英国深海控制器 DSE8610调试人员专用说明
深海控制器DSE 功能介绍

深海控制器 DSE8610模块功能介绍DSE POWER® 优控系列 DSE8610 自启动负载分配模块一、DSE8610功能介绍 二、DSE8610监控方式一、DSE8610功能介绍1、 多端口可同时使用- RS232、 RS485、USB和网络端口 2、 具有数据采集和分析功能(data logging ) 3、 超强的PLC逻辑功能 4、 DSE8610模块的兼容性 5、 模块与调速器、调压板直接相连 6、 负载分配特性 7、 其他功能1、 多端口可同时使用- RS232、 RS485、网络端口、USB和程序设定端口2、 具有数据采集和分析功能(data logging )3、 超强的PLC逻辑功能举例:①当发动机的水温大于100°C,机组以额定功率的60%输出②当发动机的水温小于95°C,机组以额定功率的90%输出4、 DSE8610模块的兼容性5、 模块与调速器、调压板直接相连5.1 模块与调速器、调压板直接相连5.2 模块与数字调速器、数字调压板直接相连6、 负载分配特性6.1 自动模式下三种启动方式 ① 远程启动信号设置为Remote start on load ,无论哪台机组如果远程信号有效,都会自启动,然后并联。
接线如下图:② 远程启动信号设置为Remote start on load demand,根据负载 的大小,自动调用或停止除主机之外其它机组 。
接线如下图:软件设置如下图:③ 远程启动信号设置为Remote start on load demand,刚开始启动时,启动 所有的机组,然后根据负载的大小,自动调用或停止除主机之外其它机 组 。
接线如下图:软件设置如下图:6.2 削峰调节白天傍晚/黄昏晚上/夜间白天傍晚/黄昏晚上/夜间DSE8610负载分配百分比DSE8610负载分配百分比7、 其他功能7.1 可设4套工作模式和保护参数可预设4种工作模式和保护参数。
深海电子DSE5500系列网络通信模块说明书
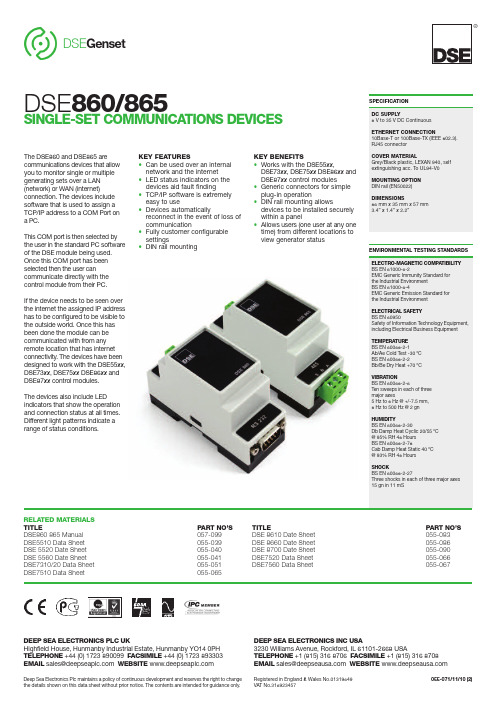
DEEP SEA ELECTRONICS PLC UKHighfield House, Hunmanby Industrial Estate, Hunmanby YO14 0PH TELEPHONE+44 (0) 1723 890099FACSIMILE +44 (0) 1723 893303 EMAIL********************WEBSITE DEEP SEA ELECTRONICS INC USA3230 Williams Avenue, Rockford, IL 61101-2668 USATELEPHONE+1 (815) 316 8706FACSIMILE +1 (815) 316 8708EMAIL********************WEBSITE 055-071/11/10 (2)KEY FEATURES•Can be used over an internal network and the internet •LED status indicators on the devices aid fault finding•TCP/IP software is extremely easy to use•Devices automaticallyreconnect in the event of loss of communication•Fully customer configurable settings•DIN rail mounting KEY BENEFITS•Works with the DSE55xx,DSE73xx, DSE75xx DSE86xx and DSE87xx control modules •Generic connectors for simple plug-in operation•DIN rail mounting allowsdevices to be installed securely within a panel•Allows users (one user at any one time) from different locations to view generator statusThe DSE860 and DSE865 are communications devices that allow you to monitor single or multiple generating sets over a LAN (network) or WAN (internet) connection. The devices include software that is used to assign a TCP/IP address to a COM Port on a PC.This COM port is then selected by the user in the standard PC softwareRELATED MATERIALSTITLE PART NO’S DSE860 865 Manual057-099 DSE5510 Data Sheet055-039 DSE 5520 Date Sheet055-040 DSE 5560 Date Sheet055-041 DSE7310/20 Data Sheet055-051 DSE7510 Data Sheet055-065TITLE PART NO’S DSE 8610 Date Sheet055-083 DSE 8660 Date Sheet055-086 DSE 8700 Date Sheet055-090 DSE7520 Data Sheet055-066 DSE7560 Data Sheet055-067DSE860/865SINGLE-SET COMMUNICA TIONS DEVICESDSE GensetRegistered in England & Wales No.01319649VAT No.316923457Deep Sea Electronics Plc maintains a policy of continuous development and reserves the right to changethe details shown on this data sheet without prior notice. The contents are intended for guidance only.SPECIFICATIONENVIRONMENTAL TESTING STANDARDS。
JM861电流探头用户手册说明书

AC Current ProbeModel JM861User ManualDESCRIPTIONThe JM861 (Catalog #2110.90) is designed for use in industrial environments. The “squared” jaws permit multiple conductor or bus bar positioning. The Model JM861 accurately measures AC current waveforms and has proportional mV output for direct readings on oscilloscopes. Three-position slide switch on the handle selects ranges. The Model JM861 offers an insulated 6.5 ft. coaxial cable with insulated BNC connector rated 600Vrms and is compatible with any AC voltmeter, multimeter, or other voltage measuring instrument with an input impedance greater than 1M , 47 pF. To achieve the stated accuracy, use theJM861 with a voltmeter having an accuracy of 0.75% or better.WARNINGThese safety warnings are provided to ensure the safety of personnel and proper operation of the instrument.•Read the instruction manual completely and follow all the safety information before attempting to use or service this instrument.•Use caution on any circuit: Potentially high voltages and currents may be present and may pose a shock hazard.•Read the Safety Specifications section prior to using the current probe. Never exceed the maximum voltage ratings given.• Safety is the responsibility of the operator.•ALWAYS connect the current probe to the display device before clamping the probe onto the sample being tested.•ALWAYS inspect the instrument, probe, probe cable, and output terminals prior to use.Replace any defective parts immediately.•NEVER use the current probe on electrical conductors rated above 600V in overvoltage category III (CAT III). Use extreme caution when clamping around bare conductors or bus bars. INTERNATIONAL ELECTRICAL SYMBOLSThis symbol signifies that the current probe is protected by double or reinforced insulation. Useonly factory specified replacement parts when servicing the instrument.This symbol signifies CAUTION! and requests that the user refer to the user manual beforeusing the instrument.This is a type A current sensor. This symbol signifies that application around and removalfrom HAZARDOUS LIVE conductors is permitted.DEFINITION OF MEASUREMENT CATEGORIESCAT I V: For measurements performed at the primary electrical supply (<1000V) such as on primary overcurrent protection devices, ripple control units, or meters.CAT III: For measurements performed in the building installation at the distribution level such as on hardwired equipment in fixed installation and circuit breakers.CAT I I: For measurements performed on circuits directly connected to the electrical distribution system.Examples are measurements on household appliances or portable tools.RECEIVING YOUR SHIPMENTUpon receiving your shipment, make sure that the contents are consistent with the packing list. Notify your distributor of any missing items. If the equipment appears to be damaged, file a claim immediately with the carrier and notify your distributor at once, giving a detailed description of any damage.ELECTRICAL SPECIFICATIONSCurrent Range:1 to 30A AC continuous cycle; 90A peak to peak1 to 300A AC continuous cycle; 900A peak to peak1 to 2400A AC continuous cycle; 9000A peak to peak 1 to 2400A AC continuous cycle for thefull temperature range(3000A if temperature is < 35°C or 95°F)Output Signal:10 mV AC/A AC (0.3V at 30A)1 mV AC/A AC (0.3V at 300A)0.1 mV AC/A AC (0.3V at 3000A) Accuracy and Phase Shift*:30A RANGEPrimary current 1.5A 6A 30A Accuracy % 2% ± 1 mV Phase shift 20° 10° 5°300A RANGEPrimary current 15A 60A 300A Accuracy % 2% ± 0.5 mV Phase shift 3° 1.5° 1°3000A RANGEPrimary current 150A 600A 3000A Accuracy % 2% ± 0.2 mV Phase shift 3° 1.5° 1°(*Reference conditions: 23°C±3°K, 20 to 85% RH, 48 to 65 Hz, external magnetic field < 40 A/m, no DC component, no external current carrying conductor, test sample centered.) Load impedance ≥ 1MΩ, 47 pF.Accuracy: Per IEC 185Ampere Second Product: 90 A.SFrequency Range: 10 to 50 kHz; current derating above 5 kHz for continuous useLoad Impedance: 1 MΩ, 47 pFWorking Voltage: 600V ACCommon Mode Voltage: 600V ACInfluence of Adjacent Conductor:0.005A/A ACInfluence of Conductor in Jaw Opening: 1% ± 0.1A of readingInfluence of Frequency from 10Hz to 10kHz: 1 dB on all rangesInfluence of DC Voltage: 0.05% per A DCMECHANICAL SPECIFICATIONS Operating Temp.: 14° to 122°F (-10° to 50°C) Storage Temp.: -40° to 176°F (-40° to 80°C) Influence of Temperature: < 0.1% per 10°K Jaw Opening: 3.54" (90mm)Maximum Conductor Size:Cable: 2.52" max. (64mm)Bus bar: 1.97 x 5.31" (50 x 135mm)2.52 x3.94" (64 x 100mm)Envelope Protection: IP 20 (IEC 529)Drop Test: 500 mm (IEC 68-2-32) Mechanical Shock: 100 g (IEC 68-2-27) Vibration:10/55/10 Hz, 0.15 mm (IEC 68-2-6) Polycarbonate Material:Handles:10% fiberglass chargedpolycarbonate UL 94 V0Jaws: ABS UL 94 V2Dimensions:4.72 x 12.40 x 1.89" (120 x 315 x 48 mm) Weight: 2.65 lbs. (1200 g)Colors: Dark gray handles with red jaws Output:Insulated 6.5 ft. (2 m) coaxial cable with insulated BNC connector rated 600V rmsSAFETY SPECIFICATIONS Electrical:Double insulation or reinforced insulation between primary or secondary and outer case of handle upon IEC 1010-2-32Common Mode Voltage:600V CAT III, Pollution: 2ORDERING INFORMATIONCurrent Probe JM861 ................... C at #2110.90 Accessories:Banana/BNC Connector XF-SS(4 mm banana plug) ....................... Cat #2111.32OPERATIONPlease make sure that you have already read and fully understand the WARNING section on page 1. Making Measurements with the AC Current Probe Model JM861•Connect the black and red terminals to the Volt AC range of your DMM or voltage measuring instrument. Select the appropriate voltage range. If the current magnitude is unknown, select the highest range (3000A AC / 3V AC) on the switch probe located inside the handle. Clamp the probe around the conductor to be tested. If the reading is less than 300mV or 30mV, select the lower range until you obtain the best resolution. Read the value display on the DMM (in mV) and divide it by the range selected. (If reading = 2.59V on the 10mV AC/A AC range, the current flowing through the probe is 2590mV ÷ 10 = 259A AC).•For best accuracy: carefully center the conductor inside the probe jaw, avoid if possible, the proximity of other conductors which may create noise.Tips for Making Precise Measurements•When using a current probe with a meter, it is important to select the range that provides the best resolution. Failure to do this may result in measurement errors.•Make sure that probe jaw mating surfaces are free of dust and contamination. Contaminants cause air gaps between the jaws, increasing the phase shift between primary and secondary. It is very critical for power measurement.MAINTENANCE:Warning• For maintenance use only original replacement parts.• To avoid electrical shock, do not attempt to perform any servicing unless you are qualified to do so.•To avoid electrical shock and/or damage to the instrument, do not get water or other foreign agents into the probe.Cleaning:To ensure optimum performance, it is important to keep the probe jaw mating surfaces clean at all times. Failure to do so may result in error in readings. To clean the probe jaws, use very fine sand paper (fine 600) to avoid scratching the jaw, then gently clean with a soft oiled cloth.REPAIR AND CALIBRATIONYou must contact our Service Center for a Customer Service Authorization number (CSA#). This will ensure that when your instrument arrives, it will be tracked and processed promptly. Please write the CSA# on the outside of the shipping container.Chauvin Arnoux®, Inc. d.b.a. AEMC® Instruments15 Faraday Drive Dover, NH 03820 USA(800)945-2362(Ext.360)•(603)749-6434(Ext.360)•*************** Array (Or contact your authorized distributor)NOTE: All customers must obtain a CSA# before returning any instrument.TECHNICAL AND SALES ASSISTANCEIf you are experiencing any technical problems, or require any assistance with the proper use or application of this instrument, please contact our technical hotline:(800) 945-2362 (Ext. 351) • (603) 749-6434 (Ext. 351) •********************LIMITED WARRANTYThe current probe is warranted to the owner for a period of 2 year s from the date of original purchase against defects in manufacture. This limited warranty is given by AEMC®Instruments, not by the distributor from whom it was purchased. This warranty is void if the unit has been tampered with, abused or if the defect is related to service not performed by AEMC® Instruments.Full warranty coverage and product registration is available on our website at:/warranty.html.Please print the online Warranty Coverage Information for your records.99-MAN 100060.v7 02/18。
PAM8610中文资料

The PAM8610 is a 10W (per channel) stereo class-D audio amplifier with DC Volume Control which offers low THD+N (0.1%), low EMI, and good PSRR thus high-quality sound reproduction. The 32 steps DC volume control has a +32dB to -75dB range.
