核电站蒸汽发生器的设计解析
AP1000核电厂蒸汽发生器制造难点及质量管理-2019年文档

AP1000核电厂蒸汽发生器制造难点及质量管理1 概述蒸汽发生器是压水堆核电厂的关键设备,是核电厂一、二回路进行热能转换、传递的热交换设备,其一次侧为一回路压力边界,在服役期间承受高温、高压、强放射性,二次侧为核蒸汽产生区,一、二回路及其介质之间由U型换热管和管板构成隔离层。
AP1000蒸汽发生器属于核平安A级,抗震等级为I类,设计寿命为60年。
由于其一次侧与二次侧的温度、压力、放射性的差异,蒸汽发生器的制造质量是极其重要的,直接影响到核电厂成套装备的整体水平、维护和长期运行可靠性。
2 结构特点和制造难点AP1000蒸汽发生器主要由以下组件组成:下封头组件、管板组件和下筒体组件和上筒体组件及内件。
采用倒U形管立式布置,自然循环,结构非常紧凑。
2.1 结构特点2.1.1 为了减少在役检查工作量和检查人员受到的辐射剂量,AP1000蒸汽发生器水室封头和上部椭圆封头设计成一体化锻件,取消了水室封头与过渡段、椭圆封头与椭圆封头环之间的焊缝,使得上下封头锻件尺寸大、结构复杂、吨位重、材质的纯洁度、致密度和各项理化性能指标要求非常高。
2.1.2 △125型蒸汽发生器的传热管采用了正三角形排列,这种排列比正方形排列更为紧凑,在管束区的单位体积内允许配置更大传热面积。
2.1.3 △125型蒸汽发生器的蒸汽枯燥器采用了效率更高的双钩型波形板结构,从而将双层枯燥器改为单层。
这一技术改进减小了汽水别离装置所占的空间,在蒸汽发生器总面积不变的情况下增加了二次侧的水装量,并加宽了正常水位的控制带,有利于改善电厂瞬态运行特性。
2.1.4 采用了抗腐蚀性能优秀的镍?t铁合金〔Inconel-690〕热处理管作为U形传热管材料,并配有二次侧炉水全挥发处理制度,以减少传热管的腐蚀。
2.1.5 管板和传热管之间采用全深度、最小剩余应力的液压胀接,以限制二次侧炉水侵入管板和传热管的间隙,从而防止间隙局部腐蚀的发生。
2.1.6 管束的直段采用三叶孔型支撑板,管束的下部取消了流量分配板。
核能发电系统设计与分析

核能发电系统设计与分析一、引言核能是一种高效、清洁的能源形式,被广泛用于发电系统。
本文将探讨核能发电系统的设计和分析,重点关注其结构和性能。
二、核能发电系统的结构核能发电系统由核反应堆、蒸汽发生器、蒸汽涡轮发电机组和冷却系统等组成。
1. 核反应堆:核反应堆是核能发电系统的核心组件。
它通常由反应堆压力容器、燃料装载机构和控制系统等组成。
其中,反应堆压力容器承载核燃料和控制系统,是核能发电系统的重要组成部分。
2. 蒸汽发生器:蒸汽发生器利用核反应堆产生的热能,将水转化为蒸汽,供给蒸汽涡轮发电机组。
蒸汽发生器具有高效能的特点,是核能发电系统中重要的热能转换设备。
3. 蒸汽涡轮发电机组:蒸汽涡轮发电机组是核能发电系统中的功率转换装置,将蒸汽的动能转化为电能。
它由高速旋转的涡轮驱动发电机,产生电能。
4. 冷却系统:冷却系统用于控制核反应堆的温度,确保其正常运行。
常用的冷却介质包括水和气体。
冷却系统对核能发电系统的安全性和效率起着重要的作用。
三、核能发电系统的性能分析核能发电系统的性能可以从以下几个方面进行分析。
1. 发电效率:核能发电系统具有高效能的优势。
核反应堆产生的热能转化为电能的效率通常在40-45%之间,远高于传统火电厂的效率。
2. 资源利用率:核能是一种可持续的能源形式,核燃料资源富集,并可以高效利用。
核能发电系统能够高度利用核燃料,减少能源的浪费。
3. 环境友好性:相比传统的化石燃料发电,核能发电系统几乎不产生二氧化碳等温室气体,对环境的污染较少。
但是,核能发电系统需要妥善处理核废料,以确保环境的安全。
4. 安全性:核能发电系统的安全性是设计和运营的重中之重。
核反应堆的控制系统、防护屏蔽和事故应急预案等都是确保系统安全的关键。
四、核能发电系统的未来趋势随着能源需求的增长和环境问题的日益突出,核能作为一种清洁的、高效的能源形式,有望在未来得到进一步发展和应用。
以下是一些核能发电系统的未来趋势。
1. 第四代核能发电技术的推广:第四代核能发电技术具有更高的安全性、高效能和资源利用效率,有望在未来得到推广应用。
核电站中的蒸汽发生器原理

核电站中的蒸汽发生器原理核电站是一种利用核能产生电能的设备,其中蒸汽发生器是核电站的重要组成部分之一。
蒸汽发生器在核能转化为电能的过程中起到关键的作用。
本文将探讨核电站中蒸汽发生器的原理和工作机制。
一、蒸汽发生器的定义和作用蒸汽发生器是将核反应堆中释放出的热量转化为蒸汽的装置。
它通过核反应堆内的燃料棒释放的热能,加热循环中的水,使其蒸发为高温高压的蒸汽,从而驱动涡轮发电机组产生电能。
蒸汽发生器在核电站中起到引导热量、提供蒸汽、保护核反应堆的作用。
它将热量从燃料棒传递给循环中的水,使水蒸发为高温高压的蒸汽。
蒸汽发生器的安全性和效率对核电站的运行至关重要。
二、蒸汽发生器的工作原理蒸汽发生器可以分为热交换器和蒸汽发生器两个部分。
热交换器主要负责将核反应堆中的热量转移到蒸汽发生器中的循环水上,蒸汽发生器则将循环水加热并转化为蒸汽。
蒸汽发生器的工作原理是通过核反应堆中的燃料棒释放的热能将主回路内的循环水加热,使其沸腾产生蒸汽。
具体的工作步骤如下:1. 循环水进入蒸汽发生器,通过主回路中的泵进行循环。
主回路中的循环水温度较低,在进入蒸汽发生器之前,循环水首先经过热交换器,与核反应堆中的高温冷却剂进行热交换。
2. 经过热交换器后,循环水的温度升高,进入蒸汽发生器。
蒸汽发生器内部分为两个部分:上部是蒸发器,下部是水冷器。
3. 上部的蒸发器部分与核反应堆的冷却剂直接接触,核反应堆通过传热表面将热量传递给循环水,使其蒸发为蒸汽。
蒸汽通过上部的蒸发器部分上升,进入涡轮发电机组产生电能。
4. 下部的水冷器部分则起到冷却蒸汽的作用。
蒸汽在涡轮中放出部分热量,并冷却为水,然后重新进入核反应堆进行循环。
通过以上的工作原理,蒸汽发生器将核反应堆中的热量高效地转化为蒸汽,驱动涡轮发电机组产生电能。
三、蒸汽发生器的特点及安全性保障蒸汽发生器具有以下几个特点:1. 高热效率:蒸汽发生器能够高效地将核能转化为蒸汽,使核电站的能源利用率更高。
压水堆核电厂蒸汽发生器支承设计及特点

