酸性光亮镀铜工艺及配方模板
酸铜电镀工艺
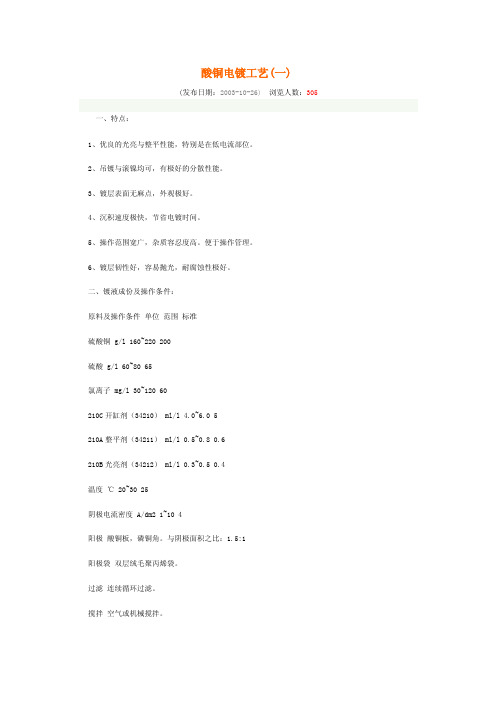
酸铜电镀工艺(一)(发布日期:2003-10-26)浏览人数:305一、特点:1、优良的光亮与整平性能,特别是在低电流部位。
2、吊镀与滚镍均可,有极好的分散性能。
3、镀层表面无麻点,外观极好。
4、沉积速度极快,节省电镀时间。
5、操作范围宽广,杂质容忍度高。
便于操作管理。
6、镀层韧性好,容易抛光,耐腐蚀性极好。
二、镀液成份及操作条件:原料及操作条件单位范围标准硫酸铜 g/l 160~220 200硫酸 g/l 60~80 65氯离子 mg/l 30~120 60210C开缸剂(34210) ml/l 4.0~6.0 5210A整平剂(34211) ml/l 0.5~0.8 0.6210B光亮剂(34212) ml/l 0.3~0.5 0.4温度℃ 20~30 25阴极电流密度 A/dm2 1~10 4阳极酸铜板,磷铜角。
与阴极面积之比:1.5:1阳极袋双层绒毛聚丙烯袋。
过滤连续循环过滤。
搅拌空气或机械搅拌。
1、注入二分之一的水于待用缸(或备用槽中),加热至40~50℃。
所用的水的氯离子含量应低于70毫克/升。
2、加入所需的硫酸铜,搅拌直至完全溶解。
3、加入2克/升活性碳粉,搅拌至少一小时。
4、用过滤泵,把溶液滤入清洁的电镀槽内。
加水到接近水位。
5、慢慢加入所需的硫酸。
此时会产生大量的热能,需强力搅拌,使温度不超过60℃。
6、把镀液冷却到25℃。
7、分析镀液氯离子含量,不足加入适量的盐酸或氯化钠,使氯离子含量达至标准。
8、按上表加入适量的添加剂搅拌均匀,在正常操作条件下,把镀液电解3~5安培小时/升,便可正式生产。
四、设备1、镀槽碳钢内衬橡胶或PVC,聚乙烯,聚丙烯等塑料。
注意槽体的绝缘和保温。
2、温度控制可用钛管冷却。
注意管道的绝缘,防止管子带电。
3、空气搅拌镀液需要平均而强烈的空气搅拌,所需气量约为15~20立方米/小时。
打气管最好离槽底50毫米,气管需钻有两排直径2~3毫米的小孔,45度角向槽底,两排小孔应相对交错,小孔间距离为80~100毫米。
酸性镀铜工艺及添加剂使用

酸性镀铜工艺及添加剂使用刘强高级工程师1. 前言全光亮酸性镀铜工艺参数即基础成分和操作参数严格按照电镀产品要求确定:要求最高光亮度和最高填平速度的铜酸比(五水硫酸铜与硫酸之比)最高可达到4.6,硫酸铜最高可达到230g/l,硫酸最低可达50g/l;随着对均镀能力和走位深度要求的提高,必须通过调低对最高光亮度和最高填平速度的要求,装饰性电镀铜酸比最低可降至1.8,硫酸铜最低可降至150g/l,硫酸最高可达到85g/l。
对于均镀能力和走位深度要求极高的线路板行业电镀铜,铜酸比最低可降至0.33,硫酸铜最低可降至50g/l,硫酸最高可达到150g/l。
因此全光亮酸性镀铜工艺的逻辑是:①硫酸铜与硫酸的维护方向因同离子效应限制,填平光亮和均匀走深要求重点的限制而完全相反;②要提高填平速度和出光光亮度,就要提高铜酸比和硫酸铜绝对含量,牺牲部分均镀能力和走位深度;要提高均镀能力和走位深度,就要降低铜酸比和硫酸铜绝对含量,牺牲部分填平速度和出光光亮度。
通过对铜酸比和硫酸铜含量的检测,就能知道在0.33-4.6铜酸比所处的位置,以及当前位置是填平光亮度不能满足要求还是均匀走深度不能满足要求。
当铜酸比、硫酸铜策略确定后,添加剂的抑制比策略应与铜酸比策略大方向一致以保持重点要求最佳化,局部相对抗,以防一边倒产生均匀走深或填平出光性能恶化。
镀液高低区沉积速度相对均衡。
例如对于填平出光型镀液,硫酸铜很高,硫酸很低,填平剂、开缸剂要低,光亮剂要高,当低位走深和均匀度不能满足要求时适当提高提高填平剂、开缸剂比例;对于均匀走深型镀液,硫酸铜很低,硫酸很高,填平剂、开缸剂要高,光亮剂要低,当填平出光速度不能满足要求时适当提高提高光亮剂比例;要达到良好的效果,不仅高低铜酸比充分发挥其长,更关键在于添加剂杨其长,避其短,力量均衡。
对填平出光要求低对均匀走深要求高的产品,大比例使用光亮剂,不仅浪费,而且导致低位达不到要求;对填平出光要求高对均匀走深要求低的产品,大比例使用填平剂、开缸剂导致出光填平速度慢,低位孔隙难填平,发黑发暗,高位电流范围被压缩,易起雾朦,甚至烧焦。
实验四--光亮电镀铜

实验四光亮电镀铜一、目的及要求1、熟悉电镀小试的装置和仪器设备。
2、掌握光亮镀铜溶液的配制及预镀工艺。
3、进行赫尔槽试验,分析光亮剂影响。
二、仪器、化学试剂直流电源、电炉、控温仪、赫尔槽及试片、电解铜板;硫酸铜、硫酸、镀铜光亮剂、镀镍溶液、镍阳极。
三、实验步骤1、工艺流程试片准备――酸洗――水洗――除油――水洗――浸蚀――预镀镍――(或铜锡合金)――水洗――酸性亮铜――水洗2、溶液配方及工艺条件预镀镍溶液:硫酸镍: 120~140g/L氯化钠: 7~9 g/L硼酸: 0~40 g/L无水硫酸钠: 50~80 g/L十二烷基硫酸钠: 0.01~0.02 g/LpH: 5.0~6.0温度: 30~50℃电流密度: 0.8~1.5A/dm2酸性亮铜溶液:硫酸铜: 200~220 g/L硫酸(1.84): 60~70 g/L四氢噻唑硫酮: 5×10-4~3×10-3 g/L盐酸: 0.02~0.08 g/L十二烷基硫酸钠: 0.05~0.2 g/L温度: 10~30℃(室温)电流密度: 1~4 A/dm2搅拌:阴极移动3、用赫尔槽实验观察光亮剂对同层质量影响,记录试验情况。
五、思考问题及要求1、酸性亮铜电镀前为什么要进行预镀?预镀工艺有哪几种?2、溶液pH对铜层质量有什么影响?4、以论文形式写出光亮剂对镀层质量影响为内容的实验报告。
附录用有机玻璃板自制赫尔槽赫尔槽结构简单,制造和使用方便。
目前国内外已广泛应用于电镀实验和工厂生产的质量管理,特别是应用于光亮电镀添加剂的控制,成为电镀工作者不可缺少的工具,267ml赫尔槽尺寸如图。
