品质改善手法
品质7大手法
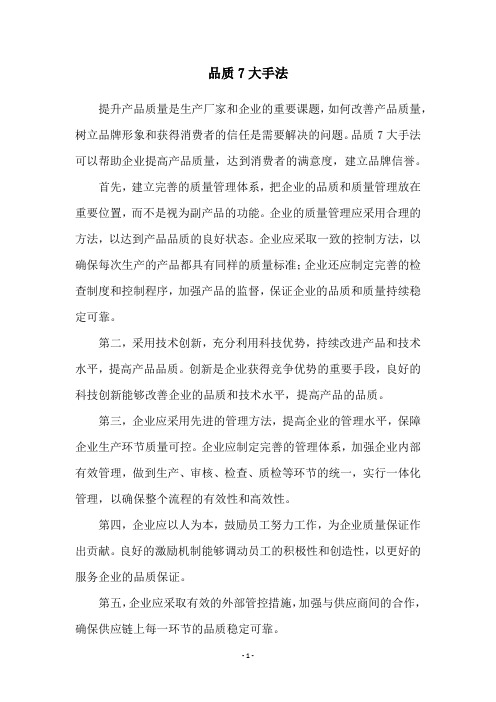
品质7大手法提升产品质量是生产厂家和企业的重要课题,如何改善产品质量,树立品牌形象和获得消费者的信任是需要解决的问题。
品质7大手法可以帮助企业提高产品质量,达到消费者的满意度,建立品牌信誉。
首先,建立完善的质量管理体系,把企业的品质和质量管理放在重要位置,而不是视为副产品的功能。
企业的质量管理应采用合理的方法,以达到产品品质的良好状态。
企业应采取一致的控制方法,以确保每次生产的产品都具有同样的质量标准;企业还应制定完善的检查制度和控制程序,加强产品的监督,保证企业的品质和质量持续稳定可靠。
第二,采用技术创新,充分利用科技优势,持续改进产品和技术水平,提高产品品质。
创新是企业获得竞争优势的重要手段,良好的科技创新能够改善企业的品质和技术水平,提高产品的品质。
第三,企业应采用先进的管理方法,提高企业的管理水平,保障企业生产环节质量可控。
企业应制定完善的管理体系,加强企业内部有效管理,做到生产、审核、检查、质检等环节的统一,实行一体化管理,以确保整个流程的有效性和高效性。
第四,企业应以人为本,鼓励员工努力工作,为企业质量保证作出贡献。
良好的激励机制能够调动员工的积极性和创造性,以更好的服务企业的品质保证。
第五,企业应采取有效的外部管控措施,加强与供应商间的合作,确保供应链上每一环节的品质稳定可靠。
第六,把握市场变化,积极调整产品结构,及时调整产品质量,满足市场变化的需求。
企业应根据市场变化,コ持续调整产品质量,创造出新的产品,提高产品品质,满足消费者的需求。
第七,加强对市场的把握,强化客户服务,满足客户的要求和需求,保证企业的品质服务水平。
企业应注重客户服务,深入到客户的需求,吸引客户的认可度,从而获得客户的信任和支持。
以上就是企业提高品质的7大手法,它们可以有效地改善企业的品质管理、技术创新、产品管理、人力资源、外部管控、市场管理和客户服务等环节,从而达到客户满意度,树立品牌信誉的目的。
然而,企业改善品质并不容易,还需要全体员工的积极配合,加强对品质管理的关注,为客户提供满意的产品和服务,从而实现企业的经济效益。
27种常用的质量管理手法

27种常用的质量管理手法质量管理是现代企业的核心竞争力,而质量管理手法是实现良好质量的关键。
以下是27种常用的质量管理手法:1. PDCA循环法PDCA循环法,即计划 - 执行 - 检查 - 行动,是一种反复进行的持续改进流程。
2. 5S管理法5S管理法,即整理 - 整顿 - 清洁 - 清理 - 保持,是一种基本的现场管理方法。
3. 6σ管理法6σ管理法,即六西格玛管理法,是一种重视数据分析和过程控制的管理方法。
4. TQM管理法TQM管理法,即全面质量管理,是一种以客户满意为导向,不断提高质量的管理方法。
5. ISO质量管理体系ISO质量管理体系,即国际标准化组织的质量管理体系,是一种被广泛应用于企业的国际标准。
6. KPI绩效管理KPI绩效管理,即关键绩效指标管理,是一种以数字化体现绩效的管理方法。
7. JIT生产方式JIT生产方式,即按需生产方式,是一种不允许存货积压的生产方式。
8. TOC理论TOC理论,即约束理论,是一种针对瓶颈及其优化的管理方法。
9. TPM管理法TPM管理法,即全员参与的设备保养和管理,是一种通过设备保养和管理,提高生产效率和质量的管理方法。
10. 8D报告8D报告,即8步问题解决法,是一种解决产品质量问题的方法。
11. FMEA分析FMEA分析,即故障模式与效应分析,是一种评估和管理潜在故障风险的方法。
12. Kaizen改善活动Kaizen改善活动,即持续改善活动,是一种定期开展的协作式改善活动。
13. 统计方法统计方法,包括抽样调查、统计分析等方法,是一种有效的质量管理工具。
14. 模拟方法模拟方法,通过模拟实现问题的复杂度阶段达成一定的结论和优化。
15. TQC质量控制TQC质量控制,即全面质量控制,是一种通过全员参与建立质量自律环境和改善质量的管理方法。
16. VMI库存管理VMI库存管理,即供应商卫星库存管理,是一种通过合理配置货物和库存,最优化在库存中缩减成本。
质量管理的七大手法

质量管理的七大手法质量管理是企业生产经营中的重要环节,它关系到产品质量和企业形象的提升。
为了有效地进行质量管理,我们可以采用七大手法,以确保产品质量的稳定和优良。
下面将详细介绍这七大手法。
1. PDCA循环法PDCA循环法是质量管理中最基础的手法之一,它由四个阶段组成:计划(Plan)、实施(Do)、检查(Check)和行动(Action)。
通过不断循环执行这四个阶段,可以持续改进质量管理体系,不断提高产品的质量水平。
