第三章 弯 曲 (2)
第三章 受弯构件分析

M A coskl M B
M
2 A
2M
AM
B
coskl
M
2 B
coskx
M A sin kl
M
2 A
2M
AM
B
cosk
l
M
2 B
kl P 故0 kx
PE s in kx 0,coskx 0
M max M x EIyx
M B
(M A / M B )2 2(M A / M B ) coskl 1 sin2 kl
A
ql 2EIk 3
,B
ql 2 EIk 3tg
kl
,C
ql 2EIk 2
,D
ql 2 EIk 3tg
kl
2
2
ql
cos kx
1 kx2
y
2EIk 3
sin kx
tg
kl 2
kx tg kl 2
l
2020/10/19
7
3.1弹性压弯构件的基本微分方程
M max
EI
y x0
EI
y xl
2)
secu 1 1 u2 5 u4 61 u6 2 24 720
考虑到:u2 2 P 2.4674 P
4 PE
PE
2020/10/19
3
3.1弹性压弯构件的基本微分方程
ym a x
0(1 1.0034
P PE
1.0038( P PE
)2
)
0(1
P Pcr
0.610
P Pcr
0.608
P Pcr
1
0.6
P Pcr
1.097
第三章 弯曲-08

式中: ——最大自由弯曲力,即自由弯曲在冲压行程结束时的弯曲力,N;
σb——材料抗拉强度,MPa; k——安全系数,一般取k=1.3; b——弯曲件宽度,mm; r——弯曲件的内弯曲半径,mm; t——板料厚度,mm。
冲压工艺与学——弯曲
2.应力状态
切向ζθ:内区受压,外区受拉。 径向ζρ :塑性弯曲时,由于变形区曲度增大,以及金属各层之间的相互 挤压的作用,从而引起变形区内的径向压应力ζρ,在板料表面ζρ= 0,由表及 里逐渐递增,至应力中性层处达到了最大值。 宽度方向ζb :对于窄板,由于宽度方向可以自由变形,因而无论是内区 还是外区ζb =0;对于宽板,因为宽度方向受到材料的制约作用,σb ≠0。内 区由于宽度方向的伸长受阻,所以σb为压应力。外区由于宽度方向的收缩受 阻,所以σb为拉应力。 结论:窄板弯曲时的应力状态是平面的,宽板则是立体的。
内移结果:外层拉伸变薄区范围逐步扩大,内层压缩增厚区范 围不断减小,外层的减薄量会大于内层增厚量,从而使弯曲区板料 厚度变薄。 规律:r/t愈小,变形程度愈大,系数ξ就愈小,弯曲区的变薄 现象也愈严重(见表3-1) 。 影响:弯曲时的厚度变薄会影响零件的质量。
四、板料长度的增加
一般弯曲件,其宽度方向尺寸b比厚度方向尺寸大得多,所以弯曲前 后的板料宽度b可近似地认为是不变的。 由于板料弯曲时中性层位置向内移动,出现了板厚的减薄,根据体积 不变条件,减薄的结果使板料长度必然增加——相对弯曲半径r/t愈小,减 薄量愈大,板料长度的增加量也愈大。 对于r/t值较小的弯曲件:在计算弯曲件的毛坯长度时,必须考虑弯曲 后的板料增长,并通过多次试验,才能得出合理的毛坯展开尺寸。有关毛
冲压工艺与学——弯曲
在r/t≤4的情况下弯曲,由试验测定系数ξ<1(见表3-1),因此,由 r 。 1 / 2 t 式(3-3)可知,当ξ<1时,应变中性层位置ρ0将小于 而 r 1 / 2 t 为塑性弯曲时的中心位置, 0 r 1 / 2 t 则表示了塑性弯曲 时应变中性层位置向内移动。 由表3-1看出:系数ξ值随r/t大小变化,r/t愈小,ξ值也愈小,应 变中性层的内移量就愈大。——凸模下行,变形程度不断增加,应 变中性层位置逐步向内移动,变形量愈大,中性层的内移量也愈大。 结论:由应变中性层内移可知,应变中性层处的纤维在弯曲前 期的变形是切向压缩,而弯曲后期必然是伸长变形,才能补偿弯曲 前期的纤维缩短,使其切向应变为零。而弯曲后期的纤维伸长变形, 一般来说,仅发生在应力中性层的外层纤维上。由此可见,应力中 性层在塑性弯曲时也是从板料中间向内层移动的,且内移量比应变 中性层还大。
弯曲ppt课件

§3.1 板料的弯曲现象及其原因
五、板料横截面的畸变、翘曲和拉裂(翘曲)
弯曲后的翘曲
§3.1 板料的弯曲现象及其原因
五、板料横截面的畸变、翘曲和拉裂(翘曲)
弯曲后的翘曲
§3.1 板料的弯曲现象及其原因
五、板料横截面的畸变、翘曲和拉裂(翘曲)
型材、管材弯曲后的剖面畸变
§3.1 板料的弯曲现象及其原因
变形程度愈大,变薄现象愈严重。 弯曲时的厚度变薄会影响零件的质量。因此,在拟定弯 曲工艺和模具设计时,必须采取有效措施,才能弯制出合乎 要求的零件。
§3.1 板料的弯曲现象及其原因
四、板料长度的增加
根据体积不变条件,弯曲区板料厚度的减薄的结果使板 料长度l必然增加。相对弯曲半径r/t愈小,减薄量愈大,板 料长度的增加量也愈大。因此,对于r/t值较小的弯曲件, 在计算弯曲件的毛坯长度时,必须考虑弯曲后板料增长, 并通过多次弯曲试验,才能得出合理的毛坯展开尺寸。
