组合砖接缝处易出现分层现象,在高炉烘炉过程中,耐材见少量水汽的蒸发通道及耐材间的热应力作用,产生大量的缝隙,给炉内串煤气带来了可趁之机,高炉生产过程中,炉内液态渣铁与渣铁自生力相结合,不断地从铁口孔排出炉外,在渣铁排放时,炉内高压气体通过这些缝隙进入铁口孔道,破坏了原力平衡的稳定性,并在排放渣铁时产生喷溅。
严重铁口喷溅大大缩短了主沟耐材的寿命,导致铁大量流失,影响了高炉经济指标。
渣铁喷溅排放不净,直接影响高炉,造成较大的经济损害。
1.炉温及炉渣碱度的影响。
5~8月高炉处于开炉初始阶段,新设备故障率,原材料管控不是很到位,经常因原材料问题炉温出现波动,9月份后设备人员原材料等管理成熟,高炉操作系统开始向运转正常标准操作制度转变,在试生产期间,经常出现长时间亏渣铁,影响高炉的稳定顺行,导致了动态波动,影响了正常生产。
高炉炉渣处理与资源化利用技术研究

高炉炉渣处理与资源化利用技术研究近年来,随着工业生产的不断发展,高炉炉渣作为一种常见的工业废弃物,如何进行有效的处理和资源化利用已成为一个备受关注的问题。
本文将从高炉炉渣的特点、炉渣处理技术以及资源化利用方面展开论述。
首先,我们需要了解高炉炉渣的特点。
高炉炉渣主要由矿渣和工艺渣两部分组成。
矿渣主要是铁矿石在高温条件下还原和熔化生成的,而工艺渣则主要是焦炭灰、烧结矿砂等在高炉内燃烧生成的。
由于高炉操作的连续性,炉渣中也会包含少量的冶炼渣、废弃物等杂质。
传统上,高炉炉渣的处理方式主要是填埋和堆放。
然而,这种处理方式存在很多问题。
填埋会导致土地资源的浪费和环境污染,而长时间的堆放则容易造成渗滤液的渗出和大气中有害气体的排放。
因此,炉渣处理技术的研究和创新势在必行。
目前,炉渣处理技术主要包括物理处理、化学处理和生物处理等几种方法。
物理处理主要是利用筛分、磁选、重力分选等方法将炉渣中的金属物质和其他有用物质分离出来,以达到减少炉渣体积和减少对环境的影响。
化学处理则是利用酸碱等化学试剂对炉渣进行脱硫、脱磷等处理,使得炉渣中的有害物质得到降解和转化。
生物处理是利用微生物的作用对炉渣进行降解和转化,实现对炉渣中有机物和重金属的去除。
除了传统的处理技术外,资源化利用技术也是炉渣处理的另一个重要方向。
在资源化利用技术中,炉渣可以被转化为建筑材料、水泥、道路铺设材料等高附加值的产品。
例如,在水泥生产过程中,炉渣可以取代部分水泥原料,减少对天然资源的依赖并降低环境污染。
此外,炉渣还可以被转化为颗粒活性炉渣、高温液相炉渣等陶瓷材料,用于建筑材料和环保装备制造。
为了进一步提高炉渣处理与资源化利用的效益,需要加强技术研究和创新。
一方面,通过优化处理流程、提高处理效率和降低处理成本,可以实现对炉渣的高效处理。
另一方面,通过开展新材料的研发和产业化推广,可以扩大炉渣的资源化利用范围。
此外,还需加强对炉渣处理过程中所产生的废水和废气的处理,以减少环境污染。
高炉炼铁过程中废渣资源化利用的技术创新

高炉炼铁过程中废渣资源化利用的技术创新由于工业化的快速发展,高炉炼铁已成为现代钢铁工业中不可或缺的环节。
然而,传统的炼铁过程会产生大量的废渣,给环境带来严重污染。
为了实现可持续发展,推动高炉炼铁过程中废渣资源化利用的技术创新势在必行。
本文将探讨当前废渣资源化利用的现状和趋势,并提出一些创新的技术解决方案。
一、废渣资源化利用的现状高炉炼铁过程中主要产生的废渣主要包括烧结矿、烟气净化渣和炉渣等。
这些废渣通常被视为浪费物料,被丢弃或填埋,给环境带来负面影响。
然而,废渣中含有很多有价值的可回收物质,如铁、钢、矿物等。
因此,将废渣转化为可再利用的资源是一种解决环境问题和实现可持续发展的有效途径。
目前,废渣资源化利用主要通过以下几种方式实现:1. 废渣回收再利用:将废渣中的有价值物质进行分离和提取,重新利用于炼铁过程或其他工业生产中。
例如,烧结矿中的铁含量较高,可以再次用于高炉冶炼过程中。
2. 废渣填充利用:将废渣用于填充坑道、道路建设和土地复垦等工程中。
废渣填充可以减少对自然资源的占用,同时改善了被填充地区的土壤质量。
3. 废渣综合利用:将不同种类的废渣进行混合利用,形成新的产品或材料。
例如,烟气净化渣中的硅酸盐可以与矿产废渣混合制备建筑材料。
尽管废渣资源化利用取得了一定的进展,但仍面临一些挑战。
首先,目前的废渣资源化利用技术还不够成熟,存在成本高、技术路线不清晰等问题。
其次,相关政策法规的缺失和监管体系不健全也制约了废渣资源化利用的发展。
