轨排生产方案
技术交底--轨排生产、轨节拼装

3、钢轨要求
①钢轨应按级别、长度分类堆码,逐根丈量,长度偏差值用白油漆写在轨端头部上。
②钢轨垛基底应平整坚实,垛底架空,各层钢轨之间用方木支垫,方木上下层同位,堆码层数应使钢轨不伤损变形。
4、轨排生产
(1)螺纹道钉锚固
1硫磺砂浆配合比根据气候及材料技术条件,理论重量配合比范围为硫磺:水泥:砂子:石蜡=1:(0.3~0.6):(1~1.5):(0.01~0.03),试验选定的实际重量配合比为硫磺:水泥:砂子:石蜡=1:0.4:1.4:0.02。
2锚固温度控制在130~160℃之间,一孔一次灌完;
3锚固后的螺旋道钉应与承轨槽面垂直,歪斜≯2°;
4螺旋道钉与锚栓孔中心偏离≯2mm;
5道钉圆台高出承轨槽面≯2mm;
6每锚2000根作一组(三个)抗拔试验,抗拔力≮60KN(18MPa)。
7为防止螺旋道钉锈蚀和提高绝缘性能,锚固后应在螺杆上涂以机油,在螺旋道钉圆(方)台下及四周承轨槽表面涂防锈绝缘涂料。涂料的配合比为石油沥青:滑石粉:机油=1:0.25:0.1(熔融绝缘防锈涂料时的温度不能超过200℃)。
②轨排装车时,必须严格按装车计划装车,装车时上下对齐误差不大于5cm,前后误差不大于10cm。如有短轨排,必须放于铺架方向端,与长轨排端头取齐。
③轨排装车发运前,基地应由专人按轨排表及调度计划认真检查轨排次序及备料是否施工注意事项:
1、施工队伍开工后每天需向我部调度人员上报当日完成进度情况和存在的问题。
②轨排在基地存放时,须上下对齐,上下对齐误差不大于10cm,前后对齐误差不大于50cm。
③轨排存放场地应平整,轨枕中部不得承重。
6、轨排装车
①铺轨基地轨排拼装好后,轨节平板车两辆一组,用16T龙门架吊装轨排后两端交叉用钢丝绳呈“8”字形捆固,轨排最下层轨节位于车辆接头处还需用8#铁丝2股将悬空轨枕与其上钢轨绑成一体,防止运输中坠落造成行车事故。
轨道施工方法、工艺及措施

轨道施工方法、工艺及措施一、轨排组装⑴工艺流程图轨排组装施工工艺流程图见下图:⑵工艺流程说明施工准备:按施工设计资料计算轨节表,备齐轨料并堆码于生产线两侧。
摆放轨枕:用10吨龙门吊将轨枕吊到组装台上。
上钢轨:利用两台10吨龙门吊吊轨。
按轨排表计算值用方尺控制钢轨相错量,将钢轨吊到轨枕承轨槽内。
画线方枕:在钢轨内侧用白油漆画线,对线方正轨枕。
散配件、组装:将配件散放在轨枕头上,用专用工具使扣件将钢轨和轨枕组装成轨排。
成品轨排检查:由质检员详细检查轨排质量是否符合标准,不合格的重新处理,并作好原始记录,在每个轨排上配齐鱼尾板及螺栓带帽,并涂油放在轨排接头上,用油漆在轨排铺设终端标注轨枕分中线,轨排号及生产班组。
吊装轨排:用两台10吨龙门吊将成品轨排按铺设顺序吊运装车或存放于轨排场。
⑶质量控制及检测轨枕检查:检查轨枕,如有不合格一律不用,对个别有缺陷的轨枕进行处理。
吊枕时轨枕生产厂标在单侧一致,如有不对的必须逐根掉头,每次自轨枕堆码场起吊不超过10根轨枕。
钢轨检查:吊轨前检查钢轨型号、长度是否与设计一致,直线段钢轨配对时两钢轨偏差在3mm以内,曲线地段按轨排表计划选配缩短轨。
并将钢轨长度正负误差值写在轨头上。
配件检查:各种零件安装齐全,位置正确。
二、铺轨机铺轨⑴艺流程图铺轨机铺轨施工工艺流程图见下图。
⑵工艺流程说明①施工准备复核铺轨面标高和线路中心线,加密线路中心桩;将中心桩引入路肩上并作明显标记;施工设备就位;在铺架基地按轨节表拼装轨节并装车。
②运输轨节到施工地点,立换装龙门架机车推送铺轨机龙门吊及轨节到施工地点。
列车编组如下:机车→龙门架→轨节→轨节→轨节→轨节。
机车推送轨节在距轨道作业1~2km处适当地点,立换装龙门架。
换装龙门架地点选在直线地段或R>1000m以上缓和曲线上,如果条件困难,可将已铺曲线轨道在立换装龙门架位置上拨直,两端拨圆顺,两换装龙门架中心距用粉笔标出位置后,搭设龙门架基础的木垛。
轨排法施工方案

轨排法施工方案轨排法是采用吊装铺设工具轨排并精调合格后,再往模板内浇筑道床板混凝土的无砟轨道施工方法。
工具轨为与设计同轨型的25m长或12.5m长定尺轨,采用与设计相同型号扣件组装工具轨排。
汽车运输轨枕、钢筋等材料沿线卸存,粗调机初调、精调设备调整轨排,GEDO轨道测量系统进行轨排精调,定位后浇筑道床板混凝土。
一、施工准备1、沉降观测评估无砟轨道施工前,必须按照无砟轨道施工标准和无砟轨道铺设评估条件进行路基、桥梁、隧道等轨下基础的质量评估,确保工后沉降、徐变监测及技术评估满足标准要求,具备条件后方可铺设无砟轨道施工。
1)路基质量评估路基填筑完成或施加预压荷载后,保证满足沉降观测和调整期,确定工后沉降评估合格。
逐项核对过渡段施工记录和检查报告,验算过渡段的沉降差异。
工后沉降和沉降差异评估分析满足:路基间隔不少于3个月的两次预测最终沉降的差值不大于8 mm,设计预测总沉降量与通过实测资料预测的总沉降量之差值不宜大于10 mm,预测的路基工后沉降值不大于15mm。
过渡段不同结构物间的预测差异沉降不不应大于5 mm,预测沉降引起沿线方向的折角应小于1/1000时,方可铺设无砟轨道。
2)桥梁质量评估对桥梁变形进行测量与分析,建立沉降观测基准点,在桥梁基础、墩台、梁部架设等施工过程中进行系统的沉降观测,桥涵主体沉降观测期一般不少于6个月。
监测墩台在不同荷载、不同阶段的沉降,分析监测数据求出桥梁墩台沉降过程曲线,预测无砟轨道铺设后墩台的均匀沉降量和相邻墩台的沉降量之差,以确定桥上铺设无砟轨道的时间。
当桥涵间隔不少于3个月的两次预测最终沉降差值不大于8 mm,设计预测总沉降量与通过实测资料预测的总沉降量之差值不宜大于10 mm,可判定沉降满足无砟轨道铺设条件。
