品质管理问题点和改善建议
质量管理方面的不足及建议

质量管理方面的不足及建议质量管理是企业发展和竞争力提升的重要组成部分。
然而,许多企业在质量管理方面存在不足之处,在以下几个方面表现出问题:质量意识不强、质量标准不明确、质量控制不严格、质量持续改进不足。
针对这些不足,我提出如下的建议。
首先,企业需要加强质量意识,树立“质量第一”的理念。
质量意识的缺失是导致许多质量问题的根本原因。
企业需要认识到质量不仅仅是生产部门的责任,而是所有员工的责任。
通过加强质量培训和教育,提高员工的质量认识,增强其主动发现和解决质量问题的能力。
其次,企业需要明确质量标准和要求,并落实到实际操作中。
质量标准的不明确会导致操作员工对质量要求的理解产生偏差,从而引发质量问题。
企业应该建立完善的质量标准体系,明确产品的质量指标和检验方法,并严格执行。
同时,建立质量档案,记录每个环节的质量检验结果,以便追溯和分析。
第三,企业应加强质量控制,确保产品符合质量要求。
质量控制是防范质量问题的重要手段。
企业应该建立完善的质量控制体系,包括原料采购、生产过程控制、成品检验等环节。
严格执行各项质量控制规定,加强对关键环节的监控和管理,及时发现和纠正质量问题,确保产品质量的稳定性和可靠性。
最后,企业应注重质量持续改进,不断提升质量水平。
质量持续改进是提高企业质量管理能力的关键。
企业应建立质量反馈机制,及时收集和分析客户反馈、质量事故和客诉情况,找出质量问题的根本原因,并采取措施进行改进。
同时,可以引入先进的质量管理方法和工具,如六西格玛、PDCA循环等,持续改进质量管理水平。
总结起来,企业在质量管理方面存在不足,主要体现在质量意识不强、质量标准不明确、质量控制不严格和质量持续改进不足。
要改善这些不足,企业应加强质量意识,明确质量标准,严格质量控制,注重质量持续改进。
只有这样,企业才能提升质量水平,增强竞争力。
分析品质管理体系存在的问题与改善方法

分析品质管理体系存在的问题与改善方法品质管理体系是企业保证产品和服务质量的重要手段,然而在实践中常常存在一些问题。
本文将从多个角度分析品质管理体系存在的问题,并提出相应的改善方法。
一、问题分析1. 缺乏明确的质量目标:许多企业在制定品质管理体系时没有明确的质量目标,导致无法有效衡量和改进质量水平。
这使得企业难以评估自身的质量绩效,并且无法有效地引导和激励员工的工作。
2. 缺乏全员参与:品质管理体系往往只被视为质量部门的职责,而忽视了其他部门和员工的参与。
这种局限性使得质量管理无法渗透到整个企业,造成质量问题的发生和滋生。
3. 缺乏有效的沟通与反馈机制:在品质管理体系中,沟通与反馈是至关重要的环节。
然而,许多企业在这方面存在问题,无法及时获取和传递质量信息,导致问题无法及时解决和改进。
4. 缺乏持续改进的机制:品质管理体系应该是一个持续改进的过程,但是很多企业只注重一次性的认证,缺乏对体系的持续改进和更新。
这种短视的做法使得企业无法适应市场变化和客户需求的变化。
二、改善方法1. 确立明确的质量目标:企业应该在制定品质管理体系时明确质量目标,并将其与企业的战略目标相衔接。
同时,要制定可量化的指标和目标,以便能够对质量绩效进行评估和改进。
2. 强调全员参与:品质管理体系需要全员参与,每个员工都应该对质量负责。
企业应该加强培训和教育,提高员工的质量意识和技能,鼓励员工积极参与质量管理活动。
3. 建立有效的沟通与反馈机制:企业应该建立起有效的沟通渠道,确保质量信息能够及时传递和反馈。
可以通过定期的会议、报告和绩效评估等方式,促进各部门之间的沟通与协作。
4. 强调持续改进:品质管理体系应该是一个持续改进的过程,企业应该建立起相应的机制和流程。
可以采用PDCA(Plan-Do-Check-Act)循环,不断进行问题分析、改进措施的制定和实施,以及效果的评估和调整。
5. 加强供应链管理:品质管理体系不仅仅局限于企业内部,还应该涵盖供应链的管理。
品质部质量改善建议
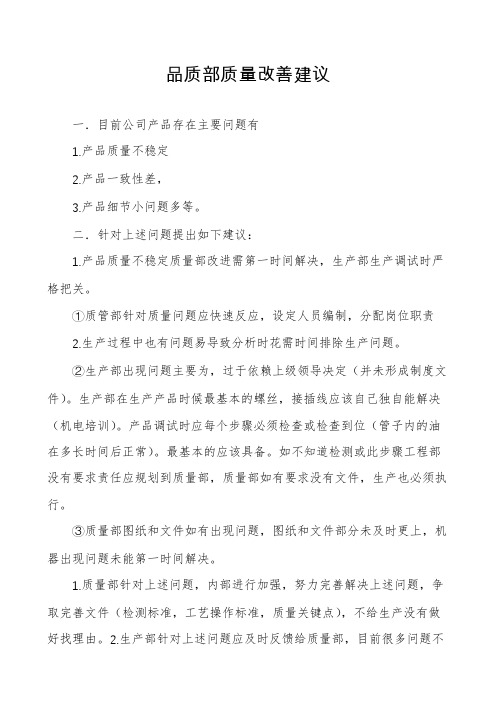
品质部质量改善建议一.目前公司产品存在主要问题有1.产品质量不稳定2.产品一致性差,3.产品细节小问题多等。
二.针对上述问题提出如下建议:1.产品质量不稳定质量部改进需第一时间解决,生产部生产调试时严格把关。
①质管部针对质量问题应快速反应,设定人员编制,分配岗位职责2.生产过程中也有问题易导致分析时花需时间排除生产问题。
②生产部出现问题主要为,过于依赖上级领导决定(并未形成制度文件)。
生产部在生产产品时候最基本的螺丝,接插线应该自己独自能解决(机电培训)。
产品调试时应每个步骤必须检查或检查到位(管子内的油在多长时间后正常)。
最基本的应该具备。
如不知道检测或此步骤工程部没有要求责任应规划到质量部,质量部如有要求没有文件,生产也必须执行。
③质量部图纸和文件如有出现问题,图纸和文件部分未及时更上,机器出现问题未能第一时间解决。
1.质量部针对上述问题,内部进行加强,努力完善解决上述问题,争取完善文件(检测标准,工艺操作标准,质量关键点),不给生产没有做好找理由。
2.生产部针对上述问题应及时反馈给质量部,目前很多问题不是该机器,该文件第一次使用未见生产反馈问题,几次以后再反映问题。
针对上述问题工程部:1.质量部日常工作需加强2.培训班组核心员工:(1)核心员工主要从事解决生产装配,线束,样机制作及工艺等,以及配合品质部工作(2)核心员工主要从事按规定要求检查和实验市场反映质量问题,生产过程中反映的问题,协助品质部检查抽检各成品,协助机电改善机器性能,新产品调试。
(3)调试人员日常工作需生产安排,但各人员工作岗位安排以及新进人员应由工程部考核安排。
不然试问日后工作能不出现问题吗?生产部:1加强对生产一线人员要求,必须严格作业。
2.发现问题及时反馈给质量部,不能有不是自己部门的问题,明知故犯。
3.机器维修时必须清理机器内的杂物,出厂时必须加强检验。
一些质量问题必须通知质管部。