26
AVCC High-voltage analog power supply (7V to 15V)
2.5V Reference for analog cells, as well as reference for unused audio input
27
V2P5
when using single-ended inputs.
3
08/2008 Rev 1.2
元器件交易网
PAM8610
10W Stereo Class-D Audio Power Amplifier with DC Volume Control
Pin Descriptions
Pin Number Name
The PAM8610 is available in a 40pin QFN 6mm*6mm package.
n Flat monitor /LCD TVS n Multi-media speaker System n DVD players, game machines n Boom Box n Music instruments
5
发电机并网模块V02DSE8610功能介绍.pdf
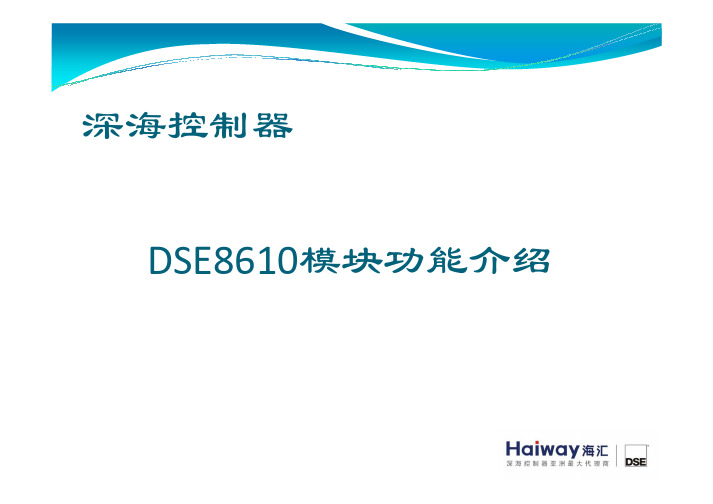
软件设置如下图:
6.2 削峰调节
白天
傍晚/黄昏
晚上/夜间
白天
傍晚/黄昏
晚上/夜间
DSE8610负载分配百分比
DSE8610负载分配百分比
7、 其他功能
7.1 可设4套工作模式和保护参数
可预设4 可预设4种工作模式和保护参数。 种工作模式和保护参数。如机组出租在 50Hz/60Hz工况切换时 50Hz/60Hz工况切换时, 工况切换时,50HZ设定 50HZ设定 1550RPM 超速停机保护, 超速停机保护,如需输出60HZ 如需输出60HZ, 60HZ,无需重新设定转速保护1850RPM 无需重新设定转速保护1850RPM。 1850RPM。可在面 板上直接选择另外一套保护参数。 板上直接选择另外一套保护参数。单相/ 单相/三相的电压超压保护设置, 三相的电压超压保护设置,同理。 同理。
1、 DSE8610模块 DSE8610模块 + PC 机
通过RS232/RS485通讯端口,使用行业标准的Modbus通信协议,可把机组信 息采集到智能楼宇系统中。 注:RS232最远传输为15米; RS485最远传输为1200米
1.1
Modbus 地址表
1.2 远程监控开关状态地址表
2、 DSE8610模块 DSE8610模块 + 触摸屏
深海控制器 DSE8610模块功能介绍
DSE POWER® 优控系列 DSE8610 自启动负载分配模块
一、DSE8610功能介绍 DSE8610功能介绍
1、 多端口可同时使用多端口可同时使用- RS232、 RS232、 RS485、 RS485、USB和网络端口 USB和网络端口 2、 具有数据采集和分析功能( 具有数据采集和分析功能(data logging ) 3、 超强的PLC逻辑功能 4、 DSE8610模块的兼容性 8610模块的兼容性 5、 模块与调速器、 模块与调速器、调压板直接相连 6、 负载分配特性 7、 其他功能
HSS8650 中文操作手册解读

DANI HSS 86.50 顶空进样器中文操作手册DANI HSS 86.50顶空进样器顶空气相色谱法是用来检测低挥发或不挥发溶剂中挥发性物质的方法。
本手册是给DANI HSS 86.50顶空进样器用户提供一个总体上地指导,它包括了安装和使用这台仪器的方针和标准,也包括了HSS 86.50维护和更换部件的信息。
安全信息DANI HSS 86.50是一台IEC(国际电工委员会)安全一级的仪器。
仪器是按照公认的安全标准进行设计并经过测试。
在进行仪器维修之前,必须断开其交流电源。
万一在加热炉里面或者上面碎了一个样品瓶,则仪器在下次使用前必须进行干燥。
安全标志本手册有一些安全标志提醒使用者注意安全操作:WARNING“警告”信息是提醒注意当前的条件或可能出现的情形会伤害用户。
CAUTION“小心”信息是提醒注意当前的条件或可能出现的情形会损坏或毁坏此产品或用户的工作结果。
1.描述DANI HSS 86.50顶空进样器主机(Fig.1)包括:1.1 进样系统1.2 操作程序1.3 气路系统1.1 进样系统进样系统包含三个主要部件(Fig.2/3):1.1.1 样品瓶盘1.1.2 加热炉1.1.3 顶空气体传输部件1.1.1样品瓶盘样品瓶盘有44个位置,位于主机的左边(1-Fig.2)。
通过一个直流马达控制一根分布有单独样品瓶位置的软带,可以向前或向后转动,从而能够带动样品瓶。
1.1.2加热炉加热炉(2-Fig.2)包括一个六位样品瓶转盘,其最大操作温度为200℃,精度1℃。
样品瓶转移系统包含一个装配在横梁(4-Fig.2)上的可移动式抓手(3-Fig.2)。
这个转移系统从样品瓶盘中抓取设定的样品瓶,通过加热炉上的一个进/出口孔(5-Fig.2)把它放进加热炉中。
在加热炉进/出口孔上部有个小盖子(6-Fig.2),打开它就可使用加热炉,这在4.1.6章节会有说明。
在加热时间内,样品瓶可以摇晃。
拿到左侧的面板(7-Fig.2)就能看到仪器内部的电路板。
V03 英国深海控制器 DSE7220模块软件界面中文介绍2011年6月28日

DSE7220 市电失效自启动控制模块
Remote start off load :远程启动,不带负载。正常情况下市电给负载供电,在自 动模式下,如果这个信号有效,仅让发电机组启动,发电 机组却不能带载。 Remote start on load :远程启动,带负载。正常情况下市电给负载供电,在自动 模式下,如果这个信号有效,不仅让发电机组启动, 而且 让发电机组带载(负载强制从市电侧切换到发电机组侧)。 Mains Fail : 市电失效延时。当模块发现市电失效后,延时一段时间启动发电 机组。 Telemetry Start: 远程启动信号保持时间。模块接收到远程启动信号一段时间后, 启动发电机组。
Mains Transient Delay :用于检测市电失效的延时,防止市电瞬间异常,其实市电 还是存在的。
Transfer Time/ Load Delay :市电负载开关断开和发动机组负载开关闭合之间的时 间;市电卸掉urn Delay :在自动模式下,万一启动信号发生什么故障,这个时间可以让发电机 组继续带载一段时间,等信号正常后继续带载。 ETS Solenoid Hold :用于控制器发出停止命令后,可让停车电磁阀带电一段时间 后,让机组完全停止下来。 Fail to Stop Delay :当控制器发出停止命令后,机组还继续运行,当这个时间延时 过后,一个停机失败报警将会产生。 Generator Transient Delay: 防止瞬间负载过大而引起的伪停机报警。
AuteX8610 说明书
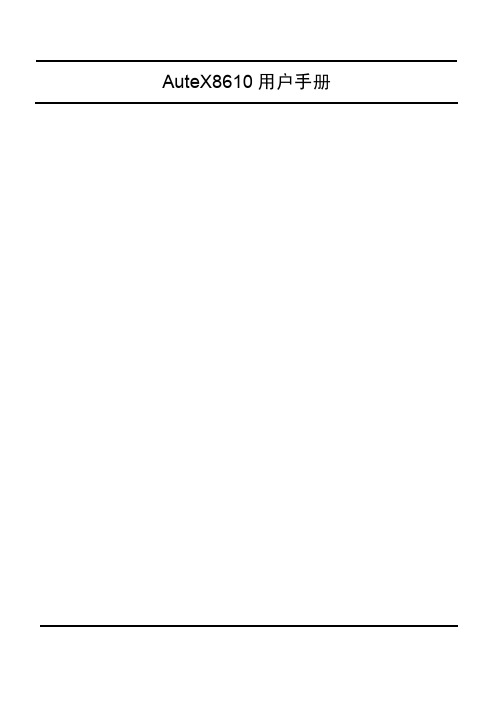
手册约定
手册中有关图标的约定如下:
图标
警告
说明
这个图标主要是提醒用户,如果采用不正确的方式操作设备,可能会对人体或设备造成伤 害,或造成业务中断、数据丢失等。如安装过程、配置业务中等。
这个图标表示提醒用户注意事项。
注意
这个图标主要给出一些与正文相关的信息,同时给用户一些指引,协助用户更好的理解正
2 产品硬件结构 ...................................................................................................................................................................... 1 2.1 机箱结构 .................................................................................................................................................................. 1 2.1.1 前面板........................................................................................................................................................... 1 2.1.2 指示灯说明.................................................................................................................................................... 3 2.2 插槽结构 .................................................................................................................................................................. 3 2.2.1 AuteX8610 插槽描述..................................................................................................................................... 3 2.3 机架式模块............................................................................................................................................................... 4 2.3.1 AuteX8610 主控交换模块 ............................................................................................................................. 4 2.3.1.1 AX81-SMU模块概述 .......................................................................................................................... 4 2.3.1.2 AX81-SMU模块接口属性 ................................................................................................................... 4 2.3.1.3 AX81-SMU模块LED指示灯说明 ........................................................................................................ 4 2.3.2 12 端口 10/100/1000BASE-T和 12 端口 1000BASE-X业务板(AX-AC-12C)............................................. 5 2.3.2.1 AX-AC-12C模块概述 ......................................................................................................................... 5 2.3.2.2 AX-AC-12C模块接口属性 .................................................................................................................. 5 2.3.2.3 AX-AC-12C模块LED指示灯说明........................................................................................................ 6 2.3.3 8 端口 10/100/1000BASE-T和 8 端口 1000BASE-X业务板(AX-AC-8C)................................................... 6 2.3.3.1 AX-AC-8C模块概述 ........................................................................................................................... 6 2.3.3.2 AX-AC-8C模块的接口属性 ................................................................................................................ 7 2.3.3.3 AX-AC-8C模块LED指示灯说明.......................................................................................................... 7 2.3.4 2 端口 10GBASE-R、12 端口 10/100/1000BASE-T和 12 端口 1000BASE-X业务板(AX81-2X12G12S) ...... 8 2.3.4.1 AX81-2X12G12S模块概述 ................................................................................................................ 8 2.3.4.2 AX81-2X2G12S模块的接口属性........................................................................................................ 8 2.3.4.3 AX81-2X12G12S模块LED指示灯说明............................................................................................... 8
TSI Model 8610 EVERWATCH MODBUS 通信应用说明书

_____________________________________TSI, TSI logo, and E VER W ATCH are registered trademarks of TSI Incorporated. Modbus is a trademark of Modicon Incorporated.TSI ® MODEL 8610 EVERWATCH ®MODBUS™ COMMUNICATIONSAPPLICATION NOTE LC-115Modbus ™ communications are installed in all Model 8610 fume hood face velocity monitors. Thisdocument provides the technical information needed to communicate between the host DDC system and the Model 8610 units. This document assumes the programmer is familiar with Modbus ™ protocol. Further technical assistance is available from TSI if your question is related to TSI interfacing to a DDC system. If you need further information regarding Modbus ™ programming in general, please contact:Modicon Incorporated One High Street North Andover, MA 01845 Phone (508) 794-0800The Modbus ™ protocol utilizes the RTU format for data transfer and Error Checking. Check the Modicon Modbus ™Protocol Reference Guide (PI-Mbus-300) for more information on CRC generation and message structures.The messages are sent at 9600 baud with 1 start bit, 8 data bits, and 2 stop bits. Do not use the parity bit. The system is set up as a master slave network. The TSI units act as slaves and respond to messages when there correct address is polled.Blocks of data can be read from each device. Using a block format will speed up the time for the data transfer. The size of the blocks is limited to 15 bytes. This means the maximum message length that can be transferred is 15 bytes. The typical response time of the device is around 0.05 seconds with a maximum of 0.1 seconds.Unique to TSIThe list of variable addresses shown below skips some numbers in the sequence due to internalModel 8610 functions. This information is not useful to the DDC system and is therefore deleted. Skipping numbers in the sequence will not cause any communication problems.RAM VariablesRAM variables can be read using the Modbus™ command 04 Read Input Registers. They can be written to using the Modbus™ command 06 Preset Single Register. The RAM variables can be read in blocks but must be written one variable at a time.8610 Fume Hood MonitorVariable Name VariableAddressInformation Provided to MasterSystem Integer DDC system receivesModel Number 0 Model Number 8610Face Velocity 1 Fume Hood Face Velocity Displayed in ft/min.Status Index 2 Status of EVERWATCH device 0 Normal 1 Low Alarm2 High Alarm3 Sensor Error5 Data ErrorLow Alarm 3 Low Alarm Setpoint Displayed in ft/min.High Alarm 4 High Alarm Setpoint Displayed in ft/min.Filter Index 5 Index for display averaging time 0 1 Second 1 2 Seconds2 3 Seconds 3 5 Seconds4 10 Seconds5 20 Seconds Alarm Mode6 Alarm Reset Mode 0 Unlatched 1 LatchedAudible Disable 7 Permanent Mute Capability 0 Off 1 OnOutput Mode 8 Analog Output Mode 0 Current 1 VoltageNetwork Protocol 9 Communications Protocol 0 Modbus 1 Cimetrics Network 10 Address of unit forcommunications.0-247Calibration CodeEnable17 Calibration pass code enable. 0 Off 1 OnConfiguration CodeEnable18 Configuration pass code enable 0 Off 1 On*Remote Low Alarm 21 Second low alarm setpoint forremote mode.Displayed in ft/min.*Remote High Alarm 22 Second high alarm setpoint forremote mode.Displayed in ft/min.*Setback Mode 23 Control mode of device. Write only variable, reading will alwaysgive a value of 2. Initiates modechange.1 put unit in setback or remote mode.0 put unit in normal mode.*Note: These items only available on 8610-AS version.EXAMPLE of 04 Read Input Registers function format.This example read variable addresses 1 and 2 (Face Velocity and Status Index).QUERY RESPONSEFieldName(Hex)FieldName(Hex)Slave Address 01 Slave Address 01Function 04Function 04Starting Address Hi 00 Byte Count 04Starting Address Lo 01 Data Hi Addr 0 00No. Of Points Hi 00 Data Lo Addr 0 64 (100 ft/min)No. Of Points Lo 02 Data Hi Addr 1 00Error Check (CRC) -- Data Lo Addr 1 00 (Normal- No Alarm)ErrorCheck(CRC)--–2–TSI Incorporated – Visit our website for more information.USA Tel: +1 800 874 2811 UK Tel: +44 149 4 459200 France Tel: +33 4 91 11 87 64 Germany Tel: +49 241 523030 India Tel: +91 80 67877200 China Tel: +86 10 8251 6588 Singapore Tel: +65 6595 6388LC-115 Rev. C©2013 TSI IncorporatedPrinted in U.S.A.EXAMPLE of 06 Preset Single Register function format. This example changes the low alarm setpoint to 60 ft/min.QUERY RESPONSE Field Name (Hex) Field Name (Hex) Slave Address 01 Slave Address 01 Function 06 Function 06 Address Hi 00 Address Hi 00 Address Lo 03 Address Lo 03 Data Hi 00 Data Hi 00 Data Lo 3C Data Lo 3C Error Check (CRC) -- Error Check (CRC) --。
V03 英国深海控制器 DSE6020模块操作说明书 2012年8月10日 .pdf