二、废渣资源化利用的技术创新为了推动高炉炼铁过程中废渣资源化利用的发展,需要进行技术创新和研发。
以下是一些可行的技术创新方案:1. 废渣熔融处理技术:通过高炉炼铁过程中炉渣的熔融处理,将废渣转化为玻璃状物质。
这种熔融处理技术可以减少废渣体积,提高废渣中有价值物质的回收率,并且可以将熔融后的产品用于建筑材料或其他工业领域。
2. 废渣碳化技术:利用废渣中的碳含量,将其进行碳化处理,生成高价值的碳材料。
2500立方米高炉冲渣问题以及处理措施
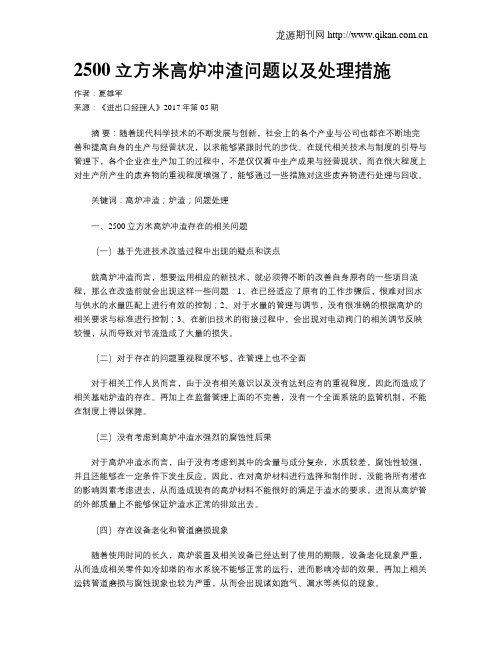
2500立方米高炉冲渣问题以及处理措施作者:夏雄军来源:《进出口经理人》2017年第05期摘要:随着现代科学技术的不断发展与创新,社会上的各个产业与公司也都在不断地完善和提高自身的生产与经营状况,以求能够紧跟时代的步伐。
在现代相关技术与制度的引导与管理下,各个企业在生产加工的过程中,不是仅仅看中生产成果与经营现状,而在很大程度上对生产所产生的废弃物的重视程度增强了,能够通过一些措施对这些废弃物进行处理与回收。
关键词:高炉冲渣;炉渣;问题处理一、2500立方米高炉冲渣存在的相关问题(一)基于先进技术改造过程中出现的疑点和误点就高炉冲渣而言,想要运用相应的新技术,就必须得不断的改善自身原有的一些项目流程,那么在改造前就会出现这样一些问题:1、在已经适应了原有的工作步骤后,很难对回水与供水的水量匹配上进行有效的控制;2、对于水量的管理与调节,没有很准确的根据高炉的相关要求与标准进行控制;3、在新旧技术的衔接过程中,会出现对电动阀门的相关调节反映较慢,从而导致对节流造成了大量的损失。
(二)对于存在的问题重视程度不够,在管理上也不全面对于相关工作人员而言,由于没有相关意识以及没有达到应有的重视程度,因此而造成了相关基础炉渣的存在。
再加上在监督管理上面的不完善,没有一个全面系统的监管机制,不能在制度上得以保障。
(三)没有考虑到高炉冲渣水强烈的腐蚀性后果对于高炉冲渣水而言,由于没有考虑到其中的含量与成分复杂,水质较差,腐蚀性较强,并且还能够在一定条件下发生反应。
因此,在对高炉材料进行选择和制作时,没能将所有潜在的影响因素考虑进去,从而造成现有的高炉材料不能很好的满足于渣水的要求,进而从高炉管的外部质量上不能够保证炉渣水正常的排放出去。
(四)存在设备老化和管道磨损现象随着使用时间的长久,高炉装置及相关设备已经达到了使用的期限,设备老化现象严重,从而造成相关零件如冷却塔的布水系统不能够正常的运行,进而影响冷却的效果。
炼铁技术创新高炉渣的形成与控制方法研究
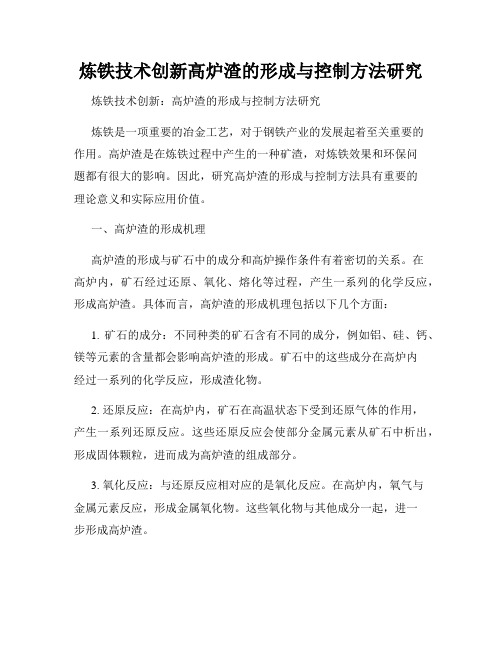
炼铁技术创新高炉渣的形成与控制方法研究炼铁技术创新:高炉渣的形成与控制方法研究炼铁是一项重要的冶金工艺,对于钢铁产业的发展起着至关重要的作用。
高炉渣是在炼铁过程中产生的一种矿渣,对炼铁效果和环保问题都有很大的影响。
因此,研究高炉渣的形成与控制方法具有重要的理论意义和实际应用价值。
一、高炉渣的形成机理高炉渣的形成与矿石中的成分和高炉操作条件有着密切的关系。
在高炉内,矿石经过还原、氧化、熔化等过程,产生一系列的化学反应,形成高炉渣。
具体而言,高炉渣的形成机理包括以下几个方面:1. 矿石的成分:不同种类的矿石含有不同的成分,例如铝、硅、钙、镁等元素的含量都会影响高炉渣的形成。
矿石中的这些成分在高炉内经过一系列的化学反应,形成渣化物。
2. 还原反应:在高炉内,矿石在高温状态下受到还原气体的作用,产生一系列还原反应。
这些还原反应会使部分金属元素从矿石中析出,形成固体颗粒,进而成为高炉渣的组成部分。
3. 氧化反应:与还原反应相对应的是氧化反应。
在高炉内,氧气与金属元素反应,形成金属氧化物。
这些氧化物与其他成分一起,进一步形成高炉渣。
4. 熔化过程:高炉温度高达数千摄氏度,这种高温下矿石中的金属氧化物和渣化物都会熔化,形成液体高炉渣。
二、高炉渣的控制方法了解高炉渣形成的机理,对于控制高炉渣的形成具有重要的指导意义。
以下是一些常用的高炉渣控制方法:1. 控制矿石成分:通过选择合适的矿石,调整矿石的成分,可以有效地控制高炉渣的形成。
例如,减少矿石中含硅和含铝的成分可以降低高炉渣中的硅酸盐含量,提高高炉渣的流动性。
2. 优化还原条件:合理控制高炉的还原条件,可以减少氧化反应产生的金属氧化物,从而减少高炉渣的产生量。