箱梁终张拉完成后即开始箱梁徐变上拱监测,桥梁架设后,结合墩台沉降监测,分析箱梁徐变上拱变化,预测每跨梁的最终徐变上拱值,确定无砟轨道施工开始时间,保证无砟轨道施工完成后梁体徐变上拱不大于7mm,终张拉完成时两体跨中弹性变形不宜大于设计值的1.05倍。
机械式单线往复式轨排组装线的设计与生产
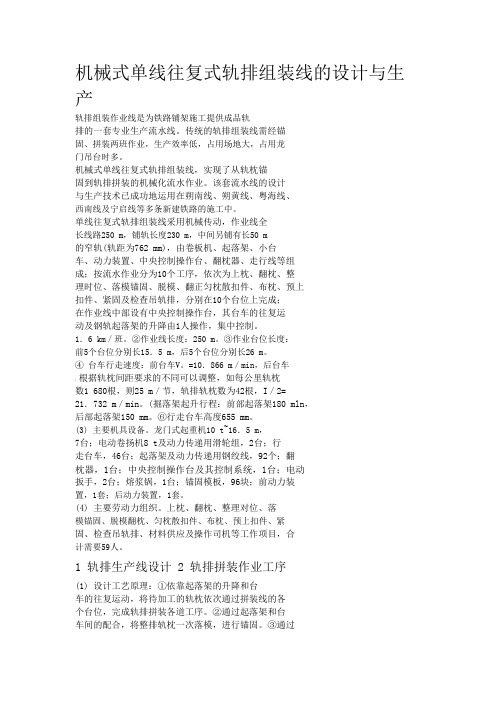
机械式单线往复式轨排组装线的设计与生产轨排组装作业线是为铁路铺架施工提供成品轨排的一套专业生产流水线。
传统的轨排组装线需经锚固、拼装两班作业,生产效率低,占用场地大,占用龙门吊台时多。
机械式单线往复式轨排组装线,实现了从轨枕锚固到轨排拼装的机械化流水作业。
该套流水线的设计与生产技术已成功地运用在朔南线、朔黄线、粤海线、西南线及宁启线等多条新建铁路的施工中。
单线往复式轨排组装线采用机械传动,作业线全长线路250 m,铺轨长度230 m,中间另铺有长50 m的窄轨(轨距为762 mm),由卷板机、起落架、小台车、动力装置、中央控制操作台、翻枕器、走行线等组成;按流水作业分为10个工序,依次为上枕、翻枕、整理时位、落模锚固、脱模、翻正匀枕散扣件、布枕、预上扣件、紧固及检查吊轨排,分别在10个台位上完成;在作业线中部设有中央控制操作台,其台车的往复运动及钢轨起落架的升降由1人操作,集中控制。
1.6 km/班。
②作业线长度:250 m。
③作业台位长度:前5个台位分别长15.5 m,后5个台位分别长26 m。
④台车行走速度:前台车V。
=10.866 m/min,后台车:根据轨枕间距要求的不同可以调整,如每公里轨枕数1 680根,则25 m/节,轨排轨枕数为42根,I/2=21.732 m/min。
(掘落架起升行程:前部起落架180 mln,后部起落架150 mm。
⑥行走台车高度655 mm。
(3) 主要机具设备。
龙门式起重机10 t~16.5 m,7台;电动卷扬机8 t及动力传递用滑轮组,2台;行走台车,46台;起落架及动力传递用钢绞线,92个;翻枕器,1台;中央控制操作台及其控制系统,1台;电动扳手,2台;熔浆锅,1台;锚固模板,96块;前动力装置,1套;后动力装置,1套。
(4) 主要劳动力组织。
上枕、翻枕、整理对位、落模锚固、脱模翻枕、匀枕散扣件、布枕、预上扣件、紧固、检查吊轨排、材料供应及操作司机等工作项目,合计需要59人。
轨排生产安全管理范本(2篇)
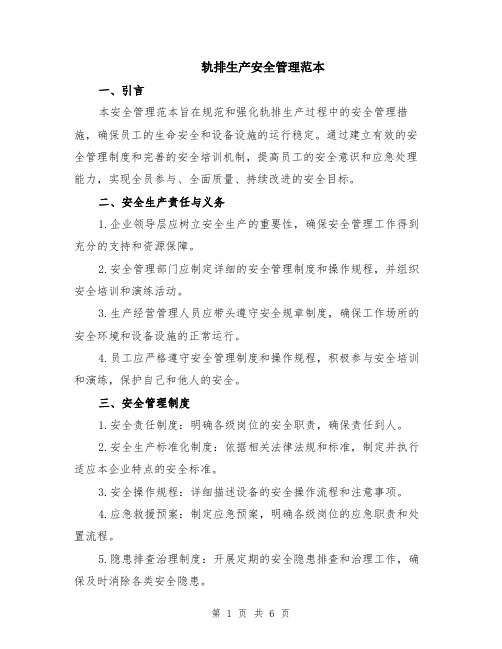
轨排生产安全管理范本一、引言本安全管理范本旨在规范和强化轨排生产过程中的安全管理措施,确保员工的生命安全和设备设施的运行稳定。
通过建立有效的安全管理制度和完善的安全培训机制,提高员工的安全意识和应急处理能力,实现全员参与、全面质量、持续改进的安全目标。
二、安全生产责任与义务1.企业领导层应树立安全生产的重要性,确保安全管理工作得到充分的支持和资源保障。
2.安全管理部门应制定详细的安全管理制度和操作规程,并组织安全培训和演练活动。
3.生产经营管理人员应带头遵守安全规章制度,确保工作场所的安全环境和设备设施的正常运行。
4.员工应严格遵守安全管理制度和操作规程,积极参与安全培训和演练,保护自己和他人的安全。
三、安全管理制度1.安全责任制度:明确各级岗位的安全职责,确保责任到人。
2.安全生产标准化制度:依据相关法律法规和标准,制定并执行适应本企业特点的安全标准。
3.安全操作规程:详细描述设备的安全操作流程和注意事项。
4.应急救援预案:制定应急预案,明确各级岗位的应急职责和处置流程。
5.隐患排查治理制度:开展定期的安全隐患排查和治理工作,确保及时消除各类安全隐患。
四、安全培训与教育1.新员工培训:对新员工进行安全培训,包括安全规章制度、紧急救援措施等方面的知识。
2.定期培训:对所有员工进行定期的安全培训,包括事故案例分析、应急演练等内容。
3.岗位培训:根据不同岗位的特点,进行专业技能培训和安全操作培训。
4.安全宣传教育:通过各种渠道宣传安全知识和安全理念,提高员工的安全意识和防范能力。
五、安全防护与控制措施1.场所安全:保持生产场所的整洁和时刻清洁,并定期进行安全巡查,及时消除各类安全隐患。
2.设备设施安全:制定设备设施的管理规范,定期进行设备巡检和维护,确保设备的安全性能。
3.环境保护措施:对生产过程中产生的废水、废气和固体废物进行有效处理和管理,保护环境。
4.个体防护措施:为员工提供适当的个体防护装备,如安全帽、防护眼镜、防护服等。
轨道工程施工方案

第一节轨道工程施工一、概述本标段为火车站,新铺线路全长99.032km,拆除线全长99.032km,4个岔心,2个长50m的安全车挡。
新建货运到发线。
二、施工方案根据本标段铺轨工程量情况及标段总工期、阶段工期的要求,结合工程分布及线路情况,线路采用人工铺轨作业。
站场路基完成后,进行轨道工程,道岔施工,根据实际情况合理安排,统筹兼顾。
三、施工技术措施(一)铺设轨排技术措施1、轨排生产严把质量关,不合格的轨料不准上路。
2、轨排生产要认真执行配轨检尺和质量验收制度,每道工序皆要层层把关,为铺设提供合格的轨排。
3、混凝土轨枕螺旋道钉锚固每2000根混凝土枕做一组(三个钉)抗拨试验,每个道钉抗拨力不小于60KN。
4、铺轨前,由线路复测组提前对路基、中桩、底碴平整度、限界净空等进行详细检查,符合要求才准施工。
5、铺轨时,路基面要预铺底碴并有中心桩;轨排中心与中心桩尽量对正,误差不超过标准要求,经检查合格后方准继续铺轨。
6、线路维修确保轨道远视直线顺直无硬弯;曲线圆顺,无反弯或鹅头,无反超高。