三.机器一性能差,产品小问题多主要为1.品控应监督生产2.计件员工在小问题上没有判别能力或明知道只为减少自身麻烦让步放行。
质量管理制度怎么改善问题

质量管理制度怎么改善问题首先,我们先来分析一下质量管理制度存在的问题。
在实际生产中,质量管理制度可能存在以下几个方面的问题:1.标准不明确:企业对产品质量的要求没有明确的标准和指标,导致生产过程中缺乏量化的目标,无法有效进行质量控制。
2.流程不规范:生产生活的各个环节之间的配合不够紧密,流程不够规范,容易导致质量问题的产生。
3.人员素质不足:缺乏专业技术和管理经验的人员,无法进行正确的质量控制。
4.反馈机制不畅:对产品质量和客户反馈的信息采集和分析不够及时,导致问题长期得不到解决。
上面只是列举了一些可能存在的问题,实际上,每个企业的情况可能都不尽相同。
但是不管哪个行业,质量是永恒的主题,不断改善质量管理制度是企业生存和发展的重要保障。
接下来,我们就针对上述问题提出一些建议,来改善质量管理制度:1.明确标准:企业应该根据产品的特点和客户的需求明确质量标准和指标,确保产品在生产过程中能够达到这些标准。
2.优化流程:企业应该对生产流程进行重新规划和优化,确保各个环节之间的配合紧密,流程规范,减少因流程问题导致的质量问题。
3.提高人员素质:企业应该加大对员工的培训力度,提高他们的专业技术和管理经验,使他们能够更好的进行质量控制。
4.加强反馈机制:企业应该建立完善的信息反馈机制,对产品质量和客户反馈的信息进行及时的收集和分析,以便及时发现和解决潜在的质量问题。
以上建议只是一些比较常见的问题和解决办法,并不全面,企业在具体实施时还需根据自身的实际情况来进行具体的改善和调整。
最后,改善质量管理制度需要全员参与,需要企业的每个员工都认识到质量是企业永恒的主题,只有不断改善和提升产品的质量,才能获得客户的信赖和支持。
因此,企业应该加大对员工的教育力度,不断提高员工的质量意识,使之成为企业质量管理的参与者和推动者。
同时,企业应该建立一套完善的质量管理制度,使之成为企业各项工作的重要组成部分,并不断进行调整和完善,以适应市场的发展和客户需求的变化。
质量控制部品质管理总结与改进建议
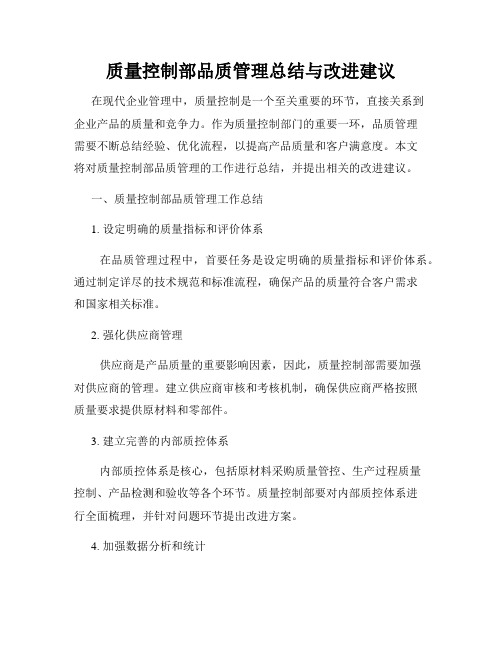
质量控制部品质管理总结与改进建议在现代企业管理中,质量控制是一个至关重要的环节,直接关系到企业产品的质量和竞争力。
作为质量控制部门的重要一环,品质管理需要不断总结经验、优化流程,以提高产品质量和客户满意度。
本文将对质量控制部品质管理的工作进行总结,并提出相关的改进建议。
一、质量控制部品质管理工作总结1. 设定明确的质量指标和评价体系在品质管理过程中,首要任务是设定明确的质量指标和评价体系。
通过制定详尽的技术规范和标准流程,确保产品的质量符合客户需求和国家相关标准。
2. 强化供应商管理供应商是产品质量的重要影响因素,因此,质量控制部需要加强对供应商的管理。
建立供应商审核和考核机制,确保供应商严格按照质量要求提供原材料和零部件。
3. 建立完善的内部质控体系内部质控体系是核心,包括原材料采购质量管控、生产过程质量控制、产品检测和验收等各个环节。
质量控制部要对内部质控体系进行全面梳理,并针对问题环节提出改进方案。
4. 加强数据分析和统计数据是质量控制的重要依据,需要收集并分析相关数据。
质量控制部门应加强数据的收集和整理工作,并通过合理的统计方法,对产品质量进行跟踪和分析,及时发现问题和异常。
5. 健全质量问题整改机制出现质量问题时,需要有一个快速而有效的整改机制。
质量控制部门要建立起完善的质量问题反馈和处理流程,及时跟进问题整改,并进行深入分析,以避免同类问题的再次发生。
二、改进建议1. 引入先进的质量管理工具当今时代,各种先进的质量管理工具不断涌现。
质量控制部门需要密切关注行业发展趋势,引入适合自身情况的先进管理工具。
例如,可以借助六西格玛管理法,通过数据分析和过程改进,提高产品质量水平。
2. 推行全员质量意识教育品质管理不仅仅是质量控制部门的责任,而应该是全员参与的工作。
质量控制部门可以与培训部门合作,开展相关的培训和教育活动,提高全员的质量意识和技能水平。
3. 加强与相关部门的沟通与合作质量控制部门与其他部门之间的沟通和合作至关重要。
【可编辑全文】品质管理问题点和改善建议
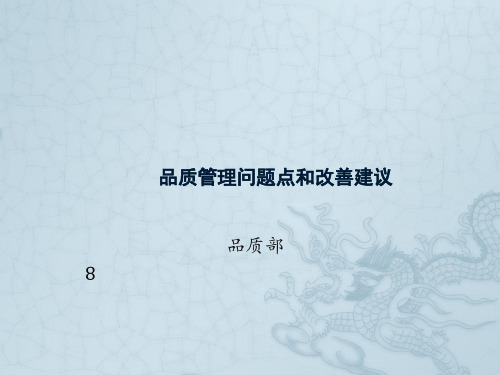
6、对于ECN工程变更,在发放ECN通知前ERP系统应该提前更新。 避免生产,检验不看ECN只看ERP 时出错。
7、对于可靠性测试标准应制定唯一一个,不必要每一种产品或 型号都编制一份,方便文件管理和使用。可靠性标准上的试验项 目要有可操作性,不能操作的项目或没有设备测试的项目不必要 写出来,这样审厂与实际操作中不会有疑问。(到底怎么做,做 还是不做这项)
样品评估记录, 改善对策,
开发部 品质部
标准内容应能符合客人要求且更加严格
产品规格书,生 产做业导书,可 靠性试验标准
开发部 生产工程部
应确保物料的质量要求准确的传达到供应商和检验部门。将原材料确认规 原村料规格书, 开发部
格书,样板发放到检验部门
图纸,样品
开发部,生产工程部,品质部应全程跟进试产(从贴片到包装)并记录存 在问题点
1、对现有检验标准进行收集整理,列出目录,进行适当的 整合,修订和完善,确保客户要求能正确反映到检验标准内 容中。 2、请市场部与客户沟通提供客户验货标准。(特别是外观 和包装要求相当重要
备注
序号
8
问题点
品质状态统计分析欠缺
9
新产品开发验证问题
10
原材料,辅料ROHS测试
改善建议
1、完善月度来料质量统计,所有供应商纳入考核体系,按月统计 结果进行评级,连续三个月C级供应商应取消资格 2、对每周生产发生的质量问题进行统计分析,相关部门对前五项 重大问题制定改善对策并落实到位。 3、每月质量问题地蚝统计分析检查周改善措施有落实情况 4、生产部每日生产质量情况进行统计,确保生产直通率达到质量 目标,对达不到直通率要求的原因要进行分析再第二日早会时告 知所有员工。 5、每周对IPQC巡检报告进行统计分析,找出前五项重要问题进 行分析解决。 6、坏机的修理必须有记录和统计分析找出主要问题来解决。 7、每月对QA抽检结果进统计找出前五项重要问题点进 行善。 8、对于客户投诉进行月度统计检查有无改善行动且是否达到果。