材料:有机玻璃;槽深:65;厚:3-5一、目的要求掌握有机玻璃黏结技术,自制267ml赫尔槽二、药品与材料:有机玻璃板3~5mm厚钢锯、细纱布180~270#、脱脂棉。
100ml棕色试剂瓶1个三氯化烷、乙醇三、有机玻璃黏结剂配制:配方:三氯甲烷95ml乙醇1~2 ml有机玻璃碎块或碎屑5克。
全光亮酸性镀铜(
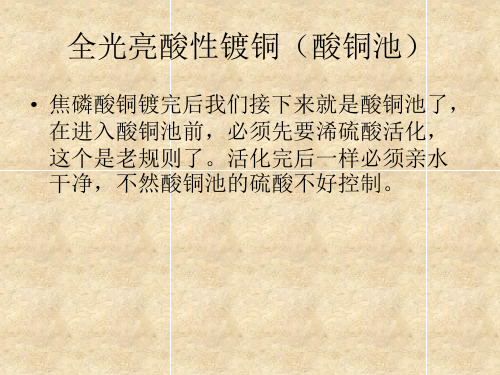
生产过程中会出现的故障
• 电镀时电压升高电流下降 出现这种情况时有以下几种。(用排除法)
度会上升注意降温。 5. 硫酸低了,也就是说硫酸少了。 6. 杂质高了也会这样,但如果平时清洁维护好一般都不会。 记住阳极必须是磷铜角,不然会出现一价铜的。出现一价铜
可以用过氧化氢(双氧水)0.03ML/L
镀层粗糙分析
1. 打底铜和焦铜镀层是不是太薄,这里我就给大 伙说一下,如果镀层少于3um时镀层是多疏松 的多孔的,大于8个um时会有所降低,最标准 的是13-15个um这是个我亲自分析实验的。
全光亮酸性镀铜(酸铜池)
• 焦磷酸铜镀完后我们接下来就是酸铜池了, 在进入酸铜池前,必须先要浠硫酸活化, 这个是老规则了。活化完后一样必须亲水 干净,不然酸铜池的硫酸不好控制。
硫酸铜盐镀铜的配方
硫酸铜(CuSo4 . 5H2o)200克每升
硫酸(H2So4)
30-40ml/L
氯离子
80-150mg/L
2. 添加剂失调(A,B,C)没有加好。 3. 电流太小,镀液中的硫酸铜含量太低。间
接的说是阳极是不是太小。 4. 亲水池中是不是有油,这个很致命的,也
是时有发生的。
有毛刺
• 这个可是时有发生的啊,也是最搞笑的。 很多能人都在这上面吃过不少苦头,因为分不清到低是哪出
了问题,我可以告诉你,酸铜支出现毛刺只有两个原因。 • 平时没有过滤,里面的杂质过多。 • 添加剂没按比例添加。 不过做为技术员一般都不会出这个差错。那还有什么原因会
酸性光亮快速电镀硬铜技术

酸性光亮快速电镀硬铜工艺的发展依赖于凹版制版技术的进步.电子雕刻凹版制版对镀层的质量要求比较严格,既要有适中的硬度,又要有良好的平整性和光亮性。
另外.考虑到生产成本和生产效率问题,需要在生产中采用特殊的添加剂并严格控制工艺参数。
目前.国内外凹版制版电镀硬铜工艺大都采用硫酸盐镀铜,该工艺成分简单、成本低.且便于控制。
现在国内的快速电镀硬铜工艺大致相同,无非所用的添加剂不同。
目前,国内常用的有日本大和的COSMO—G型添加剂,日本永辉KY型添加剂、深圳华天宇公司的J型添加剂.安美特的CUFLEX一40型添加剂、瑞典AM公司的AM型以及一些制版企业自制的添加剂,这些添加剂的用法基本相同。
1。
工艺规范工艺规范如表1所示。
2.操作条件操作条件如表2所示。
3.质量要求对快速电镀硬铜层质量要求主要有如下几个方面。
表1工艺规范硫酸铜硫酸氯离子开缸剂(MU)硬化荆整平剂200~2809/l_55-709/L80~1509/L6~8ml/L2~3ml/L(开缸)80~120ml/KAH(补充)80~I"20ml/KAH(补充)2209/L709/L120ppm8ml/L(开缸)2.5ml/L(开缸)100ml/KAH(补充)100ml/KAH(补充)青岛海联制版有限公司王庆浩(1)硬度。
硬度一般控制在180~240HV,硬度低,铜层过软.电雕网穴的网型难以保持,导致色彩还原失真,且影响版滚筒的使用寿命。
铜层过硬,会缩短电子雕刻针使用寿命,甚至断针。
(2)平整度。
良好的平整度可以减少铜层的加工量,减少表面缺陷,降低质量隐患和原材料的消耗。
(3)亮度。
亮度是衡量铜层质量的一项重要指标,是铜层晶体结构的体现。
亮度高,结晶细化,铜层硬度均匀,保持时间长,而且铜层韧性好.气孔率低,有助于延长电雕针的使用寿命,并可提高电雕质量。
1.硫酸铜硫酸铜含量对镀铜层的硬度影响不大.甚至可以忽略。
但作为该电镀工艺的主盐,必须控制好含量。
铜的含量低,不能满足高电流密度的需要,会造成镀层粗糙、砂眼、毛刺等缺陷,高电流密度区烧焦的可能性较大。
酸性光亮镀铜工艺及配方

酸性光亮镀铜工艺及配方一、酸性镀铜光亮剂特点:1、快速出光,特好的填平度,即使低电流密度区也可得到极高的填平度。
2、广泛的电流密度范围均可得到镜面亮度。
3、工作温度范围宽,18—< xmlnamespace prefix ="st1" ns ="urn:schemas-microsoft-com:office:smarttags" />40℃都可得到镜面亮度。
4、镀层内应力低,延展性好,电阻率低,可应用于各种不同的基体材料电镀。
铁件、锌合金件、塑胶件等同样适用。
5、光亮剂对杂质容忍度高,性能稳定,易于控制。
一般在使用一段长时间(约800-1000安培小时/升)后,才需用活性碳粉处理。
6、沉积速度快。
在4.5安培/平方分米的电流密度下,每分钟可镀1微米的铜层,电镀时间因而缩短。
(酸性镀铜溶液是一种强酸性的简单盐电镀溶液,镀液中没有使用络合剂。
)二、电镀工艺条件:原料范围标准硫酸铜200-240g/L220 g/L硫酸55-75g/L65 g/L氯离子15-70mg/L20-40mg/LBFJ-210Mμ5-12ml/L8 ml/LBFJ-210A0.5-1.0ml/L0.6 ml/LBFJ-210B0.5-1.0ml/L0.6 ml/L温度18-40℃24-28℃阴极电流密度0.5-10A/dm2阳极电流密度 1.5-8A/dm2搅拌空气搅拌空气搅拌三、镀液的配制:1、先在镀槽中(待用缸或备用缸)加入1/2体积蒸馏水或去离子水,加热至40-50°。
(所用水的氯离子含量应低于70mg/L(ppm))。
2、加入计算量的硫酸铜,搅拌至完全溶解。
3、加入活性炭2g/L,搅拌1小时后静止8小时用过滤泵,把溶液滤入清洁的电镀槽内。
加去离子水至规定体积。
4、在不断搅拌下慢慢加入计算量的化学纯硫酸,(注意:此时会产生大量热能,故需强力搅拌,慢慢添加,以使温度不超过60℃。