7、钢轨接头配件及其联结配件均涂油,避免生锈及腐蚀。
(二)工地接触焊、铝热焊施工技术措施1、在气温低于0℃时不宜进行工地焊接。
气温低于10℃时,焊轨前两轨端应加热到10℃以上,焊后应采取保温措施。
2、根据轨枕和扣件类型适当垫高待焊轨头后方的钢轨,以确保焊头轨顶平直度。
承受拉力的焊缝,在其轨温高于300℃时应当保压。
3、作业车焊完后,应用相应机具对钢轨焊缝进行正火、打磨、平直度检查和超声波探伤等。
(三)人工整道技术措施作业前,要确认捣固器、严格按照设计要求振捣密实,及时补砟。
(四)轨道整理技术措施无缝线路及道岔的整理作业技术措施高温时不应安排影响线路稳定性的整理作业。
高温时可安排矫直钢轨、整理扣件、整理道床外观、钢轨打磨等作业。
进行无缝线路整理作业,必须掌握轨温,观测钢轨位移,分析锁定轨温变化,按实际锁定轨温,根据作业轨温条件进行作业,严格执行“作业前,作业中,作业后测量轨温”制度,并注意做好以下各项工作:在整理地段按需要备足道碴;起道前应先拨正线路方向;起、拨道机不得安放在铝热焊缝处;扒开的道床应及时回填、夯实。
高铁无砟轨道轨排施工方案

高铁无砟轨道轨排施工方案1. 引言高速铁路作为现代交通运输的一种重要方式,其建设需要依靠高效、稳定的轨道系统。
而无砟轨道作为高速铁路的关键组成部分,对于保证列车的稳定性和行车安全至关重要。
因此,无砟轨道轨排施工方案的设计与实施对于高速铁路建设具有重要意义。
本文将针对高铁无砟轨道轨排施工方案进行详细介绍,包括施工设计原则、施工流程和施工注意事项。
2. 施工设计原则2.1 环境保护原则在无砟轨道轨排施工过程中,应充分考虑对环境的保护,尽量减少对周围生态环境的破坏。
施工方案应遵循国家和地方有关环境保护的法律法规,采取有效的措施来减少噪音、颗粒物和废水的排放。
2.2 安全原则无砟轨道轨排施工过程中,安全第一是至关重要的原则。
施工方案应充分考虑施工人员的安全保障,合理规划工作区域和施工时间,确保施工人员的安全。
2.3 资源利用原则无砟轨道轨排施工过程中,应充分利用现有资源,尽量减少对自然资源的消耗。
合理利用土方、砂石等材料,优化施工方案,提高资源利用率。
3.1 前期准备在施工前期,需进行充分的准备工作。
包括:•编制施工方案:依据设计要求,制定无砟轨道轨排施工方案,并获得相关部门的批准。
•组织施工人员:安排施工人员的组织结构和工作任务,确保施工人员的专业素质和安全意识。
•采购材料和设备:根据施工方案,采购所需的材料和设备,并进行验收和入库管理。
3.2.1 轨道测量和标定首先,需要进行轨道测量和标定工作。
通过使用专业的测量设备,准确测量轨道的位置和高程,并进行标定,为后续的轨道安装工作提供准确的基础数据。
3.2.2 地基处理地基处理是保证无砟轨道稳定性的重要工作。
首先检查地基的承载能力,确保其满足设计要求。
然后进行地基处理工作,包括地基夯实、填筑和强夯等操作,以提供良好的地基条件。
3.2.3 轨道安装在地基处理完毕后,进行轨道的安装工作。
首先需要进行轨道基座的安装,将基座与地基牢固连接。
然后按照设计要求,安装轨道的轨排,确保其水平度和防护。
02轨排生产施工作业指导书

厦门市轨道交通1号线一期工程轨道工程编号:轨排生产施工作业指导书单位:编制:审核:批准:2016年3月26日发布 2016年3月26日实施评审记录表作业文件修改记录单轨排生产施工作业指导书1、适用范围本作业指导书适用中铁十一局集团厦门市轨道交通1号线一期工程轨道工程施工2标段施工项目部铺轨基地轨排生产作业。
2、作业准备2.1、内业技术准备施工前技术人员应对施工图纸及相关的通用图纸和规范进行认真阅读、熟悉掌握轨排组装作业的设计要求和验收标准,制定施工作业方案、编制轨节表、安全保证措施及应急预案,对施工作业人员进行岗前技术、安全培训和考核,合格后方可上岗。
2.2、外业技术准备施工作业中所涉及的各种外部技术数据收集齐全。
正式施工前工艺性试验施工完毕并形成总结报告。
3、技术要求3.1检查支撑架是否有变形现象,不合格的支撑架一律剔除,短轨枕轨排支撑架每排安装8榀。
3.2安装时候确保轨下橡胶垫板居中,不得窜出轨底。
3.3扣件紧固时扭矩达到要求,弹条安装不得过紧或过松。
3.4轨距、轨枕间距等达到设计要求4、施工程序与工艺流程4.1施工程序轨排生产作业共分以下8道程序:①、依据轨排生产表取相应数量的轨枕、扣配件、钢轨②、散布扣件于轨枕上③、安放橡胶垫板II及铁垫板、拧入螺旋道钉并用专用工具紧固扣件④、安放橡胶垫板Ⅰ、吊装钢轨⑤、划分轨枕位置并匀枕⑥、组装扣件、安装弹条⑦、安放支撑架、轨距拉杆⑧、技术员自检并报监理验收4.2工艺流程5、施工要求5.1施工准备提前规划好轨排组装使用的材料,钢轨、扣件、轨枕等所使用的场地,所有进场材料都经过报审合格后方可使用,轨排拼装技术交底、轨节表编制并下发交底。
轨排拼装使用的弹条扳手、电动扳手、黄油、扭力扳手到位。
5.2施工工艺1、依据轨排生产表取相应数量的轨枕、扣配件、钢轨。
1.1技术人员下发配轨表,施工队根据当天的生产任务量,从材料管理员处领取当天所用的轨排组装材料。
(1)材料堆码要求①钢轨的堆放一般选择地面、且龙门吊能够调运的区域整齐堆放,每层轨道之间必须垫置方木,方木大小为100mm×100mm,垫木的长度必须超过钢轨堆放两侧各100mm,以防钢轨倾斜伤人,堆放高度不得超过五层,堆放必须单头对齐、标签在一头。
2-2 组合式轨排法
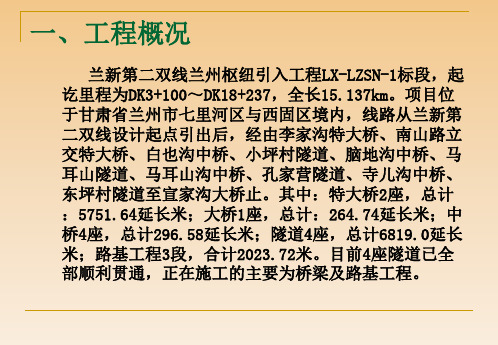
2.4道床板伸缩缝及假缝结构