质量管理存在的问题与措施

质量管理存在的问题与措施在当今竞争激烈的市场环境中,产品和服务的质量成为了企业生存和发展的关键。
然而,许多企业在质量管理方面仍存在着各种各样的问题,这些问题不仅影响了企业的声誉和竞争力,还可能导致企业的经营困境。
因此,深入分析质量管理中存在的问题,并采取有效的措施加以解决,对于企业的可持续发展具有重要意义。
一、质量管理存在的问题(一)质量意识淡薄部分企业管理者和员工对质量的重要性认识不足,缺乏质量意识。
他们往往只关注短期的生产效率和成本,而忽视了产品或服务的质量。
这种短视的行为可能会导致产品质量不稳定,客户投诉增加,从而影响企业的长期发展。
(二)质量管理体系不完善一些企业虽然建立了质量管理体系,但在实际运行中存在诸多问题。
例如,质量管理流程不清晰,职责划分不明确,导致工作推诿扯皮;质量标准不严格,执行不到位,使得产品或服务无法达到预期的质量水平;缺乏有效的质量监督和评估机制,无法及时发现和解决质量问题。
(三)缺乏有效的质量控制手段在生产过程中,部分企业缺乏科学、合理的质量控制方法和工具。
例如,没有对原材料和零部件进行严格的检验和筛选,导致不合格品流入生产环节;生产过程中的工艺参数控制不严格,影响产品的一致性和稳定性;成品检验环节存在漏洞,不能有效地检测出存在质量问题的产品。
(四)员工素质参差不齐员工是质量管理的主体,其素质的高低直接影响到质量管理的效果。
一些企业的员工缺乏必要的质量知识和技能培训,对质量管理的方法和要求不了解,工作中容易出现失误和差错。
此外,部分员工责任心不强,工作态度不认真,也会对产品或服务的质量产生不利影响。
(五)质量成本管理不善质量成本包括预防成本、鉴定成本、内部损失成本和外部损失成本。
一些企业在质量管理中只注重降低生产成本,而忽视了质量成本的管理。
例如,为了节省预防成本,减少了质量培训和质量改进的投入,导致质量问题频发,从而增加了内部损失成本和外部损失成本。
(六)供应商管理不到位供应商提供的原材料和零部件的质量直接影响到企业产品的质量。
改进质量管理的整改措施

改进质量管理的整改措施在当今竞争激烈的市场环境中,产品和服务的质量是企业生存和发展的关键。
然而,许多企业在质量管理方面仍存在着各种各样的问题,这些问题不仅影响了企业的声誉和市场竞争力,还可能导致企业的经营困境。
因此,采取有效的整改措施来改进质量管理至关重要。
一、质量管理中存在的问题1、质量意识淡薄部分员工对质量的重要性认识不足,认为只要完成任务就行,而不注重质量的提升。
这种观念导致在工作中缺乏严谨的态度,容易出现粗心大意、敷衍了事的情况。
2、质量管理体系不完善企业虽然建立了质量管理体系,但在实际运行中存在漏洞。
例如,流程不清晰、职责不明确、文件记录不规范等,使得质量管理工作无法有效地开展。
3、原材料和零部件质量控制不足在采购环节,对原材料和零部件的质量把关不严,导致不合格的材料进入生产环节,从而影响产品的整体质量。
4、生产过程中的质量监控不到位生产过程中缺乏有效的监控手段和检验标准,无法及时发现和解决质量问题。
同时,对于生产工艺的执行情况也缺乏严格的监督,导致工艺偏差影响产品质量。
5、质量数据分析和利用不充分企业虽然收集了大量的质量数据,但未能进行有效的分析和挖掘,无法从数据中发现质量问题的根源和趋势,从而难以采取针对性的改进措施。
6、员工培训不足员工缺乏必要的质量知识和技能培训,无法掌握正确的操作方法和质量控制要点,影响了工作质量和效率。
二、改进质量管理的整改措施1、强化质量意识教育(1)开展质量意识培训活动,通过案例分析、专家讲座等形式,让员工深刻认识到质量对于企业生存和发展的重要性,树立“质量第一”的观念。
(2)建立质量奖励机制,对在质量工作中表现突出的员工和团队进行表彰和奖励,激发员工的积极性和主动性。
2、完善质量管理体系(1)对现有质量管理体系进行全面梳理和优化,明确各部门和岗位的质量职责,完善流程和文件,确保质量管理工作的规范化和标准化。
(2)加强内部审核和管理评审,定期对质量管理体系的运行情况进行检查和评估,及时发现并解决存在的问题。
质量控制中常见的问题及解决办法有哪些

质量控制中常见的问题及解决办法有哪些在当今竞争激烈的市场环境中,产品和服务的质量成为企业生存和发展的关键。
然而,在质量控制的过程中,常常会遇到各种各样的问题,这些问题如果不能得到及时有效的解决,将会对企业的声誉和经济效益产生严重的影响。
本文将探讨质量控制中常见的问题,并提出相应的解决办法。
一、质量控制中常见的问题1、缺乏明确的质量标准很多企业在进行质量控制时,没有明确的质量标准,导致员工在工作中缺乏明确的指导,无法准确判断产品或服务是否符合质量要求。
这种情况容易导致产品质量参差不齐,影响企业的整体形象和市场竞争力。
2、原材料和零部件质量不稳定原材料和零部件是产品质量的基础,如果其质量不稳定,将会直接影响到最终产品的质量。
例如,原材料的成分不符合要求、零部件的尺寸偏差过大等问题,都可能导致产品在使用过程中出现故障或性能下降。
3、生产过程中的质量控制不足在生产过程中,如果没有严格的质量控制措施,容易出现操作不规范、工艺参数不合理等问题。
例如,工人未按照操作规程进行操作、设备未进行定期维护和校准等,都可能导致产品质量问题的产生。
4、检测手段和设备不完善有效的检测是保证产品质量的重要手段,如果检测手段和设备不完善,就无法及时发现产品中的质量问题。
例如,检测方法不准确、检测设备精度不够等,都可能导致不合格产品流入市场。
5、人员素质和质量意识不高员工是质量控制的主体,如果员工的素质和质量意识不高,就很难保证产品和服务的质量。
例如,员工缺乏必要的专业知识和技能、对质量问题不够重视等,都可能导致质量问题的出现。