2. 六西格玛法六西格玛法是一种以减少变异、提高质量为目标的管理方法。
它通过对各个环节的数据收集、分析和改进,以降低缺陷率和提高产品质量。
六西格玛法注重数据驱动的决策和过程改进,以确保产品质量的稳定性和可预测性。
3. 故障模式与影响分析法(FMEA)FMEA是一种通过分析潜在故障模式及其对产品性能的影响来预防故障的方法。
它通过对各个环节进行系统性的故障分析,找出潜在问题并采取相应措施,以减少故障的发生和影响,提高产品的可靠性和质量。
4. 统计过程控制(SPC)SPC是一种通过对过程数据的收集和分析,以及对过程稳定性的监控来实现质量控制的方法。
它通过建立合理的过程控制限制,及时发现和纠正过程中的变异,以确保产品质量在可接受范围内。
5. 直观化管理直观化管理是通过可视化手段,将企业的质量管理信息以图表、图形等形式展示出来,以便于管理人员和员工的理解和分析。
直观化管理可以帮助发现问题、分析原因并采取相应措施,提高质量管理的效果。
6. 5S管理5S管理是一种通过整理、整顿、清扫、清洁和素养的方式,改善工作环境和工作习惯,提高工作效率和产品质量的方法。
通过5S管理,可以减少浪费、降低差错率,提高工作效率和质量。
7. 品质环境管理品质环境管理是一种通过营造良好的工作环境和氛围,培养员工的质量意识和责任心,提高产品质量的方法。
通过建立质量文化、加强培训和激励机制等措施,可以提高员工对质量的重视程度,从而提高产品的质量水平。
品质7大手法
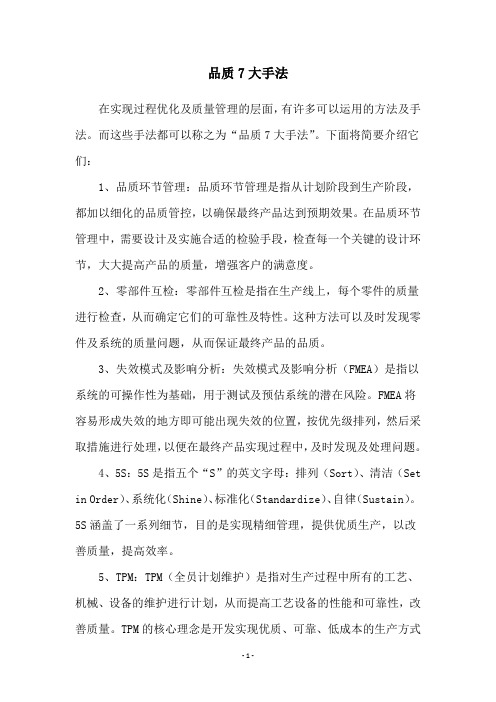
品质7大手法在实现过程优化及质量管理的层面,有许多可以运用的方法及手法。
而这些手法都可以称之为“品质7大手法”。
下面将简要介绍它们:1、品质环节管理:品质环节管理是指从计划阶段到生产阶段,都加以细化的品质管控,以确保最终产品达到预期效果。
在品质环节管理中,需要设计及实施合适的检验手段,检查每一个关键的设计环节,大大提高产品的质量,增强客户的满意度。
2、零部件互检:零部件互检是指在生产线上,每个零件的质量进行检查,从而确定它们的可靠性及特性。
这种方法可以及时发现零件及系统的质量问题,从而保证最终产品的品质。
3、失效模式及影响分析:失效模式及影响分析(FMEA)是指以系统的可操作性为基础,用于测试及预估系统的潜在风险。
FMEA将容易形成失效的地方即可能出现失效的位置,按优先级排列,然后采取措施进行处理,以便在最终产品实现过程中,及时发现及处理问题。
4、5S:5S是指五个“S”的英文字母:排列(Sort)、清洁(Set in Order)、系统化(Shine)、标准化(Standardize)、自律(Sustain)。
5S涵盖了一系列细节,目的是实现精细管理,提供优质生产,以改善质量,提高效率。
5、TPM:TPM(全员计划维护)是指对生产过程中所有的工艺、机械、设备的维护进行计划,从而提高工艺设备的性能和可靠性,改善质量。
TPM的核心理念是开发实现优质、可靠、低成本的生产方式及管理方式,以实现质量的连续改善。
6、SPC:SPC(统计过程控制)是指在生产过程中,采用统计手段对产品的表现进行监控,从而确保满足规格,达到客户满意的效果。
SPC可以将无形的质量变量变为有形的物质,把不可控的“质量”变为可以控制的状态,从而能够达到质量的预期效果。
7、品质改善:品质改善是指采取有效的措施,提高生产过程的质量水平,使产品符合客户的要求,并维持质量水平,以保持客户满意。
品质改善过程,包括纠正及预防因素,可增加客户满意度,提高企业的效益。
品质七大手法版运用

品质七大手法版运用1.流程图:流程图是用来描述一个过程的步骤和顺序。
它能够帮助识别和消除潜在的问题,并优化工作流程。
流程图可以用于制造流程、服务流程、销售流程等。
例如,制造业可以利用流程图来追踪原材料的供应链,确定生产过程中的瓶颈并降低生产时间和成本。
2.因果图:因果图也被称为鱼骨图或石川图,它用于找出问题的根本原因。
因果图以一个中心节点为起点,将问题分解为不同的因素并将其连接起来。
这种可视化的方法有助于团队分析和解决问题。
例如,在服务行业,可以利用因果图来找出导致客户不满的原因,然后采取相应的措施来改善服务质量。
3.检查表:检查表是用于记录和跟踪信息的工具。
它包含一系列问题和选项,供参与者进行勾选或填写。
检查表有助于确保过程中的每个步骤都得到正确执行,并且可以帮助提高一致性和减少错误的发生。
例如,在餐饮业,可以使用检查表来确保各种食材的质量和安全措施的执行。
4.直方图:直方图用于展示数据的分布和频率。
它能够帮助识别数据的特征和模式,并帮助做出决策。
直方图通常用于分析质量和业绩指标,以便进行改进。