路基道床板每隔3.9m设一道宽10mm,深65mm的假缝, 采用树脂嵌缝胶填充。单元道床板之间设30mm的伸缩缝 ,中层设置¢30无粘结护套式传力杆,传力杆以下采用 聚乙烯泡沫板填充,传力杆以上部分采用锯齿形聚乙烯 泡沫板填充,并以树脂防水嵌缝胶封闭。
施工计划安排
标段内无砟轨道施工主要分为两个阶段分别进行即:( 1)DK11+650~DK17+968段隧道工程;(2)DK3+100~ DK11+650段路基、桥梁、隧道及剩余DK11+650~ DK17+237段桥梁工程。计划施工工期为2013年6月1日~ 2013年10月30日,2014年2月1日~2014年4月1日共计7 个月。
一、工程概况
兰新第二双线兰州枢纽引入工程LX-LZSN-1标段,起 讫里程为DK3+100~DK18+237,全长15.137km。项目位 于甘肃省兰州市七里河区与西固区境内,线路从兰新第 二双线设计起点引出后,经由李家沟特大桥、南山路立 交特大桥、白也沟中桥、小坪村隧道、脑地沟中桥、马 耳山隧道、马耳山沟中桥、孔家营隧道、寺儿沟中桥、 东坪村隧道至宣家沟大桥止。其中:特大桥2座,总计 :5751.64延长米;大桥1座,总计:264.74延长米;中 桥4座,总计296.58延长米;隧道4座,总计6819.0延长 米;路基工程3段,合计2023.72米。目前4座隧道已全 部顺利贯通,正在施工的主要为桥梁及路基工程。
轨道排架现场存放
组合式轨道排架
工具轨
排架支腿
托梁
排架支腿
工具轨
ห้องสมุดไป่ตู้
托梁
轨向锁定器
组合式轨道排架断面
轨排组装方案及工艺流程

轨排组装方案及工艺流程英文回答:Assembling a track system and designing the corresponding process flow requires careful planning and consideration. In this response, I will outline a potential assembly scheme and the associated manufacturing processfor a track system.First, let's discuss the assembly scheme. The track system consists of various components, such as rails, brackets, and connectors. To assemble these components, I would propose the following steps:1. Preparation: Gather all the necessary components and tools required for the assembly process. This may include rails, brackets, connectors, screws, and a screwdriver.2. Rail installation: Begin by attaching the rails to the designated area. This can be done by aligning the railwith the mounting holes and securing it in place using screws. Repeat this step for all the rails in the track system.3. Bracket installation: Once the rails are in place, attach the brackets to the rails. The brackets provide support and stability to the track system. Use screws to secure the brackets to the rails, ensuring they are properly aligned and tightened.4. Connector installation: Connectors are used to join multiple sections of the track system together. Install the connectors at the designated points, ensuring they are securely attached to both the rails and brackets. This step may require the use of additional tools, such as a wrench or pliers, to tighten the connectors.5. Quality check: After the assembly is complete, conduct a thorough quality check to ensure all components are properly installed and secured. This may involve inspecting the tightness of screws, alignment of rails, and overall stability of the track system.Now, let's move on to the manufacturing process flow. The