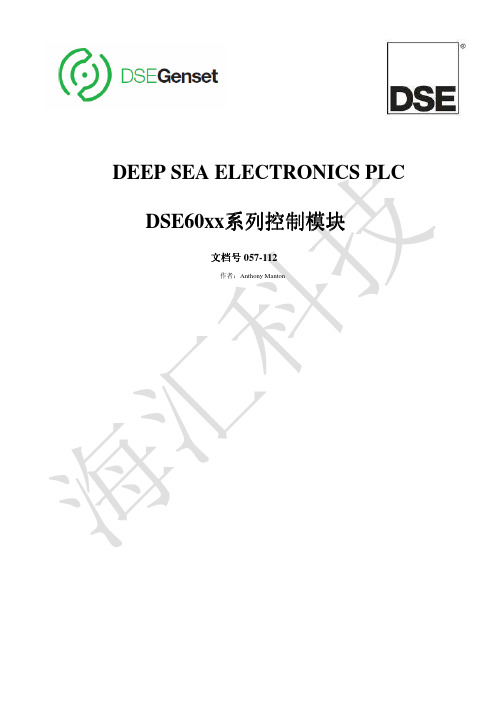
3.7 仪表累计........................................................ ...............................................9
DSE Model 60xx系列控制和仪表系统操作手册
目录
章节
页码
1 参考书目.................................................................................... .5
1.1 安装说明.......................................................................................................5 1.2 使用手册.......................................................................................................5
3.3 发电机电压/频率检测................................. ..... ..... ...................................7
3.4 输入 ...............................................................................................................8 3.4.1 数字输入.................................................................Байду номын сангаас..............................8 3.4.2 模拟输入................................................................................................8 3.4.3 充电失效警告输入 ..............................................................................9 3.4.4 转速传感器(MPU)........................................................................9
DSE520K,英国深海控制器英文说明书

D E E P S E A E L E C T R O N I C S P L C520 A u t o m at i cS t a r tD E S C R I P T I O NIssue 4 VH 23/10/01The Model 520 is an Automatic Engine Control Module designed to automatically start and stop the engine. It will indicate the operational status and fault conditions, automatically shut down the engine and indicate the engine failure by a flashing LED on the front panel. Other simultaneous faults are indicated by steady LED.Selected operational sequences, timers and alarms can be altered by the customer by using either the 807 hand held calibration unit or a PC and the 808 interface. This also provides the operator with ‘real-time’ diagnostic facilities to monitor the operation of the system either locally or remotely. Remote PC-controlled engine starting and stopping is also featured.Operation of the module is via a three position rotary switch (key-switch option available) mounted on the front panel with STOP, AUTO and MANUAL positions.Microprocessor control allows for enhanced operation. The module features a comprehensive list of timers and pre-configured sequences. This allows complex specifications to be achievedConfigurable expansion facilities are provided.Relay outputs are provided for:Fuel Solenoid OutputStart Output3 configurable outputs.Normally the relays are configured as pre-heat, load transfer and alarm outputs. However the relay function is configurable to activate on a range of 32 different functions, conditions or alarms. The relays supply positive plant supply out. Configurable inputs are available for:Low Oil PressureHigh Engine TemperatureRemote Start.This allows the module to function withnormally open or normally closed switches.Four fully configurable auxiliary inputs areprovided to give protection expansion.These can be selected to be indication,warning or shutdown inputs eitherimmediate or held off during start up.Uncommitted LED’s allow additionalannunciation.Multiple alarm channels are provided tomonitor the followingUnder/OverspeedCharge FailEmergency StopLow oil pressureHigh engine temperatureFail to StartFail to stopLoss of speed sensingProgrammable inputs as selectedFirst up alarm is indicated by a flashingLED. Subsequent simultaneous alarmsare displayed by a steady LED.DC Supply:8 to 35 V Continuous.Cranking Dropouts:Able to survive 0 V for 50 mS,providing supply was at least 10 Vbefore dropout and supply recoversto 5V.This is achieved without theneed for internal batteries.Max. Operating Current:290 mA at 12 V. 210 mA at 24 V.Max. Standby Current:50 mA at 12 V. 30 mA at 24 V.Alternator Input Range:15 - 300 V ac RMSAlternator Input Frequency:50 - 60 Hz at rated engine speed.Magnetic Input Range:0.5 V to +/- 70 V (Clamped bytransient suppressors)Magnetic Input Frequency:10Hzto 10,000 HzStart Relay Output:16 Amp DC at supply voltage.Fuel Relay Output:16 Amp DC at supply voltage.Auxiliary Relay Outputs:5 Amp DC at supply voltage.Dimensions:72 X 144 X 118.5mm (Excludingswitch)Charge Fail / Excitation Range:0 V to 35 VOperating Temperature Range:-30 to +70°Cw we ll f ut.co mC A S ED I ME N S I O N ST Y P I C A L C O N N E C T I O N S144.0mm7.5mmFF FNOTE:- When connected toa completed Panel/Gen-set Real time diagnostic status display is availablewww.w el lf u t .c om。
TX Oil Tools 海底工程干预设备说明书
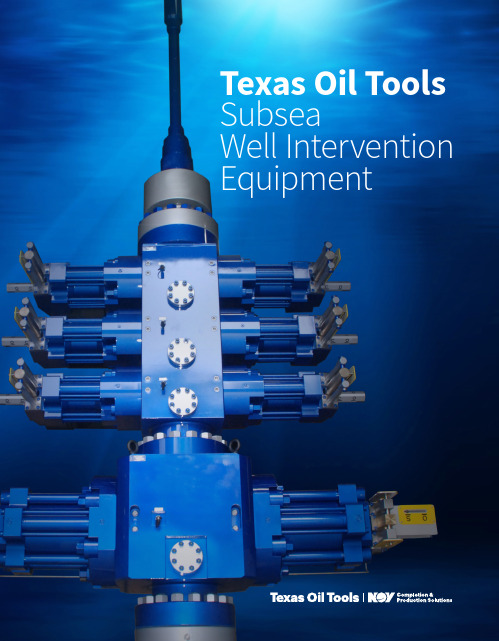
Texas Oil Tools SubseaWell Intervention EquipmentLeading specialty manufacturers and suppliers of pressure control equipmentAt NOV, we’ve come a long way in establishing ourselves as one of the leading specialty manufacturers and suppliers of pressurecontrol equipment. While you respond to your industry challenges, we’re working to develop new and more efficient solutions to your problems. Our subsea products are designed against the most stringent standards, for total control and safety during subsea well interventions in today’s demanding global environment.We understand just how important uptime is to overall success. That’s why we built a state-of-the-art service and repair facility that can get your equipment back into the field as quickly as possible. From simple redress to full recertification, our proven track record of excellence in design, manufacturing and service will help you keep your operations running at maximum efficiency, 24/7.Our subsea products can help you save time and money during subsea well interventions. In this configuration we have both an ET series single safety head and an EIA series triple wireline BOP. The safety head is a blind shear ram that meets the requirements of NORSOK D002 for a safety head. The EIA triple BOP meets the requirements of ISO 13628-7 for a subsea well intervention BOP. The subsea well intervention stack shown is used for riserless well intervention on an offshore well. This system has been used in major subsea markets including the Gulf of Mexico, North Sea, West Africa and Southeast Asia. The main benefit of a system such as this is to provide an economical method for wireline well intervention in subsea wells. The biggest savings is that a smaller vessel can be used to perform this well Intervention.Applications• All riserless coiled tubing and wireline subsea well interventions • Subsea (up to 10,000 feet in depth)• Working pressure up to 15,000 psi • -4°F to 300°F• Explosive decompression resistant seals• Currently developing subsea equipment to meet HPHT requirements Components of the Subsea Stack • Subsea wireline pack-off • Subsea stripper packer• Subsea wireline wiper assembly• Subsea grease head with multiple flow tube assemblies • Subsea head catcher with ball check assembly • Subsea hydraulic quick latch assembly • Subsea tooltrap • Triple wireline BOP •Single safety head BOPRiserless Subsea Well Intervention Subsea Well Intervention BOP (EIA Series)The EIA actuators are well control components used during a subsea wellintervention. There are two sets of rams: blind shear rams and grip seal rams. Blind shear rams are designed to cut the coiled tubing and/or wireline to form a blind seal. Grip seal rams are designed to grab, hold and seal around the coiled tubing. The EIA series BOP is an integral component of the lower wellhead riser package. It features a single line hydraulic system and an automatic, wedge-type, autolock actuator system. The autolock system secures the rams in the closed position in the event of a hydraulic failure or an emergency situation that requires disconnecting from the subsea wellhead.Each EIA series BOP can be built to your specific design requirements, including a dual-bore valve block with a combination of blind shear and grip seal ram assemblies. The combi rams offer increased functionality and the ability to use a wide range of coiled tubing and wireline sizes in a field-proven, compact design. All pressure ratings and service applications are available, including certification for use in the North Sea.Features• SSR or GSR configuration for coil and wire • 3,000 - 5,000 psi hydraulic operating pressure • Single or dual circuit• Hydraulic ram change (quick change rods)• Metal-to-metal bonnet gaskets • Hydraulic wedgelock• Ram and wedgelock position indicators Tested Benefits• Hyperbaric tested to 10,000 ft•Actuators and seals qualified from 32°F to 311°FSpecifications: EIASubsea Quick LatchThe subsea quick latch is a rugged connector designed for multiple subsea latch and unlatch connections. The latch can be stabbed at an angle due to the tapered design that guides the stinger into the connector and into the seal bore during the stab operation. The quick latch is hydraulically operated and uses a set of locking dogs to lock the two pieces of equipment together.The locking dogs work independently and are not affected by the wellbore pressure. A spring mechanism holds the piston and tool in the locked position and is unaffectedby water depth. A visual indicator and lock prevents the tool from accidently opening during unintended loss of hydraulic pressure.Features• Working pressure of 5,000, 10,000 and 15,000 psi• Working temperature of -4°F to 250°F (with optionsfor 300°F)• Elastomer wellbore seals• Bore sizes: 5.12", 7.06" and 7.375"• Hydraulically operated• Visual indicators• Fail-safe closureBenefits• Quick subsea installation• Safe and reliable connection• Allows multiple connections in subsea environment• Provides a connection so that subsea wireline toolscan be run into the wellOptions• Metal-to-metal wellbore seals• Manual locking mechanism• Inconel inlay•Rotational alignmentSubsea Actuators (EI Series)Features• SSR or GSR configuration for coiled tubing orwireline operations• 3,000 