0前言蒸汽发生器是压水堆核电厂关键设备之一,一方面起着将反应堆所产生的热量传递给二次侧工作介质水,使水成为饱和蒸汽从而推动汽轮机发电;另一方面,起着将带放射性的一回路系统与不带放射性的二回路系统隔离的作用。
蒸汽发生器支承用于在各种工况下支承蒸汽发生器,并在反应堆冷却剂系统正常运行主管道热膨胀时允许蒸汽发生器移动,在发生地震或主管道、主蒸汽管道断裂事故时限制蒸汽发生器的位移量,从而防止事故扩大。
因此,蒸汽发生器支承对核电站的安全运行有重大影响。
1蒸汽发生器支承主要结构每台蒸汽发生器支承结构由以下部分组成,包括:垂直支承、下部横向支承、上部横向支承[1],蒸汽发生器支承主要结构如图1所示。
蒸汽发生器垂直支承组件由4条立式支承腿组成。
每条支腿包括上座、叉型座套、支承管、下座等零部件。
下部横向支承组件由6个挡架和4个挡块组成。
上部横向支承由两个半环合扣而成,每个半环的端部都焊有箱形结构,通过联接螺栓将两半环两端的焊接箱连上,从而形成一个整环。
2蒸汽发生器支承设计特点由于压水堆核电厂反应堆冷却剂系统及蒸汽发生器本身的特殊性,蒸汽发生器支承相比普通设备的支承主要有如下几个特点:2.1可动型支承设计在常规电站中,设备间管道的热膨胀都是由管系自身来实现自然补偿,但是在核电站的一回路中,主管道及其有关设备的热膨胀不能借主管道本身来实现自然补偿。
在压水堆核电站中,压力容器中心保持不变,因此要求蒸汽发生器能随着运行状态的变化而移动,以满足主管道及有关设备的热膨胀要求。
这就需要蒸汽发生器支承设计为可动式结构,蒸汽发生器支腿的设计,满足了这种需求。
图1蒸汽发生器支承结构蒸汽发生器的垂直支承由4条立式支承腿组成,各条支腿为3段式结构。
支腿的两端叉型座套内装有向心关节轴承,具有活动性,从而实现蒸汽发生器能随着主管道的膨胀而移动。
2.2横向支承设计蒸汽发生器垂直支承允许蒸汽发生器的热位移。
垂直支承仅仅承受纵向载荷,而无法承受横向载荷,因此蒸汽发生器需设计横向支承。
核电站主蒸汽系统

核电站主蒸汽系统
▪ 正常运行过程中的疏水主要由管道中蒸汽冷凝或蒸 汽的湿度产生。影响系统中形成疏水和各疏水集管 中的疏水量的因素包括以下几项:
• 保温效率 • 系统压降,随着机组的老化而增加 • 汽轮机中的机械和热力性能降低,随着设备的老化
核电站主蒸汽系统
1.2 系统描述
▪ 主蒸汽系统主要由管道、阀门和相关仪表 组成。主蒸汽系统管道和部件主要布置于 汽机房内,包括从蒸汽发生器出口到主汽 阀之间的主蒸汽管道以及与连接到汽轮机 上的主蒸汽管道相连的设备和管道。
核电站主蒸汽系统
主蒸汽系统参数
名称 主蒸汽额定流量 主蒸汽压力/温度 汽机旁路额定流量 MSR壳侧额定流量(冷再热) MSR再热器管侧额定流量 至汽机轴封主蒸汽流量 至VYS的主蒸汽流量 至7号加热器的抽汽量 管道设计压力/温度
核电站主蒸汽系统
1.4 仪表和控制
1)疏水集管液位计
▪ 在主蒸汽和抽汽疏水集管上配备液位测量仪表。对于各 疏水集管,一个水位通道提供输入信号用于控制、报警 和指示。安装在疏水集管上的一只水位变送器提供水位 控制,用于排除来自该疏水集管的凝结水并通过降低汽 机进水的可能性来支持电站运行。各水位变送器的量程 涵盖相关疏水集管正常的水位控制范围。
至6号加热器的抽汽量 管道设计压力/温度
至5号除氧器的抽汽量 管道设计压力/温度
参数 6799t/h 5.38MPa/268.6℃ 2719.6t/h 4510.7t/h 324.5 t/h (一级)/182.7 t/h (二级) 13.4 t/h 待定 390.96 t/h 3.134MPa/238℃ 333.33 t/h 1.847MPa/211℃ 420.859 t/h 核电站主1蒸.0汽6系2M统 Pa
核电站蒸汽发生器的建模及仿真

性能直接影响到整个核电站的安全与经济运行。
本 文采 用集 总参 数 法 建 立 立 式 u 型 管 蒸 汽 发
生器模型 ,在 S A . T R9 0仿真支撑 平 台上构建 其仿
真模 型 。
l 压 水 堆 核 电 站蒸 汽产 生 机 理
在压 水 堆 核 电机 组 中反 应 堆 产 生 的热 量 由一 回路 载热 剂 携 带 通 过 蒸 汽 发 生 器 与 二 回路 循 环 水
G —— 工 质流 量 ;
— —
控 制体 内工质 总质 量 ;
金 属质 量 ;
—
—
c —— 金属 比热 ,本 文建 模 时 假 设其 值 为恒 定值 ;
Q——一 回路传热量 ;
回 路
Q—— 二 回路 吸热量 , 由二 回路 吸热 区
段计 算 获得 ;
— — 一
张 腾 张海 霞 祁 小兵
( 华北 电力大学控制 与计 算机 工程 学院 河北保 定 0 10 ) 7 03
[ 摘要] 针对立式 u型 自然循环蒸汽发 生器进行 建模与仿真研 究。采 用集总参数法,依据均相模
型 的基 本假设 ,给 出了各 个部 分 的数 学模 型 。基 于 S A 一 T R9 0仿 真 支撑 系统得 到 系统 的仿 真 模 型 ,并 进行
实时动 态仿 真 实验 ,验 证 了此 系统模 块化 模 型 的合理 性 。
[ 键词 ] 蒸 汽发 生器 ;核 电 ;仿 真 关 [ 中图分 类号 ] TA8 I [ 献标 识码 ] A 文 机运 转 产 电。其一 、二 回路 流程 图如 图 1 所示 。
引 言
我 国国民经济 的快速发展拉 动了能源需求 的
图 2 蒸 汽 发 生 器分 段 示 意 图
反应堆蒸汽发生器