增加还原剂的使用量、增加还原温度等都可以有效地改善还原条件。
3. 渣化物控制技术:渣化物是高炉渣形成的关键部分,对其进行控制可以达到调控高炉渣的目的。
一种常用的方法是添加渣化剂,例如石灰石、白云石等,在炼铁过程中形成易于掌控和处理的渣化物。
高炉渣处理爆炸原因及攻克措施探析

高炉渣处理爆炸原因及攻克措施探析高炉大型化发展趋势促使高炉渣处理逐渐受到人们的重视,但在处理过程中,受其自身的因素影响,容易出现爆炸情况,造成严重的影响,本文从高炉渣处理环节入手,深入进行分析,结合实际情况,从整体上进行分析,明确其爆炸原理,做好针对性预防措施,以降低爆炸事故发生几率。
标签:高炉;渣处理;爆炸原因;解决措施引言随着时代不断发展,高炉冶炼逐渐成为钢铁行业中主要的炼铁生产方式,可以生产出高质量的高炉生铁,并衍生出副产物,如高炉煤气、高炉渣以及炉尘。
高炉渣具有较多的用途,通过合理的急速水淬冷后可以作为高质量的建筑材料,实现资源的最大化利用,以满足当前的需求。
一、高炉渣处理爆炸原因分析(一)高炉渣水淬分析现阶段,我国在进行高炉渣处理过程中,主要是应用水淬工艺进行处理,通过水力冲渣进行处理,以满足生产的需求。
水淬工艺主要包括三个过程,为粒化、脱水、储运三个工艺,不同的过程其处理的目的不同,粒化的主要目的是利用高压水将高温液态渣击碎,通过水淬冷却为水渣。
脱水的目的是灵活利用过滤或者分离等方法进行水渣分离,将水渣进行集中处理,并保证其水可以进入循环使用。
储运是将当前经过处理的水渣进行集中的存储,并采用现有的技术进行二次脱水,灵活应用当前的辅助技术进行优化,满足当前的需求[1]。
(二)高炉炉渣爆炸通常情况下,高炉炉渣出炉后温度高达约为1450℃-1550℃,在进行水淬过程中,需要进行能量转化,高炉渣的温度瞬间下降,在释放大量的热同时,产生水汽,通过水蒸气进行能量转化。
高炉渣爆炸的形式较多,通常主要在高炉生产异常时容易出现爆炸,分离过程中由于热能量传递,造成水接收较大的能量,铁的含量较多,铁的导热系数又高,造成能量的聚集,并且铁容易产生凝固,形成受限空间,增大发生爆炸的几率,因此需要有效的控制铁含量。
渣中含铁是高炉冶炼的常见情况,但通常情况下其含量较少,对正常的冶炼影响较小,但如果存在悬料次数多、炉缸堆积、炉温较低等情况,将导致炉渣整体流动性降低,容易出现分离不佳情况,出现整体的异常,最终引发爆炸。
炉渣中Al2O3含量升高的影响及处理措施

炉渣中Al2O3含量升高的影响及处理措施通过对2005年1号高炉各项生产指标观察,明显地看出进入秋季高炉生产的黄金季节,产量水平却在下滑,经过对2005年9月份首秦1号高炉生产情况分析,得出渣中Al2O3升高是造成产量下滑的一项重要原因,给高炉顺行带来严重影响。
为此而成立精料小组,采取组织跟踪取样检验和统计分析的方法,通过调节烧结矿配料结构,以改善炉渣性能,从而有效控制了原燃料成分波动带来的不利影响,同时高炉做出调整,保证了高炉生产顺行,使各项技术指标维持在先进水平。
标签:高炉;Al2O3;炉渣;精料1、概况:首秦1号高炉于2004年6月6日建成投产。
设计有效容积为1200m3,18个风口2个出铁口。
采用俄罗斯卡鲁金顶燃式热风炉,煤气空气双预热,无料钟炉顶,全软水密闭循环冷却,喷涂内衬,高炉煤气连续自动分析,炉顶成像监测和炉喉十字测温煤气监测系统,螺旋排渣技术等一系列国内外新技术。
特别是高炉煤气回收系统采用全干式低压脉冲布袋除尘新工艺,是国内首次在1200m3级的高炉应用并取得成功,在热风炉全烧高炉煤气条件下,风温可达1250℃,风量最高3250m3/min,利用系数2.25,使用寿命15年,使用原料为资产烧结矿加秘鲁球团矿和澳大利亚块矿。
投产初期受单一生产线影响,每一环节都会产生瓶颈效应,使高炉生产受到限制,进入2005年以后,每月生产都超过设计利用系数,进入2005年夏季,在节能降耗方面尤为突出,6月份入炉焦比已达301Kg/t,然而到了秋季高炉的黄金生产时期产量却一度下滑。
2005年1号高炉各项经济技术指标统计如下表,经分析发现高炉渣中Al2O3含量一段时间突然升高,炉渣粘度升高,流动性变差,已经对高炉顺行带来影响。
因此如何将高炉渣中的Al2O3含量控制在合理范围内,在炉渣中Al2O3含量较高情况下,各项经济技术指标仍达先进水平,是首秦炼铁系统的重点攻关课题。
从表中显示7月到10月产量下降,焦比升高,萤石用量9月对多。