process flow outlines the sequence of steps required to assemble the track system. Here is a potential process flow for the track system assembly:1. Component preparation: Gather all the necessary components, including rails, brackets, connectors, and screws.2. Rail installation: Attach the rails to the designated area using screws.3. Bracket installation: Securely attach the brackets to the rails using screws.4. Connector installation: Install the connectors at the designated points, ensuring they are securely attached to both the rails and brackets.5. Quality check: Inspect the assembled track systemfor any defects or issues.6. Packaging: Pack the track system in suitable packaging materials to ensure safe transportation and storage.7. Shipping: Arrange for the track system to be shipped to the desired destination.中文回答:轨排组装方案及工艺流程。
GPZZ轨排生产作业指导书
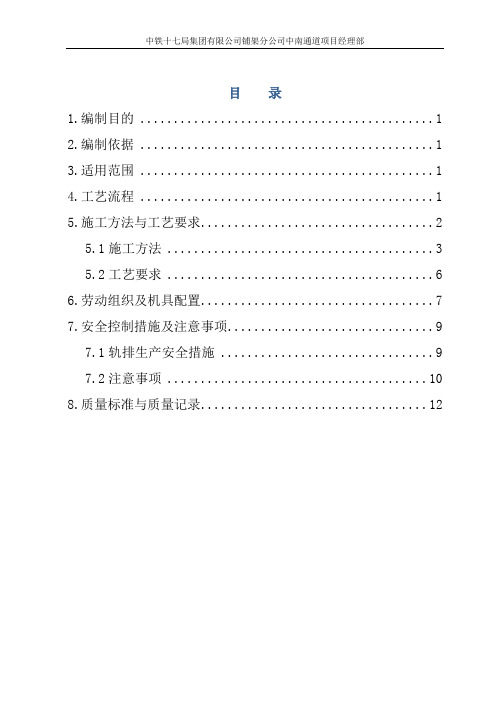
目录1.编制目的 (1)2.编制依据 (1)3.适用范围 (1)4.工艺流程 (1)5.施工方法与工艺要求 (2)5.1施工方法 (3)5.2工艺要求 (6)6.劳动组织及机具配置 (7)7.安全控制措施及注意事项 (9)7.1轨排生产安全措施 (9)7.2注意事项 (10)8.质量标准与质量记录 (12)山西中南部铁路通道ZNTJ-20标轨排生产作业指导书1.编制目的为规范轨排生产施工作业,指导施工人员进行标准化作业,确保轨排的施工质量满足规范验标要求,编制本作业指导书。
2.编制依据2.1《铁路轨道工程施工质量验收标准》(TB10413-2003);2.2《铁路轨道工程施工安全技术规程》(TB10305-2009);2.3《客货共线铁路轨道工程施工技术指南》(TZ201-2008);2.4 GPZZB轨排生产线相关技术文件。
3.适用范围本指导书适用于山西中南部铁路通道ZNTJ-20标段正线轨排生产作业。
4.工艺流程山西中南部铁路通道ZNTJ-20标段轨道工程,正线上行线采用架桥机铺设25m短轨排作为架桥机走行线,之后进行500m长钢轨换铺,轨排采用GPZZB 型轨排组装生产线生产。
轨排生产施工工艺流程见图4-1,图4-1 轨排生产施工工艺流程图5.施工方法与工艺要求5.1施工方法5.1.1轨排组装施工方法及工艺原理轨排在铺架基地内集中组装后运往工地使用架桥机铺设。
轨排组装是利用GPZZB 型轨排组装生产线进行单线往复反锚作业方法,其生产流程按工序和作业时间大致相等的原则排布,可分为一次翻枕布枕、螺纹道钉锚固、二次翻枕匀枕、上钢轨、上扣件、组装扣件、紧固螺栓、轨排检验及吊放等八道工序。
其基本的工作原理是利用液压升降平台升降动作产生的高度差和工作台车交替往复运动之间的配合来完成轨排的流水组装。
生产时,升起液压升降平台,由各工作台位上的操作人员进行基本工序的作业;而后降下升降平台,操作工作的台车前进,降落在其上的半成品轨排及配件等依次运送至下个台位,到位后升起平台开始作业,同时工作台车返回出发位置,整套动作周而复始循环作业即可完成轨排的流水组装。
正线施工方案及技术措施(轨排架轨法)综述
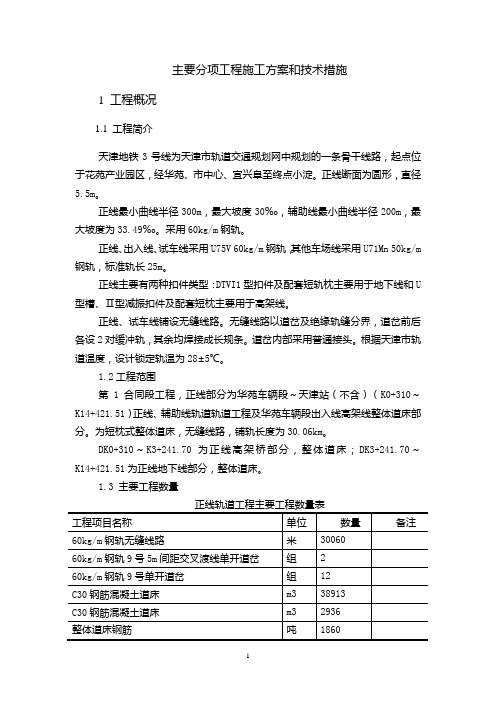
主要分项工程施工方案和技术措施1 工程概况1.1 工程简介天津地铁3号线为天津市轨道交通规划网中规划的一条骨干线路,起点位于花苑产业园区,经华苑、市中心、宜兴阜至终点小淀。
正线断面为圆形,直径5.5m。
正线最小曲线半径300m,最大坡度30‰,辅助线最小曲线半径200m,最大坡度为33.49‰。
采用60kg/m钢轨。
正线、出入线、试车线采用U75V 60kg/m钢轨,其他车场线采用U71Mn 50kg/m 钢轨,标准轨长25m。
正线主要有两种扣件类型:DTVI1型扣件及配套短轨枕主要用于地下线和U 型槽、Ⅱ型减振扣件及配套短枕主要用于高架线。
正线、试车线铺设无缝线路。
无缝线路以道岔及绝缘轨缝分界,道岔前后各设2对缓冲轨,其余均焊接成长规条。
道岔内部采用普通接头。
根据天津市轨道温度,设计锁定轨温为28±5℃。
1.2工程范围第1合同段工程,正线部分为华苑车辆段~天津站(不含)(K0+310~K14+421.51)正线、辅助线轨道轨道工程及华苑车辆段出入线高架线整体道床部分。
为短枕式整体道床,无缝线路,铺轨长度为30.06km。
DK0+310~K3+241.70为正线高架桥部分,整体道床;DK3+241.70~K14+421.51为正线地下线部分,整体道床。