or 5,000 psi hydraulic operating pressure• Single circuit design• Metal-to-metal bonnet gaskets• Hydraulic wedgelock• Ram and wedgelock position indicators•SIL 3 certifiedSpecifications: Subsea BOPThe EI series BOPs are well control components used during a subseawell intervention. There are two sets of rams: blind shear rams and gripseal rams. Blind shear rams are designed to cut the coiled tubing and/orwireline to form a blind seal. Grip seal rams are designed to grab, hold andseal around the coiled tubing. The EI series is an integral component of thelower wellhead riser package. The EI features a single line hydraulic systemand an automatic, wedge-type, autolock actuator system. The autolocksystem secures the rams in the closed position in the event of a hydraulicfailure or an emergency situation requires disconnecting from the subseawellhead.Each EI BOP can be built to your specific design requirements, including adual-bore valve block with a combination of blind shear and grip seal ramassemblies. The combi rams offer increased functionality and the abilityto use a wide range of coiled tubing and wireline sizes in a field-proven,compact design.All pressure ratings and service applications are available, includingcertification for use in the North Sea.Safety Head BOP (ET Series)Features• Multi-shear blind ram 10,000 psi or 15,000 psi working pressure • Hydraulic ram change• Metal-to-metal bonnet gaskets • Hydraulic wedgelock• Ram and wedgelock position indicators• Subsea safety head blind shear rams meeting shear requirements of NORSOK D002 for a safety headNORSOK Shear Tests• 0.108" slickline without tension, 1 strand • 0.108" slickline, 10 strands • 0.438" cable without tension• 0.438" 5 core cables without tension, 10 strands • 1.25", 0.109" wall coiled tubing, 10 strands• 3 parallel strings of heavy wall 1.5", 1.75"and 2.0" coiled tubing with 7/16 cable inside• 2.0" sinker bar, ans 4230 steel• 3.5" drill pipe S-135, 226.2 N/m (15.5 lb/ft)• 4" tubing 13 chrome l-80• 4.5" perforating gun• 4.5" 184.0 N/m (12.6 lb/ft) tubing•4 ⅝" gravel pack screen with 2 ⅜" wash pipe insideSpecifications: Safety HeadThe ET series safety head BOP is certified to API/ISO/NORSOK standards and is an integral component of the lower wellhead riser package. It features a single-line hydraulic system and an automatic, wedge-type, autolock actuator system. The autolock system secures the rams in the closed position in the event of a hydraulic failure or an emergency situation that requires disconnecting from the subsea wellhead. Each ET BOP is built to your specific design requirements and can include a single-bore valve block with a blind shear ram assembly. The shear rams offer increased functionality and the ability to use a wide range of coiled tubing and wireline sizes in a field proven, compact design. All pressure ratings and service applications are available, including certification for use in the North Sea.Subsea Triple StripperThe DZA4 subsea modular three window stripper packer is designed to pack-off on coiled tubing as it is stripped in and out of the well at working pressures up to 10,000 psi. This design provides three independent hydraulically actuated packers within the same body, allowing you to utilize one packer while the others are held in reserve. When the first packer is unable to effect a seal, the second packer is actuated. Once the second cannot effect a seal, the third packer is actuated.This effectively triples the time between packer changes and is particularly advantageous when changing packers with tubing in the well. The stripper is designed to create a dynamic seal around the work string while maintaining 10,000 psi full differential wellbore pressure. With the appropriate packing element and bushings, the stripper will be compatible with pipe sizes ranging from 1" to 2 ⅞". With our unique modular design, any additional packers can be easily added into the stack.Features• Triple packer arrangement • Extended life packers• CRA materials for dynamic and static sealing areas • CRA hydraulic ports• Rated for 10,000 ft water depth• Expanded access for packer replacement Qualifications• API PR2 Qualification• API hyperbaric tested to 10,000 ft water depthEngineering Lab Capabilities• 12 ft wide x 35 ft long x 12 ft deep • 45,000 psi hydrostatic high-pressure • 30,000 psi nitrogen gas high-pressure• -30°F to 450°F (media dependant) temperature range • 3,000 psi to 10,000 psi hydraulic control• Digital data acquisition, 30 channels simultaneous, pressure/temperature data recording •20-ton lifting capacityWe have developed a 6,000 square feet state-of-the-art high-pressure, high-temperature test facility. This engineering lab (E-Lab) is capable of providing large-sample testing (20 tons) at high-pressure and temperatures safely within its subsurface vault. Thevault measures 12' wide x 35' long x 12' deep and features electric-operated armor steel covers as a barrier. Along with the armored covers, the vault features remote explosion-proof cameras, which enable real-time monitoring of samples during testing, as well as the capability to be flooded entirely with water. It also includes multiple umbilical feed-thru ports to allow for use with a wide range of control and data cable interfaces.Current subzero testing capability includes the use of a 100-ton chiller unit utilized to flow water-based glycol mixtures/solutions for use in reduced temperature testing down to -30°F in complete submersion of the test sample.Our high-temperature testing capability is a "through sample capable" flow system utilizing a 35Kw heat skid capable of flowing hot oil to maximum 450°F (mediadependent). High-pressure testing capabilities are currently at 45,000 psi hydrostatic testing and 30,000 psi nitrogen gas. Hydraulic control systems up to 10,000 psi can be operated through our standard control panel. We also have a 40-gallon accumulator system rated to 5,000 psi used in timed shearing operations, ram cycle fatigue testing and more.All data is recorded via digital data acquisition systems that are capable of capturing up to 30 channels of equipment performance in both pressure and temperature parameters. Our above ground, free standing, 10 ft x 10 ft test bay is used to conducthydraulic function testing and hydrostatic testing up to 30,000 psi.Aftermarket SolutionsOur state-of-the-art service and repair facilities were created solely to support world-class repair and maintenance services.Service and RepairOur service and repair department provides everything from simple redress to full recertification for our customers. Thisdepartment has provided a direct link to our customers for technical support to the field.With increasingly stringent industry standards on the documentation and recertification of well control equipment, service companies have had to change their approach on product maintenance andrecertification. In response to these changes, we have allocated additional resources to our service and repair department.TrainingAs part of our commitment to provide a safe and reliable workforce, we offer an array of training programs throughout the year covering all types of well intervention and stimulation equipment. Along with these scheduled courses, we partner with our customers to integrate training packages and equipment tailored to fit your needs.Whether you are looking to gain knowledge on your equipment’s functionality orimprove the safety of your operations, our goal is to ensure that you leave the course with the confidence and skills to keep even the most demanding jobsites running at maximum efficiency, 24/7.PartsThe life cycle of your equipment is important to us. To ensure your critical parts are on hand when you need them, our global facilities are continuously replenishing inventory while providing 24/7 technical support. With our deep knowledge of your processes, we will meet your demand like no other supplier.We provide genuine OEM-supplied parts that preserve the integrity of your asset. Made of the same high-quality material as the original equipment, our 100% OEM spare parts are designed to fit your needs with every delivery. We offer a true collaboration that helpsimprove your jobsite's performance, reliability and safety in no time.Corporate Headquarters 7909 Parkwood Circle Drive Houston, Texas 77036 USAIntervention and Stimulation Equipment Headquarters 1020 Everman Parkway Ft. Worth, Texas 76140 USANational Oilwell Varco has produced this brochure for general information onlyand it is not intended for design purposes.Although every effort has been made to maintain the accuracy and reliability of its contents, National Oilwell Varco in no way assumes responsibility for liability for any loss, damage or injury resulting from the use of information and data herein. All applications for the material described are at the user’s risk and are the user’s responsibility.© 2016 National Oilwell Varco All Rights Reserved 10946_ENG_v01Texas Oil Tools Headquarters 3770 Pollok Drive Conroe, Texas 77303 USAUnited States 210 MillstoneBroussard, LA 70518 USACanada4910 - 80 Avenue, SE Calgary, Alberta T2C 2X3 CanadaMiddle EastOilfields Supply Centre B-17 Jebel All Free Zone P.O. Box 18633DubaiUnited Arab Emirates United Kingdom Badentoy Avenue Badentoy ParkAberdeenshire AB12 4YB Scotland, United Kingdom Boudary RoadHarfreys Industrial Estate Great Yarmouth Norfolk NR310LWEngland, United Kingdom。
深海电子A-10081产品说明书