反应堆蒸汽发生器
反应堆蒸汽发生器(Reactors Steam Generator,RSG)是核电厂中的一种重要设备,它是将核反应堆中产生的热能转化为电能的关键部件之一。
它的主要作用是将反应堆中传递到二次回路的高温高压水蒸汽,通过内外壳之间的热交换器,将其冷却为液态水,再通过泵送回二次回路,形成闭合的热力循环系统。
反应堆蒸汽发生器通常由两个主要部分组成:一个是工作介质水的蒸汽发生器部分,另一个是蒸汽与回路介质之间传热的热交换器部分。
在蒸汽发生器部分,通常使用铜合金、不锈钢等材料制成的U型管将水加热成为高温高压水蒸汽。
在热交换器部分,蒸汽通过管壳式热交换器与二次回路的水进行热交换,将其冷却为液态水。
反应堆蒸汽发生器是核电站中的一个重要组成部分,它的安全性和可靠性对整个核电站的运行稳定性和安全性都具有重要的影响。
在设计和运行中,需要严格遵循相关的技术标准和规范,以确保反应堆蒸汽发生器的安全可靠运行。
核工程中的蒸汽发生器设计与优化

核工程中的蒸汽发生器设计与优化1. 介绍核工程中的蒸汽发生器是核电站的重要组成部分,它负责将核反应堆中产生的热能转化为蒸汽,驱动涡轮发电机组产生电能。
蒸汽发生器的设计与优化对于核电站的安全运行和高效发电具有重要意义。
本文将深入探讨核工程中蒸汽发生器设计与优化的相关内容。
2. 蒸汽发生器原理2.1 蒸汽生成在核反应堆中,燃料棒受到裂变反应产生的高温热能作用,将水冷却剂加热至高温高压状态。
在蒸汽发生器内部,水冷却剂通过管道流动,并通过与管道外壁接触传递热量给水管内流动的水。
由于温度和压力差异,水冷却剂内部形成沿着管道轴向流动的涡旋流,并将热量传递给水管内壁。
2.2 转化为蒸汽在接触到加热后的水管内壁后,液态水开始沿着轴向上升,逐渐转化为蒸汽。
蒸汽随后通过蒸汽发生器顶部的出口离开,进入涡轮发电机组进行进一步的能量转化。
3. 设计原则3.1 安全性蒸汽发生器在设计过程中必须考虑到核电站的安全性。
首先,应该确保设计能够抵御核反应堆事故中可能出现的高温高压等极端条件。
其次,应该考虑到可能出现的泄漏和故障情况,并采取相应措施保护人员和设备安全。
3.2 效率高效发电是核电站运行中的一个重要目标。
在蒸汽发生器设计过程中,需要考虑到热量传递效率、流体流动阻力等因素,并通过合理优化设计来提高能量转化效率。
3.3 维护性蒸汽发生器是核电站中需要经常进行维护和检修的设备之一。
因此,在设计过程中需要考虑到维护人员对设备进行检修和维护时的便捷性,并确保可以快速、安全地进行必要操作。
4. 设计优化方法4.1 流体力学模拟通过使用计算流体力学(CFD)模拟软件,可以对蒸汽发生器内部的流体流动进行模拟和优化。
通过调整管道的尺寸、布局和形状,可以改善热量传递效率和流体流动阻力,从而提高蒸汽发生器的性能。
4.2 材料优化蒸汽发生器内部的材料选择对于其性能和寿命具有重要影响。
通过选择高温、耐压、耐腐蚀等性能优良的材料,可以提高蒸汽发生器的安全性和可靠性。
蒸汽发生器设计

u10 2 1i P 23960 Pa 1 1 2
进口水室 45 度转弯压降:
P2 2
进口水室至传热管束突缩压降:
u10 2 1i 29813Pa 2
u1'2 1i P3 3 5383Pa 2
下降空间流道截面积:
Fd
下降空间单相水流速:
D 4
2
si
Dw0 2 0.6210m2
ud CR D d / Fd 0.7940m / s
直管高度:
H直 L直 / 2n 4.437m
传热管总高度:
Htb H直 Rtb 5.4849m
传热管实际平均长度:
l L总 / n 2S管板 =11.3392m
2.2.5 主要管道内径 由冷却剂流速、蒸汽流速、给水流速的范围和国标设计主管道、蒸汽管道、二 回路给水管内径。 主管道设计内径:
-2-
第一章 绪论
1.1 蒸汽发生器的作用和地位
蒸汽发生器是产生汽轮机所需蒸汽的换热设备。在核反应堆中,核裂变产生的 能量由冷却剂带出,通过蒸汽发生器将热量传递给二回路的给水,使其产生具有一 定压力、一定温度和一定干度的蒸汽。此蒸汽再进入汽轮机做功,转换为电能或机 械能。在能量转换过程中,蒸汽发生器既是一回路设备,又是二回路设备,被称为 一、二回路的枢纽。实际运行经验表明,蒸汽发生器能否安全、可靠地运行,对整 个核动力装置的经济性和安全性有着十分重要的影响。因此各国都把研究与改进蒸 汽发生器当做完善压水堆核电技术的重要环节,并制定了庞大的研究计划,主要包 括蒸汽发生器热工水力分析; 腐蚀理论与传热管材料的研制; 无损探伤技术;振动、 磨损、疲劳研究;改进结构设计,减少腐蚀化学物的浓缩;改进水质控制。
核工程中的主蒸汽发生器设计与优化