例如,在制造业,可以使用直方图来评估产品的尺寸分布,并评估生产过程的稳定性。
5.散点图:散点图用于显示两个变量之间的关系。
它能够帮助识别变量之间的趋势、模式和相关性,并帮助做出决策和优化过程。
例如,在市场营销领域,可以使用散点图来展示广告投入和销售收入之间的关系,以便决策者了解投入与产出之间的关系。
6.控制图:控制图用于监控和控制过程的稳定性和可靠性。
它能够帮助检测和预测过程变化,并及时采取纠正措施。
控制图通常用于制造和生产环境中,以确保产品和过程能够持续符合要求。
例如,在汽车制造业,可以使用控制图来监测生产线的质量变化,并及时调整设备和流程。
7.帕累托图:帕累托图用于确定导致问题的主要原因。
它通过将问题按照其重要性进行排序,并标出累计百分比,以显示重要原因的贡献程度。
帕累托图有助于团队集中精力解决最重要的问题,以实现改进。
品质管理七大手法八大原则

品质管理七大手法八大原则
质量管理,是指企业建立和实施一系列效果显著的、综合性的绩效目标,以提高市场竞争力和企业绩效的过程,因此现代的质量管理大量应用了一系列有效的技术和手段。
首先,质量管理的七大手法是:改善,内控,计量控制,ISO 9000,先进制造,质量保障,可行性分析。
其中,改善是指改善已经存在的产品或服务,以提高其品质;内控是指通过规范和系统化的内部管理,进行有效的内部监督;计量控制是指使用均值控制图,移动控制图、过程能力分析,进行关键参数或关键流程的实时监控;ISO 9000是一个国际标准,强调了企业应该建立一个完善的质量管理系统,以满足客户要求;先进制造是指为提高产品质量而采取的各种质量保证手段;质量保障是指消除质量缺陷和故障;可行性分析是指对企业投资和决策的分析,确保实施后绩效符合预期。
其次,质量管理的八大原则是:「顾客至上」,「及时交付」,「质量标准」,「质量优先」,「全面提升」,「参与质量管理」,「质量审核」,「关注过程」。
首先,以顾客为中心,重视顾客需求,以满足客户需求为首要目标;其次,建立精确的质量标准,以及时发现和改正质量问题,确保高品质;第三,优先考虑质量改进:要求良好的过程控制能力,定期对工艺和质量进行完善;第四,营造跨部门合作的氛围,提高员工和管理者的技能,实现全面的提升;第五,培养员工参与决策、诊断和改进的精神,实现质量管理的效力;第六,建立完善的质量审核系统;最后,分析工艺过程,注重控制工艺,从而提高质
量表现水平。
概括起来,质量管理的七大手法和八大原则是:综合运用改善、内控、计量控制、ISO 9000、先进制造、质量保障和可行性分析。
品质管理QC七大手法
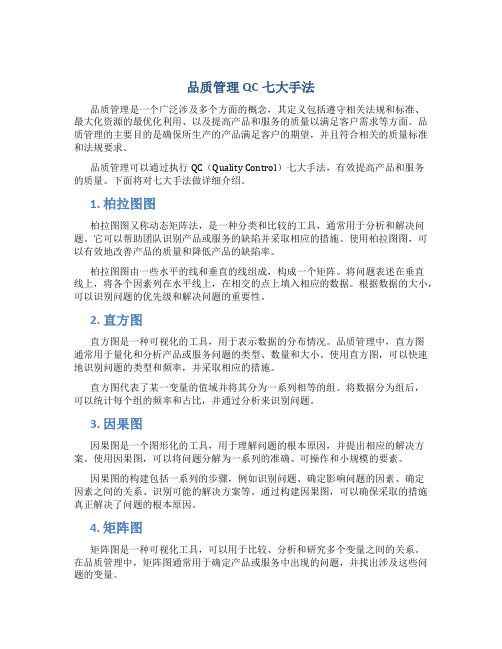
品质管理QC七大手法品质管理是一个广泛涉及多个方面的概念,其定义包括遵守相关法规和标准、最大化资源的最优化利用、以及提高产品和服务的质量以满足客户需求等方面。
品质管理的主要目的是确保所生产的产品满足客户的期望,并且符合相关的质量标准和法规要求。
品质管理可以通过执行QC(Quality Control)七大手法,有效提高产品和服务的质量。
下面将对七大手法做详细介绍。
1. 柏拉图图柏拉图图又称动态矩阵法,是一种分类和比较的工具,通常用于分析和解决问题。
它可以帮助团队识别产品或服务的缺陷并采取相应的措施。
使用柏拉图图,可以有效地改善产品的质量和降低产品的缺陷率。
柏拉图图由一些水平的线和垂直的线组成,构成一个矩阵。
将问题表述在垂直线上,将各个因素列在水平线上,在相交的点上填入相应的数据。
根据数据的大小,可以识别问题的优先级和解决问题的重要性。
2. 直方图直方图是一种可视化的工具,用于表示数据的分布情况。
品质管理中,直方图通常用于量化和分析产品或服务问题的类型、数量和大小。
使用直方图,可以快速地识别问题的类型和频率,并采取相应的措施。
直方图代表了某一变量的值域并将其分为一系列相等的组。
将数据分为组后,可以统计每个组的频率和占比,并通过分析来识别问题。
3. 因果图因果图是一个图形化的工具,用于理解问题的根本原因,并提出相应的解决方案。
使用因果图,可以将问题分解为一系列的准确、可操作和小规模的要素。
因果图的构建包括一系列的步骤,例如识别问题、确定影响问题的因素、确定因素之间的关系、识别可能的解决方案等。
通过构建因果图,可以确保采取的措施真正解决了问题的根本原因。
4. 矩阵图矩阵图是一种可视化工具,可以用于比较、分析和研究多个变量之间的关系。
在品质管理中,矩阵图通常用于确定产品或服务中出现的问题,并找出涉及这些问题的变量。
矩阵图的构建包括两个主要步骤:确定变量和比较变量。
根据变量之间的比较,可以识别问题的原因和涉及问题的变量。
5Why_品质改善手法

小朋友 在哭泣
挨了父親罵
繼續
