精馏节能技术研究
化工精馏节能技术探讨

一
加, 且受到 第一级 加热 蒸气压力及末级冷 却介质种类 的限制, 操作 愈发 困难 , 一般 由单效改为 双效可节 能5 O %, 双效 到三效 n 增加 1 7 %, 三效 到四效 仅增加 了8 %, 可见, 多效精 馏后几效所产生的节 能效果 不断下 降, 因此 工业上一般 采用双效精 馏, 其工艺流程 按加热 蒸气和物料 的流 向不同, 分为平流 、 顺流和逆流 三种。
递 增的N 个 精馏塔 中, N 个 塔 的操 作温 度也依 次递增 。 压 力和温 度较 高 塔 的塔顶 蒸汽向较低塔 的塔 釜再 沸器供热 , 同时 自 身也被冷凝 , 以此 类 推, 这样就 节省了低压塔再 沸器的能耗 和高压塔 冷凝器的水 耗。 在这个 系统 中, 只需 向第一 个最高压 力塔 供热 , 系统 即可进行工作 , 所需 能 量 约为单塔能 耗的1 / N, 如将三个 塔 串在一起采 用三效精馏 技术 , 其能 耗
Ke ywo r d s :Ch e mi c a l ,d i s t i l l a t i o n,e n e r g y s a v i n g
仅用原来的 1 / 3 , 节能幅度达  ̄ U 6 7 %, 节 能效果非 常明显。 多效精 馏 由于 随着化 工技术 的迅猛 发展, 化工技术 的进 步在化 工生产过程 中, 分 效 数增加 , 加 热蒸气用量减少, 能耗 降低 , 但效数越 多, 设 备投资费用增
工精馏 节能问题 进行讨论。
【 关键 词 l 化工节能; 精馏技术
Abs t r a c t :t he pr o c e s s o f t he m od e r n c he mi c a l i ndu s t r y
应 放在最 后分离。 简单精 馏流程 采用热 集成 技术 比无热 集成 的可 节约 操作费用5 0 %, 可见塔系热集成技 术对于分离过 程能耗 的影 响往往比单 个塔 的优化更显著 , 这是挖 掘精馏 系统 节能潜 力极大 的一种措施 , 因而 成 为节能研究者 的热点对象 。
浅析化工精馏高效节能技术开发及应用
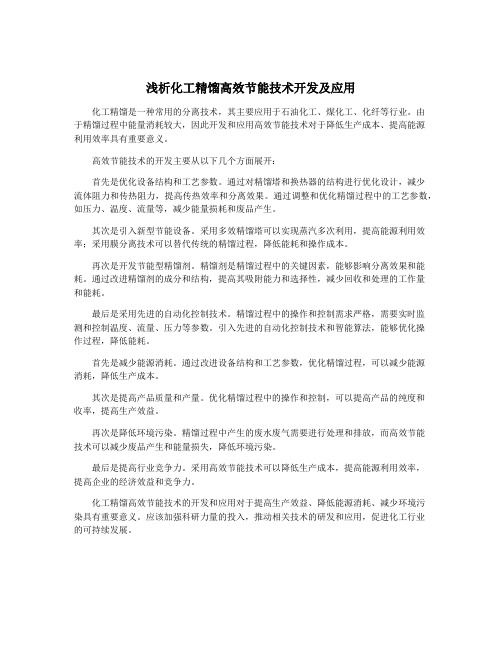
浅析化工精馏高效节能技术开发及应用化工精馏是一种常用的分离技术,其主要应用于石油化工、煤化工、化纤等行业。
由于精馏过程中能量消耗较大,因此开发和应用高效节能技术对于降低生产成本、提高能源利用效率具有重要意义。
高效节能技术的开发主要从以下几个方面展开:首先是优化设备结构和工艺参数。
通过对精馏塔和换热器的结构进行优化设计,减少流体阻力和传热阻力,提高传热效率和分离效果。
通过调整和优化精馏过程中的工艺参数,如压力、温度、流量等,减少能量损耗和废品产生。
其次是引入新型节能设备。
采用多效精馏塔可以实现蒸汽多次利用,提高能源利用效率;采用膜分离技术可以替代传统的精馏过程,降低能耗和操作成本。
再次是开发节能型精馏剂。
精馏剂是精馏过程中的关键因素,能够影响分离效果和能耗。
通过改进精馏剂的成分和结构,提高其吸附能力和选择性,减少回收和处理的工作量和能耗。
最后是采用先进的自动化控制技术。
精馏过程中的操作和控制需求严格,需要实时监测和控制温度、流量、压力等参数。
引入先进的自动化控制技术和智能算法,能够优化操作过程,降低能耗。
首先是减少能源消耗。
通过改进设备结构和工艺参数,优化精馏过程,可以减少能源消耗,降低生产成本。
其次是提高产品质量和产量。
优化精馏过程中的操作和控制,可以提高产品的纯度和收率,提高生产效益。
再次是降低环境污染。
精馏过程中产生的废水废气需要进行处理和排放,而高效节能技术可以减少废品产生和能量损失,降低环境污染。
最后是提高行业竞争力。
采用高效节能技术可以降低生产成本,提高能源利用效率,提高企业的经济效益和竞争力。
化工精馏高效节能技术的开发和应用对于提高生产效益、降低能源消耗、减少环境污染具有重要意义。
应该加强科研力量的投入,推动相关技术的研发和应用,促进化工行业的可持续发展。
精馏过程节能技术综述

精馏过程节能技术综述现代工业生产过程中,精馏过程是十分常见的一种操作,用于从混合物中分离出不同组分。
然而,传统的精馏过程存在能源浪费的问题,因为它需要大量的能源来进行加热和冷却。
因此,如何降低精馏过程的能源消耗成为了一个重要的研究方向。
在过去的几十年里,研究人员提出了多种节能技术,以下综述了一些常见的节能技术。
首先,改进传统精馏塔的设计是一种简单但有效的节能方法。
例如,使用多级精馏塔可以增加分馏塔的效率,减少需加热和冷却的动力。
此外,增加塔内的换热面积也可以改善能量利用率。
此外,通过使用先进的塔内填料和分布器,可以提高物质的传质效率,从而减少所需的塔高和物料回流比例。
其次,热力耦合是另一种常用的节能技术。
该技术通过将不同温度的流体进行热交换,来降低能源消耗。
例如,实施热力耦合可以将进出精馏塔的气体进行热交换,从而降低所需的加热和冷却负荷。
此外,热力耦合还可以用于塔内热交换,例如通过使用塔内回流来预热进入精馏塔的物料。
另外,采用较低的工艺温度和压力也可以有效地减少精馏过程的能耗。
降低工艺温度可以减少所需的加热负荷,而降低工艺压力可以减少所需的冷却负荷。
因此,在设计和操作精馏过程时,应考虑选取较低的工艺温度和压力,以降低能源消耗。
此外,使用较低的辅助能源,如太阳能、余热等,也是一种常用的节能技术。
太阳能可以用于提供所需的加热或冷却能量,从而降低对传统能源的依赖。
余热是指在其他工艺过程中产生的废热,在精馏过程中可以被回收利用,用于提供所需的加热或冷却能源,进一步减少能源消耗。
最后,引入新的分离技术也是提高精馏过程能耗效率的一种途径。
例如,膜分离技术被广泛应用于分离混合物中的气体或液体组分,并且其能耗通常较低。
相比传统的蒸馏过程,膜分离技术不需要额外的加热和冷却能源,因此能够有效地节约能源。
总的来说,精馏过程节能技术的研究和应用对能源的合理利用具有重要意义。