®DEEP SEAELECTRONICSINC 3230Williams Avenue RockfordIL 61101-2668USATELEPHONE+1(815)3168706FACSIMILE+1(815)3168708EMAIL********************WEBSITEDEEP SEA ELECTRONICS PLC Highfield HouseHunmanby Industrial Estate Hunmanby,North Yorkshire YO140PH EnglandTELEPHONE+44(0)1723890099FACSIMILE+44(0)1723893303EMAIL********************WEBSITERegistered in England &Wales No.01319649VAT No.316923457YOUR LOCALDISTRIBUTOR.DEEP SEA ELECTRONICS PLC maintains a policy of continuous development and reserves the right to change the details shown on this data sheet without prior notice.The contents are intended for guidance only .055-057/02/08(2)This data sheet is printed on 9lives 55Silk,which is produced with 55%recycled fibre from both pre and post-consumer sources,together with 45%virgin ECF fibre.TYPEAPPROVED PRODUCT®SPECIFICA TIONDC SUPPL Y8V to 35V continuousCRANKING DROPOUTSAble to survive 0V for 50mS,providing supply was at least 10V before dropout and supply recovers to 5V .This is achieved without the need for internal batteriesMAXIMUM OPERA TING CURRENT 460mA at 12V .245mA at 24V MAXIMUM ST ANDBY CURRENT 375mA at 12V .200mA at 24VAL TERNA TOR INPUT RANGE15V(L-N)to 333V AC (L-N)absolute maximum AL TERNA TOR INPUT FREQUENCY50Hz -60Hz at rated engine speed (Minimum:15V AC L-N)MAGNETIC PICK-UP VOL T AGE RANGE +/-0.5V to 70V PeakMAGNETIC INPUT FREQUENCY 10,000Hz (max)ST ART RELA Y OUTPUT 16A DC at supply voltage FUEL RELA Y OUTPUT 16A DC at supply voltageAUXILIARY RELA Y OUTPUTSThree outputs 5A DC at supply voltage Two outputs volt free 8A at 250V AC DIMENSIONS240mm x 172mm x 57mm 9.4”x 6.8”x 2.2”P ANEL CUTOUT 220mm x 160mm 8.7”x 6.3”CHARGE FAIL/EXCIT A TION RANGE 0V to 35VBUIL T IN GOVERNOR CONTROL Fully IsolatedMinimum Load Impedence:1000ΩGain Volts 0V -10V DC Offset Volts +/-10V DC BUIL T IN AVR CONTROL Fully IsolatedMinimum Load Impedence:1000ΩGain Volts 0V -10V DC Offset Volts +/-10V DC ENCLOSURE PROTECTION (front of module)IP55(with optional gasket)IP42(without gasket)DSE MARINE ®ON-BOARD WITHCONFIDENCE.DSE5510MAUTO &MANUAL ST ART CONTROL MODULE (ELECTRONIC ENGINE ENABLED)The DSE5510M is an Automatic Engine Control Module,designed to provide advanced load share functionality for diesel and gas generating sets that include non-electronic and electronic engines.The module also providesexcellent engine monitoring and protection features.The modules load share functions include,automatic synchronising with built in synchroscope and closing onto dead bus.Direct and flexible outputs from the module are provided to allow connection to the most commonly used speed governors and automatic voltage regulators (AVRs).The module has been designed to combine a maximum of 16generators and 16mains (utility)supplies up to a maximum of 20in one system,e.g.16generators and 4mains (utility)supplies (DSE5560required to synchronise with the mains).The module has the ability to monitor under/over generator volts,over current,under/over generator frequency,under speed,over speed,charge fail,emergency stop,low oil pressure,high engine temperature,fail to start,low/high DC battery volts,fail to stop,generator short circuit protection,reverse power ,generator phase rotation error ,earth fault protection,loss of speed signal,fail to open,fail to close,out of sync,MPUopen circuit failure,negative phase sequence and loss of excitation.FEA TURES•Electronic engine capability •RS232or RS485remote communications •Modbus RTU•Pin number protected front panel programming•Engine exercise timer•Back-lit LCD 4-line text display •Multiple display languages •Voltage measurement •Configurable inputs (9)•Configurable outputs (5)•Automatic start •Manual start •Audible alarm •LED indicators•Built-in governor and AVR control •Engine history event log •Engine protection•Fault condition notification to a designated PC•Front panel mounting •PC configuration •Bus failure detection•Configurable alarm timers•Configurable start &stop timers •Automatic load transfer •SMS alert messaging •Front panel mounting •Remote monitoring•Magnetic pick-upLOAD SHARE FEA TURES •ROCOF &vector shift•Automatic starting &stopping of generator on load demand•Automatic hours run balancing of generator sets •Dead bus sensing•Module has the ability to interface with existing load share lines •Direct communication from the module to the governor and AVR •Link up to 16generators •Volts &frequency matching •KW and Kvar load sharing with multiple generators BENEFITS•Sends SMS messages to engineers to notify specificengine problems (GSM Modem and SIM card required)•On-site and remote module configuration•In-built engine diagnostics removes the requirement for service equipment•Full engine protection &instrumentation without the need for additional senders (Electronic engines only)•Remote monitoring of the module using comprehensive DSE PC software•License free PCsoftwareELECTRONIC ENGINE CAPABILITYOPERA TIONThe module is operated using the front STOP/RESET,MANUAL,AUTO and START push buttons.Three of these push buttons include an LED indicator.Additional push buttons provide LCD display scroll,lamp test,mute functionality and breaker control.TIMERS &INPUT FUNCTIONSThe module has been designed to include the following timers and input functions:•Start delay timer •Stop delay timer •Crank timer •Crank rest timer•Engage attempt &manual crank limit timers •Safety on delay timer •Warm up timer •Cooling timer•Energise to stop hold timer •Pre-heat timer•Pre-heat bypass timer•Smoke limiting control timer •Fail to stop timer•Over speed over shoot timer •Breaker pulse control timers •DC battery alarm delay timers •Sync/fail to sync timerBUIL T -IN FUNCTIONS•Alternator under/over volts•Alternator under/over frequency•Warning or shutdown on engine temperature,over/under speed,oil pressure•Warning,shutdown or electrical trip on battery volts or over current •Shutdown or electrical trip on reverse power,phase rotation or short circuit fault•Earth fault shutdown•Adjustable crank cycle/attempts •Full remote control and telemetry •9configurable digital inputs•5configurable and 2fixed relay outputs •System lock input•Load switching control push-button inputs •ROCOF/vector shift (mains/utility decoupling)•Negative phase sequence •Loss of excitationINSTRUMENT A TION AND ALARMSThe DSE5510M module provides advanced metering and alarm functionality via the LCD display.The information can be accessed using the display scroll push buttons.The table below shows the instrumentation and alarm features the module provides.Generator Volts L1-N,L2-N,L3-N Generator Volts L1-L2,L2-L3,L3-L1Generator Amps L1,L2,L3Generator Frequency HzGenerator kVA L1,L2,L3,Total Generator kW L1,L2,L3,Total Generator pf L1,L2,L3,Average Generator kVAr L1,L2,L3,Total Generator KWh Generator KVAh Generator KVArhGenerator Phase Sequence Synchroscope Display Engine Speed RPM Engine Oil Pressure Engine Temperature Plant Battery Volts Engine Hours RunNumber of Start Attempts Maintenance DisplayEngine ECU diagnostics information via industry standard CAN interface Enhanced metering via CAN when connected to an electronic engineTELEMETRYThe module gives the user full telemetry facilities when using the optional communications software.The module can be connected to a PC using the DSE810PC interface or by using a suitable modem.The PC software is Microsoft Windows ™based.All access into the module can be configured to become password protected to prevent unauthorised entry.The PC software allows the module to be controlled from a remote MUNICA TIONSThe DSE5510M has a number of different communication capabilities.SMS MessagingWhen the module detects an alarm condition,it has the ability to send an SMS message to a dedicated mobile number,notifying an engineer of the problem.(GSM Modem and SIM Card required).Remote CommunicationsWhen the module detects an alarm condition,it dials out to a PC notifying the user of the exact alarm condition.Vessel ManagementThe module has been designed to be integrated into new and existing vessel management systems.PC SoftwareThe module has the ability to be configured and monitored from a remote PC,using the DSE810interface (modem required).EVENT LOGThe module includes acomprehensive event log that shows the 25most recent alarm conditions and the date and time that they occurred.This function assists the user when fault finding and maintaining the generating set.EXP ANSION MODULESDSE123Load Share Lines Interface ModuleDSE157Relay Input Expansion ModuleDSE545&DSE548Remote Annunciation Expansion Module DSE130Input Expansion Module ELECTRONIC ENGINE COMP A TIBILITY •Cummins •Deutz•John Deere •MTU •Perkins •Scania •Volvo •Generic•Plus additional manufacturersTYPICAL LOAD SHARE APPLICATIONELECTRO MAGNETIC CAP ABILITY BS EN 61000-6-2EMC Generic Emission Standard for the Industrial Environment BS EN 61000-6-4EMC Generic Emission Standard for the Industrial EnvironmentELECTRICAL SAFETY BS EN 60950Safety of Information T echnology Equipment,including Electrical Business Equipment TEMPERA TURE BS EN 60068-2-2T est Ab to +70o C 60067-2-2Hot T est Ab to -30o C 60068-2-1ColdVIBRA TIONBS EN 60068-2-6T en sweeps in each of three major axes5Hz to 8Hz @+/-7.5mm,8Hz to 500Hz @2gn HUMIDITYBS 2011part 2.160068-2-30T est Cb Ob Cyclic93%RH @40o C for 48hoursSHOCKBS EN 60068-2-27Three shocks in each of three major axes 15gn in 11mSENVIRONMENT AL TESTING ST ANDARDS®DSE5510M Array RELA TED MA TERIALSTITLE P ART NO’SDSE5510M Manual057-080DSE123Data Sheet055-044Load Share Design&Commissioning057-047Guide to Synchronising and057-045/6Load Sharing55xx Software manual057-007CAN&DSE wiring guide057-004DSE5510M Installation Instructions053-048。
论述发电机组控制系统功能

论述发电机组控制系统功能摘要:从发电机组控制原理出发,介绍了发电机组控制系统的构成,分析了发电机组的不同控制模式:单机使用控制模式,AMF控制模式,并机控制模式和并网控制模式。
总结了发电机组控制系统的功能特点,包括显示功能、保护功能和辅助功能。
以供从事发电机组工作人员参考。
关键词:发电机组控制模式显示功能保护功能辅助功能1引言发电机组被广泛用于通讯、电力、医院、金融、石油、地铁等各行各业,随着微电子技术、计算机技术、通讯技术的不断提高,发电机组控制器构成高性能、高集成度、超强通讯的智能监测监控系统,使得发电机组工作更加简单、方便、可靠、智能。
2发电机组控制原理柴油机驱动发电机运转,将柴油的能量转化为电能。
在机汽缸内,经过空气滤清器过滤后的洁净空气与喷油嘴喷射出的高压雾化充分混合,在活塞上行的挤压下,体积缩小,温度迅速升高,达到的燃点。
被点燃,混合气体剧烈燃烧,体积迅速膨胀,推动活塞下行,称为‘作功’。
各汽缸按一定顺序依次作功,作用在活塞上的推力经过连杆变成了推动曲轴转动的力量,从而带动曲轴旋转。
首先,柴油机燃油电磁阀打开,同时,电动启动起动机。
如今发动机启动普遍使用直流起动机启动,当需要发动机工作时,由起动机驱动发动机转动,使发动机自行压燃工作。
当发动机启动成功之后,起动机必须尽快脱离,否则起动机将被毁坏。
机启动成功后,转速达到1500r/min,电机频率电压均正常,达到带载条件,断路器合闸。
发电机组工作过程中,需要监测机的转速、水温及油压等运行状态,需要监测发电机的电压、频率、相序等运行状态,当机或是发电机出现故障时,应能及时发出报警信号或者自动保护停机。
3发电机组控制模式的分类发电机组按使用方式可以将控制模式分为:单机使用控制模式,AMF控制模式,并机控制模式和并网控制模式。
3.1单机使用控制模式单机使用控制模式用于单机自动化,可通过远程开机信号控制发电机组自起停。
典型控制器有郑州众智的HGM7X10系列,英国深海的DSE7X10系列以及丹麦单控的CGC412系列等。
DB使用说明书

“深呼吸”系统Deep-Breath System使用说明书Instructions感谢您购买艾尔产品!Thank you for purchasing a AIR product.在使用本产品之前,请务必先仔细阅读本使用说明书。
请务必妥善保管好本书,以便日后能随时查阅。
请在充分理解内容的基础上,正确使用。
※安全注意事项1、请经销商或专业资格人员进行安装!2、请务必保证在更换或维护设备内各功能模块时,设备处于关机状态,以免触电或受到其它意外伤害!3、请务必保证按照机箱内所配备的膨胀螺栓规格尺寸进行规范的设备吊装,以免设备掉落!※使用注意事项1、请务必按照安装要求预留设备检修口,以保证设备内各功能模块日后的正常维护保养!2、请务必按照维护保养要求,定期对设备内各功能模块进行检查,以保证各功能的可持续性!3、请务必按照运行控制要求,操作系统运行状态,以保证各功能效果实现最大化!4、使用过程中出现突然故障,请通知当地经销商或厂家,切勿自行拆卸维修!1、“深呼吸”系统原理1.1运行原理“深呼吸”系统属艾尔第三代“空气龄”系列产品!系统采用了两方面“空气龄”措施,彻底的提高了建筑室内IAQ 品质,做到了“让空气更年轻”!◇“空气龄”措施一:通过提高室内、室外空气的更新速度来改善IAQ品质。
◇“空气龄”措施二:通过直接提高室内空气的洁净度来改善IAQ品质。
“深呼吸”系统,是艾尔应用超前的设计理念,在行业内首创将新风换气理念和净化除尘理念同时植入到一套系统当中,打造真正符合中国老百姓的绿色低碳节能康居产品。
不仅仅能够室内、外空气置换,关键在于对室内、外空气高效除尘和净化功能。
其主要功能包括:◇对室外补入的空气进行高效除尘(过滤精度达到PM0.1)◇对室内空气既进行高效除尘(过滤精度达到PM0.1)又进行高效净化(杀菌、除甲醛、灭病毒)◇根据室内CO2和TVOC浓度变化,适时的补充室外氧气、排除室内CO2和TVOC◇通过大屏幕液晶开关全面智能的无人值守运行,打造私人的“室内氧吧”1.2结构原理2、“深呼吸”系统安装2.1主机安装◇请将主机安装在足以承受机器重量的地方。