吃驚 螺絲起子 (Surprise) 落下來 高興 (Pleasure)
要研究關於廣泛的範圍 , 因找不到原因
找不到原因 , 所以不需要繼續分析
11
“5Why”原因追究例子-2
不好的 分析
現象 蓋子 落掉了 Why 螺栓 鬆了 Why Why 對策 加強繫緊 螺栓
×
繫緊扭 力太少
1 有沒有用三現(現場,現物,現實)主義 2 3 4 5 6 7 8 9 10 11 12 13 14 15
有沒有確實追蹤現象發生的原理和原則 有沒有分析問題的相關事件[關於 4M] 從最後的"Why"反推回去,其Logic上是否合理 有沒有確實分析出最後的原因(真因) 是否有追究人的心理因素[人員疏忽,太忙,etc] 內容表現是否簡單和簡潔(S+V+O) 有沒有[人,設備,品質,etc]是不好"的表現或言語出現 有沒有用圖表表示及對照(容易理解的表現和內容) 有沒有制定再發生防止對策 有沒有擴展至類似事件及制定防止對策 對策有沒有完成日期 有沒有使用 [要求.請.將會…等用語] 對策有沒有具體化 合 計
評估分數 滿分 得分 5 5 5 10 5 10 10 -10 5 -10 5 10 10 10 -10 10 70 0
備
註
欄
8
重複五次「為什麼」了嗎
對一個現象,是否均可舉出五個「為什麼」呢? 說起來簡單,做起來可就困難,比如說機械不能動作: 1Why;「為什麼機械停了呢?」 「因為超負荷,所以保險絲燒斷了.」 2Why;「為什麼超負荷呢?」 「因為軸承部分的潤滑不夠.」 3Why;「為什麼潤滑不夠呢?」 「因為潤滑幫浦不能充分汲上.」 4Why;「為什麼不能充分汲上呢?」 「因為幫浦的軸心產出, 磨耗產出振動搖晃現象」 5Why;「為什麼會磨耗呢?」 「因為未裝過濾器,所以切削粉末掉進去.」 以上重複五個「為什麼」,就可很明顯地發現 「要裝上過濾器」的對策.
品质改善十大手法及流程
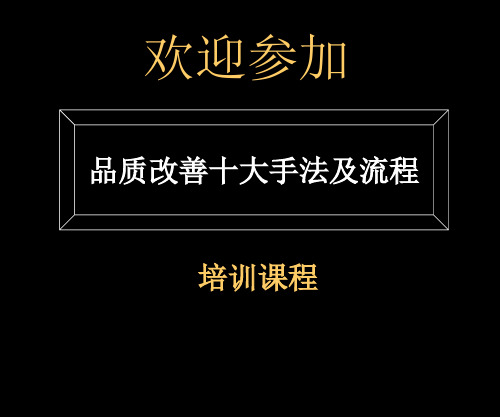
管理过程方法应用准则
Action
Plan
Check
Do
每一个过程的实施考虑
Action行动: Target 目标 Output输出
Plan计划: Input输入
With what用什么 With who 谁
Target目标
Check 检查: Output输出
Indicators measurement
例二:部门主管向你反应,近期 工作忙?希望能够增加人手,请 问你会如何回答?
第二章 数据与图表
壹、数 据
一、前 言 [凡事讲求数据]在现实工作中,这是吾人耳熟
能详的一句话,然而[数据]是什么?依据测量所获 得的数值和资料等事实,即所谓数据。所以,吾人 以为数据最主要的基本观念乃是:
数据=事实 而解决问题第一个步骤,即是根据事实经判断 后再采取行动。
(1)原物料及制品市场数据:来自原料、物料及制品市场, 搜集相关回馈之数据,以做为设计品质、订定采购及销 售策略者谓之。
(2)制程数据:在产品制造过程中,作为判断制程是否稳定、 产品是否良好,将制程中所搜集的半成品、成品予以量 测所得的数据者谓之。
(3)检验数据:为获悉采购进来的原物料,是否符合公司用 途;制程中之半成品为确保本工程之品质方得转下一工 程及成品于入库前或销售时,能符合客户需求,不致将 不良品流出或减至最低者,而施行检验得来的数据者, 均可谓之。
例,自数据分类至结果分析,可一举而成。
2 人工整理法: (1)卡片法:利用质地较坚硬的纸,做成大小相同的卡片,将
每一单位之事实,转录于卡片上,并依特定之标准分类后, 加以确认至无误为止,最后将卡片计数登录在整理表上。
(2)尽记法:以“正”字记号及“ ”棒形记号,较为常用, 经尽记后统计各类数据之所有个数的整理方法谓之尽记法。
品质7大手法

品质7大手法
现当前质量管理(QM)普遍认为,对于企业来说,要实现质量提升,应该采用7大手法。
即:定义、计划、实施、监视、测量、管理和改进。
定义是建立质量政策、目标和方向,明确质量方针,根据客户需求制定适当的质量策略,使企业可以向客户提供符合要求的产品或服务。
计划是制定具体的质量管理计划,以满足客户的期望,确定具体的质量改进计划,确保企业可以按时交付符合要求的产品。
实施是将质量管理计划付诸实施,确保每期质量要求得到满足,通过过程管理,促使企业实现质量改善。
监视主要是通过各种方式及时监控检验,以保证企业的产品和服务都能达到预期的产品质量。
测量是收集、处理和分析产品质量的相关数据,以此来衡量企业的质量水平,并就实施的质量改进进行估算和分析。
管理是负责指导企业质量管理活动,促使企业按质量标准进行管理,以保证企业在质量方面的持续改善、持续发展。
改进是持续改进企业的质量,以满足客户的需求,确保企业的质量满足客户的期望。