简述高炉渣处理技术

简述高炉渣处理技术高炉渣是一种高炉生产过程中产生的固体废弃物,因其具有较高的硬度、氧化性和化学活性,对环境和人类健康产生了一定的影响。
因此,有效地处理高炉渣已成为环境保护和可持续发展的关键措施之一。
本文将简要介绍高炉渣处理技术,并探讨其优点、挑战和未来发展。
一、高炉渣处理技术1. 物理处理法物理处理法包括重力分离、浮选、磁选、过滤等。
这些方法通过将高炉渣与相应的物质进行比较,将其分离出来。
其中,重力分离是最常用的方法,它通过让高炉渣在重力的作用下分离出来。
浮选是通过将高炉渣放入液体中,使其浮在水面上,从而实现分离。
磁选是通过磁场的作用将高炉渣中的磁性物质分离出来。
过滤是通过选择合适的滤材,将高炉渣中的非磁性物质过滤出来。
2. 化学处理法化学处理法包括熔融、中和、氧化等。
这些方法通过使用化学物质,将高炉渣中的硬度和氧化性降低,使其更容易处理。
其中,熔融是通过加热高炉渣,使其软化,然后进行熔融处理。
中和是通过添加相应的化学物质,中和高炉渣中的碱性物质。
氧化是通过使用氧气或其他氧化剂,将高炉渣中的氧化物质氧化掉。
3. 生物处理法生物处理法是利用生物反应将高炉渣转化为营养物质。
这种方法包括堆肥、生物炉渣发酵、生物洗涤等。
堆肥是将高炉渣放入堆肥箱中,通过微生物的代谢作用,将其转化为营养物质。
生物炉渣发酵是将高炉渣放入发酵罐中,通过微生物的代谢作用,将其转化为营养物质。
生物洗涤是通过将高炉渣放入洗涤塔中,利用微生物的代谢作用,将其转化为营养物质。
二、高炉渣处理技术的优点物理处理法的优点包括简单、经济、高效等。
重力分离和高炉渣过滤可以通过物理手段实现分离,不需要化学或生物处理。
浮选和磁选等方法可以筛选出高炉渣中的有用物质。
化学处理法的优点包括可以控制处理过程中的污染和危险。
生物处理法的优点包括可以利用微生物将高炉渣转化为营养物质,减少处理过程中对环境的影响。
三、高炉渣处理技术的挑战高炉渣处理技术面临着许多挑战,其中最主要的挑战是高炉渣中杂质的复杂性和难以处理的物质。
高炉渣铁持续排放不净的原因和对策

高炉渣铁持续排放不净的原因和对策摘要:高炉作为一种重要的冶炼设备,它是冶炼金属材料的主要凭借。
在高炉的使用中,渣铁持续排放问题一直是业内研究与探讨的重点。
受高炉本身设备因素、内外部环境因素及冶炼技术方式等影响,常见的渣铁排放不净原因有入炉原料质量差、炉内压差控制不当铁口喷溅等。
为了保证高炉安全作业,确保冶炼质量,针对此类问题提出严格控制原料质量、合理控制炉内压差、铁口附近高压灌浆处理的对策,以期为我国冶炼工程领域提供价值性参考。
关键词:冶炼设备;高炉;渣铁排放;问题分析;对策进入21世纪以来,随着我国工业体系的不断调整及工业不断发展,冶炼行业迅速兴起,并成为了工业体系的重要支撑。
冶炼领域中,高炉一直是常见的冶炼设备之一,它的出现,拉动了冶炼行业的发展,对人类物质生活有着重要贡献。
从高炉的本身功能特点上来看,其由炉喉、炉身、炉腰、炉腹、炉缸五部分组成,而渣铁排放作为高炉作业中重要的工作环节,直接影响着整个高炉的稳定运行。
一旦高炉出现渣铁持续排放不净的情况,就会导致大量的渣铁沉积在高炉炉内中,从而影响到冶炼质量,甚至带来安全隐患。
目前,高炉渣铁持续排放不净的原因由多种因素构成,而且隐性因素较多。
对此,本文通过对高炉渣铁持续排放不净的原因分析,提出一些解决建议,保障高炉的安全作业。
一、高炉渣铁持续排放不净的原因分析(一)入炉原料质量影响入炉原料是影响高炉渣铁排放的主要因素之一。
根基冶炼工程领域的实践与研究经验可知,很多冶炼厂为了保证冶炼产品质量,提高高炉的冶炼效率,都会对入炉原料进行化学改造,通过提高入炉原料的各种化学物质占比,以提高原料焦炭的冷热态强度。
而实际上,很多高炉设备中的焦炭冷热态强度均高于高炉的实际温度标准,虽然通过增强焦炭的冷热态强度,提高了冶炼速度,但是也必然导致焦炭在高炉中的反应性过低,气化反应的时间都相对延长,从而导致高炉中出现大量的死焦堆。
滞留的死焦堆长时间堆积在高炉排渣出口,也影响到其它渣铁的正常排放,导致新的渣铁与死焦堆混合,出现了渣铁排放不净、堆积的问题[1]。
高炉炉渣资源化利用研究与现状

高炉炉渣资源化利用研究与现状摘要:钢铁生产行业在高速发展的同时,高炉炼铁工艺产生的高炉渣不断累积。
由于缺乏有效的资源化利用方式,高炉矿渣就地堆积,占用了大量土地资源,并对周边的土壤及水体环境造成了污染。