核工程中的主蒸汽发生器设计与优化核工程中的主蒸汽发生器设计与优化引言:核工程中的主蒸汽发生器(Main Steam Generator,简称MSG)是核电站的核能转化装置之一,起到将核反应堆中的核能转化为蒸汽能量的作用。
MSG的设计与优化对于核电站的安全和经济运行具有重要的影响,因此研究和探索MSG的设计与优化问题具有重要的意义。
一、主蒸汽发生器的基本原理主蒸汽发生器是核电站中的核能转化装置,它的基本原理是通过核反应堆中的核能转化为热能,进而将热能转化为蒸汽,为汽轮机提供动力。
MSG通常由水冷壳管结构组成,壳侧为冷却剂流动路径,管侧为蒸汽流动路径。
冷却剂从核反应堆中流过,吸收核能并升温,然后进入主蒸汽发生器,通过管子和壳体之间的传热作用,将热量传递给通过管侧流动的次级流体,使其加热为蒸汽。
蒸汽经过减压器后进入汽轮机,驱动汽轮机旋转,最终产生电能。
二、主蒸汽发生器设计的考虑因素1. 安全性:主蒸汽发生器是核电站系统中具有高辐射区域的设备之一,必须保证其结构的完整性和可靠性。
设计时需要考虑各种事故条件下的安全措施,如冷却剂泄漏、管道破裂等情况,确保能安全稳定运行。
2. 蒸汽质量:主蒸汽发生器产生的蒸汽质量对于汽轮机的运行和发电效率具有重要影响。
设计时需要考虑如何最大限度地提高蒸汽的干度,减少湿蒸汽对汽轮机叶片的损伤。
3. 传热效果:主蒸汽发生器的传热效果对于核反应堆的冷却剂温度控制和蒸汽产量有重要影响。
设计时需要考虑壳管传热器的结构和流体参数等因素,使得传热效果最佳。
4. 改进措施:主蒸汽发生器设计的优化还需要考虑如何改进结构和流体参数等因素,以提高蒸汽产量和热效率。
三、主蒸汽发生器设计与优化的方法1. 数值模拟:通过数值模拟的方法,可以对主蒸汽发生器的流体参数和传热性能进行研究和仿真分析。
通过改变管子的布置方式、管子的直径和长度等参数,优化主蒸汽发生器的传热效果。
2. 实验研究:通过在实验室里搭建小型主蒸汽发生器的设备,对不同的设计方案进行实际测试,评估其传热效果和蒸汽质量。
核工程中的蒸汽发生器设计与改进研究
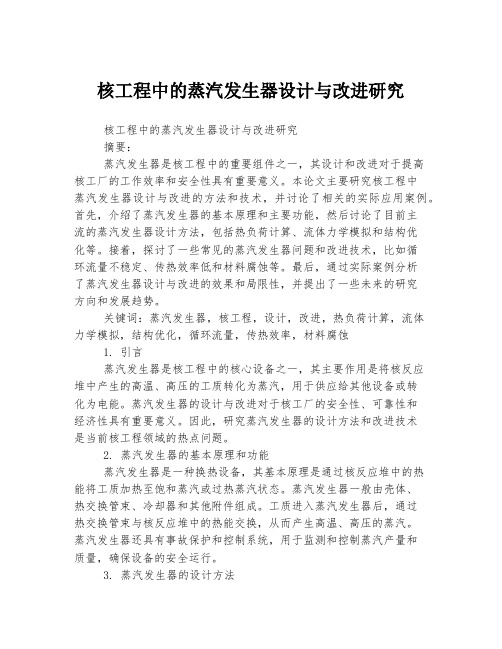
核工程中的蒸汽发生器设计与改进研究核工程中的蒸汽发生器设计与改进研究摘要:蒸汽发生器是核工程中的重要组件之一,其设计和改进对于提高核工厂的工作效率和安全性具有重要意义。
本论文主要研究核工程中蒸汽发生器设计与改进的方法和技术,并讨论了相关的实际应用案例。
首先,介绍了蒸汽发生器的基本原理和主要功能,然后讨论了目前主流的蒸汽发生器设计方法,包括热负荷计算、流体力学模拟和结构优化等。
接着,探讨了一些常见的蒸汽发生器问题和改进技术,比如循环流量不稳定、传热效率低和材料腐蚀等。
最后,通过实际案例分析了蒸汽发生器设计与改进的效果和局限性,并提出了一些未来的研究方向和发展趋势。
关键词:蒸汽发生器,核工程,设计,改进,热负荷计算,流体力学模拟,结构优化,循环流量,传热效率,材料腐蚀1. 引言蒸汽发生器是核工程中的核心设备之一,其主要作用是将核反应堆中产生的高温、高压的工质转化为蒸汽,用于供应给其他设备或转化为电能。
蒸汽发生器的设计与改进对于核工厂的安全性、可靠性和经济性具有重要意义。
因此,研究蒸汽发生器的设计方法和改进技术是当前核工程领域的热点问题。
2. 蒸汽发生器的基本原理和功能蒸汽发生器是一种换热设备,其基本原理是通过核反应堆中的热能将工质加热至饱和蒸汽或过热蒸汽状态。
蒸汽发生器一般由壳体、热交换管束、冷却器和其他附件组成。
工质进入蒸汽发生器后,通过热交换管束与核反应堆中的热能交换,从而产生高温、高压的蒸汽。
蒸汽发生器还具有事故保护和控制系统,用于监测和控制蒸汽产量和质量,确保设备的安全运行。
3. 蒸汽发生器的设计方法蒸汽发生器的设计方法主要包括热负荷计算、流体力学模拟和结构优化等。
热负荷计算是确定蒸汽发生器所需传热面积和结构尺寸的关键步骤,可以通过核反应堆的热功率和工质的流量来计算。
流体力学模拟是使用计算流体动力学(CFD)方法,通过对蒸汽发生器内部流动场的模拟和分析,评估其传热性能和流体动力学性能。
结构优化是通过优化传热管束的布局、增加传热面积和改善流体分布等方式,提高蒸汽发生器的传热效率和工作稳定性。
核工程中的蒸汽发生器设计与优化