1.3 主要工程数量2 工程重点分析及对策2.1 施工复测和定位放线施工复测、基标测设是轨道铺设的基准,尤其是基标测设的精度将直接影响轨道铺设的施工质量。
如何保证线路复测和基标测设的精确度,满足施工需要,是轨道铺设工程施工的重点。
2.2 整体道床单开道岔及交叉渡线道岔施工整体道床单开及交叉渡线道岔结构复杂,施工定位精度要求高,现场浇筑混凝土跨度大,整体质量控制难度大,铺设周期长,是制约轨道工程工期和质量控制的重点。
2.3 钢轨焊接施工钢轨焊接是保证轨道几何平顺性和内在质量的关键,焊前的型式试验、焊接过程中的参数控制、焊后处理等各个工序过程都是保证钢轨焊接质量的重点环节。
轨排组装方案及工艺流程

轨排组装方案及工艺流程英文回答:As an expert in manufacturing processes, I can provide you with a detailed assembly scheme and process flow for a track assembly. The track assembly is a critical component in various industries such as automotive, construction, and agriculture. It consists of multiple parts, including the track chain, track shoe, track link, and track roller.Firstly, let's discuss the assembly scheme. The track assembly can be divided into several sub-assemblies, which will then be combined to form the final product. The sub-assemblies can include the track chain assembly, track shoe assembly, and track roller assembly. Each sub-assembly can be manufactured separately and then brought together for final assembly.For the track chain assembly, it involves attaching the track links to the track chain. This can be done by using apress-fit method, where the links are pressed onto the chain using hydraulic or mechanical force. The track chain assembly can also include the installation of seals and lubrication points.The track shoe assembly involves attaching the track shoes to the track chain. The shoes are typically bolted or welded to the chain. The assembly process may also involve the installation of wear pads or rubber pads on the track shoes to improve traction and reduce wear.The track roller assembly includes attaching the track rollers to the track chain. The rollers are usually mounted on a shaft and secured with bolts or pins. The assembly process may also include the installation of seals and lubrication points.Now let's move on to the process flow. The assembly process can be divided into several steps, including preparation, sub-assembly, final assembly, inspection, and packaging.In the preparation stage, all the required parts and tools are gathered. The parts are checked for quality and any defects are addressed. The assembly area is also prepared, ensuring that it is clean and well-organized.Next, the sub-assembly stage begins. Each sub-assembly, such as the track chain assembly, track shoe assembly, and track roller assembly, is manufactured