有效利用高炉矿渣等二次资源,减少高炉矿渣对环境的污染,达到高炉矿渣的减量化、无害化、资源化处理,并进一步提高高炉矿渣基产品的附加值,是我国钢铁行业可持续发展的有力保障,对于建立环境友好型、资源节约型社会具有促进意义。
关键词:高炉矿渣;制备方法;陶瓷纤维;资源化高炉矿渣是在高炉炼铁过程中,铁矿石中含有的SiO},A1}03等杂质与熔剂中的CaO,Mg0等反应生成硅酸盐熔融物,经水淬处理得到含有较多孔隙且无定形、不规则的副产物[y0作为我国国民经济一大支柱的钢铁生产行业,在全行业高速发展的同时,其主要的冶炼工艺—高炉炼铁工艺产生的高炉矿渣不断累积。
由于缺乏有效的资源化利用方式,高炉矿渣就地堆积,占用了大量的土地资源,并对周边的土壤及水体环境造成了污染。
就普通的炼铁工艺而言,每冶炼It铁矿石会产生0.5一0.9t的矿渣,如不能合理地处理大储存量的高炉矿渣,不仅会造成环境污染,浪费大量能源,且会给我国经济建设带来巨大的压力,不利于钢铁行业的可持续发展。
近年来,国内的高炉矿渣主要应用于建筑材料和混凝土掺合料,其附加值较低,大量高炉矿渣等二次资源被浪费。
因此,如何对高炉矿渣更好的资源化利用,是当今钢铁行业面临的又一主要问题[0据不完全统计,我国矿业固体废弃物累计超过70亿t,占地6万多h时。
高效的开发和利用工业二次资源,变废为宝、化害为利,实现工业的可持续发展显得尤为重要[[3]1高炉矿渣的组成及性质高炉矿渣L要成分包括30%一如%的Ca0,1%一15}}0的MgO,27%一35%的SiO},5%一10%的A1}03等。
矿渣中还含有少量的Fe}03,FeO,Na}O,K}0等成分,一般情况下,这些成分含量较低,对矿渣质量的影响较小。
高铝对高炉炼铁的影响及优化
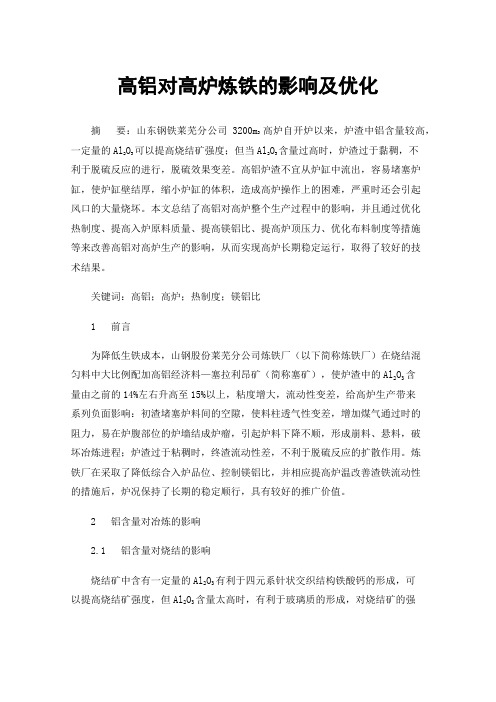
高铝对高炉炼铁的影响及优化摘要:山东钢铁莱芜分公司3200m3高炉自开炉以来,炉渣中铝含量较高,一定量的Al2O3可以提高烧结矿强度;但当Al2O3含量过高时,炉渣过于黏稠,不利于脱硫反应的进行,脱硫效果变差。
高铝炉渣不宜从炉缸中流出,容易堵塞炉缸,使炉缸壁结厚,缩小炉缸的体积,造成高炉操作上的困难,严重时还会引起风口的大量烧坏。
本文总结了高铝对高炉整个生产过程中的影响,并且通过优化热制度、提高入炉原料质量、提高镁铝比、提高炉顶压力、优化布料制度等措施等来改善高铝对高炉生产的影响,从而实现高炉长期稳定运行,取得了较好的技术结果。
关键词:高铝;高炉;热制度;镁铝比1 前言为降低生铁成本,山钢股份莱芜分公司炼铁厂(以下简称炼铁厂)在烧结混匀料中大比例配加高铝经济料—塞拉利昂矿(简称塞矿),使炉渣中的Al2O3含量由之前的14%左右升高至15%以上,粘度增大,流动性变差,给高炉生产带来系列负面影响:初渣堵塞炉料间的空隙,使料柱透气性变差,增加煤气通过时的阻力,易在炉腹部位的炉墙结成炉瘤,引起炉料下降不顺,形成崩料、悬料,破坏冶炼进程;炉渣过于粘稠时,终渣流动性差,不利于脱硫反应的扩散作用。
炼铁厂在采取了降低综合入炉品位、控制镁铝比,并相应提高炉温改善渣铁流动性的措施后,炉况保持了长期的稳定顺行,具有较好的推广价值。
2 铝含量对冶炼的影响2.1 铝含量对烧结的影响烧结矿中含有一定量的Al2O3有利于四元系针状交织结构铁酸钙的形成,可以提高烧结矿强度,但Al2O3含量太高时,有利于玻璃质的形成,对烧结矿的强度和低温还原粉化性能不利[1]。
实践证明,当烧结矿中铝含量>2.5%,对烧结矿强度和低温还原粉化性能影响较大。
2.2 铝含量对高炉生产的影响Al2O3在炉渣中有一定的脱硫效果,但弱于CaO和MgO。
对高炉生产的影响具体表现为:在炉内,压差升高,上部容易悬料,炉缸容易粘结堆积;在炉外,主沟内渣铁不易分离,渣中带铁,渣沟内炉渣流动性很差,容易结壳。
高炉专利技术使用中常见问题解决方案

高炉专利技术使用中常见问题解决方案高炉是冶金行业中重要的设备之一,其专利技术的使用对于提高生产效率和降低能耗具有重要意义。
然而,在实际应用中,我们常常会遇到一些问题。
本文将探讨高炉专利技术使用中的常见问题,并提出解决方案。
一、高炉炉渣处理问题在高炉冶炼过程中,炉渣的处理是一个关键环节。
炉渣中含有大量的有价值金属,如铁、锰等,如何有效回收这些金属成为了一个难题。
同时,炉渣的处理还涉及到环境污染的问题,如二氧化硫的排放等。