核工程中的蒸汽发生器设计与优化蒸汽发生器是核工程中一个非常重要的设备,它在核电站中起到将核能转化为电能的关键作用。
本文将介绍蒸汽发生器的设计原理、优化方法以及一些相关的挑战和问题。
蒸汽发生器的设计原理是基于热交换的原理。
在核电站中,核燃料通过核反应释放的热能被用来加热工质(通常是水)并产生蒸汽。
这个过程通过蒸汽发生器来实现,蒸汽发生器一般由大量的热交换管和壳体组成。
在设计蒸汽发生器时,有几个关键的因素需要考虑。
首先是热交换管的设计。
热交换管通常是由导热性能很好的材料,如不锈钢或铜合金制成。
在设计热交换管时,需要考虑到管内流体和管外流体的传热和流动特性,以及管道的强度和可靠性。
同时,还需要考虑如何提高热交换效率,以增加蒸汽产生的能力。
除了热交换管的设计,蒸汽发生器的壳体也是需要考虑的设计参数之一。
壳体应该具备足够的强度和稳定性,以承受高温和高压环境下的工作条件。
同时,还需要考虑如何优化壳体的换热效率,以提高蒸汽发生器的整体性能。
在蒸汽发生器的设计过程中,还需要考虑其他一些因素,如流体流动的压降、材料的选择、管道的布局等。
这些因素都会对蒸汽发生器的性能产生影响,并需要在设计过程中进行综合考虑和优化。
蒸汽发生器的优化方法可以从多个方面进行。
首先,可以优化热交换管和壳体的结构和材料,以提高传热效率和强度。
其次,可以通过改变流体流动方式和流速,以及改善管道的布局,来减小压降和提高换热效率。
此外,还可以采用先进的流体力学模拟和优化算法,来辅助设计和优化蒸汽发生器。
然而,蒸汽发生器设计和优化中也存在一些挑战和问题。
首先,由于核电站的特殊工作环境,蒸汽发生器需要具备较高的安全性和可靠性。
这就要求在设计和优化过程中考虑到各种可能的事故和故障情况,并采取相应的措施来防范和应对。
其次,蒸汽发生器设计和优化需要综合考虑多个因素,包括热力学特性、流体力学特性、材料力学特性等。
这就需要设计人员具备多学科的知识和技能,并进行综合的分析和优化。
附核电厂蒸汽循环分析

s2 3.138kJ/(kg K)
7.08MPa,
221.3℃
4
h ' 1242.0kJ/k g s ' 3.078kJ/(kg K) h" 2777.8kJ/k g s" 5.848kJ/(kg K)
h4 h ' x(h" h ') 1242.0kJ/kg 0.9956(2777.8 1242.0)kJ/kg 2771.0kJ/kg
一回路冷却剂质量流量
qm1(h1 h2 ) qm3 (h4 h3 ) Q
0
蒸汽发生器的产汽量
qm1(h1 h2 ) qm3 (h4 h3 )
It qm1(ex1 ex2 ) qm3 (ex4 ex3 )
方程
It qm1(ex1 ex2 ) qm3 (ex4 ex3 ) Ex,Q
●
ex ,T
qm1 (ex1
qm3ex4 ex2 )
qm3ex3
3
【例附-1】大亚湾核电厂每环冷却剂的流量为 17550 t/h, 一回路压力为15.5MPa,若冷却剂平均出口温度329.8℃, 平均进口温度290.8℃,蒸汽发生器产生的新蒸汽是压力 6.53MPa,干度为0.9956的湿饱和蒸汽,进入蒸汽发生器 的水压力为7.08MPa,温度为221.3℃蒸汽发生器向环境
附-1
1
一、蒸汽发生器
压水堆核电厂一回路 工作压力在15MPa左右; 冷却剂(压力水)在反应堆的
进口温度位于280℃~300℃,出 口温度即蒸汽发生器进口温度约 310℃~330℃。
大亚湾核电厂: 一回路压力15.5MPa; 冷却剂出口平均温度为329.8℃。
2
取蒸汽发生器为控制体积,稳定运行状态 ●能量方程
AP1000核电厂蒸汽发生器制造难点及质量管理-2019年文档

AP1000核电厂蒸汽发生器制造难点及质量管理-2019年文档一、背景介绍在现代能源产业中,核电是越来越受到关注的一种清洁能源,而AP1000核电站是目前最先进的核电设计之一,蒸汽发生器作为核电站重要的组成部分之一,在制造过程中面临着一系列制造难点和质量管理问题。
本文将探讨AP1000核电厂蒸汽发生器制造难点及质量管理方案。
二、制造难点1.材料选择蒸汽发生器是核电站中一个关键的部件,由于其需要承受高温、高压的蒸汽,因此需要选用高强度、高耐腐蚀的材料。
在AP1000核电站中,采用了A182F316L (22Cr-12Ni-2.5 Mo) 高强不锈钢作为蒸汽发生器管子的主要材料,这一材料的耐腐蚀性和高温强度能够满足高温高压环境下的要求。
2.焊接工艺制造蒸汽发生器时,蒸汽发生器管子之间需要通过焊接技术进行连接,AP1000核电站采用的是TIG合金焊接,该技术在保证焊点质量的同时,也能有效保证焊接过程中不会产生金属杂质和热应力等问题,可以有效降低蒸汽发生器的失效率和事故率。
3.水平定位AP1000核电站中的蒸汽发生器需要进行精确的水平定位,这一过程在制造过程中尤为重要。
影响水平定位的因素包括设备精度、安放位置、土方平整度等因素,保证蒸汽发生器水平位置的正确性,对其后续使用过程的稳定性和耐久性具有重要的影响。
三、质量管理1.制造过程中质量管控在制造蒸汽发生器的过程中,需要进行严格的质量管控,在所有环节都要关注质量的问题,包括存储、加工、焊接等方面。
需要制定相应的质量管控标准和程序,加强质量监督和管理,通过对质量管控的提升,可以有效保证制造蒸汽发生器的质量和稳定性。
2.检测手段核电站蒸汽发生器的制造需要经过多步的检测和测试,以保证其满足高温高压环境下的要求。
在制造过程中需要建立完善的检测机制,包括化学分析、色谱分析、扫描电镜等手段。
这些检测手段可以帮助检测材料的成分、强度等指标,有效保证制造出的蒸汽发生器达到高标准的质量要求。
蒸汽发生器设计

n
G1 1 1700 u1 a
-5-
a---单根传热管流通截面; 1 --一回路水平均比容
2.2.3 传热计算 一回路强迫对流换热系数:
1 0.023
传热管导热热阻:
1
di
R f 0.8 Pr 0.3 38057W / m2 ℃
P7 7
u2 2 2 15961Pa 2
蒸汽发生器一回路侧沿程和局部压降之和:
P Pf Pi 178460Pa
i 1
7
2.3.2 二回路侧阻力计算: 以循环倍率 CR 3 为例计算: 2.3.2.1 下降空间阻力 下降空间流道当量直径:
De Dsi Dw0 0.176m
1000Q C 1251.1m2 q
-6-
2.2.4 管束结构设计 传热管设计根数为 1705 根(除去半圆内的 6 根用黑点表示的拉杆) 。在圆形区 域中有 12 根为拉杆, 传热管和拉杆中心均位于图中小正方形的顶点上。 排管见 [附 录 4 程序 2][附录 4 程序 3] 半圆上每一排的根数(包括拉杆) : 67、67、67、67、67、67、67、65、65、65、63、63、61、61、61、59、57、 57、55、53、51、51、49、47、43、41、39、35、33、27、23、17、1
Re
u1' di
11
979120
u '1 —考虑堵管后的流速,通常为 1.05 u1
1 —平均壁温下的动力粘度
根据雷诺数选择紊流光滑管的尼古拉兹公式:
0.0032 0.221Re0.237 0.0117
沿程压降:
压水堆核电厂蒸汽发生器支承设计及特点