§3.1 板料的弯曲现象及其原因
三、弯曲区板料厚度的变薄
板料弯曲时,以中性层为界,外层纤维受拉使厚度减薄, 内层纤维受压使板料增厚。我们知道,在r/t≤4时,应变中性 层向内移动。内移结果:外层拉伸变薄区范围逐步扩大,内 层压缩增厚区范围不断减小,外层的减薄量会大于内层的增 厚量,从而使弯曲区厚度变薄。
§3.1 板料的弯曲现象及其原因
五、板料横截面的畸变、翘曲和拉裂(畸变)
窄板(B/t≤3) 宽板(B/t>3) 弯曲变形区的横截面变化情况
§3.1 板料的弯曲现象及其原因
五、板料横截面的畸变、翘曲和拉裂(畸变)
变形区横断面形状尺寸发生改变称为畸变。主要影响因 素为板料的相对宽度。
b/t > 3(宽板) 横断面几乎不变; b/t≤3(窄板) 断面变成了内宽外窄的扇形。
模具设计与制造第三章作业

第三章弯曲模作业参考答案3-1.板料弯曲的变形过程是怎样的?其塑性变形区在何处?答:以V形件弯曲的变形过程为例。
在弯曲开始时,板料是自由弯曲,随着凸模的下压,板料的直边与凹模工作表面逐渐靠模,曲率半径和弯曲力臂逐渐变小。
凸模继续下压,板料弯曲变形区进一步减小,曲率半径和弯曲力臂不断变小,继而板料直边部分向以前相反方向弯曲。
直至板料直边、圆角与模具全部靠模。
塑性变形区域主要发生在弯曲圆角部位,内侧受应力板材压缩变短;外侧受拉应力,板材伸长;而中性层长度不变。
3-2.弯曲变形区内,板料的横截面会发生什么变化?为什么会产生这种变化?答:1)弯曲变形区内,板料的横截面变化分两种情况:①宽板(板料宽度大于3倍板料厚度:b 〉3t),弯曲后横截面无明显变化,仍保持为矩形;②窄板(板料宽度小于3倍板料厚度:b〈3t),弯曲后原横截面矩形断面变成了扇形。
由于弯曲凸模对板料内侧摩擦力的影响不同、和板料宽度不同板料内外侧受压受拉影响塑性变形程度不同导致窄板弯曲的应力状态是平面的,应变状态是立体的;宽板弯曲的应力状态是立体的,应变状态是平面的。
3-3.什么是最小弯曲半径?影响最小弯曲半径的因素有哪些?答:1)最小弯曲半径:在保证毛坯外层纤维不发生破坏的条件下,所能弯曲零件内表面的最小圆角半径,称为最小弯曲半径。
2)影响最小弯曲半径的主要因素有:①材料的机械性能。
塑性越好的的材料外层纤维允许的变形程度的变形程度大,则允许的最小弯曲半径越小;塑性差,则最小弯曲半径变大。
板材状态也对弯曲半径有很大影响,硬材料或冷作硬化的材料允许的最小弯曲半径大。
②弯曲线方向。
当弯曲线方向与纤维方向垂直时,则最小弯曲半径小;当两者平行时,最小弯曲半径大。
③板材表面质量和侧面质量。
当板材表面和侧面质量差时,由于易产生应力集中和塑性降低使材料过早破坏,故应采用较大的弯曲半径。
如果板料未去毛刺时,可将有毛刺一边(方向)置于凸模一侧也可提高弯曲变形成型极限,减少零件外侧产生裂纹的可能。
第三章 弯曲

第三章 弯 曲
弯曲:将板料、型材、管材或棒料等按设计要求弯 成一定的角度和一定的曲率,形成所需形状零件的 冲压工序。 弯曲毛坯的种类:板料、棒料、型材、管材
本章与第2章相比:
准确工艺计算难,模具动作复杂、结构设计规律性不强。
弯 曲 成 形 典 型 零 件
生活中的弯曲件
压弯的典型形状: 典型压弯工件:
内层切向应力
内 2 3 n 1 B n 1 1 - ln 0 n 1 - - ln R 0 n 1 - - ln 0 n 3 - 1 9
§3.3 宽板弯曲时的应力和弯矩的计算
二、按宽板弯曲的平面应变状态计算变形区的应力数值 外层宽度方向上的主应力
曲
8、9-螺钉
模
10-定位板
用模具成形的弯曲件之一
用模具成形的弯曲件之二
连续弯曲模拟 闹钟双铃提环弯曲模模拟 阶梯件弯曲模 双摆块弯曲模 摆块式形件弯曲模 圆筒形件一次弯曲 自动卸料机构的摆块弯曲模
§3.1 板料的弯曲现象及其原因
(a)
(b)
(c)
(d)
在弯曲过程中,板料的弯曲半径r1、r2…rn与支点距离l1、 l2…ln随凸模下行逐渐减小,而在弯曲终了时,板料与凸、凹
第三章 弯 曲
§3.1 板料的弯曲现象及其原因 §3.2 窄板弯曲和宽板弯曲时的
应力应变状态分析 §3.3 宽板弯曲时的应力和弯矩的计算 §3.4 弯曲力计算和设备选择 §3.5 弯曲件毛坯长度计算 §3.6 最小相对弯曲半径rmin/ t的确定 §3.7 弯曲回弹 §3.8 弯曲模工作部分的尺寸计算
§3.1 板料的弯曲现象及其原因
五、板料横截面的畸变、翘曲和拉裂(畸变)
窄板(B/t≤3) 宽板(B/t>3) 弯曲变形区的横截面变化情况
第三章-----弯曲模

当中性层半径确定后,即 可按照几何方法计算中性 层展开长度,进而计算出 板料的展开长度。由于材 料的性能、弯曲方法不同, 中性层的位置将受到影响。