DSE5110,英国深海控制器英文说明书

Parameter Range 0 - Start delay 0-60m (5s)1 - Preheat0-60s (0s)2 - Crank attempt 3-60s (10s)3 - Crank rest 3-60s (10s)4 - Safety delay 8-60s (8s)5 - Warming up 0-60s(0s)6 - Return delay 0-60m (30s)7 - Cooling run 0-60m (60s)8 - E.T.S. hold 0-60s (0s)9 - Sensor fail 1-5s (2s)10 - Fail to Stop 10-60s (60s)11 - Low Oil Press.5-150PSI (15PSI)12 - High Temp 90-150°C (95°C)13 - Under Speed 0-3600RPM (1250RPM)14 - Over Speed 300-5000RPM (1750RPM)15 – Under freq’0-60Hz (40Hz)16 - Over freq’50-72Hz (57Hz)17 - Charge Alt Failure 0-25V (8V DC)18 - Flywheel teeth 46-300 (0)19 - CT Primary10-6000A (500A)ParameterSelections 20 - Alternator poles0,2,4,6,821 - Oil pressure input0 - Not used1 - Digital, close for low pressure2 - Digital, open for low pressure3 - VDO 0-5bar4 - VDO 0-10bar5 - Datcon 5bar6 - Datcon 10bar7 - Datcon 7bar8 - Murphy 7bar9 - User configured22 - Coolant temp input0 - Not used1 - Digital, close for high temperature2 - Digital, open for high temperature3 - VDO 40°C to 120°C4 - Datcon High5 - Datcon Low6 - Murphy7 - Cummins8 - PT1009 - User configuredACCESSING THE CONFIGURATION EDITOR Press the Stop/Reset and Infobuttonssimultaneously.• The LED beside the AUTO button willflash continuously to indicate thatconfiguration mode has been entered.• The first configurationsetting is displayed:From the configuration table, this example is displaying Start Delay (parameter 0). It is currently set to 5 seconds .(Factory default settings are shown in the configuration table in bold italic text)EDITING A PARAMETER• Enter the editor as described above.• Press + / - to scroll through the parameters tothe one you want to change.• Press 9 to enter editmode. The symbol will flash on the display to indicate that edit mode has been entered.• Press + / - to change the parameter to thedesired value.• Press 9 to save the value and exit edit mode forthis parameter.• The symbol will be removed from the displayto indicate that edit mode has been exited.• To select another value to edit, press the + / -buttons. Continuing to press the + and – buttons will cycle through the adjustable parameters as shown in the following lists.D E E P S E A E L E C T R O N I C SModel 5110 Configuration and installation instructions051-178ISSUE 2button. Ensure you have saved any changes button firstDIMENSIONS240mm x 172mm x 57mm (9.5” x 6.8” x 2.25”)PANEL CUTOUT 220mm x 160mm (8.7” x 6.3”)Parameter Selections23 - Fast loading0 - Noenabled 1 - Yes24 - AC system0 - 3 phases 4 wires1 - 1 phase2 wire2 -3 phases 3 wires3 - 2 phases 3 wires 25 - Oil pressure0 - Bar/PSIdisplay units 1 - kPaParameter Selection26 - Output 10 - Unused1 - Preheat mode 02 - Air flap3 - Close Generator4 - Energise to stop5 - Engine running6 - Shutdown alarm7 - System in auto8 - Auxiliary input 1 active9 - Auxiliary input 2 active10 - Auxiliary input 3 active11 - Auxiliary input 4 active12 - Auxiliary input 5 active13 - Preheat mode 114 - Preheat mode 215 - Preheat mode 316 - Warning alarm17 - Common alarm18 - Maintenance due27 - Output 20 - Unused1 - Preheat mode 02 - Air flap3 - Close Generator4 - Energise to stop5 - Engine running6 - Shutdown alarm7 - System in auto8 - Auxiliary input 1 active9 - Auxiliary input 2 active10 - Auxiliary input 3 active11 - Auxiliary input 4 active12 - Auxiliary input 5 active13 - Preheat mode 114 - Preheat mode 215 - Preheat mode 316 - Warning alarm17 - Common alarm18 - Maintenance due Parameter Selection28 - Output 30 - Unused1 - Preheat mode 02 - Air flap3 - Close Generator4 - Energise to stop5 - Engine running6 - Shutdown alarm7 - System in auto8 - Auxiliary input 1 active9 - Auxiliary input 2 active10 - Auxiliary input 3 active11 - Auxiliary input 4 active12 - Auxiliary input 5 active13 - Preheat mode 114 - Preheat mode 215 - Preheat mode 316 - Warning alarm17 - Common alarm18-Maintenance due29 - LCD 10 - Unused1 - Preheat mode 02 - Air flap3 - Close Generator4 - Energise to stop5 - Engine running6 - Shutdown alarm7 - System in auto8 - Auxiliary input 1 active9 - Auxiliary input 2 active10 - Auxiliary input 3 active11 - Auxiliary input 4 active12 - Auxiliary input 5 active13 - Preheat mode 114 - Preheat mode 215 - Preheat mode 316 - Warning alarm17 - Common alarm18 - Maintenance due30 - LCD 20 - Unused1 - Preheat mode 02 - Air flap3 - Close Generator4 - Energise to stop5 - Engine running6 - Shutdown alarm7 - System in auto8 - Auxiliary input 1 active9 - Auxiliary input 2 active10 - Auxiliary input 3 active11 - Auxiliary input 4 active12 - Auxiliary input 5 active13 - Preheat mode 114 - Preheat mode 215 - Preheat mode 316 - Warning alarm17 - Common alarm18M i t dParameter Selection31 - LCD 30 - Unused1 - Preheat mode 02 - Air flap3 - Close Generator4 - Energise to stop5 - Engine running6 - Shutdown alarm7 - System in auto8 - Auxiliary input 1 active9 - Auxiliary input 2 active10 - Auxiliary input 3 active11 - Auxiliary input 4 active12 - Auxiliary input 5 active13 - Preheat mode 114 - Preheat mode 215 - Preheat mode 316 - Warning alarm17 - Common alarm18 - Maintenance due32 - LCD 40 - Unused1 - Preheat mode 02 - Air flap3 - Close Generator4 - Energise to stop5 - Engine running6 - Shutdown alarm7 - System in auto8 - Auxiliary input 1 active9 - Auxiliary input 2 active10 - Auxiliary input 3 active11 - Auxiliary input 4 active12 - Auxiliary input 5 active13 - Preheat mode 114 - Preheat mode 215 - Preheat mode 316 - Warning alarm17 - Common alarm18 - Maintenance dueParameter Selection33 - Input 10 - Delayed, Warning, close to activate1 - Delayed, Warning, open to activate2 - Immediate, Warning, close to activate3 - Immediate, Warning, open to activate4 - Delayed, Shutdown, close to activate5 - Delayed, Shutdown, open to activate6 -Immediate, Shutdown, close to activate7 - Immediate, Shutdown, open to activate8 - Remote Start, close to activate9 - Remote Start, open to activate34 - Input 20 - Delayed, Warning, close to activate1 - Delayed, Warning, open to activate2 - Immediate, Warning, close to activate3 - Immediate, Warning, open to activate4 - Delayed, Shutdown, close to activate5 - Delayed, Shutdown, open to activate6 - Immediate, Shutdown, close to activate7 - Immediate, Shutdown, open to activate8 - Electrical trip, close to activate9 - Electrical trip, open to activate35 - Input 30 - Delayed, Warning, close to activate1 - Delayed, Warning, open to activate2 - Immediate, Warning, close to activate3 - Immediate, Warning, open to activate4 - Delayed, Shutdown, close to activate5 - Delayed, Shutdown, open to activate6 - Immediate, Shutdown, close to activat e7 - Immediate, Shutdown, open to activate8 - Lamp test, close to activate9 - Lamp test, open to activate36 - Input 40 - Delayed, Warning, close to activate1 - Delayed, Warning, open to activate2 - Immediate, Warning, close to activate3 - Immediate, Warning, open to activate4 - Delayed, Shutdown, close to activate5 - Delayed, Shutdown, open to activate6 - Immediate, Shutdown, close to activat e7 - Immediate, Shutdown, open to activate37 - Input 50 - Delayed, Warning, close to activate1 - Delayed, Warning, open to activate2 - Immediate, Warning, close to activate3 - Immediate, Warning, open to activate4 - Delayed, Shutdown, close to activate5 - Delayed, Shutdown, open to activate6 - Immediate, Shutdown, close to activate7 - Immediate, Shutdown, open to activate8 - Oil pressure, Shutdown, close to activate9 - Oil pressure, Shutdown, open to activate。
海洋控制器海洋控制器用户指南说明书

2CONTENTSNOTICES................................................ .. (3)CE INFORMATION (3)INTRODUCTION (4)GENERAL WARNINGS (4)NITROX/O2 (5)DIVING IN COLD WATER (5)SETUP & DIVE (6)REGULATOR FIRST STAGES (7)Preparation to mount a regulator on a cylinder (7)Mounting a regulator with a yoke inlet fitting (7)Removing a regulator with a yoke inlet fitting (8)Mounting a regulator with a DIN inlet fitting (8)Removing a regulator with a DIN inlet fitting (8)SECOND STAGE WITH A VENTURI SWITCH (8)Adjustments prior to entering the water (8)Adjustments during the dive (8)Adjustments after the dive (8)POST DIVE (9)REPAIRS AND SERVICE (9)GUIDELINES FOR MINIMUM SERVICE INTERVALS (10)RECORDS (10)INSPECTIONS/SERVICE RECORD (10)FIRST/SECOND STAGE PAIRING (11)CAUTION:Indicates a potentially hazardous condition or practice which, if not avoided orcorrected, may result in minor to moderate injury or damage to equipment.NOTICE:Used to point out or emphasize important condition or fact.WARNING:Indicates a potentially hazardous condition or practice which, if not avoided orcorrected, may result in serious injury or death.WARNINGS, CAUTIONS AND NOTICESCertain symbols and signal words are used throughout this document to direct your attention to issues that mayaffect your safety. The intended use of these symbols and signal words is as follows:3COPYRIGHT NOTICEThis Guide is copyrighted, all rights are reserved. It may not, in whole or in part, be copied, photocopied, reproduced, translated, or reduced to any electronic medium or machine readable form without prior consent in writing from Oceanic. Oceanic Regulator Owner’s Guide © Oceanic, 20171540 North 2200 West,Salt Lake City, UT 84116Document Control #:OC.01.05.0001TRADEMARK, TRADE NAME, AND SERVICE MARK NOTICEOceanic and the Oceanic logo are registered or unregistered trademarks of Oceanic. All rights are reserved. PATENT NOTICEU.S. Patents have been issued to protect the following design features: Orthodontic Mouthpiece (U.S. Patent No. 4,466,434) and Second Stage Regulator Depth Compensating Adjustment Mechanism (U.S. Patent No. 5,660,502).EC TYPE EXAMINATION CONDUCTED BY: Products carrying the mark 0098 have the EC Type Examination conducted by:DNV GL SE, Maritime, Brooktorkai 18 20457, Hamburg, GermanyPhone+*************************************** 0098Products carrying the mark 0474 have the EC Type Examination conducted by:RINA: Via Corsica 12, 16128 Genova, Italia: phone +39 010 53851: 0474All products sold by Oceanic in the EU (European Union) meet the following requirements where applicable. Compliance with the following where applicable.EN 250:2014: This standard describes certain minimum performance requirements for SCUBA regulators sold in the EU (European Union). Testing identifies regulators that should not be used in water colder than 50 °F / 10 °C, these regulators are marked >10 °C.EN ISO 12209:2013: All Oceanic regulator’s thread