通过改进传统精馏塔的设计、热力耦合、降低工艺温度和压力、使用低辅助能源和引入新的分离技术等方法,可以有效地降低精馏过程的能耗。
精馏过程的节能降耗

精馏过程的节能降耗精馏过程在化工产业中是一项重要的分离技术,但是它也是能耗较高的过程。
为了降低能耗,节能降耗已经成为精馏技术的一个重要研究方向。
本文将介绍几种精馏过程的节能降耗技术。
首先,提高精馏塔的热效率是提高精馏过程的一个关键。
一种常见的做法是引入换热器网络来最大程度地利用出塔冷凝液和进塔蒸汽之间的热量传递。
这种方法可以降低所需的蒸汽量,从而降低了能耗。
此外,还可以使用多效精馏、热泵或采用废热回收技术进一步提高热效率。
其次,提高精馏过程的物质效率也是节能降耗的一个重要途径。
物质效率是指在精馏过程中使用的干燥剂或者吸附剂能够更有效地去除杂质,从而减少能耗。
通过改进精馏塔的操作条件,如温度、压力和液体流速等参数,可以提高物质效率。
同时,使用高效的精馏填料或者塔板也能够提高分离效果,减少杂质的含量。
此外,使用先进的辅助技术可以进一步降低精馏过程的能耗。
例如,在精馏过程中引入膜分离技术可以减少能源消耗。
膜分离技术是一种基于材料表面或孔隙的选择性渗透性原理分离混合物的方法。
与传统的溶剂萃取或者蒸馏技术相比,膜分离技术具有能耗低、操作简单、体积小等优点。
通过将膜分离技术与精馏过程相结合,可以实现更高效的分离效果。
最后,优化精馏过程的操作策略也是节能降耗的一个重要途径。
通过优化参数设定和控制策略,可以使精馏过程更加稳定和高效。
例如,采用先进的控制算法,如模型预测控制或者模糊控制算法,可以实现对精馏过程的快速响应和精确控制,从而降低了能耗和运行成本。
总的来说,精馏过程的节能降耗是一个涉及多个方面的工程问题。
通过提高热效率、物质效率,使用先进的辅助技术和优化操作策略,可以有效地降低精馏过程的能耗。
这些节能降耗技术不仅可以减少环境污染,还可以提高精馏过程的经济效益。
因此,精馏过程的节能降耗在工业应用中具有重要的意义。
精馏过程的节能降耗

精馏过程的节能降耗摘要:精馏过程的节能,对于减少能源消耗,降低生产成本和保护环境具有十份重要的意义。
在精馏过程中可以采用最适宜回流比操作和最佳进料状态,使用中间冷凝器和中间再沸器,多效精馏技术、热泵精馏技术。
合理安排多组分物料分离流程,提高过程的分离效率、提高物料回收率,进而降低能耗。
并介绍我国精馏过程的节能现状与趋势。
关键词:精馏过程;节能;回流比;降耗,0前言在化工生产过程中,分离是非常重要的一个过程单元,它直接决定了最终产品的质量和收率,工业生产中占据着主导地位的分离方法就是精馏。
精馏是利用混合物中各组分挥发度的不同利用能量进行分离的操作单元,具有独特的优势。
据估计,化工过程中40%~70%的能耗用于分离,而精馏能耗又占其中的95%。
因此随着世界能源的日益短缺,精馏过程一直是研究者节能挖潜的热点对象,它的每一个进展都会带来巨大的经济效益。
多年来,人们已采用了多种方法和手段对精馏过程进行节能降耗的研究,按照流程是否改变及是否利用过程技术可以将其分为三类:1)利用过程技术对精馏塔的操作条件进行优化,以减少精馏塔所消耗的能量,如以产品物流预热进料、增加塔板数、减小回流比、增设中间再沸器和中间冷凝器等;2)开发了许多高效节能的特殊精馏工艺流程,如热泵精馏、多效精馏等。
1.1最适宜回流比和最佳进料状态[1]回流比直接影响再沸器和冷凝器的热负荷,决定精馏分离的净功耗,因此大体上确定了操作费用,同时还与塔设备的投资密切相关。
在最小回流比Rmin附近,随R的增长,操作线与平衡线间的距离增大,达到规定分离要求所需的塔板数减少,使得设备费用下降。
如果进一步增加回流比,在塔板数减少的同时,塔中蒸汽流率和换热器热负荷的增大,造成塔径、再沸器和冷凝器传热面积增大,使设备费用增加。
因此,应当根据总费用最小原则来选取适宜回流比。
进料状态(用加料状态参数q表示)的不同,将造成塔中精馏段和提馏段气液相流率的变化,从而影响R,以及达到规定分离要求所需的理论板数和再沸器和冷凝器的热负荷。
精馏节能技术
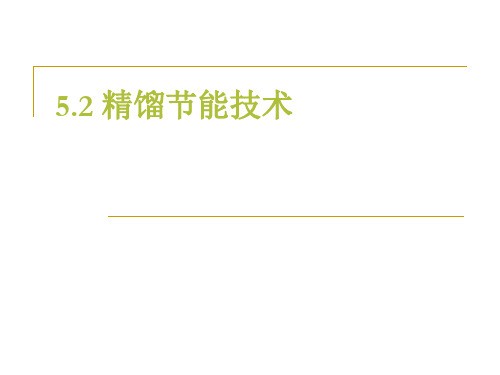
(3) 中间冷凝器和中间再沸器
如能在塔中部设置中间冷凝器,就可以采用较高温度 如能在塔中部设置中间冷凝器, 的冷却剂。 的冷却剂。 如在塔中部设置中间再沸器,对于高温塔, 如在塔中部设置中间再沸器,对于高温塔,可应用较 低温位的加热剂。 低温位的加热剂。 对于精馏,使操作线向平衡线靠拢,提高塔内分离过 对于精馏,使操作线向平衡线靠拢, 程的可逆程度。 程的可逆程度。 在生产过程中必须要由适当温位的加热剂或( 在生产过程中必须要由适当温位的加热剂或(和)冷 却剂与其相配,并需有足够大的热负荷值得利用, 却剂与其相配,并需有足够大的热负荷值得利用,再 加上塔顶和塔底的温度差要相当大, 加上塔顶和塔底的温度差要相当大,如此才会取得经 济效益。 济效益。
(5) 热泵精馏
将温度较低的塔顶蒸汽经压缩后作为塔底再沸器的热源, 将温度较低的塔顶蒸汽经压缩后作为塔底再沸器的热源, 称为热泵精馏。 称为热泵精馏。 三种典型的热泵精馏流程:使用另外的工作流体, 三种典型的热泵精馏流程:使用另外的工作流体,塔顶 蒸汽再压缩,再沸器液体闪蒸。 蒸汽再压缩,再沸器液体闪蒸。 热泵精馏是消耗一定量的机械功来提高低温蒸汽的能位 而加以利用的。因此消耗单位机械能能回收的热量是一 而加以利用的。因此消耗单位机械能能回收的热量是一 消耗单位机械能能回收的热量 项重要经济指标,称为性能系数,常记为 项重要经济指标,称为性能系数,常记为C.O.P.。 。 显然, 显然,对于沸点差小的混合物分离的精馏塔应用热泵精 馏效果会更好。 馏效果会更好。5Fra bibliotek2 精馏节能技术
精馏节能技术

热泵精馏工艺分析化工行业是能耗大户,其中精馏又是能耗极高的单元操作,而传统的精馏方式热力学效率很低,能量浪费很大。
如何降低精馏塔的能耗,充分利用低温热源,已成为人们普遍关注的问题。
对此人们提出了许多节能措施,通过大量的理论分析、实验研究以及工业应用表明其中节能效果比较显著的是热泵精馏技术。