四、弯曲力计算
弯曲力:工件完成预定弯曲时需要压力机所施加的压力。 弯曲力不仅与材料品种、材料厚度、弯曲几何参数有关,
还同设计弯曲模所确定的凸、凹模间隙大小等因数有关。 1、自由弯曲的弯曲力计算 V形弯曲件的计算F1=(0.6KBt²σb)÷(R+t) U形弯曲件的计算F1=(0.7KBt²σb)÷(R+t) 式中F1―自由弯曲力
-8中选取。
第二节 弯曲模设计示范
双向弯曲模
零件名称:铰支板 生产批量:中批量 材料:10钢,厚1.2mm 零件简图:如图3-26所示
1、弯曲工艺与模具结构
工件的冲压由落料和弯曲两道工序组成。(在此只介绍弯曲模的设计) 本工件的弯曲工艺可分为左、右两部分;左边是U形弯曲,右边是Z形弯曲。 若用两套弯曲模分别完成左、右两部分的弯曲,将增加模具费用。
凸板式模 材 中R的 弯、圆 曲角 用R凸半 :-R径凸弯R曲凸1。件 、3R弯Es Rt曲凸棒模材圆弯角曲半用径R(凸 m1m 3).R4 ;EsdR
σs-材料屈服点(MPa);
E-材料弹性模量(MPa);
d-棒材直径(mm)。
当R<(5~8)t时,工件的弯曲半径一般变化不大, 只考虑角度回弹。角度回弹的经验数值查表3-4和表 3-5得到。
曲是指在上述基础上凸模再往下压,对弯
曲件起校正作用,从而使工件产生进一步
的塑性变形。
当弯曲工件有特殊要求,
二、弯曲零件的工艺性
其圆角半径必须小于最小弯曲 圆角半径时,可设法提高材料
1、弯曲件的圆角半径 材料产生塑
平面弯曲专业知识

+Q -Q
+M -M
剪力和弯矩方程、剪力图、弯矩图
弯矩绝对值最大旳截面就是梁旳危险 截面。经过剪力方程和弯矩方程来反应剪 力和弯矩沿着梁轴变化旳规律,找到最大 剪力、最大弯矩,拟定危险截面
作出Q-x和M-x即分别为 剪力图和弯矩图
a
A
x1
1
集 中 载 荷:集中在梁旳某一点上
分 布 载 荷:作用在梁旳一段较长旳范围 内旳力,有均匀和非均匀分布(q)
集 中 力 偶:作用在纵向平面内旳力偶 (M0)
梁支座简化:简支梁、外伸梁、 悬臂梁
简 支 梁: 一端固定铰链,另一端活动铰链
外 伸 梁: 梁旳一端或两端伸出支座之外,其 他与简支梁一样
悬 臂 梁: 一端固定另一端自由旳梁
RA
x2 C
Q2
M2
Fy=0 RA – F – Q2=0
Q2 RA F F F b F l b F a l l l
M2=0 M2 – RAx2 + F (x2 – a) =0
M 2 F l a x2 Fx2 a Fa l x2
l
l
剪力符号:+Q (左上右下) +Q -Q (左下右上) -Q
Q= qx (0<x<l)
M qx x qx2
2
2
(0 x l)
x Q
l
M
Q
M
ql
q l2
2
悬臂梁旳最大弯矩位于固定端,所以固定
端A是危险截面。悬臂梁旳最大弯矩是简支
梁旳4倍。
例3-3 卧式容器可简 化为均匀载荷q作 用旳外伸梁。已知 此卧式容器旳总长 度为L,求支座应 放在什么位置,使 得容器受力情况最 佳。
弯曲与弯曲模具设计

二、弯曲件的工艺计算
2.弯曲力的计算
(1)自由弯曲力对于V形件,有
F自
0.6kbt 2 b
rt
对于U形件,有
F自
0.7kbt 2 b
rt
(2)校正弯曲力如果弯曲件在冲压行程结束时受到模具的校正
(见图3-27)
上一页 下一页
第四节 弯曲件的工艺特性及工艺计 算
二、弯曲件的工艺计算
(3)顶件力或压料力
上一页 下一页
第四节 弯曲件的工艺特性及工艺计 算
一、弯曲件的工艺性
(6)增添连接带和定位工艺孔 如图3-22所示。 (7尺寸标注 尺寸标注对弯曲件的工艺性有很大的影响。 如图3-23所示。
上一页 下一页
第四节 弯曲件的工艺特性及工艺计 算
二、弯曲件的工艺计算
1.弯曲件展开长度的确定
第三章 弯曲与弯曲模具设计
第一节 弯曲技术概述 第二节 弯曲变形过程分析 第三节 弯曲件坯料尺寸的计算 第四节 弯曲件的工艺特性及工艺计算 第五节 弯曲件的工序安排 第六节 弯曲模典型结构及结构设计
第一节 弯曲技术概述
弯曲是利用压力使金属板料、管料、棒料或型材在模具中弯 成一定曲率、一定角度和形状的变形工序。弯曲工艺在冲压 生产中占有很大的比例,应用相当广泛,如汽车纵梁、电器 仪表壳体、支架、铰链等,都是用弯曲方法成型的。
所示为V形件弯曲的变形过程。 2.弯曲变形特点 为了分析板料弯曲变形的规律,将试验用的长方形板料的 侧面画成正方形网格,如图3-4(a)所示,然后弯曲,观察其
变形特点,弯曲后情况如图3-4(b)所示。
下一页
第二节 弯曲变形过程分析
一、弯曲的变形特点
(1)变形区主要在弯曲件的圆角部分,圆角区内的正方形网 格变成厂扇形。
第三章 弯曲
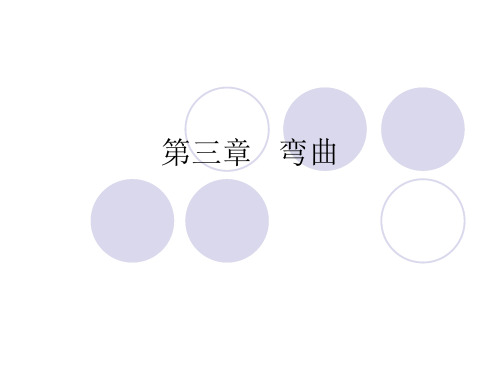