酸性镀铜光亮剂配方
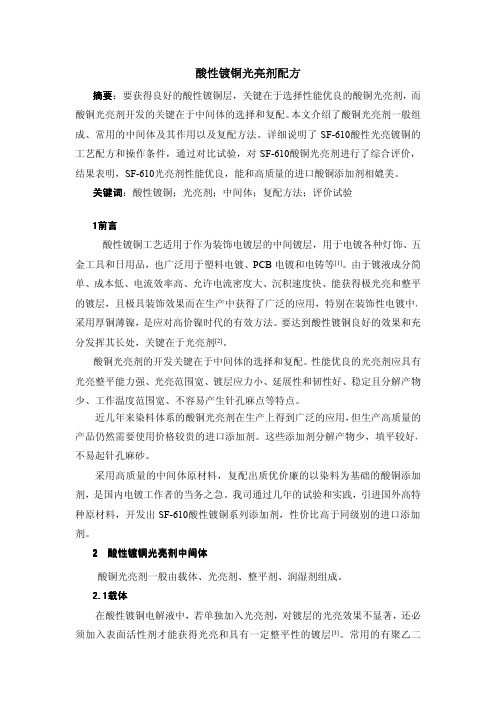
合添加剂过量情况比较,以评价光亮剂添加量使用范围。试验结果见表2:
表2 添加剂过量试验
序号
SF-610A
SF-610B
SF-610Mu
试验现象
(ml/L) (ml/L)
(ml/L)
1
0.5
0.3
8
镜面光亮
2
0.5
0.3
16
镜面光亮
3
0.5
0.3
24
低区白雾
4
1.0
0.3
8
状
5
1.5
0.3
8
镜面光亮
6
酸性镀铜光亮剂配方
摘要:要获得良好的酸性镀铜层,关键在于选择性能优良的酸铜光亮剂,而 酸铜光亮剂开发的关键在于中间体的选择和复配。本文介绍了酸铜光亮剂一般组 成、常用的中间体及其作用以及复配方法。详细说明了 SF-610酸性光亮镀铜的 工艺配方和操作条件,通过对比试验,对 SF-610酸铜光亮剂进行了综合评价, 结果表明,SF-610光亮剂性能优良,能和高质量的进口酸铜添加剂相媲美。
70mg/L(ppm)
SF-610A
0.4~0.6 ml/L
0.5 ml/L
SF-610B
0.2~0.4 ml/L
0.3 ml/L
SF-610 Mu
6~8ml/L
8ml/L
温度
20~40℃
25℃
阴极电流密度
1~6A/dm2
3~5 A/dm2
阳极
磷铜角(0.03%~0.06%
磷铜角(0.03%~0.06%
[4]张立茗、方景礼、袁国伟、沈品华 .实用电镀添加剂.北京:化学工业出版 社.2007:307.
性
外观没有明显区别
酸性镀锌光亮剂配方成分,生产工艺及配制方法

酸性镀锌光亮剂配方组成,配制方法及性能研究导读:本文详细介绍了酸性镀锌光亮剂的研究背景,理论基础,参考配方等,本文中的配方数据经过修改,如需更详细资料,可咨询我们的技术工程师。
酸性镀锌光亮剂广泛应用在电镀行业, 禾川化学引进尖端配方破译技术,专业从事酸性光亮剂成分分析、配方还原、研发外包服务,为镀锌光亮剂相关企业提供一整套配方技术解决方案。
一、背景酸性镀锌包括氯化钾镀锌、氯化钠镀锌、铵盐镀锌、硫酸盐镀锌等。
其所用光亮剂均为组合型光亮剂, 而且组成成分基本相同, 在某些情况下, 甚至可以通用。
当然, 硫酸盐镀锌工艺由于盐浓度较高, 所以光亮剂的耐盐性要求较高。
如何正确选择、使用酸性镀锌光亮剂, 就成为工艺能否成功的关键。
同样, 添加好的光亮剂, 如果使用不当也能带来很多工艺故障。
禾川化学技术团队具有丰富的分析研发经验,经过多年的技术积累,可以运用尖端的科学仪器、完善的标准图谱库、强大原材料库,彻底解决众多化工企业生产研发过程中遇到的难题,利用其八大服务优势,最终实现企业产品性能改进及新产品研发。
样品分析检测流程:样品确认—物理表征前处理—大型仪器分析—工程师解谱—分析结果验证—后续技术服务。
有任何配方技术难题,可即刻联系禾川化学技术团队,我们将为企业提供一站式配方技术解决方案!二、酸性镀锌光亮剂2.1酸性镀锌光亮剂特性2.1.1物理性能选用氯化物镀锌光亮剂, 首先要看其外观, 一般为棕黄色剂红棕色半透明粘性液体, 近来市场上也出现了无色半透明光亮剂;二要测其pH 值, 一般在6、7 之间为好, 因为接近镀液pH 值, 长期使用易保持镀液pH值的稳定; 三要测其比重, 确定光亮剂的浓度, 要求在1. 07g/ cm3 以上; 四要测其粘度, 确定水溶性, 要求适度, 若粘度过大, 水溶性不好, 在电镀中易形成缸脚。
2.1.2 化学性能1)浊点要高, 浊点是氯化物镀锌光亮剂中非常重要的参数, 一般挂镀液要求光亮剂浊点在55 e 以上,对滚镀液, 要求光亮剂浊点在60 e 以上, 测定方法是:将加有光亮剂的镀液水浴加热, 至镀液混浊, 然后冷却, 测镀液由混浊转澄清透明时温度, 即为浊点。
光亮酸铜工艺

光亮酸铜工艺光亮酸铜工艺能沉积一层高光亮、整平能力极强和延展性好的铜镀层,本工艺镀层可做为钢件、黄铜件、铝件、压铸伞件和塑料件上各种镍铬镀层组合的底层。
该工艺在整个电流密度范围内可得到高光亮、整平性优良的镀层,从而降低了研磨和/或抛光的操作成本,光亮添加剂性能稳定,在低光亮剂获得高质量的产品。
该工艺镀层与镍层的结合力优良,镀层柔软、延展性好、内应力低,非常适用于塑料电镀。
类似其它光亮酸铜工艺,在铜、铝和锌底材上进行电镀之前,也须先镀闪镀层,常用氰化镀铜,也可采用闪镀镍。
在塑料和其它非导体材料上镀酸铜时,必须首先沉积一层连续的导电金属膜层。
一·操作条件最佳范围CuSO4·5H2O g/L 187 150-220浓H2SO4(1.84)g/L 75 60-90七水硫酸亚铁g/L 3 2.5-5.0Cl- ppm 60(既18mL/100L) 40~80开缸剂%v/v 1.0 0.75~1.25补充剂%v/v 0.035 0.025~0.045整平剂%v/v 0.03 0.01~0.05阴极电流密度A/dm2 4 3~6阳极电流密度A/dm2 2 1.5~3槽电压V 3~9温度℃27 21~32搅拌强烈空气搅拌过滤连续过滤镀槽无孔炭或通过认可的橡胶衬里的镀槽空气搅拌叶轮CPVC材料加热和冷却片钛\钽\特氟隆材料加热和冷却交换器钛\钽\电镀类石墨材料镀槽通风需要过滤硅藻土材料连续过滤槽液, 每小时过滤2循环(不使用活性炭)阳极含磷轧制铜(0.02~0.06%磷),磷铜锭阳极包聚丙烯或改性聚丙烯二·开缸1、备用槽注放2/3体积的水(水中含Cl-量保证开缸后不得超过80ppm)2、缓慢加入计算量的硫酸;3、连续搅拌下,溶解所需量硫酸;4、用4.8g/L的活性炭处理,连续搅拌至少1小时,静置(最好过夜);5、将镀液过滤至镀槽,调整镀液温度至操作温度,加水至所需体积;6、调整Cl-含量至60ppm,添加0.3mL/100L试剂纯HCl(注:即盐酸含量为37%的)可提高1.1ppm [Cl-]浓度;7、加入计算量开缸剂、补充剂和整平剂,搅拌均匀。
如何配制光亮酸性镀铜的镀液?