热泵精馏是把精馏塔塔顶蒸汽加压升温,使其用作塔底再沸器的热源,回收塔顶蒸汽的冷凝潜热。
热泵精馏在下述场合应用,有望取得良好效果:(1)塔顶和塔底温差较小,因为压缩机的功耗主要取决于温差,温差越大,压缩机的功耗越大。
据国外文献报导,只要塔顶和塔底温差小于36°C,就可以获得较好的经济效果。
(2)沸点相近组分的分离,按常规方法,蒸馏塔需要较多的塔盘及较大的回流比,才能得到合格的产品,而且加热用的蒸汽或冷却用的循环水都比较多。
若采用热泵技术一般可取得较明显的经济效益。
(3)工厂蒸汽供应不足或价格偏高,有必要减少蒸汽用量或取消再沸器时。
(4)冷却水不足或者冷却水温偏高、价格偏贵,需要采用制冷技术或其他方法解决冷却问题时。
(5)—般蒸馏塔塔顶温度在38〜138C之间,如果用热泵流程对缩短投资回收期有利就可以采用,但是如果有较便宜的低压蒸汽和冷却介质来源,用热泵流程就不一定有利。
(6)蒸馏塔底再沸器温度在300C以上,采用热泵流程往往是不合适的。
以上只是对一般情况而言,对于某个具体工艺过程,还要进行全面的经济技术评定之后才能确定。
根据热泵所消耗的外界能量不同,热泵精馏可分为蒸汽加压方式和吸收式两种类型1.蒸汽加压方式蒸汽加压方式热泵精馏有两种:蒸汽压缩机方式和蒸汽喷射式。
1.1蒸汽压缩机方式蒸汽压缩机方式又可分为间接式、塔顶气体直接压缩式、分割式和塔釜液体闪蒸再沸式流程。
1.1.1间接式当塔顶气体具有腐蚀性或塔顶气体为热敏性产品或塔顶产品不宜压缩时,可以采用间接式热泵精馏,见图1。
图1间接式热泵精馏流程图它主要由精馏塔、压缩机、蒸发器、冷凝器及节流阀等组成。
化工精馏技术的应用及节能研究

化工精馏技术的应用及节能研究摘要:化工行业应积极开展节能减排工作,优化改革化工生产过程,达到降耗节能的目的,同时减少对生态环境的污染与破坏。
化工行业的发展,为人们生产生活带来了便利,但也带来了环境污染和能源浪费问题。
因此,实现化工行业可持续发展,必须采取节能减排措施,优化化工生产过程,降低能耗和污染。
化工生产过程分离与反应两个过程,其中分离过程所造成的能源消耗量占据整体能源消耗量的75%。
这是化工生产中能源浪费的主要原因,因此,降低分离过程的能耗是化工行业节能减排的一个重要方向。
关键词:化工;精馏;节能技术;应用1化工精馏分析化工蒸馏技术是将不同性质的物料放入蒸馏塔装置中,通过塔板装置实现传质传热,在塔板中进行汽化分离。
传统的蒸馏技术虽然可以实现物料的分离,但是会造成大量的蒸汽损耗,导致能源浪费。
为了实现节能降耗,化工精馏技术应运而生。
化工精馏技术能够合理利用多余热量,实现能源的有效利用。
但是,化工精馏技术受到许多因素的影响,如回流比例、环境温度、塔内压力、物料量等,需要注重控制。
如果这些因素不能得到有效的控制,将会导致化工精馏技术的效率降低,甚至出现质量问题。
传统的化工精馏需要大量能源物质加热蒸馏塔底部结构,且存在热量损耗与能源浪费现象。
因此,需要创新研发高效应用化工精馏节能降耗技术。
这样不仅可以降低能源消耗,减少对环境的影响,还可以提高生产效率,降低生产成本,推动化工行业的可持续发展。
化工精馏技术是化工行业中的重要技术之一,它的应用能够实现物料的分离和能源的节约。
在未来的发展中,化工精馏技术需要不断创新,应用高效节能降耗技术,实现更加可持续的发展。
2化工精馏高效节能技术开发及应用的现实意义2.1有助于提高化工精馏过程的效率与质量化工精馏在许多工业领域中都扮演着重要的角色,它能够将混合物质分离出不同的组分,达到纯净度的要求。
然而,精馏蒸馏塔的多流程串联运行特点使得化工精馏过程中的能量损耗现象比较严重。
精馏过程的节能降耗
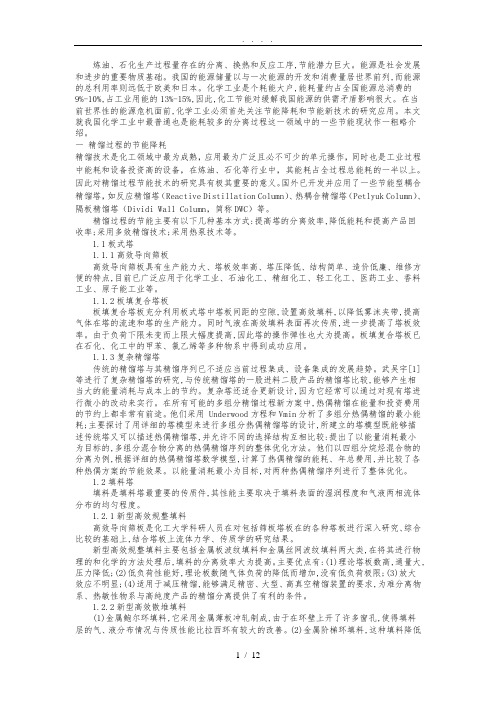
炼油、石化生产过程量存在的分离、换热和反应工序,节能潜力巨大。
能源是社会发展和进步的重要物质基础。
我国的能源储量以与一次能源的开发和消费量居世界前列,而能源的总利用率则远低于欧美和日本。
化学工业是个耗能大户,能耗量约占全国能源总消费的9%-10%,占工业用能的13%-15%,因此,化工节能对缓解我国能源的供需矛盾影响很大。
在当前世界性的能源危机面前,化学工业必须首先关注节能降耗和节能新技术的研究应用。
本文就我国化学工业中最普通也是能耗较多的分离过程这一领域中的一些节能现状作一粗略介绍。
一精馏过程的节能降耗精馏技术是化工领域中最为成熟,应用最为广泛且必不可少的单元操作,同时也是工业过程中能耗和设备投资高的设备,在炼油、石化等行业中,其能耗占全过程总能耗的一半以上。
因此对精馏过程节能技术的研究具有极其重要的意义。
国外已开发并应用了一些节能型耦合精馏塔,如反应精馏塔(Reactive Distillation Column)、热耦合精馏塔(Petlyuk Column)、隔板精馏塔(Dividi Wall Column,简称DWC)等。
精馏过程的节能主要有以下几种基本方式:提高塔的分离效率,降低能耗和提高产品回收率;采用多效精馏技术;采用热泵技术等。
1.1板式塔1.1.1高效导向筛板高效导向筛板具有生产能力大、塔板效率高、塔压降低、结构简单、造价低廉、维修方便的特点,目前已广泛应用于化学工业、石油化工、精细化工、轻工化工、医药工业、香料工业、原子能工业等。
1.1.2板填复合塔板板填复合塔板充分利用板式塔中塔板间距的空隙,设置高效填料,以降低雾沫夹带,提高气体在塔的流速和塔的生产能力。
同时气液在高效填料表面再次传质,进一步提高了塔板效率。
由于负荷下限未变而上限大幅度提高,因此塔的操作弹性也大为提高。
板填复合塔板已在石化、化工中的甲苯、氯乙烯等多种物系中得到成功应用。
1.1.3复杂精馏塔传统的精馏塔与其精馏序列已不适应当前过程集成、设备集成的发展趋势。
精馏节能减耗总结

精馏节能减耗总结引言在许多化学工艺中,精馏作为一种常见的分离技术,广泛应用于石油化工、化学制药、能源等行业。
然而,传统的精馏过程存在能源消耗大的问题。
为了减少精馏过程中的能源消耗,提高能源利用率,许多节能减耗技术被引入并逐渐得到应用。