第三章弯曲3.1 弯曲模基础教学要点【目的要求】1、弯曲的类型2、弯曲变形过程分析3、弯曲件回弹4、弯曲件的工艺性5、提高弯曲件质量的措施6、保证弯曲件质量的基本原则教学要点【重点】1、弯曲件回弹、回弹角、影响回弹的因素2、弯曲件的工艺性、最小相对弯曲半径3、影响最小相对弯曲半径的因素4、提高弯曲件质量的措施【难点】1、提高弯曲件质量的措施●弯曲--把金属板材、管材和型材弯曲成一定曲率、形状和尺寸的工件的冲压成形工艺。
弯曲成形广泛应用于制造高压容器、锅炉汽包、锅炉炉管、船体的钢板及骨肋、各种器皿、仪器仪表构件以及箱柜镶条等。
●属塑性成形工序。
弯曲模:V形弯曲模、Z形弯曲模、凹模转动弯曲模、冲孔切断弯曲级进模●问题:弯曲模与冲裁模在工作零件的结构上有何区别?●弯曲分为自由弯曲和校正弯曲。
自由弯曲:当弯曲终了时,凸模、毛坯和凹模三者紧贴后凸模不再下压。
校正弯曲:当弯曲终了时,凸模、毛坯和凹模三者紧贴后,凸模继续下压,从而使工件产生进一步塑性变形,减少了回弹,对弯曲件起到了校正作用。
方法:压弯、折弯、拉弯,辊弯、辊压成形等●压弯是最常用的弯曲方法。
所用设备大多为通用的机械压力机或液压机,也有用专用折弯压力机的。
●常用的滚弯设备是卷板机。
●对于精度要求较高,长度和曲率半径要求较大、横向尺寸要求较小的弯曲件,可在专用的拉弯机上进行拉弯。
拉弯时,板材全部厚度上都受拉应力的作用,因而只产生伸长变形,卸载后弹复引起的变形小,容易保证精度。
V形弯曲模具结构图●弯管枪的现身在第二次世界大战结束前,美、英、苏盟军部队在攻克柏林的巷战中,发现德国士兵使用了一种神奇武器--弯管枪,其结构和功能十分奇特。
使用这种弯管枪,整个人可以隐蔽在墙后,枪管则沿墙角弯曲前伸,这样,可在自己完全隐蔽的情况下准确杀伤对手。
盟军作战部队立即将这一重大发现报告给盟军情报部,情报部迅速组织多学科专家进行试验,准备生产制造这种弯管枪。
●弯管步枪弯管步枪的研制和发展始于第二次世界大战初期。
第三章 弯曲工艺及弯曲模具设计 复习题答案
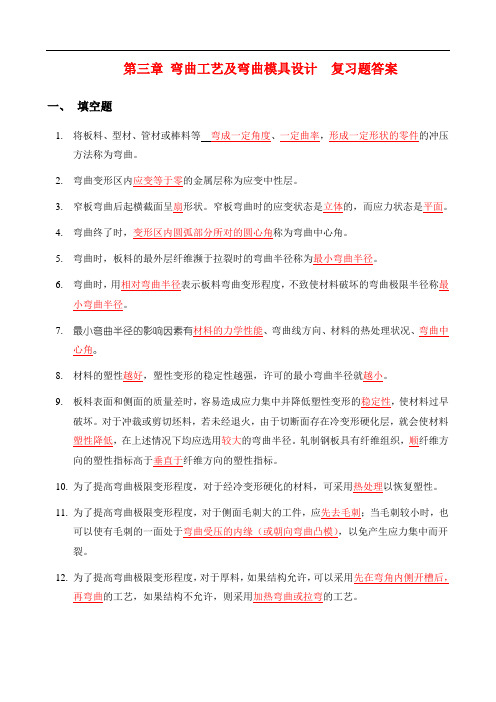
第三章弯曲工艺及弯曲模具设计复习题答案一、填空题1.将板料、型材、管材或棒料等弯成一定角度、一定曲率,形成一定形状的零件的冲压方法称为弯曲。
2.弯曲变形区内应变等于零的金属层称为应变中性层。
3.窄板弯曲后起横截面呈扇形状。
窄板弯曲时的应变状态是立体的,而应力状态是平面。
4.弯曲终了时,变形区内圆弧部分所对的圆心角称为弯曲中心角。
5.弯曲时,板料的最外层纤维濒于拉裂时的弯曲半径称为最小弯曲半径。
6.弯曲时,用相对弯曲半径表示板料弯曲变形程度,不致使材料破坏的弯曲极限半径称最小弯曲半径。
7.最小弯曲半径的影响因素有材料的力学性能、弯曲线方向、材料的热处理状况、弯曲中心角。
8.材料的塑性越好,塑性变形的稳定性越强,许可的最小弯曲半径就越小。
9.板料表面和侧面的质量差时,容易造成应力集中并降低塑性变形的稳定性,使材料过早破坏。
对于冲裁或剪切坯料,若未经退火,由于切断面存在冷变形硬化层,就会使材料塑性降低,在上述情况下均应选用较大的弯曲半径。
轧制钢板具有纤维组织,顺纤维方向的塑性指标高于垂直于纤维方向的塑性指标。
10.为了提高弯曲极限变形程度,对于经冷变形硬化的材料,可采用热处理以恢复塑性。
11.为了提高弯曲极限变形程度,对于侧面毛刺大的工件,应先去毛刺;当毛刺较小时,也可以使有毛刺的一面处于弯曲受压的内缘(或朝向弯曲凸模),以免产生应力集中而开裂。
12.为了提高弯曲极限变形程度,对于厚料,如果结构允许,可以采用先在弯角内侧开槽后,再弯曲的工艺,如果结构不允许,则采用加热弯曲或拉弯的工艺。
13.在弯曲变形区内,内层纤维切向受压而缩短应变,外层纤维切向受受拉而伸长应变,而中性层则保持不变。
14.板料塑性弯曲的变形特点是:(1)中性层内移。
(2)变形区板料的厚度变薄。
(3)变形区板料长度增加。
(4)对于细长的板料,纵向产生翘曲,对于窄板,剖面产生畸变。
15.弯曲时,当外载荷去除后,塑性变形保留下来,而弹性变形会完全消失,使弯曲件的形状和尺寸发生变化而与模具尺才不一致,这种现象叫回弹。
第三章 弯曲

坯料弯曲变形区内切向应为的分布
a)弹性弯曲b)弹 塑性弯曲c)纯塑性弯曲 a)弹性弯曲b)弹-塑性弯曲c)纯塑性弯曲 弹性弯曲b) c)
8
2 弯曲变形的特点
弯曲前
弯 曲 前 坐 标 网 格 的 变 化
9
弯曲后
二、弯曲变形的特点
板料弯曲前后的网格变化 1、弯曲变形主要发生在弯曲带中 、 心角φ范围内 心角 范围内 2、变形区内,板料在长、宽、厚 、变形区内,板料在长、 三个方向都产生了变形。 三个方向都产生了变形。 长度方向: 中性层以内逐渐缩短,中性层以外逐渐伸长。 长度方向: 中性层以内逐渐缩短,中性层以外逐渐伸长。
22