滤 ; ( 用过 滤泵把溶液 滤入清洁 的镀 槽 内,加 水 5) 至接近水位 : ( 慢慢加入 所需浓硫酸 ,此时会产 6) 生大量热量 ,故需强烈搅拌 ,慢慢添 加 ,以使温度 不 超过6 0℃ : ( 7)待镀液 温度冷 却到2 C ,取样 5c 时 j 分析溶液中氯离子含量 ,若 不足 ,应加入适量试剂级 盐酸 或氯化钠 ,使 氯离子含量达 到标准 ; ( 按 工 8) 艺加入适量 的添加剂 ,搅拌均匀 ,在正常操作条件下 把镀 液 电解3 5h ~ ,便 可正式生产 。在镀液 配制时需 注 意下列事项 : ( )新制作 的槽 要先用稀碱浸 泡 , 1 然后 水洗 ,再 用稀硫酸浸 泡 ,最后水 洗干净 ; ( 2) 视硫酸铜 的质量情 况加入双氧水 ,若其纯度高 ,可 少 至05mLL _ / ,低纯度 双氧 水可多加至2mLL - ,不管加 / 多少的双氧水需要适 当的温度 ( 一般6 0o ( C); 3) 上述所用 浓硫酸应是试 剂级硫酸 ,若使用工业硫酸 配 槽 ,必须在进行双氧水和活性炭 处理 之前加入 ,以便 把硫酸 中含有 的铁和有机杂质一同除去 ; ( 若使 4) 用粉状活性炭 ,应先用水调成糊状 ,然后加入槽 中 ; ( 5)过滤要彻底 ,镀液 内不能残 留活性 炭。其检 测
量成正 比, 电流 大、时间长,光亮剂消耗量就大 ,反 之 ,光亮剂消耗减 小。温度高 ,光亮剂消耗快 ,温度 方 法 :取 一 容 器 、 漏 斗 、 滤 纸 及 1 镀 液 ,进 行 过 OmL 低 ,光亮剂消耗 就慢一些。因此 ,要注意和 掌握光 亮 滤 ;然后用 肉眼观察滤纸上有无活性炭物质 ,即可判 剂的消耗 情况 ,做 到及时而适量补充光亮剂 ,以保持 断过滤效果。 镀液 的工艺稳定 ; ( 避 免杂质带 入槽 内,是延 长 3) 镀 液寿命的重要途径。生产中镀件掉入槽底要做到及 光 亮 酸性 镀 铜 液 中硫 酸 的作 用 如伺 ? 时捞 出,避免过夜 ,造成镀件腐蚀形成杂质 而污染镀 液。特别是要注意硝酸根 、氯根 、铬酸根等阴离子的 含量高低有何影响?
如何做酸性镀铜中的硫酸铜和硫酸的分析?
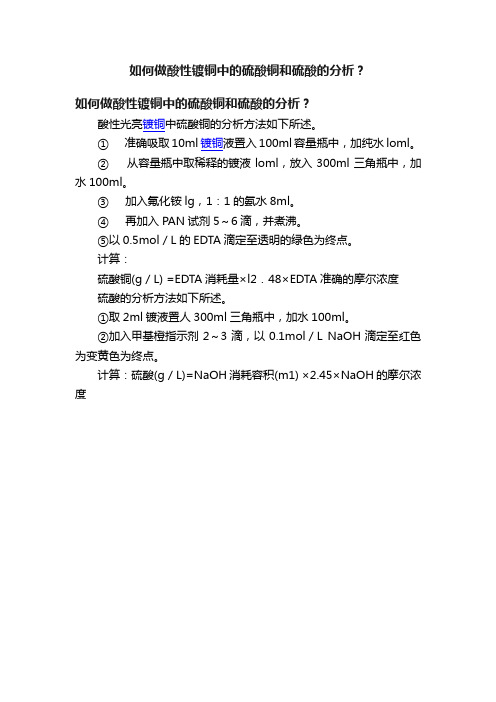
如何做酸性镀铜中的硫酸铜和硫酸的分析?
如何做酸性镀铜中的硫酸铜和硫酸的分析?