本文将对精馏节能减耗的相关技术进行总结,包括辅助加热装置、改进的精馏塔结构以及新型精馏塔填料等。
通过这些节能减耗技术的应用,精馏过程的能耗问题可以得到一定程度的改善,从而实现能源的可持续利用。
辅助加热装置传统的精馏过程中,常常需要大量的蒸汽或热能来提供塔底部的加热需求。
为了减少能源的消耗,引入一些辅助加热装置可以起到节能降耗的效果。
多效加热器多效加热器是一种高效的辅助加热装置,能够通过热传递的方式将高温废热回收利用。
其原理是在精馏塔的塔顶和塔底之间设置多级的加热器,利用顶部产生的低温蒸汽将底部的高温液体加热,从而实现能量的再利用。
热泵热泵是另一种常用的辅助加热装置,通过将低温的热能转移到高温区域,从而实现能量的传递和利用。
在精馏过程中,可以利用热泵将废热转化为可用的热能,供给精馏塔的加热需求。
这样不仅可以减少能源的消耗,还可以达到能源利用的最大化。
改进的精馏塔结构传统的精馏塔结构存在一些不利于能源节约的问题,如传质效率低、压力损失大等。
通过改进精馏塔的结构,可以减少能源的消耗,提高精馏效率。
塔板结构优化传统的精馏塔中,常见的结构是塔板结构,它的主要问题是传质效率低。
为了提高传质效率,可以引入一些新的塔板结构,如泡沫塔板、视窗塔板等。
这些新型塔板结构具有更大的表面积和更好的传质性能,能够有效地提高精馏效率,降低能源消耗。
塔内增加填料层除了改进塔板结构,也可以在精馏塔内部增加填料层,以增加界面面积,提高传质效果。
常见的填料包括金属填料、陶瓷填料、塑料填料等。
这些填料具有较大的表面积和较好的传质性能,能够增加相接触的机会,从而提高传质效率,减少能源消耗。
新型精馏塔填料塔填料作为精馏过程中的重要组成部分,对其传质效率和能源消耗有着直接的影响。
精馏的节能技术

精馏作为化工、石化、医药、食 品、冶金等行业生产过程的重要单元 操作,其能耗约占化工生产的40%-70 %。
故采取措施降低蒸馏过程中的能 耗日益重要,成为研究的重点所在。
二、精馏节能技术介绍
精馏过程净功消耗的降低:
要使精馏过程的净功消耗降低,可以降低流体流动 过程产生的压力降,减小传热过程的温度差,减小传 质过程的两相浓度与平衡浓度的差别。
对于减压操作的塔, 纸然进一步降低操 作压力可减少回流比, 但减压下塔板效率降 低,节能效果不一定显著, 必须慎垂对待。
3、热能的充分利用
(1)热交换系统
精馏系统是由塔体和热交换器组成。在 再沸器、冷凝器、进料顶热器和成晶冷却 器系统中, 热交换器最佳化是节能的重要 环节, 因为它决定了热能是否得到充分利 用的问题。
(2)多效精馏系统
多效精馏系统是由 若干压力不同的精馏塔 构成,而且依据压力高 低的顺序,相邻两个塔 的高压塔塔顶蒸汽作用 为低压塔再沸器的热源, 换言之,高压塔塔顶蒸 汽的冷凝潜热均被精馏 系统自身回收利用,使 热能得到充分有效地利 用。
图4顺流和逆流三效工艺流程图
采用两效或多效精馏是充分利用能级 的一个方法。不论采用哪种方式,其精馏 操作所需的热量与单塔精馏相比较,都可 以减少30~40%。
选择最优操作压力,是 精馏系统节能的一项有力措 施。事实证明,在一定分离 精度要求下,对某些物系降 低精馏分离塔的操作压力, 可增加被分离各组分的相对 挥发度,从而减少回流比, 降低塔釜温度,尤以沸点相 近的物系,其节能效果更为 显著。
图3操作压力对气液 平衡的影响
脱甲烷塔在5~6kg/cm2压力下操作与 30~35kg/cm2压力下操作相比,回流比可下降 1/9~1/10,一个40万吨的乙烯装置,即可节 约压缩功率3600千瓦,而且投资也可减少。
精馏过程的节能优化探讨

过程 中, 大致需要如 下设备: ① 精馏塔 ; ② 冷凝器 : ③ 再沸器 ; ④ 回流罐 ; ⑤
回流泵。
石油化工行业中的精馏装置大多采取的是连续运行的方式 , 塔顶液 体 回流和塔底上升蒸汽气流是精馏过程 连续进 行的必 要条件 连续精馏的具 体操作流程如下: 操作时, 原料液连续 加入精馏塔 内。 连 续的从 再沸器 中取 出部分液体作为塔底产品 ( 称 为 釜 残 液) ; 部 分液体被汽化 , 产 生 上 升 蒸气 , 次通过各层塔板 。塔顶蒸气进入冷凝器被 全部冷凝 , 将部分冷 凝液 用泵 ( 或借助于重力作用) 送回塔顶作为回流液体 ( 回流是精馏与普通 精馏 的本 质 区别 ) , 其余部分作为塔顶产品 ( 称 为 馏 出 液) 采出。 般情况下 。 将原料液加入的那层塔板称为进料板 。在进料板 以上的
许多 。 ② 选 取 最 佳 进 料 状 态 加料热 状态的不 同, 会 影 响 最 小 回流 比、 达 到 规 定 分 离 要 求 所 需 的 理 论板数 以及再沸器和冷凝器的热负荷 高温 精馏 ( 塔顶 、 釜温度高于的溶液送到精馏 装置 中, 使之不 断进行部
1精 馏 的原 理 和 流 程
的净功效, 因此, 基本确定了操作费用。另一方面, 回 流 比的 大 小 还 与 塔 设
备的投 资密切相关 : 在 R 附近 , R增 大, 达到 规定分离要求所 需的塔板 数 明显减少, 设备费 下降; 在较高 R处, R增大 , 塔径、 再沸器和冷凝 器的传 热 面积增大 , 设备 费又会增大 。一般情况 下, 适 宜回流比取为最小 回流比 的1 . 2 - 1 _ 3倍 , 这 时 的总 费用 相 比于 R m 会 增加 2 %~ 6 %, 但 操 作 弹 性 却 增 大
科技成果——自回热精馏节能新技术
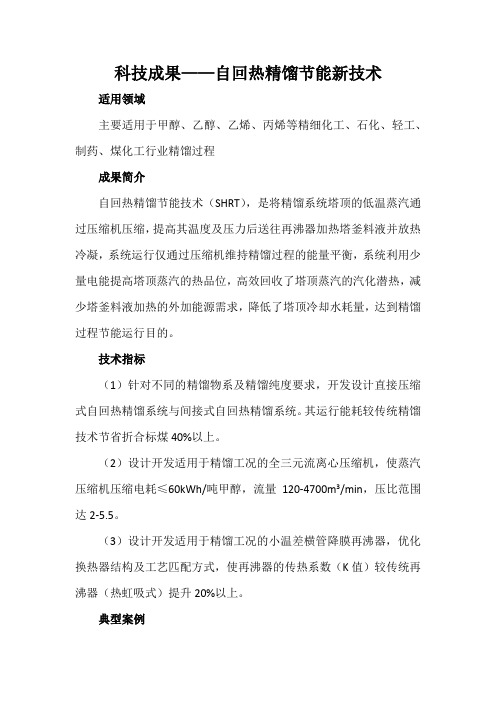
科技成果——自回热精馏节能新技术适用领域
主要适用于甲醇、乙醇、乙烯、丙烯等精细化工、石化、轻工、制药、煤化工行业精馏过程
成果简介
自回热精馏节能技术(SHRT),是将精馏系统塔顶的低温蒸汽通过压缩机压缩,提高其温度及压力后送往再沸器加热塔釜料液并放热冷凝,系统运行仅通过压缩机维持精馏过程的能量平衡,系统利用少量电能提高塔顶蒸汽的热品位,高效回收了塔顶蒸汽的汽化潜热,减少塔釜料液加热的外加能源需求,降低了塔顶冷却水耗量,达到精馏过程节能运行目的。