4.直边高度与孔边距 (1)直边高度 弯曲件的直边高度不宜过小,其值应为h>2t 弯曲件的直边高度不宜过小,其值应为h>2t (2)孔边距
2mm时 当t < 2mm时,
l ≥t
2mm时 孔的位置处于变形区外。 孔的位置处于变形区外。 当t ≥ 2mm时, l ≥ 2t
23
5.形状与尺寸的对称性 弯曲件形状与尺寸应对称分布。 弯曲件形状与尺寸应对称分布。 防止弯曲时因圆角不同,摩擦阻力不同, 防止弯曲时因圆角不同,摩擦阻力不同,造成工件尺 寸精度不高,甚至弯曲失败。 寸精度不高,甚至弯曲失败。 工艺孔、 6.工艺孔、槽及缺口 为防止交接处因受力不均或应力集中而造成开裂、圆 为防止交接处因受力不均或应力集中而造成开裂、 角部位畸变等缺陷, 角部位畸变等缺陷,应预先在弯曲件上设置工艺上必 须的工艺孔、槽和缺口。 须的工艺孔、槽和缺口。
3.弯曲半径
在保证坯料外表面纤维布发生破坏的前提下, 在保证坯料外表面纤维布发生破坏的前提下,弯曲件能够弯曲的内 表面最小圆角尺寸,成为最小弯曲半径, 表面最小圆角尺寸,成为最小弯曲半径,相应的与板料厚度的比值 成为最小相对弯曲半径。最小相对弯曲半径影响因素: 成为最小相对弯曲半径。最小相对弯曲半径影响因素: 材料的力学性能。 (1) 材料的力学性能。 材料塑性越好,塑性指标数值越高,相应的相对弯曲半径越小。 材料塑性越好,塑性指标数值越高,相应的相对弯曲半径越小。 (2) 弯曲中心角 弯曲只发生在圆角部分,直边不参与变形, 弯曲只发生在圆角部分,直边不参与变形,并非如此 圆角的直边参与变形,使最小相对弯曲半径减小。 圆角的直边参与变形,使最小相对弯曲半径减小。
第三章 曲线的凹凸与拐点
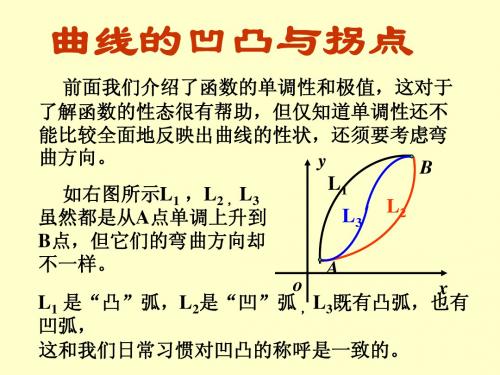
则 f ′′( x ) = [ f ′( x )]′在x0两边变号 ,
∴ f ′( x )在x0取Hale Waihona Puke 极值 ,由可导函数取得极值的 条件,
∴ f ′′( x ) = 0.
方法1: 方法1: 设函数 f ( x )在x0的邻域内二阶可导 , 且f ′′( x0 ) = 0,
(1) x0两近旁 f ′′( x )变号,点( x0 , f ( x0 ))即为拐点; ( 2) x0两近旁 f ′′( x )不变号,点( x0 , f ( x0 ))不是拐点.
例2 求 线 y = 3x4 − 4x3 +1的 点 曲 拐 及
、 的 间 凹 凸 区 .
解
2 y′′ = 36 x ( x − ). y′ = 12 x − 12 x , 3 2 令y′′ = 0, 得 x1 = 0, x2 = . 3
3 2
∵ D : ( −∞ ,+∞ )
x
f ′′( x )
(−∞ ,0) −∞
⇒ f ( xi ) ≥ f ( x0 ) + f ′( x0 )( xi − x0 ) ( i = 1,2,⋯, n)
各式乘以 pi 再相加, 再相加,得
n n n i =1 i =1 i =1
∑ pi f ( xi ) ≥ i =1
⇒
n
f ( x0 )∑ pi + f ′( x0 )[∑ pi xi − x0 ∑ pi ]
1 4 解 当x ≠ 0时, y′ = x , y′′ = − x , 时 3 9 x = 0是不可导点, y′, y′′均不存在 .
但在( −∞ ,0)内, y′′ > 0, 曲线在( −∞ ,0]上是凹的; 在(0,+∞ )内, y′′ < 0, 曲线在[0,+∞ )上是凸的. ∴ 点(0,0)是曲线 y = 3 x的拐点.
第三章曲面的第二基本形式
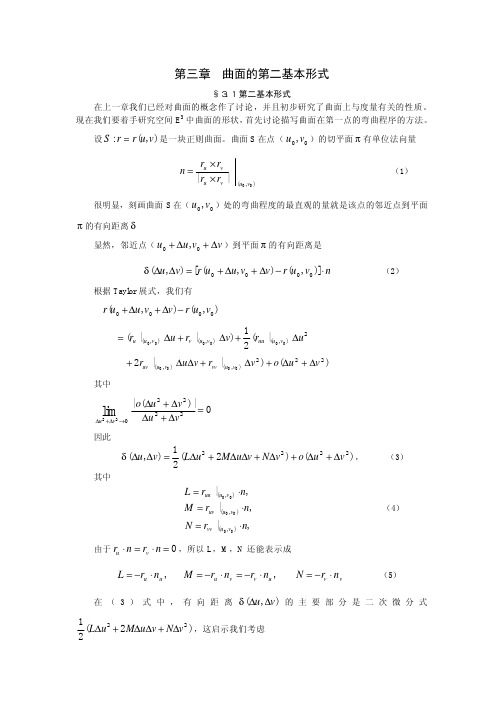
v = v( s) 是 S 上过 P 点,且在 P 点以 du : dv 为切方向的一条曲线,仍记曲面在 P 点的单位
法 向 量 为 n , α 、 β 分 别 表 示 曲 线 在 P 点 处 的 单 位 切 向 量 和 单 位 主 法 向 量, 且 记
θ = ∠( β , n) 。我们考察 C 的曲率向量 kβ 在 n 上的投影
n = ( 0,0,1)
所以
? = dr ⋅ dr = du 2 + dv 2 , ? = −dr ⋅ dn = 0
设圆柱面 S2 的方程是
(15)
u u r = (a cos , a sin , v) a a
故
u u ru = − sin , cos , 0 a a rv = (0,0,1) u u ru × rv = cos , sin , 0 = n a a u 1 u 1 ruu = − cos , − sin ,0 a a a a ruv = rvv = 0
一方面,
kβ ⋅ n = k cosθ
另一方面
kβ ⋅ n = n ⋅
结合两方面,我们看到
d 2r ? = , ds 2 ?