separately. This can involve various processes such as pressing, welding, and bolting.Once all the sub-assemblies are completed, the final assembly stage begins. The track chain, track shoe, and track roller sub-assemblies are brought together and assembled into the final product. This can involve attaching the track shoes to the track chain and securing the track rollers.After the final assembly, the track assembly undergoes inspection to ensure its quality and functionality. This can involve visual inspection, measurement, and functional testing. Any issues or defects are addressed and corrected.Finally, the track assembly is packaged for shipment or storage. This can involve protective packaging to prevent damage during transportation.中文回答:作为一个制造工艺的专家,我可以为您提供一个详细的轨排组装方案和工艺流程。
2024年轨排生产安全管(2篇)

2024年轨排生产安全管轨排生产、龙门吊起吊作业,必须在听到指挥口令后方可起吊行驶。
起吊前,必须检查钢丝绳连接处是否牢固,电动葫芦及各器具部件是否完好。
对起吊钢丝表面磨损或锈蚀直径的8%,或断丝超过6条,不得使用。
起吊物体物体时地面指挥及工作人员必须离开起吊钩垂物下面,以防砸伤、碰伤事故。
轨枕锚固、硫磺熔浆时,施工人员要注意轨枕两端残留钢筋挂伤,熔浆时,以防烫伤。
熔浆温度不得大于180℃,以免燃烧起火,施工人员应带好劳保防护用品.轨排生产散枕和散布扣件应有工作台车停稳后进行配件放稳,方可撒手,防止滚落伤人。
对上扣件、打电动板手工序,手拧预带螺帽应拧入丝以上,打电动板手要防止电线破皮漏电,接头脱落,经常检查,发现破损漏电及时包扎处理,以防触电事故发生。
轨排基地线路、道岔和道路经常有检查、维修、养护,保持一定标准,电路要有专人检查维修,保持良好状态。
轨道材料的堆码,应分门别类,整齐划一,堆码钢轨材料底层和各层之间应支垫平稳、排列整齐,垫木厚度不小于25mm,各层垫木应垂直同位,其间距不得大于5m,堆码层数可根据地基坚实程度,以不致于造成钢轨压伤变形和堆码方式而定。
对轨枕材料的堆码,高度要适宜,底层支垫要稳固,上下保持同位,确保稳固,堆放木枕区域应有防火措施和防火设施,并与生活区分开。
机械吊装应谨防触电、翻车,特殊情况,采用两台吊车同时吊一物体时,应有可行的安全措施,并报经上级批准,指定专人负责指挥,其起吊重量不得超过这两台吊车允许吊重总和的75%,否则严禁使用。
特别是汽车吊装,严禁吊重行走和左右摇摆,吊重下面严禁站人或有人行走,施工人员必须按规定穿带防护用品。
轨排生产、装车、卸车及运轨安全注意事项一、轨排生产(一)吊运各种材料要做到:1、严禁经过人上方,作业人员应避免钻入吊物下。
2、吊运轨排时禁止在轨排上站人。
3、吊物千斤绳应先择大于2.5倍安全系数。
如果用钢丝卡联接,要经常检查是否牢固。
4、电动葫芦制动器要保证制动良好,如遇制动不良,要立即停下调整修理。
铁路轨排生产,铺设,大机养道

所谓轨道铺设是指将轨道铺设在已完成并达到设计强度的路基、桥梁、隧道等工程上的工作。
轨道铺设能否如期完成,直接影响铁路交付运营的期限。
正常铺轨第一节准备工作铺轨工程是一项时间紧、任务重、劳动强度大的多工种联合作业。
因此,必须事先作好以下各项铺轨前的准备工作,使铺轨工程能顺利进行。
一、铺轨施工文件轨道工程开始施工前,线下路基、桥涵、隧道等主体工程及线路复测应已完成,此时形成的资料包括了平、纵断面及建筑物变更设计的重要内容,是铺轨工程重要、可靠的指导文件,应在建设单位的主持下,向有关施工单位办理接受。
施工单位所具备的施工设计文件和有关基础工程竣工资料,包括:车站平面图、隧道表、桥梁表(含孔跨)、架梁岔线位置表、曲线表、坡度表、水准基点表、断链表及线路情况说明书等。
根据设计文件要求、有关基础工程竣工资料、全线指导性施工组织设计、规定的铺轨总工期、有关重点工程的施工方案以及施工单位自身的铺轨能力,编制实施性施工组织设计,指导施工。
二、筹建铺轨基地铺轨基地是新建铁路的一项临时性工程,是铺轨材料的装卸、存放、轨料加工以及轨排组装、列车编组、发送的场所,是铺轨工程的后方基地。
铺轨基地在筹建时,必须全面考虑,统一规划,尽量与永久性工程相结合,做到投资少、占地少、上马快,作业方便,并使铺轨列车调度灵活,充分发挥基地的生产潜力。
(一)铺轨基地的任务铺轨基地主要负责储存轨料、组装轨排和道岔,并将轨排源源不断地供应前方,保证不间断地铺轨。
对于新建铁路有时铺轨基地也兼做部分架梁的准备工作,如存梁等。
1.储存轨料(1)接收各种轨料:钢轨、轨枕、配件及道岔材料等;(2)对各种轨料负责检查、整理、堆码及储存,轨料分别堆置后,应树牌标明规格、类型、数量;(3)对运入的轨料进行必要的加工,如必要的锯轨、钻螺栓孔等;(4)向轨排组装车间输送整理好的轨料。