技术指标
(1)针对不同的精馏物系及精馏纯度要求,开发设计直接压缩式自回热精馏系统与间接式自回热精馏系统。
其运行能耗较传统精馏技术节省折合标煤40%以上。
(2)设计开发适用于精馏工况的全三元流离心压缩机,使蒸汽压缩机压缩电耗≤60kWh/吨甲醇,流量120-4700m3/min,压比范围达2-5.5。
(3)设计开发适用于精馏工况的小温差横管降膜再沸器,优化换热器结构及工艺匹配方式,使再沸器的传热系数(K值)较传统再沸器(热虹吸式)提升20%以上。
典型案例
应用单位:江苏泰利达新材料有限公司
7.3m3/h乙醇自回热精馏节能改造项目,采用直接压缩式SHRT 技术,系统采用高效双螺杆压缩机及横管降膜式再沸器,物料经预热后进入精馏塔,塔顶蒸汽进入压缩机,压缩后的塔顶蒸汽进入再沸器对塔底物料进行加热,塔顶蒸汽冷凝液与物料换热后排出。
本项目已稳定运行近1年时间,总投资约350万元,系统改造后的能源消耗为蒸汽0.95t/h,耗电218kW,循环水量5m3/h。
年节能收益约216万元。
化工精馏高效节能技术的开发及应用
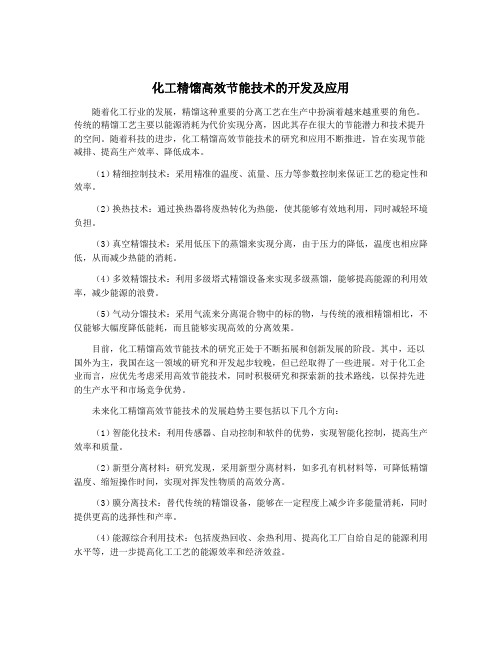
化工精馏高效节能技术的开发及应用随着化工行业的发展,精馏这种重要的分离工艺在生产中扮演着越来越重要的角色。
传统的精馏工艺主要以能源消耗为代价实现分离,因此其存在很大的节能潜力和技术提升的空间。
随着科技的进步,化工精馏高效节能技术的研究和应用不断推进,旨在实现节能减排、提高生产效率、降低成本。
(1)精细控制技术:采用精准的温度、流量、压力等参数控制来保证工艺的稳定性和效率。
(2)换热技术:通过换热器将废热转化为热能,使其能够有效地利用,同时减轻环境负担。
(3)真空精馏技术:采用低压下的蒸馏来实现分离,由于压力的降低,温度也相应降低,从而减少热能的消耗。
(4)多效精馏技术:利用多级塔式精馏设备来实现多级蒸馏,能够提高能源的利用效率,减少能源的浪费。
(5)气动分馏技术:采用气流来分离混合物中的标的物,与传统的液相精馏相比,不仅能够大幅度降低能耗,而且能够实现高效的分离效果。
目前,化工精馏高效节能技术的研究正处于不断拓展和创新发展的阶段。
其中,还以国外为主,我国在这一领域的研究和开发起步较晚,但已经取得了一些进展。
对于化工企业而言,应优先考虑采用高效节能技术,同时积极研究和探索新的技术路线,以保持先进的生产水平和市场竞争优势。
未来化工精馏高效节能技术的发展趋势主要包括以下几个方向:(1)智能化技术:利用传感器、自动控制和软件的优势,实现智能化控制,提高生产效率和质量。
(2)新型分离材料:研究发现,采用新型分离材料,如多孔有机材料等,可降低精馏温度、缩短操作时间,实现对挥发性物质的高效分离。
(3)膜分离技术:替代传统的精馏设备,能够在一定程度上减少许多能量消耗,同时提供更高的选择性和产率。
(4)能源综合利用技术:包括废热回收、余热利用、提高化工厂自给自足的能源利用水平等,进一步提高化工工艺的能源效率和经济效益。
总的来说,化工精馏高效节能技术的研究与应用是化工行业发展的重要方向之一。
持续不断的技术创新,将为化工企业带来更加可持续、高效、环境友好的生产模式,也是应对未来一系列环境和经济压力的必要手段之一。
精馏塔控制和节能优化研究综述

精馏塔控制和节能优化研究综述摘要:精馏过程是一个复杂的传质传热过程,表现为过程变量多,被控变量多,可操纵的变量也多,过程动态和机理复杂。
作为化工生产中应用最广的分离过程,精馏也是耗能较大的一种化工单元操作。
但在实际生产中,为了保证产品合格,精馏装置操作往往偏于保守,操作方法以及操作参数设置往往欠合理,过分离普遍存在。
精馏过程消耗的能量绝大部分并非用于组分分离,而是被冷却水或分离组分带走。
因此,精馏过程的节能潜力很大,收效也极为明显。
本文简单介绍了精馏原理,针对精馏塔控制和节能优化展开了深入的研究分析,结合本次研究,发表了一些自己的建议看法,希望可以对精馏塔控制以及节能优化起到一定的参考和帮助,提高精馏塔控制和节能优化有效性。
关键词:精馏塔;控制;节能优化前言:通过对精馏塔的研究过程中发现,在精馏的过程中,会消耗较多的能源,热力学的效率也会出现很大程度的降低,因此,对于化工行业来说,当前困扰着我国化工行业很多专家的一个难题。
在一般的情况下,精馏塔的设计会很大程度上的影响着资源的消耗情况,好的精馏塔结构将为化工省下大量资源,有效提高行业经济效益,降低精馏成本,由此可见,对精馏塔的研究和分析具有非常积极的意义。
1、精馏原理介绍精馏操作属于化工生产行业中较为常见的处理流程之一,其需要将混合物体内部液体部分、气体部分进行接触操作,使相关物质在固定条件下进行反应。
常规状态中,物质会在逆向流动、全面接触前提下逐渐开始反应流程,使液相内部轻组分快速进入气相内部,气相完成重组分操作,最终进入液相内部。
精馏本质属于传质活动,会导致热量不断传导,最终达成反应目标。
在压力恒定环境下,独立组分液体沸腾会持续产生加热效果,但温度却始终维持原有状态。
多组分液体会同样会在沸腾阶段持续加热,但温度会发生对应变化。
恒定压力会使溶液气相平衡与组分存在产生相对联系,组分沸腾温度点越高、浓度级别越高、平衡状态所需温度级别也会越高。
因此,相对于物质气液相平衡状态,溶液气液进入平衡具有独特表现,即气相、液相平衡浓度存在差异。
精馏的节能技术

精馏过程的节能技术摘要:精馏是化工、石化、医药等过程的重要单元操作,本文主要讨论精馏过程的节能。
从精馏过程热能的充分利用;提高蒸馏系统的分离效率,提高产品回收率来实现降低能耗;减少蒸馏过程对能量的需要和加强管理等几个方面,详细论述了精馏过程的节能技术。
关键词:精馏;节能1、前言在工业生产中,石油化学工业的能耗所占比例最大,而石油化学工业中能耗最大者为分离操作,其中又以精馏的能耗居首位。
精馏过程是一个复杂的传质传热过程,表现为:过程变量多,被控变量多,可操纵的变量也多;过程动态和机理复杂”.首先,随着石油化工的迅速发展,精馏操作的应用越来越广,分离物料的组分不断增多,分离的产品纯度要求亦不断提高,但人们同时又不希望消耗过多的能量,这就对精馏过程的控制提出了要求。