S c 科 i e n c e & 技 T e c h 视 n o l o g y 界 V i  ̄ o n
Hale Waihona Puke 压水堆核 电厂蒸汽发生器支承设计及特点
汤 臣杭
( 中 国核 动 力研 究设计 院 , 四川 成都 6 1 0 0 4 1 )
【 摘 要】 本文描 述了压 水堆核 电厂蒸汽发生器支承的结构 , 并对蒸汽发生 器支承的结构及 其设计特 点进行 了分析 。蒸汽发生器 支承具有
可动性设计、 横 向支承设计 、 间隙调整设计等特点。蒸汽发生器支承这种设计特点能够在各种工况下为蒸汽发 生器提供有效 支承。
【 关键词】 压水堆核 电厂 ; 蒸汽发 生器支承 ; 设计特点 0 前 言
蒸汽发生器是压水堆核 电厂关键设备之一 . 一方面起着将反应堆 所产生的热量传递给二次侧工作介质水 . 使水成为饱和蒸汽从而推动 汽轮机发 电: 另一方 面 . 起着将带放射性 的一 回路系统与不 带放射性 的二 回路系统隔离的作用 蒸汽发生器支承用于在各种工况下支承蒸 汽发生器 . 并在反应堆冷却剂 系统正 常运行主管道热膨胀时允许蒸汽 发生器移动 。 在 发生地震或主管道 、 主蒸 汽管道断裂事故 时限制蒸汽 发生器的位移量 . 从而防止事 故扩大 因此 . 蒸汽发 生器支 承对核 电站 的安全运行有重大影响
1 蒸 汽 发 生 器 支 承 主 要 结构
每 台蒸汽发生器支承结构由以下部分组成 。 包括 : 垂直支承 、 下部 横 向支承 、 上部横向支承I ” . 蒸汽发生器支承 主要结构如 图 1 所示 。蒸 汽发生器垂直支承组件 由 4 条立式 支承腿组成 。每条支腿包括上座 、 叉型座套 、 支承管 、 下座等零部件。下部横 向支承组件 由 6 个挡架 和 4 个挡块组成 。上部横向支承由两个 半环合扣而成 , 每个半环 的端部都 焊有 箱形结 构 . 通过联接螺栓将两半 环两端的焊接箱 连上 . 从而形 成 个整环
核电站中的蒸汽发生器是如何工作的

核电站中的蒸汽发生器是如何工作的核电站中的蒸汽发生器是核电站的重要组成部分,它起着将核能转化为电能的关键作用。
本文将介绍核电站中蒸汽发生器的工作原理及其工作过程。
一、蒸汽发生器的功能及组成蒸汽发生器是核电站中的重要设备,其主要功能是将核能转化为蒸汽能,进而驱动涡轮发电机产生电能。
蒸汽发生器通常由管束、壳体、管板、进出口以及流体分布装置等组件组成。
二、核能转化为蒸汽能的过程核电站利用核裂变反应释放出的热能将水加热,产生高温高压蒸汽,而蒸汽发生器就是负责将高温高压的反应堆冷却剂(主要是水)中的热能转化为蒸汽能的设备。
核电站中的蒸汽发生器主要通过核反应堆中的燃料棒来产生热能,并将此热能传递给通过管束内的水,使水加热并转化为蒸汽。
三、蒸汽发生器的工作原理蒸汽发生器的工作原理是通过将冷却剂(水)从一侧的进口引入管束,然后由反应堆中的燃料棒释放出的热能将冷却剂加热,转化为蒸汽。
蒸汽在管束中形成,然后通过蒸汽发生器的出口进入进一步的能量转换系统。
四、蒸汽发生器的工作过程1. 冷却剂进入管束:冷却剂从反应堆中通过管束的进口进入蒸汽发生器;2. 加热过程:在管束中,冷却剂与燃料棒内的热能发生热交换,冷却剂被加热,燃料棒释放出的热能将冷却剂加热转化为蒸汽;3. 分离过程:热能转化为蒸汽后,蒸汽与冷却剂分离,蒸汽被送往进一步的能量转换系统,冷却剂则返回反应堆进行循环;4. 蒸汽利用:送往进一步的能量转换系统的蒸汽,驱动涡轮发电机产生电能。
五、蒸汽发生器的优势和挑战1. 优势:a. 高效能转换:蒸汽发生器能够高效地将核能转换为蒸汽能,实现能源的有效利用;b. 稳定可靠:蒸汽发生器采用复杂的结构和安全系统,能够稳定可靠地工作;c. 环保节能:核能转化为蒸汽能的过程无二氧化碳等有害气体的排放,对环境友好。
2. 挑战:a. 安全风险:核电站核反应堆和蒸汽发生器的高温高压工作环境带来潜在的安全风险,需要高度重视安全措施;b. 废弃物处理:蒸汽发生器的运行会产生一定量的放射性废弃物,需要进行安全处理和储存。
蒸汽发生器讲解材料