总之,7大手法是质量管理手段,也是改善企业质量最有效的方法。
如果企业能够充分利用7大手法,严格按质量标准管理,改进和优化产品和服务,企业质量的提升将不断推进。
品质改善十大手法及流程

PDCA循环法是一种不断改进、不断完善的品质管理方法,通过持续的计划、执行、检查和处理,不断发现问题、解决问题,推动品质的持续改进。
PDCA循环法强调全员参与和团队合作,鼓励员工提出改进意见和建议,共同推动品质改善。
PDCA循环法是一种品质改善的基本方法,由美国质量管理专家W.E.Deming提出,包括Plan(计划)、Do(执行)、Check(检查)和Act(处理)四个阶段。
P阶段
确定品质改善的目标和计划,包括对现状的把握、问题的识别以及解决方案的制定等。
C阶段
对实施效果进行检查和验证,确认改善措施是否达到了预期效果。
A阶段
对实施效果进行处理,总结经验教训,将有效的措施标准化,并针对未解决的问题制定新的计划,进入下一个PDCA循环。
D阶段
按照计划实施改善措施,确保计划的执行和落实。
总结词:检查表法在品质改善中广泛应用于产品、服务、过程或系统的质量评估和改进。
分层法
CATALOGUE
08
分层法是一种通过将数据按照一定的特性进行分类,并对各类数据进行统计分析,以找出问题原因和改善方向的方法。
它通过对数据的分层,能够更准确地识别出问题的根本原因,从而采取有效的措施进行改善。
检查表法
CATALOGUE
07
总结词
检查表法是一种通过制定详细的标准和检查表,对特定对象进行检查和评估的方法。
详细描述
检查表法是一种结构化的评估方法,通过制定详细的标准和检查表,对产品、服务、过程或系统进行检查和评估,以确保达到预设的质量要求。这种方法通常用于识别和纠正问题,以及预防潜在的缺陷和错误。
详细描述
通过对流程进行优化和改进,可以提高效率、降低成本、提升质量。
品质七大手法及8D报告(一)
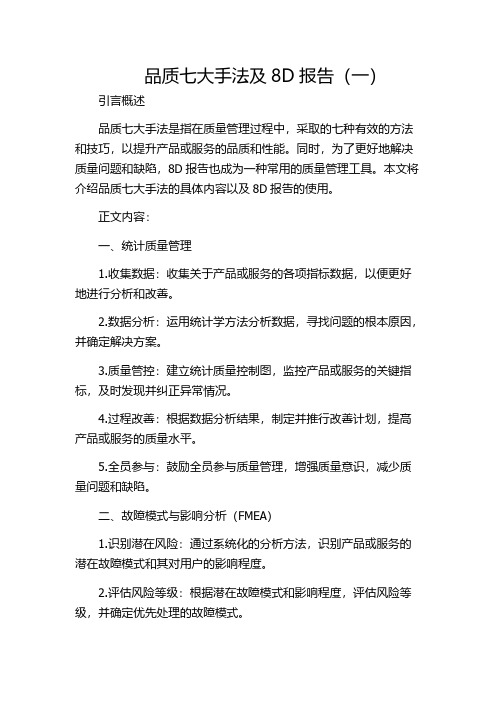
品质七大手法及8D报告(一)引言概述品质七大手法是指在质量管理过程中,采取的七种有效的方法和技巧,以提升产品或服务的品质和性能。
同时,为了更好地解决质量问题和缺陷,8D报告也成为一种常用的质量管理工具。
本文将介绍品质七大手法的具体内容以及8D报告的使用。
正文内容:一、统计质量管理1.收集数据:收集关于产品或服务的各项指标数据,以便更好地进行分析和改善。
2.数据分析:运用统计学方法分析数据,寻找问题的根本原因,并确定解决方案。
3.质量管控:建立统计质量控制图,监控产品或服务的关键指标,及时发现并纠正异常情况。
4.过程改善:根据数据分析结果,制定并推行改善计划,提高产品或服务的质量水平。
5.全员参与:鼓励全员参与质量管理,增强质量意识,减少质量问题和缺陷。
二、故障模式与影响分析(FMEA)1.识别潜在风险:通过系统化的分析方法,识别产品或服务的潜在故障模式和其对用户的影响程度。
2.评估风险等级:根据潜在故障模式和影响程度,评估风险等级,并确定优先处理的故障模式。
3.制定预防措施:在风险等级高的故障模式上,制定相应的预防措施,减少潜在风险的发生。
4.纠正措施:对已发生的故障模式,制定纠正措施,确保问题不再发生,并进行持续改进。
5.验证效果:对预防和纠正措施进行验证,确保其有效性和实施情况。
三、质量成本管理1.成本分析:对质量过程中产生的各项成本进行深入分析,包括预防成本、评价成本、内部失败成本和外部失败成本。
2.成本控制:通过制定合理的质量控制措施,减少质量问题和缺陷的发生,降低质量成本。
3.经济批量选择:在制定生产计划时,综合考虑成本和质量要求,选择适当的经济批量。
4.质量成本效益分析:对质量改进措施的成本与效益进行评估和分析,以便决策者做出合理的决策。
5.全员节约:倡导全员以经济节约的思想,降低质量成本,提高公司整体竞争力。
四、质量标准化管理1.制定标准:在产品或服务的设计阶段,制定相应的质量标准,以指导后续的生产和服务过程。
qc七大手法与品质工具改善的使用技巧

Chapter 2 品質改善的工具與技術
2-1
結束
結束
結束
結束
查檢表 1/3
查檢表乃以圖或表呈現出問題所在,期並無特定格 式,使用者可依據問題屬性設計之,並以自訂符號 填註以了解問題狀況。
點查檢表
次序 1 2 3 4 5 6 7 8
製作漢堡檢核表 項目
洗手 烤漢堡 塗沙拉醬 放蕃茄 放生菜 放肉 放蛋 裝袋
天马行空官方博客:/tmxk_docin ;QQ:1318241189;QQ群:175569632
2-9
結束
特性要因圖
特性要因圖為分析根本問題之一種工具,研究造成 特定問題或結果可能原因。又稱因果關係圖或魚骨 圖。 5M1E: Material, Method, Measurement, Machine, Man, Environment