酸性光亮镀铜中硫酸铜的分析方法如下所述。
①准确吸取10ml镀铜液置入100ml容量瓶中,加纯水loml。
②从容量瓶中取稀释的镀液loml,放入300ml三角瓶中,加水100ml。
③加入氟化铵lg,1:1的氨水8ml。
④再加入PAN试剂5~6滴,并煮沸。
⑤以0.5mol/L的EDTA滴定至透明的绿色为终点。
计算:
硫酸铜(g/L) =EDTA消耗量×l2.48×EDTA准确的摩尔浓度
硫酸的分析方法如下所述。
①取2ml镀液置人300ml三角瓶中,加水100ml。
②加入甲基橙指示剂2~3滴,以0.1mol/L NaOH滴定至红色为变黄色为终点。
计算:硫酸(g/L)=NaOH消耗容积(m1) ×2.45×NaOH的摩尔浓度。
酸性光亮铜电镀电镀镍

酸性光亮铜电镀电镀镍/金电镀锡二、工艺流程:浸酸→全板电镀铜→图形转移→酸性除油→二级逆流漂洗→微蚀→二级→浸酸→镀锡→二级逆流漂洗逆流漂洗→浸酸→图形电镀铜→二级逆流漂洗→镀镍→二级水洗→浸柠檬酸→镀金→回收→2-3级纯水洗→烘干三、流程说明:(一)、浸酸①作用与目的:除去板面氧化物,活化板面,一般浓度在5%,有的保持在10%左右,主要是防止水分带入造成槽液硫酸含量不稳定;②酸浸时间不宜太长,防止板面氧化;在使用一段时间后,酸液出现浑浊或铜含量太高时应及时更换,防止污染电镀铜缸和板件表面;③此处应使用C.P级硫酸;(二)、全板电镀铜:又叫一次铜,板电,Panel-plating①作用与目的:保护刚刚沉积的薄薄的化学铜,防止化学铜氧化后被酸浸蚀掉,通过电镀将其加后到一定程度②全板电镀铜相关工艺参数:槽液主要成分有硫酸铜和硫酸,采用高酸低铜配方,保证电镀时板面厚度分布的均匀性和对深孔小孔的深镀能力;硫酸含量多在180克/升,多者达到240克/升;硫酸铜含量一般在75克/升左右,另槽液中添加有微量的氯离子,作为辅助光泽剂和铜光剂共同发挥光泽效果;铜光剂的添加量或开缸量一般在3-5ml/L,铜光剂的添加一般按照千安小时的方法来补充或者根据实际生产板效果;全板电镀的电流计算一般按2安/平方分米乘以板上可电镀面积,对全板电来说,以即板长dm×板宽dm×2×2A/DM2;铜缸温度维持在室温状态,一般温度不超过32度,多控制在22度,因此在夏季因温度太高,铜缸建议加装冷却温控系统;③工艺维护:每日根据千安小时来及时补充铜光剂,按100-150ml/KAH补充添加;检查过滤泵是否工作正常,有无漏气现象;每隔2-3小时应用干净的湿抹布将阴极导电杆擦洗干净;每周要定期分析铜缸硫酸铜(1次/周),硫酸(1次/周),氯离子(2次/周)含量,并通过霍尔槽试验来调整光剂含量,并及时补充相关原料;每周要清洗阳极导电杆,槽体两端电接头,及时补充钛篮中的阳极铜球,用低电流0。
酸性镀铜光亮剂配方
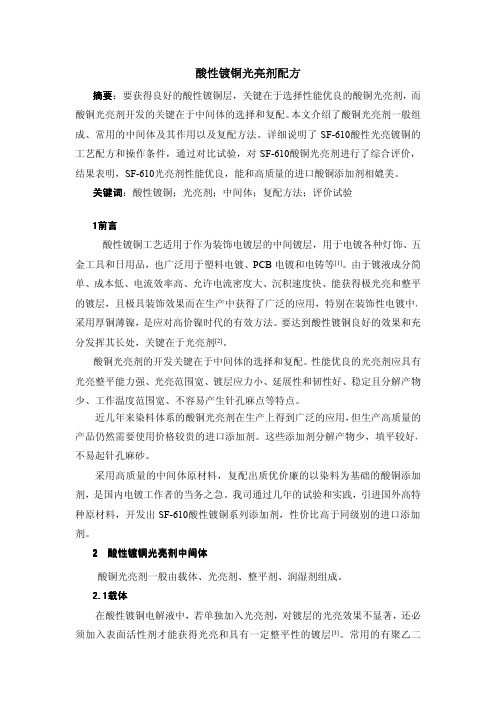
120 AH。每打完一片按理论消耗量分别补充添加剂,每10 AH 进行一次过滤并分
析、补充各成分。试验完毕后,观察试片镀层变化情况,从稳定性、清亮度、填
平性能、是否起麻砂等方面进行综合评价。试验结果见表1:
表1 镀液老化试验
对比
SF-610
香港某公司光剂
项目
稳定
较稳定,第1片和第90张片
第15Ah 后光亮度略有下降,第90
70mg/L(ppm)
SF-610A
0.4~0.6 ml/L
0.5 ml/L
SF-610B
0.2~0.4 ml/L
0.3 ml/L
SF-610 Mu
6~8ml/L
8ml/L
温度
20~40℃
25℃
阴极电流密度
1~6A/dm2
3~5 A/dm2
阳极
磷铜角(0.03%~0.06%
磷铜角(0.03%~0.06%
间10min,空气搅拌。观察不同温度下试片外观情况。试验结果见表3:
表3 耐温性能试验
温度/℃
试验现象
10
镜面光亮
20
镜面光亮
30
镜面光亮
35
镜面光亮
40
低区10mm 内起白雾
45
低区暗,大面积起白雾
从表3可以看出,要获得良好的镀层,SF-610酸铜添加剂工作范围是10~35℃。
5.6阴极极化曲线
酸性镀铜光亮剂配方
摘要:要获得良好的酸性镀铜层,关键在于选择性能优良的酸铜光亮剂,而 酸铜光亮剂开发的关键在于中间体的选择和复配。本文介绍了酸铜光亮剂一般组 成、常用的中间体及其作用以及复配方法。详细说明了 SF-610酸性光亮镀铜的 工艺配方和操作条件,通过对比试验,对 SF-610酸铜光亮剂进行了综合评价, 结果表明,SF-610光亮剂性能优良,能和高质量的进口酸铜添加剂相媲美。
酸性镀铜光亮剂配方浅谈

酸性镀铜光亮剂配方浅谈
此工艺用作装饰性酸性镀铜,适用广泛,不仅可用于钢铁件、锌合金工件上电镀,得到极佳的光亮度、整平性。
在塑料等工件上使用也能达到同样优良的效果。
特点
1.在广阔的电流密度范围内,可获得快速镜面光亮及特高整平性。
并且不容易产生针孔
及麻点。
2.镀层延展性能良好,内应力低,对镍层的结合力好,是理想的电镀层。
3.温度较高时,在低电流区不会明显降低光亮度,并在较短时间内获得高光亮镀层。
4.工作温度范围广,18-38℃都可得到较好的效果。
5.操作简便,光剂消耗量少。
6.光亮剂稳定性较高。
光亮剂加入染料,研究者对十几种染料进行了筛选,最终确认甲基紫和藏花红对扩展低DK区光亮性有效,但同时指出,加入染料后使用一些时间后,镀层易起麻点。
氯离子
过多过少的氯离子都会影响镀层的光泽和整平性。
最佳浓度范围为60-90毫克/升。
请先分析当地水质中的氯离子含量,再调整到最佳范围内。
必要时要用纯水配制。
当氯离子过少会出现树枝状条纹,过多时影响低电流区光亮度及整平性。
详解硫酸铜电镀工艺配制及操作流程
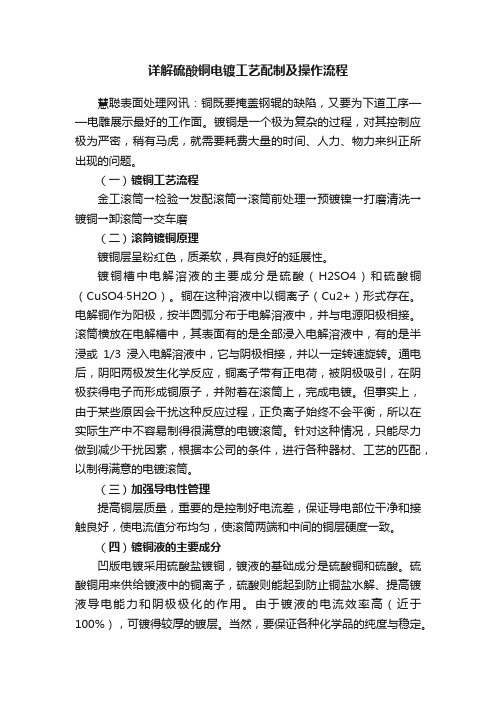
详解硫酸铜电镀工艺配制及操作流程慧聪表面处理网讯:铜既要掩盖钢辊的缺陷,又要为下道工序——电雕展示最好的工作面。