针对这一问题,可以采用以下解决方案。
首先,通过优化高炉操作参数,控制炉渣的成分和性质,以提高金属的回收率。
其次,可以引入先进的炉渣处理技术,如炉渣浸出法、炉渣磁选法等,以提高金属的回收效率。
此外,还可以采用脱硫剂等措施,降低二氧化硫的排放。
二、高炉燃料选择问题高炉的燃料选择对于冶炼效果和能耗有着重要影响。
传统的高炉燃料主要是焦炭,但其价格波动大且资源有限。
因此,如何选择合适的燃料成为了一个关键问题。
针对这一问题,可以采用以下解决方案。
首先,可以引入新型燃料,如生物质燃料、天然气等,以降低能耗和环境污染。
其次,可以采用煤气化技术,将煤转化为合成气,作为高炉的燃料。
此外,还可以通过优化高炉操作参数,提高燃烧效率,降低燃料消耗。
三、高炉炉壁耐火材料问题高炉的炉壁是承受高温和腐蚀的关键部位,其耐火材料的选择和使用对于高炉的正常运行至关重要。
然而,由于高炉内部的复杂工况,炉壁耐火材料容易磨损和腐蚀,导致炉壁寿命缩短。
针对这一问题,可以采用以下解决方案。
首先,可以引入高性能耐火材料,如高铝耐火材料、镁铝耐火材料等,以提高炉壁的耐火性能。
其次,可以采用涂层技术,对炉壁进行保护,延长炉壁的使用寿命。
此外,还可以通过优化高炉操作参数,减少对炉壁的损害,延缓炉壁的腐蚀。
四、高炉废气处理问题高炉冶炼过程中产生大量的废气,其中含有大量的有害物质,如二氧化碳、一氧化碳等。
这些废气的处理对于环境保护具有重要意义。
重钢高炉炉渣Al2O3升高的原因分析与应对措施

重钢高炉炉渣Al2O3升高的原因分析与应对措施摘要:针对重钢高炉渣中Al2O3含量的升高,分析了炉渣中Al2O3升高对高炉冶炼的不利影响,并通过统计对比分析,确定高炉入炉品位升高、渣铁比下降是导致渣中Al2O3升高的主要原因。
高炉经过采取切实可行的技术和管理措施,有效降低了渣中Al2O3含量,并在渣中Al2O3升高期间保持了高炉稳定顺行。
关键词:高炉;炉渣;Al2O3Cause Analysis and Countermeasures of Al2O3Increased in BF Slag in Chongqing SteelSHU Hao ;ZHANG Hai-feng; ZHANG Xiao-lin;YI Li(Chongqing Iron and Steel Co.Ltd)Abstract:The content of Al2O3 in Chongqing steel's BF slag increased , the adverse effect on the smelting of blast furnace was analyzed. Through statistical comparison and analysis, the increased BF charge grade and decreased slag-iron ration were the main cause leading to the Al2O3 rise in slag. Through feasible technology and management measures, it effectively reduced the Al2O3 content in slag, and maintained the stable smooth operation of the blast furnace during the increase of Al2O3 in the slag.Key words: blast furnace; slag; Al2O3在传统的高炉炼铁中,一般认为,高炉炉渣中Al2O3在15%以下为宜。
高炉渣处理技术的现状及发展趋势

高炉渣处理技术的现状及发展趋势1. 引言高炉渣是指在炼铁过程中产生的固体废弃物,主要由铁矿石中的非金属成分经冶炼后形成。
高炉渣处理是炼铁行业中的一个重要环节,不仅涉及环保问题,还能通过有效处理提取出有价值的资源,对于实现循环经济具有重要意义。
本文将介绍高炉渣处理技术的现状及发展趋势。
2. 高炉渣处理技术的现状目前,高炉渣处理技术主要分为物理方法和化学方法两大类。
2.1 物理方法物理方法是利用高炉渣的物理性质来实现处理和利用,常见的有磁选法、风选法和重选法等。
2.1.1 磁选法磁选法利用高炉渣中的磁性物质与非磁性物质的差异,通过磁力对高炉渣进行选择性分离。