2-11
結束
直方圖
直方圖(histogram)使用面最為廣泛。將蒐集之數據依據組距 (bin)分為幾組,再統計其發生次數並作成一個表。 直方圖為一種長條圖,其一軸為量測值,另一軸為百分比 或頻率..) 直方圖為SPC重要工具,因為常用統計公式應用於常態機率 分配 See example 2-2, page 36
2-32
結束
關聯圖法 1/2
將原因與結果間,或目的與手段間等複雜問題,利 用邏輯方式分析使關係明確化,步驟如下:
➢ 決定主題研究。 ➢ 組成研究團隊,以共同解決問題。 ➢ 找尋影響問題的各種可能原因。 ➢ 將原因間關係和因果關係以箭頭表示,即形成關聯
圖。 ➢ 修正圖形,即再整體討論,若有不足項目應追加之。
Chapter 2 品質改善的工具與技術
2-43
結束
PDCA循環 2/2
QC七大手法
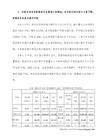
1. 关联图法--TQM推行, 方针管理, 品质管制改善, 生产方式,
生产管理改善
2.KJ法--开发, TQM推行, QCC推行, 品质改善
3. 系统图法--开发, 品质保证, 品质改善
4.矩阵图法--开发, 品质改善, 品质保证
5.矩阵开数据解析法--企划, 开发, 工程解析
四,想进行问题的剖析及追根究底时,可以用特性要因图;
五、要知道两因素之间的相关性时,用散布图来;
六、要知道整体数据的分布时及CPK时,用直方图;
七、要对制程进行分析与控制时,用管制图来识别异常。
QC即英文QUALITYCONTROL的简称,中文意义是品质控制,其在ISO8402:1994的定义是“为达到品质要求所采取的作业技术和活动”。
教材构成:
7卷录影带、讲师手册1本、学员手册1 本
影片重点:
在推行TQM的今天,如何使全公司上下各部门,
对品质管理的基本观念有正确的理解,是一件重要的事。
QC七大手法是一套易学、易懂又好用的管理改善工具。
学习目标:
1、吸收QC七手法的知识并应用。
2、在短期内就可以在工作场展开运用。
有用的质量统计管理工具当然不止七种。除了新旧七种工具以外,常用的工具还有实验设计、分布图、推移图等。
本次,主要讲的是QC七大手法,而SPC(管制图)是QC七大手法的核心部分,是本次培训的重点内容。
二、旧七种工具
学习目标:
1、手法的KNOW-HOW。
2、成为一位具思考能力的优秀管理者及幕僚人员
3、知道在策略执行的过程中,如何评估、拟订更有效的计划。
教材大纲:
亲和图法
七大手法改善案例
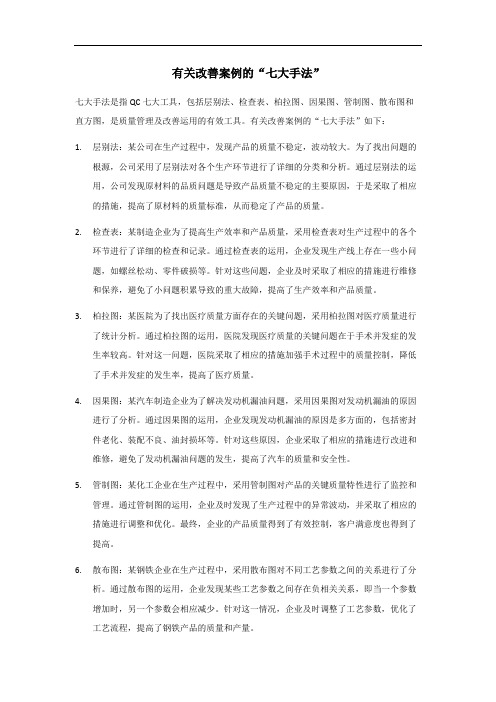
有关改善案例的“七大手法”七大手法是指QC七大工具,包括层别法、检查表、柏拉图、因果图、管制图、散布图和直方图,是质量管理及改善运用的有效工具。
有关改善案例的“七大手法”如下:1.层别法:某公司在生产过程中,发现产品的质量不稳定,波动较大。
为了找出问题的根源,公司采用了层别法对各个生产环节进行了详细的分类和分析。
通过层别法的运用,公司发现原材料的品质问题是导致产品质量不稳定的主要原因,于是采取了相应的措施,提高了原材料的质量标准,从而稳定了产品的质量。
2.检查表:某制造企业为了提高生产效率和产品质量,采用检查表对生产过程中的各个环节进行了详细的检查和记录。
通过检查表的运用,企业发现生产线上存在一些小问题,如螺丝松动、零件破损等。
针对这些问题,企业及时采取了相应的措施进行维修和保养,避免了小问题积累导致的重大故障,提高了生产效率和产品质量。
3.柏拉图:某医院为了找出医疗质量方面存在的关键问题,采用柏拉图对医疗质量进行了统计分析。
通过柏拉图的运用,医院发现医疗质量的关键问题在于手术并发症的发生率较高。
针对这一问题,医院采取了相应的措施加强手术过程中的质量控制,降低了手术并发症的发生率,提高了医疗质量。
4.因果图:某汽车制造企业为了解决发动机漏油问题,采用因果图对发动机漏油的原因进行了分析。
通过因果图的运用,企业发现发动机漏油的原因是多方面的,包括密封件老化、装配不良、油封损坏等。
针对这些原因,企业采取了相应的措施进行改进和维修,避免了发动机漏油问题的发生,提高了汽车的质量和安全性。
5.管制图:某化工企业在生产过程中,采用管制图对产品的关键质量特性进行了监控和管理。
通过管制图的运用,企业及时发现了生产过程中的异常波动,并采取了相应的措施进行调整和优化。
最终,企业的产品质量得到了有效控制,客户满意度也得到了提高。
6.散布图:某钢铁企业在生产过程中,采用散布图对不同工艺参数之间的关系进行了分析。