6、质量数据统计和分析不到位质量数据的统计和分析对于质量控制至关重要,如果这方面工作不到位,企业就无法及时发现质量问题的规律和趋势,从而难以采取有效的预防措施。
7、质量成本控制不合理质量成本包括预防成本、鉴定成本、内部损失成本和外部损失成本。
如果企业在质量成本控制方面不合理,可能会出现过度投入或投入不足的情况。
品质问题点与改善对策

品质问题点与改善对策
品质问题点:指企业在生产过程中出现的质量不合格现象或其他影响产品使用性能的问题。
改善对策: 1. 加强原材料的检验,凡是入库的原料都要严格按照质量检验标准进行检测,以保证生产所用的原材料都是质量合格的; 2. 改进生产工艺,加强对生产工艺的控制,尽量保证每一道工艺的参数按照规定的要求去操作; 3. 加强检测,建立有效的检测体系,将每一个产品的检测过程纳入质量控制环节中; 4. 科学管理,建立完善的管理体系,严格执行质量控制规范,对质量差的产品及时处理; 5. 加强培训,定期给员工进行技术培训,让员工具备更为全面的技能和知识,提升产品质量;
6. 供应商管理,建立有效的供应商管理体系,以保证供应商提供的原材料质量可靠;
7. 加强客户服务,按照客户的要求,对产品进行有效的管理,确保产品质量可靠。
品质管理年度存在的问题及对策

品质管理年度存在的问题及对策1.品质管理年度存在的问题是缺乏全面的品质管理体系。
The problem with quality management is the lack of a comprehensive quality management system.2.产品质量抽查不够严格,导致存在质量问题的产品流入市场。
The random quality checks are not strict enough, leadingto products with quality issues entering the market.3.员工对品质管理的重要性认识不够,导致工作中存在质量问题。
Employees do not have a strong awareness of theimportance of quality management, leading to quality issuesin their work.4.缺乏有效的质量管理培训,导致员工缺乏必要的品质管理知识和技能。
The lack of effective quality management training leadsto employees lacking necessary knowledge and skills inquality management.5.品质管理流程不够规范,存在操作不清晰的情况。
The quality management process is not standardized enough, leading to unclear operations.6.供应商管理不到位,导致采购的原材料质量无法得到有效保障。
Inadequate supplier management leads to a lack ofeffective quality assurance for purchased raw materials.7.一些产品存在设计缺陷,导致质量问题频发。
品质管理总结与改进建议
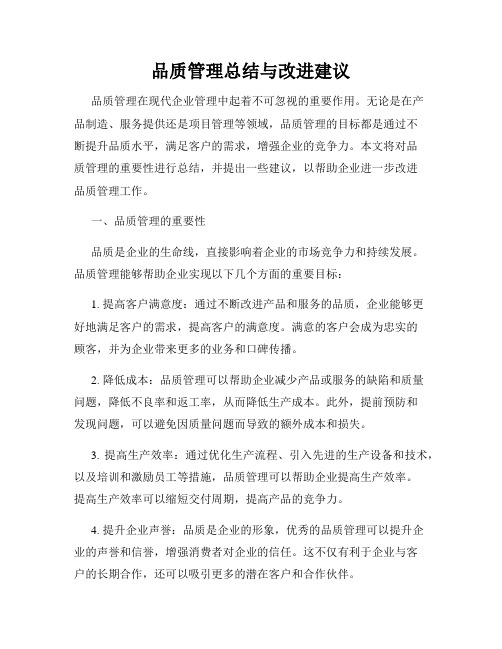
品质管理总结与改进建议品质管理在现代企业管理中起着不可忽视的重要作用。
无论是在产品制造、服务提供还是项目管理等领域,品质管理的目标都是通过不断提升品质水平,满足客户的需求,增强企业的竞争力。
本文将对品质管理的重要性进行总结,并提出一些建议,以帮助企业进一步改进品质管理工作。
一、品质管理的重要性品质是企业的生命线,直接影响着企业的市场竞争力和持续发展。
品质管理能够帮助企业实现以下几个方面的重要目标:1. 提高客户满意度:通过不断改进产品和服务的品质,企业能够更好地满足客户的需求,提高客户的满意度。
满意的客户会成为忠实的顾客,并为企业带来更多的业务和口碑传播。
2. 降低成本:品质管理可以帮助企业减少产品或服务的缺陷和质量问题,降低不良率和返工率,从而降低生产成本。
此外,提前预防和发现问题,可以避免因质量问题而导致的额外成本和损失。
3. 提高生产效率:通过优化生产流程、引入先进的生产设备和技术,以及培训和激励员工等措施,品质管理可以帮助企业提高生产效率。
提高生产效率可以缩短交付周期,提高产品的竞争力。
4. 提升企业声誉:品质是企业的形象,优秀的品质管理可以提升企业的声誉和信誉,增强消费者对企业的信任。
这不仅有利于企业与客户的长期合作,还可以吸引更多的潜在客户和合作伙伴。
二、改进建议为了进一步提升品质管理工作,以下是几点改进建议:1. 建立质量文化:企业应该树立质量意识,将品质纳入企业文化之中。
通过加强员工培训和教育,向员工灌输质量优先的理念,使其成为每位员工的自觉追求。
2. 持续改进:品质管理是一个持续改进的过程,企业应该设立一套科学有效的改进机制,定期组织品质评审和审查,找出存在的问题和瓶颈,并采取相应的措施进行改进。
3. 客户参与:客户是企业的品质判定者和最终受益者,他们的意见和反馈对于改进品质至关重要。
企业应该鼓励客户参与品质管理的各个环节,提供方便的渠道和机制,及时反馈客户的意见和需求。
4. 合理评价供应商:供应商的品质直接关系到企业产品或服务的品质,选择和评价供应商应该建立科学的评估体系,对供应商的品质进行合理评价和管理,确保供应链的稳定和可靠。
工作产品质量存在问题问题及整改措施

工作产品质量存在问题问题及整改措施在我们的工作中,保证产品质量是一项重要的任务。
然而,我们可能会遇到一些问题,导致产品质量出现了一些不足之处。
本文将探讨这些问题,并提出适当的整改措施来解决它们。
一、问题描述1.1 设计问题我们的产品设计过程存在一些问题,导致产品在实际使用中出现一些不便之处。