其次,作为化工生产中应用最广的分离过程,精馏也是耗能较大的一种化工单元操作.在实际生产中,为了保证产品合格,精馏装置操作往往偏于保守,操作方法以及操作参数设置往往欠合理。
另外,由于精馏过程消耗的能量绝大部分并非用于组分分离,而是被冷却水或分离组分带走.因此,精馏过程的节能潜力很大,合理利用精馏过程本身的热能,就能降低整个过程对能量的需求,减少能量的浪费,使节能收效也极为明显.据统计,在美国精馏过程的能耗占全国能耗的3%,如果从中节约10%,每年可节省5亿美元。
我国的炼油厂消耗的原油占其炼油量的8%~10%,其中很大一部分消耗于精馏过程.因此,在当今能源紧缺的情况下,对精馏过程的节能研究就显得十分重要.例如,美国巴特尔斯公司在波多黎各某芳烃装置的8个精馏塔上进行节能优化操作,每年可节约310万美元。
蒸馏过程的节能基本上可从以下几个方面着手:(1)精馏过程热能的充分利用;(2)提高蒸馏系统的分离效率,提高产品回收率来实现降低能耗;(3)减少蒸馏过程对能量的需要;(4)加强管理。
2、蒸馏过程热能的充分利用2。
1加强保温保冷以改进热的利用在精馏过程中使用的主要设备为精馏塔和换热器,另外还有各种管道,这些设备多为金属制成,对热的传导较为容易,加之环境温度的影响,若对其采取保温保冷的措施,可以大大降低设备与环境之间的热传递作用,从而达到节约热能的目的.强化再沸器和冷凝器中的传热可使传热温差下降,由于传热温差减小还可使塔顶冷却剂温度提高,塔釜的加热温度下降。
精馏节能技术 (1)

1 精馏过程节能原理
从能量的本质看, 精馏过程是将物理有效能转
化为扩散有效能, 同时伴随物理有效能的降价
损失。精馏过程有效能损失是由下列过程的不
可逆性引起的。一是流体流动的压降; 二是相
浓度不平衡物流间的传质或不同浓度物流间的
混合; 三是不同温度物流间的传热或不同温度
物流间的混合。
2 精馏节能的措施
济效益。
(4) 多效精馏
多效精馏原理类似于多效蒸发,即利用若干压力不同
的精馏塔,按压力高低顺序给与组合,使相邻两塔之
间将高压塔顶的蒸汽作为低压塔底的再沸器的预热介 质。从而使该分离系统能耗下降。
双效精馏需要由两座塔,并且有不同的操作压力,低
压塔的再沸器与高压塔的冷凝器耦合成一台换热器,
以高压塔顶蒸汽去加热蒸发低压塔塔底的物料。
馏段中的回流量自上而下逐步增加,提馏段中
上升蒸汽量则自下而上逐步增加。对于沸点相
近混合物精馏,所需的低温冷却剂显著降低。
3 其他节能措施
(1)选择最佳进料状态,以降低再沸器负荷 (2)选择正确的进料板位置,以避有时把单塔分为双塔, 各处理一半,对于节约能耗有利
多效精馏虽然可以节省大量能耗,但需增加设备投资, 且因两塔之间的热偶合,要求更高级的控制系统。
(5) 热泵精馏
将温度较低的塔顶蒸汽经压缩后作为塔底再沸器的热源,
称为热泵精馏。
三种典型的热泵精馏流程:使用另外的工作流体,塔顶 蒸汽再压缩,再沸器液体闪蒸。
热泵精馏是消耗一定量的机械功来提高低温蒸汽的能位
分离过程所需最小功是由原料和产物的组成、 温度和压力所决定的。要提高热力学效率只能 采取措施降低过程的净功消耗,使过程尽量接 近可逆过程。 精馏过程热力学不可逆性主要由以下原因引起: (1) 通过一定压力梯度的动量传递; (2) 通过一定温度梯度的热量传递或不同温度 物流的直接混合; (3) 通过一定浓度梯度的质量传递或者不同化 学位物流的直接混合。
双效精馏节能技术研究进展

馏 节能 的影 响 因素 , 主要 讨论 了塔 的操 作压 力 , 进
料 分配 比和 回流 比对精馏 节 能 的影 响 。高维 平[ 。 等系统 研究 了 4种 多效 精 馏 流 程 的 特点 , 建 立 节
能型精 馏流 程优 化 模 拟机 分 析 系 统 , 并 将 模 拟优
第 1 期
代 文阳 , 等. 双 效 精 馏 节 能 技 术 研 究进 展
・ 5 5 ・
器, 实 现热 集成 , 达 到节 能 目的 _ 】 ] 。按 照进 料方 向与操 作压 力梯 度 方 向是 否 一 致 , 双 效 精 馏 可 分 为 三类 : 双 效并 流 ( 分流进料) , 双效 顺 流 ( 高 压 塔 进料) 和双效 逆 流 ( 低 压塔 进料 ) _ 1 4 ] 。
l a z o g l u  ̄ 。 ] 在 1 9 8 9年建 立 了高 纯 度 双 效 精 馏 塔 的
动态 模 型来 研 究 环 干扰 以及 多 环 P I 控 制 器 上模
: 2 o 1 2 一 l O 一 1 8
1 双效精馏 的类型 与发展
双效 精馏 主要是 利用 2个精 馏 塔的操 作压力
世界上 约 9 5 互 溶液 体 混 合 物 的 分 离 都 是 用精 馏操作 的 。精馏 又是 耗 能 较 高 的单 元 操 作 ¨ 1 ] , 在 产 品生产 成本 中 占有 较 大 的 比重 , 降低 生 产 过 程 中的能耗 是 降低产 品生产 成本 提高 竞争 能力 的关
键 之一 。
中图分类号 : T Q0 2 8 . 1 3
文献标识码 : A
文章编号 : 1 0 0 8 — 0 5 1 1 ( 2 0 1 3 ) 0 1 — 0 0 5 4 — 0 4
乙醇热泵精馏的节能特性与热力学研究

乙醇热泵精馏的节能特性与热力学研究乙醇热泵精馏的节能特性与热力学研究一、引言随着全球能源危机的加剧以及环境保护意识的提高,节能成为了当下社会关注的焦点之一。
在化工工业中,乙醇的生产和精馏是能耗较高的过程之一。
因此,研究乙醇热泵精馏的节能特性和热力学行为具有重要的意义。
本文旨在通过热力学分析,探讨乙醇热泵精馏的节能特性,并提出相关的优化建议。
二、热泵精馏技术的简介热泵精馏技术是一种能耗较低的分离技术,通过使用热泵工作介质的高温废热来提供蒸馏塔的外加热,减少传统精馏过程中对蒸汽的需求。
由于乙醇精馏过程中蒸发潜热较大,因此应用热泵技术进行乙醇精馏具有很大的潜力。
三、乙醇热泵精馏的节能特性乙醇热泵精馏相较于传统的乙醇精馏具有明显的节能优势。