这种方法可以实现高炉渣中铁资源的回收,但对于非磁性物质的处理效果较差。
2.1.2 风选法风选法是利用高炉渣中的颗粒间的比重、形状和粒径等差异,通过风力对高炉渣进行分离和分类。
这种方法处理效果较好,可以实现高炉渣的资源化利用和减少对环境的污染。
2.1.3 重选法重选法是利用高炉渣中成分的密度差异进行分离,将密度大的部分分离出来。
这种方法可以有效分离出高炉渣中的重金属等有价值的资源。
2.2 化学方法化学方法主要是利用化学反应和物质间的相互作用来实现高炉渣的处理和利用,常见的有酸浸法、碱浸法和微生物处理法等。
2.2.1 酸浸法酸浸法利用酸性溶液对高炉渣进行溶解和分离。
这种方法可以高效地分离出高炉渣中的有价值金属资源。
2.2.2 碱浸法碱浸法是利用碱性溶液对高炉渣进行溶解和分离。
这种方法可以有效地去除高炉渣中的有毒物质和污染物,并实现高炉渣的资源化利用。
2.2.3 微生物处理法微生物处理法利用特定的微生物对高炉渣中的某些成分进行代谢和转化。
这种方法对于处理高炉渣中的有机物具有一定的效果,但对于无机物的处理效果较差。
3. 高炉渣处理技术的发展趋势随着社会对环保和资源利用的要求越来越高,高炉渣处理技术也在不断创新和发展。
3.1 综合利用未来的高炉渣处理技术将更加注重综合利用,将其作为资源而不是废物来处理。
资料:同钢450m3高炉高[Ti]铁、高(Al2O3)渣炉况失常分析与处理
![资料:同钢450m3高炉高[Ti]铁、高(Al2O3)渣炉况失常分析与处理](https://img.taocdn.com/s3/m/f32e79f7941ea76e58fa04e3.png)
同钢450m3高炉高[Ti]铁、高(Al2O3)渣炉况失常分析与处理高社张润堂吴建军大同煤矿集团钢铁有限公司摘要对4#高炉炉况失常的原因、机理及处理过程进行了总结分析,认为铁中[Ti] 、渣中(Al2O3)异常升高是炉况失常的主要原因,采用锰矿和净焦洗炉、堵风口恢复、疏松中心气流、控制炉温、碱度、炉外出净渣铁等措施,取得了较好效果。
关键词高炉炉况失常分析处理1 引言山西大同煤矿集团钢铁有限公司炼铁厂4#高炉有效容积450m3,自2004年10月18日点火开炉以来,因设备事故频发,原燃料成份波幅大,每年均有大的炉况失常,给全厂生产带来较大的负面影响。
4#高炉自进入2007年后,由于不断采取强化措施,加强综合管理,各项经济技术指标逐月攀升,利用系数达到了3.3――3.4t/(m3d),到6月下旬高炉日产量突破1600吨,其中23日产量达到1630.56吨,炉况稳定顺行。
随着我国钢铁产量的增加,铁矿石进口量日趋紧张,价格不断上涨,为合理利用当地资源,增强企业竞争力,同钢提出了“低成本战略”思路,充分利用大同周边地区资源及价格较便宜的外粉(7月份地矿比例增加到80%),导致入炉料杂,铁中[Ti] 、渣中(Al2O3)异常升高,铁水包粘结严重,炉缸不活,炉墙结厚,事前又没有一点防备,致使炉况失常。
2 炉况失常处理过程7月份前半月,高炉炉况处于稳定顺行的良好状态,各项生产指标均保持高的水平,具体指标见表17月份中班,由于上密封胶圈烂,17:16休风1小时更换,同时更换14#弯头。
复风后高炉开始加风,但明显感到高炉接受风量的能力较差,料线一直不动,20:20开始崩料,减风25kPa控制,顶压降至100kPa,矿批原来的20吨缩到18吨,布料角度同缩2度,由原来的αO935433,αC730.7628.7调整到αO933431,αC728.7626.7,逐步恢复炉况。
18日白班10:44风口工作呆滞,料慢,崩料1.4-4.1米,11:43料线5.3米,补净焦27吨,布料角度调整为αO1330,αC1328.7。
高炉炉渣处理方法(最新版)

高炉炉渣处理方法(最新版)Security technology is an industry that uses security technology to provide security services to society. Systematic design, service and management.( 安全管理 )单位:______________________姓名:______________________日期:______________________编号:AQ-SN-0112高炉炉渣处理方法(最新版)1.概述:高炉熔渣处理方法主要分为出干渣和水淬渣,由于干渣处理环境污染较为严重,且资源利用率低,现在已很少使用,一般只在事故处理时,设置干渣坑或渣罐出渣;目前,高炉熔渣处理主要采用水淬渣工艺,水渣可以作为水泥原料,或用于制造渣砖、轻质混凝土砌块,使资源得到合理的利用。