2.组装轨排和道岔(1)将轨料场送入的各种轨料堆放到指定地点,或整车停放在指定地点;(2)组装轨排和道岔;(3)按铺轨进度及线路技术要求,编配轨排、道岔列车,捆扎牢固,装齐配件,供应前方铺设;(4)储存已组装好的轨排和道岔。
最新技术交底--轨排生产、轨节拼装
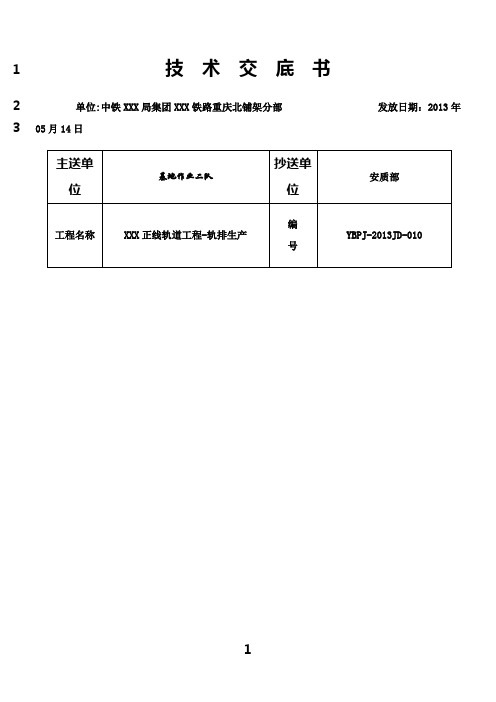
各种材料均不得混有杂物。
三、施工方法及流程:
四、施工要求
1、轨排生产前现场技术负责人应对轨排计算表进行复核,如有异议,及时反馈工程部。
2、轨枕要求
(1)轨枕质量检查
① 轨枕凡是有环裂、掉块露筋、钉孔、承轨槽面和挡肩损坏未经修好者,锚固孔尺寸偏差超过允许误差范围者,不得使用。
② 轨枕吊放应轻提轻放,逐层散布,以免损坏轨枕。
③ 轨枕锚固孔应保持干燥、清洁,孔内橡皮塞、污泥、杂物必须清除干净。
编制
审核
接收人
(2)堆码要求
① 钢筋砼枕堆码场地应平实,堆码高度不宜超过14层,各层轨枕均系上、下同位平行排列,不得交错,轨枕中部不得承重,承轨槽处垫以宽度不小于5cm的方木,其厚度高出挡肩顶面不小于2cm。
②轨排装车时,必须严格按装车计划装车,装车时上下对齐误差不大于5cm,前后误差不大于10cm。如有短轨排,必须放于铺架方向端,与长轨排端头取齐。
③轨排装车发运前,基地应由专人按轨排表及调度计划认真检查轨排次序及备料是否正确,并与铺架一队交接,作好记录。
五、施工注意事项:
1、施工队伍开工后每天需向我部调度人员上报当日完成进度情况和存在的问题。
2、施工时施工队应做好质量自检工作,当上道工序施工完后,应经我部现场质检工程师检查认可后方可进入下道工序施工;
3、交底中未明确的事宜,施工单位应及时与我部沟通,在取得书面认可后,方可进行下道工序的施工,工程量以工程完工后实际验收量为准。
编制
审核
接收人
② 同一型号的枕木应集中堆放在同一位置,以免混淆。
3、钢轨要求
① 钢轨应按级别、长度分类堆码,逐根丈量,长度偏差值用白油漆写在轨端头部上。
- 1、下载文档前请自行甄别文档内容的完整性,平台不提供额外的编辑、内容补充、找答案等附加服务。
- 2、"仅部分预览"的文档,不可在线预览部分如存在完整性等问题,可反馈申请退款(可完整预览的文档不适用该条件!)。
- 3、如文档侵犯您的权益,请联系客服反馈,我们会尽快为您处理(人工客服工作时间:9:00-18:30)。
轨排生产方案及施工工艺
一、生产方案
铺轨施工过程中采用铺轨机或桥机铺设线路,然后换铺长钢轨的施工方法。
工具轨节钢轨采用50kg/m- 25m再用轨,长轨为P60轨为了避免换长轨时扣配件的倒运,对P50工具轨排直接采用P60扣配件,这样在钉联过程中将9mm厚小胶条放置于轨枕挡肩和挡板座间即可满足施工要求,扣配件具体配置如下:
采用1667根/公里配置,枕木间距值a=b=c=600mm,设置了A 型轨排、B型轨排、C三种类型轨排。
见下图
41×0.6
40×0.6
41×0.6
二、施工工艺(轨排生产线)
吊布轨枕:机车将装有轨枕的车辆对好位,摘钩离去后,利用龙门吊将车辆上的轨枕分垛放到作业线台上,并分层布开。
吊轨枕时,每钩挂吊轨枕控制在20~24根(每层4根);钢筋混凝土枕层间的垫木集中堆码整齐。
翻枕:人工利用撬棍和缓冲木条配合翻动轨枕,使其底面向上,重复以上过程,完成翻枕作业。
硫磺锚固:项目为Ⅲ(A)型轨枕,采用固定模板反锚。
先将轨枕拨正落入模板槽内,对准钉孔,将螺旋道钉倒插进钉孔内,然后灌注熬制好的硫磺砂浆。
熔制锚固砂浆时,按选定的配合比,称好各材料的一次熔制量,先倒入砂子加热到100~120℃后,将水泥倒入加热到130℃,最后加入硫磺和石蜡,继续搅拌加热到160℃,溶浆由稀变稠成液胶状时即可放入保温锅保温待用,同时不断搅拌,使砂子不致离析;固定模板及时清扫,使轨枕承轨槽与模板密贴,以防漏浆;螺旋道钉要保持干燥并倒插入钉孔内;灌浆量控制在覆盖孔内道钉≮20mm。
轨枕翻正:用机械翻枕器自动按顺序将轨枕翻正,并将承轨槽面、螺旋道钉四周多余的砂浆铲除,清扫干净。
匀枕:作业前,根据轨排表所标明的轨枕铺设标准,调整好匀枕小车间距,轨排生产时,轨枕放落在小台车上后,进行必要的方枕,再完成匀枕作业。
吊放钢轨:提前对钢轨进行检尺并在轨头处标识,吊放时按轨排表所标钢轨长度及相错量,配对吊放在承轨槽内,用方尺方好接头,
画出轨枕间距印,方正轨枕,用油漆点在钢轨内侧轨腰上;轨排编号按顺序标在铺轨前进方向第1根枕上。
曲线缩短轨的吊放,首先以轨排表标明的铺轨前进方向确定出曲线走向,分出上下股,接头方正应在铺轨前进方向一端;曲线轨排接头相错量以上股为准。
散放安装扣件:按轨排表注明的扣件类型及号码配置,依次进行散放和安装,普通扣件在安装扣件前,先将轨下垫板调正,然后用撬棍配合,将扣件落槽,安装标准,带上帽后,手拧3扣螺纹以上。
紧固螺帽:对接头及轨枕细方后,确认轨下垫板及扣件安放正确,普通扣件再用电动搬手拧紧全部螺帽。
检查:轨排拼装好后,质检人员对轨排进行全面细致的检查,对有缺陷的轨排进行整改,同时对两端轨头进行涂油并配放鱼尾板及螺栓,校对轨排编号,确认质量符合标准后,方准出场。
轨排吊装:将拼装好的轨排按铺轨顺序吊装上车(或吊放于轨排存放场),并对装够轨排的车辆按有关规定进行加固。
起吊轨排时,应选准吊点,尽量减小轨排的挠度和摆动幅度。
完成一节成品轨排后,往复流水作业依次进行所需轨排的生产。
轨排生产工艺流程图
0010100131302020022
始时间时差成时间
施工工艺网络图。