首先,通过使用热泵工作介质的高温废热来提供蒸馏塔的外加热,可以减少对蒸汽的需求,从而降低了能耗。
其次,热泵技术能够利用回收的废热对进料进行预热,提高了塔顶温度,增强了馏分的分离效果,进一步提高了能耗效率。
另外,热泵技术还可以降低精馏塔的工作压力,减少蒸汽的产生,从而减少了与锅炉相关的运行费用。
四、乙醇热泵精馏的热力学研究对乙醇热泵精馏的热力学行为进行研究可以优化热泵设备的设计和操作。
首先,需要确定适宜的工作介质。
乙醇热泵精馏的工作介质应具备较高的汽化潜热和较低的饱和蒸汽压力,以保证充分利用高温废热和提高节能效果。
其次,需要调查系统的热力学特性,如热力学参数、平衡曲线等,以便优化精馏塔的位置、塔板数等参数。
最后,研究乙醇与工作介质的相互作用,了解在乙醇和工作介质间的传热和传质机理,进一步提高热泵精馏的效果。
五、乙醇热泵精馏的优化建议基于热泵精馏的节能特性和热力学研究,可以提出一些优化建议。
首先,选择适合乙醇热泵精馏的工作介质,如氨、甲醛等,以实现更好的节能效果。
其次,通过优化精馏塔的设计和操作,如增加塔板数、调整回流比等,提高精馏的分离效率。
最后,结合热泵技术和其他节能技术,如余热回收等,进一步提高整个生产流程的能耗效率。
- 1、下载文档前请自行甄别文档内容的完整性,平台不提供额外的编辑、内容补充、找答案等附加服务。
- 2、"仅部分预览"的文档,不可在线预览部分如存在完整性等问题,可反馈申请退款(可完整预览的文档不适用该条件!)。
- 3、如文档侵犯您的权益,请联系客服反馈,我们会尽快为您处理(人工客服工作时间:9:00-18:30)。
精馏过程中的节能技术综述能源短缺问题引起了各国的关注,同时我国工信部节能与综合利用部门负责人表示:“十二五期间,国家节能减排的指标将分解到企业头上。
”“十二五”约束性指标的分配对象将由地方政府转向行业和企业。
由此可知,节能减排的工作必须在各行各业中引起足够的重视,企业应采取实际措施努力降低能耗。
化工行业能耗高,节能减排工作的任务尤为艰巨。
分离是化工生产中非常重要的一个过程单元,它直接决定了最终产品的质量和收率,而占据着主导地位的分离方法就是精馏。
精馏通过加热液体混合物建立两相体系,利用溶液中各组分挥发度的差异实现组分的分离或提纯目的的操作单元。
精馏作为化工、石化、医药、食品、冶金等行业生产过程的重要单元操作,其能耗约占化工生产的40%-70%,故采取措施降低蒸馏过程中的能耗日益重要,成为研究的重点所在。
精馏过程节能的基本途径在于如何减少有效能得损失,从热量供应方面我们可以从热节减方面(降低向再沸器提供的能量)和热回收方面(热能的综合利用)着手进行改进,此外优化控制操作参数、减少操作裕量以及提高塔的分离效率也可降低精馏过程中的能耗[1]。
此外,按照流程是否改变及是否利用过程技术可以将其分为三类:①利用过程技术对精馏塔的操作条件进行优化,以减少精馏塔所消耗的能量,如以产品物流预热进料、增加塔板数、减小回流比、增设中间再沸器和中间冷凝器等;②开发高效节能的特殊精馏工艺流程,如热泵精馏、热偶精馏、多效精馏等;③改进精馏塔的保温材料和开发高效的塔板类型和填料。
一、高效节能的精馏技术——热泵技术热泵精馏是依据热力学第二定律,给系统加入一定的机械功,将温度较低的塔顶蒸汽加压升温,作为高温塔釜的热源。
因为回收的潜热用于过程本身,又省去了塔顶冷凝器、冷却水和塔釜加热蒸汽,可使精馏的能耗明显降低。
根据热泵所消耗的外界能量不同,热泵精馏可分为蒸汽压缩式和蒸汽喷射式两种类型。
①蒸汽压缩式热泵精馏蒸汽压缩式热泵精馏[2]又可以分为塔顶气体直接压缩式热泵精馏和单独工质循环式两种类型,如图1和图2所示。
图1,气体直接压缩式热泵精馏的原理是塔顶气体经压缩机压缩升温后进入塔底再沸器,冷凝放热使釜液再沸,冷凝液经节流阀减压后,一部分作为产品出料,另一部分作为精馏塔顶的回流。
过程特点是:(1)所需的载热介质是现成的;(2)因为只需要一个热交换器(即再沸器),压缩机的压缩比通常低于单独工质循环式的压缩比;(3)系统简单,稳定可靠。
图2,单独工质循环式热泵技术精馏,通常用于塔顶气体具有腐蚀性或塔顶气体为热敏性产品或塔顶产品不宜压缩的情况。
该过程的原理为:用单独封闭循环的工质工作。
高压气态工质在凝汽器(即精馏塔的再沸器)中冷凝放热后经节流阀减压降温,人塔顶蒸发器(即精馏塔的凝汽器)中吸热蒸发,形成低压气态工质返回压缩机压缩,进行再循环。
特点为:(1)塔中要分离的产品与工质完全隔离;(2)可使用标准精馏系统,易于设计和控制;(3)与塔顶气体直接压缩式相比较,多一个热交换器(即蒸发器),压缩机需要克服较高的温差和压力差,因此,其效率较低。
分析两种热泵技术,核心的思想在于降低向再沸器提供热量,充分利用过程中的塔顶热蒸汽中蕴含的热量,提高了整个过程的有效能效率。
②蒸汽喷射泵方式减压精馏在该流程中,塔顶蒸汽是稍含低沸点组成的水蒸汽,其一部分用蒸汽喷射泵加压升温,随驱动蒸汽一起进人塔底作为加热蒸汽。
具有如下优点:(1)新增设备只有蒸汽喷射泵,设备费低;(2)蒸汽喷射泵没有转动部件,容易维修,而且维修费低。
适合应用在:(1)精馏塔塔底和塔顶的压差不大;(2)减压精馏的真空度比较低的情况。
热泵精馏,除了开工阶段以外,可基本上不向再沸器提供另外的热能,节能效果十分显著,但要增加热泵系统的设备费,综合考虑一般一两年内可用节省下的费用收回增加的投资。
二、多效精馏多效精馏[3]采用压力依次降低的若干精馏塔串联操作,前一精馏塔的塔顶蒸汽作为下一精馏塔的再沸器的加热介质。
整个过程中,除了两端精馏塔外,中间精馏装置可以不必从外界引入加热剂和冷却剂。
具体为由于各塔操作压力不同,塔的操作压力由第l效到第N效逐级降低,前一效的塔顶蒸汽冷凝温度略高于后一效的塔釜液沸点温度。
第一效的塔釜由水蒸气加热,其塔顶蒸汽作为热源加热第2效的塔釜,同时被冷凝得到产品。
依次逐效进行,直到最后一效塔顶蒸汽被冷却介质冷凝。
这样在整个流程中只有第一效加入新鲜蒸汽,在最后一效加入冷却介质,中间各塔则不再需要加热蒸汽和冷却介质,因此多效精馏充分利用了冷热介质之间过剩的温差。