镀铜是一个极为复杂的过程,对其控制应极为严密,稍有马虎,就需要耗费大量的时间、人力、物力来纠正所出现的问题。
(一)镀铜工艺流程金工滚筒→检验→发配滚筒→滚筒前处理→预镀镍→打磨清洗→镀铜→卸滚筒→交车磨(二)滚筒镀铜原理镀铜层呈粉红色,质柔软,具有良好的延展性。
镀铜槽中电解溶液的主要成分是硫酸(H2SO4)和硫酸铜(CuSO4·5H2O)。
铜在这种溶液中以铜离子(Cu2+)形式存在。
电解铜作为阳极,按半圆弧分布于电解溶液中,并与电源阳极相接。
滚筒横放在电解槽中,其表面有的是全部浸入电解溶液中,有的是半浸或1/3浸入电解溶液中,它与阴极相接,并以一定转速旋转。
通电后,阴阳两极发生化学反应,铜离子带有正电荷,被阴极吸引,在阴极获得电子而形成铜原子,并附着在滚筒上,完成电镀。
但事实上,由于某些原因会干扰这种反应过程,正负离子始终不会平衡,所以在实际生产中不容易制得很满意的电镀滚筒。
针对这种情况,只能尽力做到减少干扰因素,根据本公司的条件,进行各种器材、工艺的匹配,以制得满意的电镀滚筒。
(三)加强导电性管理提高铜层质量,重要的是控制好电流差,保证导电部位干净和接触良好,使电流值分布均匀,使滚筒两端和中间的铜层硬度一致。
(四)镀铜液的主要成分凹版电镀采用硫酸盐镀铜,镀液的基础成分是硫酸铜和硫酸。
硫酸铜用来供给镀液中的铜离子,硫酸则能起到防止铜盐水解、提高镀液导电能力和阴极极化的作用。
由于镀液的电流效率高(近于100%),可镀得较厚的镀层。
当然,要保证各种化学品的纯度与稳定。
镀铜液的主要成分如下:1.硫酸铜(CuSO4·5H2O),是蓝色晶体,颗粒大小如玉米粒,应尽量无黄色,工业级可用。
根据生产条件和不同要求,硫酸铜的含量有的公司规范为200~250g/L,有的为210~230g/L,有的为180~220g/L。
硫酸盐光亮镀铜工艺样本

全光亮酸性镀铜全光亮酸性镀铜镀液, 是在硫酸盐镀铜镀液的基础成分中加入有机组合的光亮剂和添加剂。
所镀得的镀层光亮、柔软、孔隙率低、镀液的整平性好, 但还存在着操作温度不能高于40℃、形状复杂的零件在低电流密度区光亮较差, 槽液维护比较复杂等不足之处, 因此, 近几年来国内许多研究单位和工厂针对这些不足作进一步研究, 以期开发出更高水平的新型组合光亮剂(具有全光亮酸性镀铜工艺的操作温度在40℃以上时稳定性能优越、光亮电流密度范围宽、光亮剂用量少、维护操作方便、镀后不需除膜等优良性能)。
(一)全光亮酸性镀铜光亮剂酸铜光亮剂有二大系列: 一类是非染料体系(如传统非染料体系由M、N、SP、P组成), 另一类是染料体系(如日本进口的210), 现就非染料体系的组成、性能作简要的介绍。
1.含巯基的杂环化合物或硫脲衍生物通式为: R—SH这一类化合物, 既是光亮剂又是整平剂。
市售有代表性的有: 乙撑硫脲(N), 乙基硫脲, 甲基咪唑啉硫酮, 2-四氢噻唑硫酮, 2-巯基苯骈噻唑, 2-巯基苯骈咪唑(M)……2.聚二硫化合物通式为: R1—S—S—R2式中R1为芳香烃(苯基)、烷烃、烷基磺酸盐或杂环化合物; R2为烷基磺酸盐或杂环化合物。
这一类化合物是良好的光亮剂。
市售有代表性的有: 聚二硫二丙烷磺酸钠(SP), 苯基聚二硫丙烷磺酸钠……2.聚醚化合物通式为: (-CH2-CH20-)。
这类光亮剂实质为表面活性剂, 采用的是非离子型和阴离子型。
这类表面活性剂除了它的润湿作用能够消除镀铜层产生针孔和麻砂现象外, 还能够提高阴极极化作用, 使镀铜层的晶粒更为均匀、细致和紧密, 而且还有增大光亮范围的效果。
其不足之处是, 因为在阴极上产生一层肉眼看不见的憎水膜, 因此镀铜后必须在除膜溶液中除膜, 然后方可进行镀镍, 以保证镀层的结合力。
市售有代表性的有: 聚乙二醇(分子量为6000), OP10或OP21, 乳化剂, AE0乳化剂……上述各类光亮剂必须组合使用。
Ultra酸性光亮镀铜工艺
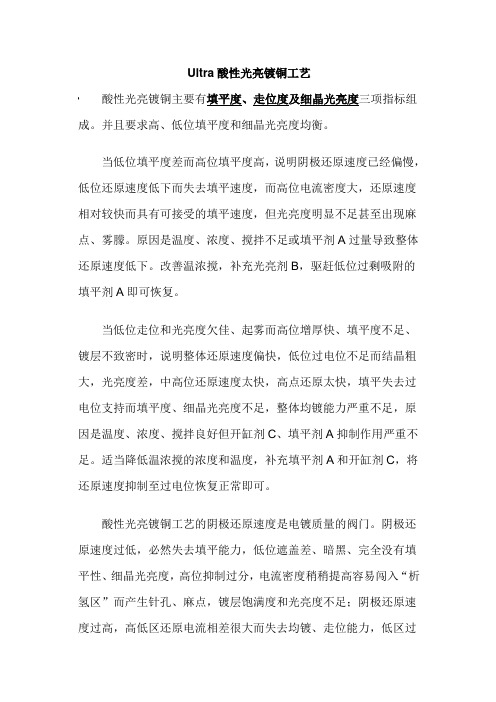
Ultra酸性光亮镀铜工艺•酸性光亮镀铜主要有填平度、走位度及细晶光亮度三项指标组成。
并且要求高、低位填平度和细晶光亮度均衡。
当低位填平度差而高位填平度高,说明阴极还原速度已经偏慢,低位还原速度低下而失去填平速度,而高位电流密度大,还原速度相对较快而具有可接受的填平速度,但光亮度明显不足甚至出现麻点、雾朦。
原因是温度、浓度、搅拌不足或填平剂A过量导致整体还原速度低下。
改善温浓搅,补充光亮剂B,驱赶低位过剩吸附的填平剂A即可恢复。
当低位走位和光亮度欠佳、起雾而高位增厚快、填平度不足、镀层不致密时,说明整体还原速度偏快,低位过电位不足而结晶粗大,光亮度差,中高位还原速度太快,高点还原太快,填平失去过电位支持而填平度、细晶光亮度不足,整体均镀能力严重不足,原因是温度、浓度、搅拌良好但开缸剂C、填平剂A抑制作用严重不足。
适当降低温浓搅的浓度和温度,补充填平剂A和开缸剂C,将还原速度抑制至过电位恢复正常即可。
酸性光亮镀铜工艺的阴极还原速度是电镀质量的阀门。
阴极还原速度过低,必然失去填平能力,低位遮盖差、暗黑、完全没有填平性、细晶光亮度,高位抑制过分,电流密度稍稍提高容易闯入“析氢区”而产生针孔、麻点,镀层饱满度和光亮度不足;阴极还原速度过高,高低区还原电流相差很大而失去均镀、走位能力,低区过电位不足导致细晶光亮度差,产生铜粉、起雾,高位光亮剂足够则细晶光亮度尚可但起纵纹,填平剂不足则出现粗糙结晶雾朦,镀层致密度很差,一价铜浓度很高,氯离子消耗很快。
由于一价铜浓度很高,电流密度稍稍提高均消耗于一价铜的快速还原,若光亮剂足够,则结晶细致光亮,但镀层增厚快,均匀度差,低位走位弱;若光亮剂不足,高低区全部电流均消耗于快速还原而镀层起雾、粗糙、麻点,高区甚至出现毛刺。
镀件容易出现边缘肥厚现象,功能件极易镀死;酸性光亮镀铜只有在还原速度控制得当,过电位、极化度与电压、电流密度协调时,具有最佳的走位能力、最佳的填平速度和最佳的细晶光亮度。