and yoke connection conforms to ISO 12209:2013. Maximum working pressure: 241 bar (3500 PSI).EN13949:2003: This standard describes special qualification testing for regulators that are to be used with gases whose oxygen content is greater than 22%. Regulators that have passed testing are marked NITROX/O 2. EN144-3: This standard describes the M26 regulator inlet fitting and M26 valve that must be used with gases containing over 22% oxygen sold in the EU (European Union). These inlet fittings and valves are marked with the maximum rated working pressure.EN12021: This standard specifies the allowable contaminates and component gases that make up compressed air. This standard is the equivalent of the USA Compressed Gas Association’s Grade E air. Both standards allow very small amounts of contaminants that are not harmful to breathe, but can cause a problem if present in systems using gases with a high percentage of oxygen.WARRANTY INFORMATIONFor details, refer to the Product Registration Card provided by your Authorized Oceanic Dealer. For additional information, visit the Oceanic web site at: 4INTRODUCTIONTHANK YOU FOR CHOOSING A REGULATOR PRODUCT FROM OCEANIC!Features and operation of the various models of Oceanic regulator first and second stages currently available are described in this owner’s guide, and/or any addendum or supplement provided with it.By following the instructions in this guide, you will understand how your regulator product works, how to make best use of its features, and how to maintain it for long term use.Some information presented may not be applicable to the specific model of regulator or accessory that you purchased.• It is essential that the diver read this guide and become familiar with the proper setup, use and care of any Oceanic regulator model. If the instructions given in this guide are not understood and followed, possible injury or death may result.• This regulator product is intended for use only by divers who have received certification from a nationally recognized course in basic open water SCUBA or higher.• This regulator must not be used by untrained persons who may not have knowledge of the potential risks and hazards of SCUBA diving.• This regulator must be used together with an instrument that measures and indicates the user’s air supply pressure.• As with all underwater life support equipment, improper use or misuse of this product can cause serious injury or death.• Read and understand the User’s Guide completely before diving with any Oceanic regulator.• If you do not fully understand how to use your new Oceanic regulator, or if you have any questions, you should seek instruction in its use from your authorized Oceanic Dealer before use.• Before each dive, inspect and test this regulator for proper operation. If any part does not function properly, DO NOT USE!• Air supplies used with the regulator must meet requirements for breathable air: Grade E in the U.S.A. or EN 12021 Annex A standards in Europe.• If you intend to dive in conditions other than those in which you received basic open water training, such as in cold water or other more severe environments, consult a professional dive instructor who is familiar with local conditions for supplemental training and best practices for that specific area. This training should include any special preparation of or handling of the equipment you intend to use. If you have not prepared for diving in an unfamiliar environment do not dive. The Authorized OceanicDealer in the area in which you want to dive should be able to provide guidance.GENERAL WARNINGS:5NITROX/O2Oceanic regulators sold throughout most of the world and outside of the EU are built using oxygen compatible components and are cleaned for service with gasses having oxygen content up to 40%. These oxygen enriched mixtures are commonly referred to in recreational SCUBA diving as “Nitrox”.WARNING:• Oxygen exposure can be toxic and can cause injury or death. Air contains 20.9% oxygen; a gas with more than 22% oxygen is considered to have a high percentage of oxygen and is called NITROX. Diving with Nitrox requires specialized advanced training and you must not dive with Nitrox unless certified for this specialty by a nationally-recognized training agency.• Oxygen accelerates combustion. Use of Nitrox or oxygen introduces a risk of a catastrophic fire, the risk increases with the percentage of oxygen in the gas. Special care must be taken to reduce this risk. • Regulators used with Nitrox or oxygen must be cleaned at least annually or any time normal compressed air has been used.• Regulators used with gasses having oxygen content exceeding 41% must be serviced by Oceanic trained personnel in a facility equipped to oxygen clean and assemble regulators for oxygen use. Nitrox has different depth and time limits than air and these limits change with the percentage of oxygen in the Nitrox. Oceanic Nitrox dive computers can help monitor these safety limits.Much of the information below is provided in compliance with EN13949 and EN144-3; this information documents best practices for using gasses with oxygen content above 22%.Regulators sold in the EU for use with Nitrox or oxygen are subjected to more extensive cleaning procedures and must be tested to ensure that the components and lubricants are safe for use in 100% oxygen at high pressure and at elevated temperature. This testing is described in EN13949:2003; regulators that have passed this testing are marked NITROX/O2. In the EU, regulators that have passed this testing are supplied with an EN144-3 M26 inlet fitting, marked with its maximum rated working pressure.The regulator and all attached accessories must be prepared for oxygen exposure. This preparation involves special cleaning and the use of special oxygen safe components and lubricants.Air used in SCUBA diving may contain minute amounts of flammable hydrocarbons that are considered safe to breathe. Over time these hydrocarbons may accumulate and represent a fire risk if used with Nitrox or oxygen. Specially filtered air is available, called hyper-filtered air. Regulators to be used with Nitrox and oxygen must not be used with normal compressed air.DIVING IN COLD WATERWARNING:• SCUBA diving in water colder than 50°F/10°C requires special equipment, training, and preparation to prevent injury or death. Training for cold water is available from a recognized and accredited SCUBA training organization.• When regulators get cold and wet, freezing can occur. Regulator freezing can result in rapid loss of air that may lead to injury or death.When a regulator operates and the gas flows through it, there is a natural chilling effect as the gas experiences a rapid drop in pressure. The gas can become much colder than the surrounding water and can compromise regulator performance, primarily from the formation of ice inside the regulator. Under these conditions the regulator can experience an uncontrollable free flow.This effect occurs more rapidly as diving depth is increased and as water temperatures decrease below 50°F (10°C) and approach the freezing point of water at 32°F (0°C).6If this occurs while you are diving, you must have an emergency plan to allow you to surface without injury. This is the reason for the requirement for special training for diving in cold water.For diving activity that occurs at water temperatures between 50°F (10°C) and 32°F (0°C), it is impossible to predict the temperature at which a regulator may freeze due to the number of variables involved.Training is available to address concerns with diving at these reduced temperatures and application of adaptive measures can reduce the risk that a regulator issue will occur and how to deal with it if it does occur. NOTICE: Certification of regulators and valves in the European Union (EU) provides no additional guidance for use of regulators approved for use below 10°C (39°F), other than a prohibition for use below 4°C (39°F) regardless of adaptive measures applied.There are measures that can be taken to reduce the risk that a regulator will freeze.Oceanic offers the following information regarding best practices to address this issue, but they are absolutely not a substitute for specialized training and practice under supervised and controlled conditions.Cold water best practices that will help reduce the occurrence of regulator freezing: • Use properly maintained, good working dive equipment designed for cold water diving.• Use air specially dried for cold water diving in your tanks.• Warm the regulator, tank, BC, diver insulation, and the diver before the dive.• Open the tank valve slowly to reduce internal pressure drop cold.• Do not use the BC inflator, dry suit inflator, or purge button before going diving.• Keep the primary second stage dry before taking the first breath.• Do not breathe from the regulator until you are in the water.• Do not remove the regulator from your mouth while diving.• Do not allow an alternate air source to free flow.• Remove the regulator from your mouth when the dive is over.• Remember to rewarm all equipment and yourself before a second dive.SETUP & DIVEA SCUBA regulator reduces the high pressure air stored in a cylinder to breathing pressure using two pressure reduction valves.The First Stage valve automatically reduces the High Pressure air to a lower pressure which fills the hoses; this is called Intermediate Stage Pressure (ISP). The ISP is routed by low pressure hoses to the primary second stage which reduces the ISP to breathing pressure, also called ambient pressure. The ISP is also routed in other low pressure hoses to BC inflators, Dry Suit fill valves, and to Alternate Air second stages.The Second Stage, also called a Demand Valve, closes and stops air flow when the diver is exhaling, and opens to supply air when the diver inhales. These are very simple valves and very dependable when properly maintained and serviced.WARNING:an authorized service facility.•in injury or death. REGULATOR FIRST STAGESdemand (i.e., when you inhale).(refer to Fig. 1) for damage and replace if required.WARNING:• Always open cylinder valves very slowly.1.2.