1.1水淬渣的按其形成过程,可以分为两大类:A:高炉熔渣直接水淬工艺。
脱水方法主要有渣池法或底滤法、因巴法、拉萨法及笼法等。
其主要工艺过程是高炉熔渣渣流被高压水水淬,然后进行渣水输送和渣水分离。
B:高炉熔渣先机械破碎后水淬工艺。
主要代表为图拉法和HK 法等。
其主要工艺过程是高炉熔渣流首先被机械破碎,在抛射到空中时进行水淬粒化,然后进行渣水分离和输送。
1.2按水渣的脱水方式可分为:A:转鼓脱水法。
经水淬或机械粒化后的水渣流到转鼓脱水器进行脱水,前者为“INBA”法(因巴法),后者为“TYNA”法(图拉法);图拉法在我国已获得国家发明专利,专利名称为“冶金熔渣粒化装置”,专利权人为“中冶集团包头钢铁设计研究总院”,为俄罗斯人与中国人共同发明。
B:渣池过滤法:渣水混合物流人沉渣池,采用抓斗吊车抓渣,渣池内的水则通过渣池底部或侧部的过滤层进行排水。
底滤式加反冲洗装置,一般称为“OCP”法,即“底滤法”;C:脱水槽式:水淬后的渣浆经渣浆泵输送到脱水槽内进行脱水。
- 1、下载文档前请自行甄别文档内容的完整性,平台不提供额外的编辑、内容补充、找答案等附加服务。
- 2、"仅部分预览"的文档,不可在线预览部分如存在完整性等问题,可反馈申请退款(可完整预览的文档不适用该条件!)。
- 3、如文档侵犯您的权益,请联系客服反馈,我们会尽快为您处理(人工客服工作时间:9:00-18:30)。
高炉高铝渣问题的探索与解决
高炉生产实践表明,炉渣Al2O3含量超过16%就会对炉况的稳定顺行产生较大的不良影响,甚至引起高炉失常。
例如,武钢7号高炉是3200m3大型高炉,装备水平先进,投产后,取得了很好的操作指标,但到2009年6月,由于原料成分大幅波动,烧结质量变差,矿石Al2O3含量高,渣铁流动性变差,渣铁不能及时排放,致使炉况顺行渐差,造成了炉况的失常,给高炉生产造成了巨大损失。
为此,武钢努力探索解决高炉高铝渣问题的有效措施。
根据生产实践经验,在Al2O3含量达到18%以上时,依靠高MgO渣来降低炉渣黏度是不可行的,因为提高炉渣MgO含量要靠提高烧结矿中白云石等熔剂配比来实现,当烧结矿中MgO含量增加时,粘结相的流动性变差,如燃耗不增加则必然引起烧结矿强度降低。
最近实验室研究的结论是,烧结矿中MgO含量以2.5%为宜,超过此范围,烧结矿转鼓指数将趋于下降。
因此,要应对原料来源失控引起的Al2O3含量过高的情况,需要研究适宜的高炉造渣制度。
降低黏度的途径有2个,一是加锰矿(MnO);二是加萤石(CaF2)。
由于加锰矿会影响生铁中Mn的含量,所以应研究适当加入萤石量的方法。
武钢7号高炉在2009年7月高炉渣中Al2O3含量全天平均高达18.6%,最高时达22.81%,严重影响了渣铁的流动性和渣铁的分离,直接导致了渣铁排放困难。
尽管采取了很多措施,如加锰矿、热洗炉等措施,但由于炉缸堆积严重,炉况长时间不见好转,最后决定用萤石洗炉。
从2009年7月24号到7月28号,8月3号至7号,加入萤石,萤石用完后再使用Mn矿。
洗炉期间补加大量净焦,用于补充炉缸热量。
从使用效果来看,萤石对炉身粘结的洗刷、对炉缸堆积的处理作用较为显著。
加入萤石以后,显著降低了炉渣的熔点,改善了炉渣的流动性,对炉前出铁排渣作用明显,这对于炉况的恢复起到了非常重要的作用。
应该指出,虽然添加萤石有利于改善炉渣流动性,但萤石对炉腹炉缸的冷却壁有严重的侵蚀作用,所以采用萤石洗炉要十分慎重。
武钢在处理7号高炉2009年7月的炉缸堆积时,萤石是通过炉料均匀加入炉内的,萤石分布于整个料面,萤石大面积和炉腹、炉缸处冷却系统接触,造成了大量风口损坏,延缓了恢复时间,以后在处理因炉渣中Al2O3偏高而引起的炉缸堆积时应加以改进。
实践表明,CaF2能降低高Al2O3炉渣黏度,但CaF2对高炉内的耐火材料也起损坏作用,因此CaF2的使用一般是在因Al2O3含量高,黏度大引起炉缸不活、炉缸堆积等情况下使用。
在武钢炉渣中Al2O3含量日平均小于18%的情况下,CaF2含量在2.0%左右就可以了。
如果在正常生产中长时间加入CaF2使用,则需要考虑高炉内耐火材料的承受能力等问题。