滚镀光亮酸铜工艺

滚镀光亮酸铜工艺一、特点光亮添加剂专用于滚镀酸铜工艺。
这类添加剂具有出光速度快,光亮范围宽,镀层结晶细的特点,还有镀液稳定性能好,处理周期长的优点。
二、工艺范围名称范围标准硫酸铜CuSO4·5H2O (克/升) 硫酸H2SO4 (克/升) 氯离子cl - (毫克/升)添加剂-A(紫色) (毫克/升)添加剂-B(黄色) (毫克/升)添加剂-C(绿色) (毫克/升) 130—17080—12050—800.3—0.80.8—1.23--5150100600.514温度(°C)阴极电流密度(A/dm2) 阳极电流密度(A/dm2) 阳极过滤搅拌20—281—20.6—1.2含磷铜连续过滤空气搅拌221.51.0含磷铜连续过滤三、添加剂消耗量光亮添加剂的消耗量,与镀液温度有关,操作温度的升高会增加消耗量,还与镀液带出损耗有关,通常情况下其消耗量:添加剂-A(紫色) 150-250毫升/千安小时添加剂-B(黄色) 50--80毫升/千安小时添加剂-C(绿色) 可参照A剂消耗量1/10补给四、注意事项1、钢铁件、锌合金件必须先进行预镀铜或预镀镍后再滚镀酸铜。
预镀层的厚度,按照镀件形状,底金属材料等因素确定。
2、添加剂-A是低电位走位剂,能提高低电流区光亮度及走位。
3、添加剂-B是改善高电流区光亮度,并防止镀层烧焦。
4、添加剂-C是开缸剂,生产过程中一般不需添加,可按镀液带出损耗,再以补充。
补充量可参照A剂消耗量的1/10左右补充。
5、光亮剂采取勤加少加为好,以达到均匀的光亮度。
五、开缸必需条件:1、冷冻机(必需保持镀液为25℃以下2、阴极面积(阴极1:阳极1.5)3、阳极材料:磷铜球4、空气搅拌装置5、连续过滤装置6、转速:8-10转/分7、滚桶内装限力条(限力条高约10m,不少于3处)8、滚镀碱铜60分钟9、滚镀酸铜40分钟10、滚镀镍30分钟。
- 1、下载文档前请自行甄别文档内容的完整性,平台不提供额外的编辑、内容补充、找答案等附加服务。
- 2、"仅部分预览"的文档,不可在线预览部分如存在完整性等问题,可反馈申请退款(可完整预览的文档不适用该条件!)。
- 3、如文档侵犯您的权益,请联系客服反馈,我们会尽快为您处理(人工客服工作时间:9:00-18:30)。
酸性光亮镀铜工艺及配方一、酸性镀铜光亮剂特点:1、快速出光, 特好的填平度, 即使低电流密度区也可得到极高的填平度。
2、广泛的电流密度范围均可得到镜面亮度。
3、工作温度范围宽, 18—< xmlnamespace prefix ="st1" ns ="urn:schemas-microsoft-com:office:smarttags" />40℃都可得到镜面亮度。
4、镀层内应力低, 延展性好, 电阻率低, 可应用于各种不同的基体材料电镀。
铁件、锌合金件、塑胶件等同样适用。
5、光亮剂对杂质容忍度高, 性能稳定, 易于控制。
一般在使用一段长时间( 约800-1000安培小时/升) 后, 才需用活性碳粉处理。
6、沉积速度快。
在4.5安培/平方分米的电流密度下,每分钟可镀1微米的铜层,电镀时间因而缩短。
( 酸性镀铜溶液是一种强酸性的简单盐电镀溶液, 镀液中没有使用络合剂。
)二、电镀工艺条件:原料范围标准硫酸铜200-240g/L220 g/L硫酸55-75g/L65 g/L氯离子15-70mg/L20-40mg/LBFJ-210Mμ5-12ml/L8 ml/LBFJ-210A0.5-1.0ml/L0.6 ml/LBFJ-210B0.5-1.0ml/L0.6 ml/L温度18-40℃24-28℃阴极电流密度0.5-10A/dm2阳极电流密度 1.5-8A/dm2搅拌空气搅拌空气搅拌三、镀液的配制:1、先在镀槽中( 待用缸或备用缸) 加入1/2体积蒸馏水或去离子水, 加热至40-50°。
( 所用水的氯离子含量应低于70mg/L( ppm) ) 。
2、加入计算量的硫酸铜, 搅拌至完全溶解。
3、加入活性炭2g/L, 搅拌1小时后静止8小时用过滤泵, 把溶液滤入清洁的电镀槽内。
加去离子水至规定体积。
4、在不断搅拌下慢慢加入计算量的化学纯硫酸, ( 注意: 此时会产生大量热能, 故需强力搅拌, 慢慢添加, 以使温度不超过60℃。
添加硫酸时要特别小心, 应穿上保护衣服, 及戴上手套、眼罩等, 以确保安全) 。
5、镀液冷却至25℃时, 加入标准量氯离子。
( 分析镀液中氯离子含量, 如不足应加入适量的盐酸或氯化钠, 使氯离子含量达到标准。
)6、加入光亮剂并搅拌均匀, 在正常操作规程条件下, 把镀液电解3-5安培小时/L, 便可正式试镀、生产。
四、镀液的成份及作用:1、硫酸铜: 在镀液中提供铜离子。
铜离子含量低, 容量在高电流密度区造成烧焦现象及出光慢, 铜离子过高时, 硫酸铜有可能结晶析出。
2、硫酸: 在镀液中起导电作用。
硫酸含量低时, 槽电压会升高, 易烧焦; 硫酸含量太多时, 阳极易钝化, 槽电压会升高, 槽下部镀不亮, 上部易烧焦。
3、氯离子: 在镀液中起催化作用。
氯离子含量过低, 镀层容易在高中电流区出现条纹, 在低电流区有雾状沉积; 氯离子含量过高时, 光亮度及填平度减弱, 在阳极上形成氯化铜, 引起阳极钝化, 槽电压会升高。
4、开缸剂。
开缸转缸或添加硫酸时使用, 开缸剂不足时, 会使镀层的高中电流区出现条纹状凹凸不平, 过多时, 低电流区发雾、对光亮度无明显影响。
5、A: 铺光剂, 为低区光亮剂, 不足时填平作用差, 过量时低区整平差。
使低电流区电镀良好。
A剂过多。
会造成低电位发黑, 高电位烧焦, 此时可加入B剂抵消。
6、B: 主光剂, 为高电位光亮剂, 使高电位区获得高填平的光亮镀层, 含量低时, 出光慢, 镀层易烧焦; 过多时, 可引起低电位区发雾, 易产生麻沙镀层, A剂消耗量增加, 在生产中, 如有足够的光亮度, 应少加或不加。