设计方案的细节不够完善,没有考虑到用户的真实需求。
这导致产品在实际使用中存在一些功能性问题,以及易用性不佳的情况。
1.2 生产问题我们的生产过程中也存在一些问题,导致产品的质量无法得到有效保证。
生产环境的精细管理工作不到位,生产线上的操作人员在操作中存在一些疏漏,导致产品在生产中出现一些不合格的情况。
1.3 测试问题产品的测试环节也存在一些问题。
测试方法和测试流程不够科学合理,未能覆盖到所有的测试场景和测试用例。
因此,在产品发布前未能发现一些潜在的问题,导致产品质量得不到充分保证。
二、整改措施2.1 设计问题的整改为了解决设计问题,我们将采取以下措施来改进产品的设计质量:(1)加强需求调研工作,深入了解用户的需求和痛点,以确保设计方案符合用户期望;(2)增加设计方案的细节和完整性,确保产品具备完善的功能性和易用性;(3)引入用户体验设计的理念,注重产品的用户体验,提高产品的用户满意度。
2.2 生产问题的整改为了解决生产问题,我们将采取以下措施来提高产品的生产质量:(1)建立严格的生产管理制度,确保每个环节都得到有效的监控和管控;(2)加强对生产操作人员的培训,提升他们的操作技能和质量意识;(3)引入自动化设备,减少人为操作的影响,提高生产的准确性和效率。
2.3 测试问题的整改为了解决测试问题,我们将采取以下措施来提升产品的测试质量:(1)优化测试方法和流程,确保能够覆盖到所有的测试场景和测试用例;(2)引入自动化测试工具,提高测试效率和准确性;(3)加强测试团队的技能培养和质量意识提升,保证测试工作的有效性和可靠性。
品质管理年度存在的问题及对策
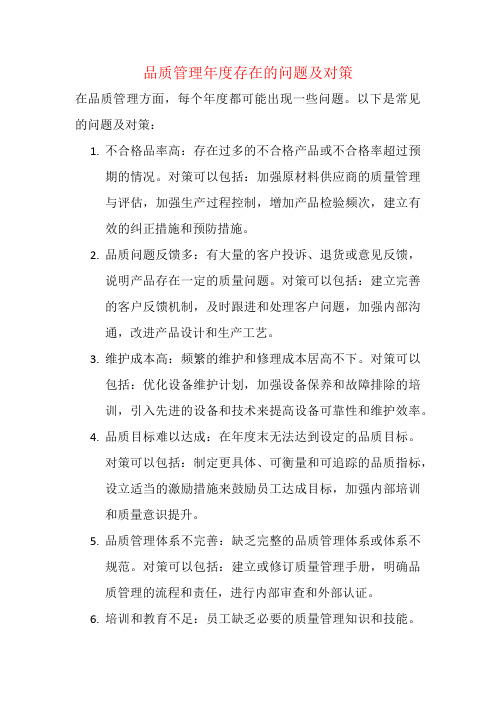
品质管理年度存在的问题及对策
在品质管理方面,每个年度都可能出现一些问题。
以下是常见的问题及对策:
1.不合格品率高:存在过多的不合格产品或不合格率超过预
期的情况。
对策可以包括:加强原材料供应商的质量管理
与评估,加强生产过程控制,增加产品检验频次,建立有
效的纠正措施和预防措施。
2.品质问题反馈多:有大量的客户投诉、退货或意见反馈,
说明产品存在一定的质量问题。
对策可以包括:建立完善
的客户反馈机制,及时跟进和处理客户问题,加强内部沟
通,改进产品设计和生产工艺。
3.维护成本高:频繁的维护和修理成本居高不下。
对策可以
包括:优化设备维护计划,加强设备保养和故障排除的培
训,引入先进的设备和技术来提高设备可靠性和维护效率。
4.品质目标难以达成:在年度末无法达到设定的品质目标。
对策可以包括:制定更具体、可衡量和可追踪的品质指标,设立适当的激励措施来鼓励员工达成目标,加强内部培训
和质量意识提升。
5.品质管理体系不完善:缺乏完整的品质管理体系或体系不
规范。
对策可以包括:建立或修订质量管理手册,明确品
质管理的流程和责任,进行内部审查和外部认证。
6.培训和教育不足:员工缺乏必要的质量管理知识和技能。
对策可以包括:制定完善的培训计划,包括品质意识培训、操作规程培训、质量问题解决方法培训等,加强员工的质
量管理意识和技能。
以上是一些常见的品质管理问题及对策,每个企业的具体情况会有所不同,需要根据实际情况进行针对性的分析和解决。
品质部工作不足及改进措施总结
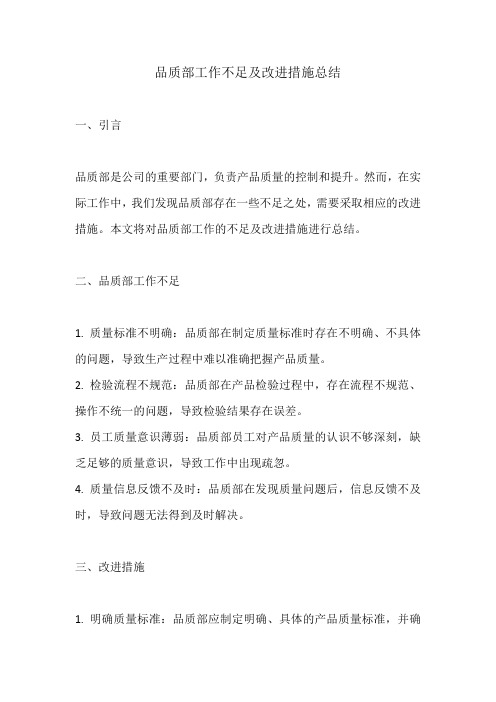
品质部工作不足及改进措施总结一、引言品质部是公司的重要部门,负责产品质量的控制和提升。
然而,在实际工作中,我们发现品质部存在一些不足之处,需要采取相应的改进措施。
本文将对品质部工作的不足及改进措施进行总结。
二、品质部工作不足1. 质量标准不明确:品质部在制定质量标准时存在不明确、不具体的问题,导致生产过程中难以准确把握产品质量。
2. 检验流程不规范:品质部在产品检验过程中,存在流程不规范、操作不统一的问题,导致检验结果存在误差。
3. 员工质量意识薄弱:品质部员工对产品质量的认识不够深刻,缺乏足够的质量意识,导致工作中出现疏忽。
4. 质量信息反馈不及时:品质部在发现质量问题后,信息反馈不及时,导致问题无法得到及时解决。
三、改进措施1. 明确质量标准:品质部应制定明确、具体的产品质量标准,并确保生产过程中严格按照标准执行。
2. 规范检验流程:品质部应对产品检验流程进行规范,统一操作方法,确保检验结果的准确性和可靠性。
3. 加强员工质量意识培训:通过培训、宣传等方式提高品质部员工的质量意识,使其充分认识到产品质量的重要性。
4. 建立质量信息反馈机制:品质部应建立完善的质量信息反馈机制,确保在发现问题后能够及时、准确地反馈给相关部门,以便问题得到及时解决。
5. 强化质量监管:品质部应加强对产品质量的监管力度,对生产过程中的关键环节进行重点把控,确保产品质量符合要求。
6. 持续改进:品质部应持续关注产品质量问题,不断优化质量标准和检验流程,提高产品质量和客户满意度。
四、总结品质部工作存在不足之处,需要采取相应的改进措施。
通过明确质量标准、规范检验流程、加强员工质量意识培训、建立质量信息反馈机制、强化质量监管和持续改进等措施,可以提升品质部的工作水平,提高产品质量和客户满意度。
品质存在问题及整改措施

品质存在问题及整改措施品质存在问题及整改措施品质是企业生存与发展的核心竞争力之一。
然而,在市场竞争激烈的环境下,很多企业在品质方面存在着一些问题。
本文将结合实际情况,探讨品质存在的问题,并提出相应的整改措施。
首先,一些企业在产品设计方面存在问题。
由于市场需求的快速变化和竞争对手的挑战,一些企业为了追求新颖和独特,过于注重外观设计而忽略了产品的功能和实用性。
这导致一些产品虽然外表华丽,但在实际使用中存在各种问题,不符合用户的需求。
因此,企业应该加强对市场需求的调研和产品设计的研发,注重产品的功能和实用性,确保产品的品质达到用户的期望。
其次,一些企业在生产过程中存在品质控制不严的问题。
生产过程中存在的品质问题主要包括原材料的选择和加工过程的质量把控。
一些企业为了追求利润最大化,选择了价格低廉的劣质原材料,导致产品在使用过程中容易出现各种问题。