尽管总能量降级和单塔一样,但它不是一次性降级的,而是逐塔降低的,这样,每个塔的塔顶、塔底温差减小了,降低了有效能损失,从而达到节能目的。
图4 多效精馏但多效精馏的投资费用高于常规精馏,故要依据实际生产情况的要求并结合经济因素综合考虑,作出决定。
三、采用经济合适的回流比,降低能耗精馏核心在于回流,而回流会造成能耗加大,故可以采用新型板式塔和高效填料塔,降低回流比,使过程能耗降低。
①新型板式塔高效导向筛板具有生产能力大、塔板效率高、塔压降低、结构简单、造价低廉、维修方便的特点。
目前已广泛应用于化学工业、石油化工、精细化工、轻工化工、医药工业、香料工业、原子能工业等。
高效导向筛板[4]的工作原理是:如图5、图6所示。
在高效导向筛板上开设了大量筛孔及少部分导向孔,通过筛孑L的气体在塔板上与液体错流,穿过液层垂直上升,通过导向筛板的气体,沿塔板水平前进,将动量传递给塔板上水平流动的液体,从而推动液体在塔板上均匀稳定前进,克服了原来塔板上的液面落差和液相返混,提高了生产能力和板效率,解决了堵塔、液泛等问题。
高效导向筛板在液流人口处增加了向上凸成斜台状的鼓泡促进器,促使液体一进入塔板就能生产鼓泡,带来了良好的气液接触与传质。
高效导向筛板具有下述特点:(1)生产能力大。
生产能力达的原因:①克服了液流上游存在的非活化区,使得气流通道增加了1/3以上。
②消除了液面梯度,使得气速均匀,生产能力的提高。
③从筛孔中上升的气体是垂直向上,从导向孔中上升的气体是水平向前,气体的合成气速是斜向上方的。
这样既延长了气体夹带雾滴的运动轨迹,减小了雾沫夹带,提高了气速和生产能力。
④由于导向筛板效率高,同样塔板数时回流比可以降低,进而提高塔的负荷与生产能力。
(2)效率高①克服了非活化区,使得塔板上鼓泡区域增加,增加了气液传质机会,提高了塔板效率。
②高效导向筛板很好地克服了液相返混,提高了塔板效率。
③消除了液面梯度,降低了漏液量和雾沫夹带,提高了塔板效率。
(3)压降低。
与泡罩塔板、浮阀塔板等塔板相比,筛板塔板由于结构简单,气流通道顺畅,因此操作压降最低。
(4)抗堵能力强。
(5)结构简单,造价低廉。
由于高效导向筛板只是在钢板上开些筛孔和导向孔,而无其它组件,因此其结构简单,重量较轻,这样工人在拆装过程中非常方便。
相应的造价也降低。
②高效填料塔填料是填料塔最重要的传质内件,填料的性能主要取决于填料表面的湿润程度和汽液两相流体分布的均匀程度。
因为填料提供了单位体积中较大的表面积,这仅是填料的几何表面,起气液传质作用的表面要比几何表面小,总有一部分填料表面未被湿润,减少了气液有效接触的相界面,从而降低了传质效果。
若想达到好的传质效果,必须使液体在整个填料表面充分湿润,形成均匀的液膜。
填料表面的湿润性能主要依赖于所处理物料的表面张力、粘度和填料表面的性质等。
尤其是对水、甘油等表面张力大的物系,必须对填料表面进行物理处理和化学处理,提高填料表面的湿润性能。
对金属材质填料,采用物理方法、化学方法及联合方法,对金属丝网波纹填料与金属板波纹填料进行表面处理,大大提高了液体在填料表面的成膜和填料的分离效率,甚至使有的分离过程由不可能成为可能,强化了分离技术与工艺。
在塑料填料方面,对于聚丙烯、聚乙烯等材质的填料,用一定技术改进表面性质(如北京化工的表面接枝技术),提高填料表面的湿润性,进而提高了填料的传质效率。
经在恶劣环境下(酸、碱环境下)应用表明:塑料填料同样具有很高的传质性能和流体力学性能,且价格便宜。
高效填料塔的填料的分离效率大为提高。
主要优点有:(1)理论塔数高、通量大、压力降低;(2)低负荷性能好、理论板数随气体负荷的降低而增加,没有低负荷极限;(3)放大效应不明显;(4)适于减压精馏,能够满足精密、大型、高真空精馏装置的要求,为难分离物系、热敏性物系及高纯度产品的精馏分离提供了有利的条件。
四、操作条件优化节能该方法主要是利用模拟软件对精馏过程的操作条件进行研究,精馏塔的主要操作条件包括操作压力、操作温度、塔板压降,进料位置及温度、理论板数、回流比以及回流温度、塔顶塔底采出量、关键组份的清晰分割程度,塔顶塔底热负荷等等,除塔的操作压力一般是给定的(在设计双效流程除外),其它的都可以作为操作变量,通过灵敏度分析、设计规定或者优化技术来确定满足分离任务的最佳值,以获得最小的冷凝负荷和再沸器热负荷,从而使精馏塔能耗最少。
此外进料热状况对精馏的能耗会产生影响.在一定的操作条件下,通过改变进料热状况,可取得良好的节能效果,且操作简单、控制方便、投资费用小,是一种很好的精馏节能措施五、中间换热节能[5]对于塔顶塔底温度差别比较大的精馏塔,可以通过增加中间换热器的方式来节省或回收热量(冷量)。
中间换热的方式有两种:中间冷凝器和中间再沸器。
对塔底再沸器来说(以塔底再沸器为基准),中间冷凝器是回收热量,中间再沸器是节省热量;对于塔顶冷凝器来说(以塔顶冷凝器为基准),中间冷凝器是节省冷量,中间再沸器是回收冷量[6]。
中间冷凝器和中间再沸器的负荷如果比较大,塔顶冷凝器和塔底再沸器的热负荷会降低,这样会导致精馏段回流比和提馏段蒸汽比(气相回流比)减少,回流比的减少,应当相应增加塔板数,才能保证产品的分离纯度,从而使设备投资费用增加。
图6 中间再沸器与中间冷凝器图6描述了这两种中间换热方式的示意流程:如果精馏塔在塔下方温度分布存在显著的变化,则可设中间再沸器使用低品位热源,以减少主再沸器高品位热量消耗,但中沸器下方塔板分离能力被削弱;当塔上部的温度分布若存在显著的变化时,则可设中间冷凝器,采用较低品位的冷剂,减少主冷凝器高品位冷剂的用量,以减少能耗,但其上方的塔板的分离能力有所下降。
将中间换热方式归类于过程技术节能,是因为原来的精馏塔没有变化,只不过增设的中间换热改变了操作线斜率,利用了低品位能源。
在分离任务一定的情况下,常规精馏塔塔釜再沸器的供热量等于设有中间再沸器的精馏塔塔釜再沸器与中间再沸器供热量之和。
设置中间再沸器前后,所需要的总的热负荷不变。
只是在设置中间再沸器后,部分热量可以采用低于塔底再沸器的廉价的废热蒸汽提供,塔的热能有效降级,这使得热效率提高。