➢ 给水流量过大
如果SGS的主给水调节阀(V250)由于设备或控制问题
出现故障或操纵员误操作,将导致给水过量。高液位报警
提醒操纵员液位正在上升。如果事件继续发展下去,主给
蒸汽发生器
概述
• 蒸汽发生器系统是核电站一、二回路的枢 纽,它的主要作用是将一回路冷却剂中的 热量传递给二回路给水,使之产生蒸汽来 驱动汽轮发电机组发 也是一回路压力边界的一部分,用于防止 放射性物质外泄。故在正常运行时,二回 路不受一回路放射性冷却剂的污染,是不 带放射性的。
甩负荷瞬态而动作;如果蒸汽排放系统不可用,主蒸汽安全阀 保护开启防止MSS超压。 ➢ 主蒸汽安全阀(V030~V035)失效 AP1000技术规格书与ASME规范的限制是一致的,允许在一些 主蒸汽安全阀不可用时降低功率运行。功率水平限制与每个蒸 汽发生器退出运行的安全阀数量的对应关系如下表。在施工设 计期间已经决定了最终的最大允许功率。
➢ 启动给水调节阀(V255)故障 启动给水泵出口设有文丘利管,在主蒸汽管线破裂SG压 力降低时限制给水流量,以限制事故后的 安全壳压力和 温度。
(2)与蒸汽系统有关的异常运行
➢ 汽轮机误停机 汽轮机停机,通过蒸汽排放阀(V038)和PORV进行排 汽。如果蒸汽排放系统可用,可以避免主蒸汽安全阀因
(2)非安全相关超压保护
SGS设置非安全相关的PORV,PORV为二次侧超压保护 提供纵深防御并防止安全阀(V030~V035)开启。
➢ 对于蒸汽管线小破口事件,首先,操纵员隔离与 破裂蒸汽管线相关的蒸汽发生器的给水。这样减 少了RCS的冷却,防止非能动安全系统动作。如 果操纵员不采取有效的行动,RCS温度继续降低, SGS接收到保护系统信号自动隔离两个蒸汽发生器的 主给水及启动给水。衰变热将由自动触发的非能动安 全系统排出。蒸汽管线小破口事件可以通过MSIV区 域的温度报警和破口区域的安全壳参数变化进行监测。
秦山核电站蒸汽发生器系统