此外,一些企业在加工过程中的质量把控不严,没有建立科学的生产流程和标准操作规范,容易导致产品质量不稳定。
因此,企业应该加强对原材料的选择和加工过程的监控,确保原材料的质量和加工过程的质量符合标准,从而提高产品的品质稳定性。
再次,一些企业在售后服务方面存在问题。
售后服务是产品品质的延展,也是企业与用户建立长久合作关系的关键。
然而,一些企业在售后服务方面存在态度不良、服务不到位的问题,导致用户在遇到问题时得不到及时的解决和满意的答复。
因此,企业应该加强对售后服务的重视,建立完善的售后服务体系,培养专业化的服务人员,提供全方位、高质量的售后服务,从而提高用户对企业的满意度。
针对以上问题,企业应该采取相应的整改措施。
首先,企业应该加强对市场需求的研究和产品设计的创新,确保产品的功能和实用性符合用户的期望。
其次,企业应该加强对生产过程的监控和质量控制,建立科学的生产流程和标准操作规范,确保产品的品质稳定性。
最后,企业应该重视售后服务,建立完善的售后服务体系,培养专业化的服务人员,提供高质量的售后服务,从而提高用户的满意度。
品质改善的建议和想法
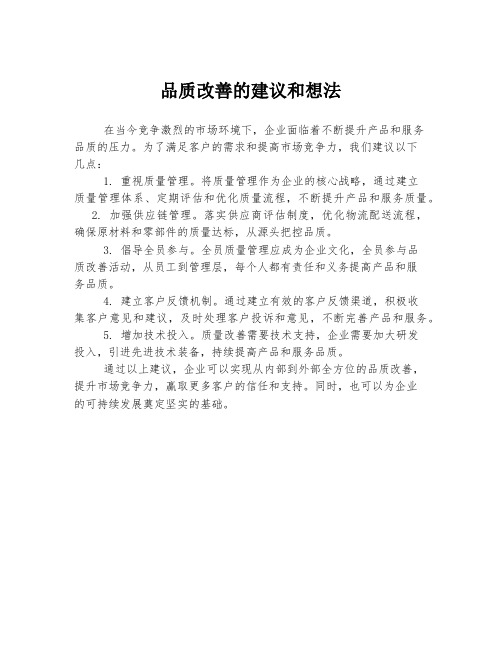
品质改善的建议和想法
在当今竞争激烈的市场环境下,企业面临着不断提升产品和服务
品质的压力。
为了满足客户的需求和提高市场竞争力,我们建议以下
几点:
1. 重视质量管理。
将质量管理作为企业的核心战略,通过建立
质量管理体系、定期评估和优化质量流程,不断提升产品和服务质量。
2. 加强供应链管理。
落实供应商评估制度,优化物流配送流程,确保原材料和零部件的质量达标,从源头把控品质。
3. 倡导全员参与。
全员质量管理应成为企业文化,全员参与品
质改善活动,从员工到管理层,每个人都有责任和义务提高产品和服
务品质。
4. 建立客户反馈机制。
通过建立有效的客户反馈渠道,积极收
集客户意见和建议,及时处理客户投诉和意见,不断完善产品和服务。
5. 增加技术投入。
质量改善需要技术支持,企业需要加大研发
投入,引进先进技术装备,持续提高产品和服务品质。
通过以上建议,企业可以实现从内部到外部全方位的品质改善,
提升市场竞争力,赢取更多客户的信任和支持。
同时,也可以为企业
的可持续发展奠定坚实的基础。
品质改善的建议和想法

品质改善的建议和想法品质改善是生产和服务行业的重要课题,它可以保证公司的竞争力和客户的满意度。
以下是一些关于品质改善建议和想法的列表:1.设立品质目标首先,公司应该设立品质目标和衡量指标,以评估产品和服务的品质水平。
这些指标可以包括客户满意度、产品缺陷率、服务响应时间等。
2.实行员工培训员工是保障产品和服务质量的关键,提高员工的技能和知识水平对于品质改善至关重要。
公司可以针对不同岗位进行培训,使员工能够更好地理解他们的职责和如何提高品质水平。
3.优化生产流程流程优化可以消除生产过程中的浪费和瑕疵,提高生产效率和品质水平。
例如,使用精益生产技术,减少库存和制造时间,提高可靠性和减少变化。
4.加强供应商管理供应商管理是生产过程中一个重要的环节,公司应该和供应商进行紧密合作,确保他们提供的原材料和零部件符合公司质量要求。
对于不能满足品质标准的供应商,公司应该采取措施,例如培训或寻找替代供应商。
5.引入新技术新技术的引入可以提供更高效的生产方式和更高的品质标准。
例如,自动化技术可以提高生产效率和质量水平,智能系统可以监测生产过程中的问题,提高产品质量。
6.加强产品测试产品测试是确保产品符合标准的关键步骤,公司应该加强产品测试环节,包括原材料测试、组装测试、成品测试等。
测试结果应该记录并及时反馈给生产部门。
7.推广质量文化质量文化是保证品质水平的最基本因素之一,公司应该培养一支具有高度质量意识的员工队伍,建立良好的品质文化和价值观,让品质意识贯穿全公司。
以上是一些关于品质改善的建议和想法,公司可以根据自身情况选择适合自己的措施,不断提高产品和服务的品质水平,满足客户需求,增强市场竞争力。
质量管理方面的不足及建议

质量管理方面的不足及建议质量管理在一个组织的运营过程中扮演着非常重要的角色,对于产品或服务的质量提升和客户满意度的提高起着关键作用。
然而,很多组织在质量管理方面存在着一些不足之处。
下面我将讨论一些常见的不足,并提出一些建议来改进质量管理。
首先,许多组织在质量目标和指标的设定方面存在不足。
有些公司倾向于设定过于宽泛的质量目标,缺乏具体性。
例如,他们可能只设定“提高产品质量”的目标,而没有明确标识应该提高哪些方面的质量。
这样的目标缺乏可衡量性和可操作性,导致无法有效跟踪和改进质量。
解决这个问题的一个建议是,组织应该设定明确的、可衡量的质量目标和指标。
这样的目标应该是具体和可操作的,并且可以与组织的战略目标相连接。
例如,一个目标可以是“减少产品的缺陷率至少10%,以提高客户满意度”。
这样的目标可以追踪和测量,可以衡量改善的成果,并与最终的客户满意度相关联。
其次,许多组织在质量监控和改进过程中存在不足。
有些公司只在最终产品或服务交付之后才进行质量检查,而忽视了在生产或提供过程中可能发生的问题。
这种被动的方法可能导致无法及时发现和纠正质量问题,增加了重做或修复的成本。
为了改善这个问题,建议组织采用主动的质量监控方法。
这包括实施实时监控和检测机制,以便在生产或提供过程中及时发现和解决质量问题。
例如,可以使用六西格玛、统计过程控制等工具和技术来监测质量数据,以及发现和纠正异常情况。
此外,组织还可以实施持续改进方法,例如质量圈、PDSA 循环等,以鼓励员工积极参与质量改进的过程。
第三,许多组织在培训和教育方面存在不足。
有些公司往往只关注技术培训和操作指导,而忽视了质量管理和质量控制的培训。
这导致了员工对于质量管理的理解和重要性的欠缺,无法有效地参与质量改进的活动。
针对这个问题的一个建议是,组织应该提供全面的质量培训和教育计划。
这包括质量管理的基本概念和方法,员工如何识别和解决质量问题,以及如何应用质量工具和技术等。