(fig. 3).3.hose will be routed over the diver’s right shoulder.4.5.6.7.8.8REMOVING A REGULATOR WITH A YOKE INLET FITTING1. After the valve has been depressurized, loosen the yoke/screw knob enough to remove the regulator.2. Dry the inlet protector cap and place it over the regulator inlet.3. Tighten the yoke/screw knob to secure to inlet protector cap.MOUNTING A REGULATOR WITH A DIN INLET FITTING1. Remove the DIN inlet protector cap. (fig. 4)2. Insert the DIN inlet fitting into the DIN valve and check the hose orientation to assurethat the primary second stage hose will be routed over the diver’s right shoulder.3. If a pressure gauge is attached, ensure it is not facing a person.4. Turn the DIN hand wheel clockwise to seal, finger tight only.5. Slowly open the cylinder valve. It should take a few seconds to pressurize the regulator.6. Once the regulator is pressurized, fully open the valve and turn clockwise 1/2 turn.7. Check the pressure gauge, and while observing the pressure gauge take a few breathsfrom the regulator. The pressure indicator should not move while breathing.8. Read the Diving in Cold Water section for cold water best practices, which prohibit test breathing.REMOVING A REGULATOR WITH A DIN INLET FITTING1. Turn the valve hand wheel clockwise to close the valve.2. Press the regulator purge valve to depressurize the valve, confirm with the pressure gauge.3. After the valve has been depressurized, loosen the DIN hand wheel and remove the regulator.4. Dry the inlet protector cap and place it over the regulator DIN inlet.5. Ensure that the protective cover is secure on the DIN inlet (fig. 4).ADJUSTMENTS PRIOR TO ENTERING THE WATERIf present, set the dive-pre-dive Venturi switch (Fig. 5/6_a) to positive (+) or dive, and turnthe breathing effort adjustment knob (Fig. 3/4_b) counter clockwise until it stops and thenturn it clockwise one turn.ADJUSTMENTS DURING THE DIVEThe breathing effort adjustment knob (Fig. 5 & 6) can be turned to change the breathingeffort to suit the diver’s comfort.ADJUSTMENTS AFTER THE DIVEIf present, set the dive-pre-dive Venturi switch to - or pre-dive.Press the regulator purge valve to depressurize the valve, and confirm withthe pressure gauge.abFIG. 4baFIG. 5FIG. 69POST DIVE• After use, the regulator must be cleaned and dried before storage.• Before cleaning the regulator, ensure that the inlet protector cap is in place. If equipped with a breathing effort adjustment knob, the knob should be turned clockwise until it clicks.• The best way to clean the regulator is to place the regulator on a cylinder, pressurize the regulator, then immerse the regulator and the cylinder in a container of warm fresh water and soak for 30 minutes or more. • If a cylinder is not available, ensure that the inlet protector cap is securely in place and immerse in a shallow container of warm water and soak for 30 minutes or more.• After cleaning, wipe the regulator with a towel and hang to air dry.• Do not store the regulator with hoses tightly coiled.REPAIRS AND SERVICEWARNING:DO NOT attempt to disassemble or repair the first or second stages, or to adjust the first stage. Doing so could cause malfunction while underwater, possibly resulting in serious injury or death. It will also void the regulator’s limited warranty.In the event that any component of your regulator assembly requires any form of repair or service, return it to your local Authorized Oceanic Dealer for professional service by a trained technician authorized to perform Oceanic factory authorized service.At least once a year, your complete regulator assembly should be inspected and serviced by an Authorized Oceanic Dealer. More frequent service is recommended if you dive in severe conditions or more frequently than an average diver (see guidelines).ANNUAL SERVICE CONSISTS OF:• Inspection• Complete disassembly• Complete reassembly• Thorough cleaning and evaluation of reusable parts• Replacement of non-reusable parts• Final adjustment and testingCosts for routine inspection and Annual Service are understood to be a normal part of operation, and are not covered by the regulator’s limited warranty.If Warranty Service is requested, or routine service parts are requested in accordance with a Registered Service Agreement, present the appropriate documents (i.e., card, receipts, and service records) to the Authorized OceanicDealer when the regulator is delivered for service.OCEANIC REGULATOR OWNER’S GUIDE10GUIDELINE FOR OCEANIC REGULATOR EQUIPMENT MINIMUM SERVICE INTERVALS Due to variations of use and storage time that Oceanic Regulator equipment may be subjected to, the Guidelines and defined Intervals given herein are subject to the discretion of the owner of the specific product. Inspection and/ or service indicated must be performed only by an Authorized Oceanic Dealer.Personally owned equipment used for recreational diving activity:• Equipment used 100 dives or less per year should be inspected at least once per year.• Equipment used more than 100 dives per year should be serviced after 100 dives prior to further use.• Equipment stored more than 6 months should be inspected/serviced as required, prior to use. Equipment used for dive training and/or consumer rental activities:• Equipment should be inspected prior to every use.• Equipment should be serviced at least once every 6 months regardless of use.• Equipment should be serviced after 100 dives prior to further use.• Equipment stored for more than 3 months should be inspected/serviced as required, prior to use. Regardless of ownership or intended use:• Equipment should be inspected/serviced if it displays any signs of leakage, malfunction, free flowing, any signs of deterioration, or improper performance or breathing effort.• Equipment should be inspected/serviced if the first stage inlet filter shows any sign of residue or discoloration. • Equipment must be inspected annually and serviced as needed or every other year, whichever comes first.RECORDSFirst Stage Model ________________________________ First Stage Serial # ____________________________ Second Stage Model _____________________________ Second Stage Serial # __________________________ Octopus Model __________________________________ Octopus Serial #_______________________________ Date of Purchase ________________________________ Oceanic Dealer _______________________________ Dealer Phone No. ________________________________INSPECTION / SERVICE RECORDDate Service Performed Dealer /üüCDX SPXSP5EDX S E C O N D S T A G EEN250A:2014EN250:2000EN250A:2000EN250A:2000EN250A:2000EN250A:2014EN250A:2014EN250A:2014EN250A:2014EN250A:1993>10C。
- 1、下载文档前请自行甄别文档内容的完整性,平台不提供额外的编辑、内容补充、找答案等附加服务。
- 2、"仅部分预览"的文档,不可在线预览部分如存在完整性等问题,可反馈申请退款(可完整预览的文档不适用该条件!)。
- 3、如文档侵犯您的权益,请联系客服反馈,我们会尽快为您处理(人工客服工作时间:9:00-18:30)。
DSE8610 操作说明书
(内部资料)
深圳海汇科技有限公司
深圳市南山区南山大道2002号光彩新天地大厦8B1-8B2 电话:0755 2646 6606 传真:0755 2646 6609
深圳海汇科技有限公司
目录
章节
页数
1 控制器界面........................................................................................................3 2 按键...................................................................................................................3 3 LED 指示灯 .......................................................................................................4 4 选择模式 ...........................................................................................................5 5 操作模式 ...........................................................................................................5 6 浏览/查看控制器测量的各种参数.......................................................................6 7 排除故障 ...........................................................................................................8 8 控制器参数设置方法 .........................................................................................9
Bus(母排)项:
查看母排上的参数 如:母排相电压、线电压、频率 和相序等
按⑾号键即 上下选择键 循环查看菜单各参数
七、排除故障
8610 控制器停机保护可按 ⑴
解除故障锁定。
停机故障信号没解除或修复前面板指示灯[14] [15] [16] LED 点亮
例如:低油压报警指示灯[15] 点亮 高水温报警指示灯[16] 点亮 其它普通报警指示[14] 点亮,可查看参考液晶显示面板报警提示信息修
深圳海汇科技有限公司
八、控制器参数设置方法: 控制器参数设定可以利用面板或设置软件进行调整。 如何在面板上调整一个参数:
1. 进入编辑模式
同时按下
和
制器处于可编辑模式
2. 修改参数
按键,屏幕出现
图标,此时表明控
ⅰ 按“ ”,“ ”键循环查看可设置的参数
ⅱ 选定设置参数后,按 将闪动
键,控制器进入参数调整状态,被调整的参数
ⅲ 按动按扭“ ”和按扭“ ”进行参数调整
3. 保存参数 参数调整完毕后,按动按扭
,调整的参数停止闪动,表明参数被保存;
4. 退出编辑模式
按住
键几秒退出编辑模式
5. 重复上述步骤对需要设置的参数选择,调整
无论是停机状态还是运行状态,均可以通过连续按动液晶显示屏
和
按钮滚动查看发电机组的实时参数。
深圳海汇科技有限公司
7 深圳市南山区南山大道 2002 号光彩新天地大厦 8B1-8B2 室
电话:0755 - 2646 6606 传真:0755 - 2646 6609
深圳海汇科技有限公司
Generator 项:如图
查看发电机各运行参数 如:发电机线电压、相电压、频率、 电流 有功功率、无功功率和总功率等
按⑾号键即 上下选择键 循环查看菜单各参数
8
17 16 15 14
7
12 13
1
2
3
二、按键
4
5
6
1、
发电机组停机、故障复位键
2、
发电机组手动模式键
3、
空键(不起任何作用)
深圳海汇科技有限公司
3 深圳市南山区南山大道 2002 号光彩新天地大厦 8B1-8B2 室
电话:0755 - 2646 6606 传真:0755 - 2646 6609
深圳海汇科技有限公司
4、
发电机组自动模式键
5、
静音键
6、
发电机组启动键(在手动模式时有效)
7、
发电合闸键(断路器合闸)
8、
发电分闸键(断路器分闸)
9、
进入及确认键
10、
左右菜单导航键,循环选择菜单
11、
上下选择键,循环查看菜单各参数
三、LED 指示灯
12、发电存在(发电机组运行正常),绿灯亮
13、发电合闸(机组给负载供电), 绿灯亮
电话:0755 - 2646 6606 传真:0755 - 2646 6609
深圳海汇科技有限公司
六、浏览/查看控制器测量的各种参数 下面以 8610 控制器显示面板为例,模块共有六大菜单功能参数测量查看,各菜 单功能又分若干小项显示发电机组各种参数,使用《二、按键》中的⑽号键即 左右菜单导航键可选择各种菜单显示,查看菜单各显示参数可使用
《二、按键》中的⑾号键即 上下选择键,循环查看菜单各种参数
Alarms 项: 如图 查看机组实时报警
按⑾号键即 上下选择键 循环查看菜单各参数
Event log 项:如图 查看机组报警历史记录
按⑾号键即 上下选择键 循环查看菜单各参数
深圳海汇科技有限公司
6 深圳市南山区南山大道 2002 号光彩新天地大厦 8B1-8B2 室
复故障,故障修复后按 ⑴
停机/复位键解除停机锁定,对应的报警指示灯
熄灭,发电机组可开机试运行。
深圳海汇科技有限公司
8 深圳市南山区南山大道 2002 号光彩新天地大厦 8B1-8B2 室
电话:0755 - 2646 6606 传真:0755 - 2646 6609
启动键,手动启动机组;如需停机按 ⑴
停止键。
2、自动模式下启动柴油发电机组
若要 8610 控制器处于自动模式,则按 ⑷
自动模式键,发电机组处于自
动待命状态,此时如有外部信号(无源远程自启动信号)输入有效,机组自动启
动盘车(一般自启动信号线的线号定义为 60#线,具体可查看控制屏内线路图或
端子排上线号),此时断开外部信号(自启动信号)时,发电机组冷却停机,时
电话:0755 - 2646 6606 传真:0755 - 2646 6609
深圳海汇科技有限公司
四、选择模式
控制器有三种工作模式:
1、按
键,控制器处于停机/复位模式。
2、按
键,控制器处于手动模式。发电机组处在待命状态,可按
键手动启动机组。
3、按
键,控制器处于自动模式,发电机组处在待命状态,接收远程
14、公共报警
绿灯亮
15、低油压报警
绿灯亮
16、高水温报警
绿灯亮
17、自动模式指示
绿灯亮
注:14-17 是客户根据实际需要自定义 4 个 LED 指示灯,在此定义 4 个 LED 灯 只是为了举例 。
深圳海汇科技有限公司
4 深圳市南山区南山大道 2002 号光彩新天地大厦 8B1-8B2 室
DSE8610 控制器自定义输出设置:
6 路自定义输出:
输入 1(8 号脚):用户可根据使用情况进行设置 输入 2(9 号脚):用户可根据使用情况进行设置 输入 3(10 号脚):用户可根据使用情况进行设置 输入 4(11 号脚):用户可根据使用情况进行设置 输入 5(12 号脚):用户可根据使用情况进行设置 输入 6(13 号脚):用户可根据使用情况进行设置
深圳海汇科技有限公司
2 深圳市南山区南山大道 2002 号光彩新天地大厦 8B1-8B2 室
电话:0755 - 2646 6606 传真:0755 - 2646 6609
深圳海汇科技有限公司
DSE8610 操作说明书
一、 控制器界面
14 15 16
17
11 10 9
9 深圳市南山区南山大道 2002 号光彩新天地大厦 8B1-8B2 室
电话:0755 - 2646 6606 传真:0755 - 2646 6609
深圳海汇科技有限公司
DSE8610 控制器自定义输入设置:
11 路自定义输入:
输入 1(60 号脚):用户可根据使用情况进行设置 输入 2(61 号脚):用户可根据使用情况进行设置 输入 3(62 号脚):用户可根据使用情况进行设置 输入 4(63 号脚):用户可根据使用情况进行设置 输入 5(64 号脚):用户可根据使用情况进行设置 输入 6(65 号脚):用户可根据使用情况进行设置 输入 7(66 号脚):用户可根据使用情况进行设置 输入 8(67 号脚):用户可根据使用情况进行设置 输入 9(68 号脚):用户可根据使用情况进行设置 输入 10(69 号脚):用户可根据使用情况进行设置 输入 11(70 号脚):用户可根据使用情况进行设置
间为 60S(冷却时间可以自行设置)。如发现发电机组运行异常可按 ⑴
停
机/复位键停机。
注:《五、操作模式》描述中⑴键-⒆键是按《二、按键》及《三、LED 指示灯》 表示的按键和指示灯数字来描述。