一、作用及设计考虑蒸汽发生器(SG)的主要作用是将一回路中水的热量传给二回路的水,使其汽化。
由于一回路水流经堆芯而带有放射性,因而蒸汽发生器与压力容器和一回路管道共同构成防止放射性外溢的第二道屏障。
在压水堆核电厂正常运行时,二回路应不受到一回路水的污染,是不具有放射性的。
压水堆核电厂蒸汽发生器是按自然循环原理运行的(图1-13)。
在这类蒸汽发生器中,保证流体的原动力是冷水柱和热水柱之间的密度差,产生的蒸汽是饱和蒸汽。
每一台饱和式蒸汽发生器按照满负荷运行时传递三分之一的反应堆热功率设计。
二、设备描述压水堆核电厂的蒸汽发生器由带有内置式汽水分离设备的立式筒体和倒置式U形管束组成,如图14。
一回路的每一个环路有一台蒸汽发生器,它是垂直布置的、自然循环的管式汽化装置。
整个装置可分为:1.给水蒸发段蒸汽发生器蒸发段的下部是由倒置的4640根倒U形管束构成。
一回路水在管内流动,二回路水在管外汽化。
这些管子焊接在585mm厚的锰-钼-镍(Mn-Mo-Ni)管板上,管板和管束承受一回路压力。
一回路水侧封头是由铸钢半球形封头构成的,在其内表面覆盖了不锈钢层,并通过焊在管板上的因科镍隔板分成两个水室(入口水室、出口水室)。
每个水室都有一个连到一回路的接管和人孔。
图 1-13 自然循环原理整个汽化装置安置在圆筒状的金属筒体内,筒体下部与管板衔接,其上部通过一个中间过渡锥体而与一个包含干燥装置的更大的金属筒体相连。
给水的入口位于该筒体的上部。
给水分配由一个环形孔管完成。
给水与干燥设备排出的水相混合,然后在由下部筒体与包围管束的圆柱形薄钢板包壳所形成的环形空间内向下流动。
在包壳下部与管板上表面之间有一个空间,在这里水加热到接近饱和温度,然后进入到管束中间,向上流动。
借助于蒸汽发生器U形管束的隔板来保持管束的间距,而在隔板之间又通过拉杆固定。
在8个抗震隔板上开有一些孔以让管子及水--蒸汽混合物通过。
此外,隔板通过一些防止管束整体振动的楔子固定在管束围板上。
- 1、下载文档前请自行甄别文档内容的完整性,平台不提供额外的编辑、内容补充、找答案等附加服务。
- 2、"仅部分预览"的文档,不可在线预览部分如存在完整性等问题,可反馈申请退款(可完整预览的文档不适用该条件!)。
- 3、如文档侵犯您的权益,请联系客服反馈,我们会尽快为您处理(人工客服工作时间:9:00-18:30)。
蒸汽发生器设计说明书时间:2012年12月2日目录第一章绪论............................................................................................................... 第二章蒸汽发生器的设计与计算...............................................................................2.1 根据热平衡确定换热量....................................................................................2.2 管径的选取以及传热管数目的确定................................................................2.3 换热面积的计算................................................................................................2.4 管束结构的计算................................................................................................2.5 强度计算............................................................................................................2.6 主要管道内径的计算........................................................................................2.7 一回路水阻力计算............................................................................................2.8 二回路水循环阻力计算....................................................................................2.9 运动压头计算....................................................................................................2.10 循环倍率的确定................................................................................................ 第三章结论与评价.......................................................................................................附录1 蒸汽发生器热力计算表附录2 蒸汽发生器水力计算表附录3 蒸汽发生器强度计算表第一章绪论蒸汽发生器是产生汽轮机所需蒸汽的换热设备。
在核反应堆中,核裂变产生的能量由冷却剂带出,通过蒸汽发生器将热量传递给二回路工质,使其产生具有一定温度一定压力和一定干度的蒸汽。
此蒸汽再进入汽轮机中做功,转换为电能或机械能。
在这个能量转换过程中,蒸汽发生器既是一回路的设备,又是二回路的设备,所以被称为一、二回路的枢纽。
蒸汽发生器作为一回路主设备,主要功能有:1、将一回路冷却剂的热量通过传热管传递给二回路给水,加热给水至沸腾,经过汽水分离后产生驱动汽轮机的干饱和蒸汽;2、作为一回路压力边界,承受一回路压力,并与一回路其他压力边界共同构成防止放射性裂变产物溢出的第三道安全屏障;3、在预期运行事件、设计基准事故工况以及过度工况下保证反应堆装置的可靠运行。
实际运行经验表明,蒸汽发生器能否安全、可靠的运行,对整个核动力装置的经济性和安全可靠性有着十分重要的影响。
据压水堆核电厂事故统计显示,蒸汽发生器在核电厂事故中居重要地位。
一些蒸汽发生器的可靠性是比较低的,它对核电厂的安全性、可靠性和经济效益有重大影响。
因此,各国都把研究与改进蒸汽发生器当做完善压水堆核电厂技术的重要环节,并制定了庞大的科研计划,主要包括蒸汽发生器热工水力分析;腐蚀理论与传热管材料的研制;无损探伤技术;振动、磨损、疲劳研究;改进结构设计,减少腐蚀化学物的浓缩;改进水质控制等。
第二章 蒸汽发生器的设计与计算蒸汽发生器的设计计算包括热力计算、水动力计算、强度计算、结构设计等。
热力学计算主要通过传热学知识计算传热管传热面积,然后与管束结构设计相结合可以得到传热管长度、管束直径等结构参数。
强度计算通过压力校验等用于选取蒸汽发生器结构材料、确定结构尺寸等。
蒸汽发生器中要通过强度计算得出的参数有传热管、上下筒体、球形下封头管板等的壁厚。
在强度计算得出参数后要留取一定余量,以满足变工况下出现超压情况的需求。
水动力计算是最后一步,因为只有结构尺寸确定,运动状态已知的情况下水力情况才得以确定。
水力计算包括一回路水阻力计算、二回路水循环阻力计算、运动压头计算等。
其中一回路水阻力计算相对简单主要包括单相水U 型管管内摩擦阻力和局部阻力两项;二回路水循环阻力计算及运动压头计算比较复杂。
因为蒸汽发生器内二回路侧流体的水力特性取决于流体工质的性质和状态、流道的结构和几何形态,以及工质的流动形式。
而且计算过程误差较大,往往需要在试验中进一步修正。
二回路水循环阻力包括下降空间阻力、上升空间阻力、汽水分离器阻力等。
而上升空间阻力又包括摩擦阻力、局部阻力、弯管区阻力、加速阻力、流量分配孔阻力五项。
设计中常用图解法来确定循环倍率,即先假设几个不同的循环倍率分别计算其运动压头和总阻力,在直角坐标系作出相应曲线,两根曲线交点即为稳定工况的循环倍率值。
循环倍率值一般取2~5为宜,其值过小会导致传热恶化,腐蚀加剧等;而过大则会增大汽水分离器负荷,使蒸汽干度降低,危机汽轮机安全。
计算过程中水力计算是在结构选型和热力计算之后进行,但是结构设计和热力计算又需要水力计算数据,因此三者往往要反复交替进行,以使设计逐步完善。
2.1根据热平衡确定换热量一回路进口焓值:'1i =1394.21 kj/kg (15.0MPa ,310℃);一回路出口焓值:''1i =1284.45 kj/kg (15.0MPa ,290℃);二回路给水焓:f i =944.38 kj/kg (5.0MPa ,220℃);二回路饱和水温:s t =263.94 ℃ (5.0MPa );二回路饱和水焓:s i =1154.50kj/kg (5.0MPa );二回路饱和蒸汽焓值:''s i =2794.23kj/kg (5.0MPa );二回路汽化潜热: r=''s i -s i =2794.23-1154.50=1639.73kj/kg (5.0MPa );排污量:s D C D s d /kg 26.1126*01.0==•=;干度:X=0.99;换热量:79.231279))((Q =-++=f s d i i D D DrX ;一回路水流量: s g i i Q G /k 43.2128)'''(*111=-=η;η=0.99为蒸汽发生器的热效率。
2.2 管径的选取以及传热管数目的确定选取传热管的外径为:d o =22mm ;节距选取为:t=1.4 d o =30.8mm ;则最小节圆半径为:min 261.6R t mm == ;负公差修正系数:ϕ=1.102; 弯曲减薄系数:min1 1.0824o R d R ϕ=+=; 传热管壁厚:,111,1 1.34200[]0.8设设ϕφσ==+oR P d S mm P ,此处取1 1.5=S mm ;传热管内径:1219=-=i o d d S mm ; 单管流通面积:2253.28341a mm d i ==π; 选取一回路侧水流速度为:s m u /5.51=; 一回路水平均比容:kg m /0013783.0v 31=(15.0MPa ,300℃,不饱和水) 则一回路侧流通面积为:2115534.0m u v G A ==U 型管数目为:188210*53.2835534.06===-a A n 根据排管最后确定U 型管数目为:1886 2.3 换热面积的计算一回路侧水导热系数:10.5614/(℃)λ=⋅W m (15.0MPa ,300℃,不饱和水) 一回路侧水普朗特数:Pr 0.8616=f (15.0MPa ,300℃,不饱和水)一回路侧水动力粘度:-518.83310kg/m s η=⨯ (15.0MPa ,300℃,不饱和水) 一回路侧雷诺数:5111105835.8Re ⨯==v d u i f η 一回路侧换热系数:295.35754Pr Re 023.04.08.011==f f i d λα传热管导热系数:17.4/(℃)w W m λ=⋅ (给定) 传热管壁热阻:52ln 9.2710/2℃λ-==⨯⋅o o w w id d R m W d 污垢热阻:522.610/℃-=⨯⋅f R m W (按I-600选定)传热温差: C t t t t t C t t t C t t t s s ︒︒︒=∆∆∆-∆=∆=-''=∆=-'=∆12.35ln 06.2606.46min maxmin max ln 1min 1max在计算传热系数k 、热负荷q 和二回路侧放热系数α2时假设k 值,进行了循环迭代。
其中:In t k q ∆=*7.015.02557.0q p =α f w i i R R d d k +++=2011*1αα得:2222W/m ;W/m ;m 27662.75W/187592.08=⋅5341.46=⋅=︒︒q C k C α。
所需的传热面积:2ln89.1232m t k Q F =∆⋅=传热裕度系数:C=1.1设计传热面积:218.1356C F m F =⋅=设 2.4 管束结构的计算传热管总长:m 07.19622d F L 0==π设总传热管排列方式:按正方形排列;最小U 型管节圆直径:m 1232.0t 4D ==节实际布管数:n=1886根管束直径:m 3408.2D tb =弯管段高为:m 1704.1R H max ==弯 平均直径:()m 232.1D D 21D tb =+=节 弯管总长:m 83.3649n D 5.0=⋅=π弯L直管总长:m 24.15972L L L =-=弯总直 管束直段高:m 2344.4n2L H ==直直 管束总高:m 4048.5H H H tb =+=弯直2.5 强度计算(1)衬筒内径:m D t tb wi 3708.22D =+=δ其中δt 是装配间隙,约10~20mm ,取15mm 。