品质管理部质量改进措施总结
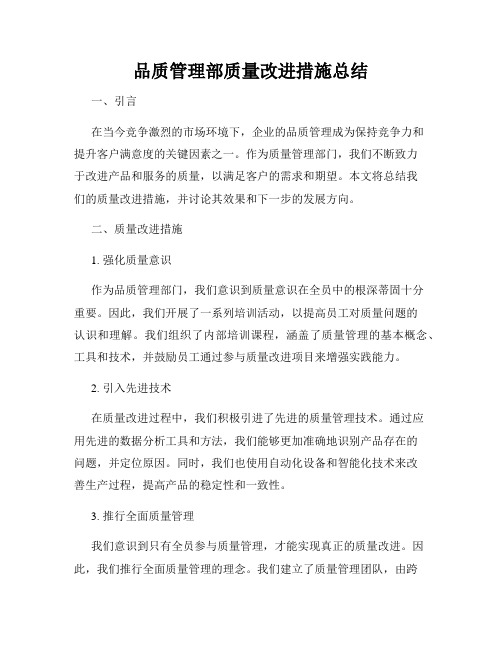
品质管理部质量改进措施总结一、引言在当今竞争激烈的市场环境下,企业的品质管理成为保持竞争力和提升客户满意度的关键因素之一。
作为质量管理部门,我们不断致力于改进产品和服务的质量,以满足客户的需求和期望。
本文将总结我们的质量改进措施,并讨论其效果和下一步的发展方向。
二、质量改进措施1. 强化质量意识作为品质管理部门,我们意识到质量意识在全员中的根深蒂固十分重要。
因此,我们开展了一系列培训活动,以提高员工对质量问题的认识和理解。
我们组织了内部培训课程,涵盖了质量管理的基本概念、工具和技术,并鼓励员工通过参与质量改进项目来增强实践能力。
2. 引入先进技术在质量改进过程中,我们积极引进了先进的质量管理技术。
通过应用先进的数据分析工具和方法,我们能够更加准确地识别产品存在的问题,并定位原因。
同时,我们也使用自动化设备和智能化技术来改善生产过程,提高产品的稳定性和一致性。
3. 推行全面质量管理我们意识到只有全员参与质量管理,才能实现真正的质量改进。
因此,我们推行全面质量管理的理念。
我们建立了质量管理团队,由跨部门的代表组成,定期开展质量问题的分析和解决。
同时,我们也鼓励员工提出改进建议,并及时反馈和落实。
4. 强化供应商管理供应商的质量水平直接关系到产品和服务的质量。
因此,我们加强了对供应商的管理和监督。
我们采用供应商评估制度,对供应商的质量管理体系、生产能力和产品质量进行评估和监控。
同时,我们与优质供应商建立了长期合作关系,共同致力于提供高品质的产品和服务。
5. 建立质量指标体系为了更好地掌握和评估质量改进的效果,我们建立了一套完善的质量指标体系。
我们分析和监控关键质量指标,如客户投诉率、产品合格率和交付准时率等,以便及时发现问题并采取相应的纠正措施。
同时,我们也定期进行内部质量审核,以确保各项质量管理工作的有效运行。
三、质量改进效果通过以上的质量改进措施,我们取得了一系列显著的成果。
首先,产品的质量得到了明显的提升,客户的满意度显著提高。
- 1、下载文档前请自行甄别文档内容的完整性,平台不提供额外的编辑、内容补充、找答案等附加服务。
- 2、"仅部分预览"的文档,不可在线预览部分如存在完整性等问题,可反馈申请退款(可完整预览的文档不适用该条件!)。
- 3、如文档侵犯您的权益,请联系客服反馈,我们会尽快为您处理(人工客服工作时间:9:00-18:30)。
品质部 8
目录
一:品质管理现状分析 二:品质管理流程设计 三:品质部门人员架构设计 四:品质部门岗位职责设计 五:品质部质量目标分解
一:品质管理现状分析
A、存在主要问题点
1. 部门质量管理目标达成情况没有落实到到位,没有进行月度统计分析并制定改善对策。 2. 供应商在选择,评估,辅导及来料异常改善跟踪及效果方面不完善。 3. 进料检验抽样方法,检难手段不完善,导至部分问题在抽样时不能发现,流入到产线。 4. 生产过程中没有进行直通率统计,不良品管理不完善,现场标识,区域划分欠缺。现场管理人员管理要求不严。 5. 对于制程问题缺少对应的书面改善措施及改善效果确认记录。 6. 人员的培训工作不到位,特别是线检FQC不固定,且相应的培训及培训效果没有得到确认,导致FQC对产品的质量要求
生产问题总结
13 QA验货
1、确定QA抽检最小批量,确保不会整批生产完才发现问题。 2、确保订单信息以及客人追加要求正确传达到QA检验员处。 3、QA 检出力的培训,客户验货标准的培训。
QA验货报告
品质部
备பைடு நூலகம்: 具体流程详见品质管理流程图
加黑部分重点控制
三、品质管理架构
QE工程师
实 验 试 测 试 员
生产工程部 品质部 各相关部门
完善生产订单内容:确保订单信息全面、准确反应客户要求。评估产能, 所需要的工装夹具,检测仪器设备是否足够可用
生产订单 验货标准
各相关部门
编
流程
号
要点
文件记录要求 责任部门
11 来料检验
应保证来料检验时间,配置合适的检验人员及检验标准样板、检验场地和 IQC检验报告 设备仪器
品质部按客户要求,检验,试验标准进行测试,对测试结果进行汇总
生产工程部对试产中各部门提出问题进行汇总,组织试产总结确认改善行 动。品质部跟踪对策实施效果并及时通报相应部门。对于严重质量问题没 有改善品质部应有权拒绝批量生产。正式作业指导书、工装夹具的完善
试产记录
样机测试报告, 可靠性测试报告
试产评估报告及 改善对策
2 产品初步设计、打样及测试 及改善
3 送样给客户确认,进一步明 确客户要求,并协定质量要 求
4 客户提出问题改善
5 制定初步检验标准,可靠性 测试标准,生产作业指导书
6 物料初步确认,质量要求正 确传达供应商
7 试产
8 检验测试
9 试产评估,总结改善行动及 改善效果确认,
10 订单评审,确定客户要求, 法律法规要求正确传达到各 责任部门
1
1
0
3
QE工 程师
跟进新产品开发和改善,制定检验测试标准和测试计划并确保有效实施,对 生产异常问题进行分析反馈跟踪。参与供应商管理以及新物料的验证。
1
1
0
4
实验室 实施新产品可靠性测试,生产抽检可靠性测试,原材料,辅料ROHS符合性测 技术员 试并出报告
1、对现有检验标准进行收集整理,列出目录,进行适当的 整合,修订和完善,确保客户要求能正确反映到检验标准内 容中。 2、请市场部与客户沟通提供客户验货标准。(特别是外观 和包装要求相当重要
备注
序号
8
问题点
品质状态统计分析欠缺
9
新产品开发验证问题
10
原材料,辅料ROHS测试
改善建议