通过散布图的运用,企业发现某些工艺参数之间存在负相关关系,即当一个参数增加时,另一个参数会相应减少。
QC七大手法-数据分析之品质改善_手把手教你绘制柏拉图,一起学起来吧
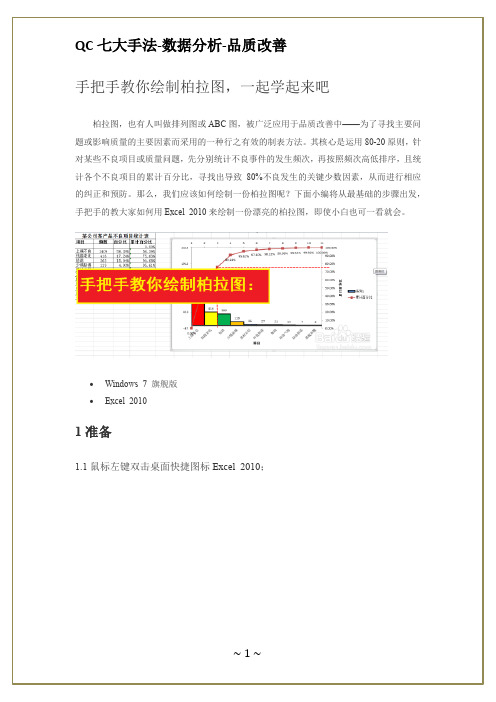
4.4鼠标右键单击红色“累计百分比”折线图,并在弹出的快捷菜单中选择“设置数据系统格式”;5.3鼠标左键单击“图形工具--布局--次坐标轴水平(类别)轴--设置所选内容格式”5.4在弹出的“设置坐标轴格式”对话框中,选择“坐标轴选项--位置坐标轴--在刻度线上”;5.5“累计百分比”系列折线将以0刻度线开始;5.6鼠标左键单击“图形工具--布局--垂直(值)轴--设置所选内容格式”;5.7在弹出的“设置坐标轴格式”对话框中,设置“坐标轴选项--最大值--固定:2413”(频次总数),设置“坐标轴选项--最小值--固定:0”;5.8重复“方法/步骤5:柏拉图制作第6-7步”设置“次坐标轴水平(值)轴”的最大值为100%(1.0),最小值为0;5.9增加数据标签:鼠标左键单击“图形工具--布局--其他数据标签选项”,并在弹出的5.10取消网格线:鼠标左键单击“图形工具--布局--网格线--主要横--无”,绘图区横网5.11增加坐标轴标题:鼠标左键单击“图形工具--布局--坐标轴标题”,分别设置主要横坐标轴标题、主要纵坐标标题和次要纵坐标标题,6.2增加80-20分割线:点击“插入--形状--直线”,按住【Shift】从80%累计百分比位置从右到左画一条直线与红色直线相交时停止,然后按住【Shift】从交点处从上到下划到柱子边框时停止;6.3 80-20分割线增粗、变虚线、变色:右键鼠标分别点击横向和纵向两条分割线,并且在弹出的快捷菜单中点击“设置对象格式”,然后在弹出的“设置形状格式”对话框中将线型“宽度”更改为2.25磅,将“短划线类型”更改为虚线,将“线型颜色”变为红色;6.4增加图表标题:鼠标左键单击“图形工具--布局--图表标题--图表上方”,为柏拉图增加图表标题,同时更改字体为隶书,字号20,颜色红色。
品质改善方法介绍-品管圈(QCC小组)

Quality Control Circle (QCC)
品管圈的组成
由规划单位分派 自行组圈
圈 长 圈 员 辅 导 员
18
Quality Control Circle (QCC)
圈的介绍-圈的组成
圈
名
圈
长
圈
员
所属单位 主要工作 活动期间
成立日期 辅导员
19
Quality Control Circle (QCC)
问题:如何缩短落差?
10
医院服务 品质之水平
Quality Control Circle (QCC)
解决问题的方法
问题
解决问题
顾客满意
11
品管圈 流程改善
ISO 9000 标竿学习
Quality Control Circle (QCC)
品管圈是啥东东?
相同部门 (工作现场)
统计计巧
5 - 10人
2
Quality Control Circle (QCC)
前言
品管圈活动几乎是世界各国无法仿效的优秀 辨法,由于推行这个活动,日本在品管方面必 能在世界上保持领导的地位,日本的品管圈是 世界上最成功的品管运动 (Juran 1976)
适合人性的品管圈活动,只要是人的话,在世
界任何国家都可能适用
28
Quality Control Circle (QCC)
门诊就医流程图
范例
开始
门诊挂号
医师看诊 开立处方
批价
是
检验
检验?
否
药局领药
离院
:开始或结束 :执行的任务或活动 :需要做决定之处 :方向和流程
29
Quality Control Circle (QCC)
- 1、下载文档前请自行甄别文档内容的完整性,平台不提供额外的编辑、内容补充、找答案等附加服务。
- 2、"仅部分预览"的文档,不可在线预览部分如存在完整性等问题,可反馈申请退款(可完整预览的文档不适用该条件!)。
- 3、如文档侵犯您的权益,请联系客服反馈,我们会尽快为您处理(人工客服工作时间:9:00-18:30)。
问题
品质改善流程简图
推定
再现试验
对策
效果确认
量产 稳定性
确认
设计变更 OR
工程改善
改善报告要点
1、故障现象、发生情况; 2、原因解析 3、改善履历 4、再现试验+市场调查 5、二次解析结果 6、对策方案 7、对策效果确认 8、效果跟踪推移图
五原则表——表样
题目 零件号 零件名
解析报告 [5原则表 ]
3.整车系统功能丧失,并由此产生关连问题(如排气管烧焦 、漏、振动、看不见等)?
4.零件对成车造成不良影响,或由于成车的结构问题,导致 零件出现不良?
2 基本原因
1.可否从主要故障中看出零件/部品、性能/尺寸等方面的问 题?
2.是否清楚主要故障与基本原因之间的联系? 3.是否对人为造成的失误进行整改?