五、添加剂的补充方法:正常操作下: 每通电1000A/H需加BFJ-210Mμ开缸剂60-80ml, A100-180ml, B 50-90ml。
ST-500A剂消耗量为80-120ml/KAH ST-500B剂消耗量为40-60ml/KAH。
六、设备1.镀槽柔钢缸内衬聚乙烯、强化聚脂或其它认可材料。
2.温度控制加温及冷却管可用石墨、钛、聚四氟乙烯、聚氯乙烯或聚乙烯等材料。
3.空气搅拌用阴极移动或压缩空气等方式搅拌镀液, 能够增大允许工作电流密度, 以加快沉积速度。
所需的空气由设有过滤器的低压无油气泵供应, 所需气量为12-20立方米/小时/平方米液面。
打气管最好离槽底30-80毫米, 与阴极铜棒同一方向。
气管需钻有两排直径3毫米的小孔, 45度角向槽底, 两排小孔应相对交错, 每边间距80-100毫米( 小孔交错间距40-50毫米) 。
镀槽最好同时有两支或以上打气管, 气管聚氯乙烯或聚乙烯材料, 内径20-40毫米, 两管间距150-250毫米。
当采用搅拌时还应配备良好的过滤设备。
在添加十二烷基硫酸钠镀液中, 不宜采用空气搅拌。
4.阴极摇摆镀液搅拌以空气搅拌为主, 同时附设阴极摇摆有利工件接触新鲜镀液。
在横向移动时, 冲程幅度为100毫米, 每分钟来回摇摆20-25次。
上下移动时, 冲程幅度为60毫米, 每分钟上下摇摆25-30次。
5、阳极电解铜极在硫酸盐镀铜镀液中往往会产生铜粉, 导致镀层产生毛刺、粗糙。
若采用含有少量磷(0.030%~0.075%)的铜阳极能够减少铜粉。
如果铜阳极含磷量过高, 便会产生一层较厚的膜, 阳极不易溶解, 导致镀液中铜含量下降。
阳极与阴极面积的比例一般为(1~2): 1, 在硫酸含量正常和无杂质干扰的情况下, 阳极不会钝化, 镀液中铜含量能基本保持平衡。
为了防止铜阳极中的不溶性杂质落入镀液内而影响镀铜层质量, 必须用阳极保护框或阳极袋(二层以上涤纶布)。
七、操作条件影响1、电流密度光亮电流密度范围随槽液中硫酸铜含量的降低和硫酸含量的升高而缩小, 随温度的升高而升高。
镀液搅拌速度影响到光亮电流密度范围, 阳极电流密度过高时, 镀层光亮性差, 添加剂消耗快, 且易钝化;操作中应根据镀液温度的变化和搅拌的强度及时调整阳极电流密度。
在较高的槽液温度和强烈的搅拌情况下, 可采用较大的电流密度; 反之, 电流就应开小一些。
不然, 将会造成镀层粗糙疵病。
在正常的阴极电流密度下, 阴极主要发生Cu2+得到电子生成金属铜的反应, H+放电的机会很少, 因此阴极电流效率接近100%。
阴极电流密度: 4A/dm2 (1-8 A/dm2)2、温度25℃(20-30℃) 对温度最好控制在23±2℃不可太高温度, 电解液温度对镀层光泽性是有影响的, 温度升高, 光亮电流密度也相应升高; 温度大于30℃以上会使光亮度下降, 特别是在中区和低区。
过低的温度会导致镀层烧焦。
3、阳极选择使用一般紫铜作阳极, 将产生大量阳极泥, 且产生大量Cu+, 从而严重影响镀层质量。
因此, 必须选择含磷量为0.1-0.3%的磷铜板作阳极, 磷含量过高, 阳极易钝化, 为了减少阳极泥污染, 阳极最好用耐酸性材料包裹, 包裹材料宜宽大些;4、槽液最大工作电量槽液的工作电量对槽液的稳定是极其重要的。
工作电流过大时, 阳极易钝化, 槽液电阻大, 镀件光亮不均匀, 光亮度差, 添加剂消耗过快。
因此,每升槽液中的电流最大为0.5A, 最5、阳、阴极面积比1: 1-36、电压2V 范围(1-4V)7、沉积速度0.85-0.9?m/min( 在4A/dm2下)8、槽液密度 1.161-1.18g/ml( 在20℃下)阳极: 磷铜球或磷铜角(含磷0.03-0.06%),阳极袋的材料为PP槽体材料: 耐酸材料( PE, PP, PTFE, PVC)冷却: 外面的材料为钛, 特氟隆, PVC, 或PE搅拌: 机械搅拌3-6m/min或空气搅拌20-30m3/h*m过滤: 过滤是必须的, 每小时能处理1-3倍的槽液量材料: PVC或PP,孔径:5-10mm加热用自动自动调温器调节温度, 外面用防腐材料( 如: 特氟隆)维护: 因蒸发损失的镀液可用去离子水补加.分析值需定期调整, 铜含量可经过对阳极面积的调整来控制, 为了避免金属杂质的过量带入, 应及时去除掉入到槽中的铁件和锌压件。
八、注意事项要避免酸性光亮镀铜故障,必须注意如下几点:(1)选择优质的磷铜阳极是保证酸性光亮镀铜质量的先决条件。
当前电镀原料市场上,广东高力表面技术有限公司生产的含磷质量分数0.04%~0.065%的五金电镀磷铜、PCB线路板磷铜是质量非常不错的产品。
(2)选择优质的酸性光亮镀铜添加剂是十分必要的。
安美特、日本大和、广东高力表面技术有限公司、安徽省巢湖市奋进表面技术有限公司等生产的系列酸性光亮镀铜添加剂都是值得信赖的产品。
(3)严格的操作规范是酸性光亮镀铜工艺的保证。
(4)酸性光亮镀铜添加剂少加、勤加,按照安培小时添加,不要盲目地追求快速光亮而多加乱加添加剂,这样只会使镀液快速失调,分解产物大量增加,缩短镀液寿命。
建议使用的体积电流密度不要超过0.25A/L,否则镀液升温很快,电流效率降低,容易造成添加剂失效,消耗量增大,有机分解产物大量增加,镀层容易产生针孔。
(5)注意槽电压和硫酸的含量。
槽电压升高,说明导电系统有问题或者阳极产生钝化。
当硫酸的含量有逐渐下降趋势时,说明阳极有钝化现象,要适当补加阳极;当硫酸含量有逐渐上升趋势时,说明阳极过多,此时,为避免阳极背面的磷铜膜脱落和防止一价铜离子的产生,要适当减少阳极。
(6)定期进行活性炭吸附处理,避免大量的有机分解产物的累积,影响产品质量。
在酸性镀铜工艺中,造成镀铜层有蓝膜的因素很多,有镀液中的硫酸含量较少,添加剂中某些成份如: 聚乙二醇类、AEO类、咪唑等表面活性剂过多以及镀液的分解产物等。
如果我们能够理性地遵照工艺规范操作,并把好原材料质量关,酸性光亮镀铜故障是比较少出现的。
参考配方:( 含量(g/L))。