1、完善月度来料质量统计,所有供应商纳入考核体系,按月统计 结果进行评级,连续三个月C级供应商应取消资格 2、对每周生产发生的质量问题进行统计分析,相关部门对前五项 重大问题制定改善对策并落实到位。 3、每月质量问题地蚝统计分析检查周改善措施有落实情况 4、生产部每日生产质量情况进行统计,确保生产直通率达到质量 目标,对达不到直通率要求的原因要进行分析再第二日早会时告 知所有员工。 5、每周对IPQC巡检报告进行统计分析,找出前五项重要问题进 行分析解决。 6、坏机的修理必须有记录和统计分析找出主要问题来解决。 7、每月对QA抽检结果进统计找出前五项重要问题点进 行善。 8、对于客户投诉进行月度统计检查有无改善行动且是否达到果。
品质主管
品质部文员
IQC
塑
电
胶
子
五
料
金
检
包
验
材
检
验
IPQC
制 程 巡 检 员
QA
组
装
包
成
装
品
抽
抽
检
检
QA
QA
四:品质部人员需求表与岗位职责
序 号
职位
职责
现有 需求 欠缺 人数 人数 人数
1
主管
全面负责品质部工作计划,组织,实施和检查工作,确保产品质量达到质量 目标符合客户要求
0
1
1
2 文员 部门人事,文件收发,质量记录统计工作
要点
文件记录要求 责任部门
产品性能参数,认证要求,外观、包装等要求必须有效传达到设计开发部 门
客户要求一览表 法律法规要求
市场部
设计开发部门严格按上述要求进行开发
产品开发任务书 开发部 (内容要全面)
必须明确客人的质量要求并确认传达到每个部门
客户质量要求 (检验标准)
市场部
应确保客人提出问题得到改善并将问题点传达到相应执行部门关注存在问 题点
改善建议
1、各部门应制定本部门质量目标,对本部门各项工作进行分解,确 定合理目标。 2、制定达成质量目标的相关措施,并进行月度统计分析,明确达成 与未达成原因。制定相应的改善对策 3、定期召开质量目标达成情况通报会,确保质量目标达成情况的传 达。 4、对每月质量目标达成情况进行公示,起到教育宣传及监督的做用。 5、质量目标达成情况列入部门主管的绩效考核。
品质部
12 正式生产,制程品质控制存、 生产部,品质部对所有发生的品质、生产效效、物料、包装材料等所有问 生产日报
在问题改善
题进行统计汇总。由生产部组织相关部门评审,品质部跟进改善措施效果 FQC检验记录
与进度及时向公司领导汇报确保所有问题有效解决或承认
IPQC巡检报告
生产部 品质部
生产抽样可靠性
测试报告
样品评估记录, 改善对策,
开发部 品质部
标准内容应能符合客人要求且更加严格
产品规格书,生 产做业导书,可 靠性试验标准
开发部 生产工程部
应确保物料的质量要求准确的传达到供应商和检验部门。将原材料确认规 原村料规格书, 开发部
格书,样板发放到检验部门
图纸,样品
开发部,生产工程部,品质部应全程跟进试产(从贴片到包装)并记录存 在问题点
1、制定ROHS管控程序和测试计划,确定重点管控物料清单。 2、实验室配备可靠性测试和ROHS测试员实施检测和管控。 3、对测试结果进行统计确保物料符合ROHS要求减少风险。
备注
序号
11
问题点
保持生产,检验等指导性资料 一致性的问题
改善建议
1、在生产订单下发前市场部应尽量与客户沟通确定最终要求, 避免经常性订单信息变更或增加要求。
2
供应商质量控制
3
进料检验检出度
4
生产过程的控制
1、完善供应商选择,评估,考核标准并执行 2、确保物料质量要求得到正确的实别并传达到供应商
1、完善物料的检验标准和抽检方法。 2、对IQC进行培训。 3、制做不良品图示 4、完善对IQC检出力的评估与考核制度。 5、建立合理的标准工时。
1、操作员必须了解产品的质量要求 2、FQC必须熟练撑握产品功能、测试方法,仪器的使用方法 3、每日必须统计生产直通率,存在问题点 4、IPQC应按QC工程图至少巡检3次并记录 5、IPQC必须按可靠性试验标准对产品进行抽检做测试 6、生产现场标识必须明确,物料,产品摆放必须合理。 7、静电管理必须按规定执行 8、检验、测试设 备必须合格有效 9、使用电网电源的产品必须核 对关键元件生产工艺必须符合认证 样机要求 10、每日质量状态要公示,重要问题要拍照公示。 11、改善方案也要公示确保相关人员都了解
5、对于产品功能一致,但结构、电子、外观有区别的产品一定 要在命名上有区分,并编制相对应的规格书,BOM表。避免混乱。
6、对于ECN工程变更,在发放ECN通知前ERP系统应该提前更新。 避免生产,检验不看ECN只看ERP 时出错。
7、对于可靠性测试标准应制定唯一一个,不必要每一种产品或 型号都编制一份,方便文件管理和使用。可靠性标准上的试验项 目要有可操作性,不能操作的项目或没有设备测试的项目不必要 写出来,这样审厂与实际操作中不会有疑问。(到底怎么做,做 还是不做这项)
1、应确保新产品相关支持文件及内容的完整,任务书内应明确开 发产品的功能,电气参数,安规认证要求,外观尺寸,目标市场, 产品包装运输方式等。 2、应确定新产品检验试验的项目和标准。 3、要严格按试验项目和标准实施 验证并记录。 4、对验证出现的问题应及时采取改善措施再次验证,否则不能批 量生产。 5、对于暂时无法改善的但又急需要生产出的问题应由市场部或最 高负责人签字确认可 暂生产才能批量生产。 6、新产品批量试产后要对生产过程和检验过程中发的问题进行统 计和分析,并制定改善计划,品质部QE负责验证改善效果并反馈 到开发部。直到所有问题得到改善为止。
备注
序号
5
问题点
制程问题的改善和跟踪欠缺
6
人员培训
7
品质部检验标准完善和培训
改善建议
1、对于生产过程中出现的问题品质部应当详细的记录,不 良率超过5%时生产部或品质部应该发出品质异常联络单。 (属于物料、设计问题的由生产部发出,属于制程不良或工 艺不良的由品质部提出。) 2、对于生产部和品质部提出的问题,生产主管,生产工程, 品质部三个部门应立即组织会议讨论解决方案。并马上实施 改善,如与设计有关则要求开发部参与共同讨论解决方案。 3、对于改善方案的改善效果生产部和品质部应进行确认可 行有效才能结案。 4、对于发生品质问题每周都应进行总结分析,确保品质问 题得到有效传达、改善和追踪到位。 5、物料品质问题采购部应协助品质部传达到供应商并追踪 供应商的改善方案,品质部IQC负责改善效果验证。采购部 应确保物料的质量要求有效的传达到供应商处并签定质量保 证协意。