工程品质改善手法
——基础版
质量管理部 2009年3月25日
目录
1、PDCA介绍 2、FTA(故障树分析法) 3、五原则表(解析报告) 4、8D方法介绍 5、工序内品质改善
目录
1、PDCA介绍 2、FTA(故障树分析法) 3、五原则表(解析报告) 4、8D方法介绍 5、工序内品质改善
PDCA 简介
运用渠道1.要求对策时:编制部门→要求对策部门 (报告单位)
2.其它、编制部门(编制-保管)
①发生状况:确认问题的发生状況和处理内容 编 部室名或供货方名 年 月 日
制 部
批准 审核 编制
门
—对策要求时→ 要求报告不良对 策时,应付上不 良对策
报 告 单 位
年月日
批准
3 找出部品机 能・故障要因
4 找出製造工 艺管理上的 要因
5 製造工艺管 理的工艺検 証和改善
断开
投
润 不滑 足脂
量
凍 結
密防
良
封 性
尘 胶
不套
防 亀尘 裂胶
套
亀 裂
橡 胶踏・・・生冬U板字锈季车配発、異 材 混 入構早管生造晨フ→:会误リ入 错 误ク回 用凍原 材 料水シ边 角結存ョン积増边边加角角料料回識用別量 材 臭・ENG转速不能错降料低(边飞角车料)回用期限
PDCA 循环是由美国统计学家戴明博士提出来的, 它反映了质量管理活动的规律.
Action 处理
Plan 计划
Check 检查
Do 执行
Plan: 现状调查 原因分析 确定要因 制订计划
PDCA 步骤
Do: 执行计划
循环
Action: 巩固措施 下一步的计划
Check: 效果检查
序
号
不良事项
P
不良原因分析
材质确认
ST12标准
1次/批
○
材质明确标示 批次先进先出确认
1次/批
○
机械性能 抗拉强度δ≥300KN
1次/批
○
材料厚度 焊机调整 定时清洁焊滚 定时修整 电极压力
尺寸 焊点数量
2.5±0.1mm 80V 60A
保持没有焊渣 形状规则
50±5MPa ≥¢5 3点
1次/批
○
1次/班
○
1次/40
○
1次/60个
不良整改报告
D
对策内容
对策 日程
责任者
效果确认
第页
C
源头改善内容
A
遗留问题
审核:
编制:
目录
1、PDCA介绍 2、FTA(故障树分析法) 3、五原则表(解析报告) 4、8D方法介绍 5、工序内品质改善
FTA——定义及作用
故障树分析FTA [FaultT ree A nailsis]
电暖器
不供暖
或者
理上的问题点作为故障的要因抽出,与其在发生
后进行对策,还不如防止重大事故发生,抽出各
个阶段的问题点,确保制造工艺阶段成品品质,
解析故障发生的内在原因。
FTA——分析应用流程
1 加完成车机 能故障重大 性等级
油 门
拉 线
不
磨
回 位
擦 増 大抽出完成車 的源自全缺陷2 找出完成车 机能故障要 因
1、PDCA介绍 2、FTA(故障树分析法) 3、五原则表(解析报告) 4、8D方法介绍 5、工序内品质改善
品質改善流程
品技領域(解析报告)
問題 (事象)
①推定
②再現 试验
⑥監視 量産
品質領域(現場的改善)
⑤量産稳定性 確認
③対策的確認
(再現试验OK为止) 根本原因確定
④工程改善
or
④设计变更
紧守以上这种改善流程
○
2次/班
○
2次/班
○
全检
○
抗拉强度 抗拉强度δ≥30KN/点 2次/天
○
焊机调整
80V 60A
1次/班
○
抗拉强度 抗拉强度δ≥300KN
2次/天
○
焊接质量
焊缝均匀
全检
○
强度
P≥1000N
1次/批
○
齿部基本尺寸 大小节圆直径 首检 1次/小时 ○
齿形角度
齿型角 25度
1次/20
○
拉刀使用寿命 2000件/次更换
两根加热管都不工作
必然
1号加热管 故障
2号加热管 故障
没有电流通过
或者
电线断路
开关接触 不良
停电
电暖器的故障
不供暖
反射板 不烫
底座 不旋转
[TOP事 项]需要解析的事项
时,同如果没有各方面
小事项
专家共同参与的话 解析不出来
经验也是很必要的
插头
作用:
故障
FTA是将绝对 不能发生的事故、故障放在
系统图(树型)的最上方,将成品设计和品质管
水平4
管理项目
基准
频度
QC表 作业标准
化学成份不合格 异材混入
机械性能不合格 钢板厚度不够
点焊不良
缝焊不良
齿型精度 新模具加工不良
电压电流不稳 电极清洁 电极形状 压力不够
焊点直径不够 焊点不够
焊点强度不够 电压电流不稳 溶接强度不够 焊接焊缝不良 抗扭曲强度
花键尺寸 齿部尺寸 拉刀更换频度 形位不符合图纸
3 整改
1.针对基本原因,是否在设计、制造方面进行调整? 2.是否确认与制造相应的FMEA、工程QC表、作业标准? (FMEA为故障模式效率分析) 3.是否提出相应的对策及是否进行验算?
4.为了使质量问题降为“0”是否对CP值进行管理?
5.为确保质量问题降为“0”、是否使用了QA机等有效对策?
目录
1次/班
○
顶端和花键
零件图 R12 与 R17
按照 新模量产前和修 修模
○ ○ ○ ○ ○ ○ ○ ○ ○ ○ ○记录 ○ ○记录 ○ ○记录 ○ ○ ○
○
FTA——作成基本观点
No 项 目
观
点
1 主要故障 1.停止、转弯弯曲、不燃烧、行驶等(重要故障举例)
2.过去的问题(其他公司及市场索赔,外协不良、制造不良等) 的例子?
氧
抵 抗 大
配 索
从完成車事象到部品事象再
到製造工艺発生要因
設 定材
設
定 错 误
配 合 量
边角料回用記録
错料 設
误
定 错 误
配 合 材
抽出製造工艺 要因源流改善 生锈
凍結
水平1
刹 车 失 效
水平2 材料不良
* * * * * *
焊接不良 损
坏
尺寸不良
FFTTAA 表—(—***事***故例障)
水平3