(1)
k cosθ = ? /?
[注 1]( 1)式右端只是点和方向的函数,给定点处,其值仅由方向 du : dv 决定,因此, 对于过点 P 且具有相同切线的诸多曲线而言, 尽管它们在 P 点的曲率 k 不同; 对应的 θ 也不 相同,但乘积 k cosθ 却是个固定值。 [注 2] ( 1 )式左端含有反映曲线弯曲程序的曲率项,而右端有反映曲面弯曲程度的第 二基本型,因此, ( 1)式把曲线与曲面的弯曲性联系起来,为我们利用曲线来研究曲面的弯 曲程序提供了方便 定义 1 称 k cosθ 为曲线 C 在 P 点处的法曲率,记为
第三章 褶 皱 构 造2

剪切褶皱作用的特点
(1)横剖面上平行轴面方向所量得的褶皱不同部位的层的 “厚度”基本相等。 (2)剪切褶皱作用形成的“褶皱”并非岩层面真正发生了弯 曲变形,而是层面沿密集的平行剪切面发生差异性滑动而呈 现出“弯曲”外貌。
(四)柔流褶皱作用
定义:高韧性和低粘度的岩石受到力的作用,发生类似 粘性流体的粘滞性流动变形,从而形成复杂多变的褶皱。 柔流褶皱作用是一种固态流变条件下的褶皱作用。如盐 丘构造中底辟核的褶皱就是一种典型的柔流褶皱。
三、褶皱形成时代的确定
褶皱的形成往往是地壳运动的结果,因此 查明褶皱的形成时代是恢复地壳运动历史 的重要方法之一。褶皱形成的时代通常用 以下方法判别。
1.角度不整合分析法
褶皱形成于不整合面下最 新褶皱岩层之后,早于上 覆最老未褶皱岩层之前。 从右图可以看出褶皱最新 岩层为S3,未褶皱最老岩 层为D3,故褶皱形成的年 代为S3以后至D3以前, 即D1-2世。
弯滑褶皱的内部构造
(3)纵弯褶皱作用的一般特点
1) 同一褶皱层各处厚度相同,褶皱形态呈I B型等厚褶皱 。
2)韧性变形
外侧因拉伸变薄, 常产生顺层劈理。
内侧因受挤压增厚, 常产生正扇形劈理。
3)脆性变形
外侧因拉伸常形 成垂直层面的张 裂。 内侧因顺层挤压 常形成平行层面 的张裂 。
外侧常形成正断层 式的共轭剪节理, 进一步发展则形成 地堑 。 内侧常形成逆断层式 的共轭剪节理,进一 步发展则成逆断层。
5、基底构造对盖层褶皱的影响
1) 基底凭依断层可形成雁行褶皱;
2) 基底隆起,可形成大型穹隆;
3) 基底断裂常使盖层形成不对称褶皱; 4) 在两基底断裂之间的断块部位常形成箱状褶皱; 5) 基底波状起伏,则可能在深层的正向地形上面出现向 斜构造,负向地形上出现背斜构造。
第3章 平面弯曲
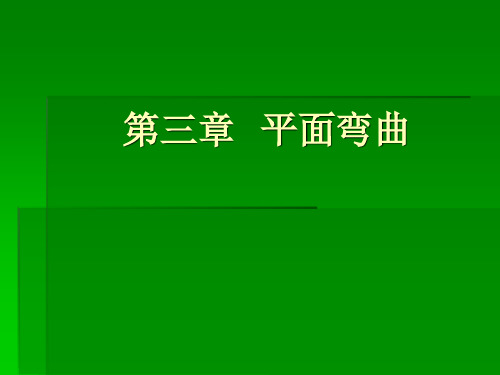
2、弯曲变形;
3、剪切变形; 4、扭转变形; 三、弯曲的概念 1、一直杆在通过杆的轴线的一个纵向平面内,如果受到垂直于轴线的 外力(即横向力) 或力偶作用,杆的轴线就变成一条曲线,这种变形称为 弯曲变形。 2、纵向对称面:由横截面对称轴和梁的轴线组成的平面,称为纵向对 称面。 3、梁在变形时,它的轴线将弯曲成在纵向对称面内的一条曲线,这种 情况称为平面弯曲。
(1) 先求出支座反力
RA = RB =
ql 2
(2) 列出剪力方程和弯矩方程
1 ql - qx (0 < x < l) 2 1 1 M = qlx - qx 2 (0 x l) 2 2 Q=
(3) 作剪力图和弯矩图 1 Qmax = ql 2
由弯矩方程可知弯矩图是一抛物 线,故要定出几点(如5个点) 的M 值,才能近似地作出弯矩图。
二、剪力和弯矩方程 剪力图和弯矩图
AC段梁的弯矩方程为
M1 = Fb x1 l (0 x1 a)
a
1
F
b
2
A
x1
1 x2
C
2
B
CB段梁的弯矩方程为
Fa M2 = (l - x 2 ) l (a x 2 l)
l
M
Fab l
画出弯矩图
M max
Fab = l
x
3.2 直梁弯曲的内力分析
3.3 平面弯曲的应力计算
三个假设: (1 ) 梁在纯弯曲时, 横截面像直线 mn、m1n1 那样, 各自偏转一个角 度, 但仍然保持平面, 且垂直于梁 轴, 这就是平面截面假设。 (2 ) 纵向纤维的变形和它到中性 层的距离有关, 且沿宽度相等。 (3 ) 纵向纤维的变形只是简单的 拉伸或压缩, 它们之间没有相互 挤压, 因此, 梁的横截面上只能产 生拉应力或压应力。由于这些应 力都垂直于横截面, 故统称为正 应力。
- 1、下载文档前请自行甄别文档内容的完整性,平台不提供额外的编辑、内容补充、找答案等附加服务。
- 2、"仅部分预览"的文档,不可在线预览部分如存在完整性等问题,可反馈申请退款(可完整预览的文档不适用该条件!)。
- 3、如文档侵犯您的权益,请联系客服反馈,我们会尽快为您处理(人工客服工作时间:9:00-18:30)。
ρ = r + xt
r:弯曲件内弯曲半径 t:材料厚度 x:中性层位移系数,查表。 弯曲件展开尺寸计算:
r/t < 0.5时,因为圆角区域发生了严重变薄,其相邻的直边也变薄,因 此需要采用经验公式计算。 对于复杂形状的弯曲件,在初步计算后,还需要反复试弯,不断修 正才能确定坯料尺寸。
3 回弹值的确定: 为了得到形状与尺寸精确的弯曲件,需要实现确定回弹值, 因为影响因素很多,理论计算方法往往不精确,而且很复杂,因此 一般是根据经验数值以及简单的计算来初步确定模具工作部分尺寸, 然后在试模时校正。
图3-21
产生偏移的原因: 1 弯曲坯料形状不对称; 2 弯曲件两边折弯个数 不相等; 3 弯曲凸凹模结构不对 称。
图3-22
控制偏移措施: 1 采用压料装置。
图3-23
2 利用工艺孔限制坯料移动。 3 对偏移量进行补偿。
4 对不对称零件,先成对弯曲,再切断。 5 尽量采用对称凸凹模结构
图3-24
0 .7 K B t σ b F自 = r+t
2
U型件:
]型件:
F = 2.4 Btσ b ac 自
上式中: F自:自由弯曲在冲压行程结束时的弯曲力; B:弯曲件的宽度; r:弯曲件的内弯曲半径; t:弯曲件材料厚度; σb:材料抗拉强度; K:安全系数,一般取1.3 a、c:系数; 校正弯曲时的弯曲力: 校正弯曲时的弯曲力一般按照下式计算:
2 应力状态 长度方向:弯曲内区受压,外区受拉,切向应力是绝对值最大的主应 力; 厚度方向:在变形区内存在径向压应力,在板料表面为0,由表及里 逐渐增加,到达中性层时达到最大值; 宽度方向:对于窄板,由于可以自由变形,因此内外区都为0,对于 宽板,内区为压应力,外区为拉应力
3.2 常见的弯曲件质量问题
则可以先弯曲成较大的圆角半径,然后通过整形工序进行整形,必要时 可以增加中减退火工序。若弯曲件的r/t较大,精度要求较高时,凸模圆 角半径可以根据回弹值作相应的修订。 二 弯曲凹模圆角半径及其工作部分的深度
凹模圆角半径不能过小,否则会使坯料滑进时的阻力增大,从而 增加弯曲力,并使坯料表面滑伤,工件结构对称时两边圆角半径应该 一致,以避免偏移。 生产中按照坯料厚度决定r凹:t<=2mm,取(3-6)t,t=(2~3) mm,取(2~3)t,t>4mm,取2t。 对于V型件弯曲,凹模底部可以开槽,或者其圆角半径为: (0.6~0.8)(r凸+t) 凹模深度应该适当,过小会使制件回弹较大,不平直,过大会浪 费模具材料,而且需要较大的压力机行程。弯曲ц形件时,若工件不 高,或者要求两边平直,则凹模高度大于制件高度。 三 凸、凹模间隙和宽度 对于V形件,可以通过调节压力及装模高度来调节间隙,对于U 形件,凸、凹模间隙对于回弹、表面质量和弯曲力都有比较大的影响, 减息越大,回弹力越大,间隙过小,会使制件壁厚变薄,降低凹模寿 命,凸、凹模间隙一般按照经验公式计算: Z = t + ∆ + ct 上式中Z为间隙,t为板料厚度, ∆为板料上偏差,c为间隙系数。
宽度与制件尺寸标注有关,标注外表面宽度时以凹模尺寸为基准, 标注内表面宽度时以凸模为基准。
3.7 辊弯和辊形
辊弯:滚轮旋转时在摩擦力的带动 下,使钢材连续进入辊轮之间而弯 曲成形的一种加工方法,一般用于 有大弯曲半径的零件。
辊弯:三个辊子之间成等腰三角形,下面两个辊子支撑毛坯,上面 的棍子施压使毛坯弯曲,调节中间辊与下面两个辊子中心连线之间 的距离,或者改变下面两个辊子的相对位置,可以得到不同曲率的 辊弯件。中间辊与下面两个辊子中心连线之间距离的计算公式为:
4 变形后板料横截面积变化情况:窄板(B/t < 3)时, 内区 因厚度受压而使宽度增加,外区因受拉而使宽 度减小,原矩形区域变成扇形,宽板情况,因为板料 在宽度方向变形受到材料彼此制约,不能自由变形, 因此横截面几乎不变。
图3-8
3.2 塑性弯曲变形区内的应力和应力状态
因为相对宽度影响变形区内的宽度方向的应变,所以随着B/t的 不同,变形区有不同的应力、应变状态。 1 应变状态: 长度方向:弯曲内区为压缩应变,外区为拉深应变,该方向为 绝对值最大主应变。 厚度方向:根据体积不变定律,因为长度方向上主应变最大, 因此厚度方向和宽度方向上必然产生与长度方向相反的主应变。在 弯曲内区为拉应变,在弯曲外区为压应变。 宽度方向:窄板时,由于材料在宽度方向上可以自由变形,所 以在弯曲内区为拉应变,在弯曲外区为压应变,在宽板弯曲时,由 于材料之间彼此制约作用,不能自由变形,宽度方向上的变形可以 认为是0
s =
( r + t + R 2 ) 2 − a 2 − r − R1
上式中: R1、R2分别为上下辊轮半径; a:下辊轮中心距; r:辊弯件内层回弹前的曲率半径; t:料厚 辊弯时,由于两端材料未能受到三辊的同时辊压,因而留下一段平 直部分,这部分直端长度为材料厚度的10倍至20倍,这些直边在 校圆时也难以完全消除,因此一般应该对板料端头进行预弯,常用 的预弯方法如下:
3.7 设计计算及弯曲模工作部分设计
1 弯曲力计算 弯曲力是设计弯曲模具和选择压力机的重要依据,特别是在弯曲坯 料较厚、弯曲线较长、相对弯曲半径较小、材料强度较大的弯曲件时, 必须计算弯曲力,对弯曲力的计算一般采用经验公式。 自由弯曲时的弯曲力 V型件:
0 .6 K B t 2σ b F自 = r+t
第三章
弯
曲
弯曲:把金属板料、型材或管材等弯成一定的曲率和角度, 弯曲:把金属板料、型材或管材等弯成一定的曲率和角度, 从而得到一定形状和尺寸零件的冲压工序。 从而得到一定形状和尺寸零件的冲压工序。 弯曲方法有压弯、折弯、拉弯、辊形等。 弯曲方法有压弯、折弯、拉弯、辊形等。
图3-1 常见弯曲方法
图3-2 常见弯曲件
小变形量、自由弯曲时的回弹尺寸:
rp =
r 3σ s r 1+ Et r (180 − ϕ ) rp
ϕ p = 180 ° −
上式中: r,φ:弯曲件的圆角半径和角度; rp,φp:凸模的圆角半径和角度; σs:弯曲件材料的屈服点 E:弯曲件材料的弹性模量; t:弯曲件的厚度。
大变形量、自由弯曲时的回弹尺寸: 大变形量时的计算尺寸:r/t ≤ 5~8时,弯曲件圆角半径回弹量很小, 可以不予考虑,只需要考虑角度的回弹值,该值可以通过查表获得, 当弯曲角不为90°时,可以按照下式计算:
图3-2 常见弯曲件
图3-4 常见弯曲件
图3-5 常见弯曲件
3.1 弯曲变形过程分析
术语: 弯曲中心角 弯曲线 弯曲半径 相对弯曲半径
图3-6 弯曲变形过程
图3-7 弯曲变形区
弯曲变形特点: 1 弯曲变形区:弯曲变形区主要集中在圆角部分,此 处正方形网格变成扇形。 2 变形区内,板料外区切向拉长,内区受压缩缩短,中间 有一层长度在变形前后保持不变,称为中性层。 3 相对弯曲半径(弯曲半径与板厚之比)较小时,中性层 位置从板料中心向内移动,使得拉深变形区域增大,内层受 压增厚区域减小,从而使变形区变薄
图3-14 材料力学性能和相对弯曲半径对回弹的影响
2 相对弯曲半径,相对弯曲半径越大,在总的变形量中弹性变形所占 的比例也越大,回弹越大。因此r/t很大的零件不容易弯曲成型。 3 弯曲角度(弯曲中心角):弯曲角度越大,弯曲变形区域越大回弹积 累越大,回弹越大。 4 弯曲方式:无底凹模回弹比有底凹模回弹大。 5 凸凹模间隙:凸凹模间隙大,材料处于松动状态,回弹大,间隙小, 材料处于被挤紧状态,回弹小。 6 弯曲件形状:弯曲件形状复杂,一次弯曲成型的角度较多,则弯曲时 各部分相互牵制作用力大,回弹值小。
图3-16
2 采用合适的弯曲工艺 用校正弯曲代替自由弯曲; 对经冷作硬化的材料进行退火处理,对回弹较大材料可以采用热弯 曲; 采用拉弯工艺方法;
图3-16
2 采用合适的弯曲工艺 用校正弯曲代替自由弯曲; 对经冷作硬化的材料进行退火处理,对回弹较大材料可以采用热弯 曲; 采用拉弯工艺方法;
图3-16
控制弯裂的措施: 1 经冷变形硬化的材料,可以通过热处理方式恢复其塑性。 2 去除坯料剪切面上的毛刺,采用整修、挤光、滚光等方法降低剪 切面的表面粗糙度。 3 弯曲时将切断面上毛面一侧处于弯曲受压的内缘。 4 对于低塑性和厚料,可以采用加热弯曲。 5 采用两次弯曲办法,第一次弯曲采用较大的相对弯曲半径,退火 后再进行第二次弯曲。 6 对于较厚板料的弯曲,可以采用开工艺槽的方法 。
控制回弹的措施: 1 改进弯曲件的设计 尽量避免过大的相对弯曲半径r/t。在弯曲变形区压出加强筋或成 形边翼,以提高刚度,抑制回弹。 采用σs/E小,力学性能稳定和板厚波动小的材料。
图3-15 结构改进
2 采用合适的弯曲工艺 用校正弯曲代替自由弯曲; 对经冷作硬化的材料进行退火处理,对回弹较大材料可以采用热弯 曲; 采用拉弯工艺方法;
∆ ϕ
=
ϕ
9 0
∆ ϕ
0
上式中: φ:弯曲件的弯曲角 ∆φ:弯曲件弯曲角为φ时的回弹角; ∆φ90:弯曲件的弯曲角为90度时的回弹角。
校正弯曲时的回弹值查表根据经验公式计算。
弯曲模工作部分是指凸模圆角半径、凹模圆角半径、凹模深度, 对于U形件弯曲还有凸、凹模之间的间隙,以及模具宽度尺寸等。 一 凸模圆角半径 当弯曲件的r/t较小时,凸模圆角半径r凸 = r > rmin,若 r凸 = r > rmin /t,
1 弯裂 弯曲时板料外侧受到拉伸,当拉伸应力超过抗拉强度时,在板 料外侧将会产生裂纹。产生裂纹的主要原因除了材料因素外,还与弯曲 半径和材料厚度比值有关,r/t越小,越容易产生裂纹。 2 板面和侧面质量,质量差,容易造成应力集中,使材料过早破坏。 3 弯曲方向:沿着纤维组织方向的力学性能较好,因此弯曲线与纤 维方向垂直时,最小弯曲相对半径可以取较小值,相反应该去较 大值。 4 弯曲中心角:弯曲中心角越小,最小弯曲半径越小。